Guide de l'impression 3D de pièces étanches : comparaison des technologies FDM, SLA et SLS
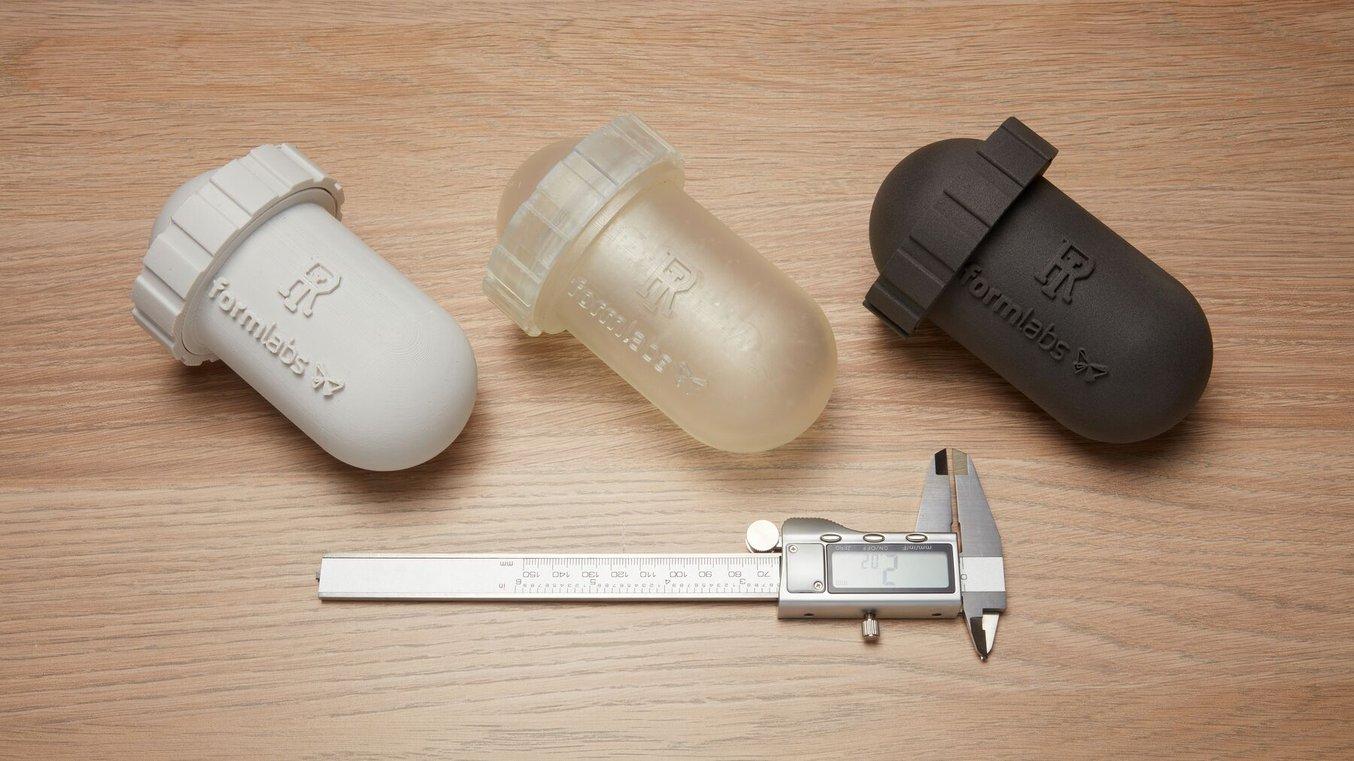
Dans divers secteurs, tels que la recherche marine, la robotique sous-marine, l'ingénierie des technologies durables, l'industrie pétrolière et gazière et la défense, des pièces personnalisées hermétiques et étanches au gaz sont souvent requises pour de faibles volumes de production. Bien que certaines technologies d'impression 3D constituent une solution idéale pour ces pièces, la perception commune des pièces fabriquées de manière additive est qu'elles sont poreuses et ne peuvent pas être déployées dans des environnements pressurisés.
Dans le cadre d'une coopération entre Formlabs et l'Undersea Robotics and Imaging Lab (URIL) de l'université de Rhode Island, des assemblages en plusieurs parties ont été imprimés à l'aide des procédés de dépôt de fil fondu (FDM), de stéréolithographie (SLA) et de frittage sélectif par laser (SLS), puis testés dans une chambre de pression sous l'eau. Les résultats de ces essais, ainsi que les diagrammes, les recommandations concernant les joints toriques et les instructions de conception, sont disponibles dans le livre blanc.
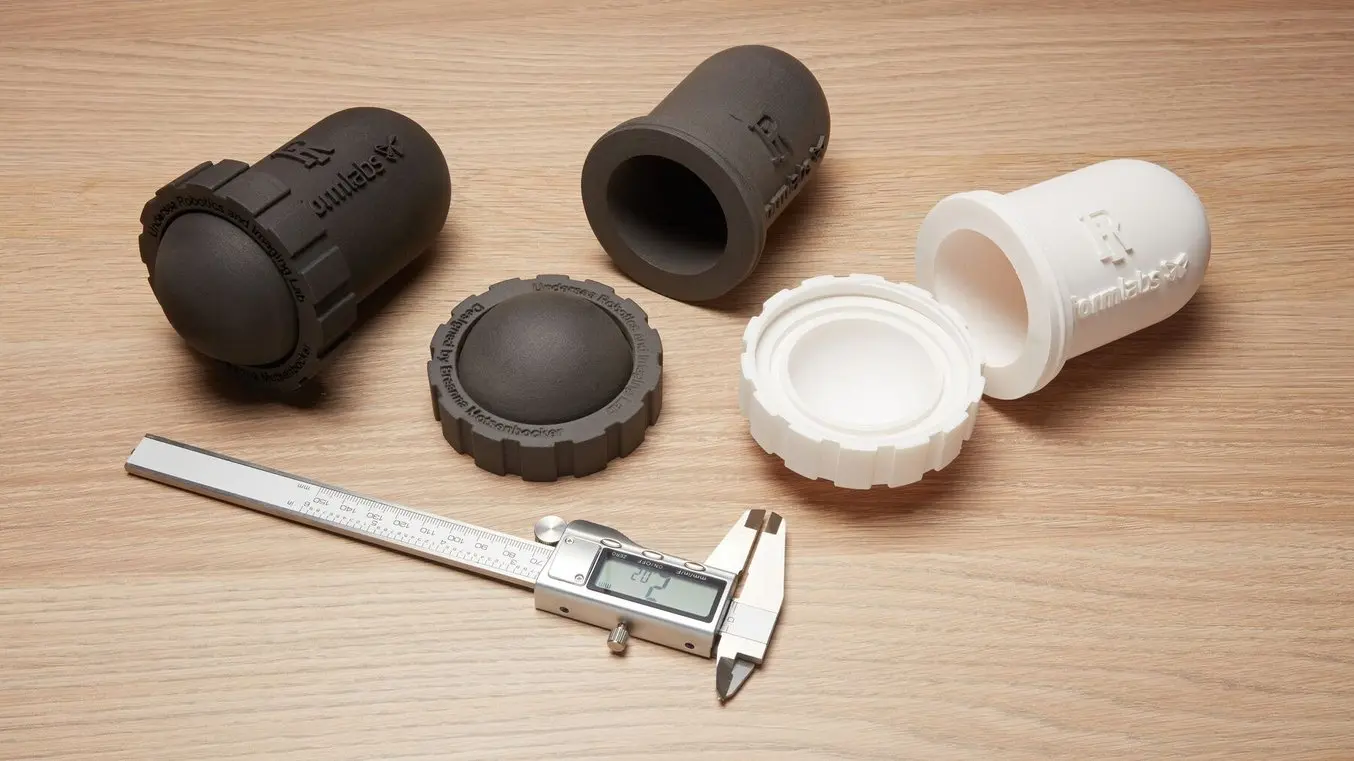
Impression 3D de boîtiers étanches et résultats des tests de pression
Dans ce livre blanc, nous fournissons les résultats des tests et des directives claires sur la façon d'imprimer en 3D des boîtiers étanches personnalisés à un prix abordable.
