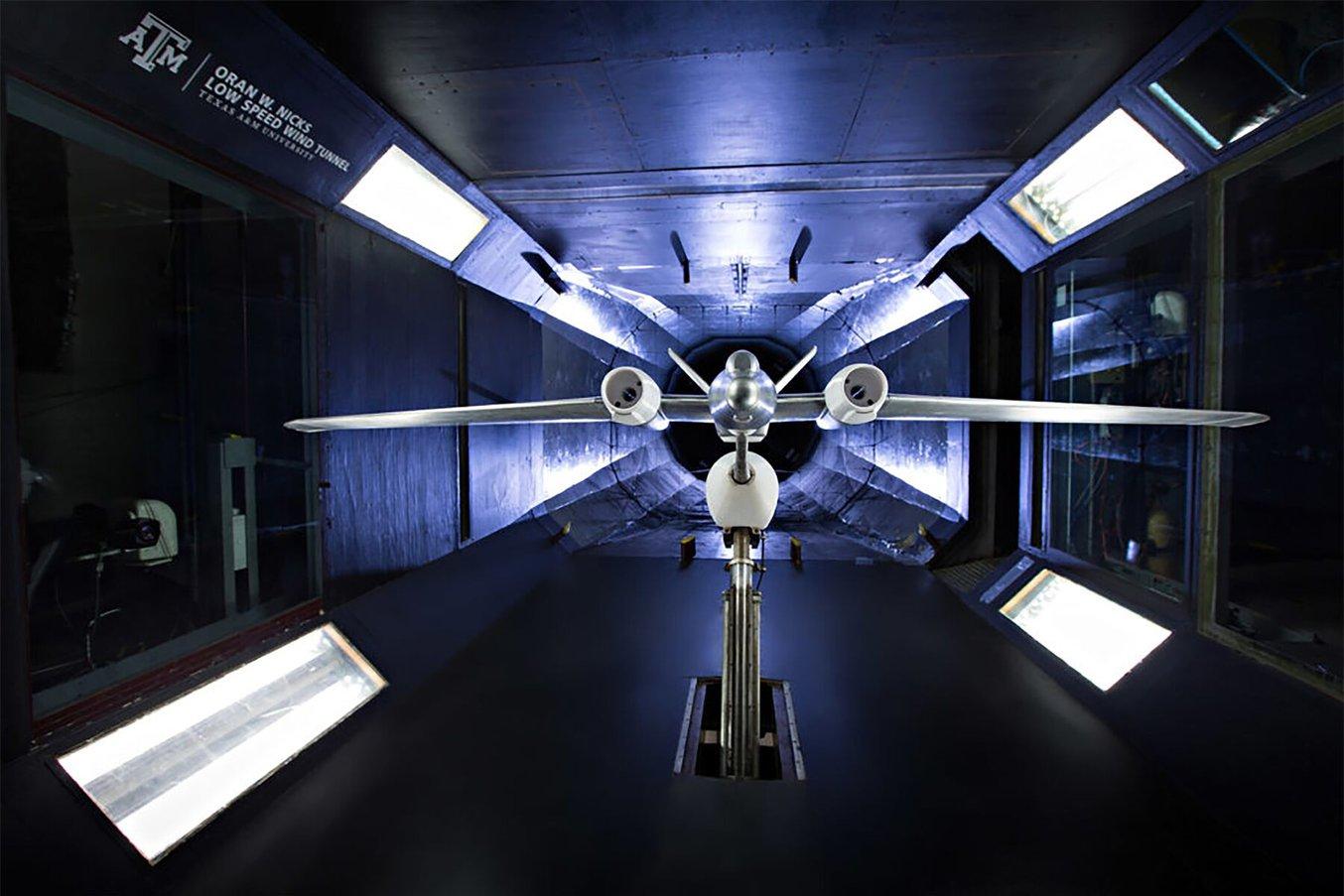
La fabrication additive, également appelée impression 3D, permet de nombreuses applications dans l'industrie aérospatiale, de la conception à la fabrication et bien plus.
L'industrie aérospatiale a été l'une des premières à adopter l'impression 3D, ou fabrication additive, lorsqu'elle a été inventée. En effet, de nombreux équipementiers, fournisseurs et agences gouvernementales utilisent l'impression 3D depuis des décennies déjà, et les dernières générations d'avions commerciaux volent avec plus de 1000 pièces imprimées en 3D.
Cependant, les imprimantes 3D industrielles traditionnelles représentent un coût phénoménal pour toutes les organisations, à l'exception des plus grandes et des mieux financées. Au cours des dix dernières années, nous avons assisté à une baisse spectaculaire du prix des imprimantes 3D, même les plus performantes, et à des innovations dans le domaine de la science des matériaux qui diversifient encore les applications possibles. Lorsque leur prix est abordable, les imprimantes 3D peuvent désormais être utilisées par de plus petites organisations et dans de nouvelles branches de grandes organisations, au lieu d'être réservées à des ateliers de prototypage centralisés. En mettant la technologie additive à la portée d'un plus grand nombre d'utilisateurs finaux, les imprimantes 3D Formlabs permettent à davantage d'ingénieurs et de chercheurs en aérospatiale de repousser leurs limites.
Continuez la lecture pour découvrir neuf façons essentielles dont l'impression 3D dynamise l'innovation dans toute l'industrie aérospatiale, de la conception à la fabrication et bien plus encore.
L'impression 3D pour le développement de produits aérospatiaux
1. Des prototypes rapides imprimés en 3D pour des essais fonctionnels de fusées
Gravity Industries met au point des combinaisons à réaction dignes d'un film de science-fiction. Leurs combinaisons à réaction sont destinées à être utilisées pour la recherche et le sauvetage, lorsqu'un hélicoptère ne peut atterrir en toute sécurité. L'utilisation de plusieurs types de technologies d'impression 3D a accéléré le processus de prototypage et de test, y compris certains tests pour lesquels la résine photopolymère thermodurcissable était le meilleur choix possible.
Sam Rogers, pilote d'essai et concepteur principal, a utilisé des pièces imprimées en Clear Resin sur la Form 3 pour développer la conception d'un allumeur de moteur de fusée refroidi par vortex. Le matériau transparent convenait parfaitement à l'environnement d'essai, de sorte que M. Rogers pouvait observer les schémas de combustion à l'intérieur du banc d'essai.
Lors des essais de conception, M. Rogers a conçu la chambre de manière modulaire, afin de pouvoir combiner différentes versions de la chambre et de la buse. Grâce à un « bouclier d'oxygène tourbillonnant » qui éloigne la chaleur la plus élevée des parois de la chambre, les pièces en résine ont chacune pu résister pendant plusieurs secondes. Cette durée était suffisante, car chaque tir d'essai ne devait durer que le temps d'observer le schéma d'allumage.
Si M. Rogers avait fait fabriquer ses dizaines de conceptions différentes en métal, cela aurait coûté énormément d'argent. Au lieu de cela, comme les essais étaient courts et que les pièces présentaient des coûts de matériaux très bas, il a opté pour une conception très performante avec des dépenses et un délai de mise en œuvre minimaux.
