Guía de impresión 3D de dispositivos médicos: De los prototipos a la comercialización
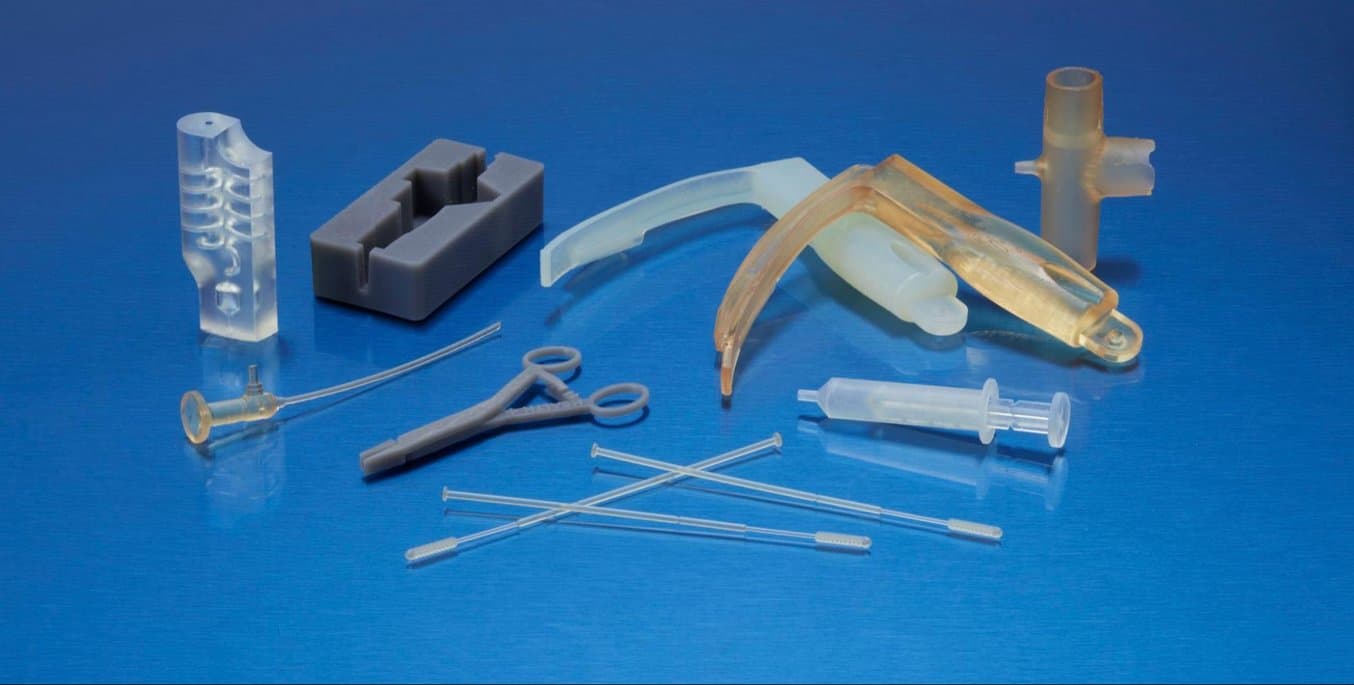
La impresión 3D lleva décadas impulsando soluciones innovadoras e influyendo en el desarrollo de los dispositivos médicos y productos sanitarios, desde la fase de I+D hasta la de fabricación. A medida que las impresoras 3D se han vuelto más asequibles y crecen las inversiones en máquinas y materiales, más empresas están accediendo a la impresión 3D y alterando el statu quo de la industria sanitaria.
Al llevar la impresión 3D a sus propias instalaciones, los desarrolladores y fabricantes de productos sanitarios pueden reducir los costes y el tiempo de lanzamiento al mercado. La tecnología hace posible un desarrollo de productos más ágil, piezas de uso final innovadoras y la creación de dispositivos médicos personalizados que serían imposibles de producir utilizando herramientas tradicionales. Como se ha demostrado desde principios de 2020, la fabricación aditiva también permite avanzar con una velocidad sin precedentes desde el concepto hasta la producción en masa de material médico de emergencia.
En esta guía exhaustiva, analizamos las diferentes aplicaciones de la impresión 3D para dispositivos médicos, comparamos los procesos de impresión 3D más comunes en el sector médico y proporcionamos un breve visión general (y enlaces a más recursos relacionados) del proceso reglamentario para los productos sanitarios impresos en 3D.
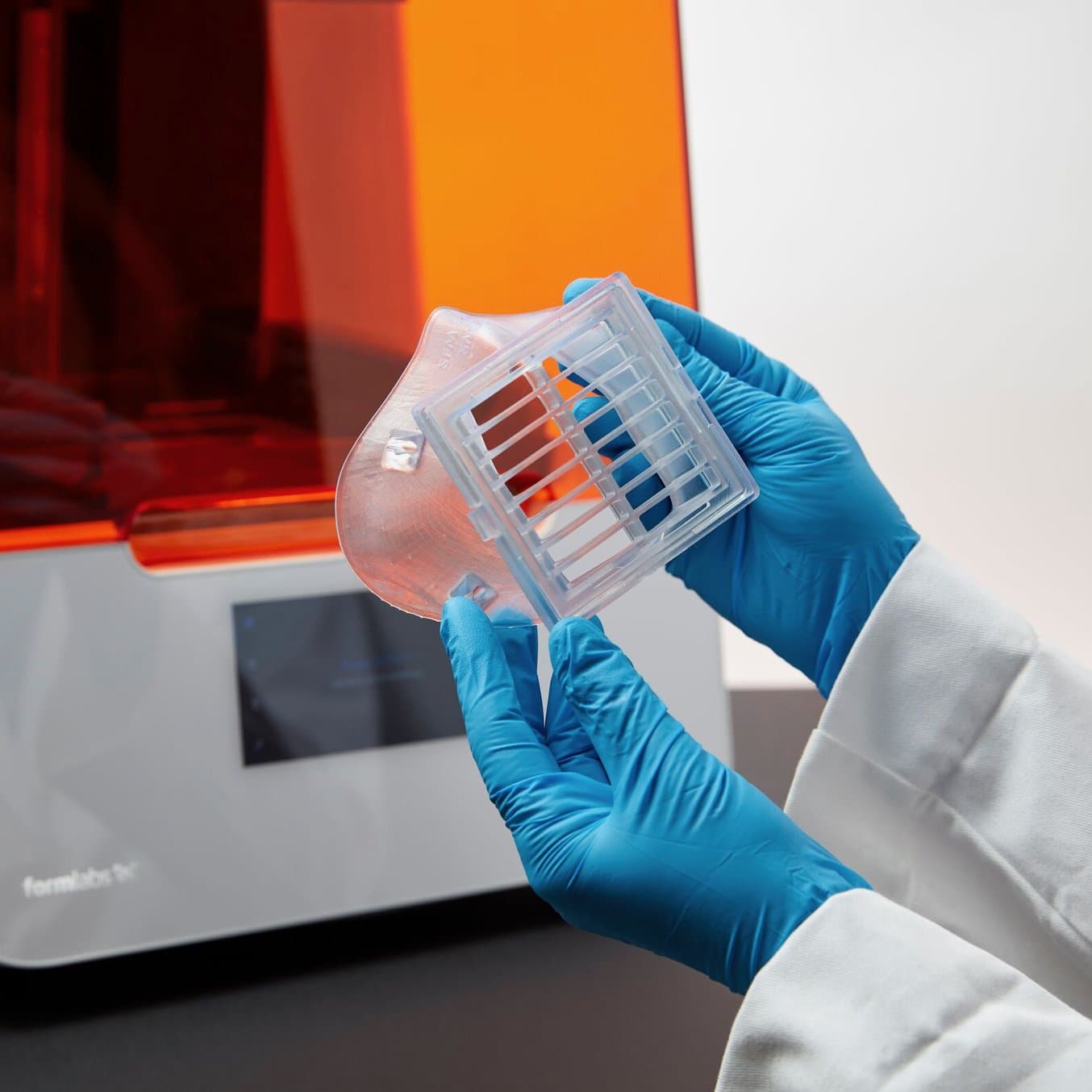
Cómo alcanzar el éxito con la impresión 3D de dispositivos médicos
En este informe, descubrirás cómo Formlabs Medical ayuda a las empresas de productos sanitarios a incorporar la fabricación digital en sus instalaciones y encontrarás inspiración en los ejemplos de cuatro empresas que están creando actualmente productos revolucionarios mediante la impresión 3D.
Aplicaciones de impresión 3D para dispositivos médicos
La combinación de velocidad, precio económico, adaptabilidad y libertad de diseño que ofrece la impresión 3D ha dado lugar a una amplia gama de casos de uso en el sector de los dispositivos médicos. Examinaremos sus aplicaciones más comunes y ejemplos reales que destacan la versatilidad de la impresión 3D.
Creación rápida de prototipos de dispositivos médicos
En el sector sanitario, el desarrollo de productos innovadores está intrínsecamente unido a la mejora de la asistencia a los pacientes y la mejora de los resultados. La creación de prototipos es un elemento clave de este proceso de iteración en el que las revisiones se realizan, se aplican y se someten a ensayo en un entorno controlado.
La creación rápida de prototipos es el conjunto de técnicas que se usan para fabricar con rapidez un modelo a escala real de una pieza o conjuntos de piezas físicos utilizando datos tridimensionales de diseño asistido por ordenador (CAD). La impresión 3D es ideal para la creación de prototipos, ya que ofrece una libertad casi ilimitada en cuanto a la forma, no requiere utillaje y puede producir piezas con propiedades mecánicas muy similares a las de las piezas producidas mediante métodos de fabricación tradicionales.
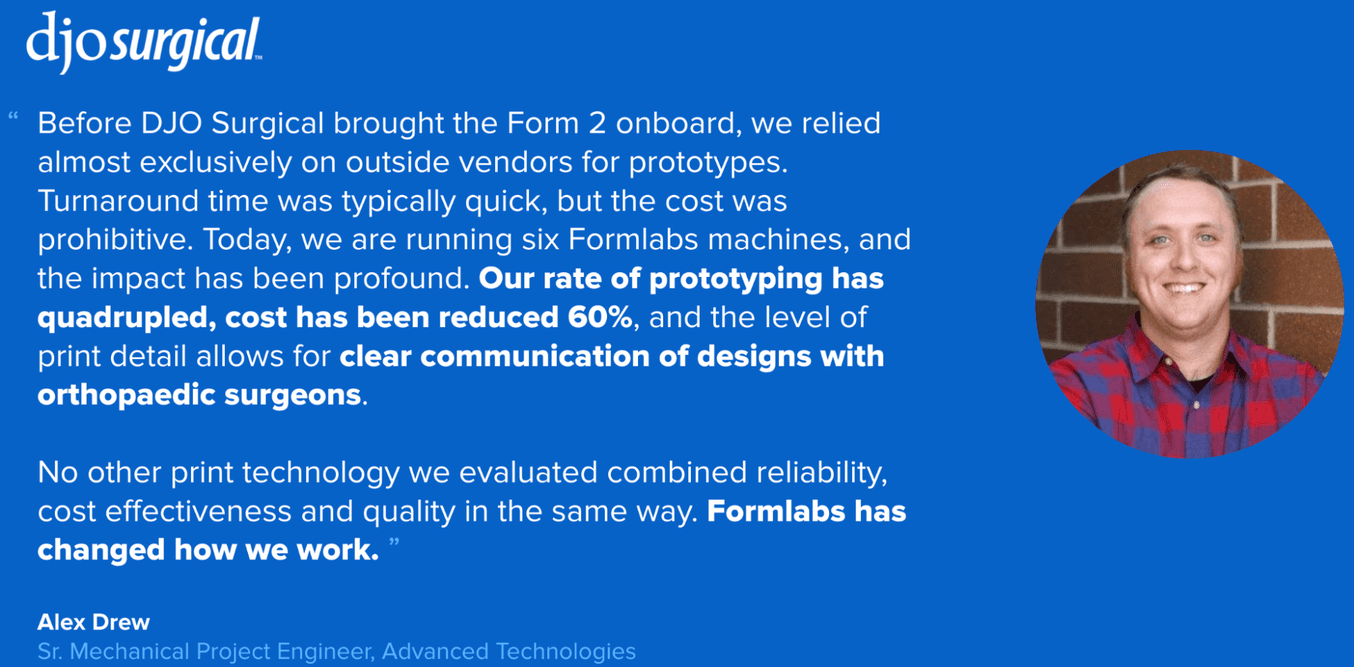
La impresión 3D proporciona a los fabricantes la flexibilidad de desarrollar prototipos estéticos, táctiles y funcionales de hasta los dispositivos médicos más complejos. Es posible crear nuevas iteraciones en unas pocas horas y validarlas para determinar si requieren más cambios. Aplicar la impresión 3D también permite desarrollar prototipos de dispositivos médicos con materiales diversos en situaciones en las que propiedades como la tenacidad, la flexibilidad o la resistencia al calor sean criterios importantes para el funcionamiento del producto.
