MOSOLF Special Vehicles GmbH ist ein führender Hersteller von Spezialfahrzeugen mit Sitz in Kippenheim, Deutschland. Das knapp 50 Mitarbeiter zählende Unternehmen produziert rund 1000 Spezial- und Einsatzfahrzeuge pro Jahr. Zu seinen Kunden zählen Länder- und Bundespolizeien, der Verteidigungssektor, der Katastrophenschutz, das Technische Hilfswerk, Kommunen sowie Industriekunden, die Fahrzeuge mit hohem Individualisierungsgrad und überragender Leistung benötigen.
In der Automobilindustrie werden die meisten Bauteile mittels Massenproduktionsverfahren wie Spritzguss gefertigt, welche bei standardmäßigen Produktionsserien von Hunderttausenden von Einheiten kosteneffizient sind. MOSOLFs Kundschaft benötigt jedoch eine breite Palette an individuellen Teilen in geringen Stückzahlen, bei denen sich die Kosten für das Produktionswerkzeug herkömmlicher Fertigungsmethoden nicht rentieren. Die ideale Lösung ist für MOSOLF daher der 3D-Druck.
„Ich schätze, dass mittlerweile jeder dritte Polizeiwagen [in Deutschland] additiv gefertigte Teile enthält. Bei MOSOLF sind wir mit dem 3D-Druck inzwischen so weit, dass eigentlich kein Fahrzeug ohne additiv gefertigtes Teil mehr den Hof verlässt. Wir drucken mittlerweile rund 5000 Teile pro Jahr mit 3D-Druck, sind aber im Aufwärtstrend. Das heißt, in jedem Fahrzeug haben wird mindestens drei Teile, wenn nicht mehr.“
Carsten Busam, Leiter der Projektplanung, MOSOLF Special Vehicles GmbH
Lesen Sie weiter, um zu erfahren, wie MOSOLF den SLS-3D-Druck (selektives Lasersintern) mit der Fuse-Serie einsetzt, um eine breite Palette von Endverbrauchsteilen für Polizeifahrzeuge und andere Spezial- und Einsatzfahrzeuge herzustellen.
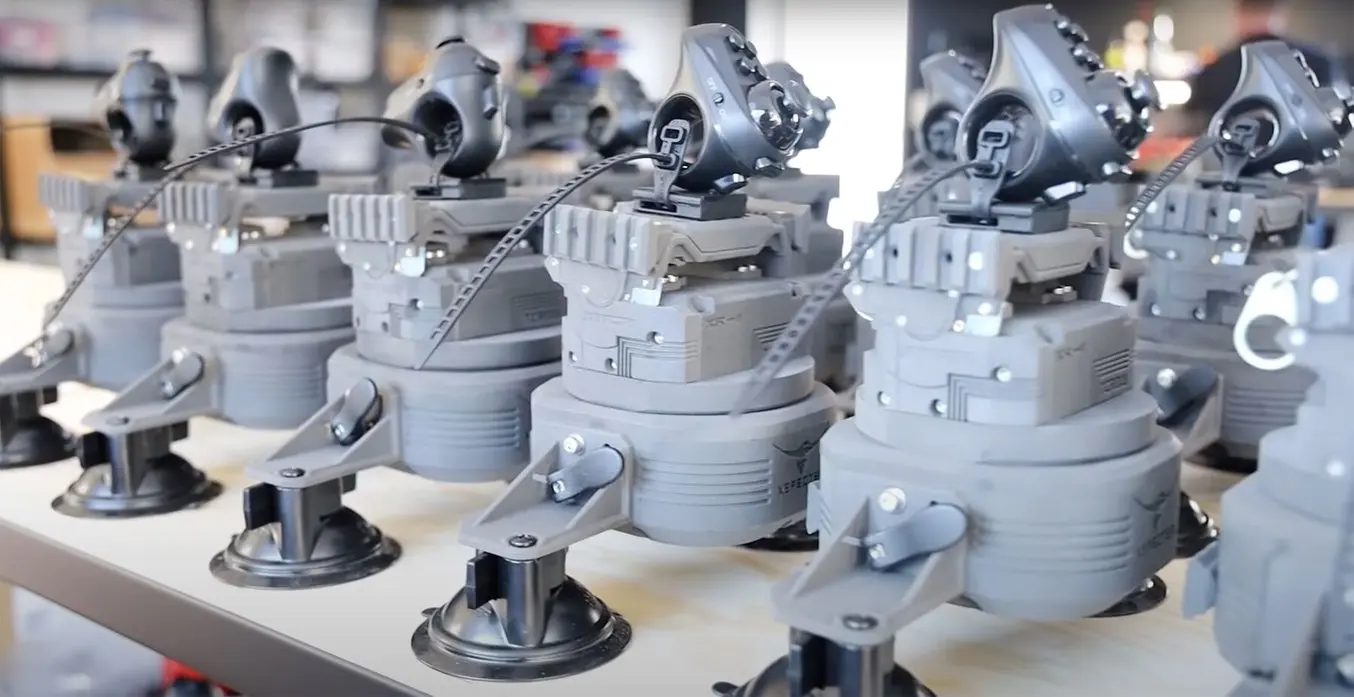
SLS-Produktion für die Endverwendung
3D-Druck für die Endverwendung ist nicht nur möglich, sondern dank des SLS-Ecosystems der Fuse-Serie auch noch erschwinglicher, agiler und leichter skalierbar denn je. Vergleichen Sie Produktionsverfahren, informieren Sie sich über unsere Mengenrabatte auf Pulver und entdecken Sie die Produktionsabläufe 15 verschiedener Hersteller, die derzeit die Fuse-Serie nutzen.
Individuelle Lösungen für die Anforderungen von 17 Polizeien in Deutschland
„Unsere größte Herausforderung ist die Vielfalt“, erklärt Busam. Jedes Bundesland und jede Polizeibehörde kauft mehrere verschiedene Fahrzeugtypen – und jedes einzelne Fahrzeug kann dann je nach seinem spezifischen Zweck eine individuelle Anpassung erfordern. Auch die zu installierenden Bauteile sind unterschiedlich – so verwenden verschiedene Polizeien Funk- oder Signalsysteme unterschiedlicher Hersteller. Das bedeutet, dass jedes Fahrzeug eine große Menge an Sonderanfertigungen erfordert.
„Wir fertigen Fahrzeuge für 17 Polizeien in Deutschland, und jeder hat seine eigenen Vorstellungen, wie eine Ergonomie aussehen soll und wie er die Bedienung haben möchte. Dementsprechend sind die Stückzahlen in der Basiskonstruktion vergleichsweise hoch, aber wenn man den Grad der Individualisierung hinzunimmt, sind sie doch wieder gering“, erläutert Busam.
Das Team von MOSOLF baut auf Serienfahrzeugen auf, was bedeutet, dass handelsübliche Autos, Lastwagen und Transporter nach Bedarf umgerüstet werden. Für jede gewünschte Funktion muss das Team einen geeigneten Verbauort finden und sicherstellen, dass das Bauteil ergonomisch, robust und ästhetisch ist. Bei älteren Modellen war die Suche nach einem Verbauort einfacher, denn diese hatten mehrere leere Plätze im Armaturenbrett oder der Konsole, die MOSOLF für individuelle Komponenten nutzen konnte. Neuere Modelle haben sich als Herausforderung erwiesen.
„Fahrzeuge sind zunehmend mit Anzeigen überladen. Es keine DIN-Schächte mehr in den Fahrzeugen. Zwar gibt es einige Aufbewahrungsfächer und ein Ladegerät für das Handy, aber Bauräume zu finden, in denen alle Bedienelemente untergebracht werden können, ist schwierig. Vor allem bei verdeckten Autos, bei denen man nicht erkennen soll, dass es sich um ein Polizeifahrzeug handelt“, berichtet Busam.
MOSOLF's Weg in die Welt des 3D-Drucks begann 2016, als die bayerische Polizei einen Auftrag zur Ausstattung ihres gesamten Arsenals an Fahrzeugen und Motorrädern mit neuen, digitalen Funkgeräten erteilte.
