Composants robotiques imprimés en 3D pour les réparations en eaux profondes
Pour les secteurs maritimes qui opèrent sur ou sous l'eau, comme la pêche, l'aquaculture ou les parcs éoliens en mer, les choses se compliquent. Les problèmes liés à la chaîne d'approvisionnement, les réparations, la maintenance et les opérations quotidiennes sont rendus plus difficiles par un environnement en constante évolution et souvent inhospitalier.
L'impression 3D permet la fabrication de pièces étanches, complexes et personnalisées, avec des applications presque infinies. Les pièces étanches imprimées en 3D sont utilisées comme composants de moteurs, outils de recherche, pales d'hélices, éléments d'équipements de plongée en eaux profondes, etc. Les nouvelles idées ne manquent pas, mais pour qu'un produit soit performant, il faut aussi une bonne méthode de conception, des tests approfondis et des outils performants pour qu'il puisse être utilisé dans l'environnement hostile sous la surface de l'eau.
Southern Ocean Subsea (SoSub), un développeur et fabricant d'applications robotiques sous-marines, crée depuis des années des systèmes robotiques pour les opérations sous-marins. En collaboration avec le partenaire de Formlabs ThingLab, SoSub s'appuie sur une imprimante Form 3 et quatre Form 3L pour créer des systèmes robotiques complexes.
Kelsey Treloar, fondateur de SoSub, et Miles Lewis, ingénieur, ont réduit le coût et les délais de production du développement de solutions personnalisées telles que leurs véhicules sous-marins télécommandés (ROV). La fabrication de systèmes robotiques complexes et étanches comme les leurs serait quasiment impossible sans l'impression 3D. L'équipe a ainsi pu contourner les inconvénients de la fabrication traditionnelle, qui entravent généralement le succès des start-ups.
« Grâce à l'impression 3D, la fabrication ne représente plus un obstacle. La seule limite est notre propre imagination : nous devons trouver des solutions intéressantes à des problèmes épineux. La question n'est donc pas de savoir si c'est faisable, mais si nous pouvons trouver la solution. Ce qui est un privilège pour les ingénieurs modernes », explique M. Lewis.
Maintenance et adaptation au marché
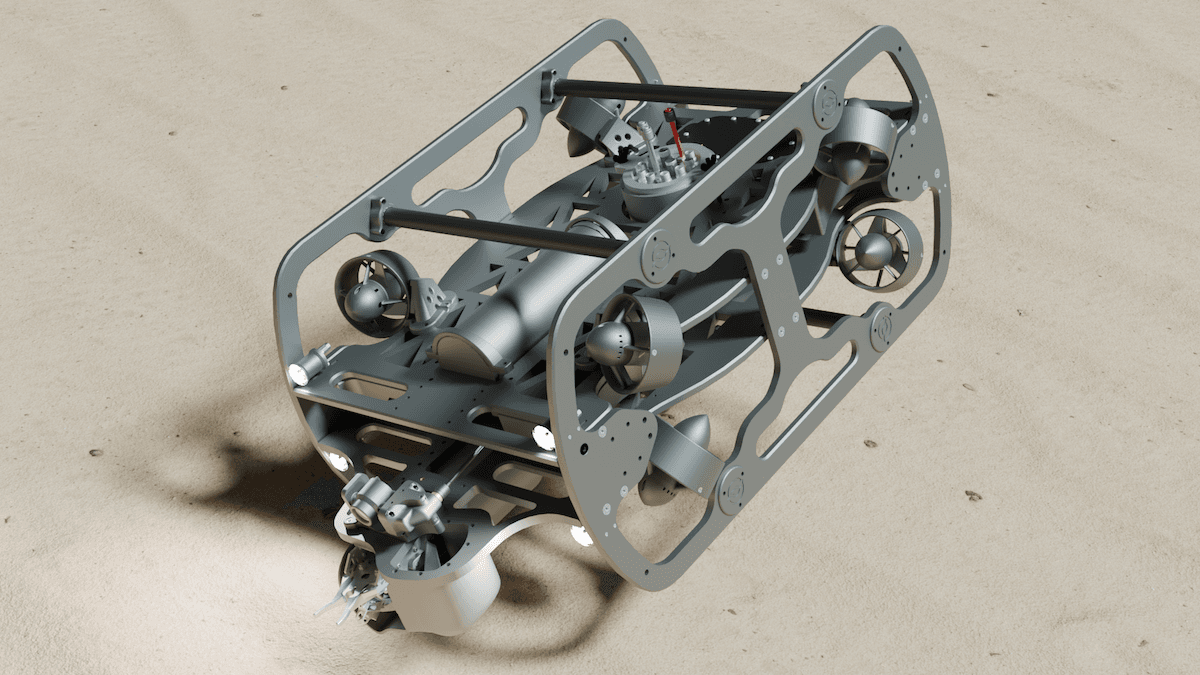
Le ROV de SoSub a d'abord été conçu comme une solution à un problème auquel M. Treloar a été confronté d'innombrables fois : le processus consistant à réparer les filets de pêche était fastidieux et pouvait être dangereux. Il devait y avoir une solution robotique.
