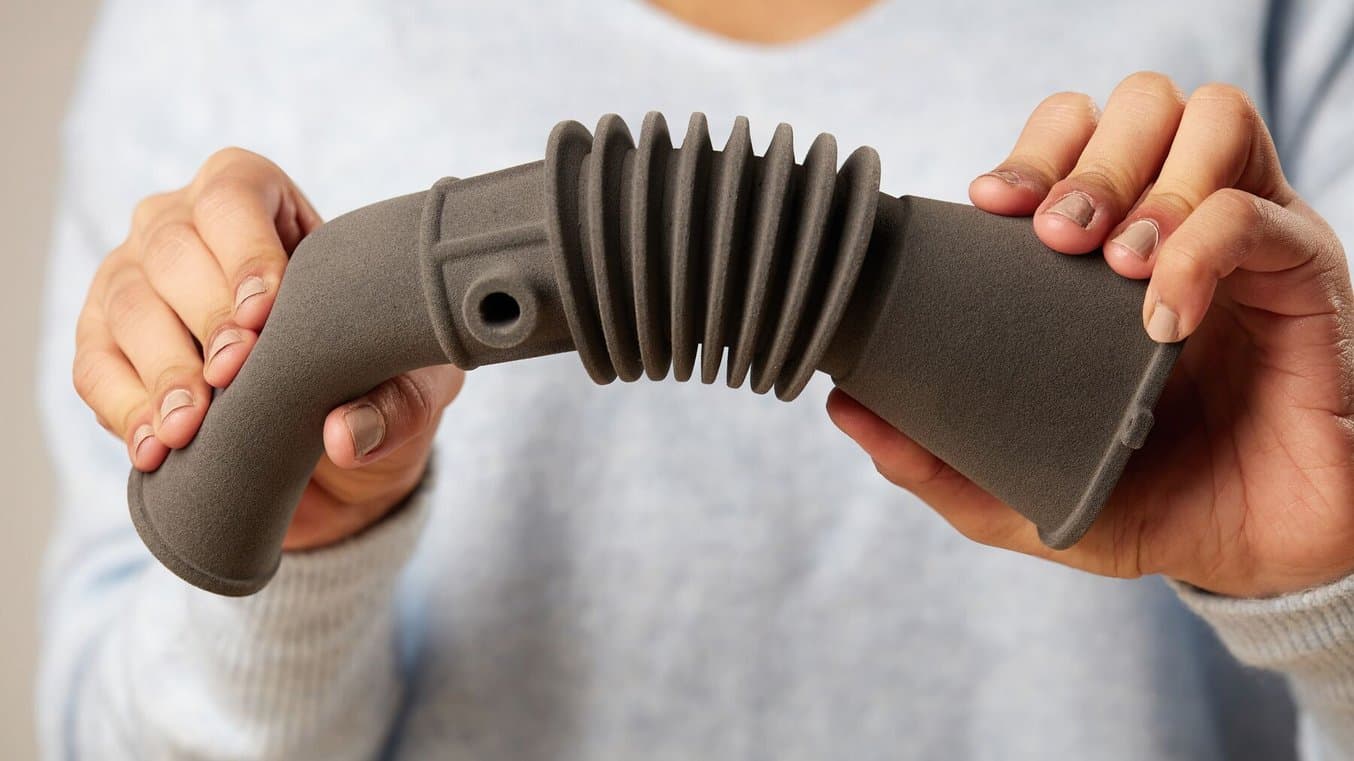
Che cos'è il poliuretano termoplastico?
Il poliuretano termoplastico (TPU) è un tipo di elastomero termoplastico (TPE) molto utilizzato nei settori automobilistico, dei trasporti, aerospaziale, degli articoli sportivi e dei dispositivi medici. Il TPU combina l'elevata resistenza delle parti in plastica con l'elasticità di quelle in gomma, per cui è perfetto per le applicazioni in cui una parte deve essere ripetutamente piegata o compressa.
Data la sua elasticità, il TPU viene spesso utilizzato come modificatore d'impatto per prodotti come caschi, imballaggi protettivi, prodotti antivibrazione e guarnizioni o sigillanti. Ha inoltre un'eccellente resistenza all'abrasione e viene utilizzato in ambienti ad alta frizione, come gli interni delle automobili, o per cavi elettrici e isolanti. Per le applicazioni in questi settori in cui è frequente la presenza di olio, si può ricorrere al TPU anche per la sua resistenza alle macchie di olio.
Come vengono realizzate le parti in TPU?
I prodotti in TPU sono molto diffusi nella vita di tutti i giorni e la loro popolarità li rende ideali per la produzione di massa, in genere attraverso i tradizionali processi di stampaggio a iniezione. Molti prodotti che crediamo siano in gomma sono in realtà realizzati in TPU.
Lostampaggio a iniezione è un metodo conveniente per produrre grandi quantità di parti, ma ha dei limiti in termini di flessibilità geometrica o personalizzazione. Le parti stampate a iniezione sono standardizzate per poter essere prodotte nell'ordine di centinaia di migliaia o di milioni di unità, per cui in settori come la produzione di dispositivi medici o di articoli sportivi è necessario trovare alternative che si prestino meglio alla produzione con volumi ridotti o alla personalizzazione.
Inoltre, la produzione di massa impedisce a piccole imprese e startup di immettere rapidamente i loro prodotti sul mercato, perché si affidano ad aziende esterne per lo stampaggio a iniezione industriale.
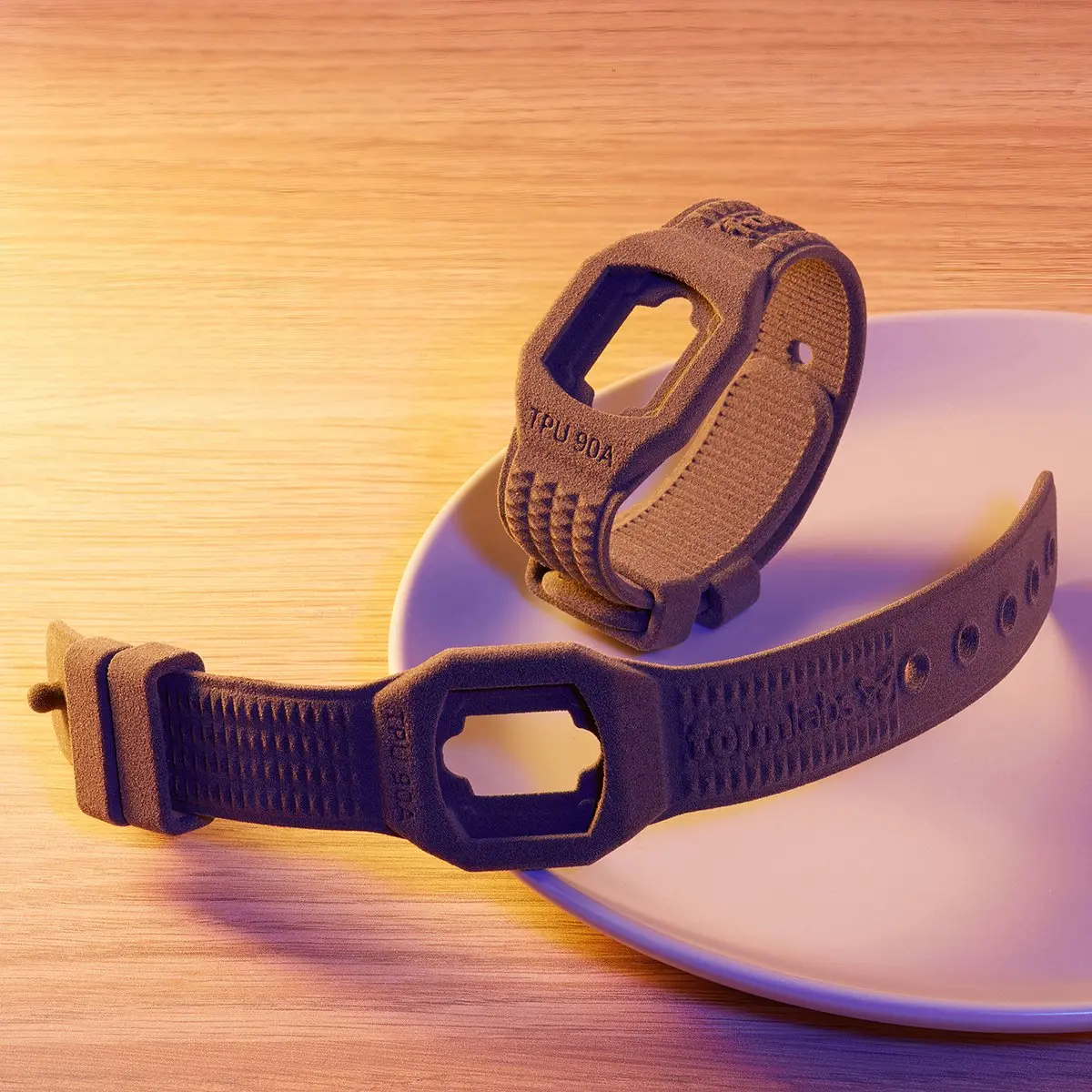
Presentazione della TPU 90A Powder per parti SLS flessibili, tenaci e sicure per il contatto con la pelle
Guarda il nostro webinar per scoprire come la TPU 90A Powder può aiutarti a produrre in-house parti morbide in gomma con le stampanti 3D della serie Fuse.
Perché stampare in 3D con il TPU?
La stampa 3D con TPU e TPE offre opportunità al di fuori dei workflow tradizionali per ottenere parti con una maggiore complessità geometrica, design personalizzati, iterazione e progettazione più rapide e produzione di volumi ridotti a costi più contenuti.
Esistono diverse opzioni per la stampa 3D con TPU, tra cui le tecnologie di modellazione a deposizione fusa (FDM) e di sinterizzazione laser selettiva (SLS). Con l'avanzare della tecnologia e dei materiali per la stampa 3D, è cresciuto esponenzialmente il numero di produttori che hanno integrato questo workflow nel loro processo.
La stampa 3D con TPU accorcia il ciclo iterativo per le applicazioni della prototipazione rapida e offre possibilità di personalizzazione per la produzione di parti per utilizzo finale. Nei settori in cui una fase del processo di sviluppo del prodotto viene solitamente esternalizzata (in genere, la fase di produzione di massa), la stampa 3D può favorire un workflow completo migliorato e integrato verticalmente.
La stampa 3D con TPU può anche aiutare a soddisfare la domanda di prodotti personalizzati. Secondo uno studio di Deloitte, per alcune categorie, oltre il 50% dei clienti ha manifestato l'interesse di acquistare prodotti o servizi personalizzati e la maggioranza ha dichiarato la propria disponibilità a pagare di più per un prodotto o servizio personalizzato. Nelle applicazioni in cui vengono comunemente utilizzati TPU e gomma, come i dispositivi di protezione tipo caschi o solette e plantari, le parti in TPU stampate in 3D sono perfette per la personalizzazione di massa di imbottiture per caschi, plantari, attrezzature sportive, occhiali, cuffie o componenti per l'impugnatura ergonomica di prodotti tecnologici.
