Il settore automobilistico sta attraversando una fase di rapida trasformazione: la sensibilità della clientela e gli obblighi normativi esercitano una crescente pressione per l'abbandono dei combustibili fossili e l'adozione di veicoli elettrici. Ford sta trainando questo processo, proprio come fece con la produzione della Model T e l'introduzione della catena di montaggio oltre 100 anni fa, e prevede di vendere esclusivamente veicoli elettrici in Europa entro il 2030.
Ford Motor Company è la sesta casa automobilistica al mondo, produce oltre 4 milioni di veicoli all'anno e conta oltre 175 000 dipendenti in tutto il mondo. Il cuore delle attività europee di Ford si trova a Colonia, nella sede fondata nel 1930 e nota soprattutto per l'assemblaggio della Ford Fiesta.
Situato poco distante dalla fabbrica, lo stabilimento di Merkenich funge da centro di sviluppo e si occupa dell'intera progettazione di tutti i veicoli per il trasporto di persone destinati al mercato europeo, tra cui modelli di successo come la Fiesta, la Focus, la Kuga e ora l'Explorer, la prima automobile completamente elettrica per il mercato europeo, che è recentemente entrata nella fase di produzione in serie nell'impianto di assemblaggio di Colonia. Il team segue anche lo sviluppo dei veicoli commerciali, collaborando con il centro tecnico Ford di Dunton, nel Regno Unito.
Ma come fa Ford a stare al passo con l'intensa concorrenza e con cicli di sviluppo sempre più brevi? Continua a leggere per scoprire come funziona lo stabilimento di Merkenich, che è determinante per la creazione di prototipi rapidi per lo sviluppo dei prodotti.
Strumenti per la produzione di prototipi a grandezza naturale per il settore automobilistico
"La prototipazione è molto importante nel processo di sviluppo. Offre al team di ingegneria la possibilità di controllare il design. Dover rilavorare uno strumento per lo stampaggio a iniezione o per la produzione è un'operazione è molto costosa, richiede molto tempo e, nel peggiore dei casi, comporta tempi di inattività. Questa situazione può essere evitata ricorrendo alla prototipazione e applicando tutte le tecnologie disponibili", ha dichiarato Sandro Piroddi, supervisore del centro di tecnologia rapida di Ford a Merkenich.
La produzione di prototipi di veicoli a grandezza naturale richiede un'ampia gamma di strumenti. Il centro di tecnologia rapida è una struttura molto grande, dotata dei più recenti metodi di fabbricazione: dispone di apparecchi per lo stampaggio a iniezione, strumenti per la formatura e un'ampia gamma di strumenti per la produzione sottrattiva, come ad esempio fresatrici adattabili anche ai pannelli più grandi del telaio.
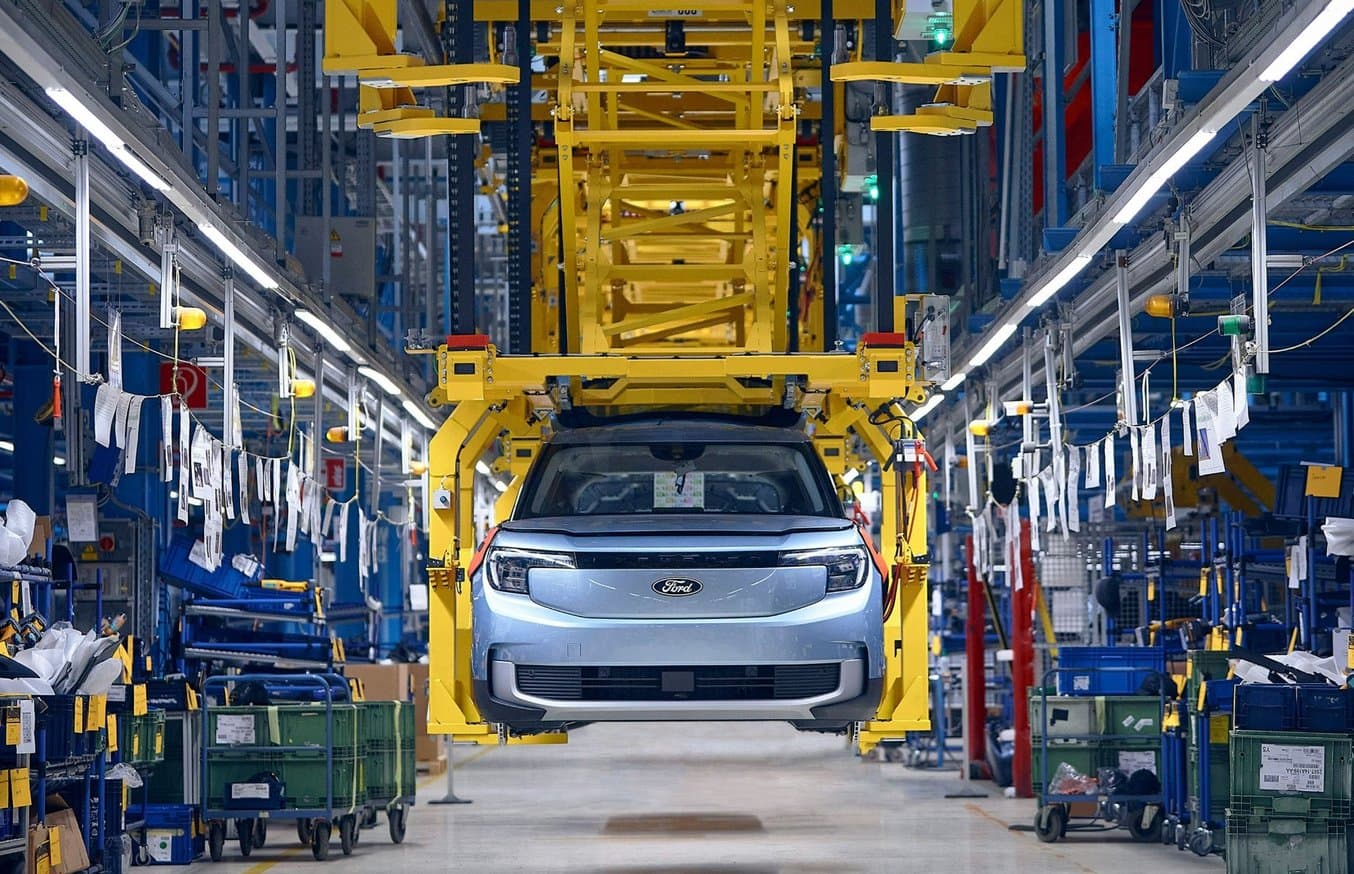
L'auto completamente elettrica Ford Explorer è recentemente entrata nella fase di produzione in serie nell'impianto di assemblaggio di Colonia.
Naturalmente, l'elenco non sarebbe completo senza la produzione additiva. Lo stabilimento di Merkenich è stato il primo in Europa a utilizzare una stampante 3D stereolitografica (SLA), nel 1994. Da allora ha ampliato la sua flotta con diverse stampanti 3D a modellazione a deposizione fusa (FDM), SLA e a sinterizzazione laser selettiva (SLS) per polimeri, oltre che per la stampa 3D in metallo.
Nonostante i primi modelli concettuali vengano ancora sviluppati in argilla, man mano che lo sviluppo del prodotto passa alle fasi successive e i singoli componenti si avvicinano alla forma finale, è sempre più importante poter testare forma e funzione con materiali e processi che si avvicinino il più possibile a quelli di produzione.
"La produzione additiva è molto importante nel processo di sviluppo. Consente di produrre parti in modo molto rapido ed efficiente e di ridurre i costi. Inoltre, è possibile intervenire in tempi brevi. Se consideriamo la tendenza verso l'elettrificazione, i tempi di sviluppo si stanno accorciando: il tempo a disposizione per sviluppare e verificare le parti dei veicoli è sempre più breve, per cui è molto importante utilizzare questa tecnologia nel processo di sviluppo. Ci rende molto più competitivi rispetto alla concorrenza."
Sandro Piroddi, supervisore del centro di tecnologia rapida di Ford
A causa dei tempi di sviluppo sempre più ristretti, il centro di tecnologia rapida è alla costante ricerca di innovazioni nel campo della produzione additiva che consentano di accelerare la realizzazione dei componenti.
Sviluppo di prototipi di design con la stampa 3D SLA
Le stampanti 3D SLA sono utilizzate principalmente in officina per i prototipi di design che richiedono una buona finitura superficiale e devono essere prodotti velocemente per iterazioni rapide. La prima stampante Formlabs utilizzata nello stabilimento di Merkenich è stata una Form 2, ma ben presto la flotta è stata ampliata con diverse unità desktop e una stampante 3D SLA di grande formato Form 3L. Inoltre, Ford è stata una delle prime aziende ad acquistare la Form 4, l'ultima stampante 3D MSLA di Formlabs.
"Credo che la Form 4 sia il miglior apparecchio che abbia mai utilizzato in termini di velocità. È davvero un'evoluzione notevole rispetto ai modelli precedenti. È più intuitiva, quindi il personale della nostra officina può imparare a usarla e ottenere parti di buona qualità con estrema semplicità", ha affermato Bruno Alves, esperto di produzione additiva e specialista di attrezzature presso Ford.
