La missione di Glassboard è chiara: assistere le aziende più ambiziose al mondo nella realizzazione di prodotti che le persone adorano usare. Il team non vuole limitarsi a creare un file CAD e una presentazione accattivante; ha deciso di avere un approccio olistico allo sviluppo dei prodotti e di aiutare le aziende a realizzarli, a negoziare i prezzi e a implementare la catena di fornitura necessaria per farli arrivare sul mercato.
Attiva nei settori più disparati, Glassboard Design ha trovato nella stampa 3D uno strumento prezioso per realizzare prodotti all'avanguardia. Nelle parole del vicepresidente operativo Grant Chapman, "Glassboard si occupa di sviluppo di prodotti a 360°, cerchiamo di avere competenze che ci permettano di affrontare praticamente qualunque sfida. Non abbiamo un unico mercato verticale. Non siamo attivi solo nel ciclismo, nel settore sanitario o nell'elettronica di consumo. Facciamo un po' di tutto. E Formlabs ha uno strumento che ci accompagna in tutti questi mercati verticali, oltre che una gamma di materiali abbastanza ampia da permetterci di fare quello che vogliamo."
In questo articolo incontreremo il team di Glassboard e scopriremo come usa una Form 2 e una Form 3BL per far sì che le sue soluzioni rispondano pienamente alle aspettative dei clienti e creare prodotti all'avanguardia.
Un materiale SLA per ogni progetto
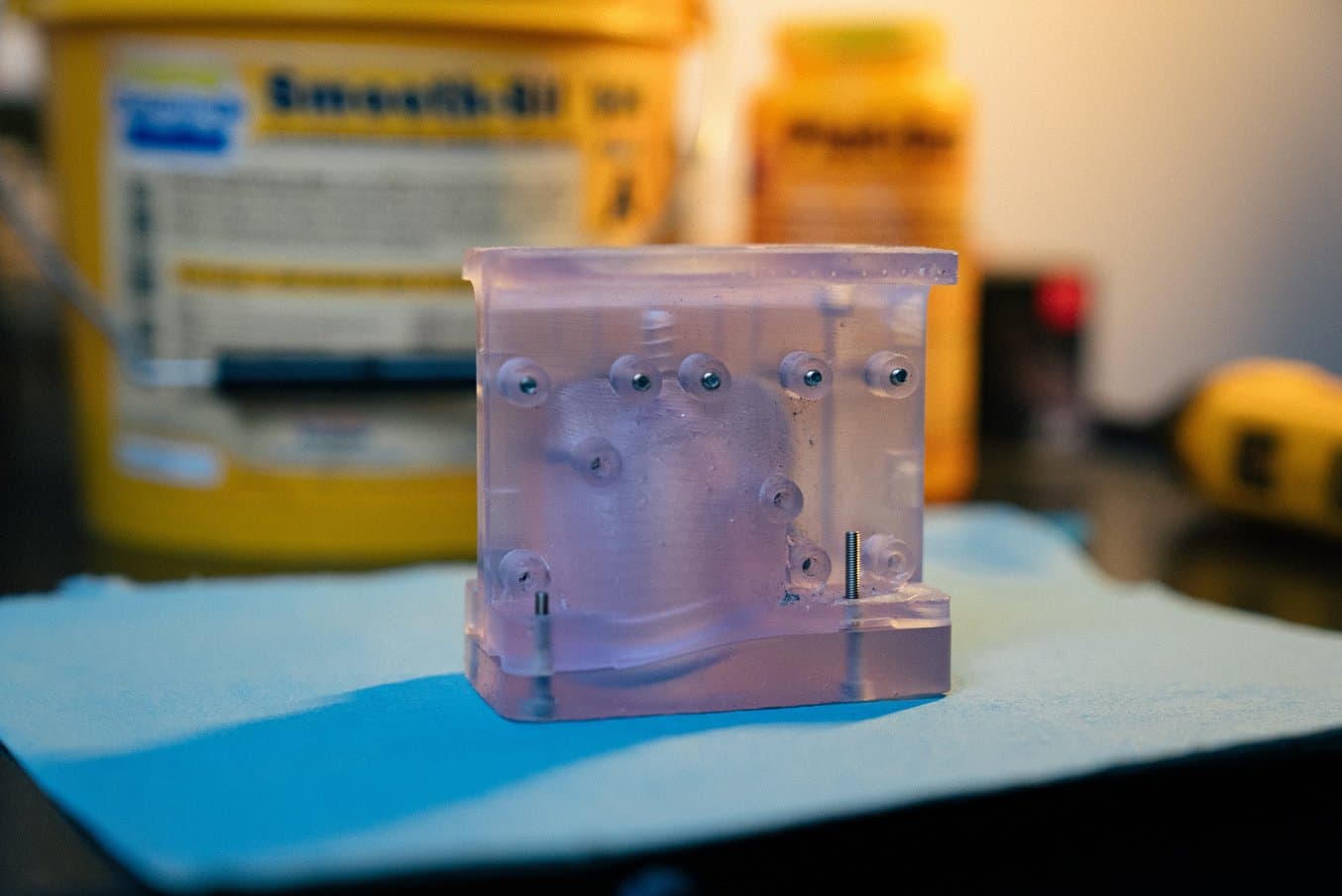
La BioMed Clear Resin è impiegata per creare stampi trasparenti che possono essere esaminati alla ricerca di bolle d'aria o altre imperfezioni.
