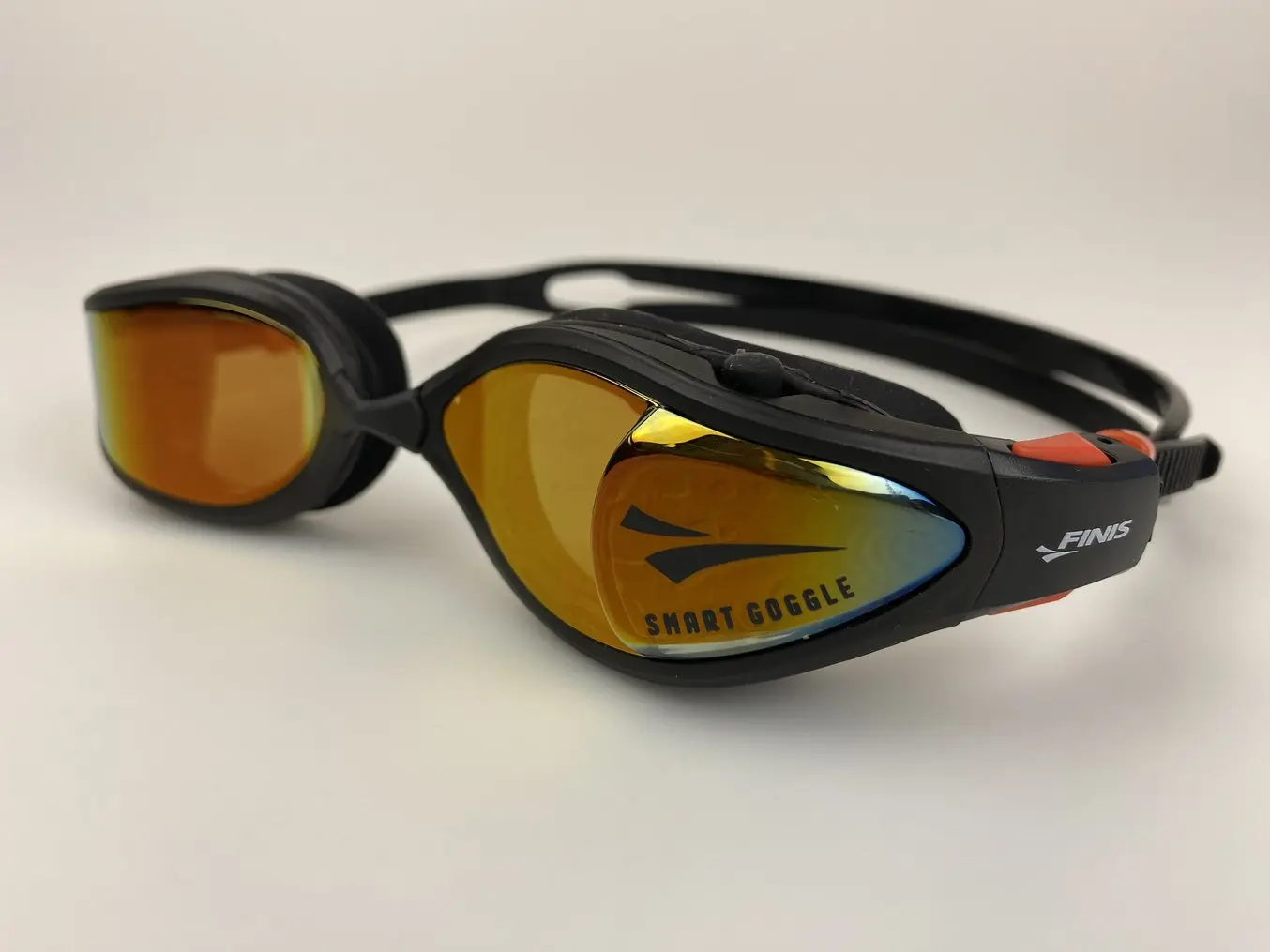
FINIS, Inc. specializes in the development of swimming and aquatic sports equipment, including cutting-edge devices like the Smart Goggle Max smart swimming goggles.
FINIS, Inc. is renowned for developing cutting-edge products that have gained the trust of swimmers across all skill levels due to their exceptional quality and performance. Based in California, USA, the company is dedicated to continuously advancing its innovative product offerings, keeping a keen focus on the changing requirements of swimmers and coaches.
David Beittel is a senior designer at FINIS who manages the product development group. Together with his team, he started using filament 3D printing for rapid prototyping, but quickly realized the need for more detailed and isotropic parts. While they still use filament printing in their development process, they turned to the Formlabs Form 3+ stereolithography (SLA) 3D printers for production-like prototypes and were impressed with the “phenomenal range of materials.” Still, as their main product lines include swim fins, goggles, and training gear, the only thing they were missing was a durable, pure silicone to fabricate parts that would be close to the end production materials.
In the past, they used to cast silicone parts in molds, which was labor intensive and generated long lead times. Now, they’re equipped with the Form 3+ resin 3D printers and the new Silicone 40A Resin, the first accessible 100% silicone resin for soft, pliable, and durable parts, which enables them to swiftly make adjustments and print functional prototypes overnight.
“It will take a month or so to make the tool. [With Silicone 40A Resin] I can come up with a different idea, make a modification, and print it overnight. The next day I can come in, take it off, clean it up, and try it in the pool right away. So what used to take weeks, I can now do in hours and I think that's kind of the real advantage.”
David Beittel, Senior Designer at FINIS, Inc.
As the team goes through internal testing, in and out of the water, they emphasize the remarkable watertightness of the material and its unparalleled rebound resilience, that are far superior to silicone-like 3D printing materials. The product development group is thrilled with the fact that Silicone 40A Resin's elasticity brings it remarkably close to the characteristics of the final production material, making it an invaluable tool for refining product designs and ensuring optimal performance during all stages of the development process.
