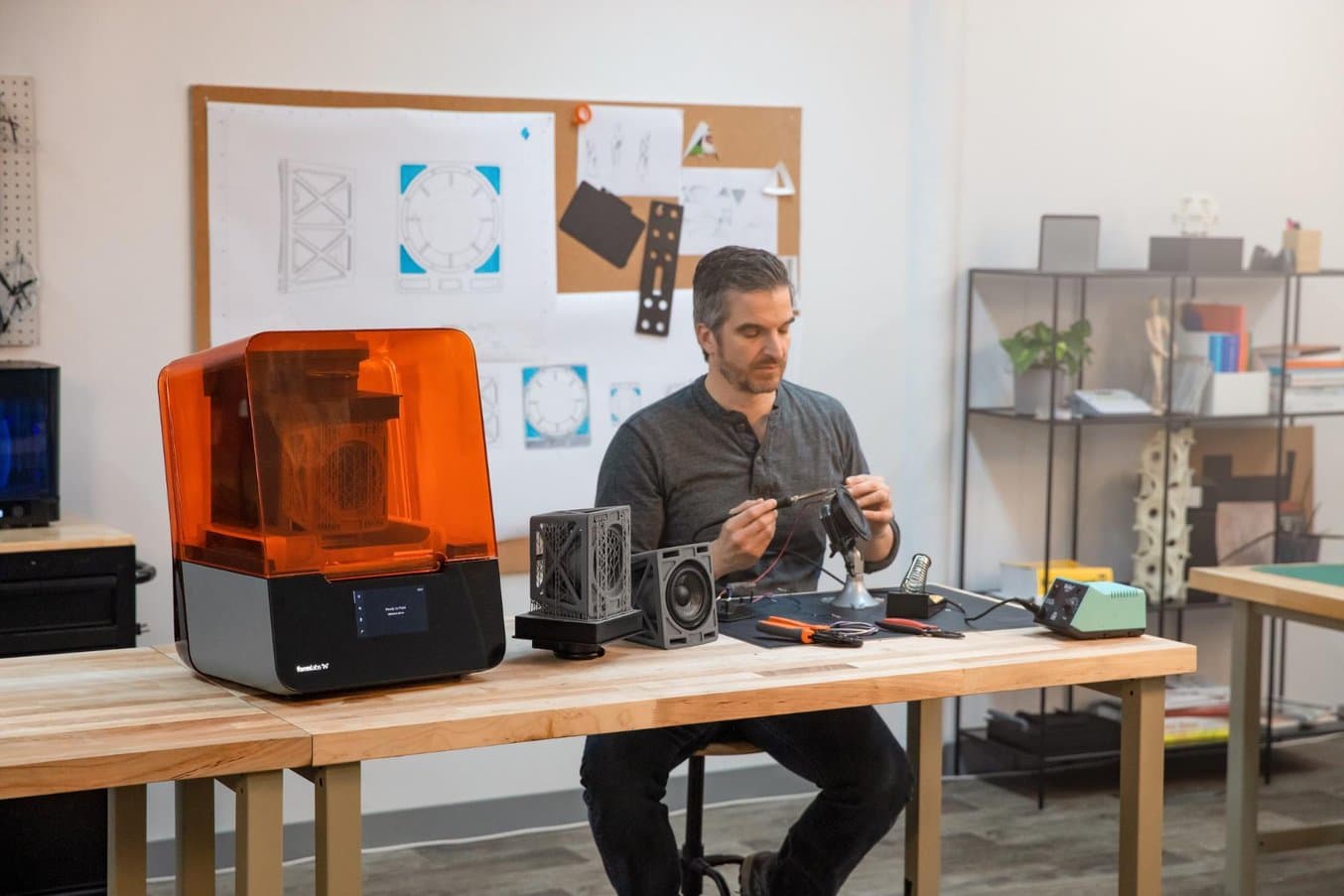
These days many of you may be experiencing disruptions at work as companies and governments react to the growing health concerns due to the COVID-19 pandemic.
