Wie PMRobotics mit SLS-gedruckten Funktionsteilen und Hilfsmitteln die Fertigung von Drohnen optimiert
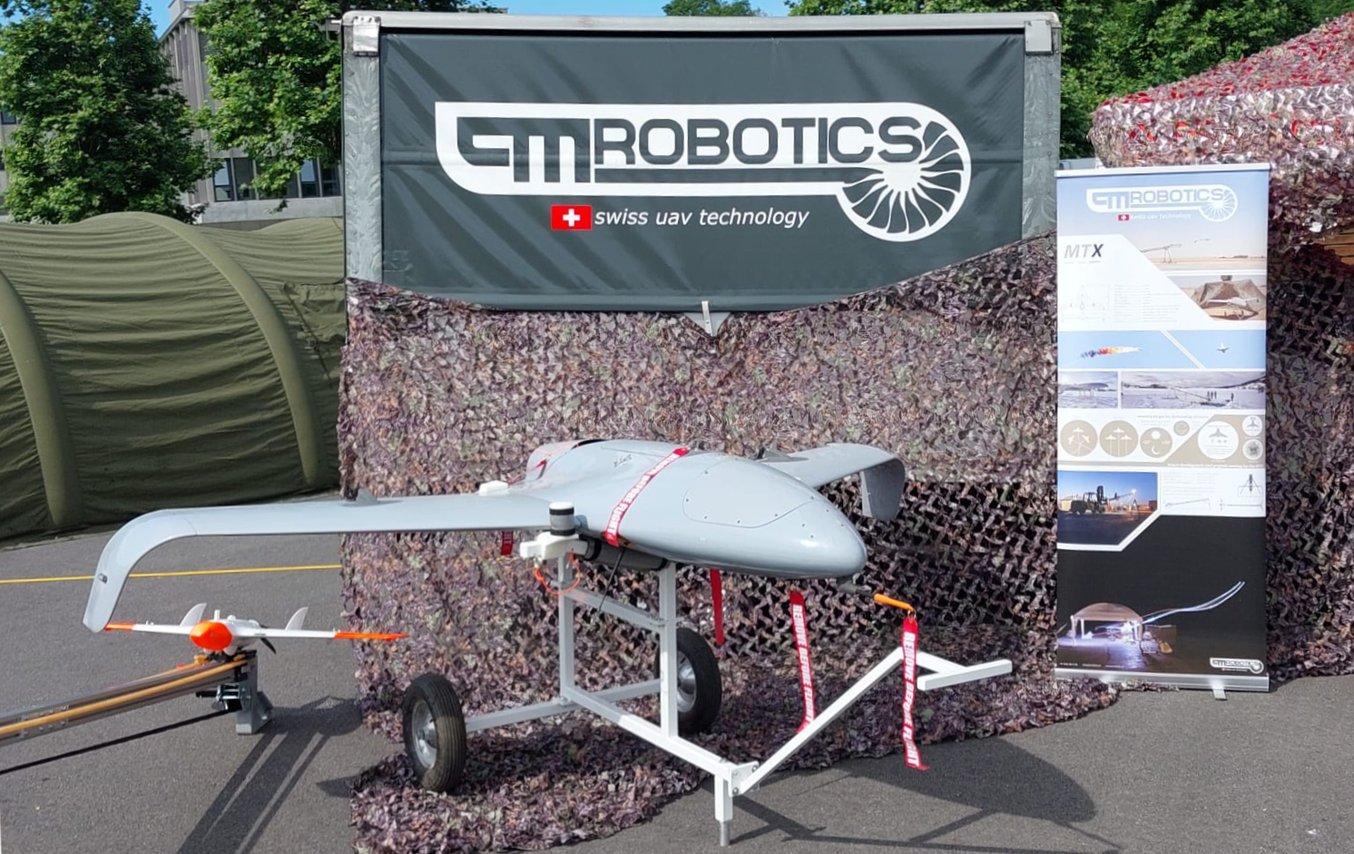
Die PMRobotics GmbH ist ein Hersteller hochprofessioneller unbemannter Luftfahrtsysteme, bestehend aus Drohnen, Datenlinks, Bodenstationen und Startvorrichtungen. Um größtmögliche Qualität, schnelle Personalisierung und umfassenden Service bieten zu können, deckt er alle Prozesse aus einer Hand ab: Von der Entwicklung über Fertigung und Montage bis hin zum Flugbetrieb.
Die ständige Herausforderung für das 2013 in Turbenthal bei Zürich gegründete Unternehmen ist das hohe Schweizer Lohnniveau. Um seine umfassende Kundenbetreuung gewinnbringend abbilden zu können, minimiert PMRobotics manuelle Arbeitsschritte durch Automatisierung und modernste Ausstattung. Als essenzielle Ergänzung seiner CNC-Fräsen und Schneidroboter setzte das Unternehmen von Beginn an auf 3D-Druck, um Prototypen, Endanwendungen und Betriebsmittel zu fertigen. So kann das Team heute nicht nur vollautonome, kundenindividuelle Zieldarstellungsdrohnen beispielsweise für Funktionstests von Luftabwehrsystemen fertigen, sondern auch Spezialaufträge aus anderen Bereichen wie der Automobilbranche bearbeiten – und das mit nur sechs Mitarbeitenden.
Wir haben mit Mitgründer und Konstrukteur Niklas Hagen darüber gesprochen, wie PMRobotics mit 3D-Druck die Entwicklungszeit seiner neuen Drohne um 9 Monate auf zwei Jahre verkürzte, Betriebsmittel für Maschinen fertigt und Klassiker des Motorsports aus dem Leistungsloch holt.
Organisches Wachstum für langfristigen Erfolg
Besonders stolz ist Niklas Hagen auf die Unabhängigkeit, mit der sein Team Drohnen herstellt. Denn beginnend von der Elektronikplatine über Autopilot, Aerodynamik und Software bis zum Chassis sind „wirklich 100 Prozent inhouse entwickelt, konzipiert und auch produziert”, so Hagen.
Dass die PMRobotics GmbH diese Bandbreite an Aufgaben mit ihrer kleinen Zahl von sechs Mitarbeitern umsetzen kann, verdankt sie ihrem seit Beginn an bestehenden Fokus auf organisches Wachstum, dessen Richtung durch die hohen Arbeitskosten in der Schweiz klar vorgegeben ist: Ausbau der Produktivität durch maschinelle Unterstützung. Durch geringe Fluktuation und kontinuierliche Investitionen in seinen Maschinenpark baute PMRobotics das Fachwissen sowie die betriebsinternen Fertigungskapazitäten auf, mit denen es heute flexibel und effizient vielfältige Produktionen durchführt.
