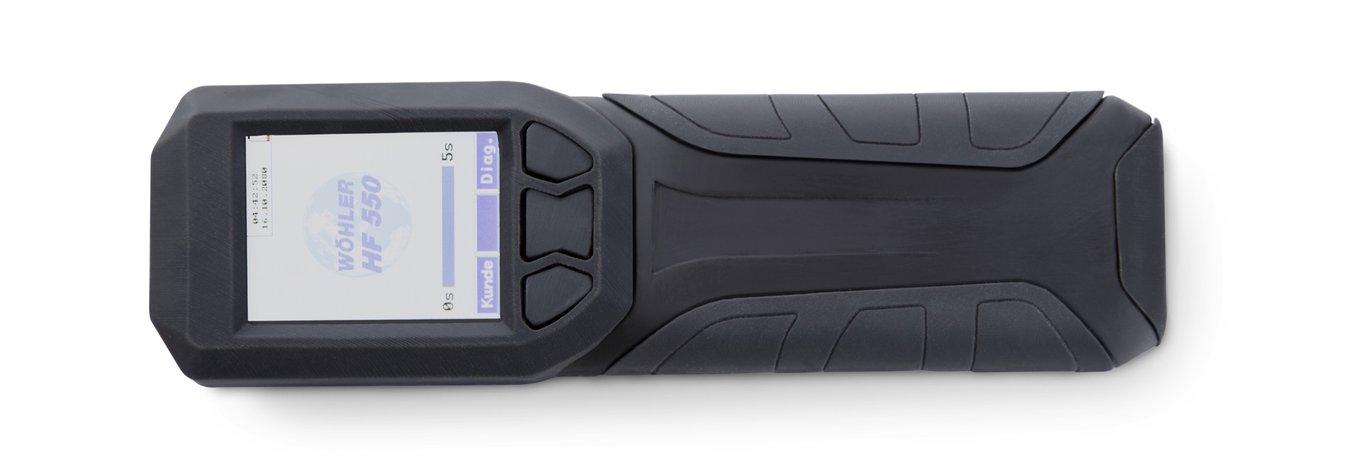
Sebastian Leifels stand vor einer Herausforderung: Er wollte einen optisch identischen, funktionsfähigen Prototypen erstellen, um ein Produkt für den Guss und die endgültige Fertigung vorzubereiten. Als Produktdesigner bei Wöhler, einem in Deutschland ansässigen Hersteller von Mess- und Inspektionstechnik, musste Sebastian einen Prototypen entwerfen, welcher dem Aussehen und der Funktionsweise des Endproduktes entspricht. Er erklärt: „In dieser Phase des Entwurfsprozesses ist es wichtig, Fehler zu vermeiden. Änderungen am finalen Spritzgießwerkzeug sowie am Endprodukt können teuer werden. Die Kosten können im drei- bis fünfstelligen Euro-Bereich liegen.”
Dieses Risiko hatte Sebastian vor Augen, als er den Prototypen für das Holzfeuchtemessgerät Wöhler HF 550 erstellte. Es handelt sich dabei um ein Gerät, das den Feuchtigkeitsgehalt von Feuerholz und Holzprodukten, wie Pellets oder Holzspänen, misst. Dies sind einige Erkenntnisse, die Sebastian Leifels und das Wöhler-Team während des Rapid Prototypings erlangten.
Betriebsinterne Prototypenfertigung führt zu einem besseren finalen Design.