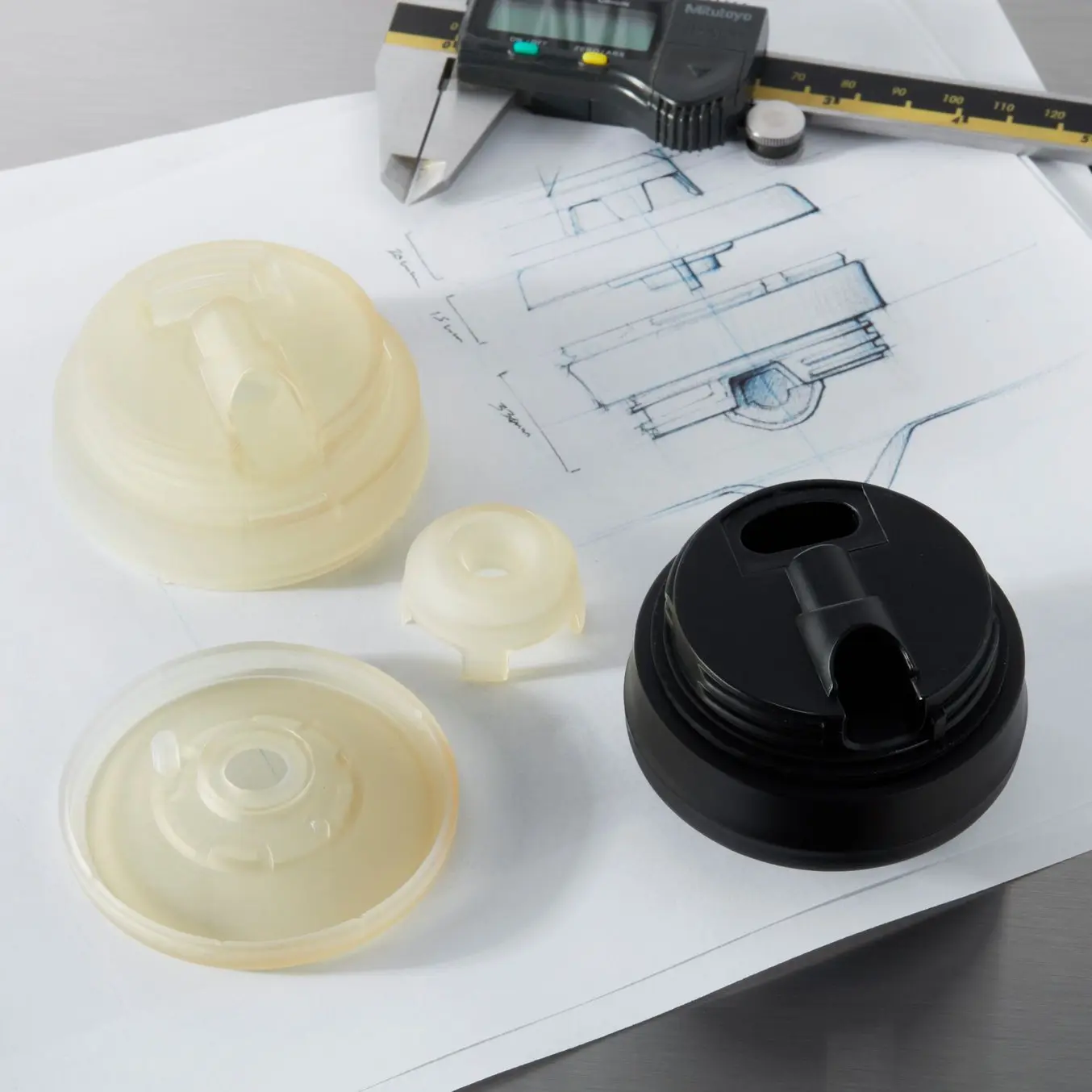
Guide de prototypage rapide pour le développement de produits
Dans ce guide, vous découvrirez comment le prototypage rapide s'intègre au processus de développement de produits, ses applications, et les outils de prototypage rapide dont les équipes de développement de produits disposent aujourd'hui.
2. Créer des pièces de fusée complexes grâce à l'impression 3D
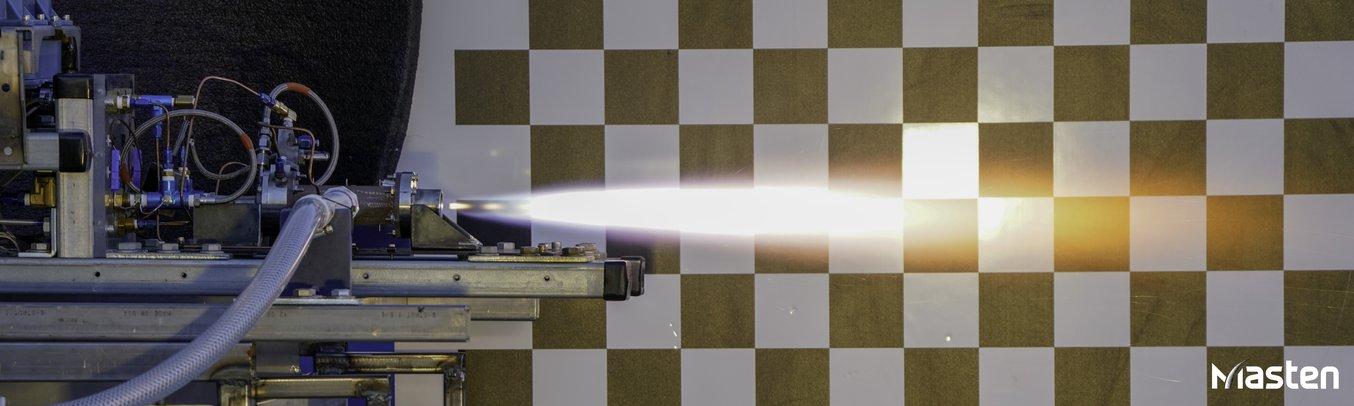
Masten Space Systems produit des pièces complexes de fusées par impression 3D.
Masten Space Systems est spécialisé dans les fusées à décollage et atterrissage verticaux. L'équipe de Masten a commencé à imprimer en 3D des moteurs de fusée en 2014. Elle a commencé par de petits propulseurs d'essai, et a ensuite fabriqué un propulseur avec une poussée de 11 339 kg en 2016. Ils utilisent à la fois des plastiques et des métaux. Selon Kimberly Devore, ingénieure de recherche et d'essai chez Masten, l'entreprise a utilisé à la fois l'usinage traditionnel et l'impression 3D pour produire des moteurs de fusée. Masten utilise encore la fabrication traditionnelle pour ses moteurs plus anciens, mais elle utilise aujourd'hui l'impression 3D en raison de sa flexibilité de conception et de la rapidité de la production.
