Wie SLA- und SLS-3D-Druck zur Überwachung des Wasserverbrauchs in Dürrezeiten beitragen

Die Auswirkungen des Klimawandels sind auf der ganzen Welt zu spüren, und der 3D-Druck hilft Unternehmen dabei, sich weiterzuentwickeln, um der Herausforderung gewachsen zu sein. Angesichts der Aktualisierung der behördlichen Vorgaben zur Wasser- und Stromnutzung als Reaktion auf anhaltende Dürren, häufigere Waldbrände und stärkeren Smog kommen Privatpersonen, Unternehmen und Gemeinden kaum damit hinterher, ihren Wasserverbrauch genau mitzuteilen und Verbesserungen nachzuweisen. Wie heißt es jedoch: Was man nicht messen kann, kann man nicht lenken. Genau da kommt Next Meters ins Spiel.
Next Meters ist ein Hersteller verbundener Wassermessgeräte und verfolgt die Mission, Menschen weiterzubilden und diejenigen zu belohnen, die sparsam mit Wasser umgehen. Das Unternehmen stellt feste Durchflussmesser her, die den Wasserverbrauch privater, kommerzieller oder kommunaler Kunden messen. Die Herausforderung liegt darin, Ausrüstung zu produzieren, die an die große Bandbreite der existierenden Vorrichtungen im Versorgungsnetzwerk angepasst werden kann. Mithilfe mehrerer Drucker der Typen Form 2, Form 3+, Form 3L und Fuse 1 konnte Next Meters Prototypen in Rekordzeit herstellen, seine Formdesigns verbessern und sogar Teile für die Endverwendung als Teil seiner Ausrüstung produzieren.
Wir haben mit David Clyde, Geschäftsführer von Next Meters, über den Markt für Wasserzähler gesprochen und erfahren, warum der 3D-Druck hier die perfekte Ergänzung für traditionelle Fertigungsprozesse bietet.
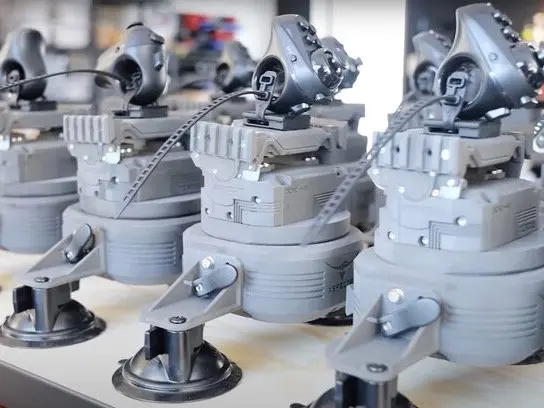
3D-gedruckte Teile für die Endverwendung im Belastungstest
In diesem Whitepaper stellen wir Formlabs' Hardware und Materialien für den 3D-Druck von Endverbrauchsteilen vor. Das Whitepaper dokumentiert verschiedene Fallstudien von Anwendern und enthält Ergebnisse von Belastungstests, um die Eignung von 3D-Druckmaterialien für Endverbrauchsanwendungen zu überprüfen.
Sparsamkeit belohnen
In der Vergangenheit waren Wasserzähler mechanische Vorrichtungen, in denen Zahnräder im Inneren eines Rohres durch den Wasserstrom angetrieben wurden, sodass der Wasserverbrauch anhand des Durchflusses berechnet werden konnte. Das bringt jedoch mehrere Probleme hervor: Gebäude mit mehreren Wohnungen haben meist nur einen von der Stadt installierten Wasserzähler und der Verbrauch wird zu gleichen Teilen auf alle Wohnungen aufgeteilt. Somit werden sparsame Wassernutzer bestraft, während Wasserverschwender belohnt werden. Darüber hinaus sind mechanische Wasserzähler weniger genau und verschlechtern sich mit der Zeit, sodass starke Diskrepanzen zwischen dem gemessenen und dem tatsächlichen Wasserverbrauch entstehen.
Next Meters entwickelt und fertigt extrem genaue und vollständig miteinander verbundene Geräte zur Wassermessung, wie etwa Ultraschall-Durchflussmesser, Leckage-Sensoren und fernsteuerbare Absperrventile. Mithilfe dieser Geräte wird selbst der geringste Wasserverlust durch Probleme wie gerissene Rohre oder leckende Dichtungen bemerkt. Gerade in den Versorgungssystemen großer Wohnhäuser läppern sich kleine Lecks mit der Zeit zu riesigen Verlusten, die die Bewohner Geld kosten und wertvolle Wasserbestände verschwenden.

