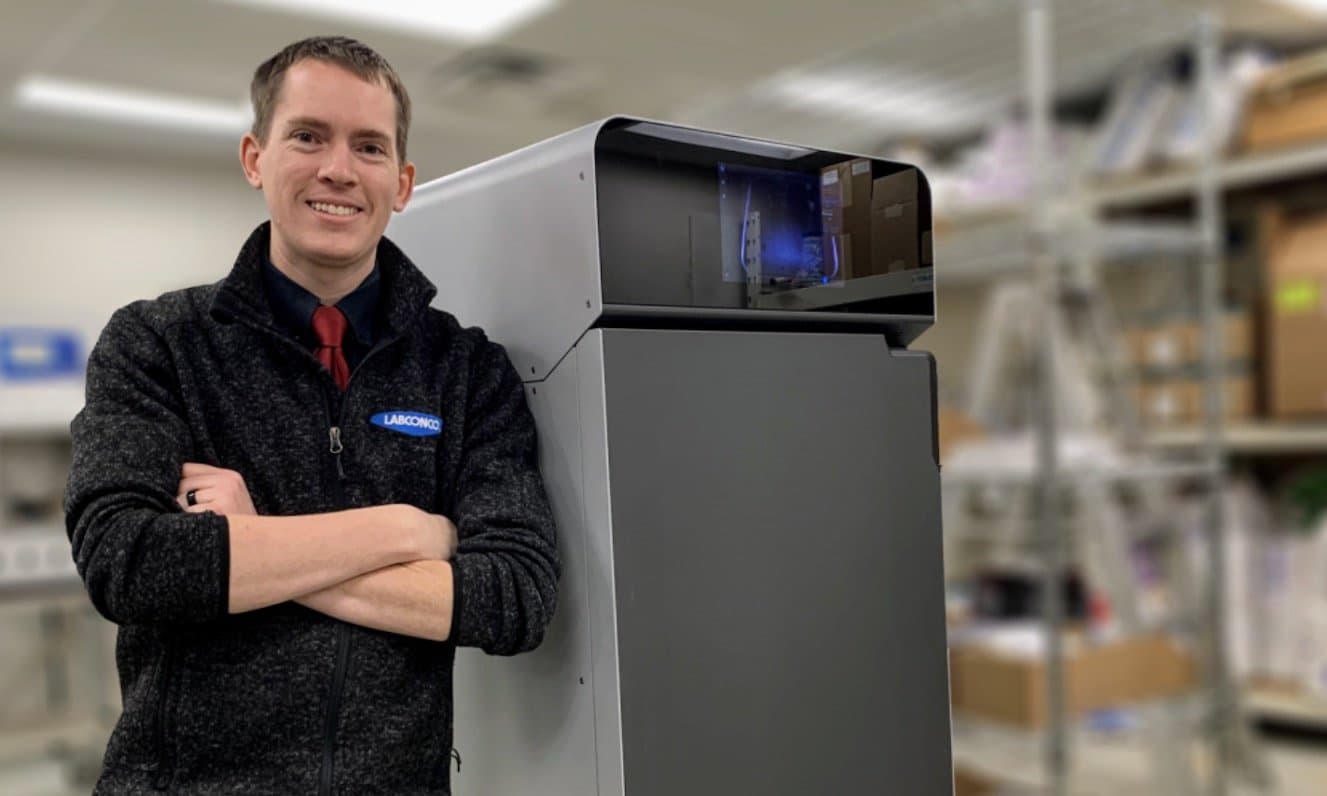
Durante il primo incontro di Brent Griffith presso Labconco all'inizio del 2020, la stampa 3D ha lasciato tutti a bocca aperta. Uno dei motivi per i quali si era riunito il team era discutere di un componente per il nuovo prodotto Logic Vue, che doveva essere stampato a iniezione. Poiché si trattava di un nuovo prodotto e la quantità delle scorte non era ancora stata stabilita, vi era la possibilità che lo strumento, il cui costo avrebbe superato i 15 000 €, producesse solo 100 parti durante il primo anno. L'elevato costo per parte che ne risultava aveva spinto il gruppo a cercare nuove soluzioni. "Dissi loro che con la stampa 3D avrei potuto completare, entro il giorno seguente, il lavoro che stavamo pianificando per l'anno intero. Rimasero tutti a bocca aperta", racconta Brent Griffith, ingegnere di prodotto presso Labconco.
A quell'epoca, Labconco non aveva alcuna stampante 3D in-house. Il giorno seguente, Griffith si presentò con diverse versioni del componente che aveva stampato a casa con le sue stampanti, dimostrando senza timore di smentita la convenienza della stampa 3D.
Attualmente, Griffith dirige per conto di Labconco un laboratorio in continua espansione composto da tre stampanti 3D a sinterizzazione laser selettiva (SLS) Fuse 1+ 3W, la Fuse Sift e la Fuse Blast, una stampante a stereolitografia (SLA) Form 3L e diverse stampanti a modellazione a deposizione fusa (FDM). Labconco è un'azienda produttrice di apparecchiature da laboratorio per svariati settori, tra cui quello dei test alimentari, dello sviluppo di prodotti farmaceutici, della diagnosi oncologica e della scienza forense. Griffith stampa centinaia di parti alla settimana, sia per ottenere un miglioramento rispetto ai componenti che sarebbero stati ottenuti tramite lavorazione meccanica o stampaggio a iniezione, sia come opzioni provvisorie quando i problemi della catena di fornitura compromettono la produzione, sia per contribuire alle fasi di sviluppo dei numerosi nuovi prodotti di Labconco.
Studio di fattibilità
Dopo aver dimostrato la validità dell'applicazione con il primo componente stampato in 3D, Griffith ha iniziato a stampare altre parti per i team ingegneristici dell'azienda, supportandone il lavoro di sviluppo, e in poco tempo ha cominciato a esserci la coda. "Ben presto l'attività è diventata frenetica", afferma Griffith.
Per scoprire cos'altro si potesse realizzare con la stampa 3D, ha iniziato a esaminare, insieme al collega ingegnere Austin Orme, le migliaia di parti, strumenti e componenti utilizzati nei prodotti Labconco. "La nostra missione era trovare un apparecchio che avesse un volume di stampa eccellente e che fornisse pezzi di alta qualità da utilizzare sia per i prototipi sia per la produzione", spiega Griffith. "Ci siamo subito resi conto che un solo apparecchio non sarebbe stato sufficiente per svolgere il lavoro, in quanto non ci avrebbe assicurato le capacità su larga scala e la flessibilità di cui avevamo bisogno per raggiungere il nostro obiettivo." Per prima cosa, il laboratorio ha aggiunto sei stampanti, tra cui tre stampanti SLS Fuse 1+ 30W e una stampante SLA di grande formato Form 3L.