« Ce qui est bien avec [l'impression 3D], c'est qu'il est possible de modéliser le produit exactement comme on le souhaite. Il n'est pas nécessaire de réaliser le même nombre d'itérations que dans le cas d'un usinage traditionnel. En fait, vous pouvez simplement concevoir la pièce comme vous le souhaitez », a déclaré M. Devore. « Souvent, avec l'usinage traditionnel, vous devez effectuer des opérations assez basiques. Chaque fonction supplémentaire que vous ajoutez représente un coût supplémentaire. »
Avec l'impression 3D, ajouter de la complexité pour améliorer les performances ne coûte pas plus cher : vous pouvez laisser libre cours à votre imagination. Comme il est relativement rapide et peu coûteux de réaliser plusieurs pièces, vous pouvez essayer de nouvelles choses. « La possibilité d'itérer rapidement change la donne. »
3. Prototyper des outils aérospatiaux grâce à l'impression 3D
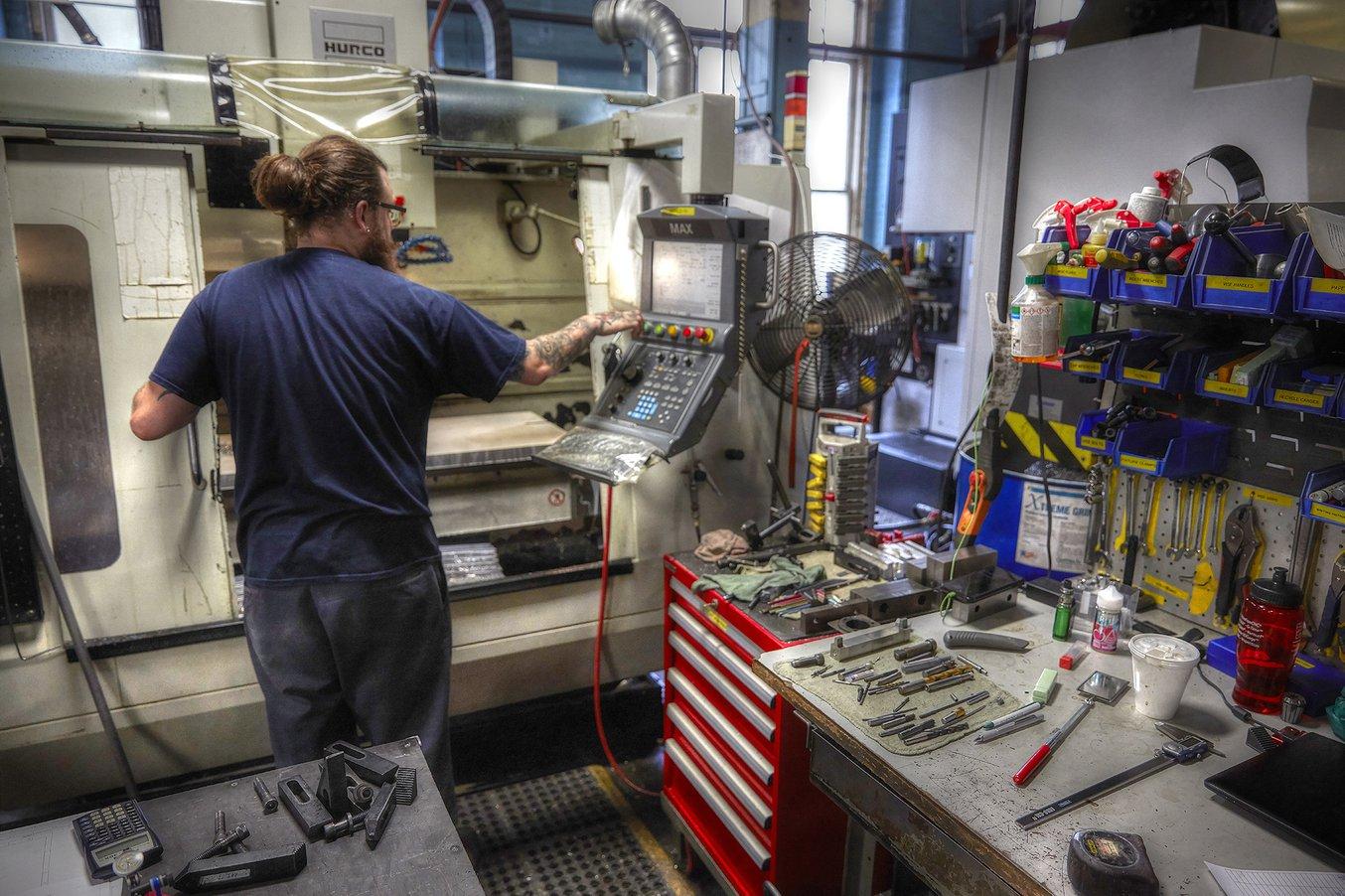
Il faut du temps et des compétences pour programmer les machines CNC. S'il n'est pas nécessaire que la pièce soit en métal, l'impression 3D peut être pratique pour fabriquer des prototypes et des outils de production, bien plus vite et à moindre coût.
A&M Tool and Design produit des pièces et des machines sur mesure pour l'aérospatiale, l'optique et la robotique. L'atelier s'est modernisé au cours du temps. Il s'est équipé de nouvelles machines (notamment des imprimantes 3D) en plus des machines traditionnelles à la fiabilité éprouvée. Ryan Little, ingénieur mécanicien chez A&M Tool, a cherché quelle imprimante 3D conviendrait le mieux à leurs besoins, et il a choisi les imprimantes 3D Formlabs.
Pour le prototypage, l'atelier a commencé à utiliser des pièces 3D pour tester l'ajustement et la fonction. Grâce à l’impression 3D, Ryan Little et l’équipe ont pu fabriquer des pièces plus rapidement, toute la journée. En paramétrant des impressions pour la nuit, ils pouvaient utiliser les pièces dès le lendemain. L’impression est particulièrement utile pour des formes coûteuses et longues à usiner sur une machine CNC.
« L’imprimante est presque comme un outil auxiliaire de la CAO », fait remarquer Ryan Little. « Nous faisons des tonnes de prototypes pour différent types d'outillage. Si nous n'avions pas la Form 2, beaucoup d'entre eux resteraient à l'état de modèles CAO avant que nous soyons prêts à usiner, et il y aurait toujours quelque chose qui ne serait jamais fabriqué ou conçu parce que ce ne serait pas pratique. »
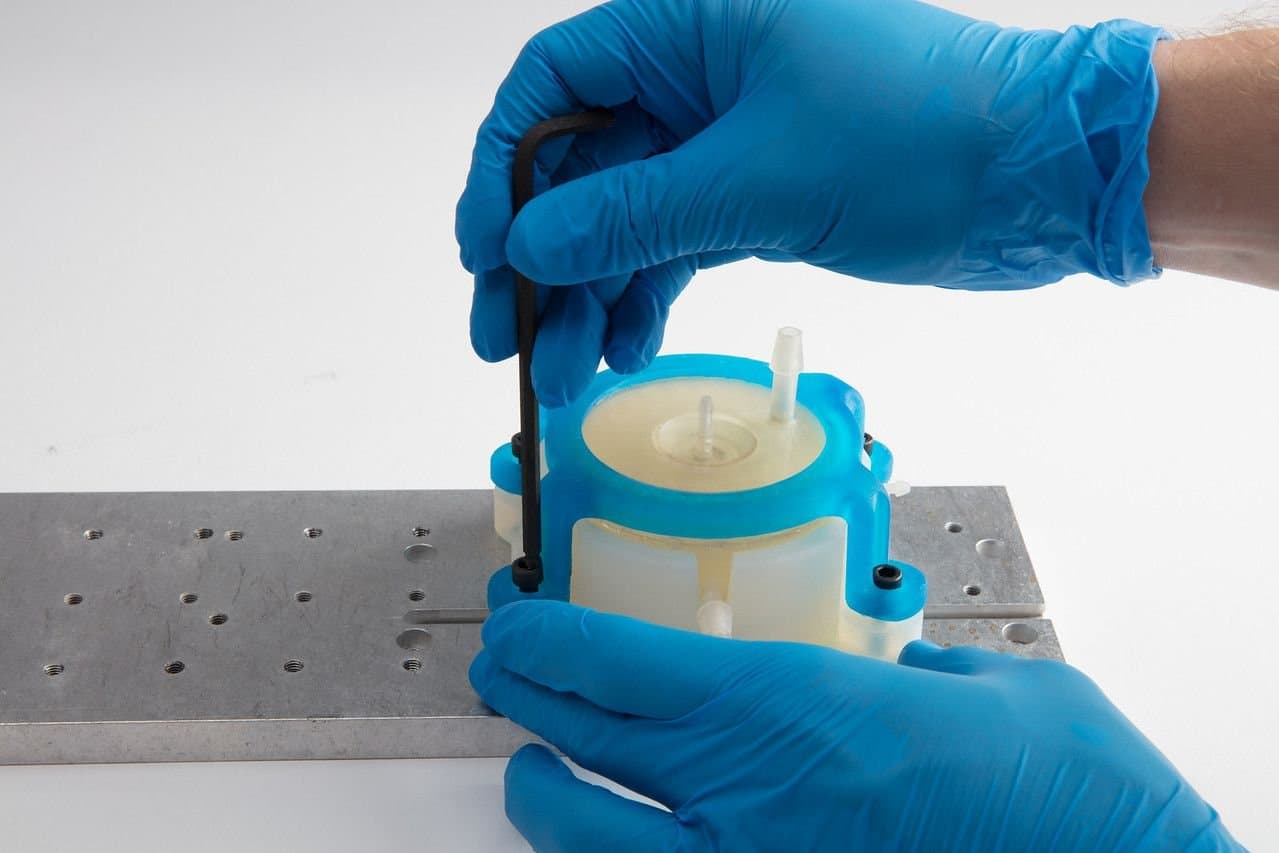
Conception de gabarits et de fixations par impression 3D
Il est essentiel pour les fabricants de maximiser la vitesse de production tout en maintenant une haute qualité des pièces. Les gabarits et les fixations sont utilisés pour rendre les processus de fabrication et d’assemblage plus simples, plus fiables et plus efficaces, réduire la durée de cycle et améliorer la sécurité des travailleurs.
