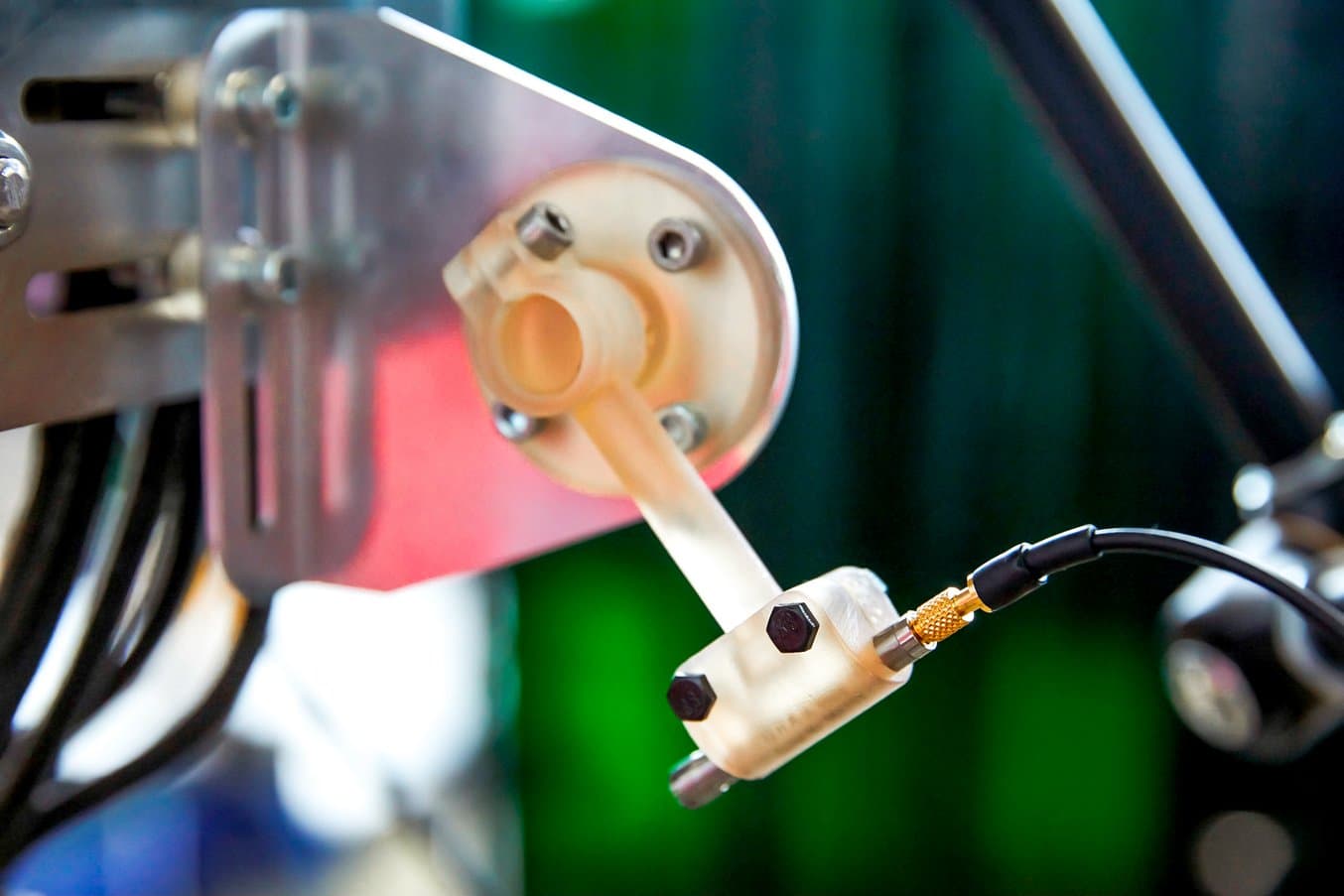
Le Nuclear Advanced Manufacturing Research Centre (Nuclear AMRC) est une collaboration entre partenaires universitaires et industriels issus de la chaîne logistique du nucléaire, qui mènent des recherches sur les solutions de fabrication avancée pour le secteur nucléaire civil dans le but d’aider les fabricants britanniques à décrocher des contrats au Royaume-Uni et dans le monde.