"Abbiamo acquistato la Form 3L per poter accedere al catalogo di resine di Formlabs. Sapevo che ci avrebbe garantito flessibilità e nuove opportunità. E infatti così è stato."
Brent Griffith, ingegnere di prodotto
Grazie alla gamma di materiali disponibili per la Form 3L e ai volumi di produzione medio-alti resi possibili dalle tre stampanti della serie Fuse, Griffith ha potuto migliorare i prodotti esistenti, risparmiare decine di migliaia di euro sui costi delle attrezzature, accelerare lo sviluppo dei progetti esistenti e sostituire le parti su richiesta.
Sostituire, migliorare, adattare in scala: le applicazioni della stampa 3D presso Labconco
Sensore di riempimento realizzato con la stampa SLS: sostituzione di un assemblaggio stampato
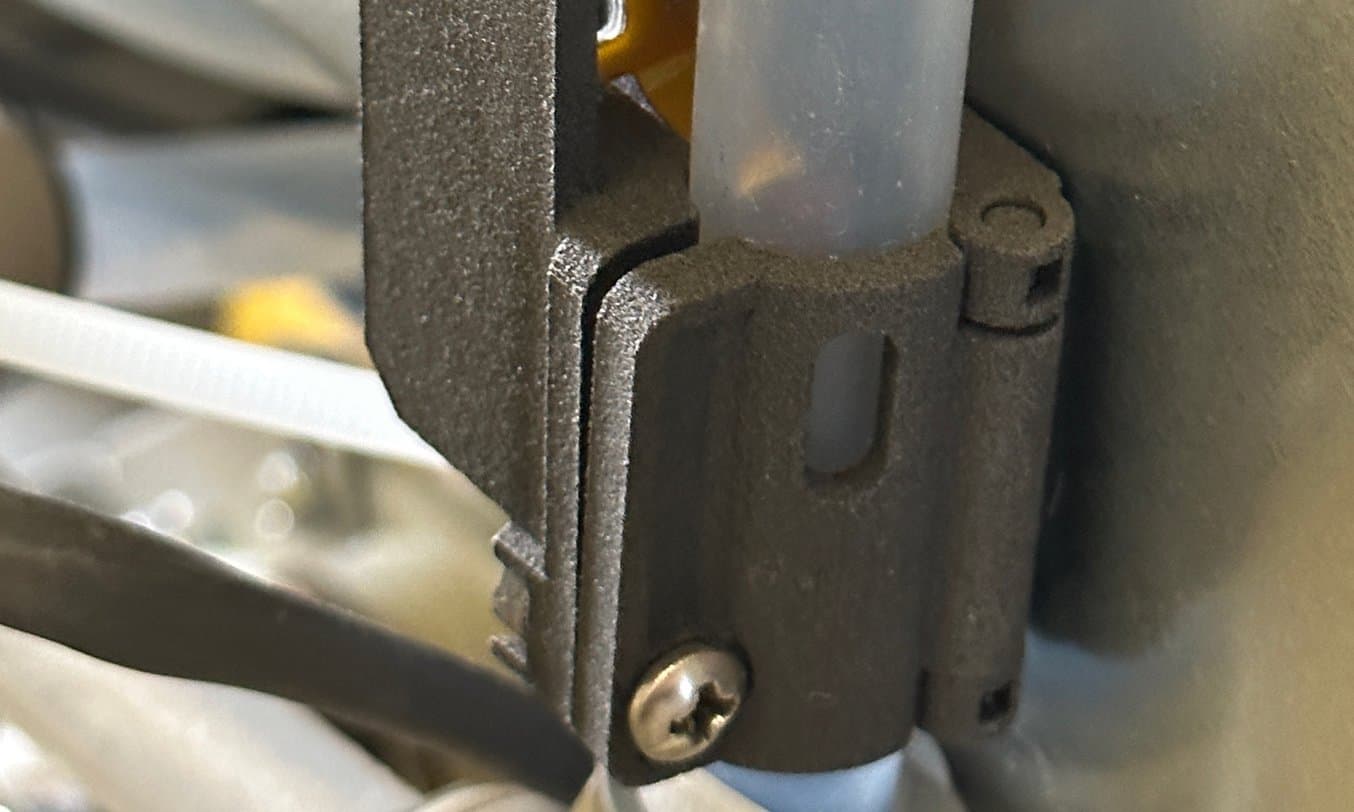
Questo componente del sensore di riempimento è dotato di una cerniera funzionante che Tim Grove, ingegnere di prodotto presso Labconco, ha progettato dopo aver visto il campione standard realizzato con la Nylon 12 Powder. Questa caratteristica consente di stampare la parte come un singolo componente invece che come un assemblaggio di più parti, riducendo il tempo di manodopera e il costo del materiale.
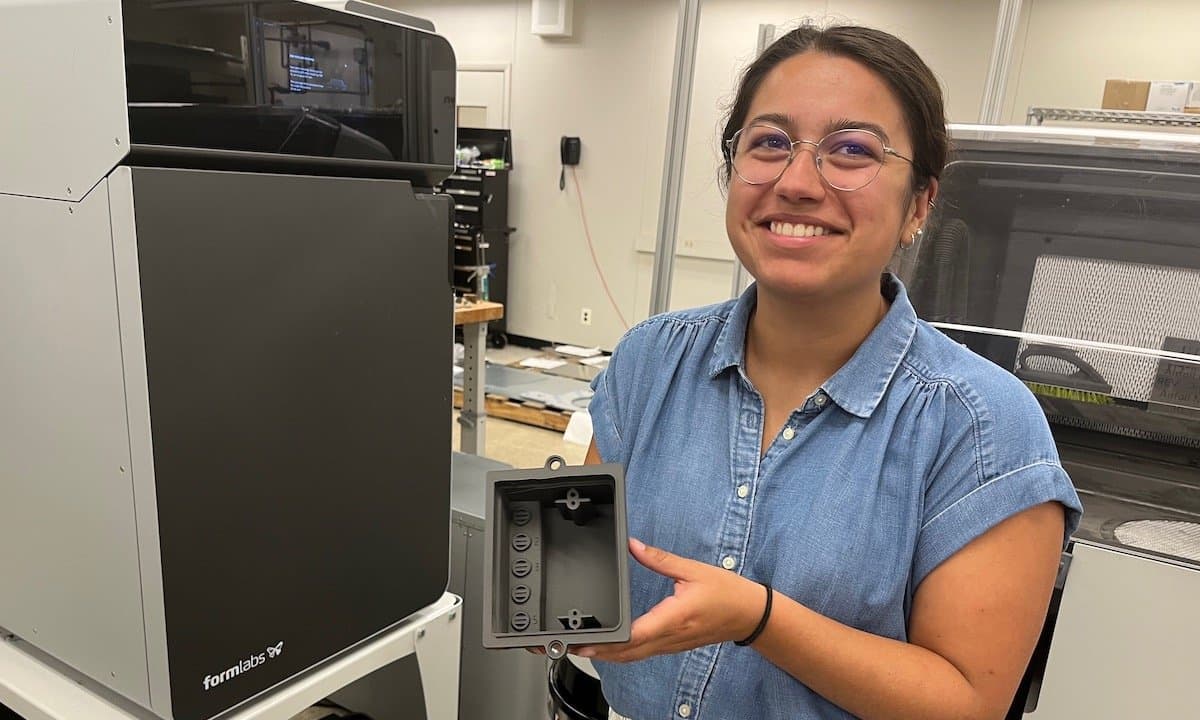
Poiché il team di ingegneria di prodotto di Labconco è riuscito ad adattare il proprio spazio di stampa 3D in modo così efficace, molti membri del team hanno accesso a tecnologie industriali come le stampanti SLS della serie Fuse. Griffith afferma che ora molti dipartimenti di Labconco stanno iniziando a pensare a un modo per incorporare la stampa 3D nei loro workflow abituali, con l'obiettivo di ridurre i costi, aumentare la flessibilità e proteggere la loro catena di fornitura.