You or your employees might be required to work from home in the coming weeks, which is more complicated to do efficiently when your job requires physical tools and not just computer and internet access. With the right setup and workflow, however, 3D printing can help maintain productivity in these challenging times.
Read on for our recommendations and tips on how Formlabs tools and software features can help you stay productive and connected with your team.
Stay Connected With Dashboard and Remote Printing
The Formlabs Dashboard empowers you to easily manage 3D printers, materials, and teams, even remotely.
With Dashboard, you can plan and organize your print queue from anywhere. When working through many print jobs, for example, you can optimize your queue to run short prints during the day, or to run prints in the same material back to back.
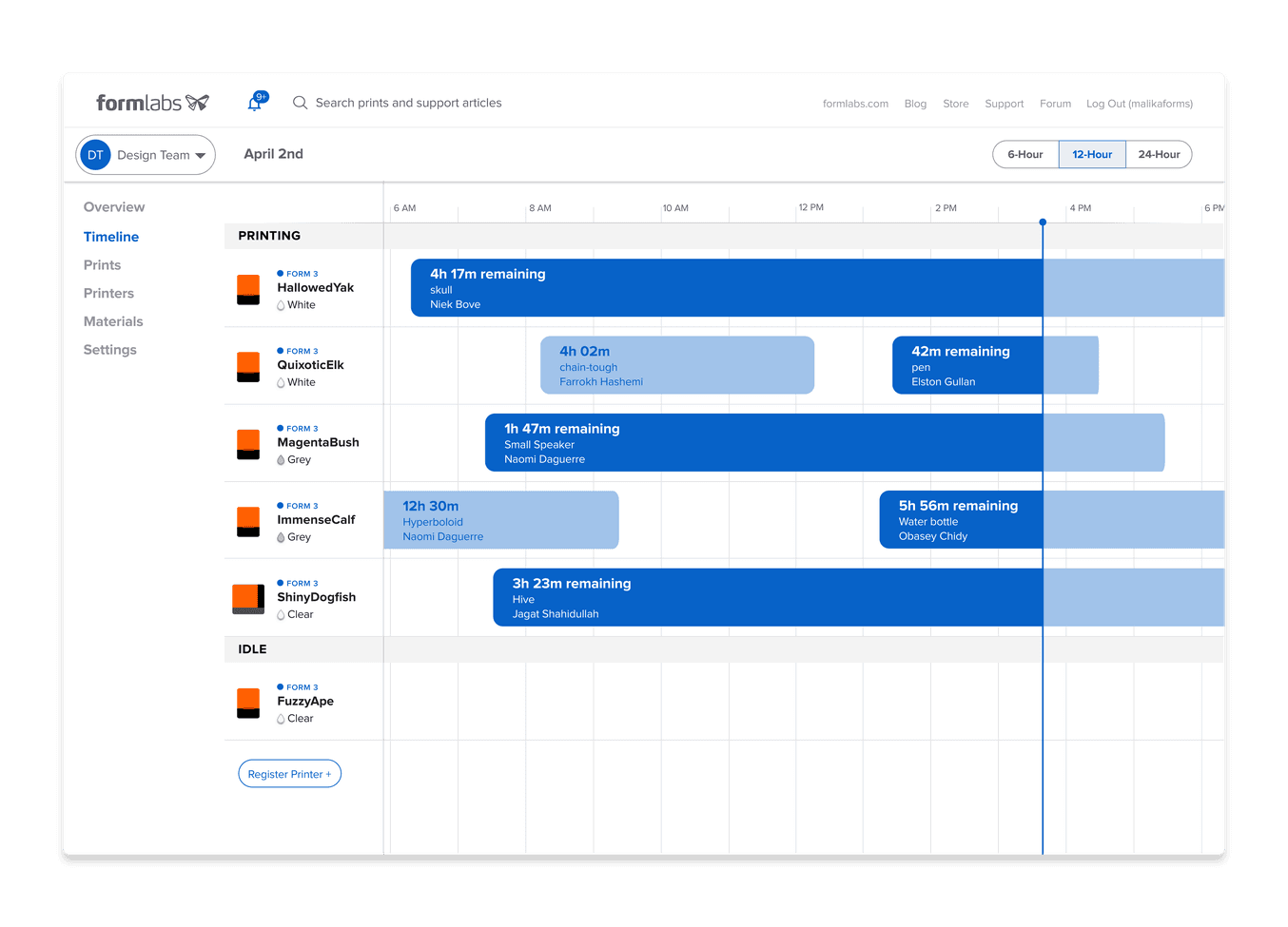
The print queue in Dashboard allows you to manage and track multiple 3D printers.
