Wie Figure Engineering ein fortschrittliches SLA-Material für das US-Verteidigungsministerium entwickelte
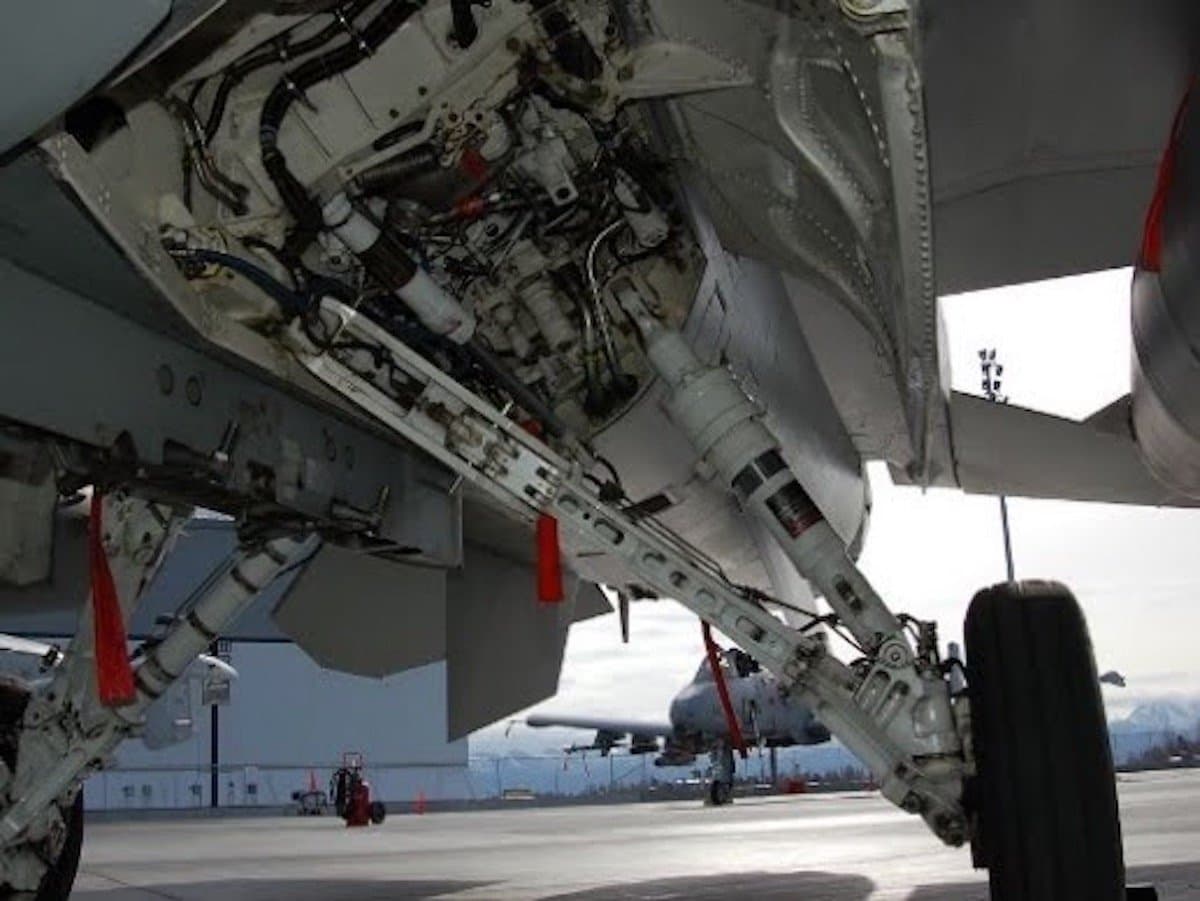
Für jede Flugstunde eines Jets des US-Verteidigungsministeriums (DoD) fallen etwa 12 Stunden Wartung an. Obwohl Wartungs-, Reparatur- und Überholungsarbeiten unerlässlich sind, damit jedes Flugzeug sicher und optimal funktioniert, werden diese Prozesse oft durch manuelle Arbeiten und traditionelle Verfahren verlangsamt.
Das Verteidigungsministerium sucht ständig nach Wegen, um diese Abläufe zu optimieren und den Workflow effizienter zu gestalten. Figure Engineering hat durch die Nutzung des neuen offenen Ecosystems von Formlabs eine innovative und erschwingliche Lösung entwickelt, um genau das zu erreichen.
Figure Engineering nutzte die Geschwindigkeit des SLA-3D-Druckers Form 4 von Formlabs, um ein neues Material speziell für Abdeckungen und Produktionswerkzeuge für den Galvanisierungsprozess zu entwickeln. Dank des Druckeinstellungseditors und des Open Material Mode konnte das Team um Mitbegründer Jonathon McDaniels den Materialentwicklungsprozess präzise abstimmen und so eine Lösung für ein millionenschweres Problem finden.
