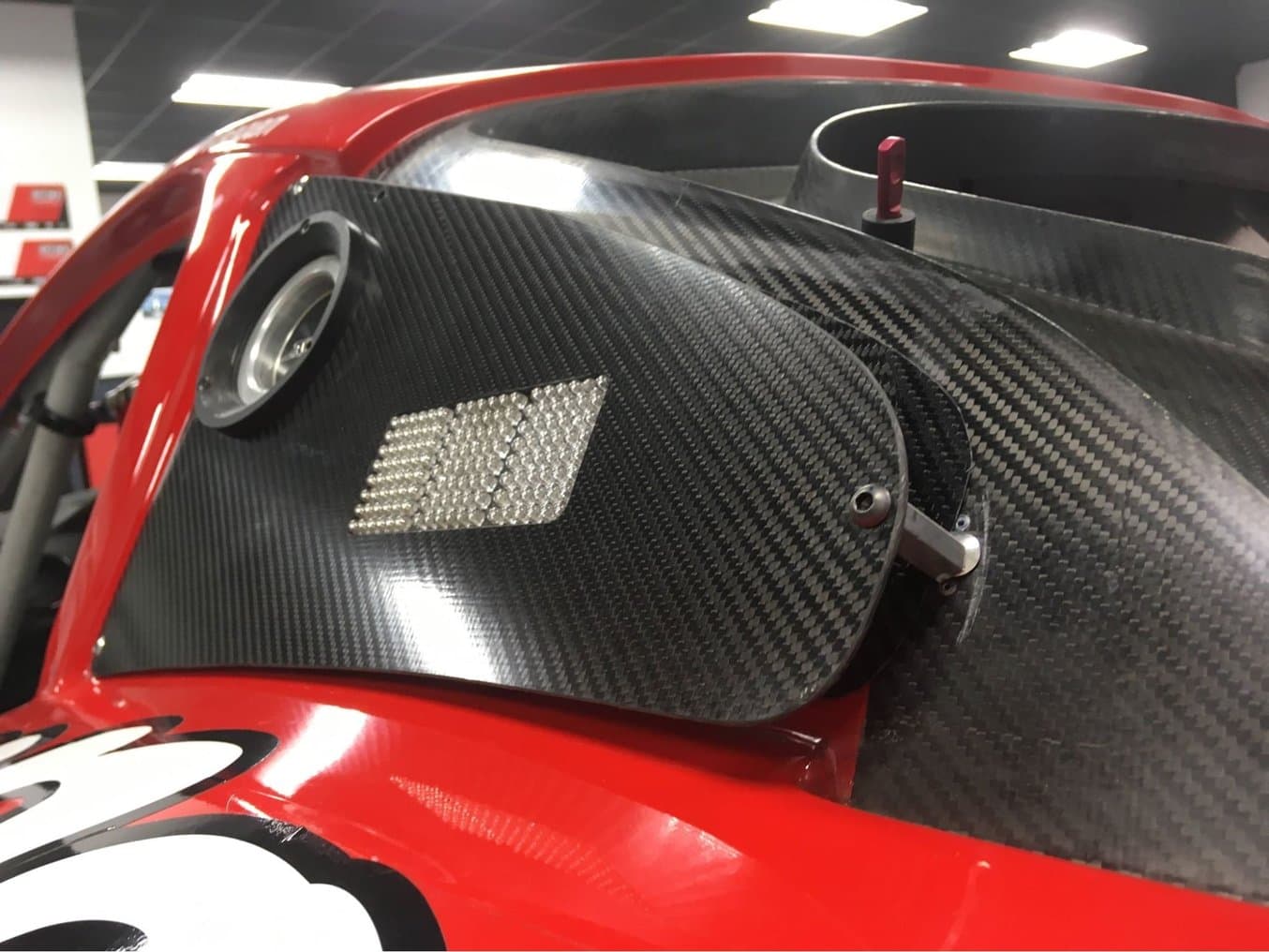
Les matériaux composites, tels que les plastiques renforcés par des fibres de carbone sont des matériaux extrêmement polyvalents et efficaces qui sont à la pointe de l’innovation sur des marchés tels que l’aérospatiale ou la santé. Ils surclassent les matériaux traditionnels tels que l’acier, l’aluminium, le bois ou le plastique et permettent de fabriquer des produits ultra-performants et légers.
Dans ce guide, vous apprendrez les bases de la fabrication de pièces en fibre de carbone, y compris les différentes méthodes de stratification, de laminage et de moulage de la fibre de carbone, et comment vous pouvez utiliser l'impression 3D pour fabriquer des moules en fibre de carbone afin de réduire les coûts et de gagner du temps.
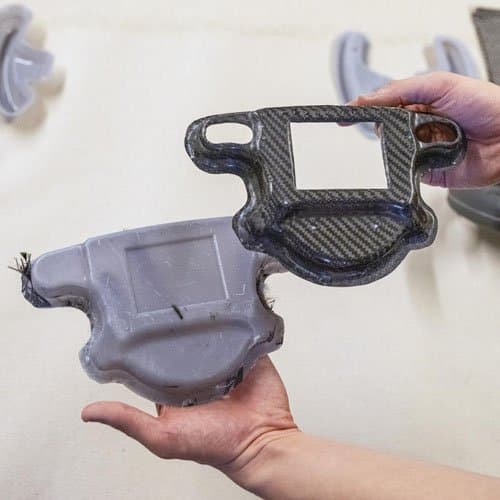
La fabrication de pièces en fibre de carbone avec des moules imprimés en 3D
Téléchargez ce livre blanc pour obtenir des instructions de conception de moules ainsi que des guides étape par étape concernant les méthodes de pré-imprégnation et de laminage manuel pour créer des pièces en fibre de carbone.
Le b. a.-ba des matériaux composites
Un matériau composite résulte de l’association d’au moins deux composants et présente des caractéristiques différentes de ses composants individuels. Les propriétés techniques, comme par exemple la résistance, l’efficacité ou la durabilité, sont généralement améliorées. Les matériaux composites sont constitués d’un renfort(fait de fibres ou de particules) rigidifié par une matrice (polymère, métallique ou céramique).
Les polymères renforcés de fibres (PRF) dominent le marché et ont favorisé l’émergence de nouvelles applications dans différents secteurs. Parmi eux, la fibre de carbone est un composite courant principalement utilisé dans les avions, les voitures de course et les vélos, car elle est plus de trois fois plus solide et rigide que l’aluminium tout en étant 40 % plus légère. Elle est composée de fibres de carbone renforcées solidarisées par une résine époxy.
