Die Addition der Sicherheit – Wie FRI-PLAST Engineering additive Fertigung für Beratung und Spritzguss nutzt

Die Experten von FRI-PLAST Engineering aus Giffers in der Schweiz wissen: Die erfolgreiche Umsetzung komplexer Kunststoffproduktionen erfordert weitreichendes Fachwissen. Hierfür können sie aus einem Schatz 25-jähriger Erfahrung mit Herstellung, Einsatz, Verarbeitung und Veredelung von Kunststoffen schöpfen. Als Kunststoffingenieur kennt sich CEO Christian Poffet bestens mit traditionellen Herstellungsverfahren wie dem Spritzguss aus. Doch nicht nur die Verschmelzung von Kunststoffen ist sein Fachgebiet, sondern auch die Verschmelzung konventioneller Methoden mit innovativen Lösungen. Um die individuellen Vorstellungen der beratenen Unternehmen in Kunststoff zu verwirklichen, sucht er stets nach neuen Verfahrensansätzen. Seit der Unternehmensgründung 2020 setzt er hierzu auf additive Fertigung als Ergänzung konventioneller Techniken, die er betriebsintern mit einem FDM- sowie dem SLA-Drucker Form 3L kostengünstig umsetzt.
Im Folgenden erfahren Sie, wie FRI-PLAST Engineering additive Fertigung nutzt, um konventionelle und innovative Produktion durch Rapid Tooling synergetisch zu verschmelzen, eine rentable Spritzgussproduktion von Kleinserien zu ermöglichen und Projektrisiken zu reduzieren.
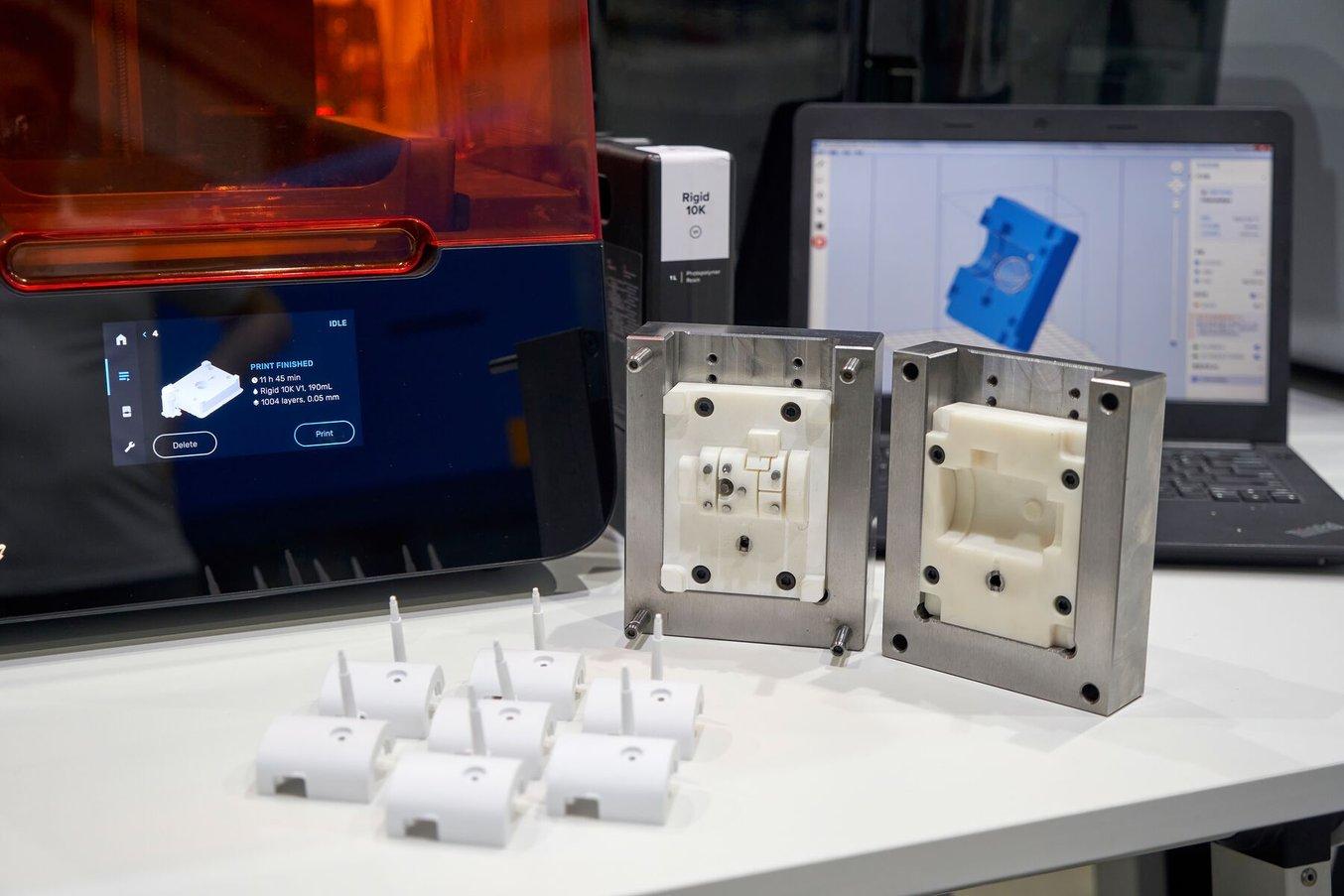
Rasches Spritzgießen von Kleinserien mit Formen aus dem 3D-Drucker
Laden Sie dieses Whitepaper herunter und erfahren Sie mehr über über die Methoden und Richtlinien zur Herstellung 3D-gedruckter Spritzgussformen, um die Kosten zu senken und Lieferzeiten zu verkürizen. Es enthält Fallstudien aus der Praxis von Braskem, Holimaker und Novus Applications.
Spritzguss-Risiken reduzieren – mit Beratung und additiver Fertigung