Ein Experte von Next Meters untersucht ein System, das demnächst mit einem auf dem SLS-Drucker Fuse 1 gedruckten Wassermessgerät versehen wird.
„Die Nachfrage nach unseren Produkten wächst aufgrund verschiedener Faktoren. Es gibt neue staatliche Vorgaben – Kalifornien setzt Gesetze zum sparsamen Wasserverbrauch durch. Der Bundesstaat hat seit Jahren mit einer Dürre zu kämpfen, die in vielen Regionen großen Schaden anrichtet. Mehrere Bundesstaaten verabschieden Gesetze, die aus Sparsamkeitsgründen die Nachverfolgung des Wasserverbrauchs vorschreiben, und auch die Leute selbst möchten besser über ihren Verbrauch informiert sein.“
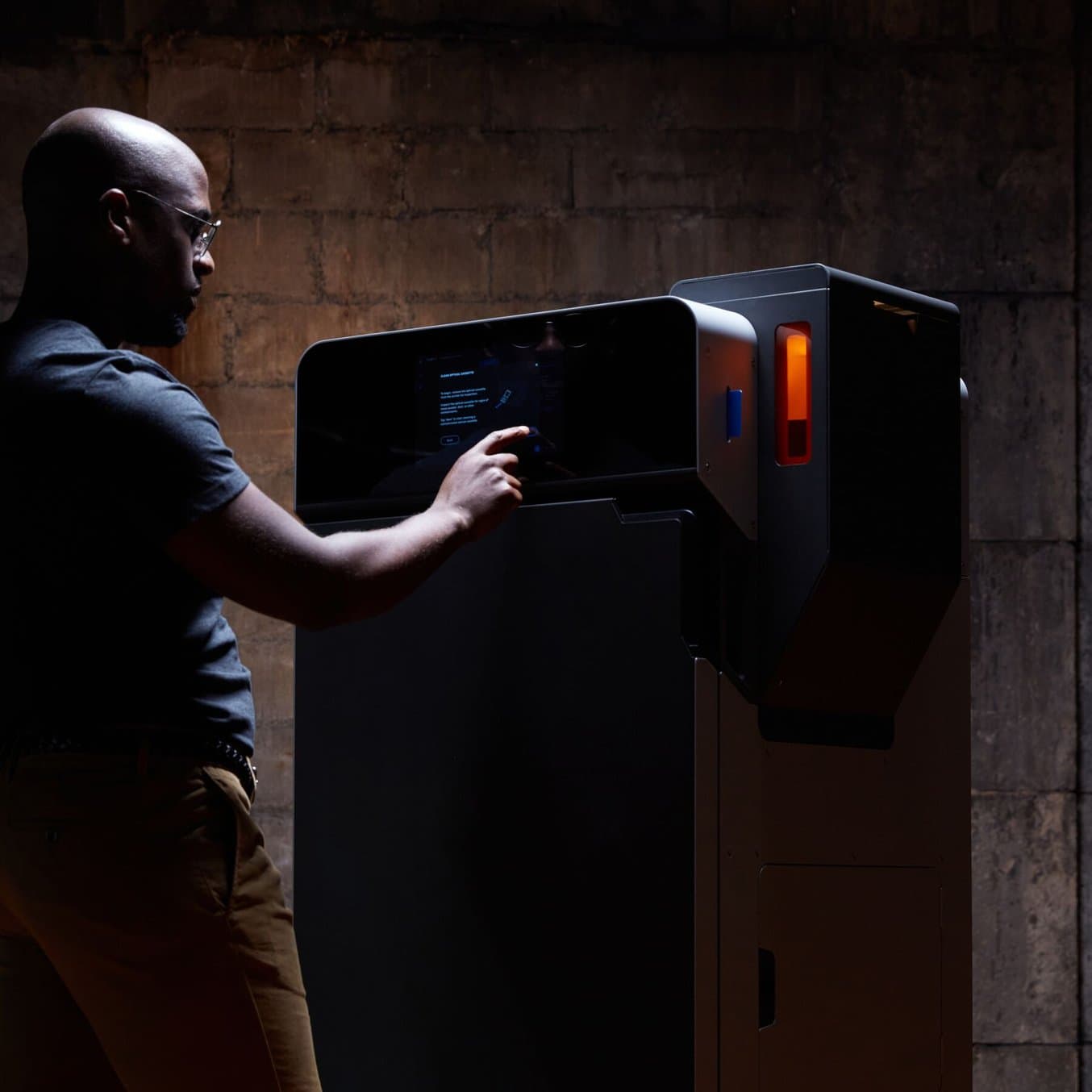
Outsourcing oder Betriebsintern: Wann sollte man SLS-3D-Druck in den eigenen Betrieb holen?