„Das Hauptthema für uns ist immer: Arbeitsstunden sparen. Ich entscheide mich immer für eine automatisierte Variante, um nicht Personal einstellen zu müssen, das man dann vielleicht nach dem Auftrag nicht mehr braucht”, erklärt Hagen.
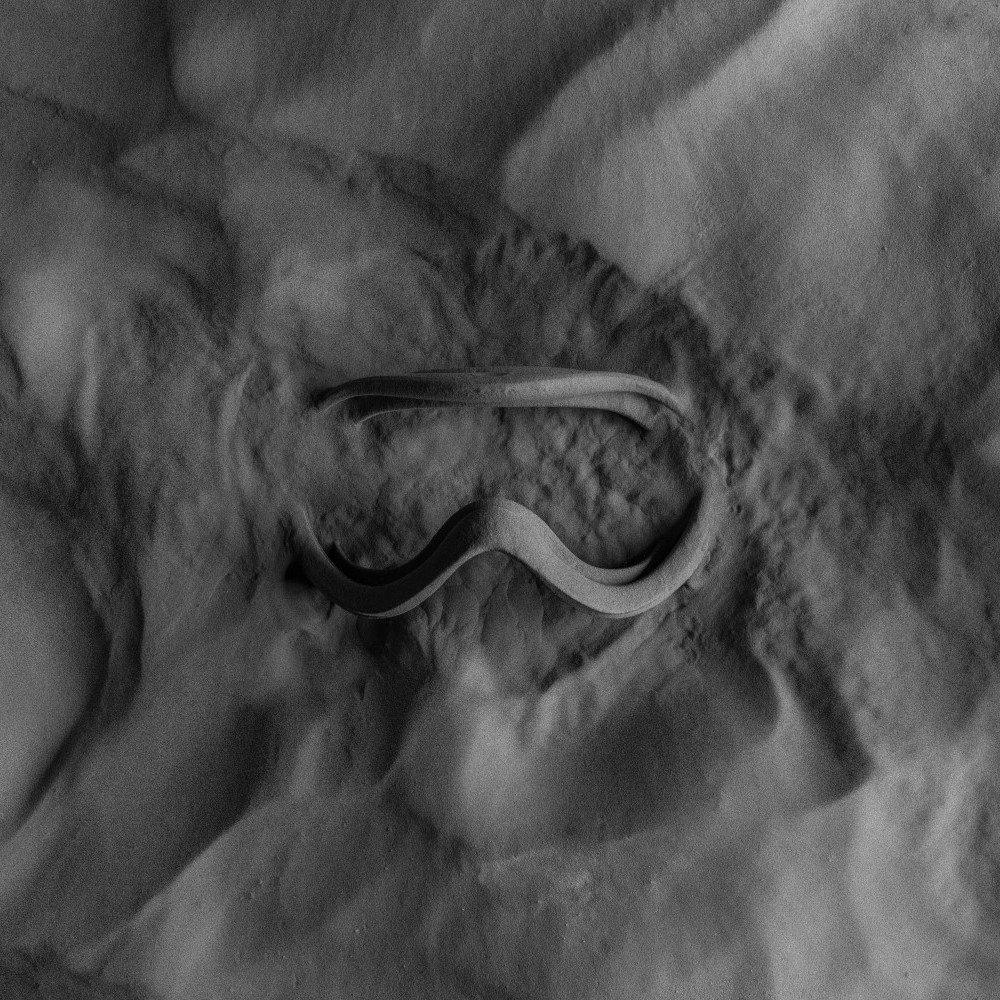
Leitfaden zum 3D-Druck mit selektivem Lasersintern (SLS)
In diesem umfangreichen Leitfaden werden wir das selektive Lasersintern und die verschiedenen, auf dem Markt erhältlichen, Systeme und Materialien sowie den Arbeitsablauf mit SLS-Druckern und die verschiedenen Anwendungen abdecken.
Als SLS erschwinglich wurde – Gesteigerte Effizienz durch betriebsintern gedruckte Prototypen, Betriebsmittel und Endanwendungen
Vor der Implementation von 3D-Druck musste Hagens Team die vielfältigen Anpassungen, die bei der vollständig internen Fertigung anfallen, noch umständlich per Hand konstruieren, was zu hohen Entwicklungs- und Produktionszeiten sowie Personalkosten führte. „Früher haben wir beispielsweise für unsere CNC-Fräse kleine, komplexe Halterungskonstruktionen aus Holz-Frästeilen und Glasfaser zusammengeklebt. Wir haben unglaublich viele solcher Baugruppen, die man montieren musste oder wo man Halter aus kleinen Teilen zusammenkleben musste”, erinnert er sich.
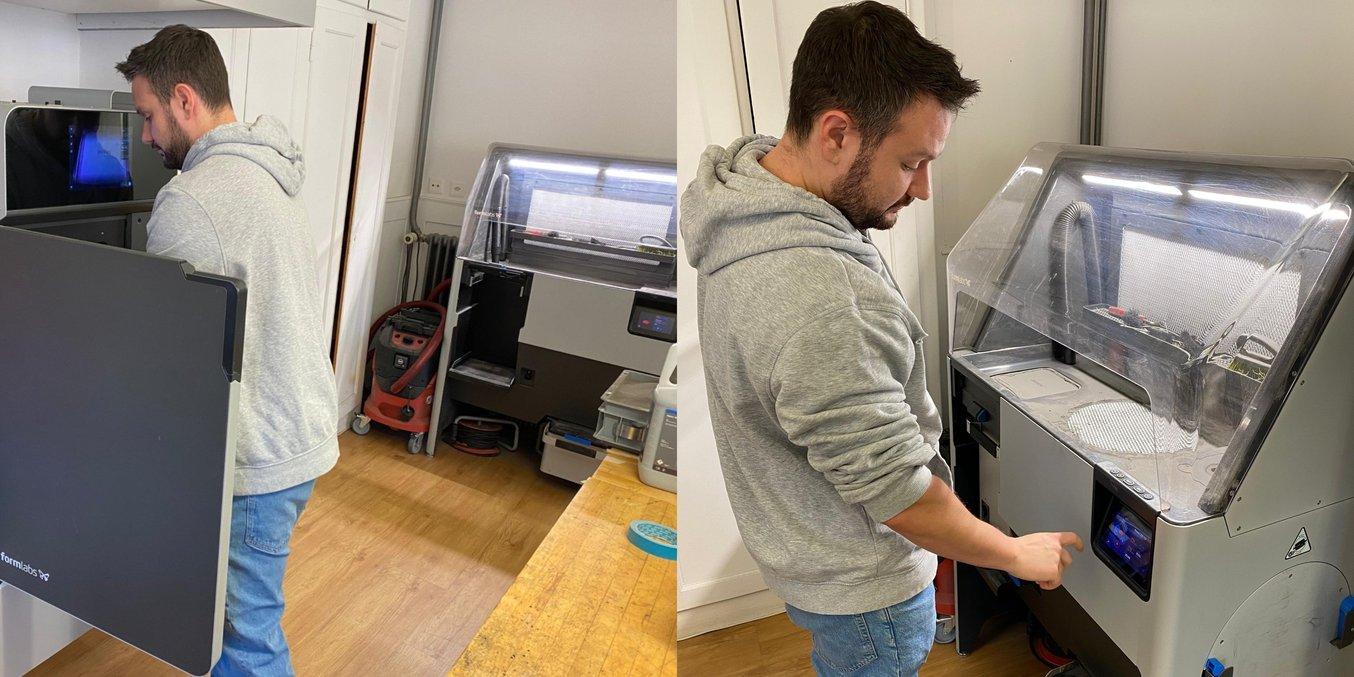
Betriebsinterne Fertigung von individuellen Halterungen und Betriebsmitteln zur Optimierung der Produktion bei PMRobotics mit dem Fuse 1+ 30W und Fuse Sift.