Das gängige Herstellungsverfahren von Kunststoffteilen ist der Spritzguss. Hierzu wird geschmolzener Kunststoff in eine Form (Spritzgusswerkzeug) eingespritzt, in welcher er aushärtet. Einmal eingerichtet überzeugt das Verfahren mit geringen Grenzkosten, hoher Präzision und enormer Verlässlichkeit. Der große Nachteil: Die dauerhaften Metallformen konventioneller Spritzgussproduktionen müssen aufwändig und energieintensiv durch spanende Bearbeitung oder Metallguss erstellt werden. Daraus folgen immense Fixkosten zu Beginn neuer Produktserien, aufgrund derer das Verfahren auf die Produktion großer Stückzahlen beschränkt und zusätzlich hochriskant ist. Denn bereits kleinste Anpassungen des Produkts – beispielsweise aufgrund veränderter Kundenwünsche, Designfehler oder mangelnder Projektplanung – erfordern neue Spritzgusswerkzeuge. Frühzeitige Planungssicherheit ist ein wesentlicher Parameter für den wirtschaftlichen Erfolg von Spritzguss-Projekten.
Die Erfahrung und Expertise von FRI-PLAST Engineering reduziert die kostspieligen Risiken der Spritzgussproduktion. Beratend steht das Team insbesondere kleineren Herstellern zur Seite, wenn fehlende Kenntnis eine sichere Planung verhindert und Projekte gefährdet. Christian Poffet identifiziert vorab zentrale Produktionskriterien, das optimale Material sowie die geeignete Verarbeitungsform zur Umsetzung der Produktanforderungen, unterstützt in der Werkzeugkonstruktion und sichert gegen antizipierte Hürden ab.
Mit dem Ziel, seiner Kundschaft die Planungssicherheit zu ermöglichen, die sie sich von seiner Fachberatung erhofft, bestand die Herausforderung für Christian Poffet darin, teuren Anpassungen von Dauerformen vorzubeugen und die Herstellung von Kleinserien zu ermöglichen – die Lösung fand er in der additiven Fertigung. Mit dieser werden seine Empfehlungen für die Beratenen erfahrbar und die Gefahr späterer Anpassung zusätzlich reduziert. Dank geringer Stückkosten und Durchlaufzeiten erstellt Christian Poffet mit 3D-Druck in jeder Projektphase gezielt Prototypen und Erstmuster zur frühzeitigen Prüfung geplanter Produkte. Für die Unternehmen schafft er so Planbarkeit und Sicherheit.