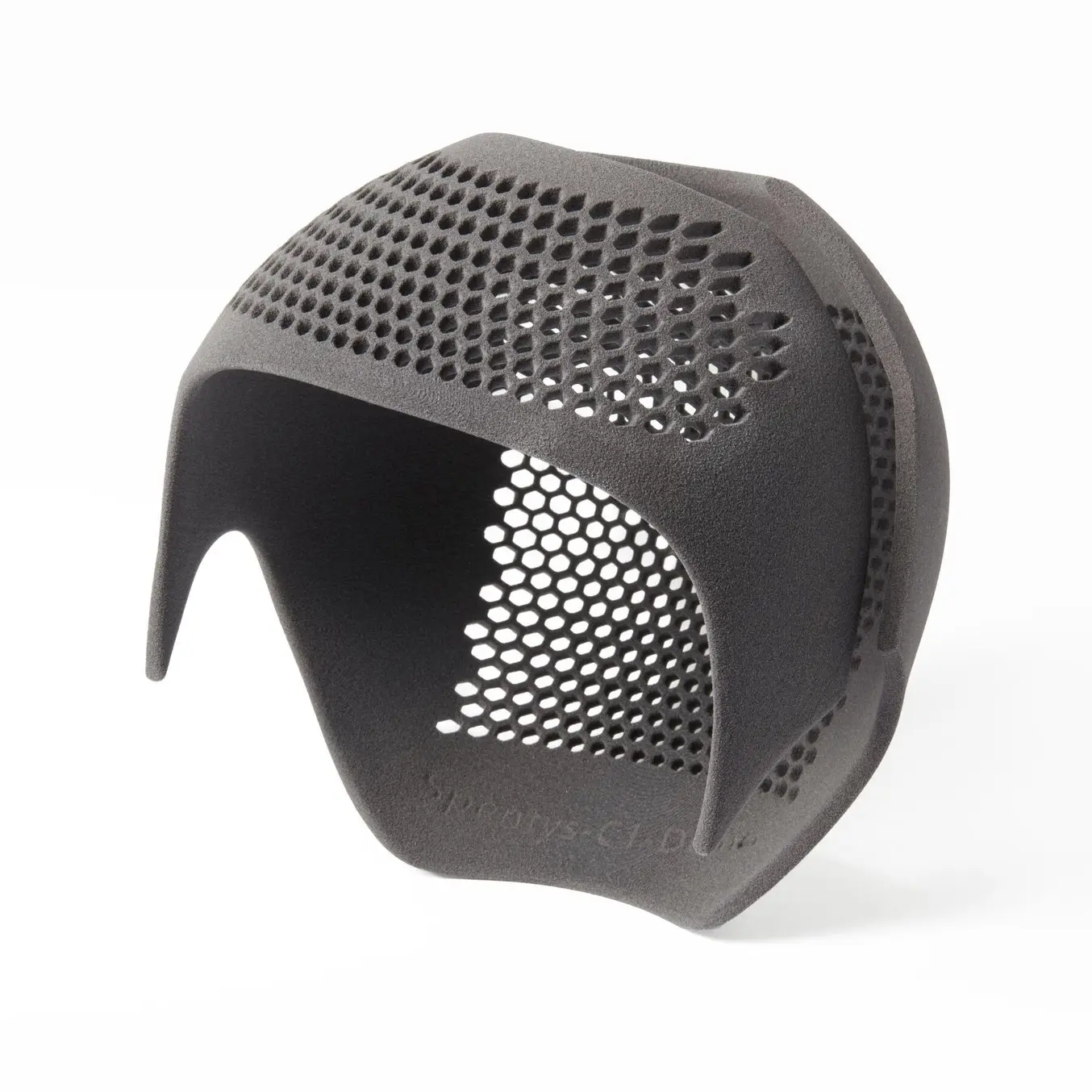
La TPU 90A Powder di Formlabs rende possibile la personalizzazione sulla base di dati antropometrici, per applicazioni come questo casco protettivo personalizzato.
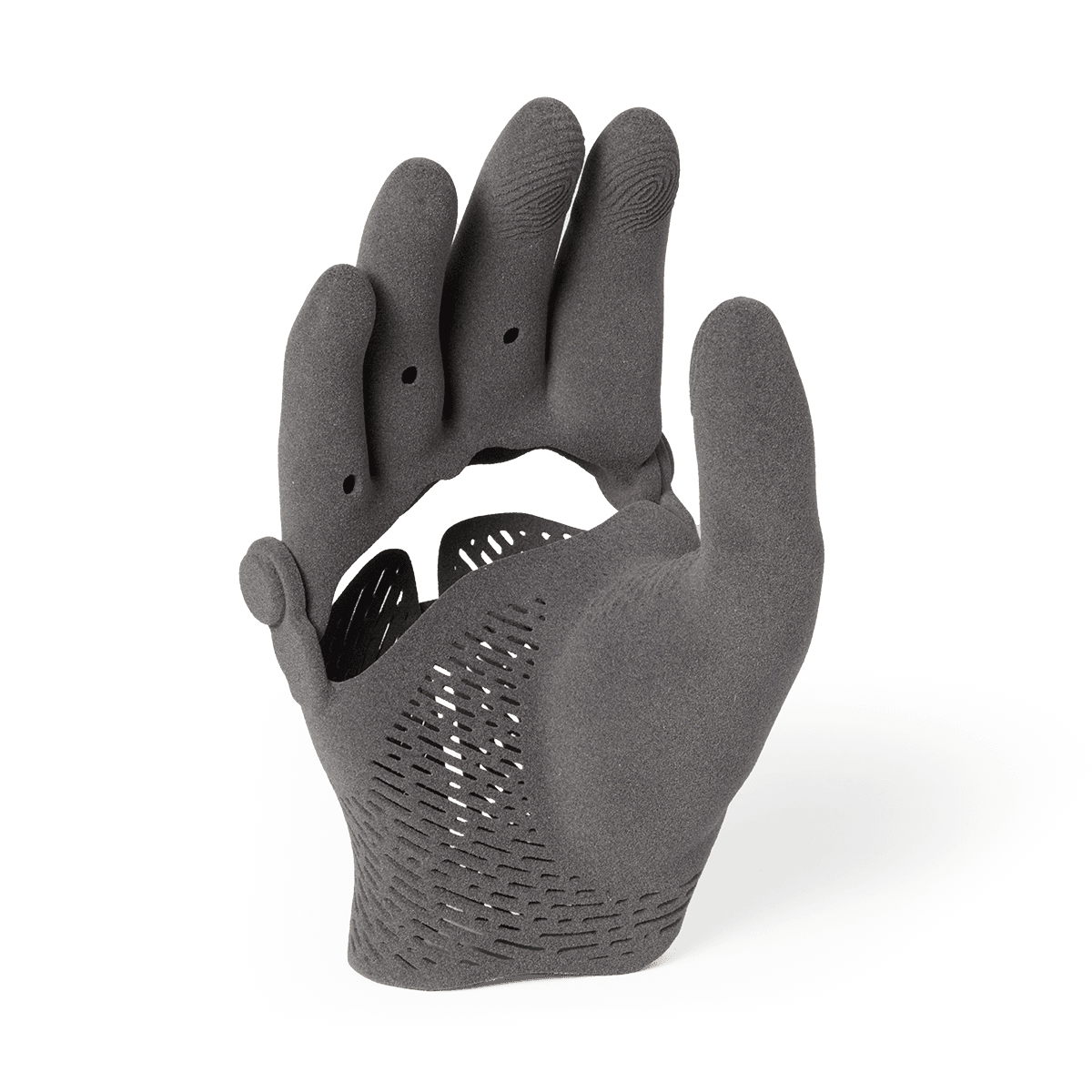
Questa copertura per protesi di mano stampata in TPU 90A Powder è flessibile, robusta e resistente.
Come stampare in 3D con il TPU
Per stampare con il TPU è possibile utilizzare le stampanti 3D SLS o FDM. Entrambe le tecnologie offrono vantaggi specifici. Prima di sceglierne una, è importante determinare quale sia la migliore per il proprio workflow e le proprie esigenze aziendali.
Stampa 3D FDM con TPU | Stampa 3D SLS con TPU | |
---|---|---|
Resistenza del materiale funzionale | ★★☆☆☆ | ★★★★★ |
Risoluzione | ★★☆☆☆ | ★★★★☆ |
Accuratezza | ★★★★☆ | ★★★★★ |
Finitura superficiale | ★★☆☆☆ | ★★★★☆ |
Rendimento | ★★☆☆☆ | ★★★★★ |
Design complessi | ★★☆☆☆ | ★★★★★ |
Facilità di utilizzo | ★★★★★ | ★★★★☆ |
Vantaggi | Apparecchi e materiali a basso costo per consumatori Semplice e veloce per parti piccole e facili | Parti funzionali, resistenti e isotropiche Rendimento di scala industriale Design autoportante Libertà di design eccellente |
Svantaggi | Le parti sono anisotropiche ma non impermeabili o funzionalmente resistenti Libertà di design limitata | Finitura superficiale leggermente ruvida |
Applicazioni | Prototipazione rapida a costo ridotto Modelli Proof-of-Concept semplici | Prototipazione funzionale Produzione con volumi ridotti di parti per utilizzo finale: guarnizioni per il settore automobilistico, sigillanti, collettori, beni di consumo, scarpe, protesi e plantari |
Stampa 3D con TPU con la tecnologia FDM
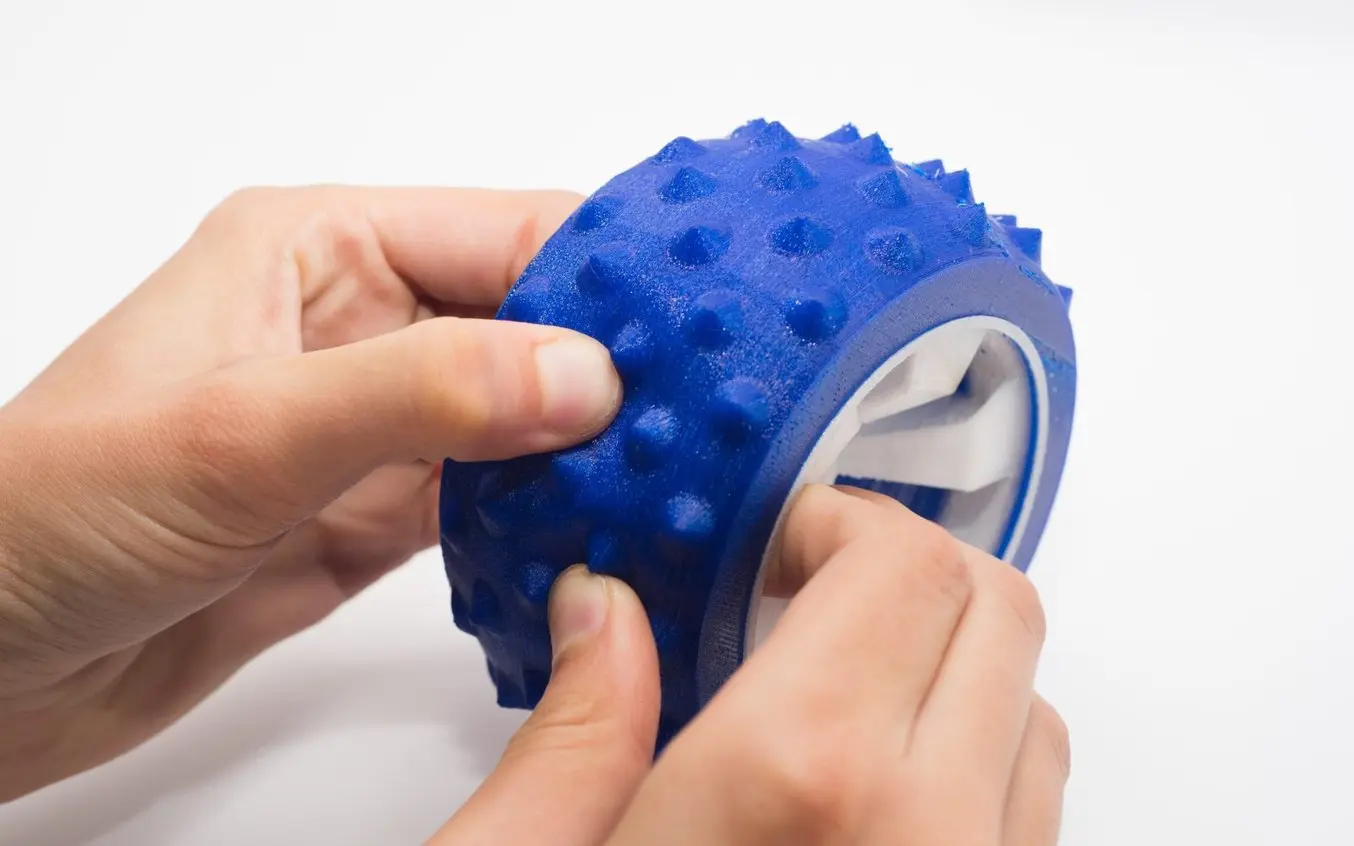
La stampa 3D con TPU su stampanti FDM è una buona opzione di base, ma il materiale è difficile da stampare in 3D e comporta dei limiti a livello di design. (Fonte dell'immagine: Hubs)
Le aziende che vogliono iniziare a stampare in 3D con il TPU possono ricorrere a una stampante FDM a basso costo, che è una buona soluzione per un workflow di base. Il filamento in TPU per la stampa FDM ha un costo contenuto e può essere un buon modo per mettere alla prova concetti di design e prototipi estetici, soprattutto se l'obiettivo finale è la produzione di massa con i metodi tradizionali di stampaggio a iniezione.
