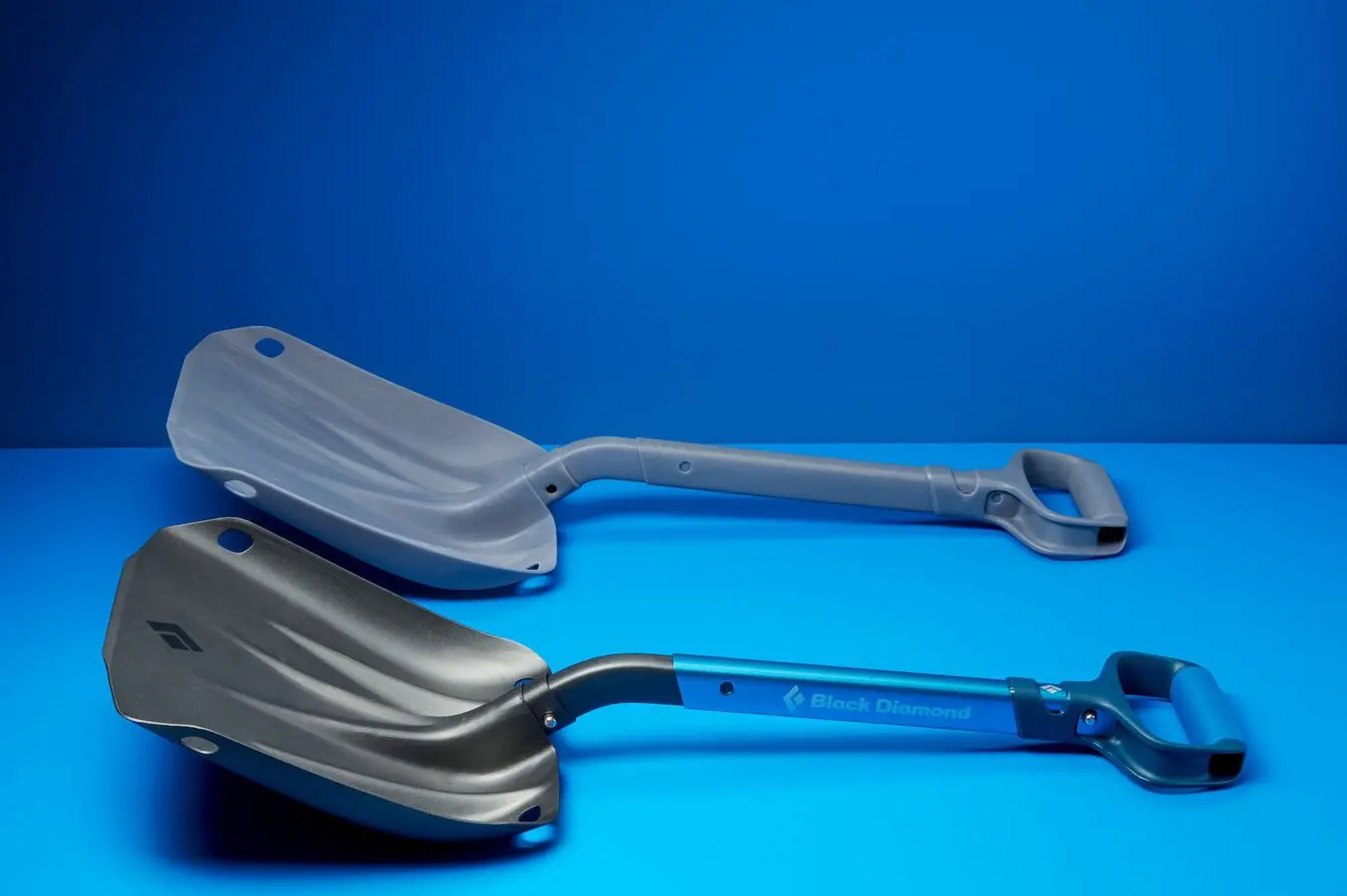
Black Diamond Equipment stellt an sein Designteam eine einzige wesentliche Bedingung: uneingeschränkte, ansteckende Begeisterung für die Ausrüstung, die das Team kreiert. Für die Outdoor- und Bergsteiger-Enthusiasten, die bei Black Diamond jeden Tag ihre Arbeit aufnehmen, ist das eine Leichtigkeit.
Das Designteam von Black Diamond ist besessen von einer Liebe zum Detail und richtet extrem hohe Anforderungen an seine Ausrüstung: So erschafft das Team zuverlässiges Hochleistungsequipment, das selbst am Berghang baumelnd Sicherheit und Spaß garantiert. An die beim Design eingesetzten Hilfsmittel stellt das Team ähnlich hohe Ansprüche. Über die Jahre hat sich seine Flotte von 3D-Druckern stetig vergrößert und umfasst nun großformatige Kunstharz-3D-Drucker, eine Flotte von Kunstharz-Druckern im Desktop-Format sowie betriebsinterne SLS-Technologie (selektives Lasersintern).
Matt Tetzl, Leiter des Produktentwicklungslabors, hat sich mit uns über den Designprozess von Black Diamond unterhalten und erklärt, wie der Form 4, der Form 3L und die Fuse-Serie dem Team dazu verholfen hat, mehr Zeit mit dem Testen der Produkte im Wasatch-Gebirge zu verbringen, anstatt im Labor auf die Fertigstellung von Drucken zu warten.