„Wir mussten für jedes Auto und jedes Motorrad eine individuelle Lösung finden. Hätten wir alle Teile aus Blech geformt, wäre das unglaublich zeitaufwändig gewesen oder die Lösungen wären nicht besonders schön gewesen, also haben wir den ersten Schritt in die 3D-Welt gemacht.“
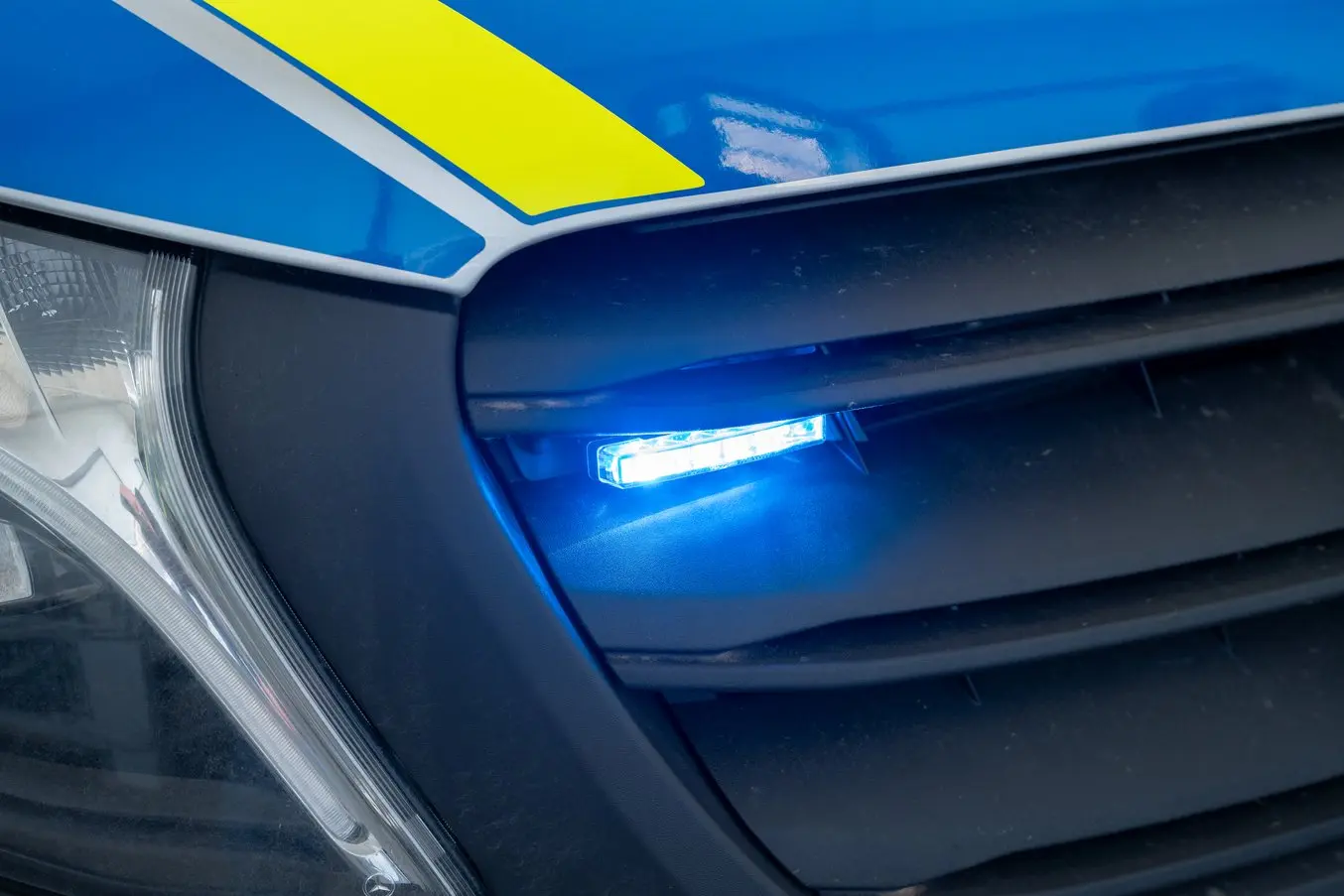
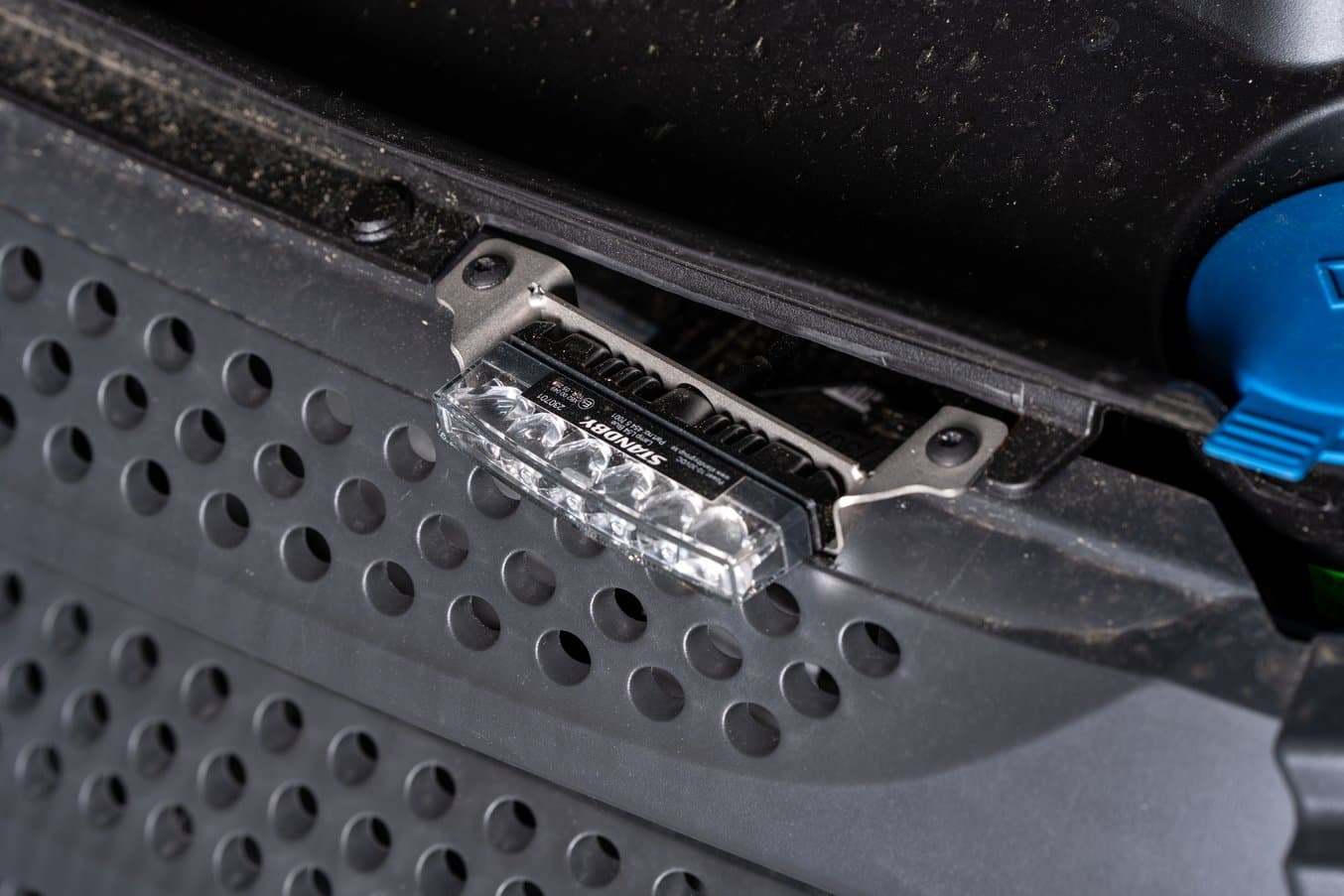
Individuelle Halterung für die LED-Frontblitzlichter von Polizeifahrzeugen. Traditionell stellte das Team diese Teile mittels Blechumformung her.
