Un veicolo su tre che esce dalla catena di montaggio ogni giorno contiene almeno un componente realizzato da Brose, una delle cinque aziende a conduzione familiare fornitrici di componenti per automobili più grandi al mondo. Fondata oltre un secolo fa a Berlino da Max Brose, l'azienda era inizialmente un'attività di commercio di accessori per automobili ed è poi diventata leader di mercato nei sistemi meccatronici. I prodotti di Brose, come assemblaggi per sedili, portelloni e portiere, sono progettati e prodotti per BMW, Volvo, Ford, Mercedes, Jeep e molti altri dei più grandi marchi automobilistici.
Il costante sviluppo di Brose e le collaborazioni di successo a lungo termine con queste aziende produttrici di componenti sono dovute in parte all'impegno dell'azienda verso l'innovazione e il miglioramento continui. La stampa 3D ha un ruolo fondamentale in molti dei suoi processi di design e produzione per l'utilizzo finale e permette all'azienda di adattarsi ai rapidi cambiamenti nel settore automobilistico.
Abbiamo visitato Brose North America, sede centrale dell'azienda, che si trova ad Auburn Hills (Michigan), e Brose New Boston a New Boston (Michigan), uno dei suoi più grandi stabilimenti di produzione per utilizzo finale, per scoprire come vengono utilizzate le stampanti 3D stereolitografiche (SLA) e a sinterizzazione laser selettiva (SLS). Matthias Schulz, responsabile della divisione di prototipazione dei sedili e del team di tecnologia additiva in questa regione, ci ha spiegato come Brose utilizzi la stampa 3D in tutto il processo, dal design alla produzione di parti per utilizzo finale, rispettando i tempi ristretti richiesti dalle aziende produttrici di componenti.
"Negli ultimi cinque anni, abbiamo assistito a rapidi cambiamenti nel settore automobilistico. I tempi di sviluppo dei nuovi prodotti si sono notevolmente ridotti, costringendoci ad adattarci: dobbiamo integrare sempre più la tecnologia additiva, che non solo riduce i tempi di produzione delle attrezzature, ma ci consente anche di accelerare la consegna delle parti."
Matthias Schulz, responsabile della prototipazione dei sedili presso Brose North America
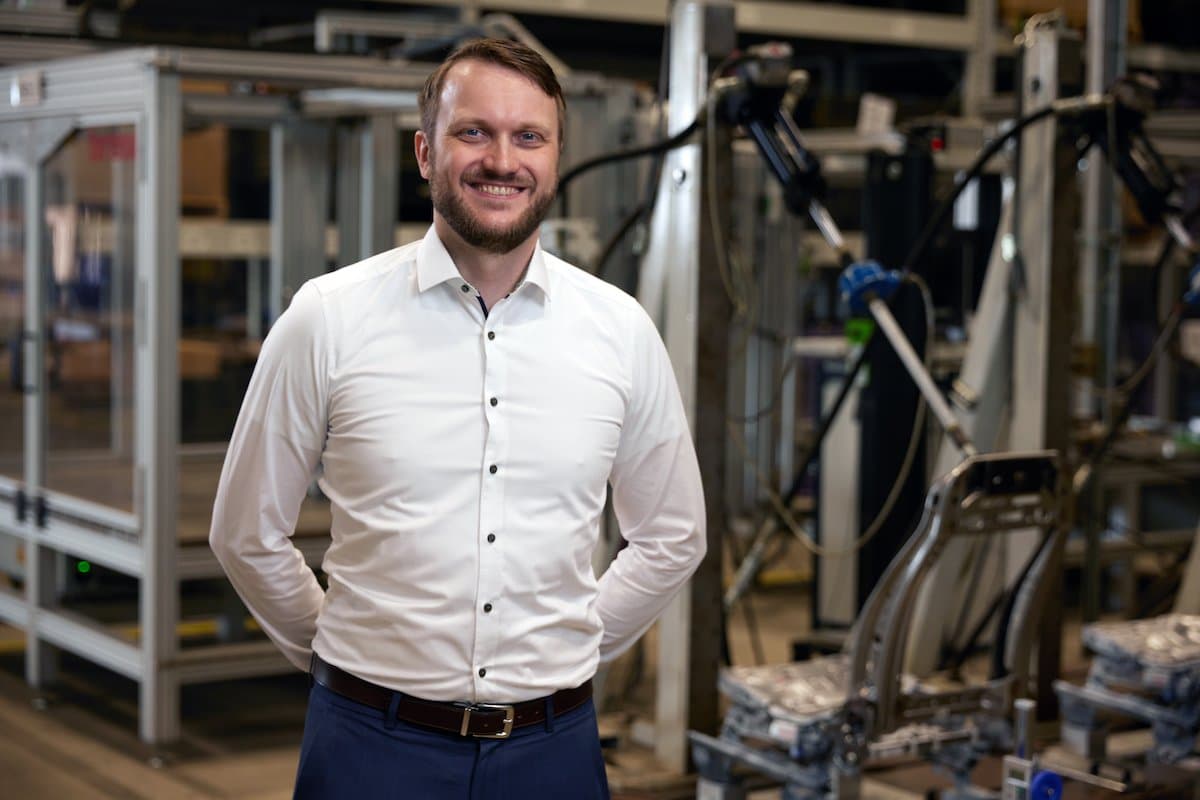
Webinar su richiesta: Come Brose usa la SLS per realizzare parti per utilizzo finale per il settore automobilistico
In questo webinar su richiesta, Matthias Schulz, responsabile della prototipazione dei sedili presso Brose North America, dimostra come l'azienda utilizzi le tecnologie SLA e SLS per qualsiasi attività, dalla produzione rapida di dime di saldatura ai cicli di produzione di 250 000 parti per utilizzo finale.
Prototipazione: non solo pezzi unici
La prototipazione è una delle applicazioni più comuni e ideali per la stampa 3D. Sebbene Brose utilizzi diverse stampanti 3D a modellazione a deposizione fusa (FDM), SLA e SLS per i prototipi, i volumi non sono quelli tipici delle parti Proof-of-Concept. Per Brose, un volume tipico di prototipi si aggira intorno alle 500 o 1000 unità.
"Utilizziamo la stampa 3D su larga scala. 'Prototipazione' per noi significa produrre diverse centinaia di parti, soprattutto in base al numero di test che dobbiamo effettuare. Oltre a soddisfare gli standard interni ed esterni, dobbiamo rispettare anche i requisiti federali. Questi ultimi ci impongono di stampare una certa quantità di parti, che generalmente equivale a 700-800 unità per prototipo", spiega Schulz.
Quantità minime elevate rendono la SLA la scelta migliore: smorzatore per la regolazione del sedile in gomma
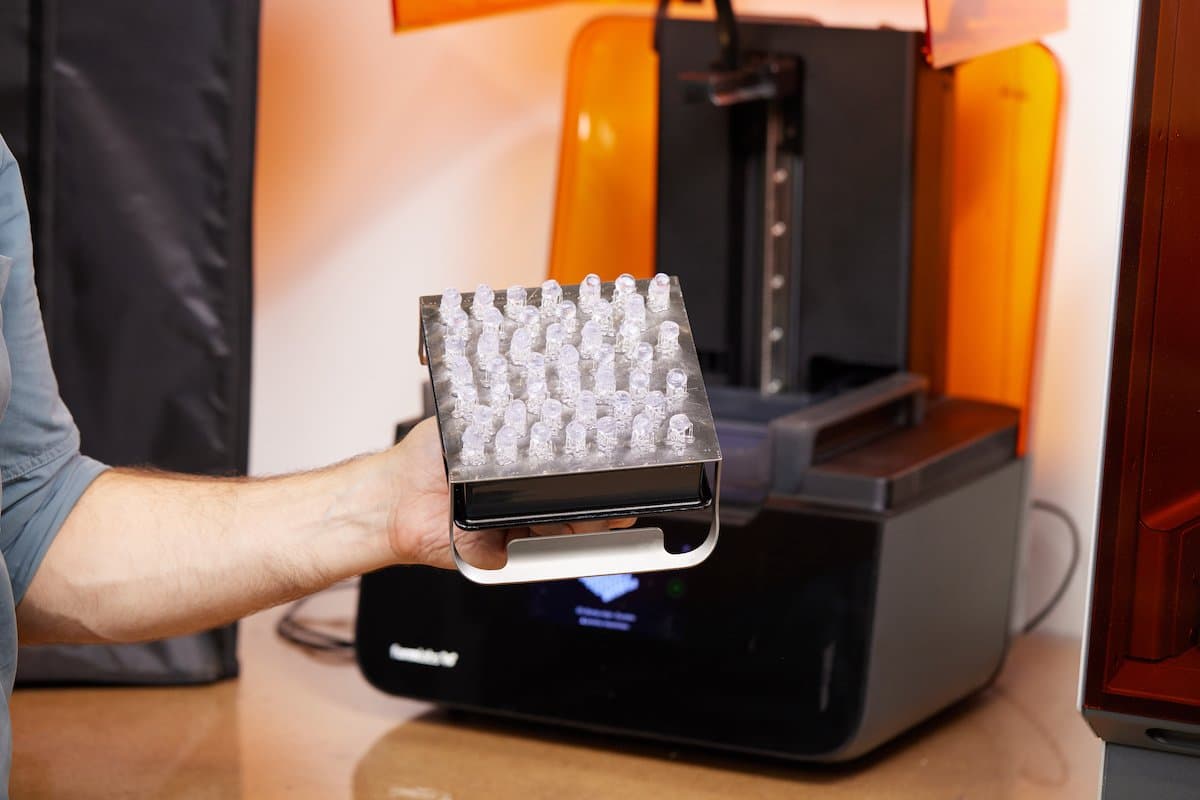
Questi prototipi sono piccoli smorzatori progettati per ridurre il rumore e migliorare il feedback tattile del gruppo sedile in metallo quando tocca il telaio del sedile. L'esternalizzazione avrebbe richiesto un ordine minimo di diversi milioni di unità, quindi Schulz e il suo team hanno deciso di realizzarli con le stampanti della serie Form per effettuare i test.