Conception et fabrication de pièces étanches sur mesure
L'étanchéité désigne quant à elle la capacité d'un objet à empêcher l'eau d'y entrer ou d'en sortir. Elle est donc étroitement liée à la conception du boîtier ou de l'assemblage en question, plutôt que de reposer uniquement sur la nature fondamentale du matériau. Cependant, si l'on considère la pression que subissent ces pièces lors de leur descente sous la surface, les propriétés spécifiques des matériaux jouent un rôle plus important. L'expérience menée par l'URIL porte sur la conception, la méthode de scellement et les propriétés des matériaux.
Applications pour les pièces étanches
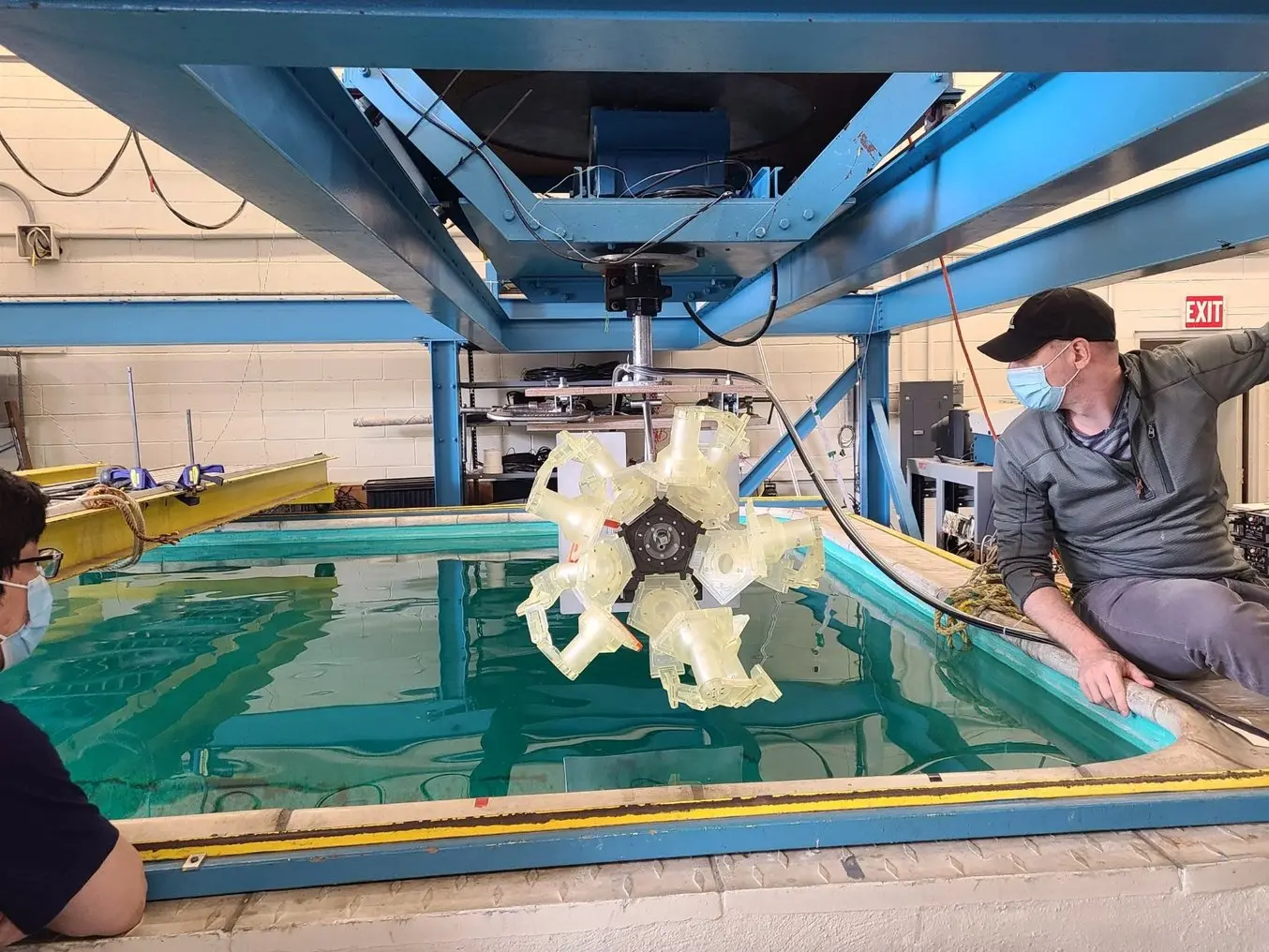
L'impression 3D permet de tester des formes nouvelles et complexes pour les équipements de test et de collecte d'échantillons, comme cet outil dont les composants sont imprimés en Clear Resin.
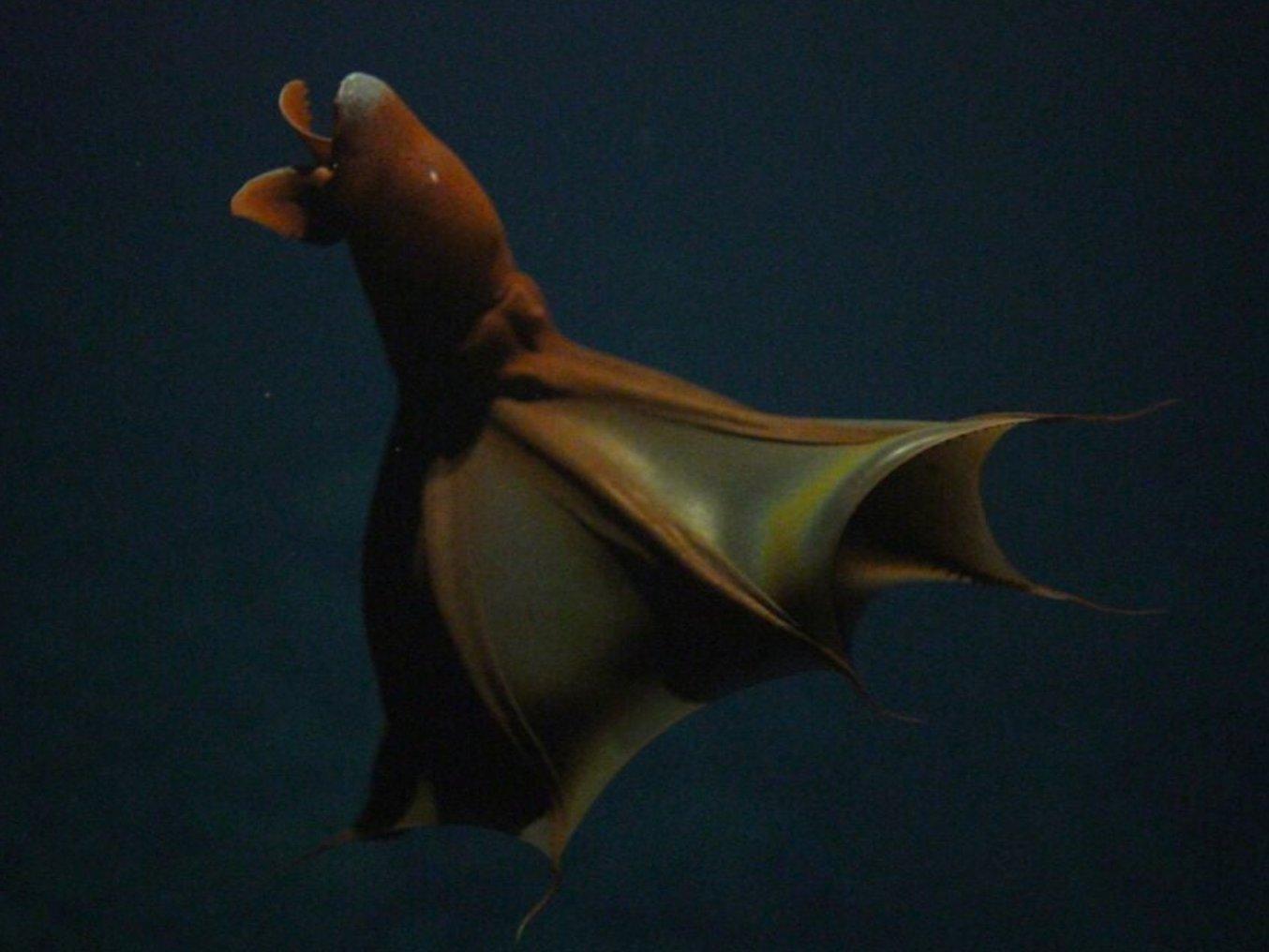
Les boîtiers étanches permettent de prendre des photos en profondeur, comme cette photo d'un vampyroteuthis, même sans appareil photo sous-marin coûteux.
