In che modo Braskem ha usato la stampa 3D per produrre stampi a iniezione per parti per uso finale
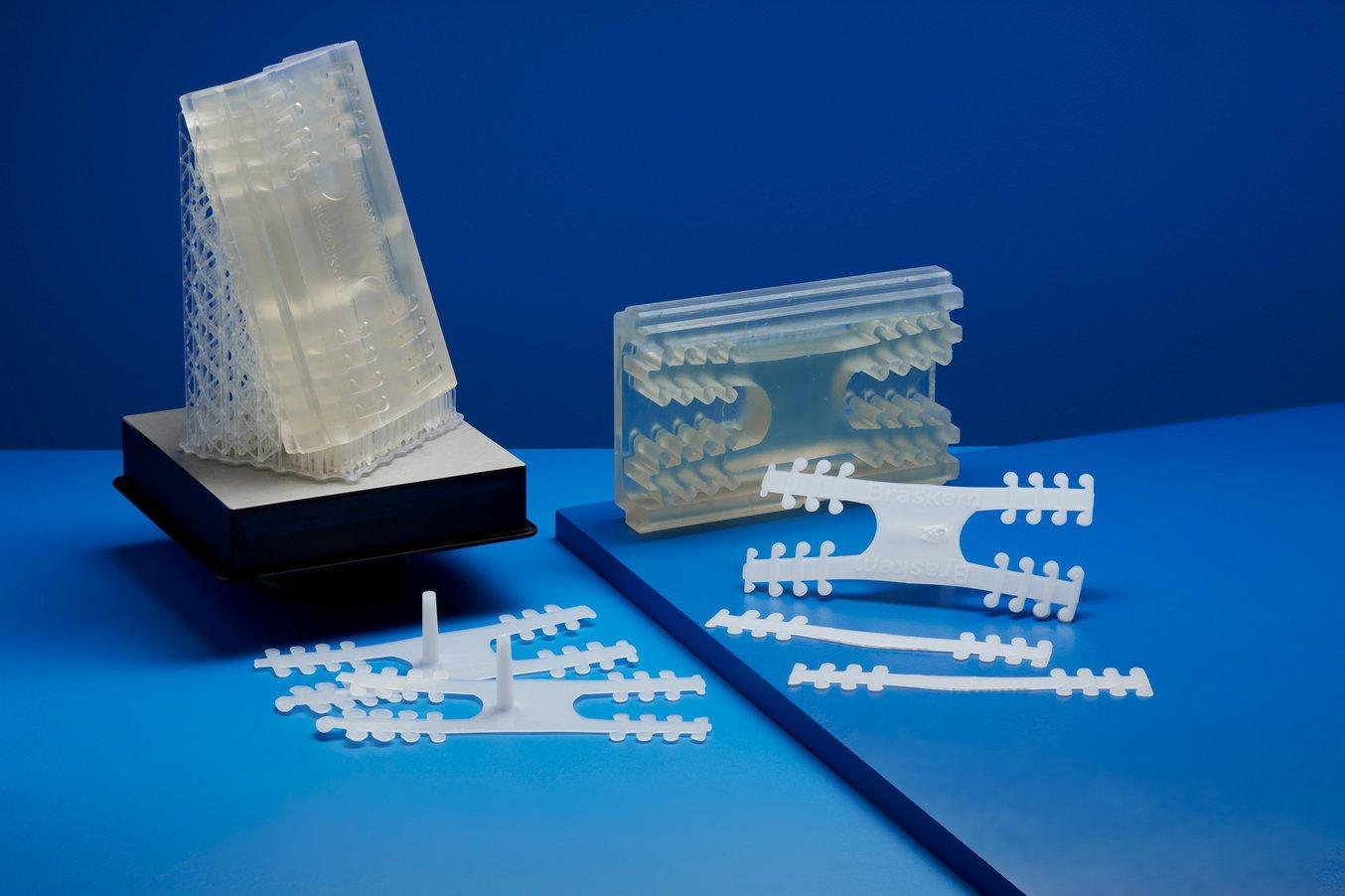
Lo stampaggio viene impiegato in diversi settori da professionisti come progettisti, imprenditori e insegnanti per creare serie di parti identiche. Lo stampaggio a iniezione in particolare è un processo di stampaggio versatile impiegato generalmente per produrre parti su larga scala. Questo metodo, utilizzato su larga scala, è conveniente, altamente efficiente, ripetibile e adatto a realizzare parti di alta qualità. Tuttavia, quando è necessario produrre in quantità minori, i costi e i tempi necessari per fabbricare stampi con normali metalli diventano problematici, e per molte aziende lo stampaggio a iniezione risulta spesso inaccessibile per le piccole quantità.