Dirty, Dull, Dangerous: Auf dem Weg zu einer besseren Lösung
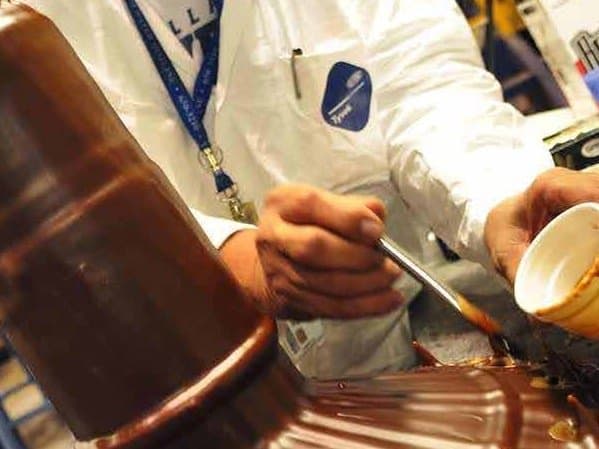
Das manuelle Lackieren zur Maskierung von Bauteilen für die Galvanisierung kann gefährlich sein, besonders wenn toxische Materialien im Spiel sind. Und sobald die Belastungsgrenzen der Mitarbeitenden erreicht sind, muss der gesamte Vorgang gestoppt werden. Das führt zu noch längeren Standzeiten der Flugzeuge.
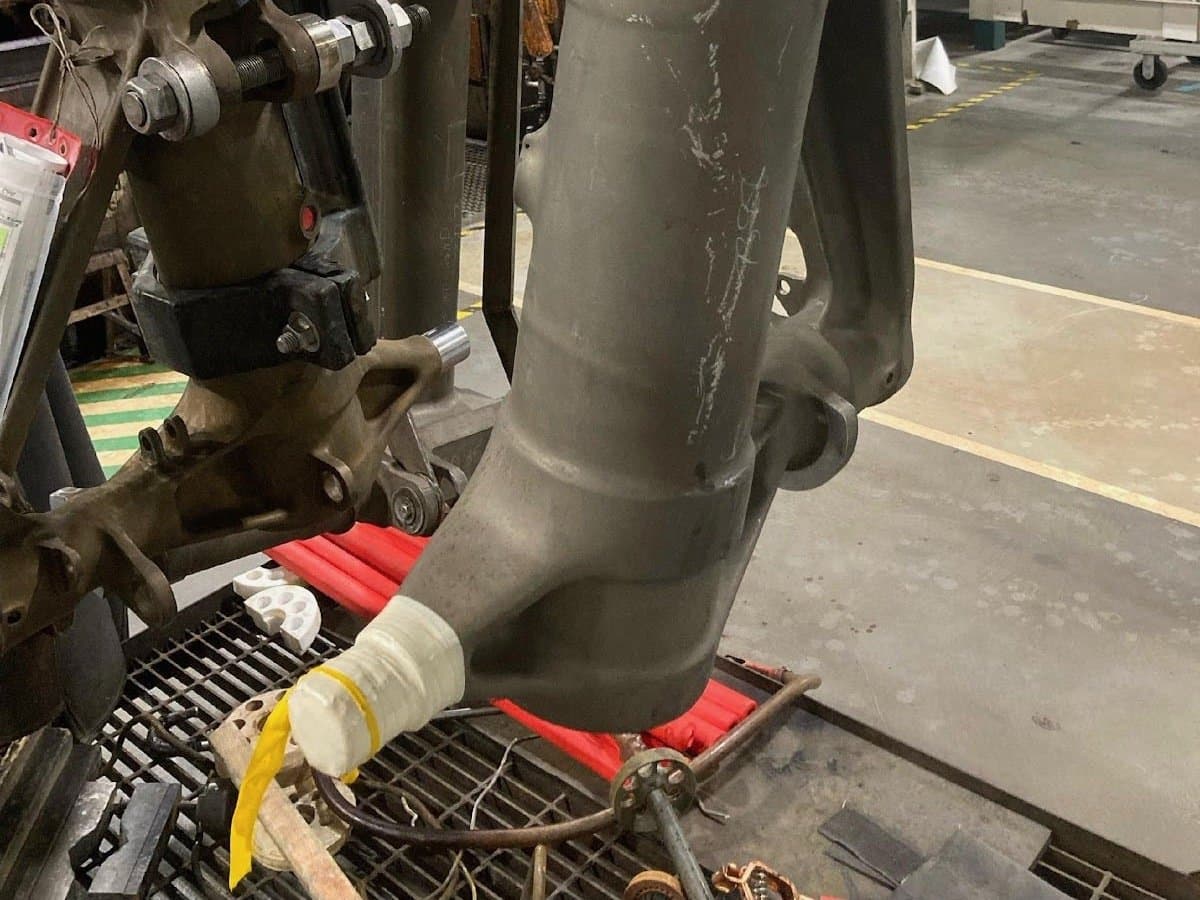
Manuelles Abkleben als Maskierung für den Galvanisierungsprozess ist nicht nur zeitraubend, sondern auch arbeitsintensiv. Außerdem muss es für jedes einzelne Bauteil wiederholt werden. Das kostet Zeit und Geld.
