New Balance et Formlabs s'associent pour révolutionner les performances et les possibilités de personnalisation des chaussures
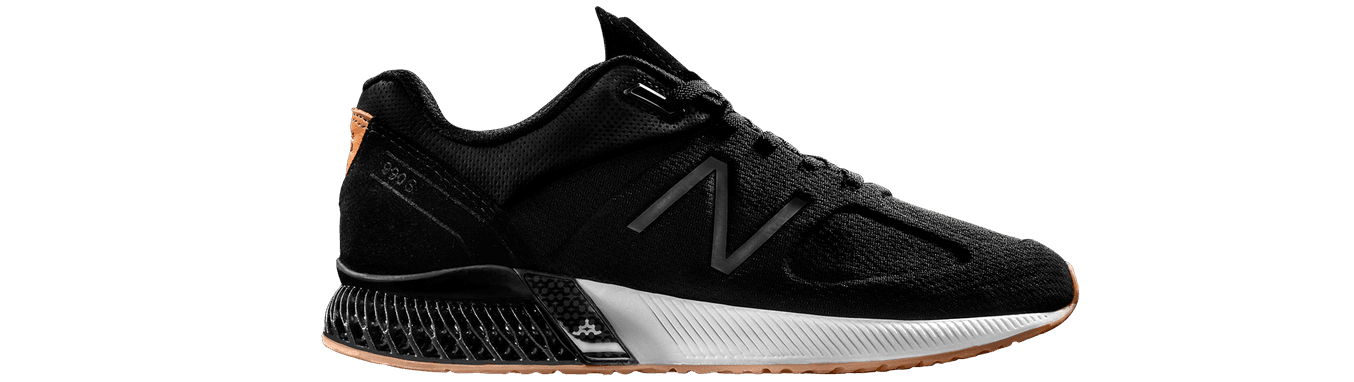
La performance est dans les détails. Dans le monde de la chaussure, cela concerne la conception et les matériaux, les deux étant dépendant de la fabrication.
En 2017, New Balance a établi un partenariat avec Formlabs pour développer un système de production en impression 3D qui ouvre la porte aux opportunités tant sur le front de la conception, que celui des matériaux. Ce système offre une liberté totale de concevoir des structures optimisées pour la performance et de fabriquer des composants personnalisés à grande échelle, tout en donnant accès à un nouveau monde de possibilités pour ce qui est des matériaux.
Cet été, la société a fait un pas de géant pour concrétiser cette vision avec l'annonce de TripleCell : une plateforme technologique haut de gamme équipée des imprimantes 3D stéréolithographiques (SLA) Formlabs et d'un tout nouveau matériau, Rebound Resin.
« TripleCell nous permet de tracer une nouvelle voie dans l'utilisation de données pour connaitre chaque millimètre d'une semelle parfaite. Formlabs a été un partenaire essentiel pour réaliser ce projet, révolutionner l'industrie, non seulement sur le plan de la performance, mais également dans la personnalisation de chaussures pour athlètes, et de la rapidité de mise sur le marché »
Katherine Petrecca, New Balance General Manager of Footwear à Innovation Design Studio
La production industrielle à petite échelle est maintenant en route sur le site de New Balance à Lawrence, dans le Massachusetts. Le premier produit issu de TripleCell, l'édition limitée 990S TripleCell, est en cours de distribution, et FuelCell Echo avec l'avant-pied réalisé avec TripleCell suivra à l'automne 2019. Un modèle de running haute-performance sera disponible en 2020.
Continuez la lecture pour en savoir plus sur les matériaux et la collaboration au processus d'impression 3D qui ont permis à New Balance de se positionner à la pointe de l'innovation dans le domaine des chaussures de sport.
Découvrez le partenariat ou contactez notre équipe de consulting pour en savoir plus sur une collaboratio avec Formlabs et comment mettre en place des solutions additives dans votre entreprise.
