As one of the world’s largest fast-moving consumer goods (FMCG) companies, Unilever is constantly developing new products for everyday use, from personal care to home care, nutrition, and more. It’s quite likely that you have one or more of their products in your home right now, given that the company owns Dove, Domestos, Cif, Knorr, Axe (Lynx), Ben & Jerry's, and dozens of other global and local brands.
FMCG is an industry in which constant consumer demand drives fierce competition, so brands have to continuously innovate and adapt their product strategy. One important area of innovation is packaging; the design of a bottle can sometimes affect customer perception as much as what’s inside. Brands like Unilever have to consider material usage, aesthetic appeal, safety, and sustainability for a vast catalog of packaging types and the products they hold. But for a “simple” plastic bottle, getting from a design on the computer screen to filling it on the manufacturing line has traditionally taken many months.
“A consumer goods company like Unilever must be on the market as soon as possible or before your competitors. You need to offer the best product at the best price in the shortest time possible to the consumers. 3D printing helps us speed up this process.“
Stefano Cademartiri, CAD & Prototyping Owner, Unilever
Learn from Stefano Cademartiri, CAD & Prototyping Owner at Unilever, and Flavio Migliarelli, R&D Design Manager at Serioplast Global Services, how they worked hand in hand to test the viability of 3D printed molds for low-volume stretch blow molding (SBM) to accelerate prototyping and pilot testing, cutting lead time by six weeks and costs by up to 90%.
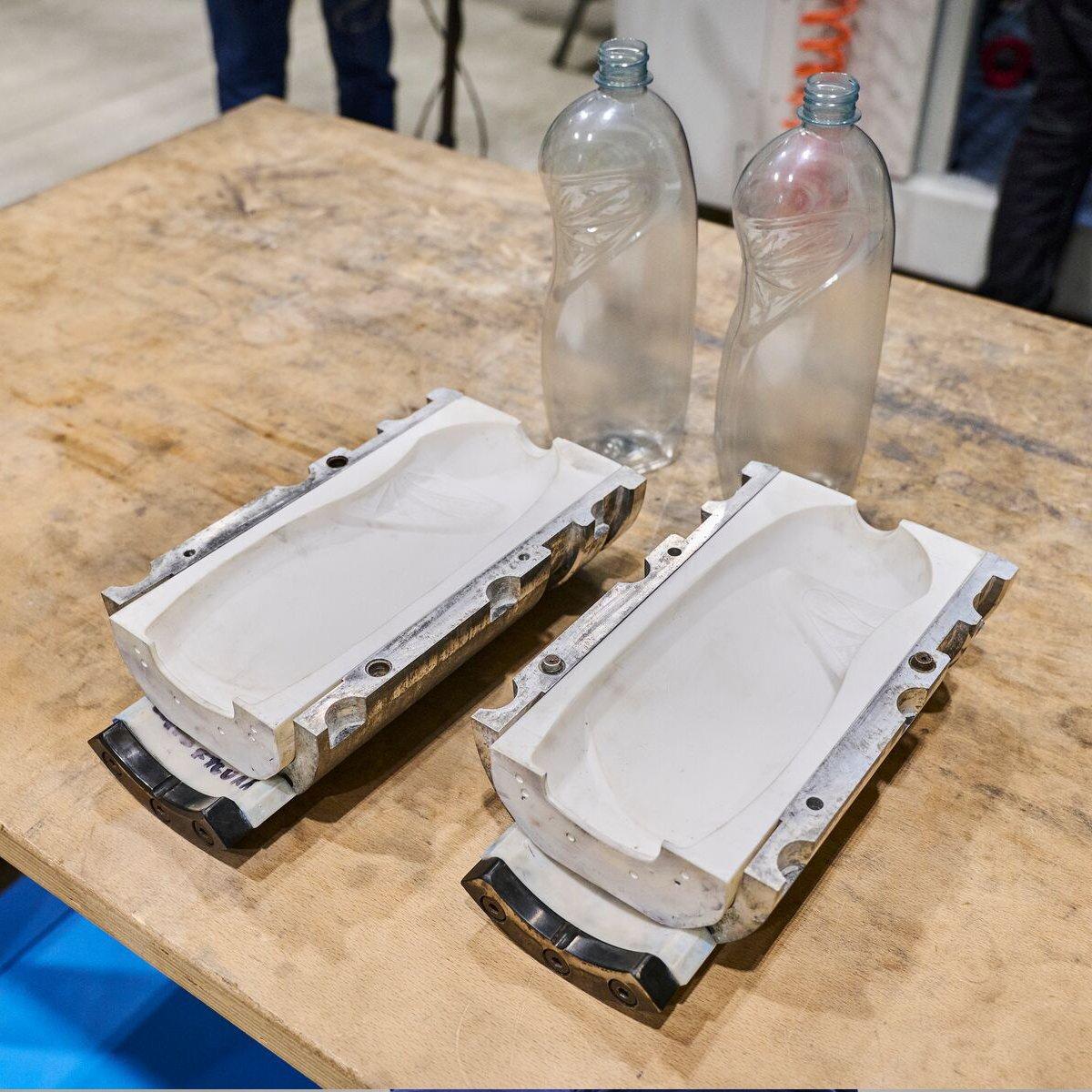
Low-Volume Rapid Stretch Blow Molding With 3D Printed Molds
This white paper provides methods and guidelines for using SLA 3D printed molds in the SBM process to lower costs and lead time during pre-production. From design and workflow considerations to molding conditions, it details the feasibility study from two industry experts, Unilever and Serioplast.
The Traditional Workflow for Developing and Testing New Bottle Designs
Plastic products such as food and beverage containers, cosmetic packaging, and medical packaging are most commonly produced with blow molding, a group of long-established rapid mass-production methods for high-quality, thin-walled parts. Blow molding has very short cycle times, typically between one and two minutes, and is extremely cost-effective for high-volume production. It is usually employed for producing millions of identical parts at low unit costs.
Blow molding works by inflating a heated plastic tube, called parison or injected preform, inside a mold until it forms into the desired shape. There are three types of blow molding processes: extrusion blow molding (EBM), injection blow molding (IBM), and stretch blow molding (SBM). SBM is commonly used to produce high-quality glass clear PET containers such as water bottles.
Serioplast is a global producer of rigid plastic packaging for the FMCG industry and is one of Unilever’s major partners for developing and producing packaging for the home and personal care market. “We produce four billion bottles per year in PET, HDPE, and PP materials,” said Migliarelli.
