Du concept à la commercialisation en quatre mois : comment Arbutus Medical a utilisé l'impression 3D pour le développement rapide de dispositifs médicaux
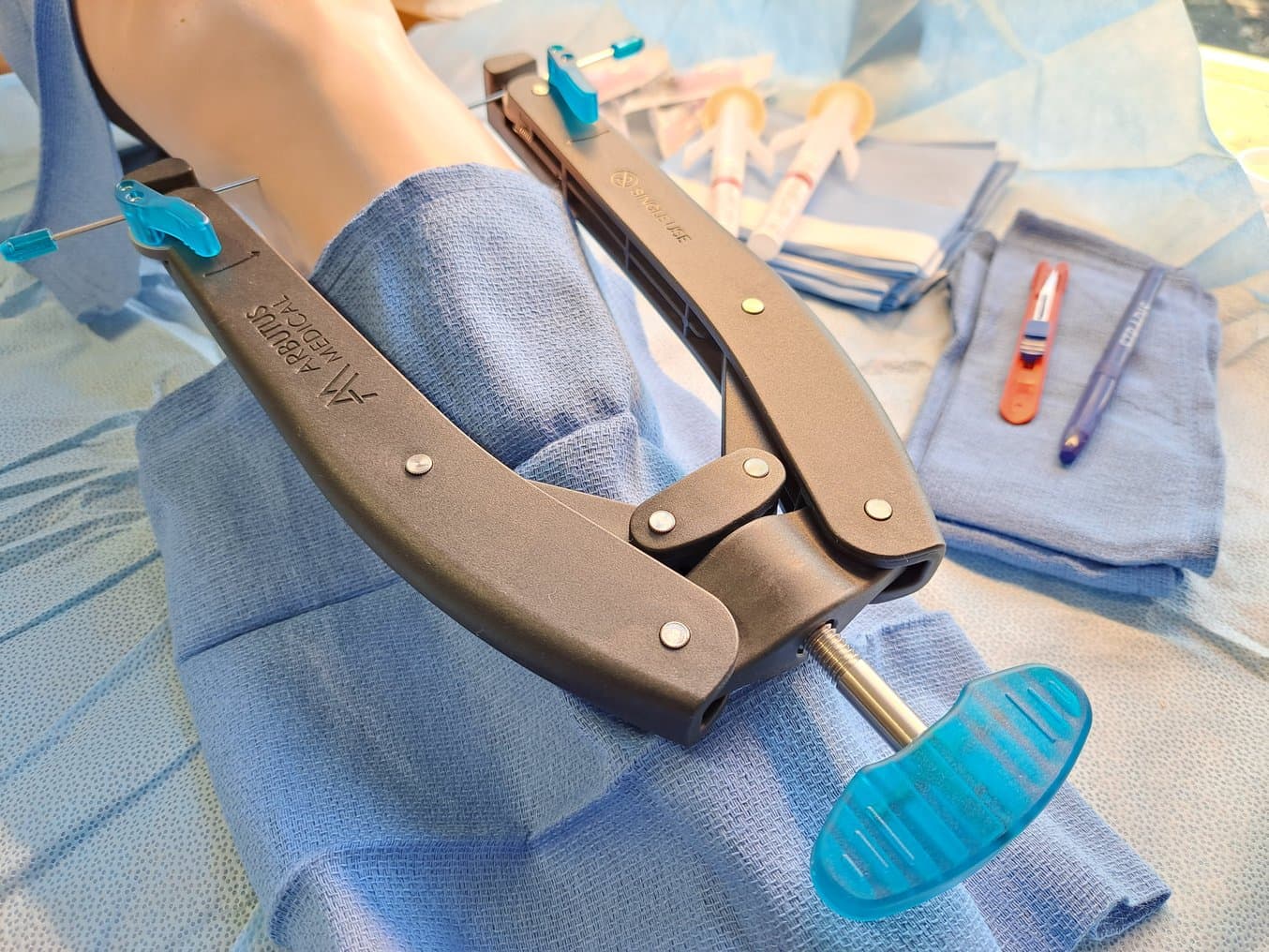
Les chirurgiens qui pratiquent des opérations mineures dans les salles d'urgence des centres de traumatologie ont souvent un accès limité aux outils dont ils ont besoin et doivent suivre des dispositifs médicaux dans d'autres secteurs de l'hôpital, ce qui entraîne des retards dans la durée des traitements. Arbutus Medical cherche à changer cela, en répondant aux difficultés rencontrées par les chirurgiens et les internes grâce à la création de kits de procédure spécialisés. Ces kits nécessitent souvent des instruments à usage unique haute performance afin de simplifier certaines procédures, permettant ainsi aux patients d’être traités plus rapidement et aux médecins de consacrer leur temps aux soins plutôt qu’à la recherche de matériel.
L'impression 3D est la clé de la conception et de la production sur le site Arbutus Medical. Radu Postole, responsable du design produit chez Arbutus Medical, utilise les imprimantes 3D résine Formlabs non seulement pour prototyper des dispositifs médicaux, mais aussi pour en fabriquer dans le cadre de tests sur les facteurs humains et de productions pilotes. Pour le dernier dispositif, un arc de Kirschner, M. Postole a travaillé avec Phil Tsao, ambassadeur de Formlabs et fondateur de Ember Prototypes, une société de prototypage rapide, d'accompagnement technique et de conception de produits, pour tirer parti de l'impression 3D et passer rapidement de l'idée à la commercialisation en un an, en utilisant même l'impression 3D pour la production à grande échelle et en imprimant plus de 800 pièces en un mois.
Pour Arbutus Medical et Ember Prototypes, la fiabilité et la vaste gamme de matériaux de l'écosystème Formlabs ont permis le développement et la production de dispositifs médicaux en une durée record.
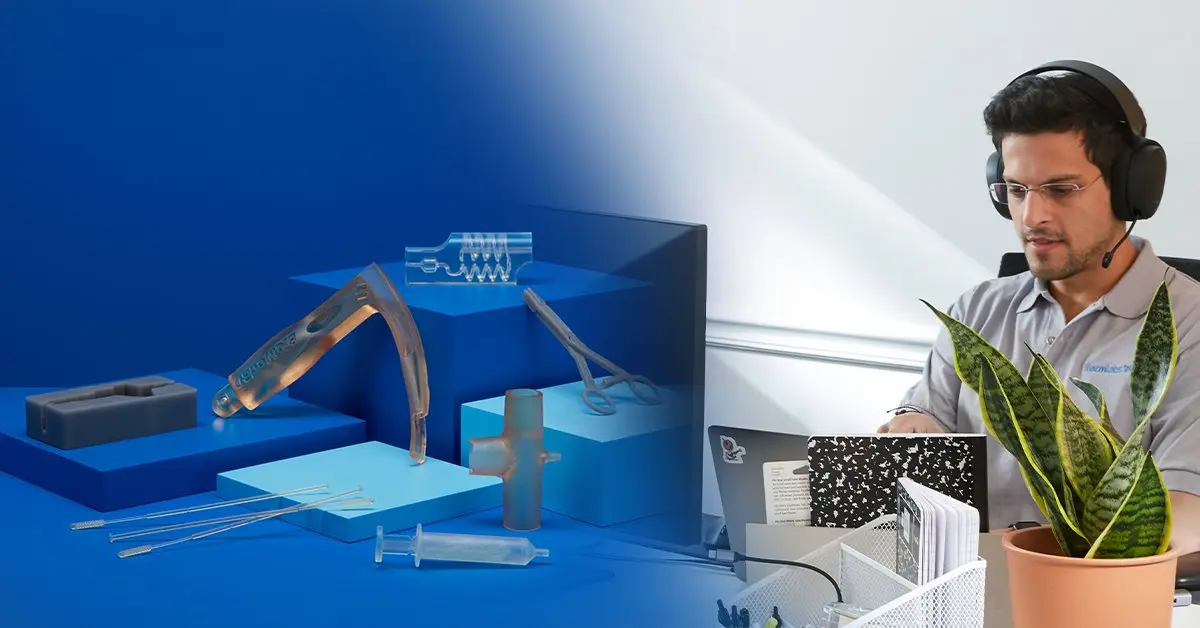
Discutez avec notre équipe commerciale médicale
Que vous deviez fabriquer des outils chirurgicaux adaptés aux patients ou un prototype de dispositif médical cardiaque, nous sommes là pour vous aider. L'équipe de Formlabs Medical est composée de spécialistes dévoués qui savent exactement comment vous soutenir et répondre aux besoins de votre entreprise.
Résoudre les problèmes des centres de traumatologie grâce à des kits de procédure spécialisés
Le TrakPak® d'Arbutus Medical a été lancé en 2021. Le kit est utilisé pour appliquer rapidement une traction squelettique chez les patients ayant subi des fractures du fémur ou du bassin, afin de réduire et stabiliser les fractures en attendant l’intervention chirurgicale. La version originale du kit comprenait une perceuse Dewalt modifiée avec un couvercle stérile et une broche implantable. Lorsque M. Postole a initialement conçu ce dispositif, il a cherché une imprimante 3D pour augmenter la vitesse à laquelle il pouvait prototyper. M. Tsao a recommandé la Form 3+ de Formlabs. Non seulement des éléments du TrakPak® ont été prototypés sur l'imprimante 3D, mais Tsao et Postole ont également pu imprimer rapidement les versions finales en quantités suffisantes pour les études sur les facteurs humains et les tests sur cadavres. Depuis sa mise sur le marché, plus de 4000 patients aux États-Unis ont été traités à l'aide du TrakPak®.