Someter a ensayo un prototipo funcional utilizando procesos de validación pensados para el mundo real proporciona al fabricante resultados en los que basar posteriores iteraciones. Los prototipos impresos en 3D también pueden servir como piezas de presentación al hacer propuestas a los inversores o entablar contacto con futuros clientes.
La facilidad de uso y el bajo coste de la impresión 3D in situ también han revolucionado el desarrollo de productos. Más del 85 % de los 50 mayores fabricantes de dispositivos médicos han adoptado la tecnología de Formlabs para producir prototipos, accesorios para la fabricación o productos de uso final. Dado que las inversiones en activos fijos que requiere es inferior a 5000 $, muchas empresas emergentes y pequeños negocios también han podido beneficiarse de la tecnología.
Por ejemplo, la empresa de diseño de dispositivos médicos del Reino Unido Coalesce Product Development desarrolla dispositivos de administración de medicamentos, como inhaladores e inyectores. Este fabricante tuvo problemas a la hora de desarrollar prototipos de dispositivos médicos complejos utilizando procesos de fabricación tradicionales, debido a los elevados costes iniciales y operaciones de larga duración asociadas con las herramientas de fabricación tradicionales.
La empresa recurrió a impresoras 3D de estereolitografía (SLA) in situ para la creación de prototipos, ensayos y creación de diversos productos en muchas formas y tamaños diferentes. Con la impresión 3D, crearon nuevos prototipos en menos de 24 horas, por un coste 10-20 veces inferior al que habría supuesto externalizar el proceso. Además de imprimir en 3D los prototipos, también imprimen en 3D sujeciones con guía y fijaciones de ensayo para acelerar los ensayos de sus inhaladores.
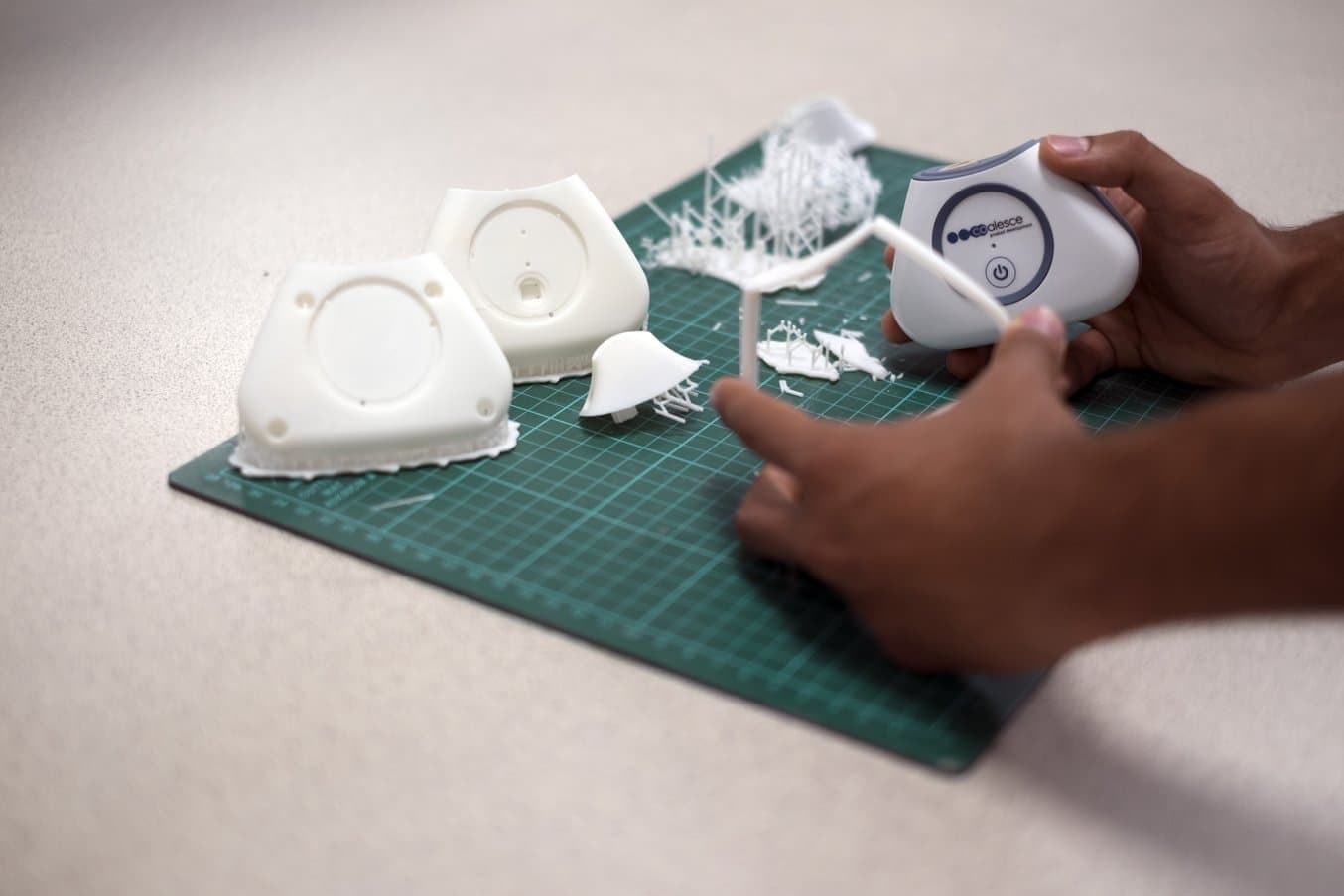
La empresa de diseño de dispositivos médicos Coalesce utiliza la impresión 3D para crear prototipos de dispositivos de administración de medicamentos, como inhaladores.
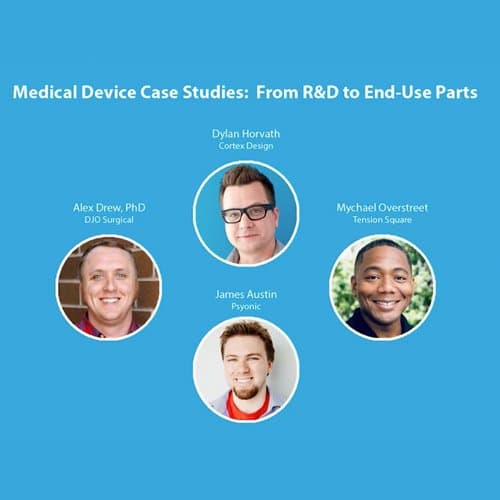
Casos de estudio de dispositivos médicos: De la I+D a las piezas de uso final
En este seminario web, Gaurav Marchanda, director de desarrollo para el mercado médico de Formlabs, ejerce de anfitrión para actuales clientes de Formlabs en la industria médica. Las empresas que nos acompañan van desde empresas emergentes hasta grandes compañías con ventas millonarias, entre las que se cuentan Cortex Design, DJO Surgical, Psyonic y TensionSquare.
Fabricación de dispositivos médicos a medida para los pacientes
La mayoría de los procesos de fabricación tradicionales como el moldeo por inyección o el termoformado requieren un utillaje caro, por lo que no son eficientes para producir piezas personalizadas. La impresión 3D afronta este desafío de dos formas.
Utillaje rápido para procesos de fabricación tradicionales
En primer lugar, la impresión 3D se puede utilizar para fabricar utillaje rápido a medida, como moldes, patrones y troqueles para diversos procesos de fabricación tradicionales, entre los que se cuentan el moldeo por inyección, el termoformado, el moldeo con silicona, el sobremolde, moldeo por inserción, el moldeo por compresión, la fundición, etc.
Un ejemplo de moldeo en vacío es el de los alineadores y retenedores dentales que se diseñan y crean en función de datos de la anatomía única de los pacientes que se captan mediante aparatos de escaneado de escritorio o intraorales. La fabricación de esos dispositivos conlleva moldear en vacío una lámina de plástico sobre un modelo personalizado en cada paso del tratamiento. Ya que las impresoras 3D pueden producir estos modelos directamente a partir de los archivos digitales en unas pocas horas, se han convertido en el principal método para producir estos dispositivos cada vez más populares en el ámbito de la ortodoncia.