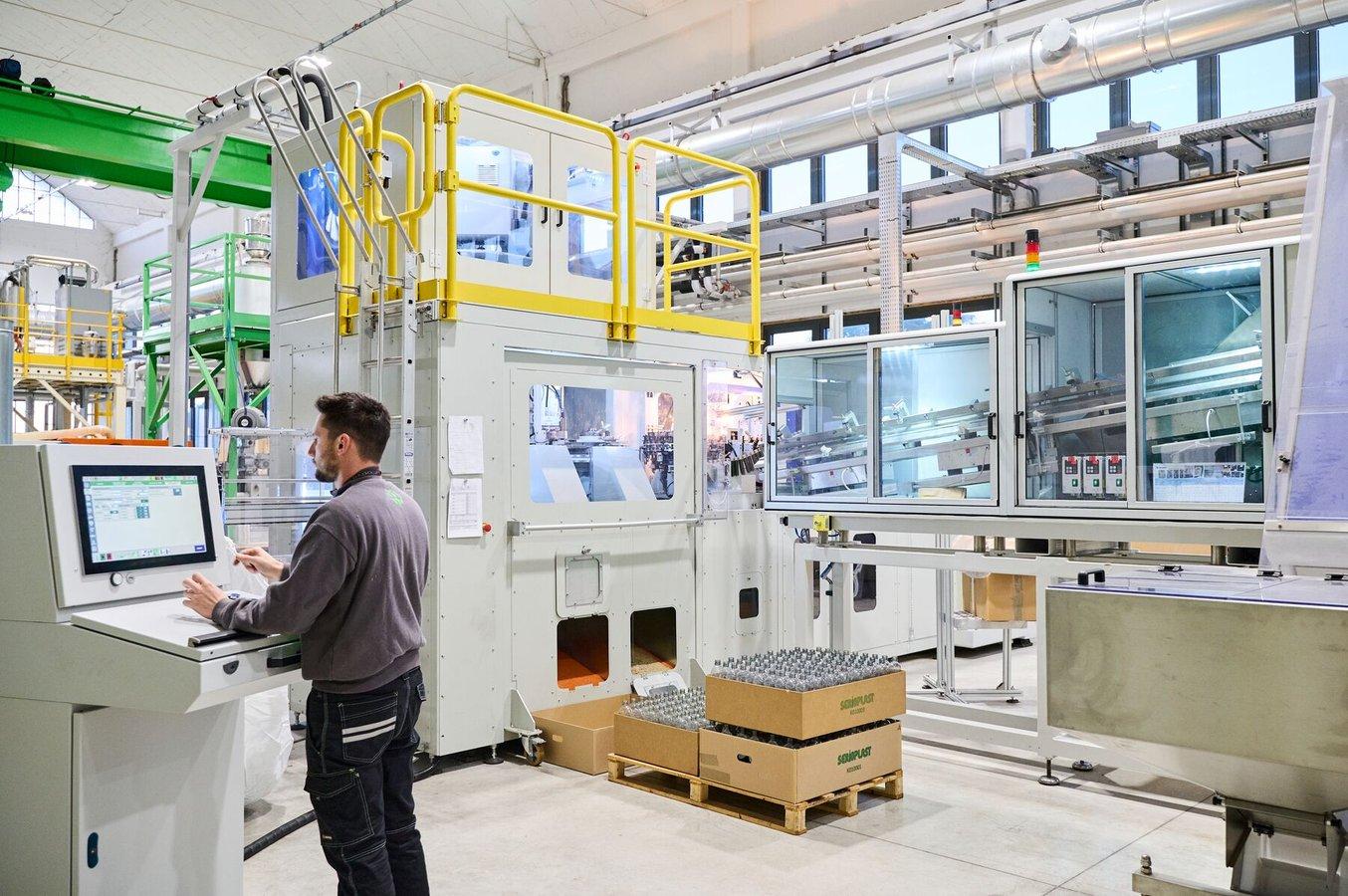
Seriomac UNIX 4 Cavities SBM machine from Serioplast in their R&D facility in Italy. Together with Unilever, they developed a new workflow for using 3D printed molds in this large-scale industrial manufacturing equipment.
Typically, Serioplast would either directly 3D print mockups for prototypes or produce them through blow molding. Traditionally, 3D printed mockups didn’t represent the right feel or transparency and were not reliable enough to be sent to consumers. However, building production-quality samples through SBM requires expensive metal tooling, adding six to nine weeks of lead time to a typical pilot testing phase due to the complexity of the process and outsourcing the production of the mold.
“We have to wait six to 12 weeks before we can give a client the real sample, so we’re wasting so many weeks just to try a new bottle design. Sometimes it's demanding and frustrating because maybe you have to start again,” said Migliarelli.
SBM molds are traditionally made out of metal by CNC machining, which requires specialized equipment, CAM software, and skilled labor. The production of metal tooling is generally outsourced to service providers offering four to eight weeks lead time and costs anywhere from $2,000 to $100,000+ depending on the complexity of the part and the number of parts per mold. Even machining a metal mold in-house normally takes six weeks as it requires several steps: lead time for material order, CAM and machine setup, manual polishing, and waiting time for machine availability.
As a result, blow molding parts in low volumes for prototyping and pilot testing has traditionally not been economically feasible. Companies like Unilever have had to plan with extended timelines and make final design decisions based on looks-like prototypes in different materials, which often led to obsolete tooling and sunken costs.
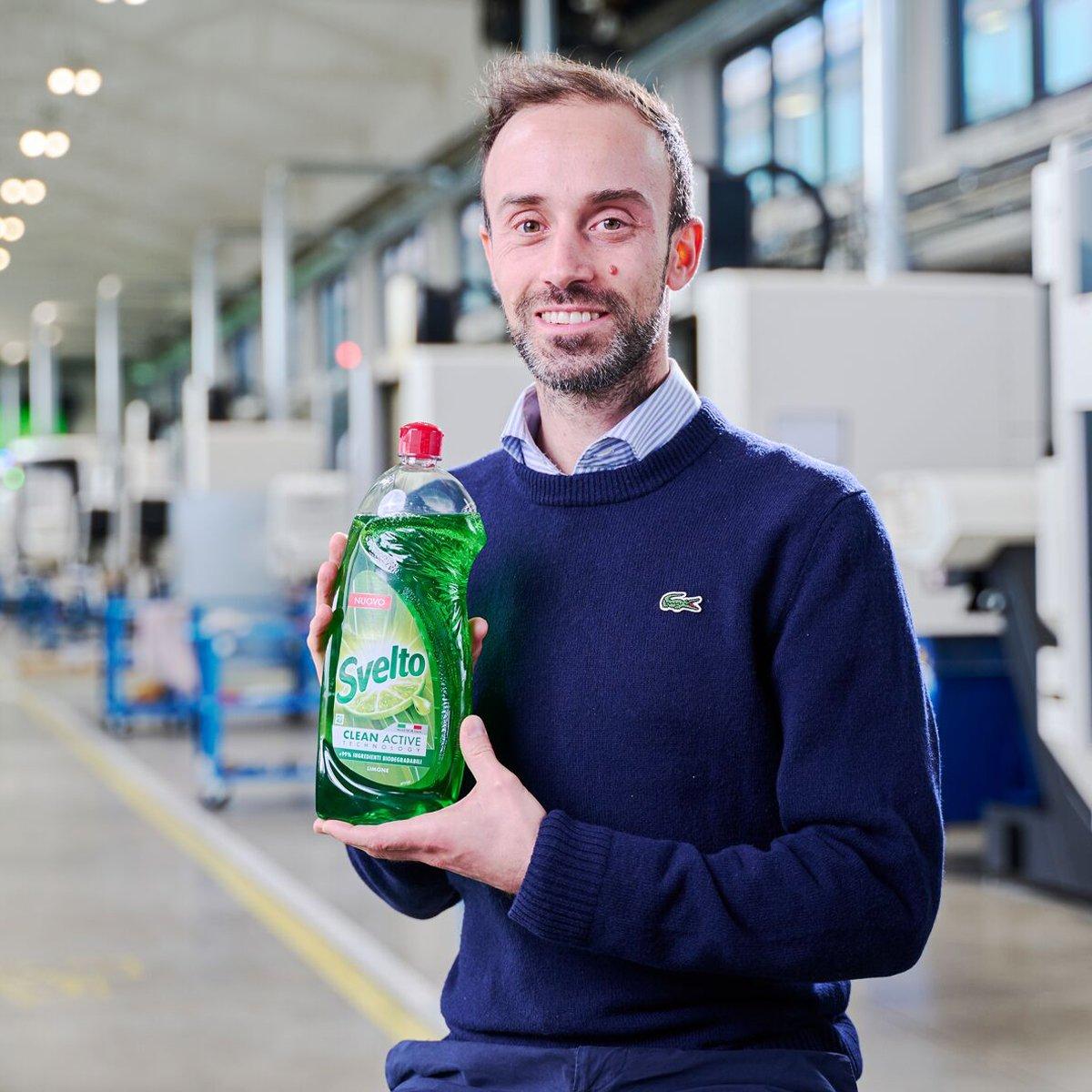
Reduce Cost and Time for Pilot Testing Packaging With Rapid Blow Molding
In this webinar, blow molding expert Flavio Migliarelli will walk you through the workflow and step-by-step method, and discuss the key benefits and applications of using 3D printed molds for rapid stretch blow molding.
