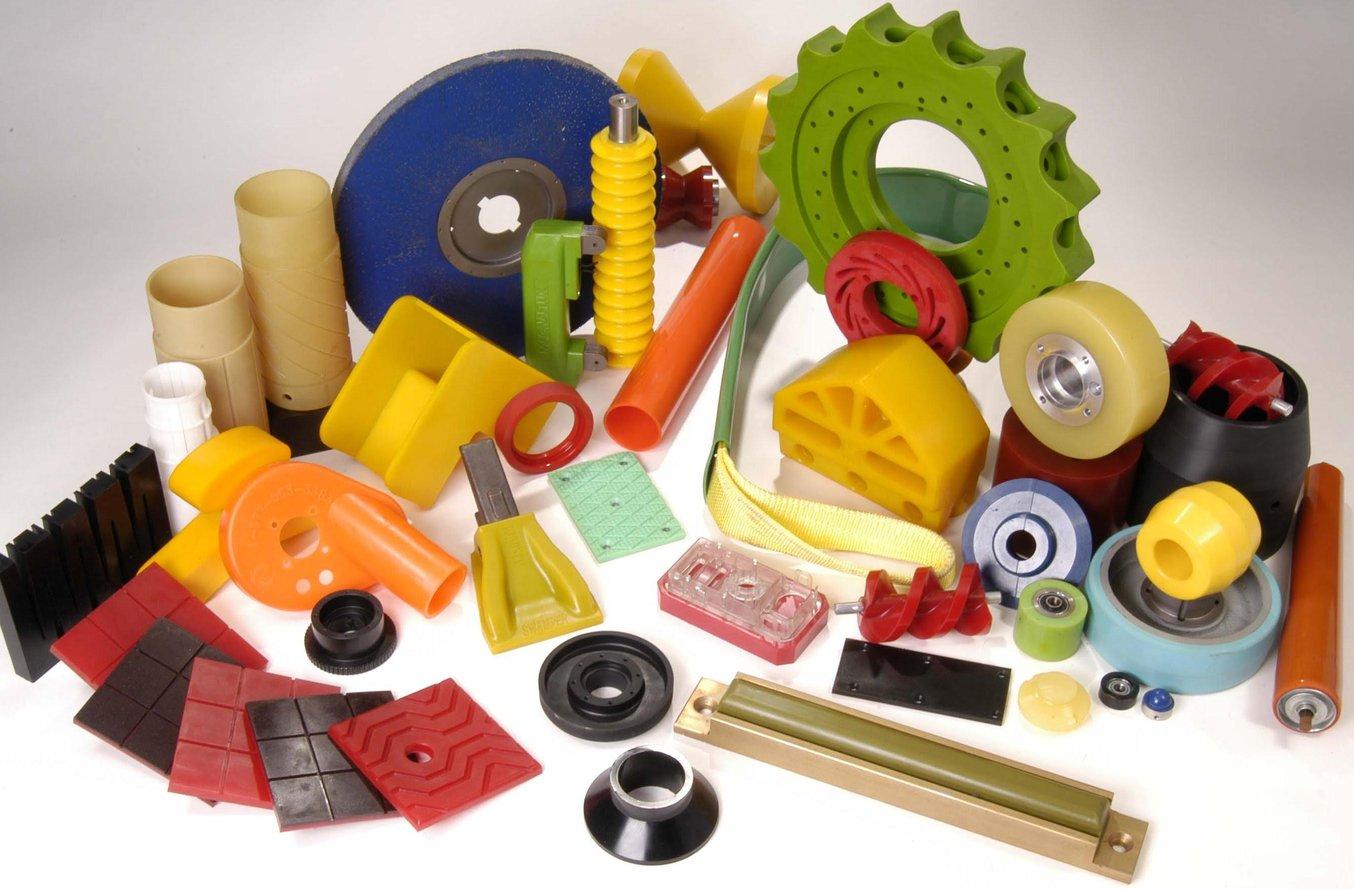
Sono essenziali, ma spesso invisibili: rulli convogliatori per linee di assemblaggio, freni di pattini a rotelle, cunei fermaruota per aerei da caccia e molto altro ancora. Forse non sono la prima cosa a cui pensiamo quando vediamo un prodotto, ma le parti in poliuretano sono fondamentali per il funzionamento di interi sistemi. Perché funzionino correttamente all'interno di assemblaggi più complessi, durante la progettazione le parti in poliuretano devono essere ottimizzate tenendo a mente consumo dei materiali, tolleranze ridotte e deformazione o sostegno di carichi per periodi prolungati.
Kastalon, azienda con sede in Illinois, Stati Uniti, da decenni mette in atto le migliori soluzioni per la produzione di migliaia di parti personalizzate in poliuretano in grado di soddisfare quest'ampia gamma di requisiti. L'ingegnere di prodotto Brian Baer ci ha raccontato come la stampante stereolitografica (SLA) di grande formato Form 3L abbia creato nuove opportunità per la produzione di attrezzature e supporti di produzione, nonché nell'ambito di ricerca e sviluppo di nuovi prodotti.
"Poter realizzare stampi completamente nuovi in 3D è un enorme vantaggio quando si tratta di apportare piccole modifiche. Un altro aspetto fantastico per noi è riuscire a ottenere una tolleranza di +/-0,005. Abbiamo realizzato progetti per noi impensabili in passato e il volume sta aumentando in modo costante."
Brian Baer, ingegnere
Kastalon combina stampa 3D e lavorazione meccanica tradizionale
Kastalon progetta e fabbrica centinaia di stampi personalizzati per produrre centinaia di migliaia di parti in poliuretano. Tradizionalmente, quando i clienti richiedono parti per utilizzo finale, il team di Kastalon ne valuta la fattibilità tramite stampaggio prima di realizzare lo stampo in alluminio o acciaio con la lavorazione meccanica.
In passato, i costi e la complessità del processo di lavorazione meccanica hanno talvolta costretto Kastalon, così come molte altre aziende produttrici di materie plastiche, a rifiutare le richieste di parti troppo complesse per lo stampaggio o non convenienti per la produzione in piccoli volumi e la prototipazione. Gli stampi con numerosi interblocchi, canali minuti o perni erano spesso sconvenienti da progettare, sottoporre a lavorazione meccanica e in alcuni casi rilavorare completamente. Ma rifiutare un ordine non è una scelta di poco conto e così Baer, che aveva lavorato con diverse tecnologie di stampa 3D durante gli anni di studio, ha iniziato a cercare alternative per la fabbricazione degli stampi.
