Die Herstellung hochpräziser Prototypen für funktionsstarke mechanische Uhren mit 3D-Druck
Uhren und deren Uhrwerke sind präzise Messgeräte, die gut aussehen und den Geschmack der Kunden treffen sollen. Diese beiden Vorgaben zu vereinen ist nicht immer einfach.
Petra Möller, Leiterin Produktmanagement bei Sinn Spezialuhren GmbH, und ihr Team stehen regelmäßig vor der Herausforderung, die Produktideen auch in der Realität stimmig umzusetzen. Um dies zu erreichen, kommt seit kurzem der Form 3 zum 3D-Druck von Prototypen der Uhren zum Einsatz.
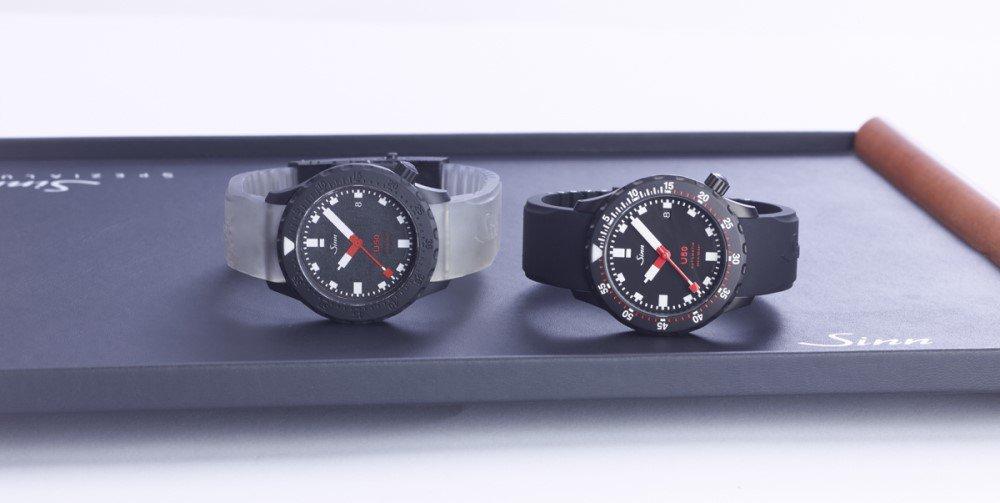
3D-gedruckte Prototypenteile im Vergleich zum finalen Produkt, die mit dem Form 3 hergestellt wurden.
Seit fast 60 Jahren steht Sinn Spezialuhren für funktionsstarke, mechanische Uhren. Das Produktportfolio reicht von Fliegeruhren über Taucheruhren und Chronographen bis zu Einsatzzeitmessern, die von Piloten, Tauchern und der Eliteeinheit GSG 9 getragen werden. Daher richtet sich die Formgebung im Entwicklungsprozess nach der gewünschten Funktionalität, was das Team oft vor Herausforderungen stellt.
Verbesserte Produktentwicklung mit Hilfe von 3D-gedruckten Prototypen
Nils Hunder arbeitet im Team von Petra Möller an der Entwicklung und Konstruktion von Gehäusen, Uhrwerken und Armbändern der Uhren. Die Aufgabe des Team ist es, mit allen Abteilungen, die in den Prozess involviert sind, Produkte bis hin zur Serienreife zu entwickeln.
Bei den Teilen der Uhren handelt sich es oft um kleine, filigrane Details, die das Aussehen und die Funktionalität der Uhr maßgeblich beeinflussen. Außerdem stellen sich im Prozess grundlegende Fragen, ob die Proportionen der Uhr passen, wie die Gehäuseform am Arm wirkt oder wie das Band am besten am Gehäuse befestigt werden kann. Oft vermitteln die Produktzeichnungen am PC oder auf dem Papier nicht optimal die Realität des Endprodukts am Arm. Daher ist es für eine erfolgreiche Produktentwicklung überaus sinnvoll, Prototypen zu erstellen, bevor die Uhr in die Serienproduktion geht.