L’un des projets sur lesquels le centre a récemment travaillé vise à développer une solution autonome pour le soudage de récipients sous pression pour le secteur nucléaire. Pour atteindre cet objectif, l’équipe a dû intégrer de nombreux capteurs à l’équipement dans un environnement dangereux à haute température.
Matthew Smart est responsable technique des projets dans le groupe d’usinage du Nuclear AMRC. Il nous raconte comment son équipe s’est servie de l’impression 3D pour fabriquer rapidement des prototypes de différents designs et produire des dizaines de pièces capables de résister aux températures élevées à proximité immédiate du soudage.
Smart et son équipe de recherche ont travaillé avec la station de fabrication additive en accès libre de l’AMRC pour fabriquer les pièces requises. Lisez notre étude de cas pour découvrir l’accès libre à l’impression 3D et l’aide qu’il apporte à des centaines d’ingénieurs sur l’ensemble du site.
Pourquoi le soudage de récipients dans le secteur du nucléaire peut prendre des mois
Les méthodes actuelles pour souder les récipients sous pression nécessitent de nombreux points d’arrêts pour permettre une inspection manuelle. Cette inspection requiert de chauffer et de refroidir les composants de nombreuses fois. Cette méthode explique la longue durée du processus ; le soudage d’un récipient de grande taille peut durer des mois. Le projet du Nuclear AMRC vise à réduire ce délai de réalisation en développant un système autonome capable de détecter tout défaut dès son apparition. De cette manière, le processus est uniquement arrêté si un défaut est réellement constaté.
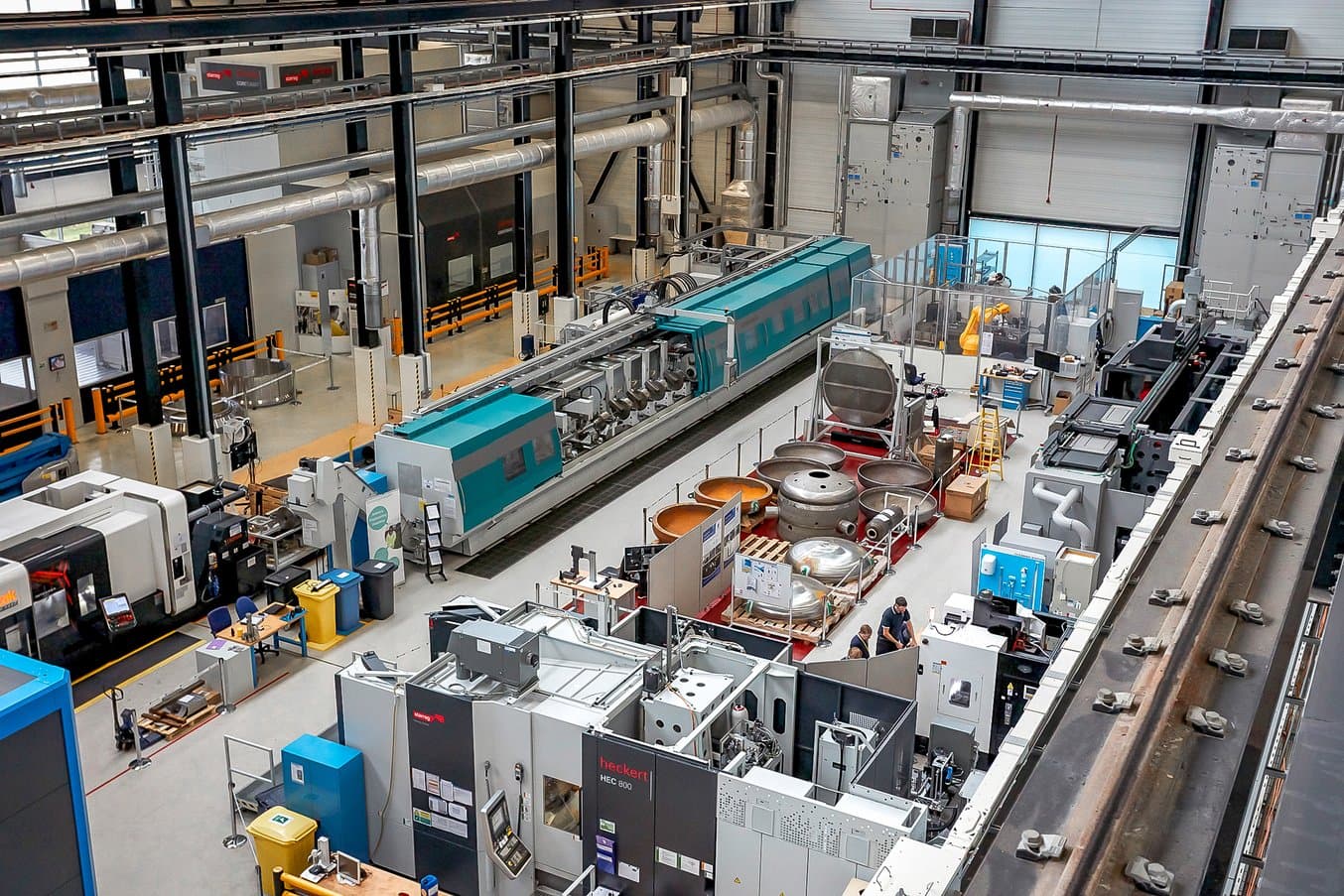
Pour analyser le processus de soudage en temps réel, le concept des chercheurs intègre de nombreux capteurs différents tels que des balayeurs laser, une surveillance acoustique, une surveillance de la tension et de l’intensité du processus, l’imagerie thermique et un système de caméra.
