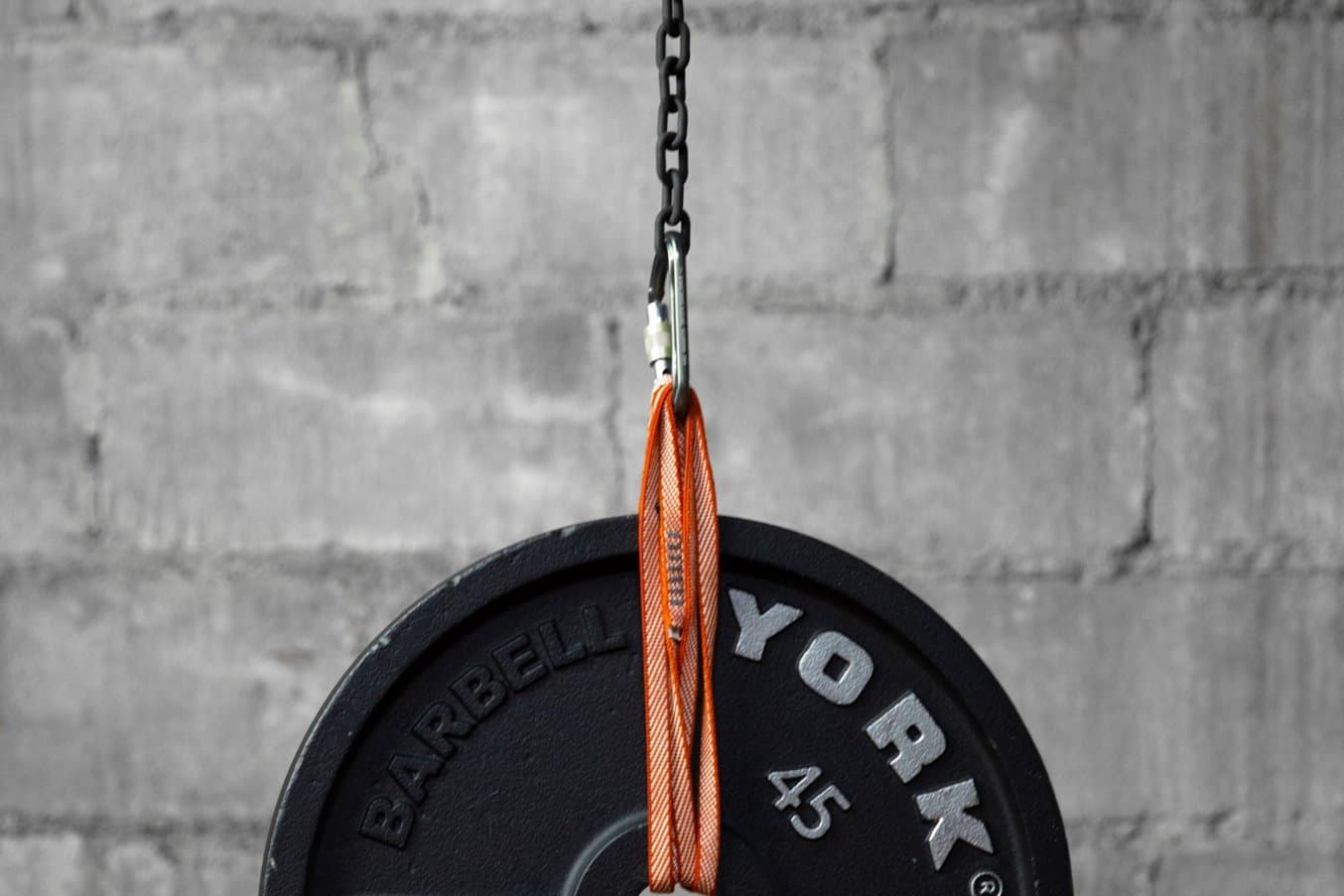
Bikes, racecars, drones, and tennis rackets—products with varied uses that all require high strength and durability without added weight. This combination of properties is found in carbon fiber composite materials that are used everywhere from the chassis of Formula 1 racecars to the frame of lightweight road bicycles.
As many professional 3D printers also commonly use polymer-based materials, including various composites, many people ask the question, “can you 3D print carbon fiber?”
Indeed, there are two methods through which 3D printing can be used to create carbon fiber parts: by supporting traditional methods of fabrication with 3D printed molds, or through the direct 3D printing of carbon fiber composites. In this article, we’ll walk through traditional means of fabrication as well as new workflows for 3D printed carbon fiber molds and direct 3D printing of carbon fiber composite parts.
Combining Traditional Methods to Create Carbon Fiber Parts With 3D Printing
Carbon fiber is a composite material traditionally manufactured by weaving long strands of carbon fibers together, then binding them further with a polymer. The strands can be woven strategically so that strength is aligned along one certain vector, or so that the end product has multilateral strength in every direction. The resulting material is then formed into the desired end product through typically one of three processes: wet lay-up, prepreg lamination, or resin transfer molding (RTM).
Wet Lay-Up
In wet lay-up manufacturing, sheets of carbon fiber are cut and pressed into a mold, then painted with a liquid resin, which, as it cures and solidifies, binds the sheets into the desired final shape. This method requires the least equipment and is also the easiest to master as a beginner. Because most of it can be done by hand, it is one of the least expensive methods, but the tradeoff is that the resulting parts have less fidelity to the mold master than parts produced through other methods.
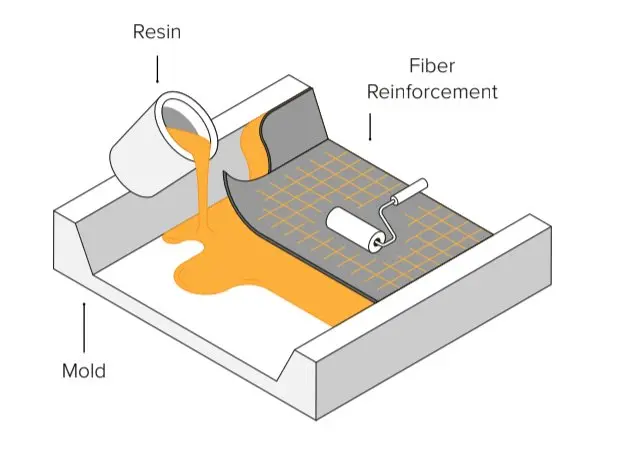
Prepreg Lamination
In this method, the carbon fiber is already infused with resin, then inserted into a mold that uses pressure and heat to form the final shape. This method is the most expensive due to the necessity of specialized equipment to store and handle the pre-infused sheets, as well as the heated and pressurized molding machine. These factors are also what make it the most repeatable and consistent, and thus most appropriate for batch production of carbon fiber parts.
