Superseding Three Resin Printers With One: How a Service Bureau Scaled Up With Form 4L

Additium3D is a Spanish service bureau that offers companies an end-to-end solution from pre-print services such as consulting, 3D design, and scanning, to additive manufacturing with 3D printing including fused deposition modeling (FDM), stereolithography (SLA), and selective laser sintering (SLS). While adopting a low-cost resin printing enabled Additium3D to increase productivity and improve pricing, this came at the cost of health and safety. “Print failures, dust, and the toxicity of Phrozen resins overwhelmed our production facility,” says Guillermo Navarro, Director at Additium3D.
Resin printing allowed Additium3D to gain a major client, but the health risks were impacting everyone, and the 30% failure rate of prints was costly. In 2025, Additium3D replaced their three Phrozen printers with one Form 4L.
“We couldn't be happier. The speed improvement that your technology has achieved is amazing compared to the Form 3 generation. With just one Form 4L, considering its productivity and reliability, we are achieving the same output as we did with three Phrozen Mega printers.”
Guillermo Navarro, Director at Additium3D
Workplace Safety
Workplace safety has been top of mind for Navarro since the severe floods in October 2024, when he was trapped inside his factory. In addition to the material damage to the company, Navarro and his brother suffered physical harm. He says, “After such an experience, we made the decision to prioritize health over profit maximization. The best part is that we discovered the economic difference was minimal, thanks to the great advantages of the Form 4L in terms of reliability.”

The severe floods in October 2024 filled Additium3D with over 25 cm of water.