Études sur les facteurs humains avec des dispositifs imprimés en 3D
Les essais sur les facteurs humains peuvent être un processus long, souvent en raison de la durée nécessaire pour se procurer des moules et démarrer la production. Grâce à l'impression 3D, M. Postole a pu fournir rapidement des prototypes fonctionnels qui pouvaient non seulement être testés sur banc et sur cadavre, mais qui ressemblaient aussi au dispositif final. L'esthétique était importante : il fallait supprimer le bruit afin que les commentaires des chirurgiens se concentrent uniquement sur les performances et la valeur des pièces.
« Étant donné qu'il s'agit d'un dispositif médical de classe II, les exigences pour la commercialisation du produit étaient relativement strictes. Nous avons donc dû réaliser une étude très détaillée sur les facteurs humains, et nous l'avons fait entièrement avec les pièces imprimées en 3D. Certaines sociétés pourraient devoir attendre d'avoir réellement les pièces moulées par injection pour réaliser l'étude des facteurs humains, mais nous avons pu enregistrer trois à quatre mois grâce à l'impression 3D. »
Radu Postole, responsable de la conception de produits, Arbutus Medical
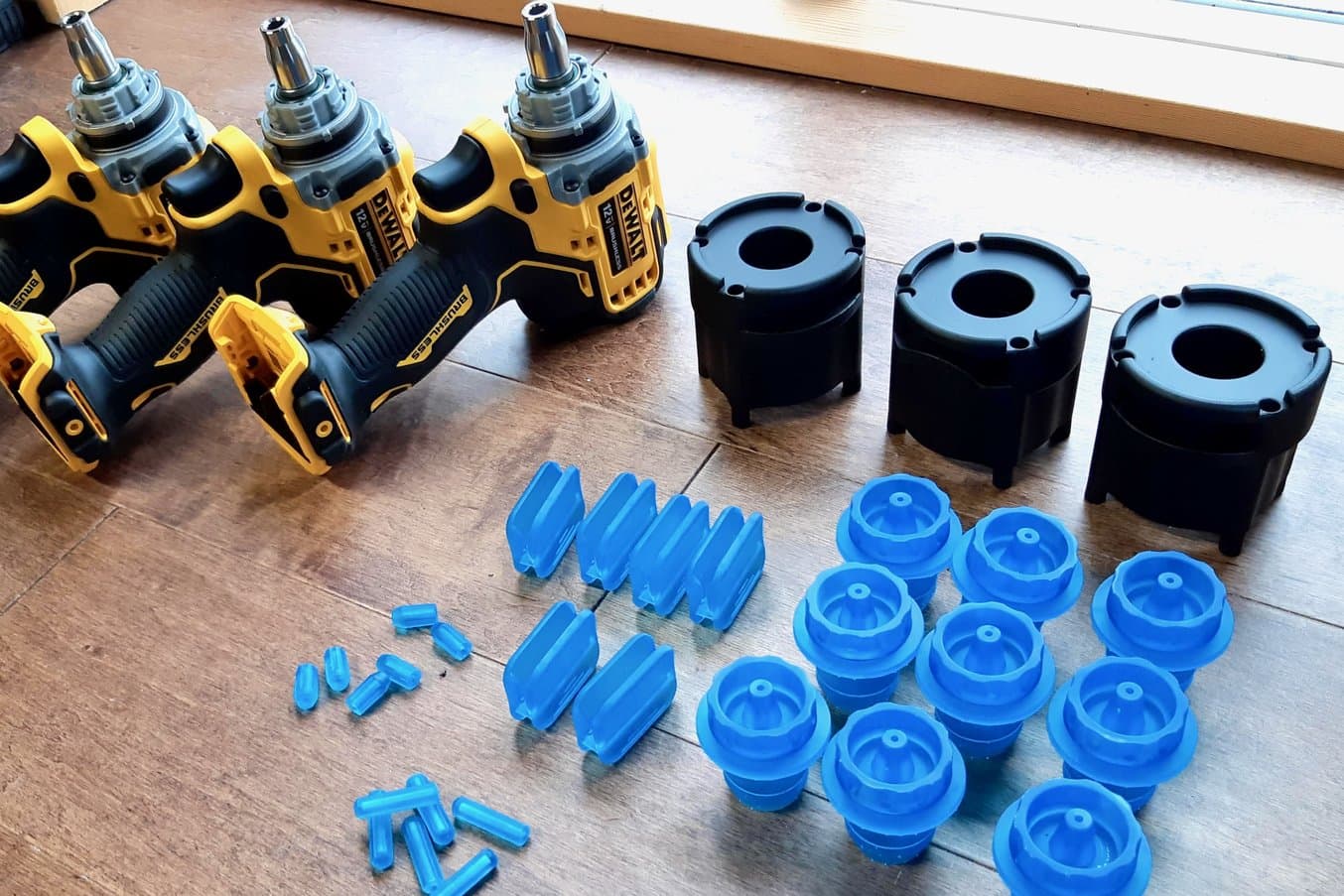
La phase de prototypage du TrakPak® a inclus l'impression 3D d'un adaptateur pour perceuse électrique, ainsi que des composants de broches.
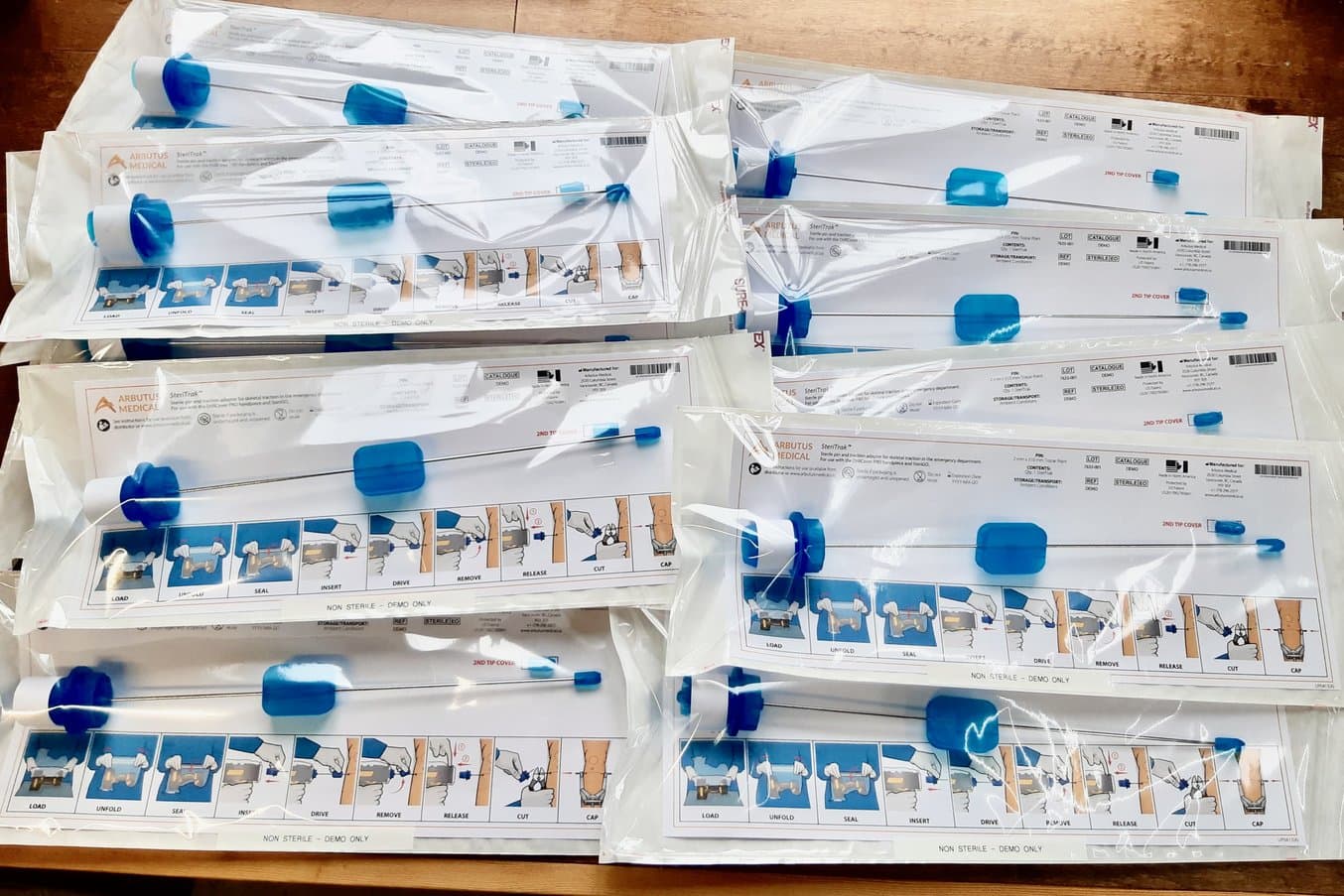
Le TrakPak® est cohérent avec un couvercle stérile à usage unique pour un perçage électrique et une broche implantable. Les composants bleus sur la broche sont imprimés en 3D.