Come è possibile produrre qualche migliaio di parti identiche nell'arco di una settimana, quando si riceve una richiesta urgente? Rispetto alla fresatura di metalli CNC, l’impiego della stampa 3D per fabbricare stampi a iniezione per la prototipazione e la produzione in piccoli volumi riduce in modo significativo i tempi e i costi, consentendo di produrre parti riproducibili di alta qualità.
Formlabs ha intervistato alcuni professionisti di Braskem, una delle aziende leader mondiali del settore petrolchimico. Michelle Sing e Jack Fallon, ingeneri dello sviluppo tecnologico, Collin Azinger, ingegnere del processo di produzione additiva, e Fabio Lamon, direttore della tecnologia di produzione additiva a livello globale, ci hanno raccontato la loro prima esperienza di stampaggio a iniezione con una parte stampata in 3D.
Produzione rapida di piccoli lotti di stampi per stampaggio a iniezione: una conversazione in diretta
Assisti al dibattito nel quale gli esperti di stampaggio a iniezione spiegheranno come la stampa 3D permetta di produrre stampi su richiesta per la creazione di centinaia di parti, passando dall’idea iniziale alla produzione nel giro di pochi giorni.
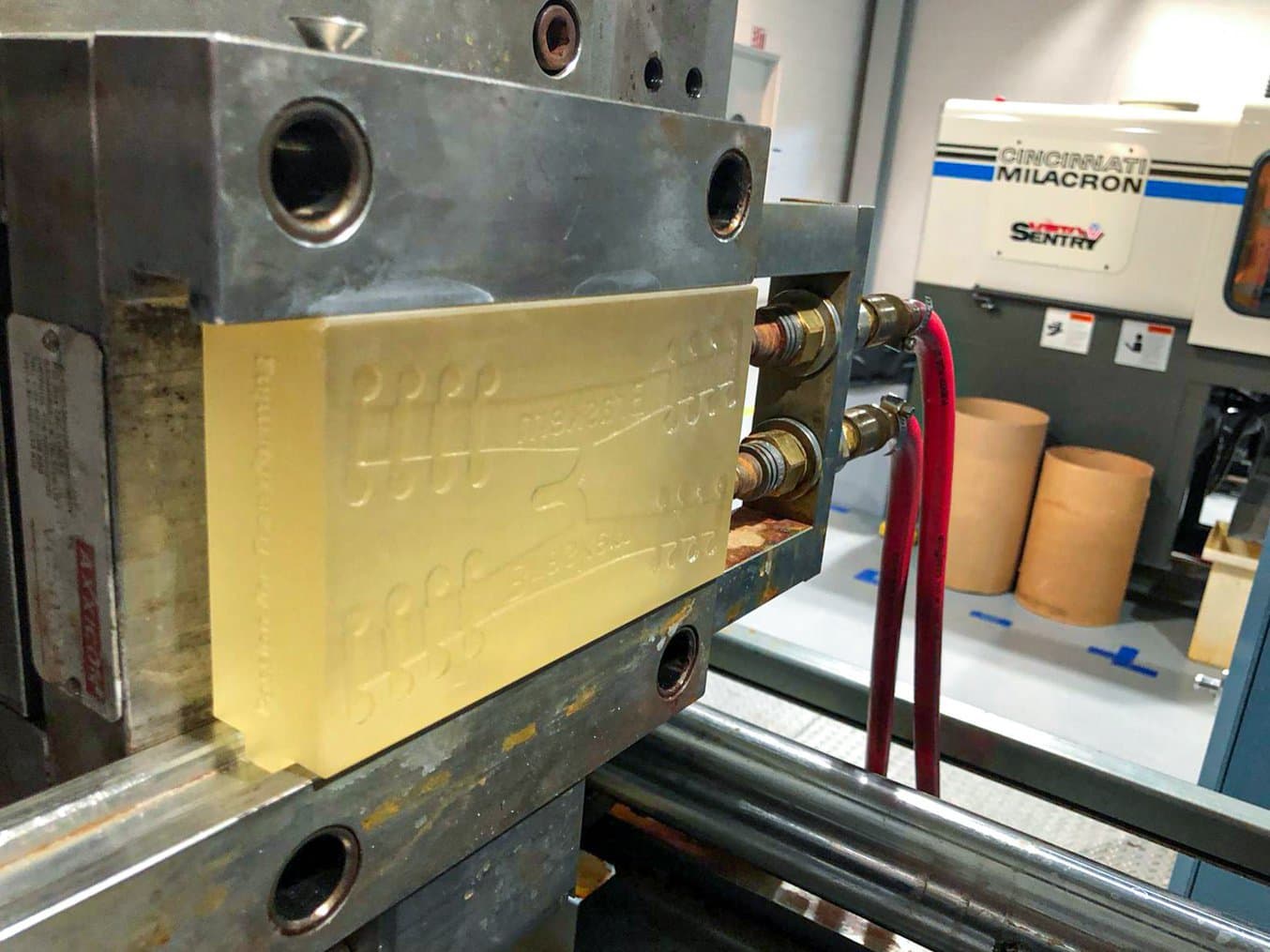
Stampa diretta o stampaggio a iniezione?
Una mattina Jake Fallon ha trovato un'e-mail urgente da uno dei vicepresidenti di Braskem: con la diffusione dell'epidemia COVID-19, l'azienda aveva la necessità di creare migliaia di estensori per mascherine per proteggere i suoi dipendenti in tutto il mondo. Come poteva fare Jake a soddisfare la richiesta con l'attrezzatura a disposizione di Braskem in 48 ore?
Quando Jake ha incontrato i suoi colleghi del team di produzione additiva di Braskem, la loro prima idea è stata quella di stampare gli estensori direttamente in 3D con una stampante a modellazione a deposizione fusa (FDM). Ma, anche con la velocità della modellazione a deposizione fusa, hanno stimato che ogni estensore avrebbe richiesto 17 minuti. Data la necessità di realizzare migliaia