Un precedente tentativo di adozione della stampa 3D aveva lasciato una parte del team insoddisfatta, per cui Baer ha capito di dover tener conto di particolari requisiti nel corso delle sue ricerche. Ciò di cui avevano bisogno era un apparecchio capace di gestire tolleranze di +/-0,005 pollici, materiali in grado di sopportare temperature di stampaggio di 180-300 °F e un sistema con un prezzo accessibile.
"Solo dopo aver scoperto Formlabs, con la sua ampia varietà di materiali capaci di sopportare temperature elevate e di rispondere a requisiti molto specifici, ho capito che questa stampante può effettivamente essere utilizzata per [il] tipo di progetti di cui ci occupiamo."
Brian Baer, ingegnere
Kastalon ha ricevuto la stampante Form 3L alla fine del 2022, ma è stato necessario eseguire alcuni test prima di coinvolgere tutto il team nel processo. Inizialmente, i colleghi erano scettici circa i materiali e le tolleranze possibili, ma dopo aver visto i pezzi di prova stampati da Baer, il loro atteggiamento è cambiato. "Ho stampato e spedito una parte al laboratorio, che ha eseguito un test sulla ruvidità superficiale (RA). Il responsabile del laboratorio è rimasto piacevolmente stupito dalla levigatezza della parte e dalla sua capacità di rispettare i requisiti richiesti", racconta Baer.
Adesso, aggiunge, è lo stesso responsabile del laboratorio a richiedere la fabbricazione delle parti tramite stampa 3D, piuttosto che tramite lavorazione meccanica. "È stato fra le prime persone a suggerire l'utilizzo della stampa 3D per i progetti idonei. Per evitare di sovraccaricare il laboratorio, già sommerso da progetti di grandi dimensioni, il responsabile ci chiede di occuparci delle parti più piccole che possono essere stampate, in modo da lasciargli più tempo per il resto", afferma Baer.
Nuove opportunità per geometrie, test e operazioni
La stampa 3D crea nuove opportunità per lo stampaggio di parti in poliuretano. Il team ingegneristico di Kastalon è ora in grado di sperimentare nuovi elementi e geometrie impossibili da realizzare con gli stampi in metallo, o ancora di apportare piccole modifiche ai design senza il timore di sprecare uno stampo realizzato con la lavorazione meccanica. Il team può serenamente proporre nuovi design perché possono essere eseguiti numerosi test e iterazioni senza sovraccaricare il laboratorio per ogni piccola modifica.
Stampo di morsetto per attrezzo di scuoiatura realizzato tramite stampa 3D
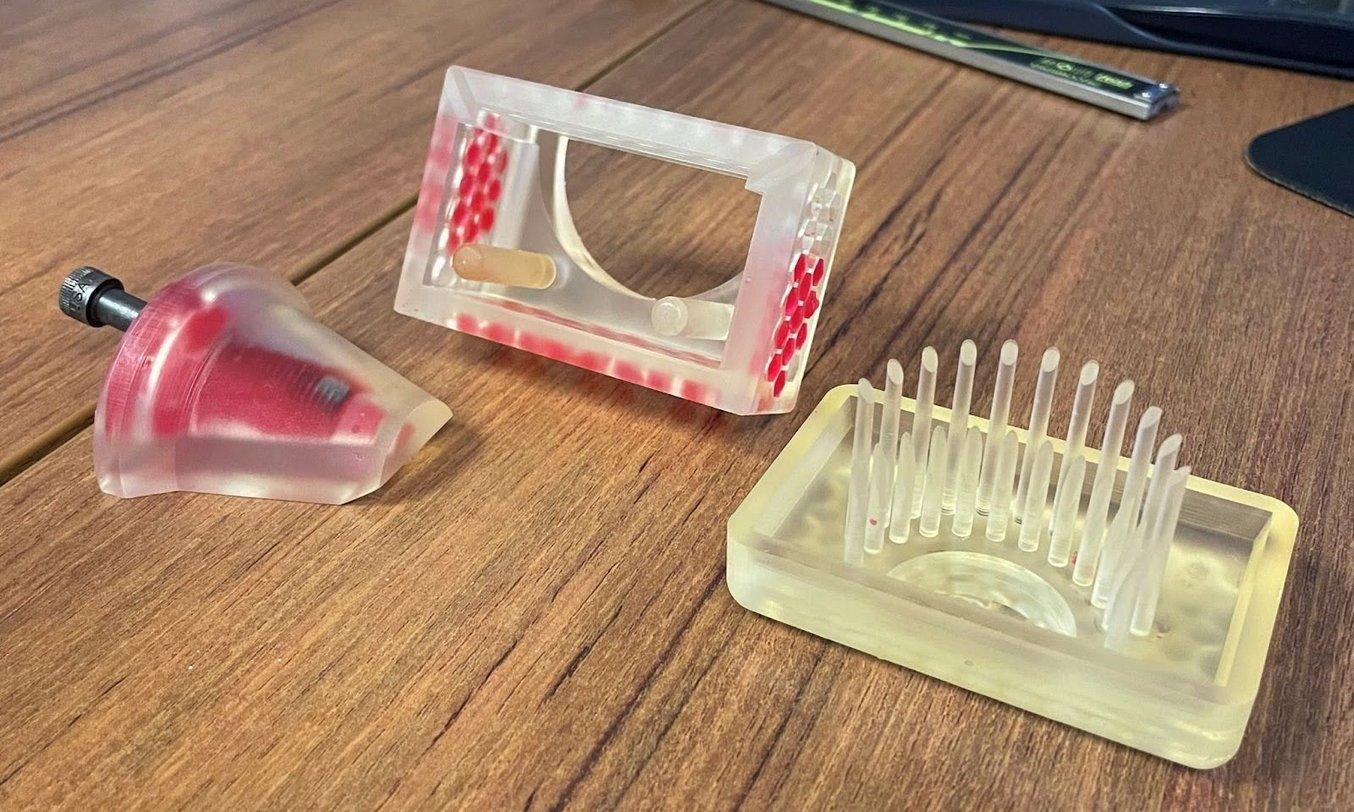
Kastalon è stata costretta a rifiutare la richiesta di un cliente per una parte con 24 fori ciechi sfalsati rispetto alla superficie superiore. Lo stampo sarebbe infatti stato troppo difficile da realizzare tramite lavorazione meccanica.