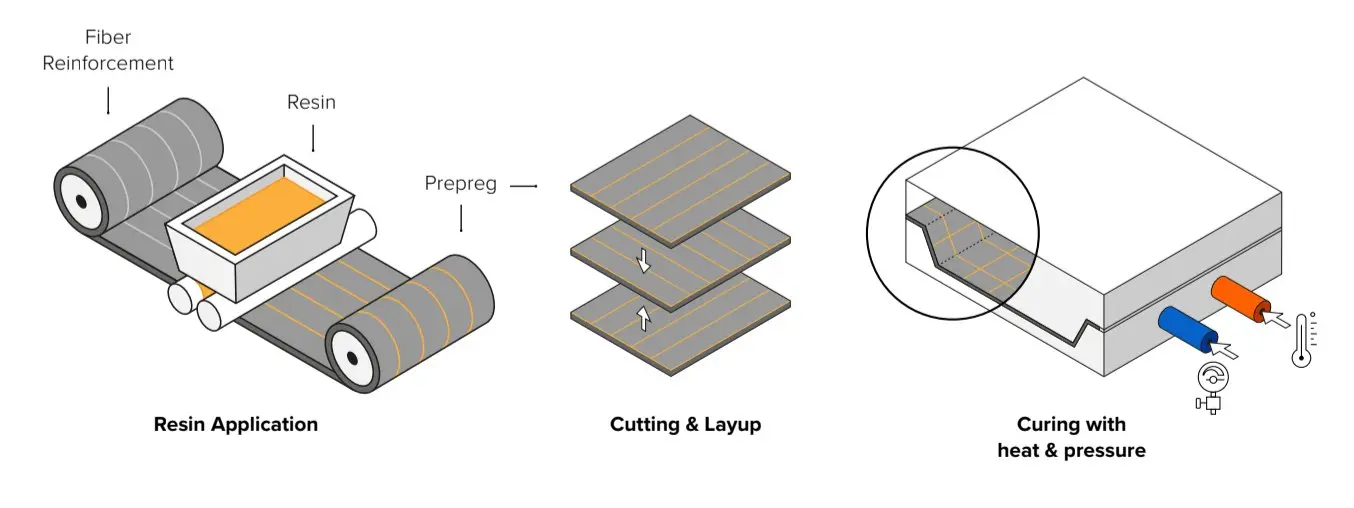
Resin Transfer Molding (RTM)
With RTM molding, the dry fiber is inserted into a two-part mold. The mold is clamped shut before forcing the resin into the cavity at high pressure. It is usually automated and used for larger volume manufacturing.
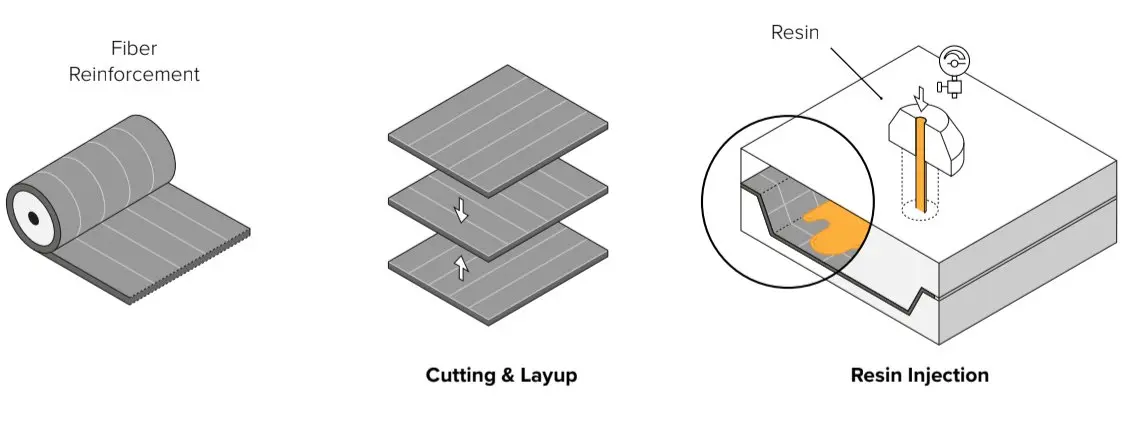
Manufacturing Carbon Fiber Parts With 3D Printed Molds
For each of the previous three methods, 3D printing can be used to bring down costs and improve lead times. All three traditional manufacturing methods require the use of a mold or multiple molds, which traditionally have been created through time-consuming subtractive processes like wood, foam, metal, plastic, or wax machining. 3D printing offers an alternative means of mold fabrication. 3D printed molds are customizable as well as more efficient and cost-effective for small batch production or customization.
For applications that require functioning prototypes like the automotive and aerospace industries, the iterative process might require hundreds of different molds. To make these iterations using traditional manufacturing methods can be expensive and time-consuming, so 3D printing provides an efficient means of low-volume production. Though 3D printed molds aren’t as suitable as metal molds for large-volume production, they can be created inexpensively in-house, speeding up product development and validation, as well as short-run production.
Molds for carbon fiber part production can be made with a variety of techniques, but the smooth surface finish and extensive materials library of stereolithography (SLA) resin 3D printers make them a common choice for in-house mold production. SLA parts have virtually no layer lines or porosity, so the carbon fiber sheets can be pressed firmly into the mold without fear of creating a textured surface.
