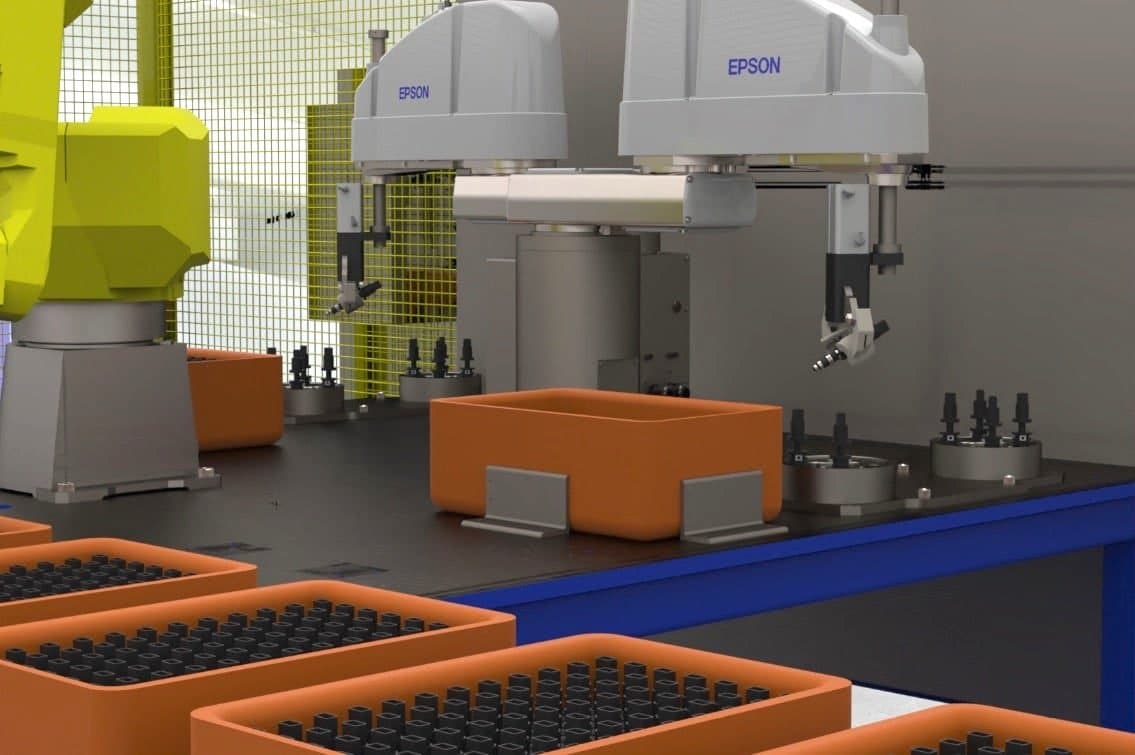
Headquartered in Wisconsin, STS Technical Group has been operating for nearly 40 years working with clients on staffing, technical design, and engineering challenges. With over 250 employees at recruitment centers around the US, the company has grown and adapted to the ever-shifting landscape of manufacturing technologies, offering new and innovative services as they emerge.
STS utilizes Formlabs 3D printing technology because of the variety of materials that are suitable for extensive use in the manufacturing environment, the capability to produce medical-grade 3D printed components, and the high quality of the printed components.
In this case study, STS Technical Group’s Director of Engineering Services Benjamin Heard walks you through the development of custom grippers for moving and positioning fuel injectors in a manufacturing environment, highlighting the advantages of 3D printing a component versus producing it with traditional production methods like casting and machining. Heard will also explain why the capabilities of the custom 3D printed grippers are far superior to the previous, traditionally manufactured grippers.
How to Choose a Production Process For Specific Components
For manufacturing a specific component, many production processes must be considered during development, such as casting, fabricating, machining, and 3D printing processes like fused deposition modeling (FDM) or stereolithography (SLA) printing.
Some advantages of 3D printing for manufacturing components:
-
Greater detail than casting and/or machining. Printing layer thickness can be as small as 25 microns.
-
More cost-effective than casting, fabricating, or machining when it comes to highly detailed designs.
-
Significantly lower lead and production times than casting, fabricating, or machining.
-
No machining is required after printing, therefore, there is no need to have expensive machining equipment that requires skilled labor and tedious setup.
-
Wide selection of durable, lightweight materials.