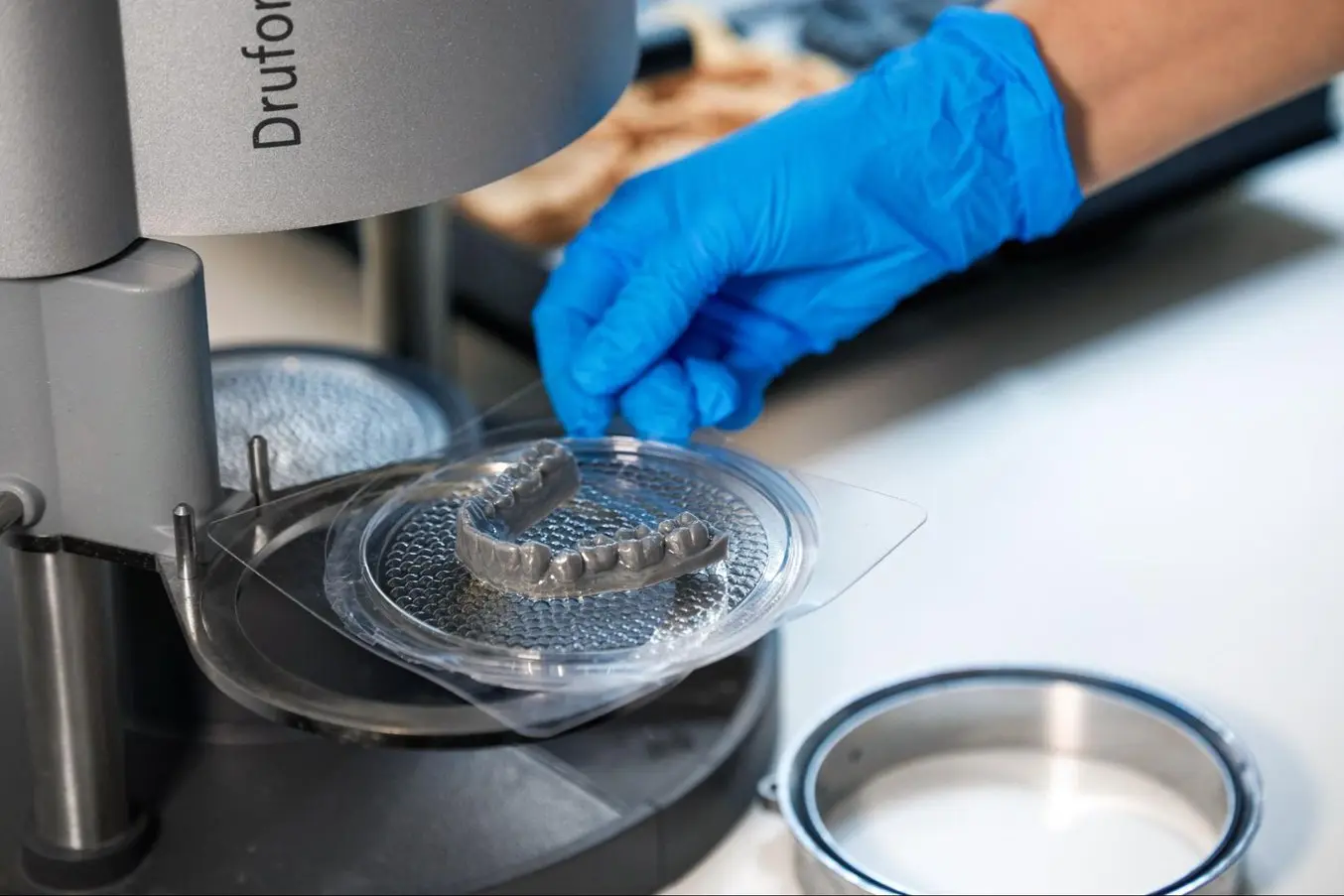
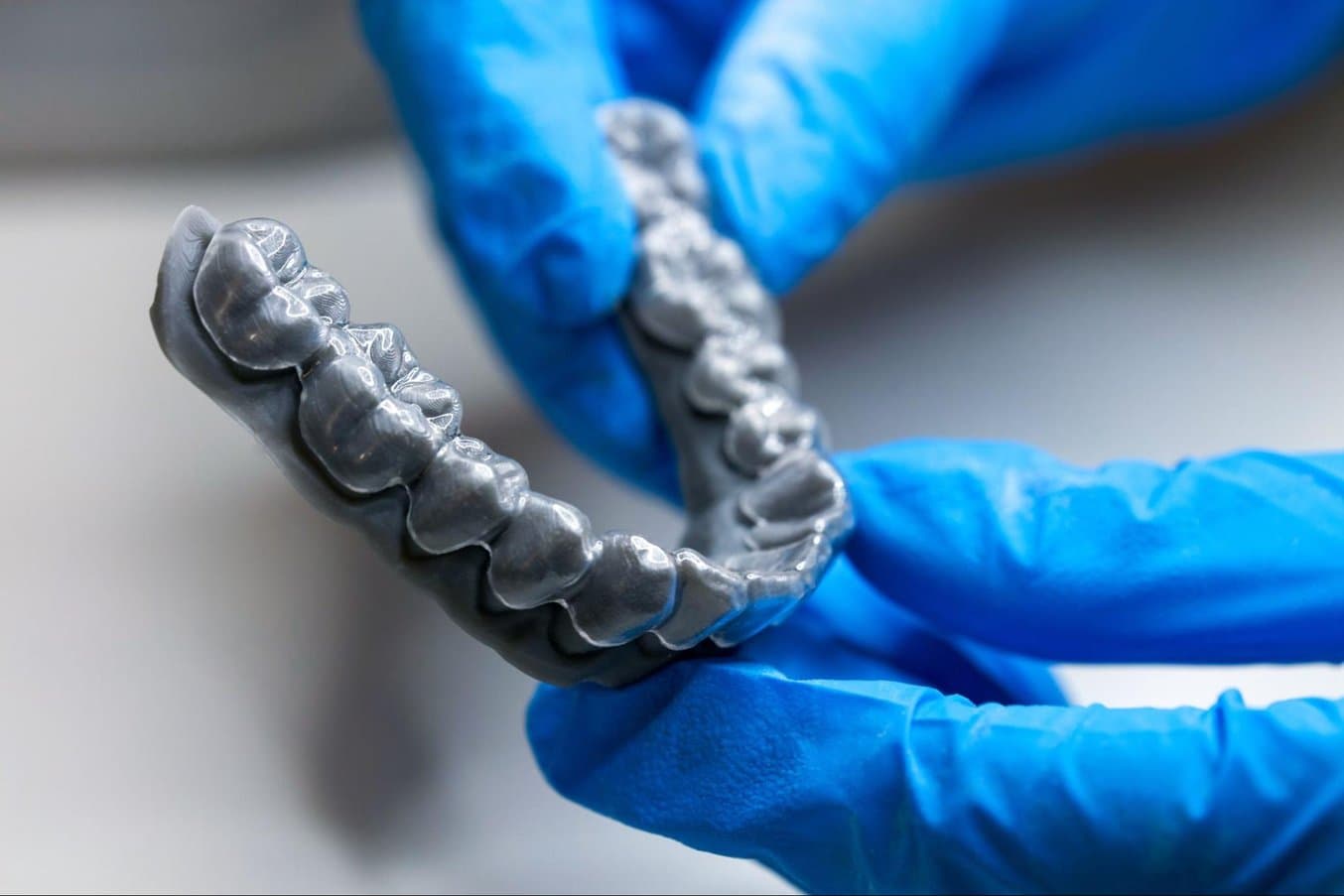
La impresión 3D es el principal método para fabricar modelos para el moldeo en vacío de alineadores y retenedores transparentes.
Otro ejemplo lo encontramos en Cosm, una empresa de dispositivos médicos que desarrolla un tratamiento de apoyo para los pacientes con trastornos del suelo pélvico. La empresa utiliza moldes impresos en 3D para el moldeo con silicona para crear un tratamiento a medida para el caso específico de cada paciente.
Usar la impresión 3D aporta a Cosm la flexibilidad y la rentabilidad que necesita para fabricar moldes personalizados para pesarios en menos de 24 horas.
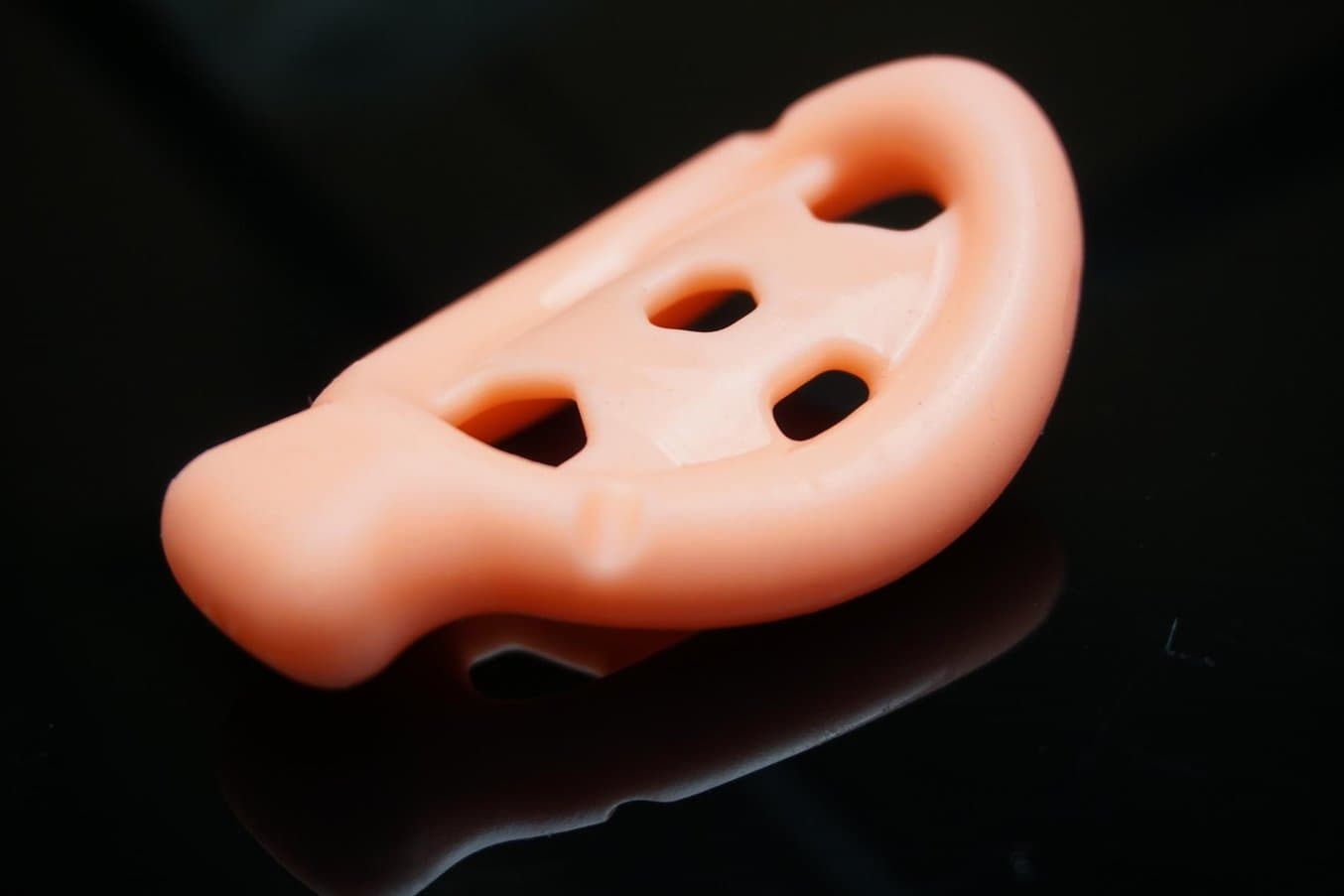
Cosm fabrica pesarios personalizados mediante el moldeo con silicona.
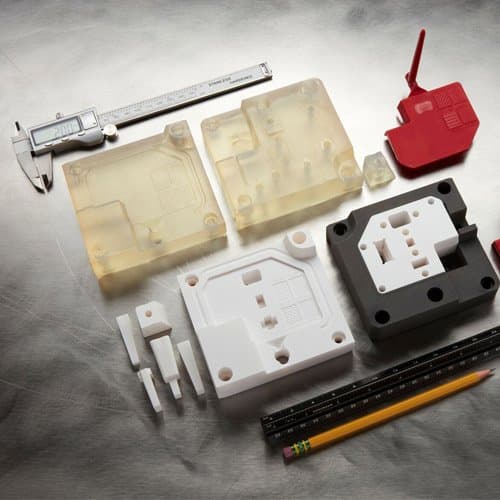
Fabricación de moldes con impresiones 3D: Técnicas para la creación de prototipos y la producción
Descarga nuestro libro blanco para conocer seis procesos de fabricación de moldes que son posibles con una impresora 3D SLA en tus instalaciones, como el moldeo por inyección, el moldeo en vacío, el moldeo con silicona y más.
Impresión 3D directa de dispositivos médicos a medida para los pacientes
En segundo lugar, la impresión 3D cada vez se usa más para fabricar dispositivos médicos de uso final adaptados a los pacientes. Dado que los procesos de impresión 3D no requieren utillaje, permiten crear piezas a medida y diseños complejos de una forma ágil y rentable.
Una vez más, la odontología es uno de los campos que están a la vanguardia de la impresión 3D en la medicina. Las guías quirúrgicas, férulas, restauraciones temporales y permanentes y las prótesis dentales se pueden imprimir en 3D directamente.
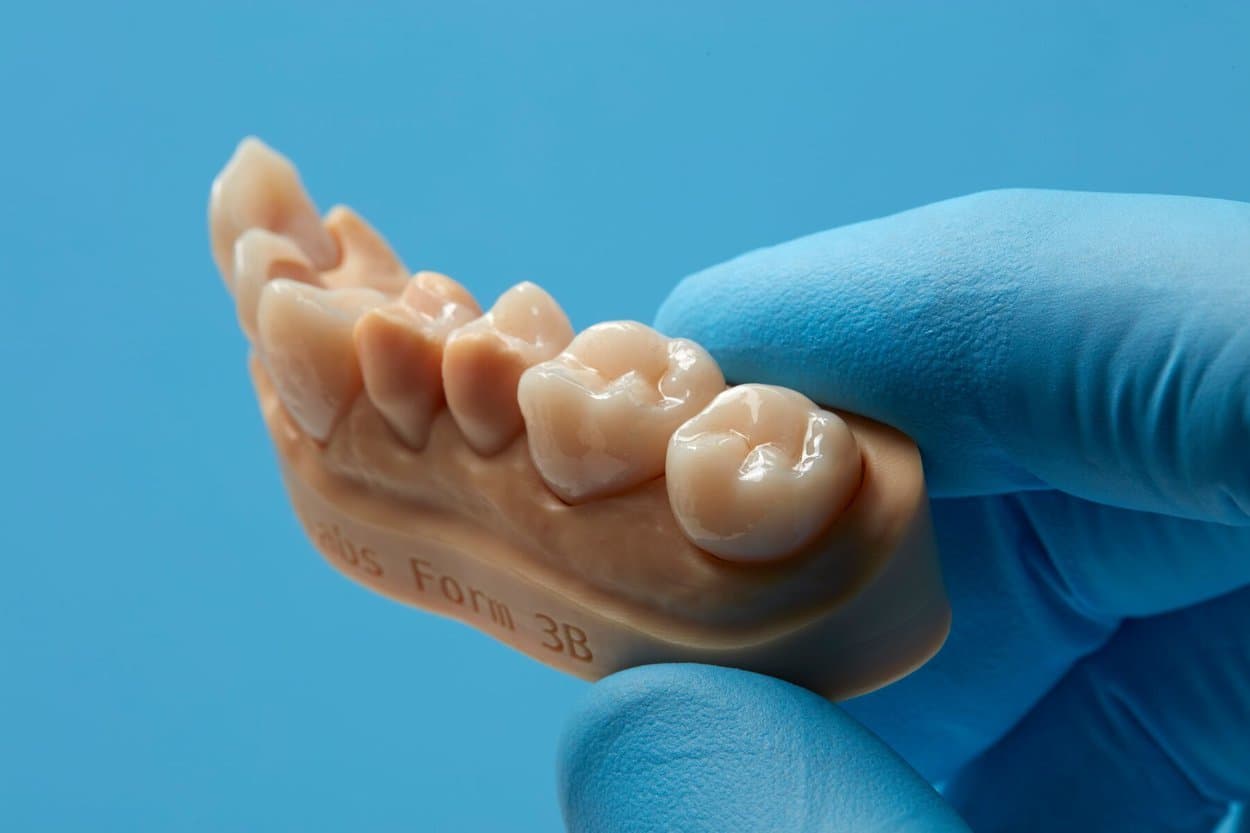
Coronas permanentes fabricadas utilizando un material de resina con partículas de cerámica.