Blow Molding Real Bottles 70% Faster and 90% Cheaper
3D printing is a powerful solution to fabricate tools rapidly and at a low cost. It requires very limited equipment, freeing up CNC capacity and skilled operators’ time for other high-value tasks. With in-house 3D printing, manufacturers and product designers can introduce rapid tooling into the product development process to validate design and manufacturing steps before transitioning to mass production. 3D printed molds are already used in processes such as injection molding or thermoforming to iterate quickly, accelerate product development, and bring better products to market.
Stereolithography (SLA) 3D printing technology is a great choice for molding. It is characterized by a smooth surface finish and high precision that the tool will transfer to the final part and that also facilitates demolding. The Form 3L is a large format SLA 3D printer that enables the fabrication of large-scale parts and molds, while being compact enough for an office.
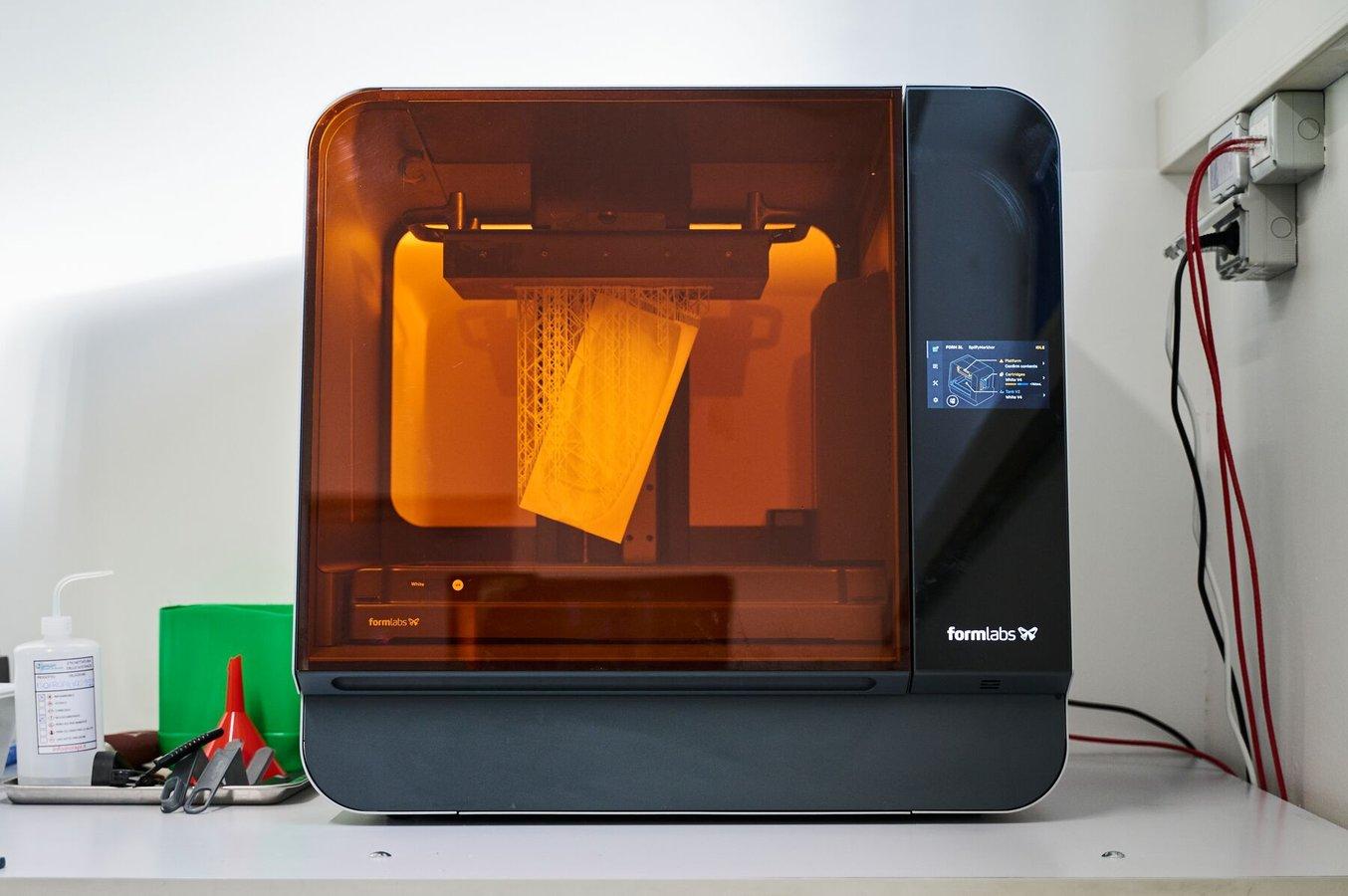
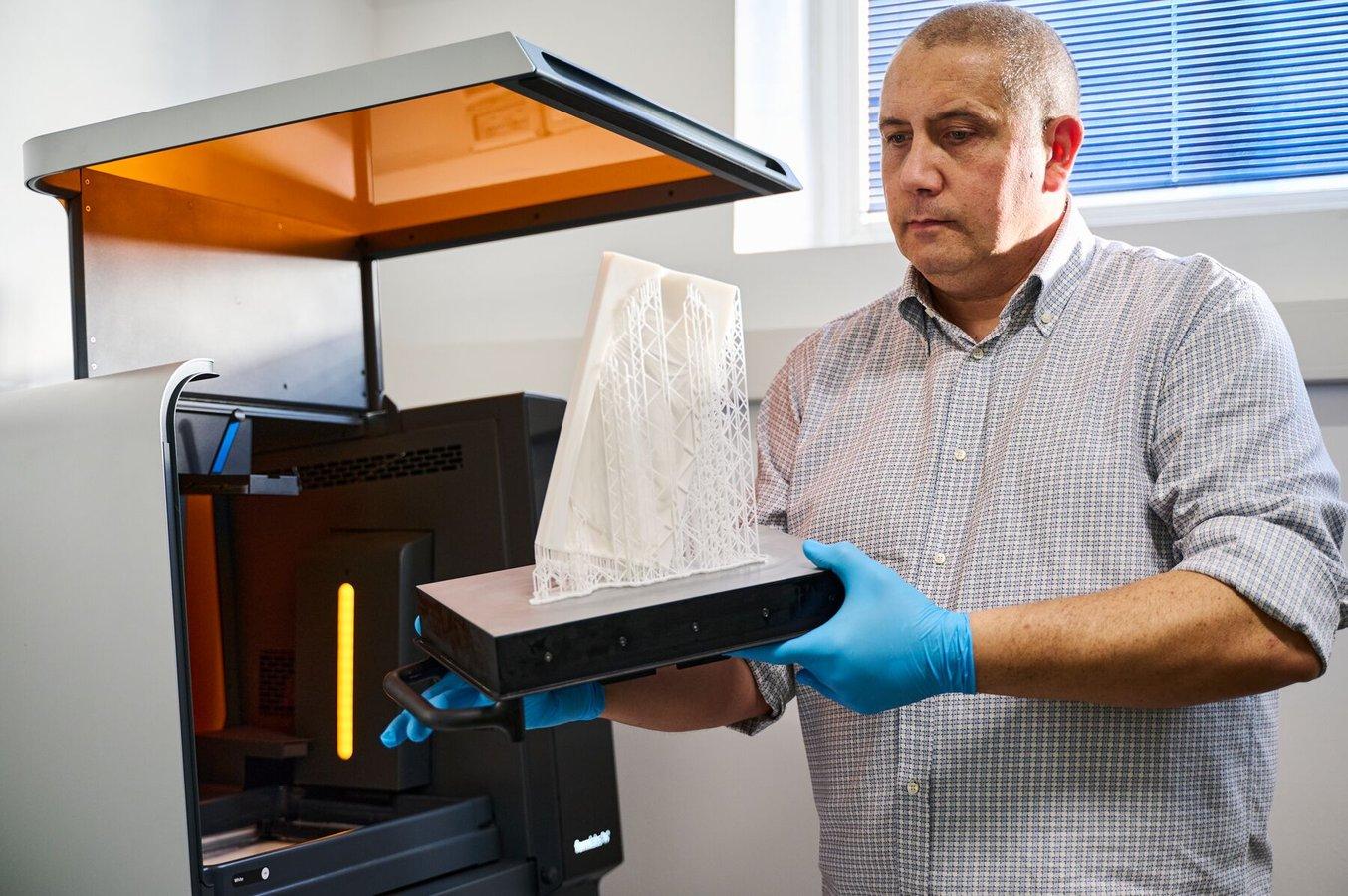
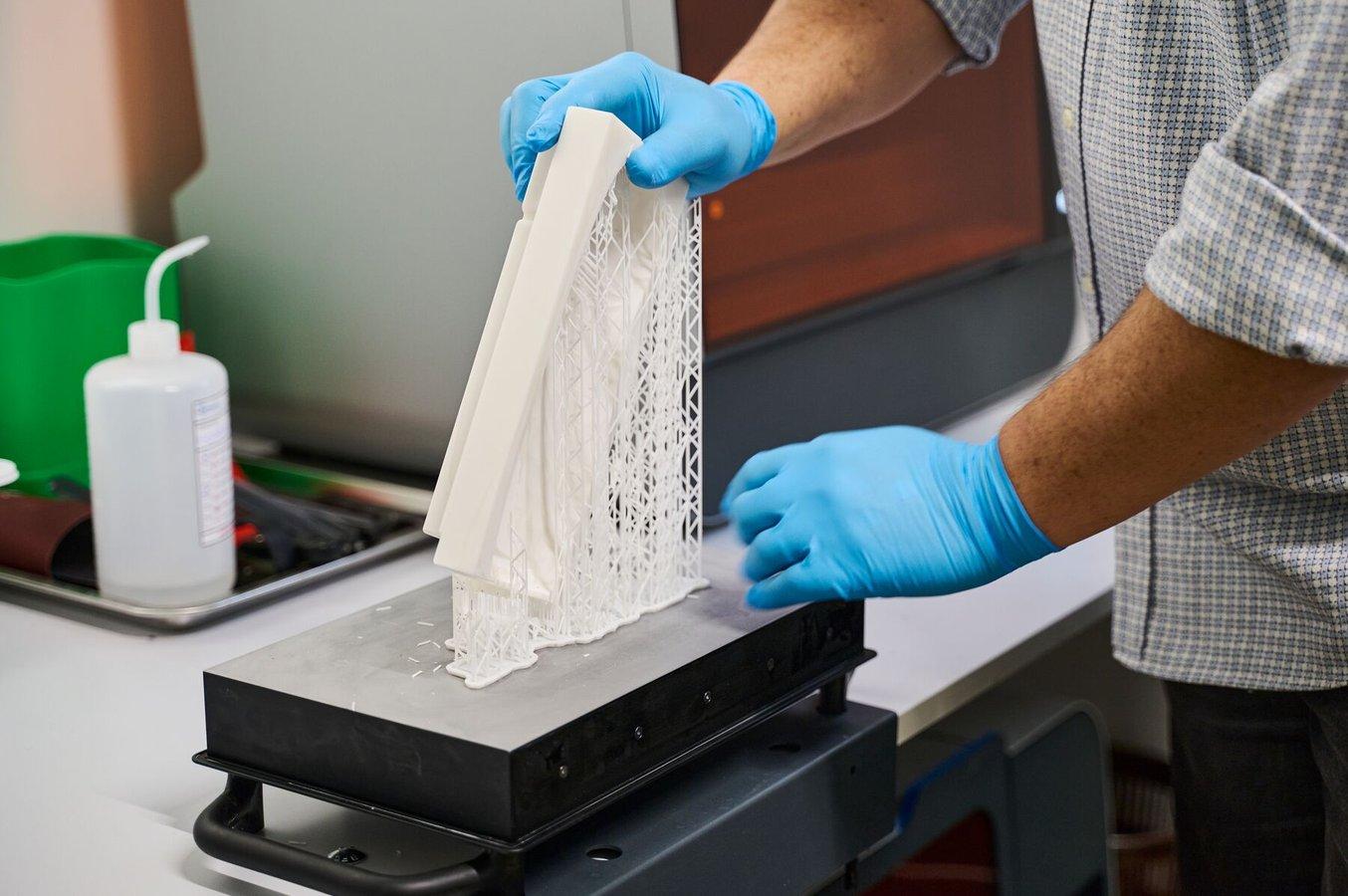
The mold is 3D printed on the Form 3L with Rigid 10K Resin.
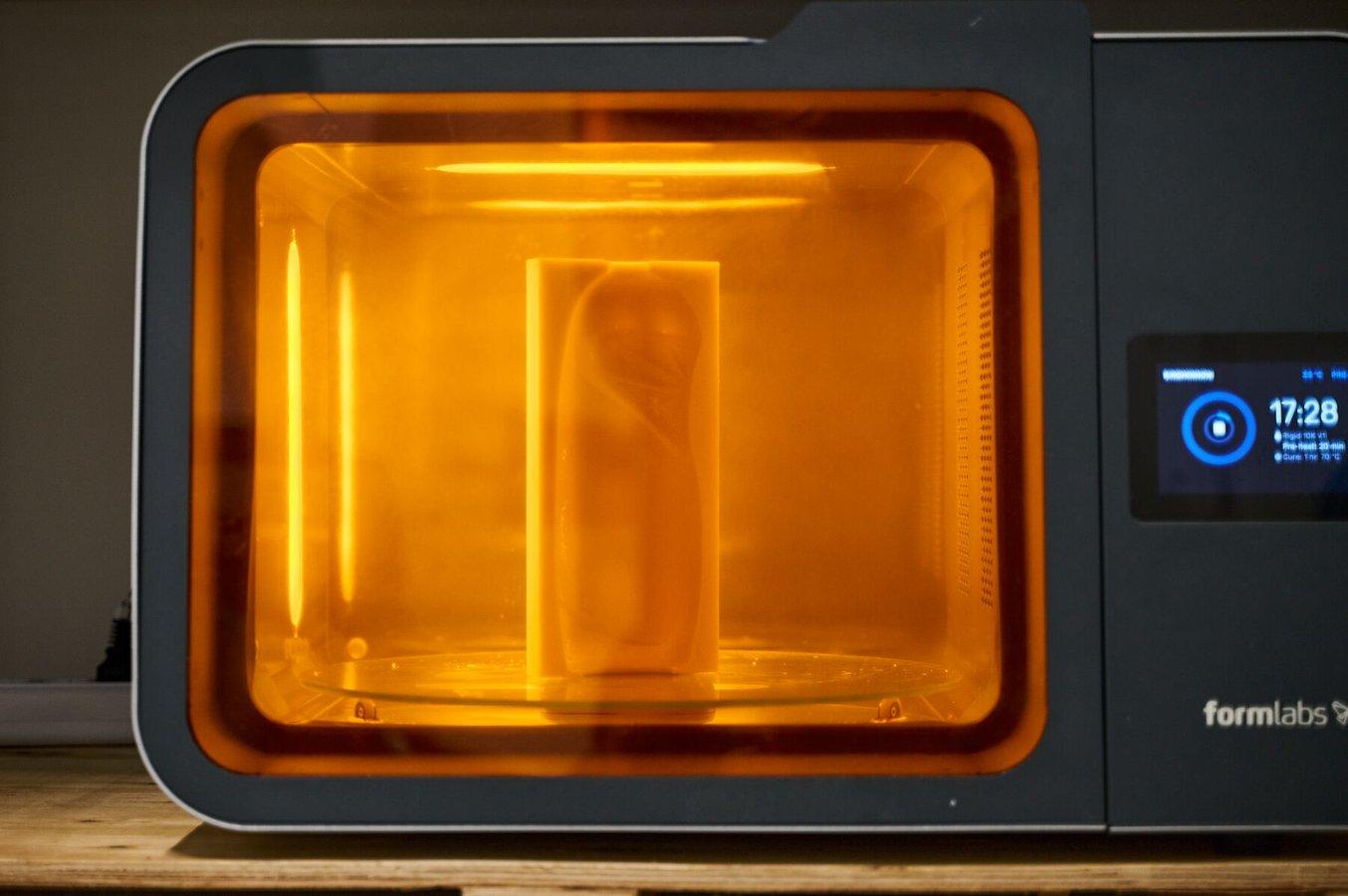
After washing, the supports are removed and the mold is post-cured.