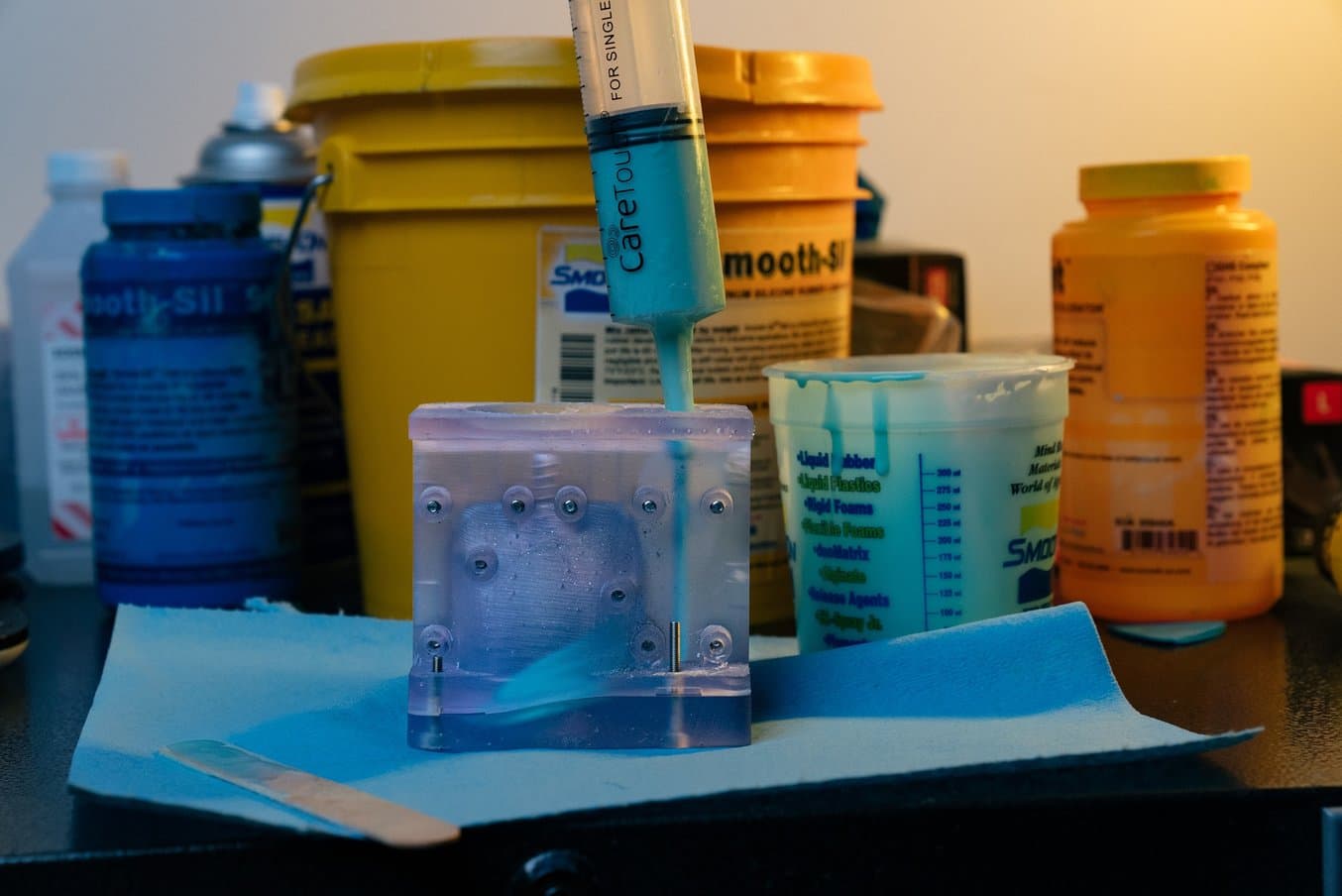
Glassboard non ha dubbi sul perché ha scelto Formlabs per stampare in 3D: c'è un materiale per ogni situazione.
Il team di Glassboard lavora su un'ampia gamma di prodotti, e per creare il prototipo perfetto ogni progetto richiede un diverso workflow o una tecnica specifica: dallo stampaggio a inieizione alla termoformatura, fino allo stampaggio in silicone. Il team necessita quindi di una stampante 3D in grado di adattarsi e rispondere a queste esigenze. Secondo Chapman, "più il catalogo di materiali si amplia, più mi semplifica la vita. È una funzione lineare."
Un progetto in particolare ne è l'esempio: di recente Glassman ha collaborato con Sunny, un'azienda che realizza prodotti per il ciclo mestruale. Sunny stava cercando di lanciare una nuova coppetta mestruale, e voleva trovare un modo innovativo per far emergere il prodotto sul mercato.
Glassboard sapeva bene che un prodotto del genere – un prodotto di consumo flessibile destinato a entrare in contatto con il corpo – avrebbe richiesto numerosi prototipi e test. Chapman si è rivolto a due dei suoi partner più affidabili – le sue stampanti 3D SLA 3D di Formlabs – e ha iniziato a stampare prototipi della coppetta in Elastic 50A Resin e Flexible 80A Resin.
"Per il prodotto di Sunny abbiamo davvero fatto ricorso a tutta la gamma di resine Formlabs, dalle più flessibili, elastiche e gommose fino alle più rigide, e tutto quello che c'è in mezzo." - Grant Chapman
Per altri progetti, il team aveva bisogno di un materiale in grado di superare i test di impatto: di certo non il primo requisito che deve possedere un dispositivo medico sensibile. Ha quindi optato per la Tough 2000 Resin e ha sottoposto la parte stampata a una serie di rigorosi test di caduta e robustezza. "Stiamo lavorando anche su un dispositivo di sicurezza che ha superato il test di impatto grazie alla Tough 2000 Resin, sopportando diverse cadute", ha affermato Chapman. "Le altre parti plastiche presenti nel prodotto erano fatte di policarbonato e sono state prodotte mediante formatura sottovuoto con stampi creati anch'essi con la Form 3BL."