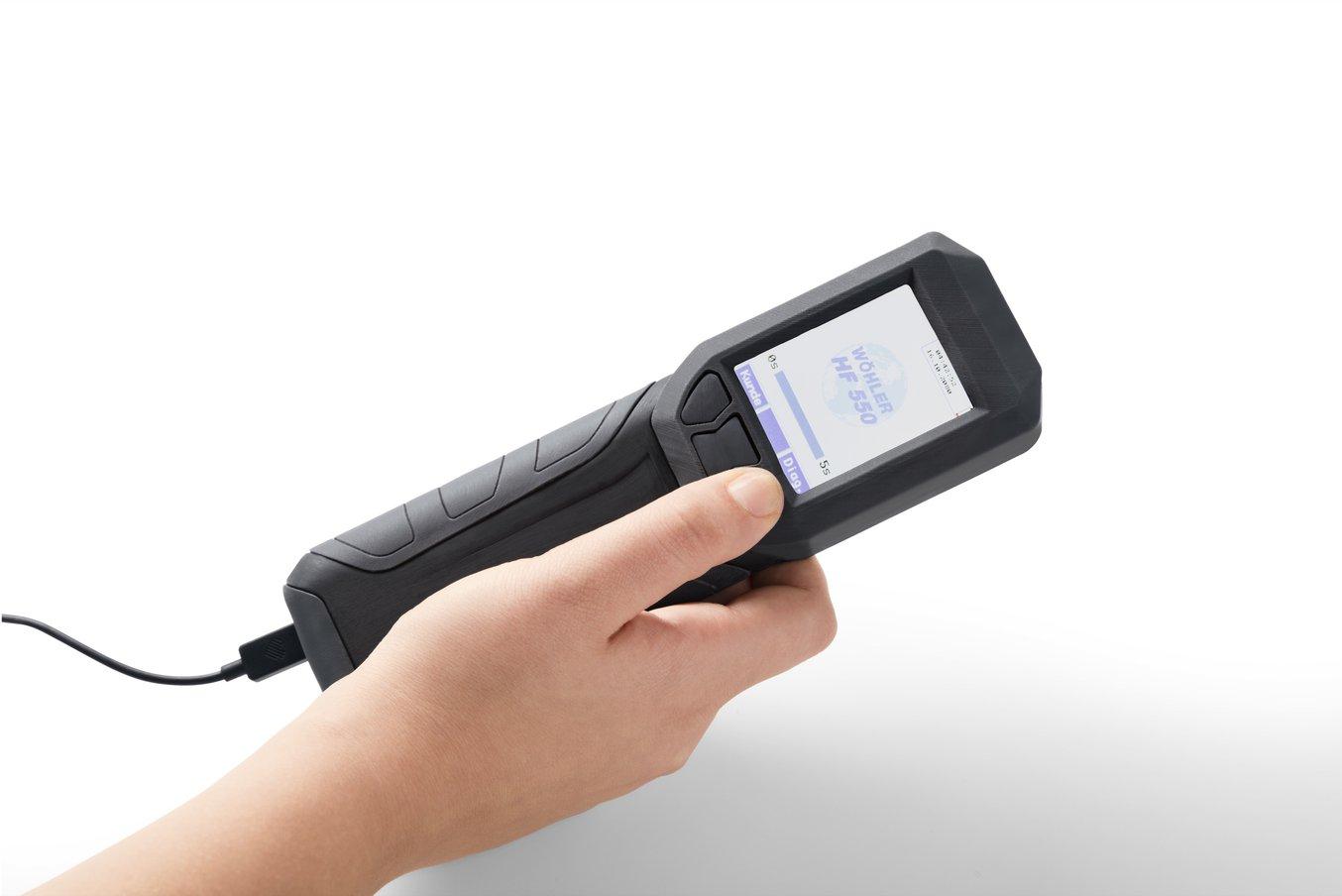
Um seine Deadlines einzuhalten, musste Sebastian Änderungen am Prototyp schnell und einfach umsetzen. Daher entschied er sich für den Einsatz des Desktop-3D-Drucks. Seine Wahl fiel auf den Formlabs 3D-Drucker, der mithilfe von Stereolithografie (SLA) innerhalb weniger Stunden präzise Modelle erstellt. Er erinnert sich: „Der Prozess der Prototypenfertigung konnte von mehreren Tagen auf wenige Stunden reduziert werden. Mit der Einführung des Druckers zum Design von Teilen des Gehäuses haben wir mehrere Wochen im gesamten Entwicklungsprozess gespart.”