Bien que la première version du TrakPak® ait résolu un problème pour les centres de traumatologie, une collaboration étroite avec les chirurgiens et les internes a mis en lumière un autre problème : l'accès limité des urgences aux broches de Kirschner (K-bow), utilisées par les chirurgiens orthopédiques pour tendre la broche implantée et fournir un moyen d'appliquer une traction sur le squelette. Les problèmes consistent à les suivre et à les récupérer, car ils sont généralement stockés près des salles d'opération mais appliqués dans les salles d'urgence, et à trouver un dispositif qui fonctionne réellement, car les dents de préhension de la broche et le mécanisme de tension s'usent souvent. Non seulement le patient attend dans la douleur que la broche soit récupérée, mais cela fait perdre de la durée aux médecins des services d'urgence. La réponse d'Arbutus Medical a été le tendeur de broches QuikBow®.
Lancé en 2023, QuikBow® réduit le recours aux centres de traitement stérile central (CSP) dans les hôpitaux, et améliore la vitesse et la qualité des soins aux patients. Avec l'aide des imprimantes Form 3, des prouesses d'impression d'Ember Prototypes et de la vaste gamme de matériaux Formlabs, le QuikBow® a été conçu, développé, testé et commercialisé en un an.
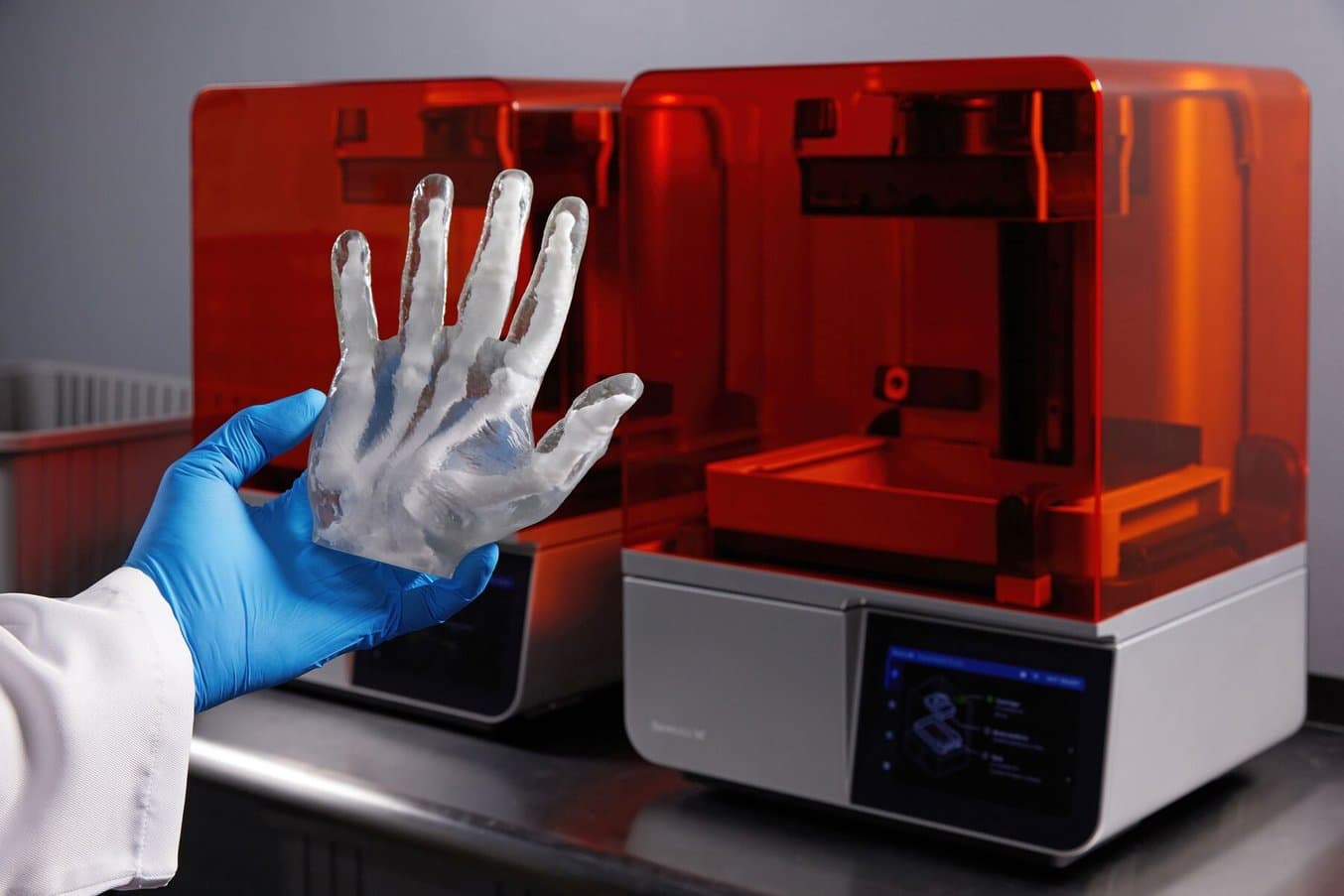
Résines biocompatibles Formlabs : un guide complet pour choisir le bon matériau
Formlabs propose actuellement plus de 40 matériaux uniques pour l'impression 3D stéréolithographique (SLA). Ce document aide les utilisateurs à comparer nos offres biocompatibles et à déterminer l'ajustement le mieux adapté à leurs applications médicales.
Prototypage rapide avec les imprimantes 3D de la série Form et Ember Prototypes
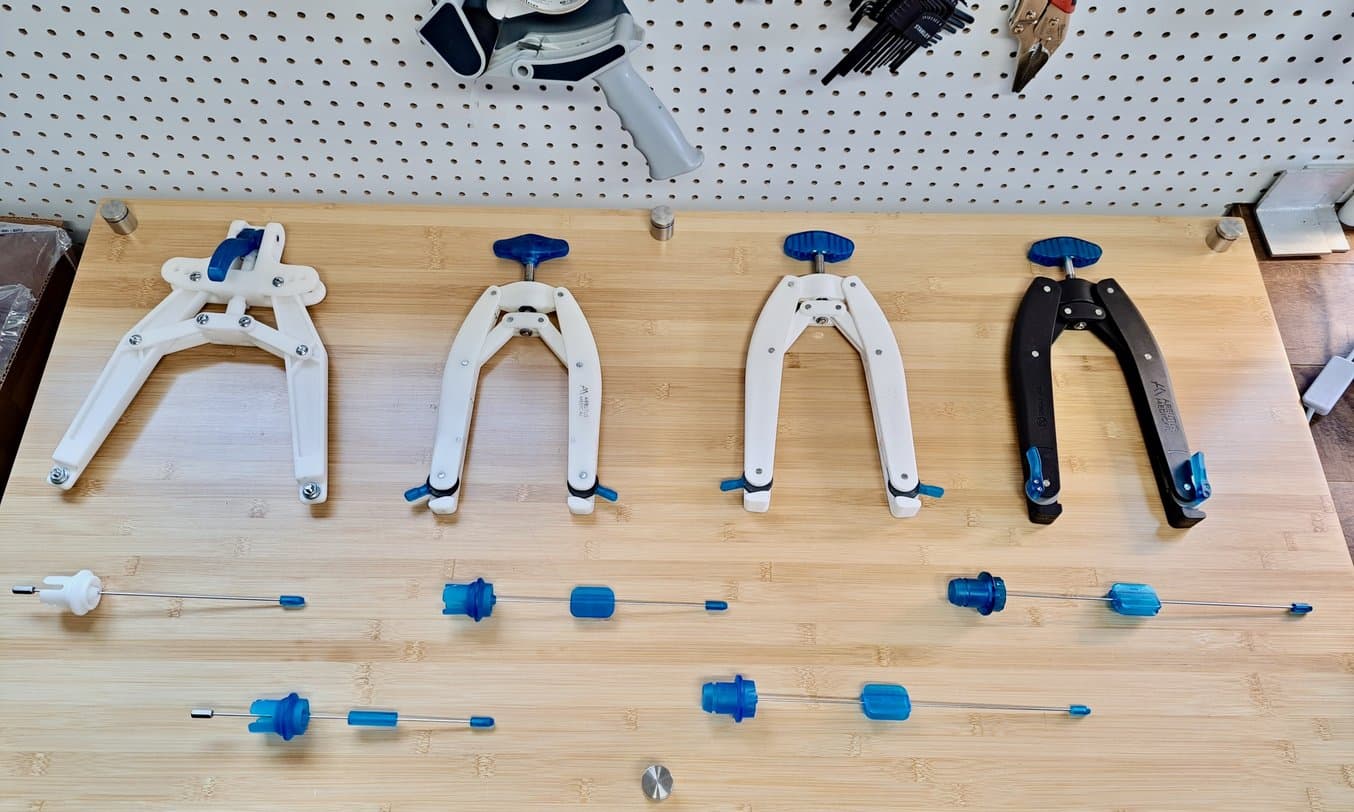
Trois prototypes du QuikBow® (blanc) et du dispositif médical final (noir). Les pièces blanches et bleues ont été imprimées en 3D sur des imprimantes de la série Form 3, et les pièces bleues désignent les points de contact avec lesquels l'utilisateur interagira.