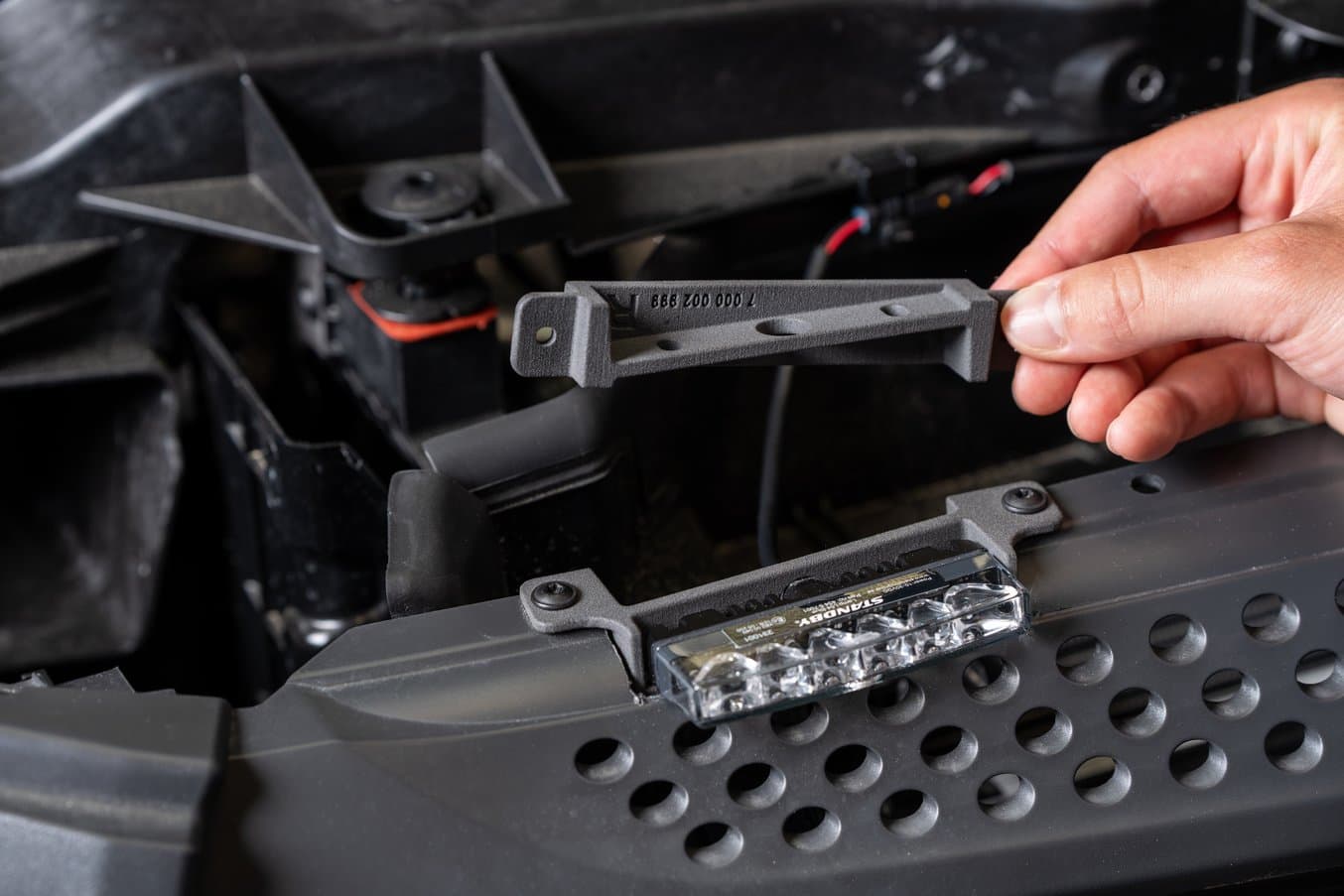
Der SLS-3D-Druck bietet jetzt eine wesentlich schnellere, einfachere und kostengünstigere Lösung.
Das Team nutzte für seine Produktion zunächst das 3D-Druckverfahren der Schmelzschichtung (FDM-3D-Druck), das zu diesem Zeitpunkt die erschwinglichste und unkomplizierteste Technologie war, die ihren Anforderungen entsprach. Schnell jedoch stießen sie an ihre Grenzen. Der FDM-Druck ließ sich schwer auf ausreichend hohe Stückzahlen skalieren, um die Aufträge abzuwickeln, und die Druckteile selbst waren nicht von industrieller Qualität.
SLS-3D-Druck wäre der logische nächste Schritt gewesen, aber mit Geräten, die bei rund 200 000 Euro beginnen, war er für kleine Unternehmen unerschwinglich – bis die Fuse-Serie von Formlabs auf den Markt kam.
„Der SLS-Druck ist ideal für MOSOLF, weil er eine hervorragende Qualität, eine hohe Genauigkeit und eine hohe Materialleistung bietet und viele Bauteile auf einmal hergestellt werden können. Es ist kosteneffizient, weil das ganze System sehr, sehr erschwinglich ist“, urteilt Gerhard Duda, Geschäftsführer und Gründer der 3D-WERK Black Forest GmbH, einem Formlabs-Partner, der von Anfang an mit dem Team von MOSOLF zusammengearbeitet hat, um die besten Lösungen für das Unternehmen zu finden.
„Das Fuse-Ecosystem war für uns das Passende, weil es für uns in Bezug auf die Bedienung und den Workflow am einfachsten zu handhaben ist“, fügt Busam hinzu.
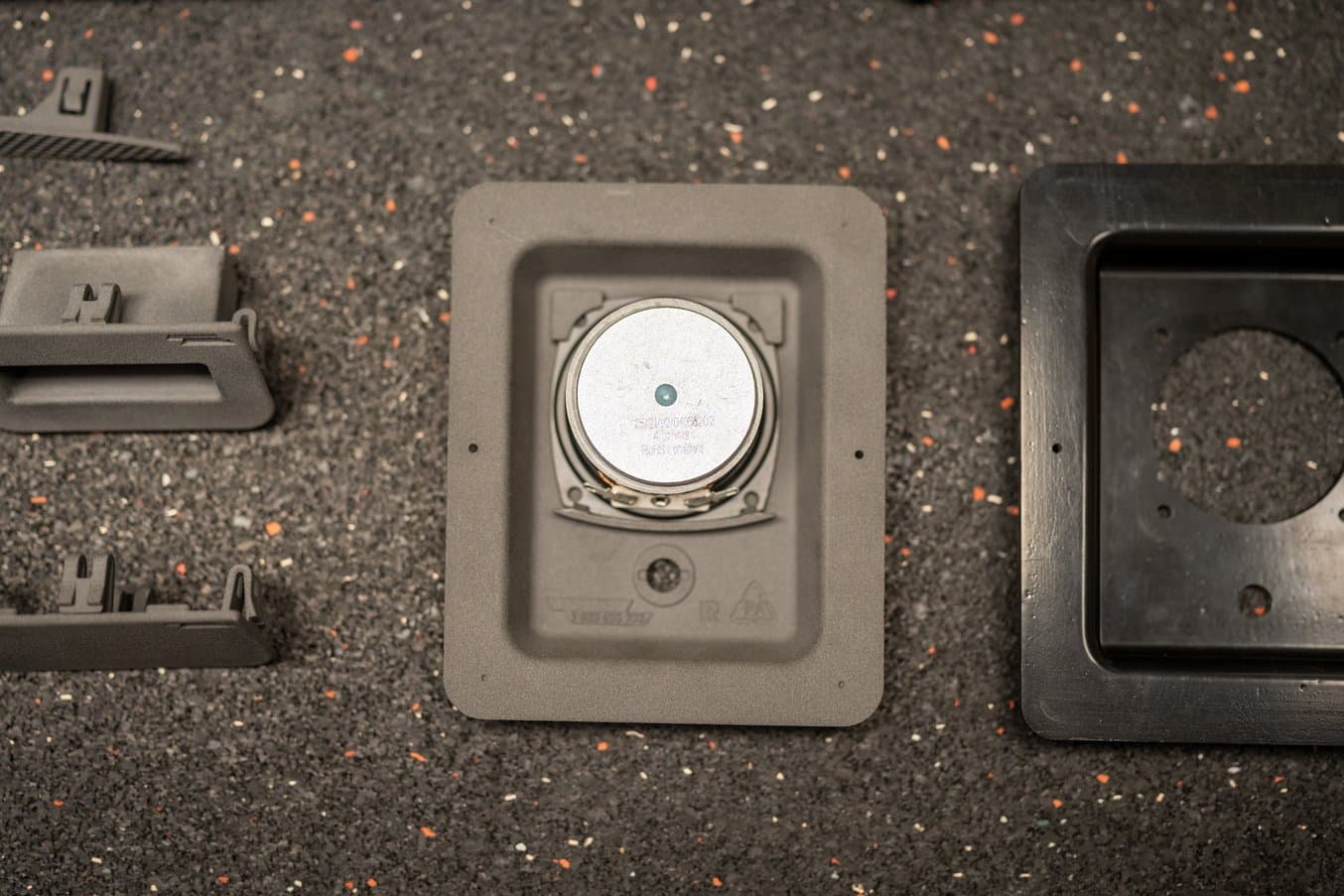
Das Design dieses Lautsprechergehäuses wurde so konzipiert, dass 70 % der Kosten vor Installation eingespart werden. Der Lautsprecherkörper wird einfach in die Einlage eingeklemmt, ohne dass eine Verklebung oder mechanische Befestigung erforderlich ist.
