Across industries, 3D printing technology is a natural ally of creativity, bringing new freedom to the processes of design and fabrication. It is fitting, then, that we are seeing artists beginning to take note and leverage the unique qualities of the technology to create 3D printed art.
The design freedom granted by layer-by-layer fabrication and the versatility of 3D printable materials are opening up new frontiers for all kinds of artists. Affordable 3D printing technologies are contributing to innovation in design and scale within fields like sculpture, fashion, and installation art as well as collaborations across disciplines.
Read on to learn about five ways in which digital technologies are giving rise to new opportunities for artists in the design, production, and even the restoration of art.
1. Making Impossible Designs Possible
The ability to accurately render complex designs is one of the greatest assets of 3D printing. It’s already revolutionizing the jewelry market, for example. And that’s just the start. Elements like actuators, LEDs, and audio devices can be embedded into the fabric of 3D printed art pieces with new degrees of responsivity.
The possibility of direct manufacturing and freeform modeling means that highly customized pieces can be created and executed with fewer limitations than traditional methods. Below, you can see a detail of Philip Beesley’s art piece “Sentient Veil,” an immersive, responsive architectural environment. The complexity of its multi-faceted design could never have been produced without digital fabrication technologies.
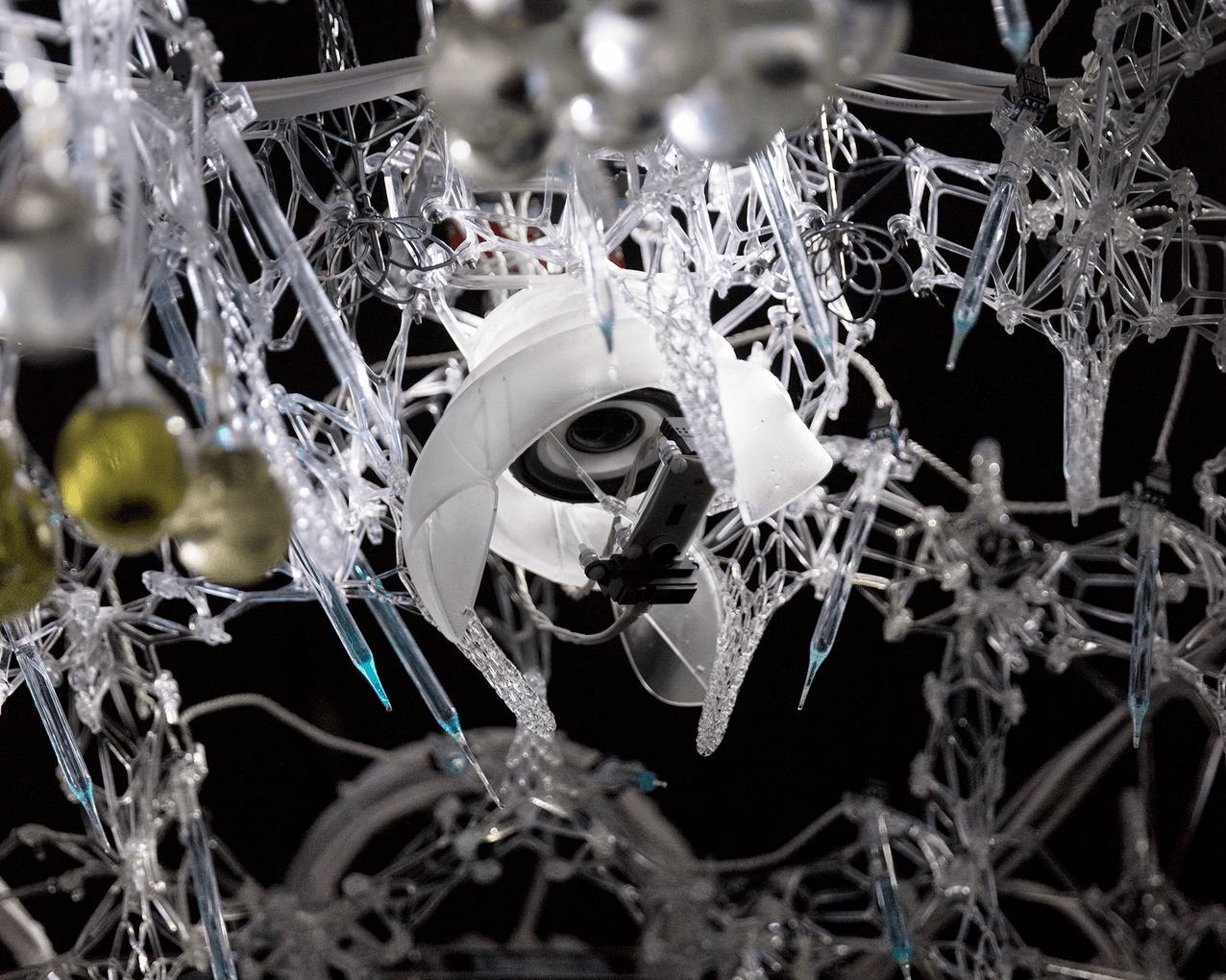
Speakers printed in Clear Resin on the Form 2 SLA 3D printer, as featured in “Sentient Veil.”