Panoz, a racing and sports car manufacturer, needed a custom air exit duct for the cockpit of a racing car in order to vent air out of the cabin and cool down the temperature inside. In collaboration with DeltaWing Manufacturing, they used a Formlabs SLA 3D printer to print the pattern in High Temp Resin, then cast a mold on that printed pattern by hand, using a high-temperature tooling epoxy. In using 3D printing, DeltaWing avoided outsourcing an expensive metal mold for this custom carbon fiber part, reducing both their overall cost and delivery time.
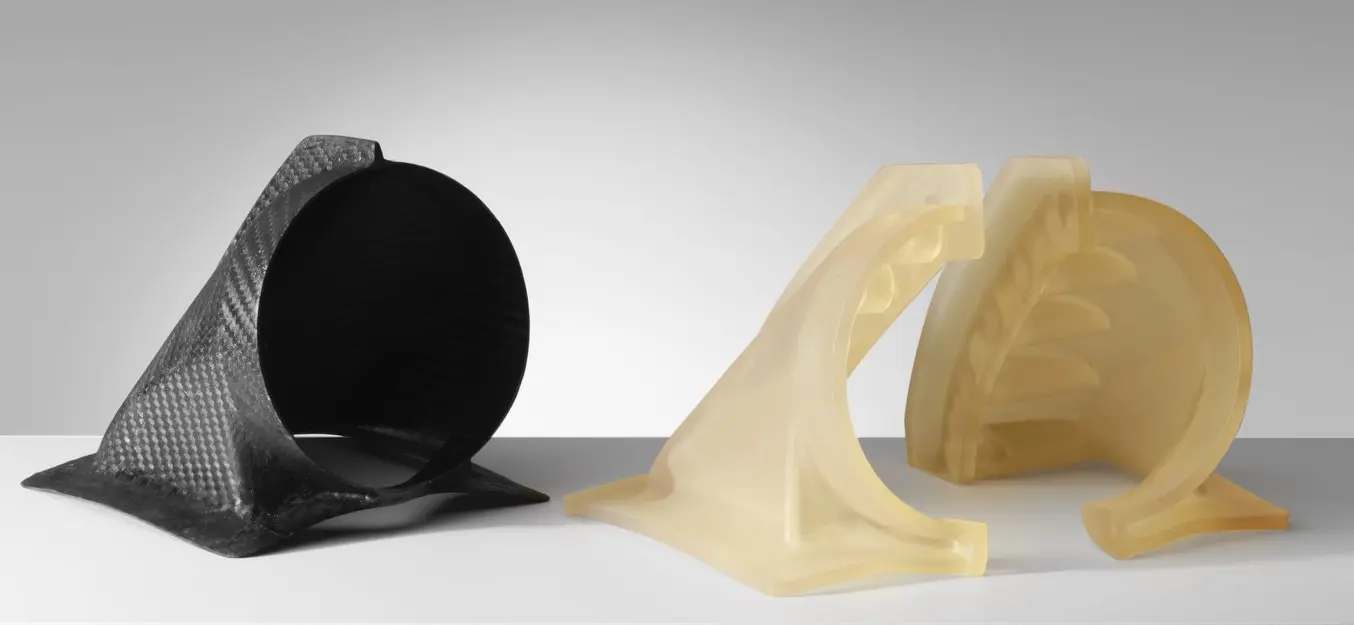
A carbon fiber fender air duct next to the two-parts mold printed with High Temp Resin, produced by DeltaWing Manufacturing.
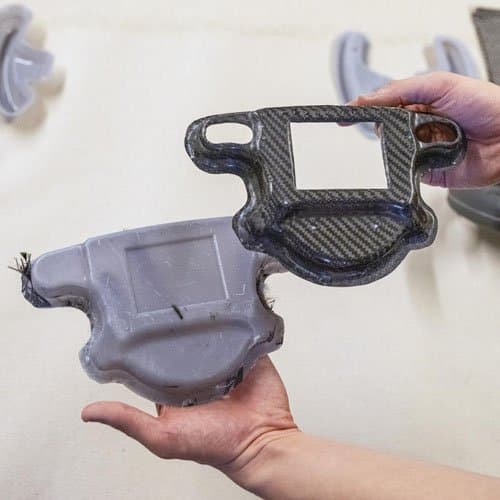
Carbon Fiber Parts Manufacturing With 3D Printed Molds
Download this white paper for composite mold design guidelines and step-by-step guides to the prepreg and hand laminating methods to create carbon fiber parts.
Direct Carbon Fiber 3D Printing
Looking for the best carbon fiber 3D printer? There is strong demand for workflows that combine the strength, durability, and ruggedness of traditional carbon fiber parts with the agility, geometric possibilities, and repeatability of 3D printing. It’s therefore not surprising that there are many 3D printing companies that offer carbon fiber 3D printing, with the two currently available processes being printing with chopped fibers or continuous fibers.
Chopped Carbon Fiber 3D Printing
Chopped fibers refer to a 3D printing composite plastic material that is imbued with small pieces of carbon fibers. These chopped fibers lend extra strength to the composite, which can be a carbon fiber filament for fused deposition modeling (FDM) or a nylon powder for selective laser sintering (SLS) 3D printing.
The main advantages of chopped carbon fiber-reinforced 3D printed materials compared to other types of polymer-based 3D printed materials are that they are strong, lightweight, heat-resistant, and less likely to creep. When compared to traditionally molded carbon fiber parts, 3D printed chopped fiber offers improved geometrical flexibility in the design of the part, especially with SLS 3D printing, potentially eliminating extensive labor associated with traditional molding, or opening up new innovative possibilities for users to incorporate this material into their workflow.
The Formlabs Fuse 1+ 30W SLS 3D printer enables this type of carbon fiber 3D printing with Nylon 11 CF Powder—the strongest material in the Formlabs SLS materials library. The Fuse 1+ 30W presents the most affordable high-performance option for SLS printing with chopped carbon fibers. While traditional industrial SLS machines also offer some carbon fiber materials, the start-up cost for adoption negates much of the added benefit for 3D printing of carbon fiber parts when compared to RTM or prepreg lamination methods.