Tuttavia, il TPU può essere un materiale difficile da stampare in 3D con le stampanti FDM: il filamento morbido ed elastico può facilmente intasare l'estrusore, provocando problemi tecnici e un basso tasso di riuscita delle stampe. Inoltre, la stampa 3D con TPU su stampanti FDM limita la libertà di design, produce parti meno precise dal punto di vista dimensionale e crea linee degli strati visibili.
Le parti in TPU realizzate con la stampa FDM sono anisotropiche, il che significa che la loro resistenza non è uniforme sui diversi assi o piani di sollecitazione. In altre parole, l'applicazione di una forza a una parte in TPU realizzata con la stampa FDM in una direzione avrà un effetto diverso rispetto all'applicazione della stessa forza da un'altra direzione. Poiché le parti in TPU spesso vengono tirate, allungate, compresse e ruotate, l'anisotropia rappresenta una vera e propria sfida nei casi in cui devono essere funzionali, anche in fase di prototipazione.
Filamenti in TPU per le stampanti FDM
Molti produttori di materiali e stampanti FDM offrono filamenti in TPU con proprietà diverse. In genere i filamenti in TPU per la stampa FDM sono materiali un po' più duri, con una durezza Shore di circa 95A, ma è possibile compensare questa caratteristica modificando i parametri di stampa o il design.
Stampa 3D con TPU con la tecnologia SLS
La stampa 3D SLS è ideale per applicazioni a più alto rendimento e più funzionali, come prototipi funzionali per i test o la produzione con volumi ridotti di prodotti per utilizzo finale personalizzabili, come plantari, imbottiture per caschi e dispositivi indossabili. La stampa 3D SLS può sfruttare la una flessibilità e la resistenza eccezionali del TPU per abbreviare i tempi per il lancio di nuovi prodotti e rivoluzionare la cura di pazienti. L'elevata resistenza alla lacerazione rende le parti in elastomero resistenti e durevoli, mentre l'accessibilità dei sistemi SLS da banco, come la serie Fuse, permette una produzione con un costo per unità ridotto. Inoltre, il basso tasso di rigenerazione aumenta la convenienza e la scalabilità del sistema, in quanto incrementa l'efficienza di utilizzo della polvere e riduce la spesa per i nuovi materiali.
Le parti in TPU realizzate con la stampa 3D SLS sono perfette per le applicazioni in cui le geometrie complesse sono necessarie o utili per le prestazioni. Data la natura autoportante della tecnologia SLS, non sono necessarie strutture di supporto ed è possibile realizzare geometrie complesse con canali interni, reticoli o strutture a fisarmonica, come quelle utilizzate nei collettori. Le strutture reticolari in gomma consentono di ottenere un'elevata resistenza alla compressione che aumenta l'efficacia di prodotti come caschi protettivi o solette e plantari per calzature.
Materiali TPU per le stampanti SLS
Esistono molti sistemi con tecnologia di sinterizzazione laser selettiva (SLS) che consentono di utilizzare un materiale in polvere di TPU. Numerosi sono apparecchi industriali di grandi dimensioni con requisiti di infrastruttura complicati, come sistemi di ventilazione, un ingombro elevato o diversi requisiti in termini di circuiti elettrici. Con l'introduzione di sistemi SLS più accessibili, come la serie Fuse di Formlabs, la stampa 3D con TPU su letto di polvere è diventata più accessibile e conveniente.
La TPU 90A Powder di Formlabs è sicura per la pelle e apre a grandi opportunità nel campo dei dispositivi indossabili e medici, nei quali le norme di sicurezza limitano l'uso di molte parti stampate in 3D. Con la TPU 90A Powder, i team di ingegneria e progettazione possono sfruttare la libertà di design della stampa 3D, l'elevata resistenza alla lacerazione e all'allungamento della gomma e la sicurezza per la pelle di molti materiali termoplastici stampati tradizionalmente, il tutto in un unico workflow.
La TPU 90A Powder di Formlabs può essere facilmente integrata in un workflow con stampanti SLS della serie Fuse già attivo, ma anche essere il primo materiale SLS con cui iniziare. Il materiale viene stampato in un ambiente aerato e non richiede un'atmosfera inerte, come invece accade per alcuni materiali SLS.
Inoltre, sulle stampanti della serie Fuse le parti in TPU non utilizzano la Surface Armor, ovvero il guscio di materiale semi-sinterizzato che circonda le parti in polvere più rigide, per cui il processo di eliminazione della polvere è abbastanza semplice utilizzando l'apparecchio per la post-elaborazione Fuse Sift.Sebbene la TPU 90A Powder non sia provvista di Surface Armor, è comunque consigliata la sabbiatura per rimuovere tutta la polvere in eccesso dalle parti, in modo da ottenere un materiale più pulito e facile con cui lavorare. La conversione di una stampante della serie Fuse alla TPU 90A Powder è assolutamente possibile, anche se Formlabs consiglia di utilizzare una Fuse Sift e una camera di stampa dedicate.
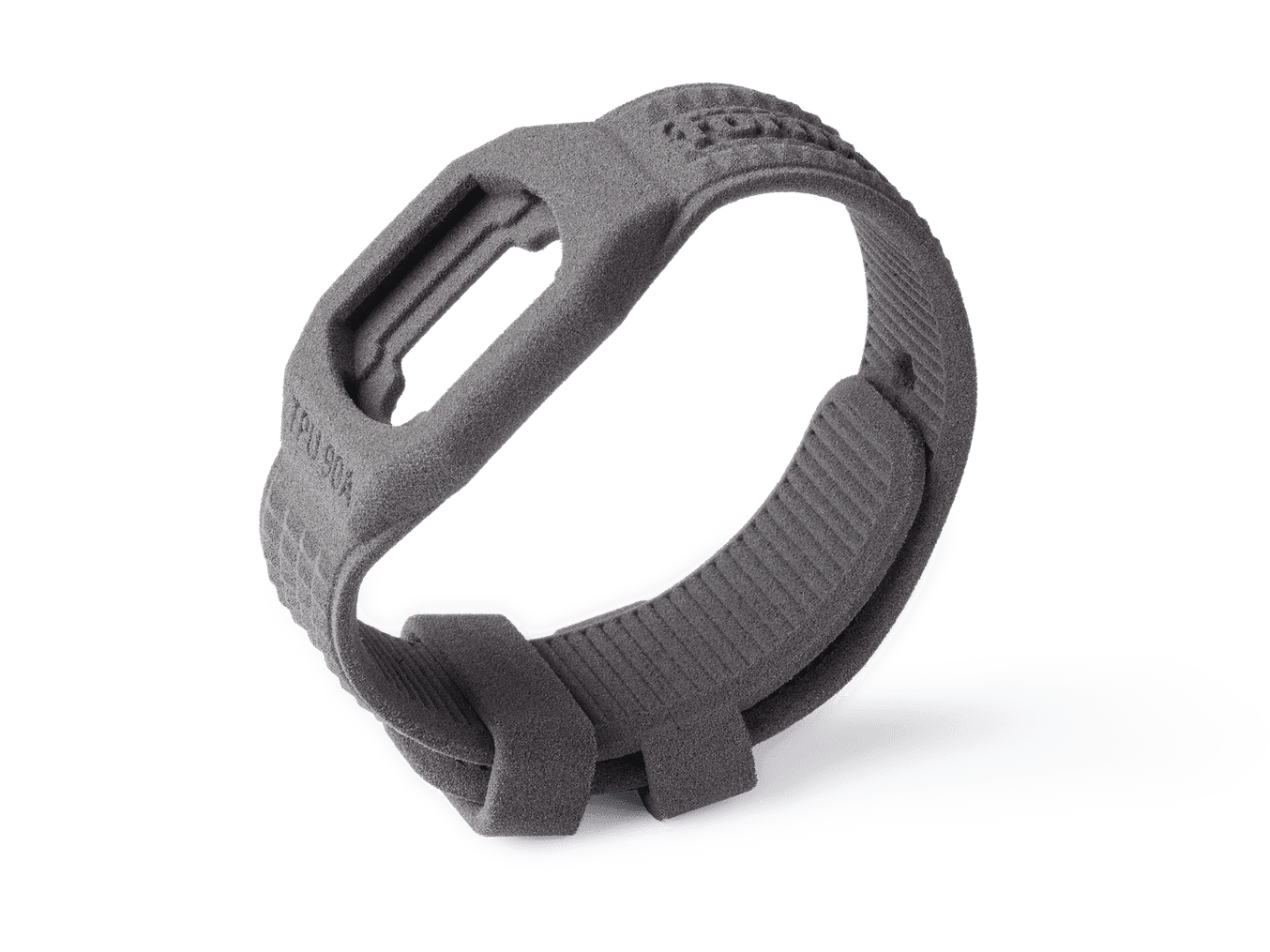
TPU 90A Powder: la polvere SLS flessibile di Formlabs
Richiedi un campione gratuito del cinturino di un orologio stampato con la TPU 90A Powder, il nostro primo materiale SLS flessibile.
Applicazioni della stampa 3D con TPU
Esistono workflow collaudati per la produzione tradizionale di parti in TPU, che sono tuttora ideali per la produzione di massa di prodotti in gomma. Tuttavia, la stampa 3D con TPU è un'ottima alternativa in molte situazioni, tra cui quelle in cui sono richiesti velocità o facilità di utilizzo, prototipazione rapida, supporti di produzione su richiesta e personalizzazione. Dall'inizio di un processo di design in cui sono necessari prototipi rapidi fino ai design definitivi per le parti per utilizzo finale, anche per i beni di consumo realizzati con la personalizzazione di massa, il TPU per la stampa 3D può rendere i workflow più veloci ed efficienti, nel rispetto delle proprietà meccaniche e della fedeltà.
Prototipazione rapida
La stampa 3D con TPU consente alle aziende che in passato ricorrevano all'esternalizzazione di portare la capacità di prototipazione in-house, riducendo i tempi di realizzazione e abbattendo i costi.
La creazione di un prototipo di casco sportivo, ad esempio, richiede la capacità di fabbricare una calotta rigida e un'imbottitura morbida interna. Alcune aziende innovative sono al lavoro per progettare nuove strutture reticolari e tecnologie antiurto per l'imbottitura, e il TPU è un materiale perfetto.
Tuttavia, la sperimentazione di nuovi design e geometrie rende i tradizionali metodi di creazione di attrezzature eccessivamente costosi, mentre l'esternalizzazione può richiedere settimane di attesa. Poter utilizzare un unico workflow e un unico tipo di tecnologia sia per la calotta rigida esterna che per l'imbottitura interna permette di eseguire iterazioni a un ritmo molto più elevato. I caschi dovranno essere sottoposti a test fisici approfonditi, per cui saranno necessarie dieci imbottiture per un singolo collaudo. Si tratta di volumi troppo elevati per realizzare a mano in modo meticoloso una superficie ammortizzante, ma troppo bassi perché lo stampaggio tradizionale del TPU sia conveniente. La soluzione è la stampa 3D in-house.
