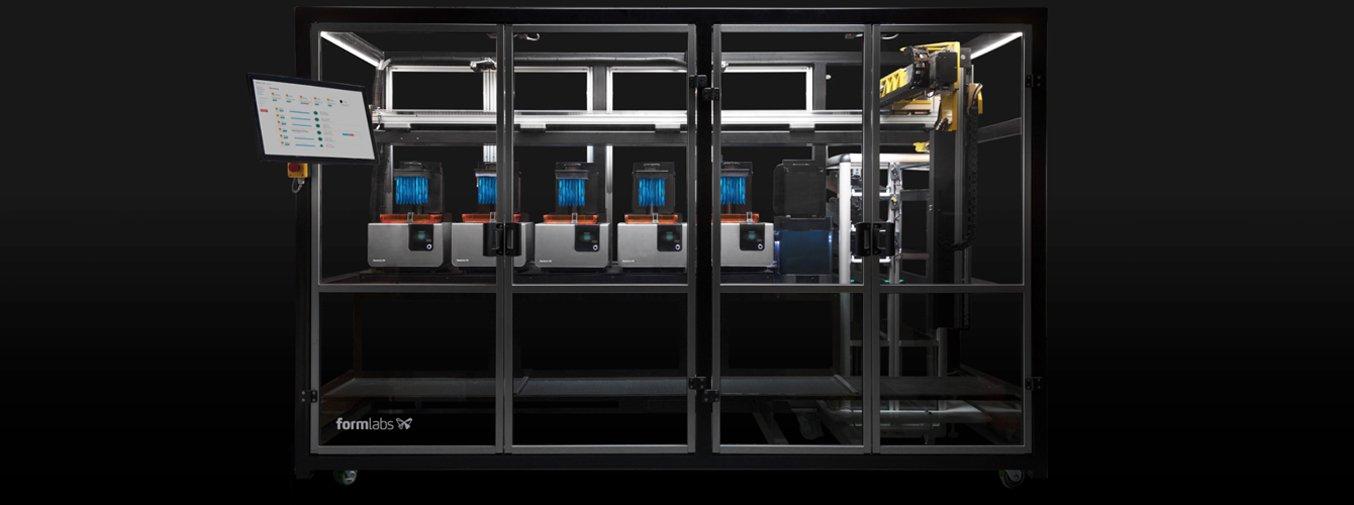
Custom manufacturing is the process of designing, engineering, and producing goods based on a customer’s unique specifications, including build to order (BTO) parts, one-offs, short production runs, as well mass customization.
Modern manufacturing theory, tools, and best practices are focused on how to make thousands or millions of identical parts or products at a low cost per unit. Design and manufacturing practices that optimize for high volume production allow companies to deliver goods at prices acceptable to consumers while providing manufacturers with small profit margins per unit, that become significant when multiplied across a full manufacturing run.
Custom or small series parts and products such as bespoke jewelry, specialty electronics, and medical or dental appliances tailored to one’s body pose unique challenges that require manufacturers to adapt production processes.
Additive manufacturing (AM), also known as 3D printing, has grown more capable as true manufacturing tools over the last decade as technologies and materials continued to improve. 3D printing is well-suited to custom manufacturing because of its high flexibility, toolless fabrication processes, and ability to quickly scale up to meet demand.
Read on to learn about the challenges of custom manufacturing and see real-world examples of how multiple industries use 3D printing for custom production, from personalized healthcare, to mass customization of consumer goods.
Watch our webinar, where Jon Bruner, director of Formlabs’ Digital Factory program and former editor at Forbes Magazine and O’Reilly Media, shares his insights on where the additive manufacturing industry is headed, and how manufacturers can leverage additive technologies to get there faster.
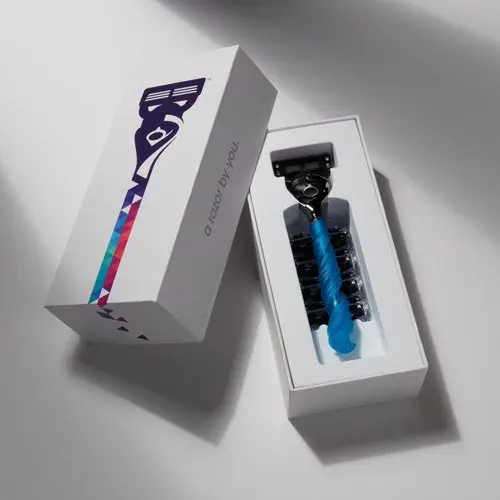
Guide to Mass Customization
This guide will provide manufacturers with insights into the different approaches to customization, how to choose the most applicable approach, and more.