Drucken und Testen hochleistungsfähiger Ausrüstung im großen Maßstab
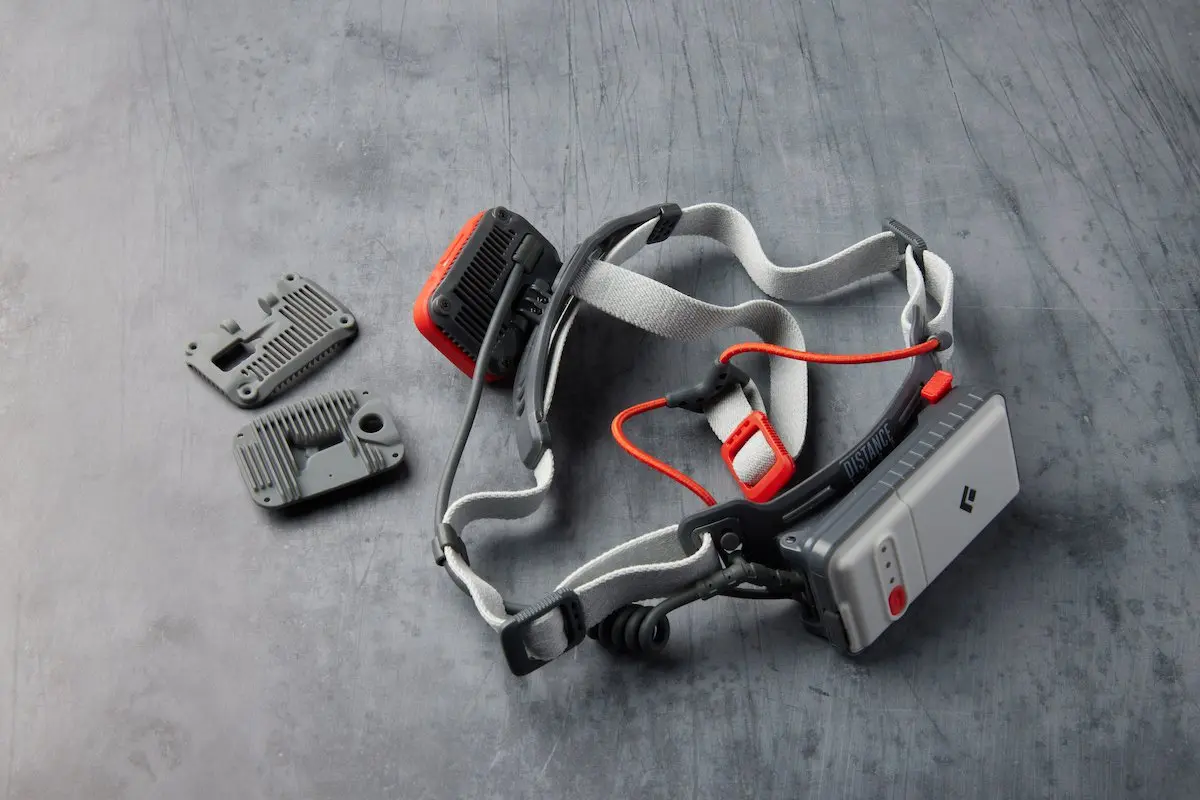
Die Schnelligkeit des Form 4 hat es Tetzl möglich gemacht, drei Iterationen dieser Kopflampenkomponente (links, Grey Resin V5) an einem Tag zu erstellen.
Das Designteam von Black Diamond trägt Sorge dafür, dass seine Produkte der Herausforderung gewachsen sind, Klettereinsteigern ein Gefühl der Sicherheit zu geben und Profis zu neuen Rekorden zu verhelfen. Derartige Ansprüche erfordern ausgiebige Tests – bei einigen Produkten sogar Millionen von Zyklen. Um diese Menge an Tests zu stemmen, ist das 3D-Drucklabor rund um die Uhr in Betrieb. „Unsere Drucker, sowohl SLA als auch SLS, laufen jeden Tag“, so Tetzl. „Mein Versprechen an die Teams ist, dass ich die Teile bis zum Folgetag liefere.“
Tetzl bearbeitet Anfragen von mehreren Teams, sowohl nach Kunstharz- als auch nach Pulverdrucken. Hierfür nutzt er Dashboard, die webbasierte Druckverwaltungssoftware für die 3D-Drucker von Formlabs. Den Großteil der für Funktionstests bestimmten Teile schickte er bisher an die Fuse-Serie, um die Festigkeit und Haltbarkeit von Nylon 12 Powder auszunutzen. Doch der Form 4 bot einen Anreiz, für viele Teile wieder zum Kunstharz-3D-Druck zu wechseln. „Wir haben den Fuse jeden Tag in Betrieb, seitdem er geliefert wurde, aber dank des Form 4 machen wir wieder mehr Kunstharzdruck. Ich kann Teile jetzt schon am selben Tag bereitstellen, an dem sie angefordert werden.“
Die Umsetzung von Prototypen oder funktionalen Testteilen innerhalb eines Tages ist für das Designteam ein immenser Vorteil. „Für die Designvalidierung ist das wirklich großartig. Statt einen Tag für den Druck zu reservieren und einen für das Testen oder Iterieren, schaffen wir jetzt alles am selben Tag“, berichtet Tetzl.