M. Treloar ne s'est pas fixé pour objectif de développer des ROV et de concevoir de nouvelles technologies sous-marines. Initialement, SoSub était une entreprise de maintenance et de réparation d'équipements de pêche et de machines sous-marines. M. Treloar a constaté qu'ils étaient régulièrement appelés pour réparer des filets et des équipements de pêche industriels. Il s'agissait d'interventions exigeantes en main-d'œuvre, au cours desquelles des équipes de plongeurs devaient recoudre les filets à la main sous l'eau. Les tâches manuelles et répétitives comme celles-ci sont effectuées depuis des années par des robots sur terre, mais sous l'eau, ce type d'intervention est plus complexe et plus coûteux. Les solutions existantes peuvent coûter des centaines de milliers de dollars et sont généralement réservées à des expéditions de recherche bien financées.
M. Treloar a commencé à expérimenter : il s'est initié à la CAO et a cherché différents moyens de fabriquer les pièces étanches qu'il concevait. « Nous avons commencé à chercher des solutions de production peu coûteuses qui pourraient être rentables pour une entreprise comme la nôtre. D'abord avec les imprimantes 3D FDM , puis en explorant d'autres voies », explique M. Treloard.
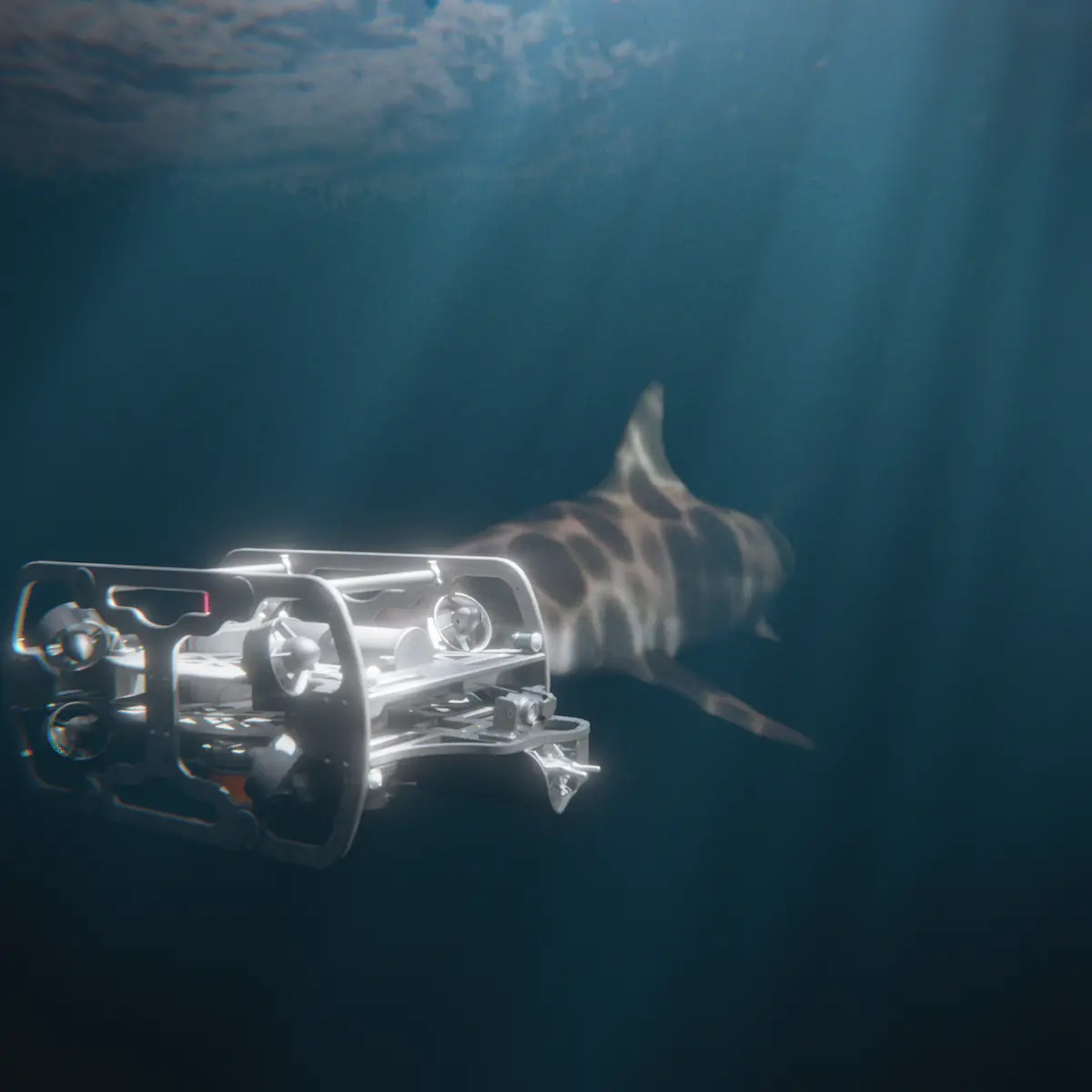