« L’intégration mécanique de tous ces capteurs différents est un véritable défi dans cet environnement dangereux. Nous devons essayer différentes configurations et orientations pour déterminer où tous ces capteurs devront être placés. Cela dit, nous devons être très flexibles dans notre manière de mener les essais et d’utiliser l’équipement car le temps d'utilisation sur cette machine revient très cher, » explique Smart.
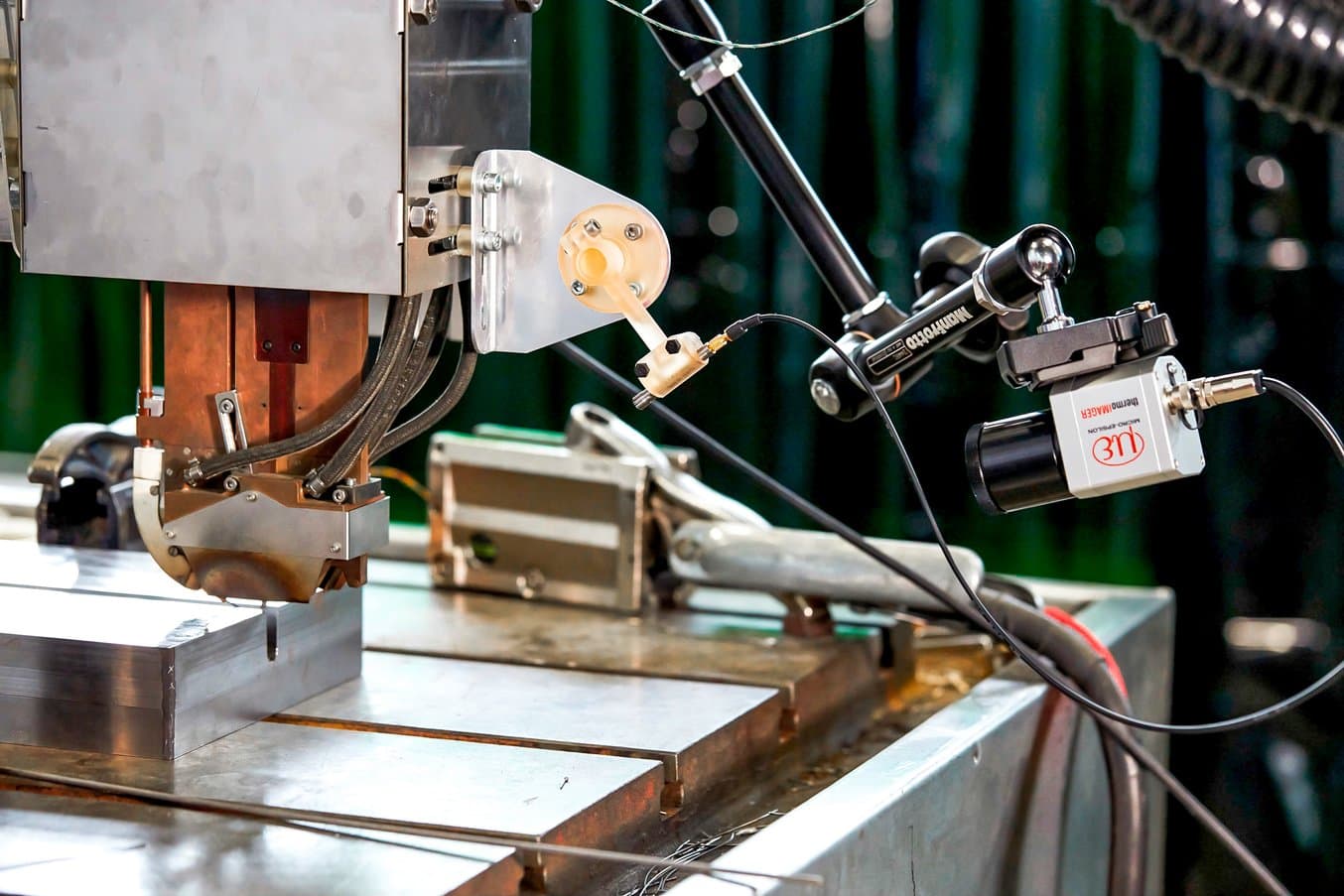
Différentes configurations de capteurs et stratégies de montage testées à un rythme soutenu avec l’impression 3D
La configuration de capteurs actuelle comporte environ douze pièces imprimées en 3D différentes, surtout des rondelles qui maintiennent les attaches ensemble et un système de montage pour les microphones. Toutes ces pièces doivent être capables de supporter les températures élevées à proximité immédiate du soudage.
High Temp Resin de Formlabs présente une température de fléchissement sous charge (TFC) de 238 °C à 0,45 MPa, ce qui fait d’elle la résine idéale pour les pièces requérant une grande thermorésistance.