The world of fashion is another creative industry eagerly adopting 3D printing technologies.
Entire bespoke outfit designs have been inspired by and then successfully produced via 3D printing techniques. Aiman Akhtar, not a fashion designer but a professional 3D printing modeler, was able to take the exact measurements of a model using a digital scan before using CAD to design a striking, one-of-a-kind fashion piece. This is just one of many instances in which digital workflows are empowering individuals to create art outside of their usual field and beyond their prior capabilities.
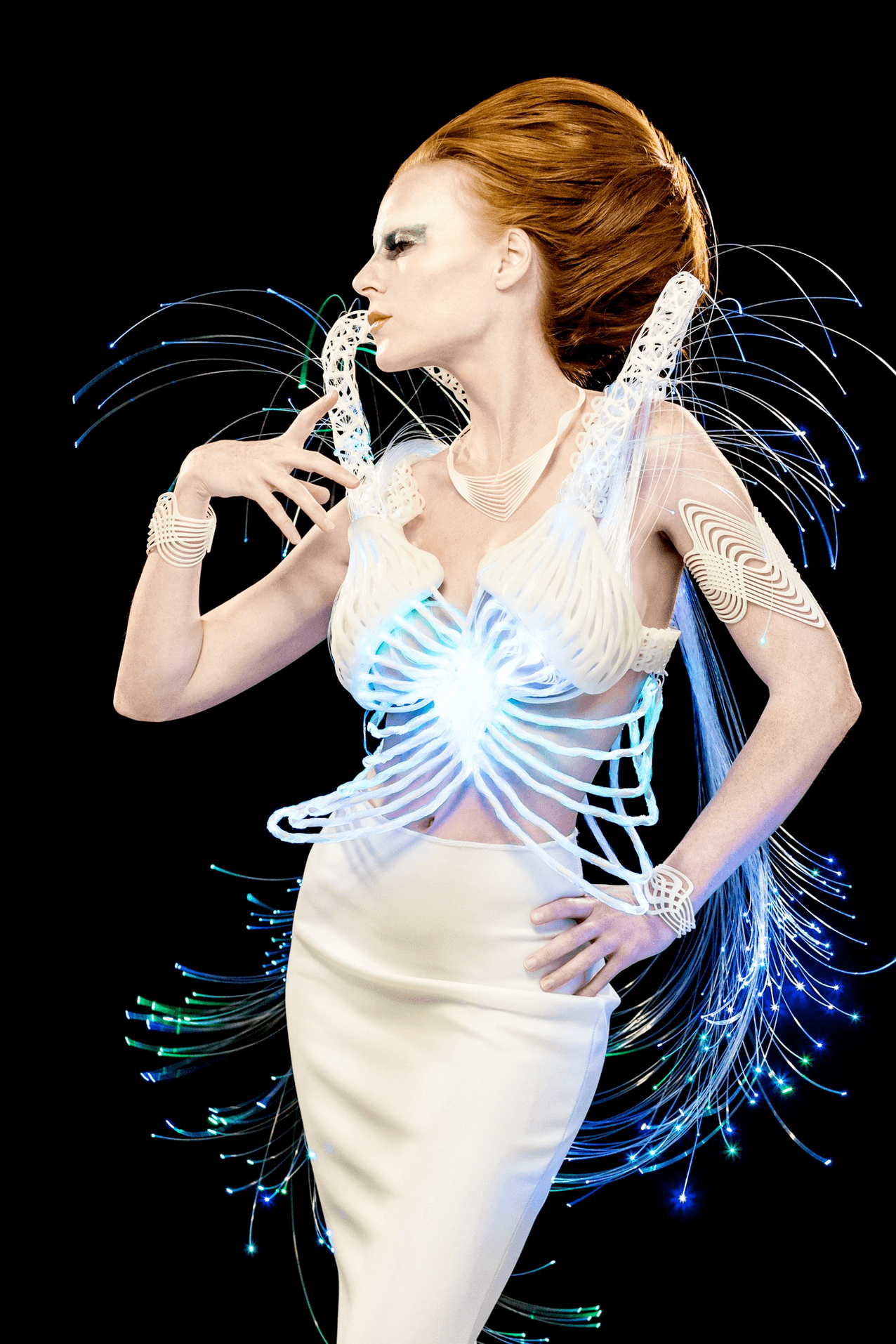
Aiman Akhtar’s outfit, designed for 3D World magazine, using digital scanning and 3D printing technologies.
