Fabrication d’attaches d’organe de préhension complexes pour un robot de transfert
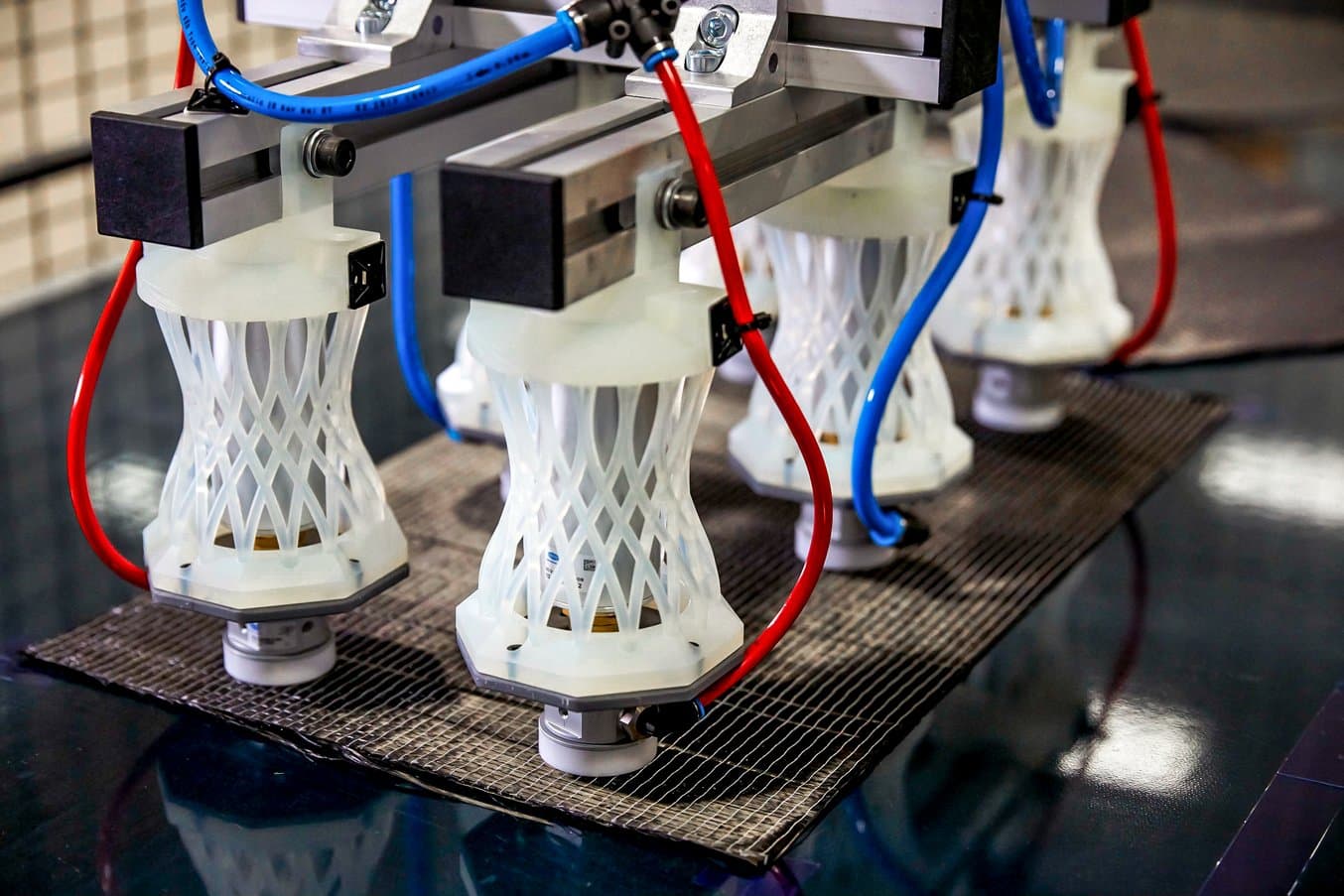
La fibre de verre et les matériaux en fibre de carbone sont de plus en plus utilisés dans l’aérospatiale, la marine, le secteur automobile et d’autres domaines à valeur élevée car ils fournissent une résistance élevée et un poids léger, mais ils posent également de nombreux défis de fabrication. Le Centre des Composites du Advanced Manufacturing Research Centre (AMRC) de l’université de Sheffield mène des recherches en utilisant des méthodes de pointe pour relever ces défis.
Pour l’un des projets en cours, les chercheurs explorent le déplacement automatique de feuilles de fibres de carbone, avec une grande exactitude et à haute vitesse, à l’aide d’un robot de transfert. Toutefois, au bout d’une longue période d’utilisation, les attaches en L qui maintenaient les organes de préhension pneumatiques du robot ont commencé à se courber sur les articulations, ce qui a entraîné des défaillances et a obligé les chercheurs à rechercher une nouvelle solution.