Schnell nach der Gründung wurde PMRobotics’ Team daher klar, dass sein Anspruch auf selbstkontrollierte, betriebsinterne Entwicklung und Fertigung ohne eine Veränderung nicht realisierbar ist. Die Lösung fand es im 3D-Druck, mit dem es einen Großteil dieser Arbeiten automatisierte, Arbeitskosten reduzierte und die Produktentwicklung durch (funktionale) Prototypen beschleunigte.
Dass wir extrem schnell Prototypen und kleine Funktionsteile mit vielen Details herstellen können, hat uns am 3D-Druck fasziniert. Bastelarbeiten für Prototypen und Halterungen konnten wir uns mit dem 3D-Druck komplett sparen. Für uns ist 3D-Druck absolut nicht mehr wegzudenken.
Niklas Hagen, Mitgründer & Konstrukteur, PMRobotics GmbH
Zunächst stand PMRobotics dafür nur ein einfacher FDM-Drucker (Fused Deposition Modelling) zur Verfügung. Während sich FDM-Druck über die Jahre für ihn kaum weiterentwickelte, ist Hagen vom Reifeprozess des SLS-Druck (Selektives Lasersintern) und den im Branchenvergleich erschwinglichen Anschaffungskosten für Formlabs industriellen SLS-Drucker Fuse 1+ 30W begeistert. „Im Bereich FDM ist in den letzten Jahren nicht mehr wahnsinnig viel passiert, aber die Entwicklung bei SLS war extrem. Als wir vor neun Jahren mit 3D-Druck angefangen haben, war es noch unvorstellbar, dass man einen eigenen SLS-Drucker zu diesem Preis in der Werkstatt stehen hat”, erklärt Niklas Hagen.
Für das Kollegium stand daher außer Frage, dass es die additiven Fertigungskapazitäten von PMRobotics durch den Fuse 1+ 30W ergänzt, als möglich wurde „diese Technologie für dieses kleine Geld zu haben”, sagt Hagen. Nach einem Besuch beim Schweizer Formlabs-Partner 3D-EDU war das Team abschließend „von der Qualität der Drucker, wie alles gemacht ist und wie die Teile aussahen, sehr begeistert”, erinnert er sich. Nicht nur unterstützte 3D-EDU PMRobotics bei der Auswahl und Implementation des optimalen 3D-Druckers, sondern steht dem Unternehmen seitdem mit umfassendem Service zur Seite.
Mit der Implementation von SLS-Druck konnte PMRobotics die Betriebsmittelfertigung deutlich optimieren. Denn „mit dem Fuse [1+ 30W] kamen nochmal so viele Anwendungsmöglichkeiten dazu. Seien es Adapter für Vakuumschläuche [von Vakuumtischen], Haltelehren, Fertigungslehren, Produktionsmittel, Hilfsmittel, Halterungen oder kleine Details an unseren CNC-Maschinen”, sagt Hagen. Darüber hinaus begeistert ihn, dass er mit SLS-3D-Druck heute, im Gegensatz zu FDM, Teile drucken kann, die „nicht offensichtlich nach 3D-Druck aussehen, sondern professionell und sauber”. So setzt sein Team 3D-Druck neben der Herstellung von Hilfsmitteln und Prototypen heute auch problemlos für die Fertigung von Endanwendungen in Kleinserie ein.
Entwicklungszeit im Sturzflug – Entwicklung und Fertigung von Drohnen mit funktionalen SLS-Drucken um 30 % beschleunigen
Wie die Produktivität von PMRobotics durch SLS-Druck gesteigert wurde, wird am Beispiel von dessen aktueller Zieldarstellungsdrohne deutlich, deren Entwicklung besonders schnell funktionieren musste, da diese von einem Kunden für einen Einsatz eingeplant war. Das Team stand dadurch in der letzten Entwicklungsphase unter starkem Zeitdruck, insbesondere weil die Vielzahl der Bauteile perfekt aufeinander abgestimmt, teilweise parallel und in mehreren Iterationen entwickelt werden mussten.