„Bei einem Beleuchtungsprojekt haben wir drei Iterationen an einem einzigen Tag fertiggestellt – bis zu unserem Meeting am Nachmittag entwarfen und druckten wir drei verschiedene Teile.“
Matt Tetzl, Manager des Produktentwicklungslabors, Black Diamond
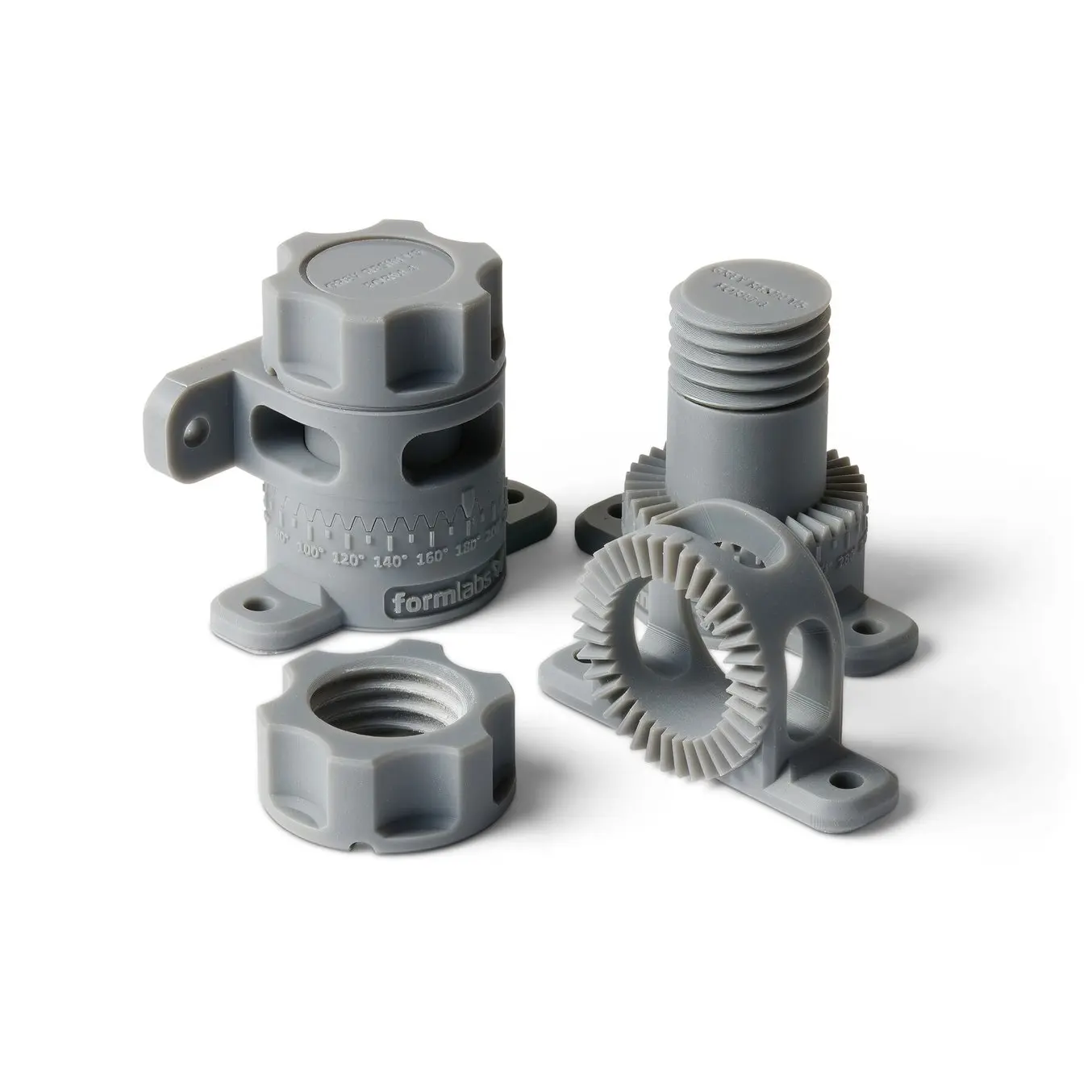
Kostenlosen Probedruck anfordern
Sehen und fühlen Sie die Qualität von Formlabs aus erster Hand. Wir senden Ihnen einen kostenlosen Probedruck aus Grey Resin V5 an Ihren Arbeitsplatz.
Zuverlässig im Labor und am Berghang
Ob Bergsport-Einsteiger oder erfahrener Klettersportler: Der Fokus sollte stets die bevorstehende Wanderstrecke oder Felswand sein, und nicht die Sorge, ob die Ausrüstung der Belastung auch standhält. Das Gleiche gilt auch für die Arbeit am Design dieser Ausrüstung – Tetzl und das Team legen das Augenmerk auf ergonomisches Design, Materialauswahl, Ermüdungstests und eine Reihe weiterer Faktoren, die beim Design erstklassigen Equipments zählen. Da bleibt kein Raum für die Sorge, ob ein Druck gelingen wird oder ob die Druckteile die Toleranzen einhalten. Der Form 4 hat dem Team vom ersten Tag an erlaubt, den Fokus ganz auf dem Produkt zu halten. „Es war Plug-and-Play. Sobald man das Gerät mit dem Netzwerk verbindet, ist es das wohlbekannte Formlabs-Ecosystem – Teile hochladen, einen Knopf drücken und die fertigen Teile abholen“, erzählt Tetzl.
Von der Einrichtung bis hin zur Integration in den Arbeitsprozess vereinfacht der Form 4 sämtliche Abläufe. „Es war sehr selbsterklärend. Direkt nach dem Auspacken nivelliert man den Drucker und legt los. Es fühlt sich genauso unkompliziert an wie alle anderen Formlabs-Systeme, die ich verwendet habe“, so Tetzl.
Dank der konsistenten Benutzerfreundlichkeit und Zuverlässigkeit des Form 4 ist er für zahlreiche Teile die naheliegende Wahl. „In 99 % der Fälle kann ich mir sicher sein, dass der Druck gelingt. Und beim Rest weiß ich, dass ich das Problem selbst lösen kann. Falls ein Drucker einmal ausfallen sollte, bekomme ich ihn noch am selben Tag wieder betriebsbereit. Es ist toll, diese Gewissheit zu haben“, urteilt Tetzl.