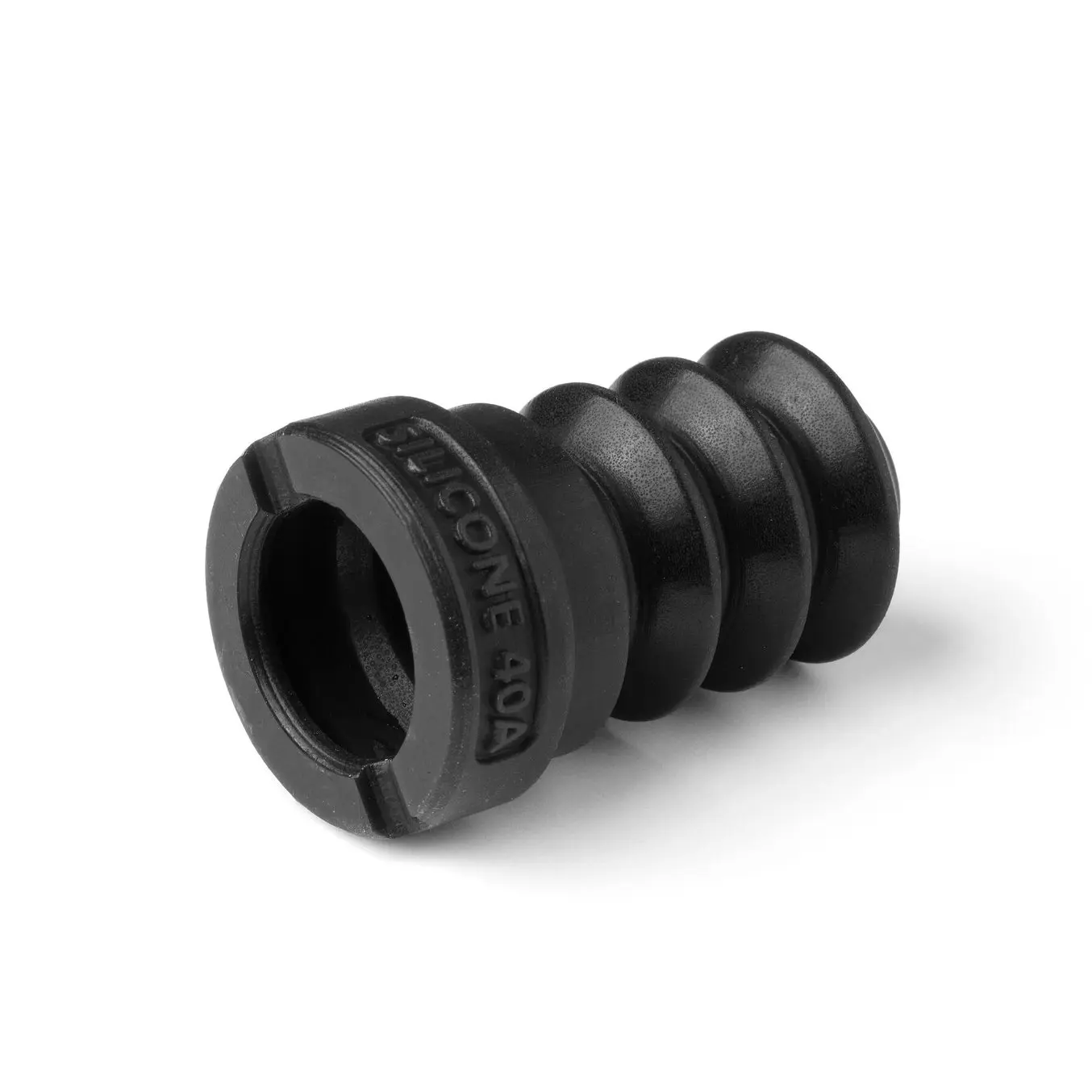
Request a Free Sample Part
See and feel Formlabs quality firsthand. We’ll ship a free Silicone 40A Resin sample part to your office.
Gasket Prototyping: A New Approach With Silicone 40A Resin
Typically, for mass production of their silicone parts, the team would opt for injection molding or compression molding. These traditional methods involve costly steel tools and lengthy lead times, often taking months. Therefore, they usually outsource urethane casts for beta prototypes and pre-production parts during product development. Although this approach is popular for producing dozens of parts, it still requires two to three weeks of lead time, limiting the possibilities for prototyping and quick design iterations.
To overcome this challenge, they integrated 3D printing into the development cycle, allowing them to refine designs and conduct internal tests before committing to rapid tooling for user testing. As a result, they can now undergo numerous cycles of "design, test, and revise" to develop better products.
While developing their newest smart goggle, the team at FINIS, Inc. ran into an issue when prototyping the new gaskets. The small module that counts your laps, stroke rate, and split times, meant to fit in the goggle, needs to be turned on and off easily. So the challenge was to develop a gasket with an integrated button that would align with the button on the module while still being watertight.
