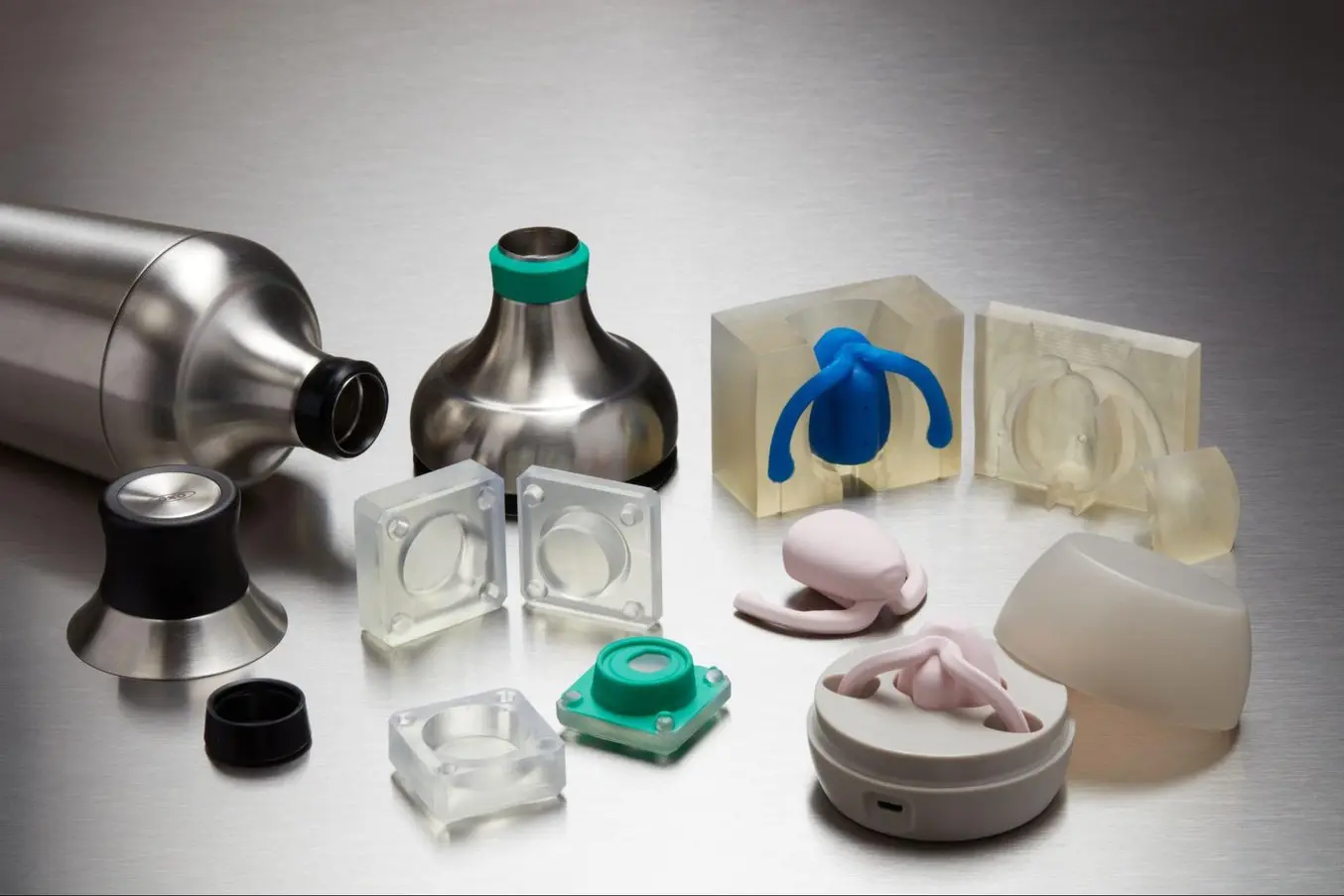
The introduction of molds in the Bronze Age elevated the crude manufacturing processes practiced by our ancestors. Mold-making techniques have been on the rise ever since, as manufacturers using advanced manufacturing techniques such as injection molding, thermoforming, or casting continue to rely on molds to create the majority of plastic, silicone, rubber, composite, and metal parts around you.
Professional manufacturers as well as hobbyists interested in taking advantage of these processes must understand how the mold-making process works, how they’re used, and how to optimize usage to meet specified throughput requirements.
This comprehensive guide will provide you with detailed information about getting started with mold making. Insight into different molding processes, choosing the best molding technique, equipment that optimizes the process, and the role of 3D printing will be discussed… and every step of the way, links to complementary in-depth content will be provided to ensure successful molding projects.
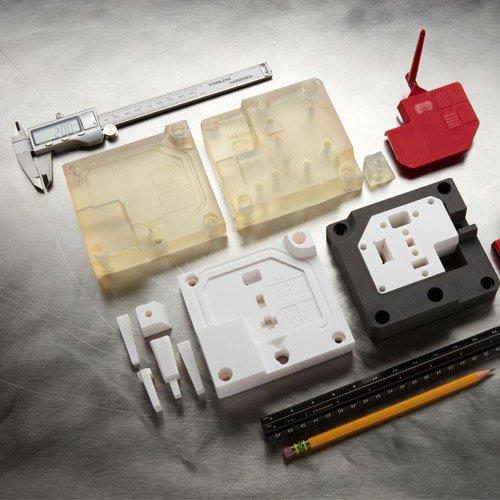
Moldmaking with 3D Prints: Techniques for Prototyping and Production
Download our white paper to learn about six moldmaking processes that are possible with an in-house SLA 3D printer, including injection molding, vacuum forming, silicone molding, and more.
What Are Molds and What Are They Used For?
A variety of manufacturing processes involve the shaping of malleable raw materials using a designed, fixed tool, structure, or frame–known as the mold. In terms of structure, molds have concave shapes (negative mold) or convex shapes (positive mold) designed according to the final design the manufacturer intends to create.
Molds are crucial to these manufacturing processes, and their main objective is the reproduction of uniform copies of the given design. Materials used in mold making include metals, plastics, ceramics, wood, foam, and more. Once designed and developed using mold-making tools, the mold is fitted into molding equipment and raw materials such as thermoplastics are poured into it or formed around it. Once solidified, the mold imprints its patterns onto the material to form the finished product.