L'impression 3D pour la fabrication aérospatiale
4. Économiser de l'argent grâce à de l'outillage personnalisé imprimé en 3D
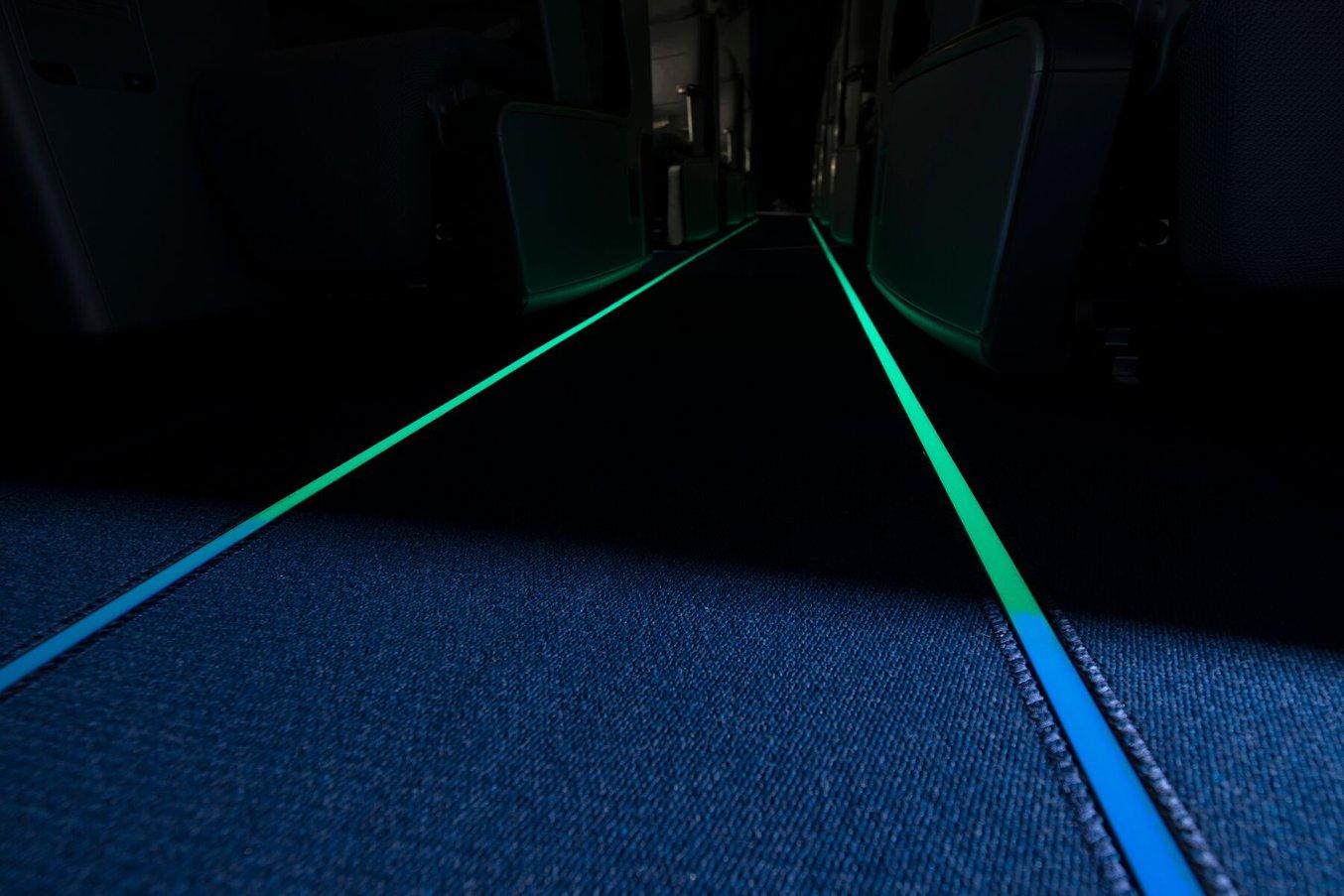
Lufthansa Technik a imprimé en 3D la buse d'extrusion pour produire ces marquages luminescents de voies d'évacuation.
Lufthansa Technik est l’un des plus grands prestataires au monde de services de maintenance, réparation et révision (MRO) pour l’aviation. La société propose des marquages de voies d’évacuation exclusifs GuideU, conçus pour une installation après-vente dans les cabines des avions. Ces marquages au sol innovants sont photoluminescents : ils sont composés de pigments de couleur auto-éclairants qui sont rechargés par l’éclairage normal de la cabine et brillent dans l’obscurité en cas de coupure d’électricité.
Avant la mise en production, différents outillages et procédés de fabrication ont été testés. L’impression 3D de buses de filage personnalisées s’est révélée être la méthode de fabrication la plus rentable et la plus flexible. « Théoriquement, nous aurions aussi pu mouler nos pièces par injection. Mais nous n’aurions jamais eu autant de flexibilité dans la forme et l’ajustement de la buse. C’est pour moi l’un des grands avantages de l’impression 3D", explique Ulrich Zarth, ingénieur de projet chez Guide U.
Cet outil de production a été imprimé sur la Form 3L en collaboration avec myprintoo, partenaire de Formlabs. La grande surface de la plateforme de fabrication de la Form 3L a permis d’imprimer 72 buses en une seule fois. Plusieurs matériaux ont été testés, avant que le choix ne se porte sur Clear Resin. Non seulement cette résine offre la stabilité et la qualité de surface requises, mais elle permet également à Lufthansa Technik de constamment optimiser son processus de production.
« Si vous voulez obtenir rapidement des formes précises, je vous recommande chaudement l'impression 3D, surtout si vous travaillez dans le secteur du plastique.
Ulrich Zarth, ingénieur de projet, Lufthansa Technik AG
Ulrich Zarth et son équipe ont gagné énormément de temps et d’argent en imprimant en 3D et en interne ce petit composant. Ils ont également évité d’imposer des quantités minimales de commande élevées et sont restés beaucoup plus flexibles dans l’optimisation de leur processus par rapport aux méthodes de fabrication traditionnelles.
