Wie das Unternehmen XSPECTER SLA und SLS-gedruckten Endbauteile in ihrer Produktion von Outdoor Kamerastativen kombiniert
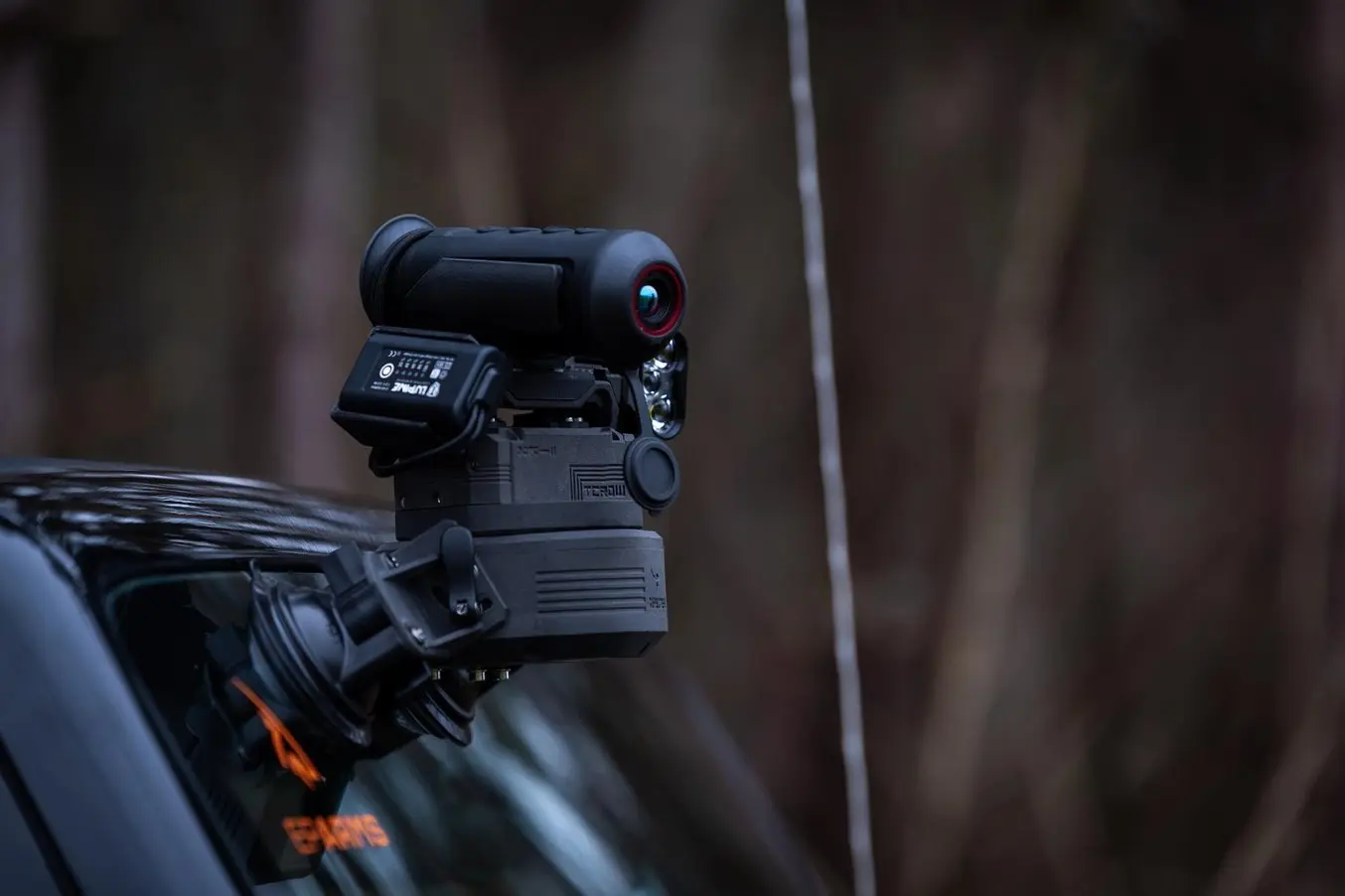
Mit einer innovativen Idee und der gewissen Motivation, haben es schon viele Entrepreneur:inne geschafft Marktlücken zu füllen. So kam auch Matthias Mähler darauf den ersten Prototypen für seine Idee eines speziellen Kamerastativs für Nachtsicht- und Wärmebildhandgeräte zu bauen, nachdem er nichts dergleichen auf dem Markt fand.
Hier bestand die Herausforderung darin ein komplexes Produktdesign umzusetzen, welches bei einem Spritzgussverfahren mit einer anfänglichen Investition von über 100.000 € verbunden gewesen wäre. Dies wäre ohne vorheriges Wissen, wie das Produkt am Markt angenommen wird sehr riskant für das von Mähler gegründete Start-up XSPECTER gewesen. Durch den Einsatz von 3D-Druckverfahren in der Entwicklung und später zur Produktion des Stativs, konnte eine solch hohe Investition umgangen werden. Mittlerweile stellt seine Firma XSPECTER ihr erstes fertig entwickeltes Kamerastativ T-Crow XRII in hausinternen Produktion her und vertreibt es erfolgreich über einen Exklusivpartner.