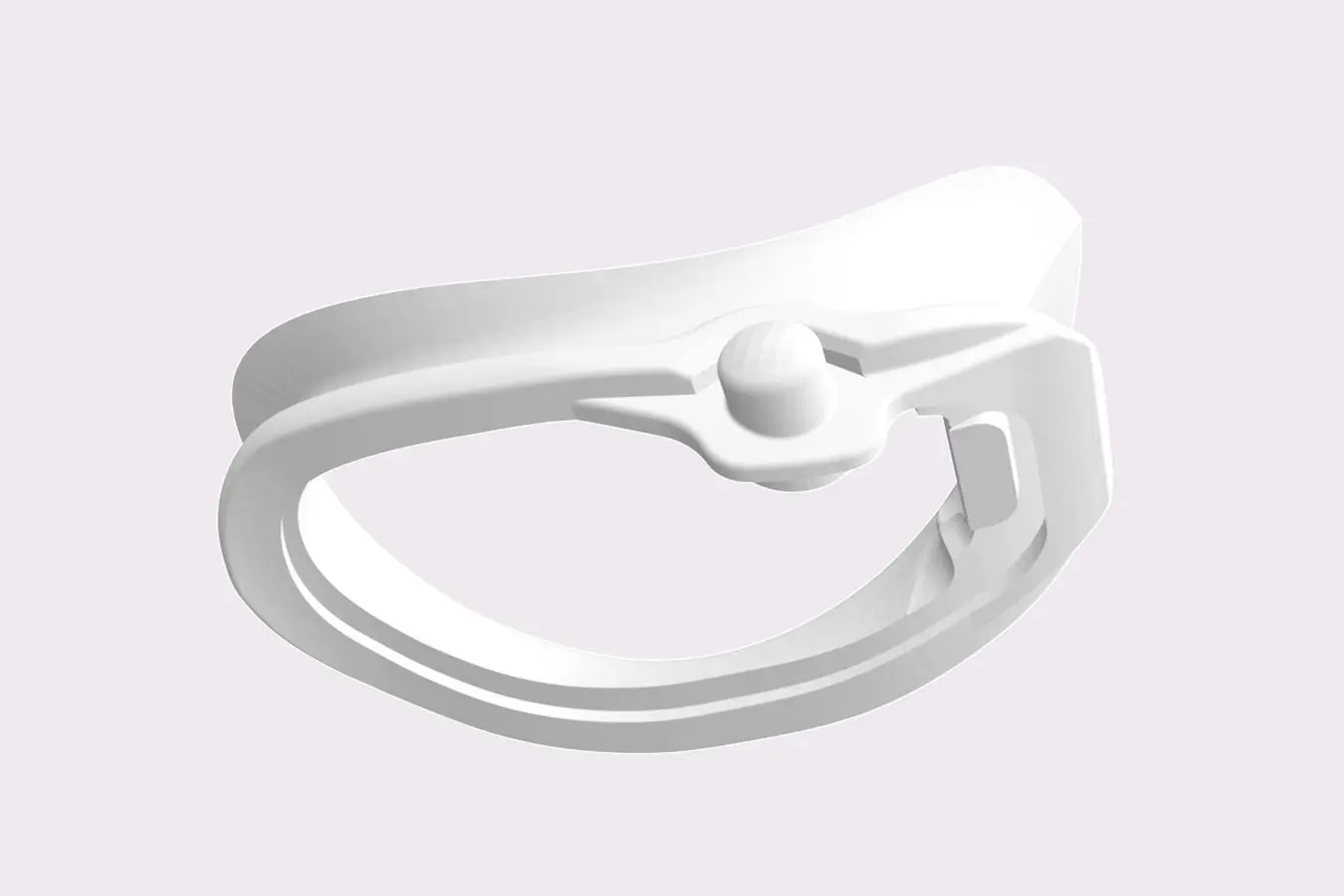
The new Smart Goggle has a complex geometry due to the integration of a button.
Before heading into urethane casting for their beta testing, the team needed to iterate on the design, "the button was a tricky design to do and it was challenging to prototype", says Beittel. Historically, the team would turn to 3D printing with Elastic 50A Resin to develop prototypes of this new gasket. However, silicone-like 3D printing materials do not have enough spring and do not rebound like real silicones. Although Elastic 50A worked well for initial prototypes, they needed a material that was close to the final silicone production material. “For the gaskets, we needed a rapid prototype material with some spring. Other materials would bend and flex, but they wouldn’t rebound like silicone.”
Producing Gasket Prototypes for Swim Goggles
Lead Time | Cost | |
---|---|---|
Urethane Casting | 2-3 weeks | $1220 for a set of two gaskets |
3D Printing With Silicone 40A Resin | 8 hours | $10 for each gasket |
When Beittel and his team got their hands on Silicone 40A Resin, the prototypes got increasingly better. The new material has significantly better rebound resilience and is very close to the production material. They used the gasket printed with Silicone 40A Resin for internal testing, and the team was amazed by how well it sealed around the eye and how watertight the material was. Beittel says that “it was a nice validation at the end that I could actually replace it for first shots from a production tool and it was very comparable.”