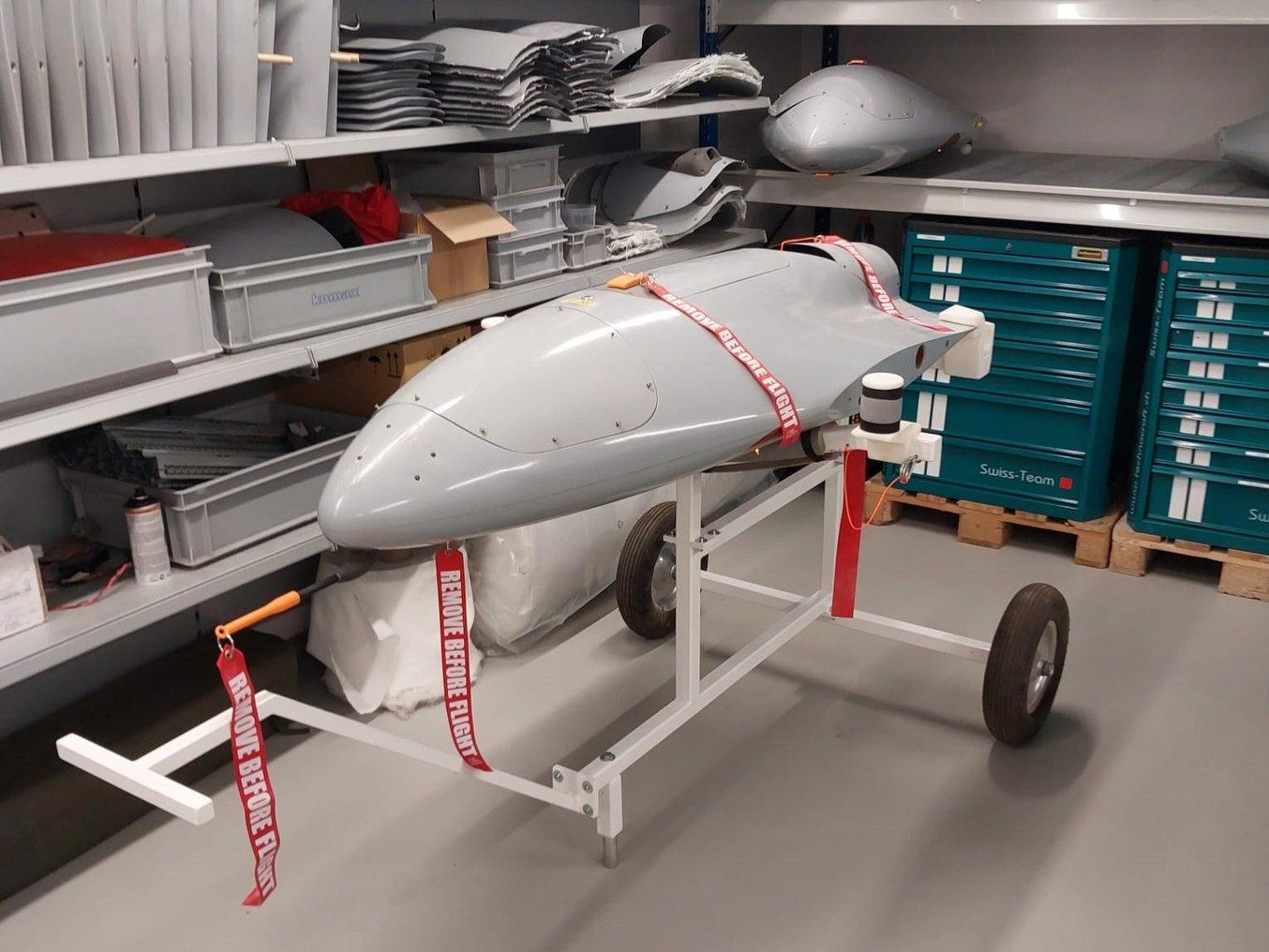
Mit betriebsinternem 3D-Druck beschleunigt PMRobotics die Entwicklung seiner Drohnen um 30 %.
Früher verlangsamten diese Iterationen die Entwicklungen von PMRobotics’ Team deutlich, da es gedruckte Prototypen aus Kunststoff von Dienstleistern bestellte und durchschnittlich vier Tage auf deren Lieferung wartete. Dies erhöhte die Markteinführungszeit seiner Drohnen und bedrohte die Einhaltung der Projektfrist im spezifischen Fall.
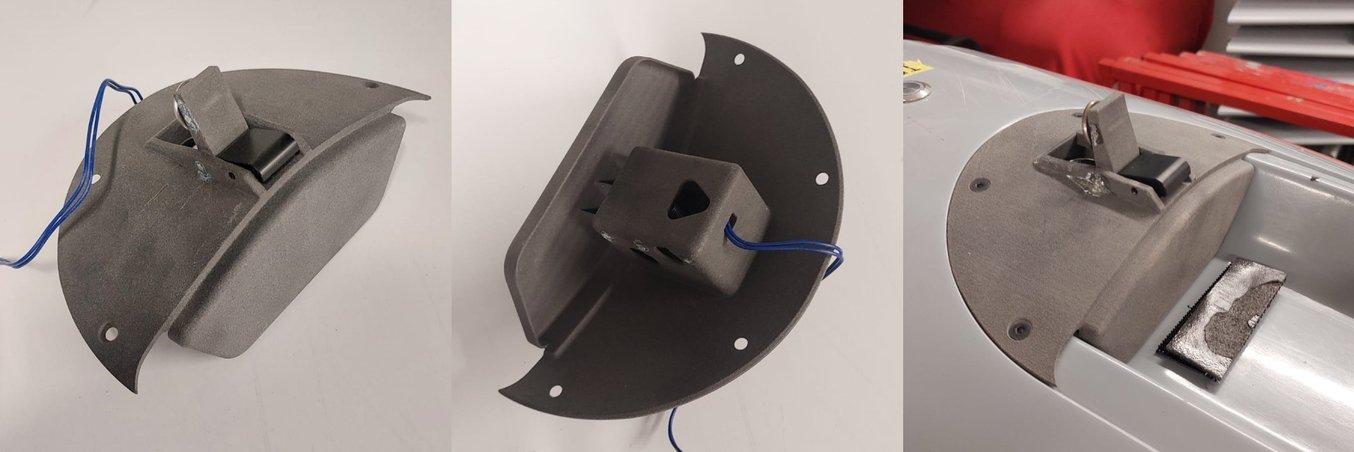
Alle Kunststoff-Bauteile der Drohne von PMRobotics werden mittels SLS-Drucks gefertigt.
Mit dem Fuse 1+ 30W druckte das Team hingegen dank dessen großen Bauraums mehrere voneinander abhängige Teile gleichzeitig über Nacht. So konnten die Mitarbeitenden ihre Arbeitszeit am nächsten Tag effizient für eventuell notwendige konzeptionelle Anpassungen einsetzen und die Entwicklung nahezu unterbrechungsfrei fortsetzen. Durch die Reduktion dienstleisterbedingter Wartezeiten verkürzte PMRobotics die gesamte Entwicklungszeit der Drohne um 30 %.
In einer Woche habe ich die Bauteile drei- bis viermal angepasst. Da ist der Fuse extrem stark. Bis andere das Teil bestellt und geliefert bekommen haben, habe ich es schon perfekt angepasst. Andere brauchen sechs, sieben Wochen dafür und ich bin in einer Woche fertig, dank des Inhouse-Prozesses [...] Insgesamt habe ich mir so ein Dreiviertel Jahr Entwicklungszeit gespart gegenüber externen Lieferungen.