Trouver des opportunités de personnalisation dans une chaîne d'approvisionnement complexe
La chaussure est un produit complexe par nature. L'industrie de la chaussure est une activité où des stocks et des volumes importants sont nécessaires, elle nécessite encore souvent beaucoup de travail manuel et de savoir-faire. New Balance présente des milliers de concepts par an et un seul modèle comprend des centaines de combinaisons de couleurs et de tailles, avec des composants fabriqués avec différents matériaux, tolérances et programmes d'outillage. Avec une demande de personnalisation grandissante, ceci devient de plus en plus compliqué. Le consommateur moderne exige des produits personnalisés pouvant être commandés depuis
n'importe où, à partir de diverses plateformes, et livrés rapidement.
À ce jour, la plupart des entreprises n’ont pu proposer que des produits hautement personnalisés à tirage unique, tirant parti de l’impression 3D pour développer et fabriquer des chaussures de sport hautement personnalisées destinées aux athlètes professionnels. En 2013, le premier athlète a concouru dans une chaussure personnalisée imprimée en 3D. Peu de temps après, nous avons vu plus de cas en football, baseball, etc.
Parallèlement à ces développements, la technologie d'impression 3D évoluait. En 2012, Formlabs introduit la Form 1 dans le but de développer la stéréolithographie (SLA) puissante, fiable, abordable, accessible et évolutive. La Form 2 a suivi en 2015 et les utilisateurs ont depuis imprimé plus de 40 millions de pièces. Maintenant, les Form 3 et 3L ouvrent la porte à d’autres possibilités au sein de Production imprimée en 3D, y compris les pièces à grande échelle.
De nos jours, l’impression 3D est en passe de faire de la personnalisation de masse une réalité pour un plus grand nombre d’entreprises, avec des exemples dans tous les secteurs, comme le pilote de la plate-forme Gillette Razor Maker ™, qui a été l’un des premiers exemples de diffusion directe. Consommation, utilisation finale des pièces imprimées en 3D.
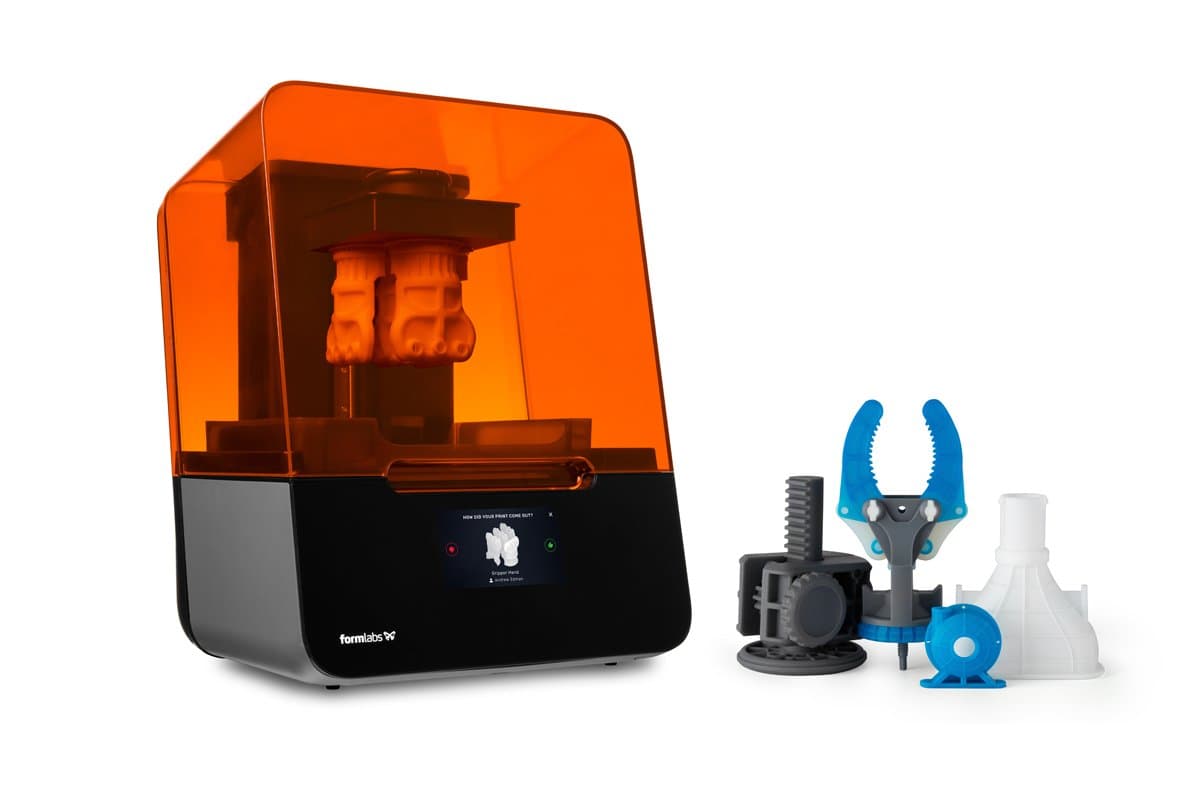
Téléchargez notre livre blanc complet pour découvrir le fonctionnement des technologies d'impression 3D en stéréolithographie (SLA), les raisons pour lesquelles l'équipe de New Balance et des milliers d'autres professionnels l'utilisent aujourd'hui, ainsi que ce que vous devez savoir pour explorer les avantages de ce processus d'impression 3D.
Téléchargez le Livre Blanc
Une conception de chaussure totalement repensée, plus rapide que jamais
En plus de ses collaborations avec des athlètes professionnels, New Balance utilisait déjà l'impression 3D pour créer ses prototypes depuis assez longtemps. Aujourd'hui, la société produit des milliers de prototypes imprimés