La linea di lavavetreria di Labconco incorpora innovazioni ingegneristiche all'avanguardia, tra cui componenti realizzati mediante produzione additiva. Un componente, l'attacco del sensore di riempimento, funge anche da protezione addizionale contro il traboccamento. Nell'approccio convenzionale, questo componente sarebbe stato prodotto in due pezzi separati attraverso lo stampaggio a iniezione e poi assemblato con un perno che tiene insieme le due parti.
Ma Tim Grove, ingegnere di prodotto presso Labconco, ha riconosciuto il potenziale di riduzione di costi e tempo che la stampa 3D SLS poteva offrire. Ispirandosi al design della cerniera utilizzato nel campione standard realizzato con la Nylon 12 Powder di Formlabs, Grove ha iniziato a ripensare il supporto del sensore di riempimento, con l'obiettivo di semplificare l'assemblaggio ed eliminare le spese associate al dover ordinare più strumenti.
Attraverso una collaborazione iterativa con Griffith, Grove ha lavorato a più versioni della parte per ottenere una funzionalità impeccabile e prestazioni senza compromessi.
"Il componente esce dalla stampante con la cerniera già funzionante e pronto all'uso. Vi sono quindi risparmi in termini di costi e flessibilità di produzione. La Nylon 12 Powder, usata su una stampante della serie Fuse, rappresenta per noi un buon polimero intermedio. Possiamo utilizzarla in svariate applicazioni e per noi è una scelta valida", sostiene Griffith.
Sensore di riempimento realizzato con la stampa SLS | Numero di componenti | Tempo di manodopera per l'assemblaggio (per 50 componenti) | Costo per parte finita (con manodopera) | |
---|---|---|---|---|
Stampaggio a iniezione | 3 | 1 ora | 4,45 € l'una + attrezzature | |
Stampa 3D SLS | 1 | 0 | 2,56 € l'una |
Ruota di soffiaggio realizzata con la stampa SLA: come risolvere l'obsolescenza di un prodotto acquistato da un fornitore esterno
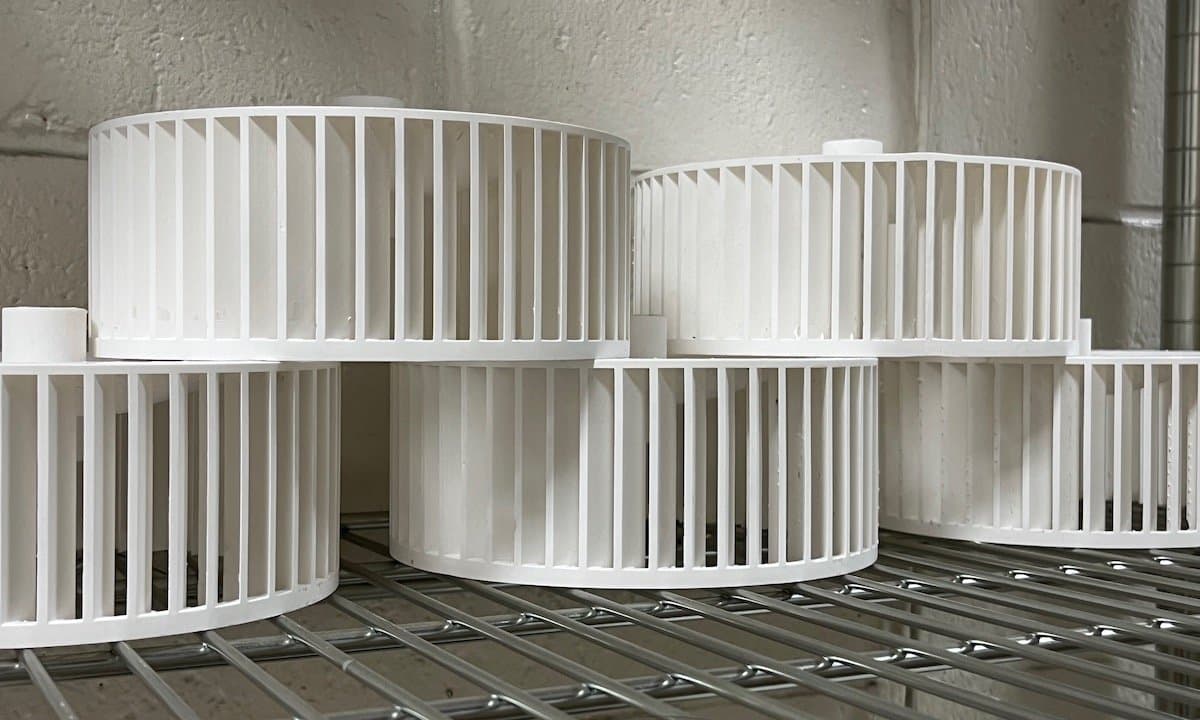
Questo componente, utilizzato nel prodotto di Labconco per l'analisi dei cereali con il metodo Kjeldahl, prima veniva acquistato da un fornitore esterno, finché quest'ultimo non ha deciso di renderlo obsoleto. Griffith ha eseguito l'ingegneria inversa del componente, quindi ha stampato la nuova versione con la Rigid 10K Resin sulla Form 3L ogni giorno per oltre un mese, ricostituendo le scorte di componenti sostitutivi e tutelandosi da futuri problemi della catena di fornitura.
Sull'apparecchio Kjeldahl di Labconco, utilizzato per l'analisi dei cereali, il team stava lavorando con un fornitore esterno che produceva uno strumento per un componente critico della ruota di soffiaggio. Poiché le quantità erano basse, il fornitore ha deciso di rendere obsoleta la parte una volta raggiunta la fine del ciclo di vita dell'attrezzatura.