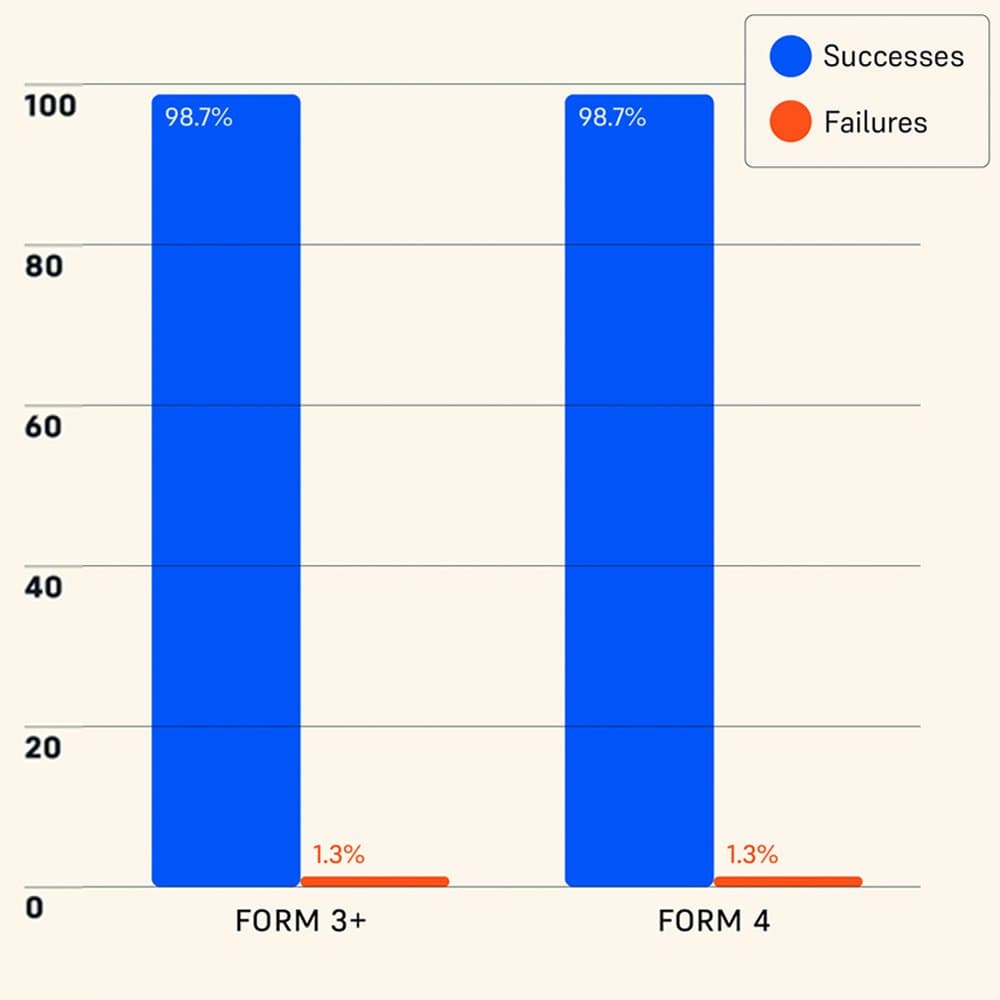
Zuverlässigkeit von Form 4 und anderen Kunstharz-3D-Druckern unabhängig getestet
Der Form 4 von Formlabs erreichte in einer Untersuchung eines unabhängigen, weltweit führenden Produkttesters eine Druckerfolgsrate von 98,7 %. Eine vollständige Beschreibung der Testmethode und die Ergebnisse finden Sie in unserem Whitepaper.
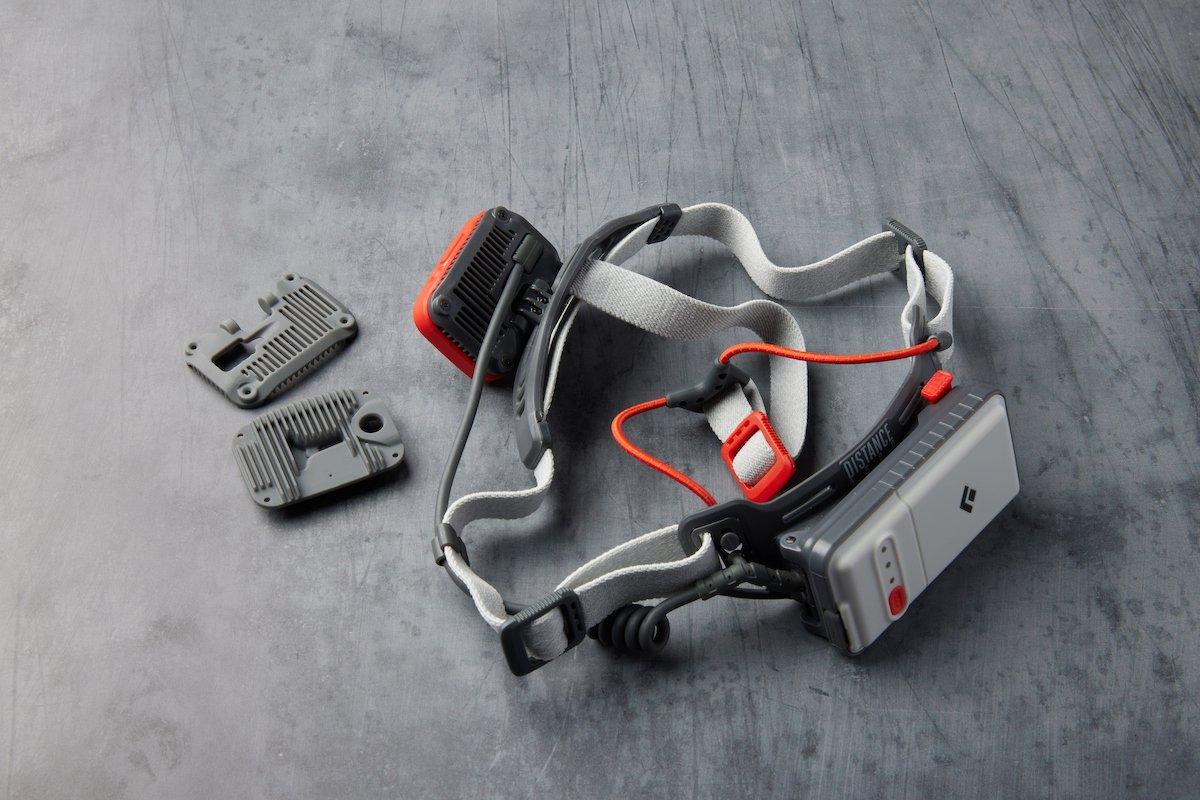
Leitfaden zum Rapid Prototyping für die Produktentwicklung
In diesem Leitfaden erfahren Sie, wie sich Rapid Prototyping in Produktentwicklungsprozesse einfügt, welche Anwendungsfälle dafür bestehen und welche Rapid-Prototyping-Werkzeuge den Produktentwicklungsteams von heute zur Verfügung stehen.
