Kriwat GmbH è un'azienda medica specializzata in ortopedia con sede a Kiel, Germania. Fin dall'inizio, l'azienda si è distinta per un'attenzione particolare alla combinazione di prestazioni sportive e ricerca medica all'avanguardia.
Michael Kriwat ha avviato l'attività nel 1987 ed è stato uno dei primi esperti in Germania di analisi della camminata sul tapis roulant per atleti professionisti e amatoriali. Da quel momento, l'azienda è cresciuta fino ad avere 75 dipendenti in sei sedi tra Kiel, Amburgo e Preetz e ha esteso i propri servizi alla produzione di bendaggi, solette, plantari e calzature ortopediche su misura.
Il settore delle cure ortopediche sta affrontando una grave carenza di manodopera qualificata: sono pochi i giovani professionisti che vogliono dedicarsi al laborioso processo di creazione di plantari e ancora meno coloro che vogliono assumersi la responsabilità di gestire queste aziende di piccole e medie dimensioni, spesso a conduzione familiare.
Continua a leggere per scoprire come Lais Kriwat, il figlio di Michael, ha sviluppato un workflow digitale per la produzione di solette con la stampa 3D a sinterizzazione laser selettiva (SLS) per modernizzare l'attività e affrontare questi problemi. Grazie a questa tecnologia, Kriwat prevede di stampare 10 000 paia di solette entro quest'anno.
Trasformazione di un'attività artigianale con la stampa 3D
Il workflow tradizionale per la produzione di solette ortopediche richiede moltissima manodopera ed è complicato sia per il cliente che per il fornitore. Per prima cosa, bisogna inserire il piede in uno stampo di schiuma per prenderne l'impronta. All'interno dell'impronta viene versato un liquido polimerico per ricreare la forma del piede, che viene poi utilizzata per produrre una soletta su misura.
Questo workflow richiede competenze specializzate e lavoro manuale in un ambiente pieno di polvere e fumi chimici. "Questo è un aspetto che mi ha preoccupato molto durante la formazione. Molte parti dovevano essere prodotte con sostanze chimiche. Altre ancora dovevano essere levigate con una smerigliatrice, per cui c'era sempre un'elevata esposizione a sostanze chimiche e polvere. Ecco perché mi sono posto l'obiettivo di rivoluzionare il flusso di lavoro", ha dichiarato Kriwat.
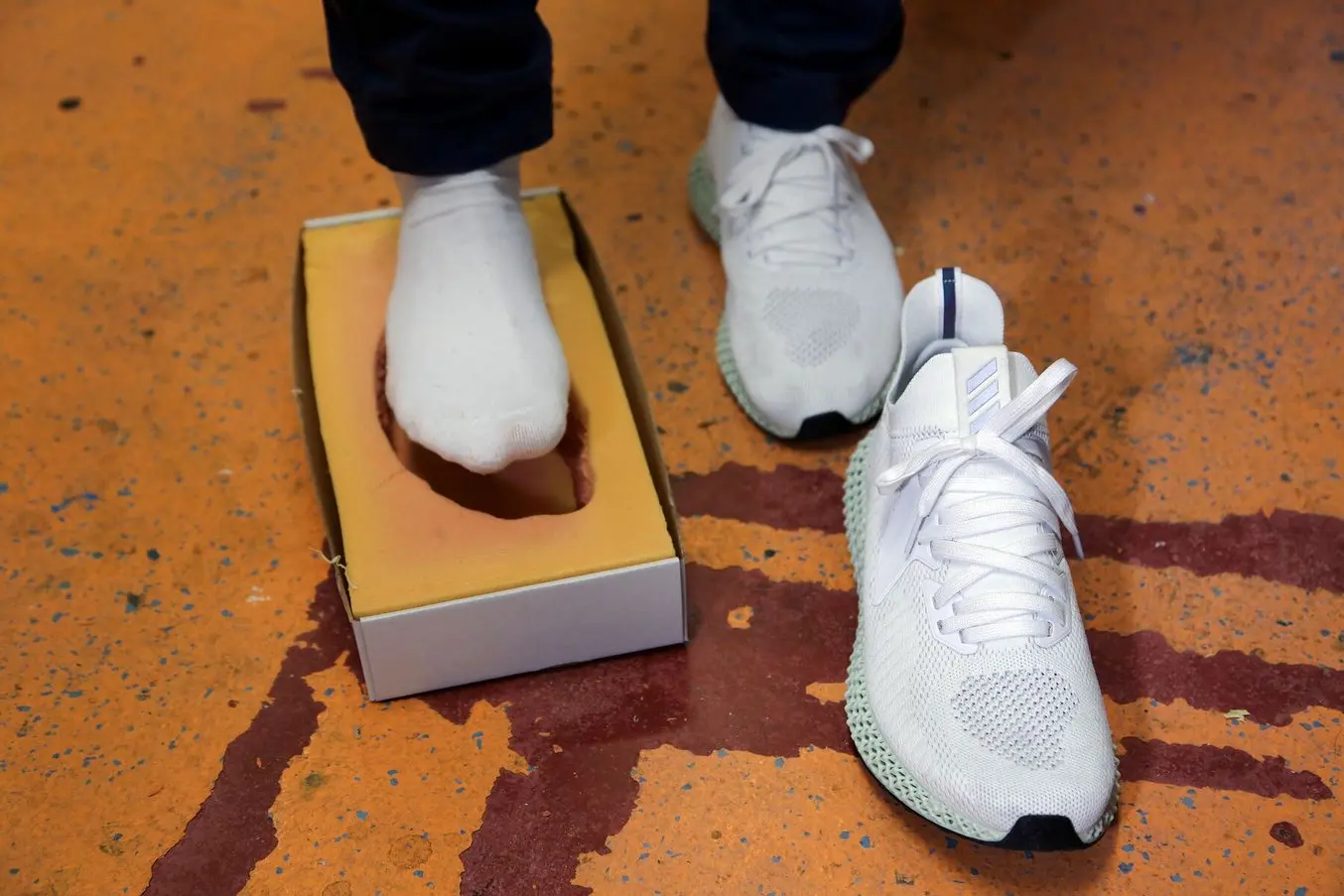
Tradizionalmente, le impronte si prendevano con uno stampo in schiuma.
