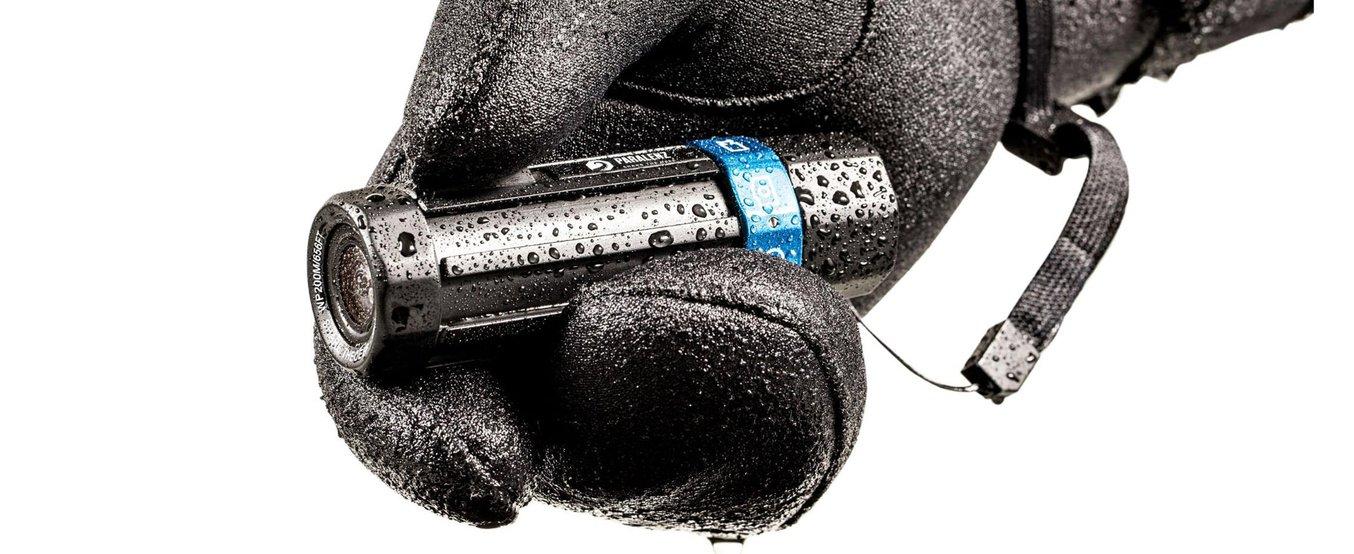
Michael Trøst und sein Team sind schon seit über 15 Jahren in der Produktentwicklung und -beratung tätig. Als ihr Kollege Martin, ein passionierter Taucher, zwischen den Allround-Action-Kameras und hochwertigen Unterwasserkameras eine Marktlücke witterte, sahen auch sie das Potenzial.
Es folgten Monate der Forschung, Entwicklung und mehrere Iterationen. Mithilfe des Stereolithografie (SLA) 3D-Druckers Form 2 stellte das Team erstaunliche Prototypen her, die dem Endprodukt in Optik, Handhabung und Leistung glichen. Mehr noch: Sie überstanden die Prüfung in Salzwasser von 150 m Tiefe.
Das Team nutzte diese Prototypen für die Erstellung seiner Marketingmaterialien und für das Crowdfunding. Auf diese Weise fand es eine treue Gruppe von Betatestern und 1.153 Investoren, die insgesamt $468.470 aufbrachten. Es blieb nur noch eine Herausforderung: die Herstellung der Kamera in Asien.
Kurz vor dem Versand der ersten Testgeräte sprachen wir mit Michael über den Werdegang der Tauchkamera von Paralenz vom Prototyp bis zur Produktion.
Ein kurzer Blick auf den Design- und Entwicklungsprozess bei Paralenz. Zu sehen sind Prototypen der Tauchkamera und Zubehörteile, die komplett mit dem 3D-Drucker Form 2 gedruckt wurden.
Wie kam es, dass Sie eine Tauchkamera für Unterwasseraufnahmen in über 200 Meter Meerestiefe entwickelt haben?