Dashboard also includes powerful tools for teams, allowing you to easily manage permissions and track 3D printing at any scale.
You can easily track jobs online and keep others in the loop when your team has to work remotely. Dashboard also allows you to set up SMS and email notifications when prints are completed.
Someone will still need to manage your company’s 3D printer or fleet or 3D printers physically, but the rest of the team can stay at home and avoid contact to reduce the chance of community spread.
Our latest desktop 3D printer, the Form 3, also introduces the ability to start prints from anywhere with Remote Print. Prime the printer before you leave, then start the next print job from anywhere in the world (not just the local network).
Tips for 3D Printing at Home
Unlike many other tools for prototyping and manufacturing, or even large-format 3D printers, Formlabs desktop stereolithography (SLA) 3D printers have a compact size and no special environmental requirements, which makes them suitable for use at home. In fact, many hobbyist SLA printer customers predominantly use their printers in their homes.
In case the majority of your team has to work from home, you should encourage colleagues to take 3D printers home to stay productive.
Transporting Formlabs 3D printers:
-
To prepare your Formlabs 3D printer for transportation, first, remove the resin cartridge, remove and clean the build platform, and then remove and cover the resin tank before placing it inside its tank case. Make sure that all accessories that contain resin are closed securely before transport.
-
For the Form 3, the Light Processing Unit (LPU) must be secured with the thumb screws and latch before transportation. Not securing the LPU may cause damage to your printer. Contact us if you can't find the screws.
-
Wrap your printer carefully and place it in its original packaging if possible.
-
Don’t forget to pack all the accessories you might need for 3D printing and post-processing: Form Wash and Form Cure or finishing kit and alternative curing solution, consumables such as resin tanks, resin cartridges, gloves, post-processing tools, IPA, etc.
Due to the COVID-19 pandemic, isopropyl alcohol (IPA) might be in short supply in some regions. For non-biocompatible applications, we recommend using tripropylene glycol monomethyl ether (TPM) in these cases. Read our article for more information about choosing the right solvent.