Per un progetto, il team di prototipazione aveva bisogno di utilizzare uno smorzatore in silicone morbido installato all'interno di un gruppo sedile. Questa parte serve a ridurre i rumori durante il movimento del sedile sul telaio, migliorando anche il feedback tattile e acustico del movimento del gruppo sedile. Coinvolgere un'azienda fornitrice estera che si occupa di produzione in serie avrebbe comportato un ordine minimo nell'ordine dei milioni di unità, mentre a Brose ne servivano solo poche centinaia per un test preliminare di design.
Oltre all'elevato costo di acquisto e spedizione di milioni di parti, i tempi di produzione erano di diverse settimane, con il rischio di dover conservare molte parti non necessarie che sarebbero poi diventate rifiuti. Invece di ordinare la parte, è stato utilizzato il software CAD già in uso per stamparne rapidamente diverse centinaia sulla Form 4, completando il tutto in una settimana. Questa soluzione ha ridotto sia i costi complessivi che i tempi di produzione del progetto.
"Siamo riusciti a stamparli con la Form 4 a un costo decisamente inferiore rispetto a quello che avremmo speso per la spedizione dall'estero e l'ordine di una quantità minima, che ci avrebbe costretto a ordinare diversi milioni di parti. Li abbiamo avuti rapidamente a disposizione e non abbiamo dovuto aspettare."
Matthias Schulz, responsabile della prototipazione dei sedili presso Brose North America
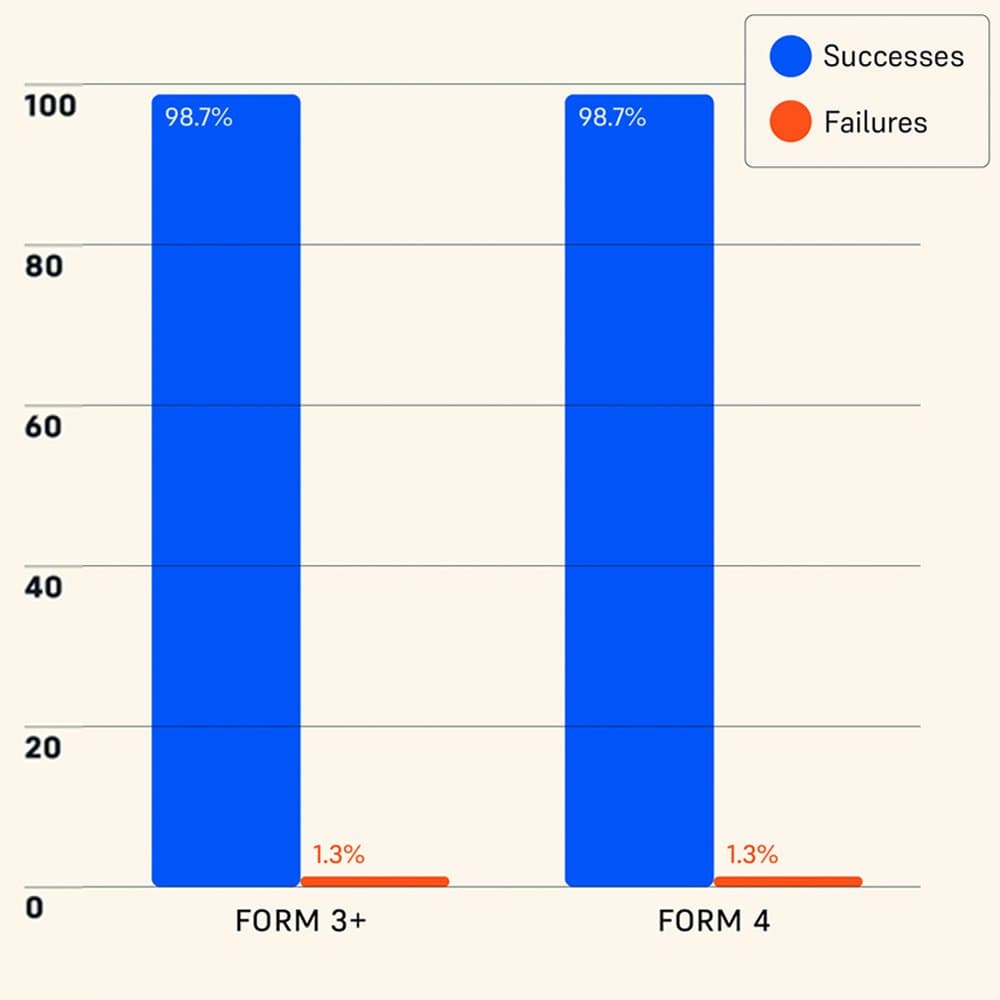
Affidabilità testata in modo indipendente della Form 4 e di altre stampanti 3D a resina
Un'azienda indipendente leader mondiale dei test sui prodotti ha misurato per la Form 4 di Formlabs un tasso di riuscita della stampa del 98,7%. Per leggere una descrizione dettagliata della metodologia del test e i risultati completi, scarica il nostro whitepaper.
Combinazione di SLA e SLS per prototipi con volumi elevati
Quando i componenti sono più complessi, grandi e voluminosi, Brose ricorre alla sua flotta di tre stampanti 3D SLS della serie Fuse per la prototipazione e la produzione. La stampa 3D SLS, grazie al letto di stampa autoportante, permette di realizzare volumi di produzione completi. Inoltre, la resistenza e le proprietà meccaniche del nylon sinterizzato rendono questa tecnologia perfetta per i componenti per utilizzo finale. In un progetto recente, il team di tecnologia additiva di Brose ha impiegato sia la tecnologia SLA che quella SLS per sviluppare il prototipo di un reticolo di ammortizzazione dei sedili.
Le parti traslucide e flessibili sono state stampate in Durable Resin con le stampanti 3D SLA della serie Form, mentre i tubi di collegamento del reticolo sono stati realizzati in Nylon 12 GF Powder utilizzando le stampanti della serie Fuse. Ogni prototipo di reticolo includeva sei parti SLS e tre SLA, ma in totale il team ha assemblato 150 di questi tappetini completi da testare come parte di assemblaggi completi di sedili.
Grazie agli strumenti di prototipazione rapida in-house, Brose ha potuto progettare, testare ed eseguire iterazioni di un componente essenziale del gruppo sedile senza dover ricorrere alla creazione di attrezzature o all'esternalizzazione. "A volte, la combinazione di SLA e SLS è la soluzione ideale, come nel caso del reticolo di ammortizzazione dei sedili. I sovrastampi sono strumenti molto complessi e costosi, perciò abbiamo progettato le parti che dovevano scattare sopra il filo con la SLS e installato le parti SLA allo stato grezzo sul filo, per poi polimerizzarle in questo modo", ha spiegato Schulz.