Niklas Hagen, Mitgründer & Konstrukteur, PMRobotics GmbH
Ohne betriebsinternen 3D-Druck | Betriebsinterner 3D-Druck | Zeitersparnis durch 3D-Druck | |
---|---|---|---|
Time-to-Market Drohne | 2 Jahre und 9 Monate | 2 Jahre | 9 Monate bzw. 27 % |
Durchlaufzeit / Teil | 4 Tage | 1 Tag | 3 Tage bzw. 75 % |
Über den iterativen Designprozess hinaus verwendete PMRobotics die SLS-3D-gedruckten Teile für sämtliche Kunststoff-Bauteile in den finalen Drohnen, die es als Kleinserie von acht Stück für den Kunden fertigte. Dank der guten Druck- und Materialqualität des Fuse 1+ 30W und des verwendeten Nylon 12 GF Powder konnte die letzte Entwicklungsphase nahtlos in die Produktionsphase übergehen, in welcher der 3D-Drucker „fast jeden Tag durchgängig gelaufen ist, mit großen Druckjobs und 30 Prozent Füllgrad”, erklärt Hagen.
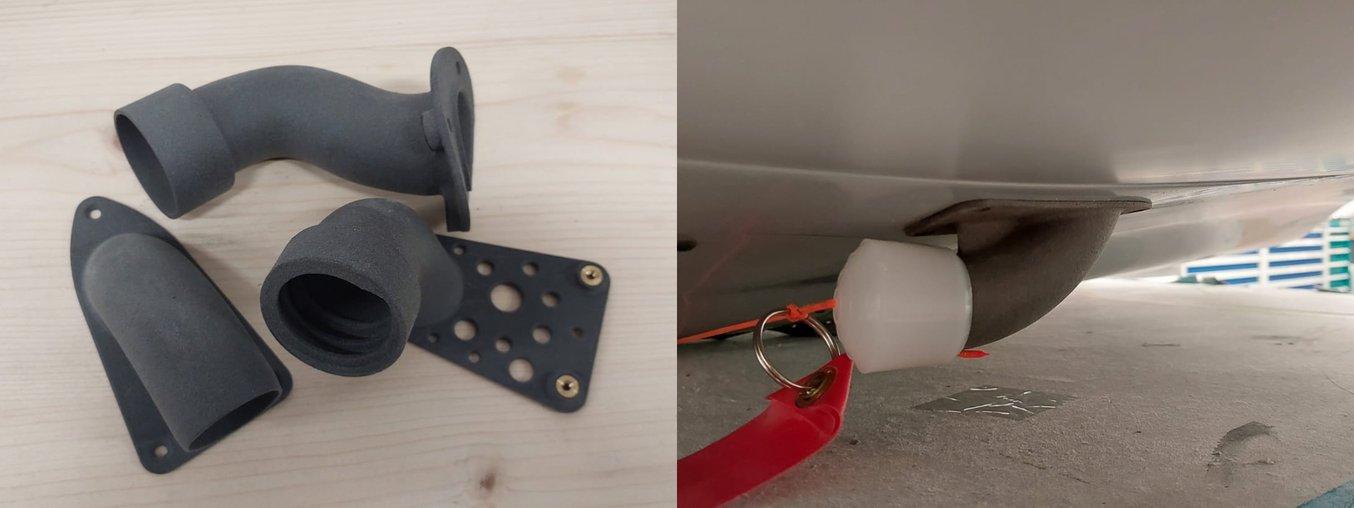
Prototypenteile können mithilfe betriebsinternen 3D-Drucks über Nacht gefertigt und schnell angepasst werden, anstatt mehrere Tage auf deren Lieferung warten zu müssen.
Mithilfe der funktionalen 3D-Drucke verwendet er die Bauteile sofort für Kundeneinsätze und optimiert sie kontinuierlich weiter. Bis alle Designfehler abschließend bereinigt sind und die Bauteile in großer Serie extern gefertigt werden, „verbauen, verkaufen und verwenden wir die Teile aus dem Fuse [1+ 30W] im aktiven Einsatz”, sagt er. Ohne die kontinuierlich aufgebauten Fertigungskapazitäten, weiß Hagen, hätte das Team die Drohnen nicht pünktlich für ihren Kundeneinsatz fertigen können und den Auftrag sowie Reputation verloren.
Allein schon für dieses eine Produkt hat sich der Fuse gelohnt, denn wir hätten das nicht so schnell und professionell fertiggestellt, hätten wir den Fuse [1+ 30W] nicht gekauft. Dass wir unsere CNC-Maschinen und den SLS-Drucker inhouse betreiben, hat uns so überhaupt ermöglicht, diesen Einsatz durchzuführen.
Niklas Hagen, Mitgründer & Konstrukteur, PMRobotics GmbH
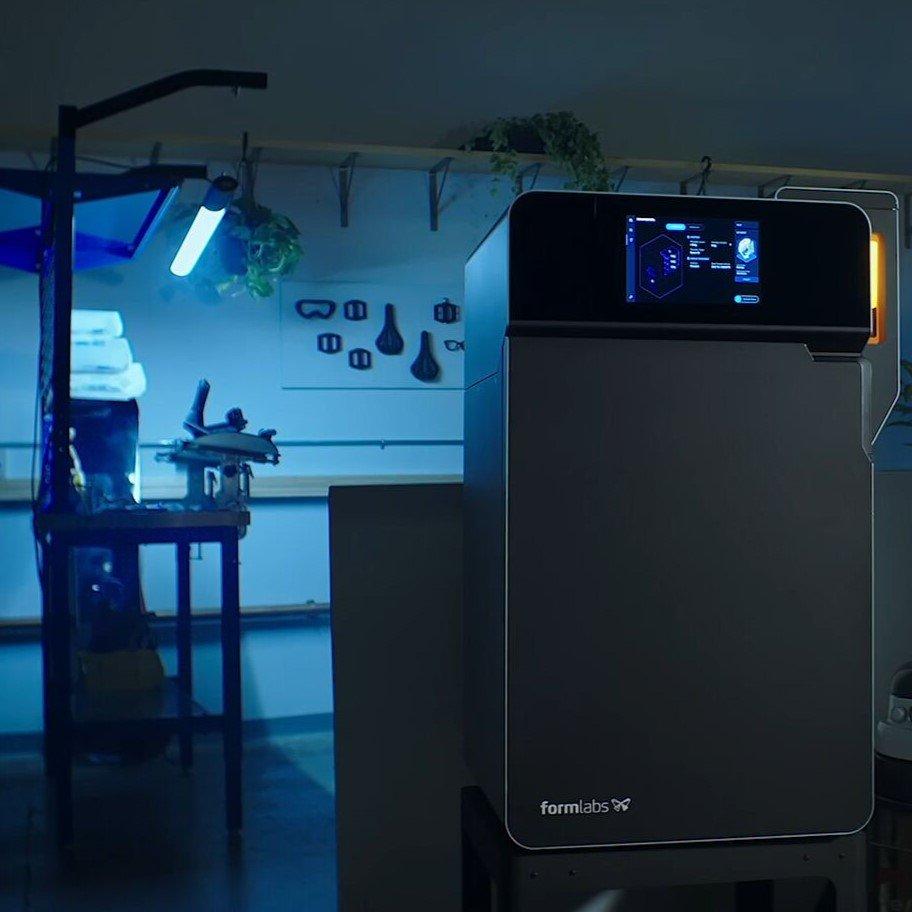
Outsourcing oder betriebsintern: Wann sollte man SLS-3D-Druck in den eigenen Betrieb holen?