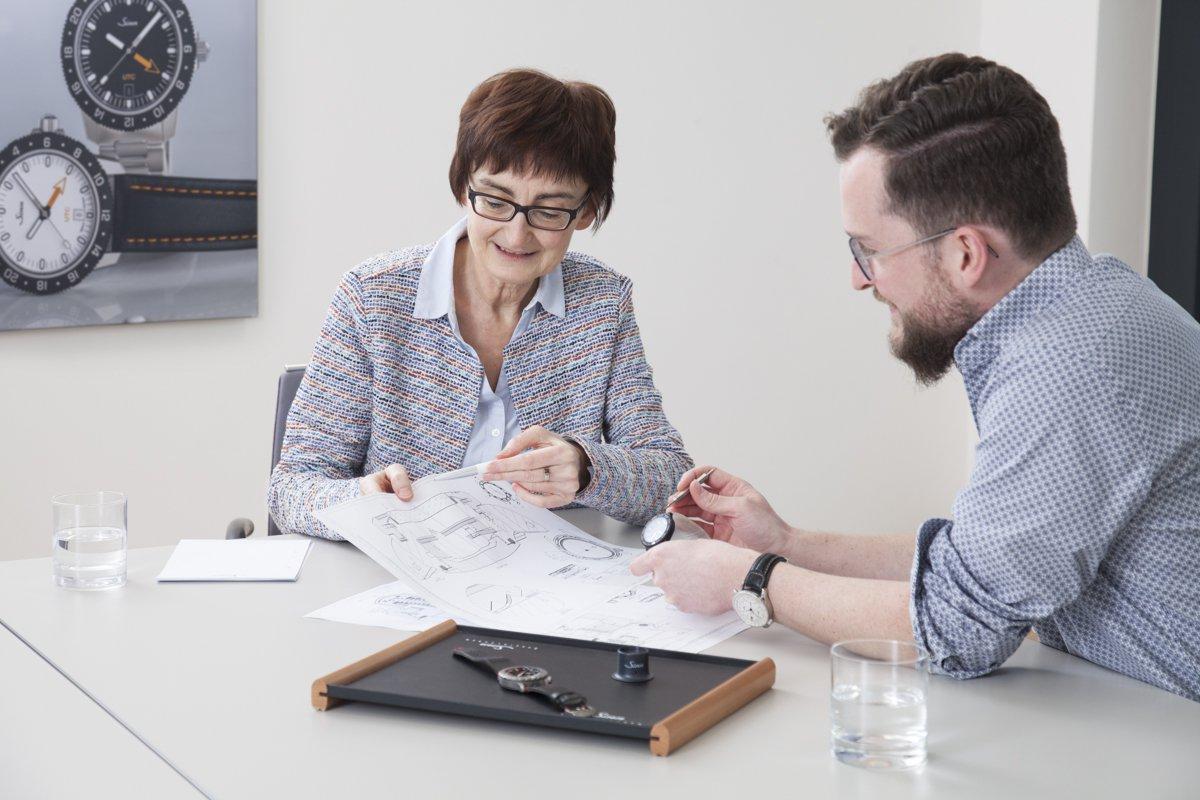
Petra Möller und Nils Hunder mit den technischen Zeichnungen und dem 3D-gedruckten Modell der Uhr.
“Der frühe Einsatz von Prototypen spart Investitionen und Fehlentwicklungen.”
Petra Möller, Leiterin Produktmanagement
Bisher kam bei Sinn für die Prototypenherstellung ein externer Dienstleister zum Einsatz. Zuerst wurden die Uhrenmodelle mittels Stereolithographie, aus einem ausgehärteten Kunstharz gefertigt, das sehr bruchgefährdet und empfindlich ist. Somit nicht das richtige Material, wenn es um Modelle geht, die für das richtige Look and Feel auch am Arm getragen werden sollen. Später stellte man dann auf den 3D-Druck mit FDM-Druckern um. Der Vorteil darin lag, dass der Wachsdruck genauere Teile drucken konnte, danach aber noch in Aluminium gegossen werden musste, was sehr zeitintensiv und kostenaufwendig ist. “Prototypen kamen früher erst viel später im Entwicklungsprozess zum Einsatz. Da war eigentlich schon alles fertig, und bevor wir auf den Startknopf an der CNC-Maschine gedrückt haben, haben wir uns die Uhr nochmal angeschaut”, so Nils Hunder.