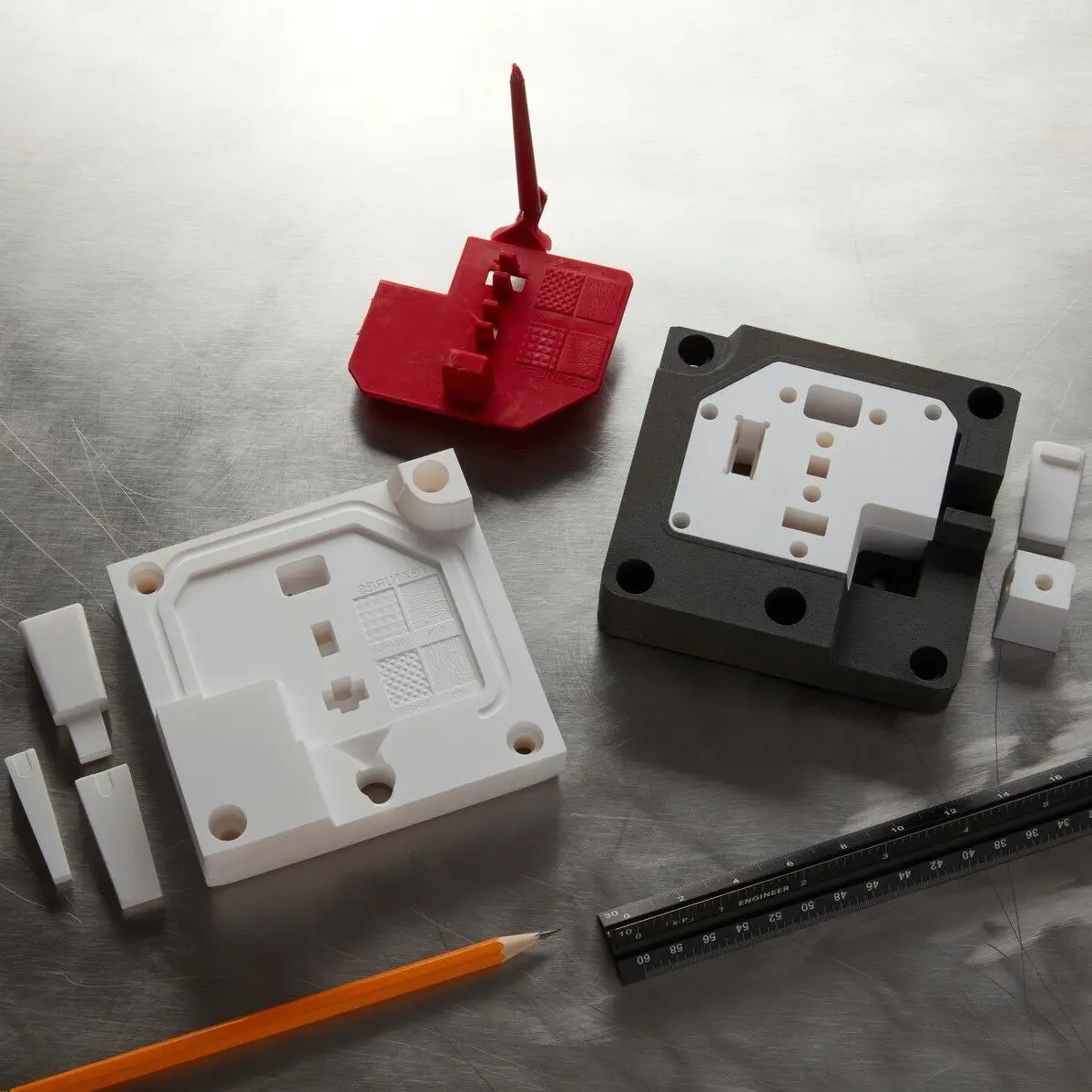
Guide de l'outillage rapide
Dans ce livre blanc, apprenez comment combiner l'outillage rapide imprimé en 3D avec des procédés de fabrication traditionnels tels que le moulage par injection, le formage sous vide ou la fonderie.
5. Gagner du temps dans la fabrication aérospatiale grâce aux gabarits de masquage imprimés en 3D
L’Integrated Manufacturing Group de l’AMRC collabore avec des partenaires industriels pour fusionner des technologies avancées et développer des systèmes intégrés. Le groupe de recherche a travaillé sur un projet pour Airbus, premier fabricant européen en aérospatiale, impliquant le perçage et l’usinage haute tolérance de composants en fibre de carbone, en aluminium et en titane. « Après avoir percé un trou, avant de passer au suivant, nous devions couvrir le premier pour éviter que tout élément issu du perçage contamine le second trou », a expliqué George Sleath, ingénieur de projet à l’AMRC.
Tout d’abord, l’équipe a essayé d’utiliser une pièce en aluminium dotée d’un petit joint torique en caoutchouc, mais cette solution ne permettait pas de résoudre le problème de façon satisfaisante. Et deux difficultés supplémentaires devaient être résolues : plusieurs tailles de bouchon différentes étaient nécessaires, et l’équipe ne disposait que de dix jours pour produire les 500 bouchons attendus.
Avec un délai de fabrication aussi court pour des produits sur mesure, l’impression 3D était l’une des rares options de production envisageables. À ce moment-là, M. Sleath n’était pas sûr des capacités internes de l’AMRC. Il a demandé des devis à trois centres d’impression externes, mais ils étaient bien trop élevés.
« J’ai ensuite parlé avec Mark Cocking de notre groupe Conception et Prototypage et je lui ai demandé quelles quantités il était possible de fabriquer en interne. J’ai attendu sa réponse durant 24 h mais lorsqu’elle est arrivée, il m’a dit "Nous en avons déjà imprimé la moitié." 250 de ces bouchons de perçage imprimés en 24 h, c’était une vitesse de production incroyable », a déclaré M. Sleath.
Finalement, M. Cocking a réussi à imprimer tous les composants en deux jours, et les bouchons ont fonctionné exactement comme prévu sur le terrain. « Les retours que j’ai reçus de la part des opérateurs chargés d’installer les bouchons sont fantastiques. La grande majorité des pièces a fourni exactement le résultat attendu et aucune ne s’est cassée durant l’opération », a déclaré M. Sleath.
6. Des pièces aérospatiales imprimées en 3D et plaquées
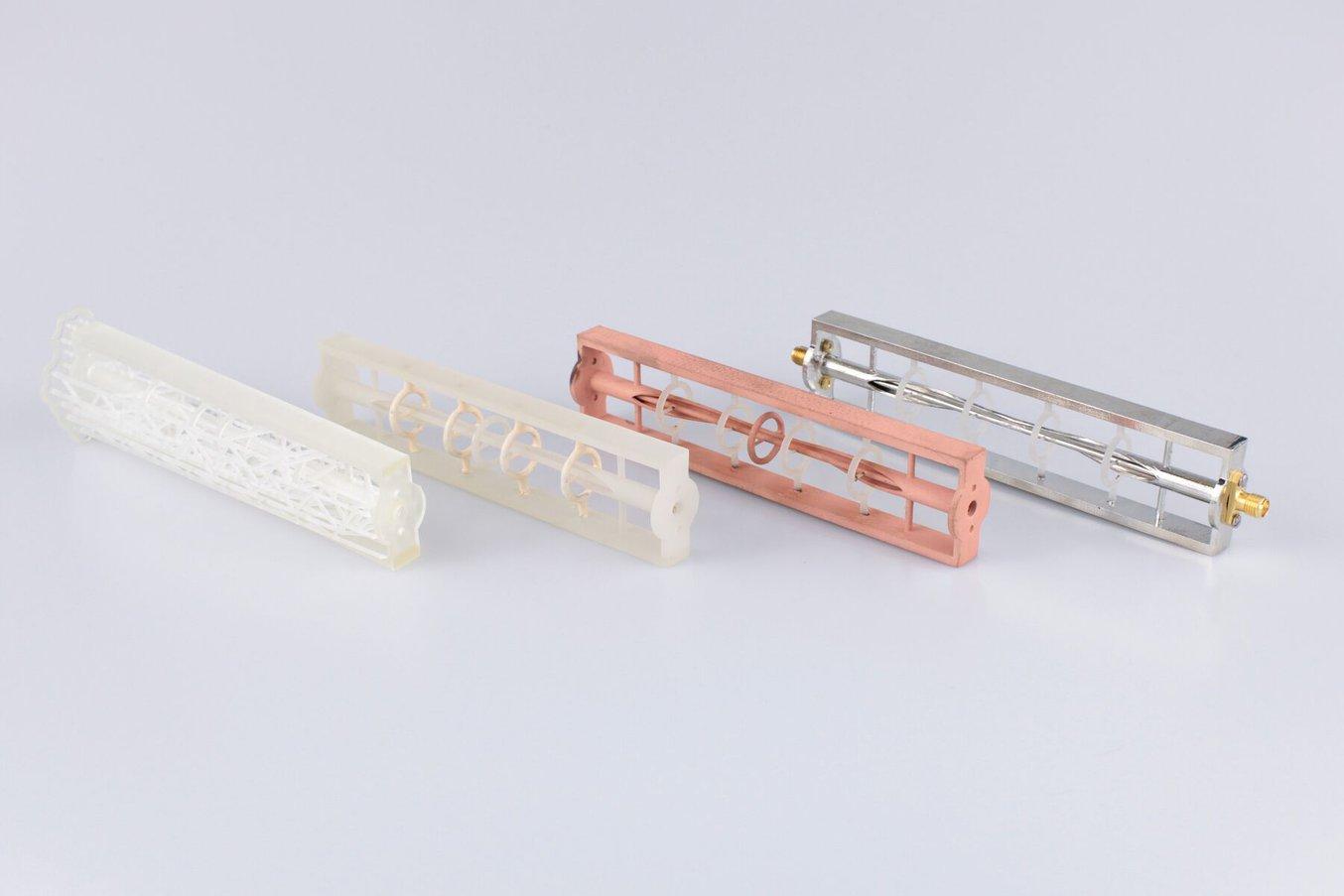
L'impression 3D de pièces d'utilisation finale permet à Elliptika de créer de nouveaux modèles d'antennes plus rapidement et d'économiser de l'argent dans le processus.