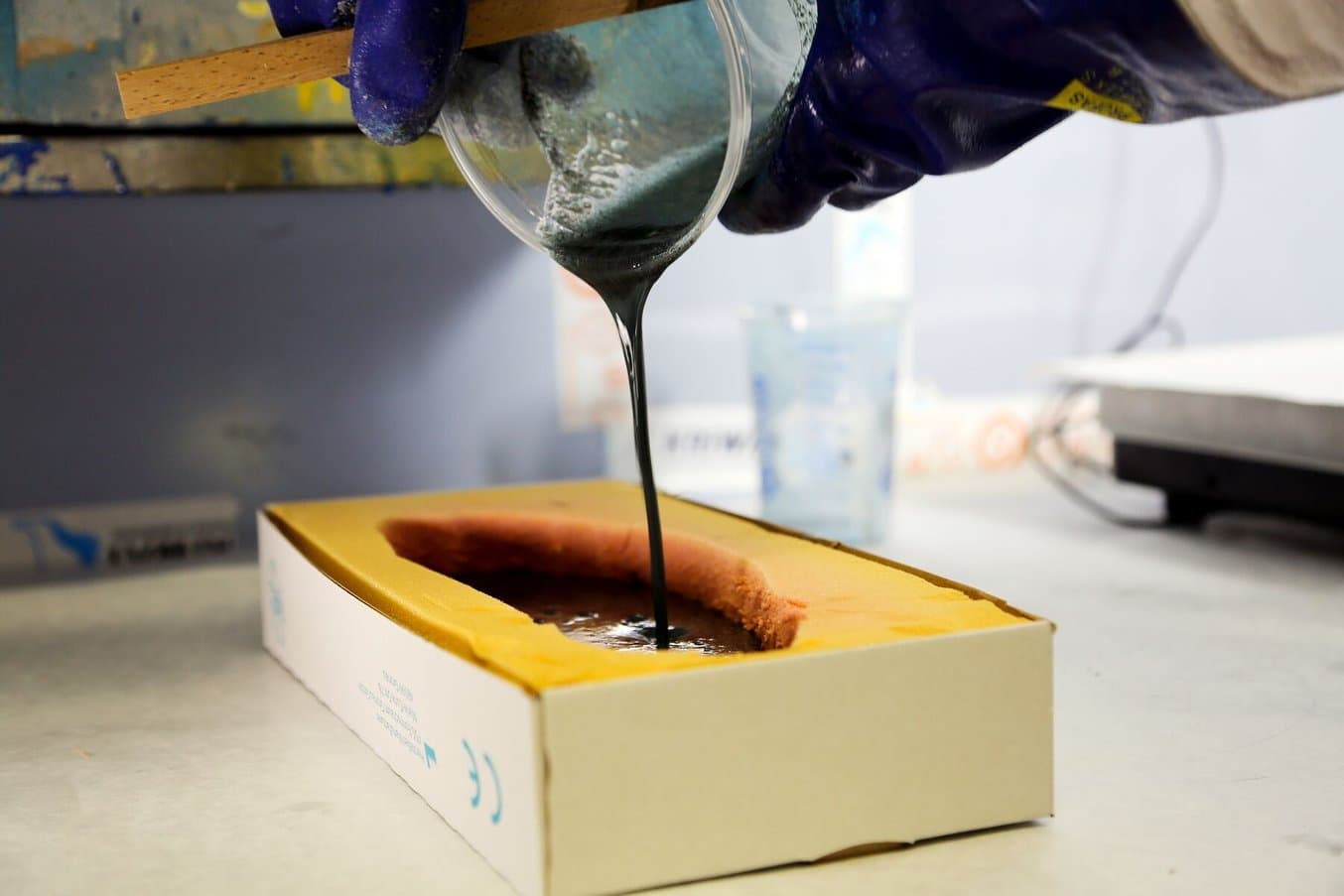
Lo stampo veniva poi riempito con sostanze chimiche per ricreare la forma del piede.