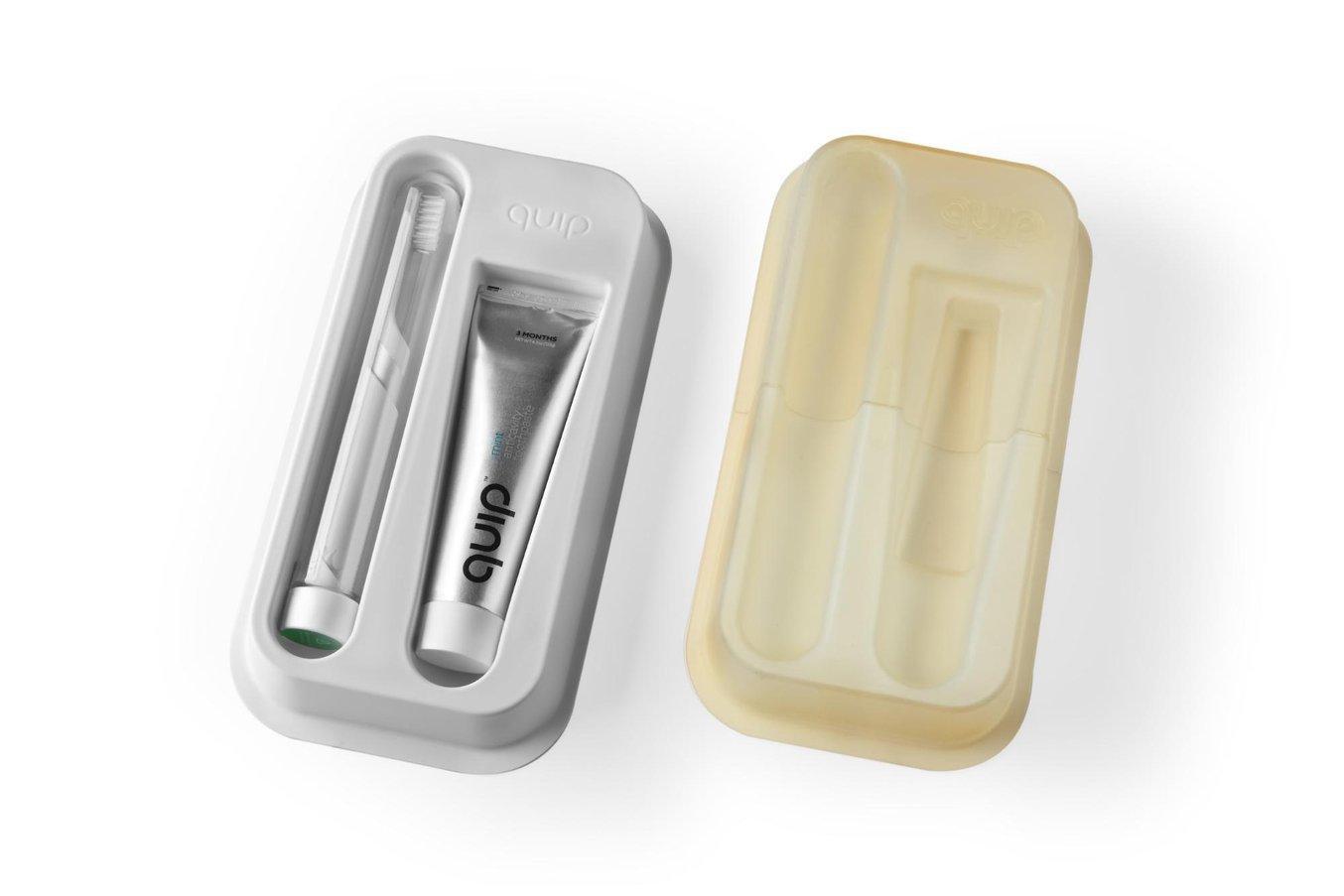
A mold for thermoforming plastic packaging and the final part.
So, what can be made with molds? Just about anything from prototypes to complex end-use parts. Molding techniques are used in manufacturing to create automotive parts, consumer products, packaging, jewelry, medical devices, and more—in fact, it’d be hard to find functional products without a single component that was manufactured with molding techniques.
Manufacturing Processes That Use Molds
Mold making is crucial to a variety of manufacturing processes; the mold serving as the blueprint from which replication takes place for many mass-produced items. Manufacturing processes that rely on molds include:
-
Injection molding is one of the most popular manufacturing processes for thermoplastic, silicone, or rubber parts. It is a cost-effective and extremely repeatable technology that yields high-quality parts for large series production. With this process, the developed mold is inserted into the injection molding machine, then heated thermoplastics or the liquefied raw material are poured into the mold. Once the material solidifies, the final part is ejected from the machine and the process is repeated in quick succession.
-
Thermoforming involves heating a plastic sheet and forming it to specific shapes using a mold. Molds provide the patterns thermoforming equipment utilize to develop a finished part. Depending on the thermoforming process, the heated, malleable material is pulled or pressed over the mold or forced onto it by vacuum. Thermoforming is the most common method for producing packaging, but it is also used in manufacturing durable end-use parts.
-
Casting involves filling a mold with molten metal or other liquefied material. The molten material cools and hardens within the mold to form the desired product. Casting is commonly used for manufacturing metallic products, as well as silicone and plastic parts.
-
Compression molding is a manufacturing process where a measured amount of molding material that’s generally preheated is compressed into the desired form using two heated molds. Compression molding is generally considered an alternative to injection molding for relatively simple designs for low and medium series of part production.
-
Blow molding is a technique that’s similar to glass-blowing. A blow-molding machine blows air into a heated tube-like piece, generally made out of plastic or glass, that is clamped into a mold. As the air is blown into it, the pressure pushes the plastic out to match the shape of the mold. Blow molding is commonly used for manufacturing hollowed products, such as bottles.
- Composite lamination involves the assembly of composite materials onto a mold and applying methods such as the wet lay-up, prepreg lamination, or resin transfer molding to form the finished composite parts out of high-performance materials, including carbon fiber, fiberglass, and kevlar.
Types of Molds
There are many types of molds that can be used as tooling solutions for the manufacturing processes highlighted above. For example, in aluminum casting, approximately seven types of mold exist, including sand casting molds, ceramic molds, and shell molds. Hence, to simplify the classification of the different mold types, the following categorization applies:
-
One-part molds refer to the simplest types of mold with uniform surfaces across all parts of the object to be molded. Mold designs or objects with one flat surface can also be reproduced using one-part or one-piece molds. Although one-part molds can be made from CAD models, these molds are generally developed from a physical master model.
-
Two-part molds provide a capable approach to producing molds for more complex designs. A two-part mold is defined as a mold with two separate parts joined together at a parting line, to produce the end product. Each produced part mirrors the different features of both parts of the model design or the master model. Making a two-part mold also usually involves developing both parts of the mold from a master model or CAD model.
-
Multi-part molds are ideal for mold designs with more complex geometries requiring a different approach compared to the process of developing one or two-part molds. Multi-part molds account for the different aspects or features of the model. Hence the completed mold will consist of multiple parts to recreate the different features of the model.