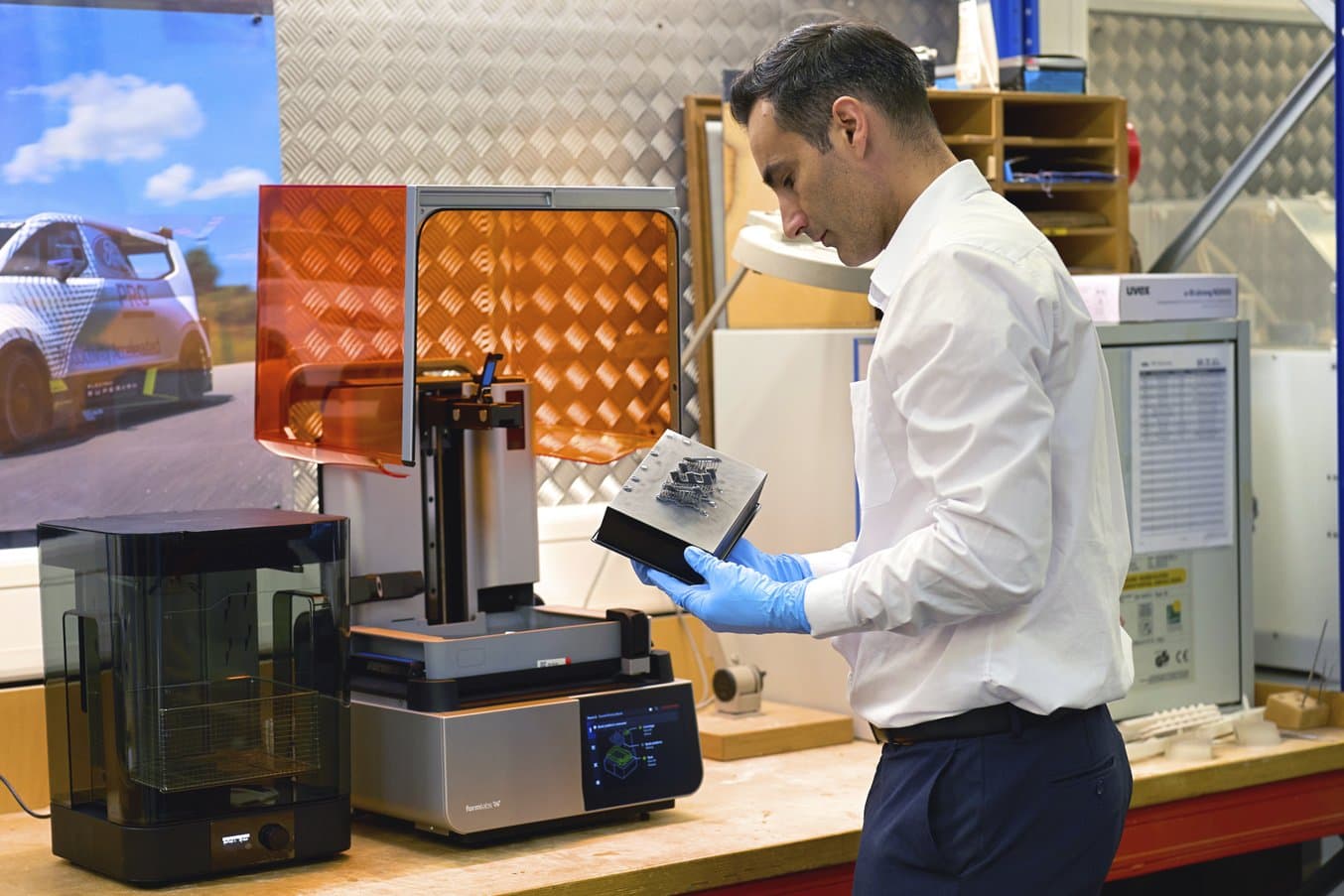
Lo stabilimento di Merkenich è stato uno dei tester beta della nuova Form 4. La velocità straordinaria della nuova stampante consentirà all'officina di realizzare i nuovi prototipi in poche ore.
"La Form 4 è davvero rivoluzionaria. La sua velocità di stampa cambierà il nostro workflow. Possiamo realizzare più parti e il rendimento è più elevato. Grazie alla Form 4, riusciamo a essere molto più flessibili e a soddisfare anche le richieste urgenti."
Sandro Piroddi, supervisore del centro di tecnologia rapida di Ford
"Alcuni anni fa occorrevano giorni per stampare le parti; oggi riusciamo a farlo in pochi minuti. In questo modo, i team di ingegneria non hanno paura di creare nuovi design o nuove iterazioni, perché sanno di poter realizzare le parti in pochissimo tempo", ha aggiunto Alves.
La velocità di stampa consente al team del centro di tecnologia rapida di soddisfare un maggior numero di richieste in meno di 24 ore, anche quelle provenienti dal Regno Unito, con la possibilità di inviare rapidamente le parti tramite una spedizione notturna.
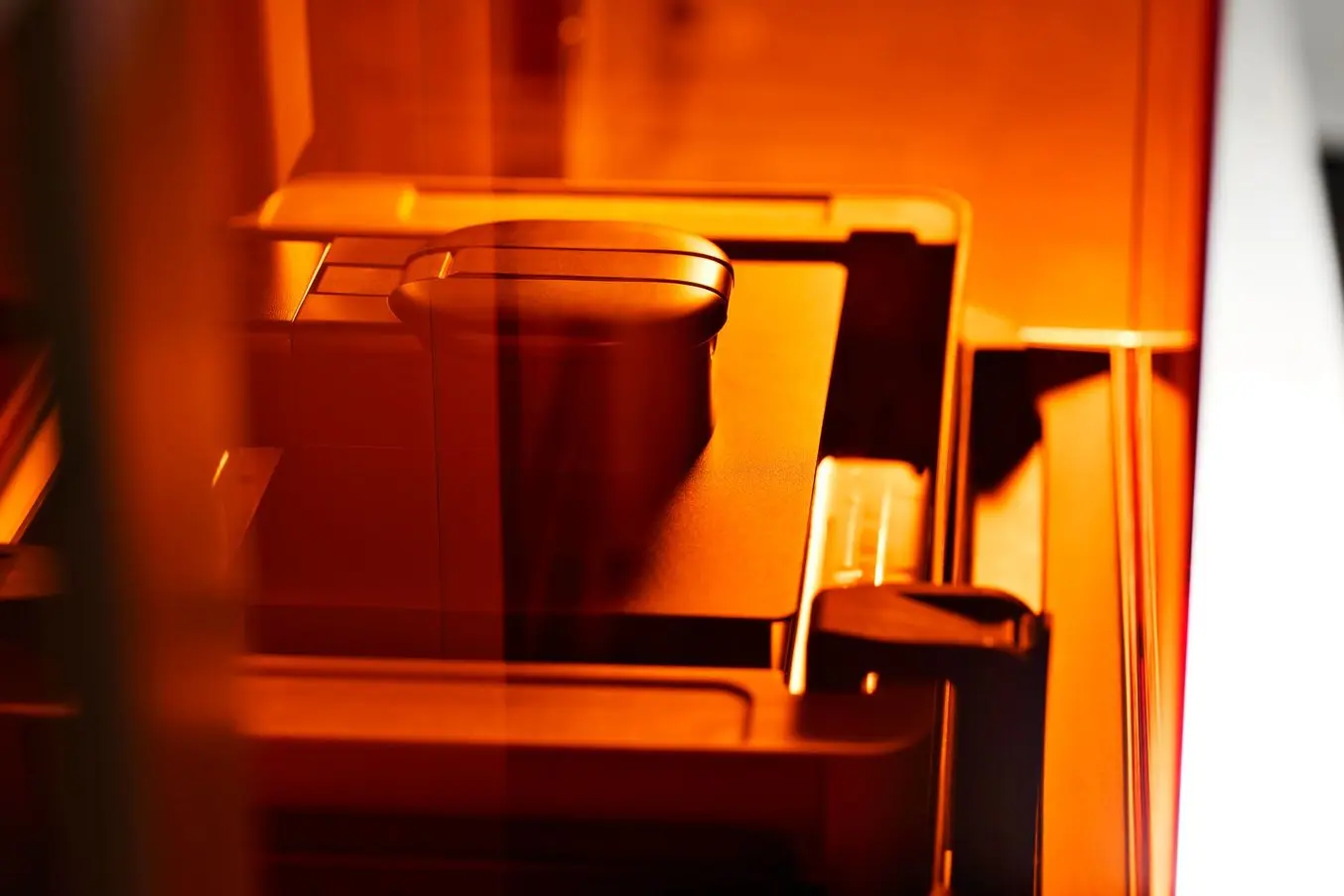
Dimostrazione di prodotto: Form 4
Scopri come la Form 4 può aiutarti a raggiungere nuovi livelli di produttività e innovazione grazie alla sua velocità, accuratezza e affidabilità senza pari.