Matthew Williams, technicien en composites sur ce projet, évoque les défis de conception qu’il a dû relever lors de la création d’un composant élastique sur mesure et le succès de l’équipe qui a réussi à fabriquer cinq modèles de ce design complexe en quelques jours seulement grâce à l’impression 3D.
Regardez notre interview de Matthew Williams, technicien en composites, pour découvrir le robot de transfert en action.
Williams a travaillé avec la station de fabrication additive en accès libre de l’AMRC pour fabriquer les pièces dont ils avaient besoin. Lisez notre étude de cas pour découvrir comment l’accès libre à l’impression 3D aide des centaines d’ingénieurs sur l’ensemble du site.
Importance de l’exactitude dans la fabrication de composites
Les matériaux composites tirent leur force de la manière dont les paquets de fibres sont tissés et disposés dans les pièces. Cela permet aux ingénieurs d’optimiser soigneusement le design selon les effets attendus d’une contrainte sur un composant, mais cela fait aussi de la fabrication des composites un processus de travail très complexe.
La disposition de feuilles de fibres de carbone est généralement un processus manuel, mais l’interaction humaine implique des variations, car les feuilles peuvent être déformées ou ne pas être correctement en place. Quelques millimètres de décalage par rapport à l’alignement suffisent à donner des pièces défectueuses et à gaspiller un matériau onéreux.
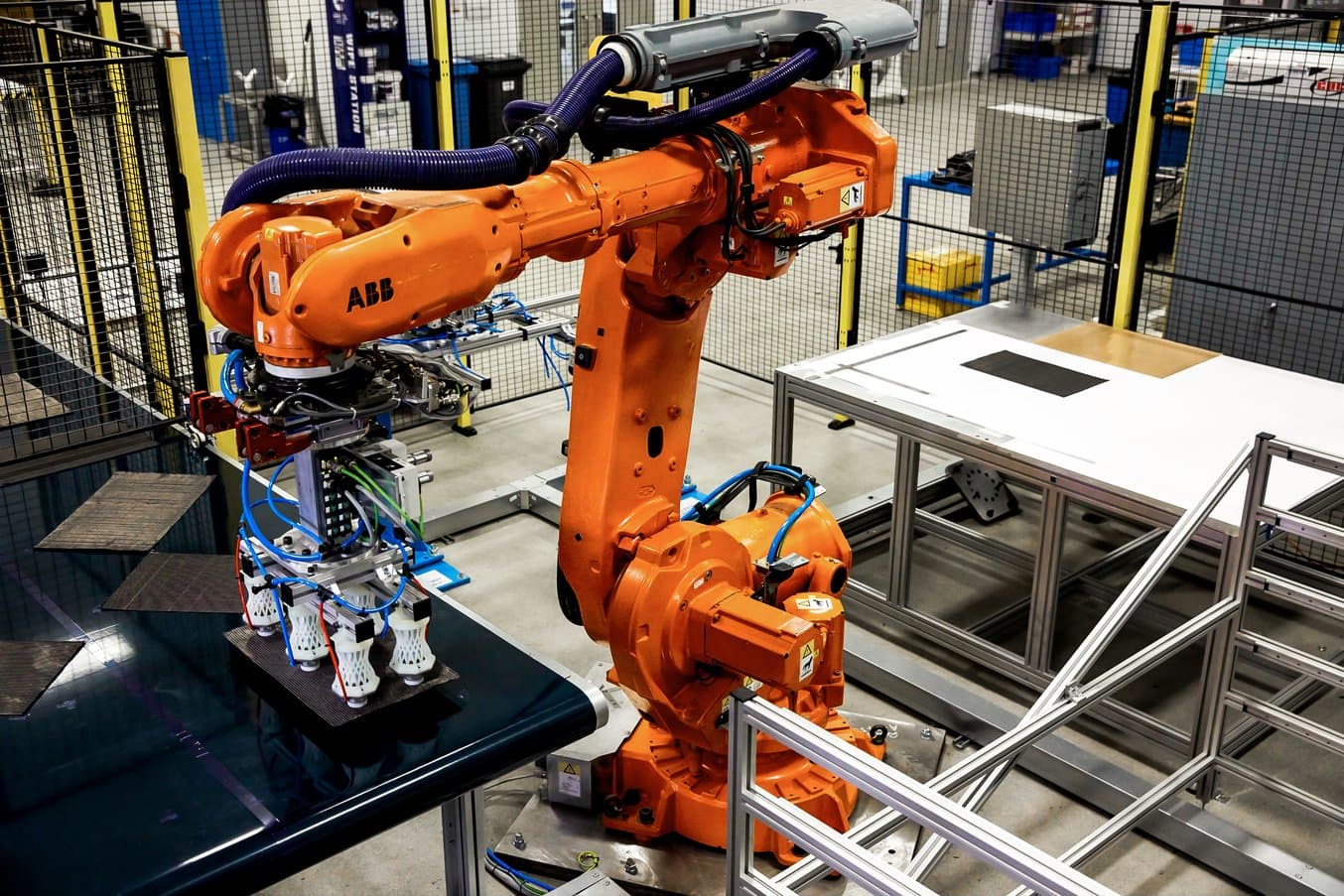
Avec une cellule de robot de transfert conçue pour créer un processus automatisé, les chercheurs tentent de réduire le gaspillage de matériaux et d’augmenter la vitesse et l’exactitude du processus. Les feuilles composites prédécoupées entrent dans la cellule sur un tapis roulant. Elles sont ensuite saisies par les six organes de préhension pneumatiques d’un robot ABB 5 axes qui déplace ensuite les feuilles et les dépose exactement les unes au-dessus des autres sur une table de la cellule.