Chapman crede che senza un catalogo di resine così ampio, molti di questi progetti non avrebbero visto la luce o si sarebbero rivelati meno validi, e aggiunge: "Il prototipo del dispositivo di sicurezza esiste unicamente grazie alla Form 3BL, ed è riuscito a superare i test per la certificazione anche allo stato di prototipo, prima ancora di essere realizzato con i polimeri".
Le tre resine preferite di Glassboard Design per risolvere i problemi posti dallo sviluppo di prodotto sono:
- La Tough 2000 Resin: "Mette la funzionalità al centro", ha affermato il team. "È così simile alla vera plastica che può essere usata perfino per prototipare parti funzionali come gli accoppiamenti a scatto e le cerniere integrate."
- La Draft Resin, perché "offre una grande accuratezza in tempi incredibilmente rapidi, e per di più si presenta bene", secondo Ben Ettinger, ingegnere di prodotto.
- E infine c'è una delle resine del cuore di Chapman, la Rigid 10K Resin: "Quando avete lanciato la Rigid 10K Resin pensavo di sognare, perché la scheda tecnica era troppo bella per essere vera. Ne ho ordinato subito un litro per provarla e i risultati sono ottimi... è la migliore."
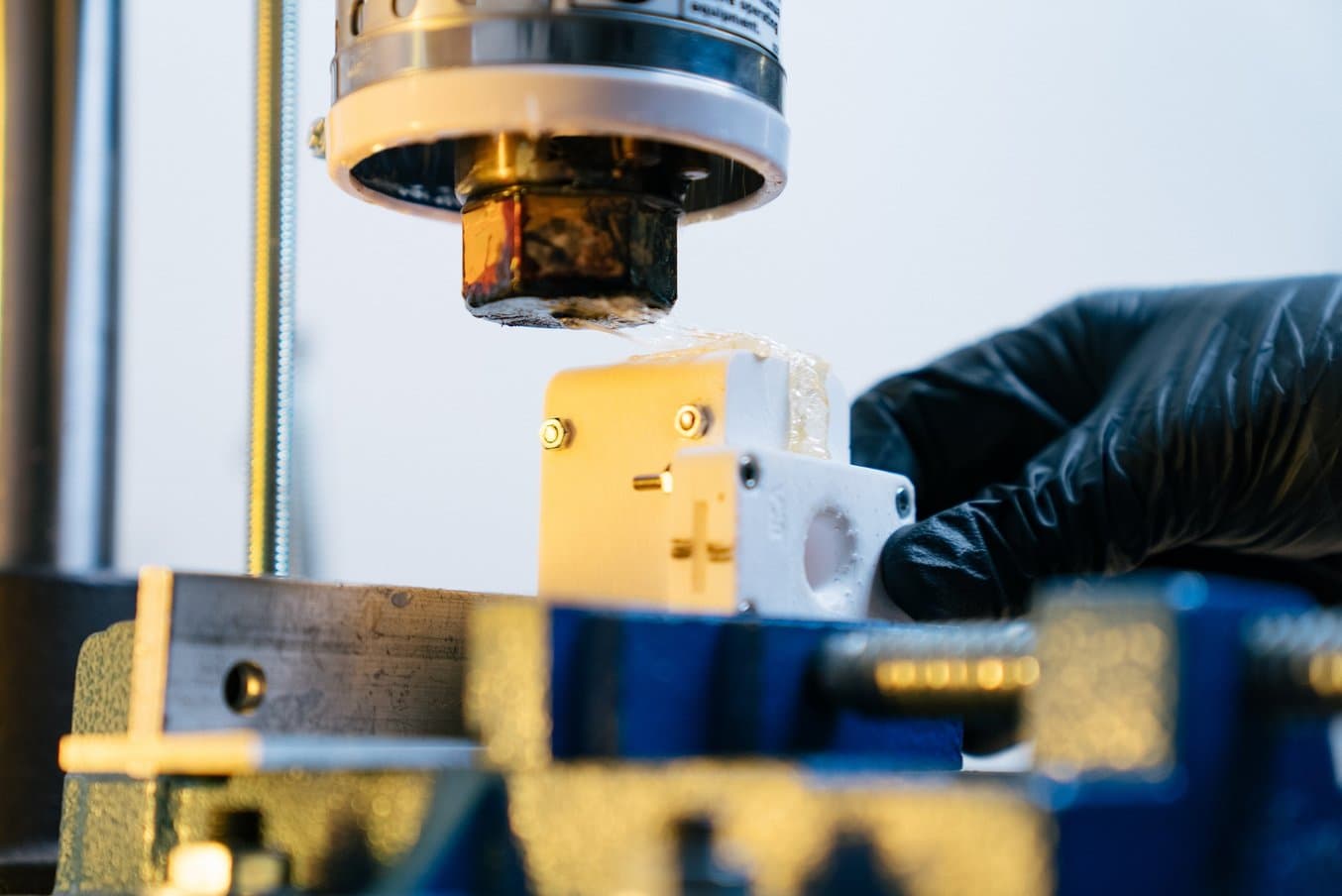
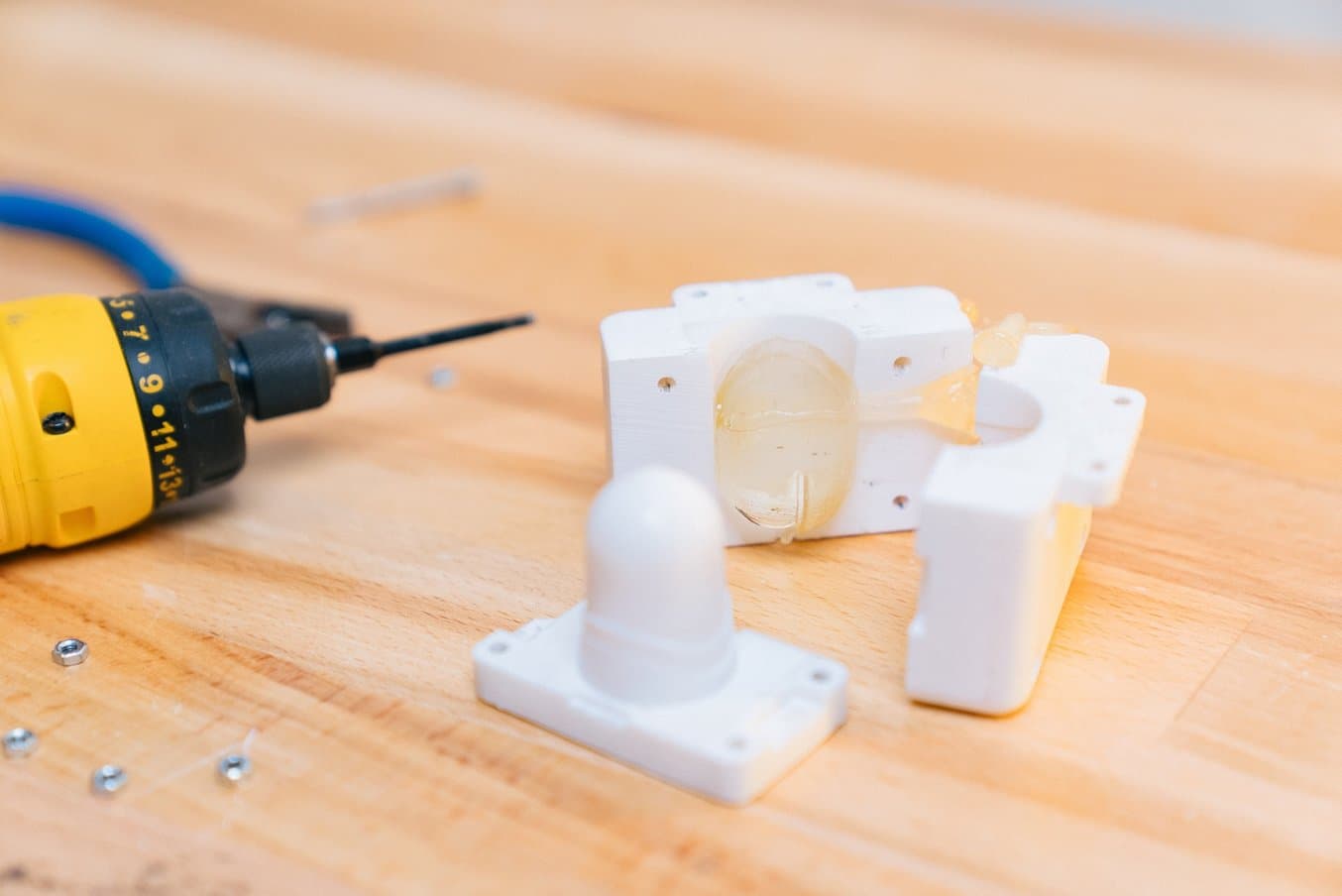
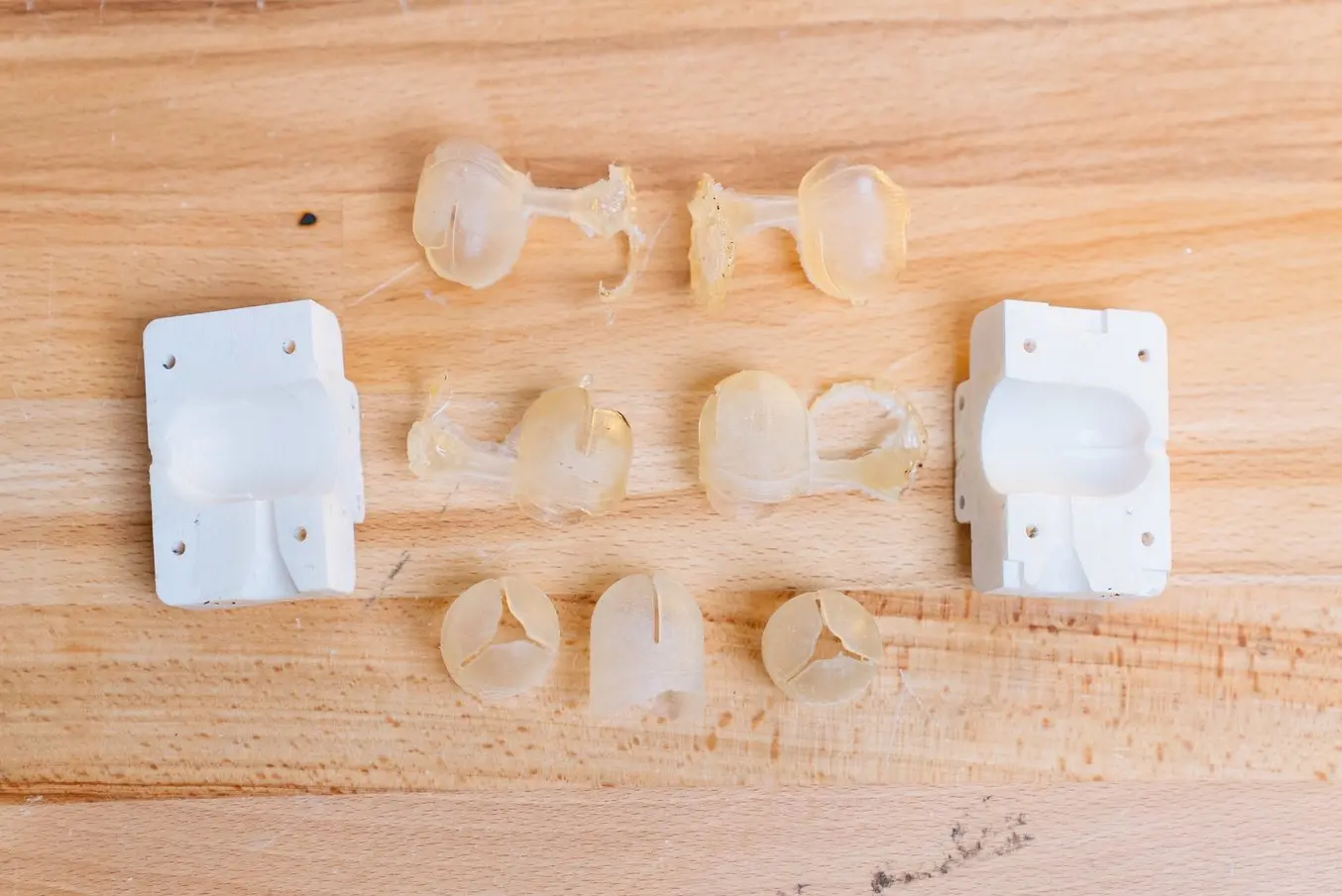
Gli stampi a iniezione stampati in 3D svolgono un ruolo essenziale nel processo di sviluppo di Glassboard.
