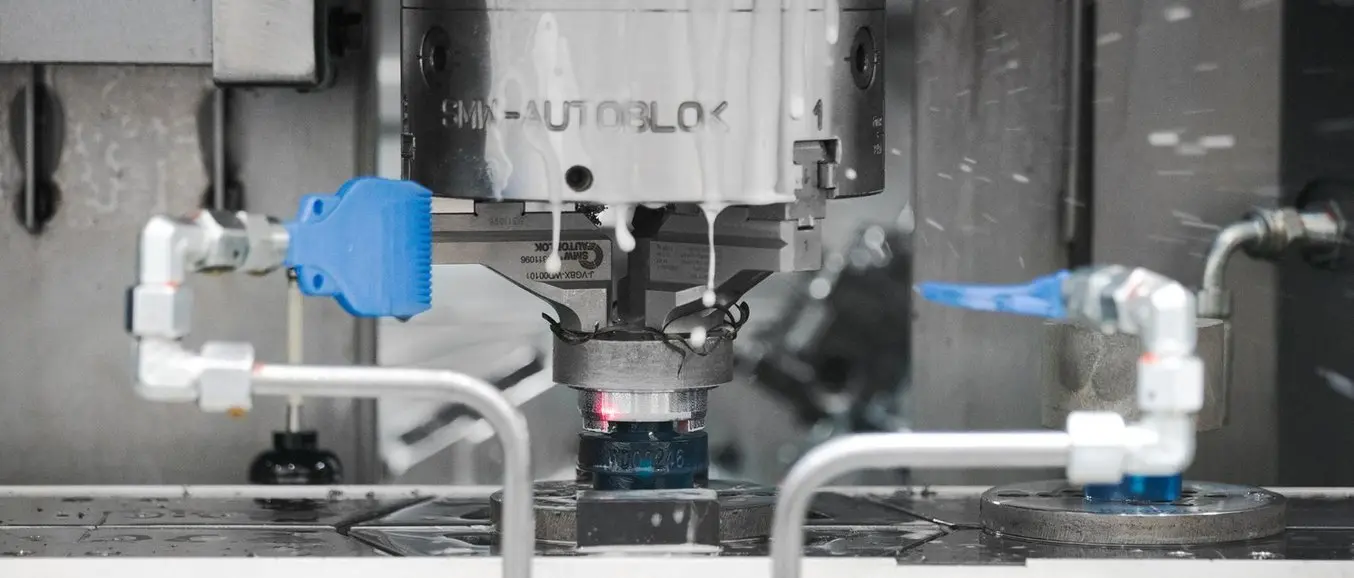
Additive manufacturing processes build objects by adding material layer by layer, while subtractive manufacturing removes material to create parts. Though these approaches are fundamentally different, subtractive and additive manufacturing processes are often used side by side due to their overlapping range of applications.
It can initially be difficult to understand how to make the most of each type of technology to optimize product development and manufacturing. Both have cases where it makes sense to use one approach over the other, for example, one process can be more useful for a certain production volume, or at a specific stage of product development.
In this guide, we’ll be taking a closer look at the various additive and subtractive manufacturing techniques and applications to help you decide how to leverage them for your own processes.
Subtractive Manufacturing
Subtractive manufacturing is an umbrella term for various controlled machining and material removal processes that start with solid blocks, bars, rods of plastic, metal, or other materials that are shaped by removing material through cutting, boring, drilling, and grinding.
These processes are either performed manually or more commonly, driven by computer numerical control (CNC).
In CNC, a virtual model designed in CAD software serves as input for the fabrication tool. Software simulation is combined with user input to generate toolpaths that guide the cutting tool through the part geometry. These instructions tell the machine how to make necessary cuts, channels, holes, and any other features that require material removal, taking into account speed of the cutting tool and feed rate of the material. CNC tools manufacture parts based on this computer-aided manufacturing (CAM) data, with little or no human assistance or interaction.
Subtractive manufacturing processes are typically used to create parts in plastics or metals for prototyping, manufacturing tooling, and end-use parts. They’re ideal for applications that require tight tolerances and geometries that are difficult to mold, cast, or produce with other traditional manufacturing methods.
Subtractive manufacturing offers a variety of material and processing methods. Softer materials are much easier to machine to their desired shape, but will wear more quickly.