Challenges in Custom Manufacturing
Compared to mass production, custom manufacturing carries a different set of challenges, both in business model and manufacturing tactics.
Process: Custom manufacturing typically avoids the use of common high-volume production methods that require complex molds and tooling as their high costs are impossible to recoup over small production runs that range from a single unit to low hundreds. Instead, manufacturers need to select alternative manufacturing processes that are more agile and have low upfront costs. Unfortunately, manufacturing processes with those characteristics also often have longer cycle times and require more labor, which ultimately results in higher cost per unit. per unit costs.
Efficiency: In any production process, maintaining efficiency is key for profitable operations, but how efficiency is achieved is dependent on the scale and style of production. In traditional mass production, emphasis is on reducing cycle times through rigorous DFM/A processes, achieving economies of scale, and reducing labor as much as possible. For custom manufacturing, the variability in design input means that standard DFM/A approaches may be ineffective as a cost control and economies of scale are difficult to achieve. Instead, custom manufacturing focuses on efficiency of demand: goods are produced just-in-time, only when ordered, versus the mass production approach of estimating demand, producing at scale, and warehousing inventory.
Quality: Mass-produced units have the benefit of being proven over time with known tolerances and performance. Deviations in product quality can be managed based on control of factors such as speed and temperature to minimize variation. Established audit systems designed for mass production use predetermined tests to verify and maintain quality of product by pulling units for testing on an interval or randomly. Custom manufacturing, with batch sizes of one unit, by definition has highly varied outputs, which increases the time and cost in validating that the manufactured product features and dimensions line up with product specifications.
Custom Manufacturing With 3D Printing
High precision additive manufacturing processes like stereolithography (SLA) and selective laser sintering (SLS) are ideal for custom production as they offer high flexibility, minimal setup, and can produce parts in a wide range of geometries and materials to respond to shifting needs. Often, AM also helps to transform traditionally handcrafted manual workflows to digital, improving quality and reducing the number of production steps and labor needs, as well as overall lead time and cost.
To better understand how additive manufacturing fits into customization workflows, let’s consider real-world examples from engineering, jewelry, dental, and consumer goods industries.
Patterns for Casting
Casting processes are used across various industries to produce complex parts that would be difficult or uneconomical to manufacture by other methods. SLA 3D printing is a common way patterns for casting directly from CAD designs, due to its high resolution and similar ability to produce fine features.
In the jewelry industry, 3D printing is part of the investment casting process. Jewelry makers begin by designing a piece digitally, then 3D printing the design in a castable resin that can be surrounded by investment material and cleanly burned away like a traditional wax model. Custom pieces can then be cast and finished, following the same workflow as with traditional processes.
A similar process is used in dentistry for creating castable or pressable crowns, bridges, and other restorations, and even in tool-free investment casting and sand casting patterns for engineering applications.

3D printing is also used to create masters for flexible latex rubber or room temperature vulcanized (RTV) silicone rubber molds. In jewelry, these inexpensive molds are used to create a limited number (around 25 to 100) wax patterns for investment casting.
Molding
One of the first high-volume use cases for 3D printing is custom clear aligners and retainers in dentistry. In this process, an orthodontist scans the patient’s dentition with an intraoral scanner, plans the treatment using CAD software, and 3D prints models for each step in the course of treatment. Each step is represented by a unique model that is used as a base to thermoform clear appliances.

High-temperature SLA resins can be used in low-pressure plastic injection molding and even to cast soft metals like pewter. While the mold quality might not match that of hard tooling, they’re suitable for small- and medium-run production where the cost of tooling might not otherwise be recoverable.
In audiology, 3D printing can also be used to produce affordable, custom earbuds. The process begins with a digital scan of the customer’s ear canal that is turned into a digital design. The 3D printed part serves as a mold that’s filled with biocompatible silicone. Once the silicone is set, a technician can remove the 3D printed shell and add a coating to get the final product.
Directly Printed End-Use Parts
Additive manufacturing is increasingly used for end-use parts. In terms of scale, dental and medical industries are leading the use of printed, patient-specific end-use parts. Today, custom orthotics, prosthetics, insoles, hearing aids, and biocompatible appliances like dentures and splints are all produced using 3D printing processes.

Shoe companies including New Balance and Adidas have announced plans to mass produce custom shoe midsoles that are 3D printed from rigid polyurethane (RPU) within the next few years. Here, 3D printing combines with traditional manufacturing methods, leveraging economies of scale offered by mass production, while improving product performance and end-user value with customized elements.