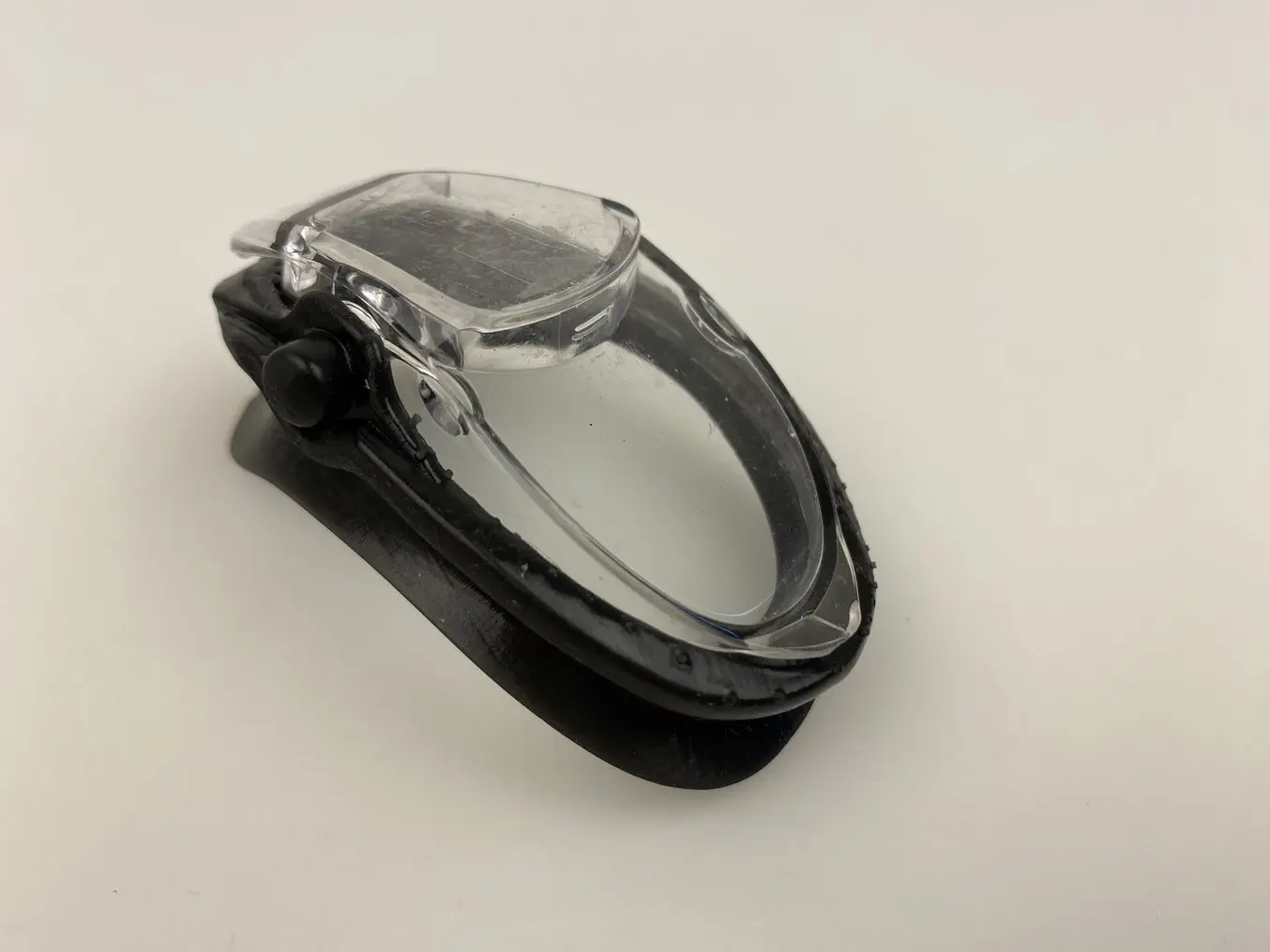
The team used the gasket printed with Silicone 40A Resin for internal testing, and they were amazed by how well it sealed around the eye.
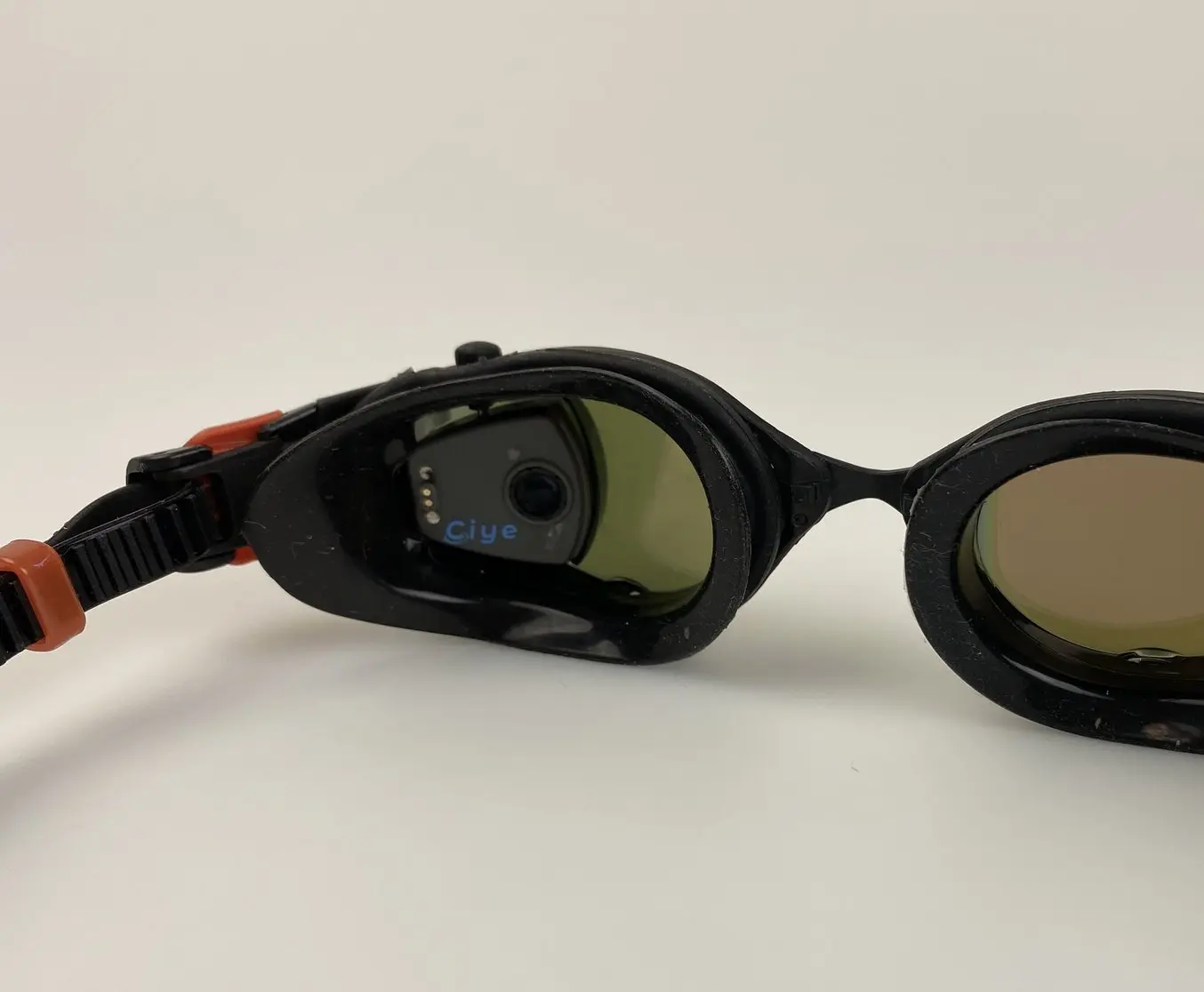
“I put in the new gasket made from [Silicone 40A Resin], swam it for a couple of weeks, and was impressed. It was a little bit softer than the production material, but it sealed around my eye well. I didn't get any leaking and was surprised it sealed around the lens and button with no additional glue.”