Lors du prototypage du QuikBow®, M. Postole s'est d'abord penché sur l'usinage des pièces de l'arc, notamment les branches. « Mais elles sont tellement massives et nécessitent tellement d'usinage que cela devenait en réalité extrêmement coûteux de faire usiner les bras pour les tests, surtout pour les plus de 30 itérations de conception que nous avons créées. L'impression 3D avec l'imprimante 3D Formlabs s'est avérée être une solution idéale. »
Au fur et à mesure de la conception, M. Postole a contacté M. Tsao chez Ember Prototypes, car les bras qu'il était en train de prototyper ne pouvaient tenir que dans la Form 3L, l'imprimante 3D SLA grand format de Formlabs. M. Tsao a une grande expérience de l'impression 3D et de la gamme de matériaux Formlabs. Il a travaillé avec M. Postole pour évaluer les meilleurs matériaux pour le QuikBow®.
Pour les bras, un matériau rigide était nécessaire. M. Tsao a imprimé les bras dans plusieurs matériaux, notamment Tough 2000 Resin, Rigid 4000 Resin, et Rigid 10K Resin, afin d'aider M. Postole à déterminer le matériau le mieux adapté à son application. En fin de compte, M. Postole a sélectionné Rigid 10K Resin comme étant la meilleure option disponible. En plus d'être tenace, l'arc doit pouvoir tendre la broche à plus de 45 kg et supporter un poids de traction de 18 kg. Pour rendre les prototypes plus résistants, M. Postole a itéré sur la conception de la pièce afin qu'elle résiste aux essais rigoureux nécessaires.
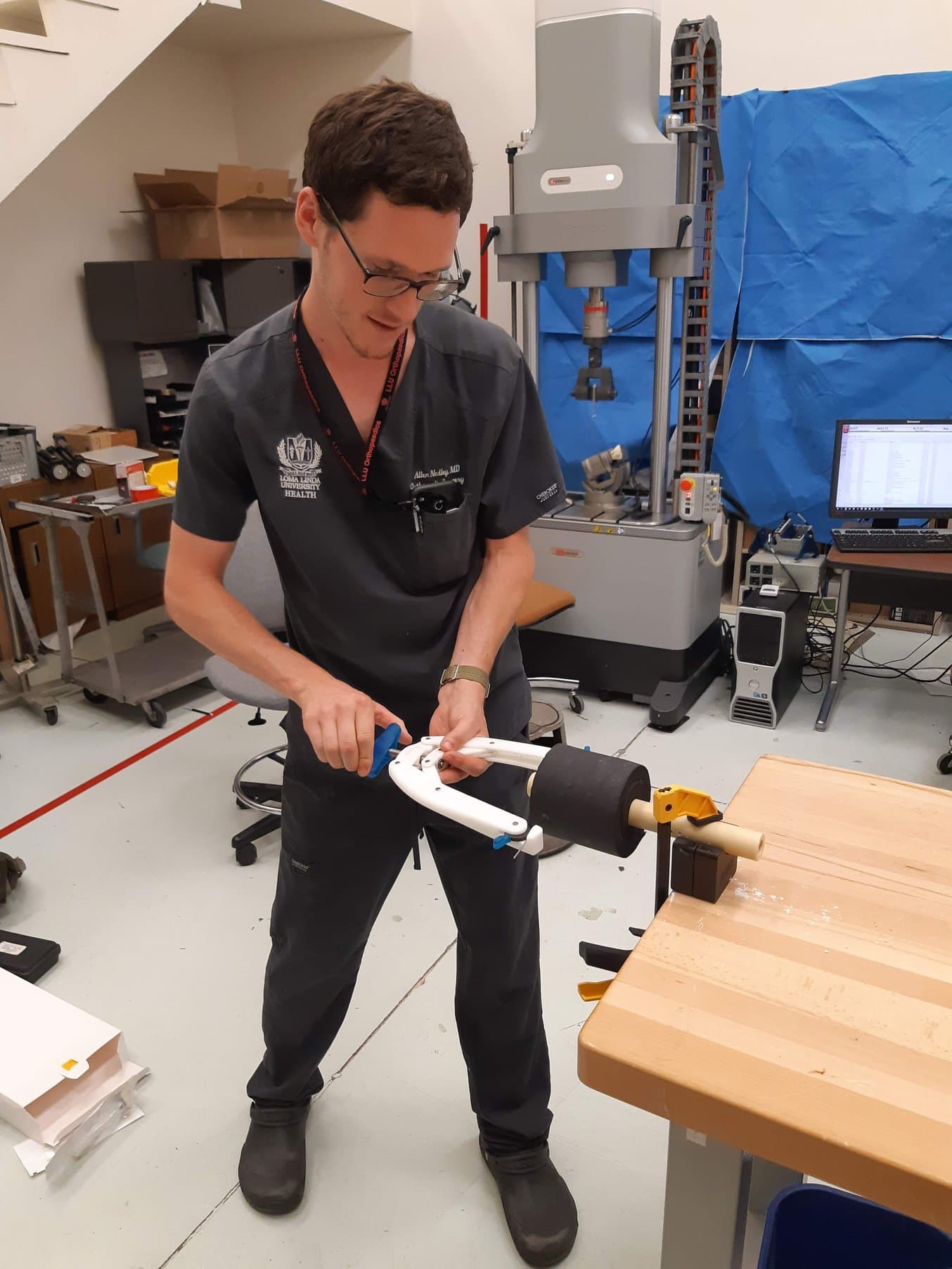
Allen Nedley, MD, chirurgien orthopédique effectuant des essais d'utilisation et de résistance sur un prototype QuikBow® à l'école de médecine de l'université de Loma Linda en Californie.
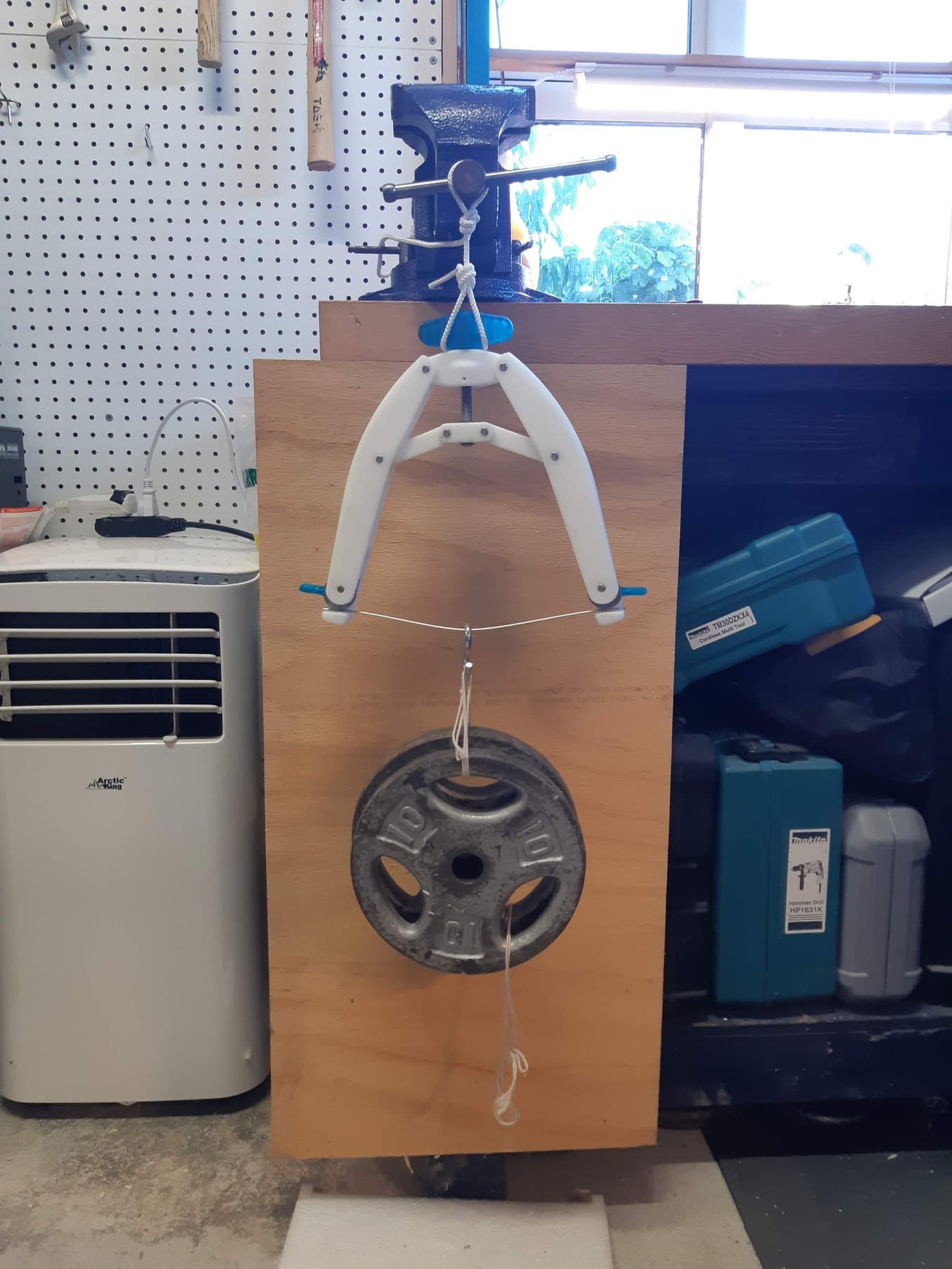
Essai de la broche QuikBow® sur un prototype imprimé en 3D.