Subtractive Manufacturing Processes
Process | Materials |
---|---|
CNC machining (turning, drilling, boring, milling, reaming) | Hard thermoplastics, thermoset plastics, soft metals, hard metals (industrial machines) |
Electrical discharge machining (EDM) | Hard metals |
Laser cutting | Thermoplastics, wood, acrylic, fabrics, metals (industrial machines) |
Water jet cutting | Plastics, hard and soft metals, stone, glass, composites |
Additive Manufacturing
In contrast to the subtractive process of removing material from a larger piece, additive manufacturing or 3D printing processes build objects by adding material one layer at a time, with each successive layer bonding to the preceding layer until the part is complete.
Just like subtractive CNC tools, additive manufacturing technologies create parts from CAD models. Preparing models for 3D printing with print preparation or slicer software is mostly automated, making job setup substantially easier and faster than with CNC tools. Depending on the technology, the 3D printer deposits material, selectively melts and fuses powder, or cures liquid photopolymer materials to create parts based on the CAM data. The 3D printed parts often require some form of cleaning and finishing to achieve their final properties and appearance before they’re ready to use.
Additive manufacturing is ideal for a range of engineering and manufacturing applications including prototyping, manufacturing tooling, and casting patterns, as well as short-run, bridge production, and custom manufacturing of final parts. Industrial 3D printers offer a very high degree of design freedom and can produce complex designs that would be impossible or excessively costly to create with any other manufacturing method.
The most common materials used in additive manufacturing are plastics and metals. Desktop and benchtop 3D printers offer an affordable solution to create plastics parts, while metals are currently limited to industrial systems.
Additive Manufacturing Processes
Process | Materials |
---|---|
Stereolithography (SLA) | Varieties of resin (thermoset plastics), high-strength, rigid, flexible, elastic, heat-resistant, castable (wax-like) |
Selective laser sintering (SLS) | Engineering thermoplastics, such as nylon |
Fused deposition modeling (FDM) | Standard thermoplastics, such as ABS, PLA, and their various blends |
Material jetting | Varieties of resin (thermosetting plastics) |
Binder jetting | Gypsum (full color), metals |
Selective laser melting (SLM) or direct metal laser sintering (DMLS) | Soft and hard metals |
Electron beam melting (EBM) | Soft and hard metals |

How to Choose a 3D Printing Technology
Having trouble finding the best 3D printing technology for your needs? In this video guide, we compare FDM, SLA, and SLS technologies across popular buying considerations.
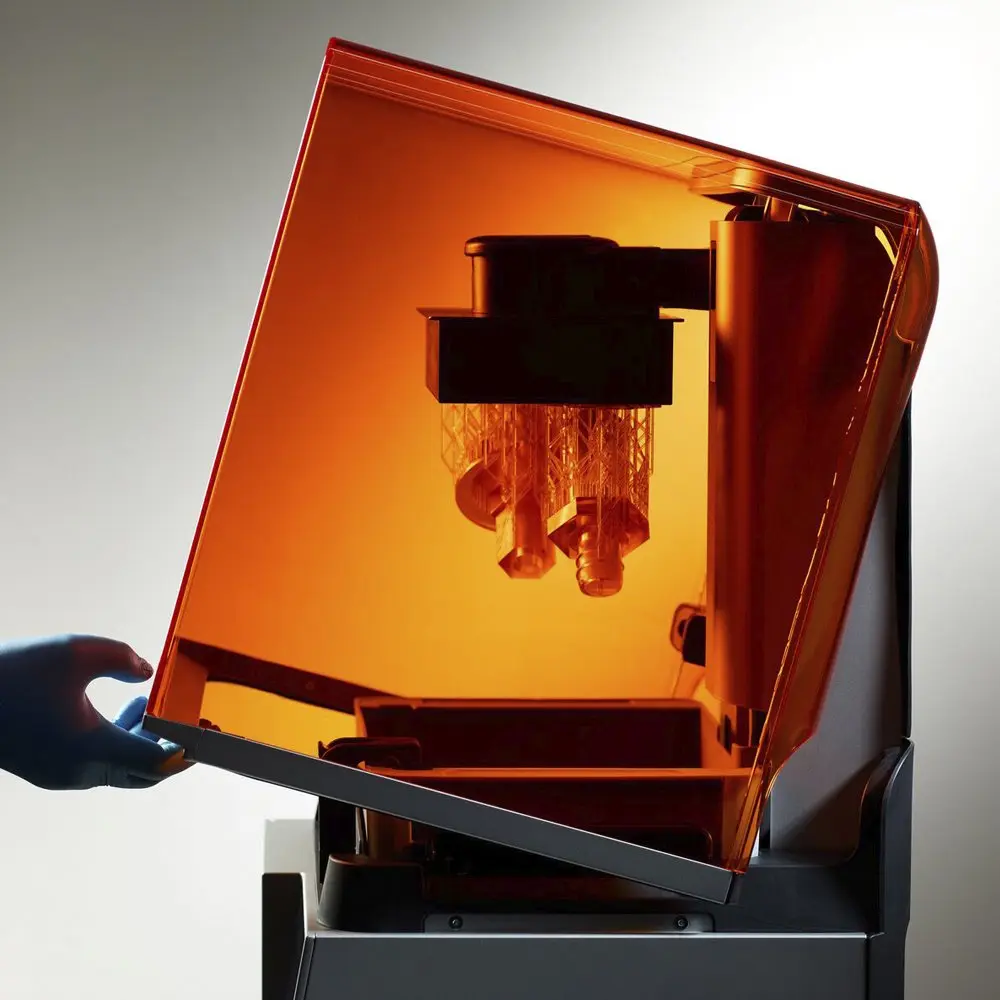
Introduction to 3D Printing With Desktop Stereolithography (SLA)
Looking for a resin 3D printer to realize your 3D models in high resolution? Download our white paper to learn how SLA printing works and why it's the most popular 3D printing process for creating models with incredible details.