Material choice is crucial for producing molds. Unilever and Serioplast needed a material that could withstand the internal pressure and the temperature of the SBM process while maintaining good dimensional accuracy and stability.
“With the help of Formlabs’ engineers, we identified the material that could give us the possibility to have a few bottles in the real materials to do our tests,” said Cademartiri.
Rigid 10K Resin is Formlabs' recommended material for SBM as it combines strength, stiffness, and thermal resistance. It is an industrial-grade, highly glass-filled material with an HDT of 218°C @ 0.45 MPa and a tensile modulus of 10,000 MPa. Tooling printed with Rigid 10K Resin has good dimensional stability and is suitable for hundreds of blow molding cycles with high repeatability.
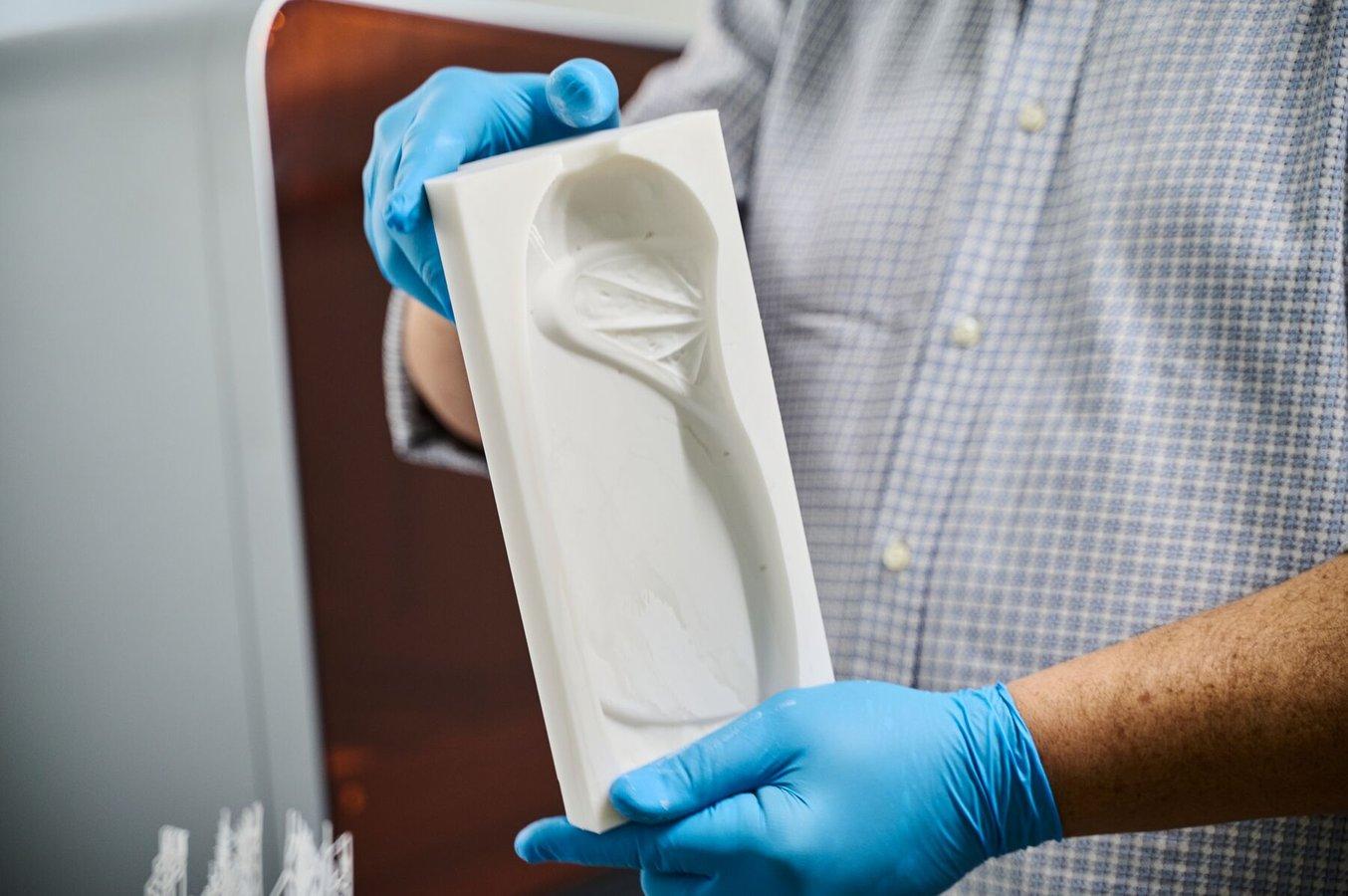
By using Rigid 10K Resin, Serioplast fabricated precise molds with smooth surface finish, capable of integrating fine features, including holes as small as 0.5 mm. They post-processed the tool with a polishing machine or manual sanding to meet the critical dimensions. Textured surfaces were incorporated in the CAD of the mold cavity.
“We have exactly fine-tuned details for the mold, especially for a bottle that has some logos or things like a lemon detail, which requires lots of precision. The Formlabs machine together with Rigid 10K Resin offers the possibility to have very good details that can then be transferred to the real bottle,” said Cademartiri.