« Nous avions des exigences très particulières en matière de résistance, de rigidité et d'esthétique, et nous avons pu y parvenir. Les chirurgiens ont rapidement compris la valeur et les performances du dispositif, même s'il s'agissait de prototypes imprimés en 3D. »
Radu Postole, responsable de la conception de produits, Arbutus Medical
Bien que la qualité esthétique des matériaux ait été un facteur de sélection, M. Tsao a placé manuellement les supports et orienté les fichiers pour s'assurer qu'un post-traitement minimal était nécessaire, afin que les impressions résultantes soient aussi propres que possible, avec une finition de surface cohérente.
« Phil a fait un travail formidable en essayant de comprendre l'utilisation finale des pièces, car cela a vraiment dicté la façon dont il les a paramétrées dans PreForm », explique M. Postole. Quelles sont les facettes esthétiques et quelles sont les caractéristiques critiques ? » Comme ces prototypes étaient envoyés pour des démonstrations et des retours utilisateurs, ils devaient ressembler à des pièces finies. En plaçant des supports internes, M. Tsao a pu livrer des pièces qui ne se distinguaient pas de celles qui avaient été moulées par injection. En plus d'une configuration spécialisée dans PreForm, Tsao a développé et imprimé en 3D un gabarit pour maintenir les pièces lors du lavage afin qu'elles aient une finition uniforme et esthétique.
« La résolution et la finition de la surface avec l'imprimante Formlabs sont si bonnes que la plupart des gens ne pourraient pas dire qu'elle a été imprimée en 3D. »
Radu Postole, responsable de la conception de produits, Arbutus Medical
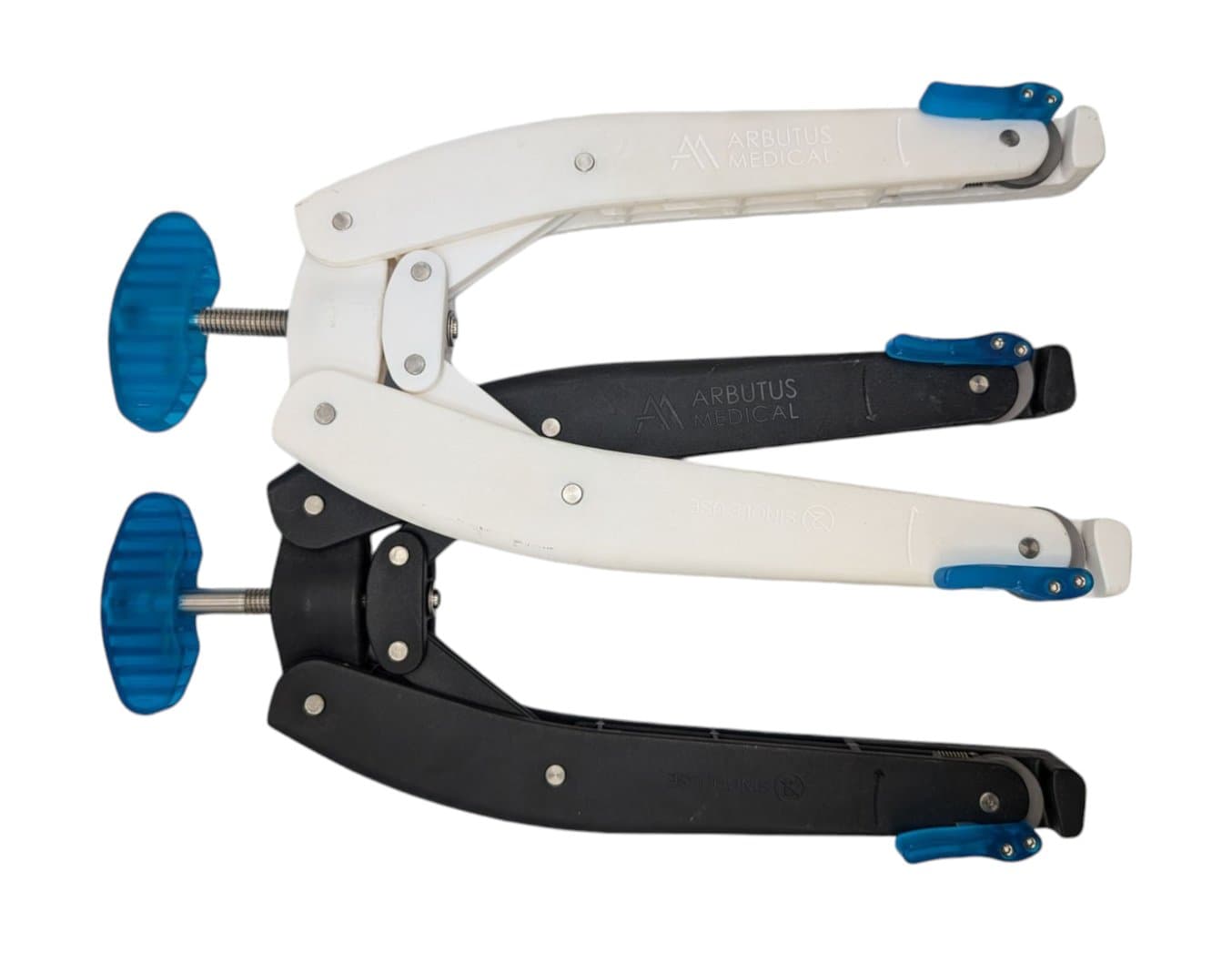
Prototypage imprimé en 3D en Rigid 10K Resin (en haut) et moulé par injection T1 (en bas). Finalement, Arbutus Medical a opté pour une couleur noire pour les dispositifs médicaux finaux, car elle masque mieux les taches de sang que le blanc.
« J'ai encore le prototype Rigid 10K Resin et le T1 moulé par injection. Chaque fois que quelqu'un vient dans mon atelier, je l'affiche comme un exemple de ce que nous pouvons faire. Les gens sont toujours époustouflés par la qualité de l'assemblage en Rigid 10K Resin. Ils ne font pas la différence avec le moulage par injection, si ce n'est la couleur. »
Phil Tsao, fondateur d'Ember Prototypes
Au cours de cette phase de prototypage, explique M. Tsao, « nous avons itéré presque toutes les semaines. Tous les trois ou quatre jours, Radu envoyait une nouvelle itération que nous imprimions et lui envoyions. Il s'agissait d'avoir un bras de prototypage rapide qui ne faisait pas partie de votre propre société, il est juste externe. »
L'un des avantages de la collaboration avec Ember Prototypes a été la durée. Grâce à l'impression des bras par M. Tsao, la Form 3+ de Postole a pu imprimer d'autres composants en interne, ce qui lui a permis de continuer à itérer rapidement. En tout, M. Postole et M. Tsao ont réalisé plus de 30 séries de prototypes en quatre mois, y compris des itérations quotidiennes qui ont été expédiées le lendemain aux chirurgiens pour obtenir leur retour.
Une partie de ce processus a consisté à analyser les réponses des utilisateurs sur la facilité d'utilisation, les performances et la perception de la valeur, une raison essentielle pour laquelle les prototypes imprimés en 3D devaient ressembler à des dispositifs finis, moulés par injection.
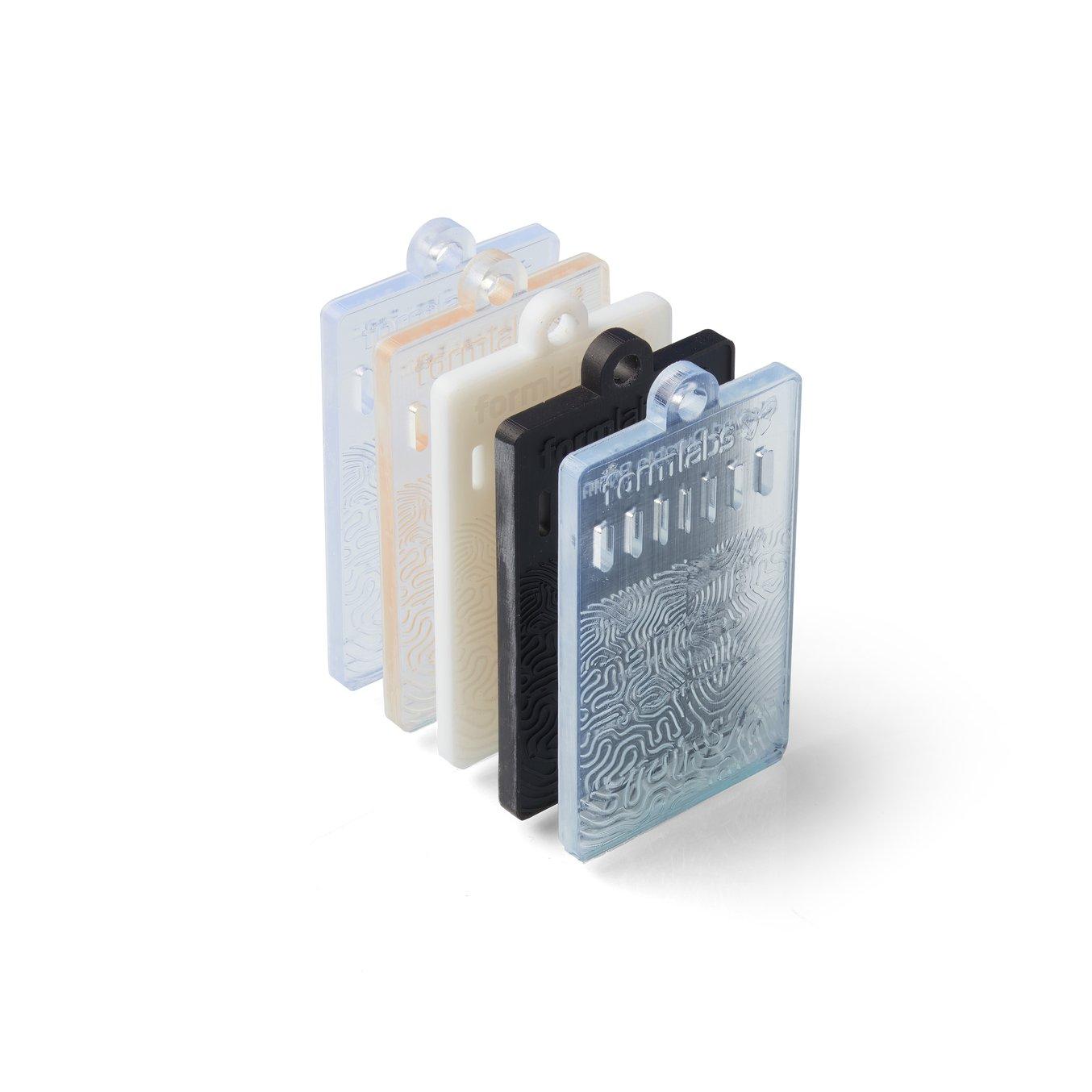
Échantillons en BioMed Resin
Chaque échantillon de résine BioMed présente des motifs en relief et en creux, des épaisseurs de découpe de 0,5 à 2,0 mm, ainsi que des informations réglementaires propres à cette résine.