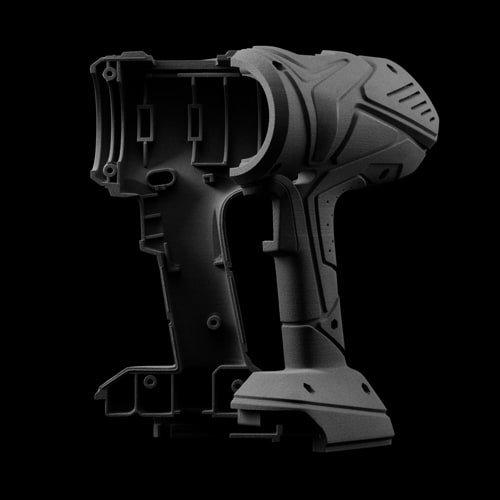
Introduction to Selective Laser Sintering (SLS) 3D Printing
Looking for a 3D printer to create strong, functional parts? Download our white paper to learn how SLS printing works and why it's a popular 3D printing process for functional prototyping and end-use production.
When to Use Subtractive and Additive Manufacturing
While there are key differences, subtractive and additive manufacturing are not mutually exclusive. In fact, they are quite often used side by side and at different stages of product development and in manufacturing.
The prototyping process, for example, often relies on both additive and subtractive tools. Early concept models and prototypes are generally more economical and faster to produce with plastic additive manufacturing processes, such as stereolithography (SLA) or selective laser sintering (SLS). 3D printing offers a wide variety of material options for the functional prototyping of plastic parts. Additive technologies are also typically better suited for small parts and highly complex or intricate designs.
When later stages of the development process require larger batches, subtractive processes become more competitive. Larger, less complex objects also lend themselves more to subtractive manufacturing. Due to the myriad choices in surface finishes and the speed of the process, subtractive manufacturing is most often the choice for fabricating finished parts. As metal 3D printed parts can be cost-prohibitive, subtractive processes are a better choice for metals parts for all but the most complex designs.
In manufacturing, subtractive and additive processes often complement each other in the production of tooling, jigs, fixtures, brackets, molds, and patterns. Manufacturers often use plastic 3D printed parts for fast, custom, low-volume, or replacement parts and opt for subtractive metal processes for higher volumes or parts that are subject to more extreme mechanical stress and strain.
Utilizing both additive and subtractive manufacturing results in a hybrid process. This allows product designers and manufacturers to combine the versatility and quick turnaround times of additive manufacturing with the strength of subtractively produced parts.