Les attaches initialement montées sur le robot pour le maintien des organes de préhension sont des attaches en L en aluminium fixées sur le flanc de l’effecteur du robot. Cependant, étant donné que les différents éléments d’équipement de la cellule ne sont pas parfaitement à niveau, au bout d’une période d’utilisation prolongée, les attaches commencent à se courber autour de l’articulation du L. Avec le temps, cette courbure s’accentue tant que l’organe de préhension n’arrive plus à saisir les feuilles sur le tapis roulant.
D’une simple attache en L à un design complexe
La conception d’un composant présentant exactement le degré d’élasticité requis s’est avérée un défi assez complexe : Williams a dû revoir son concept cinq fois.
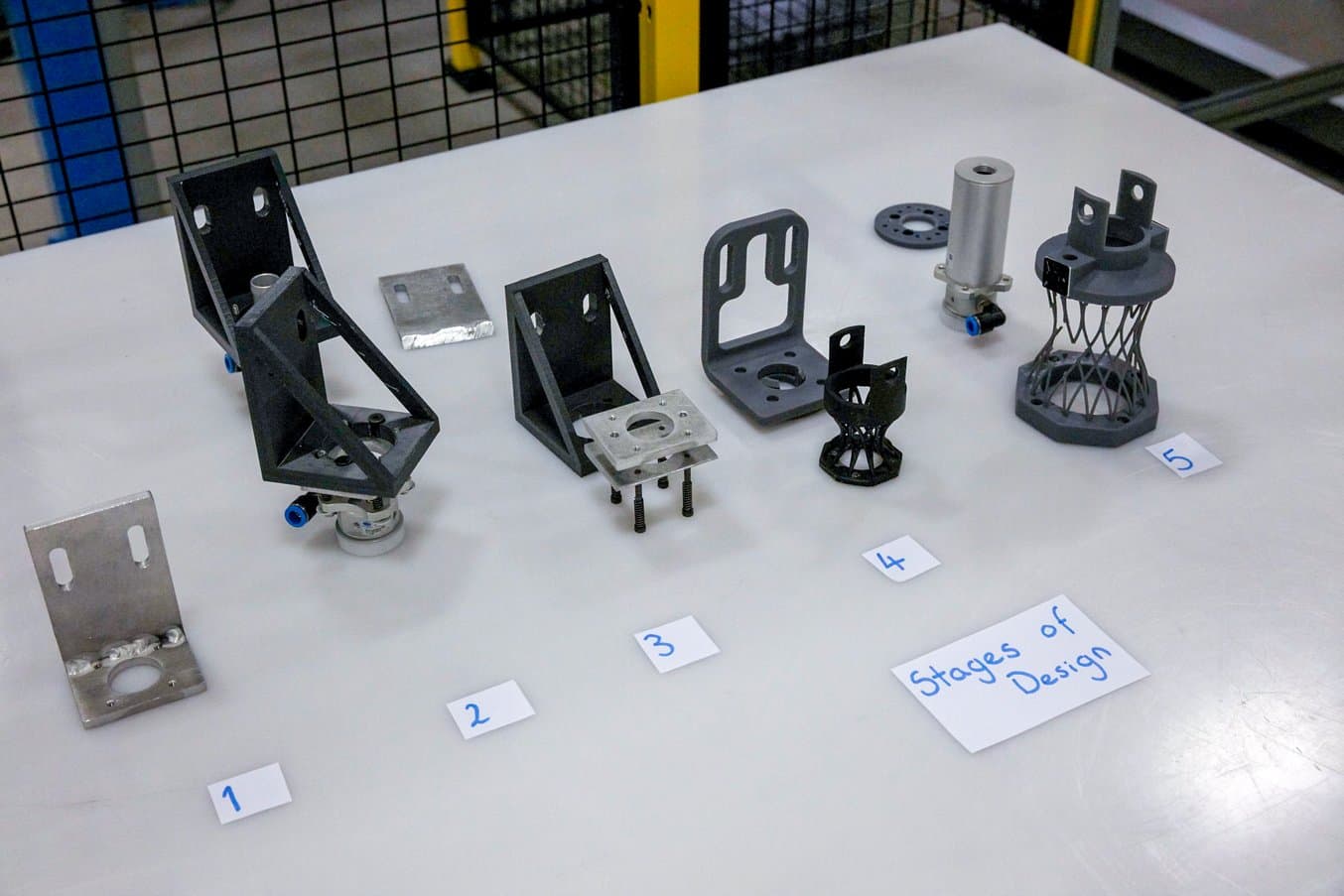
« J’ai commencé par une attache en L en aluminium qui était juste constituée de deux plaques pointées par soudage. Cette pièce ayant été soudée, une fois qu’elle se plie, elle ne reprend pas vraiment sa forme, elle reste pliée et déformée. Je suis donc passé au plastique qui, lui, reprend sa forme après la contrainte. Mais ce matériau était beaucoup plus flexible que l’aluminium et [les organes de préhension] ont dispersé les fibres sur la table. Ainsi, nous avions aggravé le problème plutôt que de l’améliorer, » a ajouté Williams.