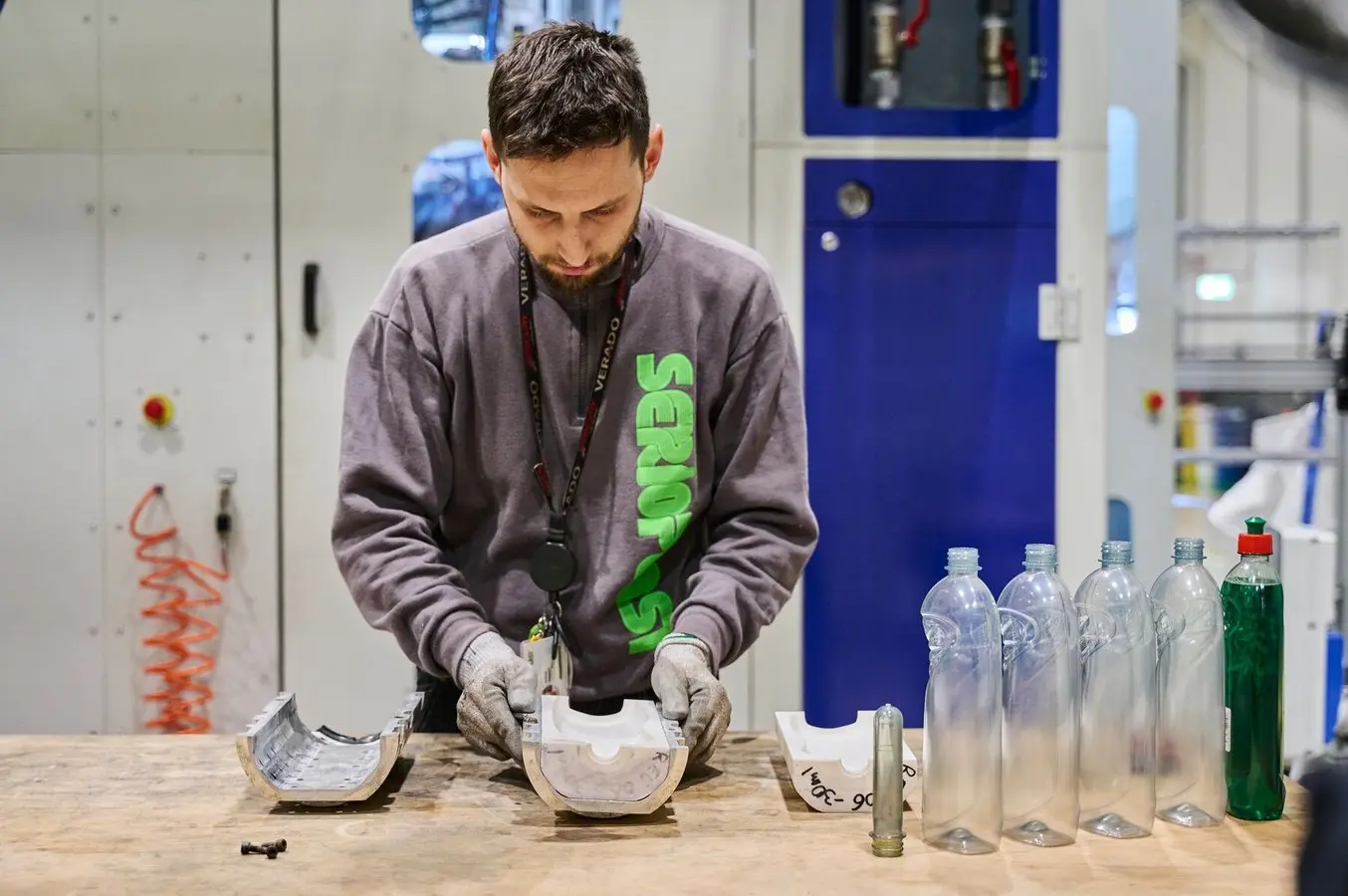
The mold 3D printed with Rigid 10K Resin is manually polished and then assembled into a metal frame.
With SLA 3D printing, a mold can be built in two days. 3D printed molds reduce the lead time to start pilot testing from six to two weeks while achieving realistic pre-production parts that are very close to production quality and molded using the same material and machinery as the eventual production units. Additionally, 3D printed molds allow operators to pilot-test multiple designs simultaneously.
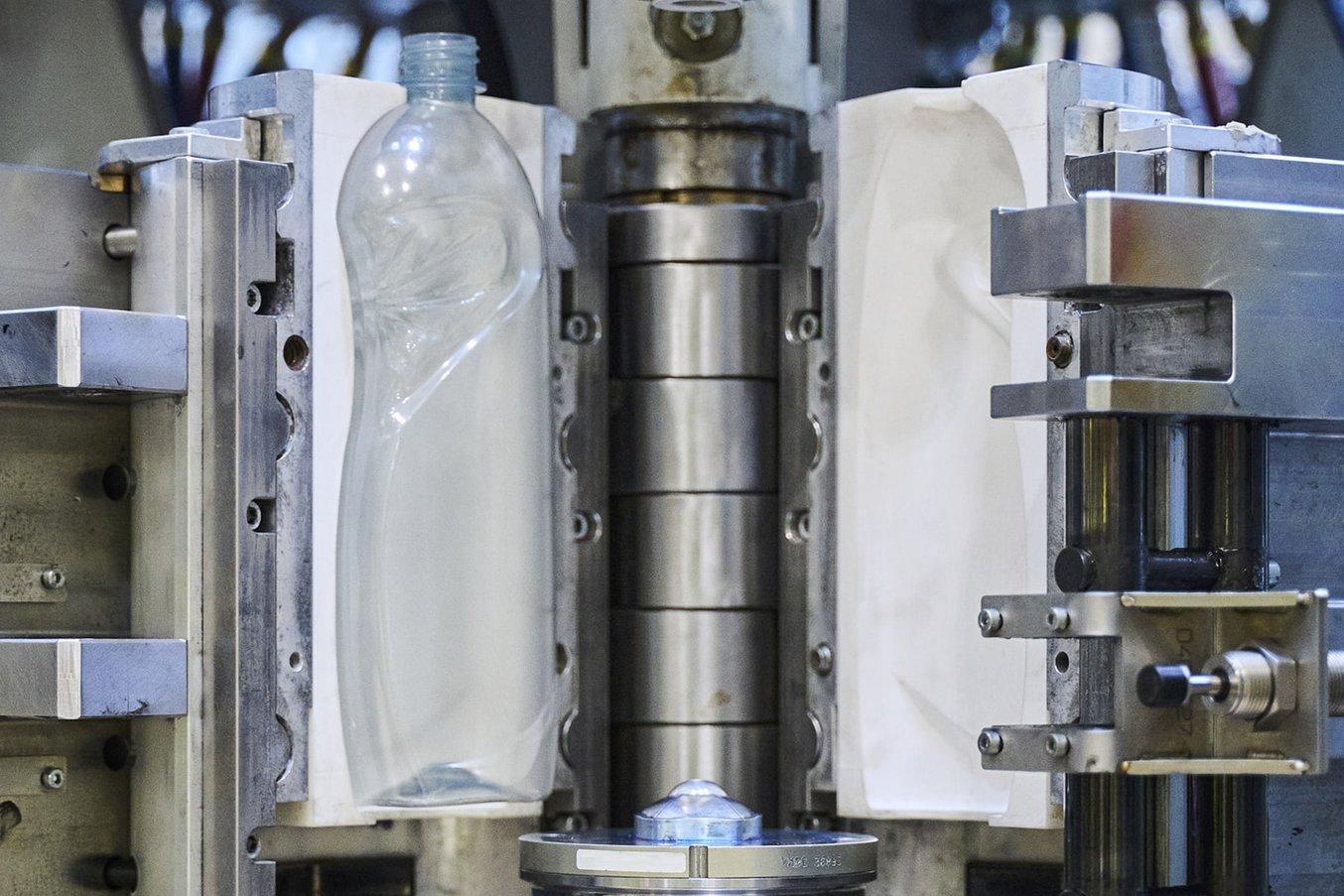
Mold 3D printed with Rigid 10K Resin for Unilever Slice 750 mL bottle installed onto the shell holder on the machine. The team can use the same process window as with a standard pilot mold, which allows them to reliably test the final process.
“With the 3D printed mold, we use a standard layout inside a shell holder that is placed in the blow molding machine. So we save a lot of time on mold design and we are able to manage our 3D printing schedule very, very easily,” said Migliarelli.