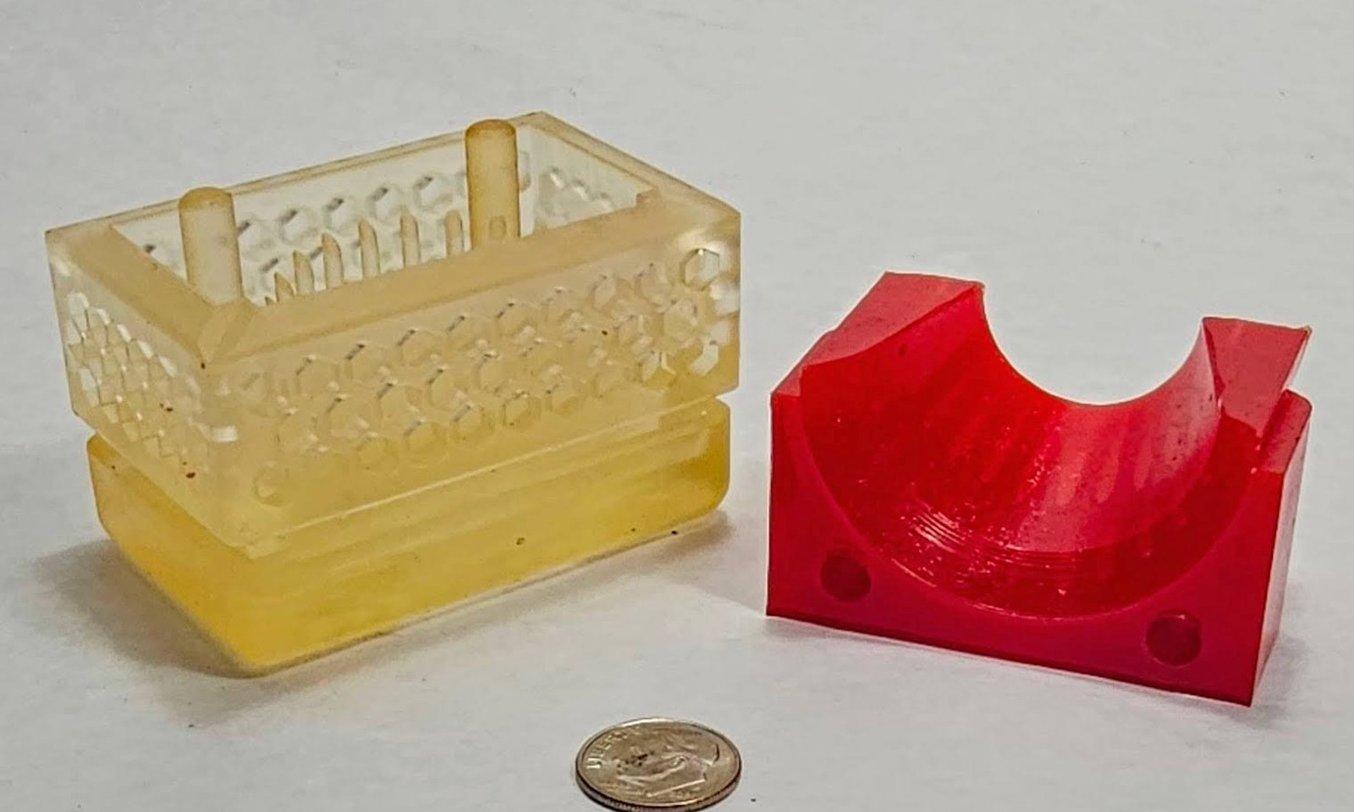
Grazie alla Form 3L e alla High Temp Resin, Baer è stato in grado di stampare e colare la parte in poliuretano finita (a destra) in mezza giornata.
Prima dell'arrivo della Form 3L, il team di Kastalon ha dovuto rifiutare l'ordine di un cliente per lo stampo di un morsetto per un attrezzo di scuoiatura. Sebbene sarebbe stato possibile realizzare lo stampo dopo numerose prove ed errori, la serie di 24 perni alti non avrebbe combaciato con l'altra parte e il gioco tra di essi sarebbe stato di 0,03125 pollici.
Il gioco e la presenza di fori ciechi sfalsati rispetto alla superficie superiore avrebbero richiesto una lavorazione meccanica estremamente difficile, con strumenti di taglio lunghi e molto precisi. Un'altra opzione prevedeva la realizzazione dei perni a uno a uno, per poi inserirli e allinearli secondo il giusto orientamento. Tuttavia, il diametro dei perni di soli 0,104 pollici rendeva il lavoro complesso.
Dopo aver valutato queste diverse possibilità di lavorazione, il team si è trovato costretto a rifiutare l'ordine. "Abbiamo discusso a lungo sulla fattibilità del progetto e la decisione di rifiutare non è stata facile", racconta Baer.
Qualche settimana dopo, in azienda è arrivata la Form 3L, che ha permesso a Baer di progettare e realizzare lo stampo in 3D in mezza giornata, dimostrando la fattibilità della stampa 3D per geometrie complesse come questa. Il costo dei materiali è stato di poco superiore ai 30 $ e la durata della progettazione di circa due ore. "Questa dimostrazione ha reso tutto il team molto fiducioso nei confronti della stampa 3D. Ha aperto gli occhi a molti colleghi che hanno capito che possiamo accettare più ordini grazie all'adozione di questa tecnica", afferma Baer.