Professional fashion designers like Mia Vilardo and Riccardo Polidoro of Miryaki are taking advantage of 3D printing as well. The fashion duo used Formlabs stereolithography (SLA) 3D printing technology to create clothing accessories that were later finished with gold and chrome plating.
Such technology is invaluable for industries where wowing clients is key to a designer's success. Polidoro has described his SLA 3D printer as “so precise that when I show a prototype to a client, they can hardly distinguish it from the real product.”
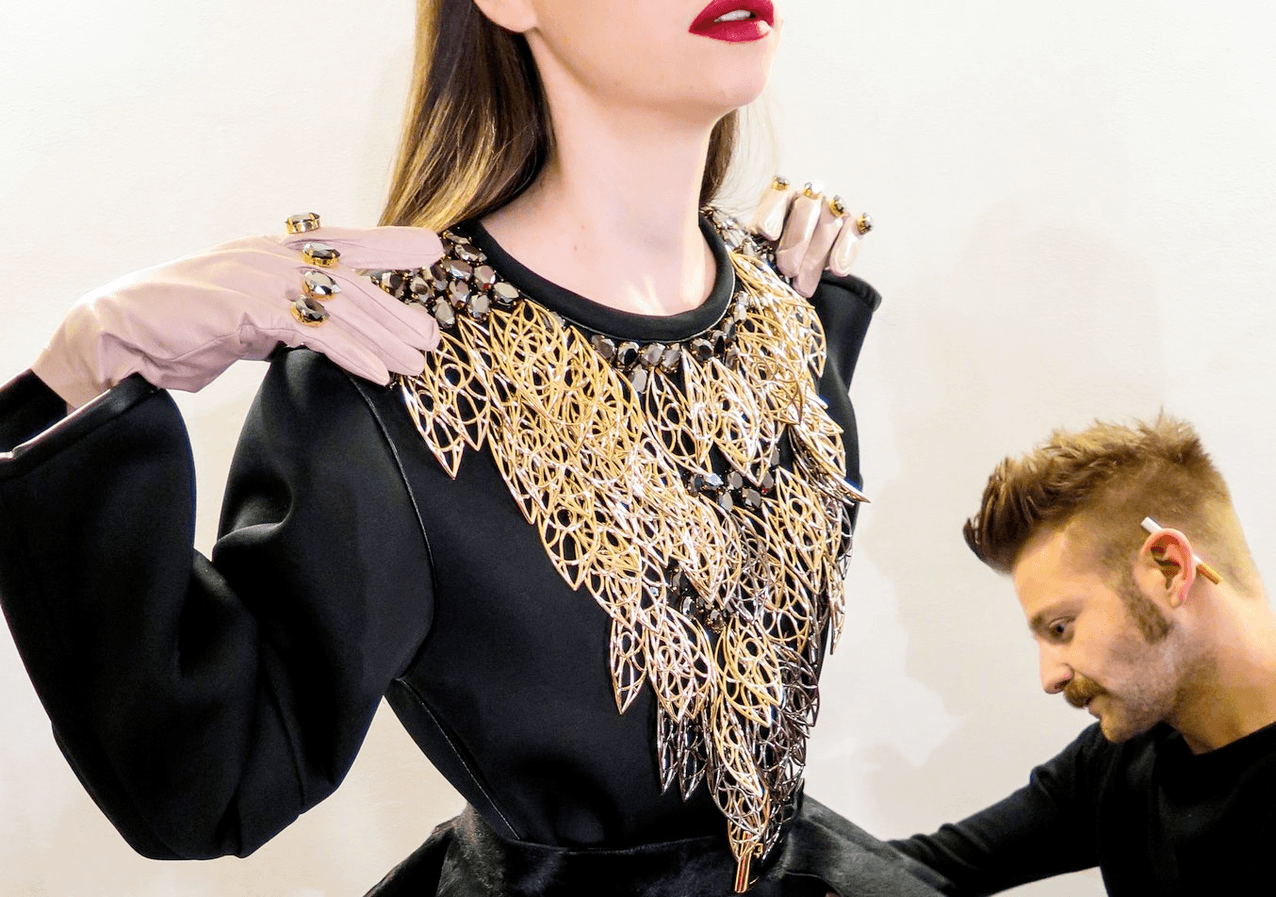
Leaves made of Clear Resin, finished with gold and chrome plating, as created by Miryaki with SLA 3D printing technology.