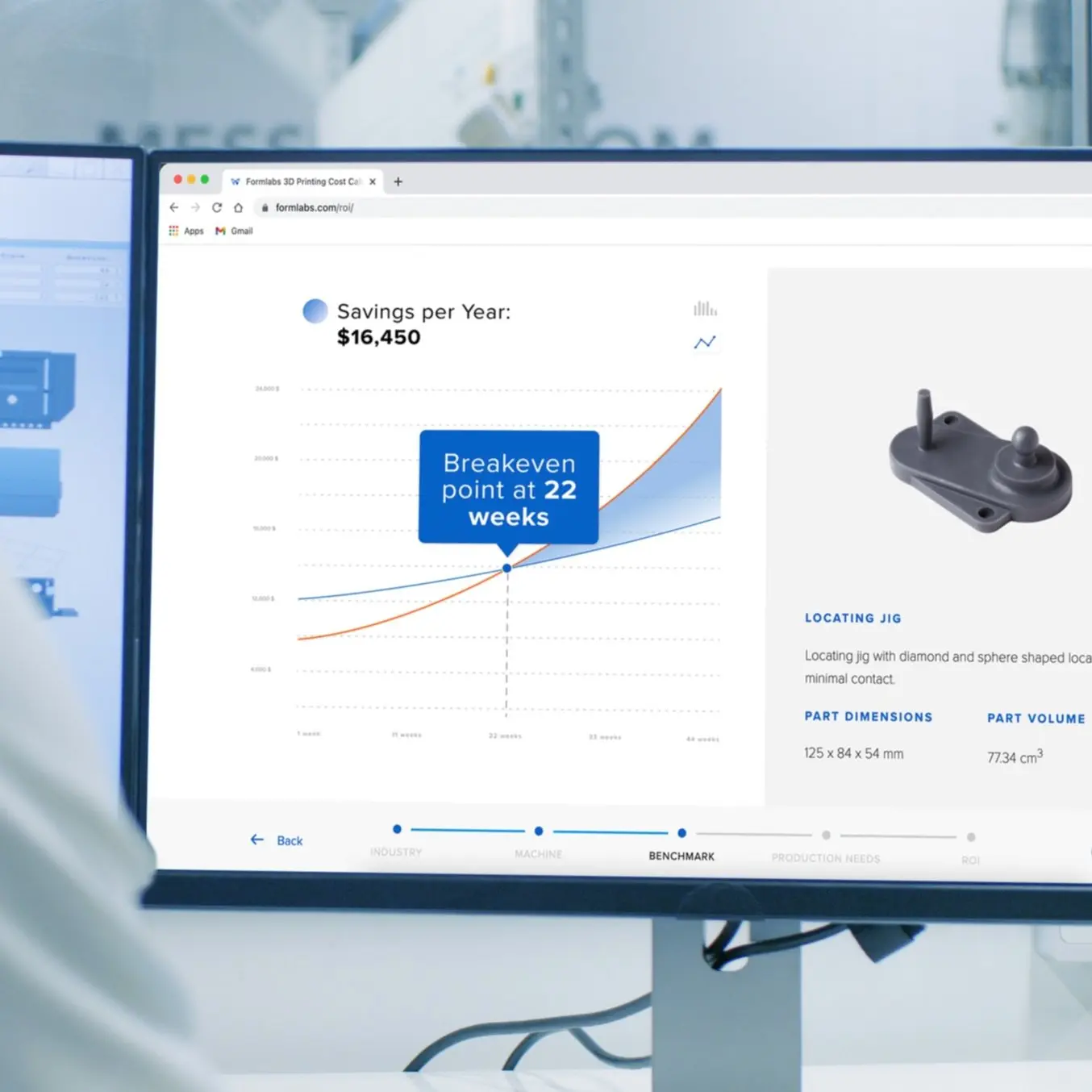
Calculate Your Time and Cost Savings
Try our interactive ROI tool to see how much time and cost you can save when 3D printing on Formlabs 3D printers.
Additive vs. Subtractive Systems
Additive and subtractive technologies come in many form factors, with a range of cost and capabilities, from desktop machines to large industrial equipment. Ultimately, you should choose the technology that makes the most sense for your business needs and applications.
Additive Manufacturing | Subtractive Manufacturing | |
---|---|---|
Equipment Costs | Professional desktop printers start at $3,500 for plastics. Large-scale industrial machines for metals start from ~$400,000. | Small CNC machines for workshops start around $2,000. More advanced workshop tools go well beyond that depending on the number of axes, features, part size, and tooling needed for specific materials. |
Training | Desktop printers are practically plug and play, requiring minor training on build setup, maintenance, machine operation, and finishing. Industrial additive manufacturing systems require dedicated staff and extensive training. | Small CNC machines require moderate training for software, job setup, maintenance, machine operation, and finishing. Larger, industrial subtractive systems require dedicated staff and extensive training. |
Facility Requirements | Desktop machines are suitable for the office and benchtop systems for a workshop environment with moderate space. Industrial 3D printers often require a dedicated space or room with HVAC control. | Small CNC machines are suitable for workshops. Industrial systems require a larger, dedicated space. |
Ancillary Equipment | Tools and (some automated) systems for cleaning, washing, post-curing, and finishing, depending on the process. | Various tooling. More advanced systems automate some processes like tool changing, chip clearing and handling, and coolant management. |
Learn more about the most common subtractive and additive fabrication tools suitable for professional workspaces, machine shops, and workshops.