Les fibres peuvent être non tissées et orientées parallèlement de manière stratégique afin d’être plus résistantes par rapport à un vecteur précis. Elles peuvent aussi être tissées pour offrir une résistance selon plusieurs vecteurs, ce qui donne par ailleurs le motif caractéristique des pièces en matériau composite. Une combinaison de ces deux techniques est souvent utilisée pour produire les pièces composites. Il existe plusieurs types de fibres, dont :
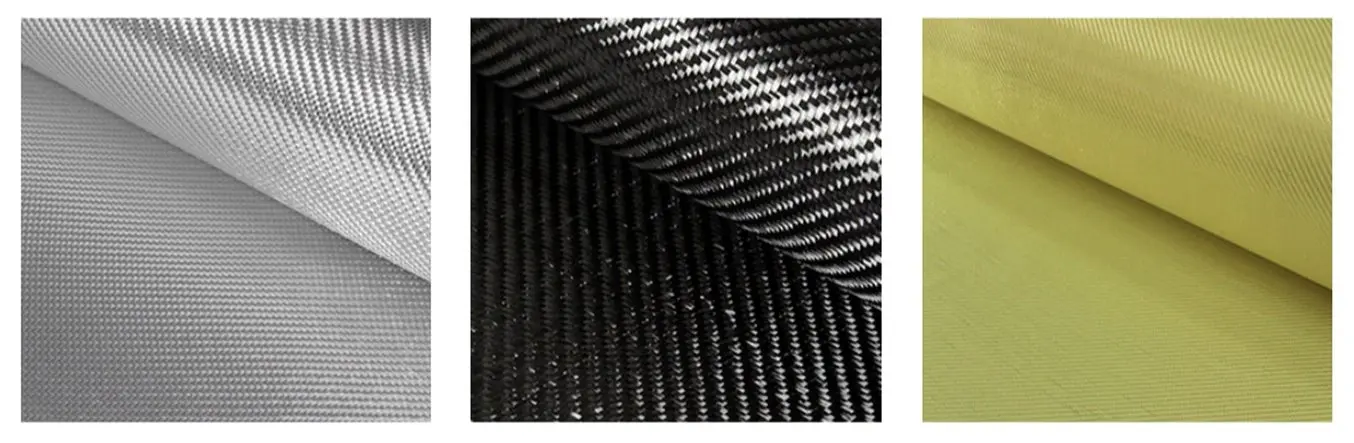
La fibre de verre | La fibre de carbone | La fibre d’aramide (Kevlar) |
---|---|---|
La fibre la plus populaire Légère, résistance modérée à la traction et à la compression Abordable et facile à utiliser | Le ratio solidité et rigidité-poids le plus élevé du secteur (la meilleure résistance à la rupture par traction, flexion et compression) Plus chère que les autres fibres | Résistance aux chocs et à l’abrasion supérieure à la fibre de carbone Faible résistance à la compression Difficile à couper ou à usiner |
De la résine est utilisée pour maintenir ces fibres entre elles et créer un composite rigide. Parmi les centaines de résines différentes qui peuvent être utilisées, voici les plus courantes :
Résine | Avantages | Inconvénients | Polymérisation |
---|---|---|---|
Époxy | La meilleure résistance à la rupture Le poids le plus léger La durée limite de stockage la plus longue | La plus chère Sensible aux variations de proportions et de température du mélange | Utilise un durcisseur spécifique (système bicomposant) Certains époxys nécessitent de la chaleur |
Polyester | Utilisation facile (le plus répandu) Résistant aux UV Le moins coûteux | Faibles solidité et résistance à la corrosion | Nécessite un catalyseur pour polymériser (PMEC) |
Vinylester | Associe les caractéristiques de l’époxy au coût du polyester Meilleurs résistance à la corrosion, thérmorésistance et allongement | Solidité inférieure à l’époxy et coût supérieur au polyester Durée limite de stockage courte | Nécessite un catalyseur pour polymériser (PMEC) |
Trois méthodes pour créer des pièces en fibre de carbone
La fabrication de PRF tels que des pièces en fibre de carbone est un processus précis et nécessitant une main-d’œuvre importante utilisé dans la production en série comme dans la production ponctuelle. Les durées de cycle vont d’une à 150 heures en fonction de la taille et de la complexité de la pièce. Dans la fabrication de PRF habituelle, les fibres droites et continues sont disposées dans la matrice pour former des feuilles qui sont ensuite stratifiées couche après couche sur la pièce finale.
Les propriétés du composite résultent aussi bien des matériaux employés que du processus de stratification : la manière dont les fibres sont appliquées influence grandement les caractéristiques de la pièce. La résine thermodurcissable et son renfort sont mis en forme dans un outil ou un moule, puis polymérisés pour former un produit robuste. Il existe différentes techniques de stratification qui peuvent être classées en trois types principaux :
1. Stratification en voie humide
Dans le drapage en voie humide, la fibre est découpée et disposée dans le moule, puis enduite de résine à la brosse, au rouleau ou au pistolet. C’est la méthode qui nécessite le plus de compétences pour créer des pièces de haute qualité, mais c’est également le processus de travail le moins coûteux et le moins exigeant pour se lancer dans la création de pièces en fibre de carbone faites maison. Si vous débutez dans la fabrication de pièces en fibre de carbone et que vous ne possédez pas encore d’équipement, nous vous recommandons de commencer par le drapage manuel en voie humide.
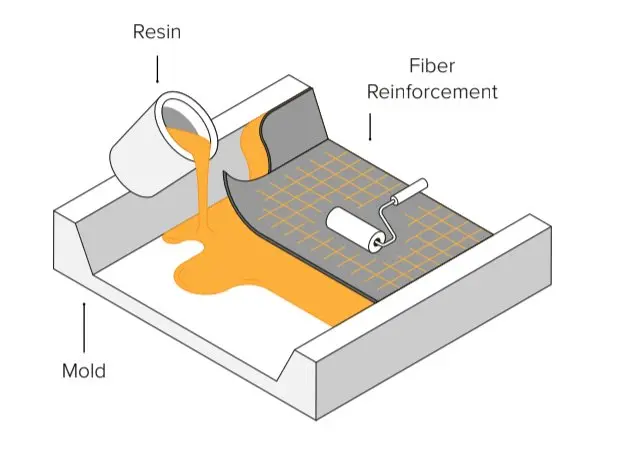
Regardez la vidéo pour voir comment fonctionne le processus de stratification de la fibre de carbone par voie humide.
2. Stratification de préimprégnés
Avec la stratification de préimprégné, la résine est préalablement injectée dans la fibre. Les feuilles préimprégnées sont stockées à basse température pour inhiber la polymérisation. Elles sont ensuite placées dans le moule, puis polymérisées en autoclave sous l’effet de la pression et de la chaleur. Cette technique est plus précise et reproductible que la précédente, car la quantité de résine est contrôlée, mais elle est aussi plus chère et n’est généralement utilisée que pour les applications haute performance.
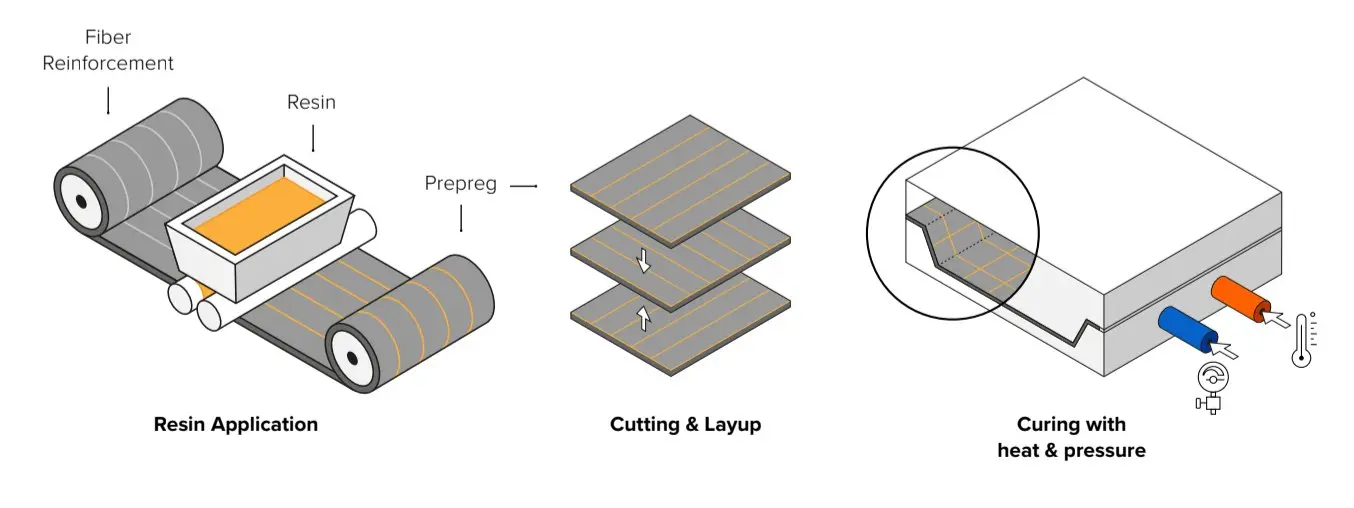
3. Moulage par transfert de résine (RTM)
Avec le moulage par transfert de résine, la fibre sèche est insérée dans un moule en deux parties. Le moule est refermé avant l'injection à haute pression de la résine dans la cavité. Cette technique est généralement automatisée et utilisée pour la fabrication à grande échelle.