Die betriebsinterne Herstellung ermöglichte dem Wöhler-Team mehr Kontrolle und Geschwindigkeit im Designprozess. Sebastian dazu: „Wenn nötig, haben wir den Drucker in der Entwicklungsphase mehrere Wochen lang Tag und Nacht laufen lassen”. Durch die größere Anzahl an Prototypen konnte das Team mehrere Ideen testen, was zu einem besseren Endprodukt führte.
Bei der Wahl der Werkzeuge bestimmt der Preis, nicht die Qualität.
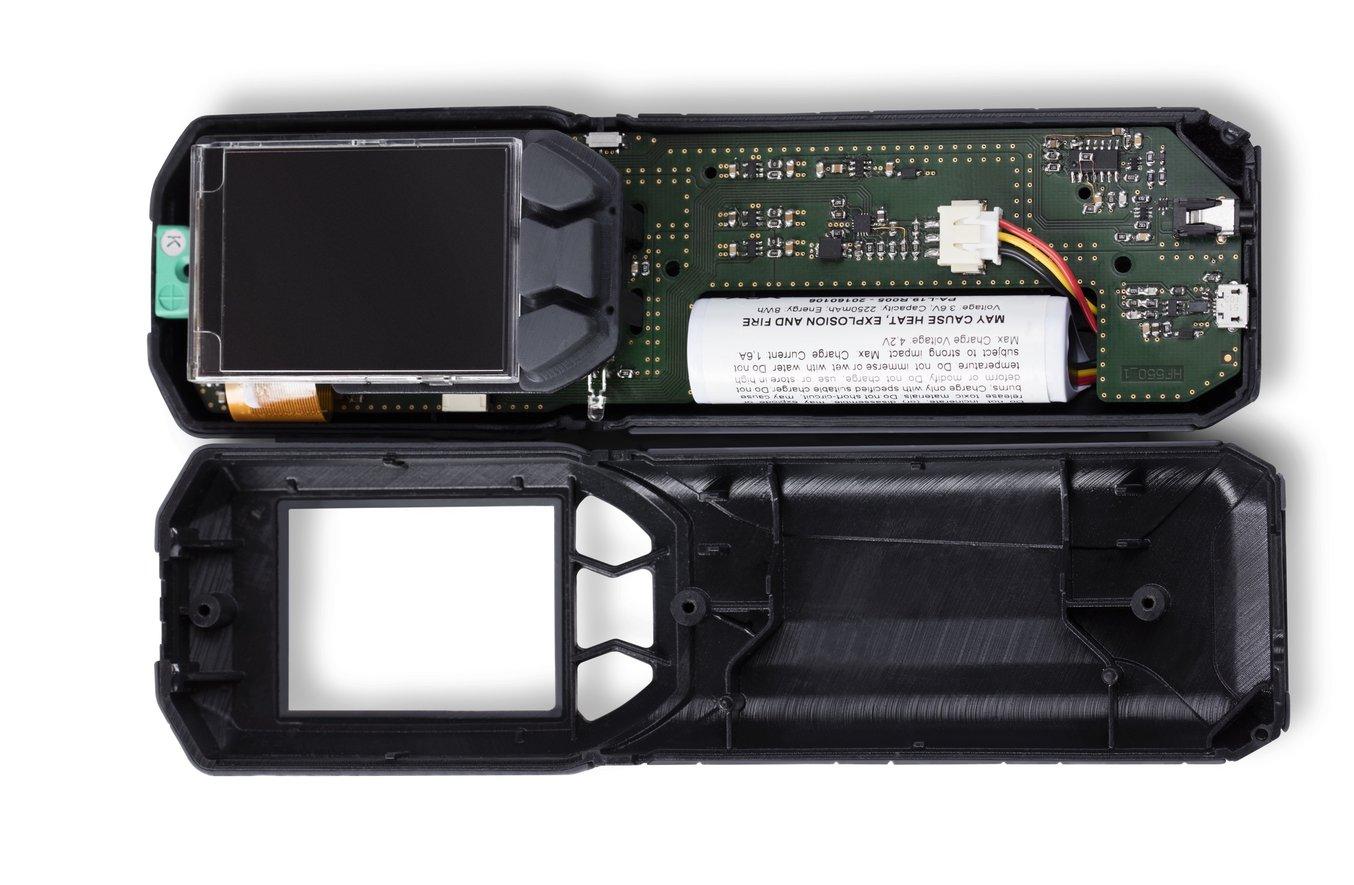
Am Anfang des Designprozesses verwendete Sebastian Leifels einen Desktop 3D-Drucker, der Schmelzschichtung (FDM – Fused Deposition Modeling) nutzte und mehr als das Vierfache des Formlabs 3D-Druckers kostete. Trotzdem war der FDM-Drucker nicht dazu in der Lage, exakte Details herzustellen. „Der Drucker ermöglichte eine höhere Präzision,” erklärt Sebastian. „Unsere Vorgängermaschine hatte eine minimale Schichtdicke von 0,178 mm. Der Formlabs 3D-Drucker hat eine minimale Schichtdicke von 0,025 mm.” Er führt aus: „Selbst wenn dieselbe Schichtdicke gewählt wird, erzeugt der Formlabs Drucker stets glattere Ergebnisse.”