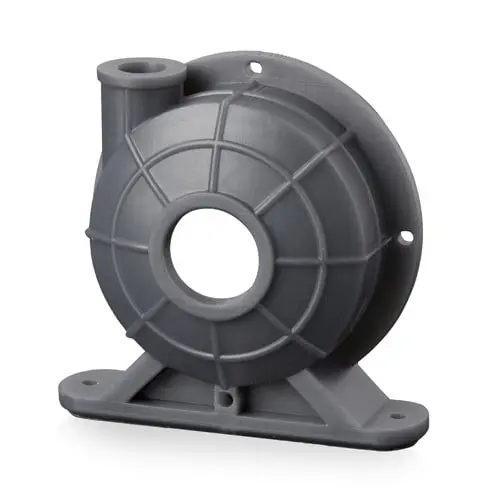
Request a Free 3D Printed Sample Part
See and feel Formlabs quality firsthand. We’ll ship a free sample part to your office.
Learn More About Additive Manufacturing
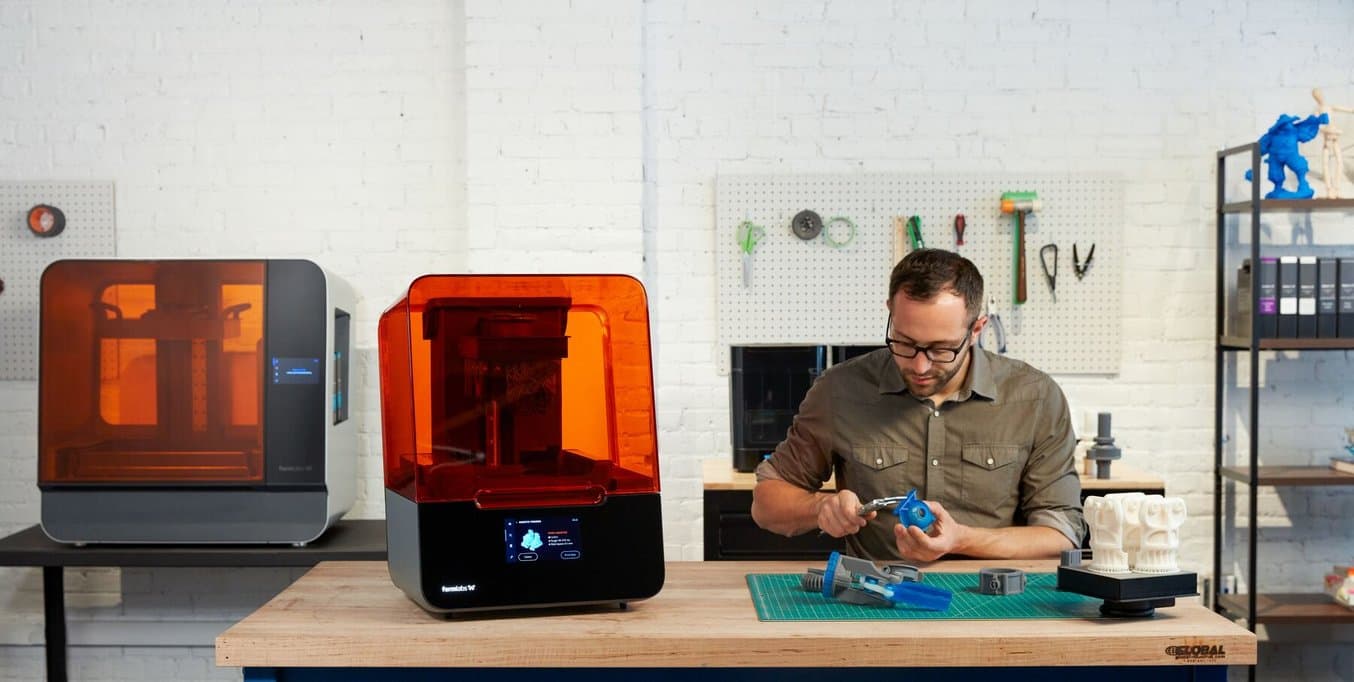
Prices have dropped significantly in recent years and compact, easy-to-use desktop additive and subtractive manufacturing tools are available today professional workspaces, machine shops, and workshops.
Learn more about 3D printing and see quality firsthand by requesting a complimentary sample part printed on a Formlabs SLA 3D printer.