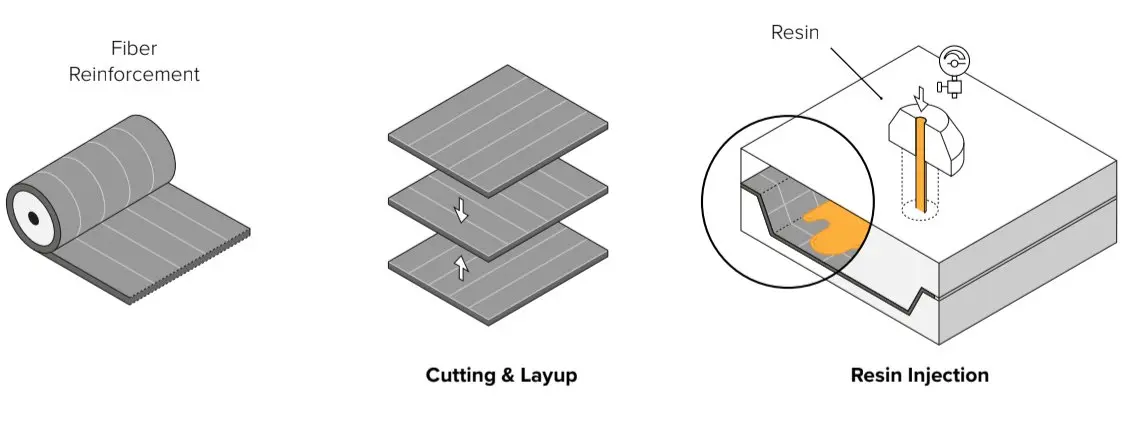
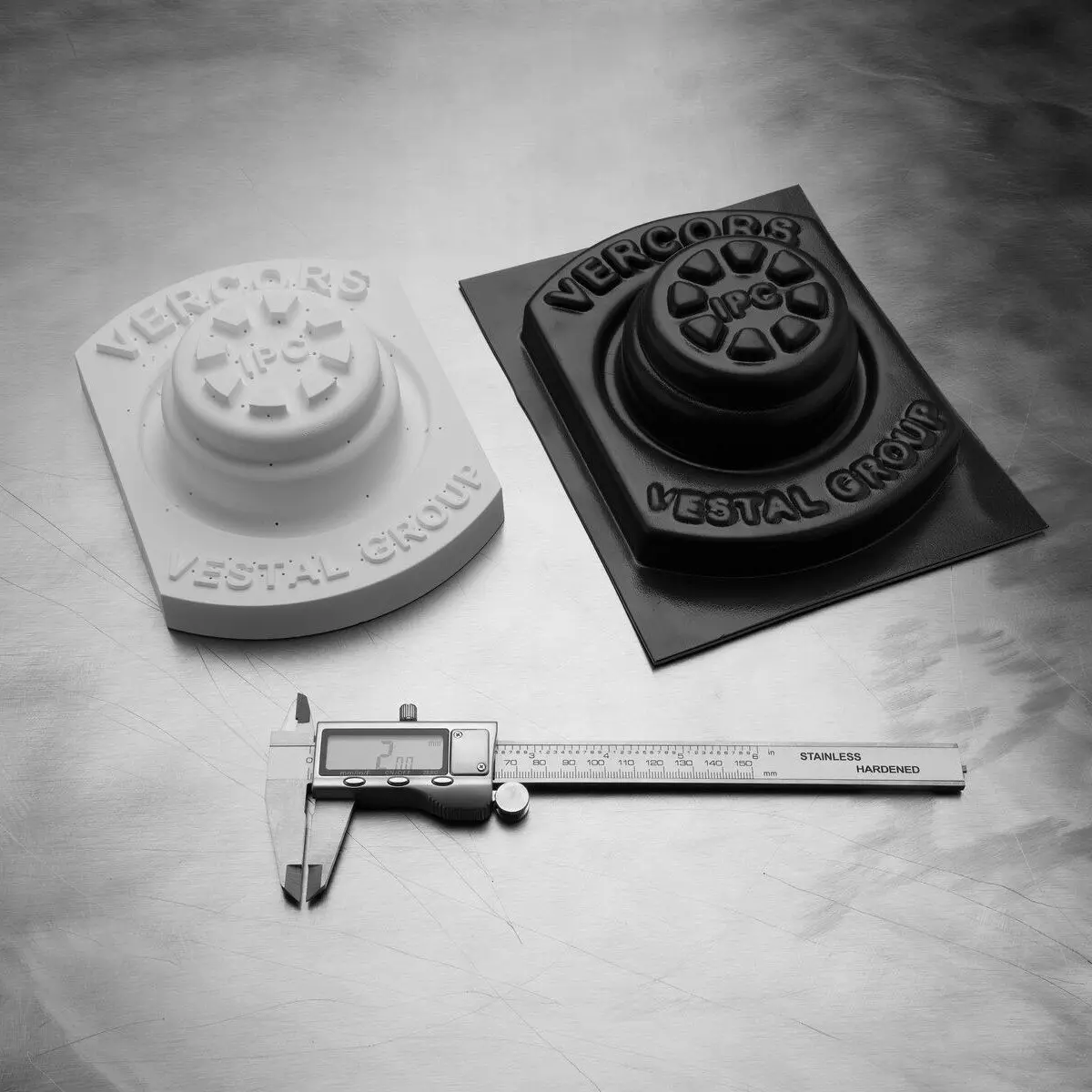
Le thermoformage rapide de petites séries avec des moules imprimés en 3D
Téléchargez notre livre blanc pour apprendre comment créer rapidement des moules complexes grâce à l’impression 3D et pour obtenir des conseils et des recommandations à suivre lors de la préparation des pièces de moule.
La création de moules imprimés en 3D pour la fabrication de pièces en fibre de carbone
Comme la qualité du moule affecte directement celle de la pièce finale, la réalisation de l’outillage est un facteur crucial de la fabrication PRF. La plupart des moules sont réalisés en cire, en mousse, en bois, en plastique ou en métal par usinage CNC ou modelage manuel. Les procédés manuels sont certes gourmands en main-d’œuvre, mais l’usinage CNC doit aussi respecter un processus de travail long et complexe, surtout pour les géométries compliquées. Sous-traiter celui-ci se traduit généralement par un coût élevé et un délai de réalisation plus long. Ces deux options nécessitent des opérateurs qualifiés et laissent peu de flexibilité pour les itérations de conception et les ajustements du moule.
La fabrication additive offre une solution pour produire rapidement et à faible coût des moules et des modèles pour la fabrication de pièces en fibre de carbone. L’utilisation d’outillage polymérique dans les procédés de fabrication est en constante augmentation. Remplacer un outillage métallique par des pièces en plastique imprimées en interne est une méthode puissante et rentable pour raccourcir les délais de production tout en développant la flexibilité de conception. Les ingénieurs travaillent déjà avec des pièces imprimées en 3D en résine polymère pour la production industrielle de gabarits et de fixations qui entrent dans des méthodes de fabrication telles que l’enroulement filamentaire ou le placement de fibres automatisé. De la même manière, des moules et des matrices imprimés en petite quantité interviennent dans le moulage par injection, le thermoformage ou le formage de tôle pour produire des séries de faible volume.
L’impression 3D de bureau en interne requiert un équipement limité et réduit la complexité des processus de travail. Des imprimantes résine de bureau professionnelles telles que la Form 3+ sont maintenant disponibles à des prix abordables. Elles sont faciles à mettre en œuvre et leur nombre peut être rapidement adapté à la demande. Fabriquer des outils et des moules de grande dimension est également possible grâce aux imprimantes 3D grand format telles que la Form 3L.
La technique d’impression 3D par stéréolithographie crée des pièces dont la finition de surface est extrêmement lisse, ce qui est essentiel pour des moules en fibre de carbone. Elle permet aussi de produire des géométries complexes avec une grande précision. En outre, la sélection de résines Formlabs offre des matériaux techniques dont les propriétés mécaniques et thermiques se prêtent bien à la fabrication de moules et de modèles.