2. Escaping the Limitations of Size
Artists have often been held back in design and execution by issues of scale, both in creating very small and very large pieces. The detailing on small art pieces can only be so intricate and attempts at very large pieces can be impossible without expensive resources. The digital workflow removes some of these restrictions.
Jewelry, for example, is an industry with a growing reliance on 3D printing, enabling jewelry designers to create more intricate designs than could ever be achieved with handcrafting alone.
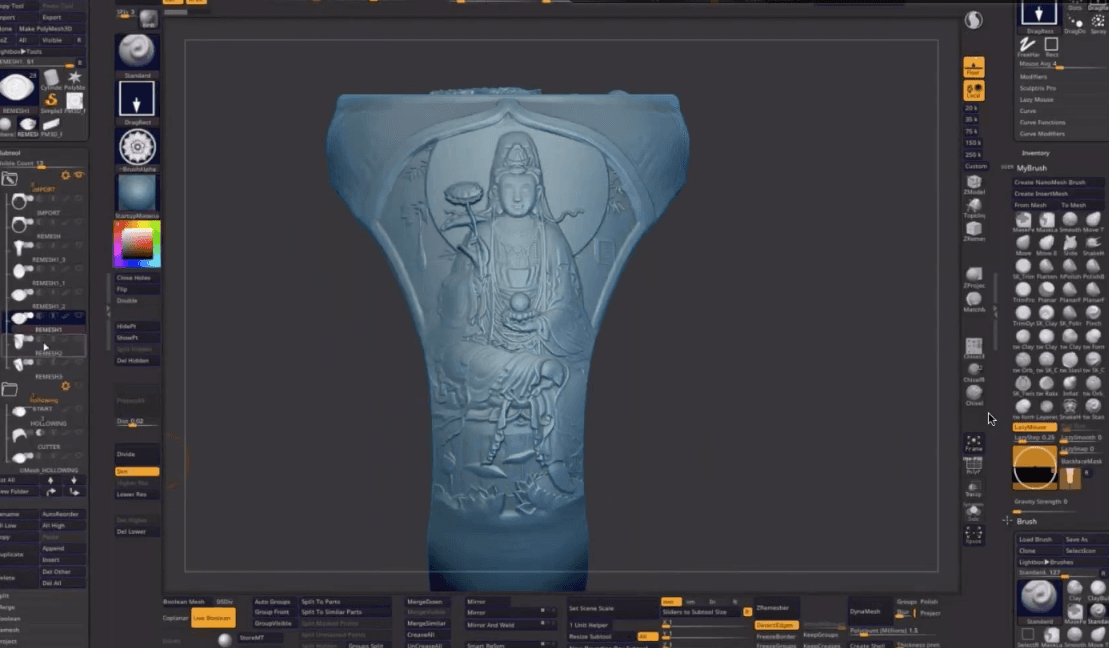
Detail of a jeweler customizing the design of a ring during the CAD design process.
Jewelry designs used to be restricted by the possibilities of hand carving. Thanks to a precisely controlled laser, SLA 3D printers can capture extraordinary design details—delicate filigrees, raised text, and detailed pavé stone settings—with amazing sharpness, giving designers much greater freedom when creating a new 3D printed art design.
3D printing’s equivalent ability to print larger structures of equivalent intricate complexity is ideal for installation artists.