Ruota no-crush
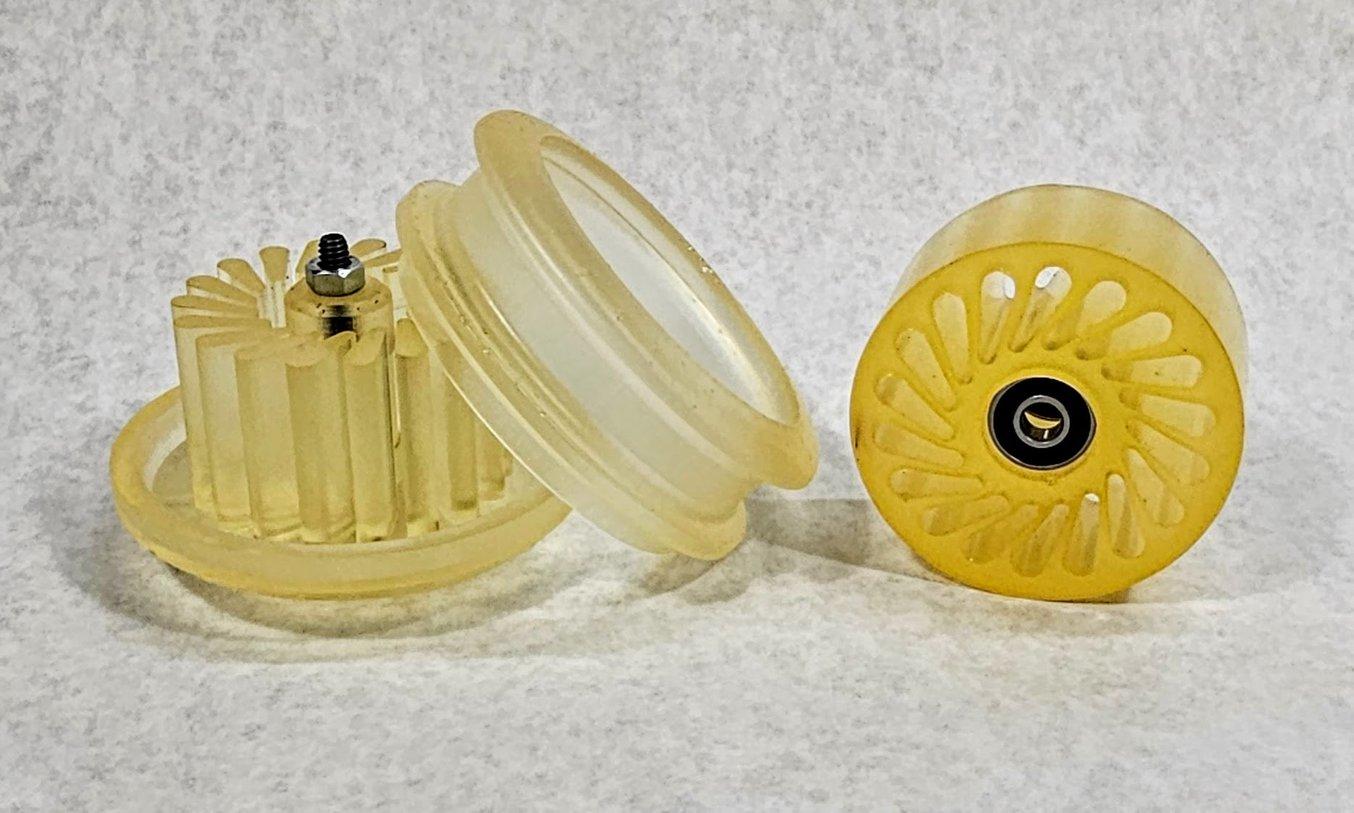
Le ruote (a destra) e i relativi stampi (a sinistra, in alto e in basso) raffigurati nell'immagine sono stati progettati per deformarsi in modo uniforme in caso di sovraccarico. Le aperture a goccia distribuiscono il peso uniformemente per evitare che la ruota schiacci il prodotto.
Nel caso di stampi con dettagli minuscoli troppo difficili da realizzare tramite lavorazione meccanica, la Form 3L dà il meglio di sé. Queste piccole ruote no-crush, utilizzate per trattenere prodotti morbidi, come imballaggi in cartone, su sistemi di convogliamento, sono usate al posto dei pacchi molle: invece di un braccio a molla che esercita una pressione sul cartone, la ruota stessa si deforma in modo uniforme per mantenerlo delicatamente in posizione.
Tuttavia, gli stampi delle ruote presentano un gioco estremamente ridotto tra le alette usate per stampare le aperture a goccia, il che rende la fabbricazione dello stampo praticamente impossibile.
Le ruote hanno una larghezza di due pollici e uno spessore delle pareti tra le alette di 0,125 pollici. "Forse non è impossibile produrre una parte profonda due pollici con un gioco di 0,125 pollici, ma il team tecnico di certo non sarebbe felice di doversi occupare di un design del genere", dice Baer.
Alle difficoltà imposte dalla lavorazione meccanica si aggiunge il fatto che uno stampo in alluminio in più parti complicherebbe il processo di assemblaggio. Ma ci sono alcuni compromessi possibili: realizzare lo stampo con lavorazione meccanica fabbricando le alette in un unico pezzo (come mostrato nell'immagine qui sopra) e sottoporre al laboratorio la complicatissima produzione del gioco, oppure produrre le alette a una a una per poi assemblarle, il che richiederebbe una configurazione più complessa e l'assemblaggio di molteplici piccole parti, con un conseguente aumento di manodopera e malcontento del team tecnico.
La stampa 3D si è rivelata la soluzione più logica. Baer ha quindi facilmente progettato su SolidWorks uno stampo in due parti con un cuscinetto rimovibile, che ha poi stampato utilizzando la High Temp Resin e la Rigid 10K Resin con la Form 3L. Utilizzando la Rigid 10K Resin, il team ha colato 25 ruote per il cliente a una frazione del costo richiesto dalla lavorazione meccanica di uno stampo. "Abbiamo realizzato numerose varietà e stili di ruote dalle dimensioni davvero ridotte. Prima di utilizzare la Form 3L, un lavoro simile sarebbe stato impensabile, perché non conveniente", afferma Baer.
Lavorazione meccanica | Stampa 3D | |
---|---|---|
Numero di componenti | 21 | 3 |
Tempo di progettazione | 7 ore | 3 ore |
Tempo di configurazione | 5 ore | - |
Tempo di esecuzione | 35 ore | 12 ore |
Tempo totale | 47 ore | 15 ore |
Modelli di molle di grandi dimensioni per test interni
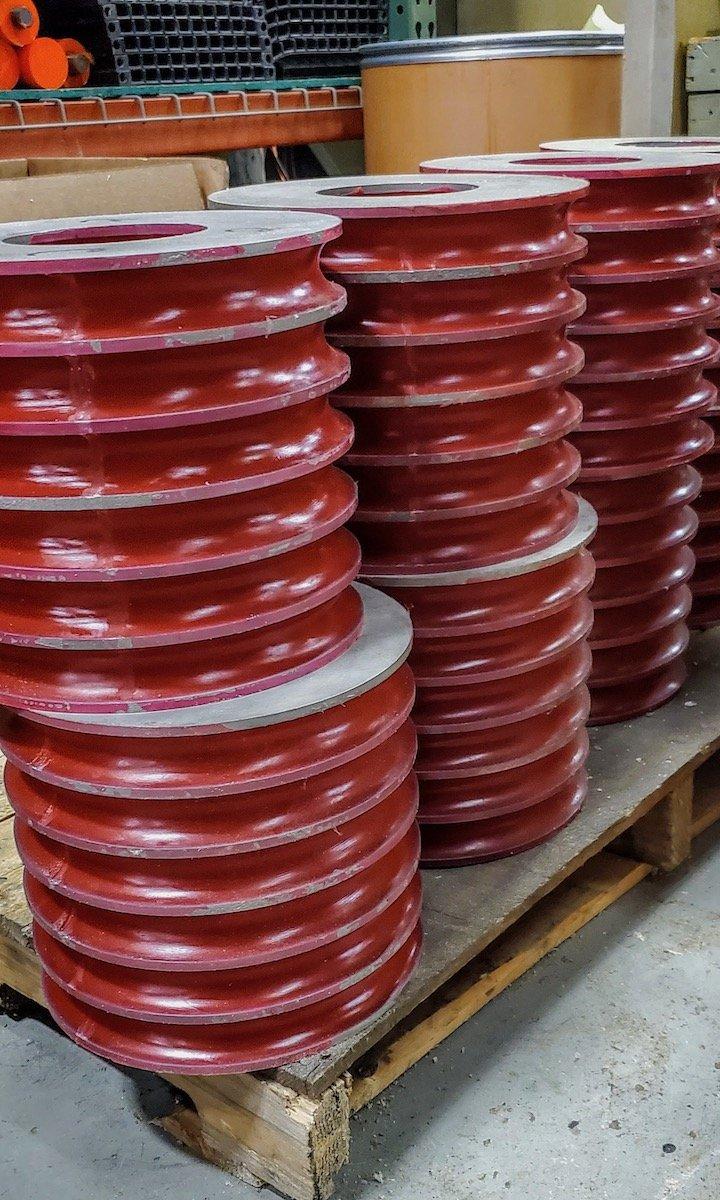
Parti in poliuretano come queste molle rosse vengono tradizionalmente colate a partire da grandi stampi in alluminio.