Figure Engineering entwickelt fortschrittliche Fertigungs- und Instandhaltungslösungen für verschiedene Abteilungen des Verteidigungsministeriums sowie für private Unternehmen. Für Flugzeuge der US-Luftwaffe, der Navy, der Armee – aber auch für kommerzielle Airlines – wurden Figure Engineering Aufgabenbereiche anvertraut, die im Wartungsprozess häufig übersehen werden: Sandstrahlen, Lackieren, Beschichten und Galvanisieren.
Diese Aufgaben werden informell oft als die „drei Ds“ bezeichnet – von dirty, dull und dangerous, also schmutzig, langweilig und gefährlich. Wie diese Bezeichnung von vermuten lässt, sind diese Vorgänge weniger sichtbar und weniger verständlich als z. B. der Austausch von Triebwerken oder Innovationen an den Flügelspitzen. Doch sie wirken sich ebenso stark auf die Leistung des Flugzeugs aus. Falls diese Verfahren aufgrund ineffizienter Arbeitsabläufe zu lange dauern, beeinträchtigt dies die Einsatzbereitschaft des Militärs, treibt die Betriebskosten in die Höhe und gefährdet Personal, das oft mit giftigen Chemikalien hantiert.
Figure Engineering hat sich auf innovative Lösungen spezialisiert, um diese Prozesse sicherer und effizienter zu gestalten, und arbeitet seit Jahren mit der Instandhaltung der US Air Force zusammen. „Die besten Lösungen entstehen in enger Zusammenarbeit mit den Verantwortlichen des Prozesses. Sie kennen die Herausforderungen am besten. Für den Galvanisierungsprozess hörten wir Aussagen wie: ‚Ich bekomme dieses Flugzeug nicht schnell genug fertig, und wir erzeugen zu viel Abfall‘,“ berichtet McDaniels.
Das Problem: Der Galvanisierungs-Workflow bei Flugzeugen
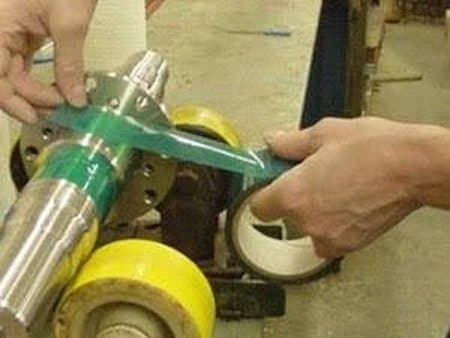
Klebeband wird per Hand aufgetragen.
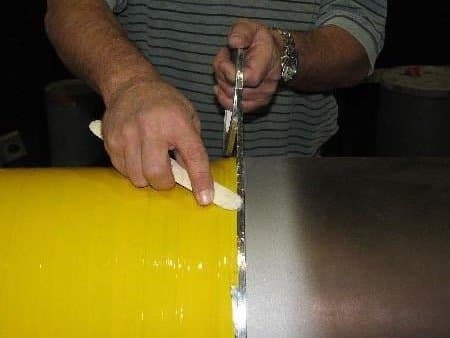
Klebeband wird per Hand zugeschnitten.

Maskierte Teile werden in das Galvanisierungsbad eingetaucht.
Einer der schwierigsten und zeitaufwändigsten Prozesse bei der Wartung, Reparatur und Überholung von Flugzeugen ist das Galvanisieren großer Fahrwerkskomponenten. Der Arbeitsablauf umfasst aggressive chemische Bäder und stundenlange, mühsame Handarbeit, um Bereiche, die nicht beschichtet werden sollen, durch das manuelle Auftragen eines ablösbaren Lacks oder durch Abkleben zu maskieren.
„Der manuelle Aufwand, der nötig ist, um die Beschichtung genau an die gewünschten Stellen zu bringen und von unerwünschten Bereichen fernzuhalten, ist extrem arbeitsintensiv, langwierig und kostspielig. Die Werkstätten wollten den Anteil dieser Handarbeit verringern und stattdessen Masken entwickeln, die man festklemmen oder verschrauben kann“, erklärt McDaniels.