-
Designs created with CAD software can be saved and reused as needed for replacement, no need for inventory.
-
3D printed items can be designed to be more compatible for installation by strategically incorporating additional material to strengthen supports, and by incorporating features for installation such as screw/bolt holes and hex cavities.
-
If an SLA 3D printed polymer part sustains severe impact during operation, it will likely break, whereas metal parts tend to bend out-of-tolerance and continue to produce out-of-spec parts.
-
Lower replacement costs and faster lead time for broken components and replacement parts.
-
Printed parts have an aesthetic appearance that can be painted or covered with a desired coating.
-
Offers an alternative for materials that are not suitable for machining because they will melt, chip, or crack during the process.
-
Lower shipping costs due to lower weight and reduced packaging material.
When deciding between casting, fabricating, machining, or 3D printing components, first consider the durability the part must possess. While metal parts produced with traditional processes do offer higher strength, durability, and wear resistance, many components have requirements that can easily be satisfied by 3D printing with specific engineering materials.
The work environment must also be considered during selection to ensure the material can withstand the temperature, moisture levels, or the presence of corrosives. 3D printing large components may pose a challenge, but large-format 3D printers, such as the Form 3L, can accommodate larger print requests.
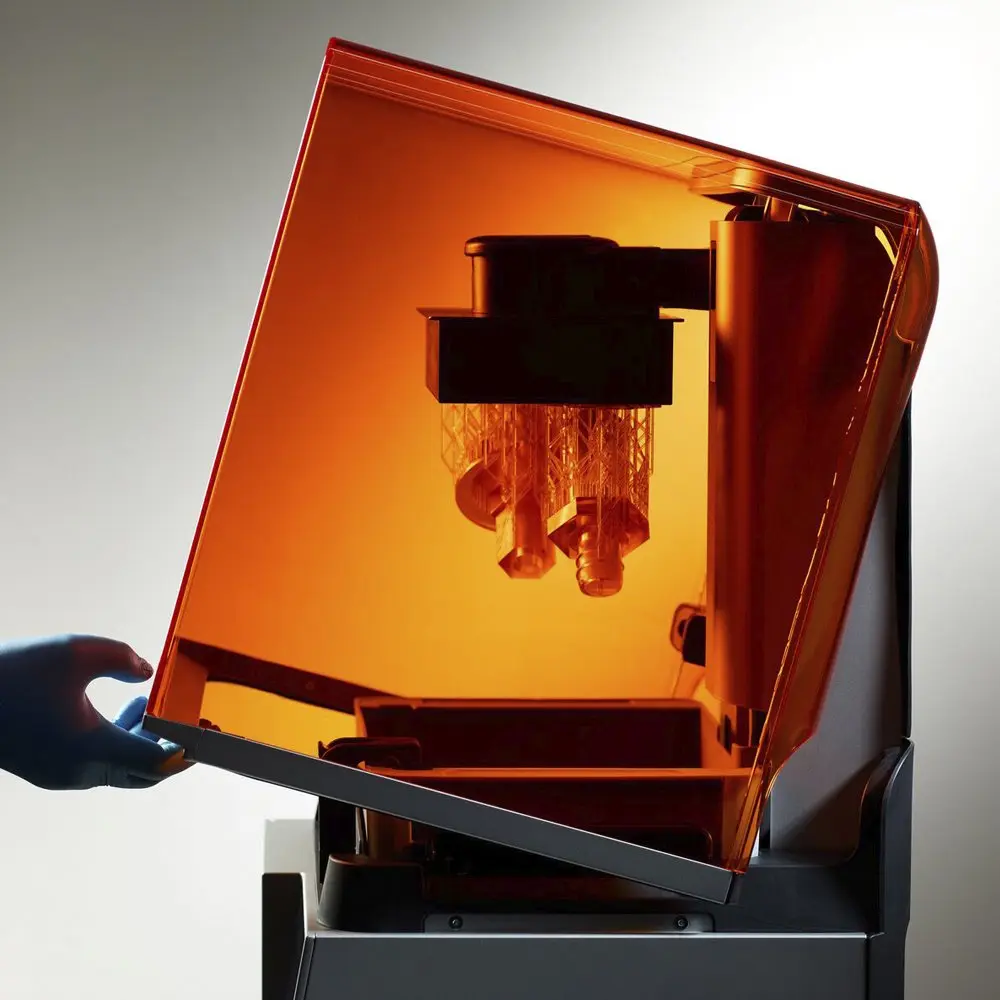
Introduction to 3D Printing With Desktop Stereolithography (SLA)
Looking for a 3D printer to realize your 3D models in high resolution? Download our white paper to learn how SLA printing works and why it's the most popular 3D printing process for creating models with incredible details.