Mähler hat uns im Interview erzählt, wie man mit einer Kombination aus unterschiedlichen 3D-Drucktechnologien ein fertiges Produkt herstellen kann und wieso er sich für diese Verfahren entschieden hat.
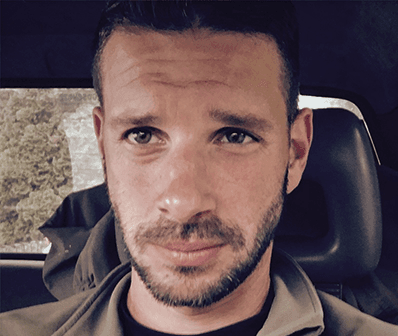
SLA- und SLS-gedruckte Endbauteile für die Produktion von Outdoor-Kamerastativen
Erfahren Sie von Jungunternehmer Matthias Mähler, wie sein Unternehmen XSPECTER SLA- und SLS-gedruckte Endbauteile in der Produktion von Outdoor-Kamerastativen für Jagd- und Bootssport sowie der Security-Branche einsetzt.
360 Grad steuerbares Kamerastativ
Nachtsicht- und Wärmebildhandgeräte gehören zur Standardausrüstung von Jäger:innen, Bootsfahrer:innen und in der Security Branche. Das Problem: die Geräte funktionieren nicht durch Glas- und Fensterscheiben hindurch. Bei nächtlicher Fahrt im Auto heißt das also für den/die Fahrer:in sein/ihr Gerät händisch aus dem offenen Fenster halten zu müssen oder immer wieder auszusteigen.