In diesem Whitepaper untersuchen wir den Mehrwert betriebsinterner SLS-3D-Drucker im Vergleich zum Outsourcing von SLS-Teilen an einen Fertigungsdienstleister.
Universallösungen gibt es nicht: 50 Jahre Wasserzähler bedeuten individuelle Anpassung
Der jüngste Anstieg der Nachfrage verschärft die Herausforderung noch, die Next Meters bevorsteht: Das Unternehmen muss Geräte zur Wassermessung anbieten, die sich auf den verschiedensten Modellen von Wasserzählern anbringen lassen, die alle zu unterschiedlichen Zeitpunkten von verschiedenen Anbietern installiert wurden. Um hierfür eine praktikable Lösung zu bieten, ob für private Kunden oder öffentliche Einrichtungen, muss Clydes Team zunächst den Typ des vorhandenen Wasserzählers ermitteln und dann entweder bestimmen, welches ihrer Produkte passen könnte, oder ein neues Gerät herstellen. Als das Unternehmen sich nach den privaten Wohnimmobilien auch in den kommunalen Bereich ausbreitete, stieg die Anzahl der Wasserzählermodelle noch weiter an und machte die Kompatibilität zu einer umso größeren Herausforderung.
„Nun, da wir auch im kommunalen Bereich tätig sind, stellen wir fest, dass viele Städte eine Vielzahl verschiedener Marken und unterschiedlich alte Wasserzähler nutzen. Selbst in Kleinstädten mit 3000 Wohneinheiten können uns sechs oder sieben verschiedene Typen von Wasserzählern begegnen. Jeder davon hat eine andere Form und Größe und benötigt für die Nachrüstung mit unseren IoT-Geräten eine individuelle Halterung“, erklärt Clyde.
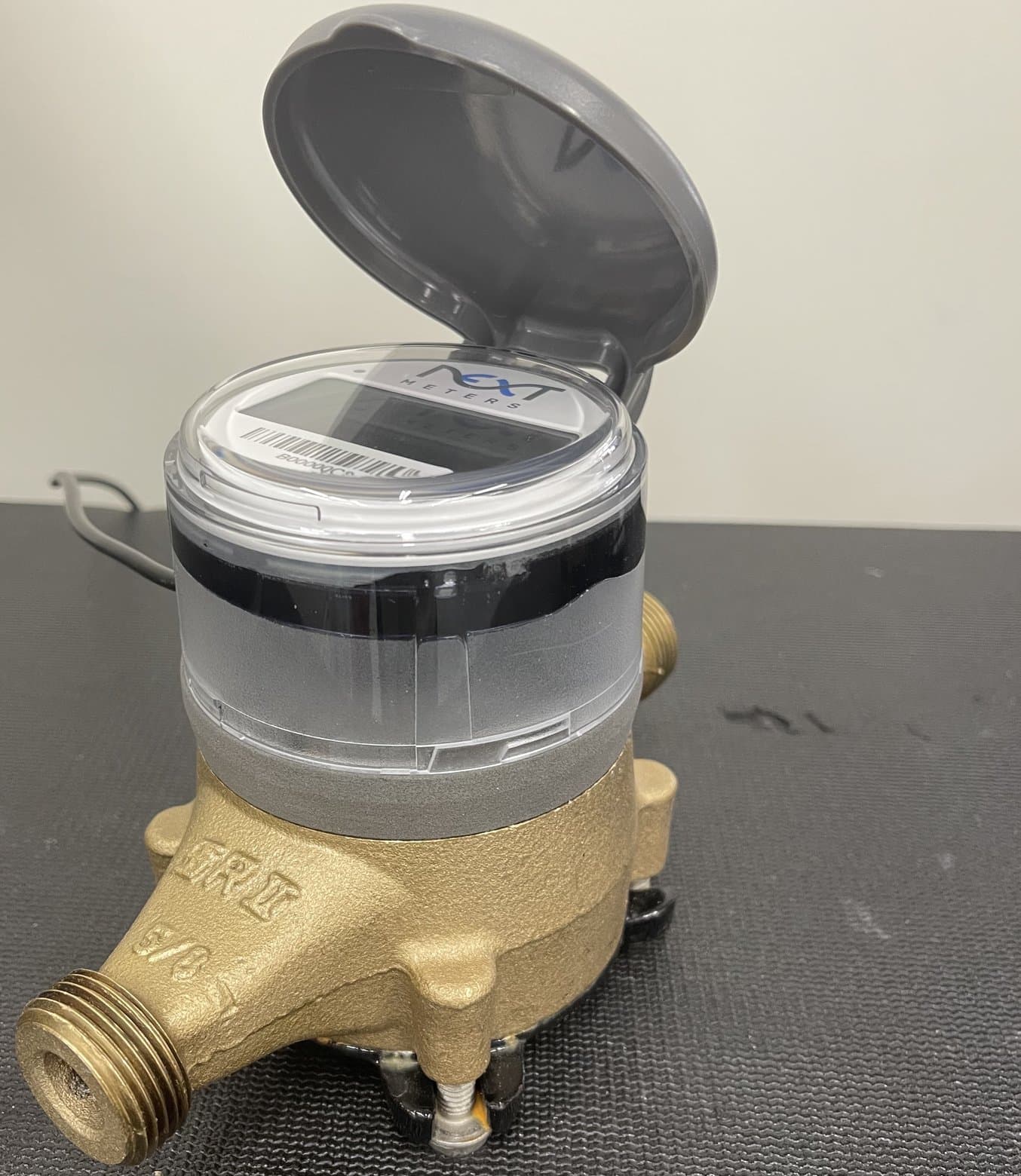
Ein Wasserzähler (transparentes Gehäuse), installiert auf einem Hahn eines Wassermesssystems (vergoldet) mithilfe einer auf dem Fuse 1 individuell SLS-3D-gedruckten Halterung (graues, mittleres Teil).