Otras aplicaciones de impresión 3D médicas de uso final son los dispositivos auditivos hechos a medida, como los audífonos y las protecciones contra el ruido, así como prótesis y órtesis personalizadas resistentes y duraderas.
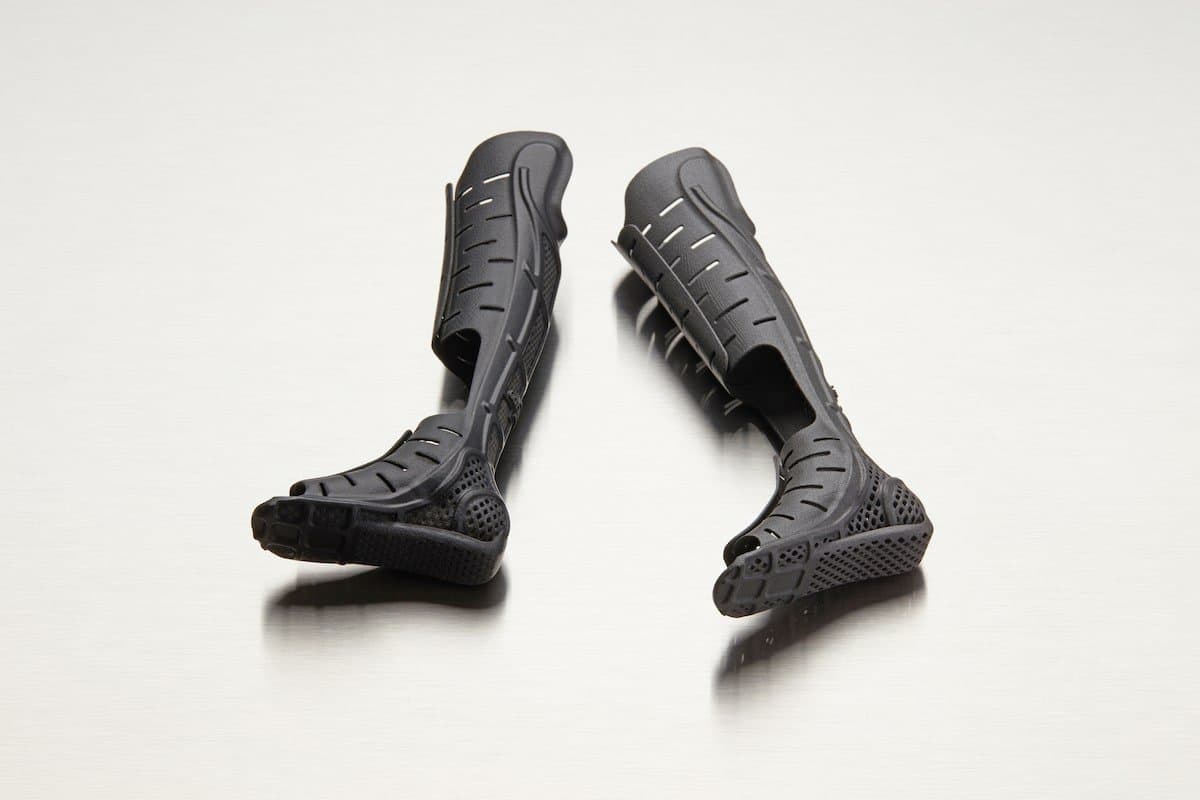
La impresión 3D se puede usar para crear prótesis y órtesis resistentes y biocompatibles adaptadas a cada paciente, a un precio asequible y más rápido que nunca.
El fabricante de instrumentos quirúrgicos restor3d aprovecha las capacidades de la impresión 3D para mejorar drásticamente los resultados de la cirugía, imprimiendo en 3D instrumentos de uso específico para implantes vertebrales cervicales. Utilizar la impresión 3D brinda la capacidad de crear herramientas estériles diseñadas por cirujanos mediante un proceso de desarrollo verdaderamente ágil. El enfoque de restor3d reduce los costes de la esterilización, el almacenaje y el quirófano para hospitales y centros quirúrgicos. Ha habido una gran demanda: más de 25 máquinas de Formlabs están fabricando dispositivos las 24 horas del día.
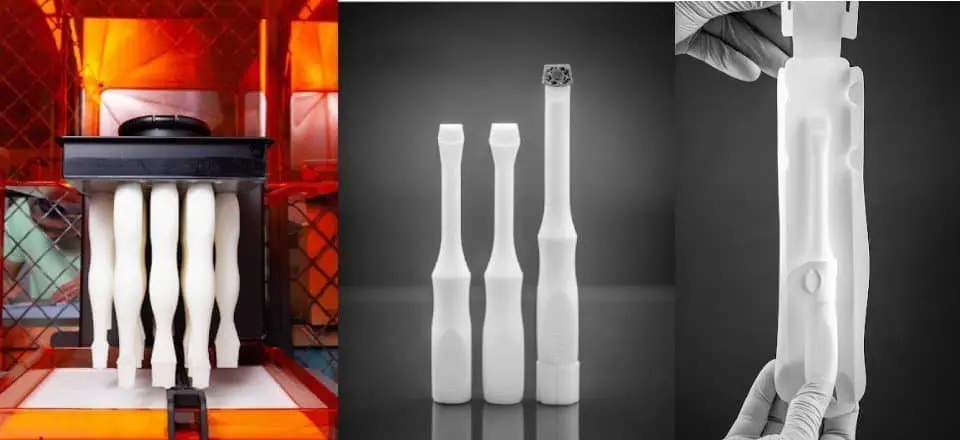
restor3d usa la impresión 3D para fabricar instrumentos quirúrgicos adaptados a operaciones específicas.
Producción de dispositivos médicos de uso final
Además de para herramientas quirúrgicas, la impresión 3D cada vez es más popular para producir dispositivos médicos o componentes de los mismos, especialmente para diseños complejos que no serían eficientes o posibles de fabricar con procesos tradicionales.
TensionSquare ha comercializado un dispositivo que mantiene un catéter de descompresión con aguja en su sitio y evita que se retuerza, doble o desenganche, problemas que pueden provocar fallecimientos evitables. Después de años de I+D, la empresa ahora está imprimiendo en 3D el dispositivo de uso final en una impresora 3D de sinterizado selectivo por láser (SLS) Fuse 1, que permite reducir la dependencia de proveedores externos y producir más de 100 dispositivos por impresora en menos de 24 horas. La empresa, fundada por un veterano del ejército y paramédico, tiene como objetivo producir millones de piezas al año mediante la impresión 3D en sus instalaciones de fabricación de EE. UU.
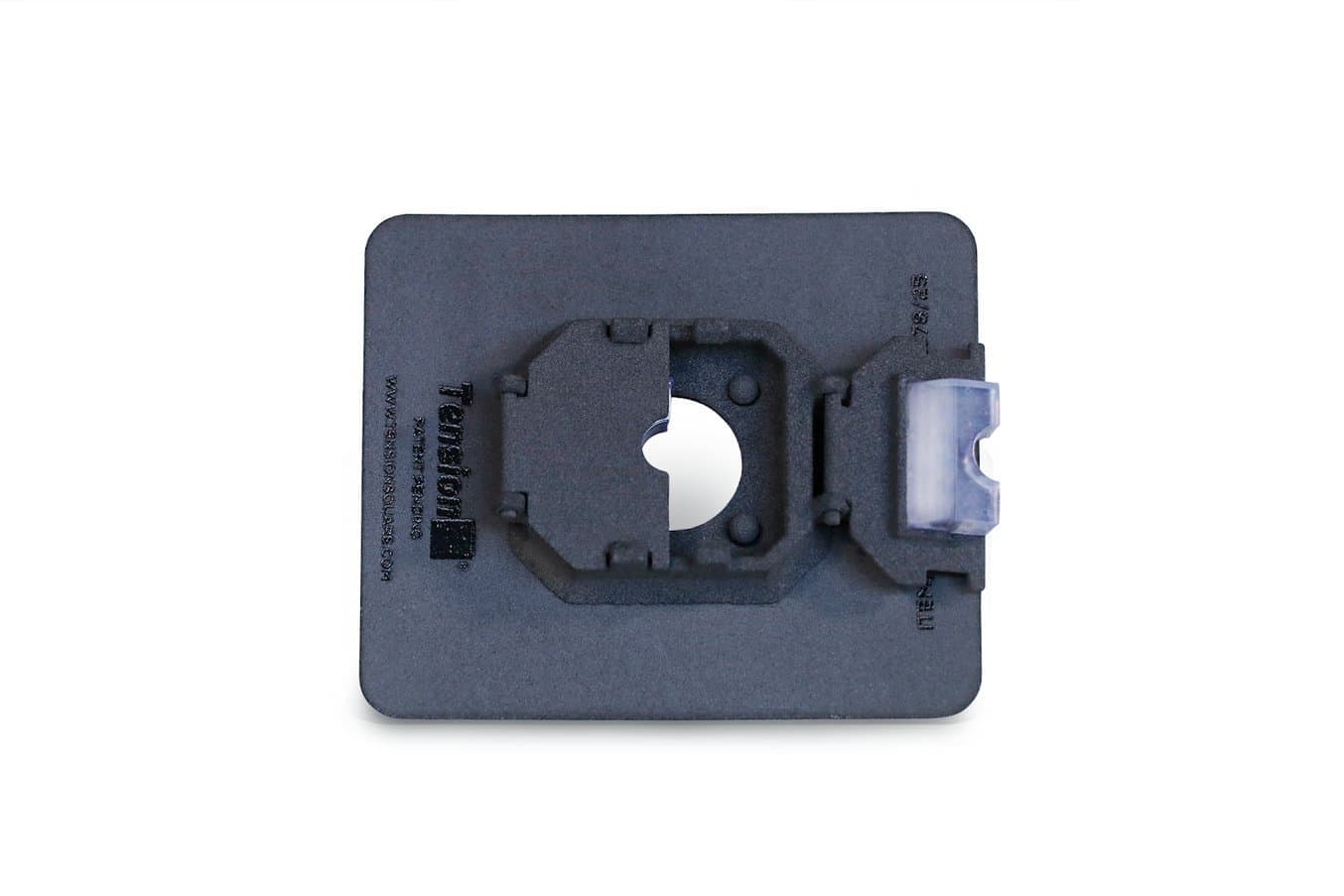
TensionSquare imprime directamente en 3D mediante SLS un dispositivo de estabilización de catéteres de descompresión para el tratamiento del neumotórax.
VO2 Master desarrolla un analizador metabólico portátil que resulta más fácil de usar y más asequible que máquinas muy extendidas. Después de utilizar mucho la impresión 3D en el proceso de creación de prototipos, la empresa decidió imprimir también en 3D las carcasas exteriores de uso final del dispositivo para poder lanzarlo más rápidamente al mercado. Las carcasas se imprimen en impresoras 3D SLA con la Tough 1500 Resin, un material resiliente que simula la resistencia y la rigidez del polipropileno. Las piezas impresas se pintan de blanco antes de sujetarlas a la mascarilla para mejorar el acabado de la superficie, resaltar el color en relieve y aumentar la durabilidad.