en 3D chaque année. Alors que le marché de l'impression 3D évoluait, la société observait les avancées. « Nous avons suivi les innovations avec les imprimantes et les matériaux 3D et nous avons commencé à envisager un avenir dans lequel ceci pourrait être intégré à des produits grand public », raconte Petrecca. « Lorsque vous pouvez utiliser des techniques telles que l'impression 3D pour vous tourner vers un modèle de fabrication à la demande, cela change la donne. Cela présente des avantages à la fois pour le consommateur et pour New Balance en tant que fabricant. Pour le consommateur, les possibilités de conception et de fabrication offerte par l'impression sont bien supérieures à celles offertes par le moulage. Cela nous offre vraiment beaucoup d'opportunités de fabriquer de meilleures pièces que celles que nous réalisons actuellement avec de la mousse et du plastique. »
La plupart des composants en mousse qu'on trouve dans les chaussures de sport sont fabriquéspar injection ou moulage par compression, ce qui limite considérablement les possibilités. Le passage àl'impression 3D pour
le prototypage et la production a toutefois ouvert de nouvelles possibilités qui étaient impossibles avec les procédés de fabrication traditionnels.
« Ce que nous pouvions faire jusqu'à présent, c'était concevoir l'extérieur de la chaussure et nous appuyer sur les propriétés inhérentes du matériau pour offrir tous les avantages que nous recherchons en termes de performances. Avec de nombreuses étapes d'assemblage à la fin », explique Dan Dempsey, Ingénieur en Fabrication Additive Senior chez New Balance. « En utilisant la fabrication additive, nous pouvons principalement faire varier la structure en treillis pour modifier effectivement des propriétés locales d'une seule et même forme, ce qui nous donne la possibilité de concevoir chaque partie du volume de la chaussure. Nous pouvons concevoir l'ensemble en commençant par l'intérieur. ».”
La fabrication en 3D permet de concevoir la pièce dans son ensemble et pas seulement des structures en mousse. Les produits TripleCell de New Balance fourniront les expressions les plus abouties du secteur de données permettant des transitions harmonieuses entre des propriétés variables en conception de chaussures.
Cette nouvelle méthode de conception ouvre la porte à tout un monde de possibilités totalement nouvelles. C'est exactement ce que TripleCell offre : un ajustement sans faille de l'ensemble de la semelle, permettant la transition
entre une zone avec un amortissement élevé à une zone de grande stabilité, en une seule conception et un seul matériau. Le prototypage et la fabrication de pièces en impression 3D transforment également l'ensemble du processus de développement du produit, réduisant ainsi de manière significative les délais de mise sur le marché.
