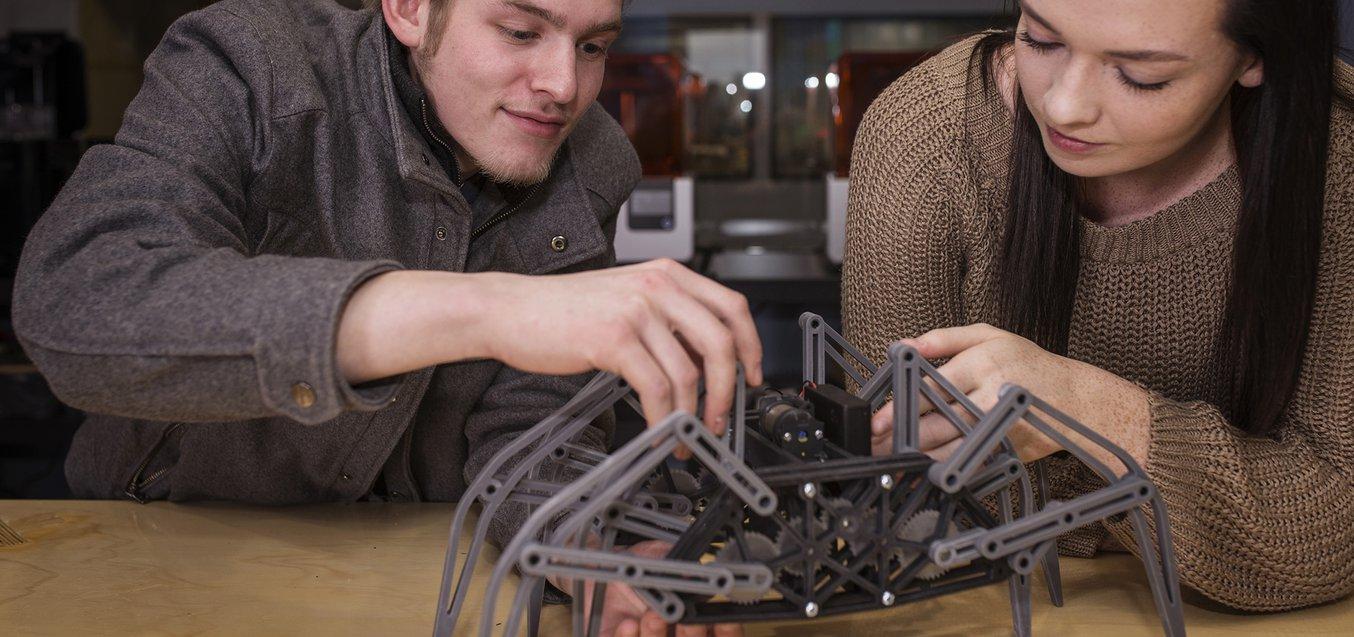
Within the past year, Morrison Institute of Technology eliminated its last manual drafting table, completing its transition to a fully digital instructional environment.
The institution provides rich teaching resources that mirror industry trends in manufacturing and industrial engineering. Their commitment to academic leadership in the Rock River Valley, Illinois, is paying off, as students consistently find employment at companies like John Deere, Caterpillar, and the Illinois Department of Transportation.
Chris Scott, president of Morrison Tech, has been with the college since 1995. He’s been the driving force behind the school’s efforts to keep pace with industry practices, and is justifiably proud of the school’s 97% job placement rate.
“My title is president, but I do just about everything. The joke around here is that we're the region’s best-kept secret, and I’d like that secret to get out a little bit,” Scott said.
Having just completed the opening of the campus’s new Innovation Center, Scott shared what has fueled Morrison Tech’s success, and how he sees additive manufacturing—a key component of the new center—fitting in with engineering instruction.
Connections With Industry: Learning and Leading
From its beginnings as a vocational college in the 1960s, Morrison Tech has focused on workforce development: placing students in meaningful careers at prestigious companies and strengthening the region’s economic stability.
“In the early twentieth century, the Rock River Valley was the mecca of manufacturing here in the United States. Sterling Rock Falls, 10 minutes from here, was once the hardware capital of the world. But many of those companies have disappeared,” Scott said.
Morrison Tech has close connections with companies that still remain, along with larger industry giants headquartered nearby, like Caterpillar and John Deere. Their current technology programs are governed by an industry advisory committee, more than half of which are alumnae of the institution.
“Certainly the companies have had a tremendous amount of influence on where our program is headed, and how it's going to get there, but we've actually also transformed a few companies along the way. We’ve been able to demonstrate the benefits of new technologies,” Scott said.