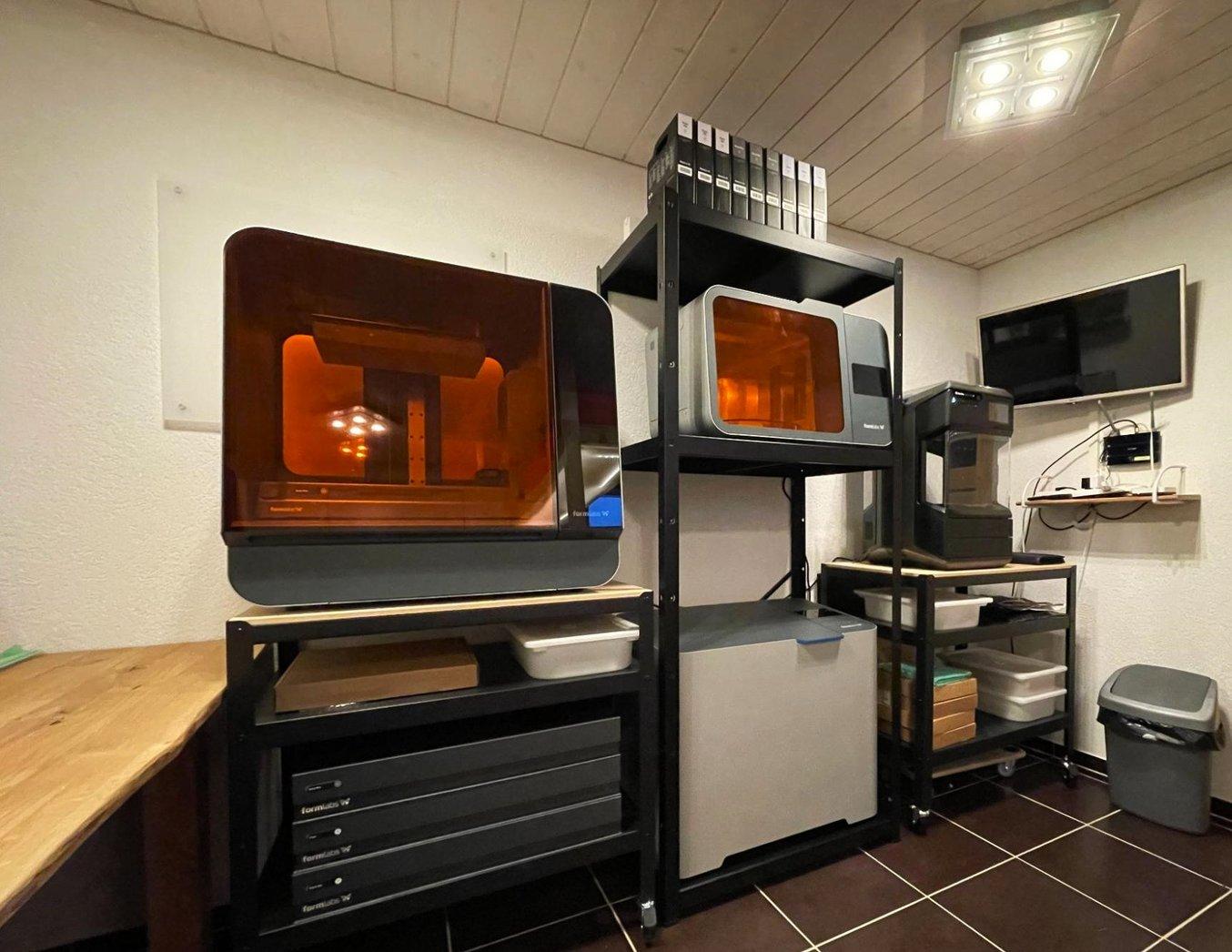
Work-Life-Balance – mit 3D-Druck fertigt Christian Poffet Prototypen im heimischen Keller.