Da im Team der Wunsch bestand, den 3D-Druck ins Haus zu holen, beobachtete Nils Hunder schon länger das Geschehen um Formlabs. Die Oberflächenqualität der SLA-Drucker begeisterte ihn, auch wenn ihn der Form 1 und Form 2 nicht komplett von ihrem Mehrwert überzeugen konnten. Da bei der SLA-Technologie häufig Stützstrukturen verwendet werden müssen, war das Team sich lange unsicher, ob ein FDM-Drucker mit auswaschbaren Stützstrukturen, aber gröberer Oberfläche die bessere Wahl wäre. Erst die Oberflächenqualität und die leicht entfernbaren Stützstrukturen des Form 3 überzeugten Petra Möller und Nils Hunder das Komplettpaket aus Form 3 mit Form Wash und Form Cure anzuschaffen. Seitdem wird der LFS-Drucker regelmäßig zur Prototypenentwicklung eingesetzt.
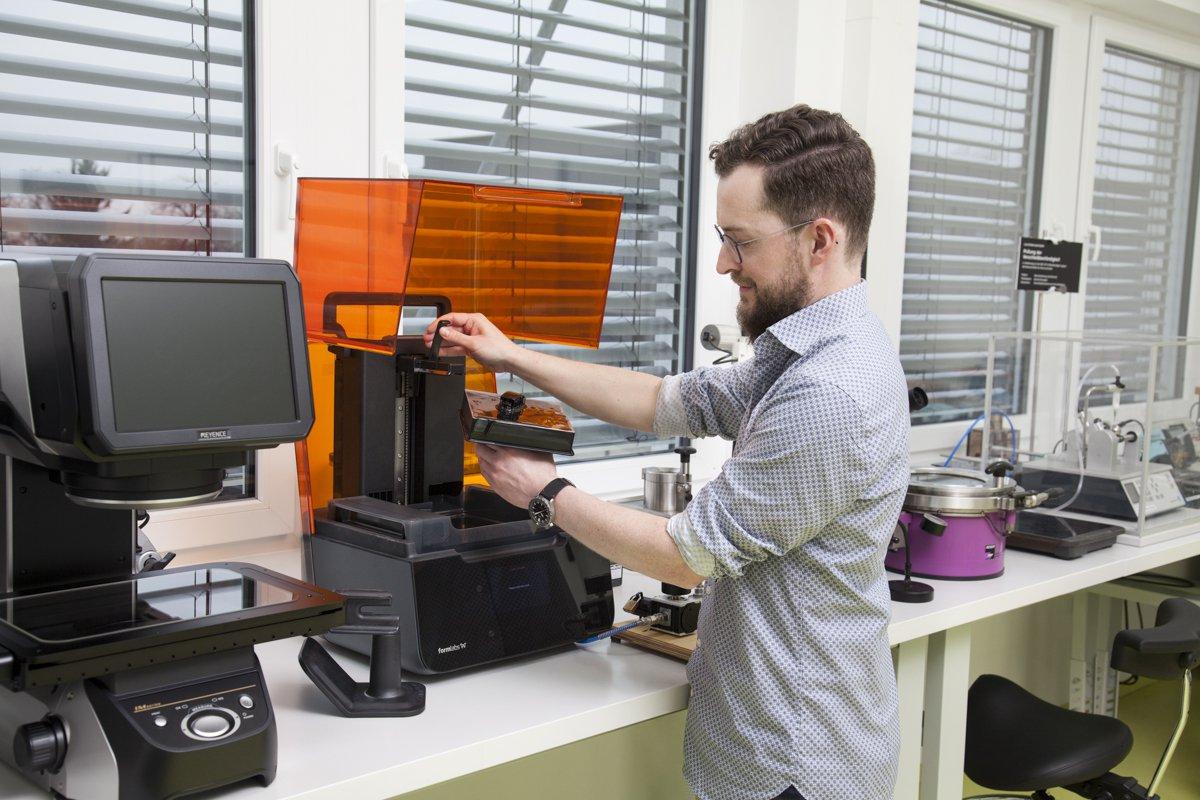
Nils Hunder bei der Bedienung des Form 3
Hochpräzise, 3D-gedruckte Prototypen über Nacht
Dank des hochpräzisen Lasers des Form 3 können filigrane Details wie Gravuren oder Riffel an der Krone des Uhrengehäuses mitgedruckt werden. Für die Uhrengehäuse wird meistens in Black Resin gedruckt. Mit einer möglichen Schichtstärke von 25 Micron kommen die Details am besten hervor, es wird so gut wie keine Nachbearbeitung benötigt und die Gehäuse können später durch z.B. Airbrush weiterverarbeitet werden.