-
Multi-cavity molds have more than one cavity that’s shaped like the same part, making it possible to manufacture multiple parts per production cycle, thus increasing productivity.
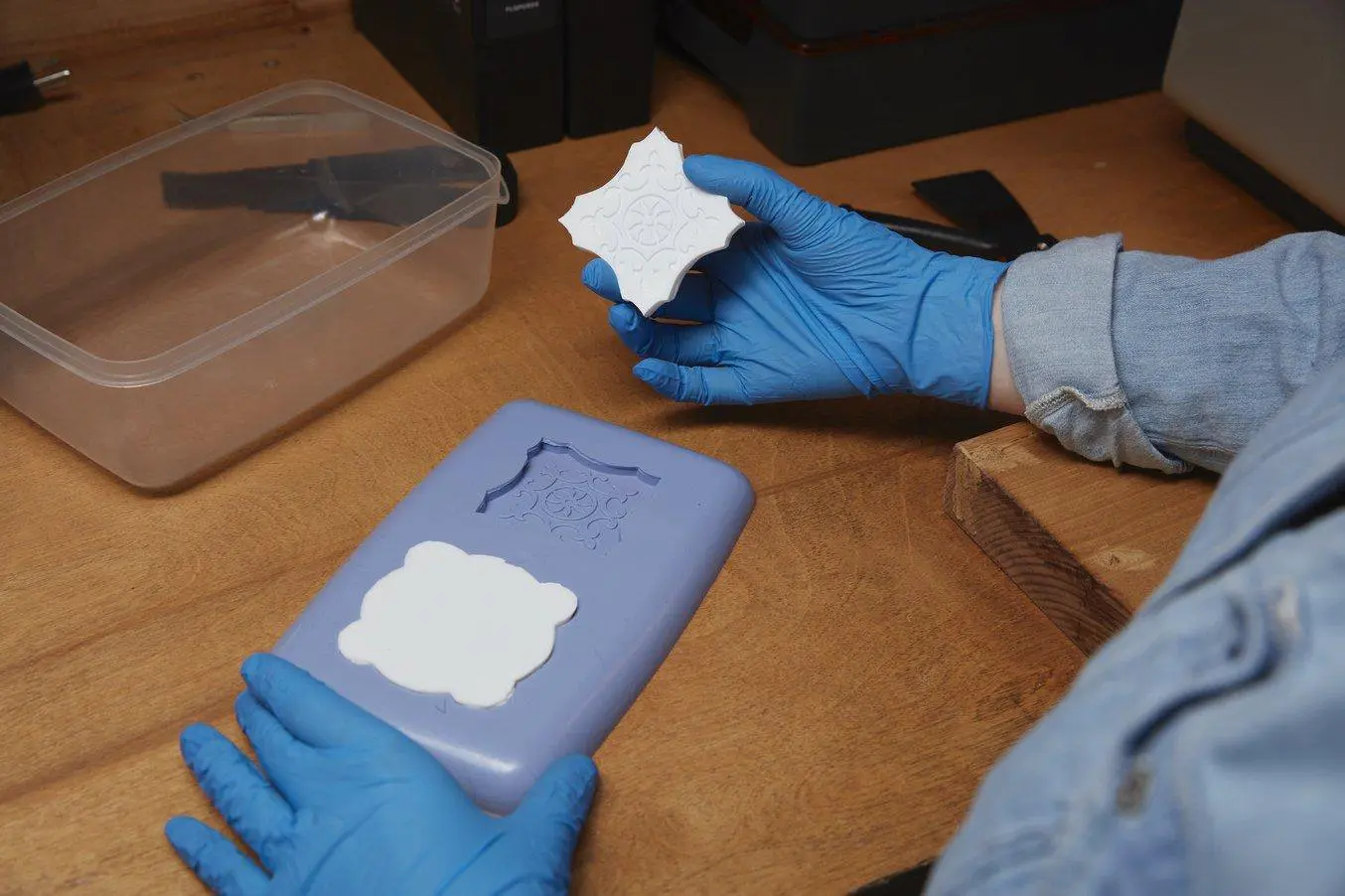
A one-piece silicone mold that can be used for designs that have a flat side and no deep undercuts.
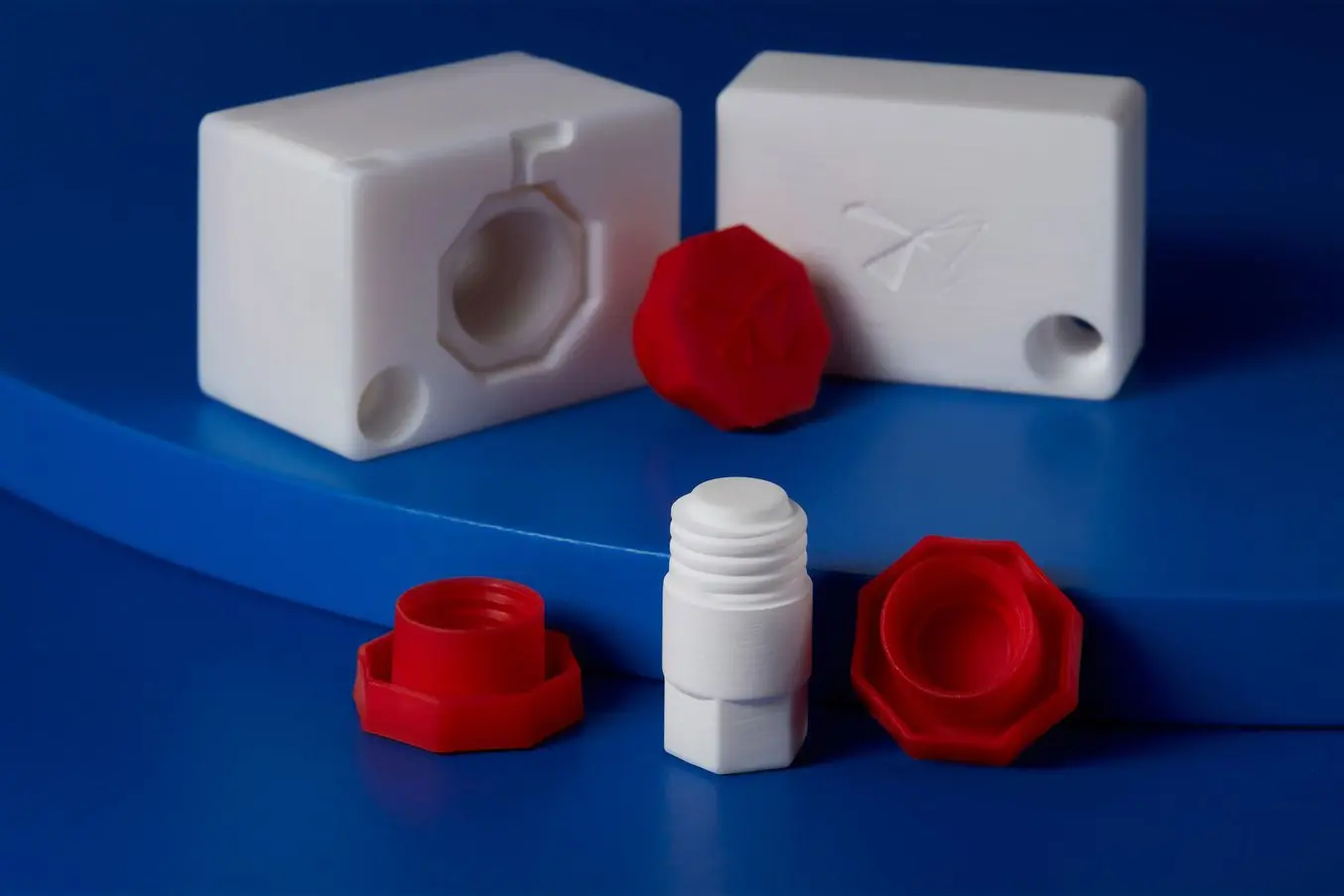
More complex designs, like this cap with a thread and undercuts, often require multi-part molds, with inserts or side-action cores.