di estensori, il tempo complessivo sarebbe stato eccessivo. In aggiunta alle stampanti FDM da banco, il Pittsburgh Tech Center di Braskem aveva a disposizione anche una Form 3 di Formlabs e l'attrezzatura industriale necessaria per lo stampaggio a iniezione. Questo ha dato origine a un’idea, ma c’erano moltissime incognite.
Che cosa può offrire lo stampaggio a iniezione? Lo stampaggio a iniezione è noto per essere un metodo veloce ed efficiente per produrre parti in serie, ma all'inizio l'idea di realizzare in 3D uno stampo in plastica per l’apparecchio completamente elettrico Cincinnati Milacron 110 Ton Roboshot destava alcune perplessità. Uno stampo in plastica sarebbe stato in grado di resistere alla pressione dell’apparecchio? Si sarebbe rotto dopo 50, 500 o addirittura 1000 gettate?
Braskem ha scelto la High Temp Resin, un materiale Formlabs in grado di realizzare stampi e inserti che possono essere utilizzati in processi impegnativi come lo stampaggio a iniezione per produrre parti per uso finale in materiali di produzione. La High Temp Resin ha una temperatura di distorsione termica di 238 °C a 0,45 MPa. Questa scelta ha avuto grande importanza, perché il team doveva mantenere la pressione al minimo per ridurre i rischi di rottura del punto di iniezione dello stampo. Questo richiedeva una temperatura più alta in modo da ridurre la viscosità e la High Temp Resin era il materiale ideale per sopportare le temperature elevate e le pressioni minori necessarie per questo specifico stampo.
Il team ha progettato uno stampo che produce due estensori per ogni gettata. Una volta estratto lo stampo realizzato in 3D dalla Form 3, sono stati rimossi i supporti ed è stato sottoposto a un processo di levigazione minimo. Man mano che le gettate si solidificavano, sono stati accumulati molti estensori. Nello stampo è stato iniettato un polipropilene flessibile a bassa viscosità in modo da ridurre la pressione all'interno della cavità e allungare la vita utile dello stampo realizzato in 3D.