Production 200 units | Machined metal mold | 3D printed mold |
---|---|---|
Equipment | In-house CNC machine or outsourcing | Form 3L Rigid 10K Resin |
Pilot testing lead time | 6-8 weeks | 2 weeks |
Tooling cost | $2,500-$10,000 | $500-$1,000 |
“With the 3D printed mold, we can save up to 70% time and 90% cost compared to the standard mold. In the past, [clients] had to wait up to 12 weeks just for one design, now we can make five designs.”
Flavio Migliarelli, R&D Design Manager, Serioplast Global Services
Running such extensive testing with traditional methods is almost impossible. They would need to invest in a metal mold for each design without the benefits of economies of scale and would never recover tooling costs.
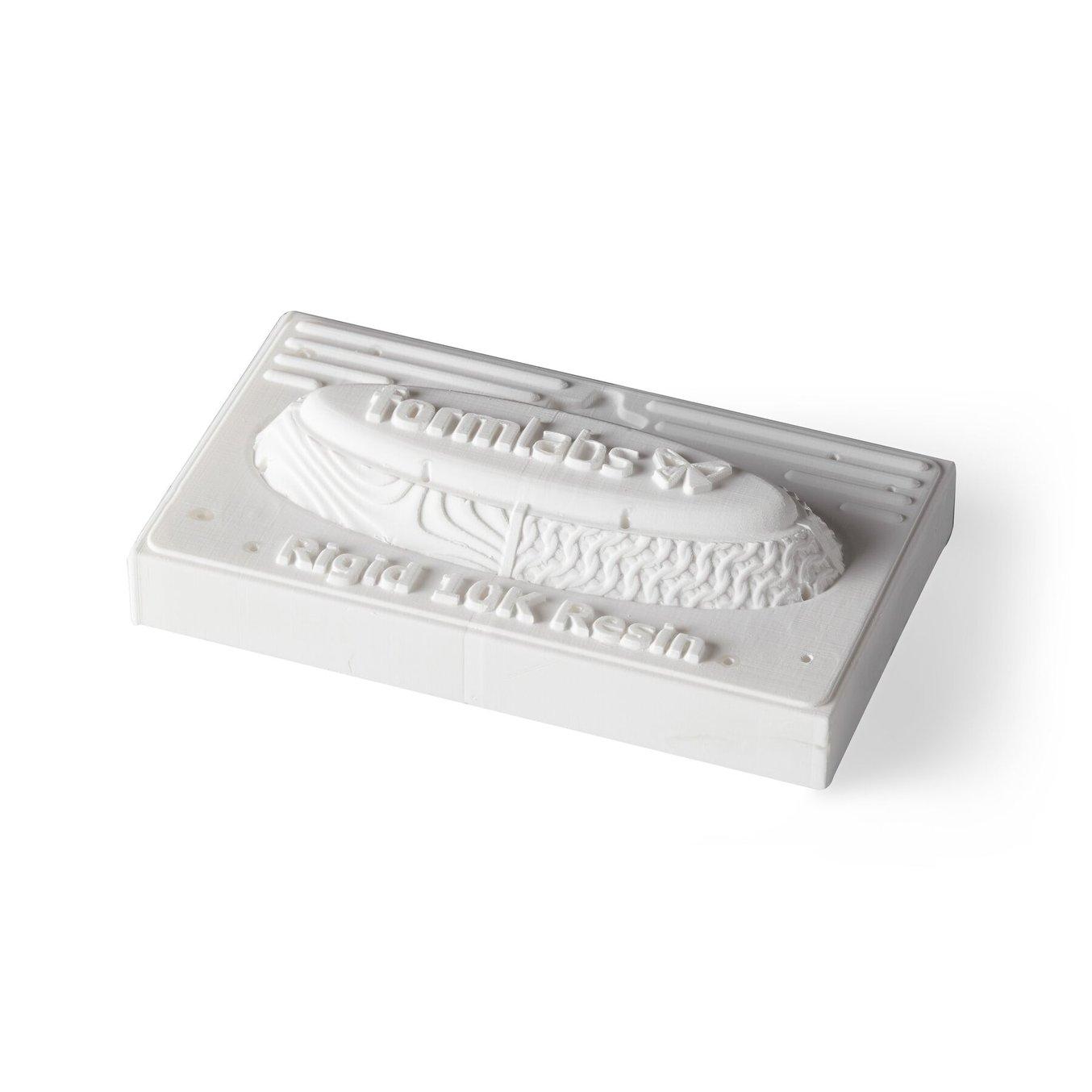
Request a Free Sample Part
See and feel Formlabs quality firsthand. We’ll ship a free sample part to your office.
From Customer Testing to Dialing in the Production Line
Primarily, the 3D printed tools are employed to produce samples for consumer testing. They are representative of the final product in terms of feeling, aesthetics, and usage, and are perceived as the real product in the eye of the consumer.
“You can have a real bottle before you do the real mold, so you can identify immediately if you are on the right path in your development or if you need to change something to avoid mistakes that can cost more.”
Stefano Cademartiri, CAD & Prototyping Owner, Unilever
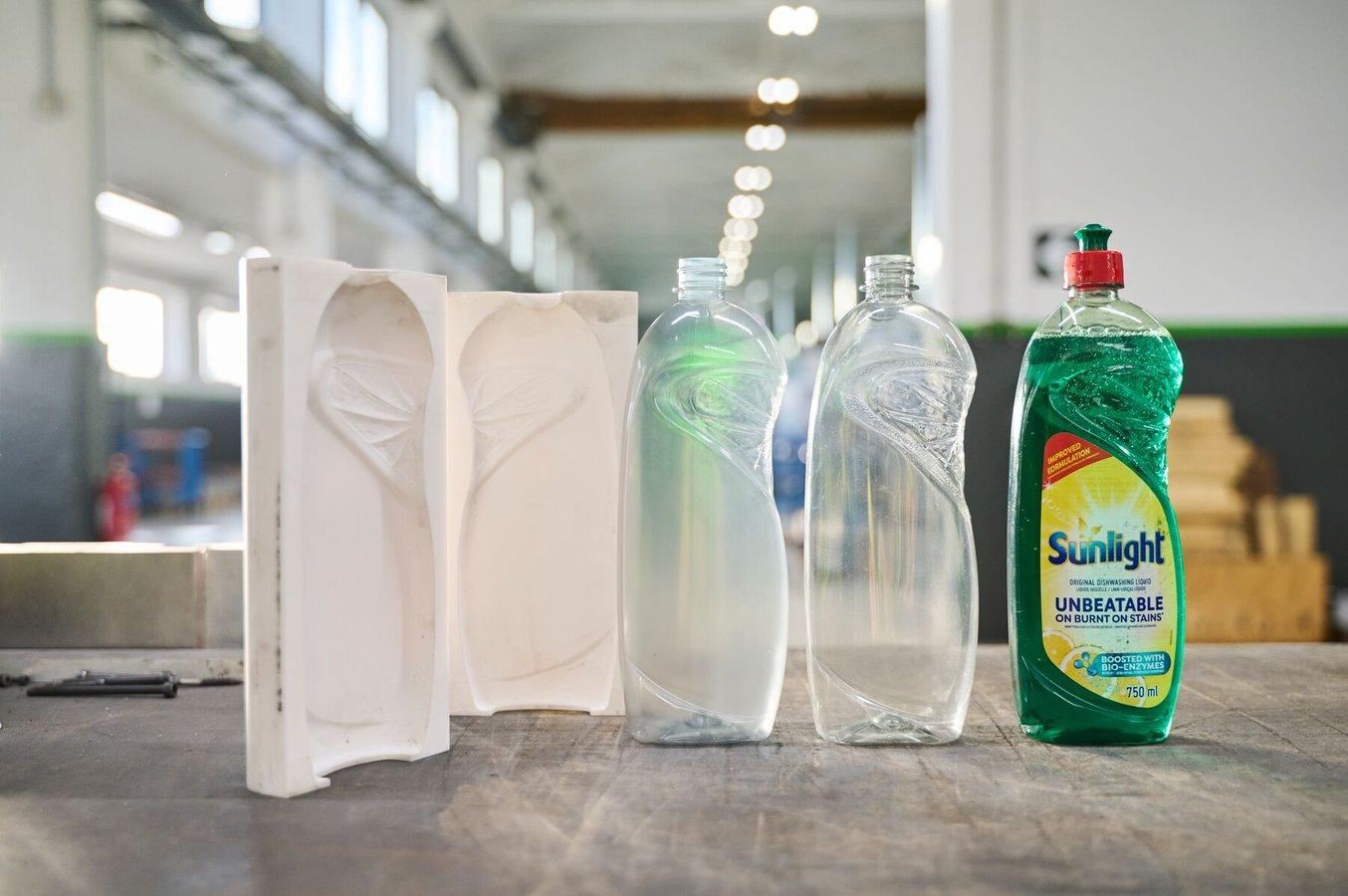
Bottles produced with a 3D printed tool are nearly indistinguishable from the final product produced through traditional metal tooling processes. From left to right: the two-part mold 3D printed with Rigid 10K Resin, a bottle produced with the mold 3D printed with Rigid 10K Resin, a bottle produced with a metal mold, and a labeled prototype bottle for customer testing.