La réparation des filets peut être dangereuse. Les systèmes robotiques limitent les risques pour les plongeurs humains et l'impression 3D rend ces systèmes rentables pour les clients de SoSub dans le secteur de la pêche.
La bonne technologie
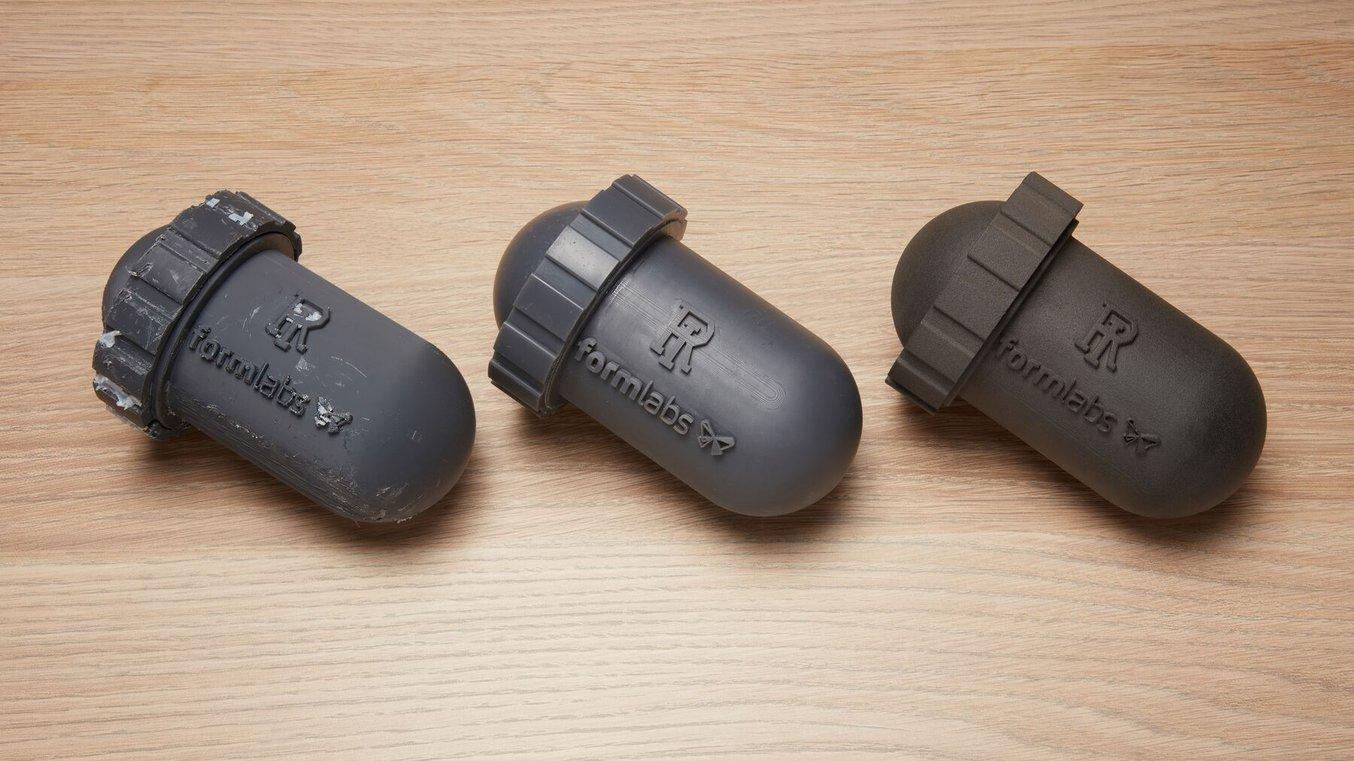
Les enceintes imprimées en 3D FDM (comme celle de gauche) ne sont pas étanches, car les pièces imprimées en 3D FDM présentent des interstices microscopiques entre les couches de filament.
D'emblée, la technologie du dépôt de fil fondu a posé des problèmes. Les imprimantes FDM ne peuvent pas créer de pièces étanches. En effet, des interstices microscopiques entre les couches, qui ne sont pas liées chimiquement, peuvent laisser pénétrer l'eau, surtout si la pression augmente avec la profondeur.
Heureusement, un collègue avait de l'expérience avec les imprimantes 3D SLA. « Il était fermement convaincu que l'impression à base de résine était suffisante, nous avons donc fait un test et cela a fonctionné. Je n'ai rien vu d'autre qui puisse le faire et nous n'aurions pas pu développer ces pièces d'une autre manière », déclare M. Treloar.