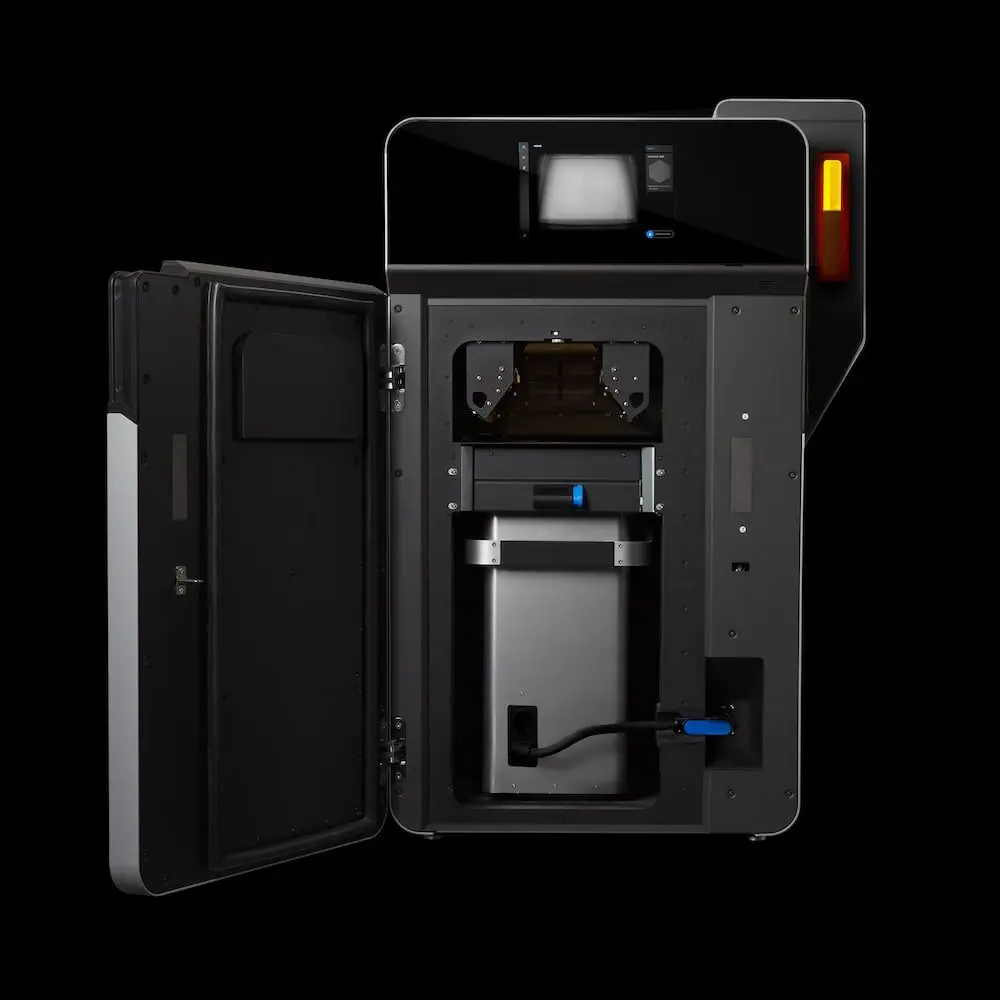
Rekordschnelle Produktion leistungsstarker SLS-Teile mit dem neuen Fuse 1+ 30W
Sehen Sie sich unsere Produktvorführung an und lassen Sie sich den Fuse 1+ 30W und den SLS-3D-Druck durch einen Formlabs-Experten erklären.
Kundenspezifische Endverbrauchsteile binnen 24 Stunden mit SLS-3D-Druck
Im Vergleich zu herkömmlichen Massenproduktionsverfahren wie Spritzguss, Thermoformen oder Blechumformung liegt der größte Vorteil der additiven Fertigung darin, dass sie kundenspezifische oder in kleinen Stückzahlen hergestellte Endverbrauchsteile ohne teures Produktionswerkzeug liefern kann.
„Wir verwenden die SLS-Technologie und insbesondere den Fuse 1+ 30W für verschiedene Bauteile, von den kleinsten, einfachsten Designs bis hin zur komplizierten Konsole, die in das Auto eingebaut wird. Wir haben diese Technologie intensiv verfolgt und der Fuse erfüllt etwa 80 % unserer Anforderungen“, so Tiberiu Morariu, Leiter der Prototypenentwicklung, des Designs und der technischen Konzeption bei MOSOLF.
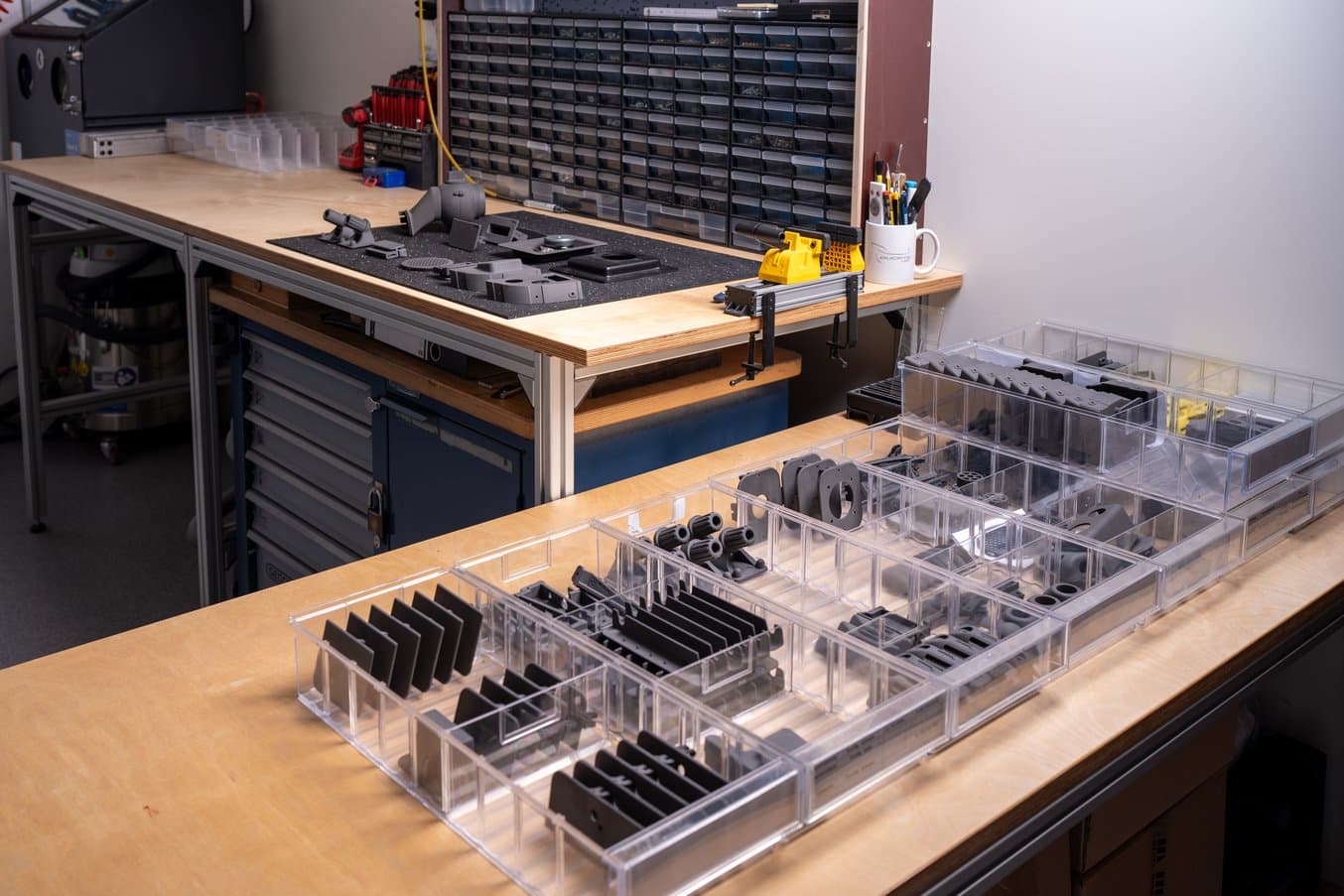
Das Team von MOSOLF druckt mit SLS-3D-Druck Dutzende von kundenspezifischen Designs, von kleinsten Abdeckungen und Gehäusen bis hin zu großen, mehrteiligen Baugruppen und Bauteilen für die Armatur.