Freizeitjäger und Unternehmer Matthias Mähler hat daraufhin eine passende Lösung für die Montage seiner Geräte an das Äußere seines Fahrzeugs gesucht.
Nach seiner Feststellung, dass es keine passende Halterung beziehungsweise kein passendes Stativ auf dem Markt gibt, hat er die Sache selbst in die Hand genommen. Er begann mit dem Prototypenbau eines stabilisierenden und steuerbaren Stativs für Nachtsicht- und Wärmebildgeräte, welches durch Saug- oder Magnetfüße an das Dach oder die Fenstercheibe eines Autos montiert werden kann.
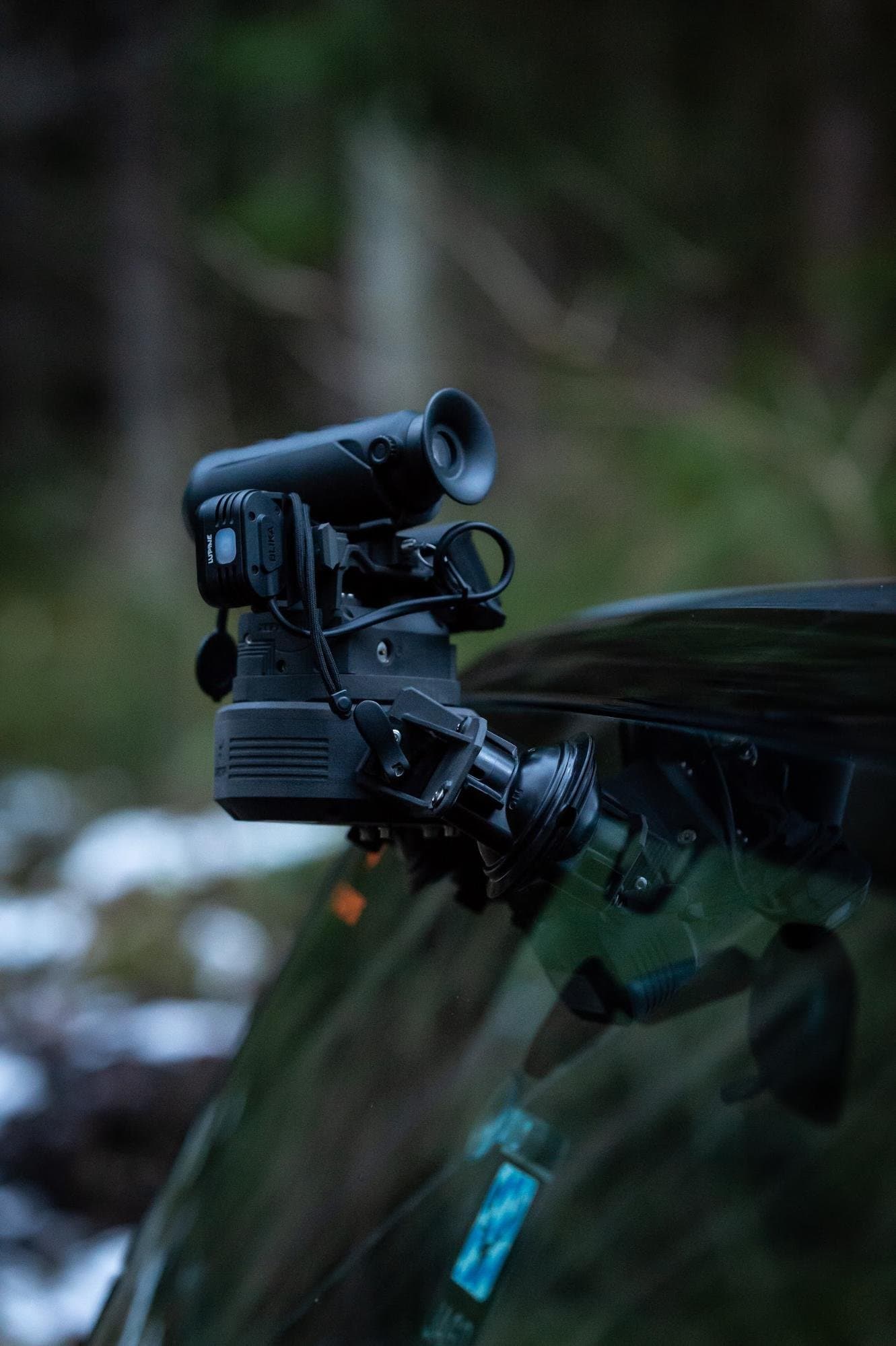
Der T-Crow XRII mit verschiedenen Kameras an der Autoscheibe (links) und auf dem Autodach (rechts)
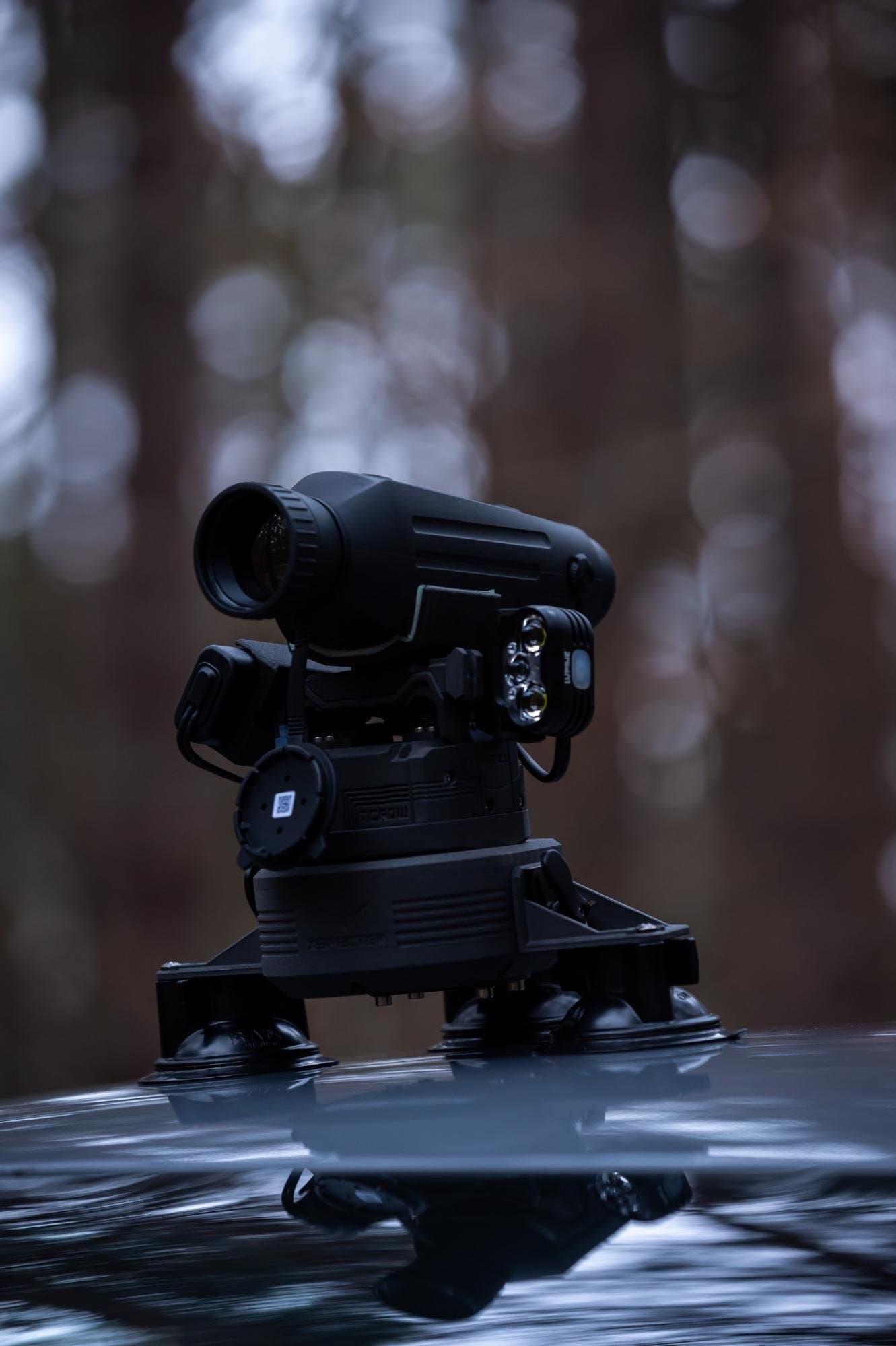
Mit einer integrierten 360° Rotation und einem zusätzlichen Neigungsbereich von 55° ermöglicht das sogenannte T-Crow Stativ von XSPECTER das Erfassen von Lebewesen und Hindernissen aus dem komfortablen Inneren eines Fahrzeugs.