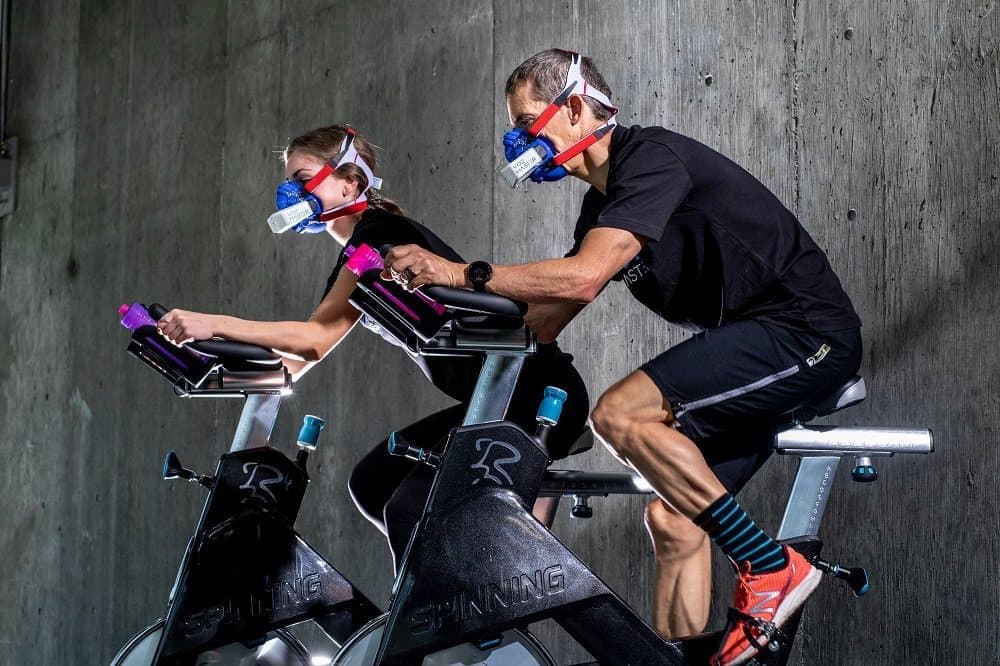
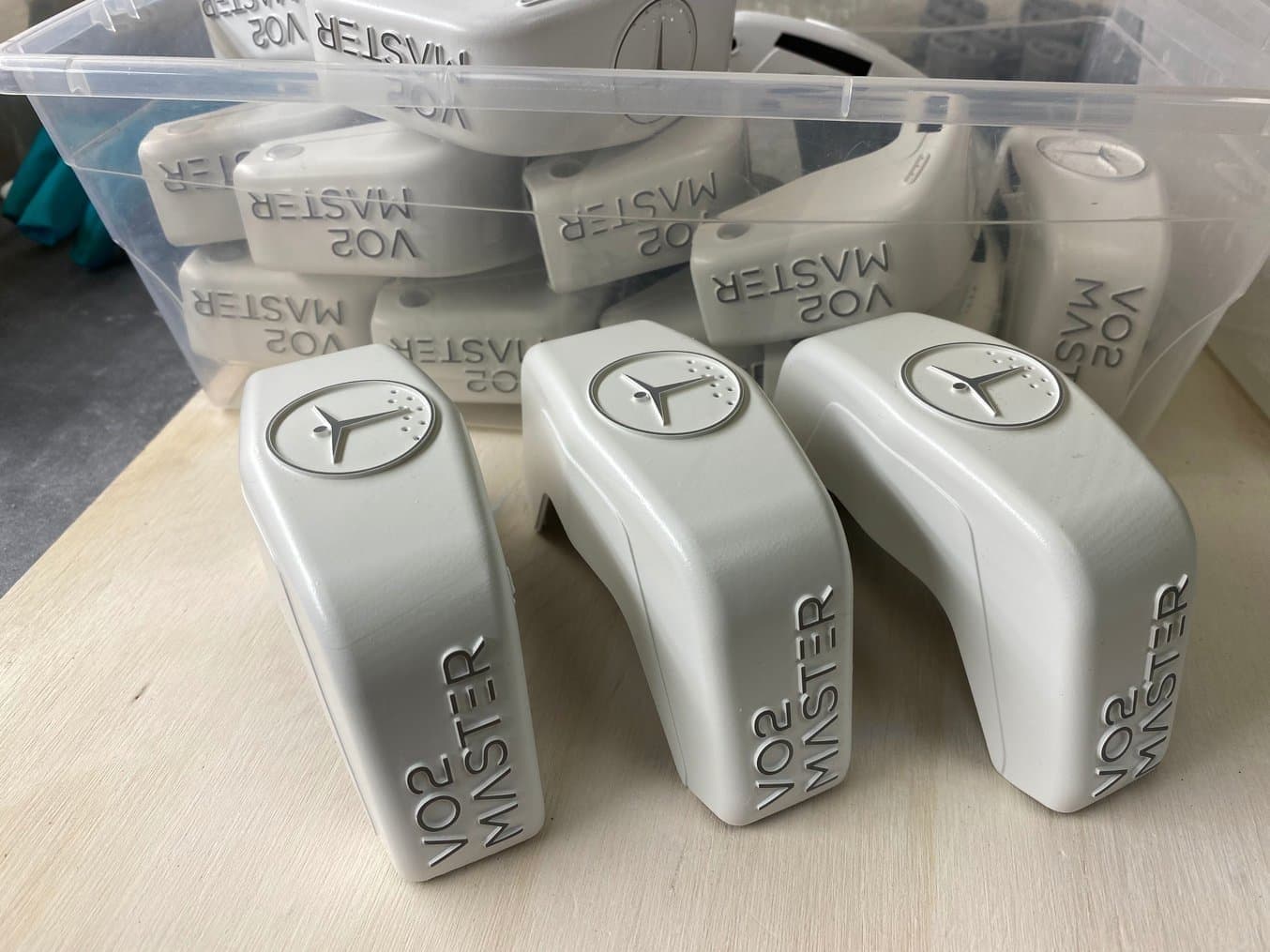
VO2 Master imprime en 3D la carcasa exterior de su analizador metabólico portátil, lo que hace posible lanzarlo al mercado más rápido.
Fabricación de suministros médicos de emergencia
La pandemia de COVID-19 sobrepasó a los centros sanitarios y a los suministros médicos de formas sin precedentes que obligaron a la mayoría de los gobiernos a buscar materiales en lugares inverosímiles. Para abordar la abrumadora necesidad de material, los fabricantes de automóviles pasaron a fabricar respiradores, mientras que las firmas de moda produjeron equipo protector para mitigar los desafíos asociados con la pandemia.
A medida que subía el número de casos de COVID-19, creció la necesidad de realizar pruebas masivas, lo que condujo a una escasez global de los hisopos nasofaríngeos necesarios para tomar muestras para las pruebas de COVID-19. Después de identificar que había una gran demanda y un suministro extremadamente limitado de hisopos nasales para test de COVID-19, un USF Health, Northwell Health y Formlabs colaboraron en equipo para crear una alternativa impresa en 3D. A lo largo de una semana, los equipos trabajaron juntos para desarrollar un prototipo de hisopo nasal y someterlo a ensayo en los laboratorios de USF Health y Northwell Health. En dos días, USF Health y Northwell Health desarrollaron prototipos utilizando las impresoras 3D de Formlabs y resinas biocompatibles y esterilizables en autoclave. Solo 12 días después de la idea inicial, el diseño final se aprobó para su uso clínico y el archivo 3D se puso a disposición de otros sistemas sanitarios de todo el mundo. Junto con el archivo, los colaboradores desarrollaron un proceso de trabajo detallado con instrucciones para los usuarios cualificados con las que imprimir los hisopos y asegurar la salud y la seguridad de los pacientes.
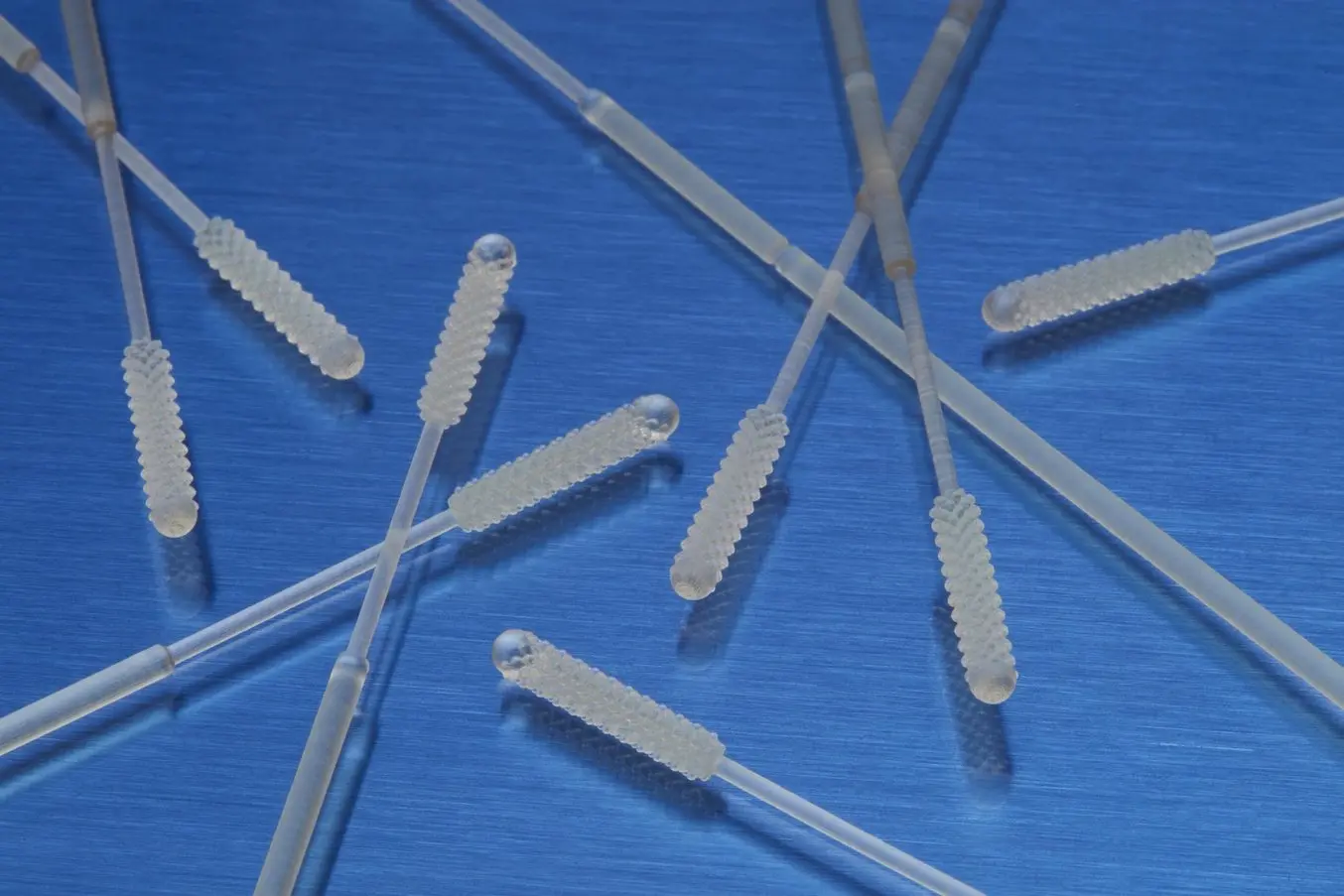
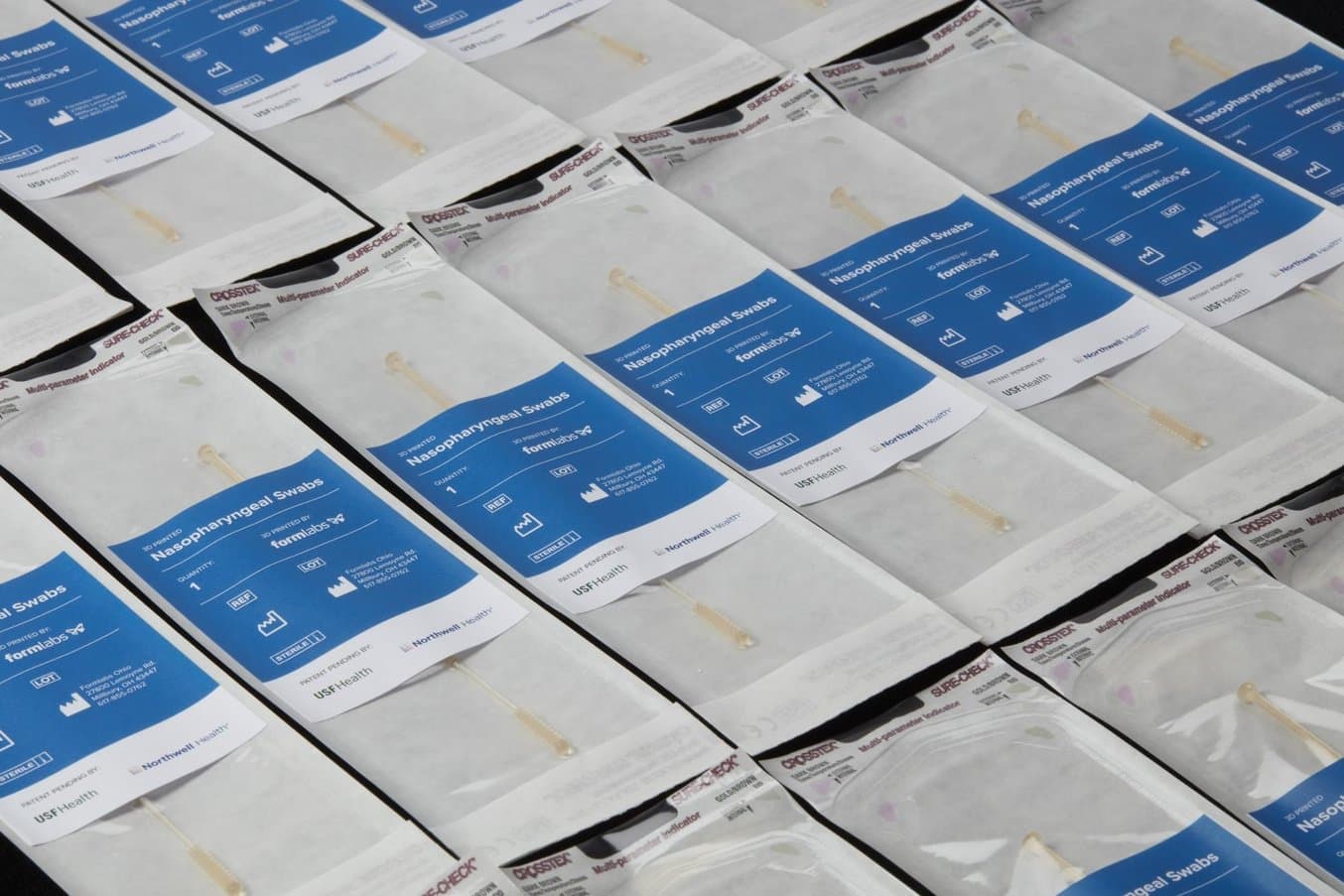
Los hisopos impresos en 3D hicieron posibles más de 70 millones de test de COVID en 25 países en las etapas tempranas de la pandemia de COVID-19.