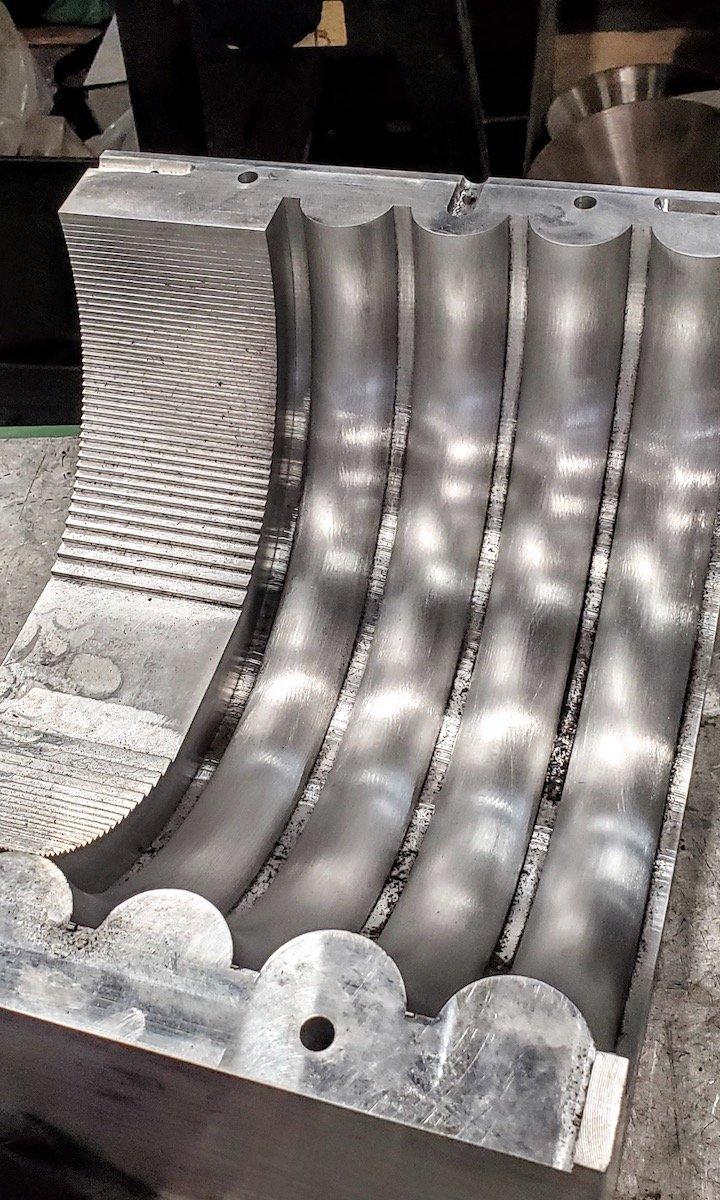
La lavorazione meccanica di questi stampi in alluminio, o talvolta in acciaio, è dispendiosa in termini di tempi e costi.
Lo stadio di baseball della squadra Houston Astros è dotato di una cupola retrattile che si apre in caso di maltempo. Kastalon è responsabile della realizzazione delle molle che tengono la cupola in posizione, anche in caso di uragani.
Prima di fabbricare stampi simili a quelli per le molle da stadio, il team di Kastalon doveva eseguire rigorosi test su design e materiali utilizzando versioni in scala ridotta. Le leggere modifiche al design e i test sui cambiamenti di flessibilità delle molle con diverse geometrie e formulazioni poliuretaniche garantivano l'ottimizzazione del prodotto finale per forti sollecitazioni prolungate nel tempo.
Tuttavia, nonostante le dimensioni ridotte, gli stampi in alluminio risultavano comunque costosi, soprattutto se usati soltanto per test interni. La Form 3L consente ora al team di testare svariati design di molle a un costo di gran lunga inferiore e senza sottrarre tempo prezioso al laboratorio.