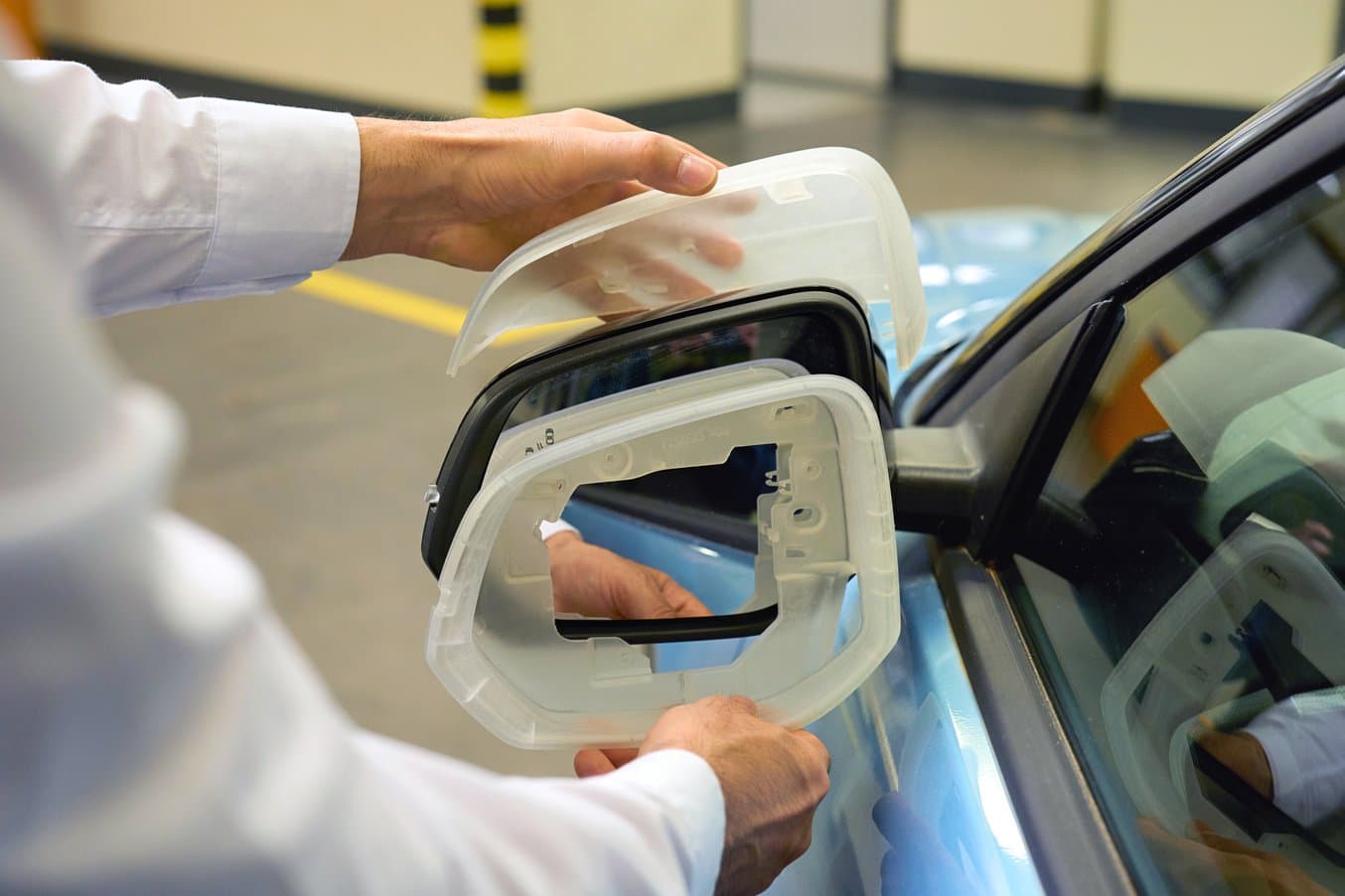
Il team ha utilizzato la stampa 3D SLA per realizzare i prototipi di molte parti della nuova Explorer, come ad esempio l'assemblaggio dello specchietto retrovisore.
Il team ha utilizzato la stampa 3D SLA per convalidare il design di molte parti esterne e interne della nuova Explorer.
"La Form 3L ci consente di stampare parti di grandi dimensioni, come le parti esterne della carrozzeria del veicolo. Abbiamo stampato questa calotta dello specchietto retrovisore per convalidare un design. La stampa 3D è adatta a questa applicazione, perché è veloce e ci permette di ottenere un'ottima qualità se paragonata alla produzione di massa", ha affermato Alves.
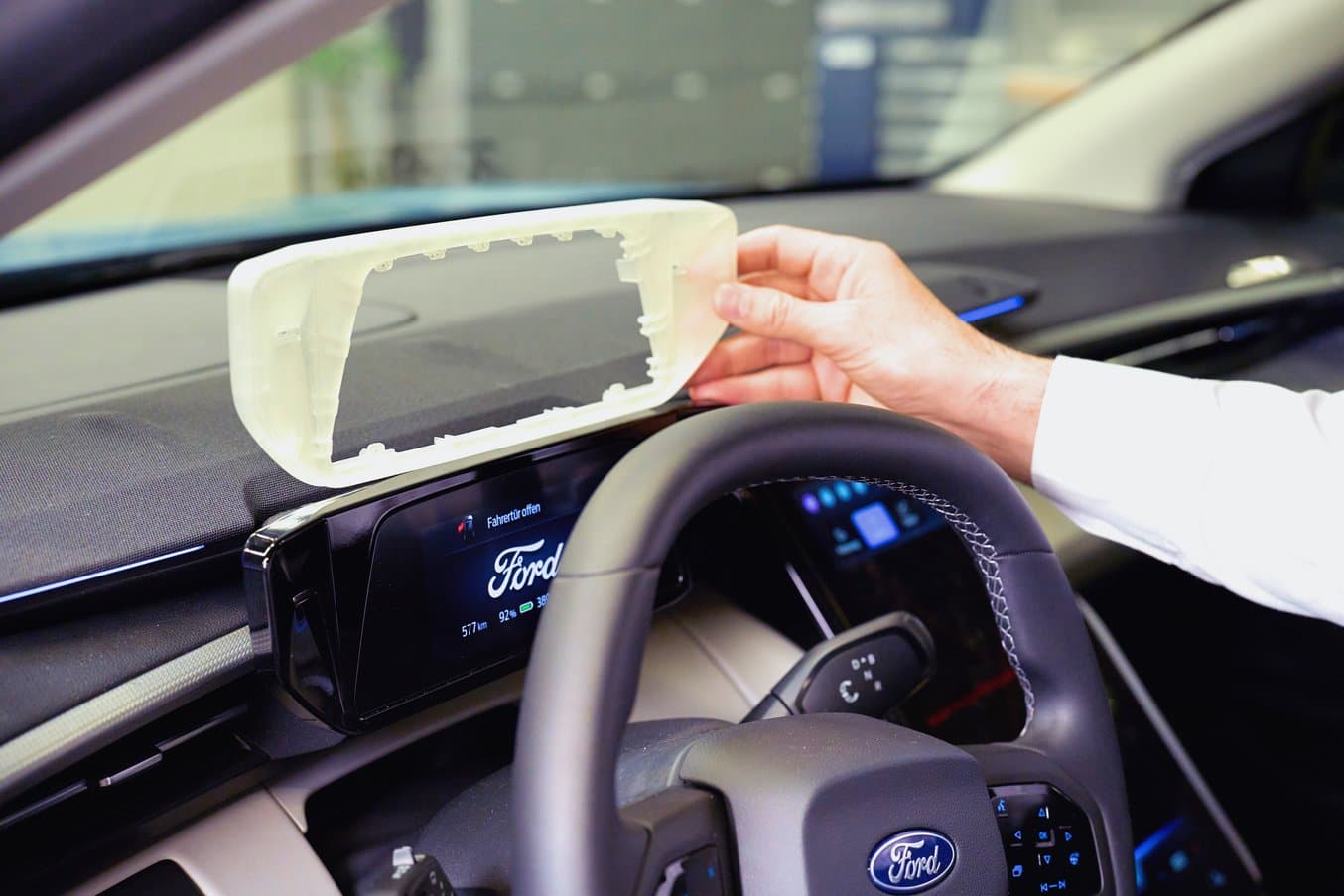
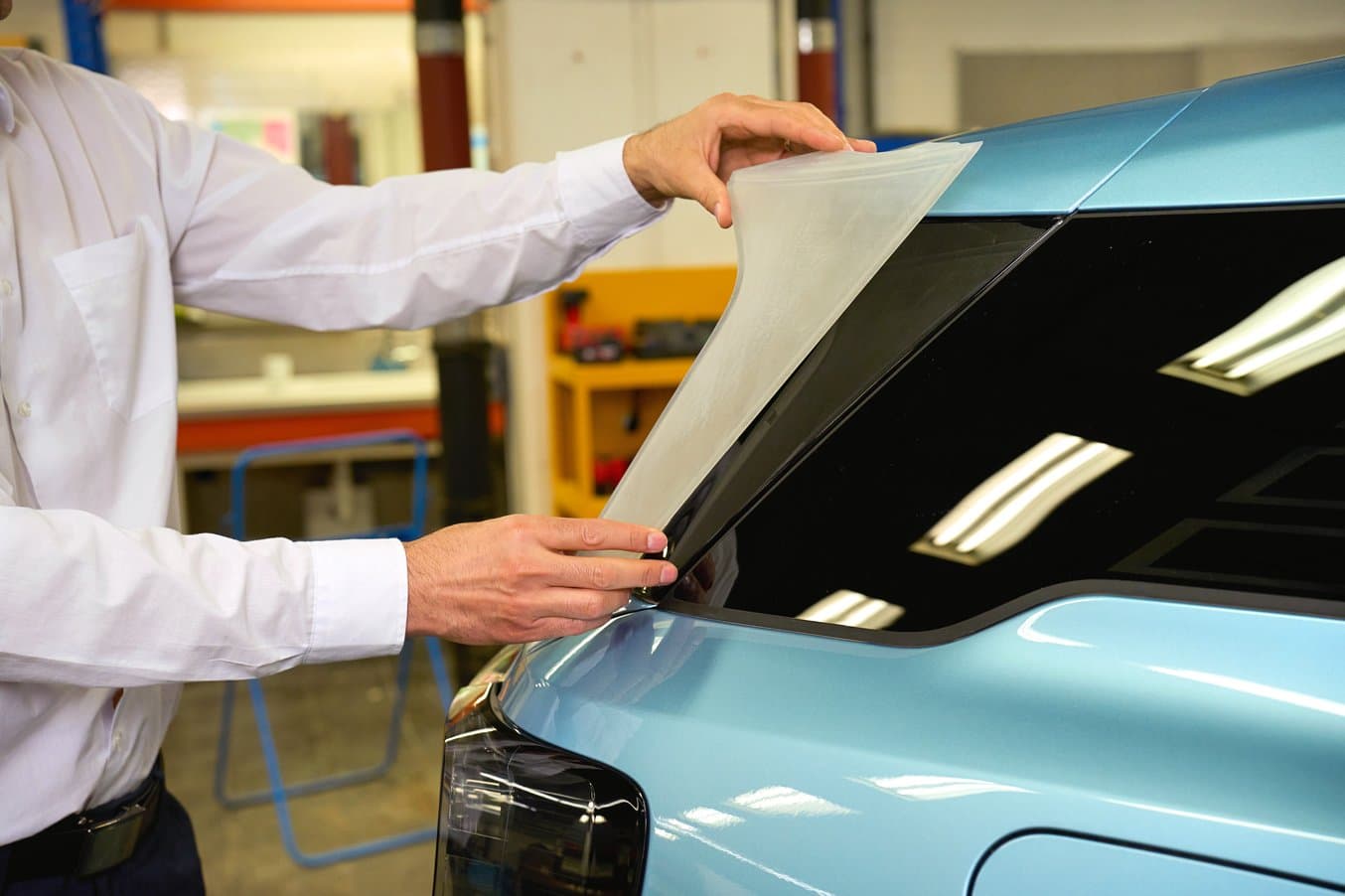
L'ampio volume di stampa della Form 3L consente al team di produrre prototipi di grandi dimensioni in un unico pezzo.