Mit Rapid Prototyping zum Produktkonzept
Mithilfe eines Fused-Deposition-Modeling-Druckers (FDM) fertigt Christian Poffet seit 2021 Teile aus Kunststoffen, die typisch für Endverbrauchsteile sind: ABS, ASA, PC und carbonfaserverstärktes PA12. Prototypen können so frühzeitig hinsichtlich ihrer Funktionalität evaluiert werden, da sie bereits aus dem geplanten Material des Endprodukts geformt sind. Dank geringer Durchlaufzeiten und Kosten prüft Christian Poffet gemeinsam mit Kund*innen konzeptionelle Weiterentwicklungen in mehreren Iterationen, um Design-Mängel zu vermeiden. Erst wenn sich die Prototypen der Prüfung bewähren, geht das Projekt in die Phase der Werkzeugentwicklung über.
Mit FDM-Druck allein konnte Christian Poffet allerdings nicht die gesamte Bandbreite von Kundenanfragen bearbeiten. Die FDM-gedruckten Prototypen halfen zwar bei der Absicherung des Produktdesigns, doch für die Entwicklung und Validierung von Werkzeugen in Vorserien waren die verfügbaren Druckmaterialien nicht geeignet. Denn FDM-Drucke sind anisotrop, zu unpräzise sowie zu wenig druck- und hitzeresistent. Diese Lücke im Portfolio von FRI-PLAST Engineering konnte Christian Poffet mit der Nutzung von Stereolithographie-Druck (SLA) für Rapid Tooling schließen.
Mit Rapid Tooling zur Serienproduktion
Rapid Tooling nennt man Techniken zur schnellen und kostengünstigen Herstellung von Werkzeugen als Ersatz teurer Dauerformen herkömmlicher Fertigung. Durch Rapid Tooling validieren Hersteller ihre Entwürfe und Materialien zusätzlich, bevor sie zur Serienproduktion übergehen. Dies beschleunigt die Produktentwicklung durch schnelle Iterationen. Mit Rapid Tooling hergestellte Werkzeuge können für die Produktion von Pilot- und Nullserien mit geringen Stückzahlen verwendet werden, um die Leistung der Teile unter realen Anwendungen in Beta- und Validierungstests zu evaluieren. In 3D-gedruckten Formen können nämlich bereits die endgültigen Produktionsmaterialien spritzgegossen werden.
So hilft Rapid Tooling bei der Fehlerbehebung im Fertigungsprozess: Fehler im Werkzeug werden erkannt, bevor man in teure Produktionswerkzeuge investiert. FRI-PLAST Engineering bietet seiner Kundschaft so die Möglichkeit, Prototypen aus spezielleren Endmaterialien, die nicht durch FDM gedruckt werden können, schon in der Entwicklungsphase auf Herz und Nieren zu testen. Und falls nötig, direkt zu optimieren. Rapid Tooling stellt damit eine Unterstützung für Rapid Prototyping dar, welches für die Beratung von FRI-PLAST Engineering und für die Planungssicherheit im Spritzguss elementar ist.