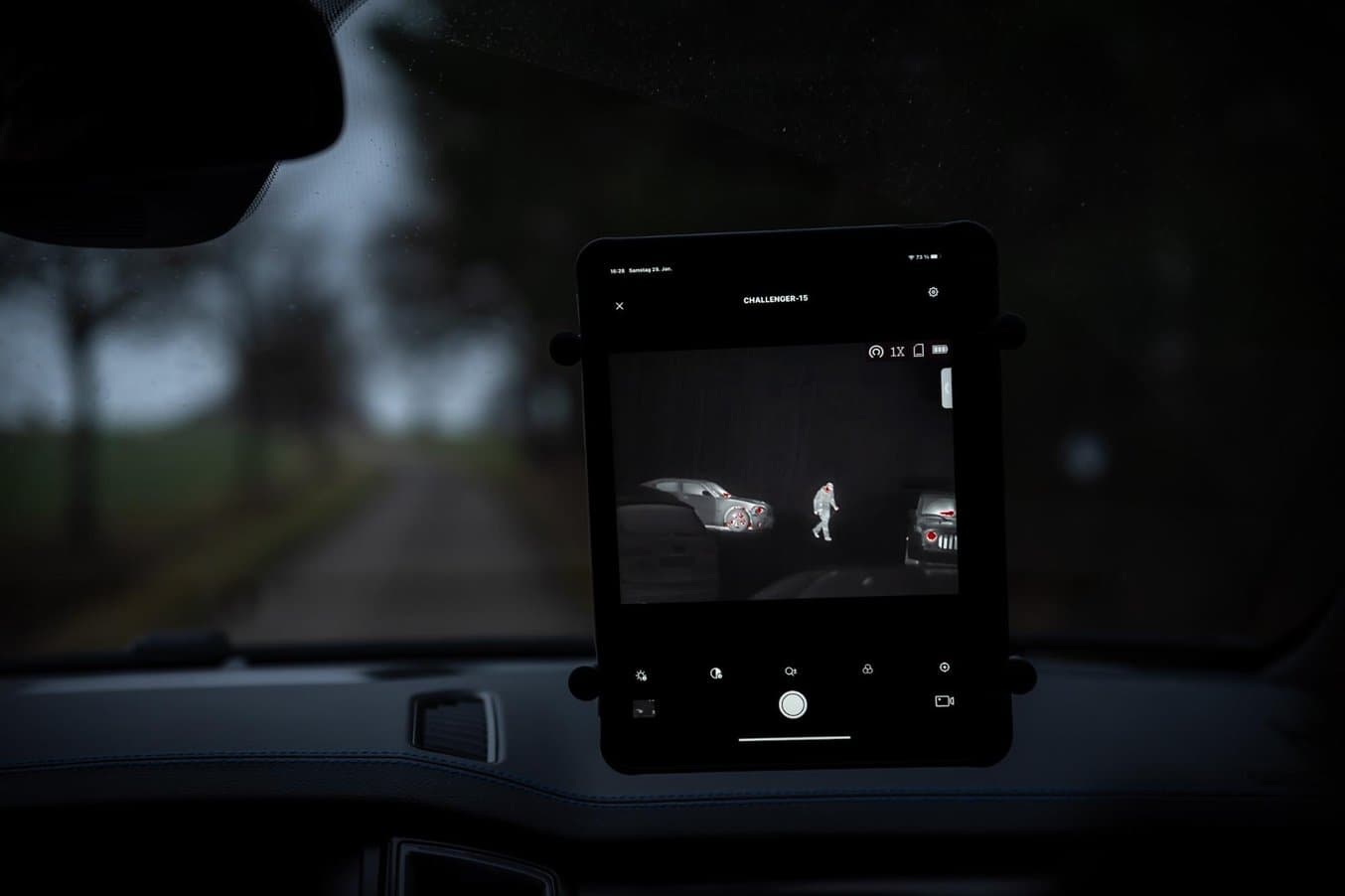
Das Wärmebild auf einem Tablet Bildschirm im Inneren des Autos
Vom Prototypen in die Serienfertigung
“Bei mir ist 3D-Druck nur dadurch nachhaltig in meine Fertigungslinie integriert worden, da ich den Prototypen im 3D-Druckverfahren hergestellt habe. Das hat so gut funktioniert, dass wir letztendlich das ganze Produkt mit verschiedenen 3D-Drucktechnologien entworfen haben und bis heute so produzieren”, erzählt Mähler.