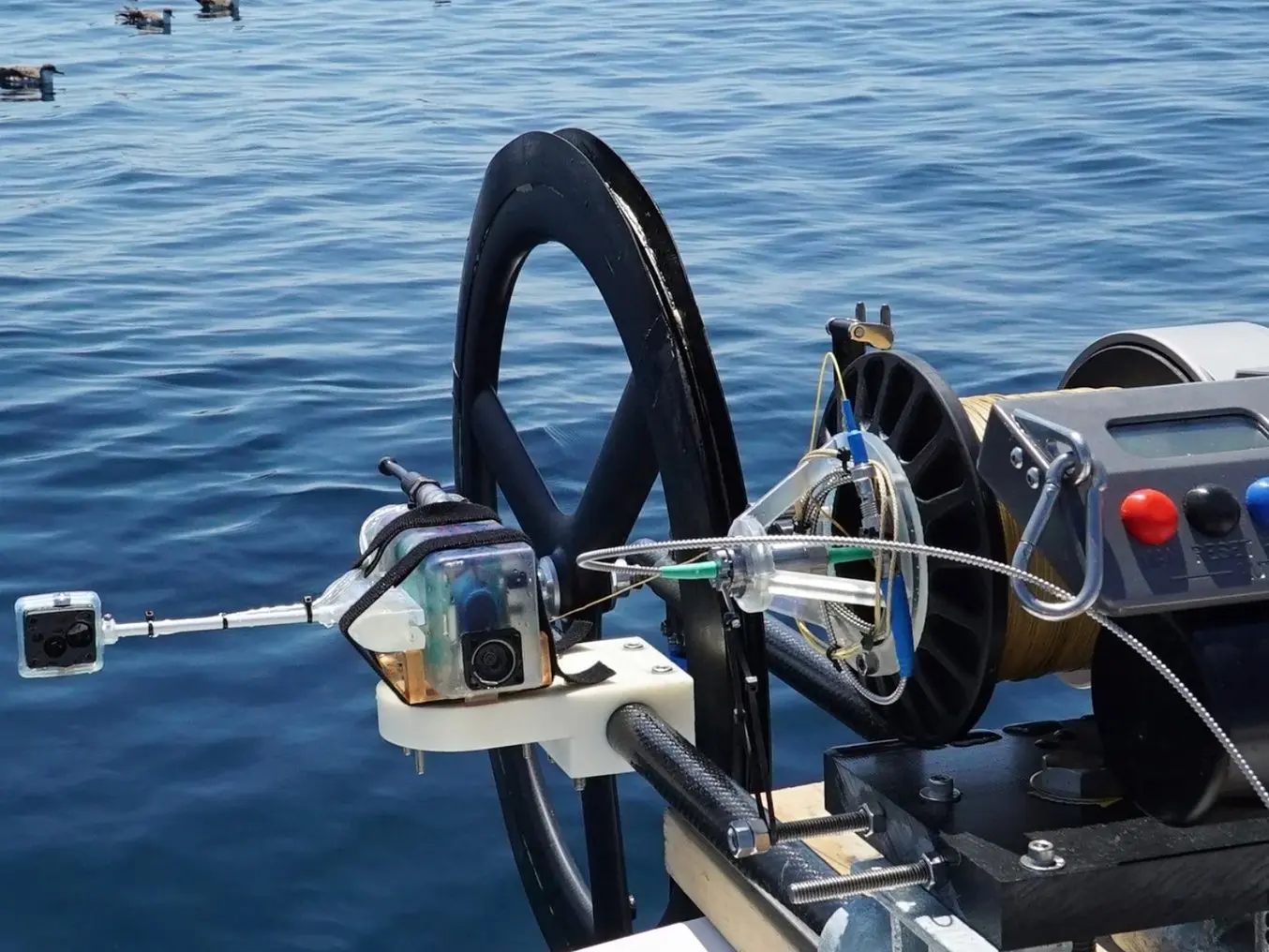
La nature agile de l'impression 3D à la demande rend possible et rentable l'utilisation de gabarits et de fixations personnalisés pour la recherche en mer.
Les pièces étanches sont utilisées dans différents contextes, tels que les moteurs hors-bord pour la navigation de plaisance, l'exploration robotique en haute mer, la photographie sous-marine, etc. Lorsque les pièces sont étanches, elles peuvent également contenir d'autres fluides. C'est pourquoi elles sont extrêmement utiles dans les applications où des tuyaux transportent des liquides entre différents composants, comme dans l'industrie automobile, la recherche chimique, les services publics, la construction et bien d'autres contextes.
Pour les applications de recherche dans les domaines de l'écologie, de la géologie ou de la climatologie, la création d'équipements d'étude et d'échantillonnage sur mesure est souvent trop coûteuse. Étant donné que chaque application est unique et que les environnements dans lesquels ils seront déployés sont en constante évolution et difficiles à gérer depuis la surface, les composants pour la recherche sous-marine ou fluidique sont souvent fabriqués sur mesure.
L'impression 3D de pièces étanches à la NOAA
Pour contrer la disparition des récifs coralliens, les équipes scientifiques et de recherche de l'Atlantic Oceanographic and Meteorological Laboratory (AOML) de la NOAA (National Oceanic and Atmospheric Administration), en collaboration avec des institutions partenaires, utilisent des méthodes innovantes pour étudier les coraux dans la nature, reproduire certaines conditions en laboratoire contrôlé et ainsi cultiver de nouvelles espèces de coraux capables de mieux résister à des conditions extrêmes.
Le site de l'AOML s'est tourné vers l'impression 3D pour faciliter ses recherches sur le terrain et en laboratoire. L'utilisation des imprimantes Formlabs a permis de normaliser, d'améliorer la précision et la comparabilité de leurs expériences et de faciliter le développement de nouvelles technologies. La gamme de matériaux disponibles pour les imprimantes Formlabs facilite la conception, l'itération et l'utilisation de pièces étanches imprimées en 3D.