Il vantaggio di un simile catalogo di resine per lo sviluppo di prodotto è evidente: la Form 2 e la Form 3BL sono macchine versatili, in grado di stare al passo con l'immaginazione di Chapman ed Ettinger e con le richieste dei loro clienti. "Tutti gli altri strumenti sono più specifici e di solito sanno fare bene una cosa sola", ha dichiarato Chapman. "Voi di Formlabs, invece, avete una resina per tutto. Che altra resina vi inventerete adesso? Di qualunque cosa si tratti, sarà eccezionale. Riguarderà un settore o un segmento che non abbiamo ancora potuto esplorare, o un materiale che non siamo ancora riusciti a prototipare, e ci permetterà di fare cose pazzesche."
La Form 3BL per lo sviluppo di prodotto
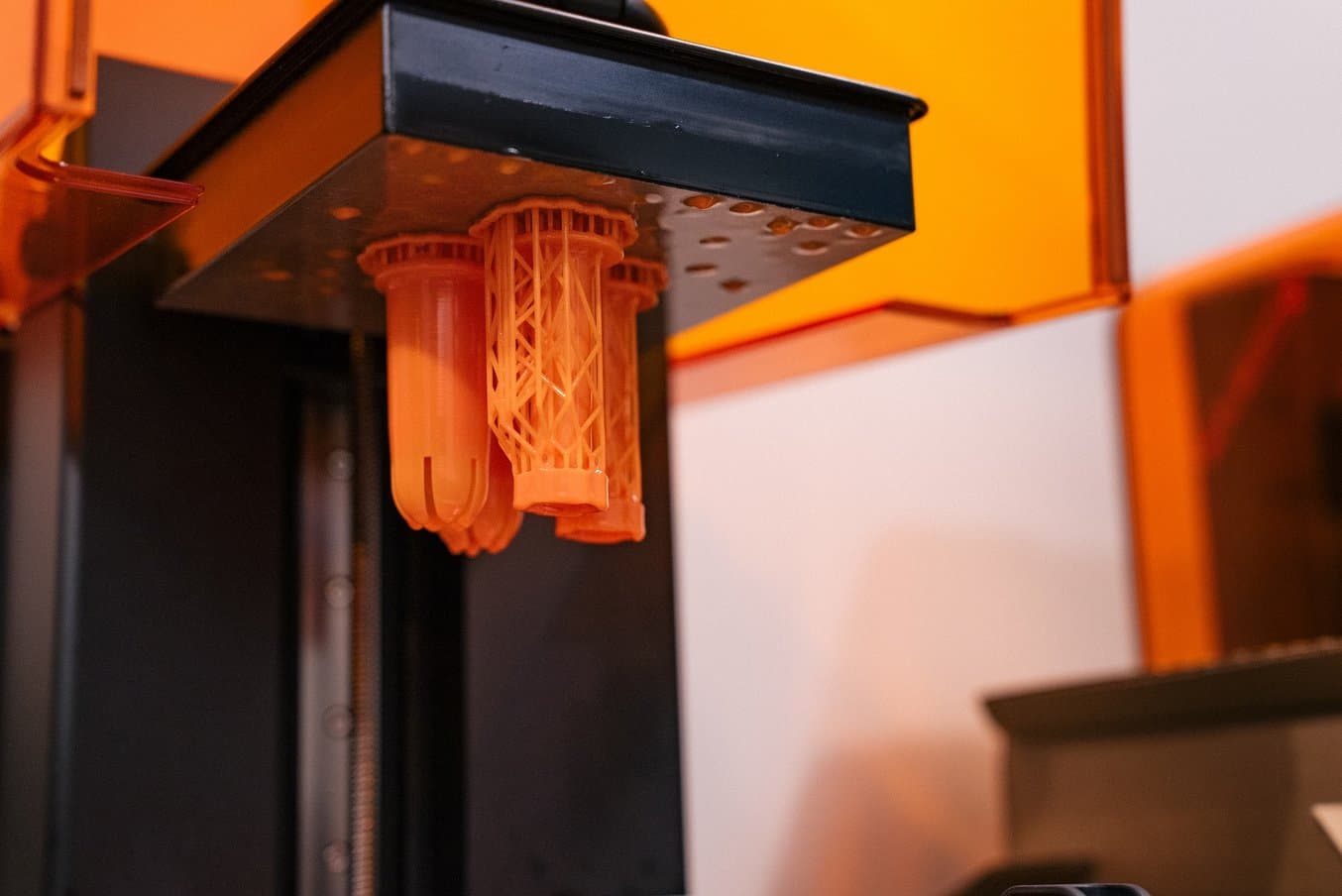
Glassboard utilizza la Form 2 e la Form 3BL.