Integrating 3D Printing in Engineering Design Instruction
Morrison Tech focuses on providing students with hands-on instruction, with a foundation in the belief that students learn by doing. 3D printing is integrated into nearly all of the school’s engineering coursework, and the designs students work on are often real-world problems.
“The local company that has been using 3D printing the longest is Wahl Clipper, an industry leader that makes pet grooming and hair cutting equipment. They've been using additive manufacturing since the 1980s, and have invested millions of dollars in their plant,” Scott said.
“We have a plastics manufacturer in the Sterling area that we do some prototype working for. They needed to diversify and find additional clients. With our help, they’re doing some work for a kitchen product manufacturer now, and a few others.”

Scott sees 3D printers primarily as a tool to make better designs. With the ability to quickly, affordably print and test physical parts, students can spot issues early in the design process, and refine their designs much faster.
“We can see things much more clearly, and indicate where problems may occur, or what may not work or may not feel right to the consumer,” Scott said. “A secondary goal is how can we bring products to market more quickly and more aggressively, and I think that's where additive manufacturing really starts to shine. We can shorten that design cycle.”
Evolving From FDM to SLA 3D Printing Technology
About 10 years ago, Morrison Tech brought in filament-based, fused deposition modeling (FDM) 3D printers. Many education institutions started with FDM printing for its low cost, though at the price of quality. Often, educators end up transitioning to stereolithography (SLA) or using a combination of FDM and SLA 3D printers. SLA 3D printing is known for its smooth surface finish that more closely matches final materials and diverse resins that can simulate functional qualities of final products.
In stereolithography (SLA) 3D printing, a laser selectively cures liquid resin into solid parts, layer by layer, whereas fused deposition modeling (FDM) builds parts by melting and extruding layers of thermoplastic filament. Learn more about the difference between SLA and FDM.
“Filament-based printing is nice, but the quality is not quite there, especially for thin-walled parts. If your goal is something that's going to be made of plastic, filament-based printing is challenging. SLA is just a much better technology for industry specifically,” Scott said. “In the last five years, the limitations of filament-based printing have become clear. We are [now] in a transition here to move all of our filament-based printing over to SLA, and specifically to the Formlabs equipment.”

“[Formlabs has] been working with a variety of new and different resin technologies that more resemble what we would do through traditional plastics, and that's really a big advantage. We feel the costs have come down enough and the technology is good enough to really start replacing our filament-based print farm and change it over to SLA.”
Looking Ahead: 3D Printing in Production
While educators at Morrison Tech primarily focus on using 3D printing in product development and prototyping coursework, Scott sees production applications becoming much more common.
“Part of the future for us in additive manufacturing is in the tool and fixture side of the equation, how we can speed that up. There's a lot of times where we don't need to make a million part run. We only need to make one hundred. Making our molds, tools, and fixtures through additive manufacturing is really an untapped market, and where a lot of the future will be headed,” Scott said.
Scott’s also looking into casting, getting a new foundry up and running. In the spring, he plans to test working with Formlabs Castable Wax Resin, 3D printing molds to create metal parts. The Innovation Center will also house a new Morgan-Press tabletop injection molding unit.

“We're going to be using the Formlabs printer to make molds that hopefully will hold up for let’s say 50-100 part runs through a traditional injection molding process. We're pretty excited about doing more of that type of work,” Scott said.
Modeling Morrison Tech’s Success
3D printing in schools is not uncommon—but true, effective use of the technology is.
Morrison Tech students build highly valuable skills that match industry needs in part because of the school’s philosophy around their equipment. Students use 3D printing as a problem-solving tool the same way industry partners do; the tech is integrated to be a part of the design and manufacturing development process.
Explore resources to find more information and inspiration for integrating 3D printing into education, and learn more about the additive manufacturing technology Morrison Tech relies on to fuel engineering instruction: Formlabs Form 2 SLA 3D printer.