Fabrication de cylindres sur mesure pour l’enroulement de filaments composites
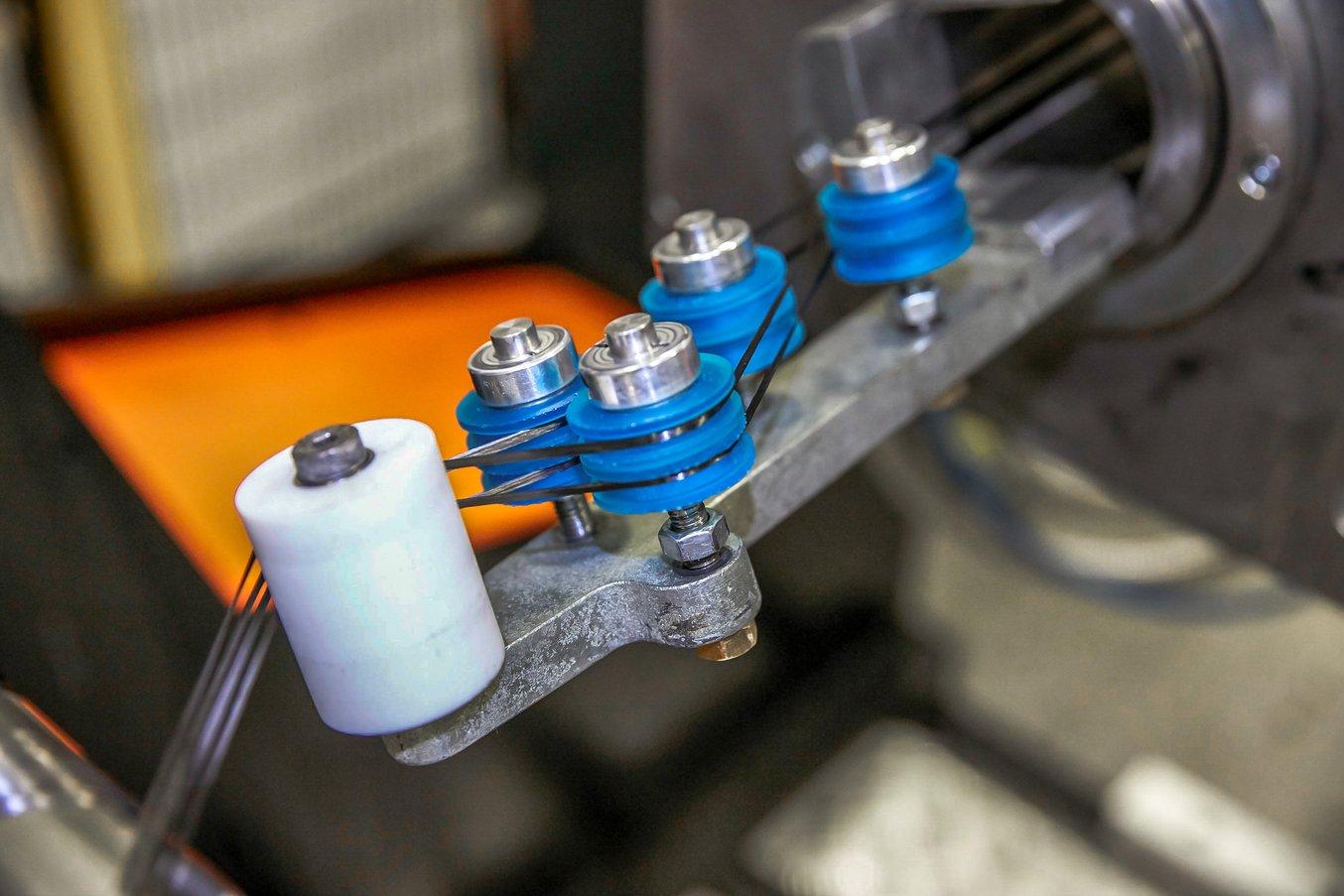
Les matériaux composites comme la fibre de verre ou de carbone tirent leur force et leur poids léger de la manière dont les paquets de fibres sont tissés et disposés dans les pièces. Ils sont une opportunité unique d’optimiser les prototypes selon les estimations des ingénieurs concernant les contraintes et leurs effets sur les composants. Mais la fabrication de ces matériaux sur mesure (donc non standardisés) est également synonyme de nombreux défis à relever.