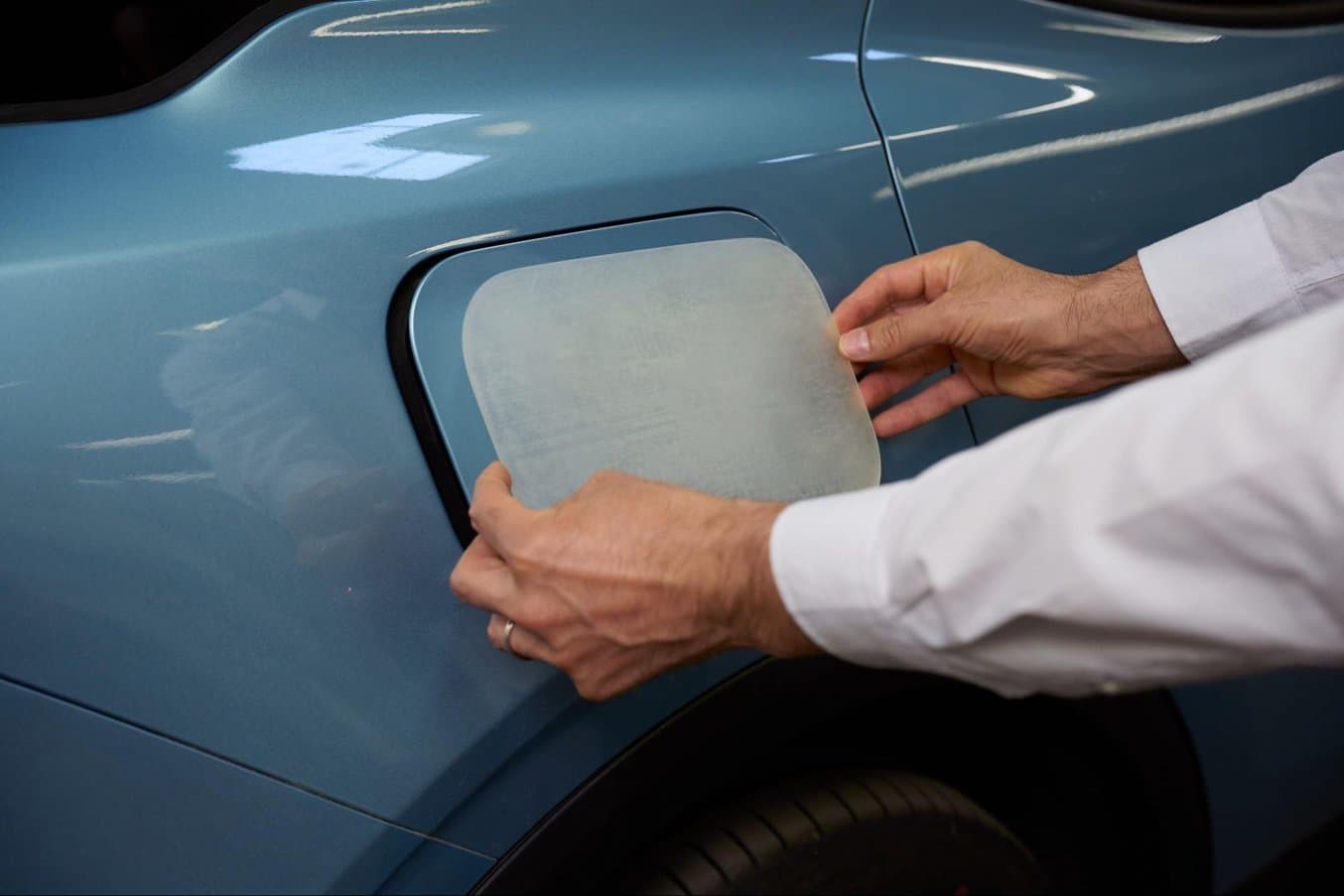
Queste parti sono state stampate in Clear Resin e sabbiate nella Fuse Blast.
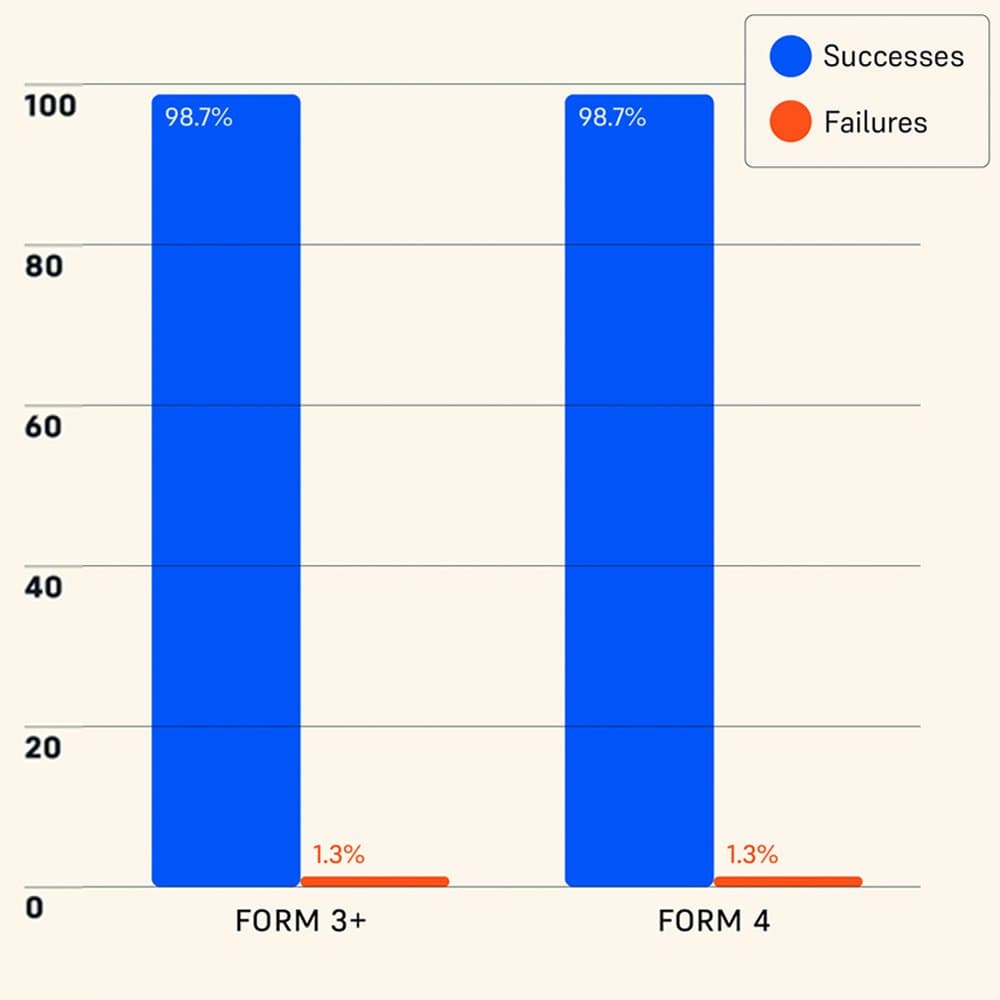
Affidabilità testata in modo indipendente della Form 4 e di altre stampanti 3D a resina
Un'azienda indipendente leader mondiale dei test sui prodotti ha misurato per la Form 4 di Formlabs un tasso di riuscita della stampa del 98,7%. Per leggere una descrizione dettagliata della metodologia del test e i risultati completi, scarica il nostro whitepaper.
Test di parti meccaniche con la stampa 3D SLS
L'officina gestisce anche numerose stampanti 3D SLS, che vengono utilizzate per testare le parti meccaniche.
"Cerchiamo sempre di testare e convalidare materiali più simili a quelli utilizzati nella produzione di massa. La Fuse 1+ 30W utilizza il [nylon] PA-12, che si avvicina molto a quello delle parti stampate a iniezione per la produzione di massa", ha dichiarato Alves.