Langwierige Konstruktion, teurer Werkzeugbau
Die Produktentwicklung begann beim Ingenieurteam von Next Meters in der Vergangenheit mit einem Tonmodell, an dem die allgemeine Form der Geräte entworfen wurde. War ein Design gefunden, das ihren Vorstellungen entsprach, ging das Team zur CAD-Modellierung über und sendete sein 3D-Modell schließlich zur Prototypenfertigung an einen Dienstleister.
„Unsere Maschinenbauingenieure haben wortwörtlich Bildhauerei betrieben. Sie haben Modelle ausgeschnitzt, in unsere CAD-Software übertragen, die Modelle an einen Dienstleister geschickt, Soft-Tooling beschafft und dann iteriert, alles noch bevor sie unsere Prototypen überhaupt testen konnten. Das war zeitaufwendig und teuer“, erinnert sich Clyde.
Eine Lösung war, bestehende Werkzeuge anzupassen, um sie mit nur geringfügigen Änderungen für neue Produkte zu nutzen, aber auch hier stieß das Team von Next Meters auf ein Hindernis. Mit jeder Anpassung verloren ihre Werkzeuge an Leistung, und nach mehreren Modifikationen mussten sie ganz entsorgt werden, obwohl ihre Herstellungskosten von 5000 bis 50 000 $ reichten und die Beschaffung eines Ersatzes mehrere Wochen dauern konnte.
Abgesehen davon, dass das Team Hunderte von Werkzeugen benötigte, war auch der Prozess ihrer Herstellung arbeitsaufwendig und kostspielig. Die komplette Fertigstellung der Vorrichtungen zögerte sich immer mehr hinaus und das Unternehmen häufte immense Ausgaben an. Daher stieg Next Meters zur Beschleunigung des Iterationsprozesses auf 3D-Druck um, angefangen mit einem Drucker des Typs Form 2, der später um einen Form 3, Form 3+ und Form 3L ergänzt wurde. Das Team nutzt die Formlabs-SLA-Drucker zur Erstellung von Konzeptmodellen für Formen und zur schnelleren Iteration, wodurch es seinen Designprozess von Monaten auf Tage verkürzen konnte.
Die CNC-Zerspanung dieser Werkzeuge hätte im besten Fall fünf bis sechs Wochen gedauert. Manchmal brauchten wir ein Jahr, um vom Konzeptdesign zum ersten Prototyp zu gelangen. Ein Jahr und mehrere Hunderttausend Dollar an Kosten. Der 3D-Druck hat es uns möglich gemacht, Designentscheidungen schnell zu treffen und erst nach der Validierung jedes Bauteils endgültiges Werkzeug zu bestellen.
David Clyde
Spritzguss für die Masse, SLS für kleine Mengen
Etwa 80 % der im Einsatz befindlichen Versorgungssysteme stammen von ein paar Hauptakteuren der Branche. Für diese Systeme lassen sich Messgeräte effizient über Spritzguss herstellen. Aber was ist mit den restlichen 20 % der Kunden, die von über einem Dutzend weiterer, kleiner Hersteller versorgt werden? Next Meters muss seinen Kunden trotzdem eine Komplettlösung anbieten. Wenn eine Stadt oder Gemeinde ihre Zählersysteme aktualisieren und aufgrund neuer Vorgaben Verbrauchsdaten beschaffen muss, dann müssen alle Anschlüsse abgedeckt werden, nicht nur die einfachen Fälle – ansonsten sind die Daten nutzlos.