La prima iterazione in assoluto dello stampo ha resistito a una pressione per il serraggio di 5 tonnellate, a un tempo di ciclo di 20 secondi, a una velocità di iniezione di 0,5 in/s, e a una pressione di mantenimento di 5000 psi per ~8 secondi. Le temperature di stampaggio medie erano intorno ai 230 °C.
“Abbiamo usato la High Temp Resin V2 a 50 micron. La qualità era ottima e la risoluzione fantastica. A prima vista sarebbe stato molto difficile distinguere la parte da una realizzata con uno stampo in metallo."
Jake Fallon
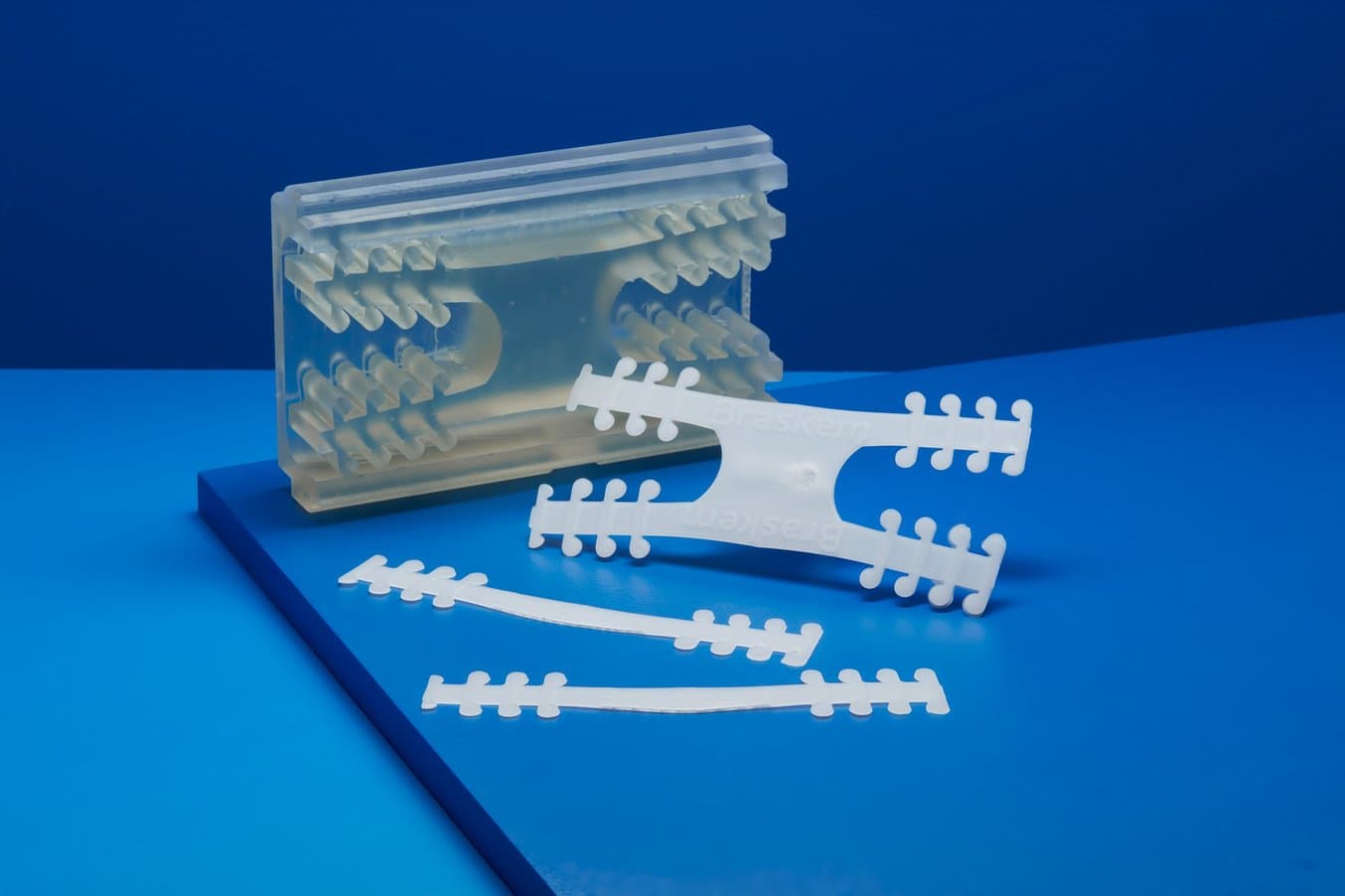
Il team ha utilizzato un normale agente spray distaccante: una confezione è bastata per una quantità tra le 40 e le 50 gettate. Il fatto di stampare a uno spessore dello strato di 50 micron ha aumentato l'efficacia dello spray, creando una finitura superficiale liscissima che ha permesso di rimuovere le parti dallo stampo con facilità. Non è stato necessario un ulteriore raffreddamento per lo stampo realizzato in 3D; e non c'è stato nessun segno di reazione tra il materiale iniettato e la resina stampata.