Raffiner les dispositifs médicaux commercialisés
QuikBow® a été lancé au début de l'année 2023. En l'espace de quelques mois, Arbutus Medical a reçu des retours indiquant que le personnel des salles d'urgence trouvait que le QuikBow® permettait d'accélérer et d'améliorer les soins aux patients. Cependant, elle nécessitait toujours l'utilisation d'un cadre de lit pour tirer la traction vers le haut, en soulevant le dispositif du tibia du patient.
Les sommiers sont des éléments encombrants qui nécessitent une installation, un stockage et un suivi particuliers, ce qui entraîne une perte de temps et de ressources dans les hôpitaux. Pour remédier à ce problème, Radu et l'équipe de conception d'Arbutus ont eu une idée : ils ont conçu des adaptateurs pour le QuikBow® avec des charnières latérales qui soulèvent l'arc de manière à ce qu'il ne touche pas le tibia du patient. « Grâce à cette innovation, nous avons pratiquement éliminé le besoin de notions de base et de systèmes de poulies conventionnels dont l'approvisionnement peut prendre jusqu'à deux heures dans l'ensemble de l'hôpital », explique M. Postole.
L'ajout des points de charnière est intervenu trois mois après la commercialisation du QuikBow®. « Nous avons rapidement imprimé en 3D différentes itérations de cet accessoire, et les avons envoyées à nos chirurgiens de confiance. Ils l'ont tellement aimé qu'ils l'ont voulu tout de suite », explique M. Postole. « C'est là que la Form 3B+ est intervenue. Nous savions qu'en choisissant le bon matériau, nous pourrions mettre immédiatement cette nouvelle fonction du produit entre les mains des chirurgiens. »
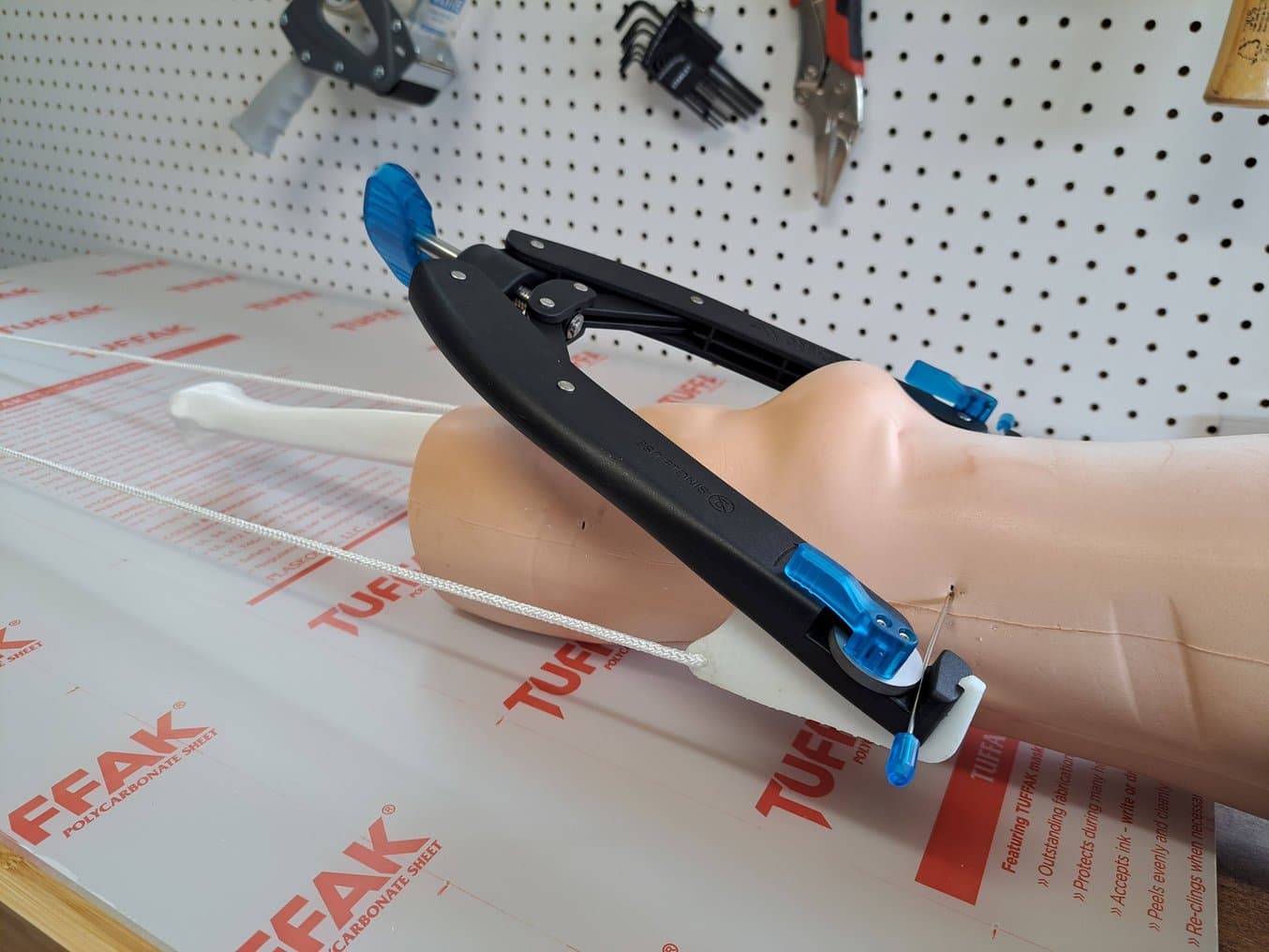
Un premier prototype des points de charnière pour le QuikBow®. En plaçant une tension sur les charnières, l'arc est dégagé du tibia, ce qui réduit le risque d'escarres.
Pour les pièces biocompatibles, M. Postole souhaitait une résine transparente utilisable avec les autres pièces translucides de l'assemblage. Il a donc choisi BioMed Clear Resin et BioMed Durable Resin, et a finalement sélectionné BioMed Durable Resin pour sa résistance supérieure aux chocs, en remarquant que « les deux matériaux étaient très résistants pour notre application. Bien que BioMed Clear Resin ait passé avec succès notre essai d'impact initial, BioMed Resin nous a donné une plus grande ligne marginale de sécurité en cas d'impacts répétés. »
En quelques mois, Arbutus Medical produisait les premières unités cliniques ayant été approuvées par leur système de qualité.
« Nous avons effectué tous les essais, toutes les vérifications, avec des pièces imprimées en 3D. Il s'agissait essentiellement d'un projet de quatre mois, de l'idée à la pièce commercialisable. »
Radu Postole, responsable de la conception de produits, Arbutus Medical
Pour la plupart des dispositifs conventionnels, il faut plus de trois mois pour faire fabriquer les moules et démarrer le moulage des pièces. Compte tenu de tous les obstacles qu'un dispositif médical doit franchir pour être utilisé dans un hôpital, Arbutus Medical souhaitait pouvoir mettre en œuvre l'amélioration immédiatement, sans attendre les moules. Une autre méthode de production était donc nécessaire.