Sebbene il team disponga di stampanti 3D SLS di grande formato in grado di stampare anche pannelli per carrozzeria di grandi dimensioni, preferisce utilizzare la Fuse 1+ 30W per le parti che si adattano al suo volume di stampa.
"La Fuse 1+ 30W ha una velocità che supera l'offerta della concorrenza. Oltretutto, questo apparecchio è molto semplice da usare per il nostro personale. In fin dei conti, ciò che ci interessa di più è poter produrre le parti velocemente e facilmente."
Bruno Alves, esperto di produzione additiva e specialista di attrezzature presso Ford
Il team è stato anche uno dei tester beta della soluzione di pulizia e lucidatura automatizzata Fuse Blast, che completa il workflow SLS e semplifica la post-elaborazione.
"La Fuse Blast accelera moltissimo il nostro processo, perché ora non è necessario pulire manualmente le parti. Basta inserirle nel cestello e avviare l'apparecchio. In passato, si trattava di un processo manuale che richiedeva molto tempo. In questo modo, il personale può dedicarsi ad altre attività e noi velocizziamo il processo", ha affermato Alves.
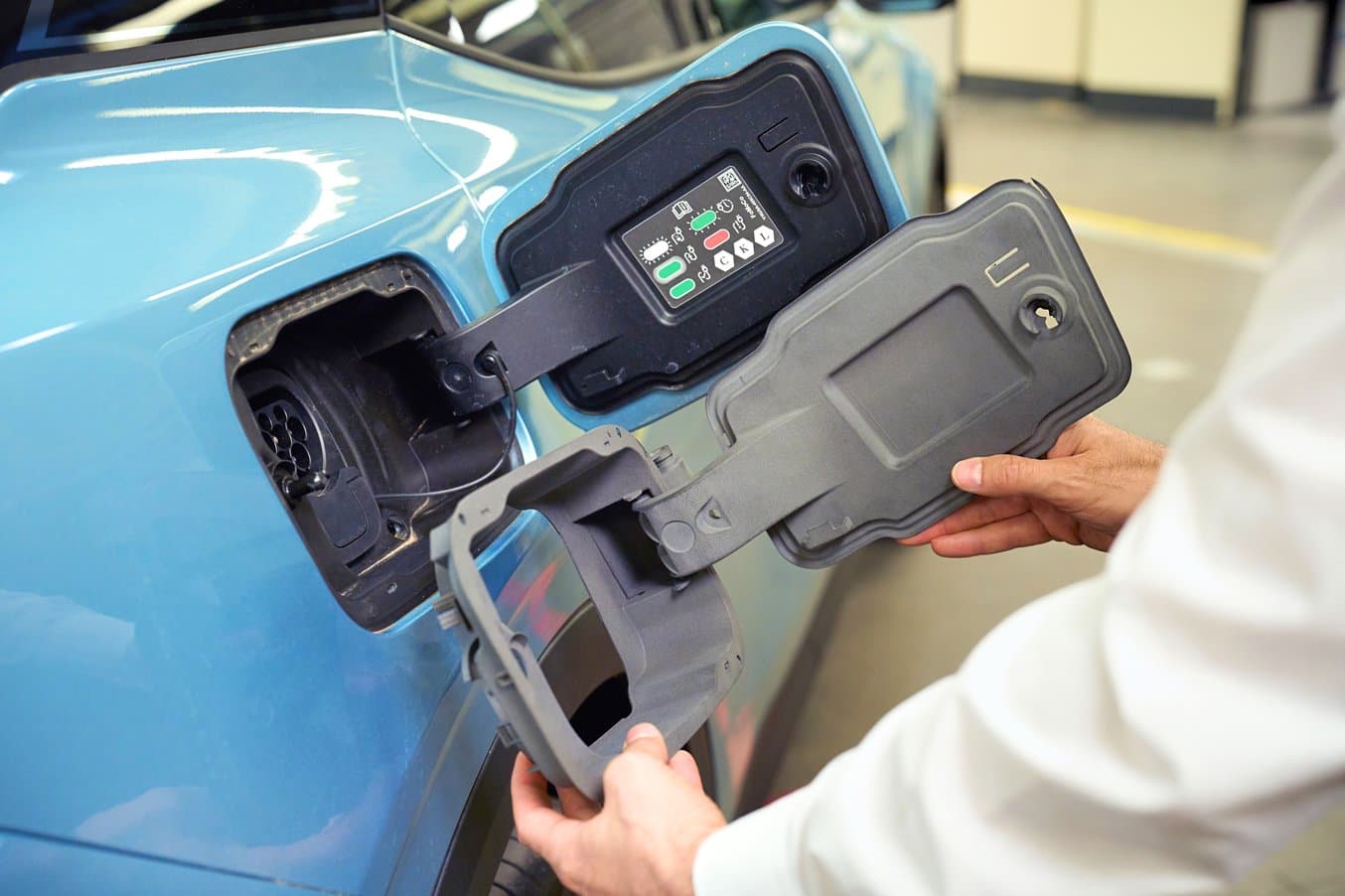
Il vano di ricarica è un assemblaggio complesso per il quale sarebbe stato impossibile realizzare un prototipo con qualsiasi altro metodo.
La natura autoportante della stampa 3D SLS semplifica la produzione di design complessi. Il team ha utilizzato la Fuse 1+ 30W per produrre diverse parti meccaniche e assemblaggi per la nuova Explore.
"Per il coperchio del vano di ricarica era importante usare la stampa SLS, perché avevamo bisogno di una parte funzionale che ci permettesse di testare i meccanismi. È un design molto complesso che non siamo in grado di produrre in altro modo. Non possiamo fresare questa parte, né utilizzare lo stampaggio a iniezione per produrre solo alcuni campioni. Pertanto, il metodo migliore è stampare con un materiale che è possibile testare fisicamente", ha affermato Alves.
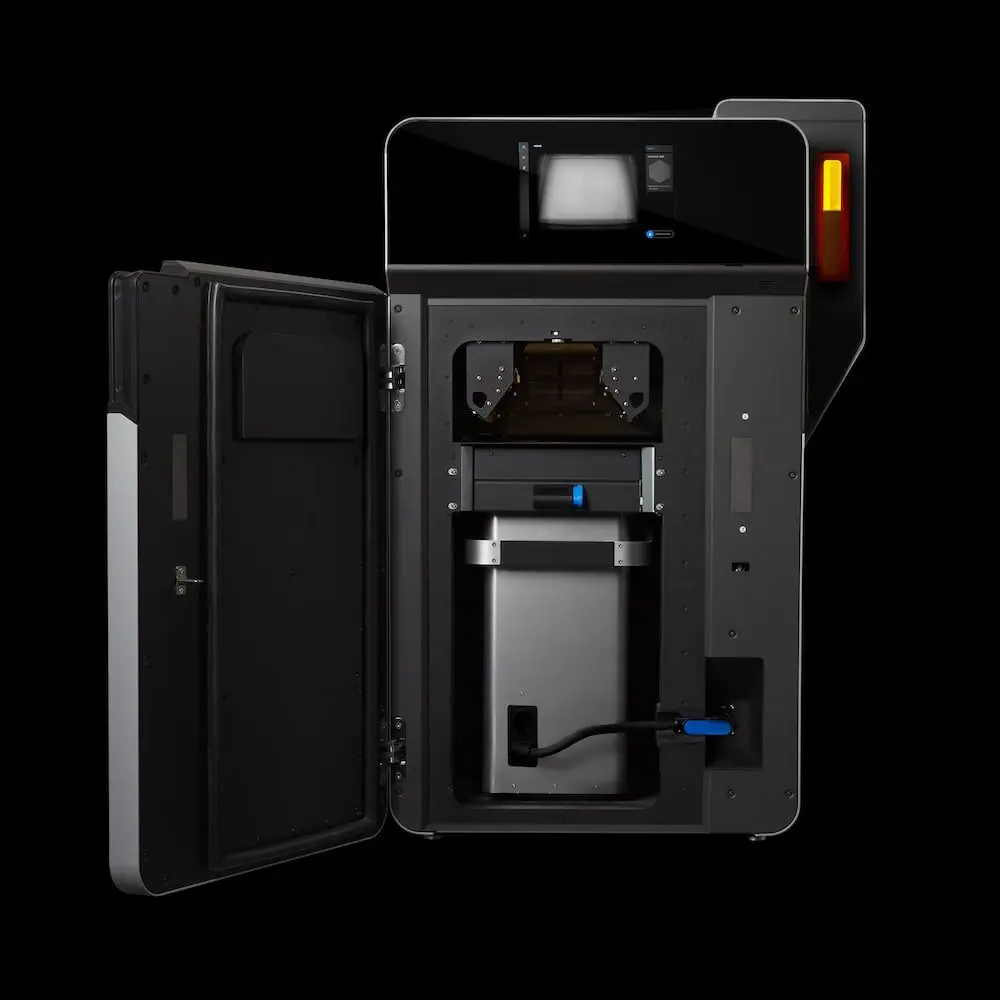
Produzione rapida di parti SLS ad alte prestazioni con la nuova Fuse 1+ 30W
Guarda la nostra dimostrazione di prodotto per un'introduzione alla Fuse 1+ 30W e alla stampa 3D SLS svolta dagli esperti di Formlabs.