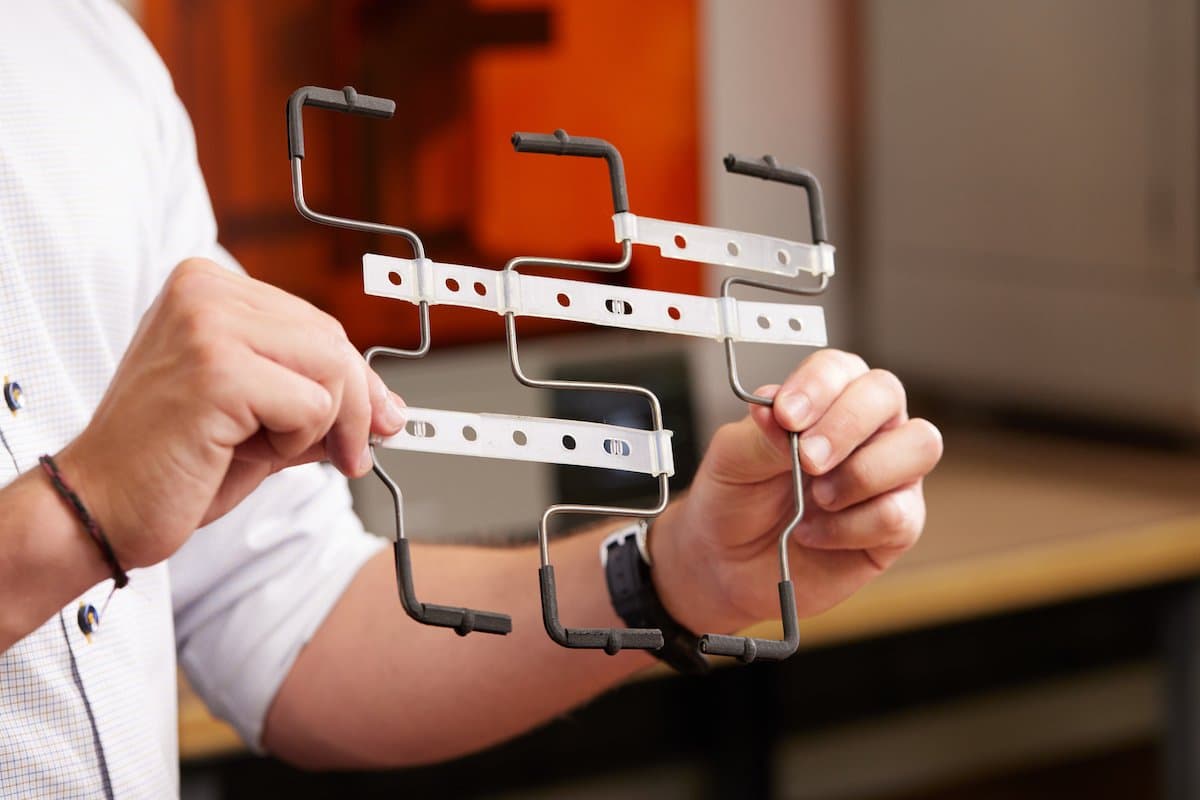
Questo reticolo di ammortizzazione dei sedili include sia parti SLA (in Durable Resin, materiale traslucido) sia parti SLS (in Nylon 12 GF Powder, materiale grigio scuro). Per i test erano necessari 150 assemblaggi completi, che comprendevano 900 parti SLS e 450 parti SLA.
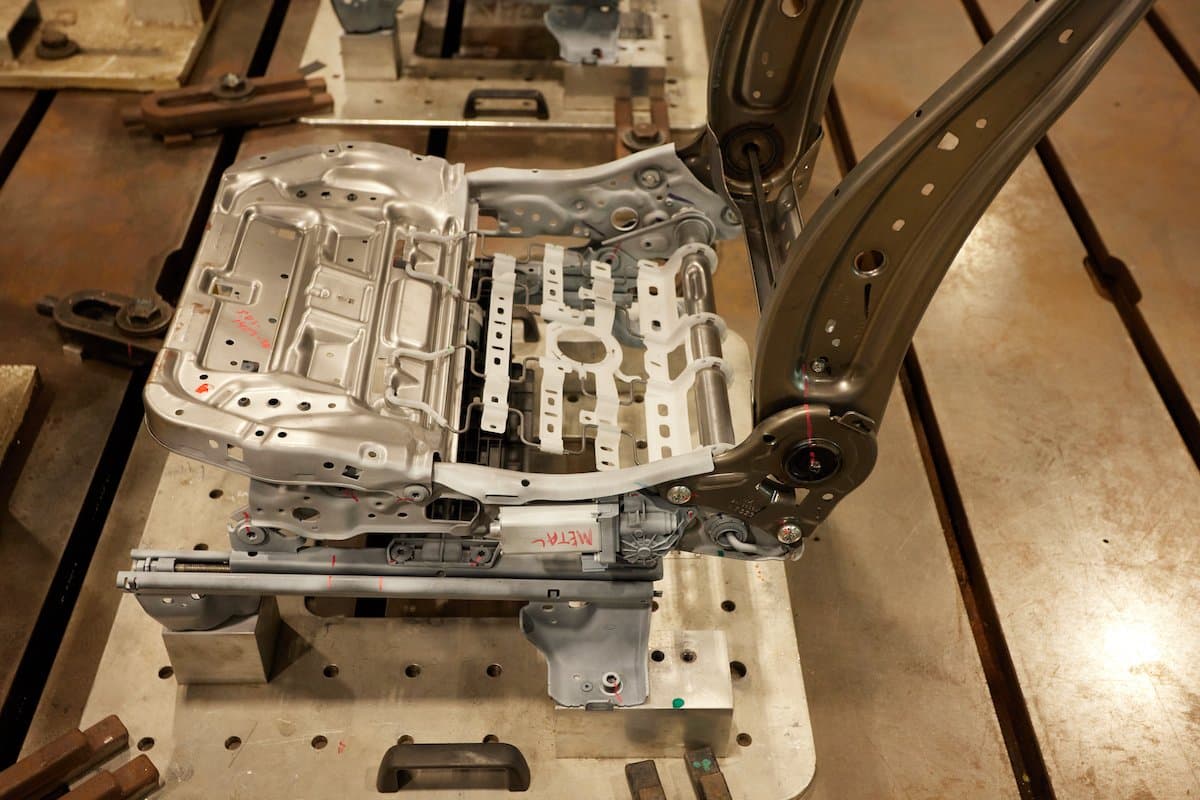
I prototipi e le versioni delle parti per utilizzo finale vengono sottoposti a prove di fatica che simulano anni di utilizzo.
Semplificazione del processo produttivo con i supporti di produzione
La produzione additiva non viene utilizzata solo come strumento di prototipazione: Brose sta integrando la tecnologia in tutti i reparti dell'azienda nell'ambito dell'iniziativa Plant Goes Additive, avviata nel 2022. La produzione di componenti automobilistici è continua e altamente controllata: ogni parte del processo è stata snellita e ottimizzata per garantire efficienza, sicurezza ed eccellenza del prodotto.
Fissaggi per saldatura robotizzata pronti in giornata stampati con la Form 4L
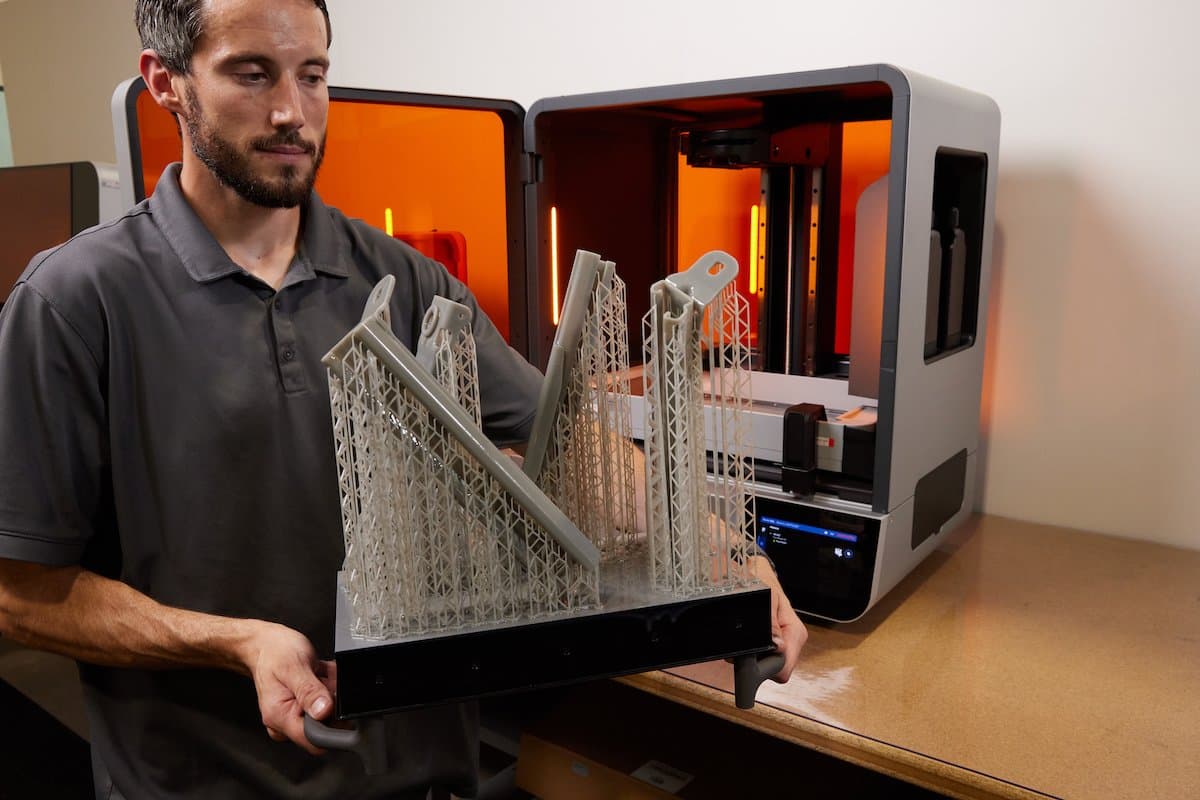
La Form 4L consente di stampare parti di grandi dimensioni in giornata, come questo fissaggio da saldatura realizzato con la Fast Model Resin.