Le chercheur a ensuite décidé de passer à un nouveau design. Plutôt que de travailler sur le côté de l’attache, les organes de préhension pneumatiques sont maintenant situés sous l’attache. Lorsqu’une contrainte est exercée sur le dessous de l’attache, elle ne plie pas mais se comprime comme un ressort. Au fur et à mesure de la progression des recherches, Williams a découvert que les organes de préhension produisaient un bruit trop important pour un environnement de travail sûr. Il devait monter un silencieux sur les organes de préhension, ce qui exigeait une attache plus grande pour accueillir le silencieux.
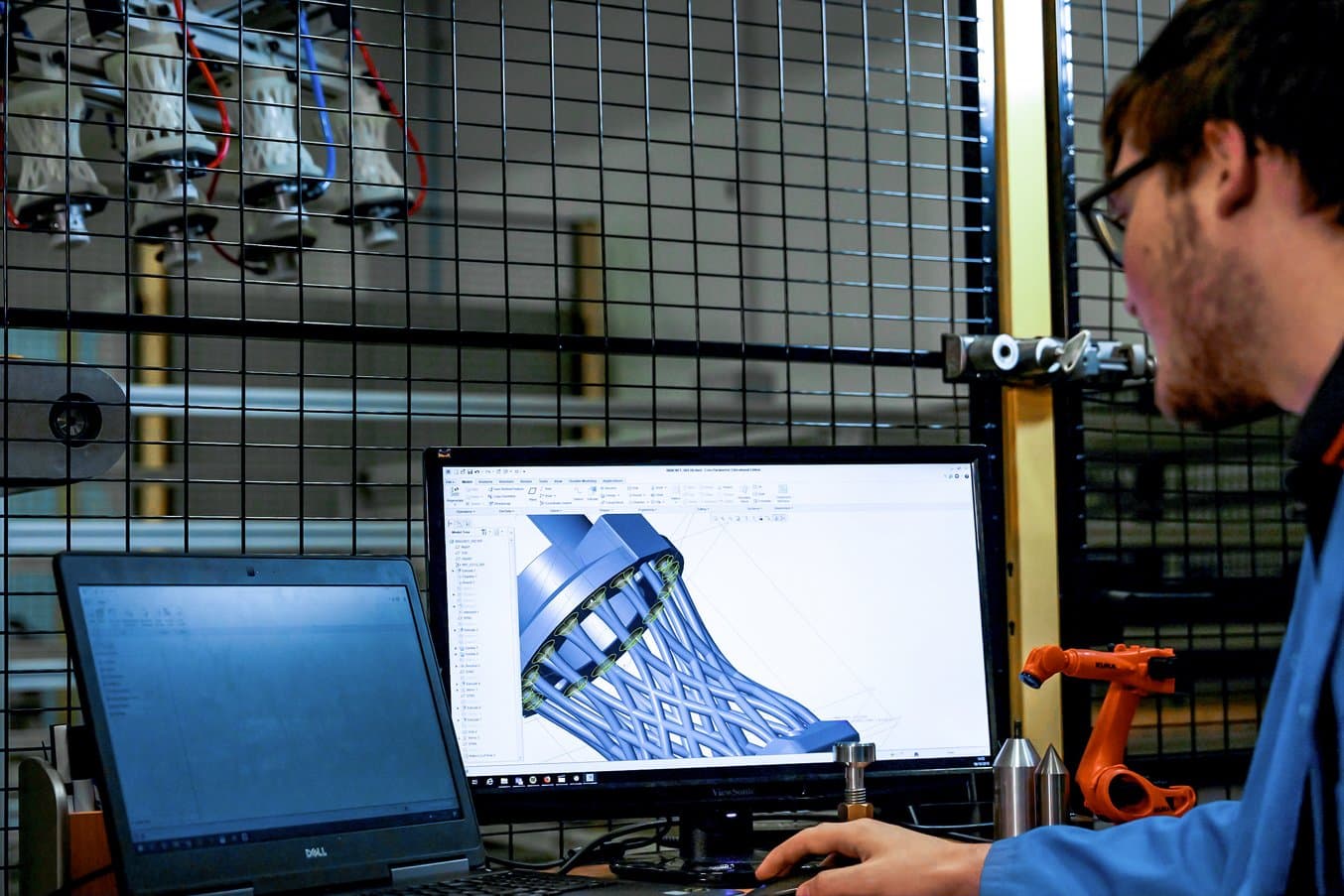
« J’ai épaissi la structure et utilisé un matériau plus durable qui fonctionne bien mieux puisqu’il est même plus élastique. Il se rétracte immédiatement après compression et fonctionne à la perfection, » a poursuivi Williams.