Als Figure Engineering jedoch begann, Abdeckungen für die Galvanisierung zu entwerfen und Prototypen herzustellen, stieß es auf eine Reihe komplexer Probleme. „Als wir die ersten Studien durchführten, stellten wir fest, dass es nichts gab, was den extremen Bedingungen des Galvanisierungsprozesses standhalten konnte. Das Material musste eine hohe chemische Beständigkeit aufweisen und hochbelastbar sein – die Teile werden ständig fallen gelassen oder mit Hämmern geschlagen, daher müssen sie sehr stoßfest sein“, so McDaniels.
Neben dem Material war auch die Wahl der richtigen Druckhardware eine Herausforderung. „Zunächst haben wir uns alle Optionen offen gelassen. Wir brauchten einen Drucker, der leicht zu bedienen und zuverlässig ist. Und gleichzeitig musste es eine bekannte Marke sein, damit wir breite Unterstützung von den verschiedenen Institutionen erhalten“, gibt McDaniels an.
Nachdem das Team mehrere Teile aus Schmelzschichtungs- (FDM) und SLS-3D-Druckern (selektives Lasersintern) getestet hatte, wurde klar, dass vollständig dichte, porenfreie Teile erforderlich waren. Die im Galvanisierungsprozess verwendeten Chemikalien drangen in die FDM- und SLS-Druckteile ein. Und nachdem sie aus dem Bad genommen wurden, traten die giftigen Chemikalien noch aus den Oberflächen hervor. Der Kunstharzdruck war die Lösung. Und obgleich Figure Engineering mehrere 3D-Drucker ausprobierte, stach einer besonders heraus.
„Es wurde ziemlich schnell klar, dass Formlabs das Unternehmen war, mit dem ich arbeiten wollte. Die niedrigeren Kosten für qualitativ hochwertigere Geräte, die hohe Zuverlässigkeit der Drucker und der bekannte Name machten Formlabs zur besten Wahl.“
Jonathon McDaniels, Mitbegründer von Figure Engineering
McDaniels begann mit dem Form 3+ und optimierte die Druckeinstellungen, während er mit dem Open Material Mode eine angepasste Materialformulierung entwickelte. Die Markteinführung des Form 4 beschleunigte den iterativen Entwicklungsprozess massiv. Und die Entwicklung der maßgeschneiderten Kunstharze nahm Fahrt auf.
„Als der Form 4 herauskam, verschwanden viele unserer Probleme über Nacht. Der Form 4 war ein echter Gamechanger, besonders beim Druck mit diesen extrem komplizierten Materialien. Wir setzen neue Grenzen des Möglichen in der additiven Polymerfertigung, um diese Materialien widerstandsfähig genug für den Galvanisierungsprozess zu machen“, führt McDaniels aus.
Entwicklung einzigartiger Materialien mit Formlabs' offenem Ecosystem
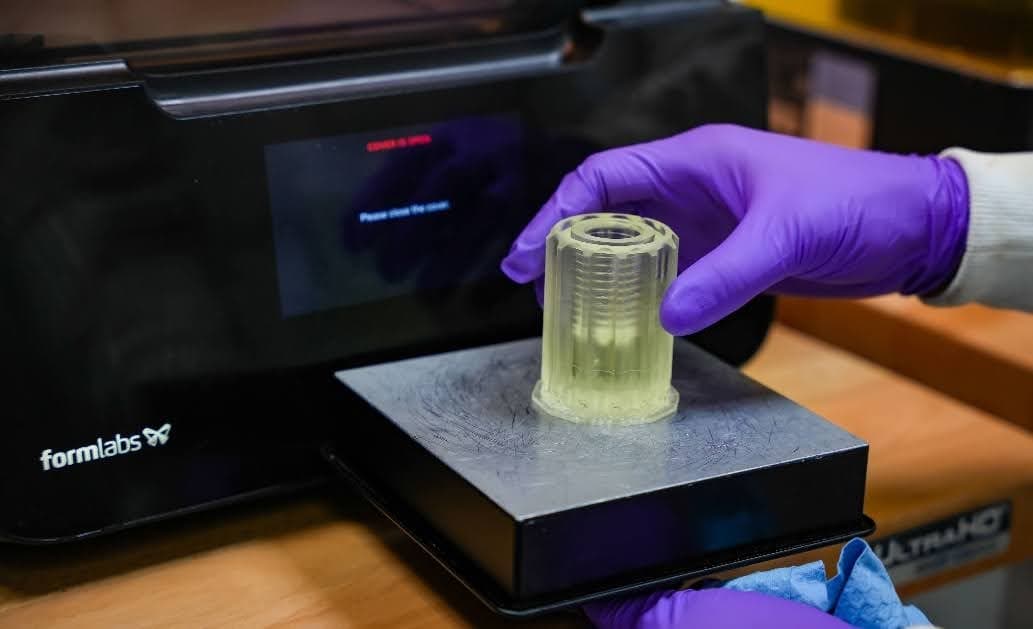
Der Form 4 verschaffte dem Team von Figure Engineering den nötigen Schub. Mit der dreifachen Menge an Iterationen pro Tag erhielt es schnelleres Feedback und konnte mehr Druckparameter in kürzerer Zeit testen, um die perfekten Einstellungen auszuloten.