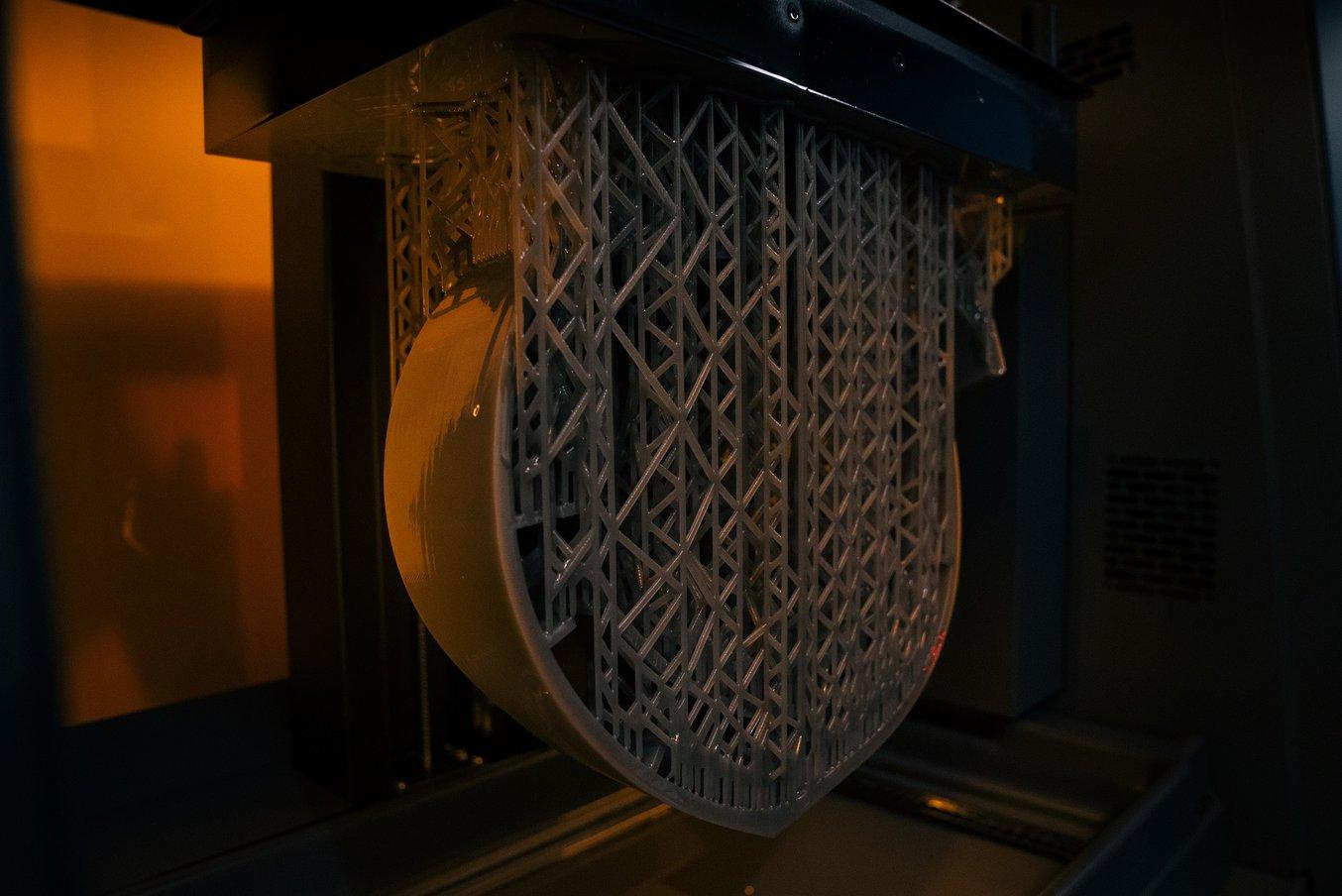
Visto il loro immediato successo con la formatura sottovuoto, il team ha iniziato a impiegarle anche in altri progetti. Come ha spiegato Chapman, "per un altro prodotto abbiamo usato molto la formatura sottovuoto. Inizialmente abbiamo creato alcuni stampi per la formatura sottovuoto di parti di grandi dimensioni con la Form 3BL e la Draft Resin. In passato questi stampi sarebbero stati prodotti con una Form 2 a pezzi e quindi assemblati, ma questo processo avrebbe comportato un tempo di stampa più lungo. Inizialmente i designer prendevano in considerazione la formatura sottovuoto solo per realizzare confezioni, vasche da bagno o scocche di caschi. Ma stiamo scoprendo che può essere impiegata anche per creare parti molto più complesse: basta aver voglia di mettersi alla prova con la progettazione degli utensili e degli sfiati. Permette anche di usare le termoplastiche per la produzione nella prototipazione, senza bisogno di ricorrere allo stampaggio a iniezione. Abbiamo appena iniziato a sfruttare il potenziale di questa tecnologia, credo, e non vedo l'ora di scoprire cos'altro riusciremo a fare da qui all'anno prossimo."