Zunächst hat Mähler mehrere Prototypen des Stativs in Zusammenarbeit mit 3D-Druck Dienstleistern auf FDM Druckern iteriert. Nachdem der grobe Produktentwurf stand, ist er mit Formlabs Partner AMPrO 3D in Kontakt getreten, um sich beraten zu lassen welche 3D-Drucktechnologien und Materialien für die erste Serienproduktion geeignet wären.
“Wie haben das Ganze dann an das SLS-Verfahren angepasst, weil man durch die Detailgenauigkeit und ohne Stützstrukturen natürlich noch viel mehr Möglichkeiten im SLS-Druck hat. Wir sind quasi nahtlos vom Prototypen in die Serienproduktion übergegangen.”
Matthias Mähler
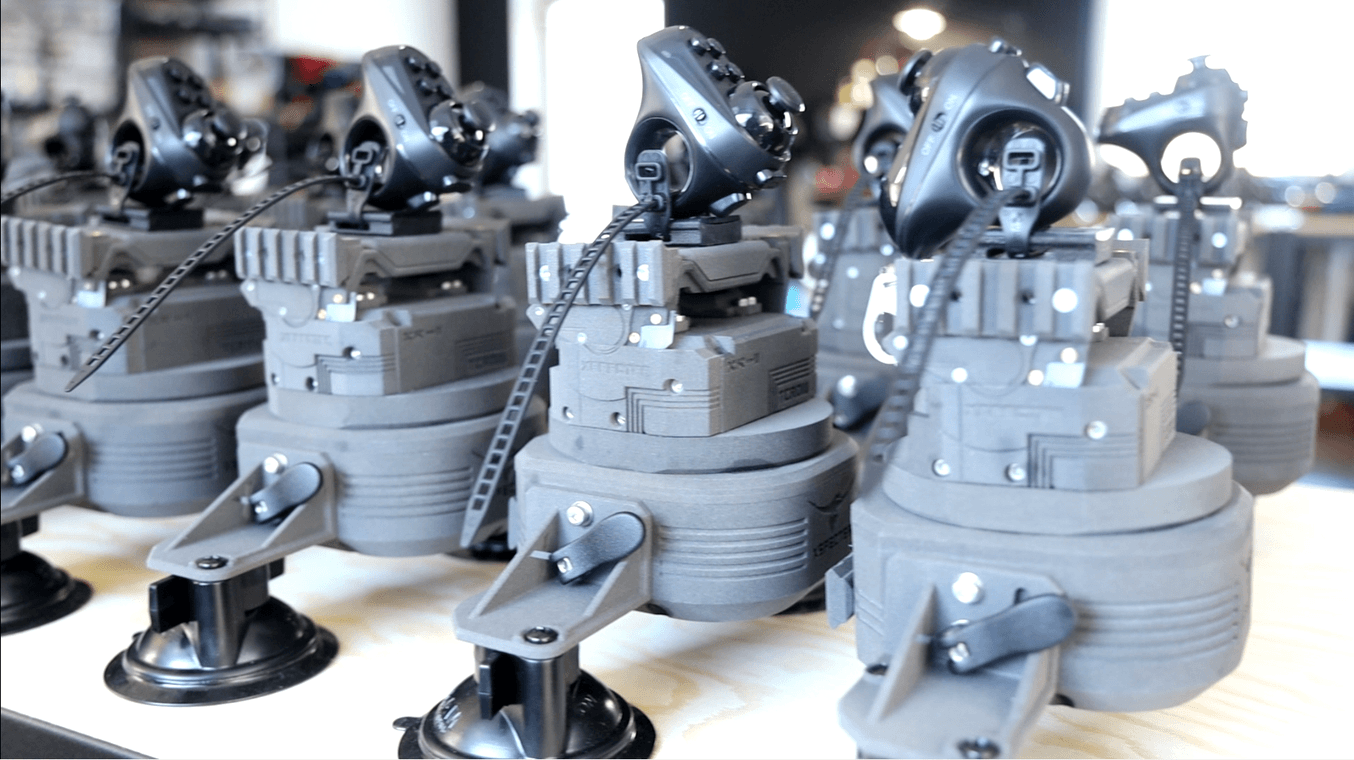
Ein versandfertiges T-Crow Stativ mit dem Gehäuse aus Nylon 12 Powder
Er entschied sich für den Formlabs SLS 3D-Drucker Fuse 1 sowie für den großformatigen SLA 3D-Drucker Form 3L, um die Serienproduktion T-Crows durch 3D-gedruckte Endverwendungtseile zu initiieren.
Nachdem die Produktion angelaufen ist hat AMPrO 3D die Produktion der T-Crows bei XSPECTER mit der Kamera begleitet, um einen Einblick zu geben, was alles möglich ist wenn man 3D-Druck geschickt einsetzt.
“Ich bin der Meinung, dass die Formlabs 3D-Drucker vom Preis-Leistungsverhältnis tatsächlich die besten Drucker sind, die man momentan auf dem Markt findet”, so Mähler.
Serienfertigung mit einer Kombination aus SLA und SLS 3D-Druck
Für die Produktion der T-Crows setzt XSPECTER auf eine Kombination aus SLA und SLS 3D-Druck und fertigt bis auf Komponenten der Elektronik ein komplett 3D-gedrucktes Kamerastativ.