Another crucial feature that helps with classifying different types of mold is the reusability rate of the developed mold. The reusability rate refers to how many uses the manufacturer intends to get out of a mold. The distinct types of mold under this classification are:
-
One-time-use or sacrificial molds: These molds reproduce a single object and once used, the mold is destroyed during the demolding process. One-time-use molds are generally made from sand, clay, silicone, wax, or plastics.
-
Reusable or permanent molds: As the name suggests, these molds can be reused for multiple cycles, from low to large production runs. For lower volumes (sometimes referred to as soft molds), reusable molds can be made out of silicone, foam, wood, plastics, or softer metals like aluminum. Larger volumes that require more durable molds without wearing out (often referred to as hard molds) are mostly made out of hard metals, such as steel.
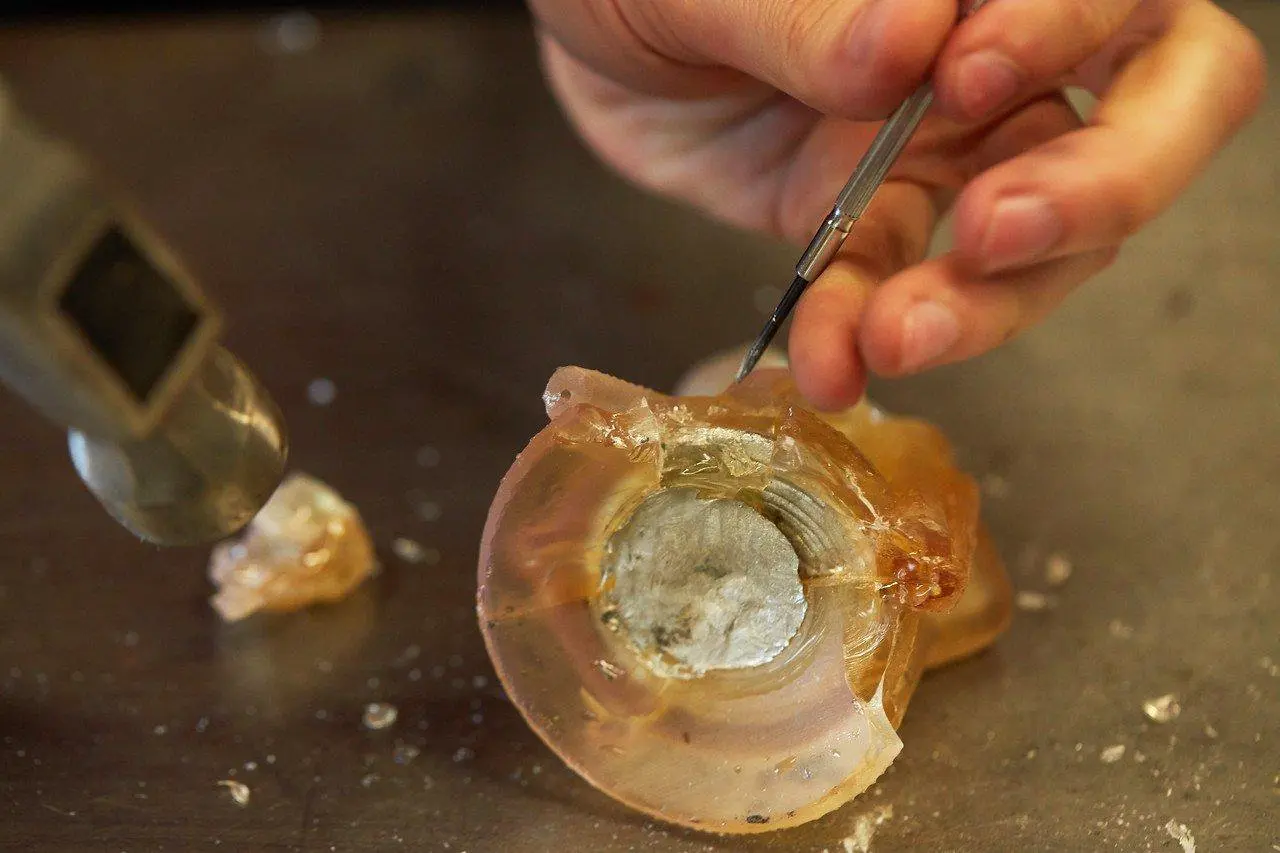
Sacrificial molds are destroyed during the demolding process.
