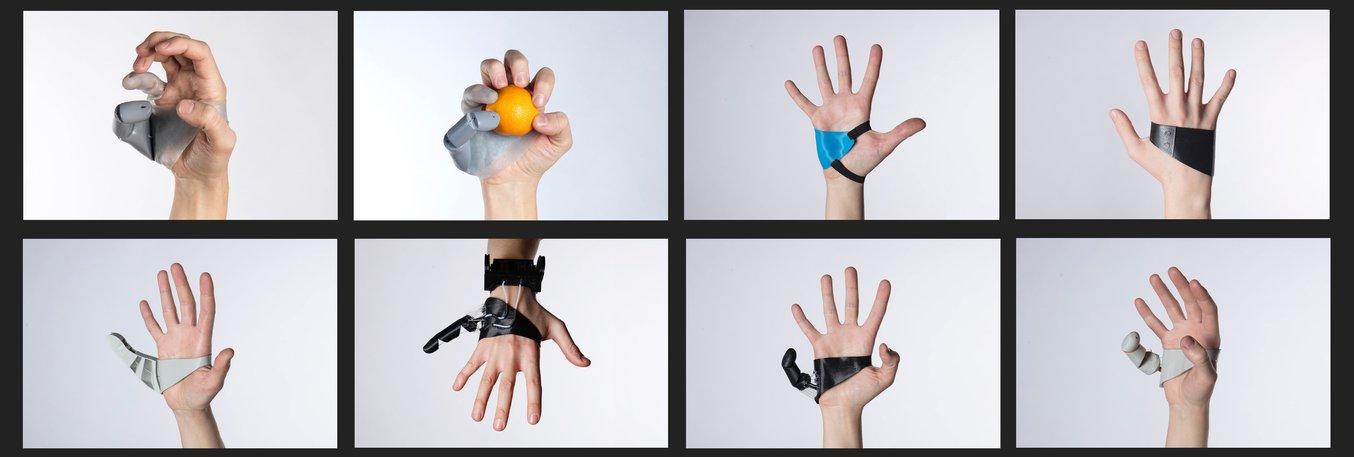
Dani Clode takes the meaning of prosthesis quite literally: rather than fixing or replacing, the Latin word's original meaning is to add something. With “The Third Thumb,” Clode has designed an attachable 3D printed thumb controlled by the feet–and challenges our perception of prosthetics.
Watch the video to learn how “The Third Thumb” works and how it extends the wearer’s abilities.
Her graduation project at the Royal College of Art in London combines a seemingly simple design with refined technology. 3D printing enabled the young designer to achieve the level of precision required for the prosthetic on an accessible machine and with a quick turnaround.
Clode’s design work is centered around the body and making human augmentation aesthetically appealing and approachable. Her previous work ranges from an experimental bone knitter, currently exhibited at the Vienna Biennale, to a prosthetic arm for the disabled model Kelly Knox.
“The Third Thumb” has been featured in various press outlets, including The Verge, Dezeen, and NBC News.
How did you get the idea for designing a 3D printed prosthetic?
The idea started when I was working on my dissertation at Royal College of Arts in London. I started to research prosthetics and became fascinated with them as a product. I came across the origin of the word “prosthesis” and found that it meant “in addition to.” This really inspired me to look into reframing prosthetics as extensions, rather than anything that “fixes” or “replaces.”
Prosthetics are such unique products; it’s a product relationship that is unlike any other, and I wanted to really explore this connection that develops between the wearer and the limb. I wanted the design to be able to be experienced by anyone.
How does 3D printing fit into your design process?
I utilize the Form 2 to prototype and realize final models. I don’t like to work on a design in 3D virtual space for too long. I usually create my first prototype, print it, and then return to Rhino to update the model. I can go back and forth like this up to five or six times before I am happy with my final print.
I think when you work in a virtual space too long, you start to lose the tangibility of the design, especially when it comes to designs that attach to the body. So it’s great that we now have the facilities as designers to be able to very quickly work in both physical and virtual space almost simultaneously.
What are special requirements or attributes of the designs you’re 3D printing?
Feeling finished was a big part of it. With so many 3D printed parts, you can tell right away how it was printed, but with the Form 2, after sanding and a little bit of oil, it looks like a finished part.
I also had some very tight tolerances with “The Third Thumb.” There are pipes running through the hand piece that house the teflon tubing for the wires; I was working with a tolerance of about ±0.2 mm.
Dani Clode used Formlabs Grey Resin for “The Third Thumb” prosthesis. Request a free sample part.

What specific aspects of the design and workflow were made possible by 3D printing?
The fast turnaround helped enormously. I also really appreciate not having to paint the prints for them to look good, I think that saved me the most time in my process.
The biggest challenge was definitely the internal pipes in my design. It was such a tight tolerance, and the Form 2 performed great with the tolerances I provided.

Your project got quite a bit of press coverage. How do you explain the hype?
I think it catches your eye online. It’s a bit weird, but it makes you think about the possibilities.

Human augmentation is also a big topic at the moment, and I think “The Third Thumb” slots into that conversation perfectly. That was really what this project was about, having conversation about ability and prosthetics.
The goal of “The Third Thumb” is to create a catalyst for society to consider human extension, framed in an approachable, accessible design. It is a tool, an experience, and a form of self-expression. When we start to extend our abilities, and when we reframe prosthetics as extensions, then we start to shift the focus from “fixing” disability, to extending ability.
What projects are on the horizon for you? Will you continue to do 3D printing and prosthetics?
I have already used the Form 2 with another project, as part of a prosthetic arm. 3D printing is the perfect medium for prosthetic projects. It enables quick prototyping, customized designs for various body sizes, and one-off production. I will definitely continue to use Form 2 resin in my work, it is a great material and the quality is to hard to beat.
Manufacturing Affordable Custom Prosthetics

Inspired by Dani Clode’s project? Learn how 3D printing empowered a Virginia startup to challenge the prosthetics industry and manufacture affordable custom prosthetic hands.