Grant Chapman
"Per realizzare le parti con la formatura sottovuoto occorrono solo 24 ore: di notte si creano gli stampi, al mattino li si polimerizza, a fine giornata si modellano e si rifiniscono i fogli di termoplastica. E ci si ritrova con una parte pronta da testare. Per me, la definizione di prototipazione rapida è questa."
Un caso d'uso inatteso della Form 3BL ha visto impiegare la sua grande piattaforma di stampa per stampare tante parti di piccole dimensioni in una volta sola. Il team inizialmente prevedeva di usare la stampante soprattutto per la prototipazione di parti e stampi di grande formato ma, come ha spiegato Chapman, grazie all'elevata precisione offerta dalla Low Force Stereolithography, in alcuni casi ha potuto affidarsi alla Form 3BL anziché alla Form 2. "Un cliente per cui stiamo realizzando, fra l'altro, stampi in due parti in uretano aveva bisogno di alcuni prototipi di una parte flessibile di piccole dimensioni per il giorno seguente", ha proseguito Chapman. "Alla fine, anziché ripulire lo stampo, riutilizzarlo e rispedirlo, abbiamo realizzato trenta nuovi stampi con la Form 3BL nel giro di una notte, e siamo riusciti ad assemblarli tutti, rispedire lo stampo originale e inviare tutti gli altri il giorno dopo. E mentre la Form 2 ha richiesto tre o quattro stampe, alla Form 3BL sono bastate una notte e una stampa.”
Chapman ha aggiunto: "La Form 3BL fin qui ci ha lasciati davvero senza parole, e gli aggiornamenti del software a cui abbiamo assistito solo negli ultimi cinque mesi, dalle impostazioni dei supporti alle resine, dalla fase beta al lancio sono stati sostanziali. In un tempo di sviluppo brevissimo la rimozione dei supporti è migliorata in modo incredibile. Insomma, sono davvero soddisfatto di questa linea di prodotti."
Materiali biocompatibili Formlabs per lo sviluppo di prodotto
Grant Chapman
"Avere accesso a materiali che risultano piacevoli a contatto con la pelle rivoluziona davvero la prototipazione delle parti che devono essere toccate con mano per essere testate."
La Dental LT Clear Resin (V2) è un materiale notevole non solo per la prototipazione di parti biocompatibili, ma anche per la realizzazione di stampi: il team usa la Form 3BL per creare stampi di grandi dimensioni. Chapman ci ha raccontato che "la caratteristica più impressionante della Dental LT Clear Resin (V2) è che è sicura a contatto con le mucose, e non abbiamo problemi a usarla nelle applicazioni dei clienti che entreranno a contatto con la pelle, come gli stampi in silicone polimerizzato per il platino o le parti stampate in 3D per uso finale. Senza contare che permette di creare stampe molto accurate e facilita tantissimo la rimozione dei supporti. E questo in fin dei conti è il più grande punto di forza di questo materiale."
Un altro dei vantaggi della Dental LT Clear Resin (V2) è che permette di creare stampi trasparenti, come ha notato Chapman: "essendo trasparente, quando riempiamo gli stampi, ci accorgiamo subito di eventuali bolle d'aria o vuoti e possiamo correre ai ripari."

Richiedi un campione gratuito
La BioMed Clear Resin è un materiale duro e resistente per applicazioni biocompatibili che richiedono il contatto a lungo termine con la pelle o con membrane mucose. Guarda e tocca con mano la precisione di Formlabs. Saremo lieti di inviare presso la tua azienda un campione gratuito.
Per molti prodotti di consumo, i progettisti non cercano di reinventare la ruota e risolvono i problemi tecnici. Per Sunny, il prodotto esiste già nelle versioni precedenti. Il punto è offrire al cliente un'esperienza superiore rispetto a quella offerta dai prodotti precedenti, ed è per questo che le iterazioni su caratteristiche minori possono determinare il successo o il fallimento di un nuovo prodotto.
Secondo Ettinger, "è questo ciò che apprezzano di più: il fatto che i loro feedback vengono prontamente recepiti, generando iterazioni del design e aggiornamenti dei nuovi prototipi che possono quindi essere testati per continuare ad alimentare il ciclo di feedback. Credo che questo sia il passaggio più soddisfacente dell'intero processo."