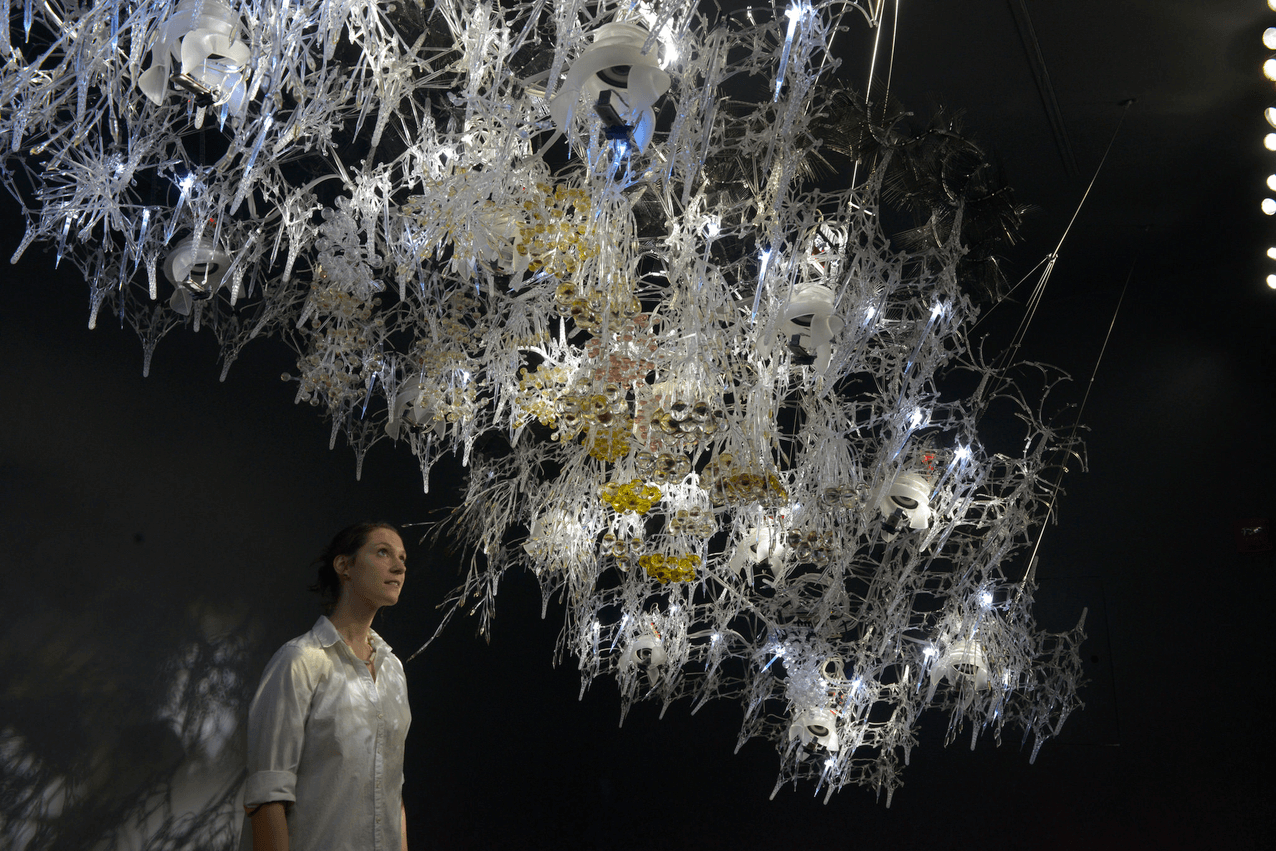
Philip Beesley used 3D printing to create short runs of highly-customized pieces for the speakers in “Sentient Veil”.
Philip Beesley is one example of an artist who has extensively integrated the workflow into his art. For the “Sentient Veil”, he was able to produce short runs of highly-customized pieces for the speakers embedded in the artwork accurately. Should he wish to create a larger installation next, he can print large parts in a single build with no assembly required by integrating space-saving design elements—like hinges, extending features, and moving parts—into his 3D model.
3. Raising Standards in Prototyping and Production
Artists using digital technologies are changing their approach to prototyping and production, whether they work with small or large media.
Many jewelers now use the same technology to customize pieces for customers by quickly creating prototypes in-house. The ease of preserving, accessing, and iterating through digitally stored designs make the production process less expensive for jewelers, too.
Artists looking to create many copies of smaller works find the ease and speed of digital prototyping a highly empowering manufacturing strategy. For example, jewelers and ceramics artists can cheaply and efficiently design, prototype, and produce large quantities of identical items, based on a single, easily—preserved design stored digitally.
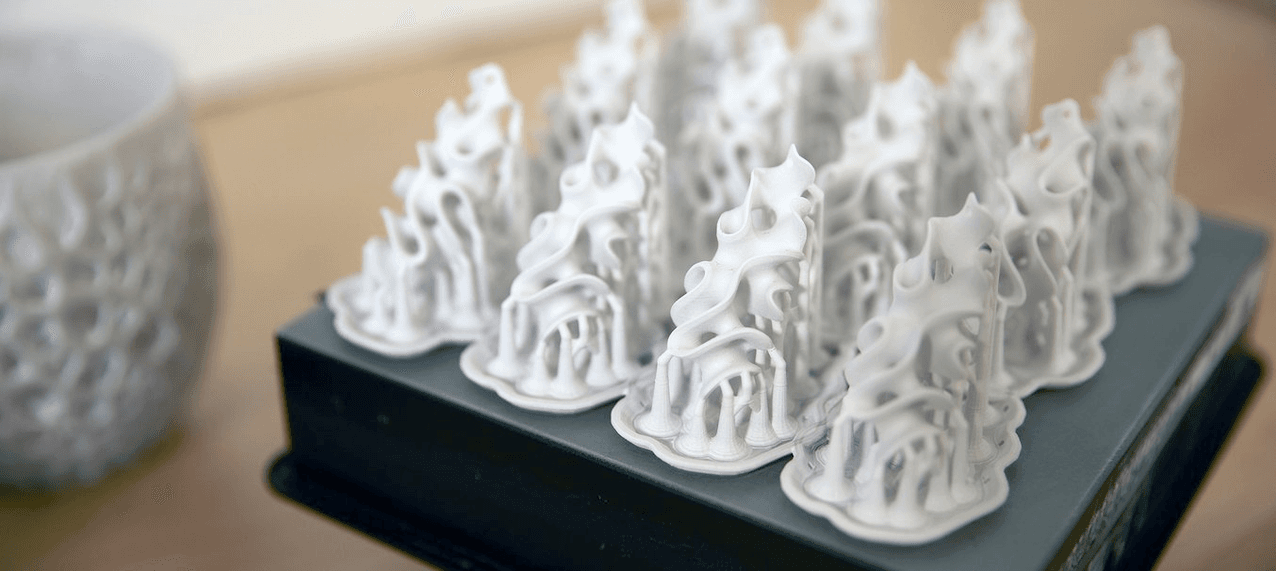
3D printing makes it easy to preserve, access, and iterate through digitally stored designs and produce complex parts at scale.