In ogni fase della catena di fornitura del settore automobilistico, le parti in metallo sono componenti fondamentali del prodotto complessivo e la saldatura è un passaggio fondamentale del processo di assemblaggio. Presso Brose North America, dove il team di tecnologia additiva gestisce una flotta di stampanti SLA e SLS, gli apparecchi robotici di saldatura devono adattarsi continuamente a diverse linee di prodotti. In uno stabilimento, le saldatrici rimangono programmate per una sola linea di prodotti, ma nella sede centrale due apparecchi robotici si occupano della saldatura dei prototipi dei sedili di tutte le diverse linee.
Ogni volta che l'apparecchio passa a una nuova linea di prodotti, il reparto di saldatura deve riprogrammarne i parametri. Programmare un apparecchio robotico di saldatura usando binari in metallo comporta un'ingente spesa, inoltre molto spesso questi componenti non sono disponibili nel momento in cui la postazione di saldatura è pronta per istruire l'apparecchio. La stampa 3D rappresenta una soluzione rapida e conveniente al problema, poiché per questo tipo di parti sono necessarie proprio velocità e accuratezza dimensionale.
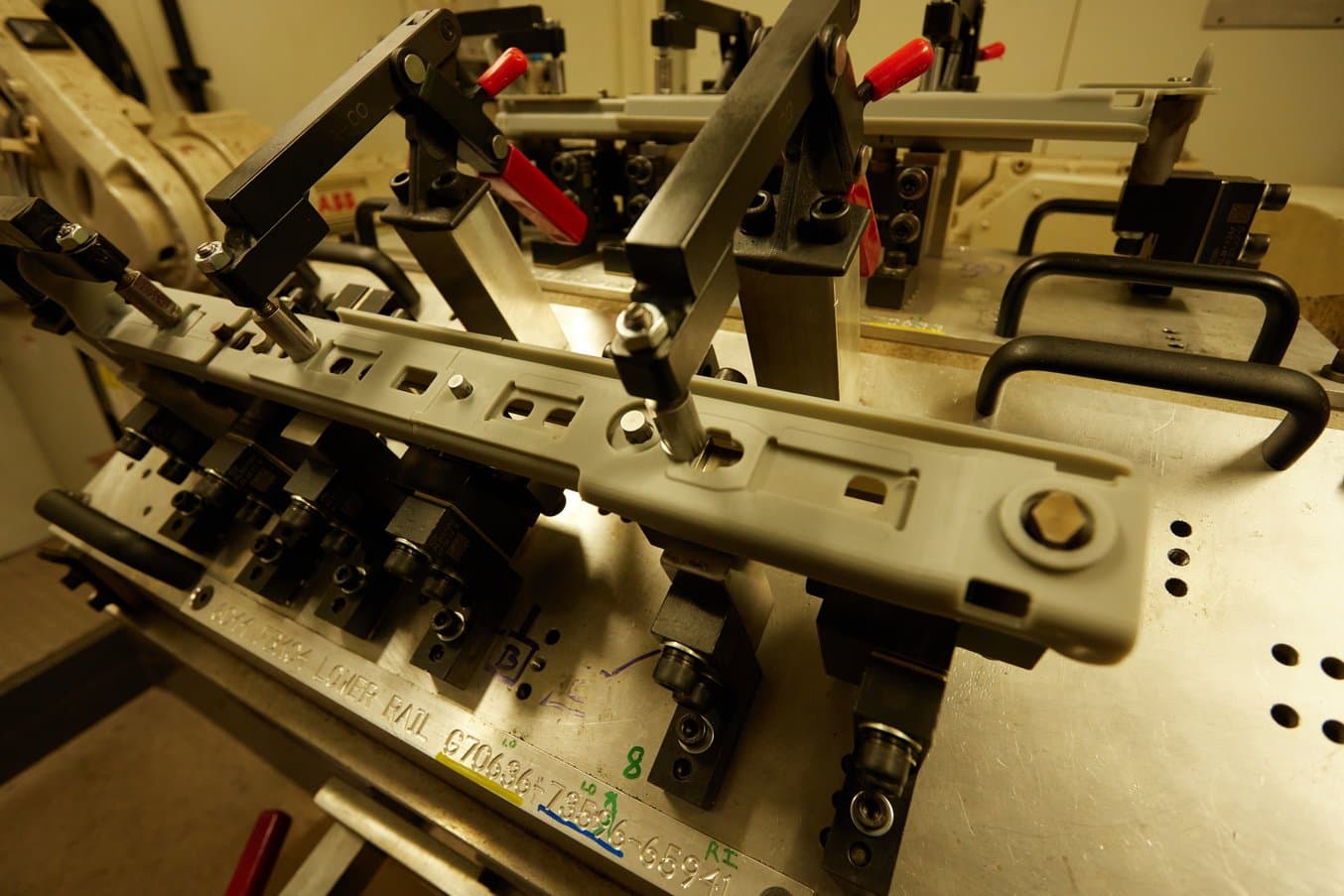
Questa parte di sedile è stata stampata sulla Form 4L in Fast Model Resin, quindi è stata lavata, polimerizzata e assemblata nell'apparecchio robotico di saldatura in meno di tre ore. Queste tempistiche permettono al team di insegnare i movimenti all'apparecchio rapidamente.
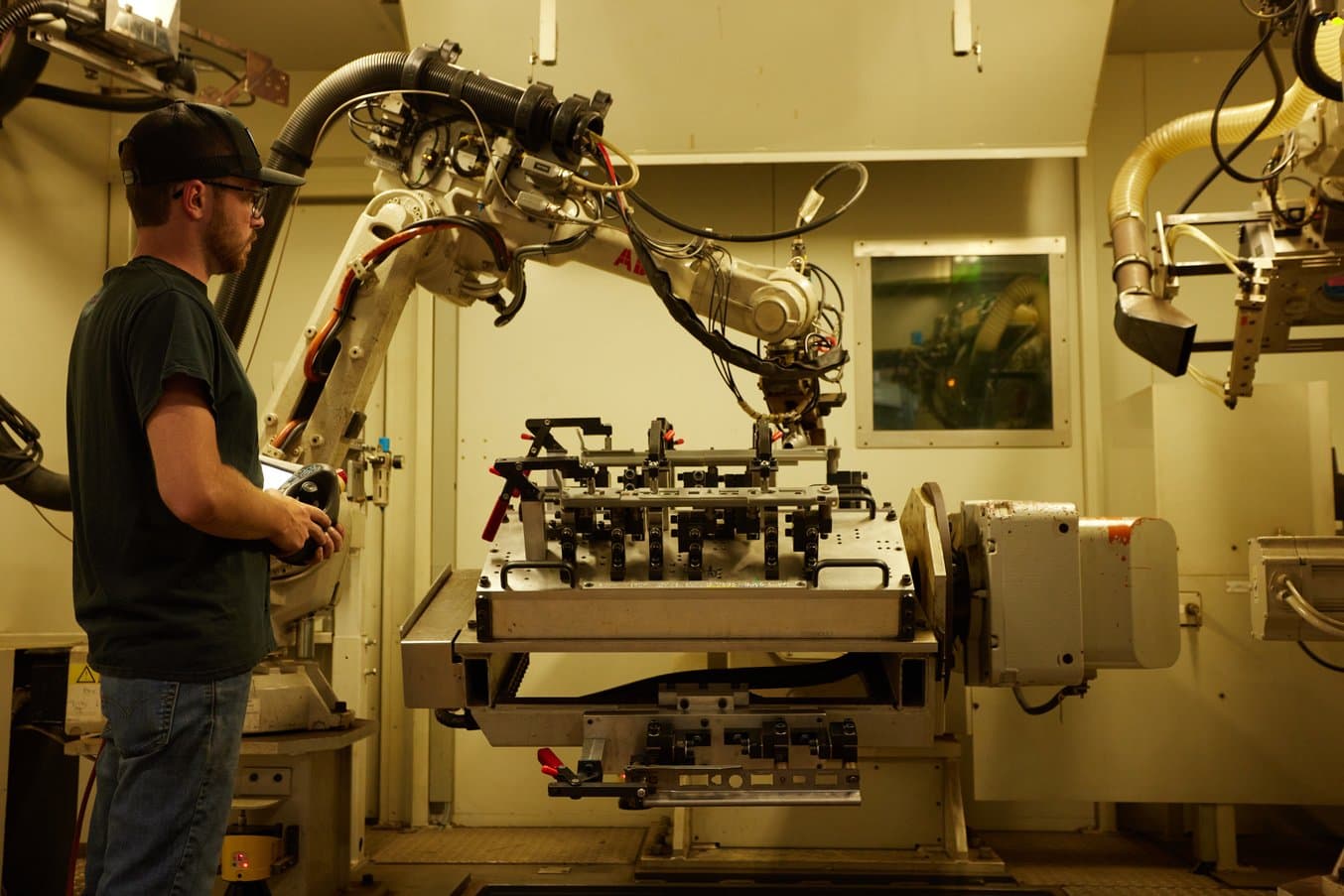
Fissaggi come questo aiutano il team di saldatura a passare da una linea di prodotti all'altra in modo rapido ed efficiente. Questi fissaggi sono estremamente accurati, convenienti e replicabili all'infinito in caso di modifiche o sostituzioni.