A questo punto, Labconco avrebbe dovuto mettersi alla ricerca di un nuovo fornitore, attendere la progettazione e la produzione di un nuovo strumento e di un nuovo stampo, nonché sostenere un costo elevato per i materiali e la manodopera. "Abbiamo esaminato una decina di soluzioni diverse, ma nessuna era in grado di soddisfare le nostre specifiche, soprattutto per quanto riguardava la compatibilità chimica. Così ho preso una copia, ho eseguito l'ingegneria inversa del componente, l'ho ottimizzato e l'ho stampato con la Rigid 10K Resin", racconta Griffith. "Dopo aver effettuato dei test per verificarne la tenuta, abbiamo deciso che era la soluzione migliore."
La loro stampante SLA di grande formato, la Form 3L, è arrivata appena in tempo: hanno stampato la ruota di soffiaggio sottoposta a ingegneria inversa per 40 giorni di fila, con l'obiettivo di ricostituire le scorte della parte.
"La Rigid 10K Resin è stata la scelta ideale per diversi componenti. La compatibilità chimica era in linea con le nostre esigenze per quanto riguarda gli acidi, in questo caso particolare, l'acido solforico vaporizzato. Grazie al passaggio alla produzione additiva risparmiamo centinaia di ore che prima trascorrevamo a verificare fornitori e materiali che poi non si rivelavano validi. Da questo punto di vista, si tratta di una scelta vincente", afferma Griffith.
Ruota di soffiaggio realizzata con la stampa SLA | Costo |
---|---|
Originale stampata a iniezione | 178,77 € |
Riprogettata e stampata con la Rigid 10K Resin | 52,65 € |
Separatore della gabbia del cuscinetto realizzato con la stampa SLS: da 500 € a 20 €
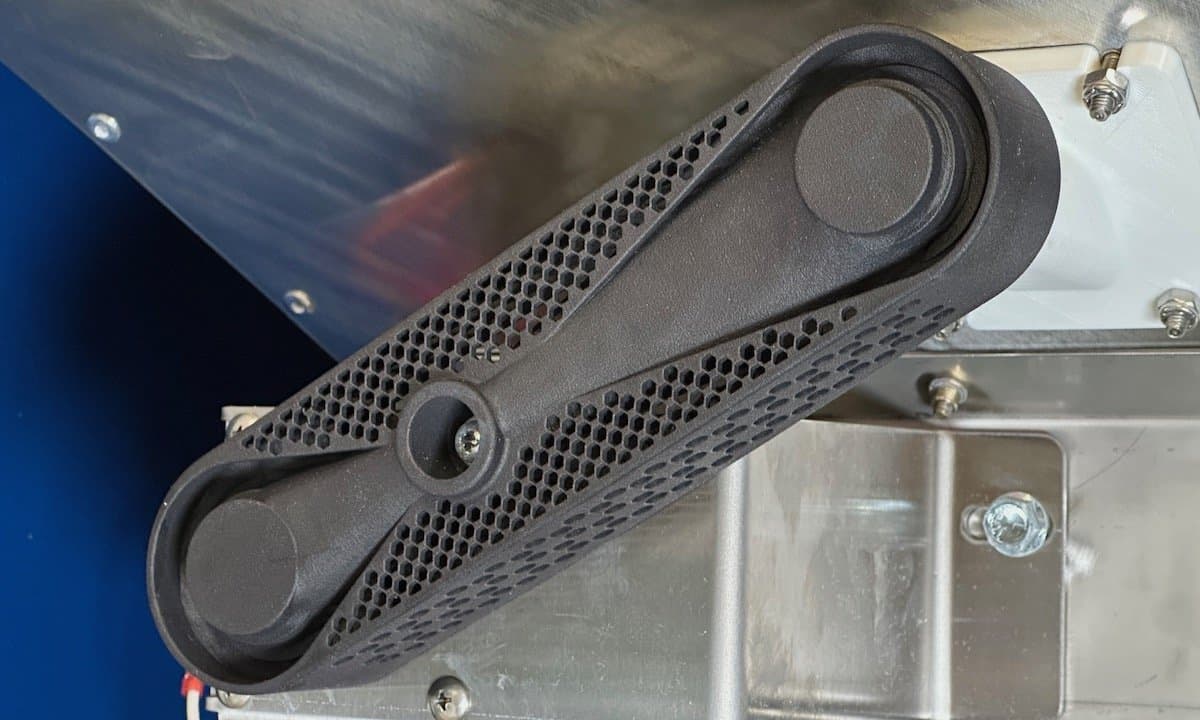
Griffith avrebbe potuto stampare questa parte come copia esatta del componente per il quale un'officina meccanica esterna aveva fatto un preventivo di circa 500 €. Ha deciso invece di applicare i principi appresi durante il programma di design e produzione additiva della Penn State e l'ha riprogettata per sfruttare le possibilità geometriche offerte dalla stampa 3D SLS. Il costo del nuovo componente è di circa 21 €; in questo modo Labconco ha risparmiato centinaia di euro e ridotto i tempi di consegna a meno di due giorni.
Anche se alcuni componenti sono relativamente semplici, i metodi di fabbricazione tradizionali possono comunque risultare costosi. Il preventivo di un'officina meccanica esterna per la realizzazione di una parte e di un separatore per distanziare due cuscinetti tra loro, impedendo che entrino in contatto, ammontava a circa 500 € l'uno. La parte era destinata a un nuovo prodotto e Labconco aveva già dimostrato il caso d'uso per il suo laboratorio di stampa 3D. Griffith ha subito iniziato a stampare il separatore sulla Fuse 1+ 30W, il che ha permesso di ridurre il costo a circa 45 €, più o meno un decimo di quanto sarebbe costato esternalizzare il lavoro.
Ma il processo di miglioramento non si è fermato qui. Griffith ha applicato i principi appresi nel corso di laurea del programma di design e produzione additiva della Penn State e ha riformulato il processo, trasformando una semplice operazione di sostituzione in una revisione completa nell'ottica dell'ottimizzazione.
"Ho potuto mettere in pratica quello che avevo imparato, ovvero come applicare gli aspetti opportunistici e restrittivi della produzione additiva. La domanda da porsi non è se sia possibile realizzare un componente con la produzione additiva, ma se sia opportuno farlo. In questo caso, avremmo potuto realizzare una semplice sostituzione, ma così facendo non avremmo sfruttato le opportunità offerte dalla produzione additiva. Grazie alle stampanti della serie Fuse, che offrono pochissimi vincoli geometrici, ho potuto sbizzarrirmi e provare cose nuove."
Brent Griffith, ingegnere di prodotto
Ha potuto ridurre l'utilizzo di materiale in tutta la parte grazie al design generativo, pur mantenendo le caratteristiche di sicurezza del separatore che garantivano la protezione degli operatori. Nel giro di un giorno ha ottenuto un design rivisto e ottimizzato, e Labconco ha dato il via alla stampa 3D SLS in-house delle parti a un costo di circa 20 € l'una.