L’entreprise Elliptika s’est spécialisée dans la conception et le développement de produits et de solutions RF (radiofréquences) et microondes. Elle conçoit des filtres et des antennes sur mesure, utilisés pour la recherche et le développement dans l’automobile, la défense, la médecine et l’éducation. Les concepteurs Gwendal Cochet et Alexandre Manchec doivent réaliser des géométries complexes, maintenir les coûts à un niveau bas et fournir des conceptions rapidement. Pour répondre à ces exigences poussées, l’équipe devait chercher au-delà des techniques de fabrication traditionnelles.
L’équipe d’Elliptika a travaillé avec différents procédés de fabrication additive et a déterminé que c’est l’impression 3D par stéréolithographie qui se combine le mieux à la galvanoplastie, en raison de la surface lisse des pièces imprimées. "Après impression 3D de la pièce, nous devons supprimer les supports, nettoyer la surface et la polymériser. Ensuite, la pièce est soumise à un procédé chimique qui dépose une fine couche de cuivre à sa surface (environ 3 µm). Finalement, la pièce peut recevoir un traitement de finition de surface, comme le dépôt d’une couche plus épaisse d’étain. »
Elliptika a rentabilisé son imprimante 3D Formlabs en seulement deux tâches d’impression. La fabrication d’une pièce par un sous-traitant coûte environ 3000 €. Le coût de la main-d’œuvre et du matériel pour imprimer en 3D et plaquer par galvanoplastie une antenne en interne est de 20 € seulement.
L’équipe a également accéléré son rythme de travail. Avec les procédés de production traditionnels, la fabrication d’une antenne peut prendre jusqu’à trois mois. « Grâce à l’impression 3D en interne, nous obtenons nos pièces de travail en deux jours. Une journée pour l’impression, une journée pour la galvanoplastie, et elles sont prêtes à fonctionner. C’est donc vraiment, vraiment plus court », a déclaré M. Cochet.
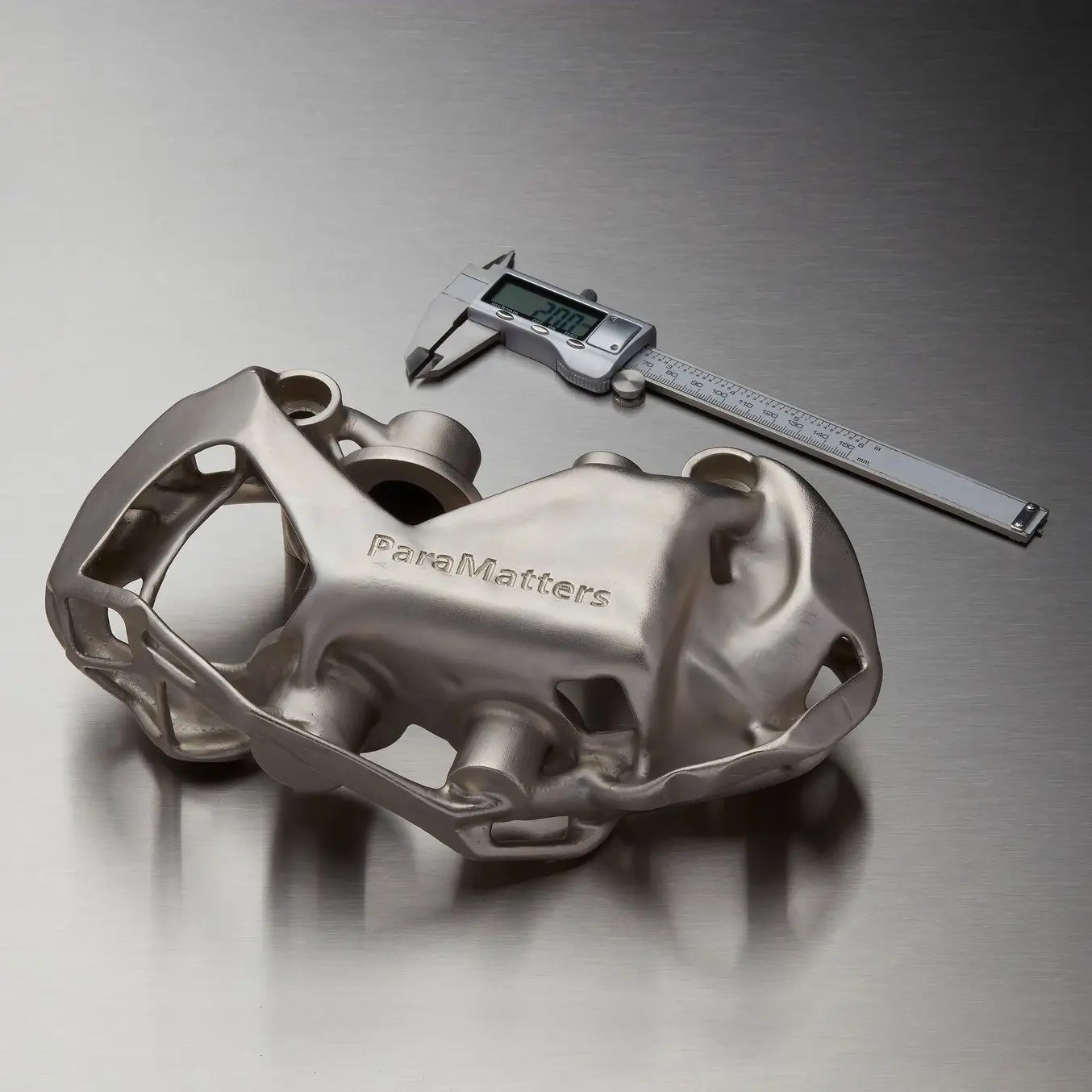
La résistance du métal : stratégies et exemples d'utilisation pour la galvanoplastie de pièces SLA
Lisez la suite pour savoir comment les ingénieurs ajoutent du métal aux impressions 3D en résine et à quelles applications surprenantes les pièces métalliques hybrides peuvent donner accès, permettant notamment (mais pas seulement) d'augmenter la résistance et la durabilité.