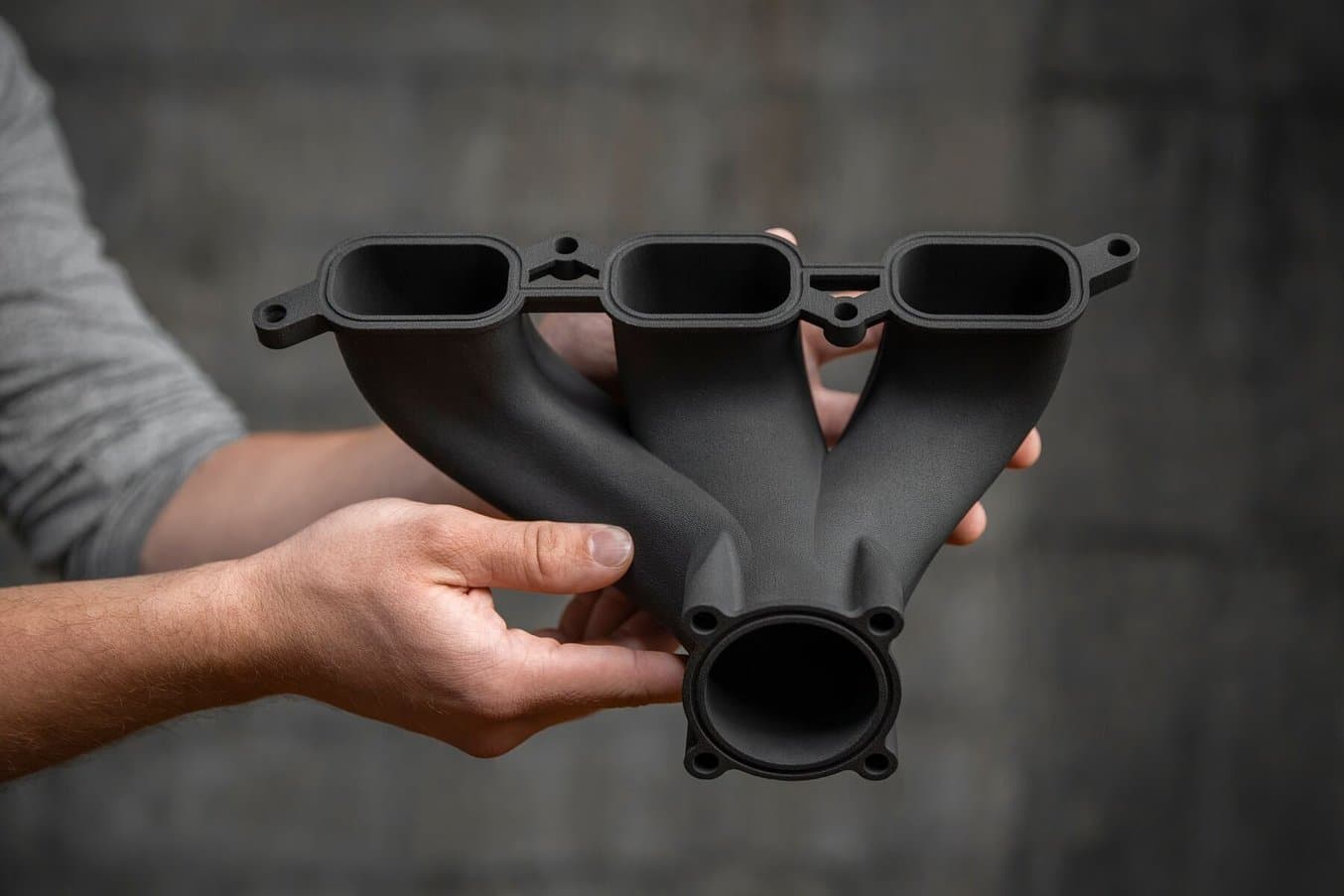
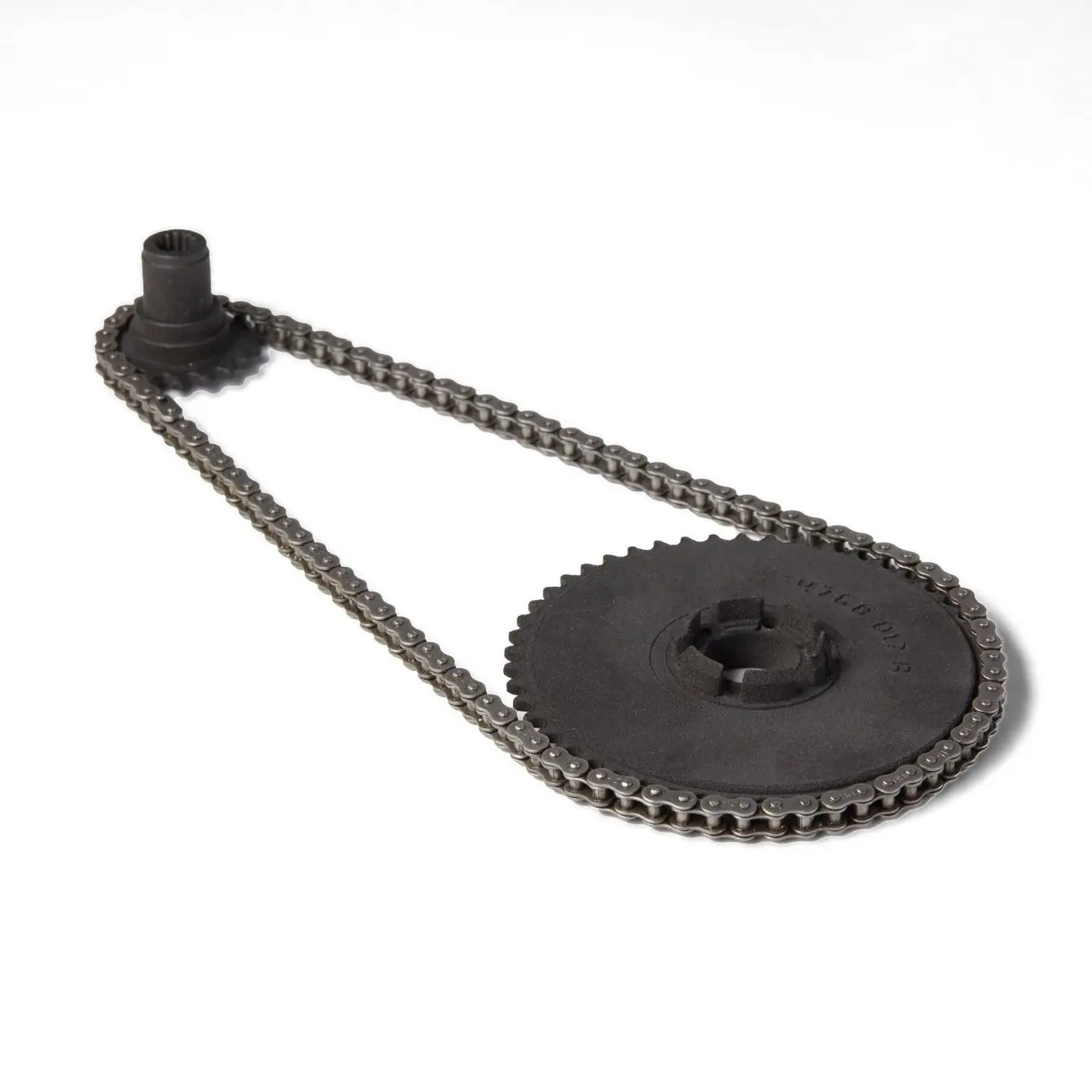
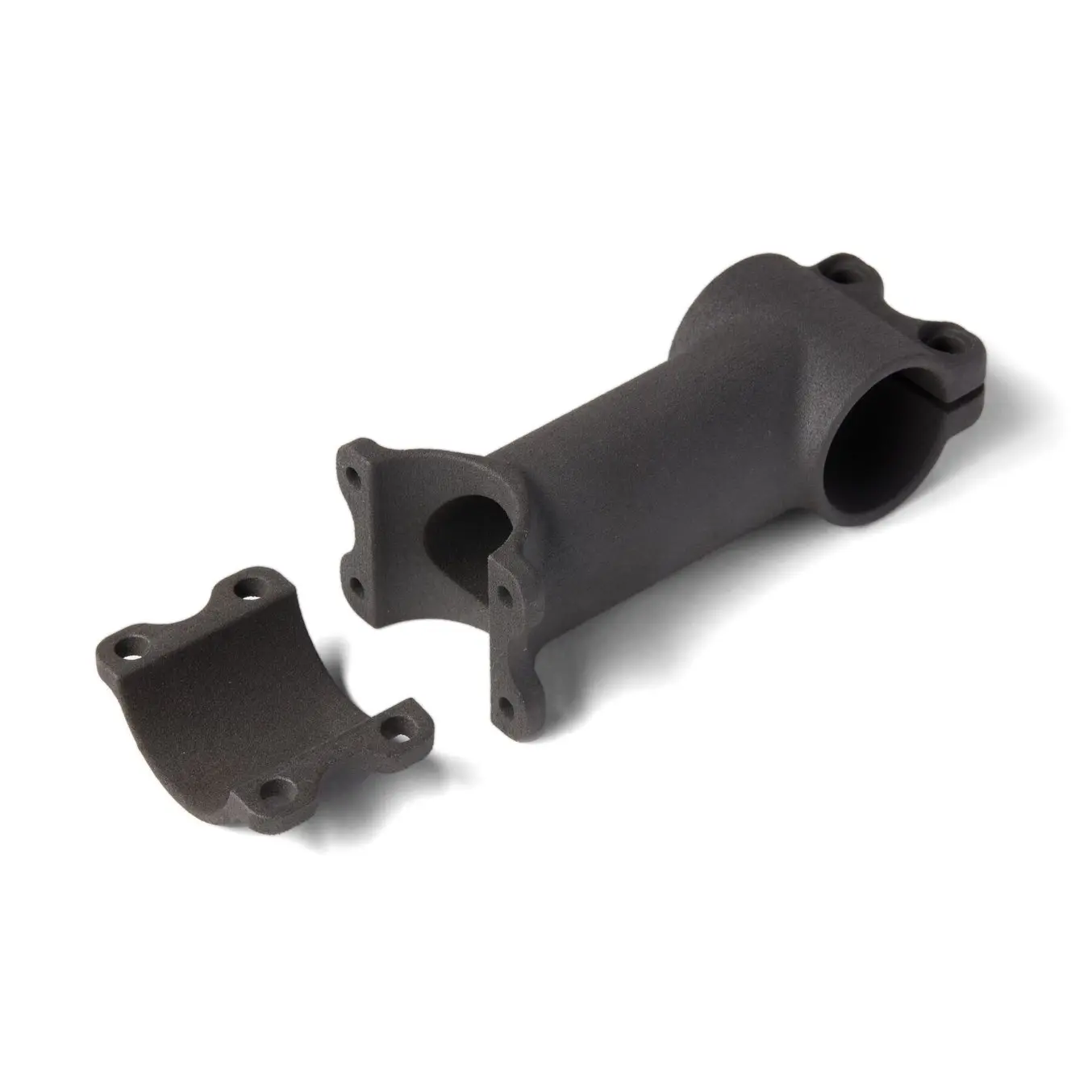
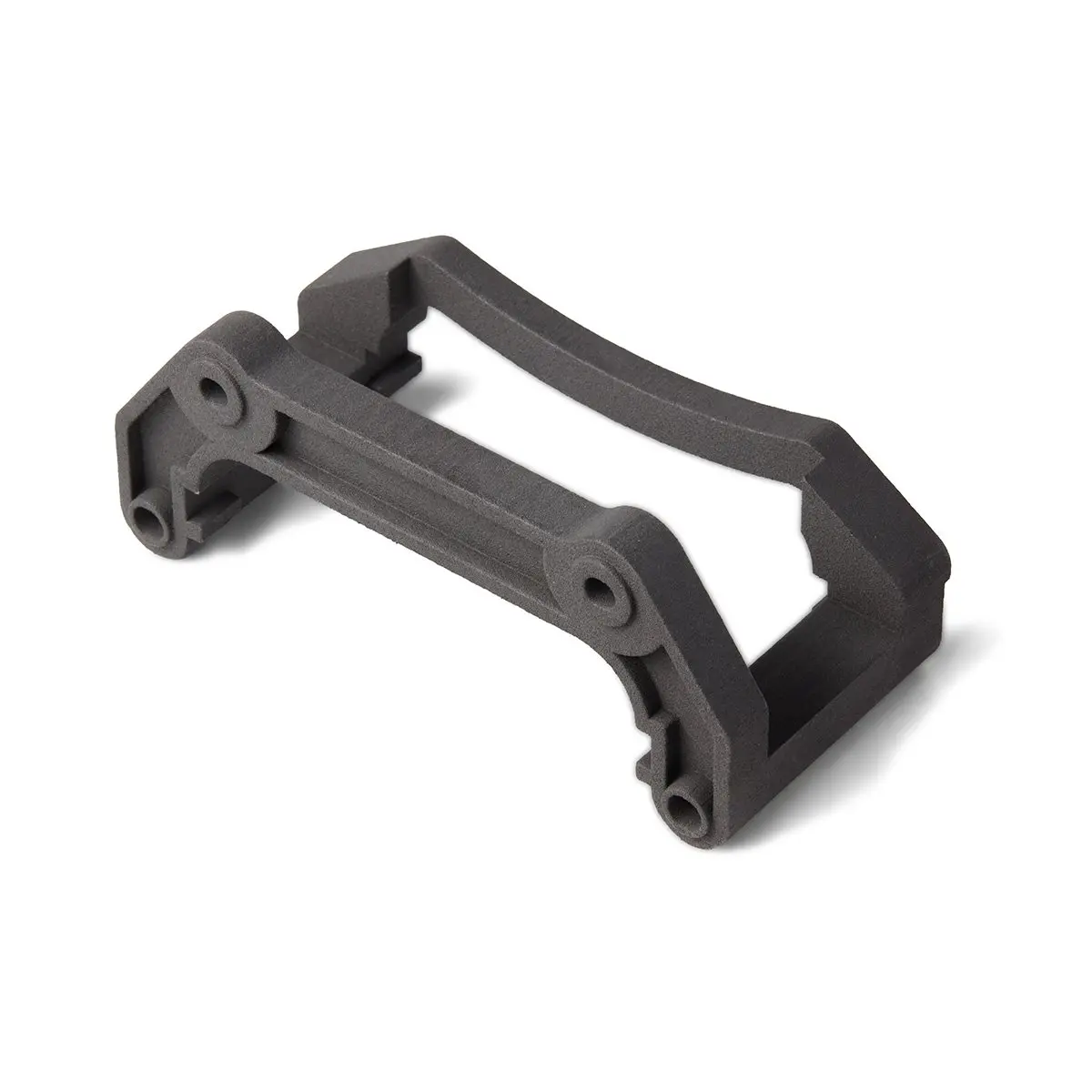