Seit unserer Unternehmensgründung im Jahr 2000 filmen wir Werbeaufnahmen, Special Effects für Filme und Stop-Motion-Aufnahmen. Mit der Zeit kamen 3D-Scanning, CNC und 3D-Drucken hinzu. Ich glaube, wir haben unseren ersten 3D-Drucker vor 15 Jahren erworben. Seitdem sind wir zunehmend in die Konstruktion vorgedrungen. Mittlerweile beschäftigen wir hauptsächlich Design-Ingenieure und Techniker in der Produktentwicklung.
Mein Kollege Martin wollte eine Tauchkamera entwickeln, weil er in diesem Bereich eine Marktlücke sah. GoPro und andere Allround-Action-Kameras sind eigentlich nicht für das Tauchen konzipiert. Auch in puncto Preis ist es ein großer Sprung zu hochwertigen Kameras mit Aluminiumgehäusen und Blitzlichtern – insgesamt viel größere und teurere Geräte. Er suchte eine einfachere, erschwinglichere Möglichkeit, seine eigenen Tauchgänge zu filmen.
Wie haben Sie so realistische Prototypen hinbekommen?
Sobald die Teile aus dem Drucker kommen, werden sie gereinigt, geschliffen und lackiert – das ist alles Übungssache. Das Objektiv wird gegossen, nachdem wir eine Matrize in 3D gedruckt haben. Dann wird eine Gussform aus Silikon hergestellt. Die Logos werden auf einem Tintenstrahldrucker gedruckt, in den größere Teile passen. Der Form 2 spart uns viele Arbeitsstunden, weil Druckteile schon fast fertig aus dem Gerät kommen. FDM-Modelle erfordern etwa dreimal soviel Zeit, um ein hochwertiges Finish zu erreichen. Wenn man viele Teile hat, erzielt man nicht das gleiche Finish bei allen Modellen, egal wie lange man daran arbeitet.

Nutzen Sie unsere Tutorials, um sich mit den Schritten der Nachbearbeitung, von der Grundierung, Lackierung und Montage von SLA 3D-gedruckten Teilen vertraut zu machen.
Wie haben Ihnen diese realistischen Prototypen beim Übergang zur Fertigung geholfen?
Vor unseren ersten Gesprächen mit den verschiedenen Unternehmen in China, die unsere Bauteile produzieren sollten, haben wir Drucke der Bauteile angefertigt, damit wir ihnen zeigen konnten, wie das Produkt aussehen und funktionieren soll. Wenn sie Teile herstellen sollten, die in andere Teile passen müssen, haben wir ebenfalls Drucke angefertigt, damit wir anschaulich machen konnten, „So muss Ihr Teil in das andere Teil passen“. So haben sie anstelle von einfachen 3D-Modellen das echte Bauteil bekommen.
Zuweilen kommt es in China wegen Kommunikationsproblemen zu unerwarteten Fehlern, besonders wenn es um präzise technische Details geht. Diese Fehler sind kostspielig. Selbst eine Kleinigkeit kann die Entwicklung um eine Woche verzögern, kritische Fehler haben gut und gern wochenlange Verspätungen zur Folge. Bei dieser Kamera haben wir 17 verschiedene Zulieferer, die maßgefertigte Teile herstellen, daher ist es entscheidend, dass wir uns einig sind. Wenn wir Leuten das tatsächliche Bauteil zeigen, verstehen sie das Produkt viel besser.

Es gab ein Gespräch, bei dem es sogar eine Weile gedauert hat, bis sie verstanden haben, was wir wollten, weil sie glaubten, die Kamera, die wir ihnen gegeben haben, sei das Endprodukt. Sie sagten, „Wir sollen das herstellen, aber Sie haben es doch schon. Warum brauchen Sie …“ Wir mussten ihnen erst erklären, dass es nicht echt, sondern ein Prototyp war.