Das Gehäuse wird auf dem Fuse 1 hergestellt. Dank des Formlabs Materials Nylon 12 Powder bleibt das Gehäuse leicht und ist resistent gegen viele Umwelteinflüsse. Außerdem eignet es sich sehr gut, um nachträglich Gewindebuchsen für die spätere Montage einzuschmelzen.
Für Achsen und Zahnräder benutzt XSPECTER ihren Form 3L und das Durable Resin von Formlabs. Durch die flexiblen, trotzdem schlagfesten und gleitfähigen Eigenschaften des Materials, wird der Einbau von Übermaßpassungen möglich, welches für das Zweiachs Steuerungssystem benötigt wird.
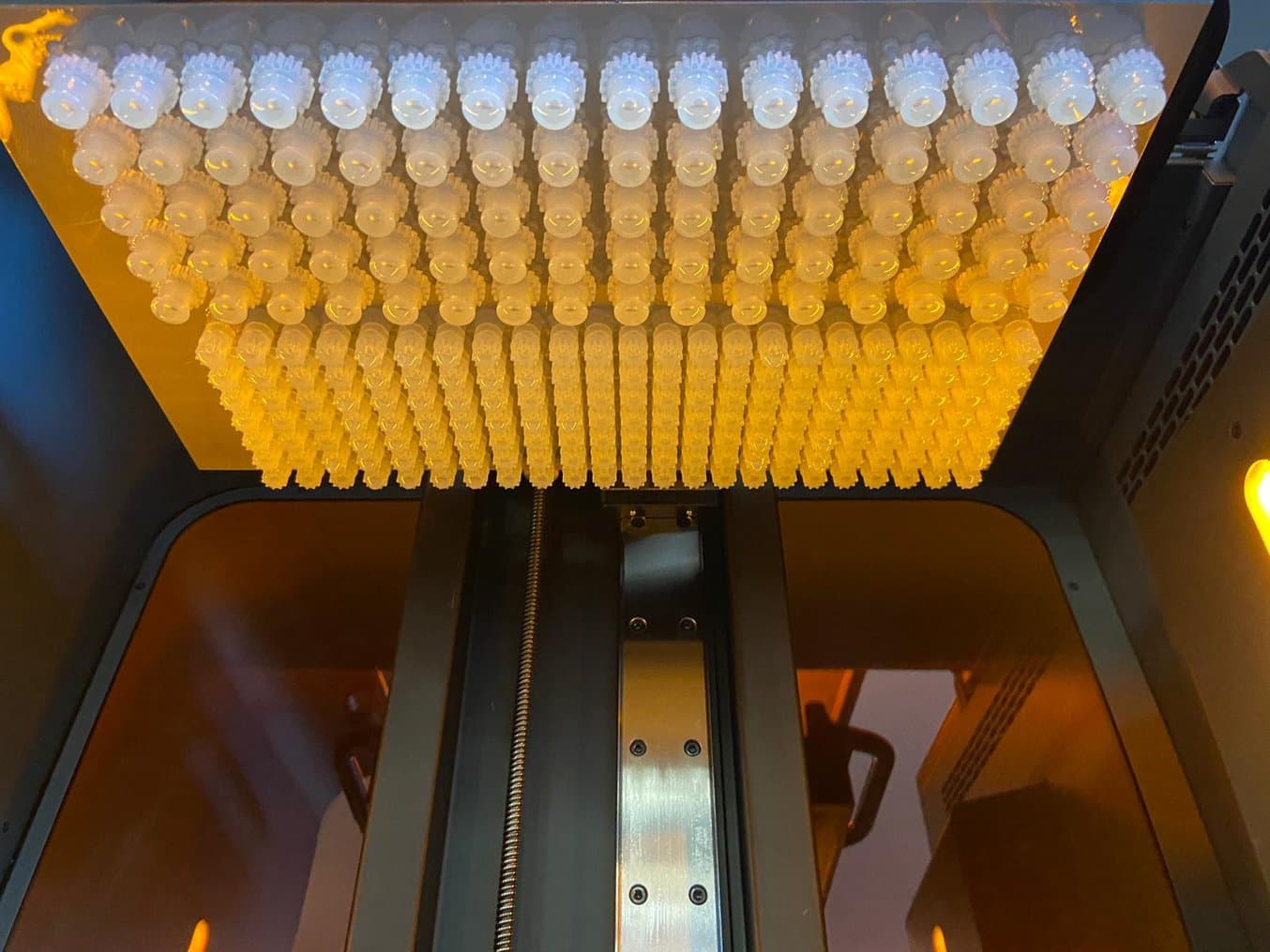
Zahnräder für den T-Crow aus Durable Resin auf der Build Platform des Form 3Ls
Nachdem die Einzelteile alle hausintern gedruckt und nachbearbeitet wurden, werden sie mittels der Gewindeeinsätze zusammengebaut und sind innerhalb von drei Tagen komplett versandfertig.