Il team di Brose ha da poco ricevuto una stampante 3D a resina di grande formato Form 4L. La configurazione è stata completata in solo 30 minuti, a seguito della quale il personale ha iniziato a stampare parti di grande formato per la configurazione della saldatura usando la Fast Model Resin. Le parti, divise in quattro pezzi, occupavano quasi l'intero volume di stampa. Nonostante le dimensioni, la Form 4L ha completato la stampa in meno di due ore e appena 45 minuti dopo, a seguito di una rapida fase di lavaggio e polimerizzazione post-stampa, il fissaggio era già montato sull'apparecchio robotico.
"La nuova Form 4L di Formlabs ci permette di stampare parti di grande formato rapidamente. Ad esempio, usiamo la Form 4L per creare parti di impostazione per le celle di saldatura nel giro di qualche ora piuttosto che in una notte intera. In questo modo, il team di saldatura di Brose può programmare l'apparecchio robotico prima dell'arrivo dei componenti di stampaggio in metallo. Con la nuova Fast Model Resin, otteniamo il livello di dettagli e la rigidità che ci servono in tempi mai visti prima."
Matthias Schulz, responsabile della prototipazione dei sedili presso Brose North America
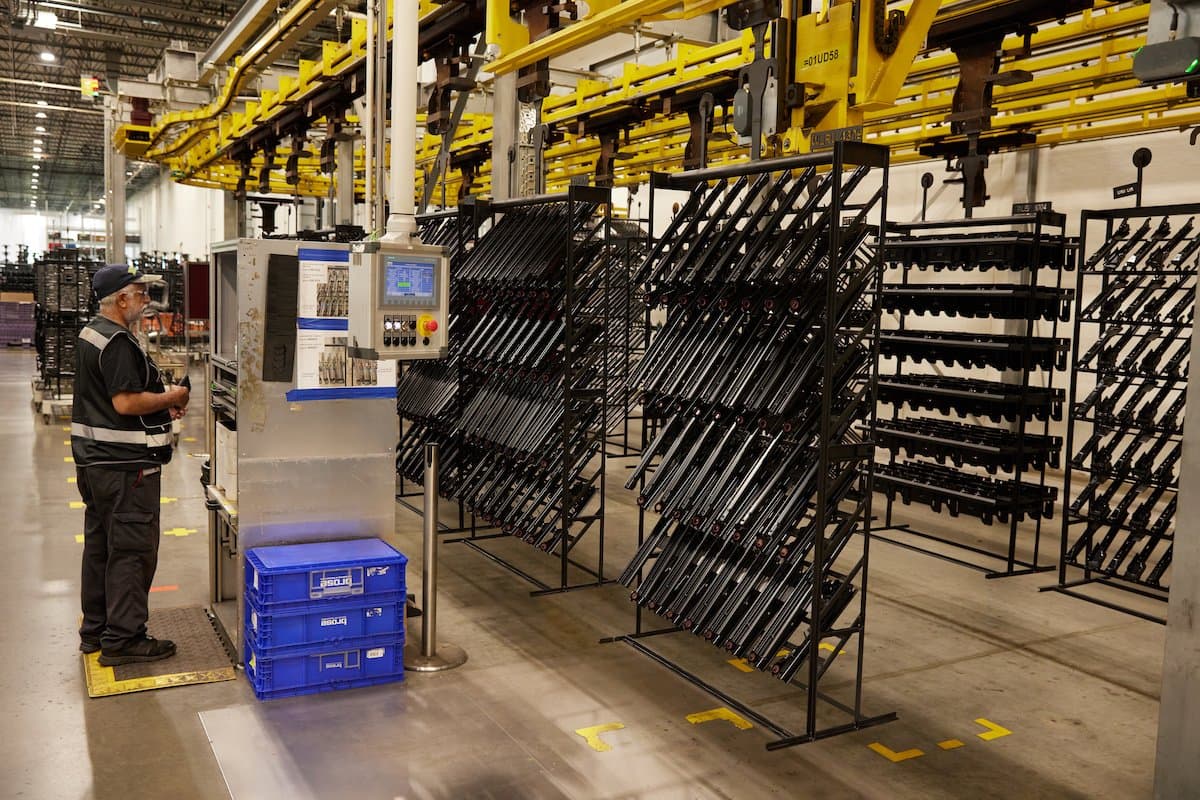
Nello stabilimento Brose New Boston, vengono saldate insieme migliaia di guide per creare la base del gruppo sedile. Il test dei parametri di saldatura è una fase fondamentale nel processo di produzione.
I parametri di saldatura definiti presso la sede centrale di Brose North America utilizzando prototipi e parti di installazione stampate in 3D saranno successivamente utilizzati per la produzione di massa dei telai dei sedili saldati. Le guide dei sedili, visibili nella foto, verranno assemblate nello stabilimento Brose New Boston utilizzando grandi apparecchi robotici di saldatura.
Riduzione dei costi operativi con i connettori di fine linea presso Brose New Boston
Nello stabilimento Brose New Boston, situato a circa trenta minuti dal centro di Detroit, il team utilizza la stampa 3D per realizzare supporti di produzione personalizzati che semplificano il processo di assemblaggio. Le parti stampate in 3D devono essere rigorosamente testate prima di essere integrate nella produzione, ma una volta fatto, contribuiscono a ridurre gli sprechi, migliorare le tempistiche e far funzionare gli apparecchi con regolarità.