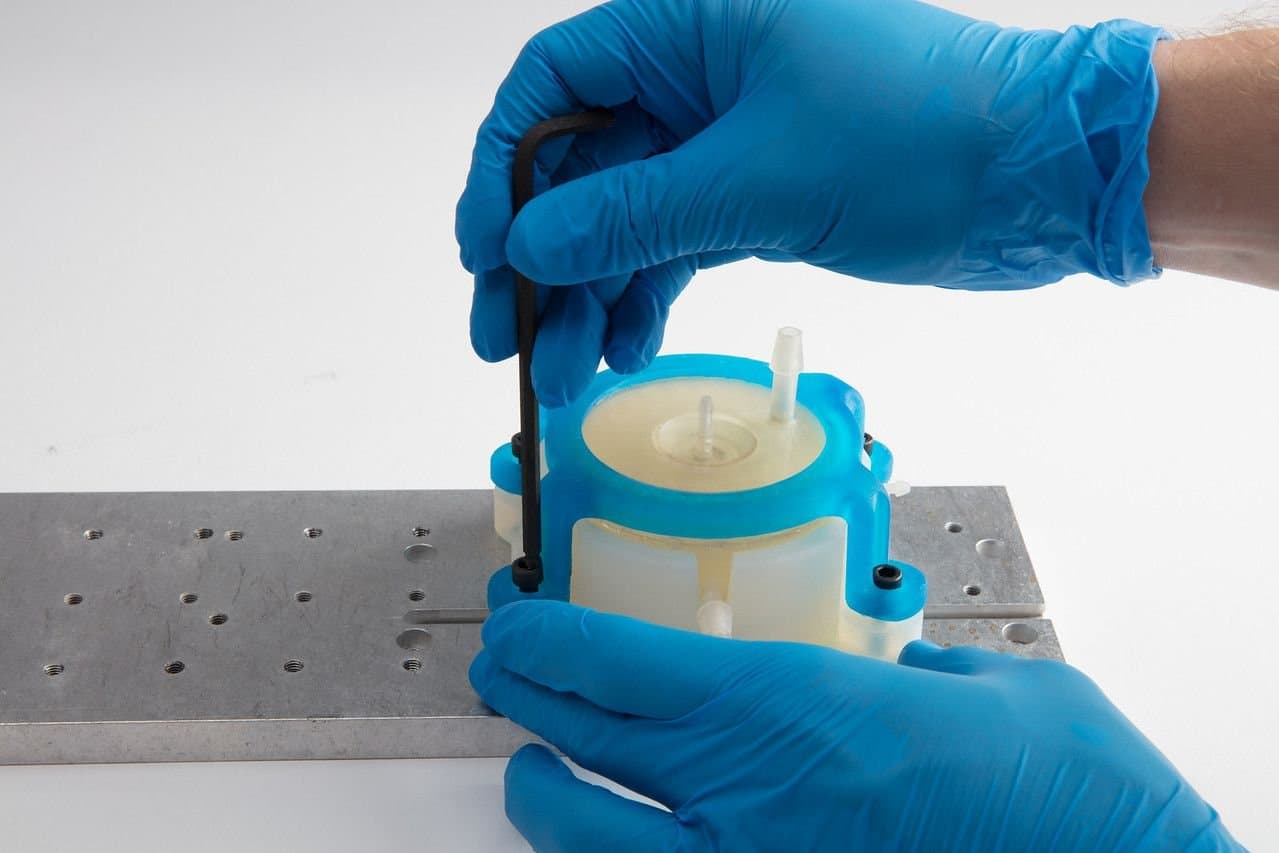
Gabarits et fixations avec l'impression 3D
Téléchargez notre Livre Blanc pour apprendre comment réduire les coûts et la période de développement et créer des processus de travail davantage optimisés avec les gabarits et fixations imprimés en 3D.
Téléchargez le Livre Blanc
Une liberté de conception et des itérations rapides avec l’impression 3D
« L’impression 3D me donne davantage de liberté lorsqu’il s’agit de créer et de concevoir une pièce. Je peux créer et fabriquer quasiment toutes les formes que je souhaite car ces machines sont extrêmement flexibles. Quel avantage quand on doit créer des formes complexes comme celle que j’ai dû fabriquer pour régler ce problème !, » a ajouté Williams.