„Es macht für eine Stadt keinen Sinn, nur 80 % der Daten erfassen zu können. Wir müssen uns auch um die Sonderfälle kümmern, damit wir unseren Kunden nicht nur eine partielle, sondern eine Komplettlösung bieten können“, erklärt Clyde.
Die Abdeckung der letzten 20 % des Marktes stellte Next Meters vor eine neue Herausforderung. Obwohl Sie ihren Formenbau und den Iterationsprozess durch die SLA-Drucker beschleunigen konnten, wäre die Spritzgussfertigung dennoch unbezahlbar, da die benötigten Stückzahlen niedrig sind. Next Meters nutzte zwar bereits die Bandbreite der für ihre SLA-Geräte verfügbaren Formlabs-Materialien aus, doch die 3D-gedruckten Kunstharzteile eigneten sich nicht als Produktionsteile, da hierfür eine durchschnittliche Lebensdauer von 15 Jahren erforderlich war. Deshalb suchte Next Meters nach einer kosteneffizienten Lösung zur Herstellung von Produktionsteilen in kleinen Stückzahlen.
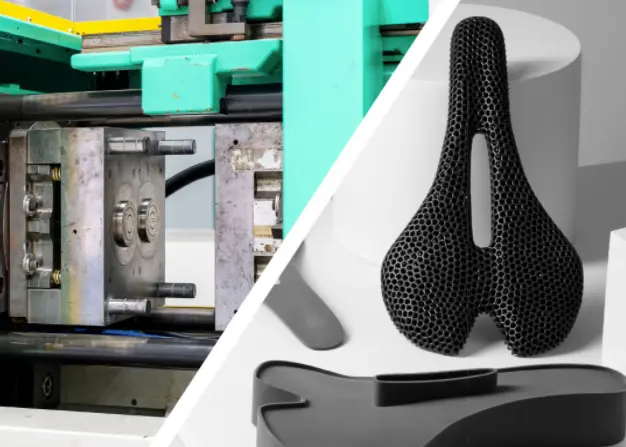
SLS-3D-Druck oder Spritzguss: Wann sollte man Spritzgussteile durch 3D-Druck ersetzen?
Dieses Whitepaper zeigt die Kostendynamik für Anwendungsfälle aus der Praxis und stellt Leitfäden vor für den Einsatz von SLS-3D-Druck, Spritzguss oder einer Kombination beider Verfahren.
Ende 2021 erwarb Clydes Team einen 3D-Drucker für selektives Lasersintern (SLS), den Fuse 1, sowie die Nachbearbeitungsstation Fuse Sift und Nylon 12 Powder. Später wurde ihre Materialpalette noch um Nylon 11 Powder ergänzt. Das Team nutzt Nylon 12 Powder, um Prototypen für die Halterungen der Wasserzähler zu erstellen, und fertigt mit Nylon 11 Powder die endgültigen Gebrauchsteile.
„Es sind Dutzende von Zählermodellen im Umlauf, in so geringen Mengen, dass sich die Werkzeugkosten niemals rentieren würden. Für solche Zähler drucken wir deshalb nach Bedarf Teile auf dem Fuse 1. Jetzt sind wir in der Lage, sowohl für die gängigsten Zählermodelle als auch für die anderen 20 % passende Ausrüstung bereitzustellen, und mit dem SLS-Drucker geht es viel schneller und günstiger“, so Clyde.
Turbulenzen voraus: Selbststützender 3D-Druck als Lösung für Durchflussprobleme
Der Fuse 1 bietet durch die selbststützende Funktion seines Druckbettes noch einen weiteren Vorteil. Für Komponenten des Ultraschall-Durchflussmessers ist Reibung der größte Feind: Das Wasser muss ungebremst durch den Zähler fließen können, damit eine akkurate Messung möglich ist. Für komplexe Bauteile nutzt Next Meters den Fuse 1, um ohne Stützstrukturen Teile mit internen Details zu fertigen.
Eine Gussform für derart komplizierte Teile zu kreieren, würde Monate an Zeit und Beträge im sechsstelligen Bereich kosten. Doch mithilfe des betriebsinternen SLS-Drucks kann Next Meters funktionsfähige Bauteile in nur wenigen Tagen selbst produzieren.