Formlabs Nylon 11 CF Powder is strong, lightweight, and heat resistant, making it ideal for automotive, aerospace, and manufacturing applications.
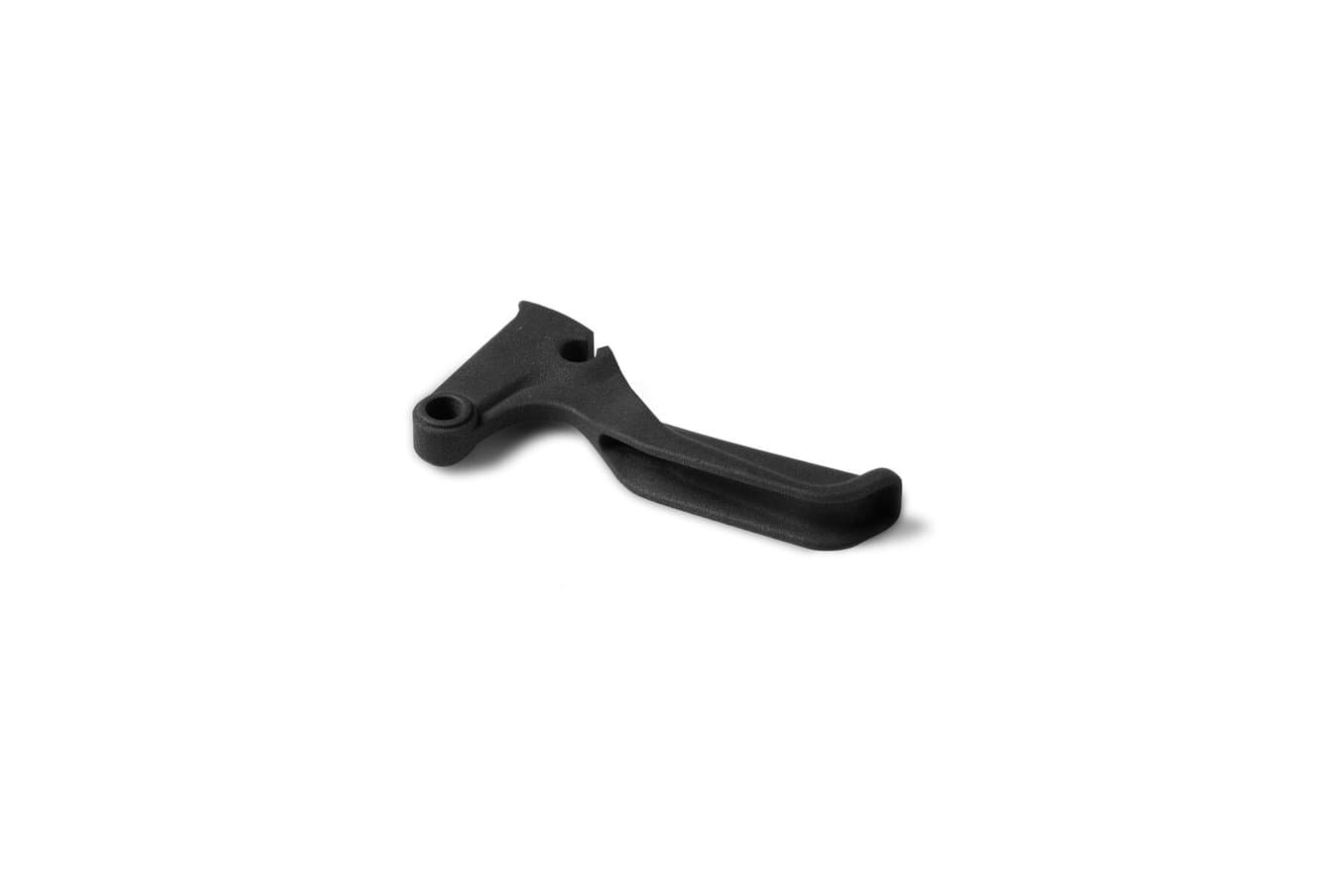
Request a Free Sample Part
See and feel Formlabs quality firsthand. We’ll ship a free sample part to your office.