4. Erasing Boundaries Between Artistic Disciplines
Because 3D printing is so versatile and its use cases are so diverse, remarkable interdisciplinary pieces are being made with the technology as well. Nervous System’s “Porifera” project is one example.
Nervous System’s creates unique art, jewelry, and housewares through mash-ups of computer science, math, biology, and architecture. Their project takes inspiration from unlikely sources, like biological processes, which are then mapped into new forms using CAD and turned into ceramics using the unique Ceramic Resin material.
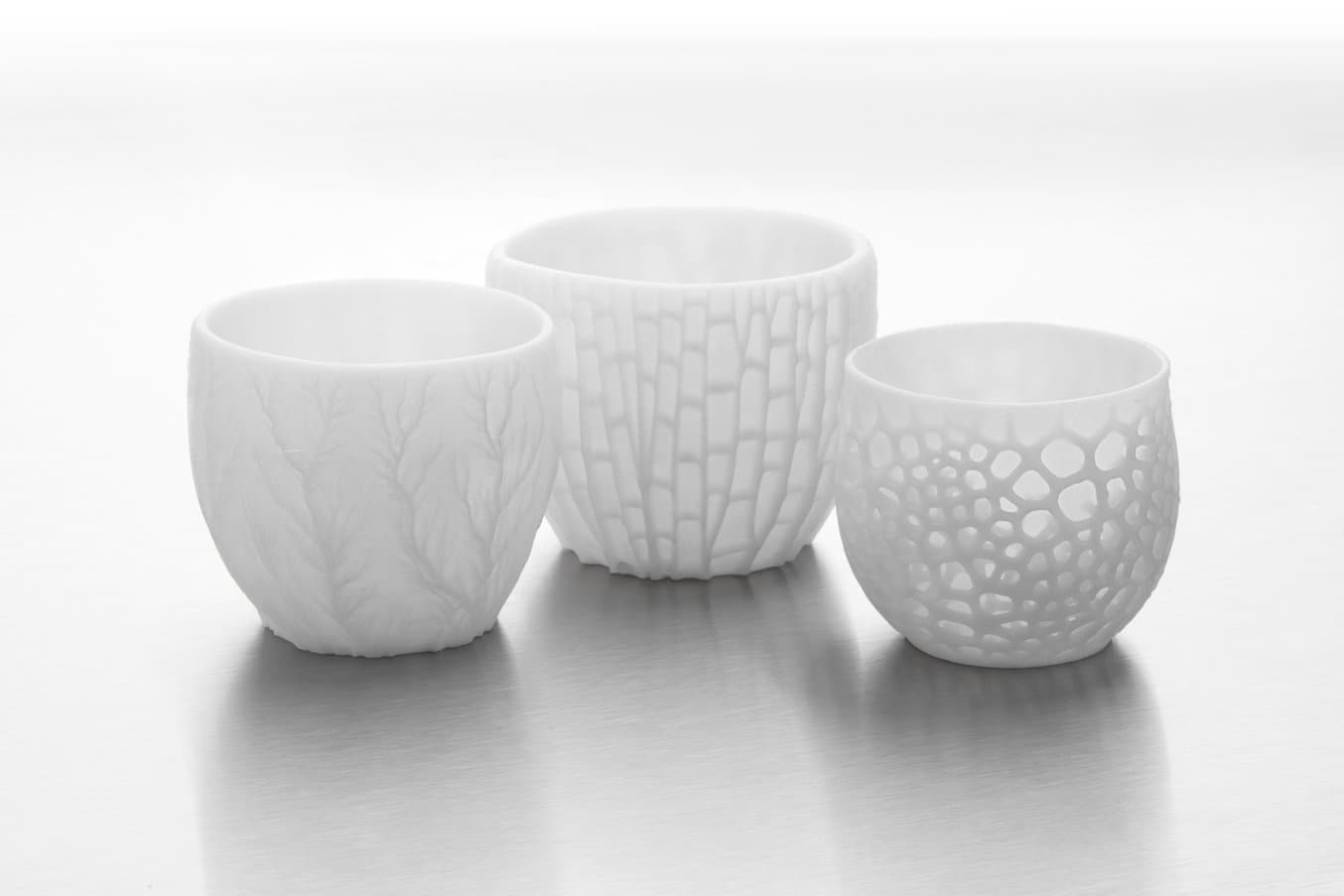
Nervous System used Ceramic Resin to create a cellular tea set. The intricate design would be impossible to create with traditional ceramic techniques.