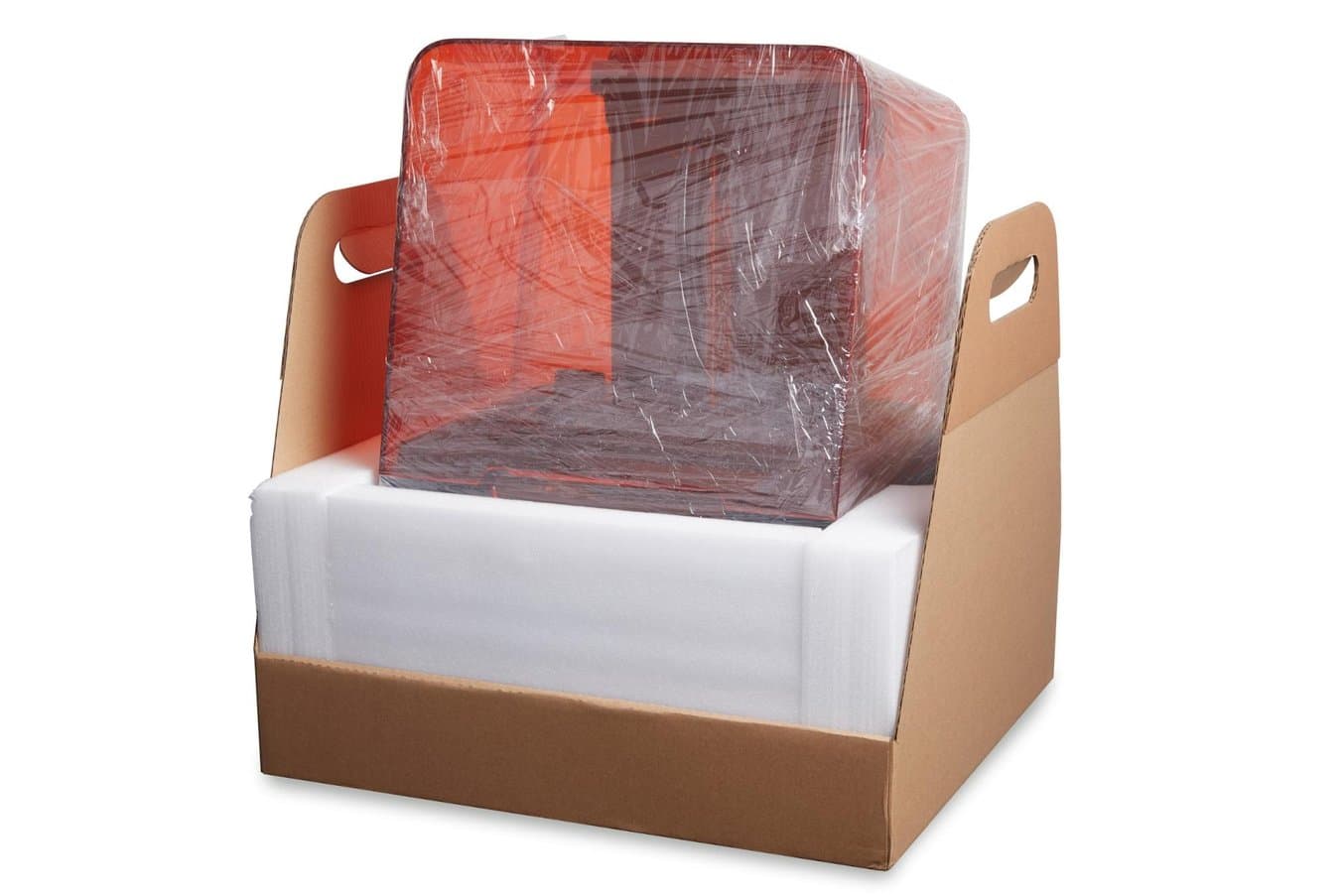
Guidelines for setting up the printer at home:
-
Prepare a clean, dry space out of direct sunlight. The Form 3 is designed to be able to operate on your desk, but some may prefer to find a dedicated room or corner for their 3D printer and its accessories.
-
Ideally, use Form Wash and Cure to reduce space needs, save time, and keep the environment clean easily.
-
As resin 3D printing involves chemicals and resin, make sure to keep the printer and other tools secured from children and pets.
-
Your printer will have to be leveled and set up. Read the setup instructions for the Form 3 and Form 2.
Do you have any questions or concerns? While most of our colleagues are also working from home, we remain fully operational. You can contact Formlabs Support here.
Collaborating on Physical Parts and Prototypes With Distributed Teams
With multiple 3D printers, teams across multiple locations can collaborate more effectively. By using the same 3D printers and materials, professionals can iterate and produce parts on different machines seamlessly.
As a practical example, let’s look at how Dr. Sam Pashneh-Tala collaborates internationally on the design of bioreactors with Aptus Bioreactors.
Although Aptus is based in South Carolina in the US and Dr. Pashneh-Tala’s lab is in The University of Sheffield in the UK, they both use Formlabs desktop 3D printers within their research facilities. This allows bioreactor components to be designed, 3D printed, and tested by Aptus, who then share the designs digitally with Dr. Pashneh-Tala for printing in his lab. Dr. Pashneh-Tala can then test the components, redesign as needed, and send these digitally back to Aptus.
This streamlined approach harnesses digital manufacturing capabilities and enables seamless collaboration and the rapid iteration of designs across two continents. Regardless of the distance, it can now also help any temporarily distributed team.
Save Time and Reduce Reliance on Outsourced Providers
Even if you're not planning to work from home or bring printers out of the office, having in-house 3D printing as a capability at your company can build resiliency during uncertain times by offering you control over the fabrication process and reducing reliance on outsourced providers, who may shut down or struggle to ship your parts.