L'impression 3D pour une production provisoire avec Ember Prototypes
Souhaitant un retour d'information continu sur les nouveaux points d'articulation de l'arc tout en continuant à fournir le QuikBow® aux chirurgiens, M. Postole ne voulait pas s'engager à fabriquer des moules pour les points d'articulation de l'arc, car les moules coûtent 25 000 $ et ne peuvent pas être facilement modifiés une fois qu'ils ont été produits. M. Postole explique : « C'est là que la Form 3B a été utilisée, car c'était une transition provisoire parfaite : nous avons simplement continué à les imprimer en 3D. Finalement, la demande est devenue si forte que nous ne pouvions plus suivre en interne, et c'est là qu'Ember est intervenu et a essentiellement pris en charge toute l'impression 3D. »
L'impression 3D permet non seulement une production rapide, mais aussi une production utilisant les mêmes flux de travail que ceux utilisés lors du prototypage, pour une efficacité accrue. De plus, en ajoutant des lots d'impression ou des imprimantes, la production peut facilement être adaptée à l'augmentation de la demande.
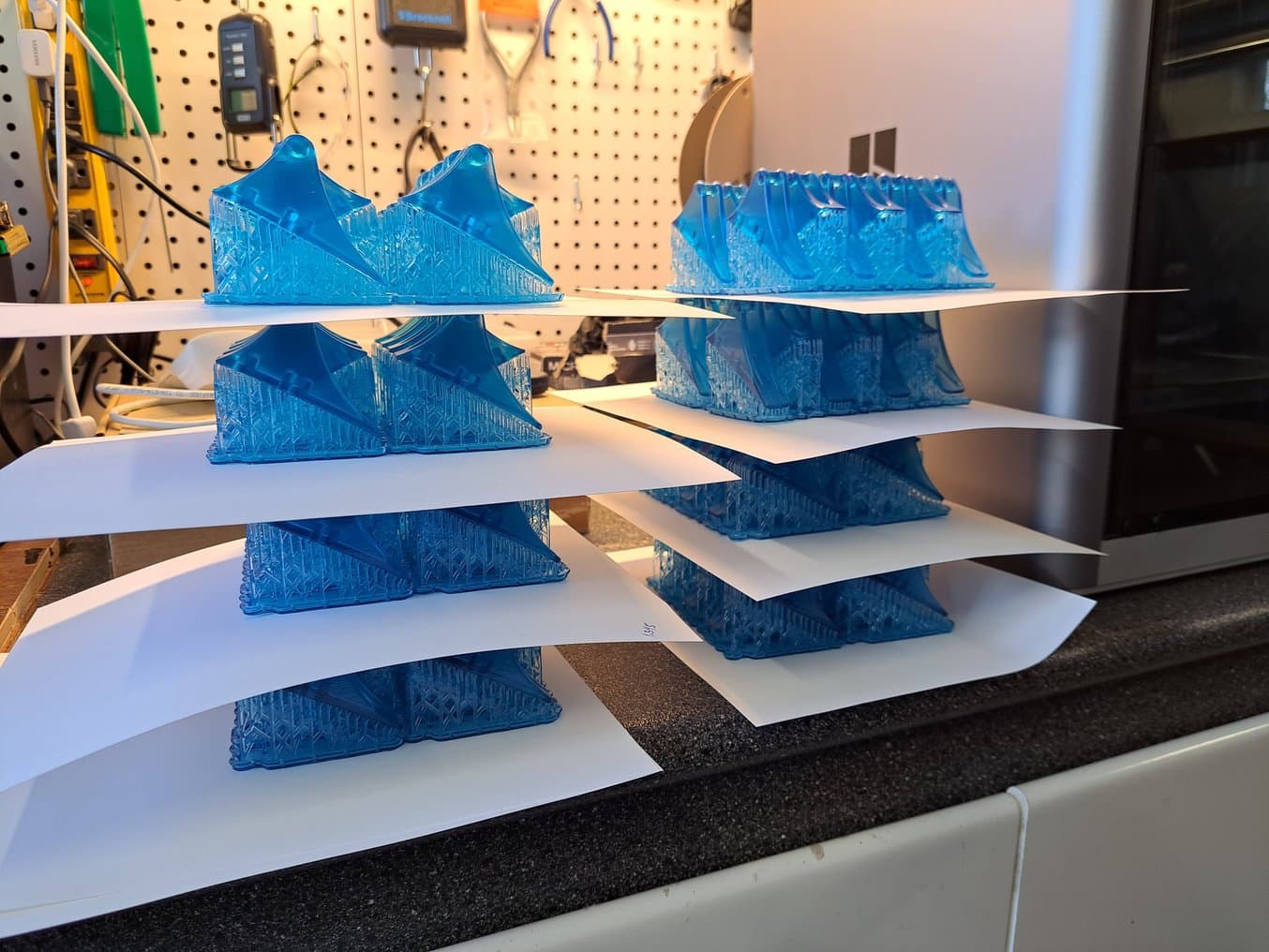
Des séries de production limitées de la charnière QuikBow® ont été imprimées sur la Form 3B+.
La demande augmentant, Arbutus Medical a sous-traité l'impression 3D des charnières à Ember Prototypes, où M. Tsao imprimait deux lots de pièces par jour. Cette production provisoire a permis à Arbutus Medical d'aider à améliorer les soins aux patients et de démarrer la production du nouveau produit cinq à six mois plus tôt, tout en réduisant le risque en n'ayant pas à investir dans des moules coûteux avant d'avoir reçu davantage de retours cliniques.
Au début, Arbutus Medical pensait avoir besoin de 200 à 500 pièces au total, mais très vite, Tsao imprimait environ 200 pièces par semaine (14 pièces par impression, deux impressions par jour) et livrait environ 800 pièces par mois. L'impression 3D à ce niveau de production impliquait des considérations particulières, notamment le lavage et l'agencement des pièces. M. Tsao a conçu et imprimé en 3D un gabarit personnalisé pour tenir les pièces lors du lavage, afin de garantir la meilleure finition esthétique. Lors de l'agencement des pièces, il a constaté que le papier ou d'autres matériaux pouvaient laisser des fibres sur les pièces, mais que le fait de les placer dans des sacs en plastique permettait de les garder propres. Ces ajouts au flux de travail ont permis à M. Tsao de livrer des pièces ayant l’apparence et la texture de pièces moulées par injection, sans les coûts élevés associés et tout en permettant de continuer à affiner la conception.
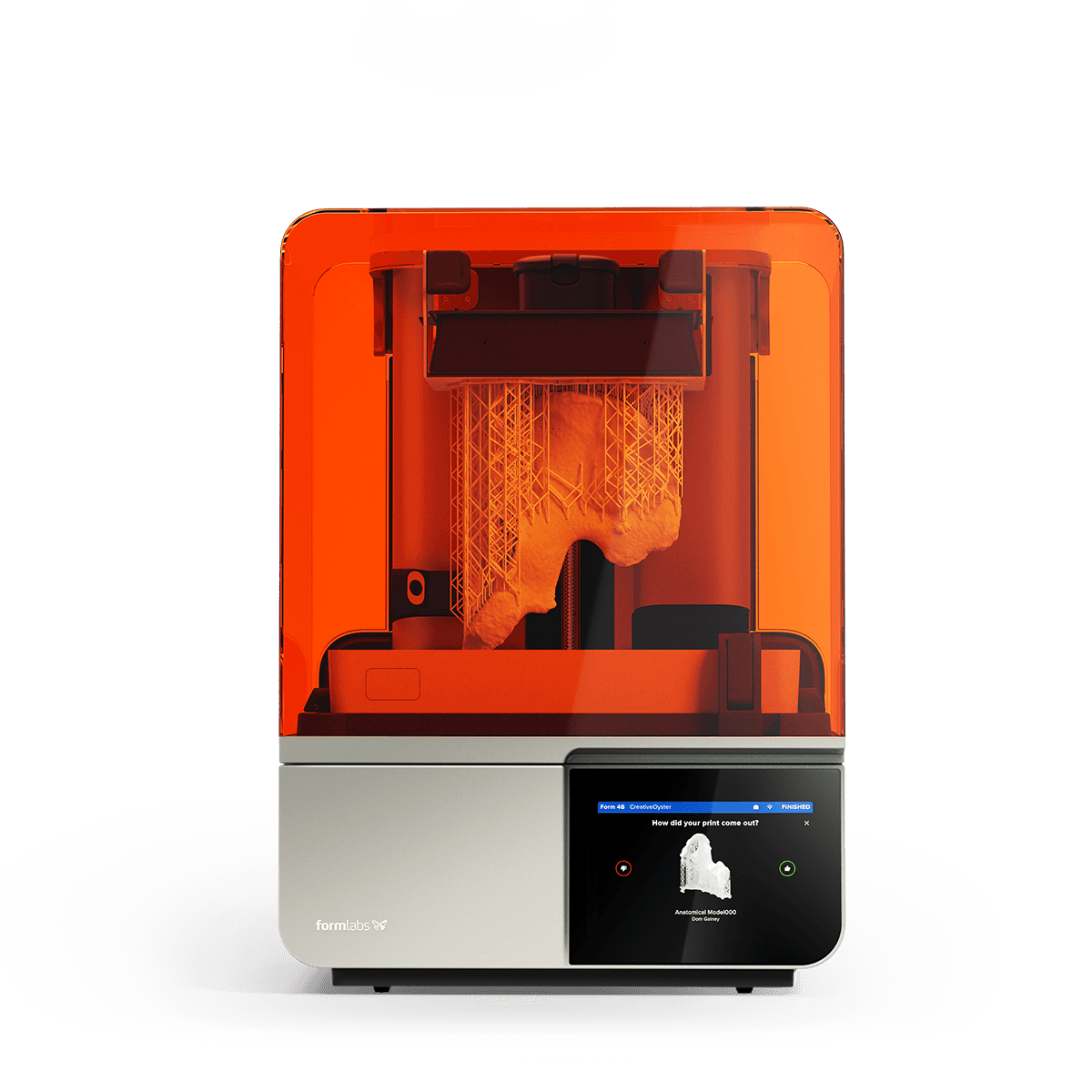
Introduction à la Form 4B : production plus rapide, précision accrue et conformité réglementaire
L'équipe de Formlabs Healthcare présente notre dernier produit, la Form 4B. Après une présentation technique, Bradley Heil, responsable qualité et réglementation chez Formlabs, aborde les aspects réglementaires de la fabrication de dispositifs médicaux à l'aide des imprimantes 3D Formlabs.