Le Centre des Composites de l’Advanced Manufacturing Research Centre (AMRC) de l’université de Sheffield mène des recherches en utilisant des méthodes de pointe pour relever ces défis pour des secteurs à valeur élevée comme l’aérospatiale, la marine ou le secteur automobile.
Dans le cadre de l’un des projets de recherche de cette structure, les ingénieurs examinent l’enroulement filamentaire qui est généralement utilisé pour fabriquer des conduites de carburant, des tuyaux, des récipients et des arbres pour les secteurs de l’aérospatiale et de l’automobile. Les chercheurs travaillent avec divers matériaux de largeurs différentes, ce qui les oblige à adapter le système pour traiter les fibres avec la plus grande exactitude, qui est primordiale dans l’aérospatiale.
Alexander Shaw, technicien en automatisation composite travaillant sur ce projet, nous raconte comment les chercheurs ont conçu et imprimé en 3D différentes versions de cylindres sur mesure. Il nous raconte également leur collaboration avec la station de fabrication additive de l’AMRC pour fabriquer les pièces en quelques jours seulement.
Regardez cette vidéo pour découvrir le fonctionnement du Composites Centre et retracer le parcours des chercheurs qui ont utilisé des cylindres sur mesure pour l’enroulement filamentaire.
Shaw et son équipe de recherche ont travaillé avec la station de fabrication additive en accès libre de l’AMRC pour fabriquer les pièces requises. Lisez notre étude de cas pour découvrir l’accès libre à l’impression 3D et l’aide qu’il apporte à des centaines d’ingénieurs sur l’ensemble du site.
Le challenge des composites
Une machine d’enroulement filamentaire fonctionne ainsi : une bobine de fibres passe par un bain de résine puis entre de minces cylindres pour passer du cantre situé à l’arrière du système à la tête de déroulement fixée à un robot KUKA 6 axes. Les fils de fibres atteignent ensuite un mandrin métallique qui tourne comme un tour. La tête du robot se déplace et dépose la fibre sur le mandrin en rotation.