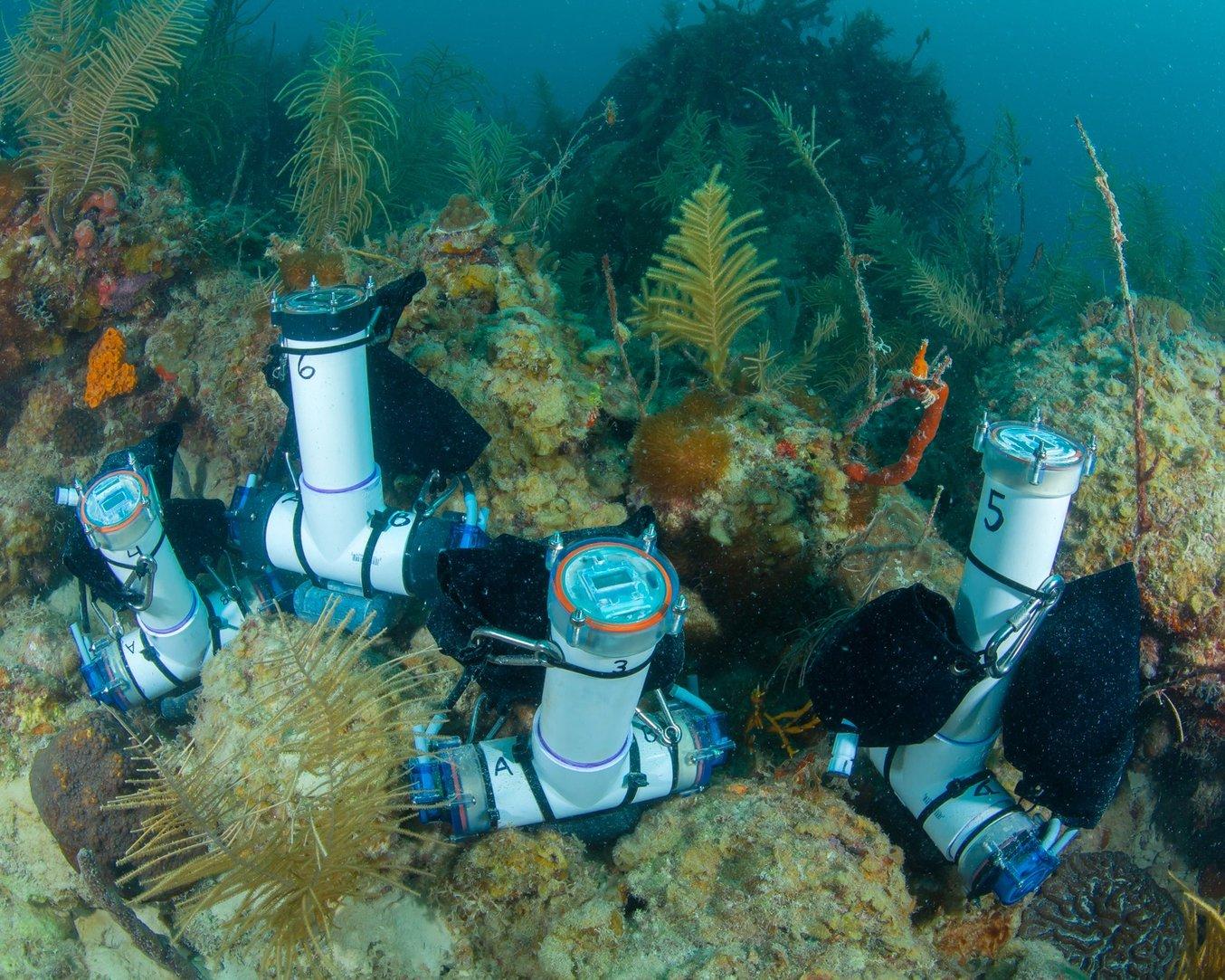
Les recherches de l'AOML nécessitent des équipements sophistiqués et souvent personnalisés pour surveiller les habitats coralliens sauvages. (Images avec l'aimable autorisation de la NOAA)
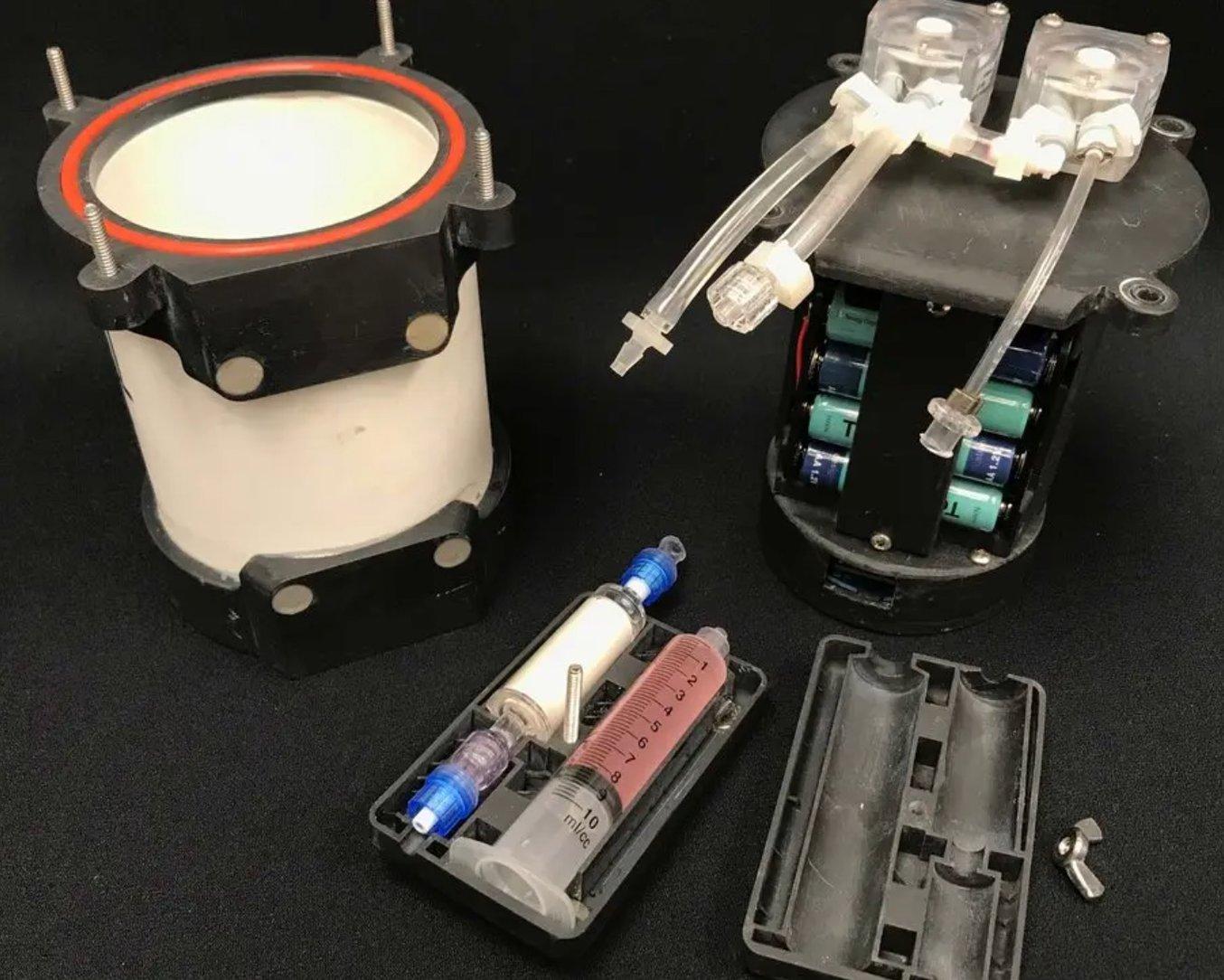
Le laboratoire de l'AOML a conçu et fabriqué cet échantillonneur automatique d'ADN électronique sous-marin en utilisant les imprimantes SLA de Formlabs pour produire le capuchon de protection, la cartouche d'échantillonnage et l'assemblage interne.
En utilisant quatre imprimantes à résine Formlabs ainsi que l'imprimante à frittage sélectif par laser (SLS) Fuse 1, Nate Formel et ses collègues de l'AOML impriment des boîtiers d'échantillonnage robustes, des gabarits pour les capteurs et les équipements expérimentaux, ainsi que des composants personnalisés pour leurs aquariums internes. Ils y étudient la santé des coraux et cherchent des méthodes pour améliorer leur résistance aux conditions extrêmes du changement climatique et à l'augmentation de la température de l'eau.