Das Material macht's: Vielseitigkeit, Genauigkeit und Leistung
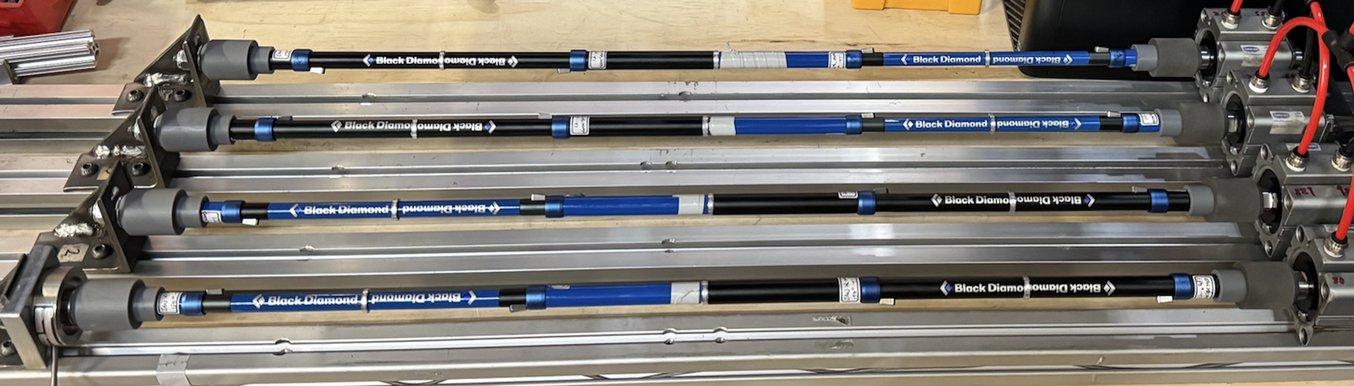
Diese Konfiguration für Ermüdungstests eines Trekkingstocks beinhaltet Halterungen, die auf dem Form 4 aus Grey Resin V5 (links) bzw. auf dem Fuse 1+ 30W aus Nylon 12 Powder (rechts) gedruckt wurden.
Für hochgradig technische Produkte wie die Ausrüstung von Black Diamond muss der Entwicklungsprozess eine große Bandbreite an Materialeigenschaften sowie ausgiebige Prüfungen abdecken. Der Produktentwicklungszyklus eines leichten Trekkingstocks stellte den Form 4 und das neue Grey Resin V5 kürzlich auf die Probe.
Bisher wurden die Komponenten des Trekkingstocks in einer Variante aus Nylon 12 Powder aus dem Fuse-Drucker getestet. „Die meisten unserer Funktionstests machen wir mit Nylonteilen, aber diese Haltevorrichtung haben wir auf dem Form 4 gedruckt, weil wir so innerhalb von Stunden mehrere Designs ausprobieren konnten“, erklärt Tetzl.
Obwohl das Team zunächst unsicher war, ob SLA-Kunstharz der rigorosen Belastungs- und der Reibungsprüfung standhalten würde, die der Trekkingstock durchläuft, widerstanden die Knöpfe aus Grey Resin V5 am Mechanismus des Stocks mehr als einer Million Zyklen mit 35 Pfund Belastung je Zyklus – und dann mehr als einer Million weiteren. „Es ist stärker als die Vorgängerversionen. Bei Helmen erhalten wir einen höheren Detailgrad als mit dem Form 3“, so Tetzl.
Dieser Detailgrad ist entscheidend für die großen Helmprototypen, die das Team auf seinen Desktop- und Benchtop-Druckern fertigt – dem Form 4 und dem Form 3L. „Die Oberflächenqualität ist sehr gut. Das Team ist wirklich beeindruckt von allen Teilen, die wir aus Grey Resin und Clear Resin auf dem Form 4 gedruckt haben.“
Form 3L erweitert die Grenzen des Möglichen
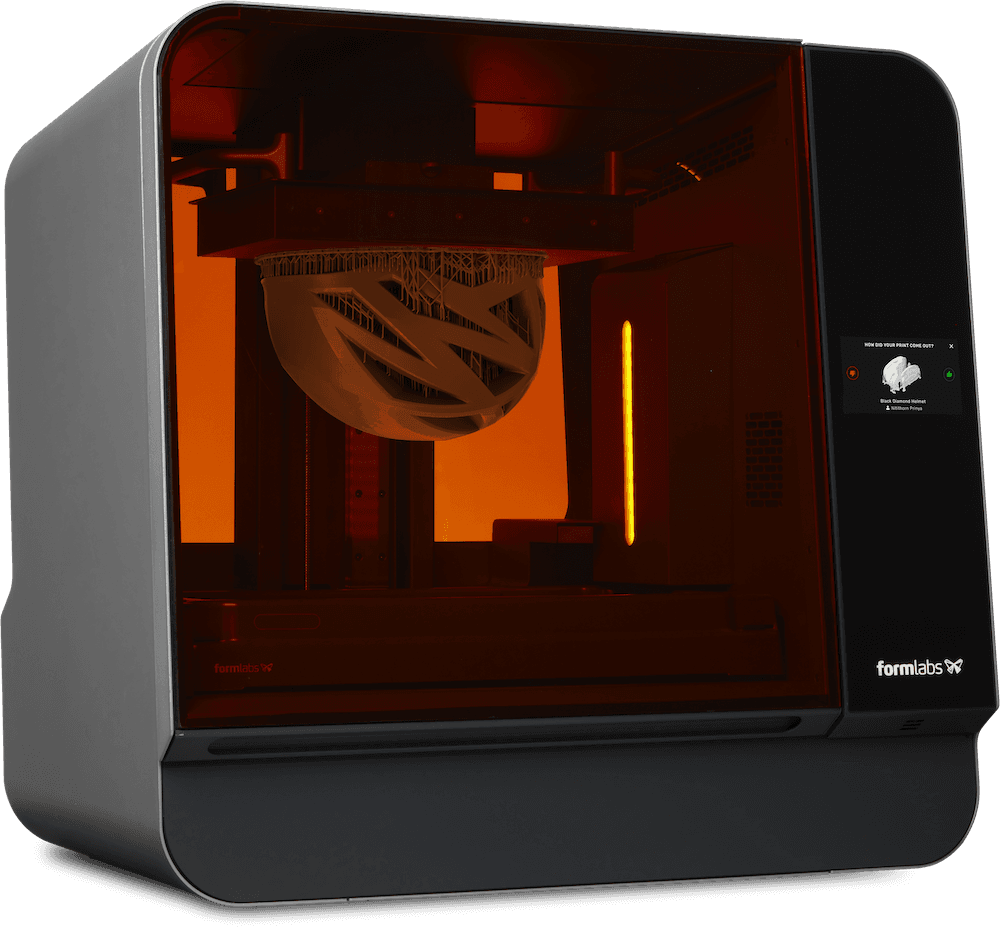
Der Kunstharz-3D-Druck im Benchtop-Format eröffnet die Prototypenfertigung in Lebensgröße, ohne auf Oberflächenqualität und Materialvielfalt zu verzichten.