„Komplexere Drucke erledigen wir auf dem Fuse 1, entfernen das Pulver im Fuse Sift und bearbeiten die Teile durch Sandstrahlen nach. Da keine Stützstrukturen zu berücksichtigen sind, erhalten wir einen höheren Detailgrad, und die Teile können sich in Funktionsbaugruppen gut ineinanderfügen und interagieren. Bei einem Wasserzähler mit einer sieben Zoll langen Durchflussröhre zum Beispiel, da können wir keine Stützstrukturen aus der Röhre entfernen. Die Huckel von den Stützen würden den Wasserstrom beeinflussen, zu Turbulenzen führen und damit die Messung verfälschen“, erklärt Clyde.
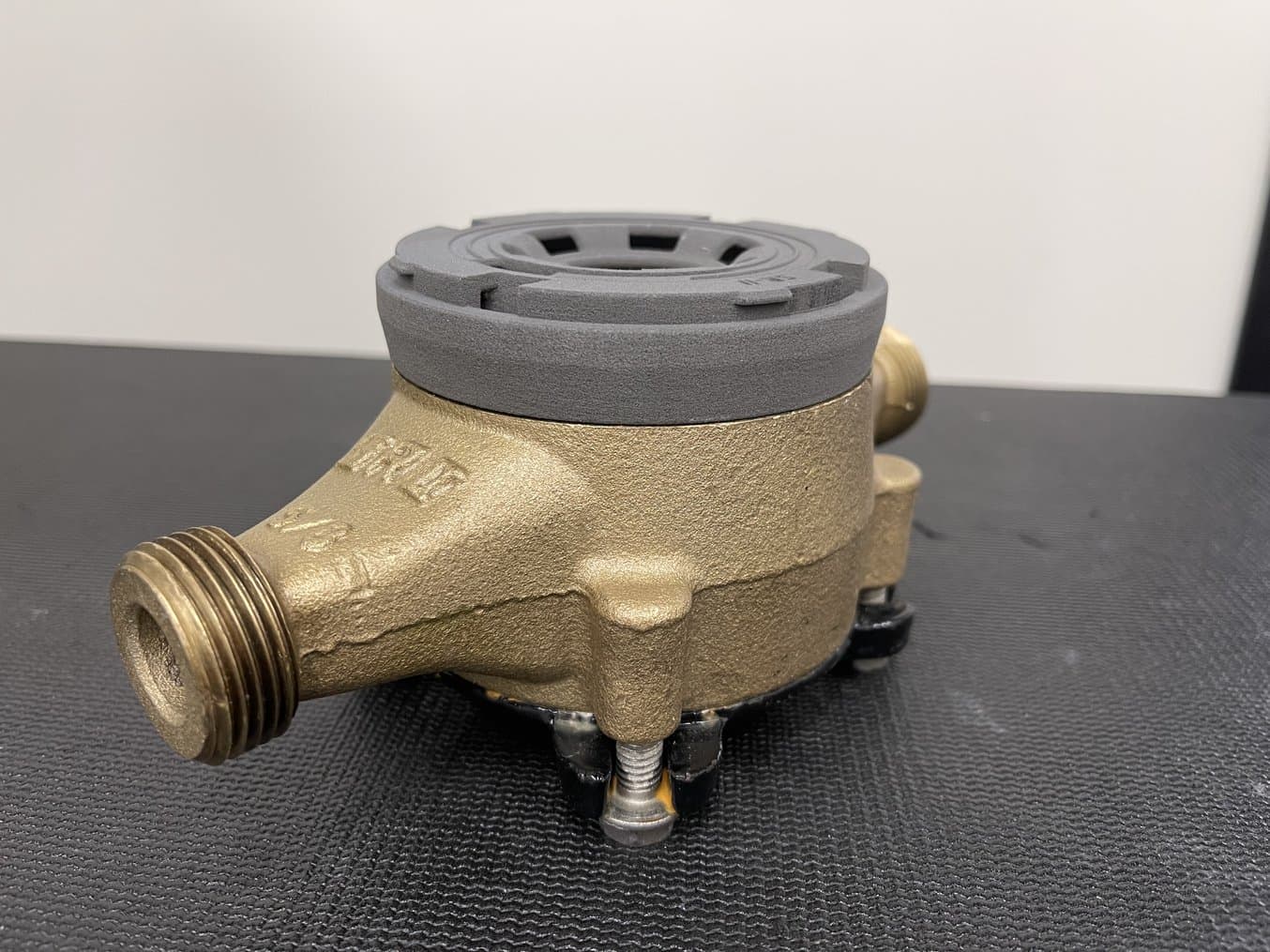
Die auf dem Fuse 1 gedruckte Komponente der maßgefertigten Wasserzähler von Next Meters.