Los hospitales, laboratorios dentales y centros médicos académicos que habían estado utilizando sus impresoras 3D para fabricar dispositivos quirúrgicos a medida para los pacientes pudieron cambiar sus objetivos y llenar el vacío en sus propias cadenas de suministro produciendo in situ hisopos impresos en 3D. Con el diseño accesible, el equipo asequible y los procesos validados que se utilizaron, el diseño de hisopo hizo posible realizar más de 70 millones de test de COVID en 25 países.
Otras soluciones para satisfacer la necesidad de más respiradores incluían la conversión de máquinas de presión positiva de dos niveles en las vías respiratorias (BiPAP) que se utilizan normalmente para tratar la apnea del sueño. Una conversión con éxito requiere utilizar un adaptador BiPAP que transforme estás máquinas en respiradores mecánicos invasivos.
Para garantizar que se crearan rápidamente suficientes adaptadores BiPAP para proporcionar a los pacientes asistencia respiratoria, Northwell Health, uno de los proveedores de servicios sanitarios más grandes de Nueva York, diseñó adaptadores BiPAP imprimibles en 3D. La Administración de Medicamentos y Alimentos Americana (FDA) concedió a Formlabs una Autorización de Uso de Emergencia (EUA) para imprimir en 3D estos adaptadores para apoyar a centros sanitarios mientras los respiradores tradicionales no estaban disponibles.
Procesos de impresión 3D para dispositivos médicos
En lo que respecta a imprimir en 3D dispositivos médicos, no todos los métodos dan el mismo resultado. Es importante elegir la tecnología de impresión 3D adecuada para casos de uso específicos.
Las tecnologías de impresión 3D más populares para los dispositivos médicos incluyen la estereolitografía (SLA), el sinterizado selectivo por láser (SLS) y el modelado por deposición fundida (FDM) para las piezas de plástico y el sinterizado directo de metal por láser (DMLS) y la fusión selectiva por láser (SLM) para los metales.
Estereolitografía (SLA)
Las impresoras 3D SLA usan un láser para curar resina líquida y convertirla en plástico endurecido en un proceso conocido como fotopolimerización. La SLA es uno de los procesos más populares entre los profesionales de la medicina por su alta resolución, su precisión y la versatilidad de sus materiales.
-
Ventajas de la SLA
Las piezas realizadas mediante SLA tienen la mayor resolución y precisión, los detalles más nítidos y el acabado más liso de todas las tecnologías de impresión 3D. Sin embargo, la principal ventaja de la SLA reside en su versatilidad. Las fórmulas de resina para SLA ofrecen una gran variedad de propiedades ópticas, mecánicas y térmicas capaces de igualar las de los termoplásticos estándar, industriales y para ingeniería.
La impresión por SLA es una excelente opción para prototipos de dispositivos médicos con un alto nivel de detalle que requieren una escasa tolerancia y superficies lisas, así como para moldes, utillaje, patrones, modelos médicos y piezas de uso final funcionales. La SLA también ofrece la selección más amplia de materiales biocompatibles para aplicaciones médicas y odontológicas. Con la Draft Resin, las impresoras SLA de Formlabs son además la opción más rápida para imprimir en 3D prototipos de gran tamaño, hasta diez veces más rápido que el FDM.
-
Desventajas de la SLA
La gran versatilidad de la SLA hace que su precio sea ligeramente más caro que el del FDM pero sigue siendo más asequible que cualquier otro proceso de impresión 3D. Las piezas de resina para SLA también requieren un posacabado después de la impresión, que incluye lavar las piezas y poscurarlas.
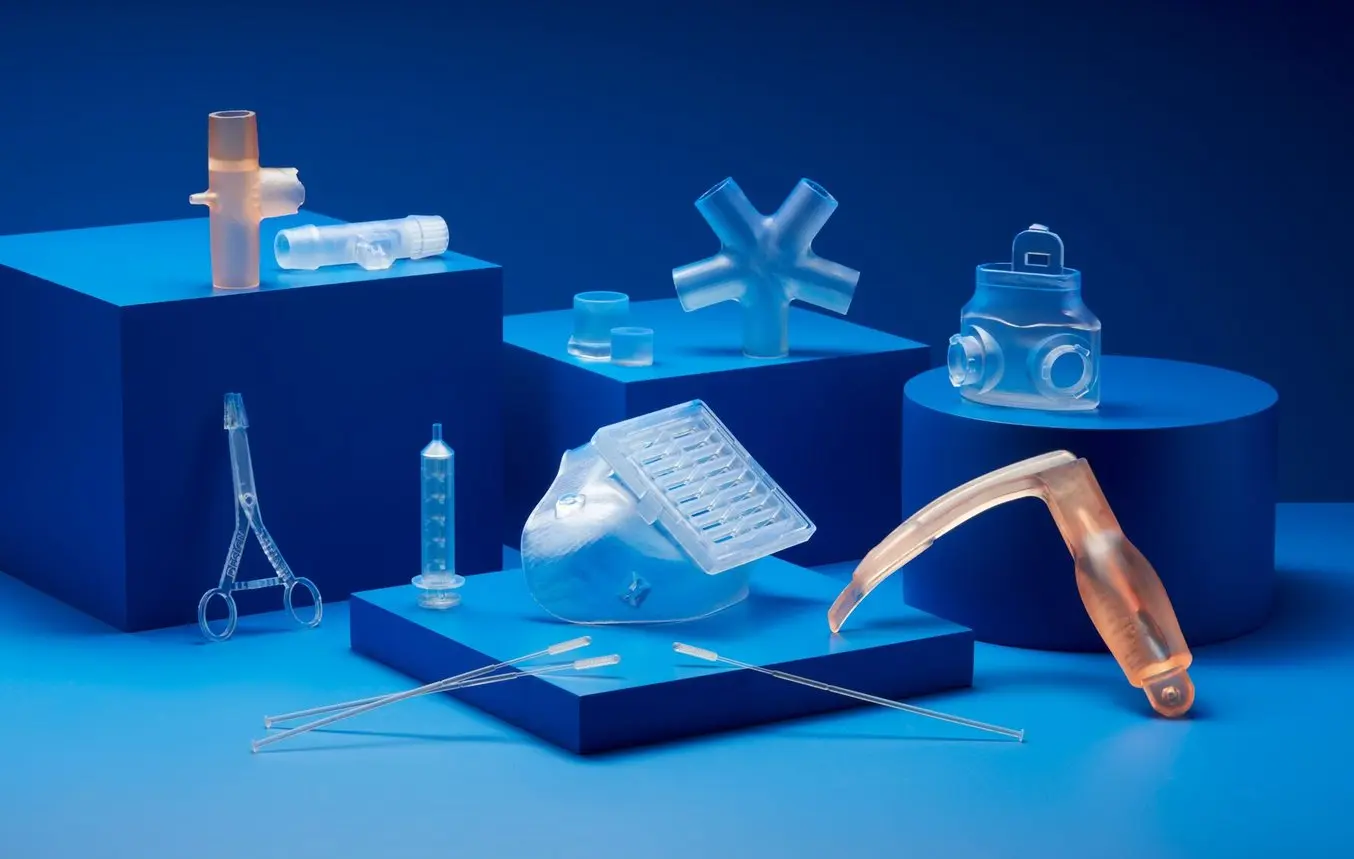
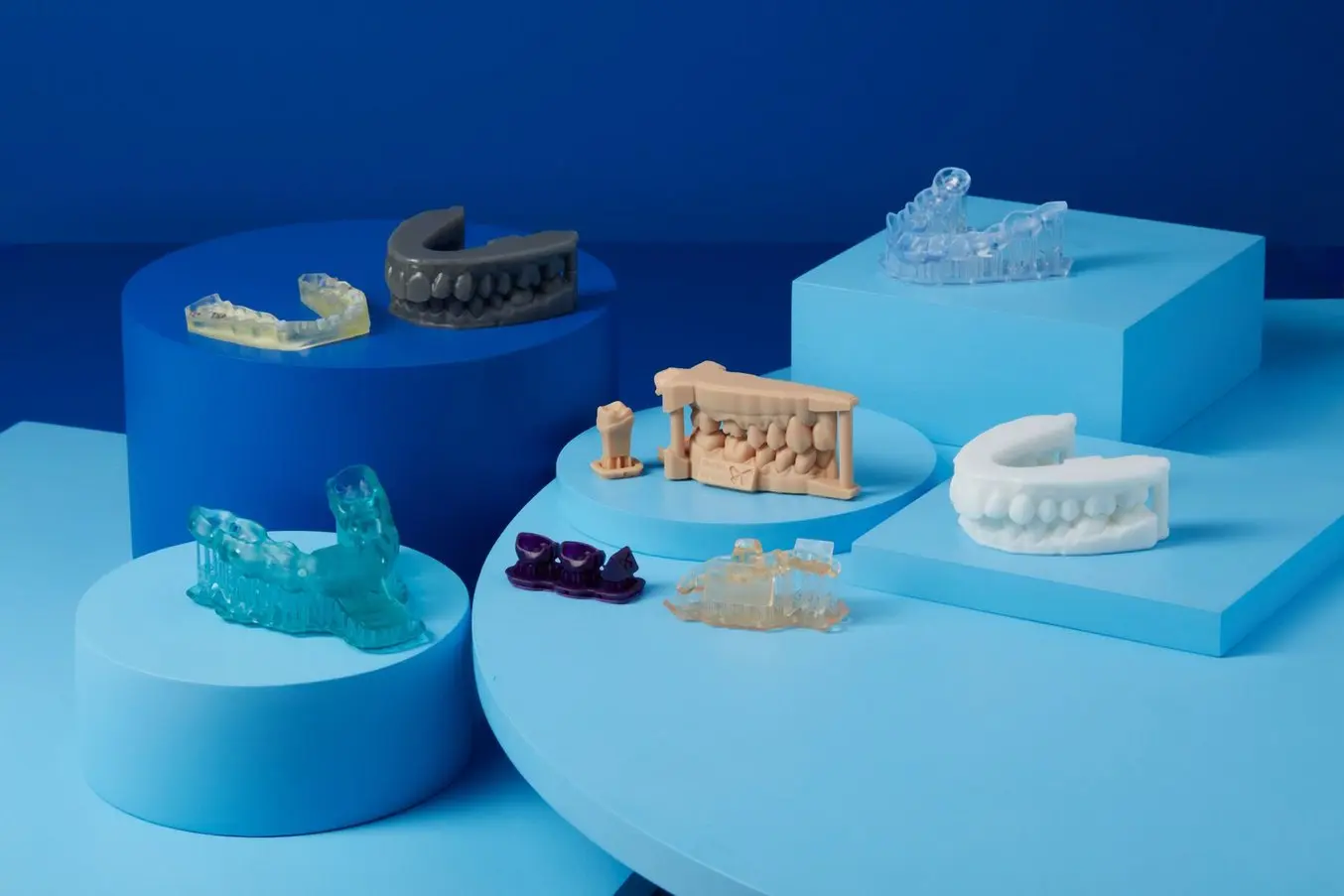
La impresión 3D SLA ofrece una amplia selección de materiales de impresión 3D, incluidos materiales biocompatibles, para diversas aplicaciones médicas y odontológicas.