Depuis qu'elle s'est lancée dans l'impression 3D résine, l'entreprise SoSub a élargi son parc d'imprimantes 3D en acquérant quatre imprimantes SLA grand format de type Form 3L et une imprimante de bureau Form 3. « Les imprimantes ont jeté les bases qui nous ont permis de démarrer cette tâche », explique M. Lewis.
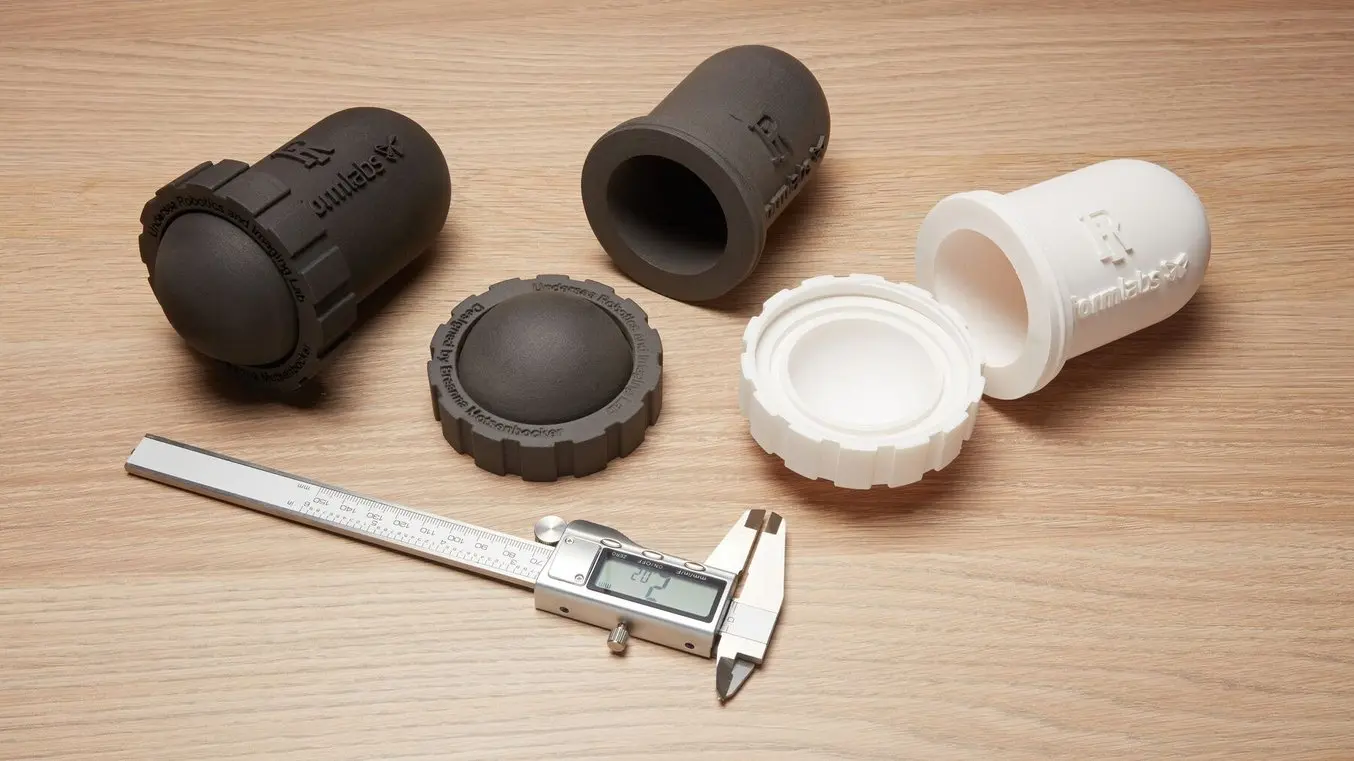
Impression 3D de boîtiers étanches et résultats des tests de pression
Dans ce livre blanc, nous fournissons les résultats des tests et des directives claires sur la façon d'imprimer en 3D des boîtiers étanches personnalisés à un prix abordable.
Composants sous-marins : relever le défi
Les applications robotiques sous-marines nécessitent des pièces qui résistent à des contraintes répétées, respectent des tolérances strictes et présentent une précision dimensionnelle élevée afin de pouvoir être intégrées dans des assemblages qui doivent être étanchéifiés par des joints toriques et ne doivent présenter aucun défaut d'uniformité, aucune bavure, aucune ligne ou aucun artefact d'impression. Les pièces qui correspondent à cette liste de spécifications sont traditionnellement usinées à partir de métal ou moulées par injection, mais la sous-traitance à des fournisseurs est coûteuse et peut prendre des semaines ou des mois.
L'impression 3D permet à M. Lewis et à M. Treloar de concevoir, prototyper et tester des pièces qui peuvent imiter les plastiques moulés par injection ou même les plastiques usinés.
« Si l'on regarde le secteur des ROV, la plupart des pièces sont usinées ou moulées par injection, ce qui implique des délais de production longs et des prix excessivement élevés. Comme il s'agit d'un marché de niche, les composants peuvent coûter des milliers de dollars. L'un des avantages concurrentiels de SoSub est que nous pouvons travailler très rapidement, mais aussi à moindre coût, grâce à l'impression 3D. »
Kelsey Treloar, fondateur et PDG de SoSub
Les matériaux Formlabs peuvent manipuler non seulement les surfaces lisses nécessaires à ces pièces finales, mais aussi la pression des opérations sous-marines. SoSub a évalué les enceintes imprimées en Rigid 10K Resin, Tough 2000 Resin, et Grey Resin pour leur étanchéité même à des centaines de mètres de profondeur. « Nous avons pris un petit serveur standard à 100 $ et imprimé un boîtier en 3D. Les résultats ont été nettement supérieurs à nos attentes et l'engin est descendu à 600 mètres de profondeur. Il est possible de fabriquer un actionneur de serveur sous-marin capable de descendre à 600 mètres en une demi-journée », explique M. Lewis. Une autre enceinte en Rigid 10K Resin a également réussi à dépasser les 1000 mètres de profondeur.