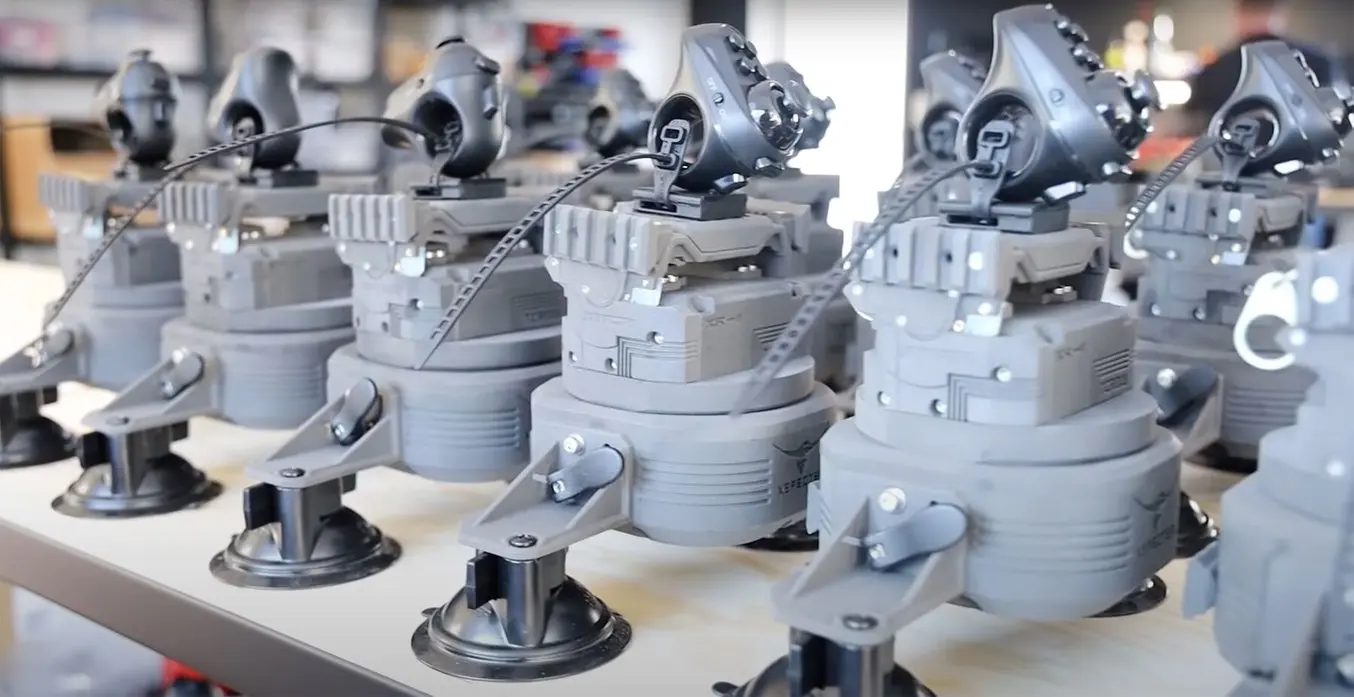
Produzione SLS per utilizzo finale
La stampa 3D per utilizzo finale non è solamente possibile, ma ora, grazie all'ecosistema SLS Fuse, è anche più economica, agile e scalabile che mai. Visita la nostra pagina dedicata alla produzione SLS per confrontare i metodi, scoprire di più sui prezzi all'ingrosso della polvere e vedere come 15 aziende utilizzano già la serie Fuse.
Stampaggio a iniezione in-house con inserti per stampi realizzati in 3D
Avere a disposizione diverse tecnologie in-house consente al centro di tecnologia rapida di creare workflow ibridi, ad esempio combinando processi di produzione tradizionali con la creazione rapida di attrezzature stampate in 3D.
A seconda dell'applicazione prevista, il team può individuare il processo produttivo e il materiale più adeguato, con l'obiettivo di ottimizzare i costi, la velocità e l'efficienza complessiva del workflow. Ad esempio, nei crash test i componenti devono essere costruiti con lo stesso materiale e processo utilizzati nella produzione di massa. Nel caso dei componenti in plastica, si utilizza solitamente lo stampaggio a iniezione, un processo che tradizionalmente prevede l'uso di attrezzature in metallo che richiedono un considerevole dispendio di tempo e denaro.
"Gli inserti stampati in 3D per lo stampaggio a iniezione hanno un grande potenziale, poiché ci consentono di realizzare le iterazioni del design in modo molto rapido. Stampiamo le cavità nei nuclei e poi possiamo modificarle all'interno dello strumento e iniettare le parti", ha dichiarato Alves.
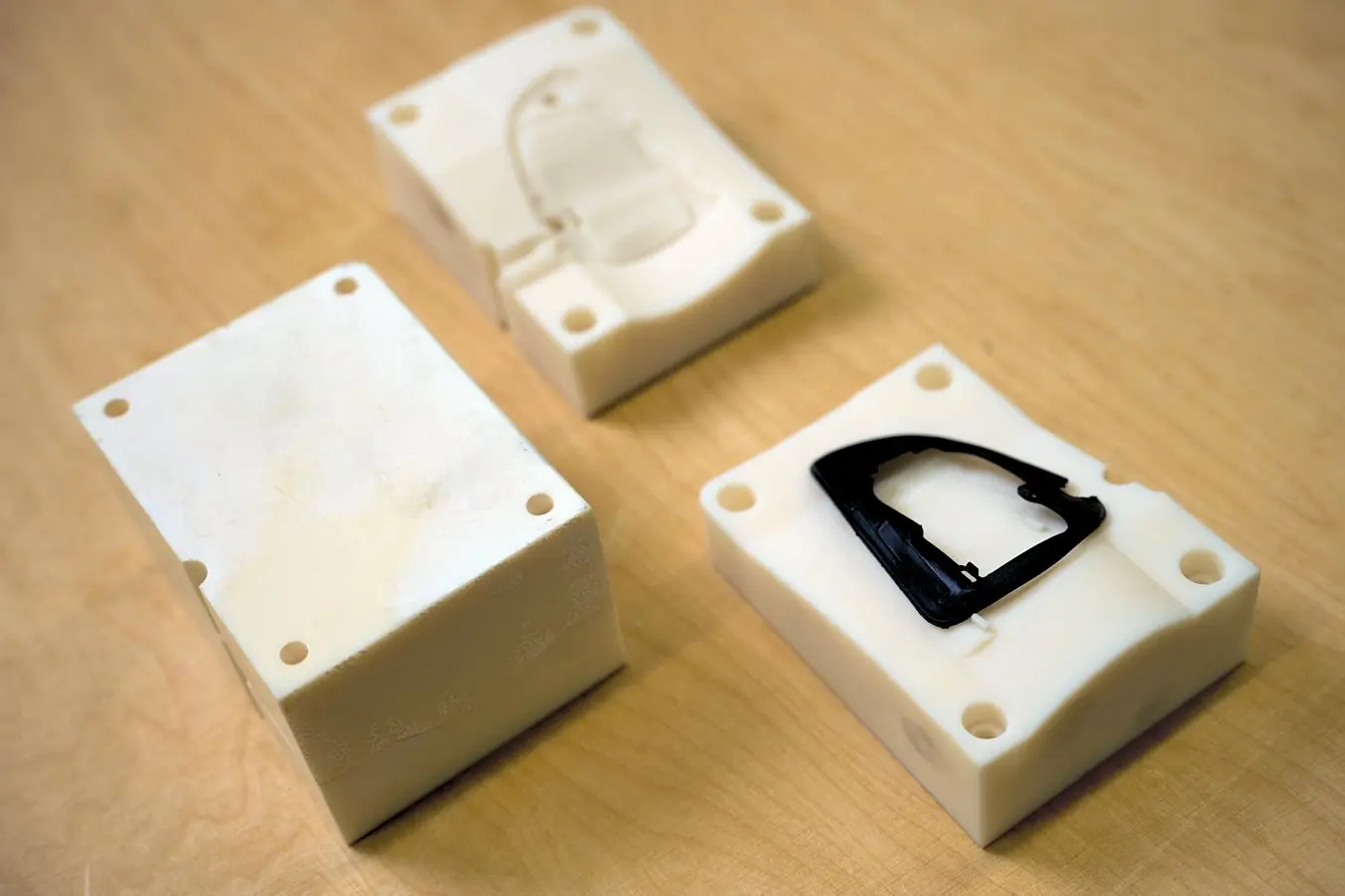
Il team ha prodotto gli inserti per lo stampaggio a iniezione in Rigid 10K Resin sulle stampanti SLA.