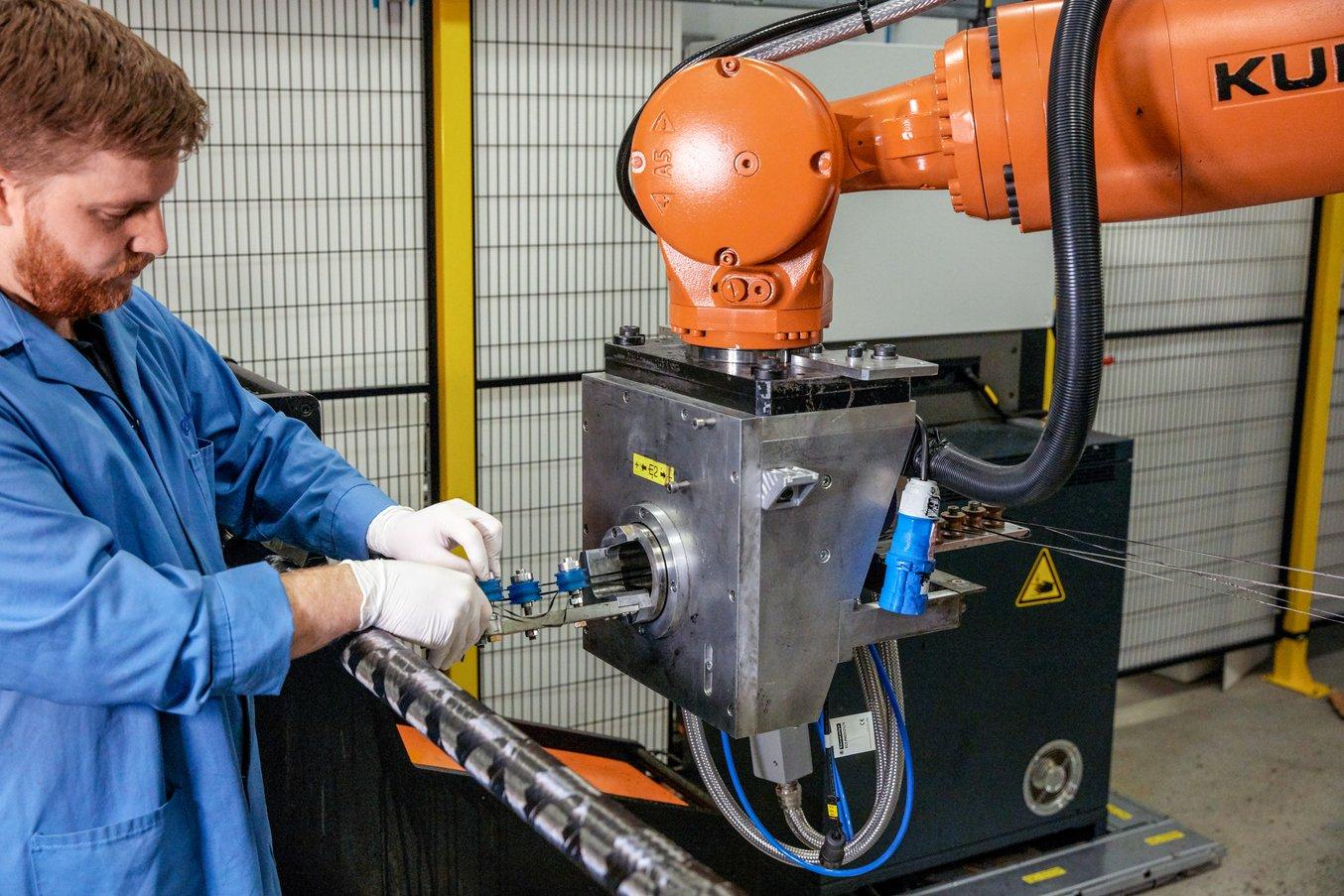
Différentes fibres peuvent présenter différentes largeurs de matériaux ou être légèrement irrégulières, ce qui peut causer des problèmes pour faire passer la fibre à travers les cylindres. Lorsque le chercheur est passé à un matériau différent qui était légèrement plus mince que le matériau précédemment utilisé, la variation supplémentaire de la largeur l’a obligé à fabriquer un cylindre légèrement plus petit que la pièce fournie à l’origine avec la machine.
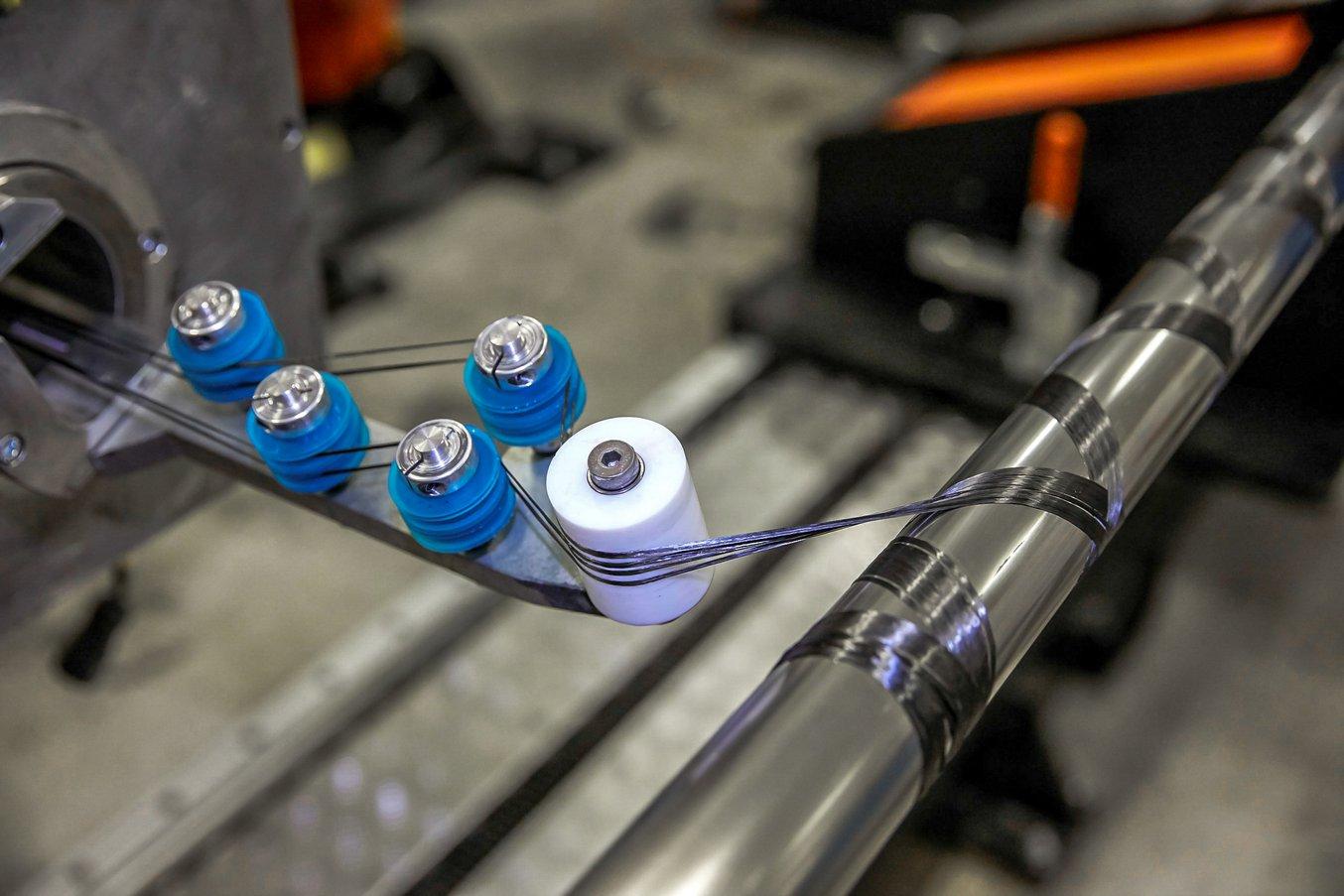
« Si vous avez une largeur de câble de filament inférieure au matériau que vous faites passer par les cylindres, vous laissez des espaces entre les câbles de filament, ce qui laisse un vide. Si ces espaces sont supérieurs à un millimètre environ, les pièces ne répondent pas aux exigences de l’aérospatiale, » a déclaré Shaw.
Production des pièces à l’aide d’outils d’impression 3D ou d’usinage