Die Kombination verschiedener Materialien verbessert Anwendertests.
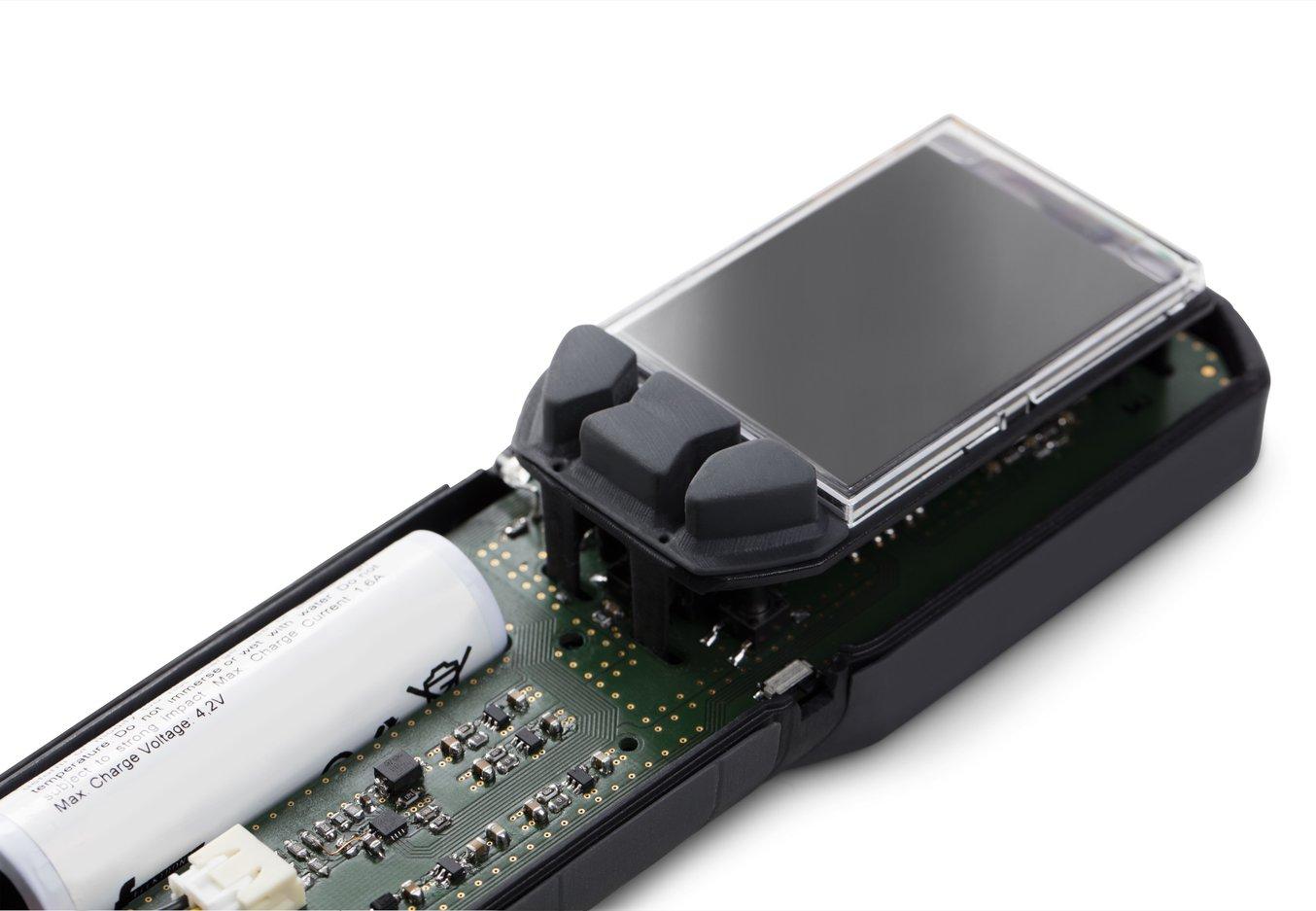
Um den Prototypen des Holzfeuchtemessgeräts zu erstellen, musste Sebastian mehrere verschiedene Materialien verwenden. Der vorherige FDM 3D-Drucker des Teams konnte keine flexiblen Materialien drucken, sodass ein komplexer Prozess notwendig war. Zunächst entwarfen sie ein Test-Gussmodell und druckten es mithilfe des FDM-Druckers. Dann folgte eine aufwendige Nachbearbeitung, um die Oberfläche zu glätten. Abschließend wurde das Modell mit einem Gummigemisch ausgegossen. Sebastian erinnert sich: „Dies war ein zeitintensiver Prozess, und wir konnten dennoch keine feinen Details erreichen. Nun haben wir unseren Prozess vereinfacht, indem wir Detailteile direkt drucken.”
Sebastian benutzte Black Resin für das Gehäuse und Flexible Resin für das Bedienfeld. Die Tasten müssen sich eindrücken lassen, wenn der Nutzer sie betätigt. Daher müssen die Knopf-Wände sehr dünn und dennoch widerstandsfähig sein. Er sagt, dass Flexible Resin es dem Team erlaubte, „eine Vielzahl von Tests an den Prototypen durchzuführen, ohne dass es zu einer Beschädigung oder funktionalen Einschränkung der Teile kam.”
Durch den betriebsinternen 3D-Druck haben wir den Vorteil, die Teile für jedes Gerät vor der Serienproduktion testen zu können. Das Risiko, das Gerät später überarbeiten zu müssen, ist gering.
Sebastian und sein Team benutzen den Formlabs 3D-Druckernun für alle Prototypen bei Wöhler: „Durch den betriebsinternen 3D-Druck haben wir den Vorteil, die Teile für jedes Gerät vor der Serienproduktion testen zu können. Das Risiko, das Gerät später überarbeiten zu müssen, ist gering." Die Verwendung einer einzigen Maschine, die verschiedene Materialien herstellen kann, eröffnet dem Wöhler-Team neue Möglichkeiten für die Prototypenfertigung. Obwohl betriebsinterner 3D-Druck Zeit und Geld spart, liegt der größte Vorteil darin, dass bessere Endprodukte erstellt werden können.