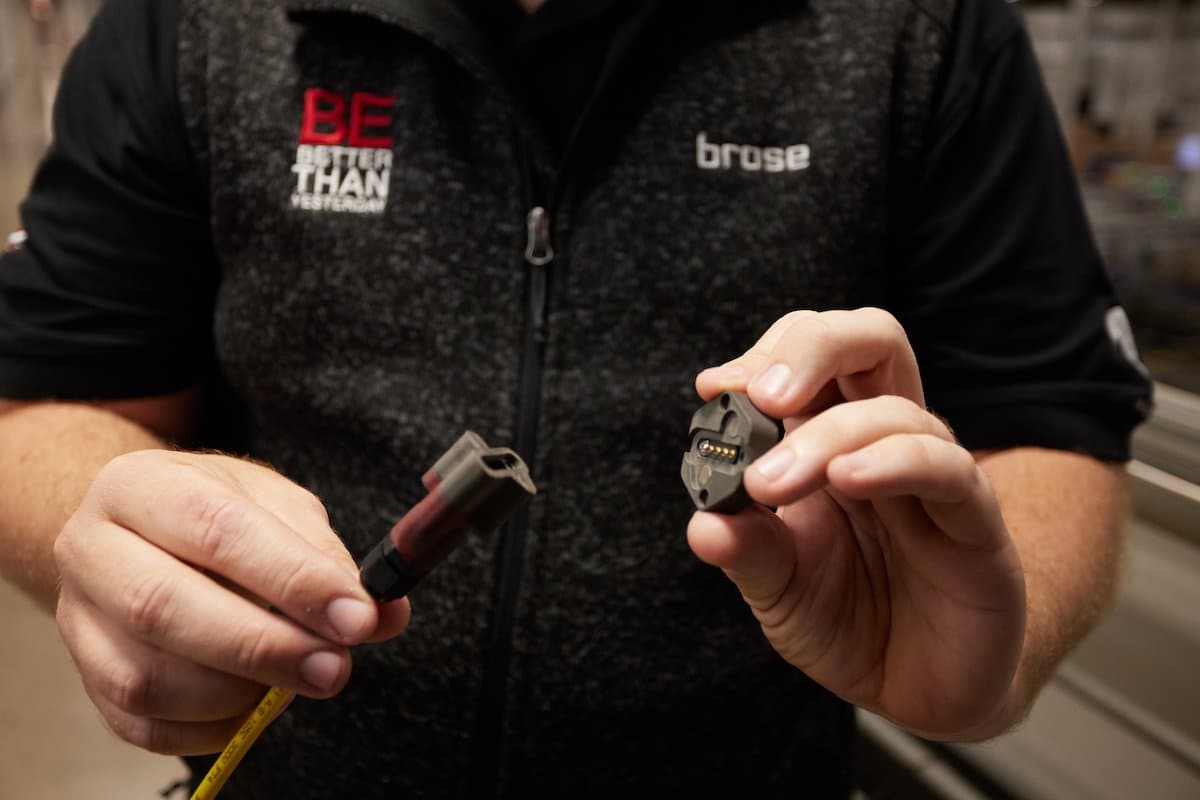
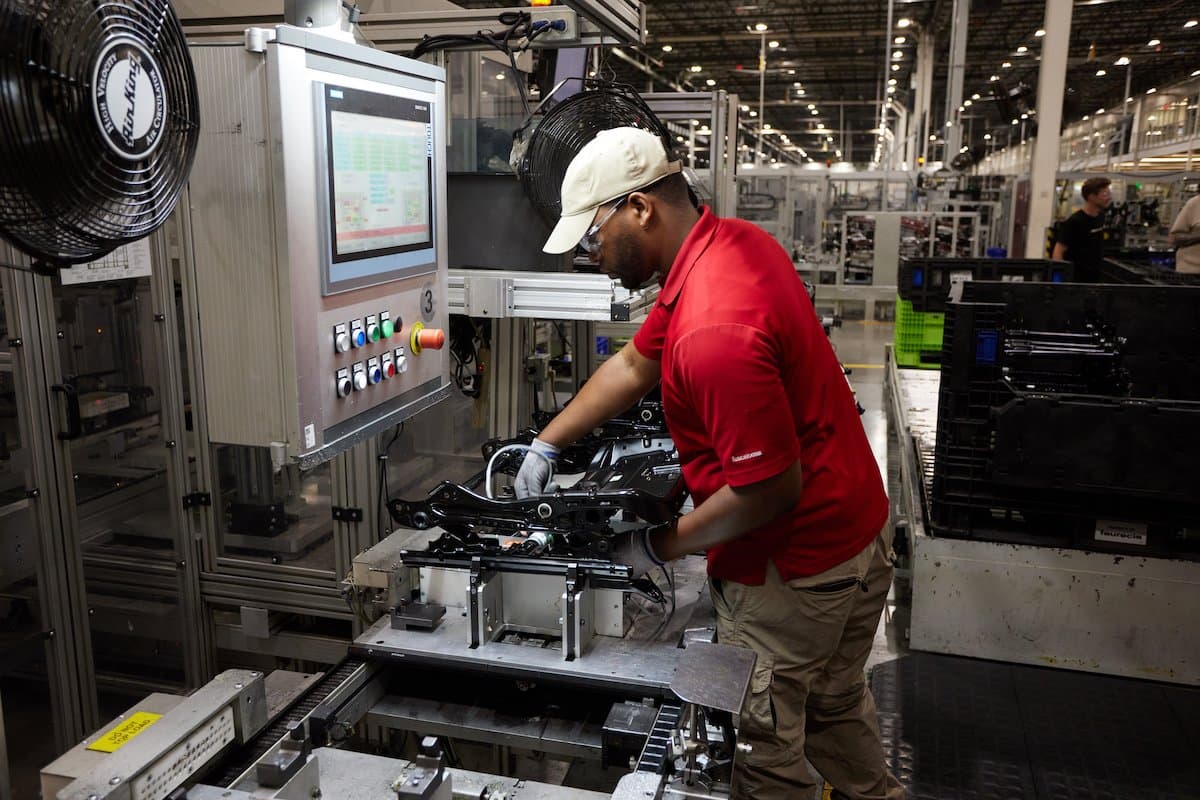
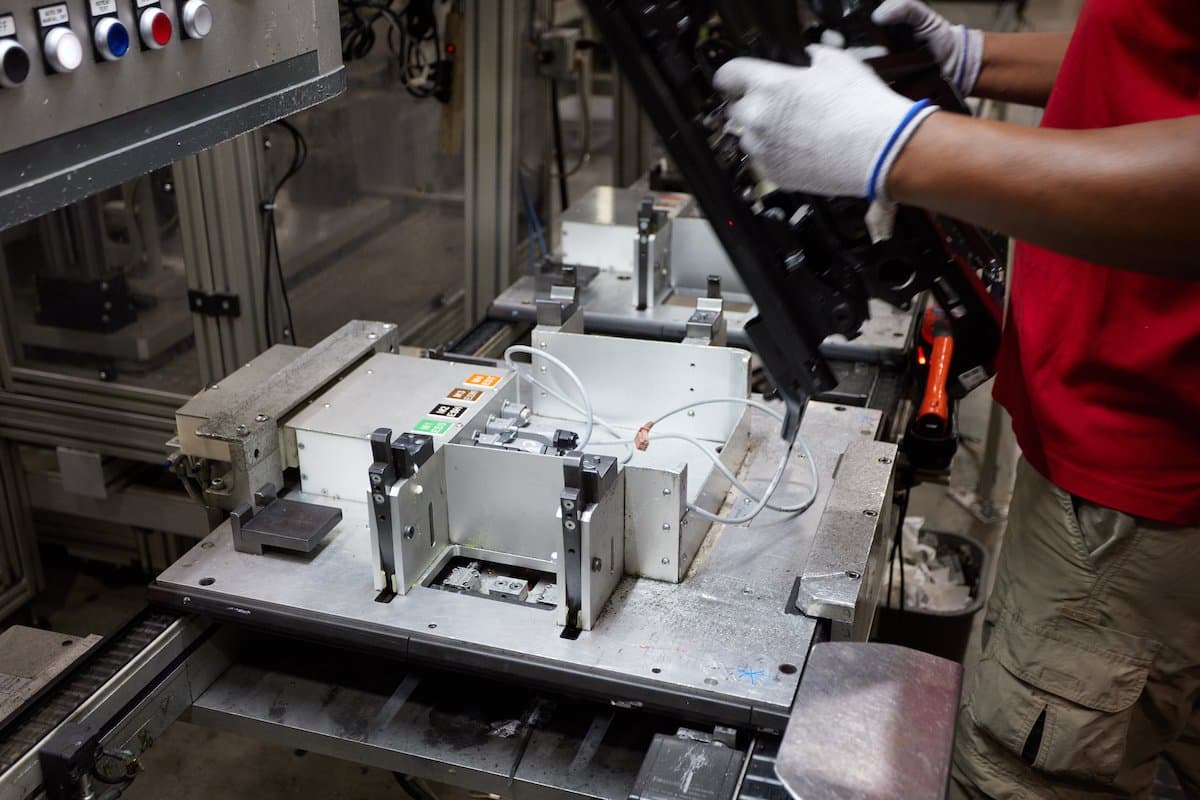

Il connettore di fine linea è stato implementato nella fase finale del processo di assemblaggio del sedile. Dopo aver collegato il telaio del sedile alla presa elettrica e aver eseguito il controllo finale, il personale tecnico rimuove il sedile per passare alla fase successiva del processo. Molte volte capitava di dimenticare il collegamento elettrico e, nel rimuovere il sedile, di rompere il cavo, causando un danno di qualche centinaio di dollari alla linea di assemblaggio e interrompendo la produzione.
Il team di tecnologia additiva ha collaborato con il team di Brose New Boston per progettare una linea di connettori magnetici che si attacca facilmente alla linea e al telaio del sedile, ma si sgancia altrettanto facilmente se il personale tecnico rimuove il telaio del sedile senza scollegare manualmente il cavo. "Utilizziamo i supporti di produzione stampati in 3D per ridurre l'usura dei macchinari. Ci permettono di effettuare riparazioni più rapide sulla linea di produzione. Questo si traduce in una riduzione dei tempi di inattività e ci aiuta ad aumentare la produttività complessiva", ha affermato Schulz.