"La stampa 3D ci offre enormi vantaggi in termini di possibilità geometriche. Se si alleggerisce una parte o si applicano diverse tecniche di design, è possibile combinare i componenti in modi mai visti prima. Possiamo implementare la produzione in-house e risparmiare molto denaro", dice Griffith.
Separatore della gabbia del cuscinetto realizzato con la stampa SLS: da 500 € a 20 € | Costo (inclusa manodopera) | Tempo di realizzazione |
---|---|---|
Lavorazione meccanica | 485,82 € | 2-3 settimane |
Sostituzione semplice con SLS | 43,50 € | 29 ore |
Ottimizzazione per la stampa SLS | 21,08 € | 28 ore |
Parti SLS per i test: riduzione del numero dei componenti e miglioramento della funzionalità
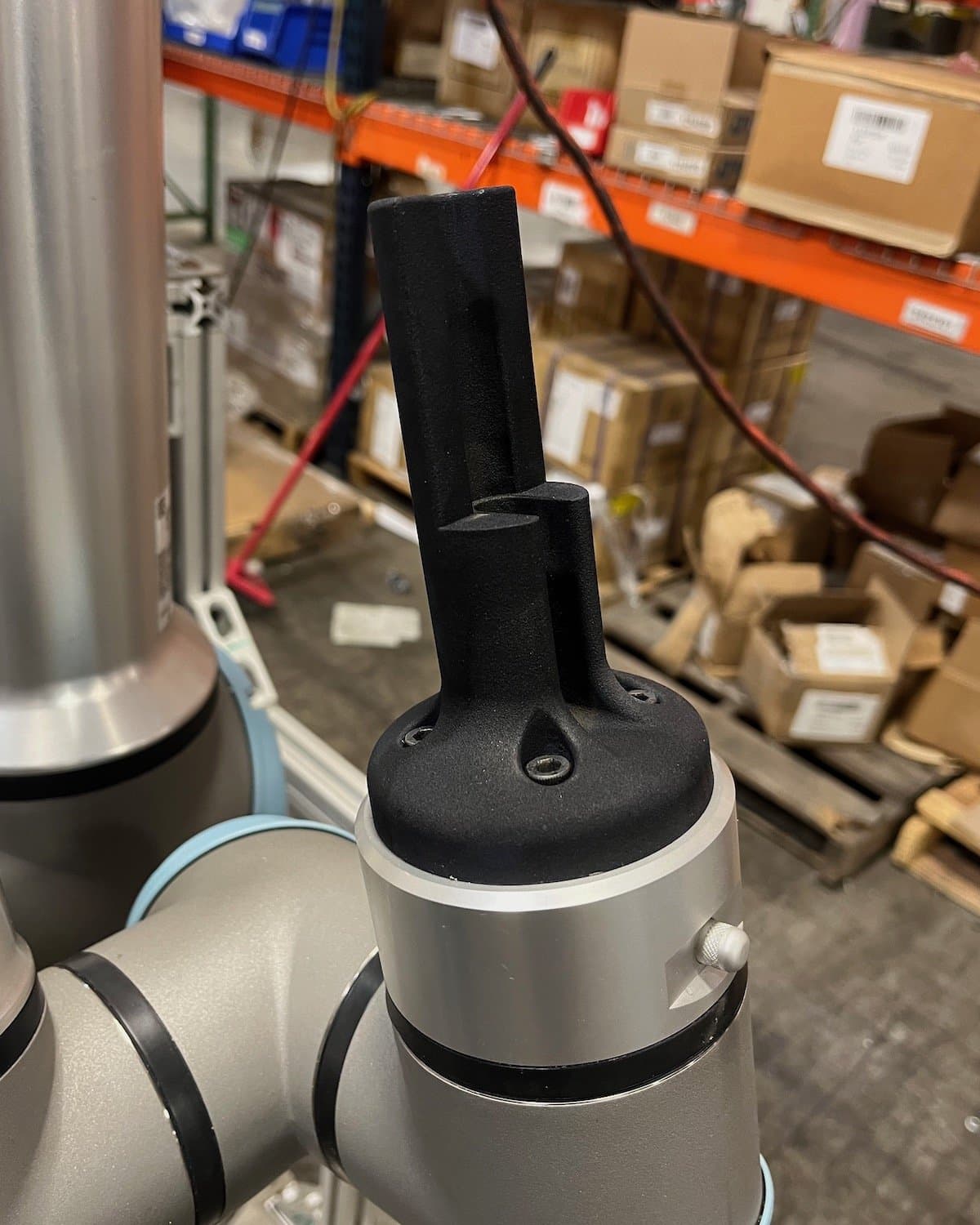
Per aiutare Labconco a passare in maniera fluida a un workflow ibrido che combina attività manuali e attuatori robotici, Griffith e il suo team hanno progettato attrezzature ed effettori personalizzati, che hanno poi stampato con la Nylon 12 Powder sulle stampanti della serie Fuse.
