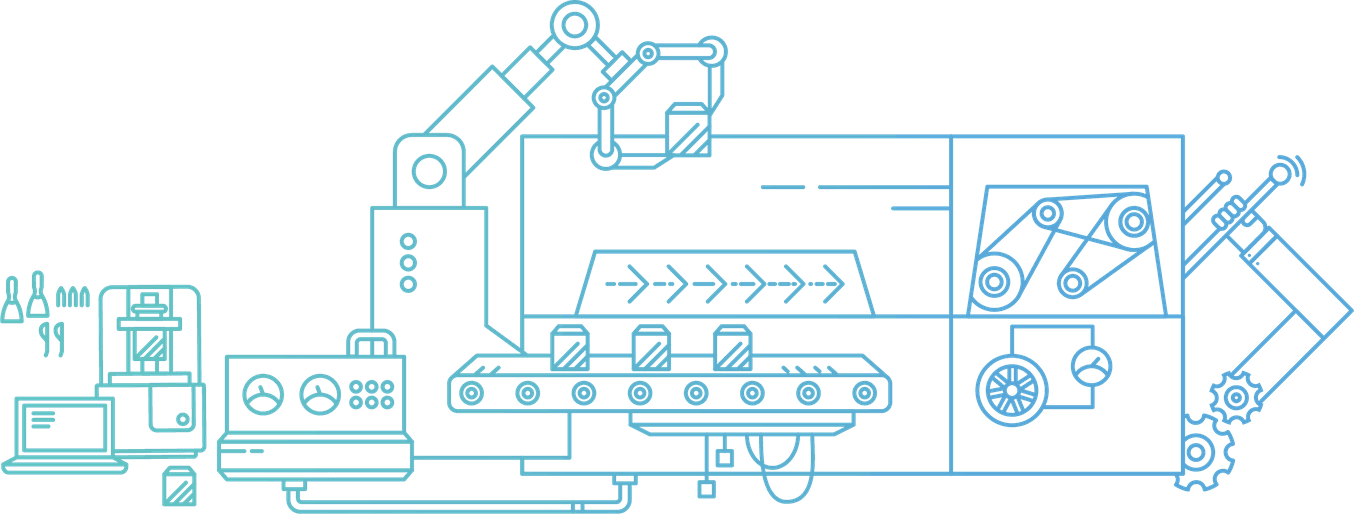
In honor of our conference on digital manufacturing, The Digital Factory, Formlabs is pleased to publish the first episode of our limited-run podcast! In this series, hosted by O’Reilly Media’s Jon Bruner, we’ll explore the future of the factory floor through conversations with experts who are changing the way things are made.
In episode 1, we sit down with Formlabs CEO and founder Max Lobovsky to explore the present and future of 3D printing. Play the full podcast below to hear:
- Max’s take on where additive manufacturing is headed
- The role of other design and engineering tools alongside 3D printing
- What’s next for Formlabs products
Max Lobovsky on What’s Next for 3D Printing
What’s the status of the additive manufacturing industry now, and how does Formlabs fit into that landscape?
“There was this big wave of hype, starting around five years ago, where people got interested in the idea of consumer 3D printing,” says Max, “That phase of public discussion has mostly gone away, but there’s still a huge amount of interest in growing applications for 3D printing, in different professional, engineering, and manufacturing use cases.”
On Where 3D Printing is Already Normalized:
“At this point, in almost any field where 3D design is part of what you’re doing, from product design, mechanical engineering, industrial design, architecture, jewelry, even dental, 3D printing has found its way in. It’s either already very common in places like product design, or sort of on track to be totally normal.”
On Simplifying the 3D Printing Workflow:
“The end goal we think about in this part of the 3D printing market is to make 3D printing more like 2D printing, where if you work on a document, or you’re any way involved in some kind of 2D design, documents, photos, whatever, you press print on your office 2D printer, and you don’t really think about the cost, or how long it’s going to take, or really worry about it. If you want the thing on paper, you get it. And I think we’re part of the way to bringing 3D printing to that level for anyone involved in 3D design.”
On Making 3D Printing for Production More Accessible:
“One of the biggest aspects to [making 3D printing for production more accessible] is driving the per-part cost down. Basically, it comes down to two questions. Can you make the part with all of the requirements of the part? Which is often largely a materials question. Can you make something out of the right materials? Can you drive the per-part cost down to be competitive with some traditional manufacturing methods?”
On the Potential of Generative Design:
“Generative design tools like nTopology allow you to go beyond replacing a part that you made some other way with 3D printing, but actually making a better part that can only be 3D printed. Especially in the near term, this is very important. If you can make it better, lighter, faster, stronger, through 3D printing, that offers some real advantages.”
On the Learning Curve for New Production Tools:
“Especially as we talk about more production use cases, we can help adoption by getting more people to understand how to work with the tools. Your average mechanical engineer or designer learned their sort of implicit understanding of the different fabrication processes and the constraints on the parts they’re designing over time, slowly picking it up, and most manufacturing technologies are hundreds of years old. 3D printing is still in the infancy of being understood by the people designing these parts.”
Join the Conversation at The Digital Factory
Stay tuned for the next episode of the podcast in a couple weeks, and consider joining Formlabs on June 5 in Cambridge, MA, at The Digital Factory, a one-day conference on digital manufacturing. Hear more from Max Lobovsky and Jon Bruner and intermingle with business pioneers, investors, innovators, startups, and thought leaders reinventing the factory floor.