Die Schnelligkeit, große Materialauswahl und Oberflächenqualität erlauben es dem Designteam von Black Diamond, Prototypen schneller zu fertigen und dabei mehr Kontrolle über den gesamten Prozess zu bewahren. „Wir hatten den Form 3L ursprünglich ausschließlich zur Fertigung von Helmprototypen angeschafft – in den ersten paar Monaten nannten wir ihn sogar den ‚Helmdrucker'. Dann wurde uns klar, dass wir ihn auch für eine Reihe anderer Projekte nutzen können, bei denen es auf ein so großes Volumen ankommt“, so Tetzl.
Vor einigen Jahren unternahm Black Diamond mehrere Schritte, um die Entwicklung einer kompetitiven und sehr technischen Produktkategorie in den eigenen Betrieb zu verlegen: Schuhwerk. Das Team hatte einen firmeninternen Schuster engagiert und erkannte gleich die Möglichkeiten des Form 3L, als dieser für die Helmproduktion angeschafft wurde. „Uns wurde klar, dass wir Zwischensohlen mit einem hohen Detailgrad und Oberflächenfinish in voller Größe umsetzen können. Das Footwear-Team macht eine Menge wirklich winziger Anpassungen am Design der Zwischensohlen, weswegen betriebsinterne Druckkapazitäten im Großformat eine große Hilfe für sie darstellen“, erklärt Tetzl.
War der Form 3L zunächst einfach nur der „Helmdrucker“, so hat er sich innerhalb kürzester Zeit zu einem vielseitigen Hilfsmittel entwickelt, das verschiedenste Projekte möglich macht. In den finalen Entwicklungsphasen eines Eisgeräts druckte das Team mithilfe des Form 3L Prototypen in Lebensgröße, um das Griffgefühl und das Hängen zu testen, ohne die Gefahr, dass ein aus mehreren Teilen montierter Prototyp auseinanderbrechen könnte. Nach vier Jahren verschiedener Designversionen wurden die finalen Iterationsphasen durch den internen großformatigen Kunstharz-3D-Druck enorm beschleunigt.
„Man kann sich ein Eisgerät den ganzen Tag lang ansehen, aber am Ende kommt es darauf an, wie es sich anfühlt. Dass wir es 3D-drucken können und einen Eindruck vom Griffgefühl und dem Hängegefühl erhalten, ist sehr viel wert“, so Tetzl.
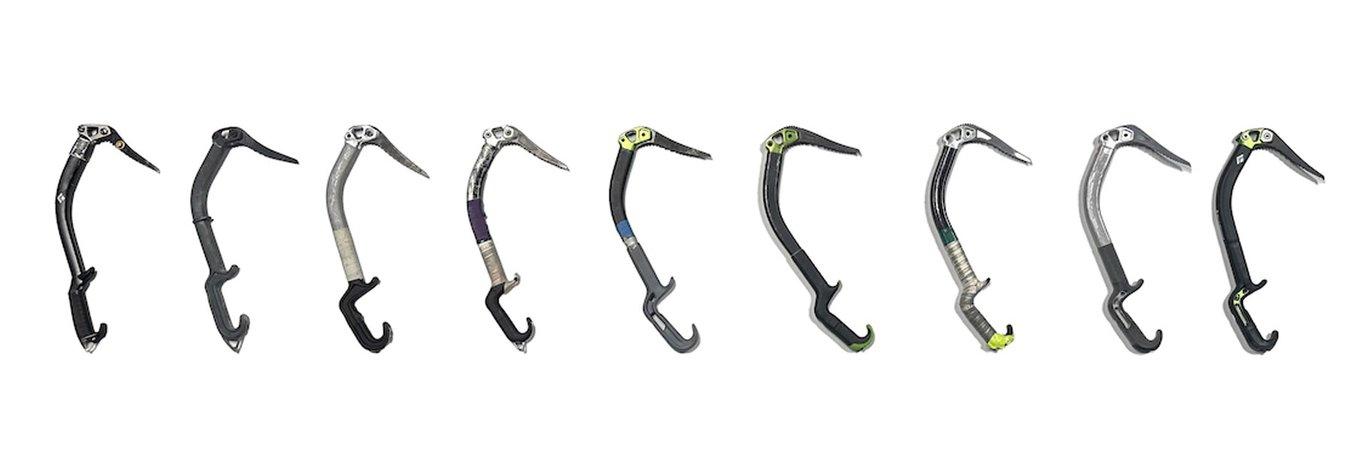
Dank 3D-Druck und betriebsinterner SLA- und SLS-Kapazitäten war es dem Team möglich, Prototypen des Eisgeräts zu erstellen, ohne sich zu sorgen, dass die Montage der Baugruppe das Griffgefühl oder die Schwungkraft beeinflusst.
Die Haptik der Teile ist auch von den Materialien abhängig. Tetzl druckt die überwiegende Mehrheit seiner Teile aus Grey Resin, verwendet für die Herstellung mehrteiliger Urethangussformen jedoch auch Clear Resin. „Wir nutzen den Form 3L mit Clear Resin als Plattform für den Formenbau, besonders für Formen aus mehreren Teilen. Clear Resin ergibt sehr gute Drucke, und es ist praktisch, dass wir das Urethan beim Füllen der Kavität sehen können“, erklärt Tetzl. Die Formen aus Clear Resin werden gewaschen, nachgehärtet, mit Urethan-Formtrennmittel eingesprüht und schließlich befüllt und für 15 Minuten stehen gelassen. Mit betriebsintern 3D-gedruckten Formen lassen sich vollkommen funktionsfähige Prototypen aus weicheren, UV-beständigen Materialien wie Urethan herstellen, ohne dass der Werkzeugbau ausgelagert werden muss.
Bevor das Team Kapazitäten zum großformatigen 3D-Druck in den Betrieb holte, stellte das Outsourcing von Gussformen und großen Prototypen wie Helmen eine hohe Ausgabe dar und verlängerte die Durchlaufzeit des Designprozesses zusätzlich. Die erhöhte Kontrolle über den Entwicklungsprozess von Helmen, Zwischensohlen und Gussformen sorgt nun für niedrigere Kosten und umso kürzere Durchlaufzeiten.