In diesem Whitepaper untersuchen wir den Mehrwert von betriebsinternem selektiven Lasersintern (SLS) im Vergleich zum Outsourcing von SLS-Teilen an einen Fertigungsdienstleister.
Alte Liebe rostet nicht — 75 % reduzierte Kosten für Oldtimer-Spezialanfertigungen durch SLS-Druck
Der betriebsinterne SLS-3D-Druck eröffnet PMRobotics neben der Drohnenentwicklung weitere Einnahmequellen durch Konstruktion erschwinglicher kundenindividueller Endanwendungen beispielsweise aus der Automobilbranche.
So wollte zuletzt ein passionierter Hobby-Motorsportler seinem treuen Alpine V6 mit einer Aufrüstung neues Leben einhauchen. Bereits damals fiel der bis 1991 gefertigte Klassiker durch ein spürbares Leistungsloch bei niedrigen Drehzahlen auf, dessen Nachteil für die Rundenzeiten gegenüber moderner Konkurrenz heute noch größer ist. Er richtete sich daher an PMRobotics, um den Motor des Oldtimers durch einen neuen Ansaugkrümmer inklusive Einspritzungen mit modernen Drosselklappen kompatibel zu machen. Doch für ältere Autos sind nur selten passende Ersatzteile oder Aufrüstungen erhältlich. Der Ansaugkrümmer musste vom Team daher selbst konstruiert und gefertigt werden, wobei nicht nur besonders komplexe Geometrien, enge Toleranzen, temperatur- und Benzinbeständigkeit, sondern auch das knappe Hobby-Budget des Kunden beachtet werden mussten.
Ohne den Fuse 1+ 30W hätten die Konstrukteur*innen auf konventionelle Verfahren wie Fräsen oder Guss zurückgreifen müssen, die für sie, aufgrund der komplexen Geometrie des Ansaugkrümmers, zeitintensiv und für den Kunden zu teuer gewesen wären. Durch die Fertigung mithilfe des Fuse 1+ 30W reduzierten sie die Kosten des Ansaugkrümmer um 75 % gegenüber dem Einsatz von Fräsen. Der klassische Ansatz mit Aluminium-Guss wäre im Vergleich zum 3D-Druck sogar „noch viel teurer gewesen, weil man dafür Formen herstellen muss und den aufwendigen Gussprozess sowie Nachbearbeitung hat”, erklärt Hagen und ergänzt: „3D-Druck hat hier ein extrem sauberes Teil und die technisch perfekte Lösung ermöglicht. Diese vielen Versätze und Formunterschiede kann man ohne Kopfschmerzen drucken und der Übergang und die Oberfläche sind perfekt.”
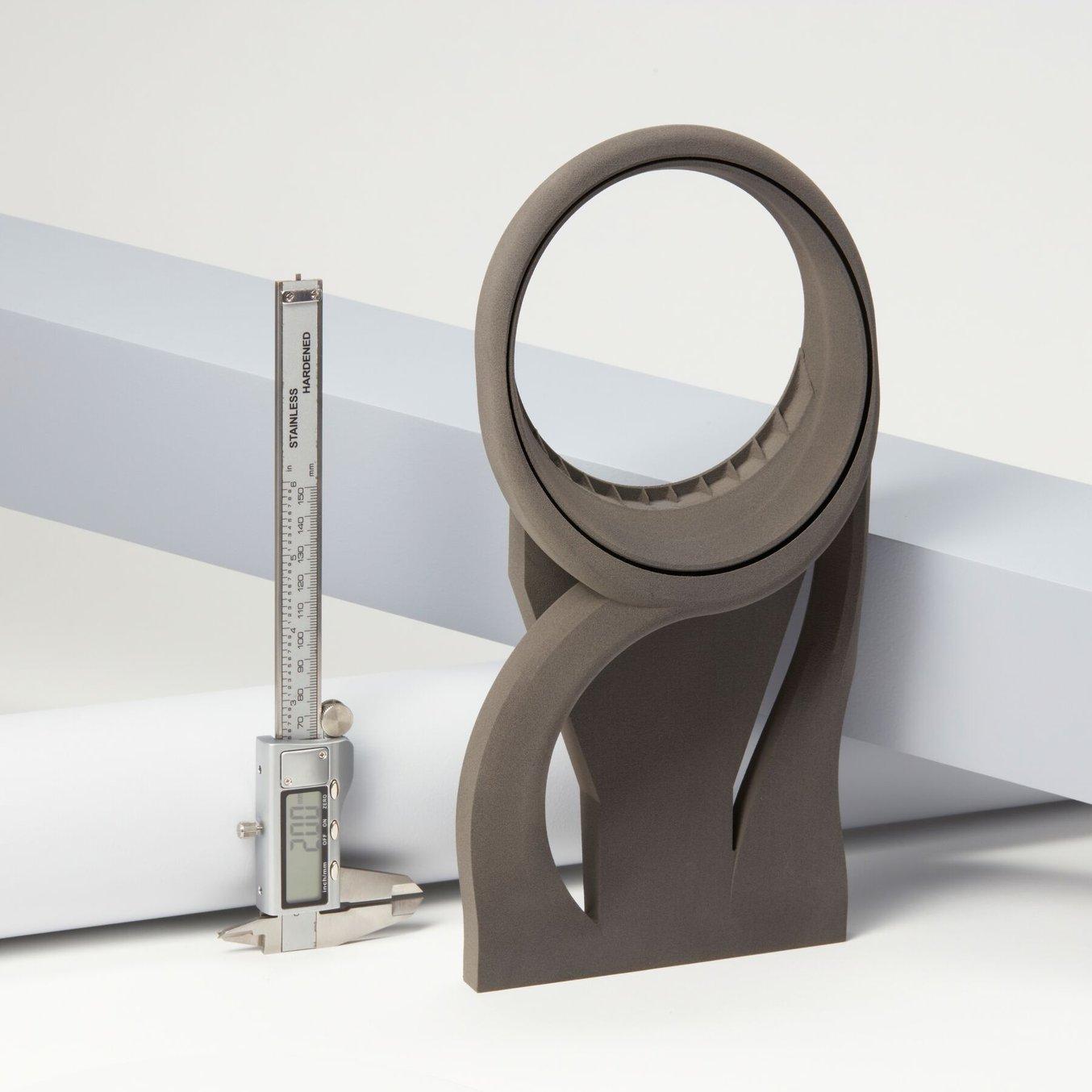
Globaler Automobilzulieferer Brose nutzt SLS 3D-Druck, um Endverbrauchsteile herzustellen
Erfahren Sie, wie Brose, einer der weltweit größten Automobilzulieferer in Familienbesitz, den Einsatz des Fuse 1 und des SLS-3D-Drucks für die Serienfertigung plant.