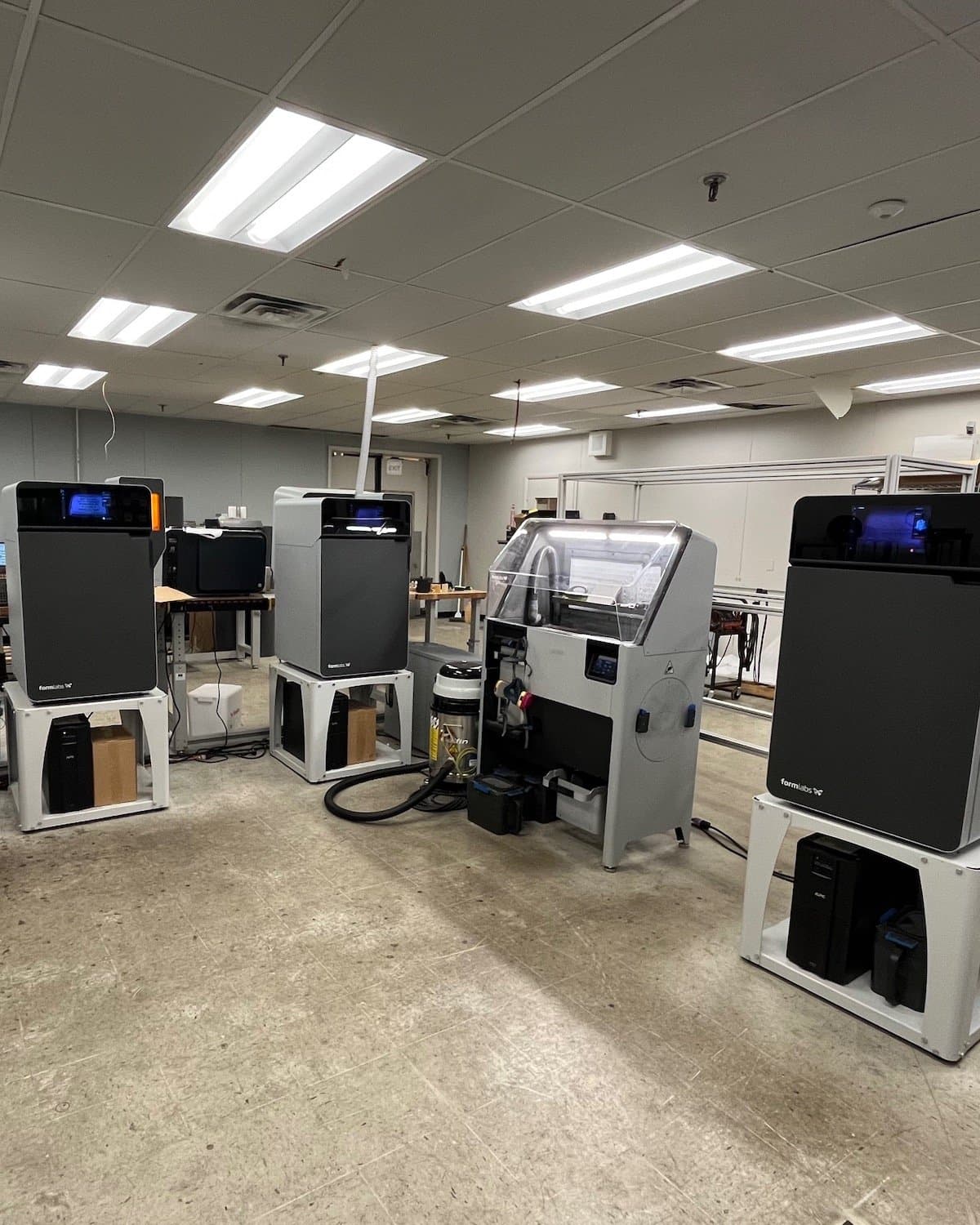
Le dimensioni compatte e il basso impatto energetico delle stampanti 3D SLS della serie Fuse hanno permesso a Griffith e al suo team di ampliare la gamma di applicazioni adatte a parti SLS resistenti e robuste. Ciò è stato possibile incrementando le operazioni di stampa SLS.
L'incessante ricerca dell'eccellenza da parte di Labconco si estende al collaudo dei componenti critici utilizzati in uno dei suoi prodotti di punta, gli armadietti di sicurezza biologica. Questi armadietti sono fondamentali per la salvaguardia del personale e dei prodotti manipolati al loro interno e si basano su specifici schemi di flusso d'aria e filtri HEPA. Per garantire il massimo livello di prestazioni, questi filtri sono sottoposti a rigorosi test e certificazioni prima di essere contrassegnati come completi.
In passato, questo processo di collaudo era affidato in larga misura a operatori umani, il che implicava possibili variabilità e limitazioni. Tuttavia, Labconco ha adottato un approccio trasformativo, sfruttando la potenza dei sistemi robotici per automatizzare la scansione di ogni filtro con una precisione impeccabile. Questo passaggio all'automazione ha reso necessario lo sviluppo di attrezzature ed effettori finali personalizzati per i bracci robotici incaricati di condurre i test. I metodi tradizionali di fabbricazione sarebbero stati estremamente costosi e avrebbero richiesto mesi. Ma grazie al basso volume di parti richieste, la stampa 3D sugli apparecchi della serie Fuse è stata una parte importante dell'approccio trasformativo.
Grazie alla produzione in-house delle parti SLS sulla Fuse 1+ 30W, Labconco ha raggiunto un notevole utilizzo giornaliero di questi componenti, aumentando l'accuratezza e l'affidabilità dei test sulla sicurezza dei prodotti. L'adozione della produzione additiva si è dimostrata decisiva in quanto non solo ha semplificato le operazioni, ma ha anche permesso a Labconco di garantire la sicurezza e le prestazioni senza compromessi dei suoi prodotti.
Componenti dell'effettore | Costo |
---|---|
Lavorazione meccanica | 508,32 € |
Stampa 3D SLS | 73,44 € |
Componente della cappa aspirante: produzione SLS con volumi medi per una maggiore agilità
Labconco è stata la prima azienda a commercializzare la produzione di cappe aspiranti, che ora è una delle divisioni di prodotto più importanti. Le cappe aspiranti sono indispensabili per le attività su larga scala in ambito chimico, farmaceutico o agricolo.
Un componente, un fermo meccanico dell'anta che impedisce agli utenti di aprire l'anta della cappa oltre un determinato punto (riducendo così i costi energetici), veniva precedentemente stampato a iniezione. La necessità di ordinare grandi volumi, prodotti su un unico strumento, limitava la capacità di Labconco di apportare modifiche o personalizzare gli ordini per i grandi clienti. Ma gli strumenti si usurano e talvolta i fornitori non sono del tutto affidabili nel sostituirli. Per ovviare ai problemi della catena di fornitura, Griffith ha iniziato a stampare questi fermi dell'anta sulla Fuse 1+ 30W e ora produce tra i 50 e i 100 componenti alla settimana con la Nylon 12 Powder.
"Se la parte viene prodotta mediante stampaggio, non è semplice effettuare modifiche. Non succede spesso, ma in passato la strada dello stampaggio a iniezione per alcuni componenti ci è costata cara, perché una volta ricevuti e messi in uso, hanno iniziato a rompersi o a non funzionare come previsto. Ora gli ingegneri sono consapevoli che, se si passa alla stampa 3D di alcune parti, è molto meno faticoso riprogettarle in caso di necessità, e il numero di opzioni per le modifiche che si possono apportare è maggiore. Non è sempre possibile quantificarne il valore in termini di denaro, e credo che la produzione additiva offra notevoli vantaggi intangibili che vengono spesso trascurati", afferma Griffith.
Un altro vantaggio derivante dall'integrazione in-house della tecnologia di stampa 3D è la fiducia che infonde ai membri più giovani del personale all'inizio della loro carriera. Poiché non è necessaria la perfezione assoluta per ordinare un nuovo strumento, sono più disposti a sperimentare o a proporre nuove idee. Gli ingegneri più giovani non hanno alle spalle un'esperienza ventennale che permette loro di guardare una parte e capire subito se funzionerà o meno. Avere la possibilità di stampare in 3D, sperimentare e provare uno o più aspetti è molto stimolante, e se il risultato non è quello desiderato, non devono preoccuparsene più di tanto", afferma Griffith. "Il nostro obiettivo è quello di lasciare loro la libertà di concentrarsi sulla ricerca della soluzione migliore e più creativa per qualsiasi problema e la stampa 3D è una parte importante di questa prospettiva".