« Nous disposons désormais de ces composants imprimés en 3D très personnalisés, dotés des points de connexion et des trous de passage nécessaires pour nous permettre de prélever des échantillons. Le modèle de collecteur original qui coûtait 1000 $ est maintenant fabriqué pour 220 $. Cela signifie que pour chaque collecteur que j'avais en service, j'en ai cinq aujourd'hui. », explique M. Formel.
Méthodes de fabrication actuelles des pièces étanches
Les méthodes actuelles de fabrication de ces composants étanches impliquent généralement l'utilisation de matériaux très courants, tels que le métal, le plastique moulé par injection ou le caoutchouc. Les composants produits en série sont abordables, mais leur configuration pour répondre aux besoins spécifiques de chaque application peut s'avérer difficile et nécessiter des connecteurs, des fixations ou des boîtiers personnalisés. Pour les assemblages à composants multiples, l'étanchéité des composants est assurée par une combinaison de filetages, d'éléments d'emboîtement ou d'accouplement, de joints toriques ou de joints d'étanchéité.
Le choix des joints toriques peut s'avérer extrêmement difficile et la configuration des paramètres appropriés pour chaque boîtier peut prendre beaucoup de temps. Le manuel Parker sur les joints toriques contient des milliers de recommandations basées sur la compression, le diamètre, l'épaisseur, le matériau, la pression et d'autres caractéristiques. Le processus de choix d'un joint torique personnalisé est si difficile que des composants standardisés et produits en série sont souvent utilisés, ce qui limite la capacité d'innovation et les nouvelles applications.
L'impression 3D de pièces étanches : choisir la bonne technique d'impression 3D
Les applications sous-marines ont toujours été réservées aux entreprises disposant de fonds importants et capables de construire des machines et des équipements personnalisés coûteux. L'impression 3D pourrait changer la donne, car elle permet de fabriquer des pièces personnalisées pour la recherche et le développement à une fraction du coût des méthodes traditionnelles. Pour mettre en œuvre avec succès une solution sous-marine imprimée en 3D, le type de technologie et de matériau utilisé doit être soigneusement évalué.
Les technologies SLA et SLS sont toutes deux largement utilisées dans les domaines de l'ingénierie et de la recherche, mais elles offrent également des performances optimales dans différentes situations. La technologie SLS est remarquable pour la production en faible volume de pièces à usage final. De plus, elle dispose d'un catalogue de matériaux bien connus, comme le nylon et le polyuréthane thermoplastique, et permet de créer des pièces durables et de qualité industrielle. Les imprimantes SLA excellent lorsqu'une finition de surface lisse et des propriétés des matériaux très spécifiques sont requises. Dans ce test, la finition de surface lisse des pièces moulées par SLA et leur densité ont contribué à une performance optimale dans un environnement pressurisé.Les imprimantes à dépôt de fil fondu (FDM) sont souvent utilisées pour le prototypage rapide, mais elles ne permettent pas de créer des pièces étanches et ne sont donc pas utilisées dans des applications étanches.
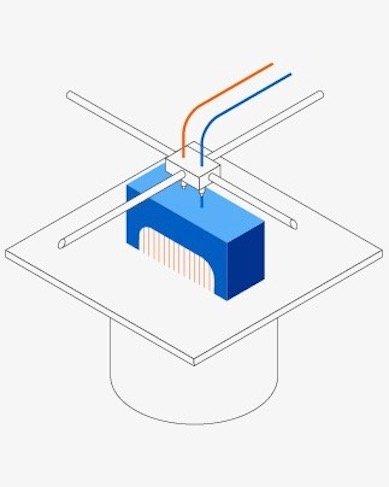
La technique d'impression 3D par dépôt de fil fondu (FDM).
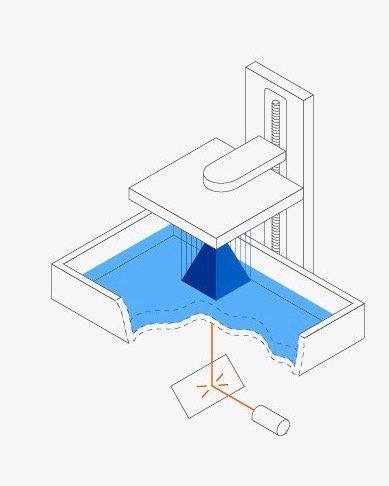
Technique d'impression 3D par stéréolithographie (SLA).
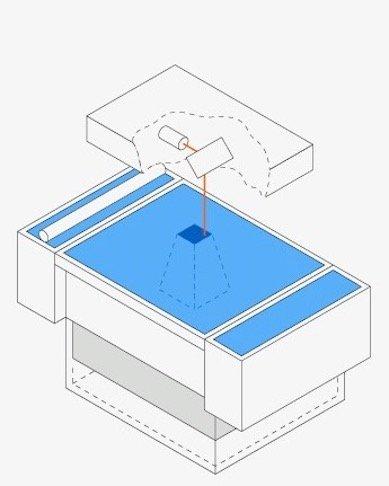
Technique d'impression 3D par frittage sélectif par laser (SLS).
Dépôt de fil fondu (FDM)
La technologie d'impression 3D la plus connue, le dépôt de fil fondu (FDM), ne permet pas de créer des pièces étanches. De cette incapacité découle l'idée fausse selon laquelle, en général, les pièces imprimées en 3D ne peuvent pas être utilisées dans des applications étanches. La technologie FDM est basée sur l'extrusion de plastique fondu à travers une buse, qui dépose le matériau couche par couche, mais sans liaison chimique entre elles.
Les pièces imprimées par FDM sont anisotropes, ce qui signifie qu'elles ont des propriétés mécaniques différentes selon la direction dans laquelle la contrainte mécanique s'exerce sur elles et qu'elles sont moins denses qu'un objet similaire imprimé à l'aide d'autres méthodes. Les couches n'étant pas chimiquement liées entre elles, les liquides peuvent s'infiltrer à la surface de la pièce par les interstices microscopiques entre les couches. Les boîtiers imprimés sur des imprimantes FDM ne sont donc pas étanches, à moins que les pièces ne soient fortement post-traitées et fermées après une étape supplémentaire telle que le lissage à la vapeur ou le revêtement. Ces pièces implosent sous la pression et se fissurent le long des lignes de couche.
Si vous devez créer des pièces étanches à l'air avec des imprimantes 3D FDM, vous pouvez tirer parti de certaines techniques pour tenter d'améliorer l'étanchéité, notamment en concevant la pièce sans interstices, fissures ou autres ouvertures, ainsi qu'en recourant à la « surextrusion » et à l'utilisation de couches plus épaisses. En outre, certaines étapes supplémentaires de post-traitement, telles que le ponçage, le chanfreinage et le revêtement, restent nécessaires. Les boîtiers imprimés sur des imprimantes FDM ne sont donc pas étanches, à moins que les pièces ne soient fortement post-traitées et fermées après une étape supplémentaire telle que le lissage à la vapeur ou le revêtement.
Stéréolithographie (SLA)
Les pièces imprimées en 3D par stéréolithographie (SLA), à l'inverse, sont étanches, car chaque couche est chimiquement liée à la suivante. Les pièces imprimées par SLA sont formées par un processus dans lequel un laser polymérise de la résine liquide, une couche à la fois, en liant les chaînes de polymères à l'intérieur de cette couche ainsi qu'avec les couches qui la précèdent et la suivent directement. Ce procédé crée des finitions de surface lisses, pratiquement sans lignes de couche, et une surface non poreuse à travers laquelle l'eau ne peut pas pénétrer. Ces pièces ont des tolérances extrêmement bonnes, de sorte que les assemblages à plusieurs composants, tels que les boîtiers utilisés pour les tests de cet article, peuvent être enfilés les uns dans les autres sans qu'il y ait le moindre espace d'air entre eux. Lorsqu'ils sont associés à un joint d'étanchéité, les boîtiers deviennent complètement étanches et peuvent résister à des pressions extrêmement élevées.