L'un des principaux avantages du flux de travail de Formlabs a été l'estimation des performances mécaniques dans le logiciel Fusion 360 d'Autodesk pour les résines Formlabs. « Avec les matériaux techniques Formlabs, ils publient les données pour l'analyse FEI pour la simulation. Nous ne pouvons pas faire cela avec d'autres matériaux. Si un client souhaite une estimation de la résistance de sa pièce, nous pouvons le faire et lui dire qu'il devrait être en mesure de manipuler cette pièce. Nous pourrons alors procéder aux essais nécessaires pour le confirmer », explique M. Lewis.
Ajouter de la complexité pour simplifier les choses
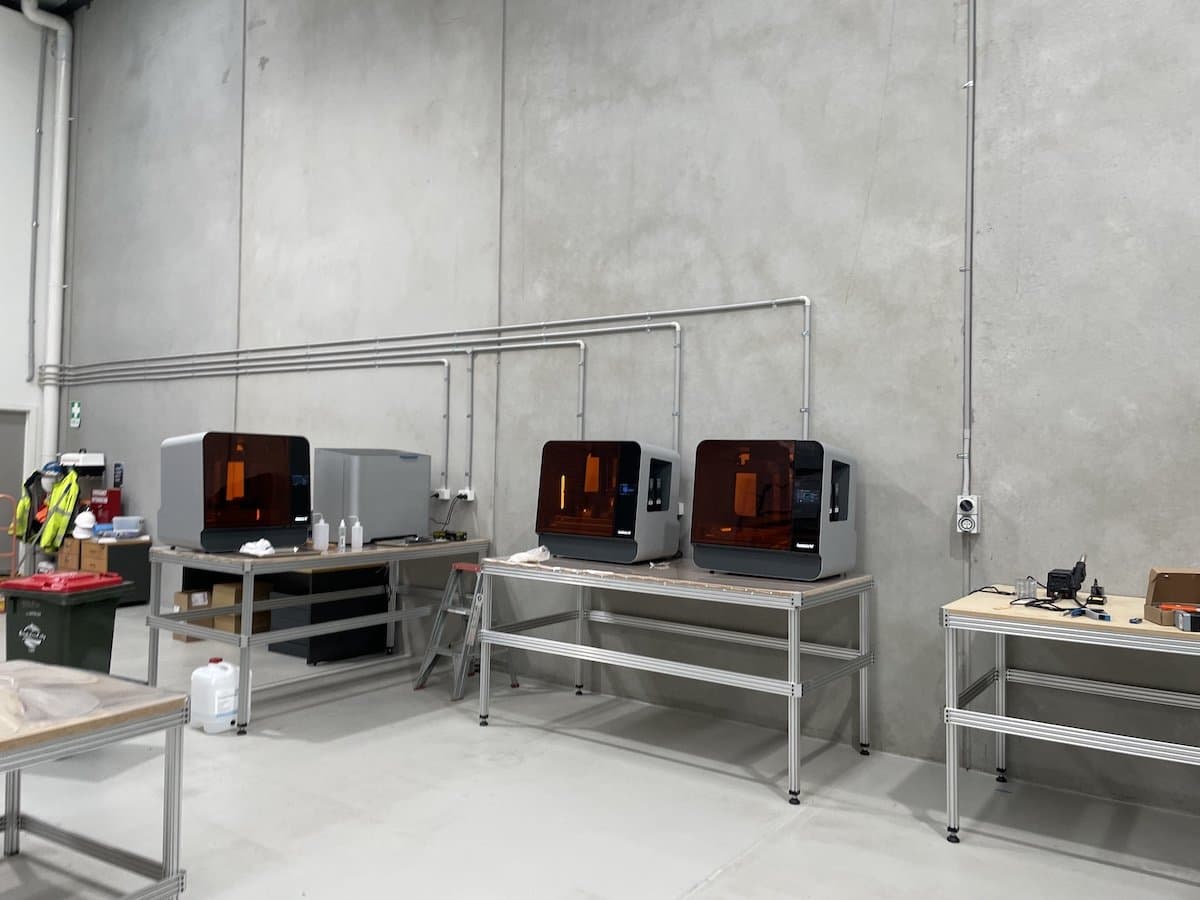
Les imprimantes 3D Form 3L de SoSub leur permettent de concevoir, de tester et de produire des pièces finales étanches et précises sur le plan dimensionnel.