Designing and 3D Printing Custom Fuel Injector Grippers
Many factors are considered when designing grippers for pick and place operations. The materials used in the picked component and the gripper, grip strength, geometry of the picked component, radial jaws versus linear jaw motion, surrounding clearances, and the required pick and place location tolerances.
The gripper finger material is typically selected to be significantly stronger and harder than the picked part to ensure that the arms won’t wear after thousands or even millions of cycles. A typical gripper material is hardened steel, which can cause marring on softer picked part surfaces. When the finish is delicate, coatings or shoes are added to the grippers. Additionally, when parts are moved into position for additional machine work to be performed on the item, poor grip contact could result in misplacement of the part and the creation of machined defects.
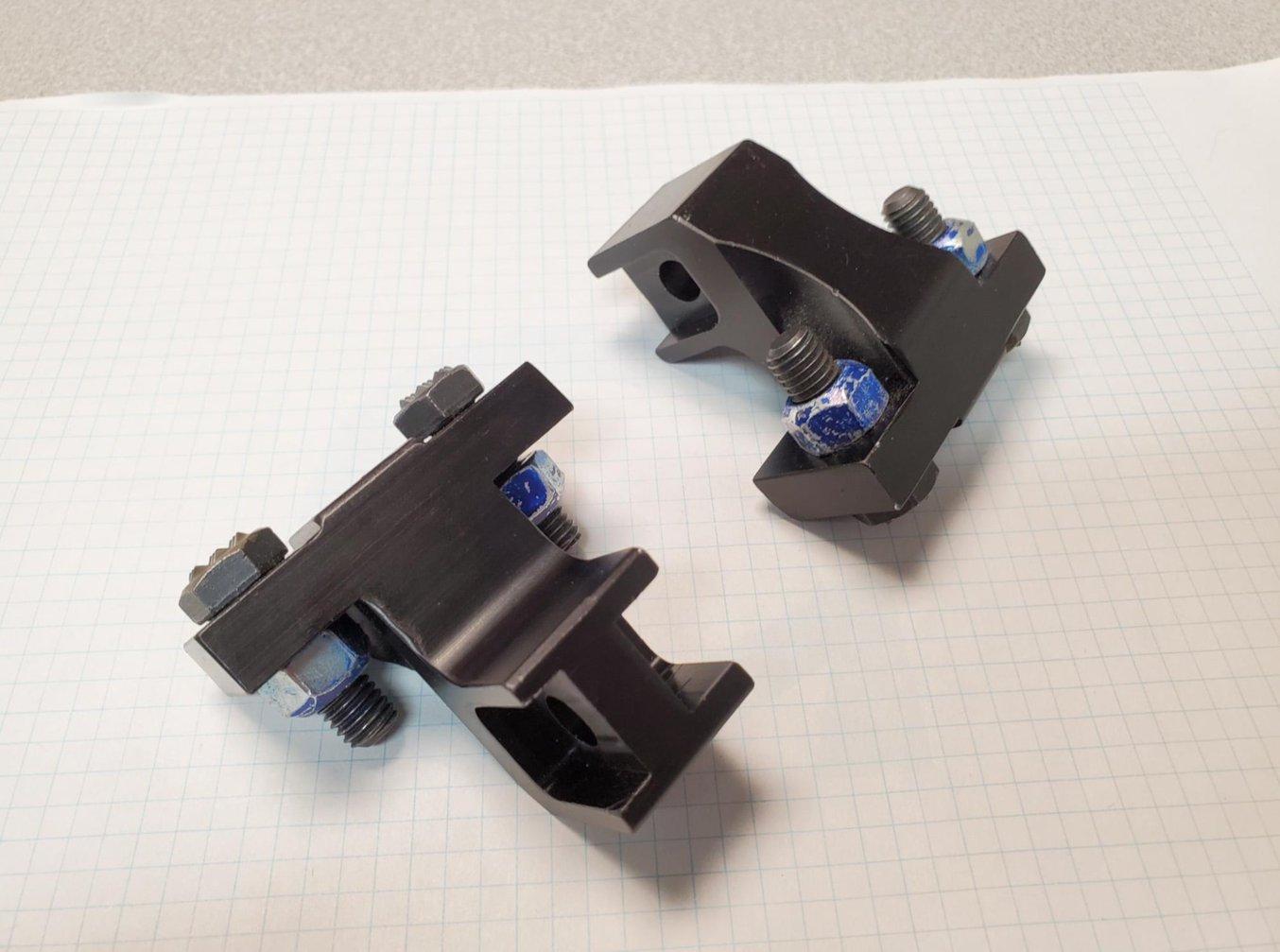
The generic grippers that were originally installed on the pneumatic cylinder.