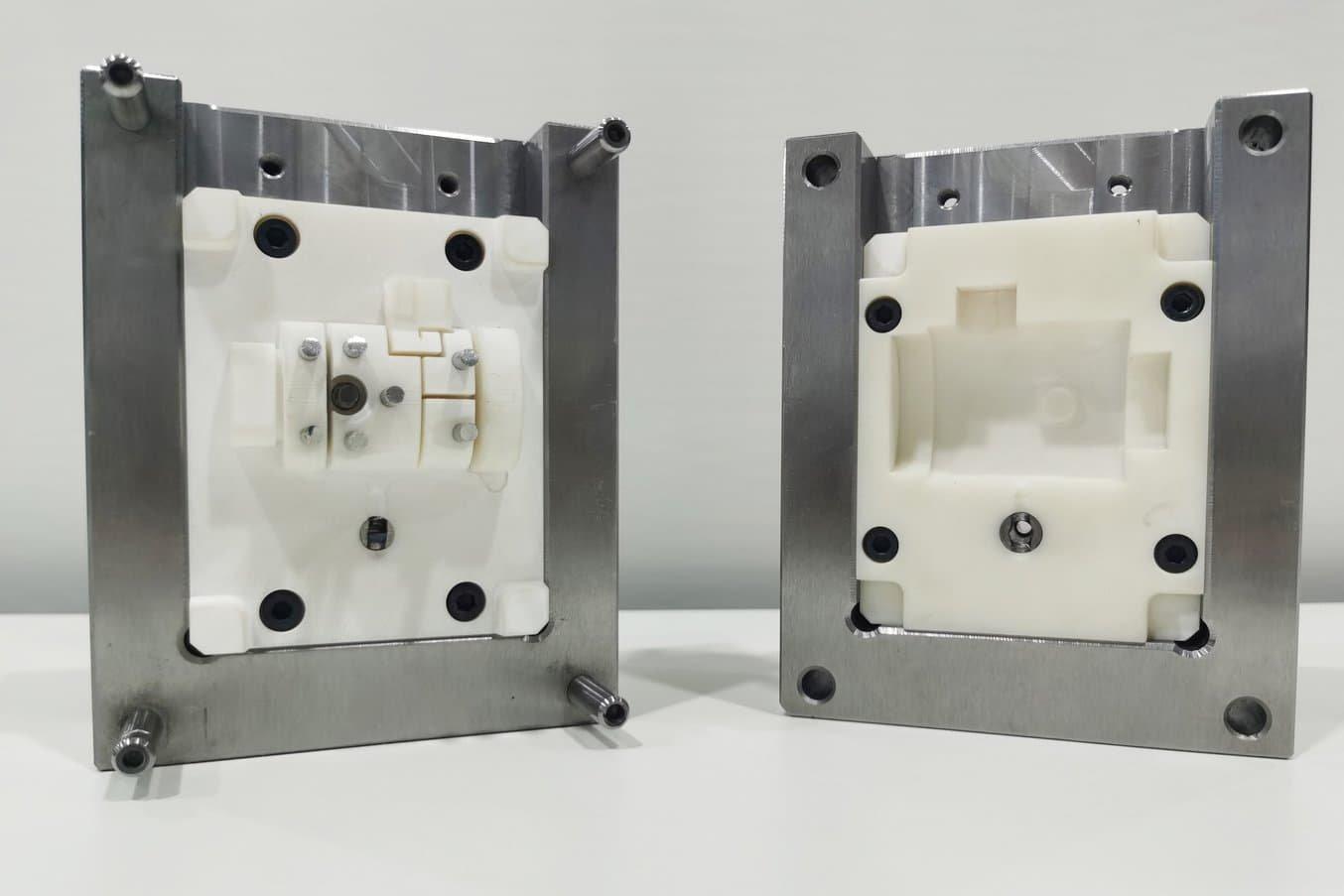
Reusable molds can be reused for multiple cycles.
How to Choose a Mold-Making Technique?
What’s the best mold-making technique for a given application? It depends on a couple of important factors, including the desired end-part material, the intended manufacturing process, the geometry of the model, and the production volume.
A simplified, step-by-step approach to choosing the best technique for your manufacturing project is covered in stages below:
1. Outline the Development Criteria for Your Project
A manufacturing master plan can help create clear-cut details of what is to be expected from a project, its development timeline, and the available budget. Whether you’re planning to create custom parts or mass-produce thousands of the same item will define what options to pick in the next steps. The development criteria might vary depending on the project, but generally include the design of the part, size, material, quality, required tolerances, timeline, required production volume, cost constraints, etc.
In product development, the initial document that answers many of these questions is often the product requirements document (PRD), while the bill of materials (BOM) is the comprehensive list of parts, items, assemblies, and other materials required to create a product.
2. Select the Manufacturing Process
The right manufacturing process for a certain part is largely dependent on the development criteria. In some cases, multiple production processes can be used to create any given design. As a rule of thumb, choose the process that can produce the given part with the required quality, at the lowest costs, while fulfilling the rest of the development criteria. The material choice and manufacturing volume are likely the most important factors driving your decision.
For plastic parts, you can read our guide to manufacturing processes for plastics.
3. Select the Mold-Making Technique
Once you settle on the right manufacturing process, the type of mold for the process is also largely defined by the development criteria. While the exact factors are dependent on the manufacturing process, here are some of the most important considerations when choosing a mold-making technique:
-
Design of the part: Try to simplify the design as much as possible and align it with the design rules of the given manufacturing process to be able to choose the technique that can achieve the lowest costs. Simple designs might only require molds that can be created with manual techniques, while complex designs often require multi-part molds and digital manufacturing tools like 3D printers or CNC machining to create.
-
Production volume: Large-volume production runs require durable molds that can accurately replicate models without wearing out after a few uses. However, fabricating such tools comes with high costs and lead times. For one-off parts and lower volume batches, it might be more efficient to choose cheaper molds that can be created faster, such as sacrificial molds or soft molds that can be discarded when they begin to show signs of irreparable wear.
-
Quality: Tighter tolerances require more precise molds and tools to create, such as digital manufacturing tools, and need to be more durable to ensure consistent part quality over multiple cycles.
-
Timeline: Producing complex metal molds often takes months through a service provider. If you’re working on a shorter timeline, try to look for alternatives that can shorten the lead time, such as 3D printed rapid tooling.
-
Material: Materials that have a higher melting point or are more abrasive will require molds that are more durable and can create the required volume of parts without degradation.
How to Make a Mold For Different Manufacturing Processes
This section provides a brief overview of mold-making techniques for different manufacturing processes. Follow our links for in-depth guides and the step-by-step workflow for each process.
There are two major techniques for mold making—the direct and indirect mold-making processes. The indirect mold-making approach involves developing molds from a physical master model, or pattern. The direct process involves developing a mold directly from the (digital) design, most commonly often using digital manufacturing processes.
Silicone Molds for Casting
Silicone casting is one of the most popular processes that leverage molds. Product developers, engineers, DIY makers, and even chefs all make silicone molds to create one-off or smaller runs of parts from plastics and a variety of other materials. Silicone is a strong choice for mold-making because it can be used to easily create custom designs and the molds themselves are also quite durable, so you can use them repeatedly without fear of breakage.
Depending on your design, you might need a one-piece or two-piece mold. The processes for making these molds are similar, but it will take a bit longer to create a two-part mold. Use the step-by-step instruction in the video or our practical guide to making silicone molds to create your own molds.