« Le délai normal entre le premier croquis sur papier et la mise sur le marché est de 15 à 18 mois. Et quand nous construisons de outils et attendons les pièces en mousse et en caoutchouc, nous devons nous attendre à des délais de 4 à 6 semaines », explique Petrecca. « En éliminant le moulage, nous pouvons gagner des mois sur le temps de développement. La technologie TripleCell permet de produire facilement plusieurs conceptions en même temps, en réinventant la méthode d'essais et de test itératifs traditionnelle. Nous avons eu la possibilité de générer et demodifier des milliers d'options avant de choisir les structures hautes performances spécialement conçues pour la course que vous voyez aujourd'hui. »
Développer Rebound Resin et un système continu de production en impression 3D
Au début du projet, l'équipe de New Balance a su qu'elle avait besoin d'un matériau très spécifique qui n'existait pas encore dans le secteur de la fabrication additive, ainsi que d'un excellent partenaire pour l'aider à donner vie au système tout entier. En 2017, la société a annoncé sa collaboration avec Formlabs, intégrant ainsi la technique d'impression 3Dà la fabrication à grande échelle de chaussures de sport dans son usine du Massachusetts.
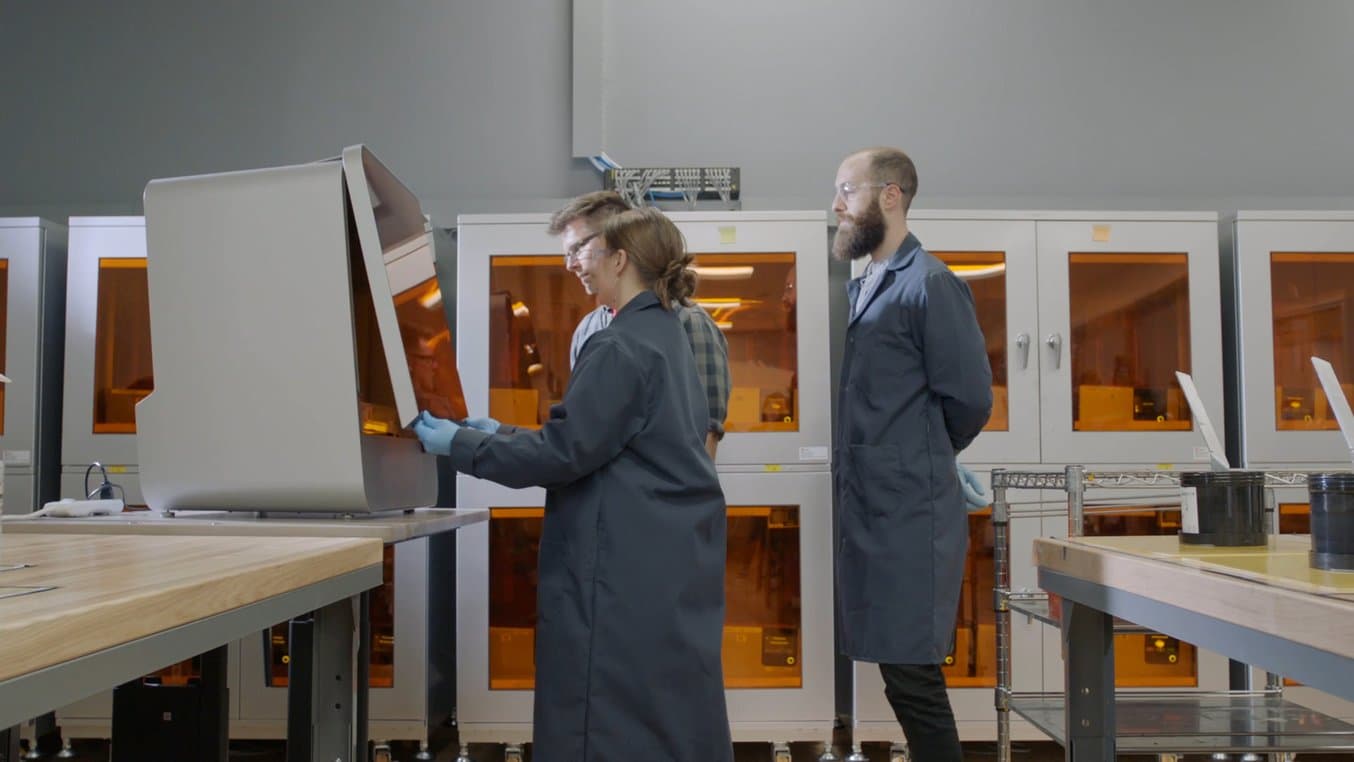
Depuis, Formlabs travaille étroitement avec New Balance du début à la fin. Les équipes de chaque entreprise ont collaboré, depuis la recherche et le développement préliminaires à la mise au point de centaines de formulations de matériaux exploratoires, pour développer un procédé de production (comprenant des fonctionnalités logicielles personnalisées), « Tout commence et finit avec les propriétés que vous pouvez obtenir pour le produit réalisé. Vous pouvez utiliserl 'imprimante la plus rapide du monde ou disposer d'une imprimante à un million de dollars, mais cela n'a aucune importance si les propriétés de votre résine ne conviennent pas à l'application à laquelle elle est destinée », reconnait Dempsey.
New Balance et Formlabs ont développé un matériau exclusif pour New Balance en partant de zéro, afin de supporter toutes les applications de production industrielle et d'utilisation finale nécessaires. Le résultat en est Rebound Resin. Conçu pour créer des structures en treillis élastiques et solides, le matériau présente un retour élastique bien plus élevé, une résistance au déchirement et une capacité d'allongement bien supérieures à tout autre matériau Formlabs SLA.