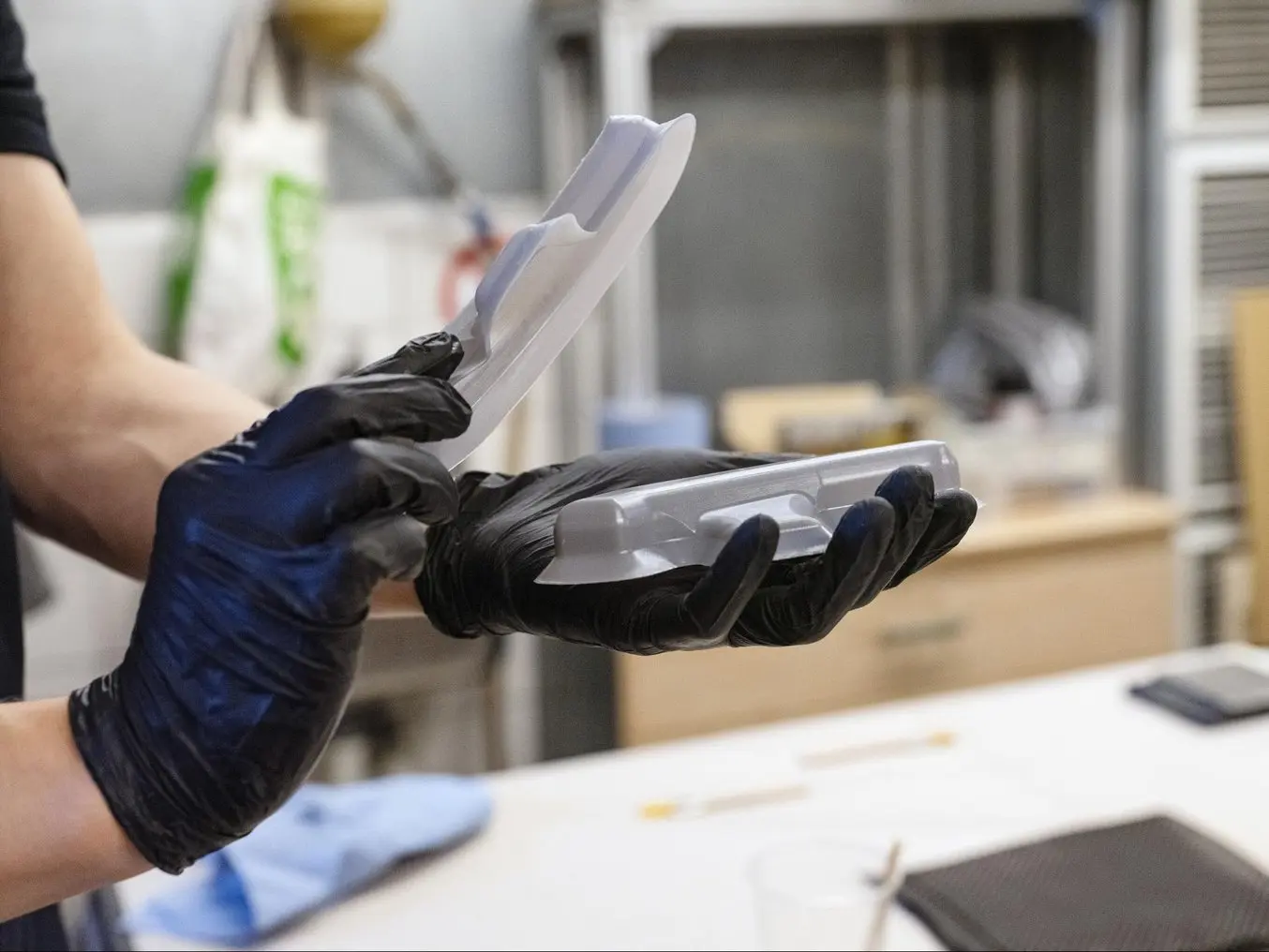
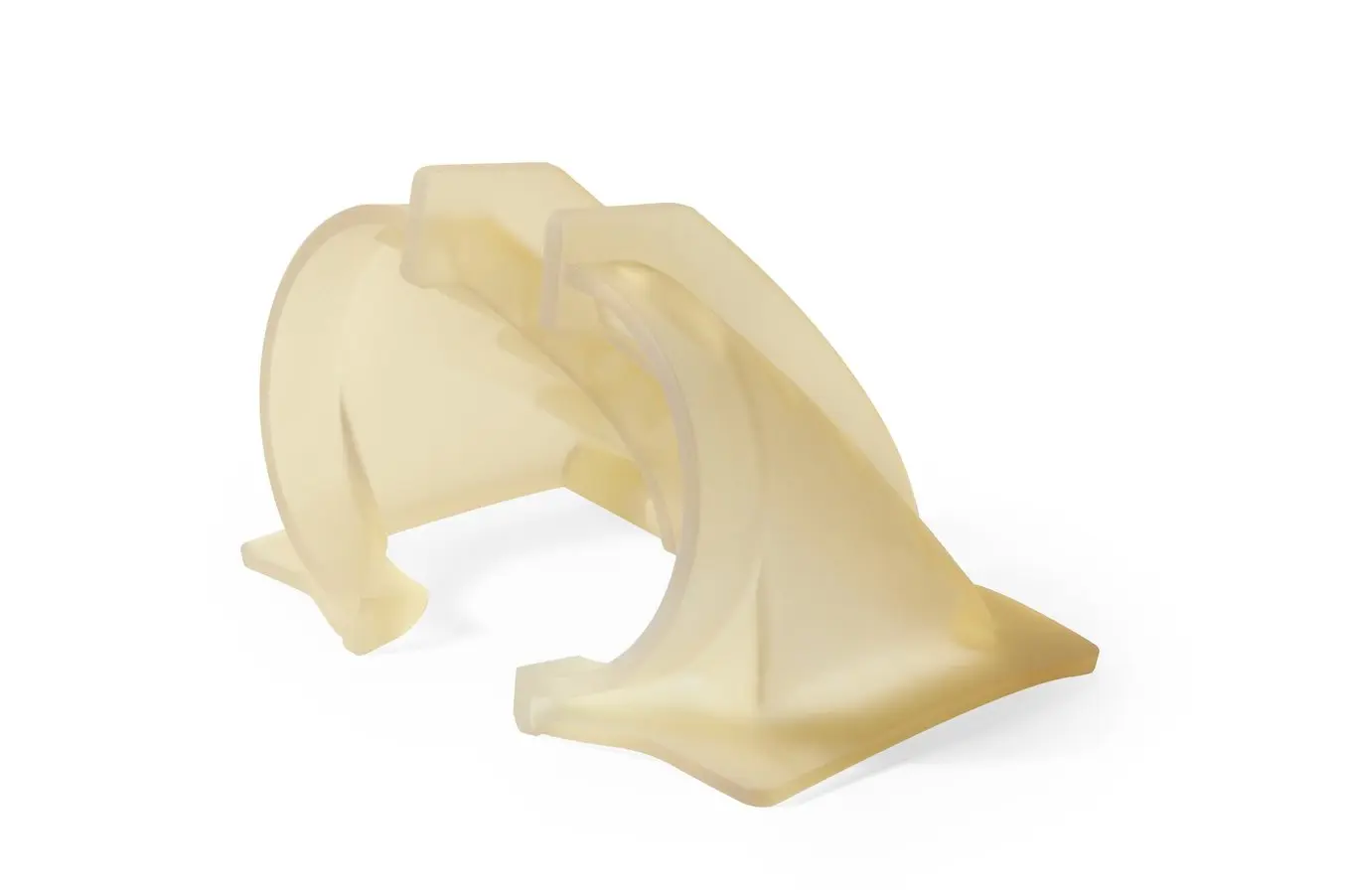
Les moules imprimés en 3D pour la fabrication de pièces en fibre de carbone peuvent réduire les coûts et les délais de production.
Pour la production à petite échelle, les ingénieurs peuvent imprimer directement le moule à moindre coût et en quelques heures, sans avoir à le sculpter manuellement, ni à se préoccuper d’équipement à commande numérique par ordinateur, de logiciel FAO, de paramétrage de machines, d’équipement de serrage, d’outillage et d’évacuation des copeaux. Les délais de réalisation et la main-d’œuvre pour la fabrication du moule sont réduits de manière drastique, ce qui permet des itérations de conception rapides et une personnalisation des pièces. Ils peuvent même réaliser des formes de moule compliquées qui présentent des détails fins qui seraient difficiles à fabriquer avec des méthodes traditionnelles.
L’équipe de Formula Student de la TU Berlin (FaSTTUBe) a fabriqué une dizaine de pièces en fibre de carbone pour ses voitures de course. Les ingénieurs de l’équipe ont stratifié manuellement dans un moule imprimé directement avec Tough 1500 Resin de Formlabs. Cette résine se caractérise par un module de traction de 1,5 GPa et un allongement à la rupture de 51 %. Non seulement elle reste solide et soutient les plis lors du drapage, mais elle est aussi assez flexible pour pouvoir séparer la pièce du moule après polymérisation.