Pour adapter le système aux nouveaux matériaux, Shaw a observé les cylindres standard et conçu trois nouvelles versions, toutes de diamètres et de largeurs différents selon le matériau utilisé. Par exemple, pour un matériau de 0,25 pouce, il a imprimé des cylindres avec une partie médiane de 0,25 pouce et des parties extérieures d’1/8 de pouce, de sorte que lorsqu’il assemble deux fils côte à côte, il n’y a aucun espace entre le cantre supérieur et le cantre inférieur.
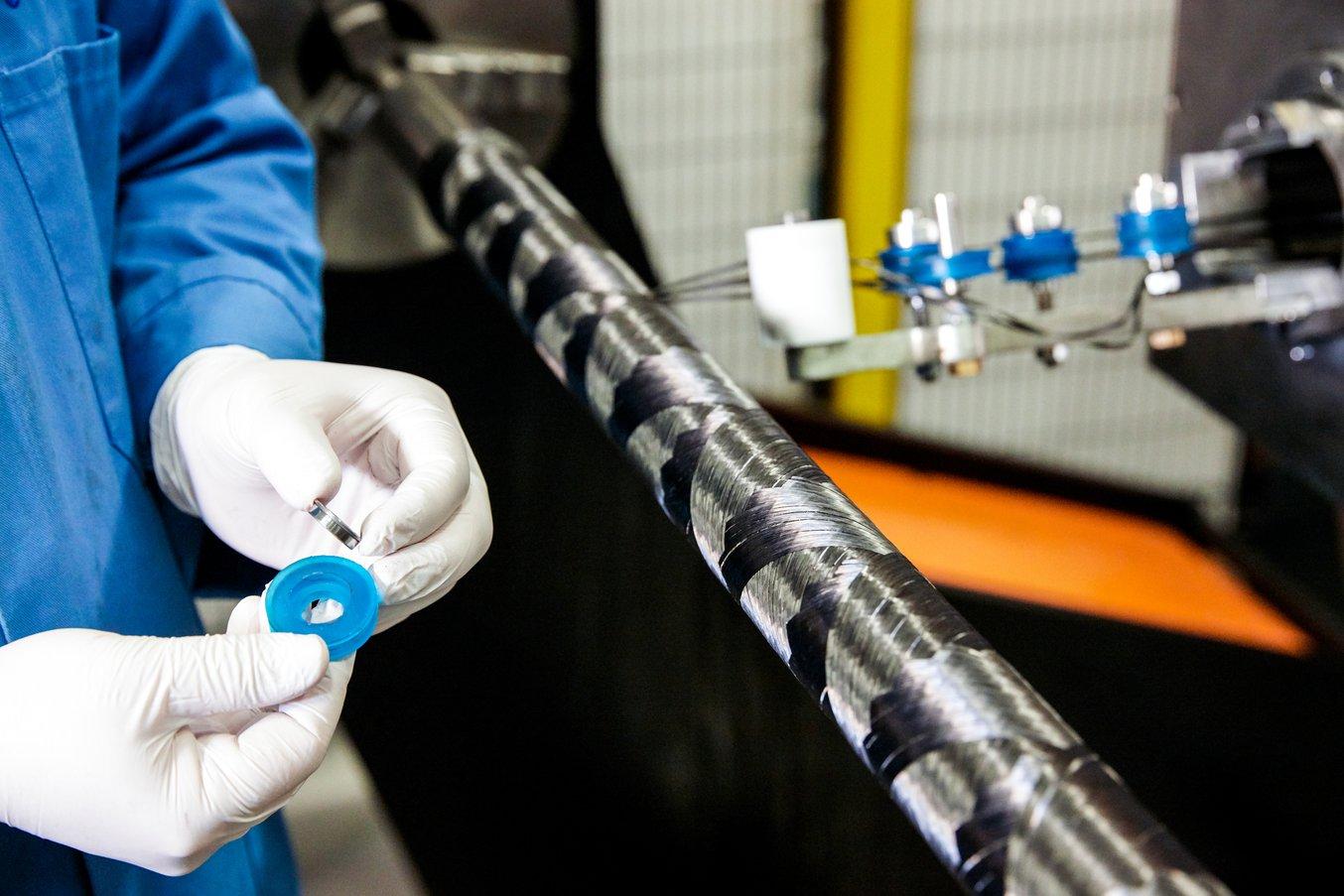
L’équipe avait besoin des nouveaux cylindres dès que possible pour pouvoir poursuivre le projet. Elle a donc décidé que l’impression 3D serait la meilleure option pour fabriquer les pièces.
« Si nous avions fait usiner les nouveaux cylindres, nous aurions eu des coûts bien plus élevés et les délais de réalisation auraient été d’une semaine peut-être, alors qu’avec les imprimantes 3D de Formlabs, nous sommes à même d’imprimer quelque chose que nous pouvons prendre en main le jour même, » a poursuivi Shaw.
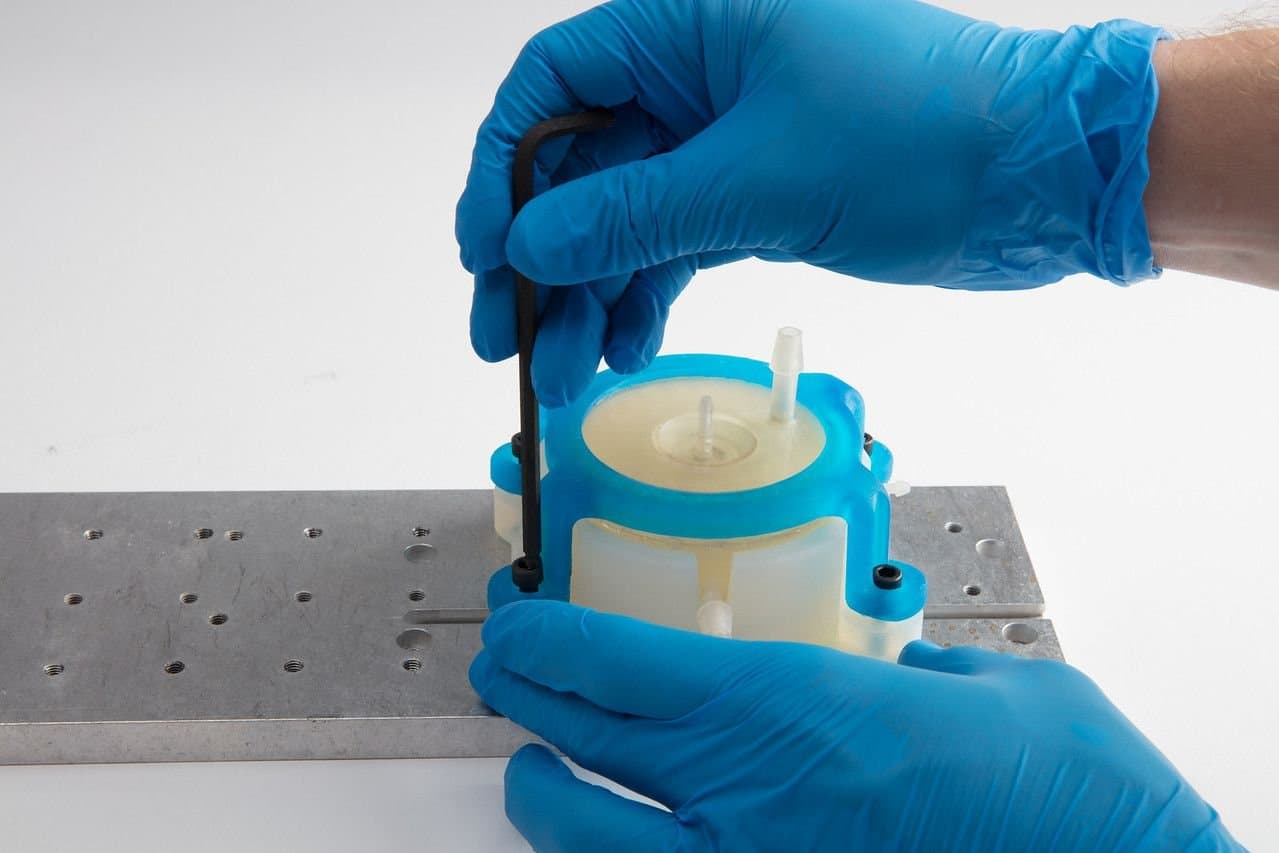
Gabarits et fixations en impression 3D
Téléchargez notre Livre Blanc pour apprendre comment réduire les coûts et la période de développement et créer des processus de travail davantage optimisés avec les gabarits et fixations imprimés en 3D.
Téléchargez le Livre Blanc
Utilisation de la station d’impression 3D en interne
« L’impression 3D est un sujet auquel nous nous sommes déjà intéressés par le passé. Seulement, cette technologie n’était pas accessible pour tous. Avant, seules trois ou quatre personnes étaient formées pour utiliser les machines. Le logiciel et le système entier demandaient plus de temps de familiarisation, » a indiqué Shaw.
Shaw a travaillé avec le groupe Conception et Prototypage de l’AMRC pour fabriquer les pièces imprimées en 3D. Le groupe a récemment installé une nouvelle station de fabrication additive avec un parc de 12 imprimantes 3D de stéréolithographie (SLA) Form 2 permettant un libre accès à l’impression 3D pour tous les ingénieurs sur l’ensemble du site.