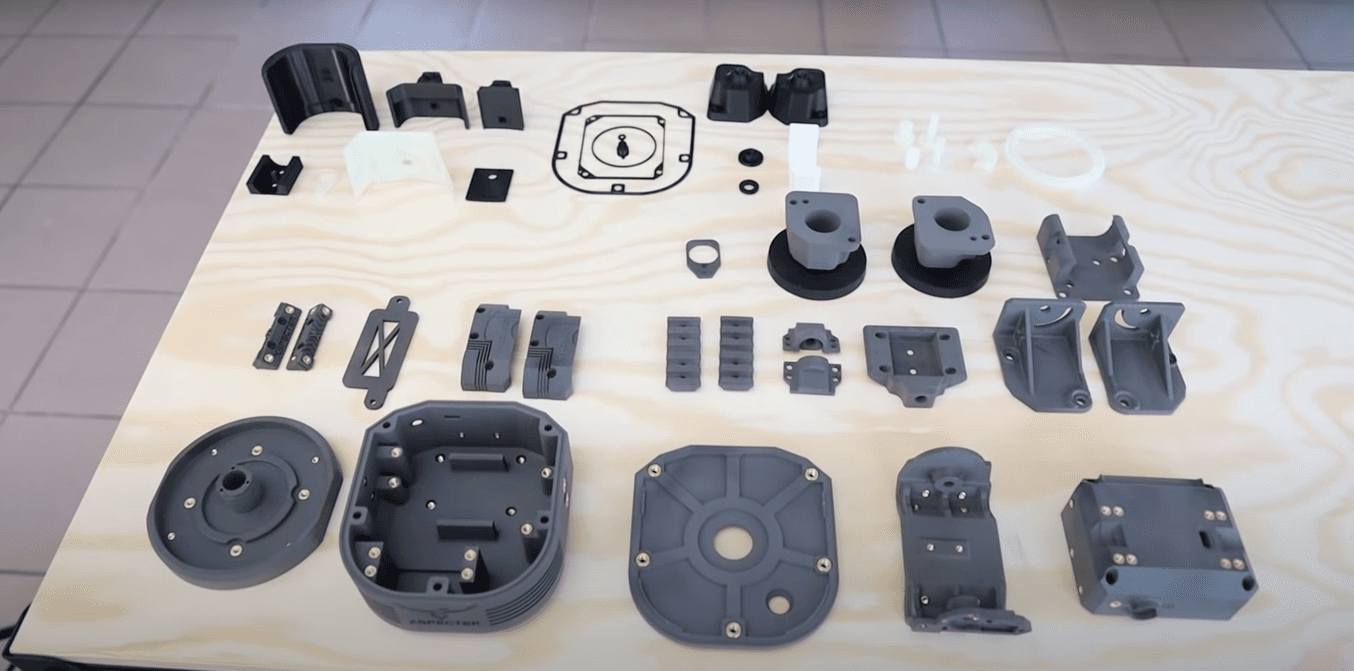
Alle Einzelteile des T-Crows vor dem Zusammenbau
“Mit den Druckern, die wir momentan haben würden wir in einem Jahr 1.500 komplette T-Crows versandfertig produzieren können, “ erzählt Mähler.
Konstruktive Flexibilität dank 3D-Druck
Ein grundlegender Vorteil und ausschlaggebender Entscheidungsfaktor für die komplett hausinterne 3D-Druck Produktion ist die enorme Flexibilität, die gewonnen wird.
“Mit dem 3D-Druck sind wir einfach konstruktiv freier als mit herkömmlichen Methoden, wie einem Spritzgussverfahren. Wir nennen das ein lebendes Produkt. Wenn wir einen Fehler am Design finden oder Kundenfeedback bekommen, können wir eine neue Iteration von heute auf morgen umsetzen. Das schaffst du mit keinem anderen Verfahren.”
Matthias Mähler
Designänderungen dieser Art werden beispielsweise bei der Anpassung der Adapter verschiedener Kameras vorgenommen, sodass die Stative universell einsetzbar sind. Die unterschiedlichen filigranen Designs werden direkt mit in das 3D-gedruckte Gehäuseteil integriert. Wenn eine neue Kamera auf den Markt kommt, kann Mähler also auch für diese die entsprechenden Änderungen an seinem T-Crow Stativ rapide vornehmen und verkaufen.
Auch in der Reaktionsgeschwindigkeit bei wechselnden Zulieferern für Einzelteile konnte XSPECTER durch die Flexibilität des 3D-Drucks schon enorm Zeit und Geld einsparen.
“Ich habe einmal den Ein- und Ausschalter nicht mehr von unserem ursprünglichen Zulieferer bekommen und war gezwungen auf einen anderen umzusteigen. Das hieß für uns, dass die Aussparung des Ein- und Ausschalters um etwa zwei Millimeter vergrößert werden musste, was ich quasi über Nacht geändert habe,“ erklärt Mähler.
Bei einem für circa 120.000€ in Auftrag gegebenen Spritzgussverfahren hätte ein solche Abänderung der Urform nochmal mehr Zeit und Geld eingefordert.