« Si nous devions fabriquer ces pièces en appliquant une méthode traditionnelle, nous devrions être bien plus méticuleux lors du processus de design concernant la définition des exigences et la détermination exhaustive des tolérances exactes avant de fabriquer les pièces. En imprimant les attaches 3D, nous pouvons faire des tests, imprimer plusieurs versions avec différentes tolérances et essayer différentes orientations et différentes tailles. Cela signifie que nous pouvons être bien plus innovants et essayer les choses bien plus rapidement, » a ajouté Smart.
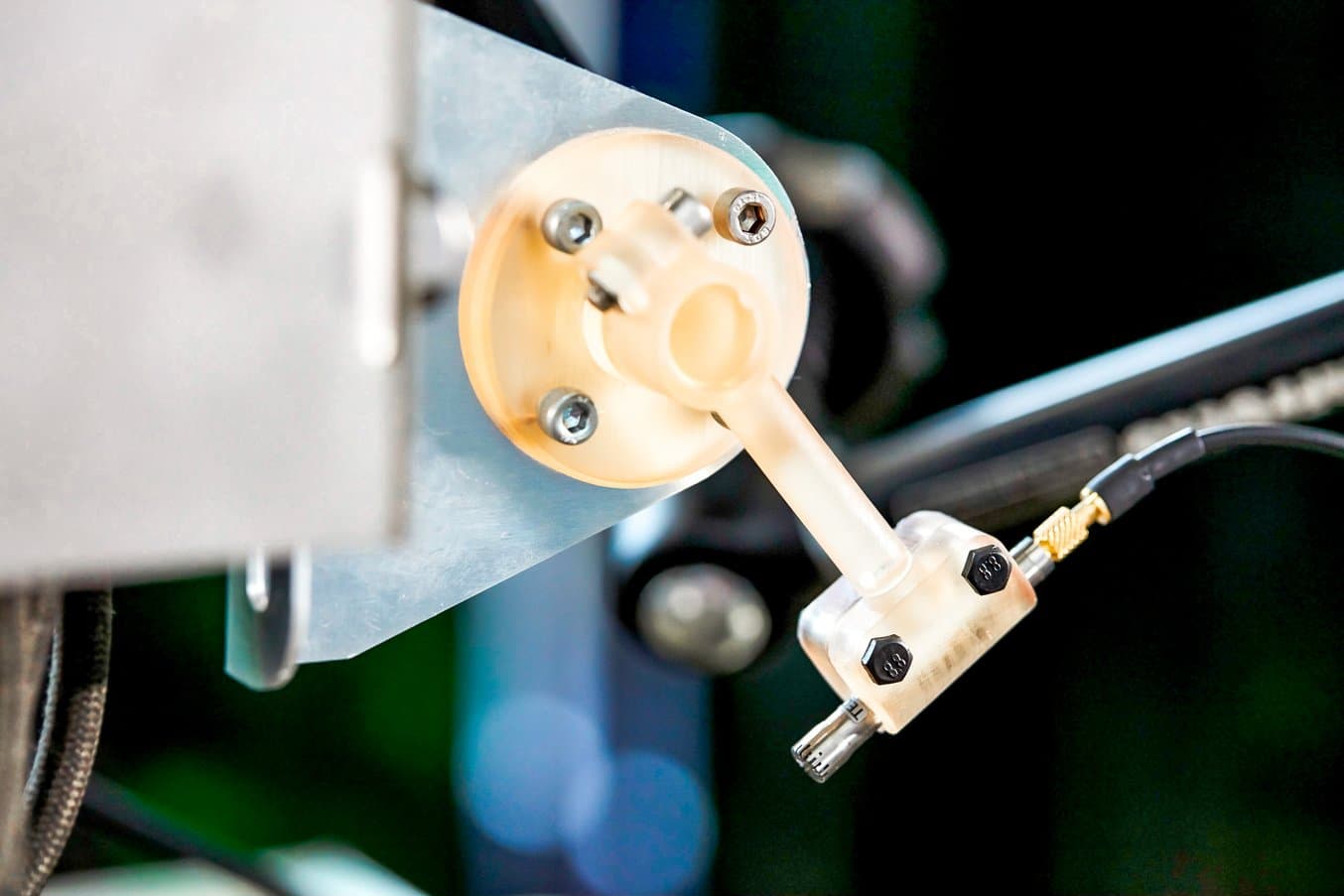
La possibilité d’utiliser l’impression pour essayer rapidement les différentes configurations de capteurs et les différentes stratégies de montage permet à l’équipe d’être très polyvalente et de réduire considérablement les coûts et les délais de fabrication des pièces.