Le stampanti 3D SLS della serie Fuse possono facilmente stampare più strutture reticolari in gomma con la TPU 90A Powder, con leggere variazioni per testare diversi design. Modificando il design della parte, ad esempio cambiando lo spessore delle pareti, è possibile produrre parti con diversi livelli di durezza per applicazioni diverse o come iterazioni dopo i test.
Il workflow della serie Fuse consente di accedere a più materiali che includono una vasta gamma di proprietà meccaniche, di mantenere lo sviluppo e la produzione in-house e di poter progettare molti componenti diversi con un'unica tecnologia. La TPU 90A Powder introduce un tipo di prodotto inedito, che può essere prototipato direttamente con la stampa 3D con la stessa piattaforma affidabile della serie Fuse.
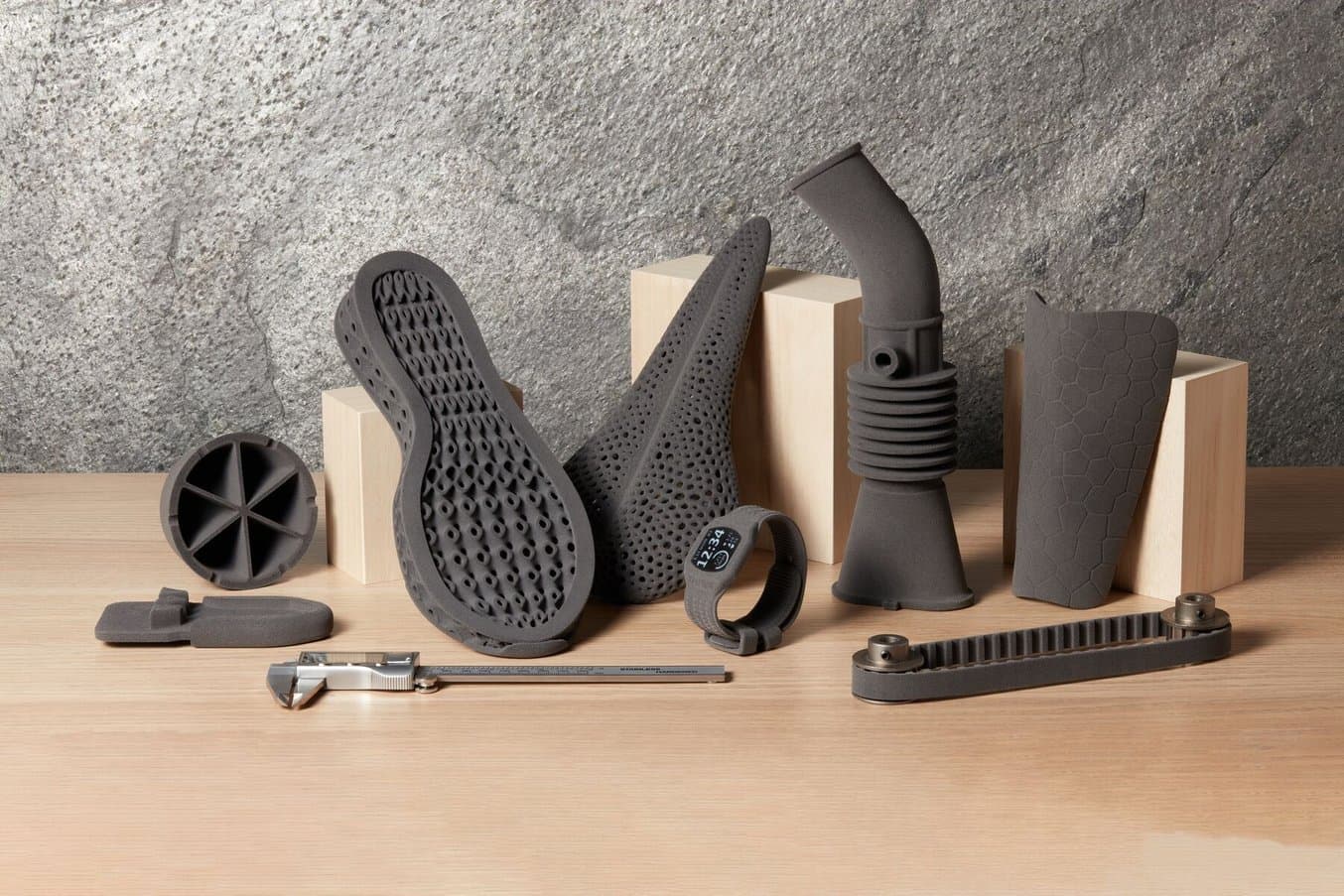
La TPU 90A Powder è il materiale ideale per la realizzazione di prototipi funzionali per parti che richiedono flessibilità, come dispositivi indossabili sicuri per il contatto con la pelle, attrezzature sportive ad alte prestazioni o solette per scarpe.
Supporti di produzione
Per chi non lavora nel settore della fabbricazione può essere difficile distinguere tra i vari tipi di supporti di produzione. A prescindere dal fatto che si tratti di una dima, una staffa, un involucro o uno dei tanti altri modi in cui gli apparecchi vengono tenuti insieme, il concetto di fondo rimane lo stesso: quando sono necessari, lo sono davvero. Il TPU è la risposta a un problema che molti produttori si trovano ad affrontare, ovvero come evitare che una tecnologia di produzione da milioni di dollari si usuri troppo.
I supporti di produzione morbidi possono aiutare a prolungare la durata di apparecchiature pesanti, attutendo gli urti o fornendo un'impugnatura dalla forma perfetta. Quando un sigillo o una guarnizione si rompe dopo anni di utilizzo continuo, è possibile stampare istantaneamente la parte di ricambio e rimettere in funzione la linea di produzione in poche ore, invece di aspettare giorni o settimane per riceverne una nuova.
Arricchire il catalogo di materiali è un'ulteriore sicurezza per i produttori, poiché garantisce loro una protezione contro la rottura imprevista di parti o componenti di apparecchi. Poter contare su maggiori proprietà meccaniche in-house consente di ridurre l'impatto dei ritardi della catena di fornitura e dei costi elevati delle riparazioni effettuate dai produttori originali dei componenti. Grazie alle parti in gomma stampate in 3D, ora è possibile riparare o sostituire su richiesta un intero sottoinsieme di componenti delle attrezzature. Evitando l'interruzione di una linea di produzione o di un processo, si possono risparmiare migliaia di dollari al giorno.
Il TPU può essere utilizzato per gli smorzatori nei test automobilistici e aerospaziali, ma anche per le dime destinate ai processi industriali, come la termoformatura di parti dalla forma unica. Nelle fabbriche automobilistiche, i grandi sistemi robotici operano su binari che devono piegarsi e ruotare. Ammortizzatori personalizzati e alloggiamenti morbidi possono evitare l'attrito e allungare la vita utile di questi apparecchi.
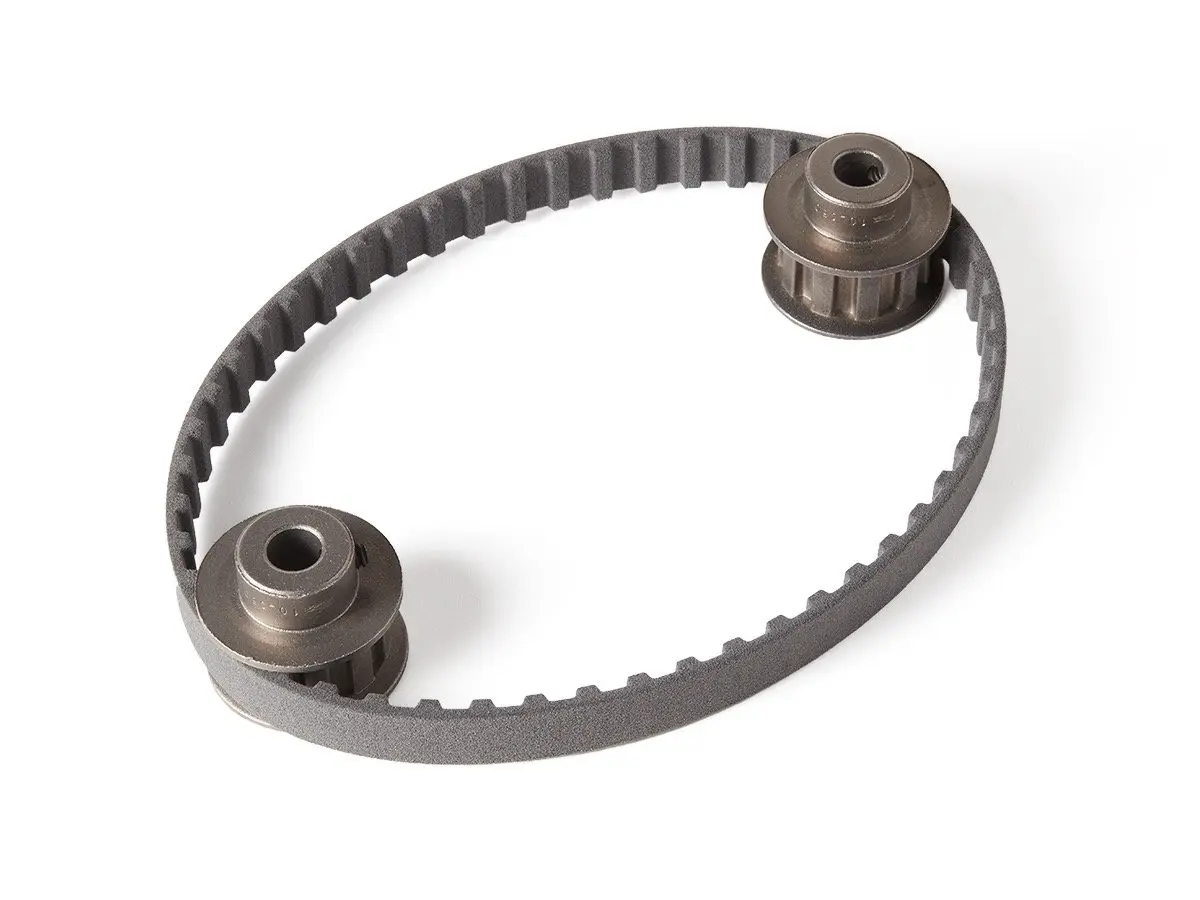
Avere a disposizione un materiale come il TPU significa che è possibile progettare e stampare in giornata parti di ricambio e supporti di produzione flessibili, in modo che la produzione non subisca mai interruzioni.
Prodotti personalizzati indossabili realizzati con volumi ridotti
Nei settori dello sport, della moda e delle tecnologie indossabili, i marchi che puntano a conquistare maggiori quote di mercato devono necessariamente offrire opzioni di personalizzazione. Fino a quando la stampa 3D non è diventata accessibile, i costi associati alla creazione di attrezzature rendevano quasi impossibile la produzione di volumi ridotti o di pezzi unici.
Tuttavia, prima dell'introduzione del TPU, la maggior parte dei materiali per la stampa 3D risultavano troppo rigidi per gli articoli sportivi o i dispositivi indossabili. Dalle suole per scarpe personalizzabili sulla base della pianta e della distribuzione del peso di una persona, ai caschi da football progettati per attutire gli urti, fino al cinturino per orologio adattato alla forma del polso, le possibilità sono infinite.