Free of the restrictions imposed by the usual design and manufacturing techniques, even their most unusual geometric designs have structural integrity and durability when created using a 3D printer. Digital tools are the cornerstone of their project and proof that 3D printing can inform the entire ethos of an artistic project as well as influence its choice of production method.
Another notable interdisciplinary project enabled by the digital workflow is the work of Benjamin Dillenburger and Michael Hansmeyer. Founders of Digital Grotesque, the men combine their passions for architectural design and computing into 3D printed art. Their interactive grotto environments, inspired by Antoni Gaudi, were entirely 3D printed. The result is a perfect demonstration of the large yet intricate creations possible with 3D printing.
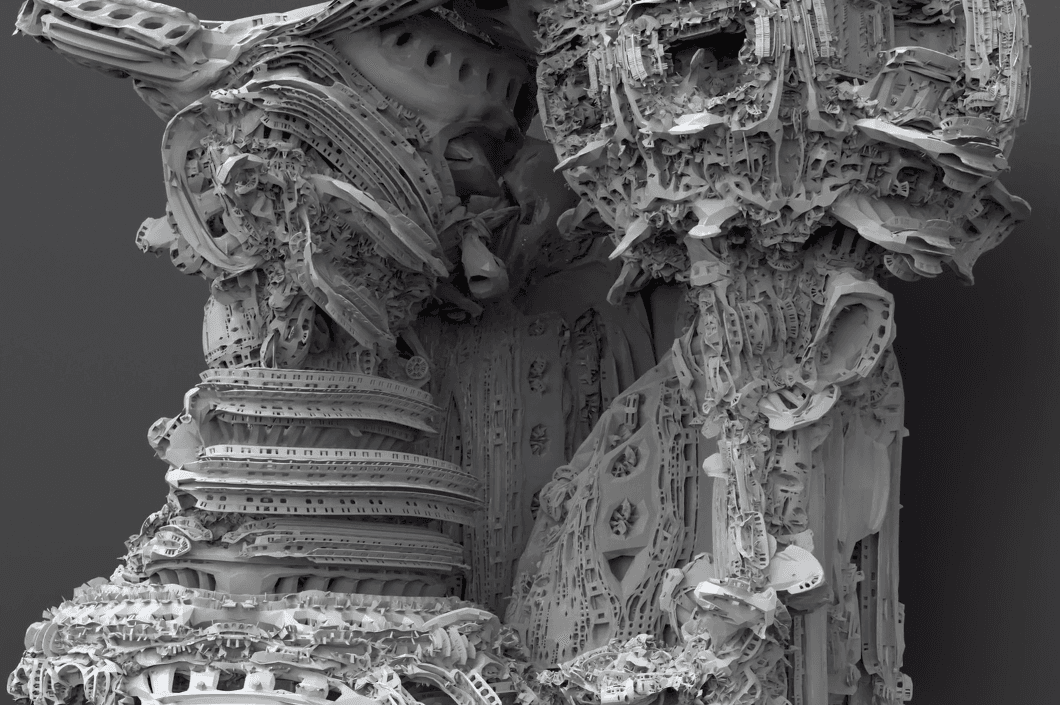
Detail of a CAD rendering of Digital Grotesque’s “Grotto II” (Source: digital-grotesque.com)
The materials used to create 3D printed art also vary widely. Resin varieties are used to great effect by Nervous System and Miryaki, while the Digital Grotesque grottoes were printed using five tons of sandstone.
5. Revolutionizing the Art Restoration Process
Digital technologies are not just for designing and producing entirely new creations. With them, formerly impossible restoration of historical artworks is becoming feasible.