After the floods, Guillermo and Carlos made the decision to prioritize their health.
Top among the issues with Additium3D’s low-cost resin printers were health and safety conditions. Navarro says, “The toxicity of Phrozen resins overwhelmed our production facility. My brother even needed medical attention due to eyelid irritation caused by exposure to these resins.”
Formlabs resins are developed without the use of 4-Acryloylmorpholine (ACMO), a harmful and hazardous chemical found in many other resins. Additionally, resin cartridges and tanks are designed to reduce resin exposure, while Form 4 Series 3D printers feature automatic resin dispensing and smart sensors to improve user safety and experience. From printing through post-processing, Formlabs workflows are developed for user ease and safety. After using Form 4L, Navarro says, “The cleanliness of our production facility and our health and safety conditions have improved. Additionally, our client now refuses to accept any other print quality, and they are willing to pay more for better parts.”
Speed
Additium3D started with three Phrozen Mega 8K 3D printers as the combined build volume matched their production requirements. However, Navarro says, “Phrozen print times were not as fast as calculated in their software, reducing the productivity in some cases up to 50%, as it was not possible to make two print shifts per day and machine.” While one Form 4L has a comparable build volume, the print speed and reliability of Form 4L enables Additium3D to exceed the output of three Phrozen Mega 3D printers.
“The key difference lies in the productivity, reliability, and overall efficiency of the Form 4L. Its print speed, perfectly aligned with our daily shifts, allows for up to three full jobs per day, something the Mega couldn’t come close to.”
Guillermo Navarro, Director at Additium3D
The speed of Form 4L enables Additium3D to average two large prints per working day, printing prototypes and end-use parts, including mid-size production runs of high-end decorative pieces and figurines.
Reliability and Consistency
Failed prints result in wasted resin, time spent reprinting, and mess that requires manual clean-up. While a printer can be fast, if the part has to be reprinted, this can double the expected time to part, which is why speed combined with reliability are key.
“While the Phrozen printers had a failure rate of over 30% — due to adhesion problems, firmware bugs, or inconsistent results — the Form 4L has proven to be nearly flawless. This has a direct impact on actual production costs: while Phrozen resin is about half the price, the waste from failed prints and time lost made the real cost per part almost the same.”
Guillermo Navarro, Director at Additium3D
For batches of prints, consistency of print quality is also important. “We got tired of throwing away parts for different defects,” says Navarro of parts from the low-cost resin printers. “Not only parts that failed during the printing process, but also surface defects such as pinholes, resin cracks, layer shifts, warping, and layer separation that become very visible after having the parts painted.”
With Form 4L, Navarro has found that less than one percent of parts fail or have issues. This metric aligns with independent, third-party testing of Form 4 and other resin printers, which found that Form 4 has a 98.7% print success rate.
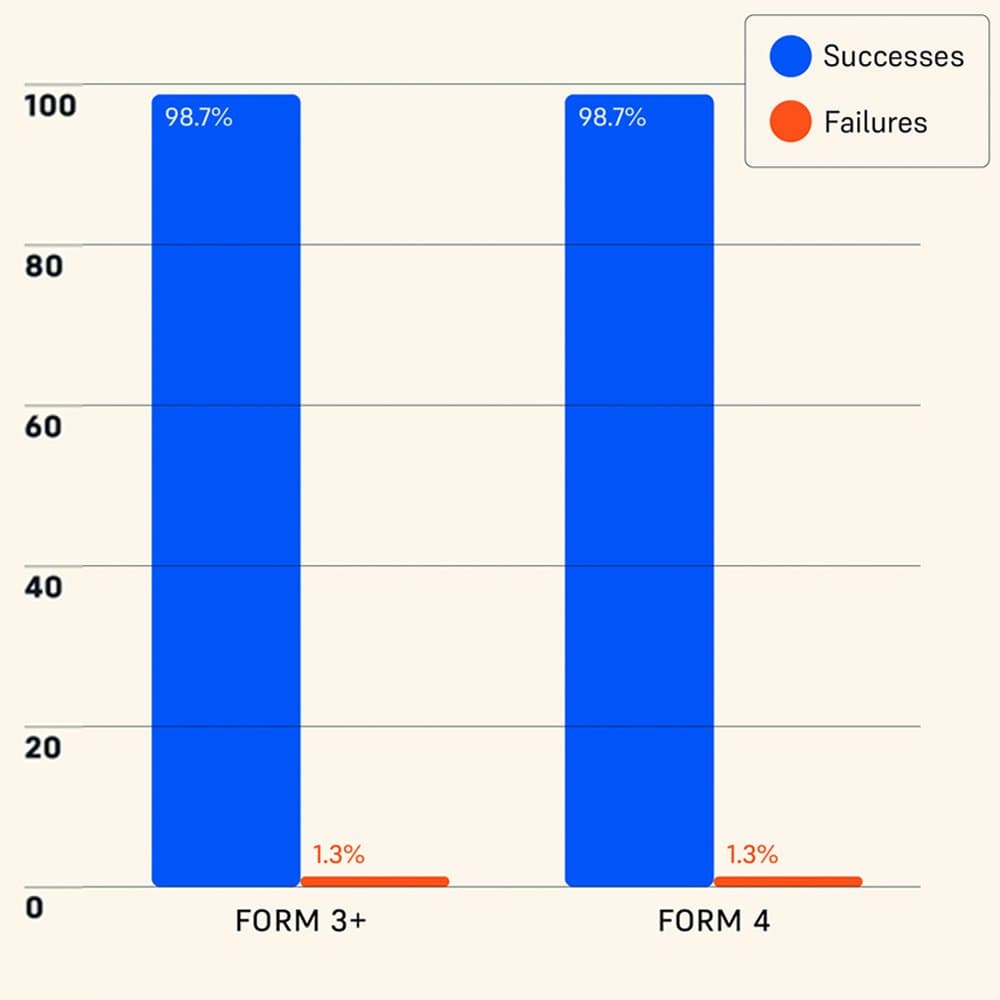
Independently Tested Reliability of Form 4 and Other Resin 3D Printers
Formlabs Form 4 was measured to have a 98.7% print success rate by an independent global leader in product testing. Read a complete description of the test methodology and see the results in our white paper.
Print Preparation Software
Every step in a workflow matters when it comes to efficiency. PreForm, Formlabs’ print preparation software, enables users to set up parts for printing with one click. With other slicers, Navarro found that the software would miss placing supports in key places, or place supports in undesirable areas based on piece geometry.
“PreForm keeps this simple and intelligent, making more compact, lighter, and easier to remove support structures. That combines with the interference detection. In the end, we have more parts per print and less material usage. Compared to our previous solution, we can place double the parts in the same build plate size.”
Carlos Navarro, CTO, Additium3D
Light-touch supports are easier to remove and result in smoother surface finishes, for less time spent post-processing and finishing. Additionally, PreForm’s print time estimates and material usage give service bureaus the information needed to quickly quote price and time to clients.
Versatile, High-Performance Materials
“For teams working on large-format prototypes who want to explore and test with a wide variety of high-performance materials, the technical resin portfolio from Formlabs — ranging from flexible and impact-resistant resins to high-temperature or biocompatible options — opens up possibilities that very few printers in this price range can offer.”
Guillermo Navarro, Director at Additium3D
Additium3D began printing with Clear Resin V5 and White Resin V5, as they were most suitable for the projects they’ve received. These are general-purpose resins formulated to leverage the technology of Form 4 Series 3D printers. Additium3D uses White Resin V5 for looks-like prototypes for client presentation, as well as for parts that need to be painted.