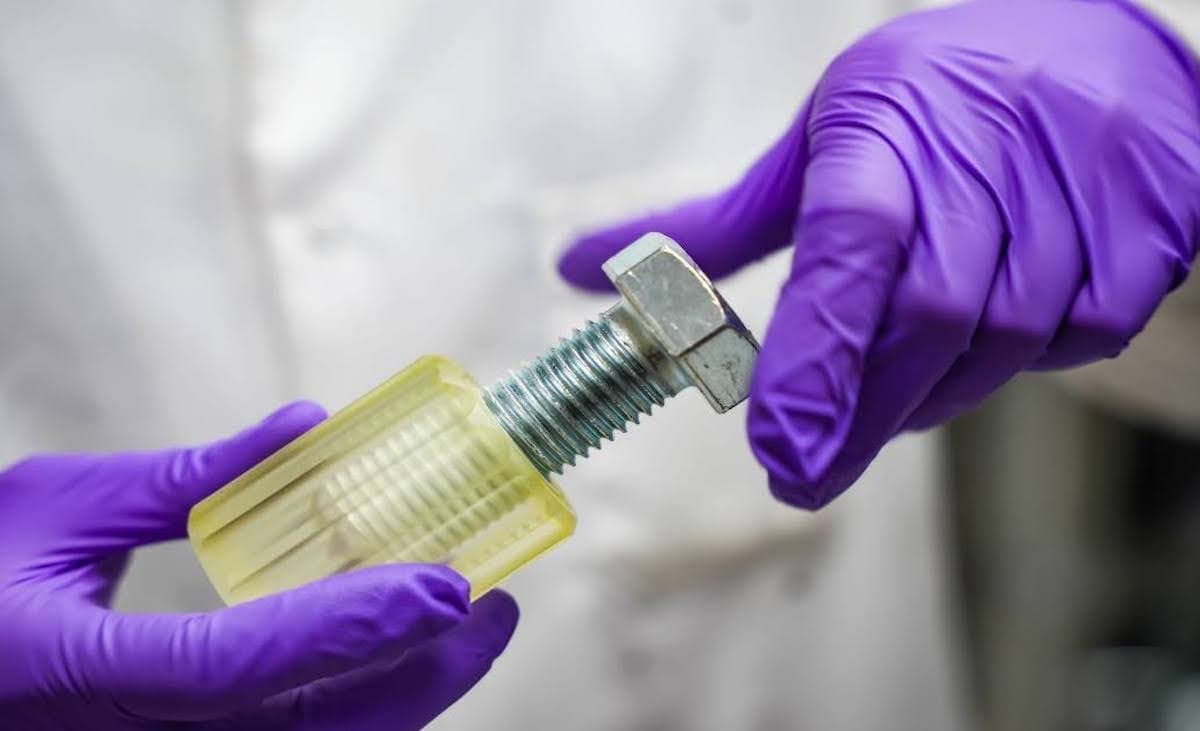
Das von Figure Engineering eigens entwickelte Material ermöglicht die Herstellung hoch chemikalienbeständiger, robuster und wiederverwendbarer Maskierungswerkzeuge – wie dieses hier, das bei der Galvanisierung direkt auf eine große Schraube aufgesetzt wird.
Dank der hohen Druckgeschwindigkeit des Form 4 führte das Team von Figure Engineering mehr als doppelt so viele Tests durch wie vorher. Der entscheidende Faktor war jedoch die Anpassung der Druckereinstellungen, der Schlüssel zur Entwicklung eines neuen, voll funktionsfähigen und technisch fortschrittlichen Materials.
„Ohne den Open Material Mode und die Anpassung der Druckeinstellungen hätten wir gar nicht erst anfangen können“, sagt McDaniels. Die Entwicklung neuer Materialien und das Feinjustieren der Druckereinstellungen erfordert ein Verständnis dafür, wie jede Einstellung das Endergebnis beeinflusst. McDaniels' Hintergrund in der Chemieingenieurtechnik war dabei hilfreich, als er zusammen mit dem Team von Formlabs an der Feinabstimmung bestimmter Prozesse arbeitete. „Die Bearbeitung der Druckeinstellungen war ziemlich einfach. Zu verstehen, wie der Drucker funktioniert, wie das Kunstharz einfließt und die erste Schicht stützt – für solche Dinge gab es klare Informationen. Man bringt seine Zahlen in den richtigen Bereich, und dann entstehen die Teile so, wie sie sollen. Wenn man das verstanden hat, sind die Einstellungen leicht zu verwenden“, meint McDaniels.