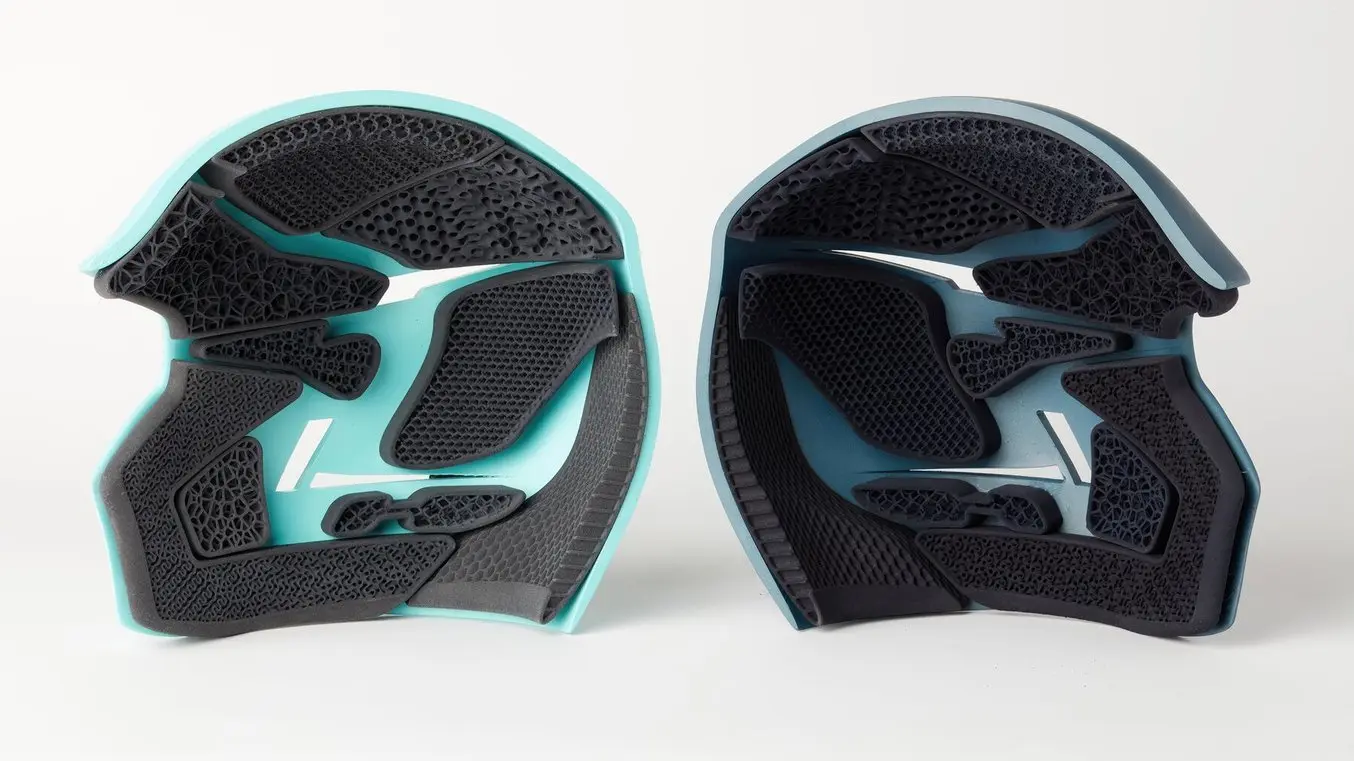
Casco per football americano con imbottiture stampate su misura in TPU su una stampante 3D SLS della serie Fuse.
Dispositivi medici
Grazie alla sua eccezionale durata e resistenza, il TPU per la stampa 3D è ideale per protesi, plantari, apparecchi su misura e dispositivi medici. La possibilità di stampare in 3D parti per utilizzo finale flessibili e resistenti crea nuove opportunità ai professionisti del settore medico, poiché combina l'elevato allungamento a rottura e la straordinaria resistenza alla lacerazione dei materiali in gomma con la libertà di design e la resistenza della stampa 3D SLS.
Il TPU è un elastomero flessibile, ideale per la stampa 3D di parti mediche come:
-
Prototipi di dispositivi medici e dispositivi medici e componenti per utilizzo finale
-
Solette plantari e rivestimenti protesici
-
Dispositivi indossabili, guarnizioni, componenti antiurto e tubi
-
Tutori, caschetti di rimodellamento cranico
-
Solette correttive e per calzature sportive
La stampa 3D nel settore sanitario, sebbene sia una realtà in forte espansione, è limitata dai rigorosi requisiti dei materiali, sia per quanto riguarda le certificazioni di sicurezza che per le proprietà meccaniche e di resistenza. Il TPU per la stampa 3D apre a maggiori opportunità per diverse applicazioni, aggiungendo un ulteriore strumento ai processi già esistenti.
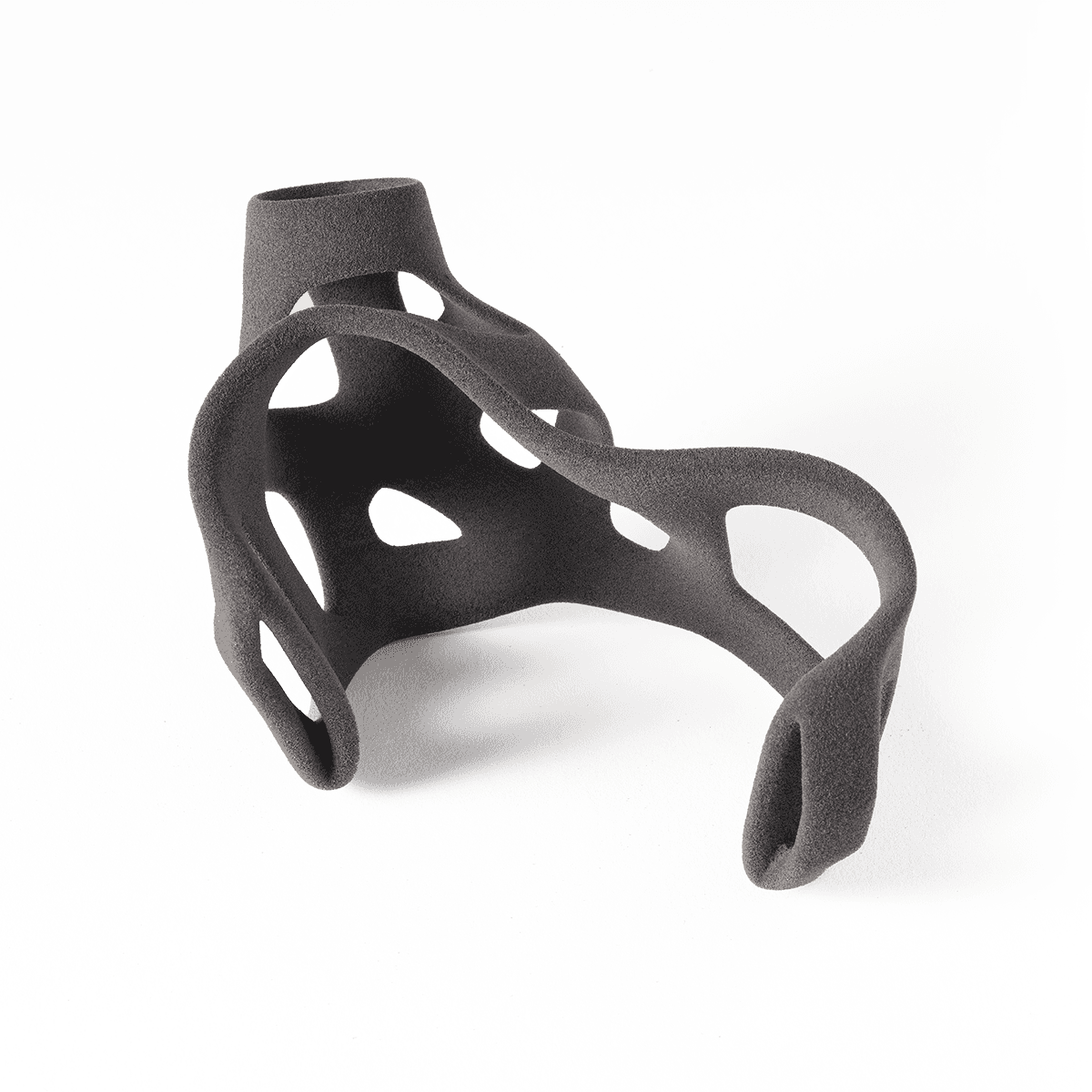
Questo tutore ortopedico per pollice realizzato su misura fornisce più flessibilità e controllo rispetto a un tutore tradizionale ed è stato progettato per supportare il dito e prevenire ulteriori lesioni.
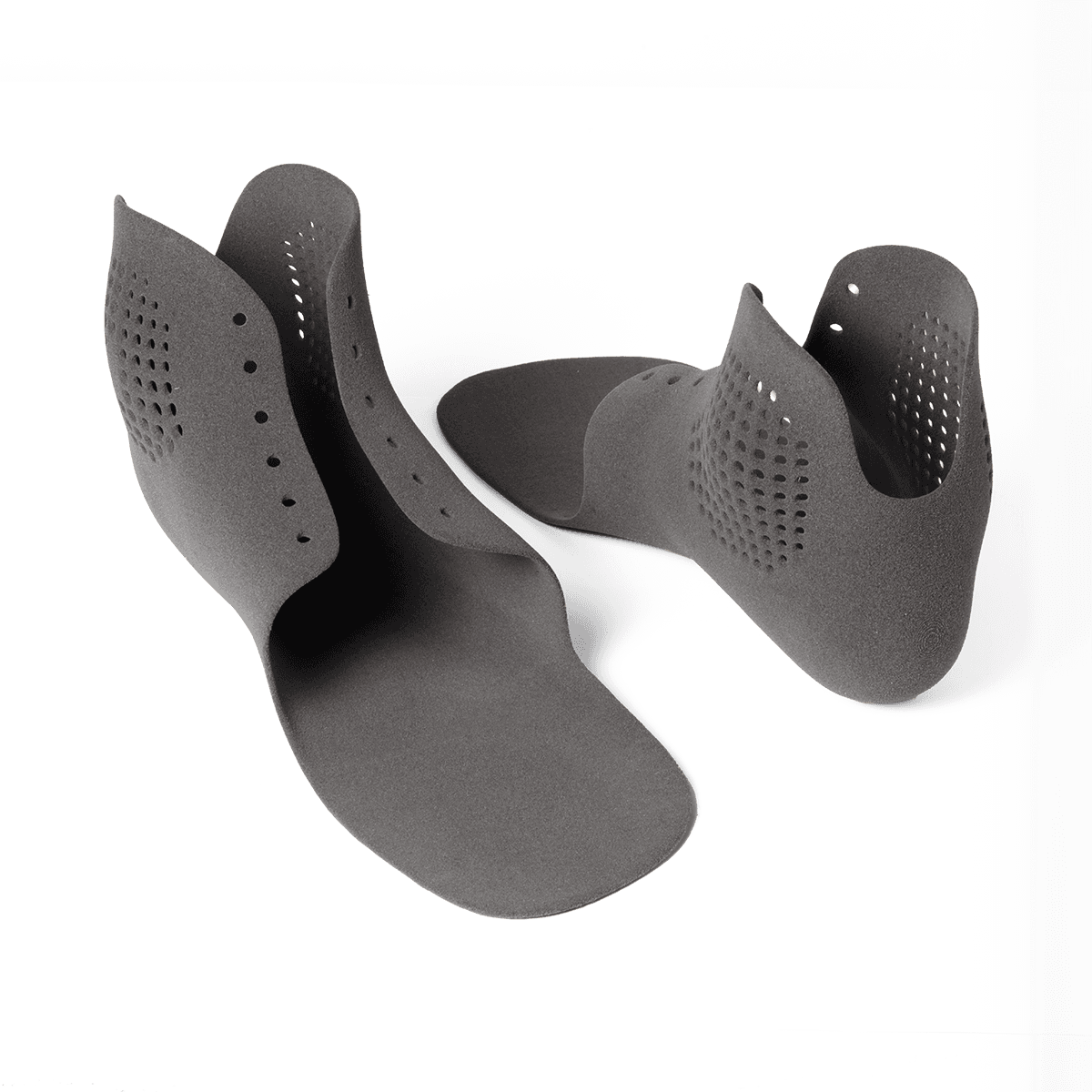
Il TPU è ideale per un'ampia gamma di dispositivi ortopedici, come i rivestimenti per calzature e le solette sportive o correttive.