Injection Molds
Molds for injection molding are traditionally made out of metal by CNC machining or electric discharge machining (EDM). These are expensive industrial methods that require specialized equipment, high-end software, and skilled labor. As a result, the production of a metal mold typically takes four to eight weeks and costs anywhere from $2,000 to $100,000+ depending on the shape and the complexity of the part.
However, there are alternatives to machining molds out of metal. Leveraging in-house 3D printing to fabricate injection molds for prototyping and low-volume production significantly reduces cost and time compared to metal molds, while still producing high-quality and repeatable parts.
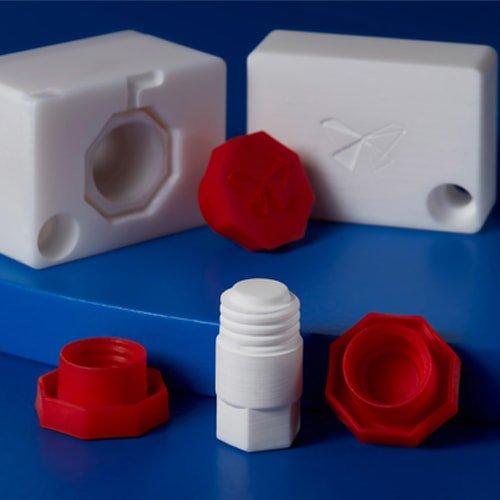
Low-Volume Rapid Injection Molding With 3D Printed Molds
Download our white paper for guidelines for using 3D printed molds in the injection molding process to lower costs and lead time and see real-life case studies with Braskem, Holimaker, and Novus Applications.
Thermoforming Molds
The molds required for the thermoforming process can be developed using diverse manufacturing processes, including hand sculpting wood, CNC machining plastic, structural foam, fiberglass, engineered composites, or metals, 3D printing polymers, or casting plaster or metal.
Many businesses are turning to stereolithography (SLA) 3D printing to create molds for thermoforming processes, because it offers a fast turnaround time at a low price point, especially for shorter runs, custom parts, and prototype designs. 3D printing also offers unmatched design freedom to create complex and intricate molds.
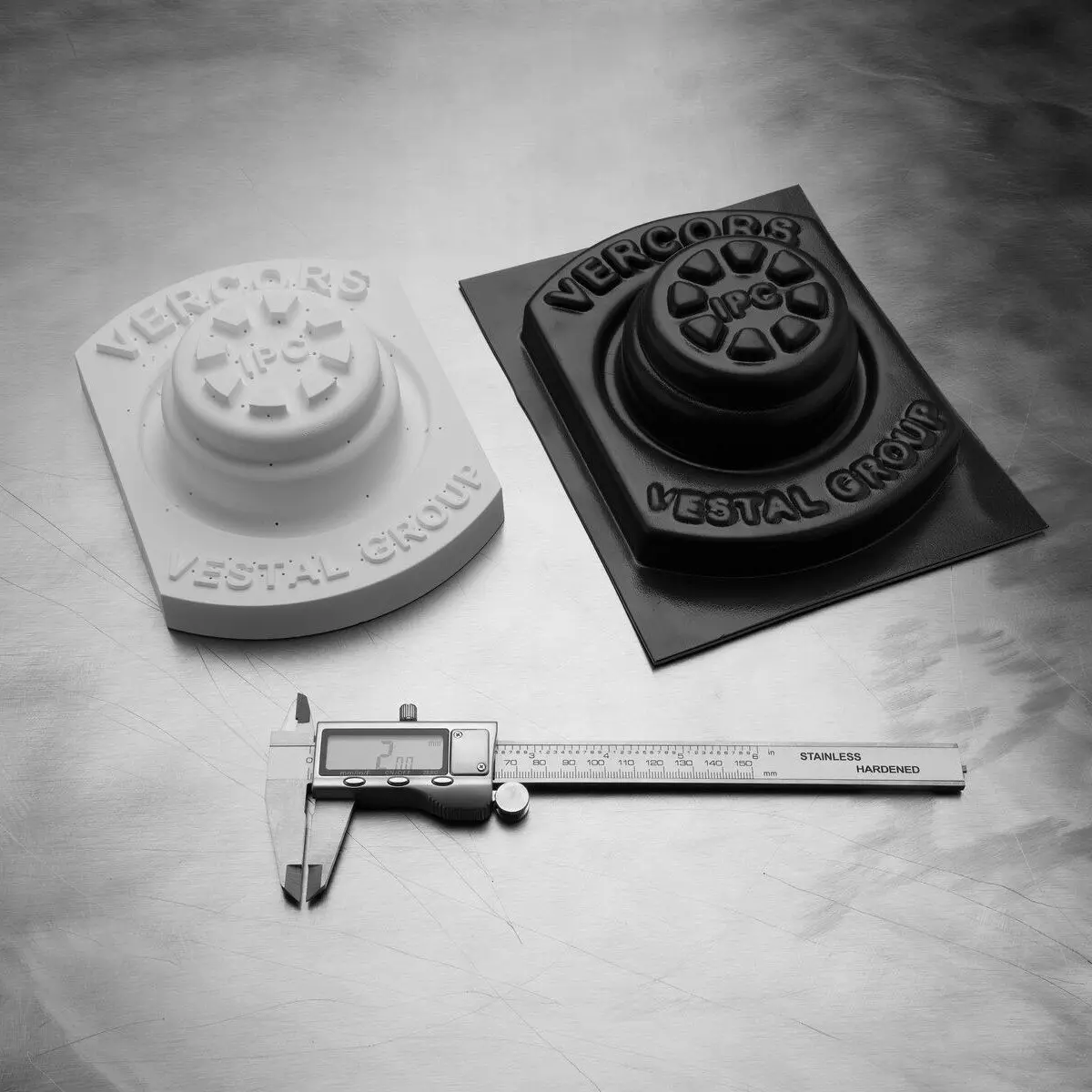
Low-Volume Rapid Thermoforming With 3D Printed Molds
Download our white paper to see how to create complex molds with 3D printing fast and learn about tips and guidelines that you’ll want to follow when preparing your mold parts.
Compression Molding
Depending on the material or charge you will be compression molding, you have several options for creating molds, including die casting, CNC machining, or 3D printing. The key is that your molds need to be able to withstand the compression molding process, so if you are using heat, you will need to create molds that can handle dramatic temperature changes. Molds will also need to be able to withstand the amount of pressure applied during compression.