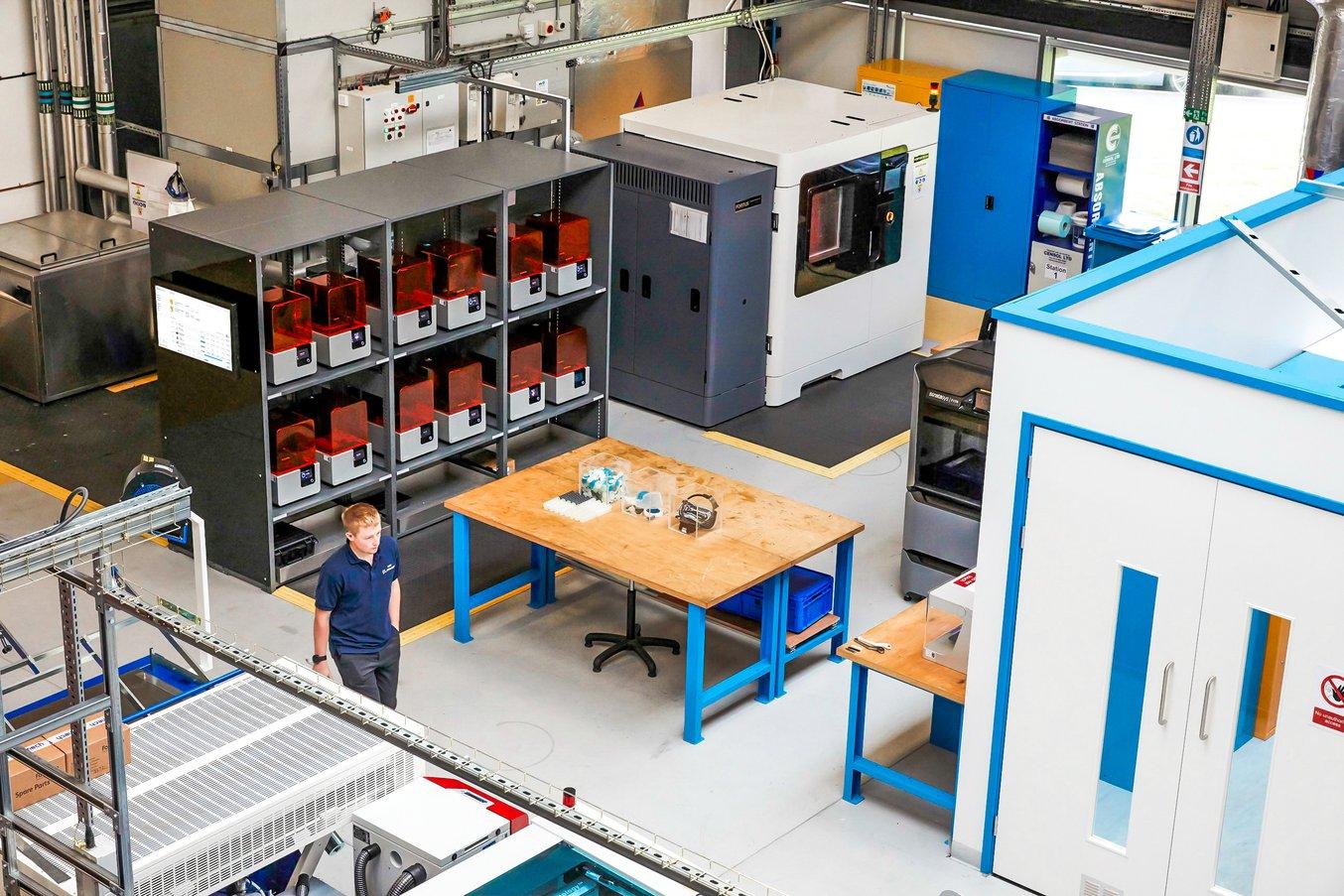
Après avoir reçu les nouvelles imprimantes, Mark Cocking, responsable technique impression 3D et polymères, a demandé à tous les membres du Centre des Composites si quiconque était intéressé par une formation.
« Je pense que 90 % des personnes travaillant au Centre des Composites ont dit "oui, nous avons vraiment besoin de ces machines". Nous avons pu découvrir le logiciel et approfondir tous les détails en 20-30 minutes. Le logiciel est si facile d’utilisation, il suffit de créer un STL et de l’importer dans le logiciel par glisser-déposer, ce dernier se chargera du reste pour vous. Ce sont désormais près de douze personnes dans notre groupe qui ont suivi la formation pour les imprimantes Formlabs, » a déclaré Shaw.
Découvrez la station d’impression 3D et l’assistance qu’elle fournit à des centaines d’ingénieurs de l’AMRC
Apprenez-en plus sur la station d’impression 3D de l’AMRC et découvrez les autres applications telles que l’impression 3D par lots de 500 de bouchons de perçage haute précision pour des essais de perçage pour Airbus, une attache de capteur thermorésistante pour une application de soudage et les attaches complexes de l’organe de préhension d’un robot pour la fabrication de composites.
Vous souhaitez en savoir plus sur les imprimantes et les technologies utilisées dans la station d’impression 3D de l’AMRC ? Explorez la Form 3, la Form 3L et la sélection de résines techniques Formlabs pour voir si elles s’appliquent à votre propre projet, ou demandez un échantillon 3D gratuit pour découvrir nos matériaux directement.