Produzione in serie di unità provvisorie per parti per utilizzo finale per il settore automobilistico
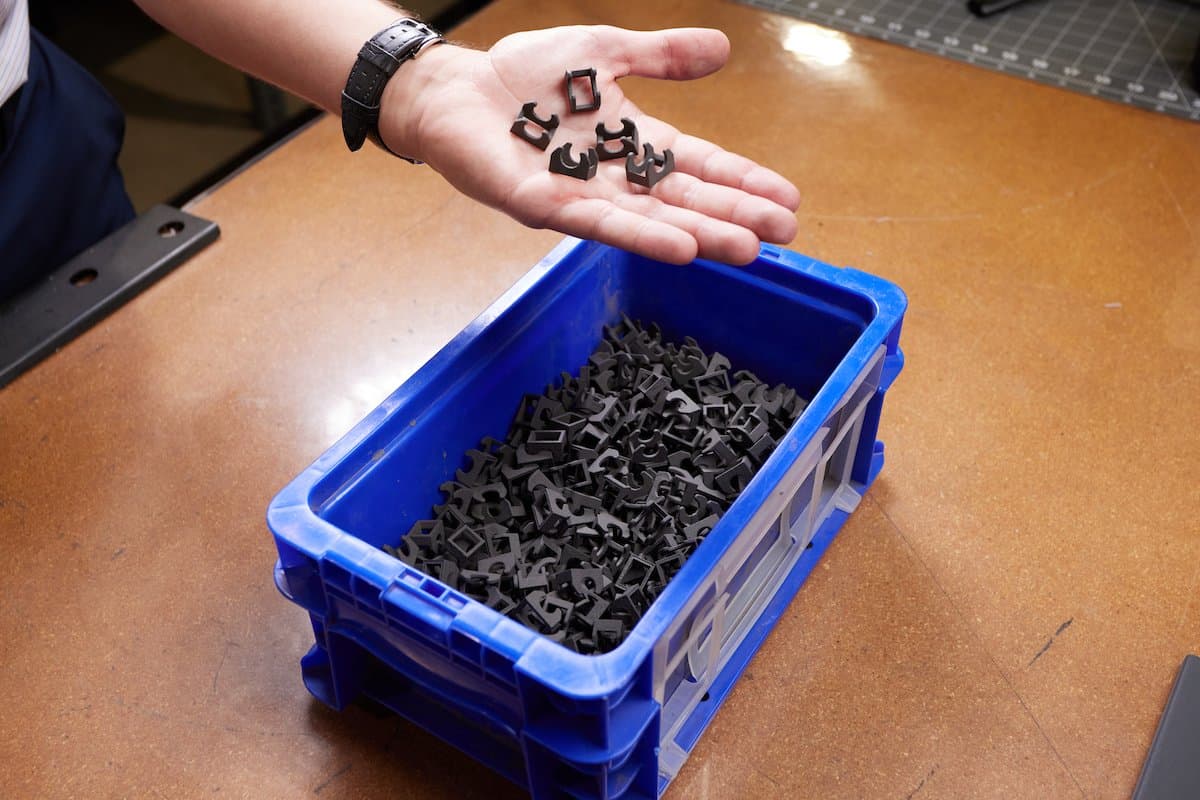
Brose stamperà in 3D 250 000 di queste clip per i sedili della BMW X7.
Secondo Schulz, il settore automobilistico ha subito un rapido cambiamento, soprattutto negli ultimi cinque anni. La crescita dei veicoli elettrici, l'aumento della domanda di caratteristiche personalizzate e le preoccupazioni legate alla catena di fornitura hanno spinto le aziende produttrici di componenti a investire maggiormente nella produzione additiva come alternativa affidabile per la produzione.
"Abbiamo sempre più clienti che richiedono la tecnologia additiva. Questa tecnologia è fondamentale anche per rispondere alle esigenze dell'utente finale, che desidera una maggiore personalizzazione dei veicoli. Di conseguenza, la tecnologia additiva è sempre più richiesta dalle aziende produttrici di componenti", ha sostenuto Schulz.
La stampa 3D di parti per utilizzo finale, soprattutto nel settore automobilistico, che ha requisiti normativi stringenti, non è sempre stata possibile. Tuttavia, il team di produzione additiva di Brose si è assicurato di adottare questa tecnologia solo quando la qualità dell'hardware e dei materiali ha permesso di realizzare parti ad alte prestazioni in modo affidabile.
"Abbiamo scelto di utilizzare gli apparecchi di Formlabs perché la disponibilità dei materiali e l'uniformità delle stampe sono migliorate così tanto da rendere la tecnologia pronta per il settore automobilistico. Tuttavia, abbiamo problemi legati a sicurezza e resistenza, soprattutto con le aziende produttrici di componenti, che stiamo provando a risolvere. In collaborazione con Formlabs, abbiamo dimostrato di poter implementare parti simili a quelle dell'attuale BMW X7."
Matthias Schulz, responsabile della prototipazione dei sedili presso Brose North America
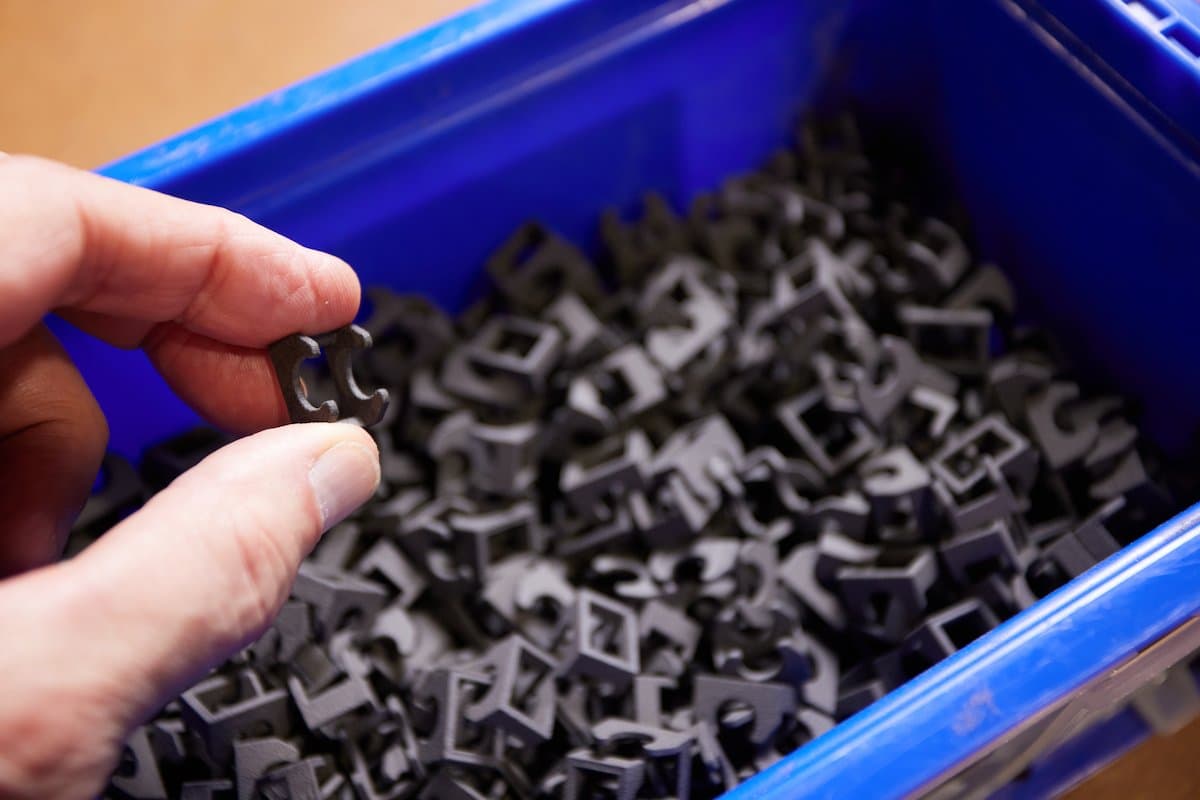
Applicazione: componenti per sedili della BMW X7
Workflow: scansione 3D, iterazione e stampa 3D sulle stampanti 3D SLS della serie Fuse per la produzione di parti per utilizzo finale.
Volume: 250 000
Dettagli della stampa:
- Stampante: Fuse 1 e Fuse 1+ 30W
- Materiale: Nylon 12 GF Powder
- Volume di stampa: 1.440 unità per camera di stampa
- Parti al mese: 16 000
Perché la stampa 3D?
- Stampa di unità provvisorie per consentire un periodo di transizione necessario per la disponibilità delle attrezzature
Brose utilizza la stampa 3D per la produzione di parti per utilizzo finale come un'alternativa rapida ed economica ai metodi tradizionali. Quando un'azienda produttrice di componenti richiede una parte o la modifica di una parte esistente, per la quale non è possibile realizzare le attrezzature o che non può essere prodotta in massa velocemente, il team di tecnologia additiva di Brose valuta l'idoneità alla stampa 3D. Una fase importante di questo processo consiste nell'ingegneria inversa e nella scansione dei componenti esistenti.