Als wahre Universallösung hat sich für PMRobotics Nylon 12 GF Powder bewährt, welches es sowohl für seine Drohnenarbeiten oder Montagehilfen nutzt und auch für den Ansaugkrümmer verwendete. Für das weite Spektrum der Anwendungen von „sehr massiven Teilen bis hin zu ganz feinen Konstruktionen” schätzt Hagen die hohe Steifigkeit und Treue zum CAD-Modell von Nylon 12 GF Powder. Durch dessen Vielseitigkeit kann er das Material dauerhaft im Fuse 1+ 30W geladen lassen und so Aufwände für die Reinigung sowie damit verbundene Personalkosten sparen. Bei spezifischen Aufträgen, die andere Druckmaterialien erfordern, wendet er sich an 3D-EDU und dessen Netzwerk für kurzfristige Unterstützung.
Im Fall des Ansaugkrümmers war zusätzlich die gute Temperatur- und Chemiebeständigkeit des Materials gefordert, ohne die sich „das Teil auflösen, in den Motor geraten und unter Umständen einen Motorschaden erzeugen [könnte]”, sagt Hagen. Denn eingesetzt hinter der Kraftstoffeinspritzung ist der Ansaugkrümmer durchgängig Motorenwärme sowie Benzindämpfen ausgesetzt. „Im Gegensatz zu einem FDM-Teil ermöglicht der Fuse [1+ 30W] hier wirklich ein schönes, homogenes Material mit ausreichender Temperaturstabilität. Und es ist zusätzlich noch benzinfest”, erklärt er.
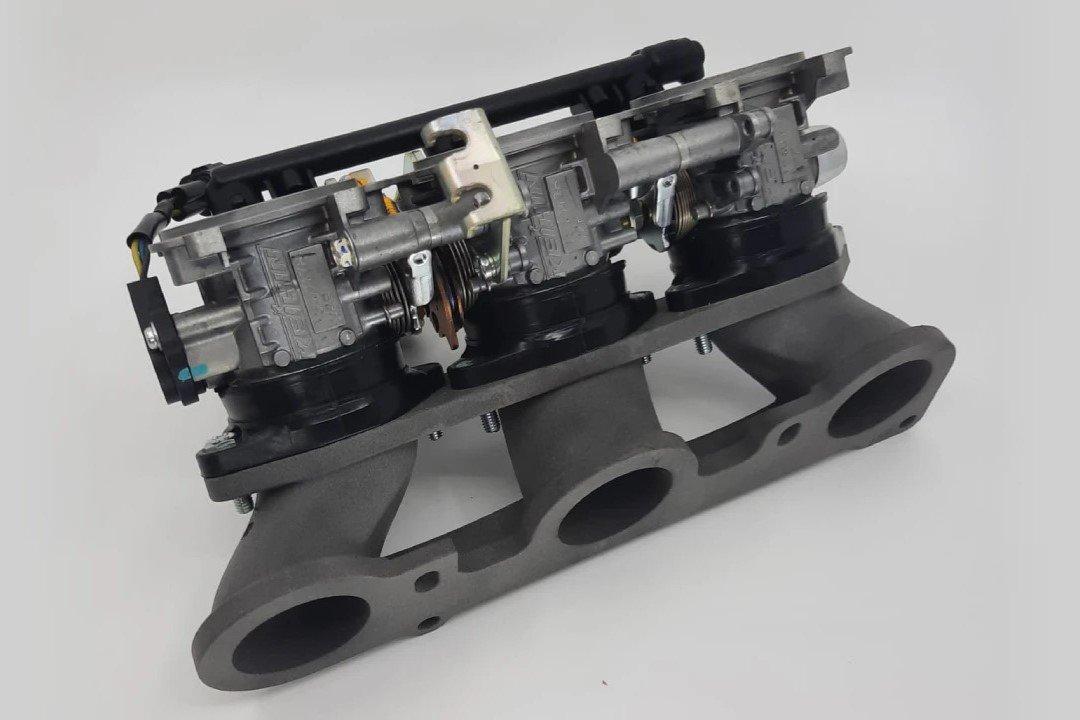
Der 3D-gedruckte Ansaugkrümmer aus Nylon 12 GF hält den hohen Temperaturen und chemischer Beanspruchung im Motor dauerhaft stand.
Durch die geringen Stückkosten des SLS-Drucks kann Hagen Kundenaufträge wie diesen gewinnbringend bearbeiten, bei denen er zumeist Einzelstücke innerhalb enger Budgets fertigen muss. Dies eröffnet PMRobotics zusätzliche Umsatzquellen. „Das war eine ganz klassische, exemplarische Kundenarbeit, ein Spezialauftrag. Da braucht es nur ein Stück. Dafür ist natürlich der Fuse 1[+ 30W] ideal, um das umzusetzen”, so Hagen.
Alles im (Brems)Griff – Mit 3D-gedruckten Betriebsmitteln konventionelle Produktionen optimieren
Mit betriebsinternem SLS-3D-Druck kann Hagens Team nicht nur teure konventionelle oder händische Verfahren für Prototyping und Endandwendungen ersetzen, sondern auch die Nutzung seines Maschinenparks optimieren.