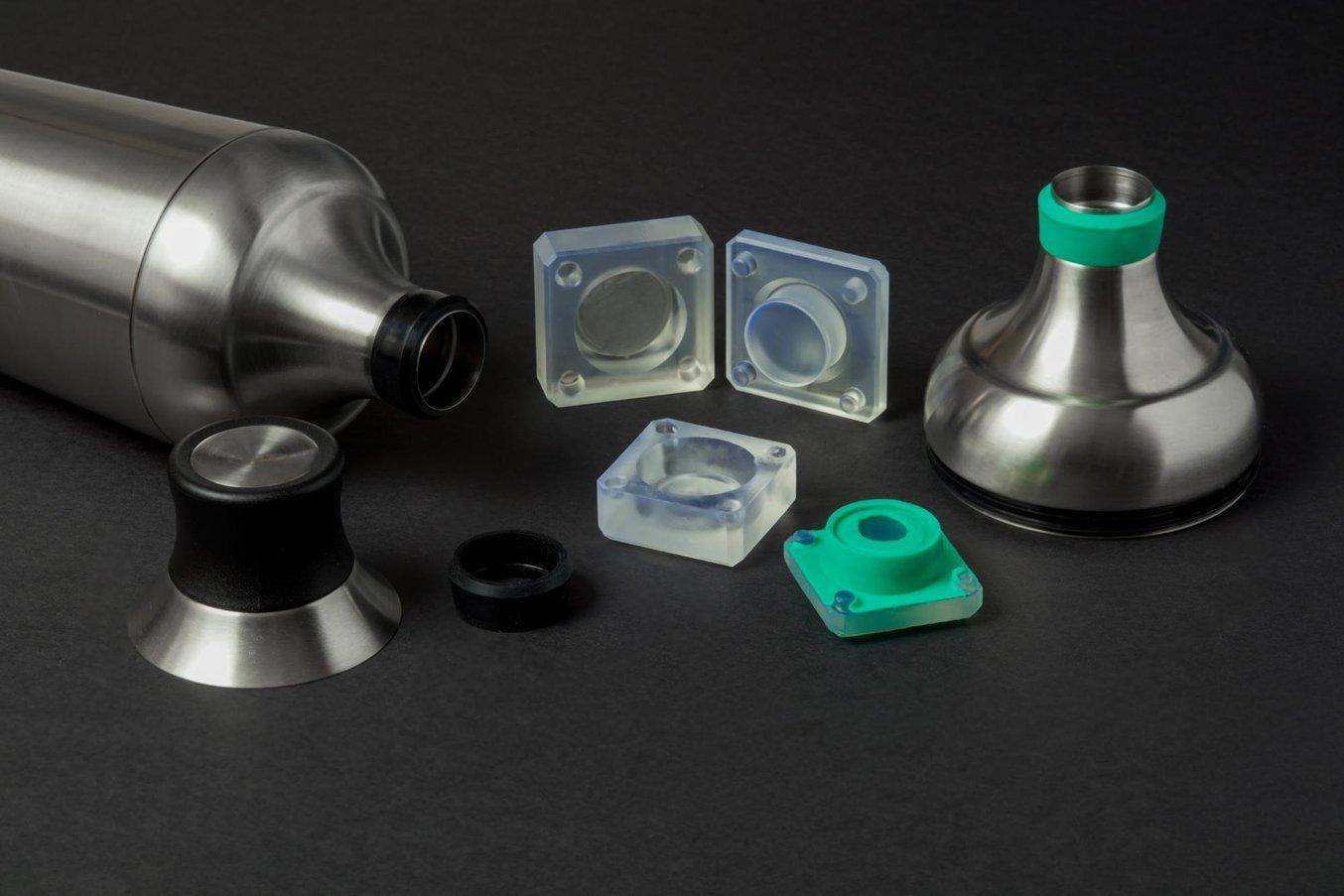
3D printing is a fast and cheap method for creating molds for compression molding.
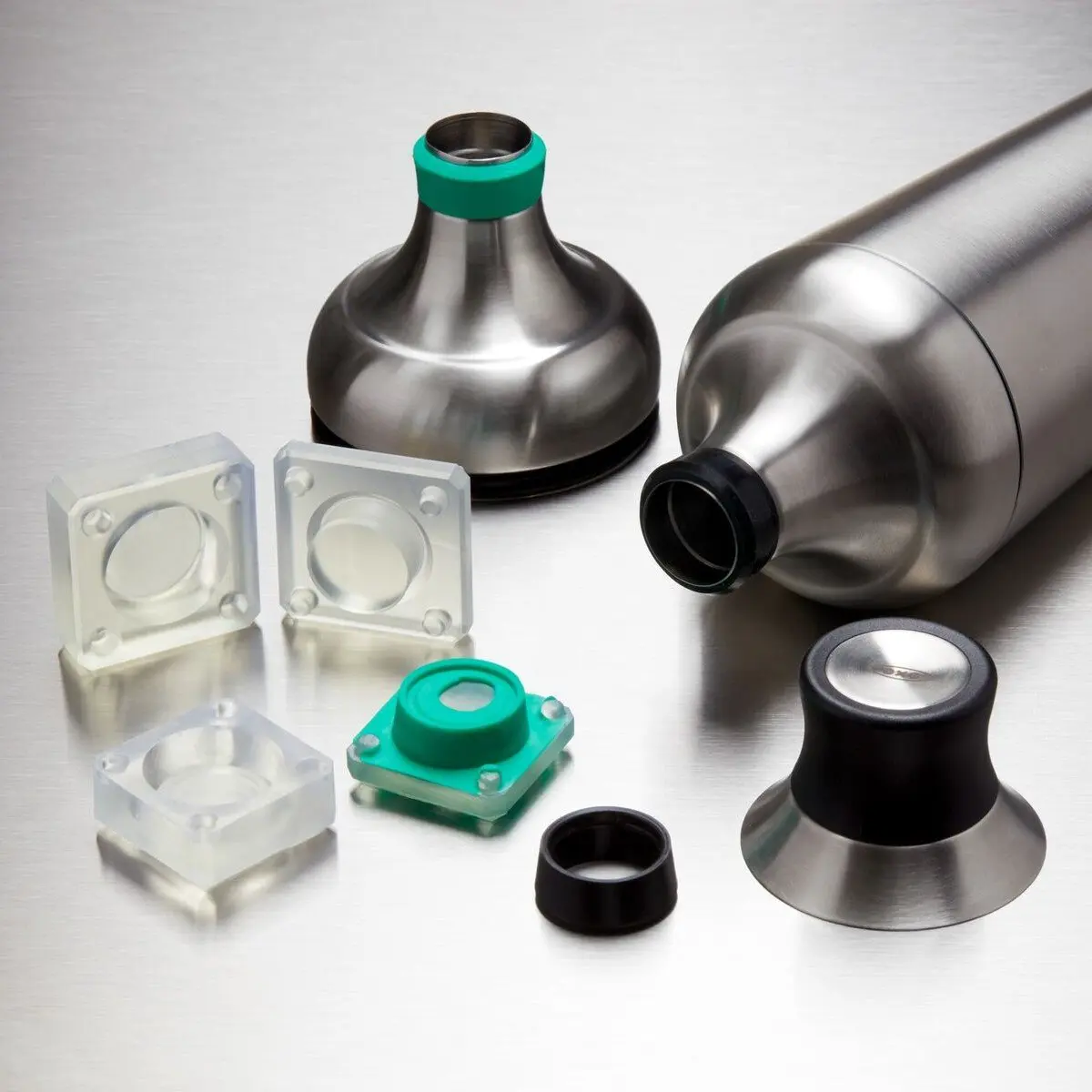
Silicone Part Production With 3D Printed Tools
Download this report for a step by step guide on 3D printed tooling for silicone part production, with mold design best practices and customer case studies.