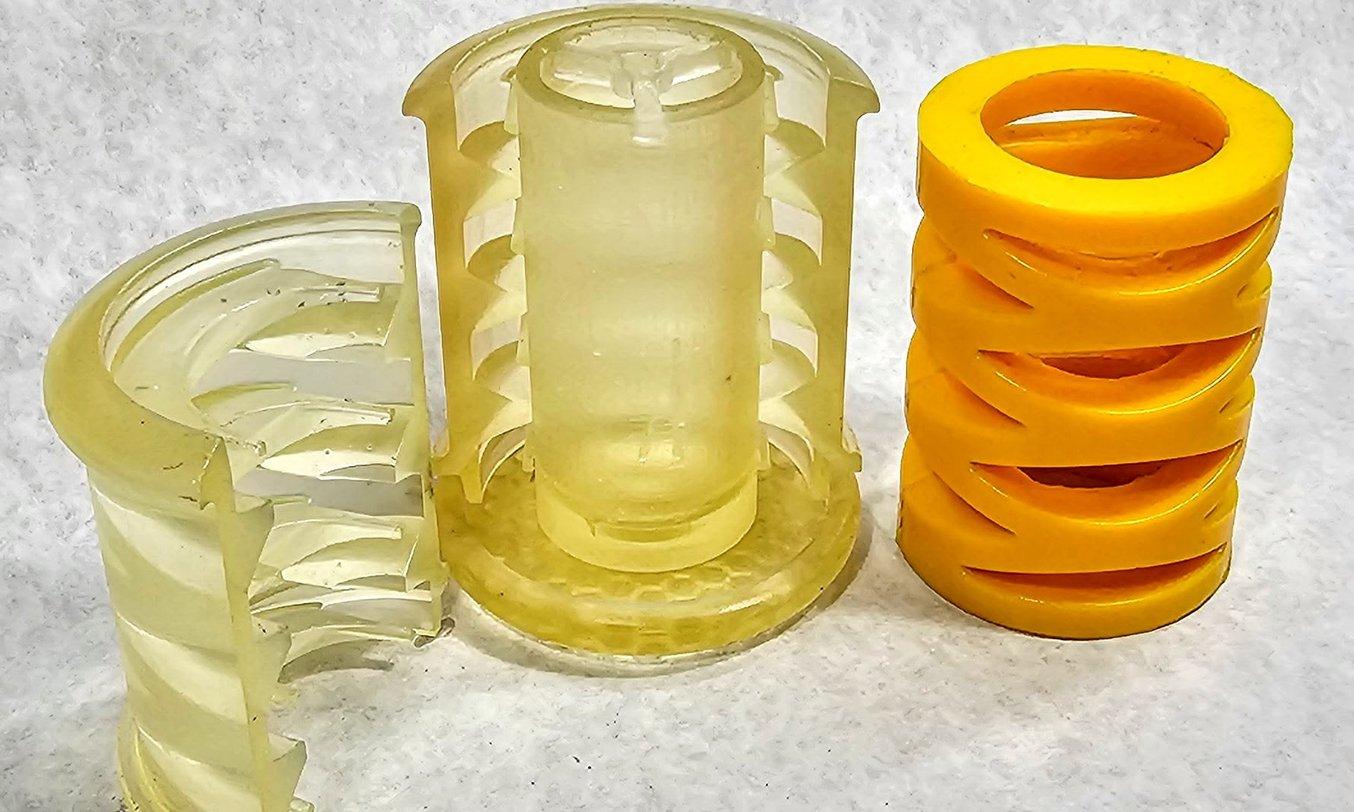
Gli stampi (in High Temp Resin, a sinistra) e le molle colate in poliuretano (di color arancione, a destra) dell'immagine qui sopra sono prototipi la cui geometria è progettata per riprodurre molle a tazza impilate.
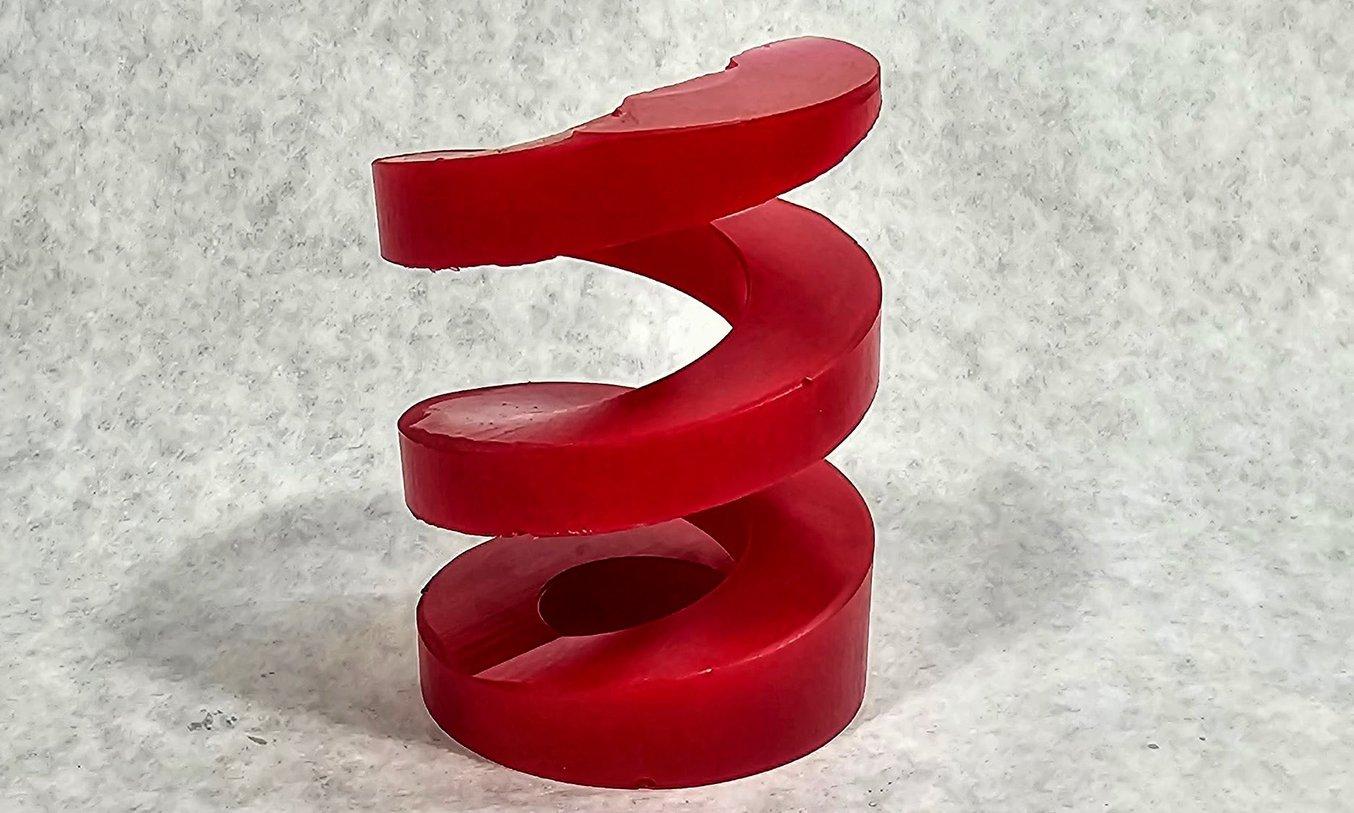
La stampa 3D consente a Baer e al suo team di sperimentare nuove geometrie e design senza aumentare la quantità di lavoro del laboratorio.