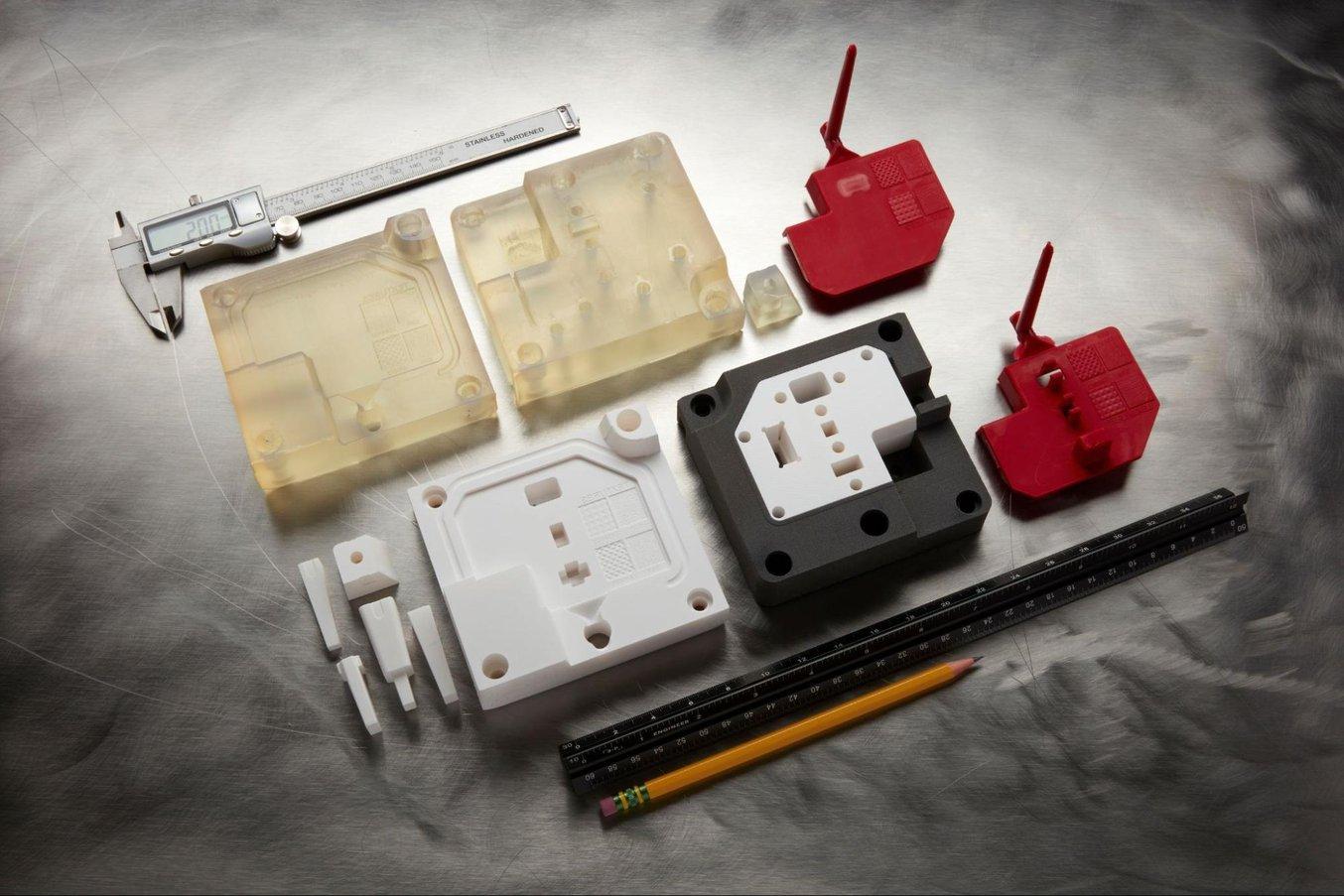
Leitfaden zum Rapid Tooling
Lernen Sie in diesem Whitepaper, wie Sie Rapid Tooling mit konventionellen Fertigungsverfahren wie Spritzguss, Thermoformen und Guss kombinieren.
Darüber hinaus bietet Rapid Tooling die Möglichkeit, Maßanfertigungen oder Kleinserien von Endverbrauchsteilen herzustellen, die mit konventioneller Werkzeugbestückung schlicht unerschwinglich wären. Dies betrifft gerade Hersteller, die aufgrund fehlender Erfahrung besonders von FRI-PLAST Engineerings Beratung profitieren. Kleinere und junge Unternehmen können ihre Nachfrage nur schwer prognostizieren und befinden sich häufig noch im Entwicklungsprozess, weshalb sie zunächst nur mit geringen Stückzahlen planen, bei denen sich die Anschaffungskosten von Dauerformen aus Metall nicht amortisieren. Durch die Anwendung additiver Fertigung im Spritzguss kann die Vorlaufzeit der Produktion von Monaten auf nur wenige Tage reduziert werden. Die drastische Verringerung der Kosten zur Herstellung der Formen macht bereits die Herstellung geringster Stückzahlen rentabel. Die Kostencharakteristika von Serien unterschiedlicher Volumina werden in der folgenden Tabelle an einer exemplarischen Produktion verdeutlicht.