Frittage sélectif par laser (SLS)
Pour la création de pièces, la technologie de frittage sélectif par laser (SLS) fritte une section transversale de la pièce sur un lit de poudre, qui est ensuite recouvert d'une nouvelle couche de poudre. Ce processus se répète couche par couche jusqu'à ce que la pièce soit entièrement formée. Les pièces obtenues sont dans une certaine mesure isotropes, mais peuvent présenter des propriétés mécaniques différentes selon le sens d'application de la force. Les pièces SLS sont étanches lorsqu'elles sont conçues avec les tolérances et les techniques de scellement appropriées.
Conseils de conception pour l'impression 3D de pièces étanches
Comme nous l'avons déjà mentionné, l'étanchéité d'un boîtier dépend à la fois de l'étanchéité des composants eux-mêmes et de la conception de la pièce, c'est-à-dire de la manière dont ces composants sont assemblés. Les techniques d'impression 3D SLA et SLS peuvent créer des composants avec des tolérances si étroites que les boîtiers emboîtables ou ceux avec des pièces filetées peuvent être complètement étanches sans nécessiter d'étapes supplémentaires. Toutefois, dans des environnements extrêmement pressurisés, tels que ceux testés dans cet essai, des mesures supplémentaires telles que l'utilisation de joints toriques peuvent accroître l'efficacité des boîtiers.
Conception du boîtier
L'Undersea Robotics and Imaging Laboratory (URIL) de l'université de Rhode Island a pour mission de démocratiser la recherche en eaux profondes. Grâce à des imprimantes 3D abordables comme la Form 3+ et la Form 3L grand format, il est aujourd'hui possible de concevoir et de fabriquer des instruments très complexes pour l'exploration en eaux profondes et de partager les conceptions avec la communauté scientifique.
L'URIL a publié plusieurs études sur ses recherches en eaux profondes, notamment un guide sur la conception inédite du DEEPi, un système d'acquisition et de contrôle d'images en eaux profondes, une étude sur l'utilisation de systèmes de stabilisation passifs pour permettre d'imprimer en SLA sur une embarcation en mouvement, et une analyse de l'utilisation du biomimétisme dans la conception de boîtiers en se basant sur la forme des nautiloïdes.
Brennan Philips, chercheur principal, et Breanna Motsenbocker, étudiante en doctorat, effectuent depuis des années des itérations de leurs caméras sous-marines et de leurs boîtiers robotisés, et ont publié plusieurs articles pour illustrer les résultats de leurs travaux. Le laboratoire a publié sa conception de source ouverte afin de rendre le processus de fabrication accessible aux communautés qui ne disposent pas des fonds nécessaires à la collecte de données ou à la recherche sous-marine.
L'URIL a mis à disposition les deux modèles, l'un utilisé dans les essais à paroi mince et l'autre, non testé, à paroi plus épaisse, sous forme de code source ouvert pour une reproduction publique. Pour accéder à ces modèles, téléchargez le livre blanc complet.
Conceptions biomimétiques
Philips et Motsenbocker, en collaboration avec d'autres équipes de recherche, ont également étudié comment les conceptions biomimétiques peuvent améliorer la fonctionnalité de leurs boîtiers étanches. Dans un article publié en octobre 2023, des équipes de chercheurs ont observé comment la coquille de Nautilus pompilius (un membre de la famille des mollusques) empêche l'eau de pénétrer à l'intérieur, même à des profondeurs extrêmes. Les résultats pourraient nous éclairer sur la manière dont les morphologies complexes de leurs coquilles peuvent indiquer des géométries résistantes à la pression comparables aux géométries « idéales » actuellement utilisées dans la robotique marine en eaux profondes, c'est-à-dire des sphères et des cylindres simples, dont le rapport surface/volume est réduit au minimum et dont le processus de fabrication est plus facile. Pour découvrir les résultats complets de leur recherche, lisez l'article publié dans la revue.
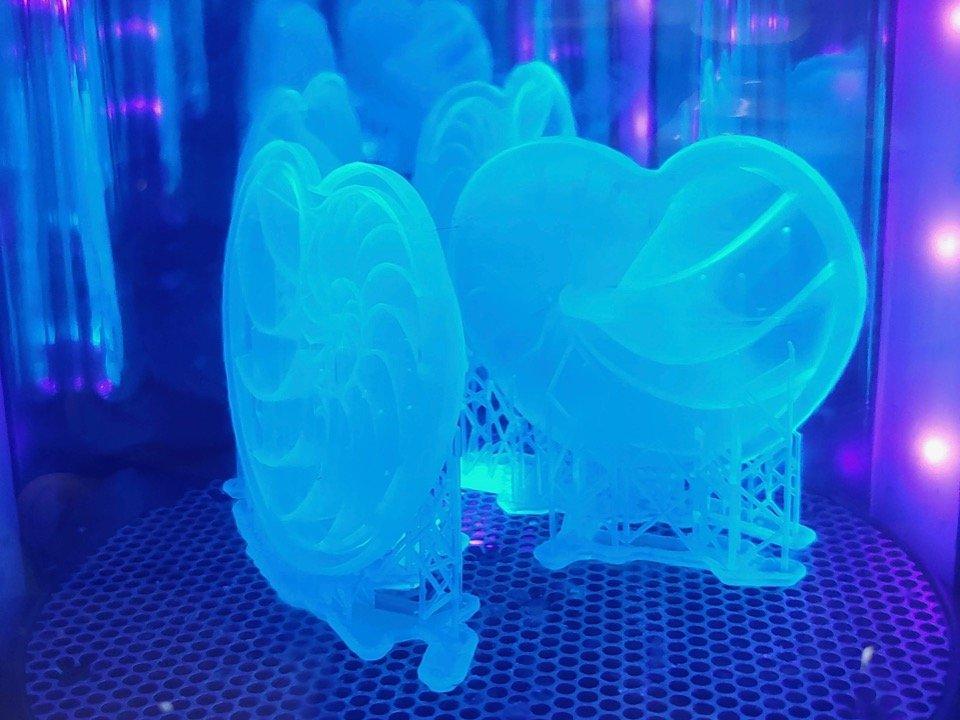
Ces composants imprimés en 3D ont été conçus en s'inspirant du Nautilus pompilius, un membre de la famille des mollusques qui peut résister à des pressions extrêmement élevées sous l'eau sans que sa coquille ne soit endommagée.
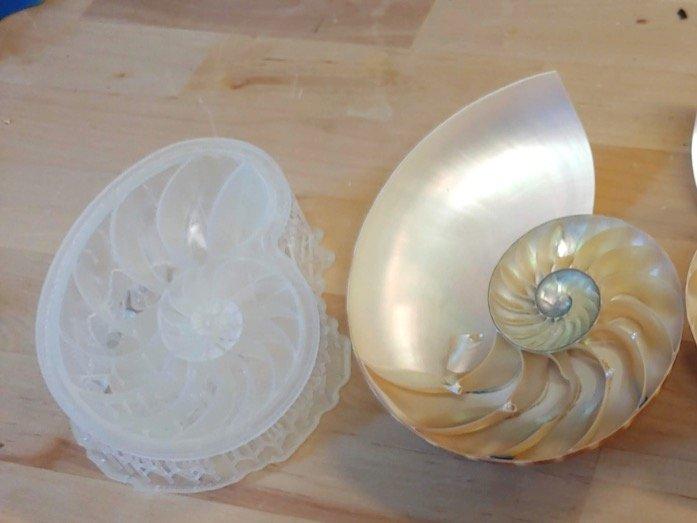
La numérisation de mollusques (à droite) et l'utilisation de la conception numérique pour recréer leur géométrie en vue de l'impression 3D (à gauche, en Clear Resin) peuvent aider les équipes de recherche à comprendre comment ces animaux ont évolué pour survivre dans des environnements inhospitaliers.