"Ora possiamo stampare e testare molte forme e geometrie particolari che prima avrebbero richiesto una quantità inimmaginabile di denaro soltanto per i test o per la fase di ricerca e sviluppo", afferma Baer. La possibilità di testare nuove forme e geometrie complesse senza aggiungere costi elevati per la manodopera e i materiali per la lavorazione meccanica consente a Kastalon non solo di accettare più ordini, ma anche di realizzare parti migliori per la sua clientela.
Stampi di rulli: come evitare la lavorazione meccanica del poliuretano morbido
Il workflow tradizionale per i rulli rivestiti o i manicotti di guida per rulli prevedeva una colata cilindrica di materiale poliuretanico seguita da una fase aggiuntiva di lavorazione meccanica per ottenere la finitura superficiale desiderata e la dimensione necessaria del diametro esterno. La fase aggiuntiva di lavorazione meccanica dei solchi può essere effettuata in vari stili e dimensioni in base all'applicazione del rullo. In questo caso specifico, la lavorazione meccanica di lunghi solchi orizzontali in poliuretano morbido si è rivelata un compito difficoltoso. Per gli ordini in grandi volumi, questa fase manuale richiedeva molta manodopera, con una conseguente riduzione dei guadagni e lunghe ore di lavoro per il laboratorio. "La lavorazione meccanica del poliuretano morbido è complicata e non sempre fornisce buoni risultati o perfette finiture dopo il taglio", spiega Baer.
La realizzazione dei solchi tramite lavorazione meccanica diretta avrebbe richiesto circa tre ore per rullo, ma la stessa tecnica applicata a un solo stampo in metallo era troppo costosa e rischiosa, soprattutto nel caso di uno stampo con una geometria mai sperimentata prima e dal risultato finale incerto. Per realizzare uno stampo in metallo servirebbe uno strumento a filo o un modellatore con testa a dividere, entrambi apparecchi costosi appositi per specifiche geometrie e applicazioni.
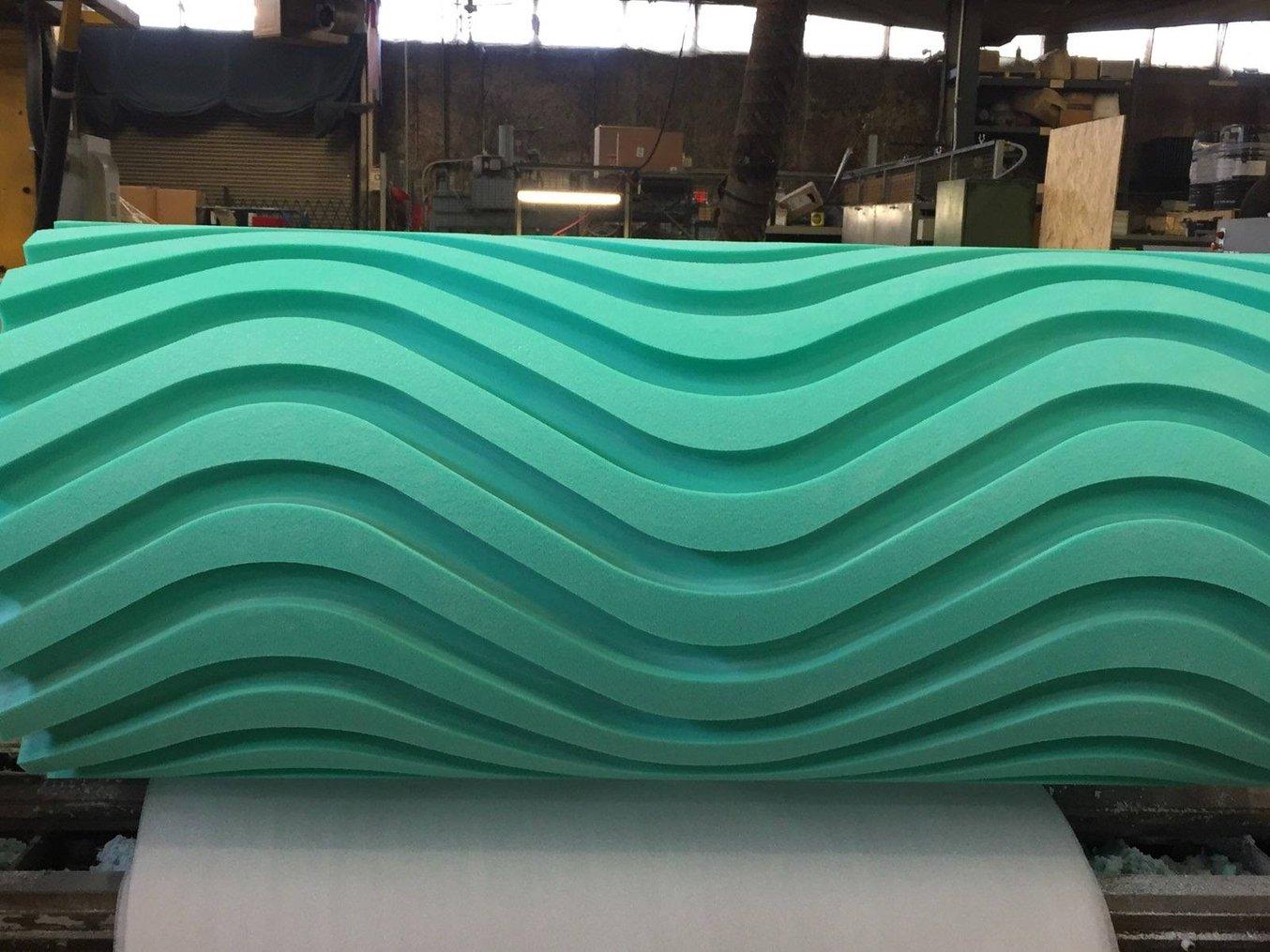
La lavorazione meccanica del poliuretano morbido può essere complicata e dispendiosa in termini di tempo, soprattutto per parti molto grandi come il rullo rappresentato in questa immagine, che è stato colato sotto forma di cilindro e poi sottoposto a lavorazione meccanica per ottenere la forma finale.