Many FDM 3D printers can operate with carbon fiber filaments, but printing with these materials is more complicated than with standard ABS or PLA filaments, leading to frequent clogging and more maintenance as the abrasive filament wears down brass nozzles. FDM 3D printers specially designed for chopped carbon fiber filaments are also available, but at a premium.
The main limitation of both SLS and FDM chopped fiber 3D printed parts is that they should be considered more like strong 3D printed parts and not genuine alternatives to traditional carbon fiber parts with woven and continuous fibers. They also offer the biggest increase in strength in the direction they were laid down during 3D printing—X direction for SLS parts and XY plane for FDM parts. Traditional methods of carbon fiber part creation enable multidirectional strength by the careful planning and placement of different sheets of carbon fiber in the pre-mold set-up.
Continuous Carbon Fiber 3D Printing
Continuous carbon fiber 3D printing is available on some specialized FDM 3D printers and the parts it produces can approach traditional carbon fiber parts in terms of strength, but similar to chopped fiber FDM printers, only on the XY plane. With these printers, continuous strands of carbon fiber are mixed with the thermoplastic, and the strands can be applied strategically, to selectively enforce certain planes or axes of pressure. This method can utilize either a dual extruder nozzle to lay down a combination of carbon fiber threads and polymer, or a two-in-one, in which one nozzle deposits the carbon fiber thread while the other heats and extrudes the filament.
Continuous carbon fiber 3D printing offers an alternative comparable to traditional molded carbon fiber parts, albeit with limited design freedom. Though these parts are incredibly strong, that strength is only in the XY plane, and prints need to be oriented to match that strength with the direction of force applied. For designs where this is possible, this method can be used to replace aluminum parts and to create sturdy manufacturing aids or end-use parts.
Comparison: Traditional Carbon Fiber Fabrication and Carbon Fiber 3D Printing Workflows
Wet Lay-Up | Pre-Preg Lamination | Resin Transfer Molding | Chopped Fibers FDM 3D Printing | Chopped Fibers SLS 3D Printing | Continuous Fibers FDM 3D Printing | |
---|---|---|---|---|---|---|
Manufacturer and Model | Various | Various | Various | Markforged Onyx, Markforged X3 | Formlabs Fuse 1+ 30W | Markforged Mark Two, Desktop Metal Fiber, Markforged X7 |
Accuracy | ★★★☆☆ | ★★★★★ | ★★★★★ | ★★★☆☆ | ★★★★★ | ★★★☆☆ |
Surface Finish | ★★★☆☆ | ★★★★★ | ★★★★★ | ★★★☆☆ | ★★★★☆ | ★★★☆☆ |
Design Freedom | ★★★☆☆ | ★★★☆☆ | ★★★☆☆ | ★★★★☆ | ★★★★★ | ★★★★☆ |
Lightweight | ★★★★★ | ★★★★★ | ★★★★★ | ★★★★☆ | ★★★★☆ | ★★★★☆ |
Strength | ★★★★★ | ★★★★★ | ★★★★★ | ★★★☆☆ | ★★★☆☆ | ★★★★★ |
Strength in Which Directions | XYZ | XYZ | XYZ | XY | X(Y) | XY |
Throughput | ★☆☆☆☆ | ★★★☆☆ | ★★★★★ | ★★★☆☆ | ★★★★☆ | ★★★☆☆ |
Equipment Cost (specific) | Variable, starting at <$100 | Variable, starting at <$3000 | Variable, generally $100,000+ | Desktop solutions start at $5,000, industrial solutions around $40,000 | Complete industrial solution starting at $39,243 | Desktop solutions start at $20,000, industrial solutions around $70,000 |
Per Part Cost | $$$$ | $$$ | $$ | $$$ | $$ | $$$$ |
Ideal For | Custom high performance products, entry-level workflow | Low to medium volume production | High volume production | Rapid iterations, strong 3D printed parts | Rapid iterations, complex geometries, small batch production of strong 3D printed parts | Rapid iterations, 3D printed parts as strong as traditional carbon fiber composites (in XY directions) |
Advantages | High strength Low equipment cost | High strength | High strength Precision and repeatability Automation possibilities | Inexpensive No tooling required | Precision and repeatability Design freedom No tooling required | High strength No tooling required |
Drawbacks | Labor intensive Difficult to maintain high quality | Labor intensive | Expensive tooling and machinery | Anisotropic strength Lower strength Hard to print | Anisotropic strength Lower strength | Anisotropic strength |
How Strong Is 3D Printed Carbon Fiber?
The mechanical properties of 3D printed carbon fiber composites surpass almost every other 3D printed plastic in terms of strength and temperature resistance. Let’s look at how chopped fibers compare to continuous fiber 3D printing and common materials for reference.
Manufacturing Process | SLS - Chopped Fibers | FDM - Chopped Fibers | FDM - Continuous Fibers | FDM - Continuous Fibers | Injection Molding | Casting or Machining |
---|---|---|---|---|---|---|
Material | Formlabs Nylon 11 CF Powder | Carbon Fiber-Filled Nylon Filament | Nylon 6 Filament + Carbon Fiber | PEEK Filament + Carbon Fiber | ABS | Aluminum |
Tensile Modulus (GPa) | 1.6 - 5.3 | 2.4 | 60 - 100 | 145 | 2.3 | 70 |
Ultimate Tensile Strength (MPa) | 38 - 69 | 40 | 800 - 1000 | 2400 | 39 | 310 |
Flexural Modulus (GPa) | 4.2 | 3.0 | 51 - 71 | 124 | 2.4 | 70 |
Flexural Strength (MPa) | 110 | 71 | 540 - 800 | 1300 | 74 | 310 |
Elongation at Break | 5 - 15% | 25% | 1.5% | N/A | 6 - 15% | N/A |
Notched Izod (J/m) | 74 | 330 | 960 | N/A | 200 | N/A |
Heat Deflection Temp. @ 0.45 MPa (°C) | 188 | 145 | 105 | N/A | 70 - 107 | N/A |
Applications for Carbon Fiber 3D Printed Parts
The high strength, light weight, as well as impact, heat, and chemical resistance of carbon fiber 3D printed parts make them ideal for a variety of applications where 3D printing wasn’t even considered before. Plastic and carbon fiber composite 3D printed parts can now stand up to the heat generated by automotive or aerospace engine components, be used as replacements for machined aluminum parts and manufacturing aids, and enable the production of long-lasting, high-impact equipment.