„Die Anforderungen sind von Bundesland zu Bundesland und von Polizeidienststelle zu Polizeidienststelle unterschiedlich. Mit 3D-Druck ist das einfach leichter umzusetzen. Man kann von Fahrzeug zu Fahrzeug schnell umkonstruieren. Wenn es sich um das gleiche Auto handelt, bleibt die Kontur gleich, aber die Systeme, die anschließend in das Fahrzeug eingebaut werden, die sind sehr unterschiedlich“, erklärt Morariu.
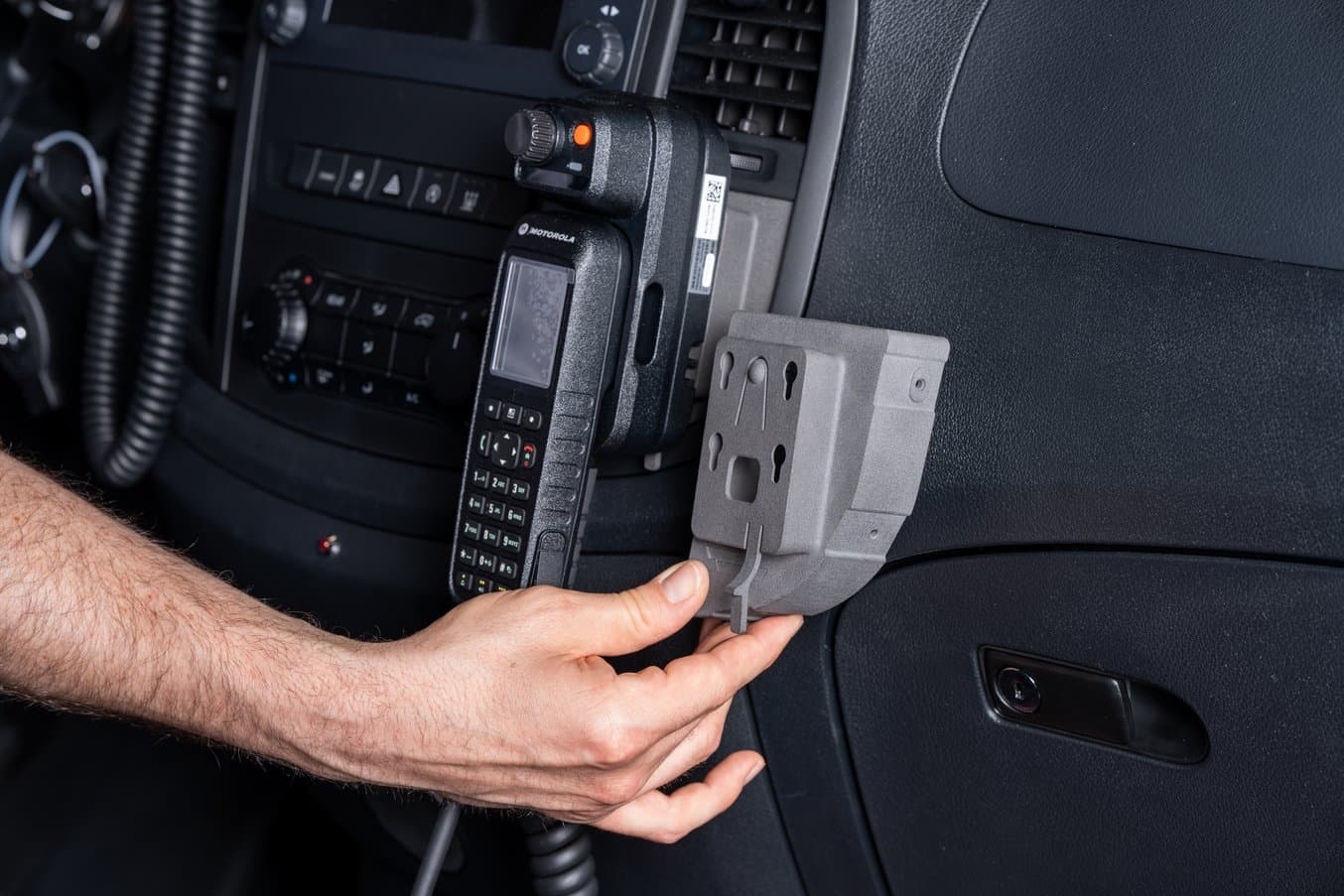
Die Halterung des Funkgeräts ist ein gutes Beispiel für die Anpassung. Die Befestigung an der Konsole funktioniert bei jedem Mercedes-Transporter gleich, aber die gesamte Baugruppe kann leicht mit verschiedenen Halterungen für Funkgeräte verschiedener Hersteller modifiziert werden.
Die unkomplizierte Individualisierung beschleunigt sowohl die Prototypenentwicklung als auch die Produktion erheblich, zumal sowohl Prototypen als auch endgültige Teile für auf demselben Gerät hergestellt werden können.
„Für mich als Designer gibt es nichts Schöneres, als heute eine Idee im Kopf zu haben, sie zu zeichnen und sie dann am nächsten Tag in den Händen zu halten und zu betrachten“, so Morariu.