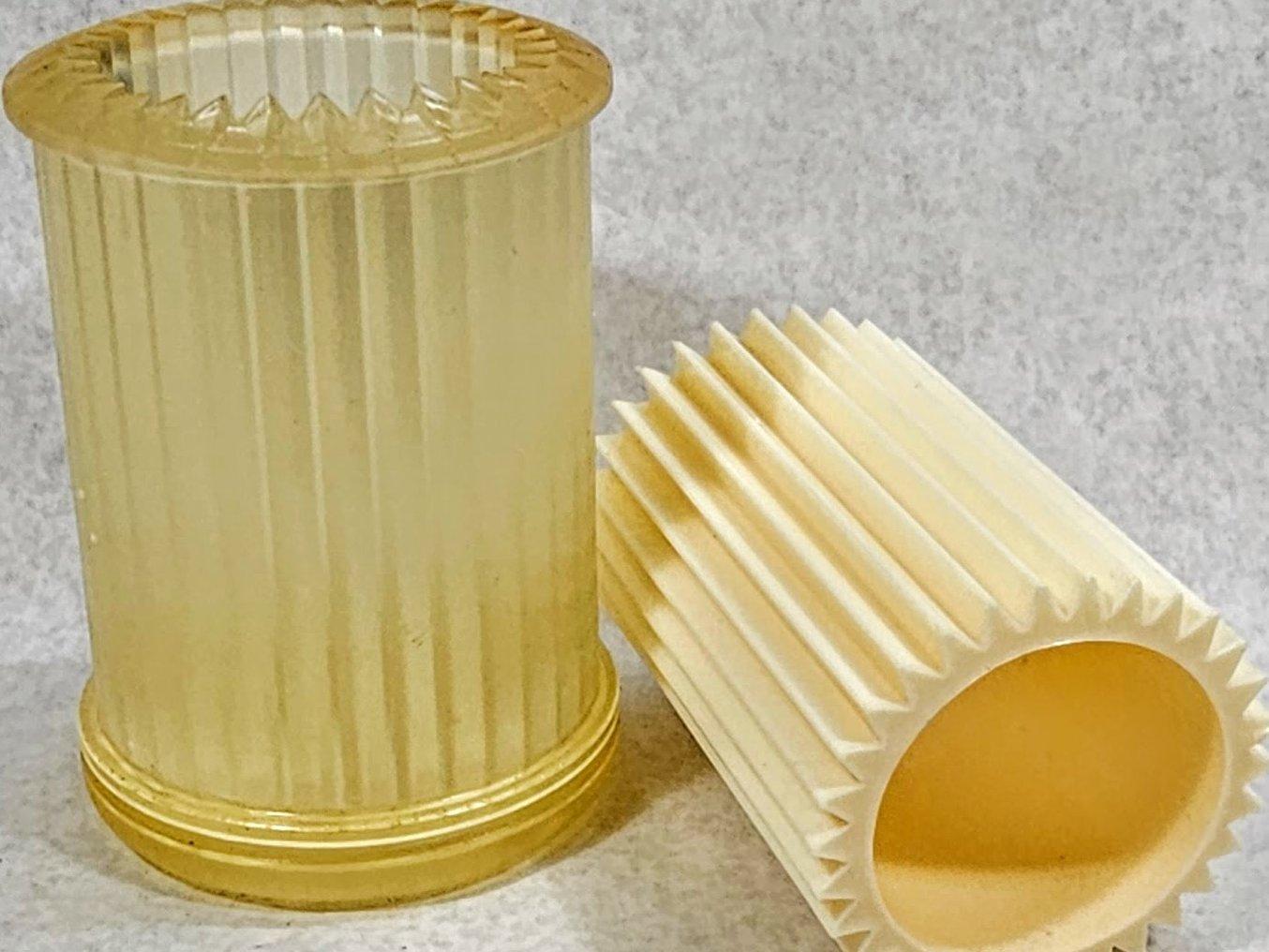
Per parti di piccole dimensioni, la lavorazione meccanica di minuscoli solchi può rivelarsi praticamente impossibile. Baer ha iniziato a realizzare stampi in 3D con solchi preformati, in modo da ottenere con ogni colata una parte completa che non richieda più lavorazione del necessario.
L'ingegnere, consapevole della situazione, si è incaricato personalmente di sperimentare un procedimento diverso. Ha quindi progettato e realizzato uno stampo 3D già dotato di solchi per colare il poliuretano direttamente nella forma desiderata. La stampa diretta con la Form 3L usando la High Temp Resin o la Rigid 10K Resin si è rivelata una soluzione conveniente che ha permesso di eliminare i lunghi interventi manuali.
Per la scelta dei materiali, Baer considera fattori come risoluzione, spessore dello strato, costo al litro, resistenza e colore/trasparenza, e la maggior parte delle volte opta per la High Temp Resin e la Rigid 10K Resin. Per i prototipi, i pezzi unici o le applicazioni di stampaggio in volumi estremamente ridotti, la scelta ricade sulla High Temp Resin per il suo costo inferiore e la trasparenza. Quest'ultima caratteristica è particolarmente utile per i prototipi, poiché rende l'interno visibile e consente di stabilire se occorre apportare delle modifiche. Per le parti da colare in volumi più elevati, il team opta invece per la Rigid 10K Resin, che possiede proprietà meccaniche avanzate. "Ultimamente abbiamo usato la Rigid 10K Resin più spesso, soprattutto per la sua migliore resistenza durante la rimozione dello stampo."
Lavorazione meccanica | Stampo realizzato in 3D | |
---|---|---|
Parti all’anno | 40 | 40 |
Impostazione dello stampo | 1 ora | 1 ora |
Manodopera post-stampaggio per pezzo | 3 ore | 0 ore |
Tempo totale | 160 ore | 40 ore |
Maggiore capacità produttiva e prodotti migliori
In meno di un anno, la Form 3L ha trasformato il processo decisionale di Kastalon. Ormai libero dalle tradizionali limitazioni della lavorazione meccanica, il team ingegneristico può finalmente accettare nuovi ordini considerati un tempo irrealizzabili, e ha ottimizzato i processi che prima richiedevano migliaia di dollari per manodopera e materiali.
"Ora il nostro team ha molta più fiducia in questa tecnologia. I volumi di produzione sono aumentati e in particolare sono in costante crescita gli ordini di stampe da realizzare sulla Form 3L. Siamo in grado di sperimentare con parti nuove e aiutare il team vendite a dare alla clientela ciò che desidera, anche solo per uno o due clienti, semplicemente per dimostrare che si può fare."
Brian Baer, ingegnere
Il team tecnico di Kastalon si è costruito nel tempo una reputazione di precisione, costanza ed eccellenza. Non è stato facile all'inizio convincere il team a introdurre gli stampi realizzati in 3D nel workflow, ma i risultati parlano da soli. Grazie alle comprovate proprietà meccaniche, tolleranze e libertà geometrica rese possibili dalla stereolitografia, anche il responsabile del laboratorio oggi opta per la stampa 3D delle parti.
Per maggiori informazioni sulla produzione rapida di attrezzature, visita la nostra pagina delle applicazioni. Per scoprire la Form 3L, visita la nostra pagina del prodotto.