Kleines Produktionsvolumen | Mittleres Produktionsvolumen | Großes Produktionsvolumen | |
---|---|---|---|
Produktionsvolumen | 100 | 5000 | 100 000 |
Methode | Betriebsinterne(r) Spritzgussproduktion und Formenbau | Ausgelagerte(r) Spritzgussproduktion und Formenbau | Ausgelagerte(r) Spritzgussproduktion und Formenbau |
Form | 3D-gedrucktes Polymer | Bearbeitetes Aluminium | Bearbeiteter Stahl |
Durchlaufzeit bis zum Endprodukt | 1–3 Tage | 3–4 Wochen | 4–8 Wochen |
Erforderliche Geräte | 3D-Drucker, Desktop-Spritzgießmaschine* | - | - |
Formenkosten | 100$ | 3,000$ | 20 000 $ |
Materialkosten | 0,5 $/Teil | 0,5 $/Teil | 0,5 $/Teil |
Arbeitskosten oder Auslagerungskosten | 2,5 $/Teil | 1,5 $/Teil | 1 $/Teil |
Produktionskosten insgesamt | 400$ | 13 000 $ | 170 000 $ |
Kosten pro Teil | 4$ | 2,6 $ | 1,7 $ |
* Die Anschaffungskosten werden in diesem Beispiel nicht in die Produktionskosten eingerechnet, da die Kosten für diese Werkzeuge auf mehrere Projekte aufgeteilt werden können. Der Kauf einer Desktop-Spritzgießmaschine und eines SLA-3D-Druckers ermöglicht es Unternehmen, für weniger als 10 000 $ in den Spritzguss einzusteigen.
Stereolithographie-Druck mit beständigen Kunstharzen
Doch die Anforderungen an Druckmaterial und -präzision zur additiven Herstellung von Spritzgusswerkzeugen sind hoch. Als kleines Dienstleistungs- und Beratungsbüro musste FRI-PLAST Engineering diese hohen Ansprüche zusätzlich erschwinglich erfüllen können. Sich des Mehrwerts guter Beratung bewusst, wandte sich Poffet an die Schweizer Experten für additive Fertigung der 3D-EDU GmbH. Gemeinsam fanden sie FRI-PLAST Engineerings optimale Lösung zur Umsetzung hausinternen Rapid Toolings: den SLA-Drucker Form 3L. Nicht nur für den Spritzguss druckt Christian Poffet seit dessen Anschaffung im Jahr 2023 großformatige Prototypenwerkzeuge. Auch für die Werkzeugentwicklung für den Greiferbau im Automationsbereich nutzt er den 3D-Drucker von Formlabs, ebenso wie für Produktprototypen, die vorher FDM-gedruckt wurden.
"Der Form 3L wird schon zu Beginn eines Projektes sehr früh in der Design-Gestaltung eingesetzt, um dem Kunden ein visuelles und haptisches Muster zur Verfügung zu stellen. Die Arbeit wird so sehr stark erleichtert, da der Kunde sein zukünftiges Produkt bereits in den Händen hält. Die Druckqualität und -präzision des Form 3L unterscheidet sich massiv vom FDM-Druck."