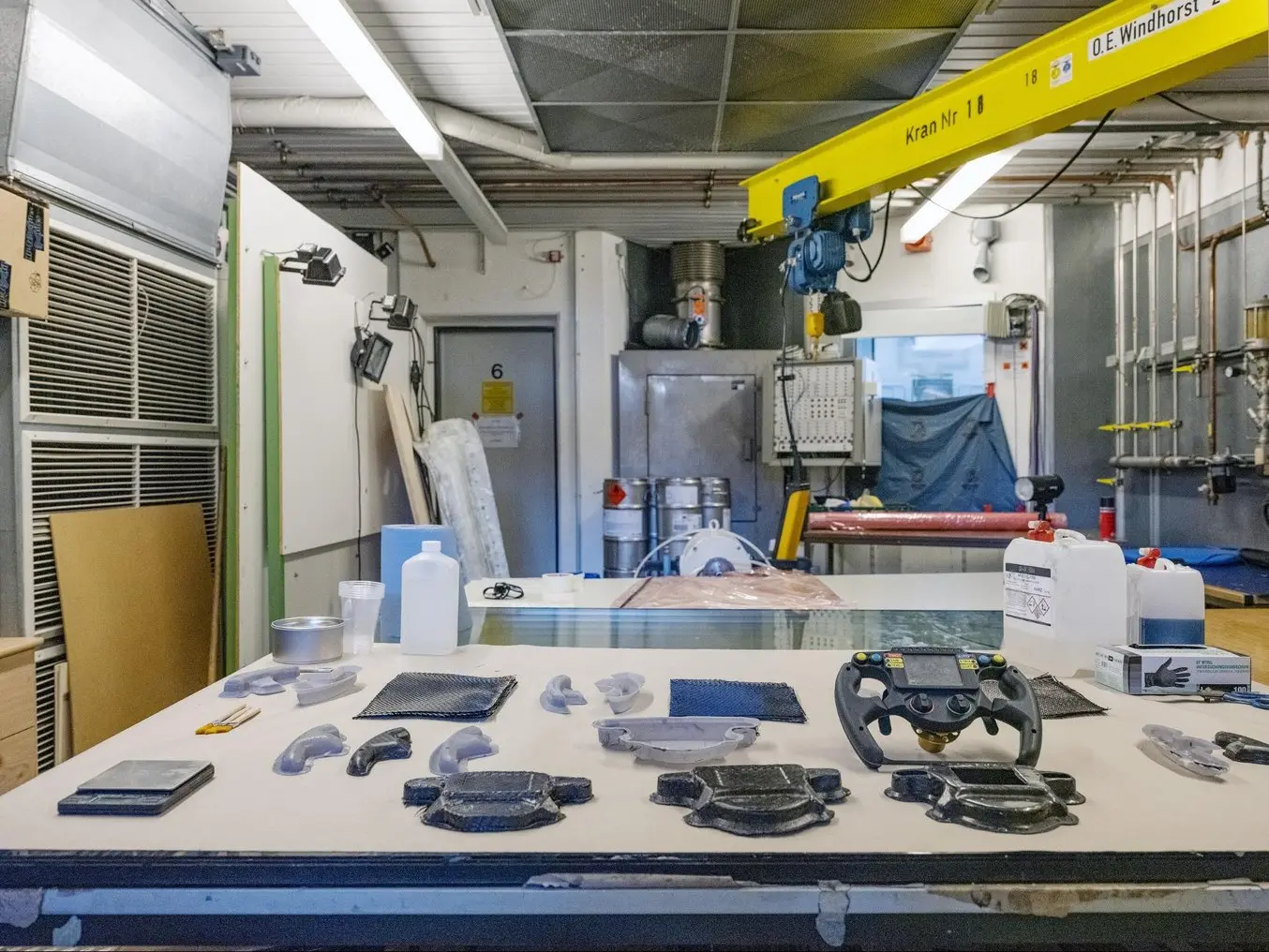
Le banc de test de la FaSTTUBe avec le matériel de fabrication des pièces en fibre de carbone.
Bien que cette technique ne mette pas en œuvre des conditions de polymérisation intensives, d’autres procédés de stratification impliquent souvent des pressions et des températures plus élevées. La société DeltaWing Manufacturing utilise High Temp Resin pour créer des composants d’écoulement de l’air par technique de préimprégnation. High Temp Resin présente une température de fléchissement sous charge (TFC) de 238 °C à 0,45 MPa et est capable de résister à la chaleur et à la pression d’un autoclave. DeltaWing Manufacturing a imprimé directement des moules pour la production d’une série d’environ 10 pièces sur mesure.
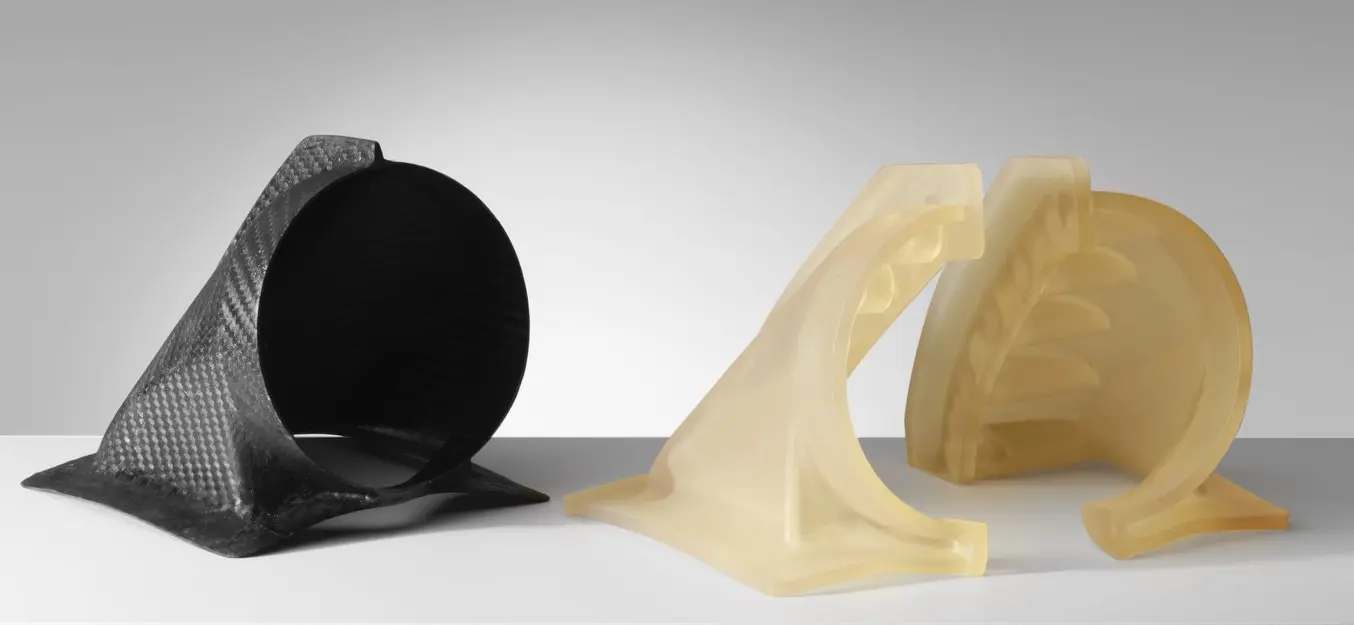
Un conduit d’aération d’aile en fibre de carbone à côté du moule en deux parties imprimé avec High Temp Resin, produit par DeltaWing Manufacturing.
Les moules polymériques imprimés directement en 3D sont des outils très intéressants pour optimiser les productions en petite série. Cependant, leur durée de vie est réduite par rapport aux moules traditionnels, ce qui les rend inadaptés aux séries de grand volume.
Pour augmenter la production, DeltaWing Manufacturing imprime des modèles de moule avec la High Temp Resin, puis réalise les moules en résine. Imprimer le modèle est aussi une solution alternative efficace pour les techniques de stratification qui nécessitent des conditions de polymérisation trop intensives pour les moules imprimés en 3D. Les fabricants peuvent imprimer des modèles sur mesure à la demande en éliminant quand même une étape de leur procédé de réalisation de moule : la fabrication du modèle.