Molds for Metal Casting
Though all metal casting techniques share the same core process, there are various methods better suited for different applications. Some of the most common methods include die casting, investment casting, and sand casting.
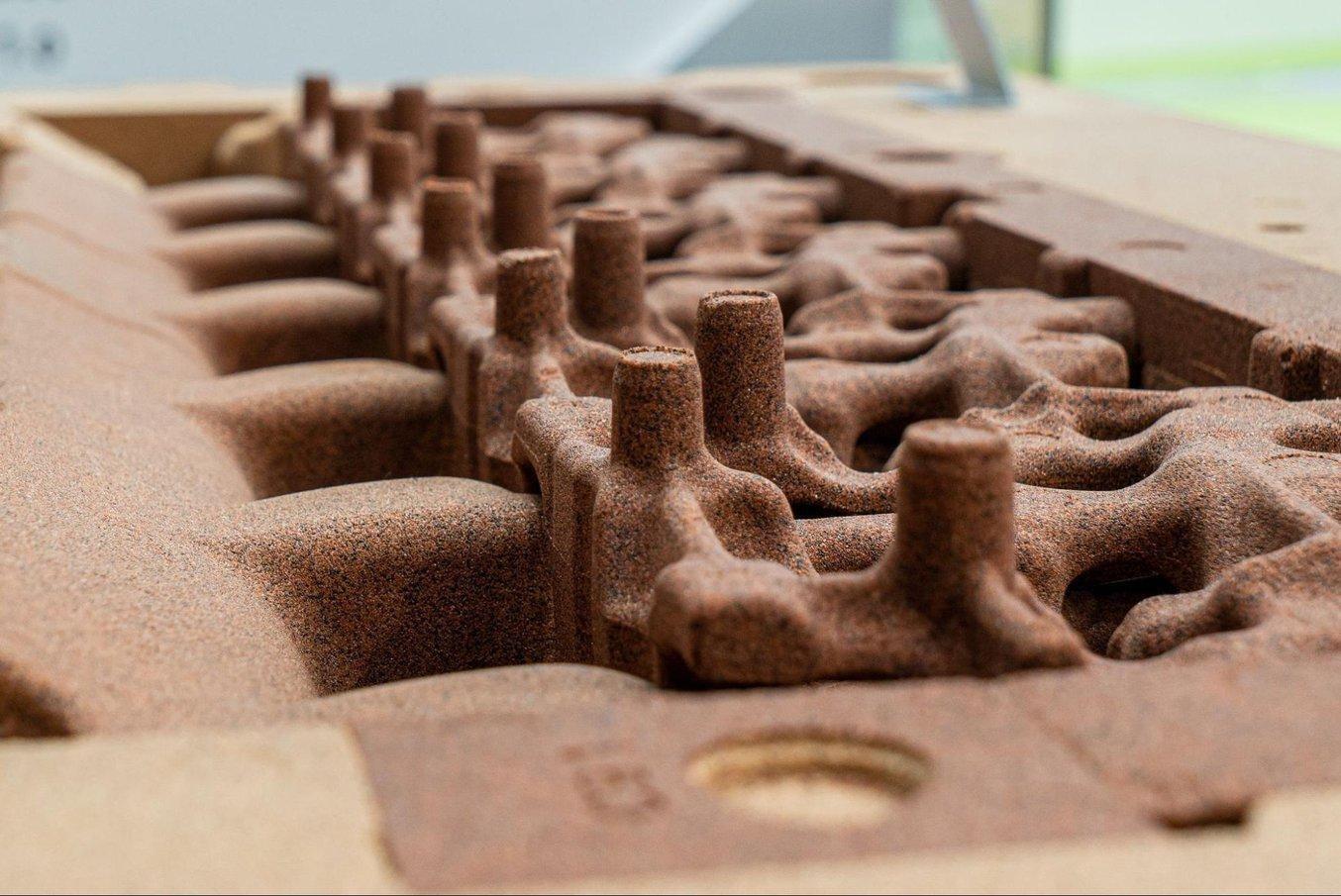
A mold for sand casting.
Both patterns for indirect mold-making and molds for directly casting metal parts can be made using multiple methods. Read our guide to metal casting for details on each process.
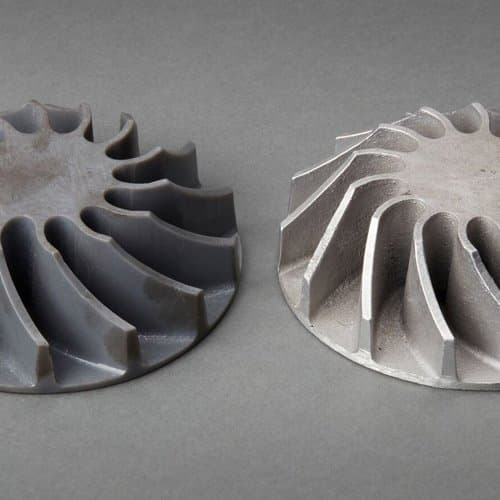
Fabricating Metal Parts With 3D Printing
Get design guidelines for creating 3D printed patterns, walk through the step-by-step direct investment casting process, and explore guidelines for indirect investment casting and sand casting.
Get Started With 3D Printing Molds
Combining traditional production techniques like injection molding, thermoforming, or silicone casting with 3D printed molds allows you to bring products to market faster with a more time and cost-efficient manufacturing process. Desktop 3D printing offers businesses a versatile, cost-effective approach to developing master models and molds for both the direct and indirect mold-making processes, entirely in house.
Download our white paper to learn about six mold-making processes that are possible with an in-house SLA 3D printer, illustrated with real-life case studies.