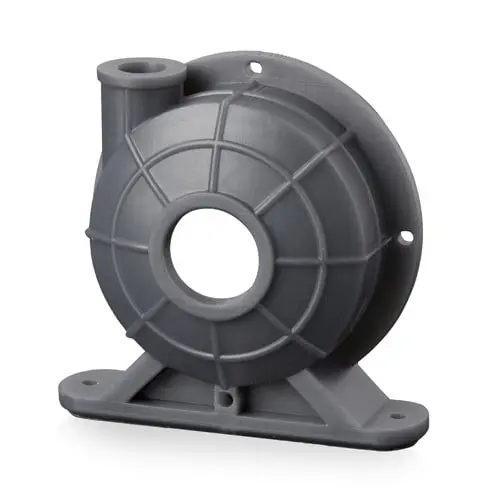
Solicita una muestra gratuita
Experimenta la calidad de Formlabs de primera mano. Enviaremos una pieza de muestra gratuita a tu lugar de trabajo.
Sinterizado selectivo por láser (SLS)
Las impresoras 3D SLS usan un láser de alta potencia para fundir pequeñas partículas de polvo de polímero. El polvo sin fundir sirve como soporte para la pieza durante la impresión y elimina la necesidad de agregar expresamente estructuras de soporte, por lo que el SLS es una opción especialmente eficaz para piezas mecánicas complejas.
La capacidad del SLS para producir piezas con excelentes capacidades mecánicas lo convierte en la tecnología de fabricación aditiva con polímeros más común para aplicaciones industriales. En función del material, las piezas de nylon de SLS también pueden ser biocompatibles y esterilizables.
-
Ventajas del SLS
Dado que la impresión por SLS no requiere estructuras de soporte específicas, es ideal para geometrías complejas, como relieves interiores, socavados, paredes delgadas y negativos de piezas. Las piezas producidas mediante SLS tienen excelentes características mecánicas, con una resistencia similar a la de las piezas moldeadas por inyección.
El material más común para SLS es el nylon, un popular termoplástico para ingeniería con excelentes propiedades mecánicas. El nylon es ligero, resistente y flexible, así como estable frente a impactos, productos químicos, calor, luz UV, polvo y suciedad. Las piezas de nylon impresas en 3D también pueden ser biocompatibles y no sensibilizantes, lo que significa que pueden estar listas para llevarlas como prendas y son seguras de usar en muchos contextos.
La combinación de un bajo coste por pieza, una alta productividad, materiales establecidos y biocompatibilidad hace que el SLS sea una elección popular entre los desarrolladores de dispositivos médicos para la creación de prototipos funcionales y una alternativa rentable al moldeo por inyección para la fabricación limitada o el lanzamiento rápido de productos (conocido como bridge manufacturing).
-
Desventajas del SLS
Las impresoras 3D SLS tienen un precio de entrada más alto que las tecnologías de FDM o SLA. Aunque el nylon es un material versátil, el catálogo de materiales para el SLS es más limitado que para el FDM y la SLA. Las piezas salen de la impresora con un acabado de la superficie ligeramente rugoso, por lo que requieren un granallado para obtener un acabado liso.

La impresión 3D SLS es ideal para prototipos funcionales resistentes y piezas de uso final, como prótesis y órtesis.
Modelado por deposición fundida (FDM)
El FDM, también conocido como fabricación con filamento fundido (FFF), construye piezas derritiendo y extruyendo un filamento termoplástico que un extrusor deposita capa por capa en el área de impresión.
El FDM es la forma más extendida de impresión 3D al alcance del consumidor, fomentada por la aparición de las impresoras 3D para aficionados. Sin embargo, las impresoras FDM industriales también son populares entre los profesionales.
-
Ventajas del FDM
La impresión por FDM funciona con varios termoplásticos estándar, como el acrilonitrilo butadieno estireno (ABS), el ácido poliláctico (PLA) y sus diversas mezclas. Esto genera un precio inicial y de los materiales más bajo. El FDM se ajusta mejor a modelos de prueba de concepto básicos y a la creación de prototipos de bajo coste para piezas sencillas. Algunas materiales de FDM también son biocompatibles.
-
Desventajas del FDM
El FDM es la técnica que menor resolución y precisión tiene comparada con otras tecnologías de impresión 3D para plástico como la SLA y el SLS. No es la mejor opción para imprimir diseños complejos o piezas con relieves complicados. Obtener un acabado de gran calidad requiere procesos de pulido químicos y mecánicos en los que hay que invertir mucho tiempo y mano de obra. Algunas impresoras 3D FDM industriales usan soportes solubles para mitigar algunos de estos inconvenientes y ofrecen una mayor variedad de termoplásticos para ingeniería, pero estos tienen un precio elevado. Además, el FDM tiende a ser más lento al crear impresiones grandes que la SLA o el SLS.
Sinterizado directo de metal por láser (DMLS) y fusión selectiva por láser (SLM)
Las impresoras 3D de sinterizado directo de metal por láser (DMLS) y fusión selectiva por láser (SLM) funcionan de forma parecida a las impresoras SLS, pero en lugar de fundir polímeros en polvo, unen partículas de polvo metálico capa a capa utilizando un láser.
Las impresoras 3D DMLS y SLM pueden crear productos de metal resistentes, precisos y complejos, lo que hace este proceso ideal para diversas aplicaciones sanitarias.
-
Ventajas del DMLS y la SLM
La mayor ventaja de estos procesos son los materiales, obviamente, ya que las impresoras 3D DMLS y SLM son capaces de producir dispositivos de médicos y componentes de uso final a partir de metal. Estos procesos pueden reproducir geometrías complejas y los productos acabados son resistentes, duraderos y biocompatibles. Se pueden utilizar para fabricar implantes genéricos (de cadera, rodilla, vertebrales, etc.), implantes a medida para el tratamiento de tumores y traumatismos, prótesis dentales y productos de tecnología médica y ortopédica.
-
Desventajas del DMLS y la SLM
Mientras que los precios de las impresoras 3D de metal han empezado a bajar, con costes que van de 200 000 $ a más de un millón de dólares, estos sistemas siguen sin ser accesibles para la mayoría de los negocios. Los procesos de impresión 3D de metal también conllevan un proceso de trabajo arduo y complejo.
Por otro lado, la impresión 3D SLA es adecuada para procesos de trabajo de fundición que produzcan piezas de metal a bajo coste, con una mayor libertad de diseño y en menos tiempo que con los métodos tradicionales.
Compara los procesos de impresión 3D para dispositivos médicos
La siguiente tabla muestra las tecnologías de impresión 3D que están mejor equipadas para ocuparse de las distintas aplicaciones de los dispositivos médicos impresos en 3D.
Estereolitografía (SLA) | Sinterizado selectivo por láser (SLS) | Modelado por deposición fundida (FDM) | Impresión 3D de metal (DMLS, SLM) | |
---|---|---|---|---|
Volumen de impresión | Hasta 300 × 335 × 200 mm (impresoras 3D de escritorio y de trabajo) | Hasta 165 × 165 × 300 mm (impresoras 3D de trabajo industriales) | Hasta 300 × 300 × 600 mm (impresoras 3D de escritorio y de trabajo) | Hasta 400 × 400 × 400 mm (DMLS/SLM industrial de gran tamaño) |
Gama de precios | Desde 3500 $ | Desde 16 500 $ | Desde 2500 $ | Desde 200,000 $ |
Materiales | Variedades de resina (plásticos termoendurecibles). Resinas estándar, para ingeniería (similares al ABS, al polipropileno y a la silicona; flexibles, resistentes a la temperatura, rígidas), para aplicaciones de fundición, dentales y médicas (biocompatibles). | Termoplásticos para ingeniería, normalmente el nylon y sus compuestos (el nylon es biocompatible y esterilizable). | Termoplásticos estándar, como el ABS, el PLA y sus diversas mezclas. | Acero inoxidable, acero de herramientas, titanio, cromo-cobalto y aluminio. |
Aplicaciones ideales | Prototipos con un alto nivel de detalle que requieren una escasa tolerancia y superficies lisas, así como moldes, utillaje, patrones, modelos médicos, piezas funcionales y dispositivos médicos y odontológicos de uso final. | Geometrías complejas, prototipos funcionales, órtesis, prótesis, fabricación en series cortas o lanzamiento rápido de productos. | Modelos de prueba de concepto básicos, creación de prototipos de bajo coste para piezas sencillas. | Piezas resistentes y duraderas con geometrías complejas, implantes, prótesis dentales, componentes médicos y ortopédicos hechos de metal. |
Biocompatibilidad de los materiales de impresión 3D
En función de la aplicación deseada, es posible que sean necesarias piezas biocompatibles para los dispositivos médicos. Presentar la información de biocompatibilidad es obligatorio para solicitudes 510(k) y autorizaciones provisionales de registro (PMA) en Estados Unidos, así como para otros certificados reglamentarios en otros países. Certifica que el dispositivo será compatible con el sistema biológico al que está destinado. Si la información no existe o es inadecuada, puede haber retrasos considerables a la hora de lanzar el producto al mercado.
Los requisitos para ensayos de biocompatibilidad se deberían determinar en función del uso previsto del dispositivo (tipo, área y duración de la exposición). Determinar los requisitos de ensayo al principio del proceso de desarrollo permitirá que haya tiempo más que suficiente para completar los ensayos antes de la solicitud a los organismos normativos. Debería partir del contacto esperado entre el dispositivo y el cuerpo humano.
El contacto se suele definir mediante tres categorías diferentes:
-
Contacto directo: entra en contacto físico con el paciente.
-
Contacto indirecto: entra en contacto físico con un fluido, gas u otro material que está en contacto directo con el paciente.
-
Sin contacto: No tiene un contacto directo o indirecto con el paciente y, por consiguiente, está exento de los requisitos de biocompatibilidad.