Belastungstest unter realitätsnahen Bedingungen
Um sicherzustellen, dass die Bauteile in der Endverwendung auch den umweltbedingten Anforderungen standhalten, verfügt Next Meters über ein eigenes Team zur Durchführung von Tests. Die 3D-gedruckte Halterung aus Nylon 11 Powder, mit der die Geräte an bestehende Wasserzähler angebracht werden, muss keine externen regulatorischen Prüfungen durchlaufen. Deshalb setzt Next Meters einen eigenen umfassenden Prüfprozess ein, um die Leistungsfähigkeit seiner Teile beim Praxiseinsatz zu gewährleisten.
Mithilfe einer modernen Klimakammer testet das Team die Halterung drei Monate lang bei täglich mehrfachen Temperaturwechseln von 70 °C auf 0 °C und wieder zurück, um einen 15-jährigen Gebrauch im Freien zu simulieren. Da die Tests erfolgreich waren, begann das Team mit der Produktion dieser Endverbrauchsteile auf dem Fuse 1 und setzt inzwischen zwei Materialien ein.
„Mittlerweile sind etwa 250 auf dem Fuse 1 gedruckte Halterungen im Einsatz, die für drei verschiedene Wasserzähler angepasst und aus Nylon 11 Powder hergestellt wurden. Die Prototypen fertigen wir aus Nylon 12 Powder, weil es eine bessere Neuzuführungsrate hat, dann reinigen wir die Maschine und wechseln für die Teile, die im Feld eingesetzt werden, zu Nylon 11 Powder.“
David Clyde
3D-Druck unterstützt Wachstum und Weiterbildung
Da die Fertigung von Produktionsteilen auf Abruf dank des Fuse 1 kosteneffizient geworden ist und auch die Ausgaben für die Entwicklungs- und Prototyping-Phase gesenkt wurden, kann Next Meters sein Geschäft nun weiter ausdehnen und noch mehr Kommunen erreichen. Ein Teil des Unternehmenswachstums ist auch seinen internen Programmen zur Ausbildung und beruflichen Entwicklung zu verdanken. Mehr und mehr Unternehmen stützen sich auf die additive Fertigung, was bedeutet, dass Arbeitskräfte sich die nötigen Fertigkeiten zur Implementierung der Technologie aneignen müssen. Hierfür hat Next Meters eine interne Lösung entwickelt. Alle Mitarbeitenden haben die Möglichkeit, die 3D-Drucker auf Abruf zu nutzen, und viele haben diese Option ausgenutzt, um sich im Bereich Produktdesign und Advanced Manufacturing weiterzubilden.
„Mehrere Mitarbeiter außerhalb unseres Entwicklungsteams haben sich selbst Kenntnisse im Maschinenbau angeeignet und das Unternehmen mit diesen neuen Fertigkeiten vorangebracht. Es ist schön, die Kreativität unserer Belegschaft zu erleben und diejenigen, die lernen und sich beruflich weiterentwickeln wollen, zu unterstützen“, so Clyde.
Zusätzlich arbeitet Clyde mit einem örtlichen 3D-Druck-Club zusammen, um auch Schüler*innen Zugang zum 3D-Druck und Lernmöglichkeiten zu bieten. Jeden Monat besuchen Lernende das Prototyping-Labor von Next Meters und können dort ihre eigenen Designs auf den FDM-, SLA- und SLS-Druckern drucken. Clyde sieht darin eine Chance, die Implementierung der Technologie voranzubringen und die Branche im Ganzen zu fördern, indem er zukünftige Arbeitskräfte weiterbildet.
„Es macht Spaß, zu beobachten, wie sie den Prozess durchdenken. Der 3D-Druck wird sich in der Fertigung auf jeden Fall ausbreiten – die Jugend ist offen dafür und entwirft Teile, die speziell darauf ausgelegt sind, anders als traditionelle Maschinenbauingenieure, die ihre Designpraktiken erst anpassen müssen. Genau deswegen unterstützen wir diese jungen Leute, denn diese jungen Ingenieure werden einmal die Zukunft der Fertigung verändern“, meint Clyde.