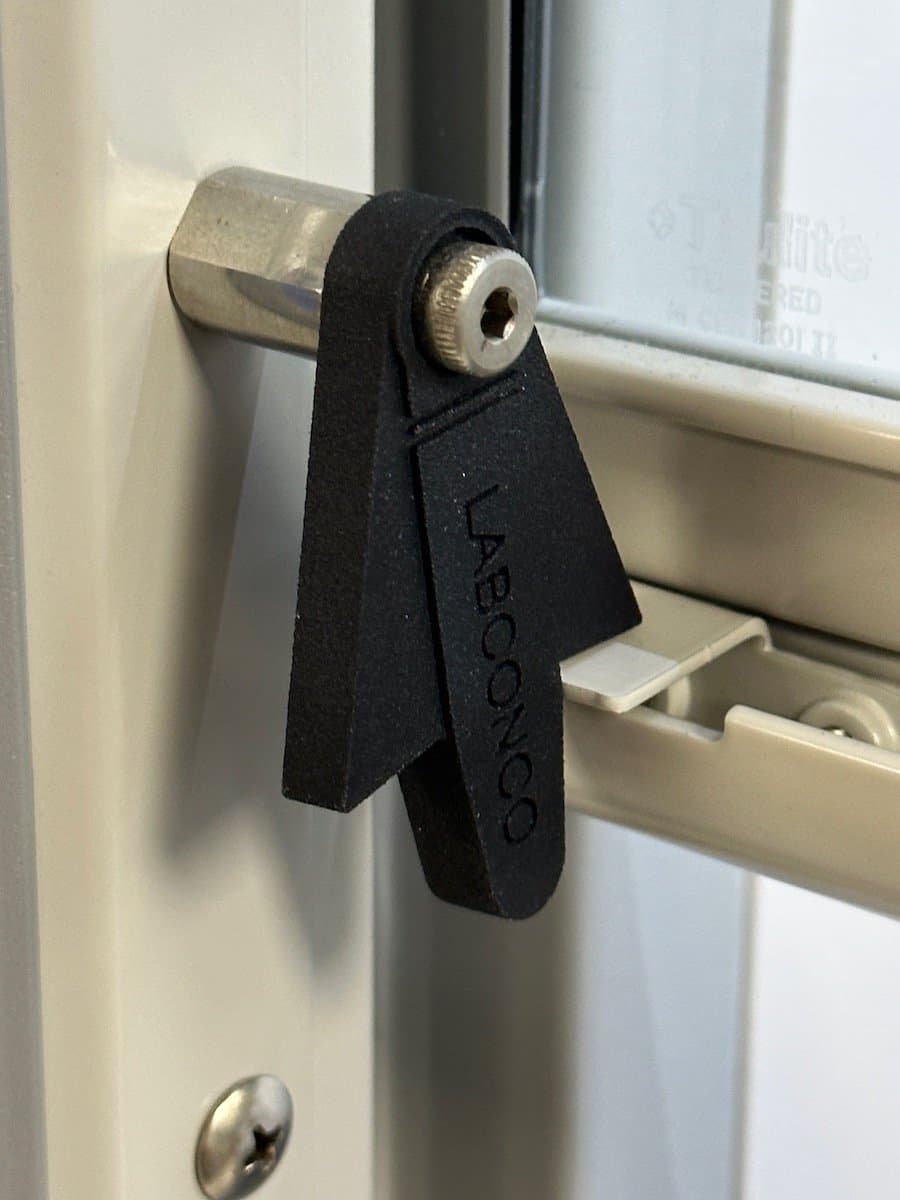
Griffith produce ogni settimana da 50 a 100 fermi dell'anta con la Nylon 12 Powder sulla Fuse 1+ 30W, evitando così i costi e i rischi associati ai workflow che prevedono l'utilizzo di attrezzature non modificabili.
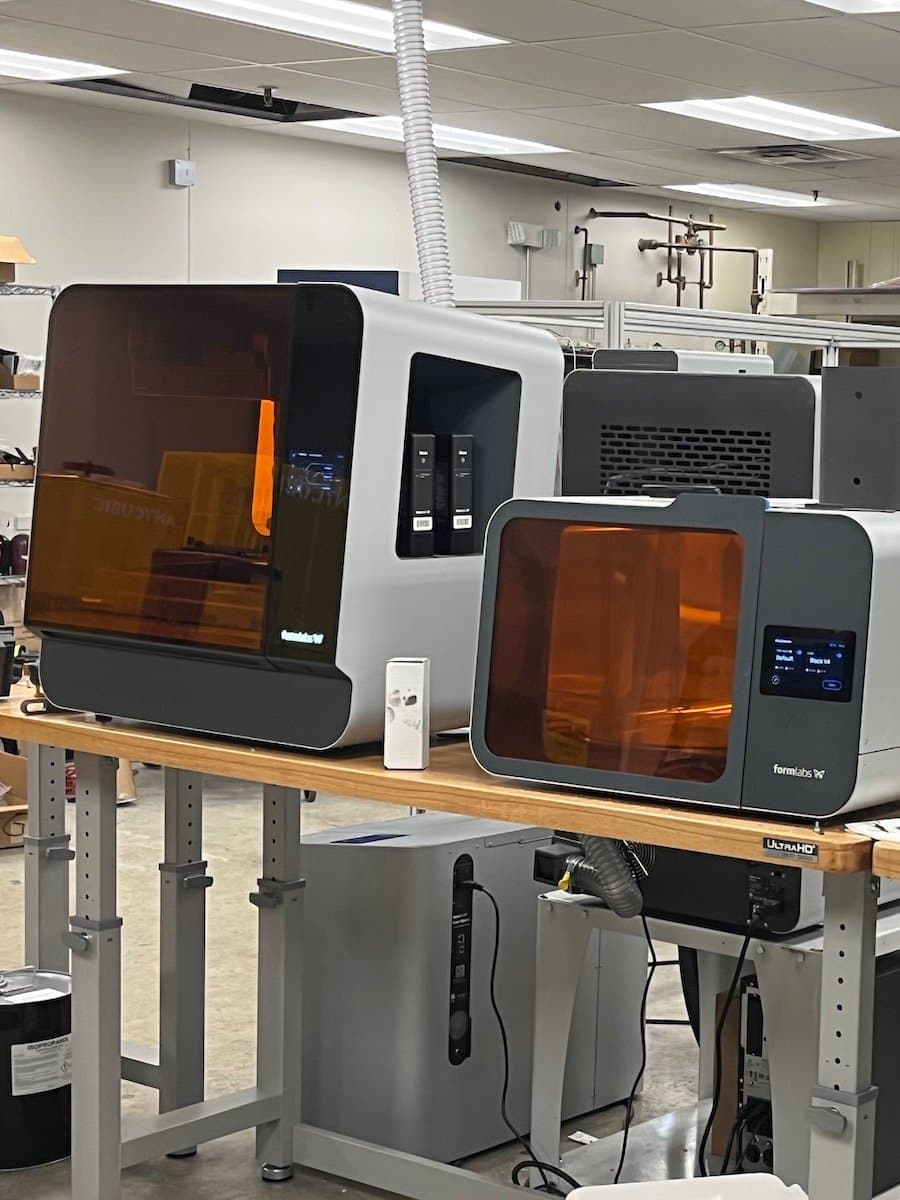
La facilità di utilizzo delle stampanti SLS e SLA (come la Form 3L e la Form Cure L qui mostrate) fa sì che i membri più giovani del team, che hanno appena iniziato la loro carriera, possano prendere confidenza con la nuova tecnologia e sperimentare nuove idee.