“Wir setzen den Form 3 hauptsächlich im Konstruktionsprozess ein, um schon erste Entwürfe möglichst zeitnah anzuschauen, wie die Uhr von den Proportionen her wirkt und wie sie sich am Handgelenk trägt.”
Nils Hunder, Verantwortlicher für Konstruktion und Produktentwicklung sowie Prototypenentwicklung
Auch der Form Wash und das korrekte Waschen der Druckteile in TPM mit anschließender Spülung in IPA stellte sich als essentiell wichtig heraus. Oft werden feine Kanäle zur Befestigung der Armbänder gedruckt, die sich beim Nachhärten mit flüssigem Material verschließen, wenn die Modelle nicht gründlich gewaschen wurden.
Abgesehen von dieser Erkenntnis war die Implementierung des 3D-Drucks bei Sinn Spezialuhren ein Kinderspiel. Der 3D-Druck wird jetzt bereits in einem frühen Stadium der Prototypen- und Modellentwicklung eingesetzt. Dabei werden Modelle oft über Nacht gedruckt und benötigen nur wenig Nachbearbeitung, sodass Anpassungen frühzeitig stattfinden können.
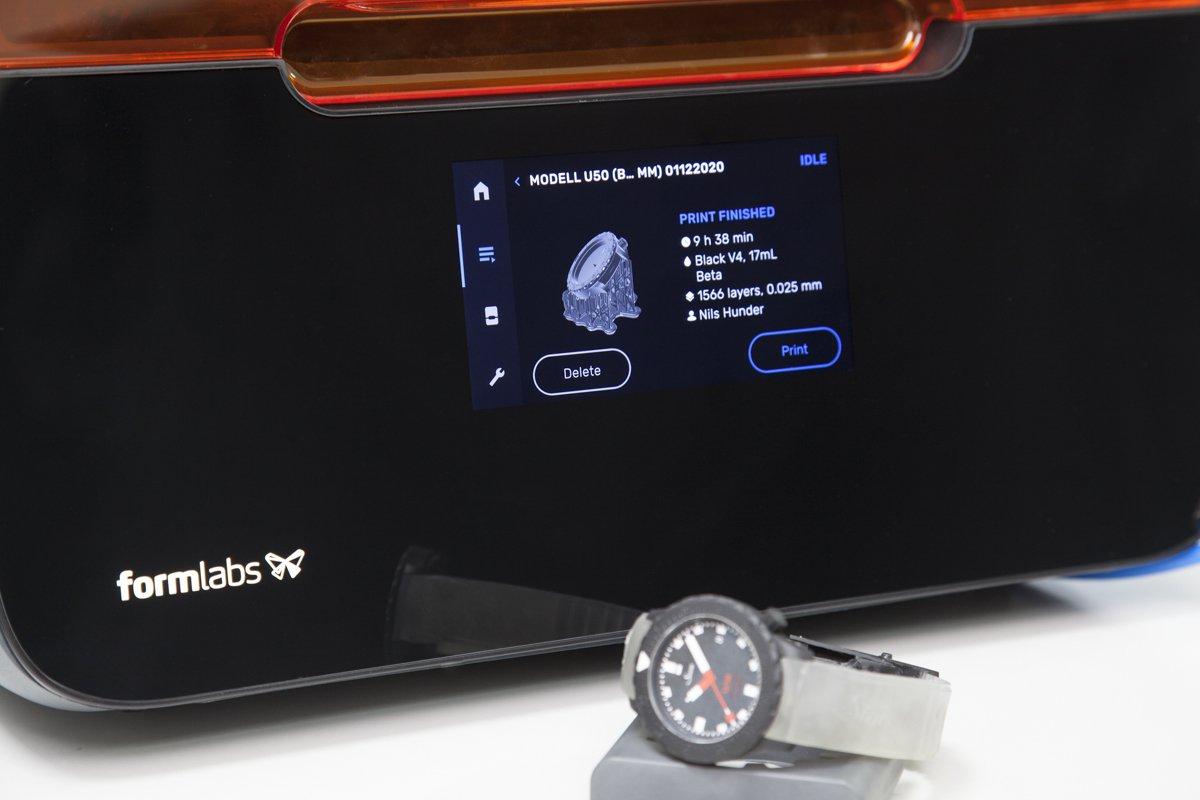
Der Prototyp einer Uhr vor dem Form 3
Aufgrund der stetigen Materialentwicklungen von Formlabs bekommt das Team regelmäßig Anregungen für neue Ideen. So besitzt Flexible 80A Resin dieselbe Shorehärte wie das Silikon der Armbänder, sodass deren Modelle zukünftig auch gedruckt werden.