Weniger Arbeitsaufwand und Kosten
Die Entwicklung eines Kunstharzes zur Maskierung von Bauteilen für die Galvanisierung erforderte spezielle Materialeigenschaften, die in keinem bestehenden System verfügbar waren. Formlabs bot Figure Engineering eine Plattform als Grundlage für die Forschung – ein schneller und zuverlässiger 3D-Drucker, Zugang zu Druckeinstellungen und Software sowie ein engagierter Support, der eng mit McDaniels und seinem Team zusammenarbeitete.
Die von Figure Engineering entwickelte Sonderformulierung wird bereits in einer Wartungswerkstatt der US Air Force eingesetzt. Sobald die Maskierungsteile entworfen und gedruckt sind, reduziert ihre Implementierung im Galvanisierungsprozess die Vorbereitungszeit der Flugzeugkomponenten erheblich. „Ziel ist weniger manuelle Arbeit in diesem Prozess, um das Personal so weit wie möglich von den chemischen Bädern fernzuhalten“, erklärt McDaniels.
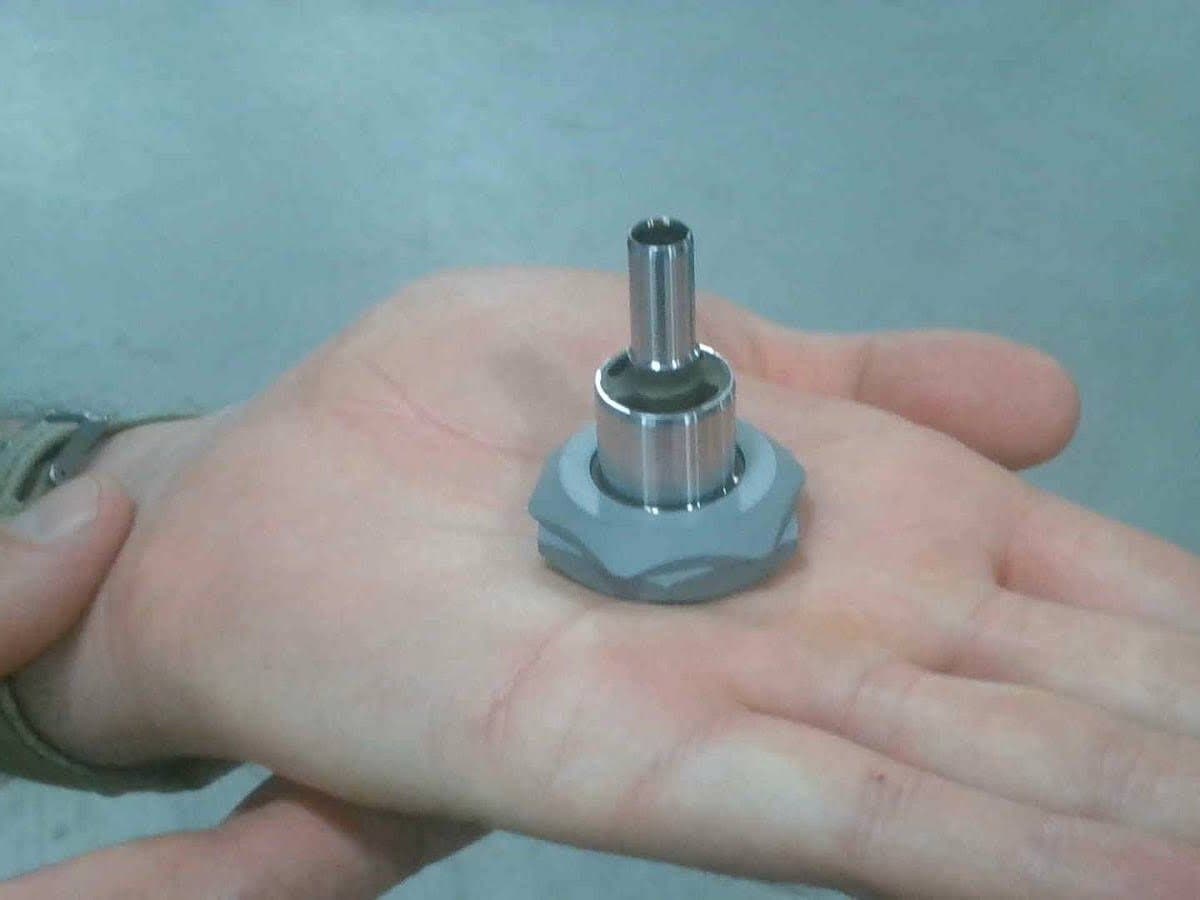
Die manuelle Anfertigung einer Maske für diese Metallschraube kostet etwa 250 $ pro Stück. Der 3D-Druck mit integriertem Gewinde aus Resist™ hingegen kostet gerade einmal 5 $ pro Stück.