La Fuse Blast è l'ultima arrivata nell'ecosistema SLS di Labconco
Con volumi di produzione di oltre un centinaio di parti SLS alla settimana, le fasi di post-elaborazione manuali, come la sabbiatura e la pulizia, richiedevano ore di manodopera, togliendo tempo prezioso ad altre attività di design e ingegneria più redditizie. "L'azienda vuole che ci dedichiamo alla ricerca di nuove opportunità, alla riprogettazione dei componenti per migliorarli e al taglio dei costi, invece di rimanere qui a pulire manualmente tutte queste parti", afferma Griffith.
Oltre ad aver implementato un costoso sistema di sabbiatura automatizzato, Labconco ha anche introdotto la Fuse Blast per completare il suo ecosistema SLS Fuse. Dopo l'installazione, che ha richiesto una decina minuti, Griffith ha implementato la pulizia e la sabbiatura automatica di due camere di stampa complete della serie Fuse. "L'installazione è stata semplicissima. Le dimensioni sono quasi identiche a quelle del nostro sistema di sabbiatura manuale. Se hai spazio per un sistema di sabbiatura manuale, un normale requisito di ogni azienda che offre servizi di stampa SLS, allora avrai spazio anche per una Fuse Blast", afferma Griffith.
Parti con qualità e prestazioni migliorate
I team di Labconco che avevano richiesto le parti hanno notato subito una differenza nella finitura superficiale e nella qualità.
"La Fuse Blast ha fatto subito una grande differenza. Tutti gli ingegneri a cui distribuivo le parti in fase di prototipazione notavano che erano diverse, prima ancora che dicessi loro che avevamo automatizzato la post-elaborazione. Hanno notato subito che le parti avevano meno polvere residua, un aspetto migliore ed erano più lisce. La differenza nella qualità delle parti era notevole."
Brent Griffith, ingegnere di prodotto presso Labconco
Le superfici lisce e l'assenza di polvere residua hanno avuto un effetto inaspettato sulle prestazioni delle parti; infatti, gli apparecchi funzionavano in modo più efficiente con componenti realizzati tramite stampa SLS e puliti con la Fuse Blast. "Il grado di pulizia molto più elevato ci ha permesso di ottenere prestazioni leggermente migliori di alcuni componenti in produzione, specialmente nei cicli preparatori iniziali per uno dei nostri prodotti", afferma Griffith.
Le parti ottenute erano praticamente identiche a quelle pulite utilizzando l'altro costoso sistema di sabbiatura automatizzato dell'azienda. "Non noto differenze tra le due parti. [La Fuse Blast] ha senza dubbio superato qualsiasi aspettativa", dichiara Griffith.
Post-elaborazione più rapida, più tempo per l'ottimizzazione del design
L'automazione offerta dalla Fuse Blast non soltanto consente a Griffith e al suo team di eliminare il tempo impiegato per la sabbiatura manuale delle parti, ma va oltre, riducendo anche il tempo di utilizzo della Fuse Sift. In precedenza, un maggior tempo di utilizzo della Fuse Sift ci permetteva di accorciare i tempi della sabbiatura manuale. Oggi, invece, la Fuse Blast esegue cicli automatizzati restituendo parti pulite, anche se inizialmente le parti sono ancora ricoperte di polvere. "Ora presto molta meno attenzione alla quantità di polvere che viene rimossa con la[Fuse Sift], perché so bene di cosa è capace la Fuse Blast. La pulizia accurata delle parti nella Fuse Sift non si traduce più in un risparmio di tempo. Qualsiasi recupero di polvere, anche piccolo, che avremmo ottenuto con una maggiore accuratezza nella Sift Fuse non è giustificato dal costo aggiuntivo della manodopera per ottenerlo", dice Griffith.
Nel caso di una parte per cui era previsto un tasso di produzione costante di circa 50 unità alla settimana, il team di Griffith eseguiva la sabbiatura manuale e puliva tre fori per ciascuna parte servendosi di uno scovolino. Grazie alla Fuse Blast, ora può impostare un ciclo automatizzato e dedicarsi ad altre attività, per poi recuperare parti perfettamente pulite dopo 20-30 minuti. "La Fuse Blast è un'unità fenomenale. Riesce perfettamente a rimuovere i residui dai fori, il che per noi è un enorme vantaggio in termini di tempo risparmiato", afferma Griffith.
Incremento delle operazioni di stampa 3D
Griffith e il suo collega si sono avvicinati alla stampa 3D in modo sistematico: il loro controllo iniziale ha dimostrato l'utilità dei primi sei apparecchi che hanno introdotto. Poiché con il tempo hanno trovato nuovi vantaggi in termini di risparmi sui costi, riduzione di manodopera e miglioramento del design per l'ampio catalogo di componenti dell'azienda, il loro obiettivo è ampliare le capacità di stampa 3D.
"Ogni volta che mi trovo davanti una parte, la prima domanda che mi pongo è se sia possibile migliorarla con la produzione additiva. Credo che la ricerca di queste opportunità sia stata l'ambito in cui siamo riusciti a eccellere e a risparmiare di più, o a tagliare buona parte dei costi di molti componenti", afferma Griffith.
I vantaggi sono evidenti per l'intera azienda: i team che lavorano con clienti con applicazioni specifiche o di nicchia possono proporre con sicurezza soluzioni economicamente vantaggiose grazie alla potenza della produzione in-house a basso volume. "Spesso possiamo soddisfare le richieste in modo conveniente anche per clienti che hanno bisogno solo di cinque, dieci o cinquanta parti personalizzate. Siamo in grado di rispondere rapidamente alle esigenze del mercato", afferma Griffith.
Da quel primo esempio che ha fatto calare il silenzio nella stanza, Griffith ha costruito un business case per produttori di tutte le dimensioni: la produzione in-house con la stampa 3D SLA e SLS può consentire nuove applicazioni e migliorare il successo dell'azienda, nonché ottimizzare le prestazioni dei prodotti, proteggere dai problemi della catena di fornitura e ridurre i costi.
Se vuoi scoprire di più su come introdurre in-house la stampa SLS e SLA, prenota una consulenza con il nostro team vendite dedicato alla produzione.