3D-Drucken von schnellen und kosteneffizienten Produktionswerkzeugen für die Uhrenindustrie
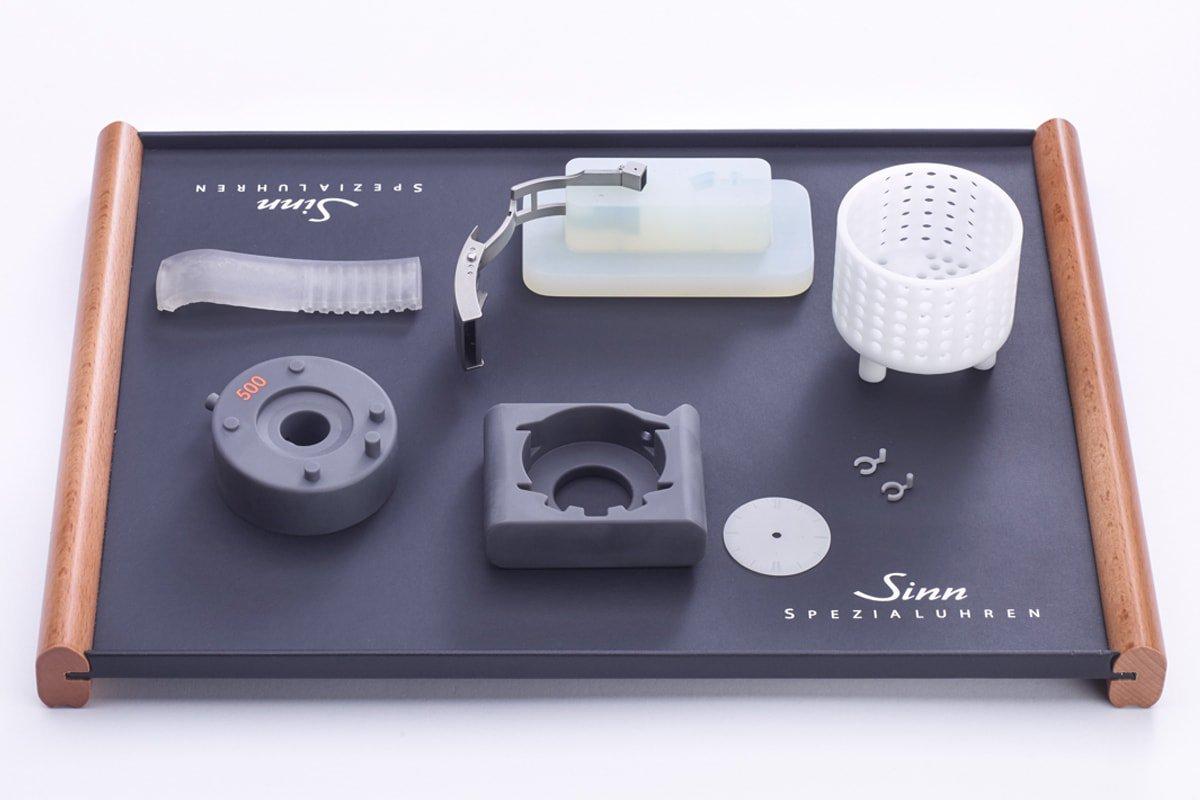
3D-gedruckte, prototypische Uhrenbestandteile, Vorrichtungen und Prüfgeräte, die mit dem Form 3 hergestellt wurden.
Nach der Anschaffung des ersten 3D-Druckers entdeckte das Team von Sinn schnell weitere wertvolle Anwendungsfälle für das Gerät, die über den Prototypenbau hinausgehen. Die Vielseitigkeit und Konsistenz des Form 3 bei der Produktion hochwertiger Drucke eignet sich für verschiedene Anwendungen in der Produktentwicklung und -produktion.
Lesen Sie unseren nächsten Artikel, um zu erfahren, wie das Unternehmen den 3D-Druck für die Herstellung von Produktionswerkzeugen, wie Halterungen, Vorrichtungen und Prüfgeräten, nutzt.