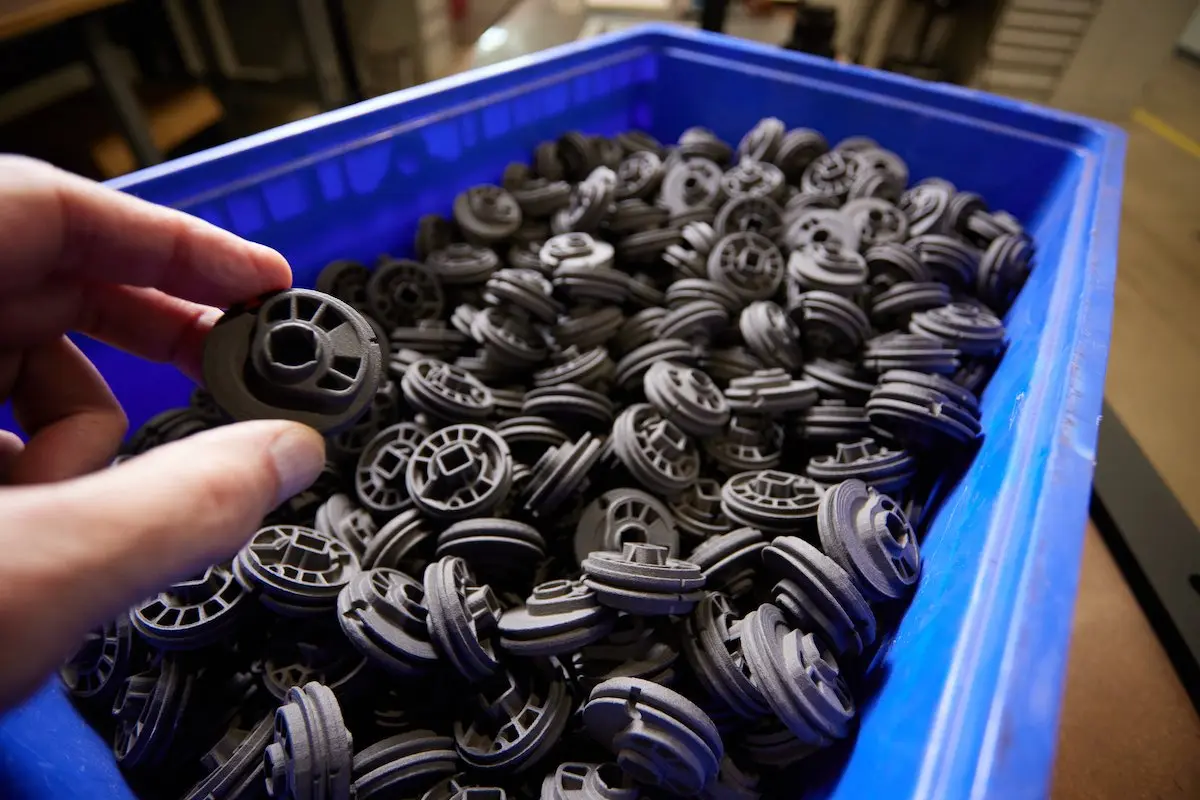
Applicazione: componente di un cavo Bodwen
Workflow: scansione 3D, iterazione e stampa 3D sulle stampanti 3D SLS della serie Fuse per la produzione di parti per utilizzo finale.
Volume: 20 000
Dettagli della stampa:
- Stampante: Fuse 1 e Fuse 1+ 30W
- Materiale: Nylon 12 GF Powder
- Rendimento: 144 parti per ciascuna camera di stampa, 1000 parti a settimana
Perché la stampa 3D?
- Stampa di unità provvisorie per consentire un periodo di transizione necessario per la disponibilità delle attrezzature
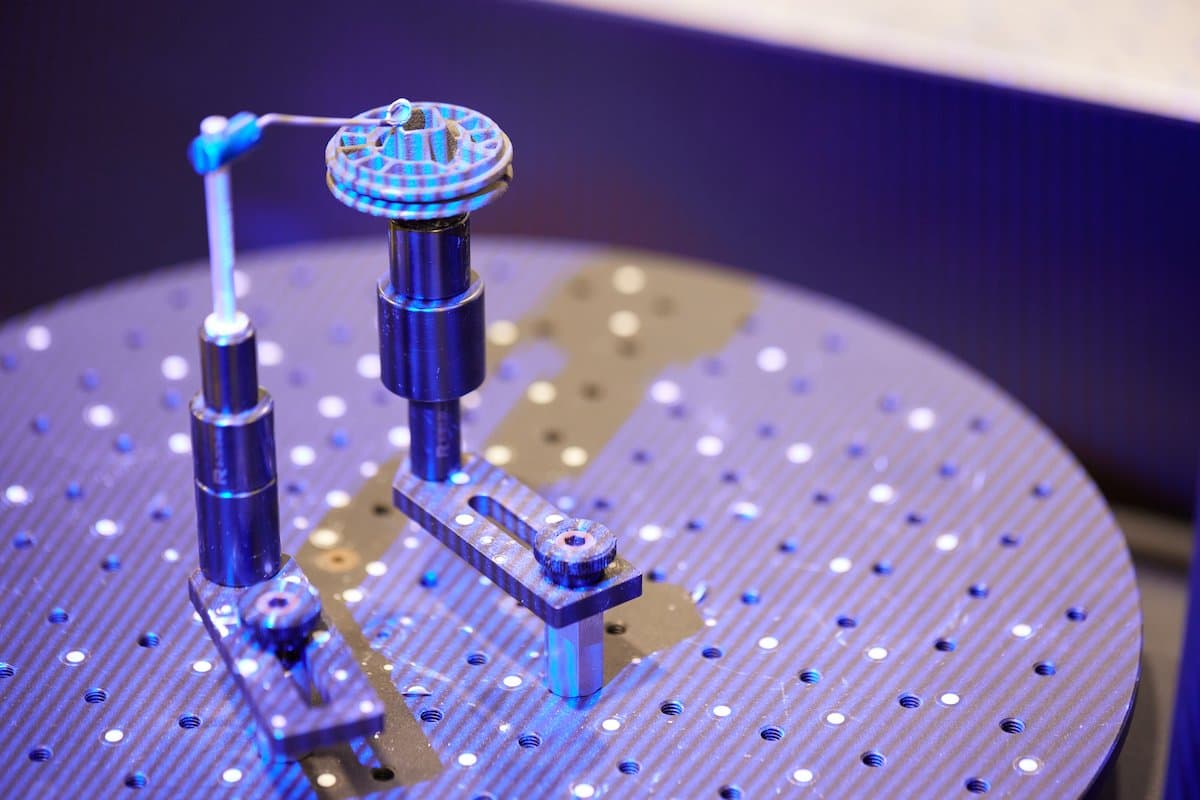
Brose spesso scansiona componenti già esistenti o iterazioni precedenti, in modo da poter apportare modifiche nel software CAD e stampare in 3D la versione aggiornata nella stessa giornata.
La parte in questione è il componente di un cavo Bodwen; 20 000 unità saranno prodotte con la flotta di stampanti 3D SLS della serie Fuse di Brose e saranno inserite nel gruppo sedile finale per un'importante e rinomata azienda produttrice di componenti.
"Brose ha deciso di portare in-house la SLS con Formlabs perché la tecnologia SLS ci consente di stampare in 3D in modo rapido e veloce, con minori requisiti di post-elaborazione rispetto alla SLA. Riusciamo a stampare volumi molto elevati, condizione necessaria per supportare la stampa di unità provvisorie o altre parti per utilizzo finale per le aziende produttrici di componenti", ha affermato Schulz.
Con tre stampanti 3D SLS della serie Fuse che funzionano ininterrottamente per produrre prototipi, supporti di produzione e centinaia di migliaia di componenti per utilizzo finale, affidabilità e coerenza sono fondamentali. Il team utilizza la Nylon 12 GF Powder per la sua accuratezza dimensionale e per la sua somiglianza con il nylon stampato a iniezione, anche nel caso di volumi di produzione elevati. Al termine di ogni ciclo di stampa, viene effettuata una rapida manutenzione della Fuse 1 o della Fuse 1+ 30W, un'operazione che richiede solo circa quindici minuti, garantendo una produzione continua ed efficiente.
"Formlabs sa come progettare una stampante di facile manutenzione. Gli apparecchi sono estremamente affidabili e gli errori di stampa sono rari, permettendoci di stampare volumi più elevati di parti con la sicurezza di poter passare alla produzione", ha affermato Schulz.
Produzione accelerata nel settore automobilistico con le stampanti 3D
L'impegno di Brose verso il miglioramento continuo ha spinto l'azienda a investire in nuove tecnologie, come la produzione additiva e l'automazione, con l'obiettivo di semplificare i processi e offrire soluzioni innovative alla clientela. La stampa 3D sta assumendo un ruolo sempre più rilevante all'interno dell'azienda e i leader come Schulz si impegnano a trovare nuovi modi per sfruttarne i tempi di produzione rapidi e i costi spesso inferiori.
Grazie a strumenti veloci e potenti come la Form 4, la Form 4L e le stampanti della serie Fuse, è possibile realizzare prototipi, supporti di produzione e componenti per utilizzo finale in poche ore o giorni, anziché in settimane o mesi. "Formlabs è il partner ideale per noi. Avevamo bisogno di una soluzione pronta all'uso che ci consentisse di produrre volumi più elevati di parti con minore supporto ingegneristico. Il software, l'assistenza e le stampanti di Formlabs rappresentano sono perfetti per questo."
Per scoprire di più sulla stampa 3D nel settore automobilistico, visita il nostro sito web. Richiedi un campione per toccare con mano la qualità delle stampe 3D SLA o SLS.