Wir überlegen uns gerade, ob wir einen weiteren Form 2 kaufen und in China aufbauen sollen, damit wir bei den nächsten Produkten, die wir entwickeln, Zeit sparen können. Wir haben in China einen Kollegen, dem wir die Dateien einfach schicken können. So können wir die Teile in ein paar Stunden sowohl hier im Büro als auch in China drucken, damit unser Kollege sie direkt zu den Herstellern mitnehmen kann. Momentan dauert es 2-5 Tage, um Teile von unserem Büro nach China zu senden, je nachdem, wie viel man für die Fracht ausgibt. Dieser Prozess wird dadurch noch beschleunigt.
Wie hat Sie der 3D-Druck beim Entwicklungsprozess unterstützt?
Wir benutzen 3D-Druck für alles. Wir produzieren viele Prototypen, und das schon sehr früh. Zu Anfang haben wir mit vielen Tauchern gesprochen und die erfassten Informationen grafisch dargestellt. Dadurch erkannten wir, welche Merkmale ihnen am wichtigsten waren. So konnten wir eingrenzen, welche Eigenschaften unser Produkt unbedingt haben musste.
Wir haben zunächst 3-4 unterschiedliche Grundmodelle skizziert, bevor wir uns auf eines einigten. Anschließend haben wir eine Menge Größen getestet. Wir haben Modelle mit vier verschiedenen Größen gedruckt, um das Volumen, Gewicht und die Handhabung zu bewerten. Außerdem haben wir Taucher gebeten, das von ihnen bevorzugte Modell auszuwählen. Wir haben viele verschiedene Versionen des Knopfes hergestellt und mit Handschuhen ausprobiert, bevor wir das beste Design auswählten. Insgesamt haben wir sieben oder acht verschiedene Designs getestet, die allesamt gedruckt worden waren.
An diesem Punkt haben wir alle Einzelteile entworfen. Bei einem derart kompakten Produkt ist die Designfreiheit eingeschränkt. Daher haben wir lange gebraucht, um das Design zu optimieren und dabei sicherzustellen, dass es alle erforderlichen Eigenschaften hat. Im Lauf der Entwicklung des Kamerainneren hat sich viel geändert. Die Batterie ist letztendlich kleiner ausgefallen, weil wir den Sensor, das Objektiv und ein paar andere Teile geändert haben. Da gibt es jede Menge Hin und Her. Wir haben von jeder Veränderung der Kamera 3D-Drucke angefertigt. Insgesamt haben wir innerhalb weniger Monate mit dem Form 2 etwa 20-25 verschiedene Gehäuse gedruckt.

Zuletzt fertigten wir die endgültigen Prototypen an, die wir lackiert, getestet und auch im Video für die Finanzierungskampagne benutzt haben. Wenn wir für die Kampagne auf der Kickstarter-Plattform keine richtigen Produkte gehabt hätten, die wie echte Kameras aussehen, wäre es nahezu unmöglich gewesen, das Geld aufzubringen.
Die Arbeit mit dem Form 2 hat uns nicht nur schnelle Iterationen im Entwicklungsprozess ermöglicht, sondern auch eine Menge Geld gespart. Wir hatten früher ein hohes Budget für SLA-Modelle – allein für dieses Projekt hätten wir früher über $15.000 für SLA-Teile ausgegeben. Der Form 2 und sämtliche Materialien haben weniger als ein Drittel davon gekostet. Damit hat sich die ursprüngliche Investition schon mehrfach bezahlt gemacht..
Wie hat sich der Form 2 auf Ihre Produktivität ausgewirkt?
Vor dem Form 2 haben wir drei Geräte gestartet, um sicherzustellen, dass mindestens eines funktionierte. Es kam vor, dass wir einen Tag nach Beginn der Fertigung feststellten, dass ein Teil nicht fertig war, weil das Gerät ausgefallen war. Der Form 2 ist der erste Drucker, auf den wir uns zu verlassen wagen. Bis jetzt schlug nur einer von über 200 Druckaufträgen fehl. Wir drucken jeden Tag, oft mehrmals, und auf dem Drucker laufen dauernd irgendwelche Projekte, von 3D-Scandateien über kleine, präzise bis zu großen Teilen. Er läuft ununterbrochen. Ich würde sagen, das Beste für uns ist, dass wir uns darauf verlassen können – so einen 3D-Drucker haben wir zum ersten Mal. Unsere anderen Geräte erfordern viel Instandhaltung. Man muss sie reinigen und ab und zu auseinandernehmen. Der Form 2 ist anwenderfreundlich – ich würde sagen, der fast perfekte 3D-Drucker.