David Beittel, Senior Designer at FINIS, Inc.
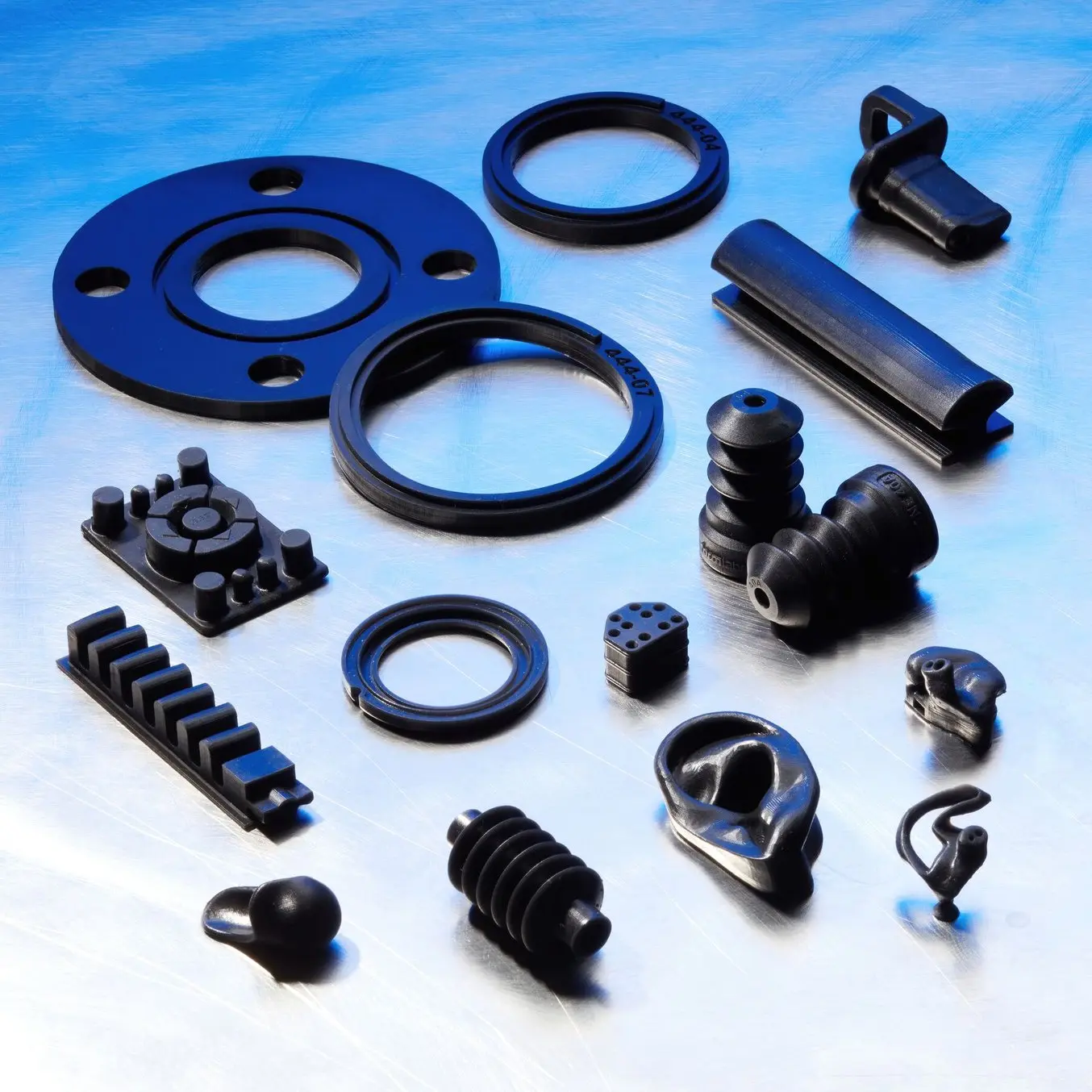
Introducing Silicone 40A Resin
In this webinar, our 3D printing experts walk you through the key benefits and applications of Silicone 40A Resin and present the material properties and the workflow for this resin.
Flexible and Fast: Swim Gear Development With SLA 3D Printers
One of FINIS, Inc.’s most popular products is the underwater bone conduction MP3 player. Loved by many, the team set out to explore a new less bulky “over the ear” version. One challenge they encountered was the headset's slight instability when swimmers perform vigorous movements like pushing off the wall or doing flip turns. In response, Beittel and his team sought to improve this by developing a small silicone add-on that securely attaches to the headset, enabling the goggle strap to go across it and give it extra stability.