Betriebsintern gefertigte Nylonteile für Praxistests und mehr
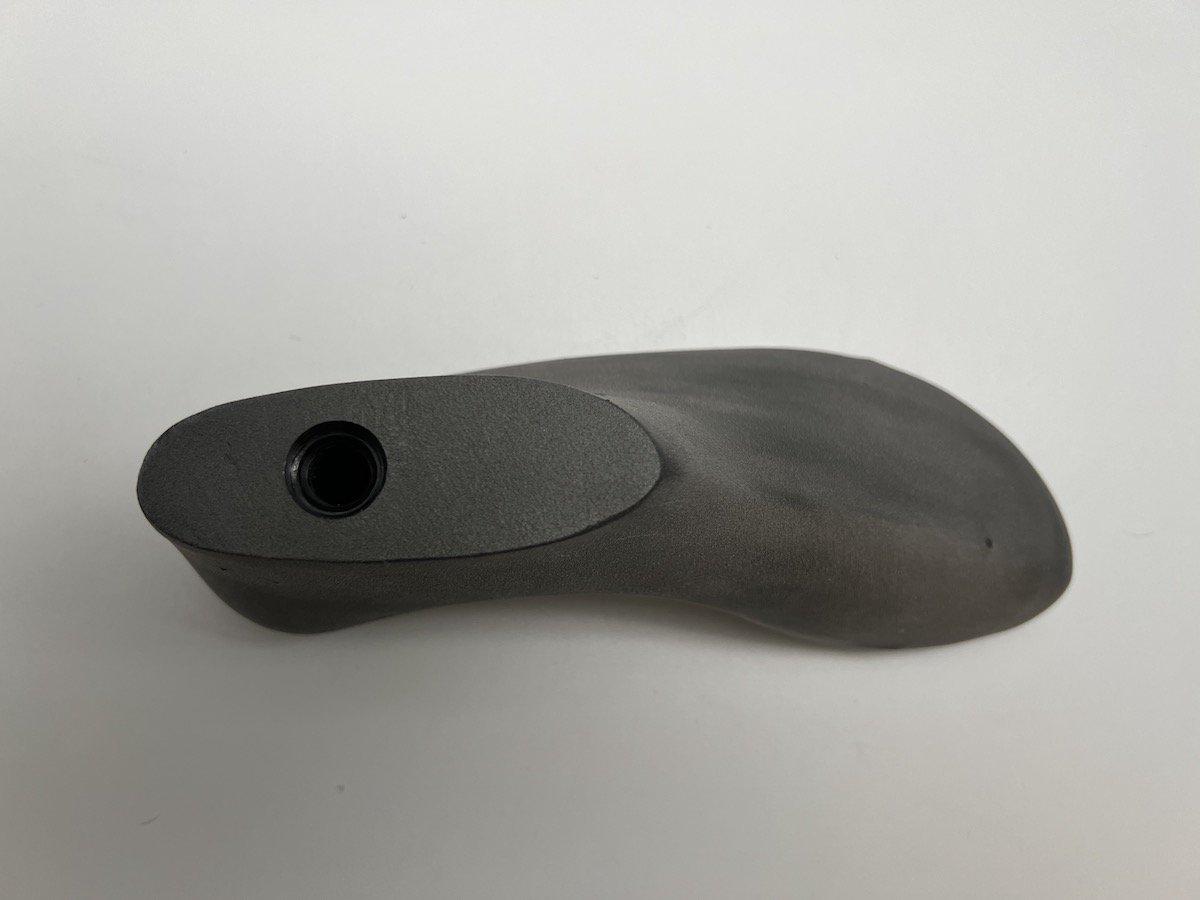
Mit diesem Leisten, der betriebsintern aus Nylon 12 Powder auf dem Fuse 1+ 30W gedruckt wurde, senkt das Team Kosten – bei Outsourcing kann ein zerspantes Nylonteil wie dieses bis zu 2000 $ kosten, während der betriebsinterne Druck nur 65 $ kostet.
Zusätzlich zum großformatigen Kunstharz-3D-Druck hat Tetzls Team auch den SLS-Druck ins eigene Haus verlagert. Nach der Designvalidierung mit Kunstharz setzte es für die Funktionstests in der Praxis robustere, für die Endverwendung geeignete Materialien ein.
Früher hatte Tetzl Teile an einen 3D-Druck-Dienstleister mit einem MJF-Drucker gesendet, der ihn jedoch teuer zu stehen kam. „Es war der gleiche Prozess mit den gleichen Materialien, also machte es Sinn, die Sache betriebsintern zu lösen, um schneller und kostengünstiger zu arbeiten. Das Ergebnis war genau das, was wir wollten: Wir erhalten die meisten Teile 80 % günstiger“, berichtet Tetzl.
Bei derartigen Prototypen für Praxistests ist es wichtig, dass sie schwerer Belastung und hoher Beanspruchung standhalten können. Die Festigkeit und Haltbarkeit von Nylon 12 Powder haben es dem Team von Black Diamond erlaubt, die Prototypen in ihrer Lieblingsumgebung einzusetzen – draußen auf einem Berg. Bei der Weltmeisterschaft im Eisklettern 2023 in Edmonton, Kanada, verwendete ein Teilnehmer ein Eisgerät mit einem Griff, der aus Nylon 12 Powder auf dem Fuse 1+ 30W gedruckt wurde. Dabei fiel das Eisgerät 24 Meter tief auf das darunterliegende Eis, überstand den Aufschlag jedoch ohne jegliche Brüche oder Schäden. „Wir hatten schon funktionale Komponenten in Skiern, wir haben interne Komponenten für einen Falltester gefertigt, die wiederholt einer erheblichen Belastung standhalten müssen. Wir können jetzt endlich hochfeste 3D-gedruckte Teile intern herstellen“, so Tetzl.
Der Fuse 1+ 30W hilft dem Unternehmen auch dabei, die Entwicklungskosten für Schuhe zu senken. Der firmeninterne Schuster verwendet für das Formen von Schuhen oder Stiefeln große Leisten, die in der Regel aus Nylon gedreht werden. Diese großformatigen Teile bezog das Team früher von einem Fertigungsdienstleister, doch durch den Druck der Leisten mit Nylon 12 Powder auf dem Fuse 1+ 30W konnte es seine Kosten von 2000 $ auf nur 65 $ senken und zudem die Durchlaufzeit verkürzen. „Der Fuse hat uns den Weg geebnet, um unsere Tätigkeiten mit Nylon für unsere neuen Schuhprojekte zu skalieren.“
Indem Black Diamond den Fuse 1+ 30W fast täglich bei 15 bis 20 % Packdichte in Betrieb hat, kann das Team seine Schuhentwicklung mittels SLS-3D-Druck effizient und kostengünstig skalieren und seine Kapazitäten für Funktionstests erhöhen.