Ein weiteres Problem sind schlecht passende Teile, was bei anderen Druckern häufig vorkam. Wenn man etwas Rundes in CAD entwirft, wird es auch rund gedruckt. Wenn wir es in unterschiedliche Taschen aufteilen, passen sogar die Gewinde. Wir entwerfen fertigungsgerechte Bauteile, daher ist entscheidend, dass unser Prototyping-Tool den endgültigen Fertigungsprozess simulieren kann, ohne dass wir die Teile für den 3D-Druck modifizieren müssen. Unsere Teile werden bereits mit den richtigen Winkeln für den Fertigungsprozess gezeichnet, egal ob sie aus Aluminium stranggepresst, gefräst oder spritzgegossen werden sollen. Nachdem wir alle Teile auf Form und Passgenauigkeit geprüft hatten, waren wir überzeugt, dass wir in die Produktion gehen konnten.
Wir haben die Prototypen sogar für die Prüfungen im Drucktank und Tauchgänge im Meer benutzt. Wenn sich ein Prototyp in der Tiefe bewährt, kann man davon ausgehen, dass das Endprodukt auch keine Probleme haben wird. Die 3D-Druckteile funktionierten problemlos in 150 m Tiefe und mit dem Endprodukt aus Aluminium sind wir jetzt bei fast 400 m Tiefe.
Erleichtert der Zugang zu Desktop-3D-Druckern den Eintritt in die Hardware-Entwicklung?
Der Form 2 ist ein fantastisches Gerät, das uns viel Zeit spart. Vorher mussten wir viele Aufgaben per Hand oder mit der CNC-Fräse erledigen, was beides zusätzliche Fertigkeiten erforderte. Jetzt ist es einfacher, aber ein sehr guter Stift allein reicht nicht aus, man muss auch zeichnen können. Man muss die richtige Idee und handwerkliche Begabung haben, um Teile für das Gerät zu modellieren. Allerdings vereinfacht und beschleunigt das Gerät den Prozess, weil man nicht lernen muss, wie man eine CNC-Fräse oder andere Werkzeuge bedient.
Mehr noch: Sogar Jugendliche können es benutzen. Wir haben auch Projekte mit Schulen durchgeführt, um Schülern die Modellierung in 3D beizubringen. Einige haben uns mit ihren Fähigkeiten beeindruckt. Sie haben schon in einem halben Jahr Dinge hergestellt, die wir nicht für möglich hielten.
Was kommt als Nächstes, nachdem die Produktion angelaufen ist?
Wir sind fast fertig mit der Produktion der ersten Serie für unsere Beta-Tester. Wir planen, sie vor Jahresende zu versenden, arbeiten aber noch an einigen Zubehörteilen. Eines davon ist ein Third-Person-Viewer, dessen Prototyp wir ebenfalls auf dem Form 2 herstellen. Er funktioniert wie ein Selfie-Stick, aber mit Schwimmern (Auftriebskörpern), damit sich der Taucher von hinten selbst filmen kann.

Für den Beta-Test haben sich 250 Teilnehmer in 37 Ländern angemeldet. Wir versenden die Kameras zum Probelauf rund um die Welt, damit sie in vielen unterschiedlichen Umgebungen und Anwendungen geprüft werden können. Wir haben alle möglichen Taucher: Höhlentaucher aus Finnland und Mexiko, Freitaucher aus Belgien und Florida, technische Taucher aus Australien und Kanada, Speerfischer aus Hawaii und Afrika. Wir schicken sogar Kameras in die Antarktis und nach Alaska. Mit dem eingegangenen Feedback finden wir hoffentlich alle Fehler, die in einem Produkt der ersten Generation üblich sind, bevor wir das endgültige Produkt um den Februar herum lancieren.