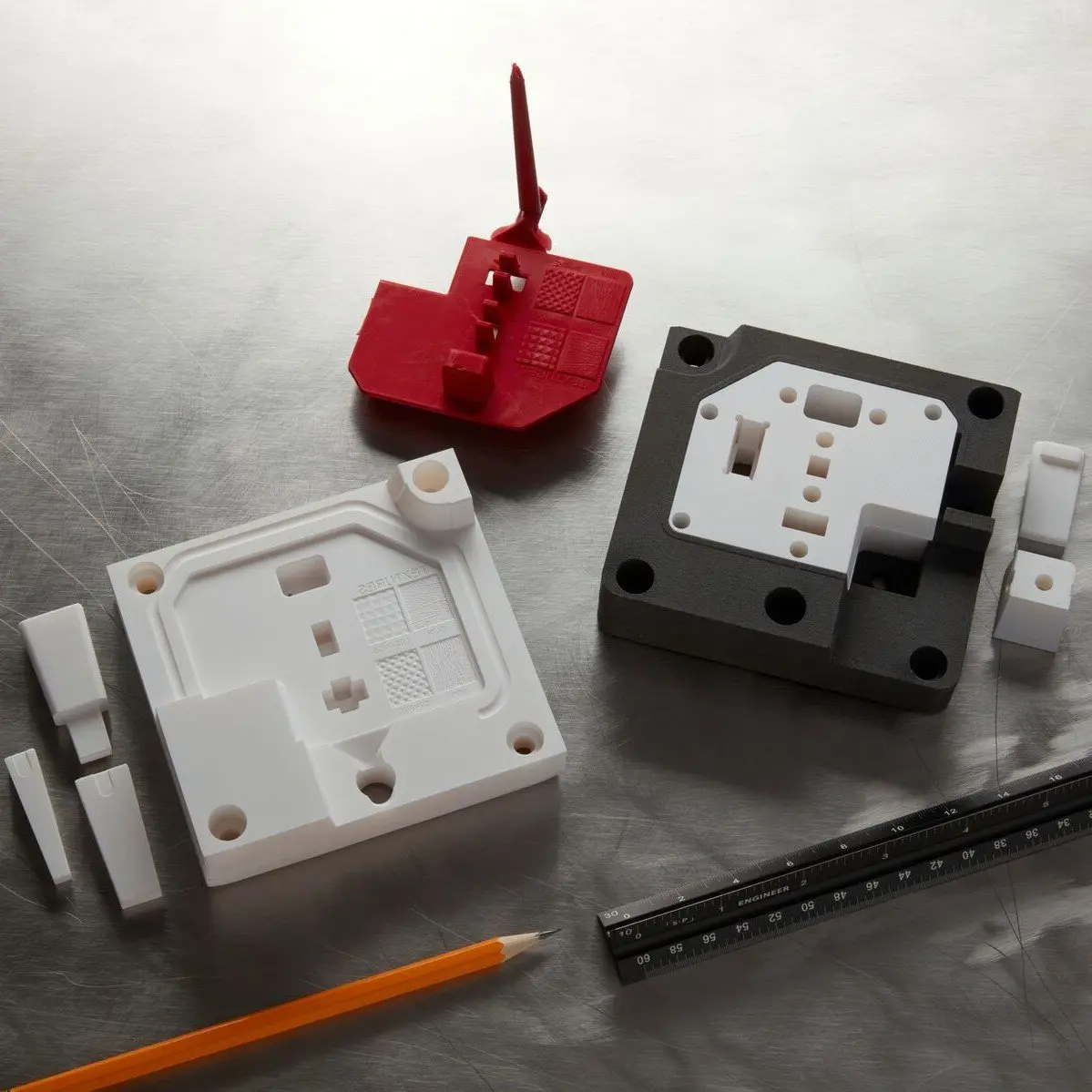
Guide de l'outillage rapide
Dans ce livre blanc, apprenez comment combiner l'outillage rapide imprimé en 3D avec des procédés de fabrication traditionnels tels que le moulage par injection, le formage sous vide ou la fonderie.
Impression 3D de fibres de carbone
Il existe une forte demande pour des flux de travail combinant la résistance, la durabilité et la robustesse des pièces traditionnelles en fibre de carbone avec l'agilité, les possibilités géométriques et la répétabilité de l'impression 3D. Il n'est donc pas surprenant que de nombreuses entreprises proposent l'impression 3D de fibre de carbone, les deux procédés actuellement disponibles étant l'impression avec des fibres coupées ou continues.