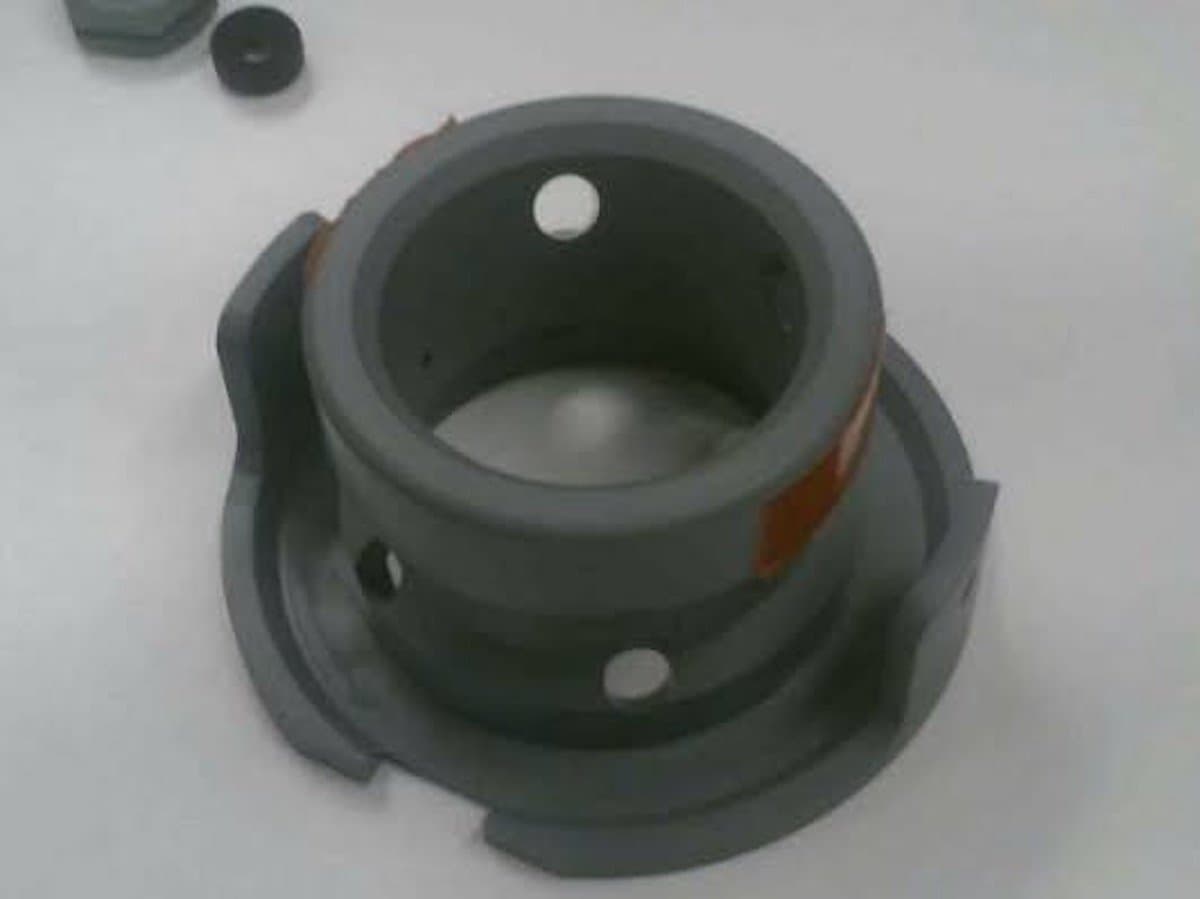
Für dieses große Teil fallen Material- und Arbeitskosten von etwa 550 $ an, während der traditionelle Handmaskierungsprozess Kosten zwischen 2000 $ und 4000 $ verursacht.
Jedes 3D-gedruckte Teil kann für bis zu 20 Galvanisierungszyklen wiederverwendet werden. Lacke und Klebebänder hingegen sind Einwegprodukte und Galvanisierer verbrauchen jährlich Millionenbeträge an Lack und Klebeband. Design, Druck und Nachbearbeitung im 3D-Druck mögen zeitaufwändig sein, aber die Entwürfe lassen sich problemlos zwischen Abteilungen, Standorten oder sogar verschiedenen Streitkräften teilen, sodass jedes Flugzeug mit einem zu galvanisierenden Teil das gleiche Design verwenden kann, das ganz nach Bedarf ausgedruckt wird. Zudem können 3D-gedruckte Masken in Chargen produziert und bis zur Verwendung gelagert werden. Das Maskieren ist ein großer Engpass im Galvanisierungsprozess und der Wechsel auf 3D-gedruckte Masken löst dieses Problem.