Casi di studio
Componenti protettivi per apparecchi realizzati da Heidelberg, azienda leader nelle macchine da stampa
Heidelberger Druckmaschinen AG è la principale azienda produttrice di macchine da stampa offset al mondo, presente in oltre 170 Paesi con quasi 10 000 dipendenti. Produce un'ampia gamma di strumenti e soluzioni di automazione per l'intera catena del valore nel settore della stampa, da alcune delle più grandi e veloci macchine da stampa all'avanguardia a taglierine e piegatrici.
L'azienda utilizza una stampante 3D SLS Fuse 1+ 30W per creare componenti di apparecchi, tra cui parti leggere per i robot pick-and-place, nuovi componenti per le piegatrici e parti sostitutive per i componenti in acciaio degli apparecchi. La TPU 90A Powder consente a Heidelberger di creare parti flessibili capaci di resistere agli urti e abbastanza malleabili da adattarsi all'interno di apparecchi rigidi già in uso.
Poiché le parti sostitutive o i supporti di produzione devono essere inseriti in sistemi robotici esistenti, spesso hanno forme complesse e inusuali. Si tratta di parti che vengono sviluppate appositamente per l'applicazione desiderata sulla base delle sollecitazioni e delle forze a cui verranno sottoposte e che devono resistere a un'usura costante. Le parti stampate in 3D sono spesso combinate con altri elementi come cuscinetti in metallo o componenti rivestiti in teflon, che hanno proprietà anti-frizione. Alcune parti sono meno complesse, ma richiedono comunque un'elevata accuratezza o delicatezza.
Le parti flessibili in poliuretano termoplastico sono usate per impedire la contaminazione, proteggere gli spigoli vivi e i sensori o evitare l'usura. La stampa 3D SLS con la TPU 90A Powder offre un workflow perfetto per questo tipo di parti e consente di proteggere apparecchi costosi da danni causati da un uso molto intenso.
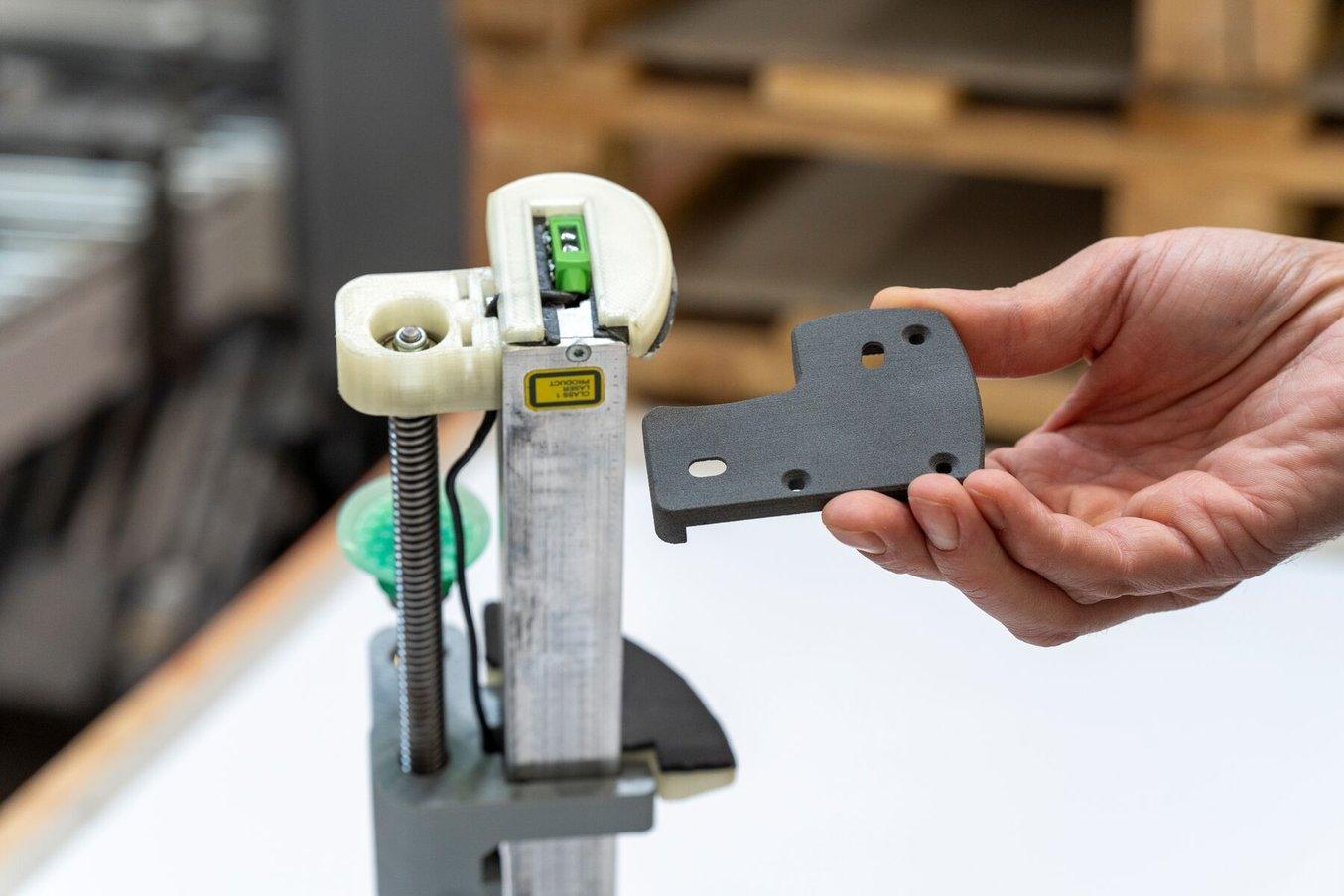
Parte flessibile stampata in TPU 90A Powder che protegge i sensori e altri componenti per organi di presa.
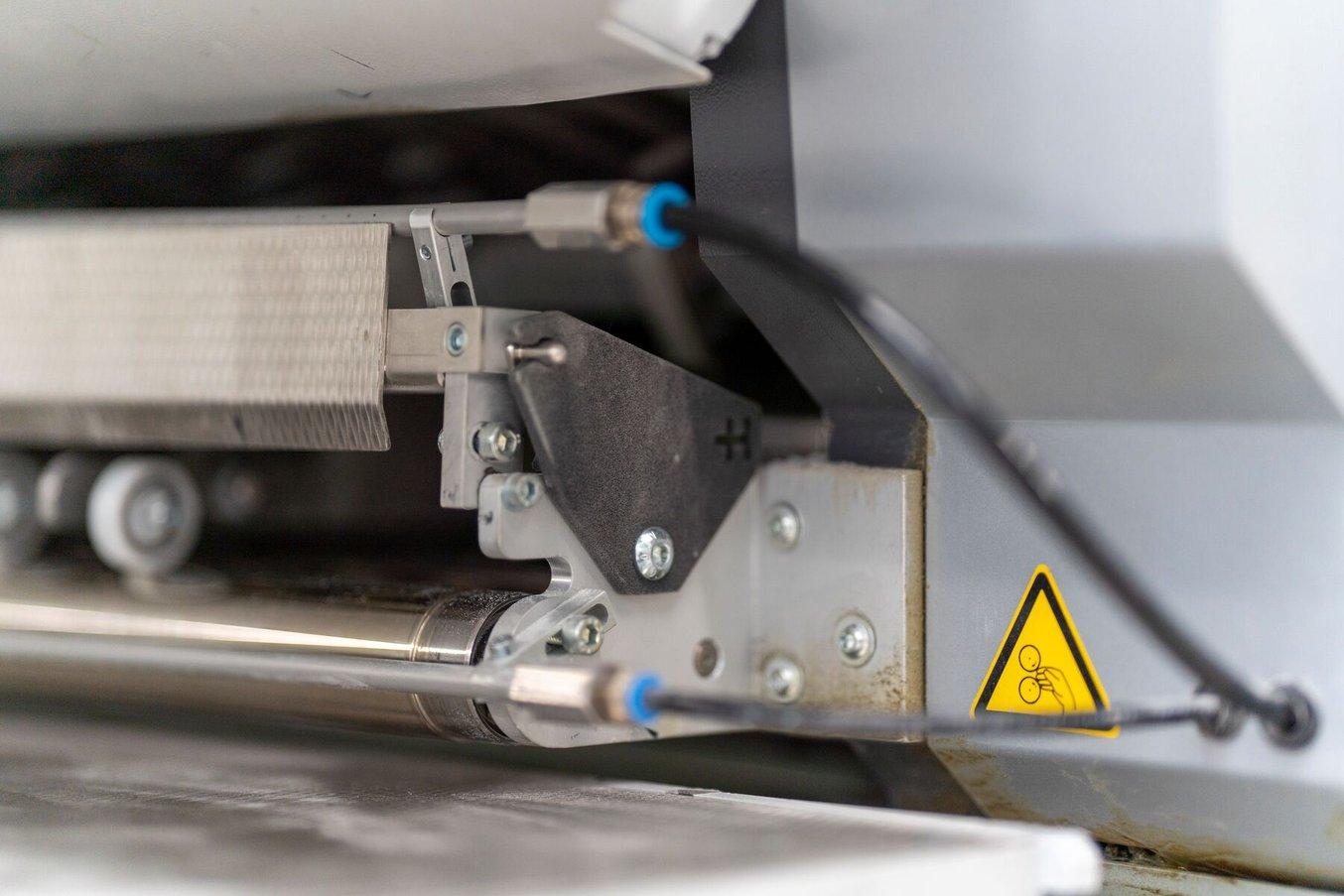
Le parti flessibili sono ideali per i componenti con accoppiamento a scatto. Proteggendo gli spigoli vivi, proteggono anche il personale.
Una parte specifica, ovvero una guida dei cavi stampata in TPU 90A Powder, protegge i cavi elettrici dall'esposizione a frizione elevata, aumentandone la longevità e riducendo al minimo i tempi di inattività. Se uno dei cavi si spezza o si sfilaccia, l'intero apparecchio rimane fuori uso finché non viene ordinata e installata la parte sostitutiva. Componenti come questa guida dei cavi per la protezione degli apparecchi possono fare la differenza nell'operatività di una fabbrica.