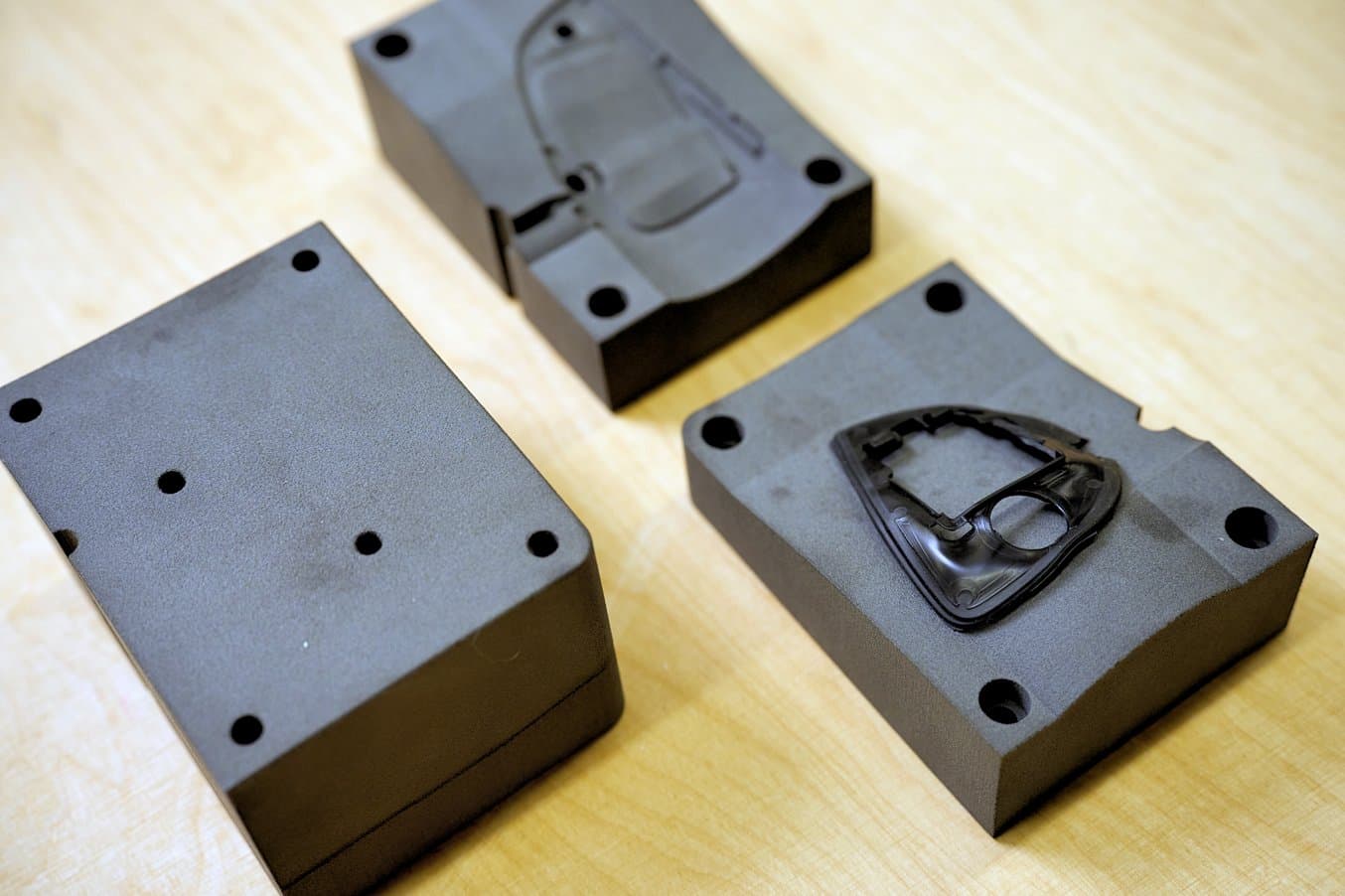
Utilizzano la Nylon 12 Powder sulle stampanti SLS per la stessa applicazione.
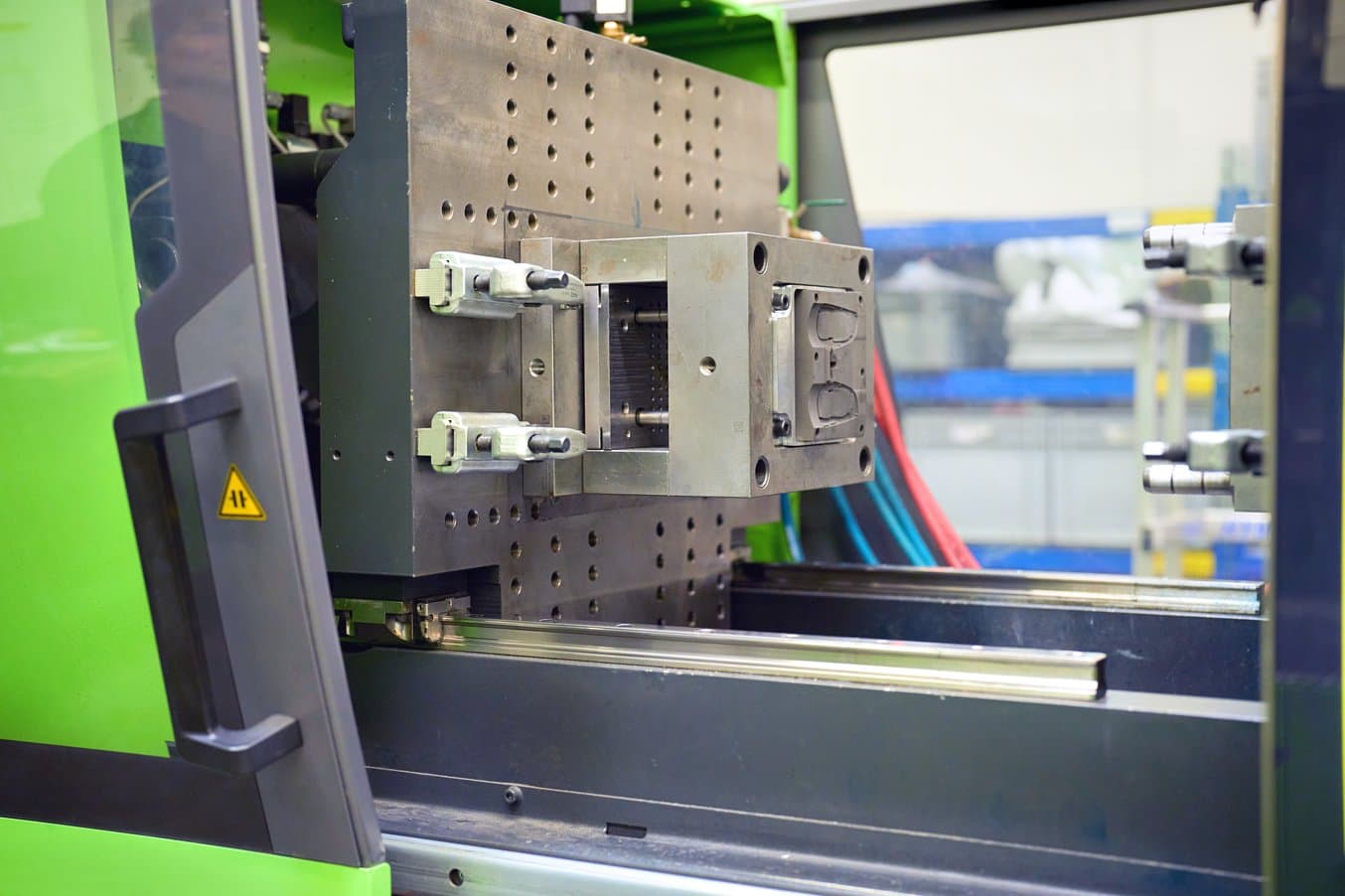
La stampa 3D consente al team di produrre rapidamente inserti per lo stampaggio di diversi design e iterazioni rapide utilizzando un apparecchio in-house per lo stampaggio a iniezione industriale.
Il team ha prodotto componenti in gomma per l'assemblaggio della maniglia delle portiere della nuova Explorer utilizzando inserti stampati in 3D nell'apparecchio in-house per lo stampaggio a iniezione.
"Si è trattato di un processo complesso perché abbiamo utilizzato diversi inserti e ci sono anche diversi design per cui era previsto un numero elevato di iterazioni. Solitamente, l'esternalizzazione dello stampaggio a iniezione richiede due o tre mesi. La produzione additiva in-house ci permette di accorciare il processo fino a due o tre settimane al massimo. Per questo progetto, se avessimo dovuto utilizzare strumenti esterni, avremmo impiegato molto più tempo e non sarebbe stato possibile produrre le parti in tempo", ha dichiarato Alves.
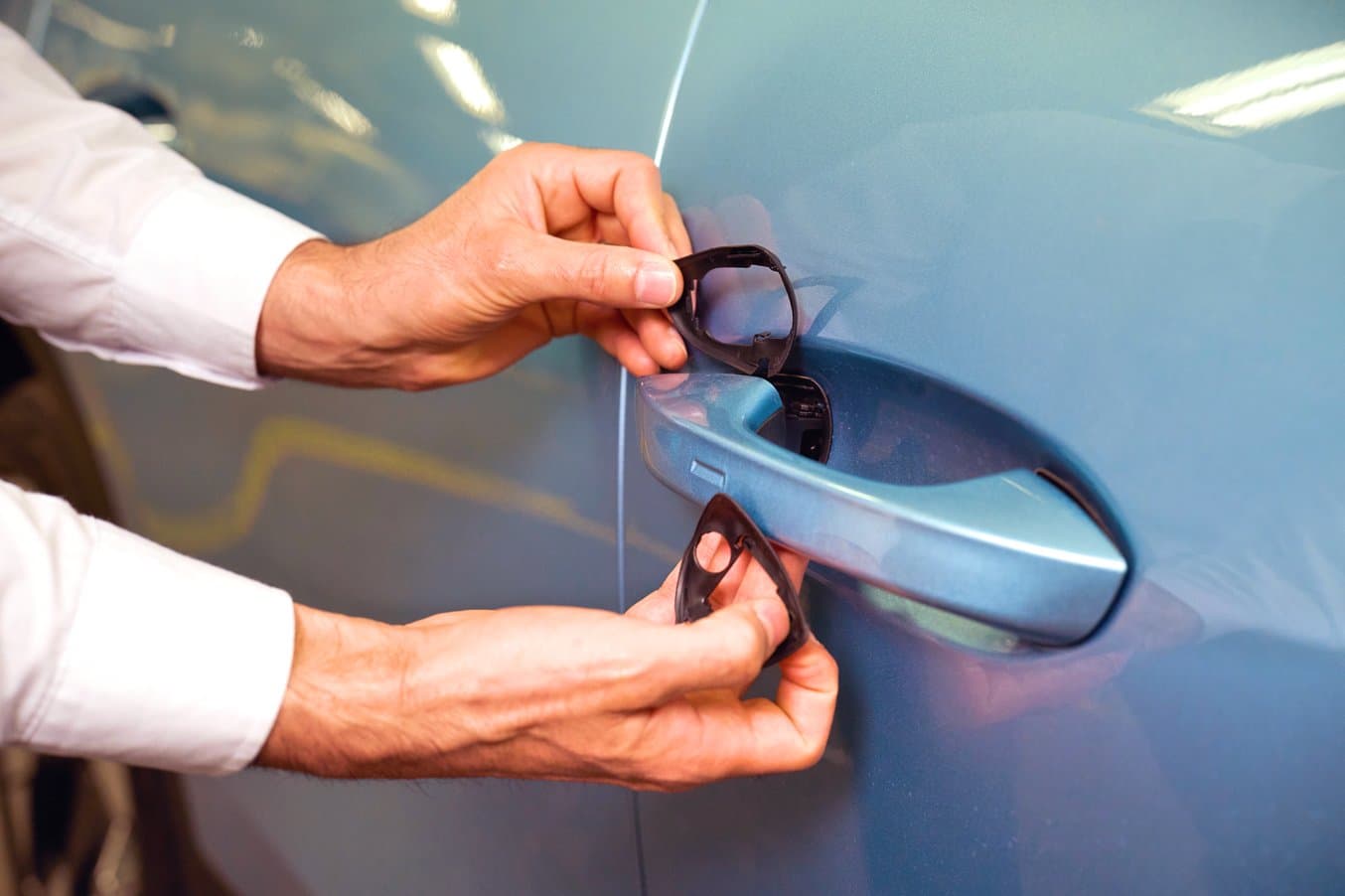
Ciascun design delle maniglie delle portiere comprende due di questi componenti in gomma per l'assorbimento delle vibrazioni e l'isolamento. Per il SUV a quattro porte, questo si traduce in otto componenti unici per ogni iterazione del design.