„Der größte Effekt des 3D-Drucks auf die betriebsinterne Fertigung ist, dass wir in vielen Bereichen deutlich schneller geworden sind. Mit den herkömmlichen Verfahren haben wir Lieferzeiten von vier bis sechs Wochen, vor allem wenn die Teile beschichtet werden müssen. Mit 3D-Druck können wir Teile praktisch über Nacht beschaffen. Hätten wir keinen Zugang zum 3D-Druck, wären unsere Arbeitsabläufe deutlich langwieriger und komplizierter, weil wir jedes Teil wahrscheinlich mehrmals fertigen und anpassen müssten.“
Carsten Busam, Leiter der Projektplanung, MOSOLF Special Vehicles GmbH
SLS-3D-Druck | Blechumformung | Thermoformen | Spritzguss | |
---|---|---|---|---|
Zeit vom Design über den Prototyp zum Serienteil | 1–2 Wochen | 6–8 Wochen | 6–8 Wochen | 6–8 Wochen |
Durchlaufzeit für Endverbrauchsteile | 1–2 Tage | 6–8 Wochen | 6–8 Wochen | 6–8 Wochen |
Andere Faktoren | Kein Produktionswerkzeug erforderlich Einfache Individualisierung Designfreiheit Überlegene Ästhetik | Produktionswerkzeug erforderlich Eingeschränkte Designfreiheit Schwierigere Individualisierung Schlechtere Ästhetik | Produktionswerkzeug erforderlich Eingeschränkte Designfreiheit Schwierigere Individualisierung | Teures Produktionswerkzeug erforderlich Keine Indivdualisierungsoptionen Weniger Designfreiheit |
„Heutzutage werden die Autos immer ästhetischer und die Innenräume immer flüssiger. Stauräume werden immer dynamischer und komplizierter. Der 3D-Druck ist sehr wichtig für das Design und die Ergonomie des Autos, denn das kann man mit anderen Technologien wie Thermoformen oder Blechumformung nicht immer umsetzen. Auch die Anbindung am Fahrzeug selber können wir bei diesen komplizierten Formen am besten mit 3D-Druck lösen. Mit 3D-Druck kann ich freier entwerfen, ich kann meine Kreativität in Design und Form voll entfalten.“
Tiberiu Morariu, Prototyping, Design und technische Konzeption, MOSOLF Special Vehicles GmbH
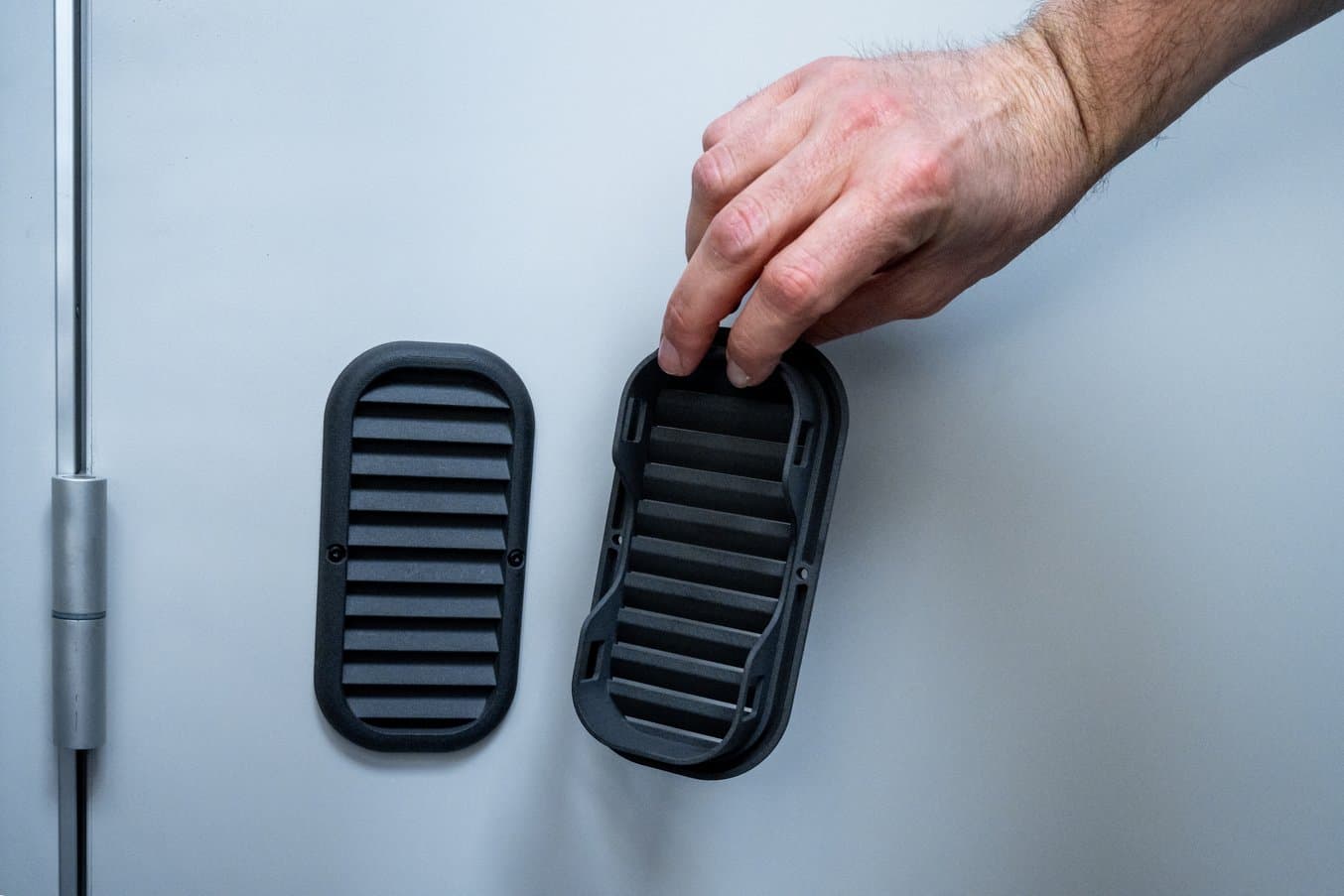
Bei dieser Belüftungsöffnung handelt es sich um ein Einwegventil, das in einem Spezialfahrzeug für Brandstiftungsermittlungen das schwarze vom weißen Fach trennt. Die Baugruppe hat ein relativ komplexes Design und besteht aus drei miteinander verschraubten Bauteilen. Ursprünglich versuchte das Team, sie mittels FDM-3D-Druck zu produzieren. Aufgrund der runden Form und der dünnen Wände stieß es jedoch auf Schwierigkeiten und wechselte zum SLS-Druck, da dieser mehr Designfreiheit bietet.
Einer der Hauptvorteile des SLS-3D-Drucks besteht darin, dass Konstruktionsteams mit den mechanischen Eigenschaften der verfügbaren Materialien bereits vertraut sind, z. B. Nylon, das in der Automobilindustrie häufig für die Herstellung von Teilen für den Innen- und Außenbereich zum Einsatz kommt. Das Team von MOSOLF hat ein gutes Verständnis von der Leistung von SLS-3D-gedruckten Teilen aus Nylon, sodass es beim Design die Funktionalität im Fokus behalten und sogar einige Originalbauteile aus Metall ersetzen kann.
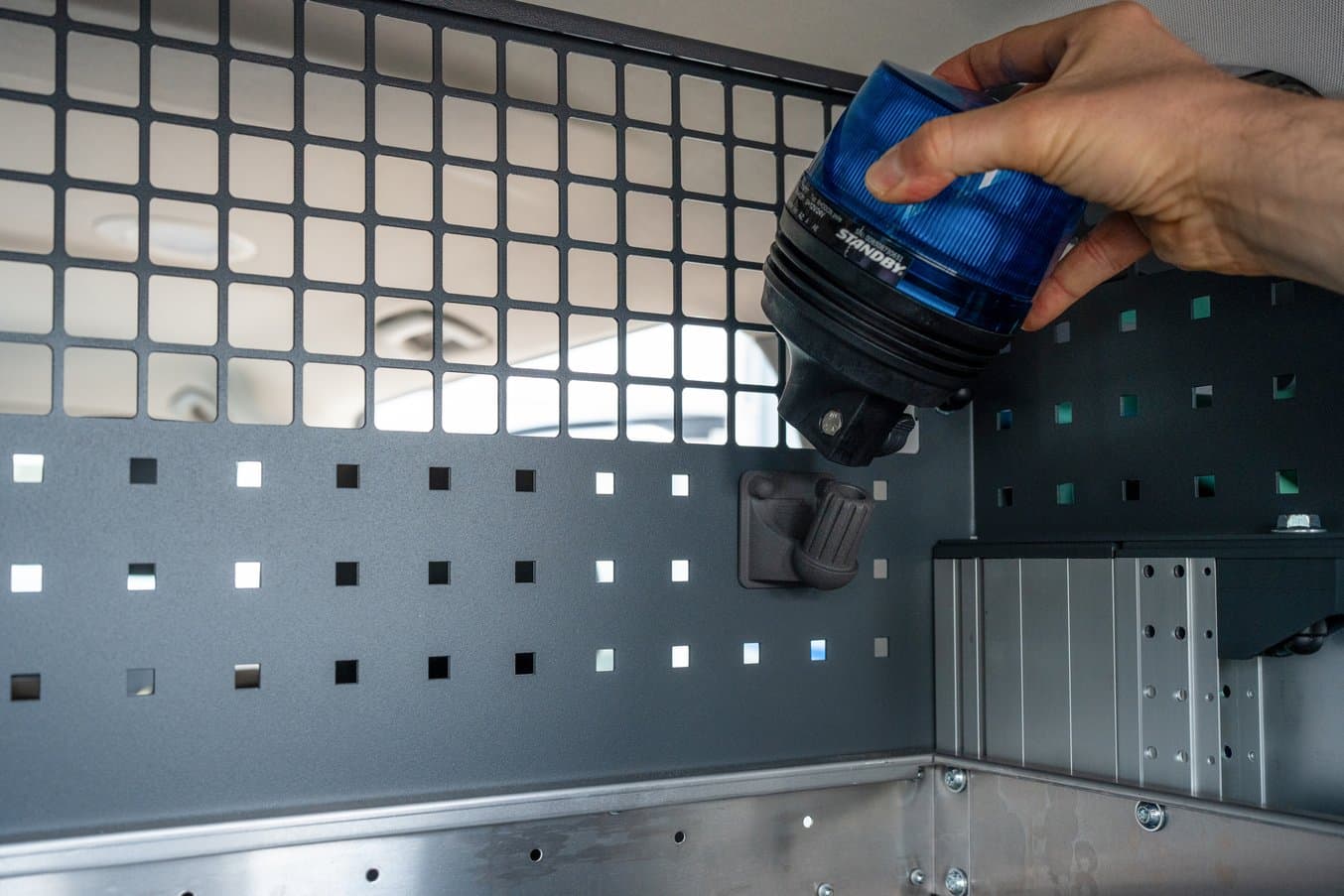
Klipp-Halterung im Laderaum für eine abnehmbare Notleuchte.