Se non avesse avuto accesso alla stampa 3D, Braskem avrebbe dovuto far produrre a terzi un costoso stampo in metallo, con grande dispendio di tempo e denaro. Grazie alla stampa 3D il team ha prodotto migliaia di estensori nel giro di una settimana dall'arrivo dell’e-mail del vicepresidente, e ha potuto spedirli agli uffici in tutto il mondo.
Iterazioni di design e iniezioni
"Con le iterazioni di design abbiamo ridotto del 28% il materiale utilizzato"
Jake Fallon
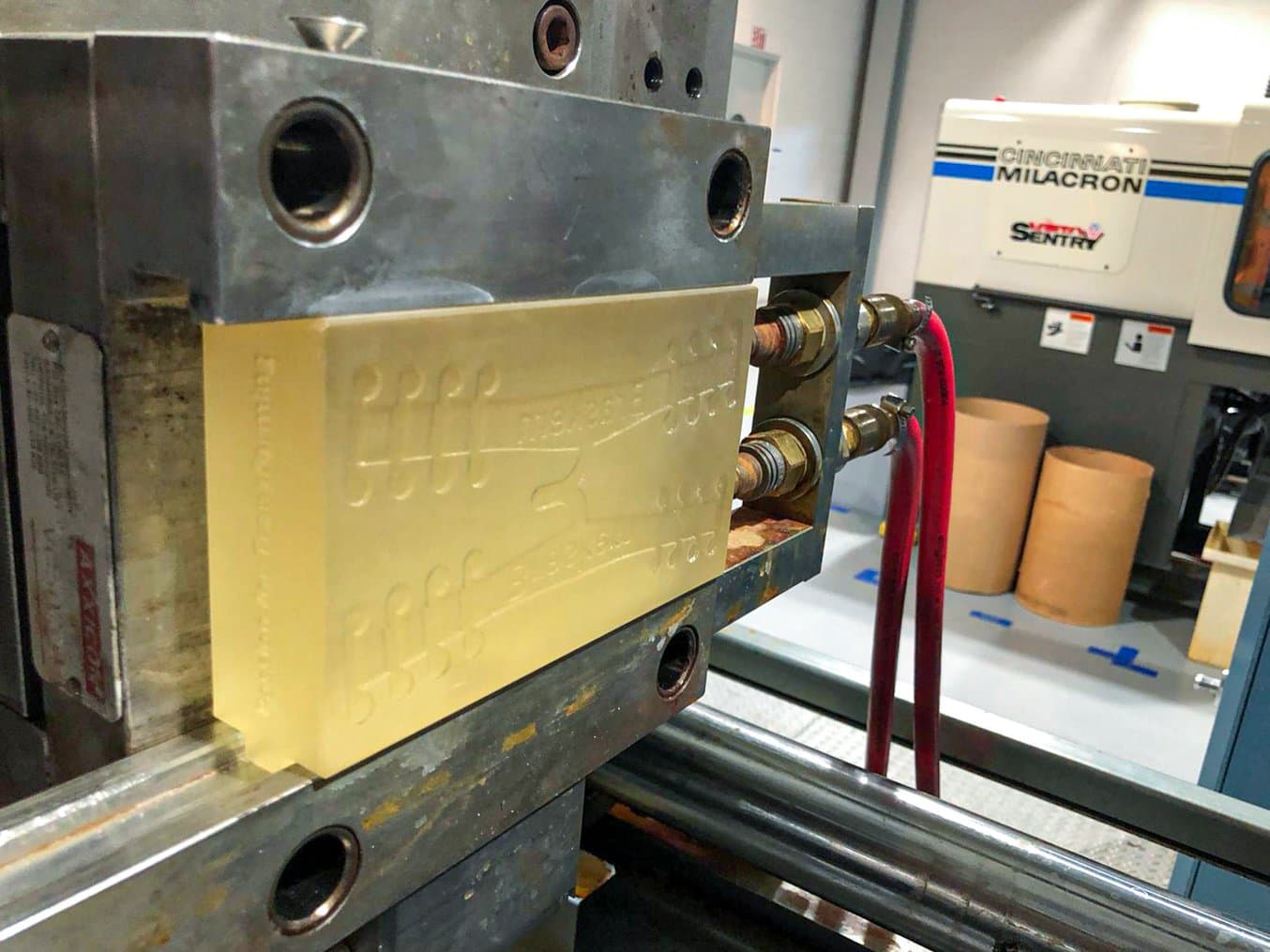
Mentre l’apparecchio Roboshot creava gli estensori, Jake ha ripreso il suo software CAD per modificare il design dello stampo, con l'obiettivo di allargare il punto di iniezione. Jake voleva ridurre la pressione e aumentare il flusso all'interno della cavità per allungare la vita utile dello stampo ed evitare fuoriuscite di materiale. Durante il processo di rifinitura è riuscito a ridurre del 28% la quantità di High Temp Resin usata per realizzare lo stampo, facendo così risparmiare denaro all'azienda e accorciando il tempo di stampa.
Anche se lo stampo V1 aveva funzionato al primo tentativo, lo stampo V2, ora dotato di un punto di iniezione più ampio, è stato progettato per sopportare migliaia di gettate. Il nuovo stampo può sopportare almeno 1500 gettate prima di dover essere sostituito, e questo ha permesso al team di produrre gli estensori necessari. Il nuovo stampo potenziato, che permetteva di creare quattro estensori al minuto, era proprio quello di cui il team aveva bisogno per completare la sua missione.
Il team di Braskem prevede decine di potenziali usi futuri per gli stampi realizzati in 3D. Gli stampi economici, i cui costi di produzione non superano i 100 $ a unità, potrebbero aiutare i clienti a realizzare rapidamente parti in piccoli lotti. Un esempio è il packaging