Die Vielzahl von verwendeten Maschinen mit passenden Betriebsmittel und Ersatzteilen auszustatten, ist eine ständige Herausforderung für PMRobotics. Mit dem Fuse 1+ 30W drucken die Mitarbeiter*innen vielfältige Betriebsmittel wie Adapter für Vakuumschläuche, Montagehalter und Lehren für Vakuumtische, CNC-Fräsen und Schneidroboter. So passen sie die Produktionsanlagen flexibel und zügig an die aktuellen Projekte an, etwa individuelle Kundenaufträge, reduzieren Stillstandszeiten und verringern Personalkosten für die langwierige Suche nach minderwertigen Hilfsmitteln.
„Mit dem Fuse [1+ 30W] kann ich sehr, sehr viele tägliche Probleme viel flexibler lösen. Zum Beispiel habe ich selbstgebaute Vakuumtische mit großen Luftschläuchen für unsere KUKA-Roboter. Anstatt stundenlang irgendeinen Schlauchanschluss zu suchen und den dann bestellen zu müssen, kann ich den selbst in CAD entwerfen und habe einen Tag später meinen Schlauchanschluss mit Schnellverschluss, genau so, wie ich will”, erklärt Hagen exemplarisch.
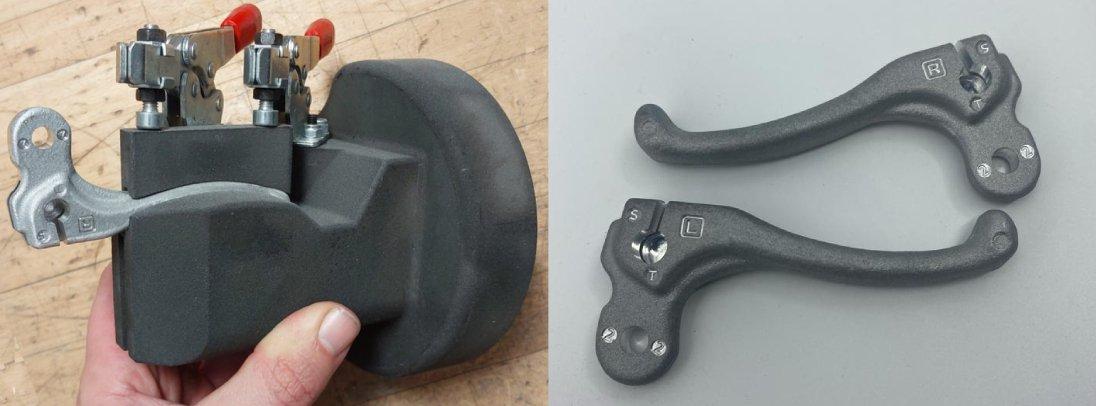
Mit passgenauen 3D-gedruckten Halterungen optimiert PMRobotics die Nutzung seiner CNC-Fräsen für individuelle Kundenaufträge.
Während das Team Halter, Lehren und Bohrschablonen zuvor aufwendig händisch bastelte oder liefern ließ, kann es heute „individuelle Lösung einfach günstiger und vor allem zeitsparender drucken”, die ihm ermöglichen „viel professioneller, schneller und sauberer zu arbeiten”, erklärt Hagen. Durch den 3D-Druck kann es so Personalaufwand und -kosten für die Vorbereitung der Produktion reduzieren und die Fertigungsqualität der teuren Anlagen optimieren.
Insbesondere für schnelle Vorbereitung von Produktionen mit kleinen gedruckten Hilfsmitteln schätzen die Mitarbeitenden die einfache Bedienung und Verlässlichkeit des Fuse 1+ 30W. Durch die gute Bedienoberfläche können sie Drucke schnell und risikoarm vorbereiten, um ihre Arbeitszeit produktiv für Kundenprojekte einzusetzen.
Der Fuse [1+ 30W] ist der einfachste Drucker, den wir haben. Mit FDM habe ich viel mehr Einstellungsaufwand, obwohl der Druck viel weniger komplex ist. Der Fuse [1+ 30W] ist wirklich sicher für den dümmsten anzunehmenden User. Ich kann nichts einstellen, ich kann nichts versauen. Das ist wirklich schon fast wie ein Papierdrucker. Und das schätze ich am meisten am Formlabs-System: dass es einfach funktioniert und stabil ist.
Niklas Hagen, Mitgründer & Konstrukteur, PMRobotics GmbH
Mit betriebsinternem 3D-Druck in zukünftigen Erfolg investieren
Unverständlich ist für Hagen, dass nicht längst mehr produzierende Unternehmen betriebsinternen 3D-Druck nutzen, wenn er die breiten Anwendungsfelder betrachtet, die sein Team mit dem Fuse 1+ 30W bearbeitet. Regelmäßig druckt er Teile im Auftrag eines jungen Automobil-Unternehmens, das Dieselfahrzeuge auf Elektroantrieb umrüstet, und fragt sich: „Warum haben die als innovative Firma keinen einigermaßen gescheiten Drucker?”
Dass auch größere Unternehmen auf die Vorteile von 3D-Druck verzichten, kann sich Hagen nur durch eine kurzsichtige Unternehmensphilosophie erklären. Seiner Meinung nach unterschätzen viele Hersteller noch immer die Chancen der additiven Fertigung aus Angst vor Investitionen, obwohl sie von der Qualität der gedruckten Teile begeistert sind.
Ich empfehle vielen: Ihr müsst mal etwas Geld ausgeben und dann habt ihr einen Drucker, der Plug-and-Play läuft und nicht mühsam ist. Aber ich sehe ganz oft, dass große oder mittelständische Firmen sich vor der Investition scheuen. Stattdessen kaufen sie dann für 300 Euro einen 3D-Drucker, irgendeinen China-Schrott, ehrlich gesagt.
Niklas Hagen, Mitgründer & Konstrukteur, PMRobotics GmbH
Niklas Hagen und PMRobotics werden auch in Zukunft ihrer Philosophie kontinuierlichen Wachstums treu bleiben, konsequent in ihre Produktionsanlagen investieren und ihr Fachwissen vertiefen. Aufgrund dieser Kombination aus Expertise und Ausstattung können sie sich aktuell vor Anfragen zu Drohnen-Entwicklungsprojekten im Bereich Prototyping kaum retten.
Darüber hinaus werden sie ihre eigenen Drohnen insbesondere im Bereich Kleinzieldarstellung weiterentwickeln. Hagen freut sich, dass er und seine Kolleg*innen für diese Projekte auf funktionale Prototypenteile und Betriebsmittel aus dem Fuse 1+ 30W setzen können, und versucht „durch ständige Tests innovativ zu bleiben und zu schauen, was sie alles durch 3D-Druck ersetzen können".