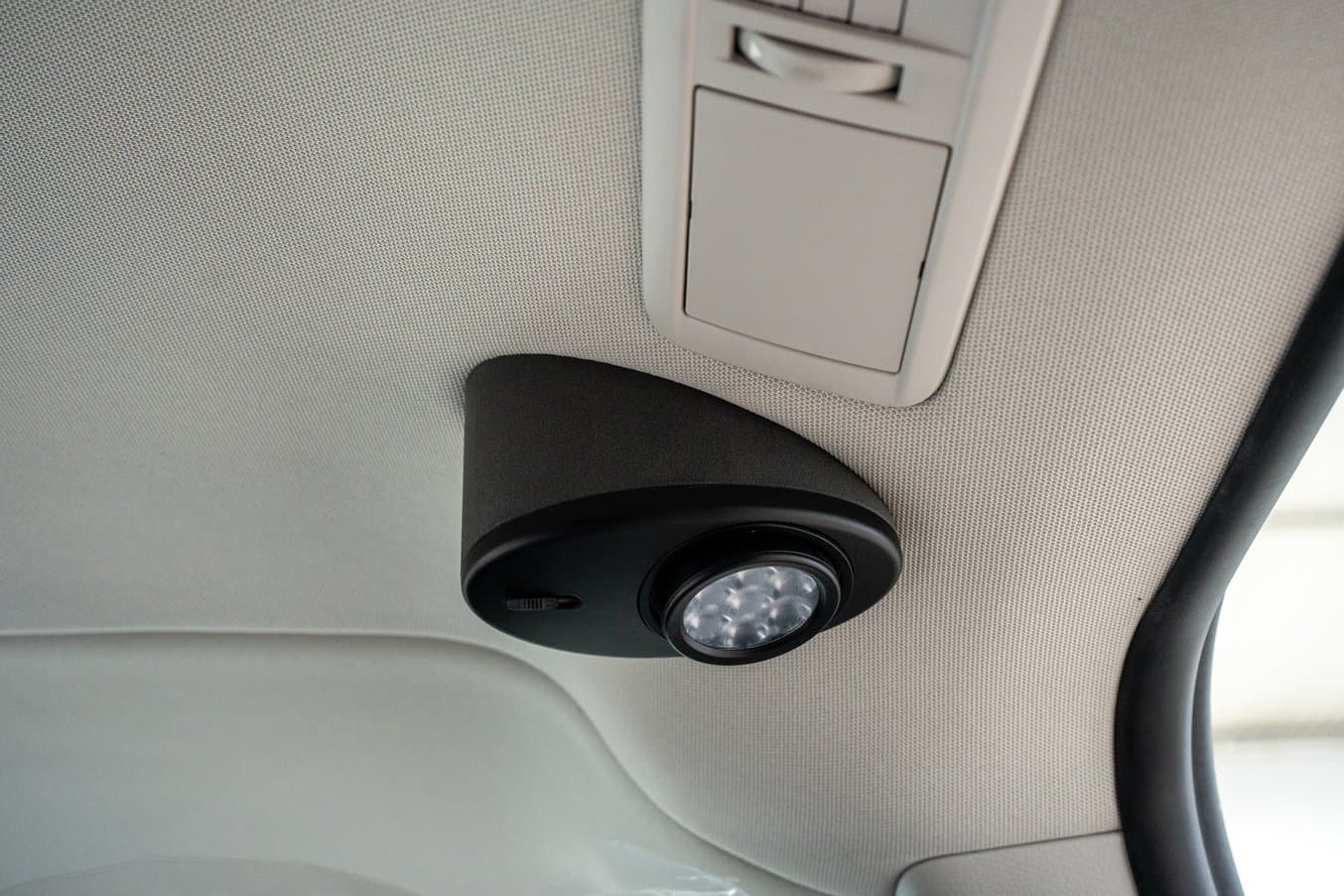
Gehäuse und Halterung für eine Deckenleuchte.
„Mit dem Fuse-Ecosystem haben Sie natürlich das perfekte Material. Es ist einsatzbereit. Das gibt es schon sehr, sehr lange. Und es ist gründlich getestet worden“, fasst Duda zusammen.
Neben der Haltbarkeit ist die Hitzebeständigkeit eines der wichtigsten Kriterien für Anwendungen in der Automobilindustrie. Das FDM-Material PLA kommt hierfür nicht infrage, da seine Wärmeformbeständigkeitstemperatur (HDT) nur etwa 50 ºC bei 0,45 MPa beträgt. ABS hat eine HDT von 90 ºC bei 0,45 MPa, was zwar besser ist, aber immer noch an oder unter der Grenze für viele Anwendungen liegt. Mit einer HDT von 171 °C bei 0,45 MPa bietet Formlabs' Nylon 12 Powder eine wesentlich höhere Hitzebeständigkeit, sodass keine Gefahr besteht, dass Funktionsteile wie z. B. eine Funkgerätehalterung versagen, wenn sich das Fahrzeug im Sommer auf dem Parkplatz aufheizt.
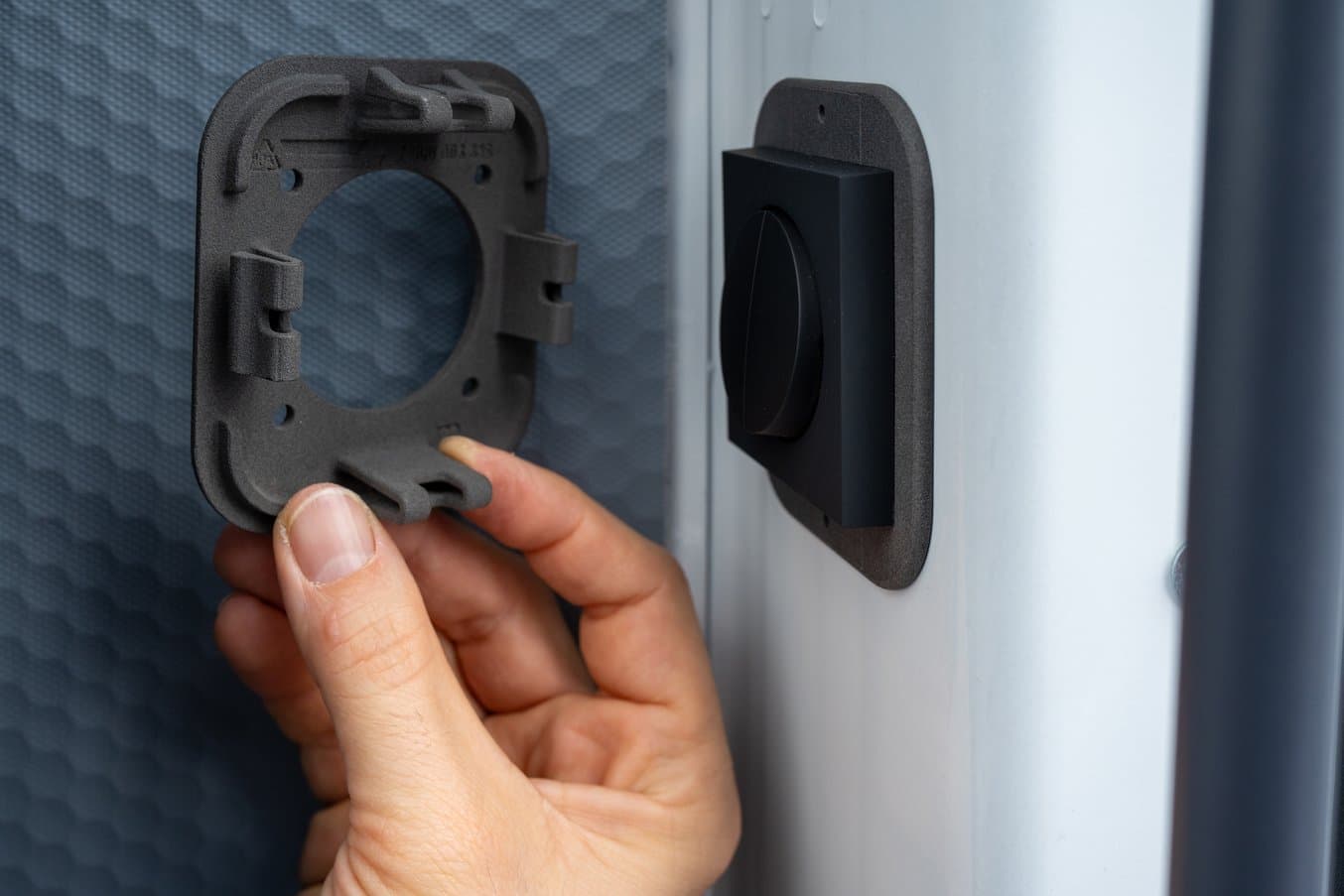
Gehäuse einer Steckdose.