stagionale per valorizzare un determinato prodotto in corrispondenza di un particolare momento dell'anno. Prima le aziende più piccole non avrebbero potuto compensare i costi di stampi e attrezzature in metallo. Ma la realizzare in 3D di stampi che sopportano migliaia di gettate potrebbe aprire nuove possibilità di marketing e branding.
Scopri di più
"Il tempo è stato il nostro vantaggio principale. Abbiamo testato lo stampo in una settimana, e ci è bastato un giorno per creare un secondo design che ha apportato migliorie significative."
Jake Fallon
Il team di Braskem è rimasto colpito dal modo in cui lo stampaggio a iniezione ha permesso di estendere l’utilizzo della loro stampante 3D al di là della prototipazione rapida, e nell'ambito della produzione. Con centinaia di materiali a disposizione per lo stampaggio a iniezione, Braskem è stato a lungo un partner affidabile per le aziende che utilizzano lo stampaggio a iniezione per la produzione in serie. Inoltre la società vende oltre 300 materiali per la termoformatura, lo stampaggio per soffiaggio e altri processi di fabbricazione che potrebbero trarre vantaggio dagli stampi realizzati in 3D.
In futuro il team vorrebbe esplorare le possibilità dello stampaggio a iniezione con la Form 3L, data la sua capacità di creare parti di grandi dimensioni. Secondo Jake "lo stampo realizzato in 3D era appena sotto i limiti di volume di stampa della Form 3; non vediamo l'ora di esplorare le opportunità offerte dalla Form 3L."
Scarica il nostro whitepaper gratuito o guarda il webinar per conoscere il workflow del processo nel dettaglio e ottenere linee guida per la progettazione e altre buone pratiche su come utilizzare stampi realizzati in 3D per i processi di stampaggio a iniezione e vedere i casi studio reali di Novus Applications e Holimaker.