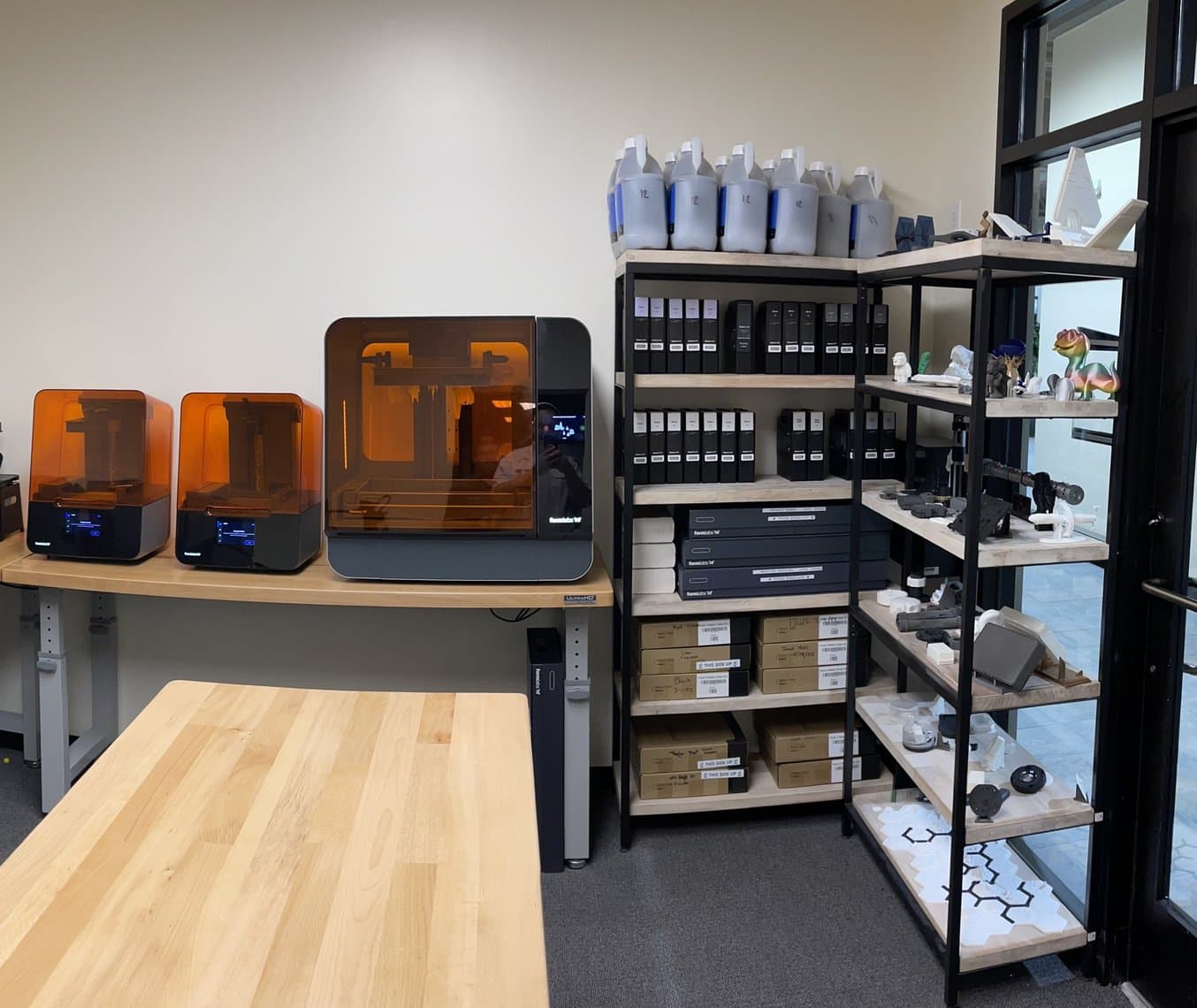
Der Form 3L erlaubt es den Mitarbeitenden und Mitgliedern des 3D-Druck-Clubs, großformatige Prototypen und Modelle zu drucken.
Zugang erleichtern
Dank des neuen kombinierten Arbeitsprozesses mit Spritzguss und 3D-Druck ist Next Meters für jede Situation gewappnet und kann weitere Gemeinden dabei unterstützen, ihren Wasserverbrauch korrekt zu messen und Personen zu belohnen, die mit dieser immer kostbareren Ressource sparsam umgehen. Der 3D-Druck hat die Prototypenfertigung und Entwicklungsphase des Unternehmens beschleunigt, die Kosten des Werkzeugbaus reduziert und die Produktion von Endverbrauchsteilen möglich gemacht. Noch dazu bietet er den Mitarbeitenden und der Gemeinschaft Hilfsmittel zur Weiterbildung und Schulung.
„Die Investition in unser 3D-Drucklabor hat uns nicht nur eine schnellere und kosteneffizientere Fertigungsmethode beschert, sondern uns auch erlaubt, unsere hohen Qualitätsansprüche beizubehalten, indem wir einen größeren Teil des Prozesses im eigenen Haus erledigen und unter Kontrolle halten. Wir freuen uns darauf, unsere Kapazitäten im 3D-Druck weiter auszudehnen, und sind gespannt darauf, was die Zukunft bringt.“
David Clyde