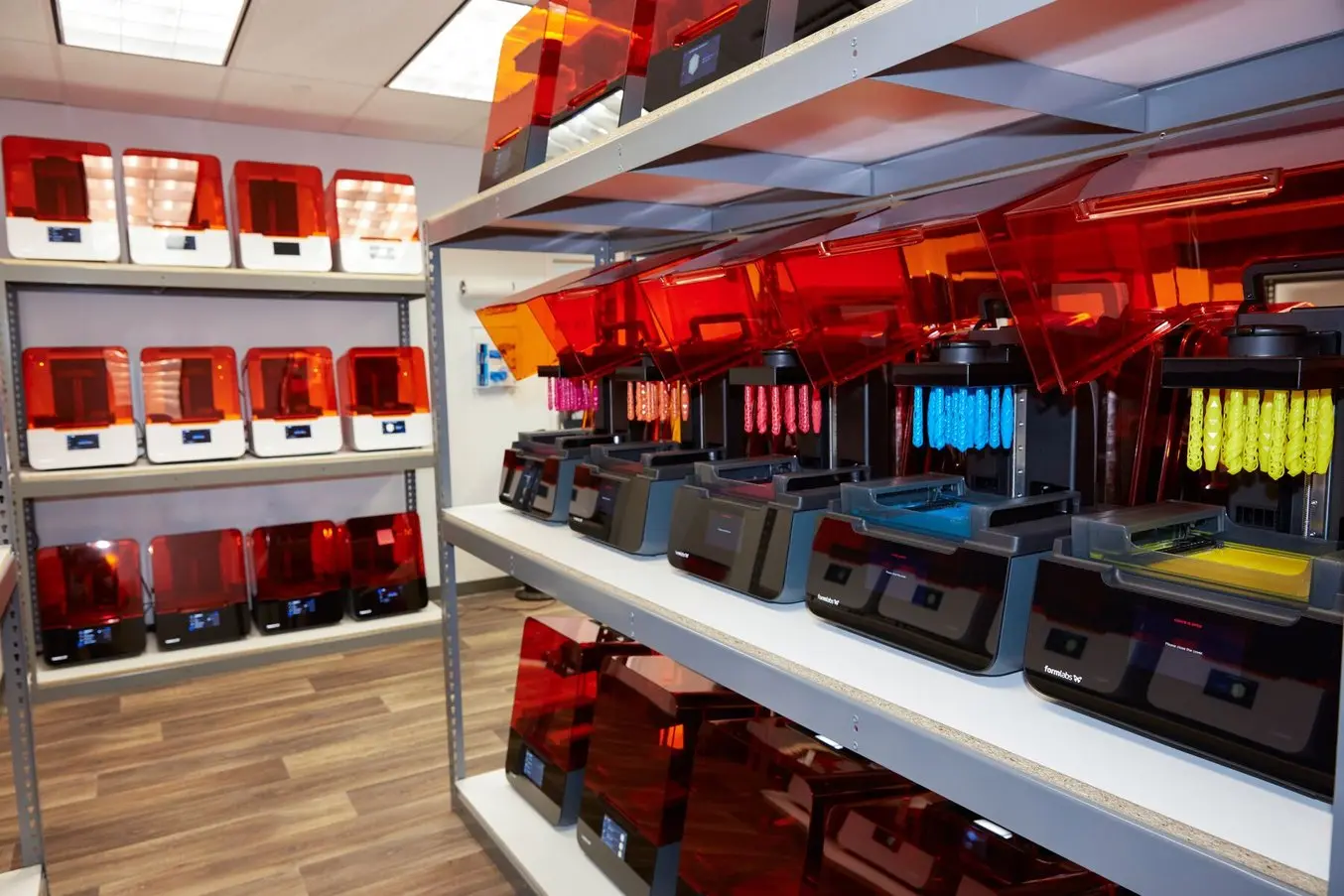
How to Unlock Low Volume Production and Custom Manufacturing with 3D Printed End-Use Parts
Watch this webinar to learn how to achieve custom manufacturing and low volume production of end-use parts quickly and cost-effectively with industrial 3D printers.
Improving Economics for Mass Customization
Healthcare, dental, and jewelry industries are the first to take advantage of additive manufacturing for mass customization, but as technologies and materials improve and costs shrink, 3D printing applications are expanding for a wider range of products, like consumer goods and functional parts for industrial equipment.

One of the most promising trends is mass customization, which combines the flexibility of custom-made products with the low unit costs achieved in mass production. Customized products can offer tangible benefits and create higher value perception for customers while providing higher margins than mass production for the manufacturers.
By reducing the time it takes a product to get from concept to the customer, additive manufacturing will also enable companies to become more agile in manufacturing and respond faster to trends and changes in customer needs.