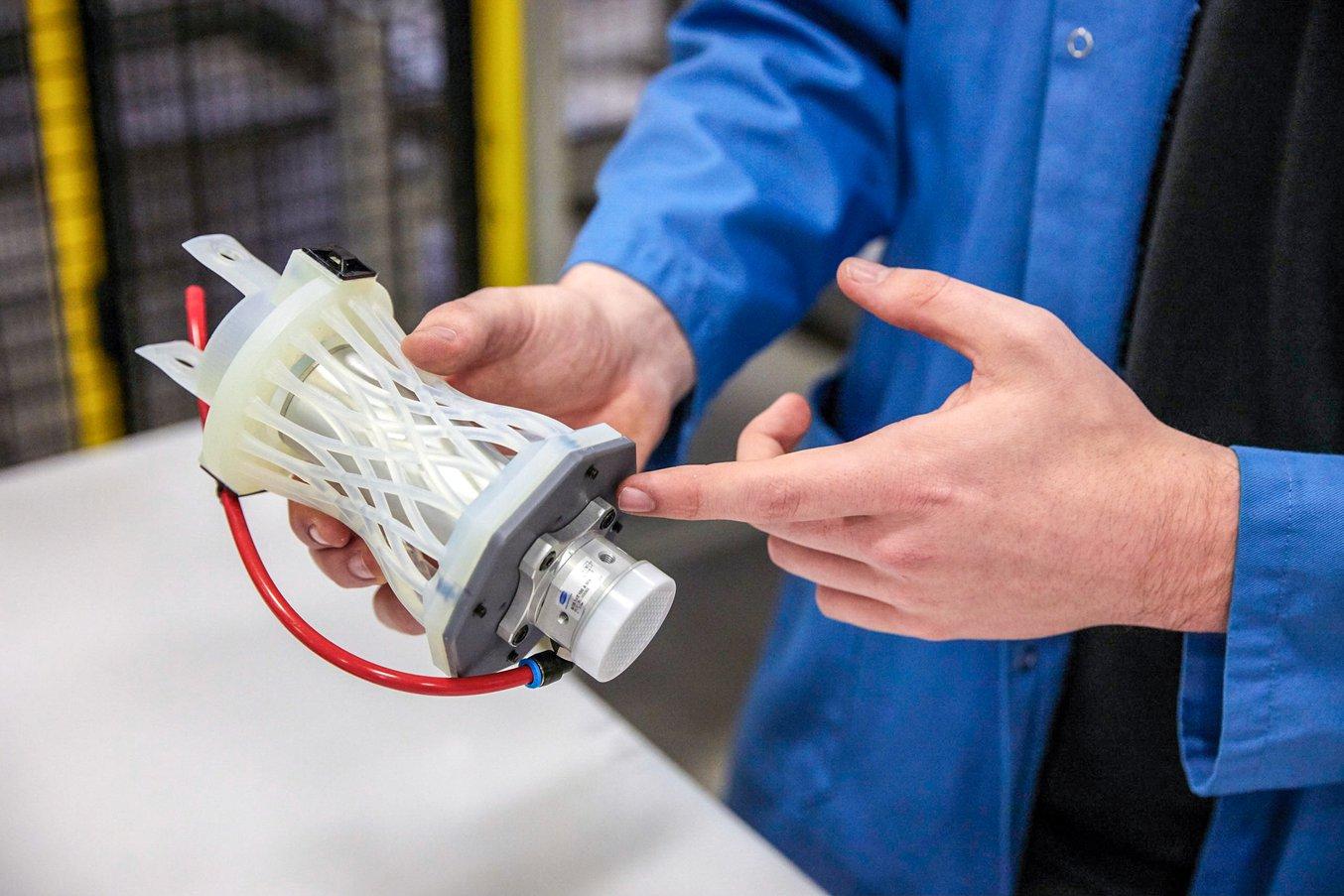
L’impression 3D a permis à Williams d’être plus créatif et plus agile dans le processus de conception et de ne pas être limité par les règles de conception associées aux méthodes de fabrication traditionnelles.
« Lorsque vous concevez une pièce à usiner, vous devez réfléchir à de nombreux autres aspects tels que la façon dont vous la fixerez et la manière dont vous amènerez l’outil à un certain emplacement. La pièce est assez complexe à l’intérieur, par conséquent l’espace dont un outil aurait besoin pour créer les poches et les éléments depuis l’intérieur serait probablement insuffisant. Je devais simplifier le design ou créer un nouveau design complexe. Cette option pouvait ne pas fonctionner aussi bien et elle serait plus onéreuse et plus chronophage, » a affirmé Williams.
Des imprimantes 3D à disposition en interne signifiaient pour Williams la capacité de fabriquer de nouveaux modèles rapidement et d’économiser des mois de délai de réalisation sur l’ensemble du projet.