Christian Poffet, CEO von FRI-PLAST Engineering

Mit 3D-gedruckten Prototypen aus dem Form 3L kann Christian Poffet den Entwicklungsprozess veranschaulichen
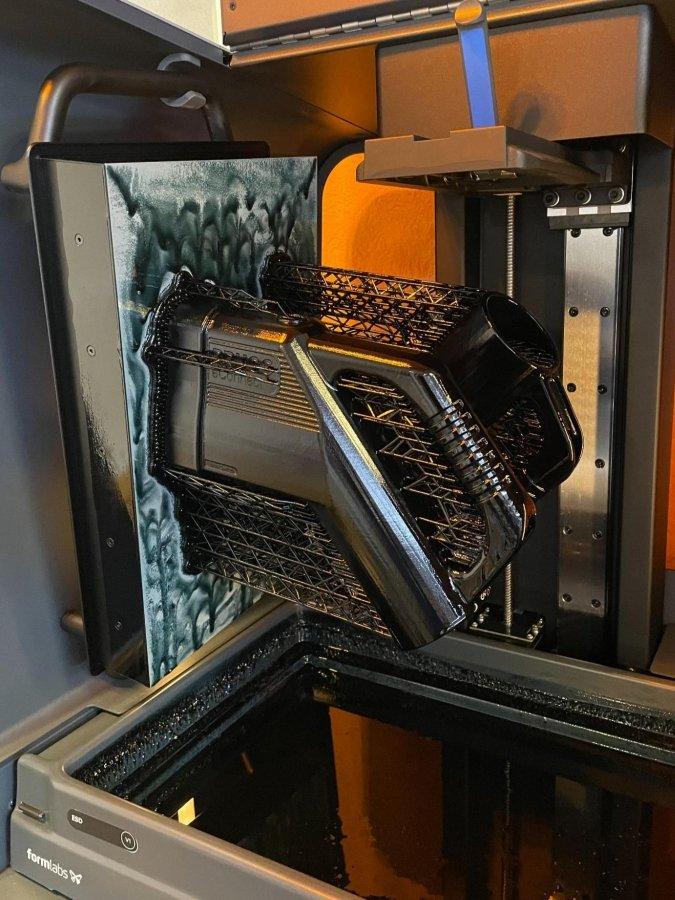
Wie 3D-Druck FRI-PLAST Engineering seitdem in der Umsetzung von Spritzguss-Projekten unterstützt, verdeutlicht ein jüngeres Beispiel ihrer vielseitigen Kundenprojekte. Zu Beginn steht häufig, dass Christian Poffet anhand der gewünschten Produkteigenschaften identifiziert, welcher Kunststoff und welche Verarbeitungsform hierfür geeignet ist. Im konkreten Fall fiel die Wahl auf das hochdichte und spannungsrissbeständige Polyethylen PE-HE7541, welches nur im Spritzgussverfahren sinnvoll verarbeitet werden kann. Die Herausforderung in diesem Anwendungsfall bestand darin, das Werkzeug so zu gestalten, dass der Kunde kostengünstig und schnell Teile aus dem Endmaterial zur Verfügung erhält. Zur Validierung der Formen in einer Vorserie von etwa 50 Stück wurden daher Werkzeugprototypen mit dem Form 3L erstellt. Dafür wurde Rigid 10K Resin verwendet, welches der hohen Temperatur und dem Druck, die für das Spritzgießen notwendig sind, über mehrere Zyklen hinweg standhalten kann.
Für den Spritzgießer war die Verwendung 3D-gedruckter Werkzeuge eine Premiere und spannende Abwechslung zugleich, da sich der gesamte Prozess von der Arbeit mit Stahlformen unterscheidet. Auf Grundlage der Rückmeldungen des Spritzgießers wurde die Qualität der Werkzeuge schrittweise mit mehreren Drucken optimiert. In kürzester Zeit konnte dieser so saubere Teile in Produktqualität herstellen und war begeistert, wie schnell seine Wünsche berücksichtigt werden konnten. Durch die Prüfung des 3D-gedruckten Werkzeuges in dieser Kleinserie konnte das für die spätere Serienproduktion gefertigte Stahlwerkzeug im Vorfeld optimiert werden.
"Durch den Einsatz des Form 3L konnte die Qualität des danach gebauten Stahlwerkzeuges, für die Serienfertigung, so schon im Vorfeld massiv optimiert werden, da gewonnene Erkenntnisse direkt umgesetzt wurden."