« Les composants imprimés en 3D TripleCell offrent un amorti plus vif et plus élastique que jamais avec la mousse, avec la possibilité d'être produit à la demande dans notre propre usine dans le Massachusetts », déclare Petrecca.
«Tout commence et finit avec les propriétés que vous pouvez obtenir de ce que vous faites. Vous pouvez utiliser l’imprimante la plus rapide du monde ou une imprimante d’un million de dollars, mais cela n’a aucune importance si vos propriétés matérielles ne peuvent pas supporter l’application pour laquelle elles sont conçues. »,
Dan Dempsey, New Balance Senior Additive Manufacturing Engineer
Repousser les limites de la conception et de la fabrication de chaussures
La collaboration TripleCell marque une nouvelle étape dans les applications de l'impression 3D, en passant du prototypage à la production en série. La technologie de pointe TripleCell est désormais exploitée exclusivement dans les usines New Balance aux États-Unis. L'année prochaine, New Balance prévoit d'augmenter la production de TripleCell à plus de 10 000 paires par an et de poursuivre la croissance au sein de son site de production industrielle.
À l'avenir, TripleCell constitue le fondement de l'exploitation de données uniques sur les athlètes et d'informations éclairées sur les performances afin de créer des chaussures personnalisées dans un nombre illimité de combinaisons et de les produire à la demande, en réduisant les délais de développement et en accélérant la livraison du concept au consommateur.
« Là où nous en sommes aujourd'hui est le fruit du travail réalisé en interne et du partenariat externe avec Formlabs qui a vraiment permis de faire avancer notre programme », déclare Petrecca. « Nous avons démontré que nous sommes capables d'intensifier notre fabrication additive pour la rendre viable à l'échelle de la production industrielle. Pour ce qui est de nos projets futurs, rien n'est impossible. »
En coulisse: la plateforme TripleCell de New Balance et Razor Maker de Gillette
Pour en savoir plus sur l’approche de New Balance en matière d’impression 3D et sur l’utilisation de Formlabs, regardez notre pannel Formlabs User Summit 2019 sur la transformation d’entreprise, avec New Balance et Gillette.