Outre les coûts et les délais de production, SoSub crée des pièces qui ne peuvent pas être fabriquées de manière traditionnelle en raison de leur complexité, ce qui a influencé son approche de la création de nouvelles pièces. Afin de réduire le nombre de composants distincts dans un assemblage pour en faciliter la manipulation et l'exploitation, SoSub conçoit pour la fabrication additive. « Les pièces que l'on fabrique traditionnellement par usinage seraient totalement impossibles à réaliser avec de tels designs ou extrêmement coûteuses. Il faut donc complètement repenser la conception des pièces et les rendre aussi complexes que possible afin qu'elles puissent être imprimées en une seule pièce. Il suffit d'éliminer huit processus de fabrication, ce qui rend à la fois le montage et le processus de conception plus rapides et plus faciles », explique M. Lewis.
Cage à pieuvre : l'impression 3D de la conception à l'utilisation finale

Tough 2000 Resin est très résistante et offre une excellente précision dimensionnelle, ce qui la rend parfaite pour les boîtiers étanches de la partie principale de la cage à pieuvre.
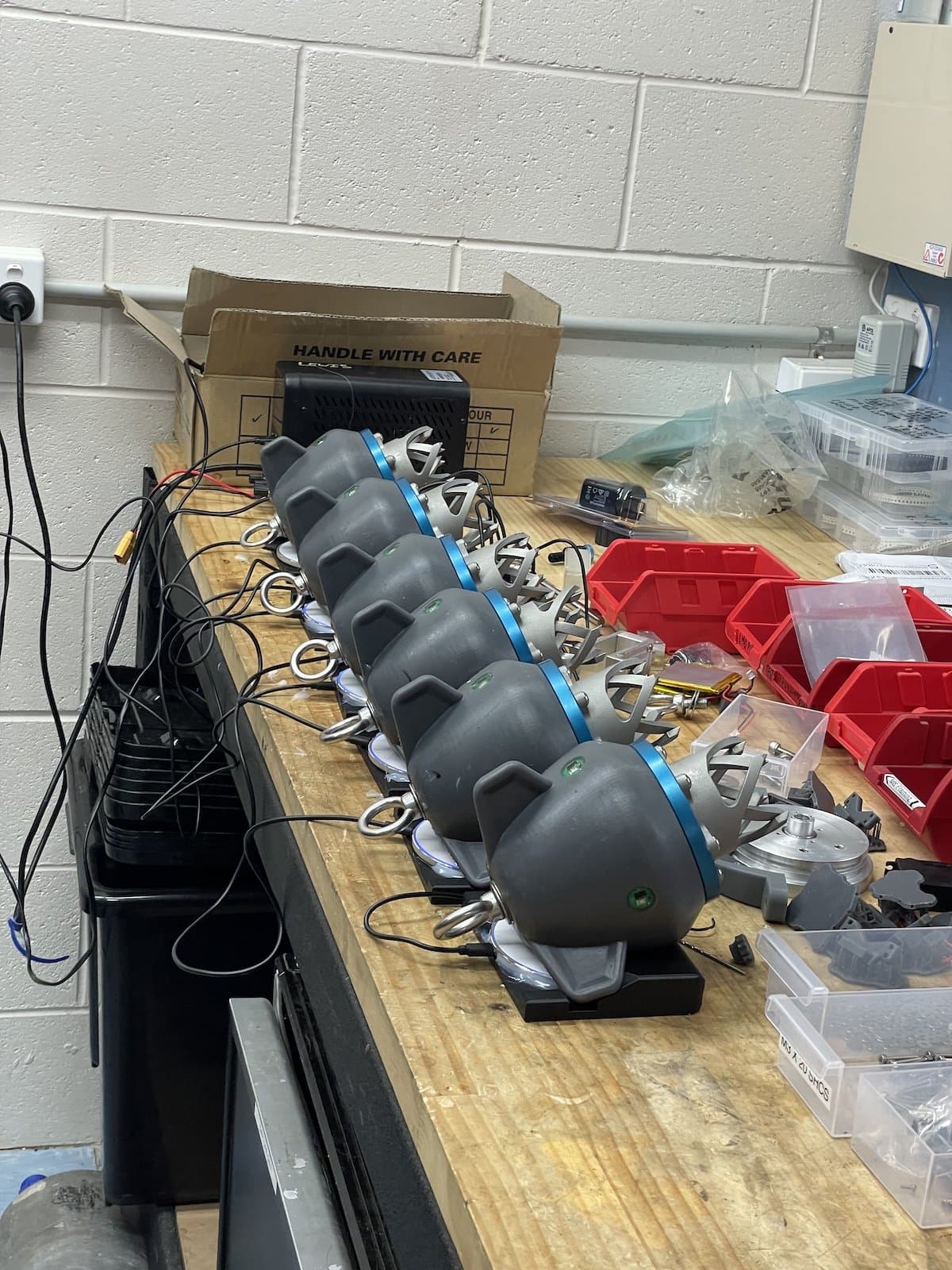
La cage assemblée se compose d'un boîtier imprimé en 3D sur la Form 3L avec Tough 2000 Resin et de « dents » imprimées en 3D pour la fixation au filet.
L'impression 3D a permis à SoSub de trouver des solutions créatives à des problèmes compliqués. L'équipe de SoSub a été appelée dans les fermes aquacoles en mer, près de Melbourne, pour développer un ROV destiné à une tâche très spécifique. Les grands filets de pêche doivent être étirés des bateaux et étendus dans l'eau, une tâche généralement accomplie par des plongeurs et qui exigeait beaucoup de main-d'œuvre et de travail répétitif. La difficulté consistait à concevoir un actionneur capable d'agir avec autant de dextérité que des mains humaines, alors que le filet flottait dans l'eau, et de s'y agripper suffisamment. La difficulté consistait à concevoir un actionneur qui agisse avec autant d'habileté que les mains humaines et qui maintienne suffisamment le filet flottant dans l'eau.