Christian Poffet, CEO von FRI-PLAST Engineering
Projekt | |
---|---|
Unternehmen | Medizinunternehmen |
Produkt | Bottom Cover |
Anforderungen | Teil aus finalem Material für Ultraschallversuche |
Spritzgussmaterial | PE-HE7541 (140 C) |
Anzahl der Teile aus einer Form | > 50 |
Zykluszeit | 3 Minuten |
Durchlaufzeit des Projekts (Konstruktion, 3D-Druck, Nachbearbeitung, Bemusterung) | 3 Wochen |
Mit dem Form 3L konnte Poffet das Wachstum von FRI-PLAST Engineering unterstützen. Mit SLA-Druck kann er flexibler als je zuvor Kundenanfragen bearbeiten, reduziert Projektkosten sowie -durchlaufzeiten und schließt so mehr Projekte pro Jahr ab.
"Wäre der Form 3L nicht vorhanden, wären die Projektkosten höher und auch die Flexibilität um einiges mehr eingeschränkt. Die Kunden entscheiden kurzfristiger, einen Druck umzusetzen, im Wissen, dass die Infrastruktur bei FRI-PLAST da ist."
Christian Poffet, CEO von FRI-PLAST Engineering

Spritzgussteile in unter 24 Stunden? Leitfaden für schnellen Spritzguss in Kleinserie
Erfahren Sie, wie Sie durch Stereolithografie-3D-Druck (SLA) gefertigte Formen in Ihrem Spritzgussverfahren einsetzen, um Kosten und Durchlaufzeiten zu verringern und bessere Produkte zu liefern. Anhand realer Fallstudien zeigen wir Ihnen, wie der 3D-Druck die Herstellung von Rapid Tooling auf Abruf und damit die schnelle Kleinserienproduktion von Thermoplastteilen ermöglicht.
Die Kraft der Synergie
Es ist gerade der Charme des Unbekannten, welcher neue Projekte so spannend und die Suche nach Innovationen so vielversprechend macht. Wird hierfür die Beratung durch Experten wie FRI-PLAST Engineering hinzugenommen, können Risiken frühzeitig reduziert werden. Zusätzliche Sicherheit schaffen Prototypen, die durch Rapid Prototyping und Rapid Tooling mithilfe additiver Fertigung von Beratern wie Christian Poffet kostengünstig betriebsintern hergestellt werden. Durch die Synergie additiver Fertigung mit traditionellem Spritzguss ist FRI-PLAST Engineering heute in der Lage, in kürzester Zeit funktionale Prototypen im Endmaterial zu fertigen, welche höchsten Ansprüchen genügen und Kund*innen die Sicherheit geben können, die sie zur Umsetzung neuer Projekte benötigen. Auch FRI-PLAST Engineering selbst konnte bei der Suche nach Innovativität von der Expertise eines Partners profitieren: 3D-EDU.
"Die 3D-EDU GmbH bietet einen ausgezeichneten Service im Anwendungsbereich, da sie selbst die verwendeten Drucker für Kunden einsetzen und so kompetent mit fachlichem Know-How zur Seite stehen. Man kann jederzeit anrufen und es wird sofort geholfen und unterstützt."
Christian Poffet, CEO von FRI-PLAST Engineering
So werden Synergien genutzt – erstens durch die Zusammenarbeit mit beratenden Experten und zweitens die Verbindung von Herstellungsverfahren. Auch in Zukunft wird FRI-PLAST Engineering nach innovativen Einsatzmöglichkeiten additiver Fertigung suchen. Bereits heute setzen sie den Form 3L , dank dessen vielseitiger Druckmaterialien für die Umsetzung unterschiedlicher Kundenprojekte ein und planen den "Form 3L in Zukunft noch viel häufiger für die Umsetzung von Prototypenwerkzeugen einzusetzen. Bei jedem Kundenprojekt kommt es auf andere Anforderungen an. Mal wird die Festigkeit gefordert, mal soll die Haptik beurteilt werden oder es wird die Genauigkeit und auch die Geometrietreue gefordert. Da hilft einfach die Vielfalt der Materialien, die Prototypen für den Kunden so nah an die Realität zu bringen, damit der Kunde schnell seine Tests einsatzgerecht durchführen kann", erklärt Chritian Poffet voller Vorfreude auf neue Projekte.