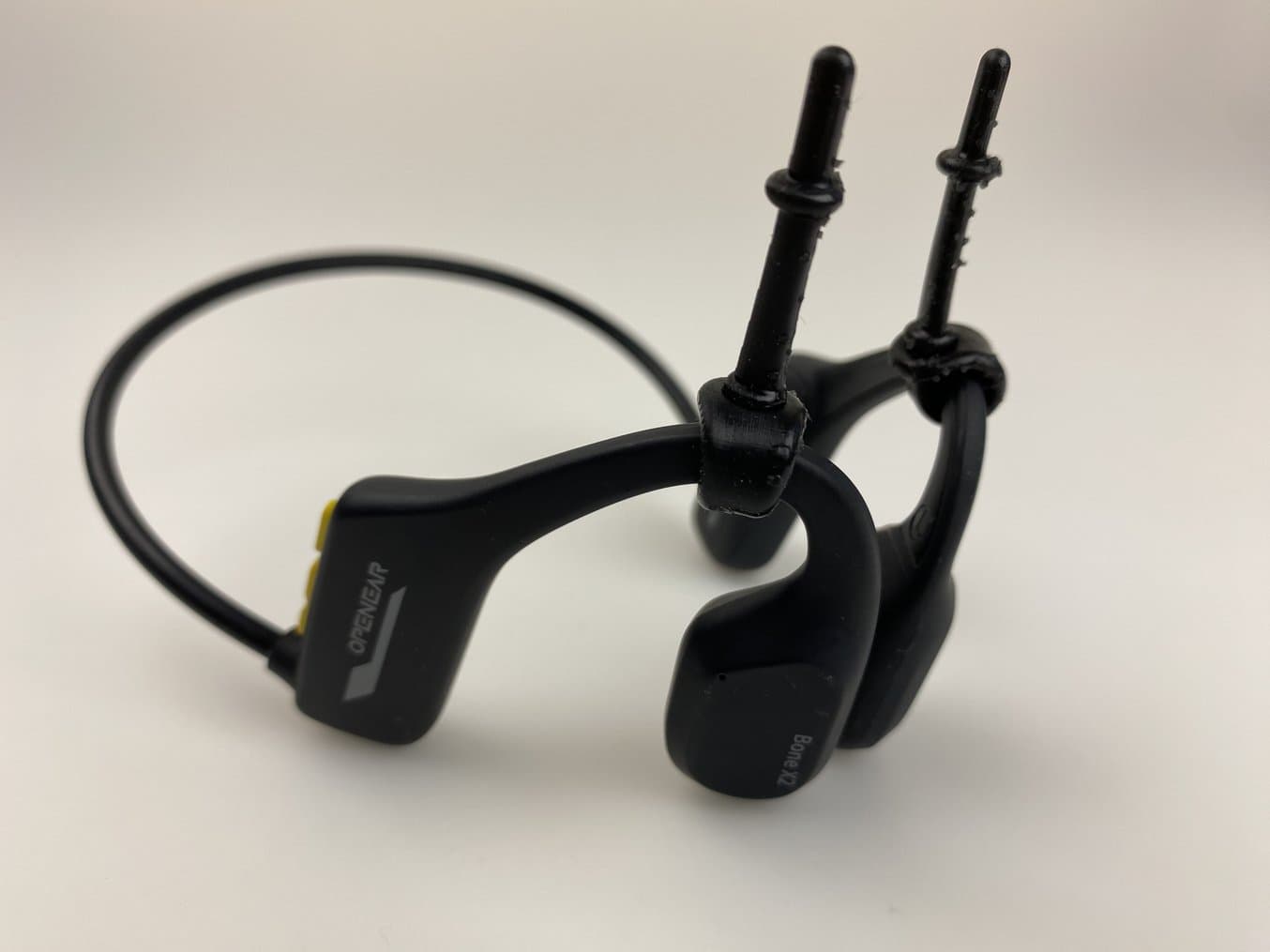
The team developed a small silicone add-on to secure the headset and give it extra stability.
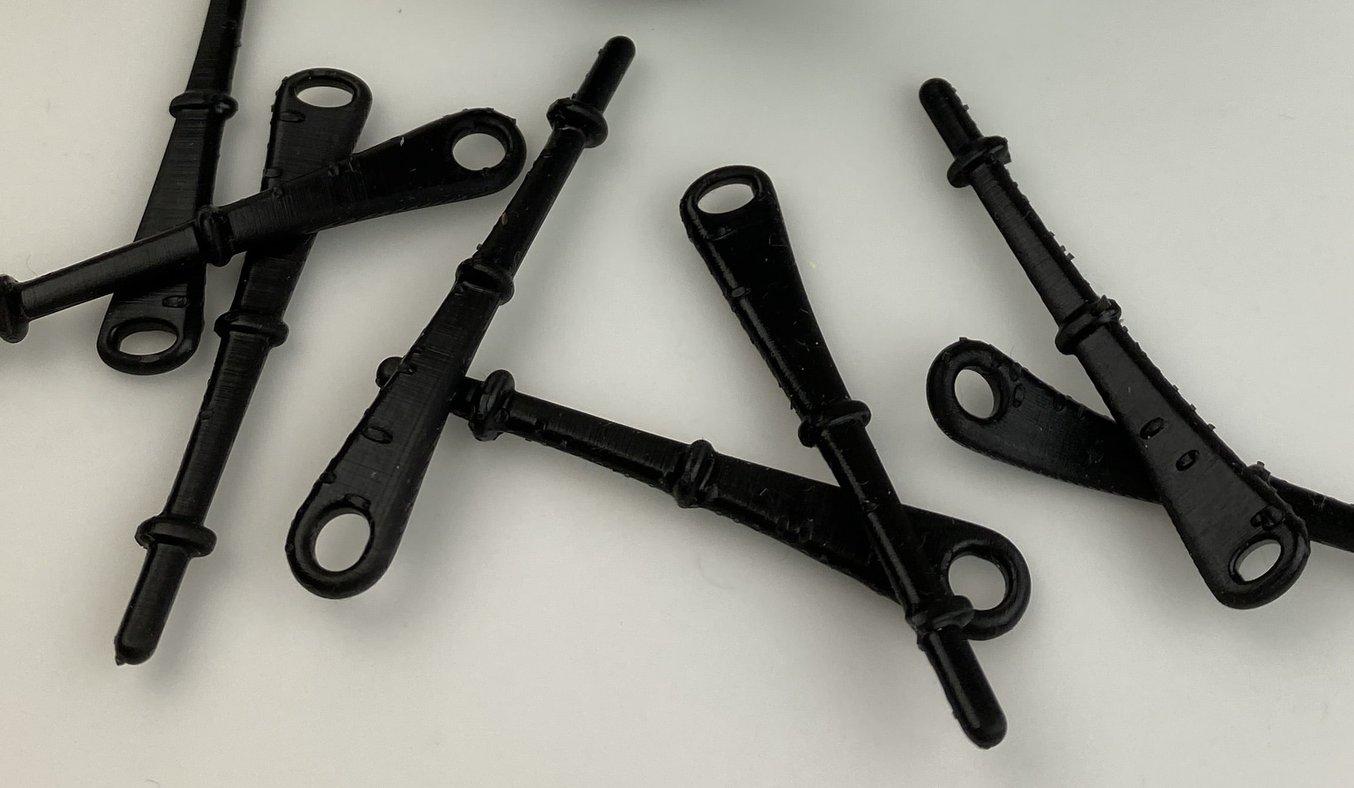
The product development group tested various 3D printed iterations to get it right. “We made little tweaks to see which was easiest for the user to put on, which one worked well in the pool,” says Beittel. Previously, they used silicone-like materials from Formlabs’ materials library but found that they didn’t have the necessary flex to fit through the holes and keep a tight fit on the headset, while they were also more prone to tearing.