L'impression 3D dans la recherche et l'enseignement
7. Tester des pièces imprimées en 3D dans l'espace
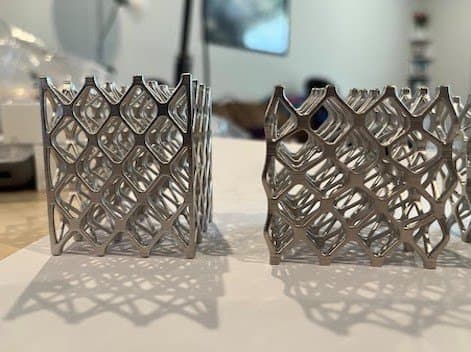
Échantillon de compression de treillis en Rigid 10K Resin avant le test (à gauche) et après le test (à droite), la charge venant du haut.
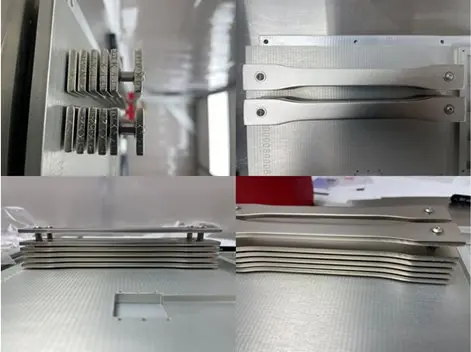
Des pièces envoyées à l'ISS, imprimées en 3D avec Rigid 10K Resin et plaquées.
Les chercheurs de la NASA étudient les performances des pièces SLA plaquées dans l'espace. Des ingénieurs du Goddard Space Flight Center de la NASA ont conçu des supports qui ont été imprimés en 3D sur des imprimantes Formlabs, galvanisés et envoyés dans l'espace à bord d'une mission commerciale de ravitaillement de SpaceX (CRS-25) vers la station spatiale internationale (ISS) au cours de l'été 2022.
À l'aide de la plateforme d'essai de la station spatiale internationale Materials International Space Station Experiment (MISSE-16) d'Alpha Space, les échantillons seront exposés à l'environnement externe de la station spatiale et seront ensuite renvoyés sur terre pour d'autres tests. Les résultats devraient indiquer de quelle manière la NASA et éventuellement d'autres fabricants aérospatiaux pourraient utiliser la fabrication additive et la galvanoplastie pour fabriquer leurs futurs produits.
8. Des pièces imprimées en 3D pour les essais en soufflerie
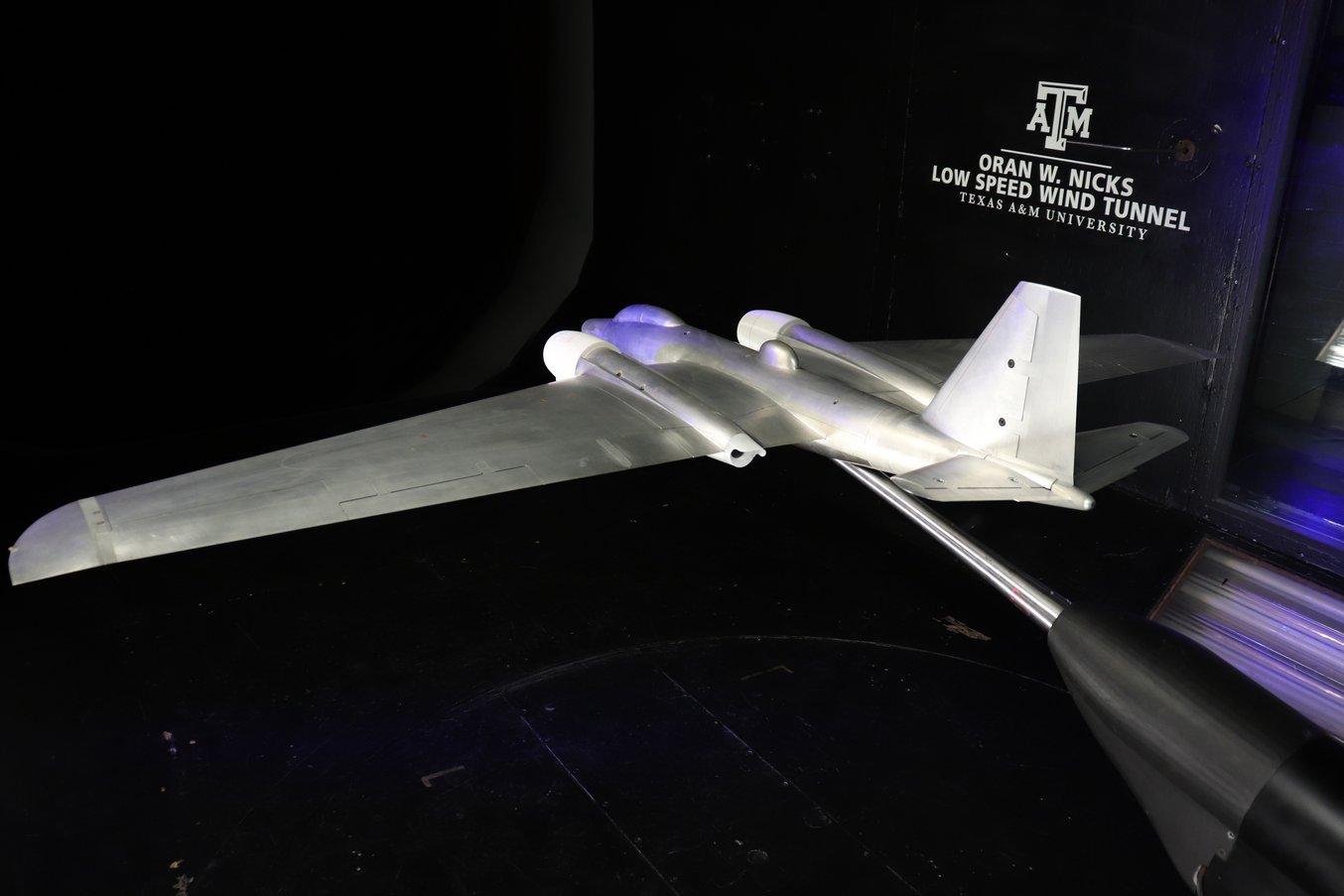
Des composants haute performance imprimés en 3D peuvent être montés sur des modèles réduits d'avions dans une soufflerie.
Des professeurs et des étudiants du monde entier utilisent les imprimantes 3D Formlabs pour réaliser des essais en soufflerie afin d'étayer leurs recherches.
La soufflerie à basse vitesse Oran W. Nicks de Texas A&M effectue des essais pour toute une série de projets. Lisa Brown, responsable et ingénieure à la soufflerie Texas A&M, aide les chercheurs à élaborer leurs plans d'essai, à concevoir les modèles et à créer le code qui leur permet de collecter les données. Son équipe utilise l'impression 3D pour créer des modèles réduits afin de tester différents objets.
Mme Brown se souvient d'un projet dans lequel l'équipe a étudié une pale d'hélicoptère et a intégré l'impression 3D dans le test. « Si nous allons assez vite et que les pales battent assez rapidement, des ondes de choc se produisent sur le bord des pales. C'est exactement ce que nous ne voulons pas qu'il se produise avec un hélicoptère. Nous avons donc pu voir ces ondes de choc se produire dans notre soufflerie à faible vitesse, ce qui était vraiment fascinant », a déclaré M. Brown. « Nous avions un petit insert imprimé sur ce bord avec des capteurs à l'intérieur. Le modèle entier était donc une aile en aluminium avec ce petit insert que nous pouvions remplacer. »
Pour savoir quel matériau Brown a choisi et pourquoi, lisez notre étude de cas.