Algunos fabricantes de impresoras 3D y materiales de impresión 3D, como Formlabs, realizan ensayos de biocompatibilidad basándose en las Normas ISO 10993, ISO 18562 e ISO 7405 y publican la información sobre los materiales pertinentes.
Dado que los ensayos se realizan con muestras impresas normalizadas, los fabricantes son responsables de seguir las instrucciones de impresión y posacabado y de validar de forma independiente la biocompatibilidad de sus respectivas piezas.
Aprobación reglamentaria de dispositivos médicos impresos en 3D
Los dispositivos médicos impresos en 3D deben cumplir las normativas vigentes en sus respectivas ubicaciones.
Parte de este proceso consiste en establecer un sistema de gestión de la calidad compuesto por una base de reglas, procedimientos, formularios e instrucciones de trabajo, junto con su secuencia, interacciones y recursos necesarios para realizar negocios como una empresa de productos sanitarios.
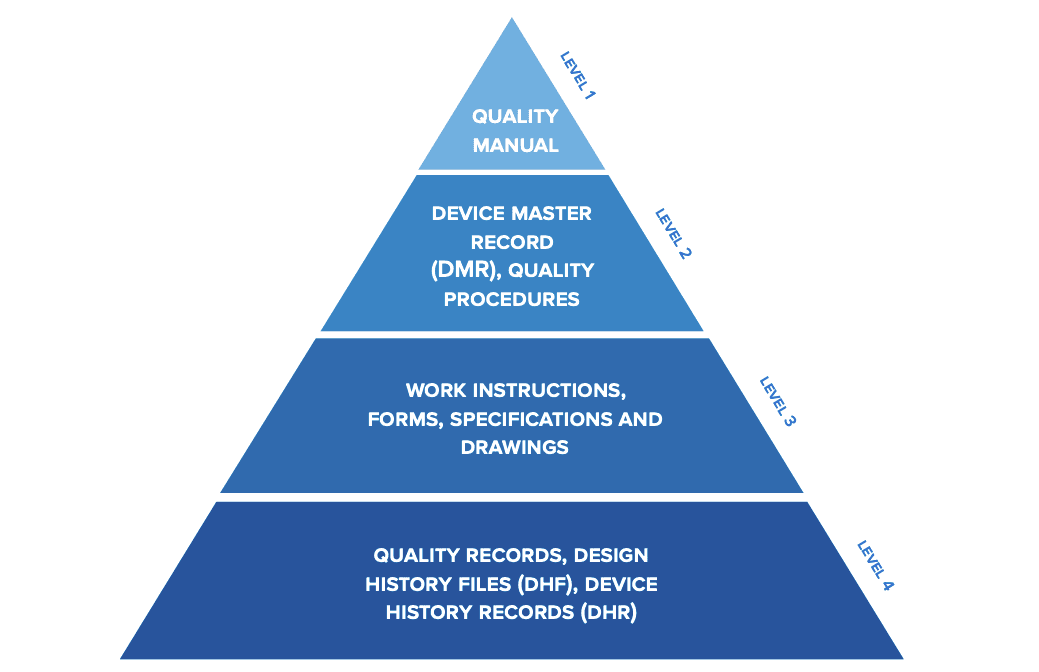
Ejemplo de una jerarquía de sistema de gestión de la calidad.
Los registros de calidad son documentación que demuestra que el sistema de gestión de la calidad está funcionando y describe cómo tu empresa aborda las normativas relativas a dispositivos médicos. La FDA define las reglas en el apartado 820 del capítulo 21 del documento CFR. Si planeas entrar en el mercado estadounidense, es necesario seguir estas normativas.
Fuera de EE. UU., Europa requiere que se establezca un sistema de calidad para cumplir las normativas sobre dispositivos médicos (y/o normativas para productos sanitarios de diagnóstico in vitro). Muchas empresas de dispositivos médicos aplican un sistema de calidad certificado mediante la Norma ISO 13485:2016 para cumplir los requisitos de la UE.
Para informarte sobre los requisitos reglamentarios específicos, descarga nuestro libro blanco exhaustivo elaborado en colaboración con el socio de Formlabs Greenlight Guru, que incluye diversos recursos para apoyar a los usuarios en cada paso del proceso.
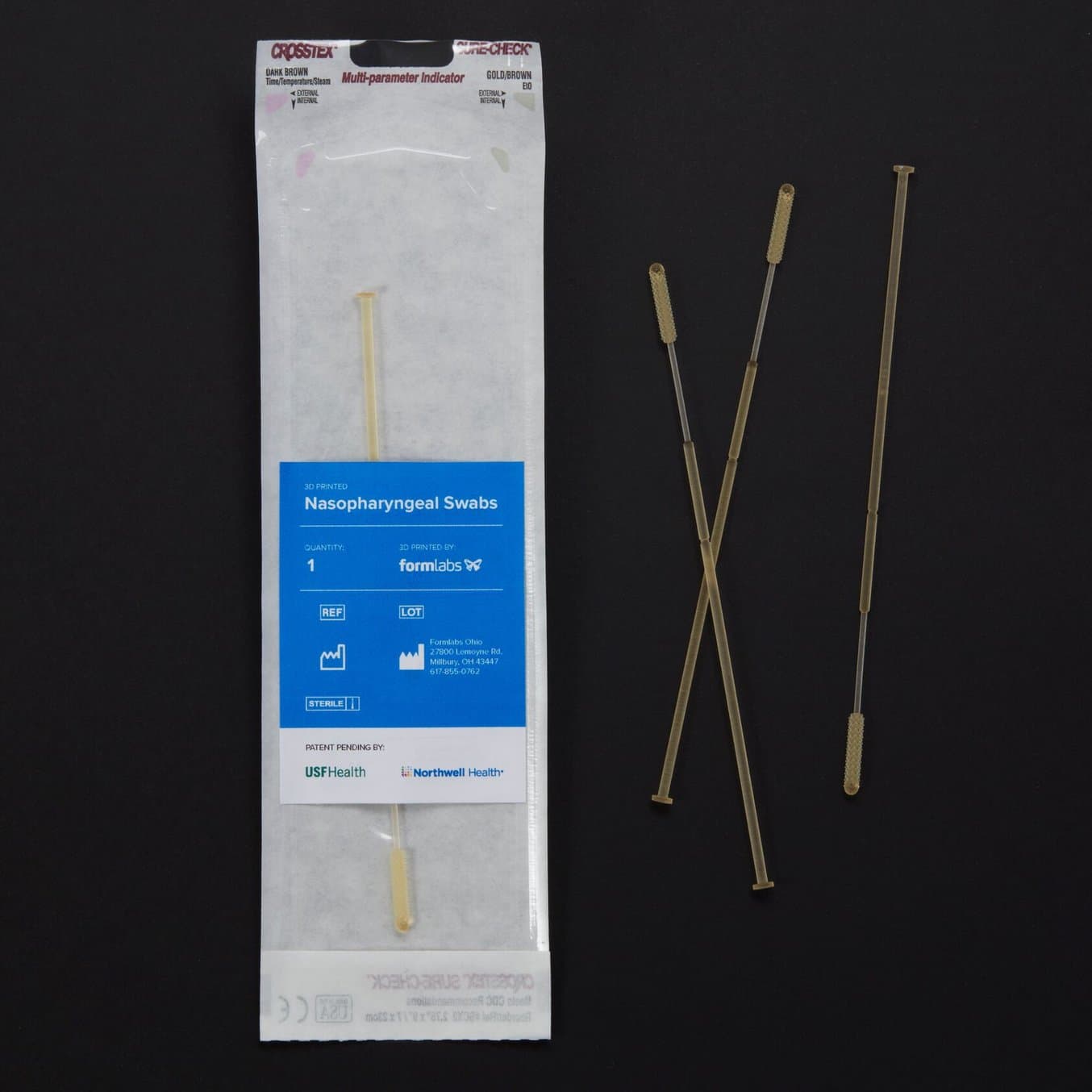
La guía definitiva de control de calidad y asuntos normativos para la impresión 3D médica
El objetivo de este libro blanco es guiar a los usuarios de la industria de los dispositivos médicos por cada etapa del proceso de desarrollo de productos, desde la evaluación de métodos de fabricación y tecnologías de impresión 3D hasta requisitos normativos para la comercialización de dispositivos médicos de uso final impresos en 3D.
Empieza a imprimir en 3D dispositivos médicos
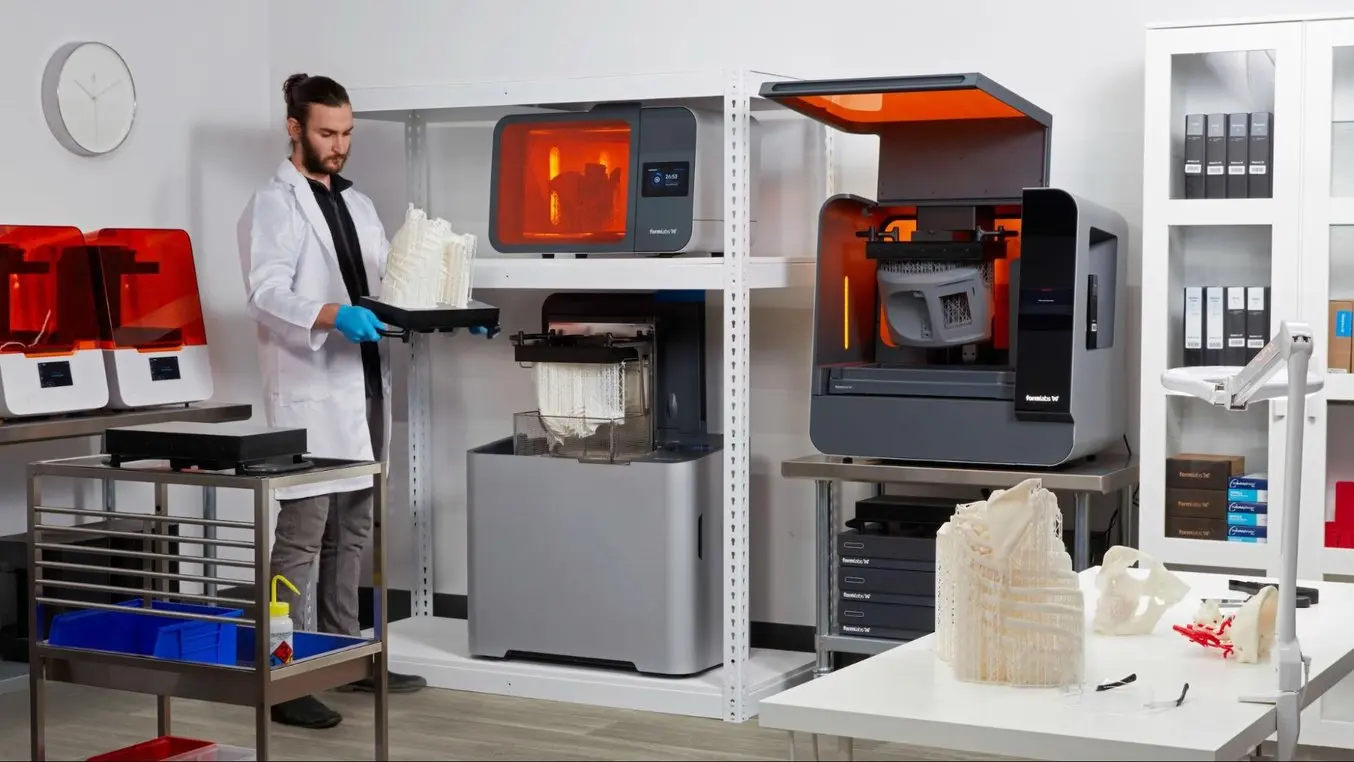
Para las empresas de dispositivos médicos, la impresión 3D in situ permite realizar ciclos de iteración rápidos, acortando el ciclo de desarrollo de productos y creando más tiempo para soluciones creativas.
Todos los centros médicos deberían tener acceso a las herramientas más modernas para mejorar la asistencia y proporcionar la mejor experiencia posible para el paciente. Comienza ya a usarlas o expande la producción de tus instalaciones con Formlabs, un socio fiable que está a la vanguardia de la impresión 3D médica.
Ponte en contacto con nuestros expertos médicos para saber más acerca de cómo la impresión 3D puede complementar tu actual proceso de diseño y fabricación de dispositivos médicos.