Les moteurs du prototypage et de la production : les imprimantes 3D de la série Form

Form Wash, Form 3B et Form 3L chez Ember Prototypes. M. Tsao utilise la Form 3B pour la production de pièces biocompatibles et la Form 3L pour l'impression grand format.
M. Tsao utilise les imprimantes résine Formlabs depuis la sortie de la Form 2. Depuis, il utilise la Form 3, la Form 3B pour l'impression biocompatible et la Form 3L pour l'impression grand format.
« Pour moi, le principal facteur est la facilité d'utilisation dès la sortie de la boîte, puis la sélection des matériaux. Je travaille non seulement avec des gens comme Radu, mais aussi avec beaucoup d'autres startups et sociétés d'ingénierie et de technologie, et tout le monde a des exigences très différentes. Certaines personnes ont besoin de pièces à faible frottement. Certaines personnes ne se soucient que de l'esthétique. Certaines personnes ont besoin d'une très grande rigidité, comme Radu et Arbutus. Pouvoir disposer de cette vaste gamme de matériaux et savoir exactement quelles sont les propriétés mécaniques et à quel point elles sont reproductibles est vraiment important pour Ember. »
Phil Tsao, fondateur d'Ember Prototypes
Jusqu'en 2019, M. Postole utilisait des imprimantes à dépôt de fil fondu. « Nous n'arrivions pas à obtenir les performances de l'impression FDM. Les pièces n'étaient pas solides. Les buses se bouchaient constamment. Cela demandait des interactions fréquentes et nous faisait perdre beaucoup de temps », a déclaré M. Postole. Il a demandé à M. Tsao de lui recommander une imprimante 3D et, « dès qu'il nous a recommandé la Form 3 et que nous l'avons eue, nous avons été époustouflés par les pièces solides et par la possibilité de faire des impressions répétées sans aucun problème. »
En fin de compte, explique M. Postole, « le fait de pouvoir imprimer en 3D des dispositifs à usage clinique nous a permis à la fois d'arriver rapidement sur le marché, et de valider rapidement la valeur et l'adéquation du produit au marché. »
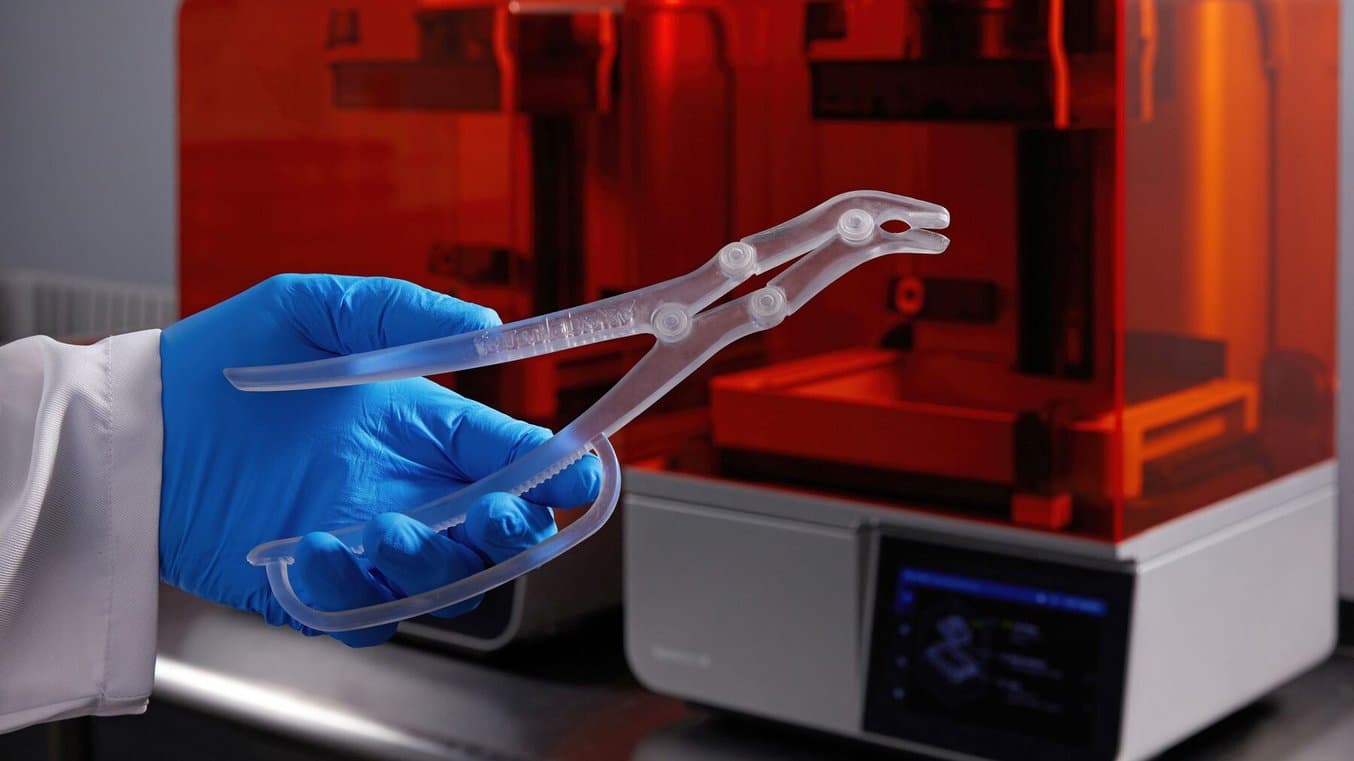
Du prototypage à la production : comment l'impression 3D en interne améliore le développement des dispositifs médicaux
Les dispositifs médicaux ont généralement des cycles de développement plus longs que les biens consommables, en partie à cause des essais cliniques, de la qualité et des exigences réglementaires. La réduction du nombre de cycles de prototypage, voire l'impression directe en 3D de dispositifs finaux, peut avoir un impact significatif sur la vitesse de mise sur le marché.
Ce que réserve l'avenir
Initialement, M. Postole pensait qu'Arbutus Medical imprimerait indéfiniment en 3D les points de charnière adaptatifs pour QuikBow®. Toutefois, lorsqu'il s'est rendu compte qu'ils étaient en passe de produire environ 10 000 pièces par an, Arbutus Medical a procédé à une analyse des coûts et a choisi de s'orienter vers le moulage par injection une fois que les chirurgiens ont confirmé que la conception n'avait pas besoin d'être modifiée. Pour le prochain dispositif qu'il est en train de mettre au point, Radu envisage de recourir à l'impression 3D pour la production, en évaluant les propriétés des matériaux, les options et les coûts.
« À mesure que les propriétés des matériaux s'améliorent, que les coûts baissent et que la vitesse d'impression augmente, je vois clairement comment nous pourrions, pour beaucoup plus d'appareils, simplement imprimer en 3D plus longtemps, jusqu'à ce que nous ayons besoin de 10 000 par an. »
Radu Postole, responsable de la conception de produits, Arbutus Medical
Pour Arbutus Medical, l'impression 3D et le moulage par injection sont deux méthodes de fabrication importantes. Grâce à l'impression 3D, il est possible de produire des prototypes visuels et fonctionnels, de continuer à affiner le produit aux premiers stades de la commercialisation et d'assurer une production temporaire en attendant les moules.
« Nous bénéficions désormais d'un flux de travail qui fonctionne comme il se doit. Nous utilisons la Form 3 pour fabriquer des prototypes rapides et de haute fidélité qui impressionnent nos utilisateurs finaux, comme les chirurgiens. Nous avons quelque chose qui fonctionne très bien pour nous et nous allons simplement continuer à itérer et à trouver de nouvelles façons d'aider à améliorer les soins aux patients. »
Radu Postole, responsable de la conception de produits, Arbutus Medical
Arbutus Medical et Ember Prototypes continuent à travailler ensemble. La diversité des projets sur lesquels M. Tsao travaille chez Ember Prototypes révèle des points problématiques en matière de fabrication et de production, et il est déterminé à les résoudre dans le cadre de l'aide qu'il apporte à ses clients, notamment Arbutus Medical.
« Nous avons fabriqué des produits internes qui résolvent spécifiquement les problèmes dans la fabrication, l'impression 3D et la production. Nous commençons maintenant à les transformer en nos propres produits. L'écosystème Formlabs en est une partie assez importante. »
Phil Tsao, fondateur d'Ember Prototypes
Explorez les ressources sur l'impression 3D pour le développement de dispositifs médicaux, ou adressez-vous à un expert en impression 3D pour en savoir plus sur l'utilisation des imprimantes 3D pour vos besoins en matière de prototypage, de fabrication et de production.