L'affidabilità è tutto
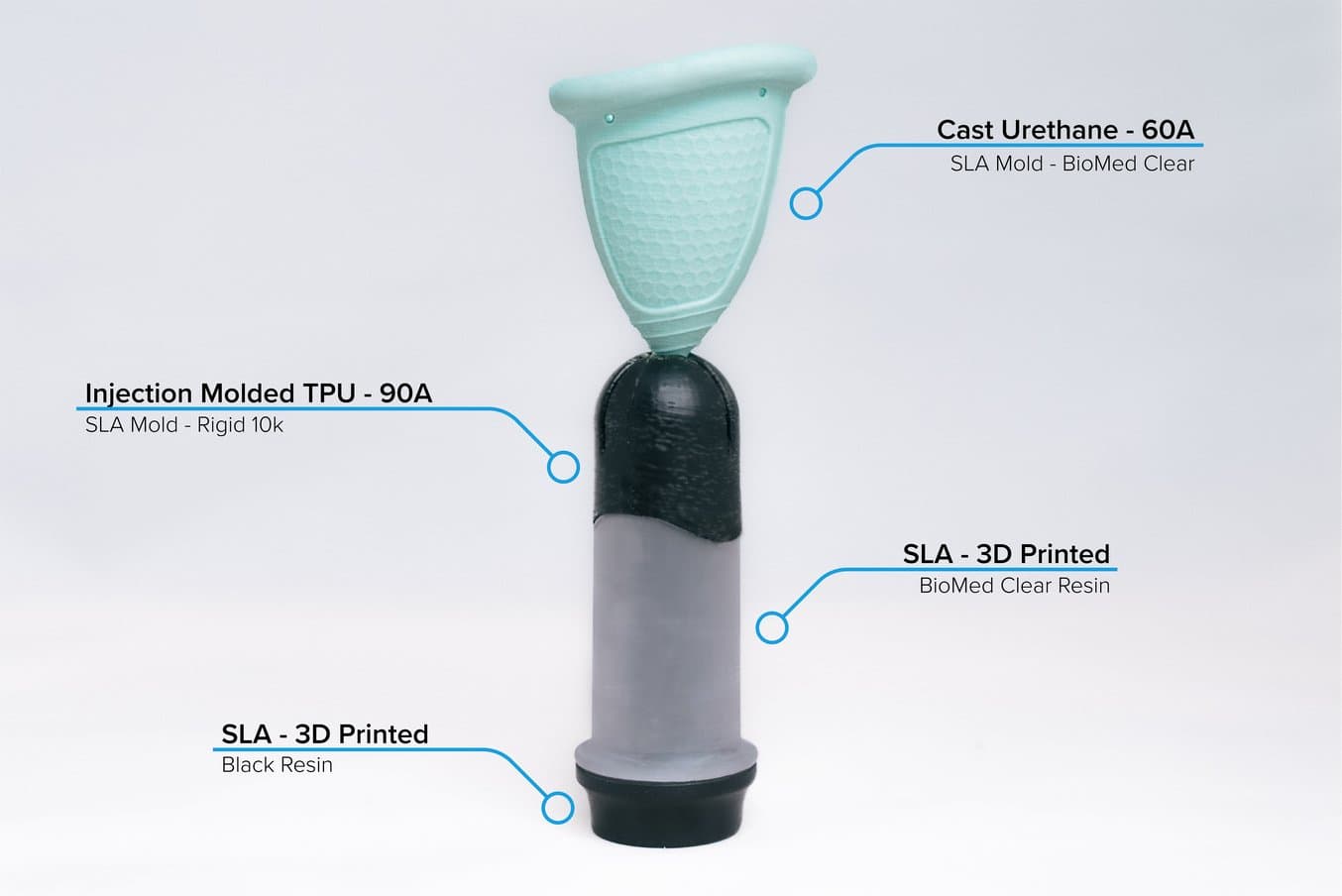
Le diverse parti utilizzate per creare l'applicatore e la coppetta per Sunny.
Qualunque sia la sfida, il team di Glassboard non ha paura di affrontarla, e ha bisogno di strumenti all'altezza. L'affidabilità è essenziale per il successo e la rapidità di stampa del progetto di Sunny. Dovendo stampare decine di prototipi, eventuali problemi nel processo di stampa potevano ostacolare la riuscita del progetto.
Per Chapman, "le stampanti Formlabs sono davvero affidabili. Il problema non è solo che se una stampante si rompe occorrono due ore per ripararla: può capitare che si rompa di notte, quando magari tu contavi di poter stampare una parte per spedirla il giorno dopo e rispettare le scadenze fissate dal cliente. In questi casi l'affidabilità è tutto. Il punto non è il tempo di inattività, è la mancanza della stampa che pensavi sarebbe stata pronta da consegnare al cliente come promesso. Se una stampante si guasta o ha un problema, rischi di non rispettare una scadenza, ecco perché l'affidabilità è così importante."
In totale, per la coppetta e l'applicatore di Sunny, il team ha creato oltre 100 prototipi. Dato che il prodotto entra in contatto con il corpo umano, e in una zona così delicata, sapeva che non sarebbero bastate un paio di stampe per perfezionare il design. Il prodotto deve presentarsi bene, inserirsi alla perfezione e adattarsi a diverse tipologie fisiche. Ecco perché Chapman sostiene che la rapidità delle iterazioni è essenziale: "di fatto con tutti i prodotti che sviluppiamo in-house il nostro obiettivo è capire come eseguirne dei prototipi nel modo più rapido e facile possibile. E poi anche come testarli in una forma più vicina possibile a quella definitiva prima di avviare la lavorazione, prima di doverci interfacciare con il produttore. Come fare il maggior numero possibile di test già in fase di prototipazione?".
Scopri di più sulla stampa 3D per il design di prodotto

Chapman riassume la sua opinione sulla stampa 3D con queste parole: "È uno strumento che vorrei aver scoperto anni fa, perché oggi lo usiamo davvero per tutto". Vista la loro affidabilità e versatilità, Glassboard prevede di usare la Form 2 e la Form 3BL in tutti i progetti a venire.
Per saperne di più su Glassboard e seguire i loro prossimi progetti, visita il loro sito.
Per scoprire come sfruttare la stampa 3D per i tuoi prodotti, visita la nostra pagina dedicata alla Form 3L. Puoi anche richiedere un campione gratuito stampato con la Form 3L cliccando qui.