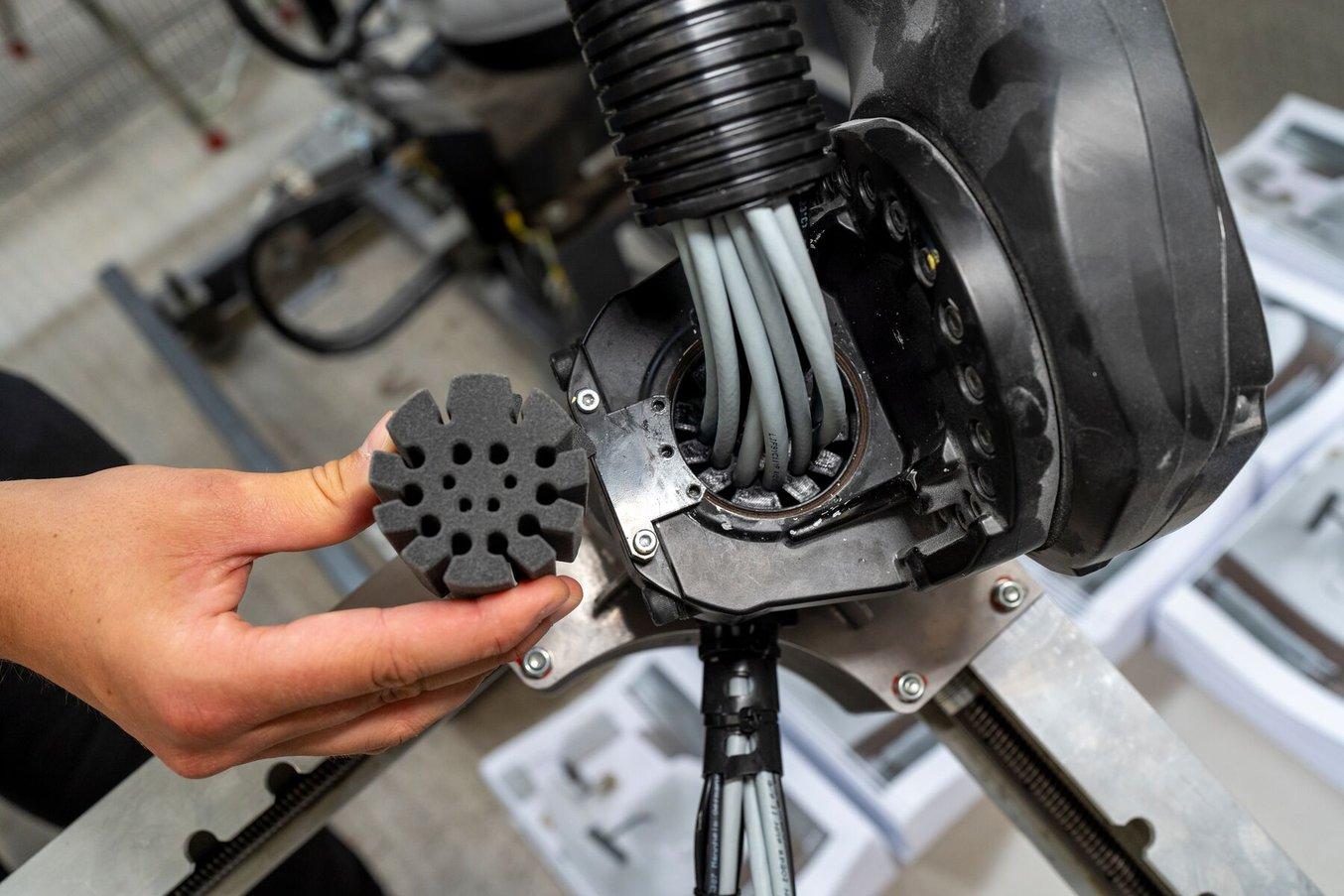
Questa guida flessibile, prodotta con una stampante 3D SLS della serie Fuse, ha un design complesso e offre una soluzione resistente a lungo termine per proteggere i cavi dall'usura.
L'accessibilità e la convenienza della serie Fuse e della TPU 90A Powder permettono all'azienda di assumere il controllo della catena di fornitura e soddisfare le esigenze interne di manutenzione. Le parti in TPU 90A Powder sono ideali per proteggere gli apparecchi e prolungare così la vita utile dei componenti, contribuendo essenzialmente a ridurre i costi e a evitare i tempi di inattività.
Deutsche Bahn mantiene i treni operativi grazie a supporti di produzione in TPU
A Neumünster, in Germania, si trova la sede di Deutsche Bahn destinata alla revisione e manutenzione dei treni pubblici tedeschi. Qui sfruttano la stampa 3D per rendere le operazioni il più efficienti possibile. Grazie all'integrazione della stampa 3D nel suo workflow, Deutsche Bahn ha risparmiato milioni di euro e ridotto i tempi di consegna, consentendo di riportare i vagoni sui binari più velocemente.
Carsten Wolfgramm, ingegnere di produzione ed esperto di produzione additiva, supervisiona l'utilizzo delle due stampanti 3D SLS Fuse 1+ 30W dell'azienda, adibite una alla stampa in Nylon 12 Powder e l'altra alla stampa in TPU 90A Powder. Wolfgramm ha affermato: "Utilizziamo le stampanti Formlabs perché il rapporto prezzo/prestazioni è imbattibile. Sono affidabili e davvero plug-and-play, soprattutto quelle SLS. In questo modo si semplifica molto il lavoro di iterazione continua delle parti. Funzionano 24 ore su 24, sette giorni su sette, tutto l'anno."
Una delle operazioni di manutenzione più frequenti richiede la rimozione dei ripiani portabagagli allo scopo di riverniciare e rivestire le pareti dei vagoni. Lo spostamento dei ripiani danneggia spesso le pareti, vanificando tutto il lavoro svolto dal team di manutenzione. Per evitare questo inconveniente, il team di Deutsche Bahn ha progettato e stampato in 3D delle coperture su misura per i ripiani utilizzando la TPU 90A Powder. Le coperture vengono fatte scorrere sopra questi ultimi a protezione dei bordi, in modo da non danneggiare gli interni del vagone appena riverniciati durante la rimozione e il riposizionamento.
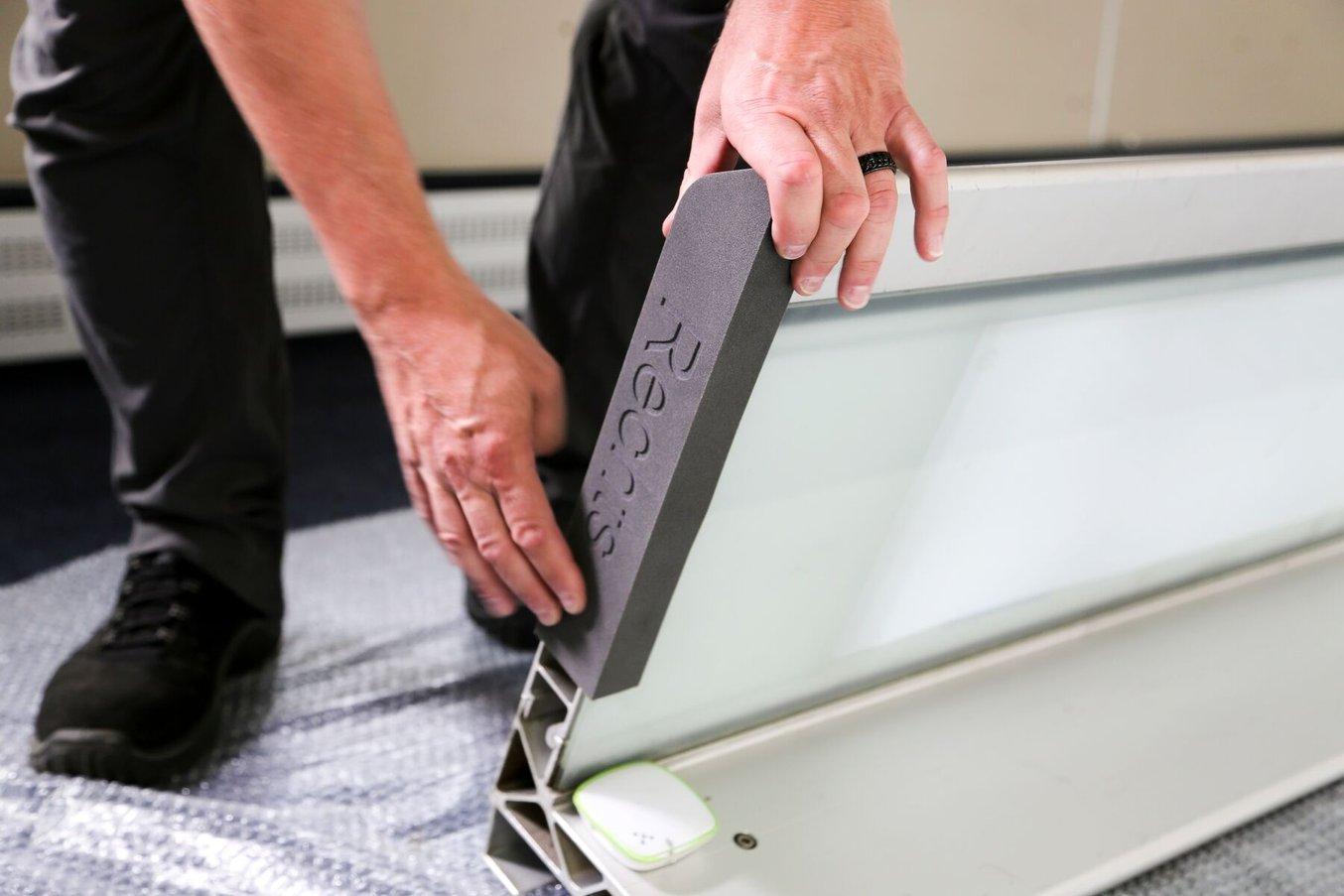
Il team utilizza un materiale flessibile, la TPU 90A Powder, per la protezione contro graffi e urti.
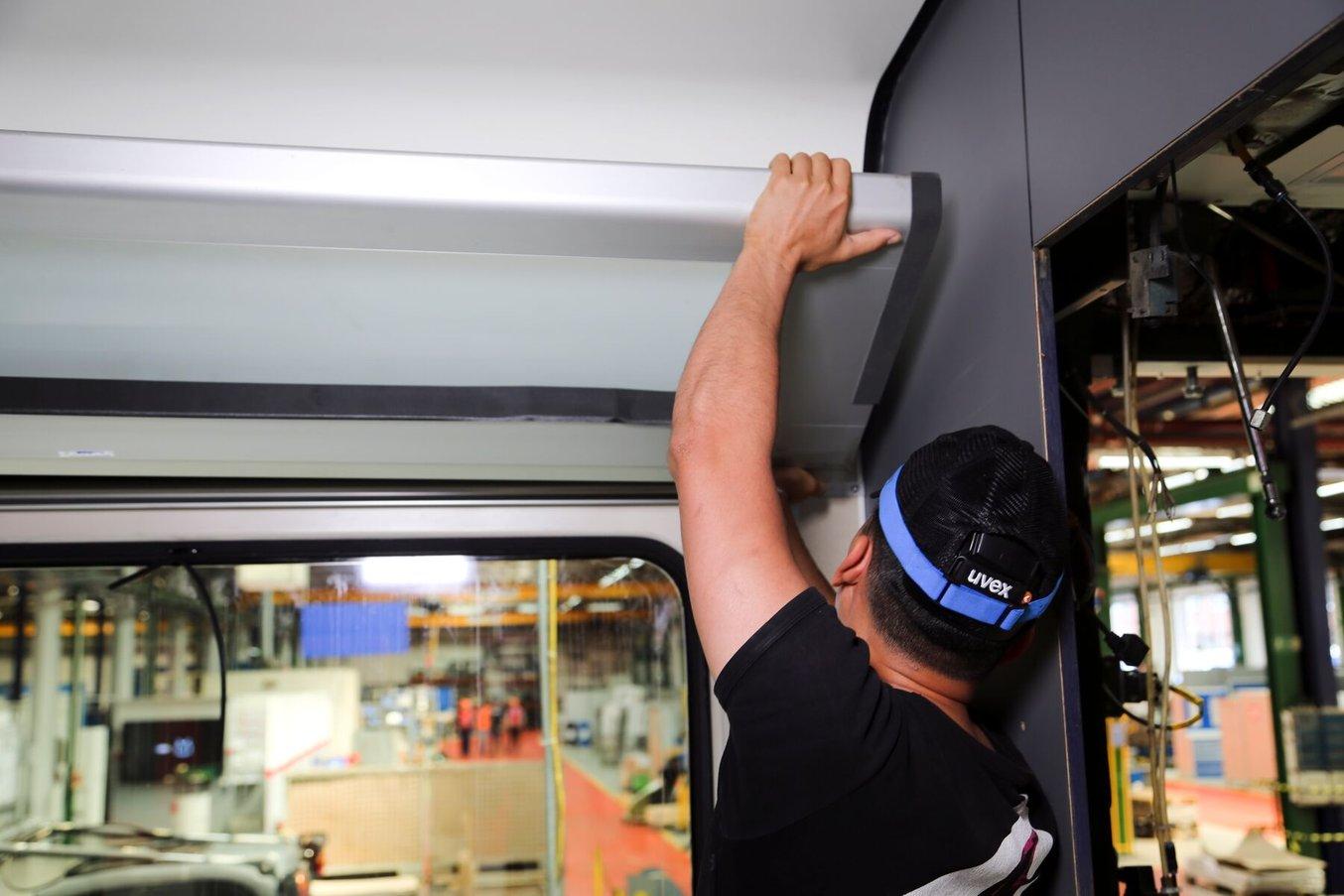
La stampa 3D SLS consente di realizzare una parte sottile che si inserisce tra il portabagagli e la parete.