L'utilisation de fibres de carbone coupées, de Nylon 11 CF Powder pour l'imprimante 3D industrielle SLS Fuse 1+ 30W permet aux fabricants de créer des pièces solides, légères et résistantes à la chaleur, sans avoir recours aux méthodes traditionnelles de superposition ou d'usinage.
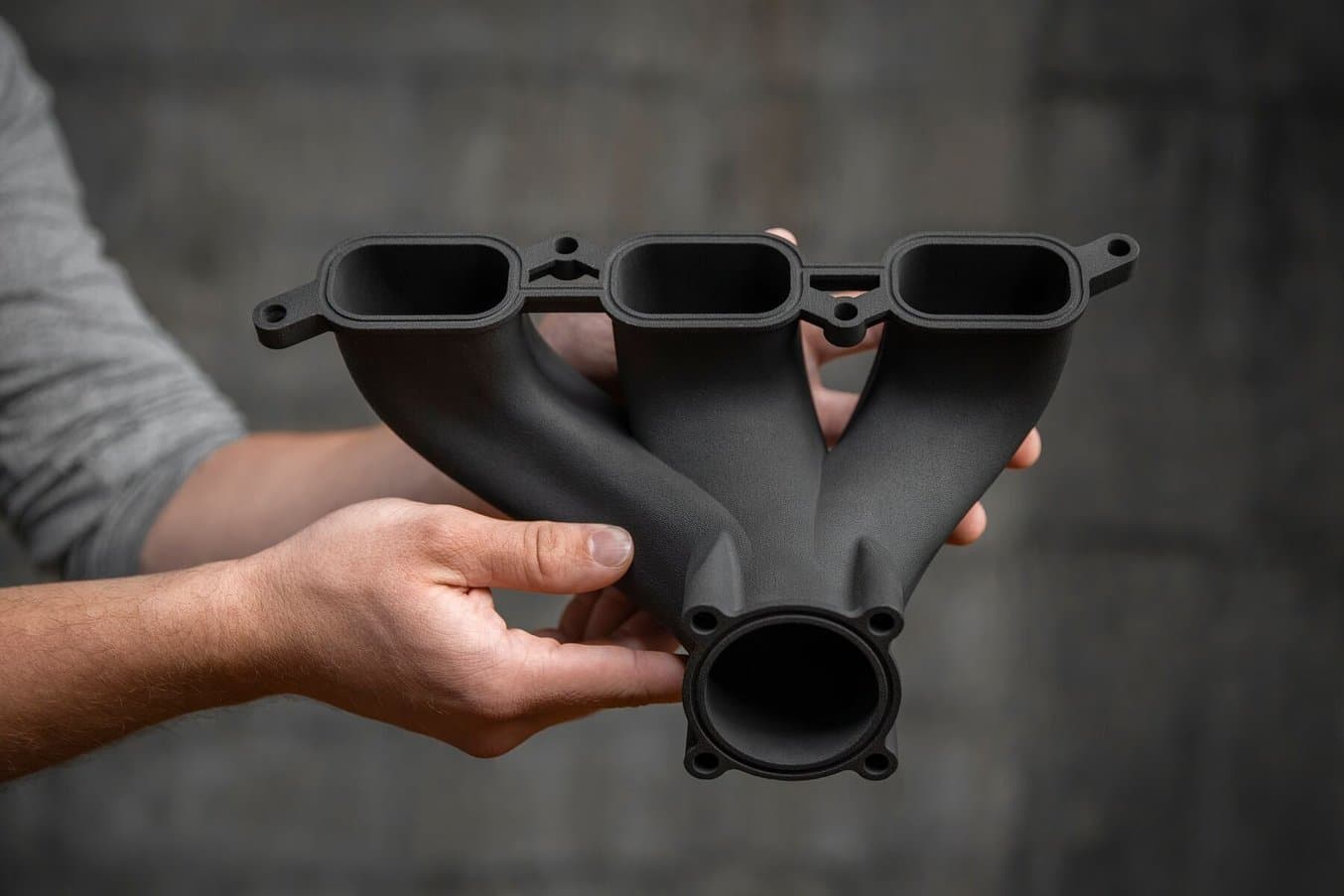
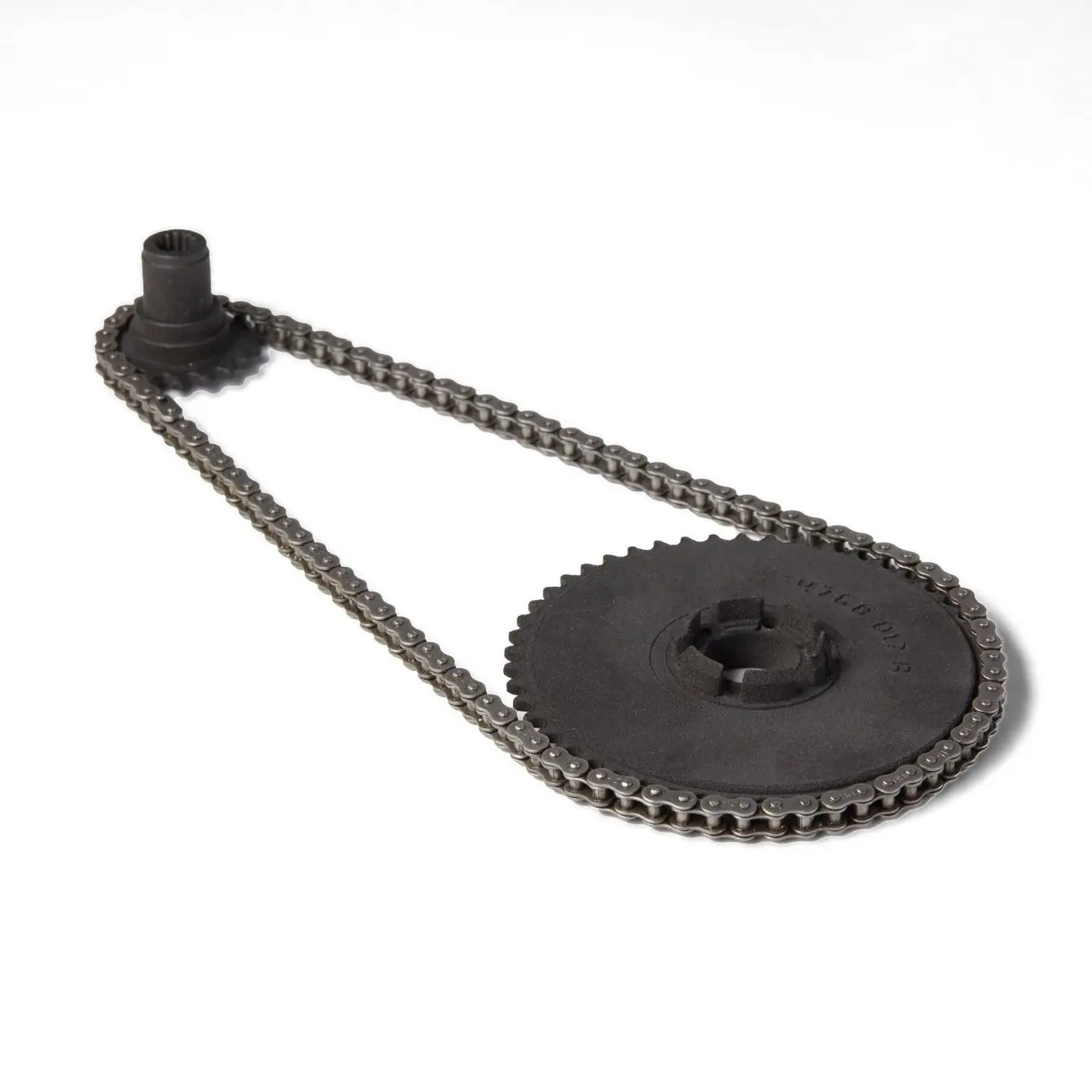
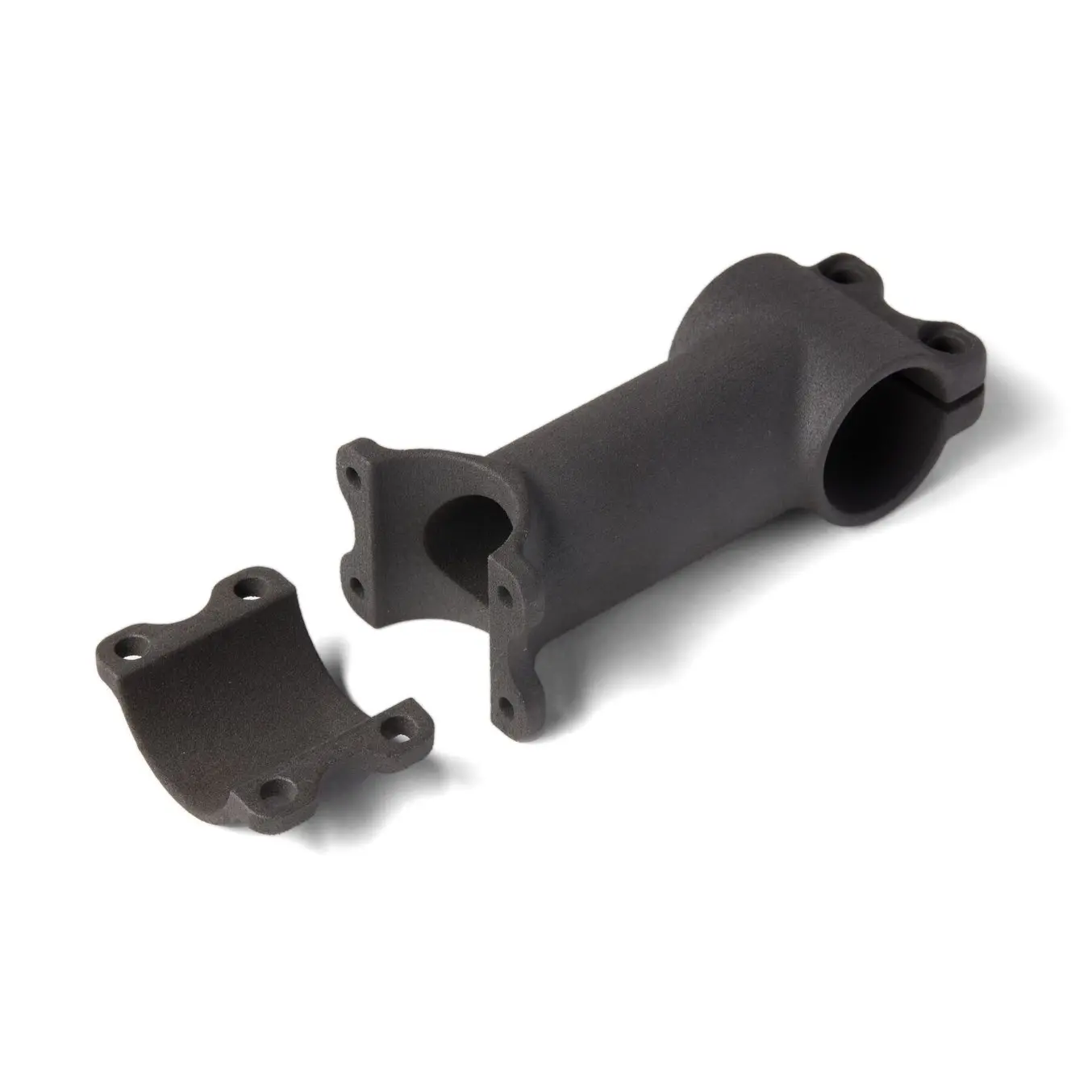
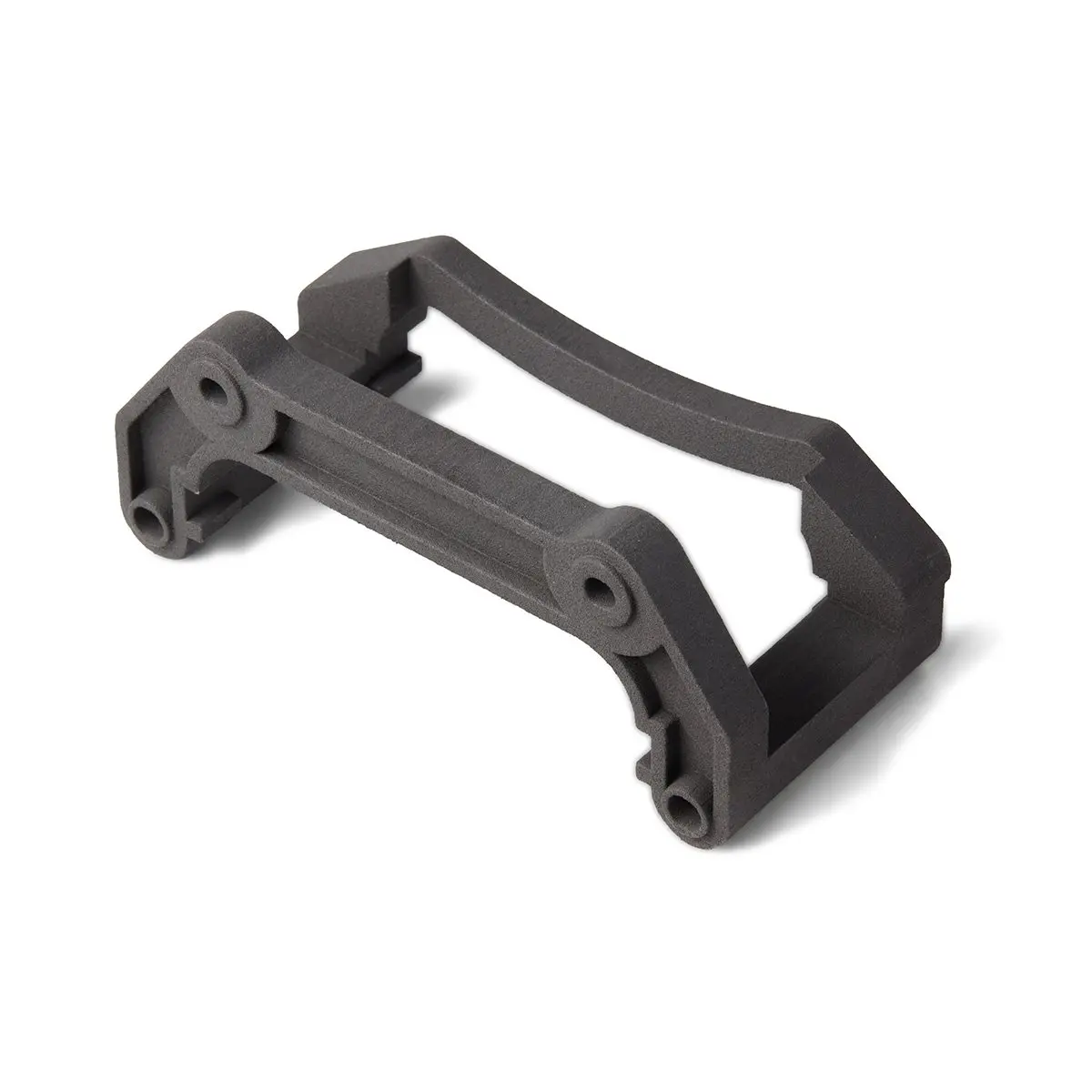
Nylon 11 CF Powder de Formlabs est solide, légère et résistante à la chaleur, ce qui la rend idéale pour les applications automobiles, aérospatiales et de production industrielle.
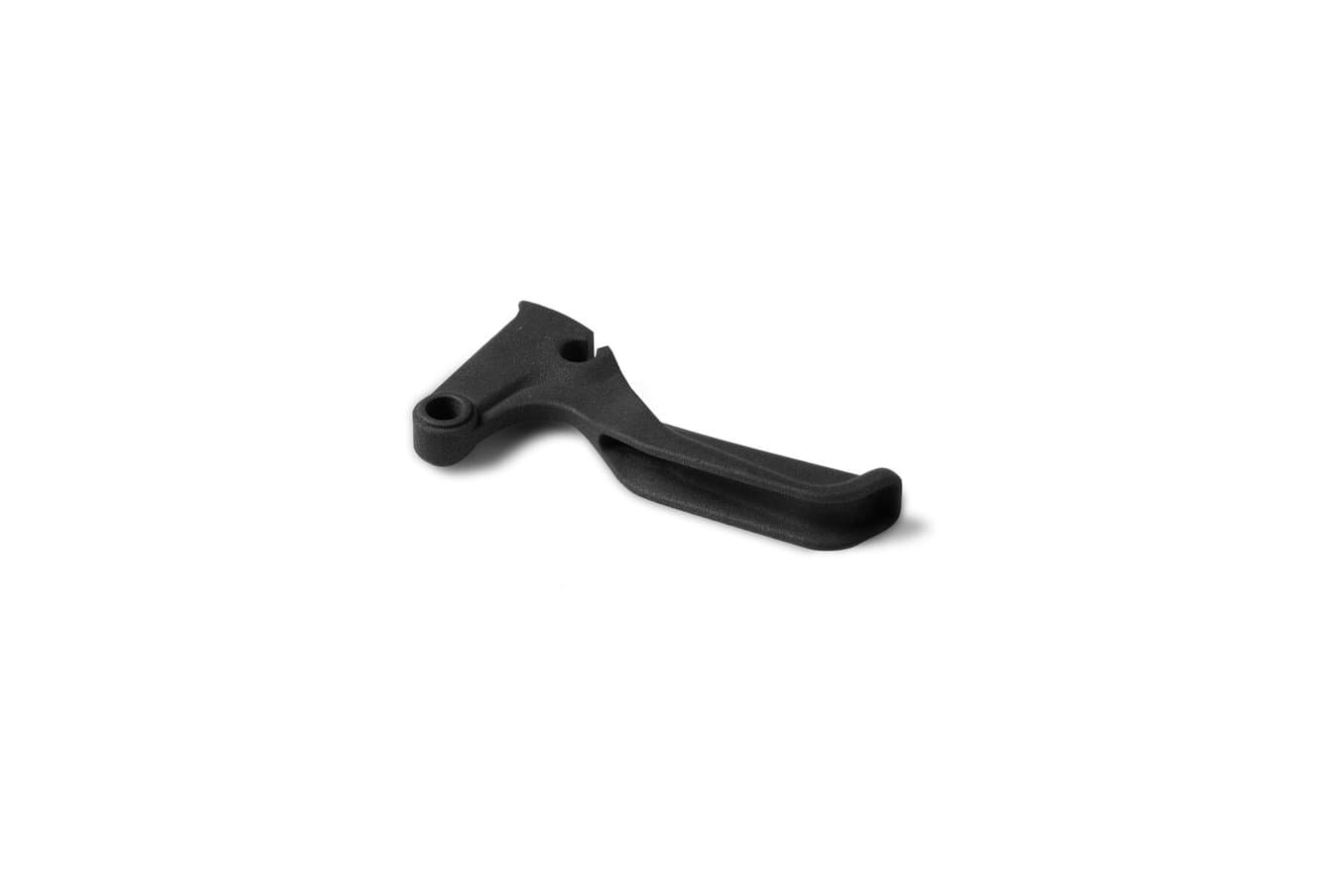
Commander un échantillon gratuit
Examinez et constatez par vous-même la qualité Formlabs. Nous enverrons un échantillon gratuit à votre bureau.
Guide de démarrage pour la fabrication en fibre de carbone
La fabrication avec polymère renforcé de fibres est un processus passionnant, mais complexe et gourmand en main-d’œuvre. Utiliser des moules et des modèles imprimés en 3D pour réaliser des pièces en fibre de carbone permet aux entreprises de réduire la complexité du processus de travail, d’améliorer leur flexibilité et les possibilités de conception, ainsi que de réduire les coûts et les délais de réalisation.
À travers les études de cas de TU Berlin et de DeltaWing Manufacturing, notre livre blanc présente trois processus de travail pour intégrer l’impression 3D à la fabrication composite grâce à la production rapide de moules et de modèles.