The elasticity and durability of Silicone 40A Resin greatly improved the prototyping process, addressing these challenges effectively. Beittel adds that it’s important to him how the material looks, feels, and behaves, to see if it’s close enough to the production material. He appreciates that the material doesn’t take a set and retains its shape after repeated use.
“It does feel and behave like a production material. I like that it has a little springiness, rebounds much better, and doesn’t take a set. I think it's close to some of the production materials we use and absolutely close enough to use during development.”
David Beittel, Senior Designer at FINIS, Inc.
Without 3D printing, they would have opted for injection molding with a small tool and modified the mold if needed. But this would have substantially slowed the process down with at least a month of lead time for each iteration. Beittel emphasizes that Silicone 40A Resin allows them to go through the development cycle fast, by taking fast decisions, producing the parts quickly, and going through testing promptly.
This way, the team can narrow down the models and ensure they work properly before ordering the final production tooling. “Once you get into the tooling, you're limited. You can make a few changes, but they tend to be time-consuming, expensive, and they tend to reduce the quality of the tool.”
Another application that heavily depended on Silicone 40A Resin’s elasticity was the mermaid fins, which quickly rose to fame in recent years. As more and more people join the “mermaid world”, as Beittel puts it, it is crucial for the swimming gear company to be able to follow the trends and adapt to the larger foot sizes of the mermen that are now swimming with the mermaids. The team wanted to test the market before mass manufacturing multiple versions of this product. To do so, the product development group came up with a strap extension that can be added to the foot pocket to accommodate all types of feet.
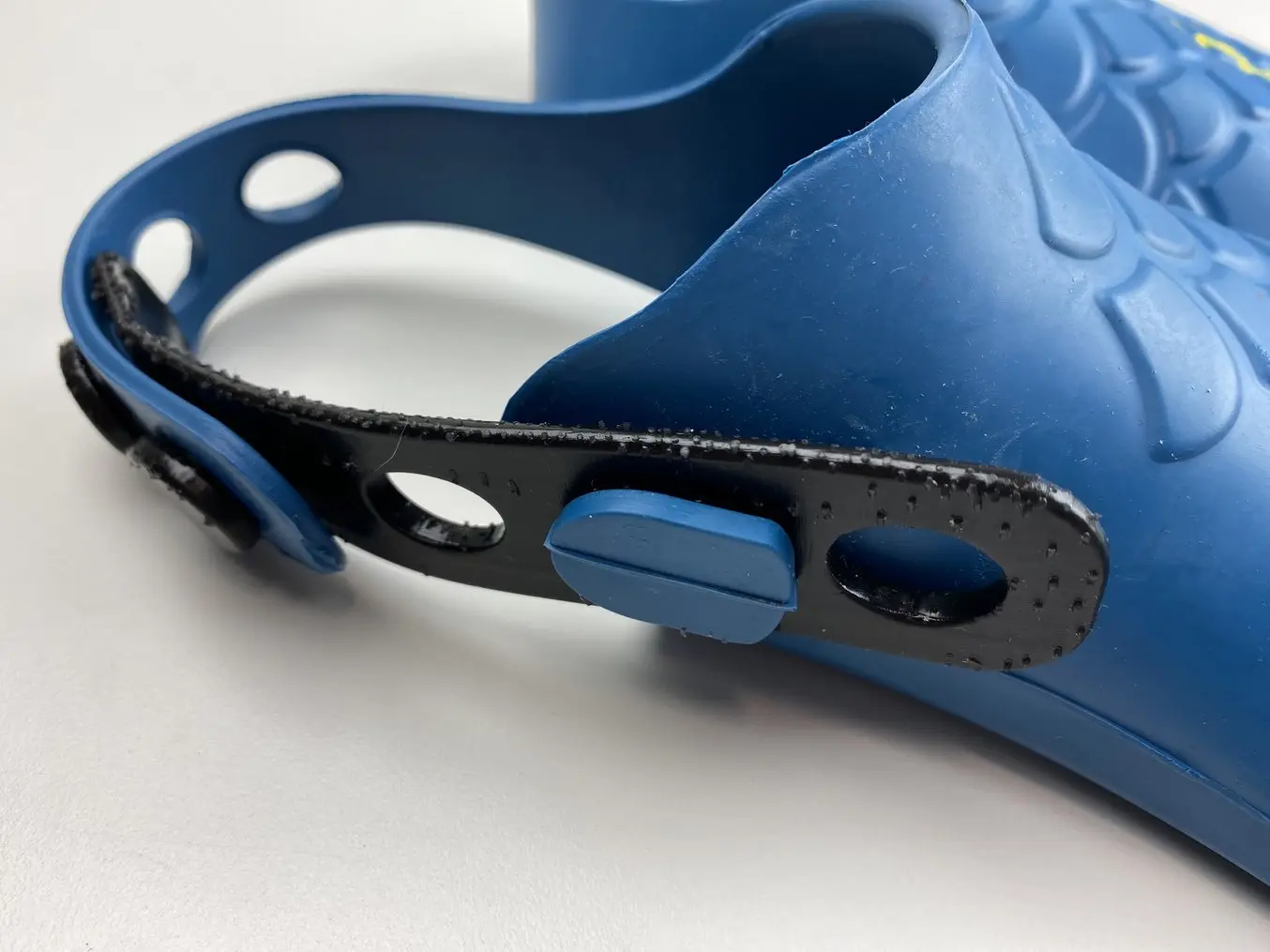
The product development group developed a strap extension to accommodate all sizes.