« Sans impression, nous passerions des journées entières à nous occuper de formalités administratives, trier le matériel, réaliser la conception et sous-traiter la fabrication à une entreprise, contre quelques heures sur un logiciel de CAO et les coûts du plastique. Une fraction du temps requis avec la méthode traditionnelle, » a poursuivi Smart.
« Vous ne pouvez pas vraiment chiffrer l’agilité de ce processus car il permet tellement plus de tests et d'itérations. Admettons que vous ayez envoyé un design pour la fabrication d’un prototype et que les essais révèlent qu’il ne convient pas, vous devriez tout recommencer. Nous parlons de plusieurs semaines entre les essais des différents prototypes. Avec l’impression 3D, ce sont deux jours. Le rythme de l’innovation est impossible à chiffrer. »
« Vous ne pouvez pas vraiment chiffrer l’agilité de ce processus car il permet tellement plus de tests et d'itérations. Le rythme de l’innovation est impossible à chiffrer. »
George Sleath - AMRC
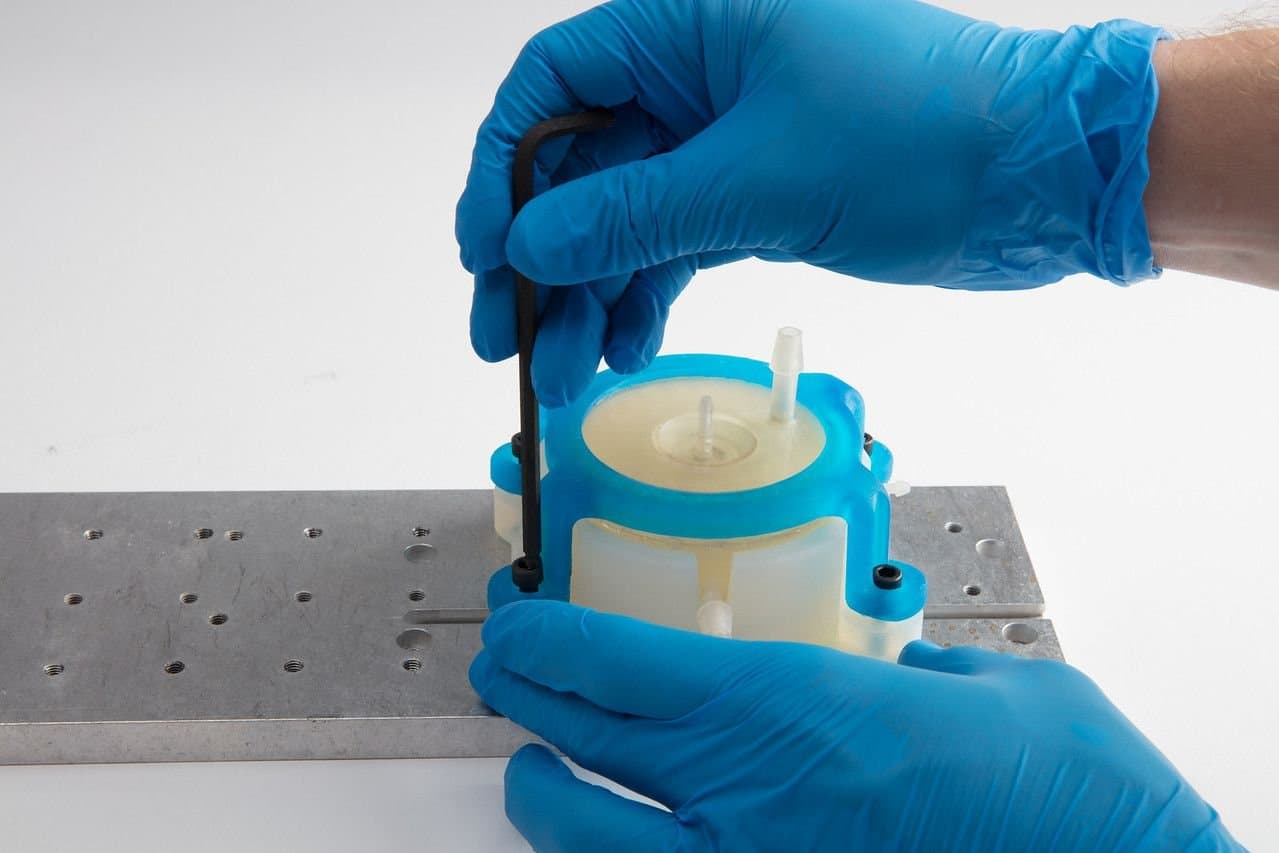
Gabratis et fixations en impresison 3D
Téléchargez notre livre blanc pour apprendre comment réduire les coûts et la période de développement et créer des processus de travail optimisés avec les gabarits et fixations imprimés en 3D.
Téléchargez le Livre Blanc
Une station d’impression 3D en interne pour réduire les délais de réalisation
Smart a travaillé avec le groupe Conception et Prototyage de l’AMRC pour fabriquer les pièces imprimées en 3D. Le groupe a récemment installé une nouvelle station de fabrication additive avec un parc de 12 imprimantes 3D stéréolithographique (SLA) Form 2 permettant un libre accès à l’impression 3D pour tous les ingénieurs sur l’ensemble du site.
« Nous travaillons assez étroitement avec le groupe de conception. Ils n’ont pas perdu de temps et nous ont immédiatement impliqués en nous démontrant ce qu’il est possible de faire et les équipements disponibles, et ils nous ont appris à optimiser le design pour obtenir une impression rapide et facile sur les imprimantes 3D. Cette accessibilité et la connaissance des capacités sont essentielles pour utiliser les imprimantes au sein du groupe de recherche, » a affirmé Smart.