Additium3D uses Resin Pumping System to improve efficiency with fewer resin cartridge changes.
“We’ve been truly impressed with the new formulation of Clear Resin — its transparency and definition are a big step up from the previous version, and it’s been essential for producing visual or functional parts that need to simulate glass or transparent plastic.”
Guillermo Navarro, Director at Additium3D
Beyond general purpose resins, Additium3D has been working with Elastic 50A Resin, a soft, transparent elastomer with a 50A Shore durometer, for a client who requires test parts with very high flexibility. Durable Resin, similar in strength and stiffness to polyethylene (PE), is also a frequently used material, ideal for squeezable prototypes, low-friction assemblies, and jigs and fixtures undergoing significant impacts.
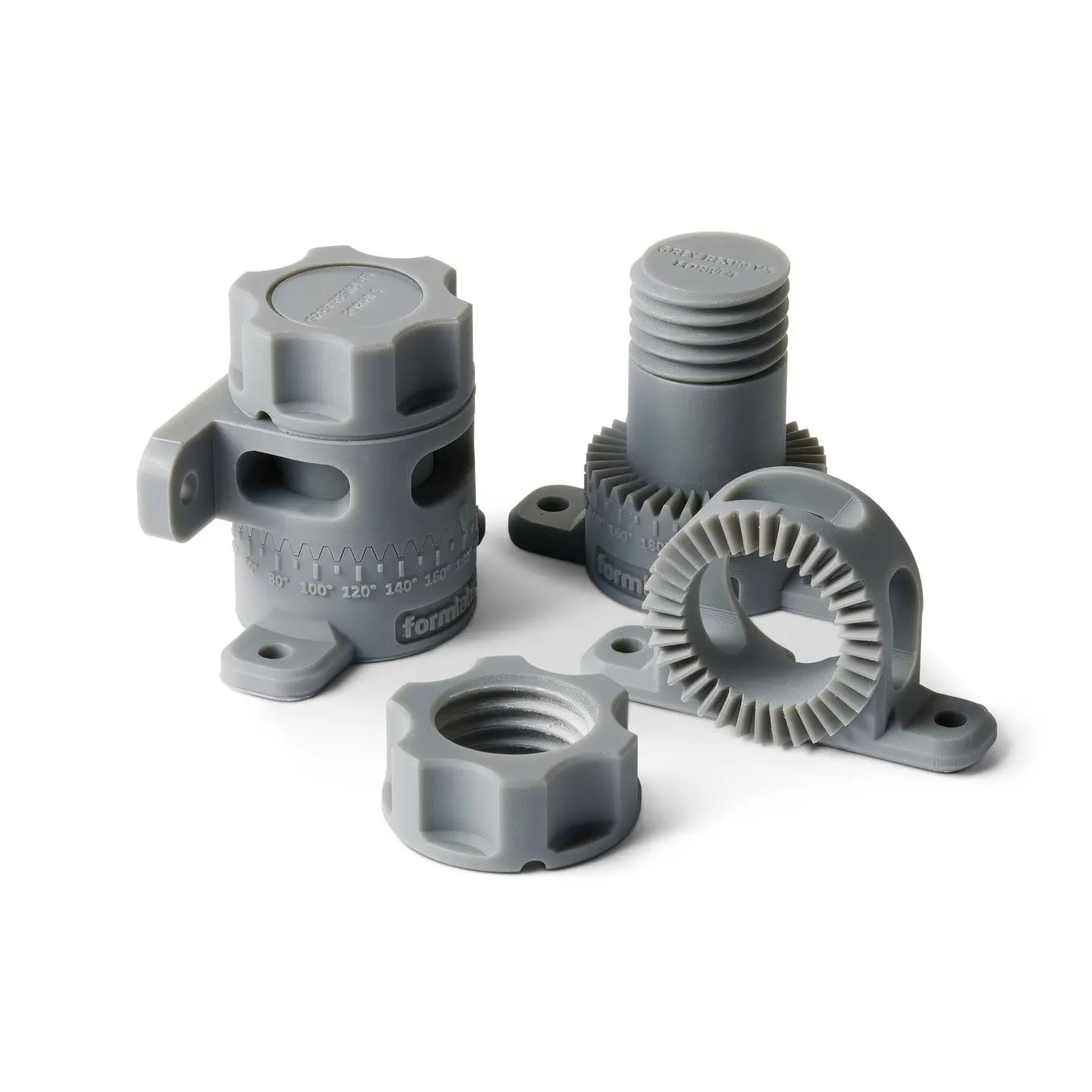
Request a Free Sample Part
See and feel Formlabs quality firsthand. We’ll ship a free 3D printed sample part to your office.
Growing a Service Bureau: Expanding 3D Printing and Material Options
“Whether it's for short-run manufacturing or high-end functional prototyping, the Form 4L is a truly powerful and versatile tool. We can go from concept to part in a matter of hours, validate complex geometries with no extra cost, and produce anything from a single unit to medium batches with outstanding efficiency. Its speed, reliability, and large build volume have allowed us to take on projects that were previously unfeasible with other technologies.”
Guillermo Navarro, Director at Additium3D

In addition to Formlabs SLA 3D printing, Additium3D offers SLS 3D printing on Fuse 1+ 30W.
As Additium3D takes on new projects, they are scaling up their 3D printing options, installing the Fuse Ecosystem for SLS 3D printing and post-processing, considering Form 4B so that they can add biomedical resins to their material options, and even the potential of adding a second Form 4L to further expand their throughput. All of this is in service to their mission of providing their clients with professional, high-quality parts and services.
To learn more, explore Formlabs 3D printers or contact sales.