In general, the gripper jaws are cut in a ‘V’ shape for picked items that are cylindrical or have non-flat edges. This shape offers reliable contact to the picked part in two locations per side in a soft tangent contact. More importantly, it is a simple and cost-effective design that can be scaled to any number of processes.
The drawbacks of this design include force concentrations which are stressful to both the gripper and the item, resulting in isolated gripper wear. Additionally, ‘V’ grippers can only abstractly position an item, resulting in a need for a secondary positioning mechanism for additional manufacturing processes.
By choosing 3D printing to produce the grippers, the design options greatly increase and form-fitting grips that distribute force across a larger contact area are possible to produce.
In our example, we used a Creaform laser 3D scanner and VX Elements modeling software to get a virtual 3D scan of the fuel injector to assist with the design of the grippers. The scan resulted in an image with intricate details, instead of having to tediously measure every gap, cylinder, and opening on the fuel injector. The scanned image could then be imported into 3D CAD software to generate an extremely detailed design using a mold feature in the software.
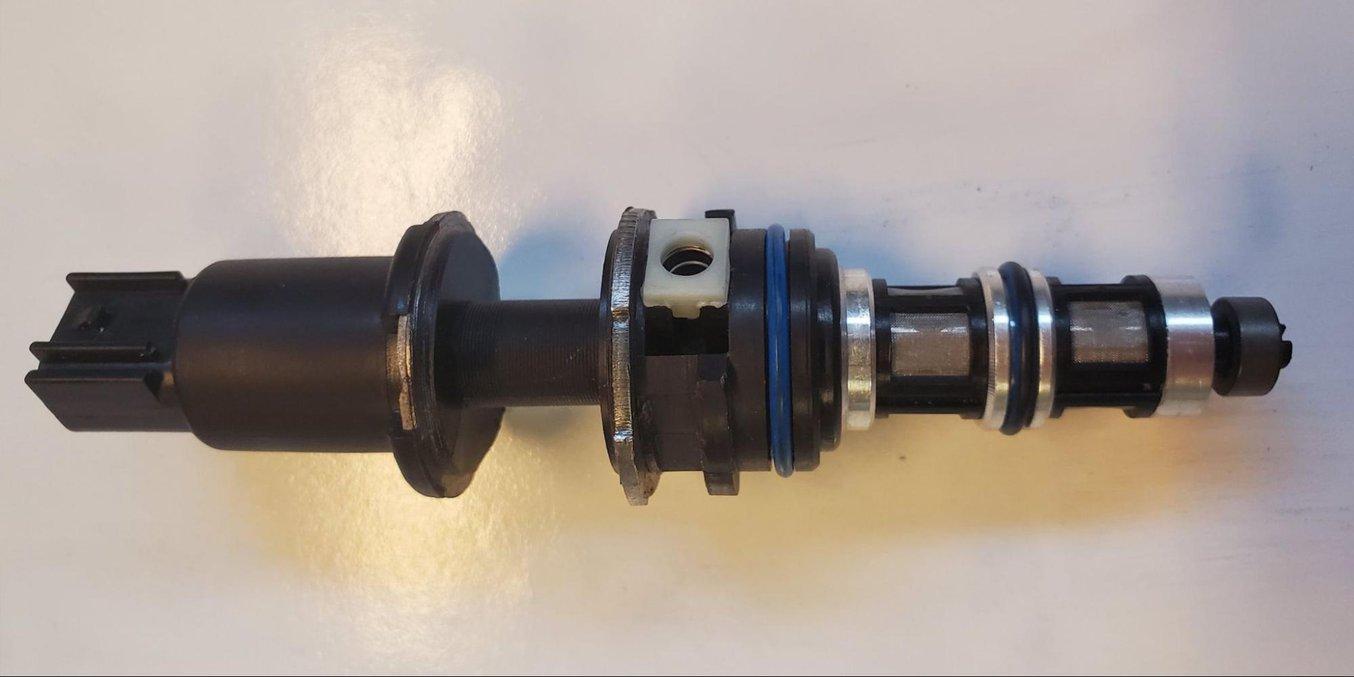
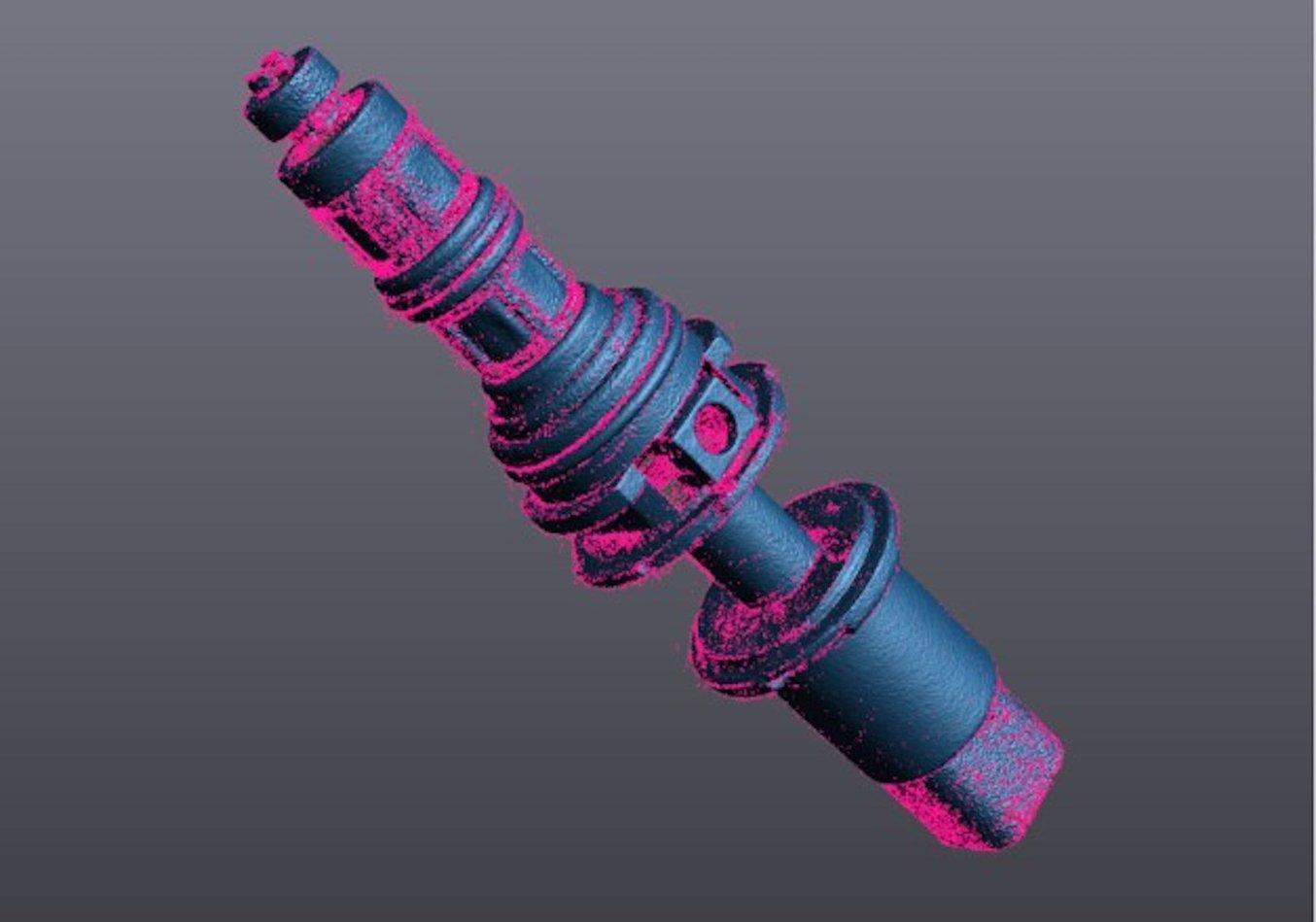
The fuel injector (top) was 3D scanned to create a model (bottom) that could be used to create the custom grippers.