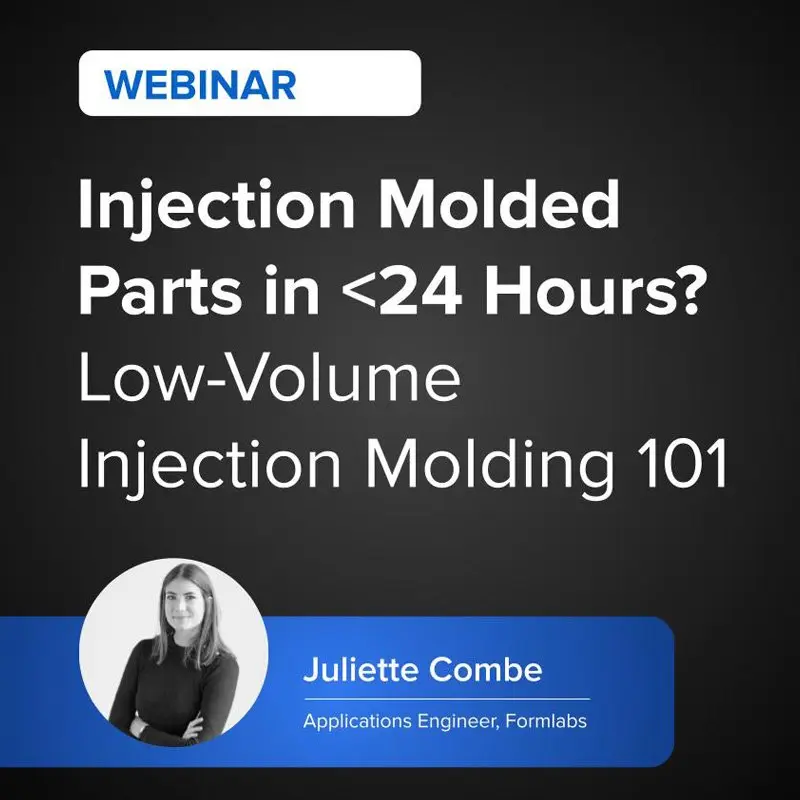
Parti stampate a iniezione in meno di 24 ore? Introduzione allo stampaggio a iniezione per volumi ridotti
In questo webinar illustreremo come utilizzare la stampa 3D stereolitografica nel processo di stampaggio a iniezione, al fine di abbattere i costi, ridurre i tempi di produzione e portare sul mercato prodotti migliori.
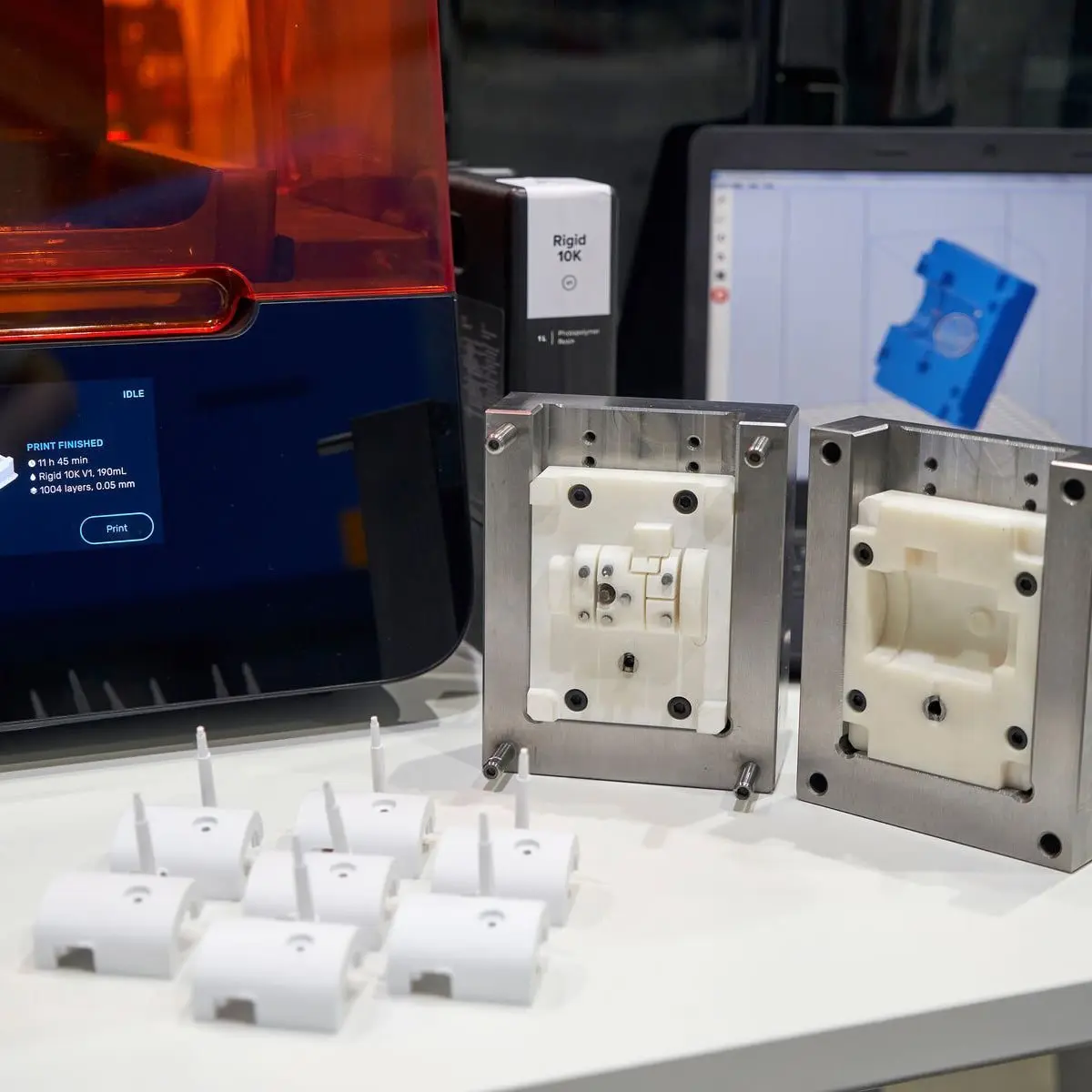
Stampaggio a iniezione rapido su scala ridotta con stampi realizzati in 3D
Scarica il nostro whitepaper per ottenere linee guida su come utilizzare stampi realizzati in 3D per i processi di stampaggio a iniezione, in modo tale da poter ridurre costi e tempi di consegna. Inoltre, potrai esaminare i casi di studio reali di Braskem, Holimaker e Novus Applications.
Accelerazione verso l'elettrificazione
L'impegno di Ford per produrre solo veicoli completamente elettrici entro il 2030 impone una tabella di marcia ambiziosa per lo stabilimento di Merkenich. Per raggiungere gli obiettivi prefissati, l'azienda dovrà continuare a trovare tecnologie all'avanguardia e a sperimentare nuovi workflow innovativi. Rimanere competitivi comporta la necessità di spingersi oltre i limiti e integrare nuovi materiali, processi e apparecchi, come le attrezzature e la stampa 3D in-house.
"Le aziende concorrenti stanno accelerando il processo di sviluppo. Non possiamo restare indietro. La soluzione è testare nuovi materiali, processi e apparecchi in arrivo sul mercato. Se in questo momento non avessimo a disposizione la produzione additiva, non saremmo in grado di affrontare la concorrenza, né di essere così veloci. La stampa 3D ci permette di avere il miglior prodotto che possiamo offrire alla clientela in tempi più brevi", ha dichiarato Alves.