Erhöhte Kapazität durch den Form 4
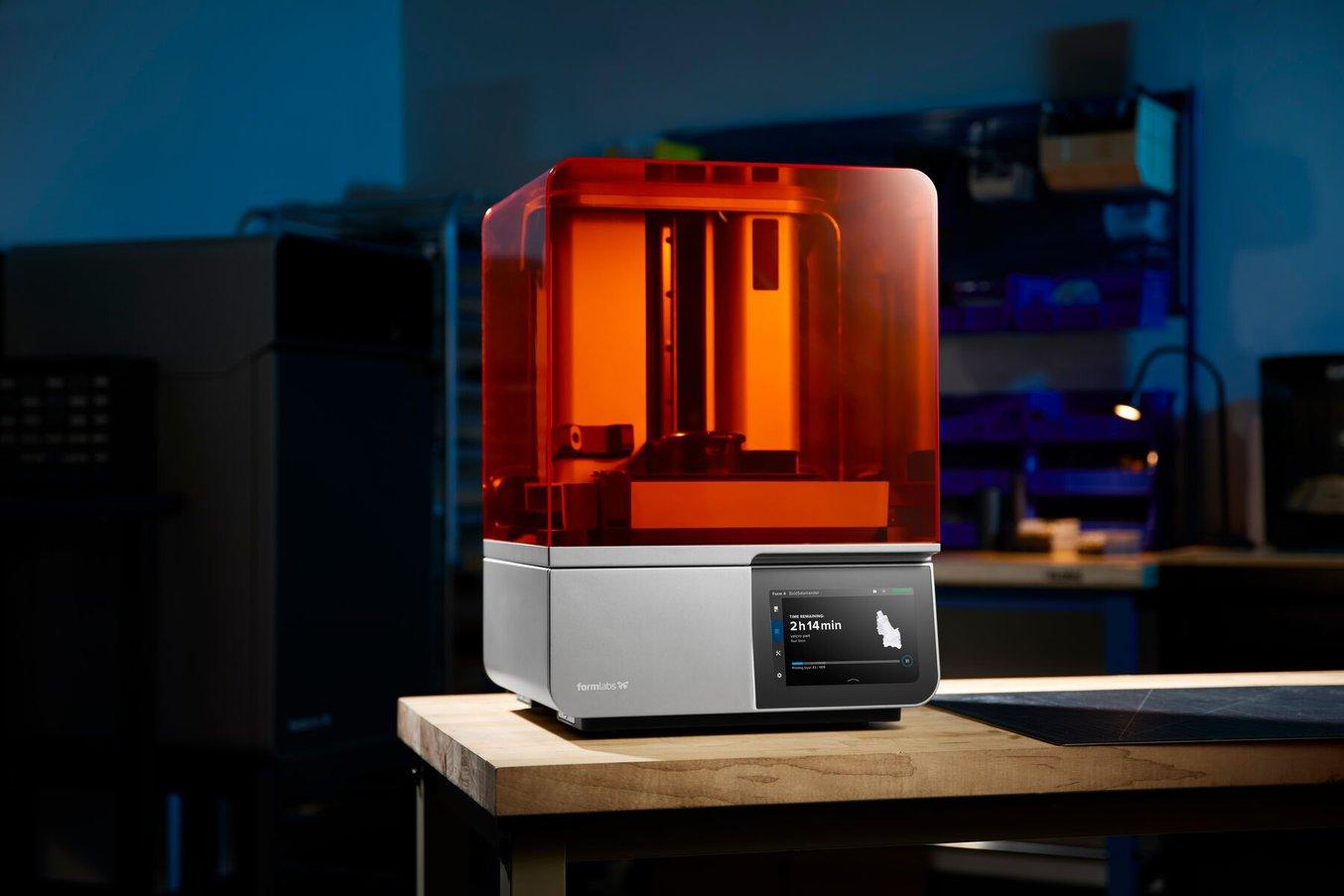
Seine Zuverlässigkeit und Schnelligkeit machen den Form 4 zu einer wertvollen Ergänzung in Black Diamonds 3D-Druckerflotte. Mehrere Iterationen am Tag drucken zu können erlaubt es dem Team, weniger Zeit mit dem Warten auf Druckteile und mehr Zeit mit der Kreation der nächsten großen Innovation im Bergsteigen zu verbringen.
Bei Hunderten von Produkten und einer Druckwarteschlange, die niemals zu schrumpfen scheint, ist Tetzl auf Zuverlässigkeit, Schnelligkeit und einheitliche Druckqualität angewiesen. Black Diamond hat wieder und wieder auf Formlabs-Drucker gesetzt: Sein Arbeitsprozess stützte sich zunächst auf den Form 2, dann den Form 3, den Form 3+, den Form 3L, den Fuse 1+ 30W und nun den Form 4. Für die Herstellung von Ausrüstung, der Klettersportler, Wanderer und Bergsteiger ihre Freizeitgestaltung und zum Teil sogar ihr Leben anvertrauen, braucht das Designteam von Black Diamond Hilfsmittel, auf die es sich ebenso zuversichtlich verlassen kann. Hinsichtlich dieser Zuverlässigkeit lässt das Team keinerlei Kompromisse zu, auch nicht der Schnelligkeit oder Materialvielfalt zuliebe. Wie Tetzl feststellte, bietet der Form 4 jedoch dasselbe System, mit dem er vertraut ist.
„Wir hatten keinen einzigen Fehldruck auf dem Form 4.“
Matt Tetzl, Manager des Produktentwicklungslabors, Black Diamond
Dank der Schnelligkeit des Form 4 verbringt das Team von Black Diamond so viel Zeit wie nur möglich mit seiner liebsten Beschäftigung, dem Testen seiner branchenführenden Produkte in der Wasatch-Gebirgskette – und umso weniger Zeit mit dem Warten auf Drucke.