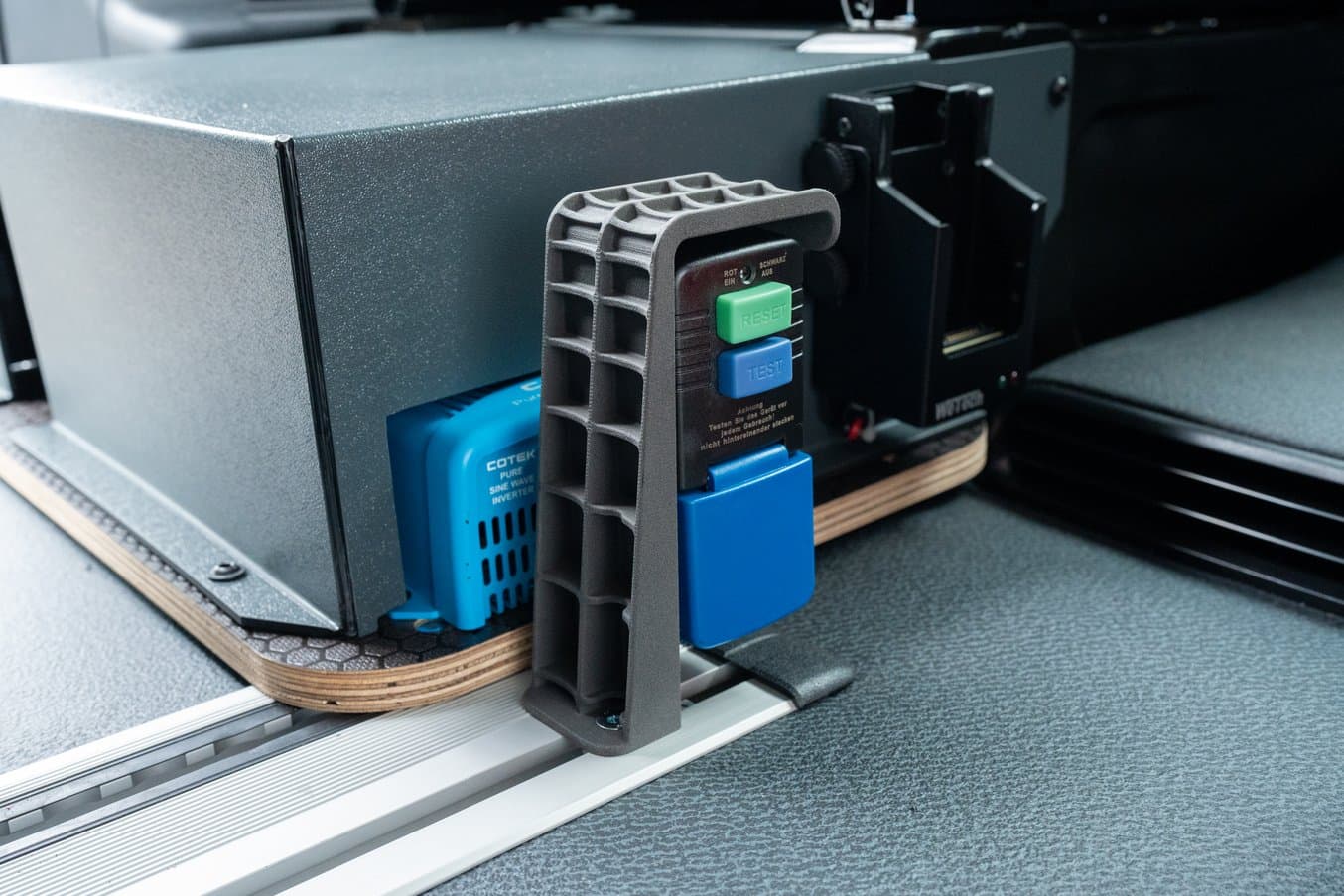
Schutzabdeckung zur Vermeidung versehentlicher Schäden bei Bewegungen im Auto.
In manchen Fällen werden Fahrzeuge an Polizei- oder Notfallkräfte verleast und nach ihrer Nutzungsdauer an Zivilisten oder andere Staatsorgane verkauft. Um dies zu ermöglichen, muss das MOSOLF-Team bei der Nachrüstung Schäden oder dauerhafte Veränderungen an den Fahrzeugen vermeiden, sodass sie am Ende ihrer Nutzungsdauer leichter in ihren ursprünglichen Zustand zurückversetzt werden können. Die additive Fertigung macht auch dies einfacher: Anstatt bestehende Bauteile permanent zu verändern, ersetzt das Team sie gegen 3D-gedruckte Teile, die später ausgetauscht werden können.
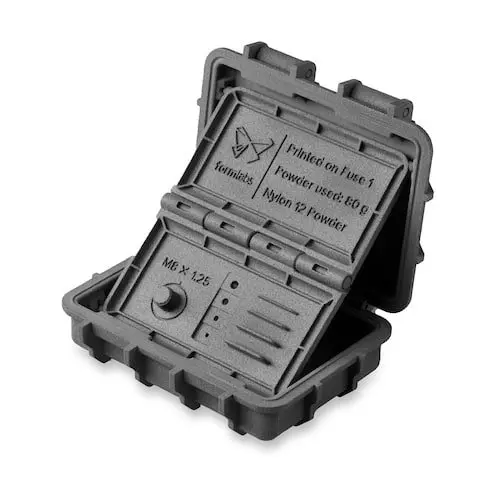
Kostenlosen SLS-Probedruck anfordern
Sehen und fühlen Sie die Qualität von Formlabs aus erster Hand. Wir senden Ihnen einen kostenlosen Probedruck aus dem Fuse 1+ 30W an Ihren Arbeitsplatz.
Polizeifahrzeuge der Zukunft setzen noch stärker auf 3D-Druck
Aufbauend auf ihrem Erfolg mit dem SLS-3D-Druck prüfen die Teams von MOSOLF und 3D-WERK nun, wie sie weitere Materialien und zusätzliche Drucker einsetzen können, um eine noch größere Bandbreite an Bauteilen in Spezialfahrzeugen zu ersetzen.
„Es passiert mir auch jetzt noch, nach den vielen Jahren, wo wir den additiven Bereich betreiben, dass ich staunend vor Produkten stehe, die wir selbst konstruiert haben, die wir selbst gedruckt haben, mit all den Funktionalitäten und Möglichkeiten, die der 3D-Druck bietet“, so Michael Ringwald, Geschäftsführer bei MOSOLF.