A secondary use of the modular mold is to validate the SBM process as well as the PET preform that will be blown, looking at the process windows, stretch ratio, and material distribution achievable. Serioplast produces the preforms in-house through injection molding. While some preforms are custom-made for a specific bottle, they usually work with standardized items that users can’t modify. The Serioplast team wanted to understand the range of capabilities available through this stock preform. Knowing this information helps them determine if a given preform is suitable to blow mold a specific bottle before going into production.
“We are using the same process window as with a standard pilot mold. This is super good, because we can test the final process windows and see what happens to the bottle. We are talking about up to 30 bar pressure. It's absolutely good and reliable on that. We are also talking about 100 °C heating for the preform, without any wearing on the cavity of the 3D printed mold. We could produce very easily up to 100, 200 bottles every day. We can go up to 1000 with more time,” said Migliarelli.
The third application for producing rapid molds is to test some aspects of the production line early on. Because the bottles formed with 3D printed molds are so close to the production units, they can be employed to carry out some primary validation of the filling line such as the movement of the line, the operation of the star wheels for the bottle-filling machines, the capping, or the action of the robotic case packer. Pilot testing the manufacturing line early allows factories to anticipate spare parts, prepare the line for mass production, and accelerate their time to market.
Bringing Better Products to the Market Faster
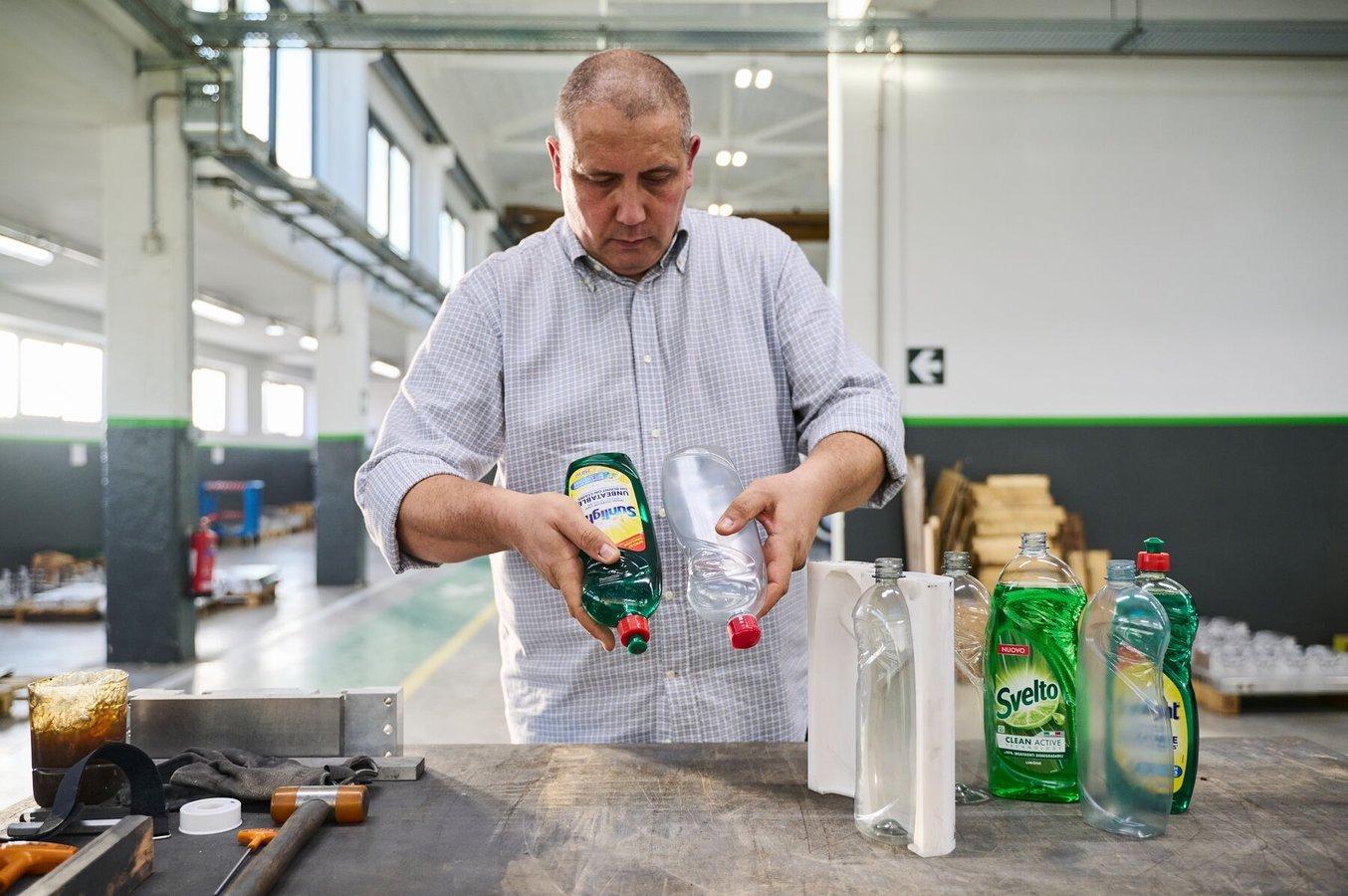
Cademartiri and Serioplast have already tested about 15 different models of bottles with the new process.
With Formlabs SLA printers and Rigid 10K Resin, Unilever and Serioplast were able to reduce lead times by up to 70% and tooling costs by up to 90% to produce pilot runs of 200 units in only two weeks.
“In Formlabs, we found a very good partner not only for selling the machine but also for supporting us in discovering the properties of these materials. This partnership helped me identify the possibility of starting this journey with the 3D printed molds,” said Cademartiri.
The new workflow will enable Unilever to bring better products to the market faster and drastically reduce the risks and costs associated with developing packaging.
“The big impact we have with the 3D printer is the possibility to have your dreams come true. Something that’s on your screen is in your hands in a couple of weeks. A real product, with a real bottle, with a real cap, and a real label,” said Cademartiri.
Do you have questions about using an SLA printer for blow molding or other engineering and manufacturing applications? Download our white paper for the detailed workflow, reach out to our solutions specialists, or request a free sample part printed in Rigid 10K Resin.