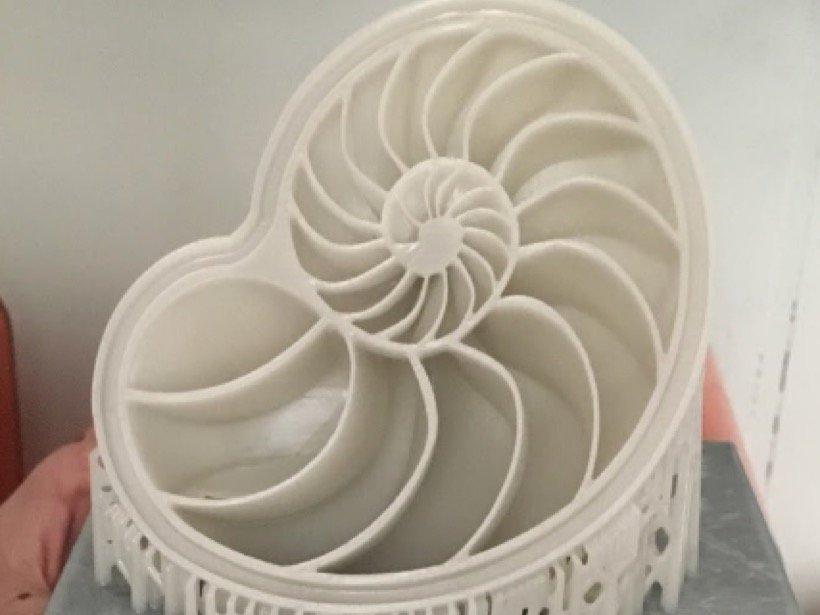
Cette pièce plus grande, imprimée en White Resin, pourrait être utilisée pour enfermer de petites caméras destinées à la recherche en eaux profondes.
Comment choisir un joint torique pour un boîtier étanche imprimé en 3D
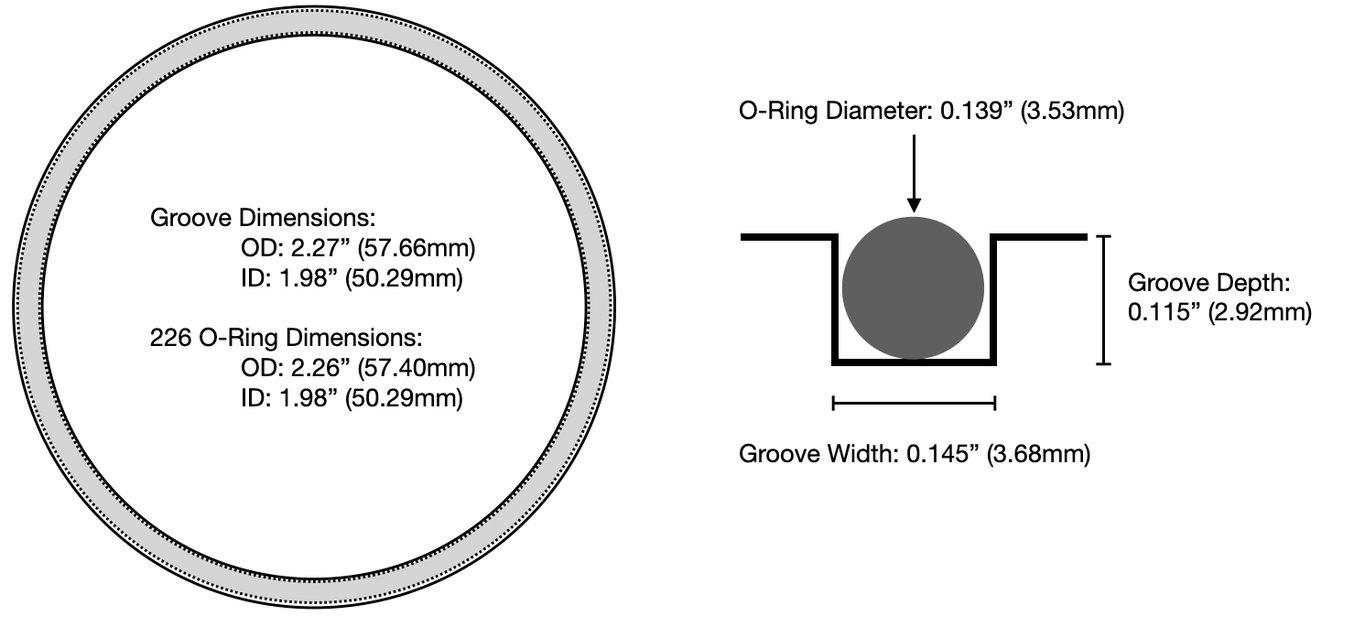
Lors de ses essais, l'URIL a réussi à utiliser aussi bien des joints toriques que des obturateurs d'alésage, mais elle préfère les joints toriques.
Une fois les diamètres intérieur et extérieur de l'interne choisis, un joint torique à étanchéité frontale peut être sélectionné sur la base du diamètre intérieur. Le joint torique doit bien s'adapter à la surface entre l'embout et le corps de base du boîtier. Les joints toriques de taille 2 selon la norme AS568, c'est-à-dire les joints toriques d'une épaisseur de cordon de 3,53 mm, donnent le scellement le plus fiable pour les pièces imprimées en 3D SLA. Pour connaître les recommandations et les conclusions spécifiques de l'URIL, téléchargez le livre blanc dans son intégralité.
Impression 3D étanche : essais et résultats
Les technologies FDM, SLA et SLS ont été utilisées pour la fabrication des boîtiers. Le boîtier en Nylon 12 GF Powder a été imprimé sur l'imprimante SLS Fuse 1+ 30W, tandis que les autres matériaux (Grey Resin, Clear Resin, BioMed Amber Resin et Rigid 10K Resin) ont été imprimés sur l'imprimante SLA Form 3+. Les pièces imprimées par FDM sur une imprimante Craftbot avec du filament d'acide polylactique se sont avérées absorber l'eau immédiatement après l'immersion et ont donc été éliminées des tests.