Nach oben sind keine Grenzen gesetzt
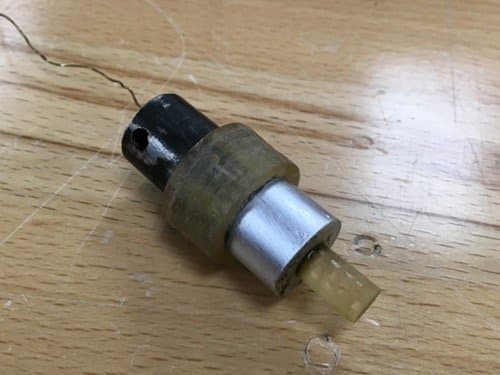
Phase 1: Machbarkeitsstudie
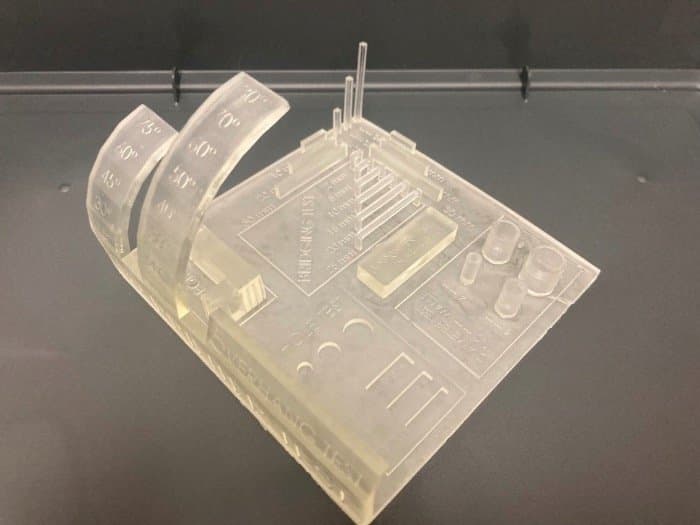
Phase 2: Entwicklung
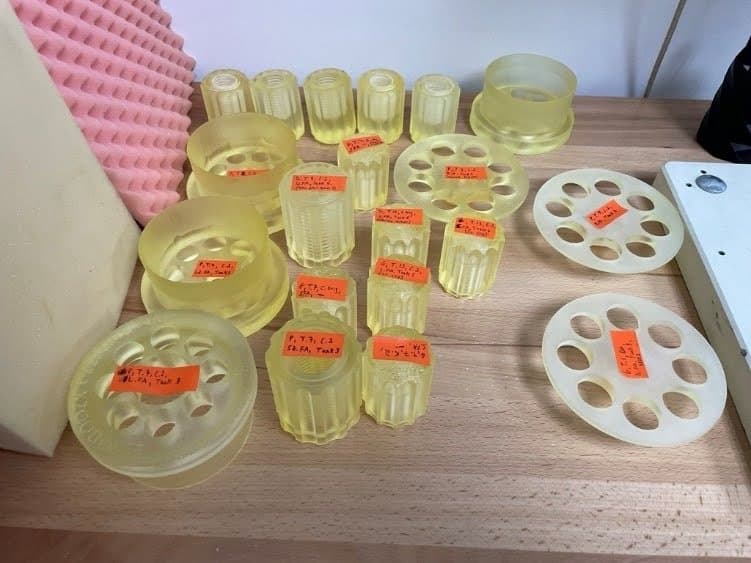
Phase 3: Erste Demonstration
Die Partnerschaft zwischen Figure Engineering und Formlabs hat bewiesen, dass sich große und komplexe Herausforderungen am effektivsten durch Zusammenarbeit lösen lassen. Die chemieingenieurtechnische Expertise von Figure Engineering und das tiefe Verständnis des vorliegenden Problems waren entscheidend. Aber es brauchte mehr als nur einen 3D-Drucker, um zur richtigen Lösung zu gelangen. Nötig waren vor allem Anpassung und Unterstützung innerhalb einer leistungsstarken 3D-Druckplattform.
Mithilfe von Formlabs' offenem Ecosystem und Open Material Mode entwickelten McDaniels und sein Team ein völlig neues Material und einen Workflow für das Verteidigungsministerium. Das spart potenziell Millionen an Material- und Arbeitskosten und verbessert die Sicherheit des Wartungspersonals im ganzen Land. „Unsere Arbeit wäre ohne den Open Material Mode nicht möglich gewesen“, so McDaniels. „Das hat sogar unsere Denkweise in Bezug auf neue Projekte verändert. Dies wird nicht das letzte 3D-Druckmaterial gewesen sein, das wir herstellen. Wir arbeiten mit Verteidigungsministerien und sogar mit kommerziellen, privaten Airlines zusammen. Der Open Material Mode öffnet uns das Tor zu diesen Geschäftsmöglichkeiten.“
Erfahren Sie mehr über Formlabs' offenes Ecosystem oder fordern Sie einen kostenlosen Probedruck an, um sich selbst von der Qualität des Form 4 zu überzeugen.