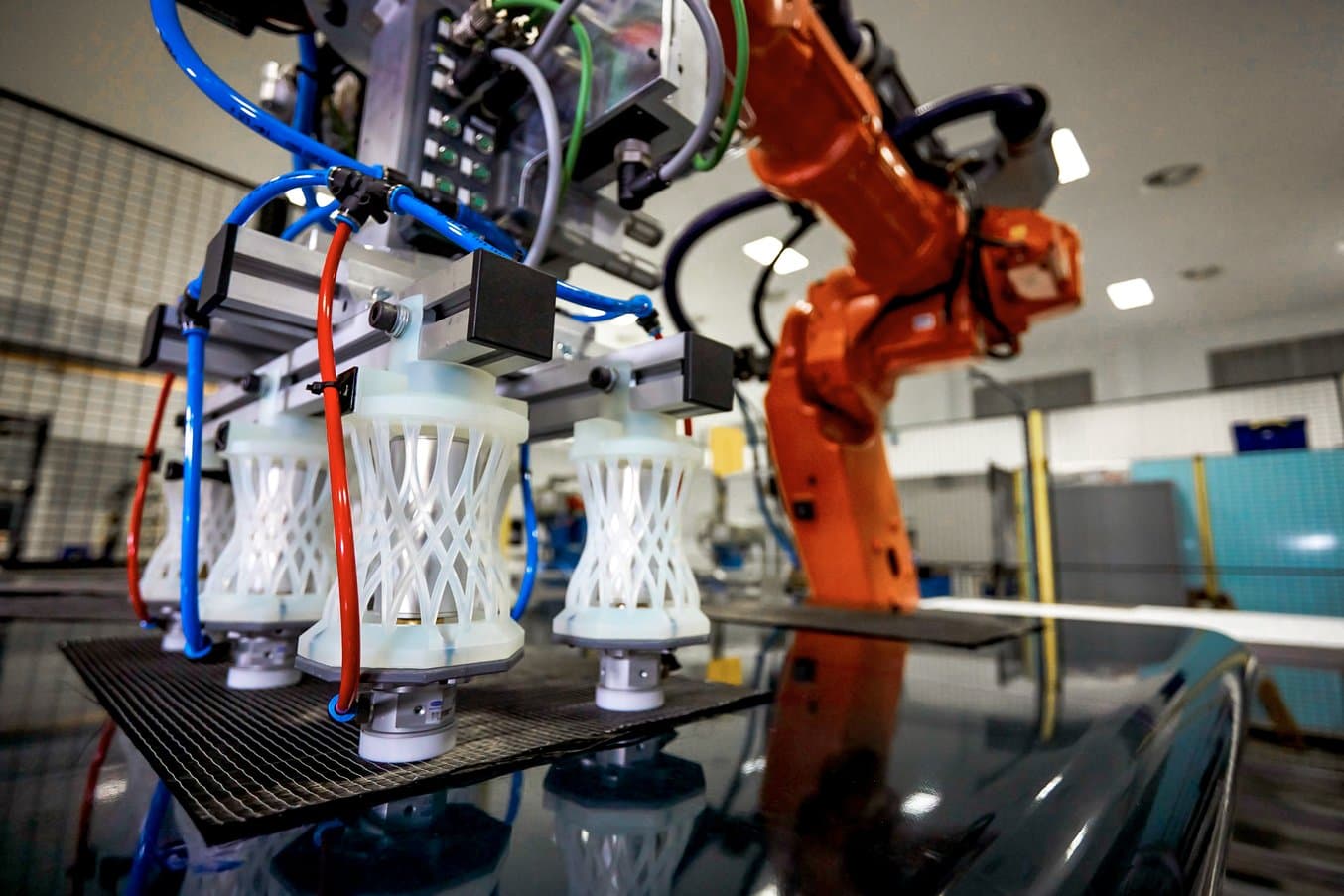
« J’ai créé cinq modèles du jeu de six organes de préhension, ce qui aurait pu durer 10 à 15 semaines si je les avais usinés, et je ne compte pas le temps des essais, » a affirmé Williams.
« L’impression 3D d’une pièce dure six heures seulement et si un modèle ne fonctionne pas, il me suffit de créer un nouveau design la journée, pendant que je travaille. Avant de rentrer chez moi le soir, je peux lancer l’imprimante et l’impression sera terminée le lendemain matin. De cette façon, je peux travailler la journée sur la nouvelle pièce, » a ajouté Williams.
« Avant de rentrer chez moi le soir, je peux lancer l’imprimante et l’impression sera terminée le lendemain matin. De cette façon, je peux travailler la journée sur la nouvelle pièce.»
Matthew Williams, AMRC
Découvrez la station d’impression 3D et l’assistance qu’elle fournit à des centaines d’ingénieurs de l’AMRC
Williams a collaboré avec le groupe Conception et Prototypage de l’AMRC pour fabriquer ses pièces imprimées en 3D. Le groupe a récemment installé une nouvelle station de fabrication additive avec un parc de 12 imprimantes 3D de stéréolithographie (SLA) Form 2 permettant un libre accès à l’impression 3D pour tous les ingénieurs sur l’ensemble du site.