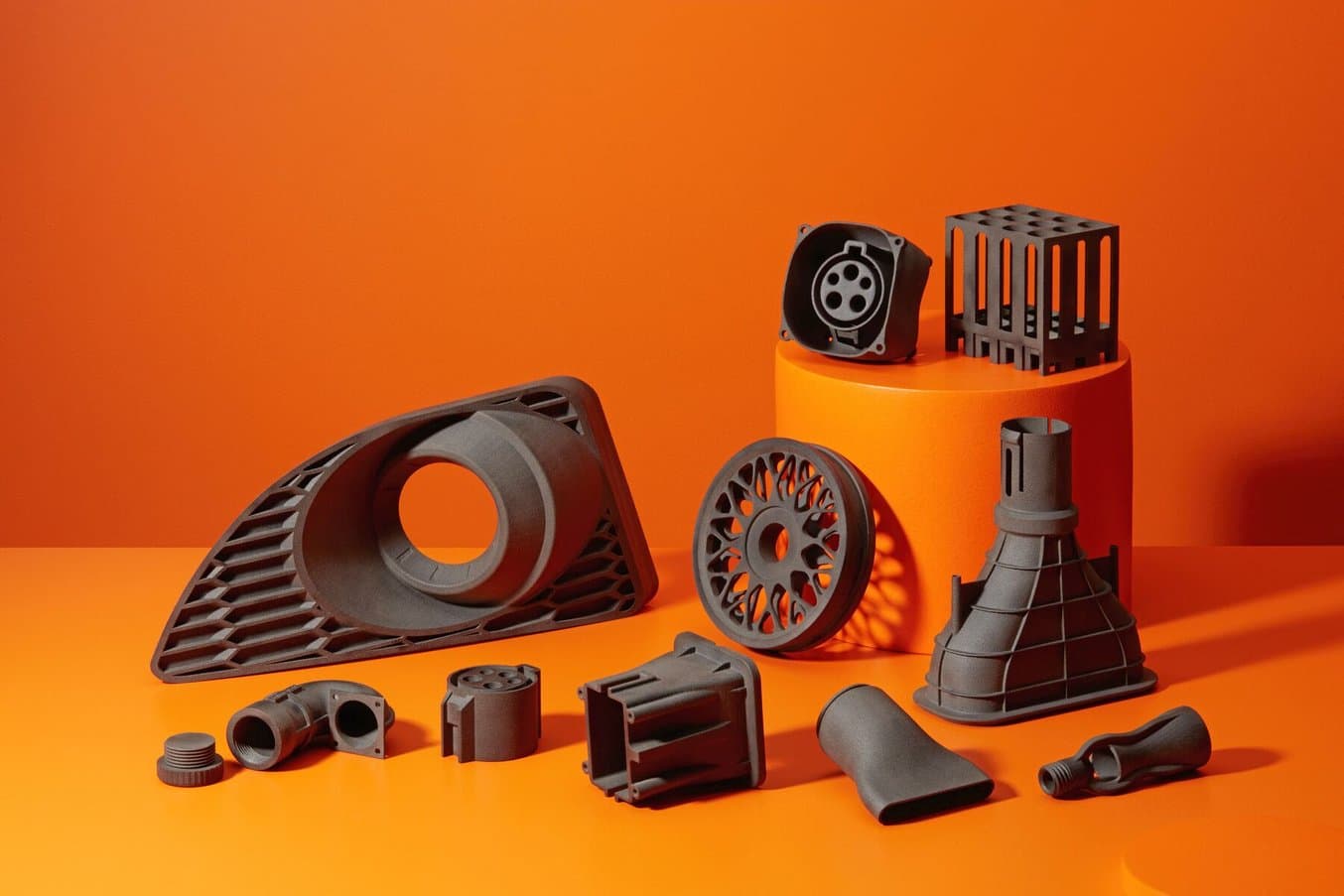
Carbon fiber 3D printed parts are ideal for rapid prototyping, producing wear-resistant and durable manufacturing aids such as jigs and fixtures, and the small batch production of strong end-use parts with complex geometries.
3D printing technology has opened up new possibilities in design and manufacturing, and 3D printed carbon fiber composites take that even further, allowing users in the automotive, aerospace, defense, and manufacturing industries to quickly and efficiently produce high-strength, temperature-resistant parts with geometric flexibility. By bypassing traditional machining or molding processes, these users can more easily create custom parts, replacement parts, and functional prototypes. Though not a total replacement for traditional techniques due to the singular plane of added strength, 3D printed carbon fiber parts are still stronger than almost most other plastics, making them singularly useful in many applications.
The right process to produce carbon fiber parts by molding or directly by 3D printing is highly dependent on the specific application, and factors like part design, production volume, and more. SLS 3D printing with chopped fibers offers a sweet spot for those looking to manufacture strong parts, but not necessarily to the degree of traditional molded carbon fiber parts.
The Formlabs Fuse 1+ 30W with Nylon 11 CF Powder enables businesses without extensive funding and on tight time schedules to iterate rapidly and produce end-use parts with strength and advanced mechanical properties, unlike traditional plastics. They can also functionally test their parts and then change the design with only a slight CAD modification, improving their product’s performance, and getting to market sooner.
Request a free sample part now to see the quality and strength of an SLS 3D printed chopped fiber part firsthand or speak to one of our specialists to find the right solution for your application.