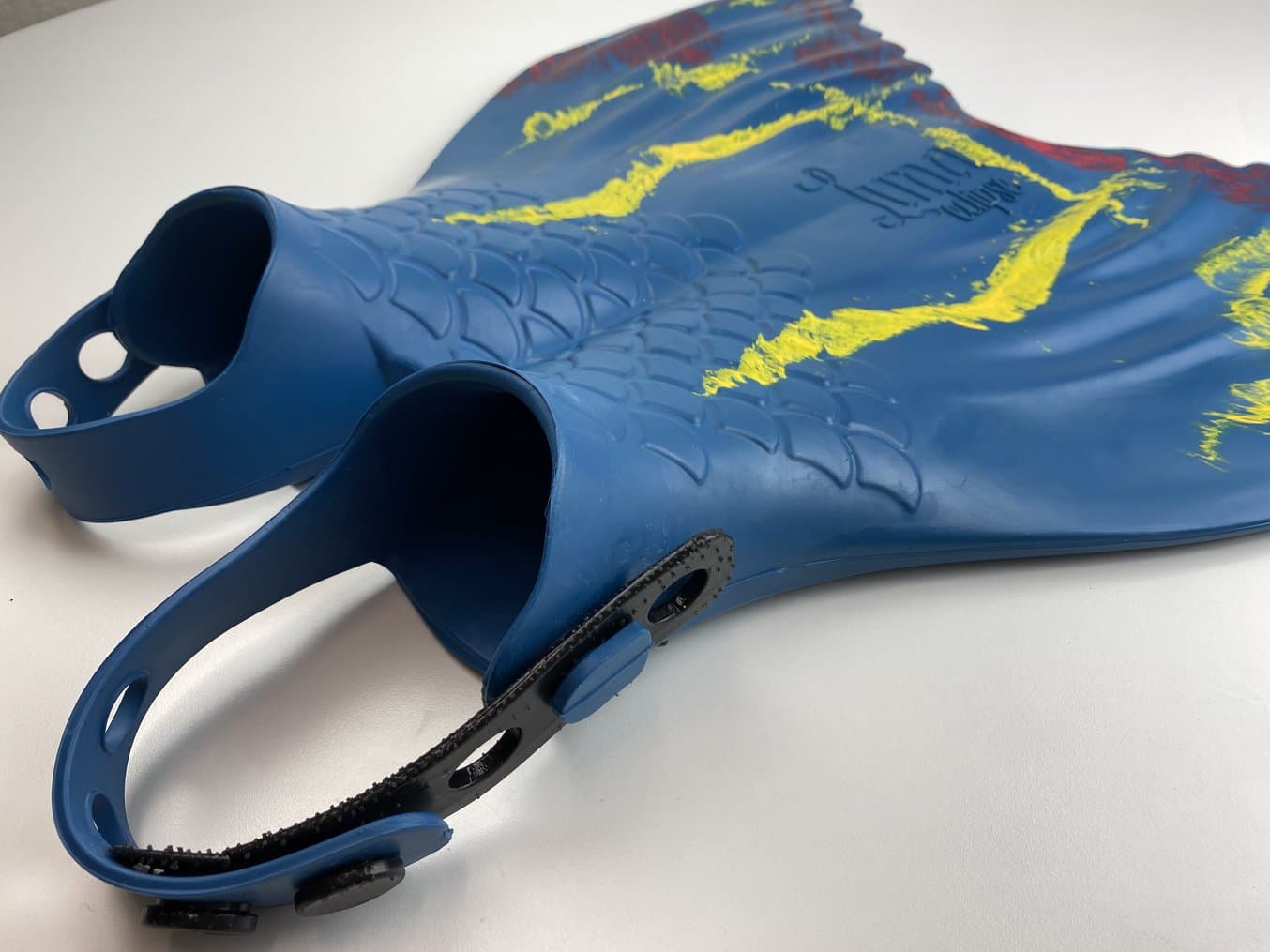
As in the previous case, the team first tested the other flexible materials before getting access to Silicone 40A Resin, and there’s no debating, the new material is in a league of its own. Flexible 80A Resin and Elastic 50A Resin, while great for initial prototyping and design iterations, lack the capacity to withstand repeated tension and strain, often leading to tearing during testing, while Silicone 40A Resin's elasticity remains unmatched.
Embracing The Future of Swim Gear
“Having an SLA printer in house at this price point is just amazing. I never thought I would be able to do that,” says Beittel.
Introducing Silicone 40A Resin into their workflow empowered the product development group at FINIS to accelerate the prototyping stages. Beittel was thrilled to see that the new material worked well for functional prototypes and internal testing of gaskets on goggles and various other rubber parts, thanks to its exceptional mechanical properties.