SLA 3D printers can be used to create prototypes, manufacturing tools, replacement parts, and other applications in many cases 80-90% faster than with outsourced providers. And that is in times without widespread supply chain issues and closed facilities.
To take a practical example, there are 700 3D printed parts at work on Ashley Furniture’s factory floor in Arcadia, Wisconsin, right alongside industrial robots and CNC milling workhorses, from assembly to fabrication. With in-house 3D printing, they managed to cut the lead time for most of their parts from multiple weeks to less than 24 hours.
Alignment Pins for Ashley Furniture
Outsourcing to machine shop | 3D printing in-house | |
---|---|---|
Cost | 1,200 minimum order quantity, $10 per part | No minimum quantity, $5.90 per part |
Lead time | 3-4 weeks | 15 h 30 min for 16 parts from two printers |
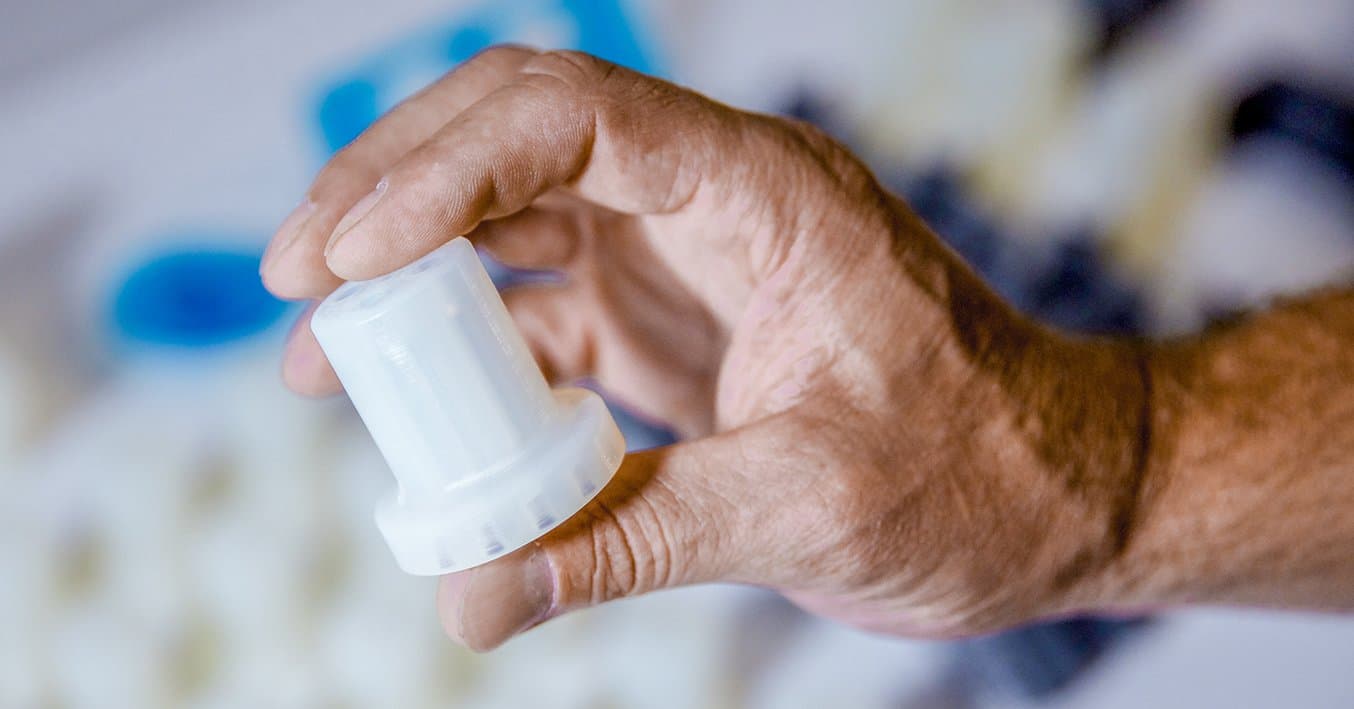