“3D-Druck ist meiner Meinung nach zukunftsweisend, insbesondere dann wenn man als Unternehmen Kund:innen Feedback mit einbeziehen möchte. Wir sind jetzt zwar schon in der Serie, aber wir entwickeln unsere Stative trotzdem stetig anhand des Feedbacks weiter.“
Matthias Mähler
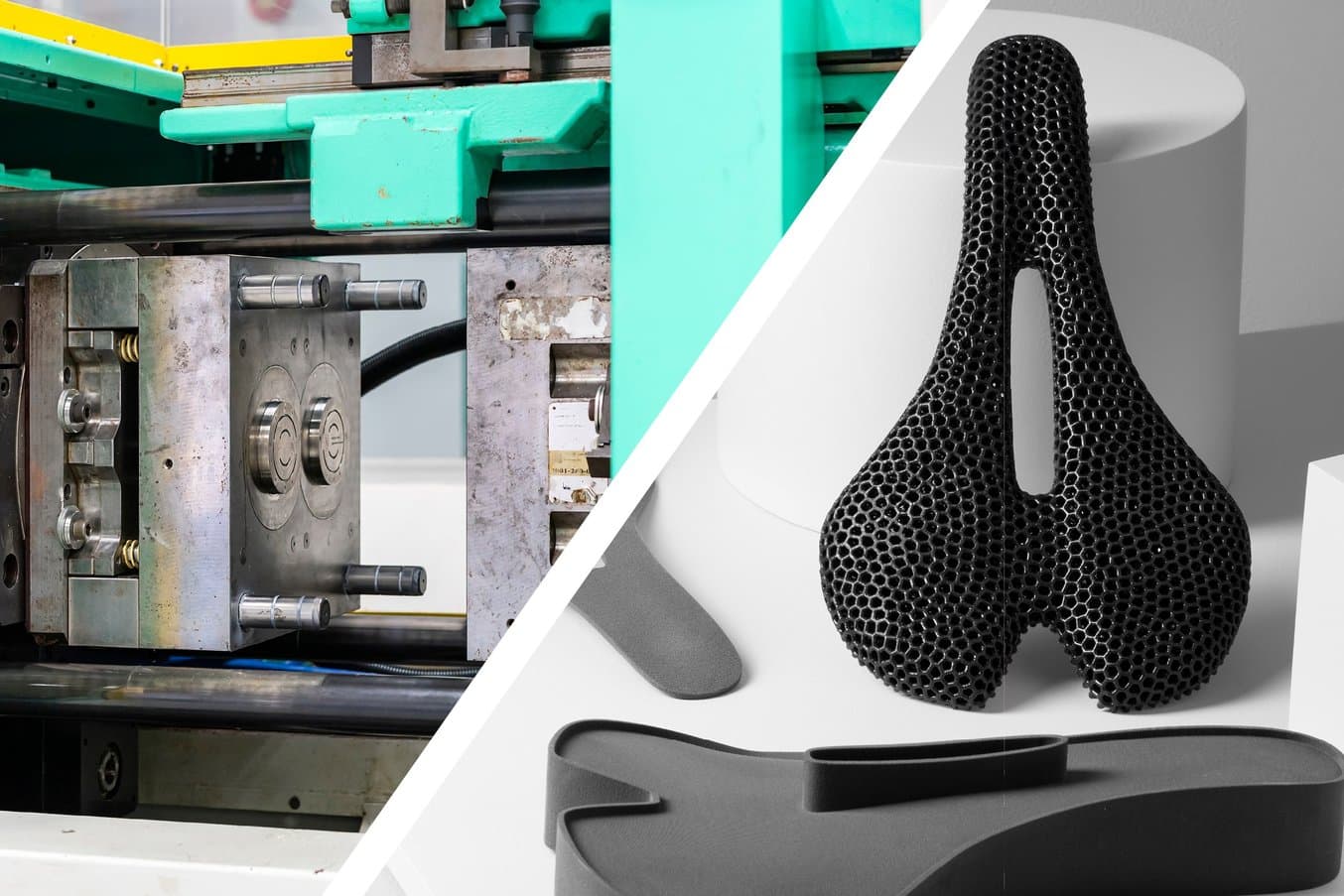
SLS-3D-Druck oder Spritzguss: Wann sollte man Spritzgussteile durch 3D-Druck ersetzen?
In diesem Whitepaper werden der Spritzguss und seine Vor- und Nachteile erörtert sowie der SLS-3D-Druck und die Anwendungen vorgestellt, bei denen er als ergänzende Technologie eingesetzt werden kann.
Da XSPECTER mit ihren momentanen Druckerkapazitäten auf die gleiche Stückzahl mit geringeren Kosten als mit einem Spritzgussverfahren kommt und sie in Ihrer Strategie sehr auf die Flexibilitätsvorteile von SLS 3D-Druck setzen, kann Mähler sich auch in der vorhersehbaren Zukunft keine andere Fertigungstechnik für sein Produkt vorstellen.
Das nächste Projekt Mählers ist der sogenannte Sea-Crow: eine maritime Variante des Kamerastativs, welches auch Suchscheinwerfer involvieren soll und wiederum als nächtliche Navigationshilfe auf dem Wasser funktioniert.