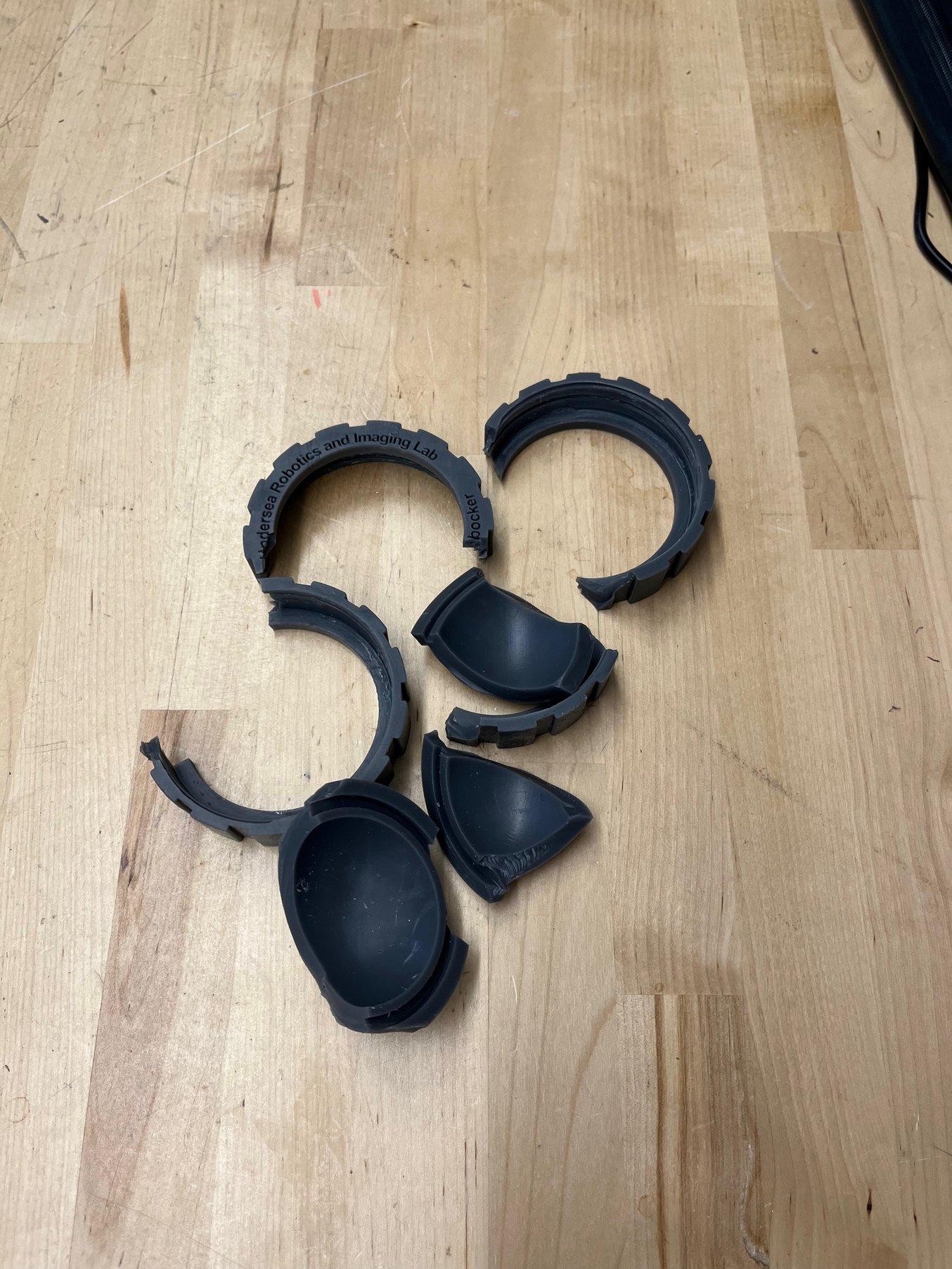
Nylon 12 GF Powder a implosé à la pression la plus faible, soit une moyenne de 1304 psi.
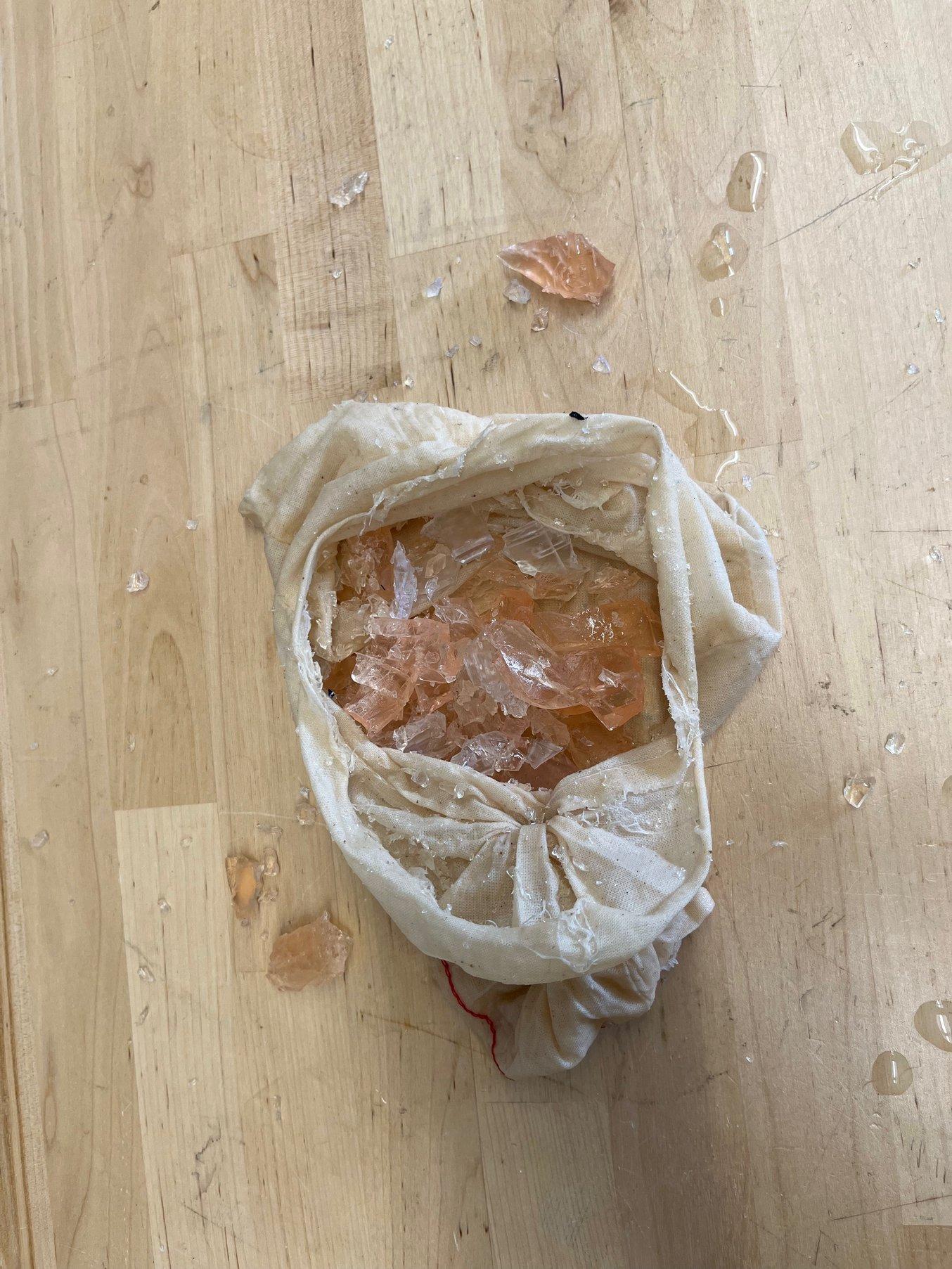
BioMed Amber Resin a résisté à une pression beaucoup plus élevée, implosant à une moyenne de 2907 psi.
Les résultats ont démontré que l'impression 3D SLA et SLS sont des méthodes efficaces pour créer des boîtiers étanches lorsqu'elles sont associées à des joints toriques, l'impression 3D SLA s'imposant nettement, certaines pièces ayant résisté à la pression maximale équivalente à des profondeurs de 4000 m sous le niveau de la mer. Les pièces imprimées par FDM se sont révélées inadaptées à cette application, car elles prennent l'eau dès qu'elles sont immergées et ne peuvent résister à aucune pression.
Les matériaux SLA plus rigides ont fait preuve des meilleures performances sous pression. Des méthodes de post-traitement comme le sablage permettent d'améliorer encore les performances en réduisant la porosité de surface. Pour accéder aux performances complètes et voir comment chaque matériau s'est comporté, téléchargez notre livre blanc.
Pour en savoir plus sur la robotique sous-marine et sur la manière de tirer parti des imprimantes 3D et des matériaux pour fabriquer des enceintes totalement étanches et résistantes à la pression, contactez notre équipe, qui pourra vous mettre en relation avec des experts du réseau Formlabs travaillant actuellement sur ces applications.