First, art restorers use 3D scanning to evaluate antiques prior to restoration. They work with digital modeling software to recreate missing elements by using existing parts of the sculptures as a basis for subsequent restorations to minimize the risk of interpretation. Restorers then use 3D printing to create prototypes for quality control and pre-visualization, and also for final material restorations.
Thanks to this digital workflow, entirely new standards of accuracy are being established in restoration. Just as with the creation of original art, the digital tools adapt to both small-scale restorations (many of them too small and finely detailed, or based around no longer practiced crafts, to be restored manually) and large-scale ones.
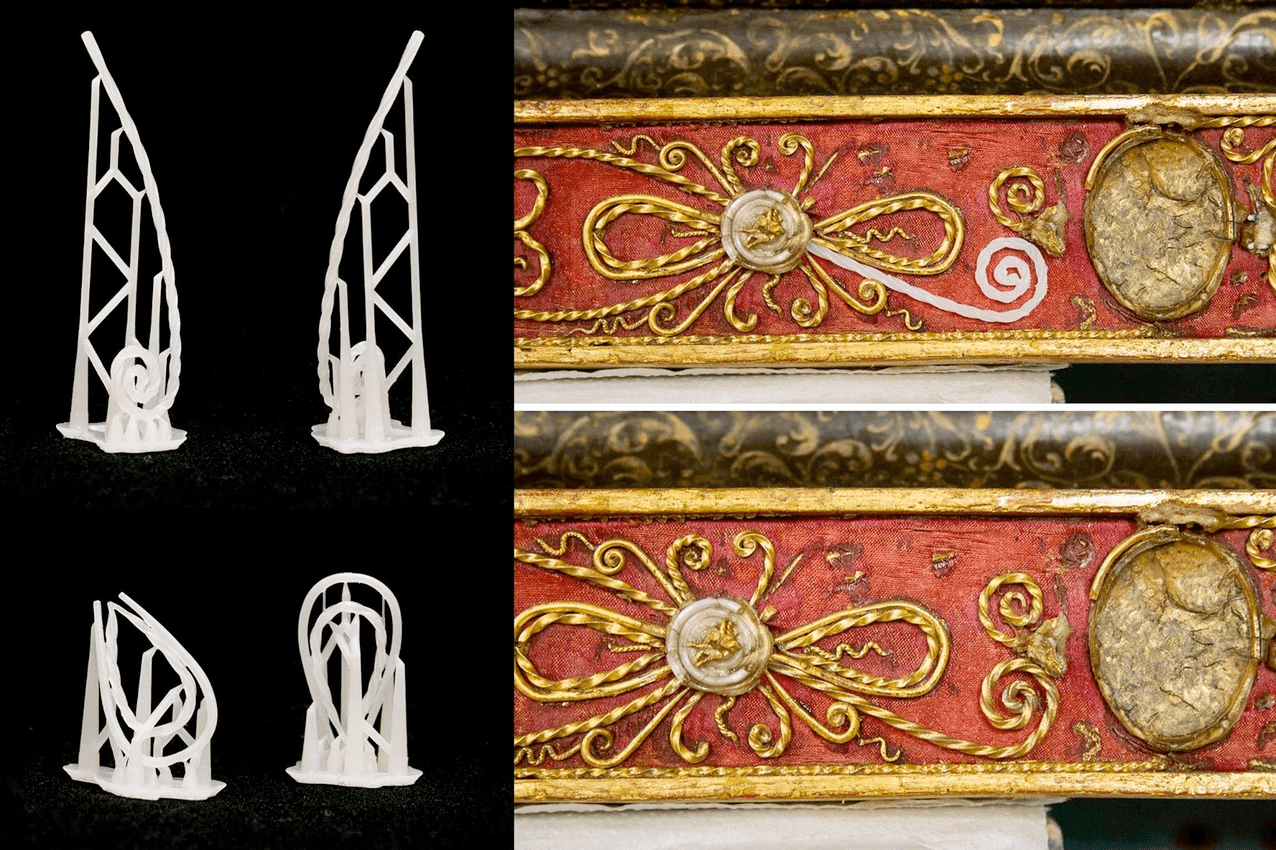
Missing pieces on this multi-material reliquary were designed via 3D scanning, then printed and painted to match the color of the artwork before being inserted.
We’re only now beginning to see just how valuable 3D printing technology can be to art technicians, sculptors, architects, and installation artists. More excitingly still, individuals from completely different backgrounds, like computer science or mathematics, are finding themselves empowered to create 3D printed art using these digital tools.
The technology’s ability to transcend barriers is one of its chief assets. Its increasing adoption will see more artistic dreams turned into realities.