« En un mois et demi, nous sommes passés d'un concept très approximatif à un produit fini, en imprimant en 3D des prototypes de test des dents en Grey Resin et des prototypes du boîtier en Tough 2000 Resin. L'impression 3D nous donne la certitude que nous pouvons réellement créer quelque chose dans un délai court. Cela nous permet de prendre plus de risques en matière de conception », explique M. Treloar.
SoSub a livré huit ages à pieuvres entièrement fonctionnelles à la ferme en l'espace de deux mois. La conception finale a des dents imprimées en 3D en métal, mais conserve le boîtier en Tough 2000 Resin. « Grey Resin permet d'obtenir de bons détails, tandis que Tough 2000 Resin est un matériau assez résistant, pour les cas où l'on souhaite obtenir des détails similaires à ceux de Grey Resin, mais avec plus de ténacité », explique M. Lewis.
Plans numériques pour l'avenir
SoSub ne fait que commencer à répondre à la demande écrasante de machines personnalisables dans les secteurs maritimes. À l'avenir, ils envisagent d'aller au-delà des solutions complètes. « À terme, nous voulons atteindre des centaines d'unités par an, et nous utiliserons toujours l'impression 3D. Nous pouvons demander à nos clients d'acheter eux-mêmes des imprimantes et de leur vendre ensuite les fichiers, de sorte que tout peut être fabriqué sur place », explique M. Treloar. Pour l'instant, la clientèle de SoSub pour les solutions entièrement imprimées est encore en pleine croissance, mais M. Treloar et M. Lewis sont convaincus que l'impression 3D peut s'adapter à de nouveaux projets plus compliqués. « Nous utilisons nos imprimantes pour toutes sortes de choses différentes. Non seulement pour l'usage initial pour lequel nous avons acheté les imprimantes, mais aussi pour créer de toutes nouvelles idées », explique M. Treloar.
Pour découvrir comment imprimer en 3D des enceintes étanches, téléchargez notre livre blanc. Pour explorer la Form 3L, visitez notre page.