Our new detailed radial gripper design mounts onto the rotary arms attached to the piston of a pneumatic cylinder.
The new gripper was prototyped and manufactured on a Formlabs Form 3 SLA 3D printer. Formlabs offers multiple materials for rapid prototyping, such as Draft Resin for quick prototypes. In our case, Standard Black Resin was used to develop the initial prototype of the design. Both gripper halves could be printed on the Form 3 in a single build. Materials can be changed easily, which accelerates getting to a final product from the original idea.
Manufacturing the end-use component required a more durable material to sustain the production environment. As a result, Rigid 4000 Resin was used to make the final grippers. This extremely stiff, glass-filled polymer material offers high durability, rigidity, and an appealing finish for the printed parts.
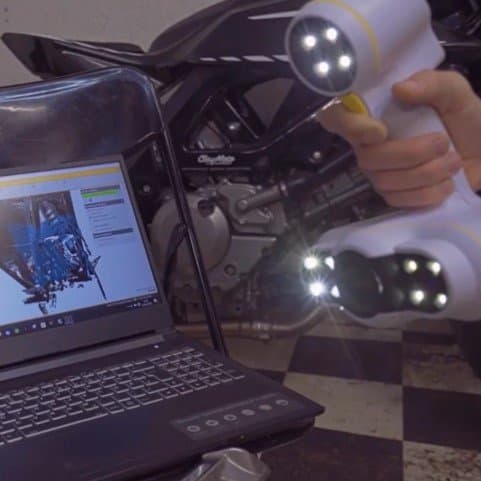
How 3D Scanning Supports the Modern Product Development Process
Watch this webinar with Peel 3D to explore how to integrate 3D scanners into your 3D printing workflow to elevate your product development process.
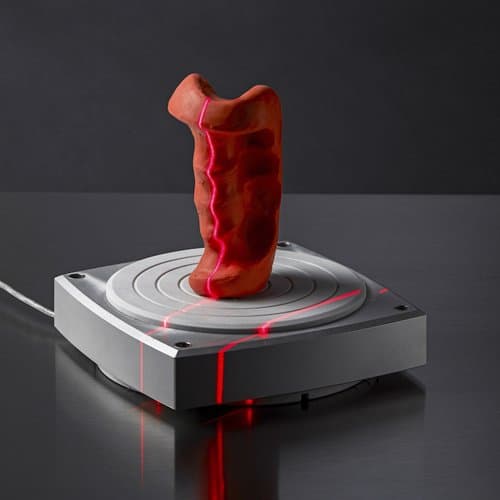
3D Scanning for Reverse Engineering, Restoration, and Metrology
3D scanning and printing workflows can be applied to replication and restoration, reverse engineering, metrology, and more. Download our white paper or watch our webinar to learn how to start using these technologies to sophisticate your own design workflows.
Results
The process of designing and 3D printing the irregular grippers was a complete success and they operate as expected. The capabilities of the 3D printed grippers are far superior to the previous grippers.