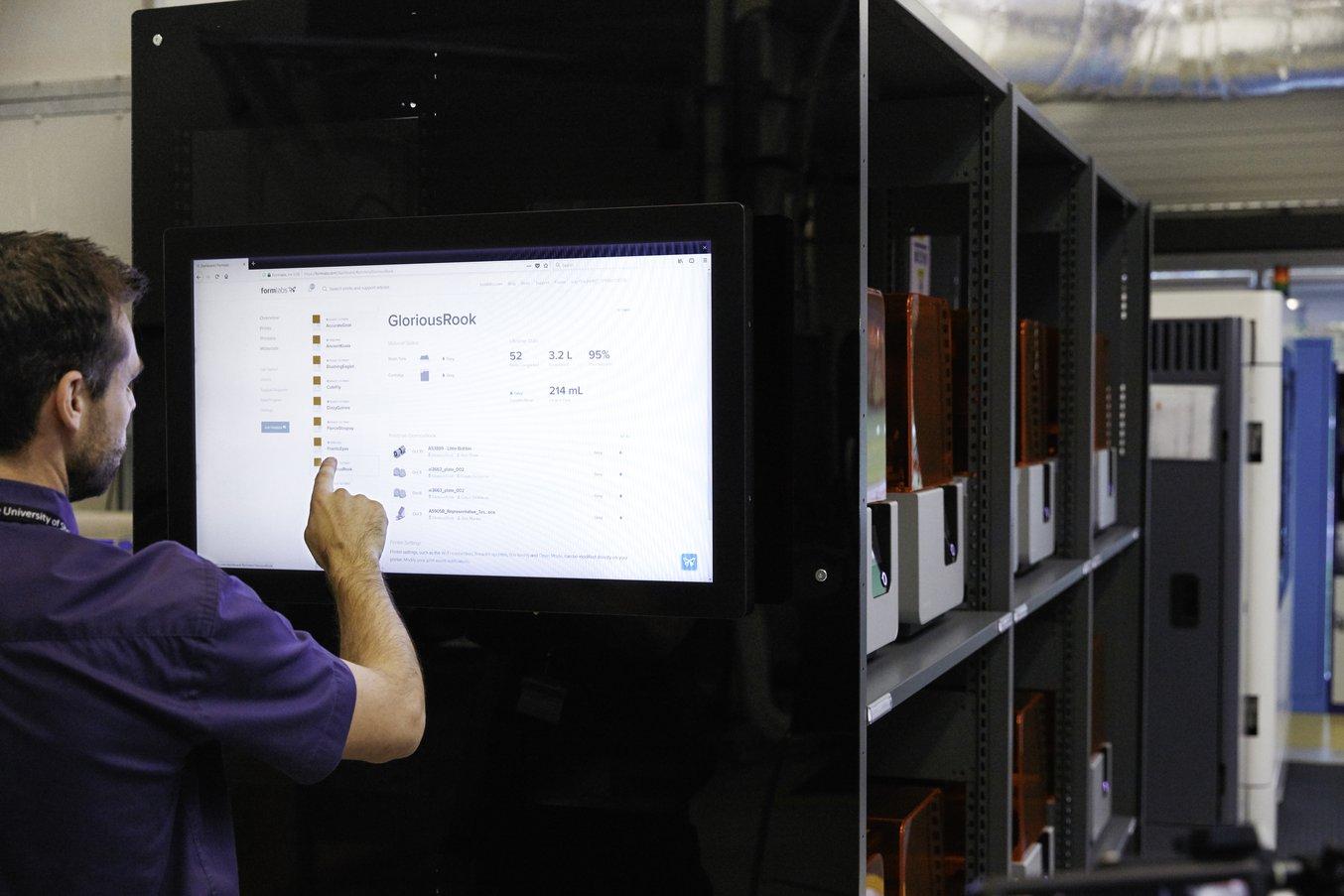
« Sans cette [station d’impression 3D], j’aurais eu connaissance de cette technologie mais je n’aurais rien su de ses possibilités ni de la façon de concevoir quelque chose en vue de la fabrication. J’ai été formé sur certaines des machines et le fait de les avoir en libre accès et de pouvoir envoyer des composants à fabriquer ici est incroyablement utile, » s’est réjoui Smart.
Découvrez la station d’impression 3D et l’assistance qu’elle fournit à des centaines d’ingénieurs de l’AMRC
Apprenez-en plus sur la station d’impression 3D de l’AMRC et découvrez les autres applications telles que l’impression 3D par lots de 500 bouchons de perçage haute précision pour des essais de perçage pour Airbus, des attaches très complexes pour l’organe de préhension d’un robot et des cylindres d’enroulement filamentaire sur mesure pour la fabrication de composites.
Vous souhaitez en savoir plus sur les imprimantes et les technologies utilisées dans la station d’impression 3D de l’AMRC ? Explorez la Form 3, la Form 3L et la sélection de résines techniques Formlabs pour voir si elles s’appliquent à votre propre projet, ou demandez un échantillon 3D gratuit pour découvrir nos matériaux directement.