"Prima di poter contare su questa protezione stampata in 3D, il personale cercava di evitare i graffi usando del pluriball o accorgimenti simili, che non sempre si rivelavano efficaci. Grazie alle parti in TPU, siamo finalmente riusciti a prevenire qualsiasi tipo di danno."
Carsten Wolfgramm, ingegnere di produzione ed esperto di produzione additiva presso Deutsche Bahn
La stampa 3D di parti destinate a manutenzione, riparazione e revisione consente di risparmiare e ridurre al minimo i tempi di manodopera. Adottando questa soluzione, Deutsche Bahn mostra una nuova strada alle grandi aziende di trasporto, incentivandole all'integrazione della stampa 3D nei loro workflow. La possibilità di stampare in 3D in-house parti flessibili e personalizzabili, come queste coperture protettive, consente a Deutsche Bahn di rendere i processi più efficienti e riportare i treni sui binari più velocemente.
Radio Flyer crea prototipi in TPU per bici elettriche e giocattolo
Punto di riferimento per le famiglie americane da oltre un secolo, Radio Flyer è il produttore dello storico Little Red Wagon®, un carrettino giocattolo diventato talmente riconoscibile da meritare l'ingresso nella National Toy Hall of Fame. L'azienda è il più grande fabbricante al mondo di veicoli giocattolo come carrettini, monopattini, tricicli, go-kart, nonché biciclette elettriche e molti altri prodotti innovativi che le hanno permesso di guadagnarsi un posto nella cultura popolare, ma soprattutto nei sogni di ogni bambino e bambina.
La stampa 3D è un elemento molto importante del processo di sviluppo di Radio Flyer e Agostino Lobello, tecnico di progettazione dell'azienda, ha scoperto che la TPU 90A Powder permette di creare prototipi perfettamente funzionanti. "La finitura superficiale a elevata aderenza è di gran lunga superiore a quella che si può ottenere con i TPE/TPU per la stampa in 3D coi quali ho lavorato in passato. È molto simile a quella del TPE/TPU stampato a iniezione, il che è fantastico per le applicazioni di prototipazione. Questo processo è efficace sia dal punto dei vista dei costi che dei tempi perché, al momento, l'unica alternativa sarebbe quella di usare un prototipo e iniettarvi all'interno vero e proprio TPE o un altro uretano", ha dichiarato Lobello.
"Non vediamo l'ora di usare questo materiale per raggi, manopole, paraurti e imbottiture di sellini, ma anche per creare prototipi di molle in TPE con una specifica flessibilità."
Agostino Lobello, ingegnere progettista
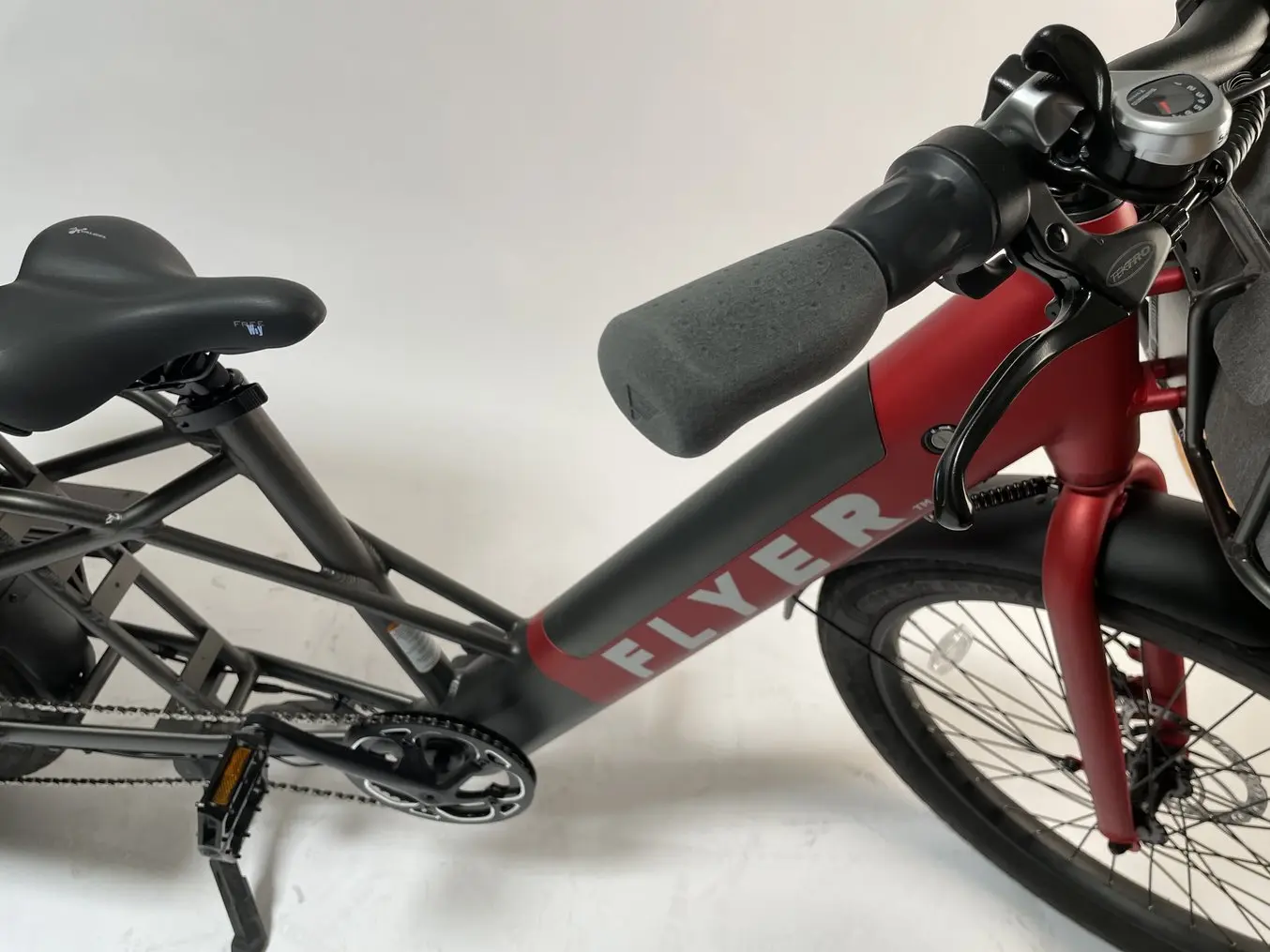
Usare la TPU 90A Powder sulle stampanti della serie Fuse permette a Radio Flyer di creare prototipi funzionali di parti, come le manopole morbide della bici elettrica da trasporto Flyer™ L885.
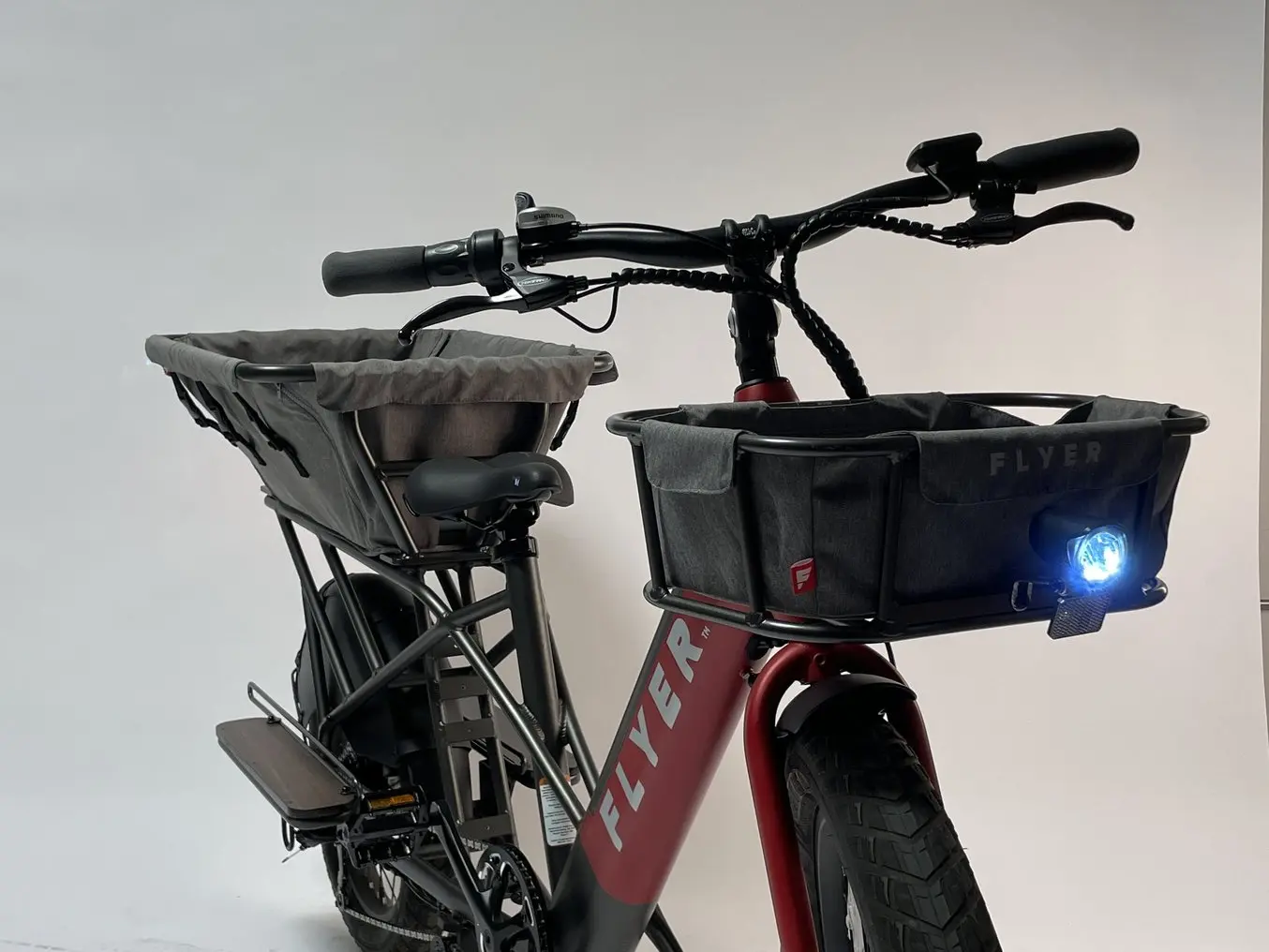
Inizia a stampare 3D con il TPU con la serie Fuse
Un workflow di stampa 3D SLS accessibile con la polvere di TPU consente ai produttori di migliorare il processo di design grazie a una prototipazione iterativa di alta qualità o di realizzare parti per utilizzo finale personalizzate.
L'ecosistema SLS Fuse, che comprende le stampanti e la Fuse Sift, è compatto, economico e accessibile. La TPU 90A Powder di Formlabs offre nuove applicazioni e semplifica i workflow creando parti resistenti, flessibili e isotropiche che in precedenza richiedevano lo stampaggio. Le soluzioni di fabbricazione in-house di parti in gomma garantiscono maggiore controllo e flessibilità nel processo di design e produzione, indipendentemente dall'applicazione o dal settore in cui si opera. La TPU 90A Powder di Formlabs è stata valutata come sicura per la pelle, aspetto che apre a ulteriori possibilità per il settore sanitario e dei dispositivi indossabili.
Per ulteriori informazioni sulla produzione di parti in TPU stampate in 3D con il workflow SLS di Formlabs, puoi richiedere un campione gratuito realizzato con la TPU 90A Powder o contattare il nostro team vendite per parlare della tua applicazione specifica.