De l'autre côté de l'océan Atlantique, la soufflerie de l'Institut de technologie de Karlsruhe (KIT) teste également des pièces imprimées en 3D. Le doctorant Lars von Deyn étudie les méthodes de prévision des écoulements turbulents. Ses travaux pourraient permettre d'orienter les choix en matière de matériaux et de conception afin de réduire les frottements.
Pour créer ses pièces d'essai, M. von Deyn s'est tourné vers l'impression 3D. "J'aimerais examiner des structures qui sont très difficiles à produire à l'aide de procédés d'usinage," explique-t-il. Il a choisi la Form 3L parce que son grand volume d'impression lui permettait de couvrir la zone d'essai de la soufflerie avec moins de pièces individuelles, et donc moins d'interruptions dans le modèle.
Découvrez les résultats de ses expériences dans notre étude de cas.
9. Former la prochaine génération d'ingénieurs grâce à l'impression 3D
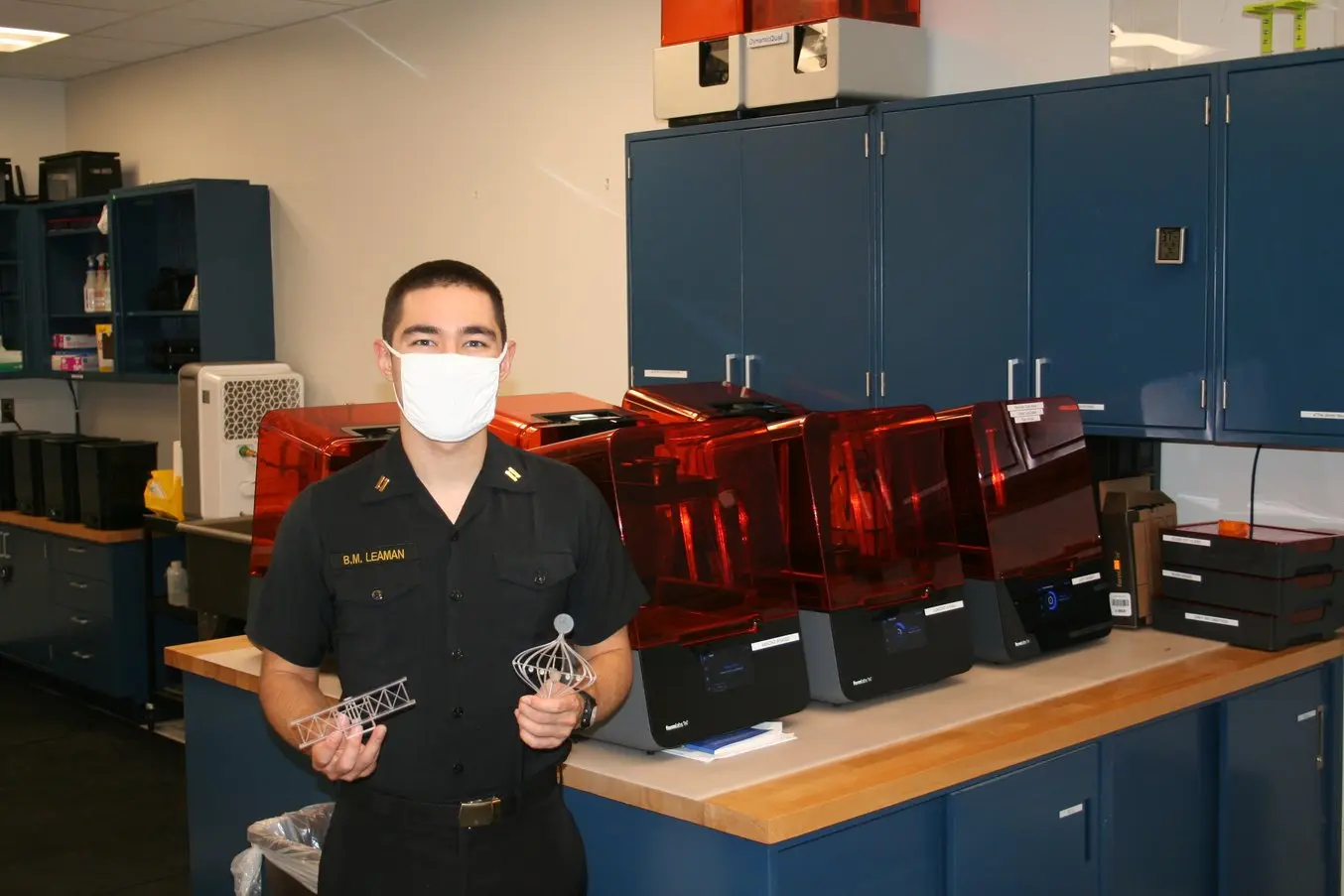
L'aspirant 1/C Ben Leaman, étudiant en architecture navale à l'USNA, montre ses impressions primées réalisées avec des imprimantes Formlabs Form 3 lors d'un concours AM Olympics en 2021.
L'Académie navale des États-Unis (USNA) prépare de jeunes hommes et femmes à devenir des officiers professionnels dans la marine et le corps des Marines des États-Unis. Le capitaine Brad Baker, professeur associé à l'USNA, s'est rendu compte que le rythme d'apprentissage de ses étudiants en ingénierie était entravé par le manque d'accès aux outils de fabrication. Même si un atelier d'usinage était mis à la disposition des étudiants pour leurs travaux de fin d'études, chaque individu ou équipe n'était en mesure de réaliser que trois ou quatre itérations au cours d'une année.
Le capitaine Baker n'a pas été le premier professeur du campus à proposer aux étudiants d'utiliser des imprimantes 3D pour leurs cours, mais en créant le MakerSpaceUSNA, il a rassemblé toutes les capacités de conception et de fabrication en un seul lieu centralisé. N'ayant au départ que quelques imprimantes à dépôt de fil fondu (FDM), il a peu à peu intégré ces machines dans le programme d'ingénierie mécanique et les a mises à la disposition des étudiants pour leurs projets de fin d'études.
Lorsque les étudiants entrent dans le cursus d'ingénierie, ils apprennent d'abord à utiliser un logiciel CAO, puis à faire fonctionner des imprimantes FDM, avant de passer aux imprimantes stéréolithographiques (SLA) et à frittage sélectif par laser (SLS). À présent, ils se familiarisent même avec le scan 3D et peuvent réaliser des projets complets de rétro-ingénierie en utilisant simultanément tous les outils dont ils ont appris à se servir.
Le MakerSpaceUSNA met à disposition des imprimantes FDM, SLA et SLS fiables et de haute qualité. Ainsi, chaque étudiant peut faire l'expérience de plusieurs technologies d'impression 3D. L'enseignement pratique et l'apprentissage par l'échec prônés par le capitaine Baker permettent aux étudiants ingénieurs de mieux se préparer à une carrière dans la marine américaine, et à bien plus encore.
Quelle est la prochaine étape pour l'impression 3D dans l'aérospatiale ?
Avec des technologies additives plus puissantes et plus accessibles que jamais, l'industrie est prête à recevoir des contributions plus innovantes que jamais. Il est difficile de dire si les plus grandes percées des 5 à 10 prochaines années viendront des équipementiers, des fournisseurs, des agences publiques, des startups ou des universités. Mais comme l'impression 3D n'a jamais fait autant d'adeptes qu'aujourd'hui, ces innovations ne devraient pas tarder.
À mesure que l'industrie aérospatiale prend conscience des avantages de l'impression 3D et que la technologie et la gamme de matériaux disponibles deviennent de plus en plus polyvalentes, la technologie additive continuera à remodeler la façon dont nous construisons et entretenons les avions et les engins spatiaux.