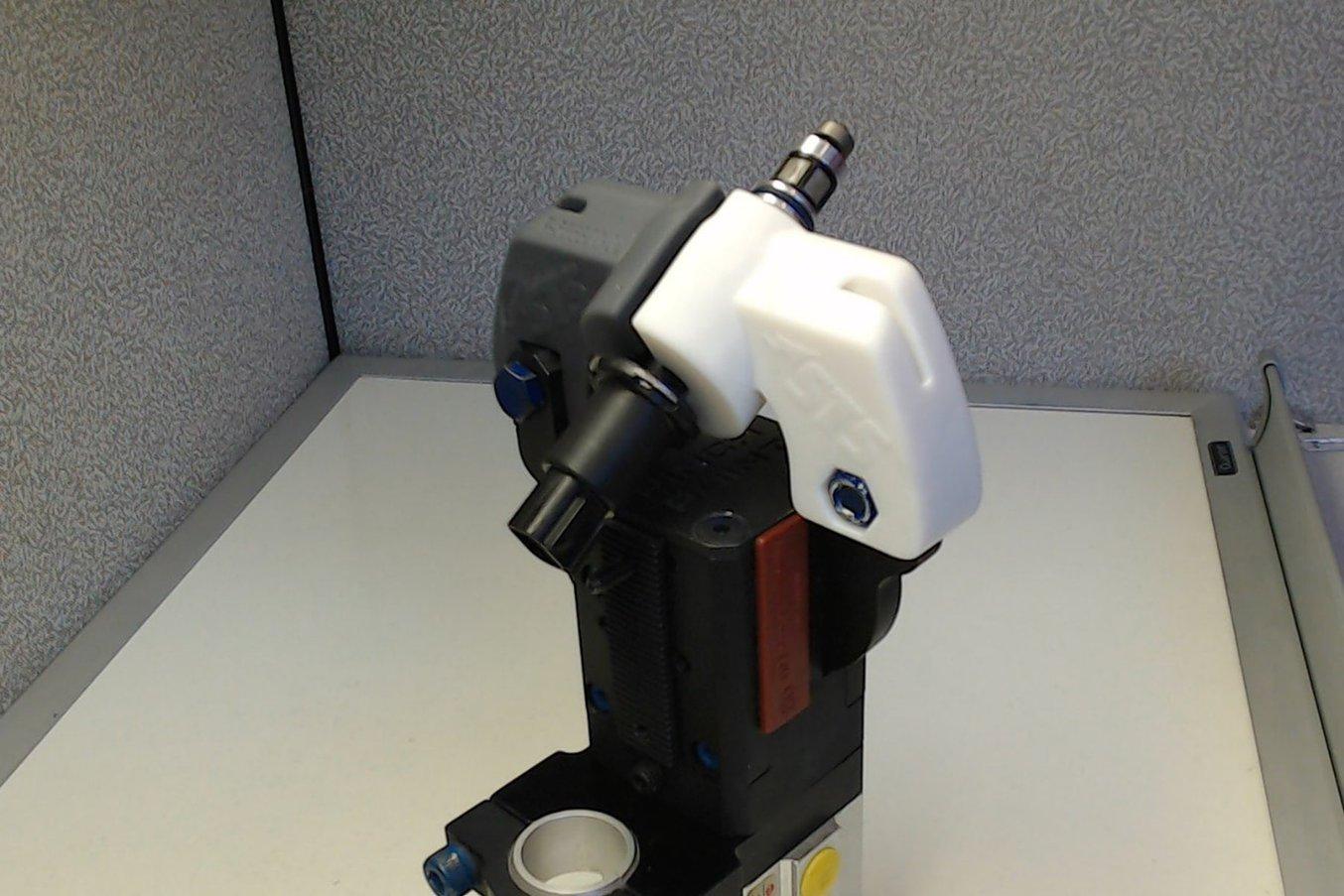
The pneumatic cylinder assembly; complete with 3D printed grippers holding the fuel injector.
The advantages of the 3D printed grippers are the following:
-
Greater surface area to grasp the fuel injector, leading to less force concentrated areas which could damage or scratch the fuel injector and wear the gripper. Even if the gripper were to sustain wear, the unique fully encompassing gripper design will still allow the gripper to operate at the desired level.
-
With the grippers operating in a radial gripping motion, clearance on the interior edges of the grippers can be incorporated in the design instead of machined. This eliminates square edges in the gripping cavity and allows for the uniform gripping and full release of the fuel injector.
-
The detailed gripper jaws align and orient the fuel injector to the desired position, decreasing the amount of additional equipment and manufacturing stations needed to orient the picked parts.
-
With the fully encompassing gripper design, less gripper pressure is required to grasp the fuel injector, which led to lower pneumatic or hydraulic pressure requirements for the material handling equipment.
-
The grippers are designed to eliminate thin component structures and provide a unique design to maximize the material strength of resin, while including a hex cavity which encompasses a hex nut in the assembly to simplify installation.
-
Serialization or labeling of the SLA printed component is achieved during the printing process, eliminating stamping or etching processes.
Conclusion
The Formlabs Form 3, equipped with a wide array of printing materials, provides an exceptional alternative to traditional manufacturing processes for manufacturing custom components, such as manufacturing aids.
Printed components offer adequate durability, cost far less for more detailed designs, and can be produced and implemented in a fraction of the time. The future of automated manufacturing will consist of highly detailed products designed with CAD software and 3D printed using a variety of materials.
Using Formlabs 3D printers and CAD software, STS Technical Group can design and engineer highly detailed irregular components for its customers.