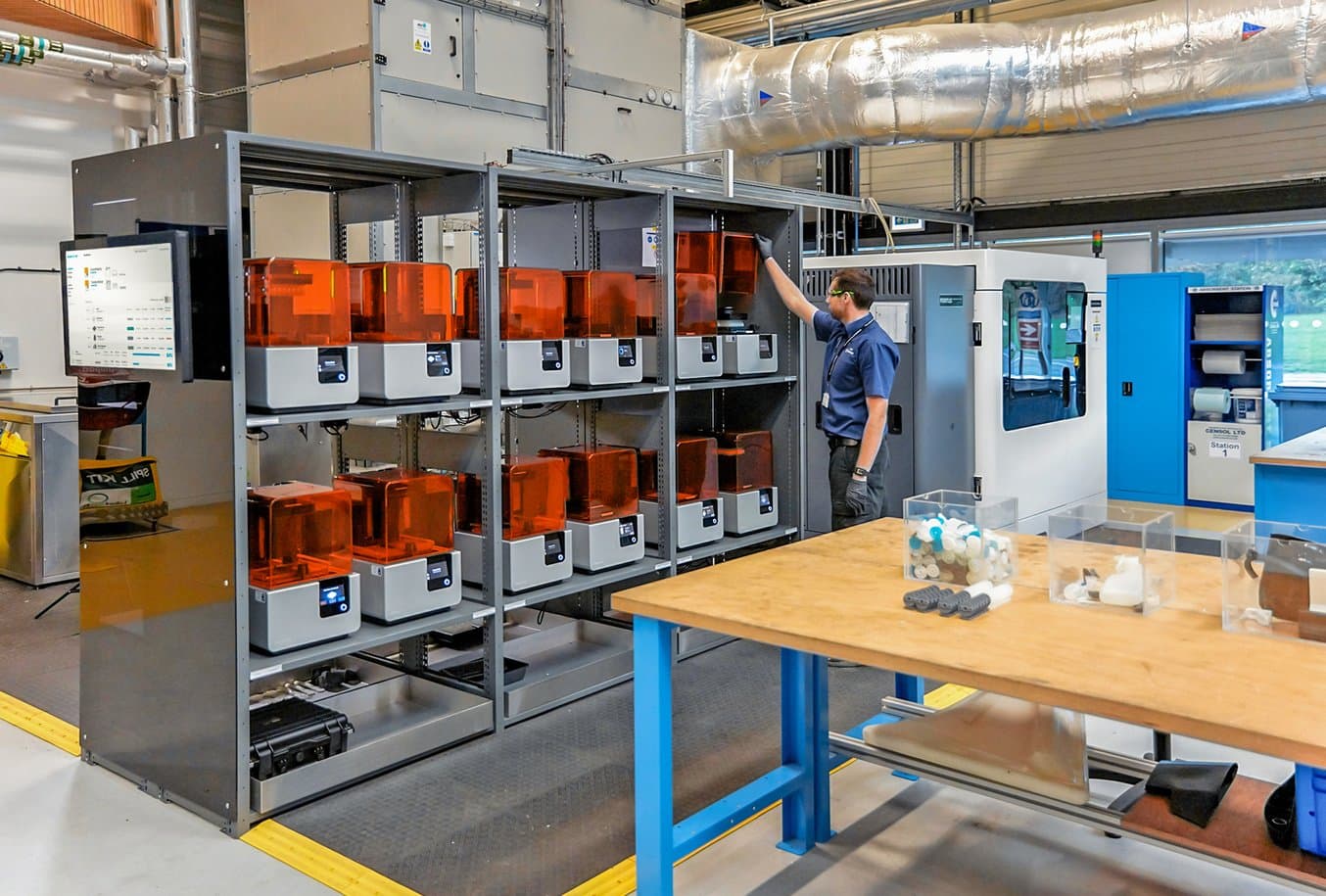
« Avoir [les imprimantes] sur place, c'est vraiment fantastique. Je gagne un temps fou car je peux juste configurer mes impressions, traverser la rue lorsqu’elles sont terminées, les retirer de l’imprimante et les ramener ici pour les utiliser immédiatement. C’est bien plus rapide que de devoir s’adresser à quelqu’un chez un prestataire externe pour les fabriquer et les faire expédier ici, » se réjouit Williams.
Apprenez-en plus sur la station d’impression 3D de l’AMRC et découvrez les autres applications telles que l’impression 3D par lots de 500 bouchons de perçage haute précision pour des essais de perçage pour Airbus, une attache de capteur thermorésistante pour une application de soudage et des cylindres d’enroulement filamentaire sur mesure pour la fabrication de composites.
Vous souhaitez en savoir plus sur les imprimantes et les technologies utilisées dans la station d’impression 3D de l’AMRC ? Explorez la Form 3, la Form 3L et la sélection de résines techniques Formlabs pour voir si elles s’appliquent à votre propre projet, ou demandez un échantillon 3D gratuit pour découvrir nos matériaux directement.