Essendo entrato da poco nel settore, Kriwat ha potuto constatare in prima persona le difficoltà del workflow tradizionale. Ciò lo ha aiutato a identificare i cambiamenti necessari per far sì che la professione continuasse a essere ambita.
"Oggi, la più grande sfida per il settore è senza dubbio la mancanza di personale. È difficile trovare persone che vogliano ancora fare il nostro mestiere e intraprendere una carriera nell'artigianato. Dobbiamo rendere questo lavoro interessante. In questo senso, le nuove tecnologie sono molto importanti", ha detto Kriwat.
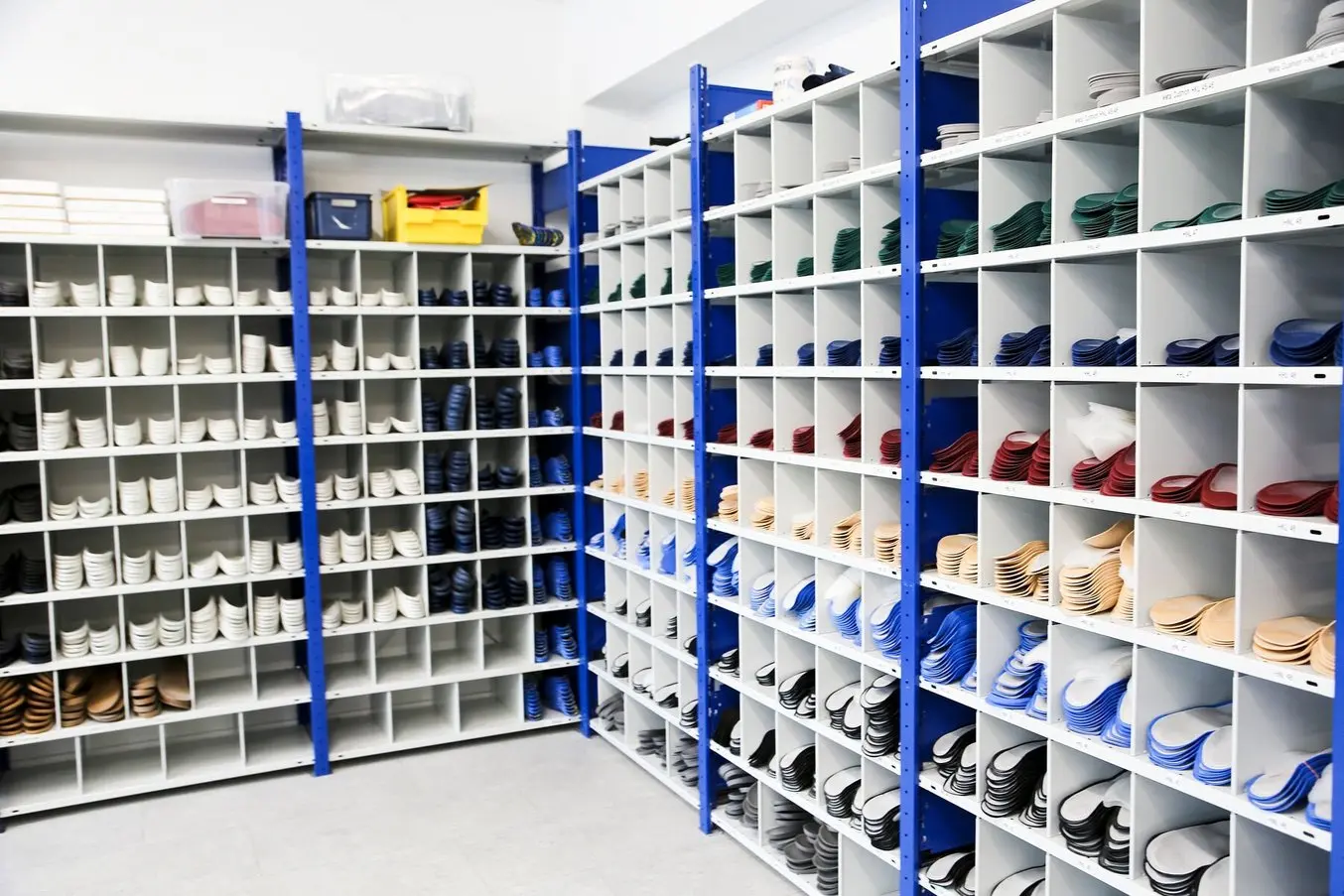
Kriwat GmbH produce migliaia di solette ogni anno.
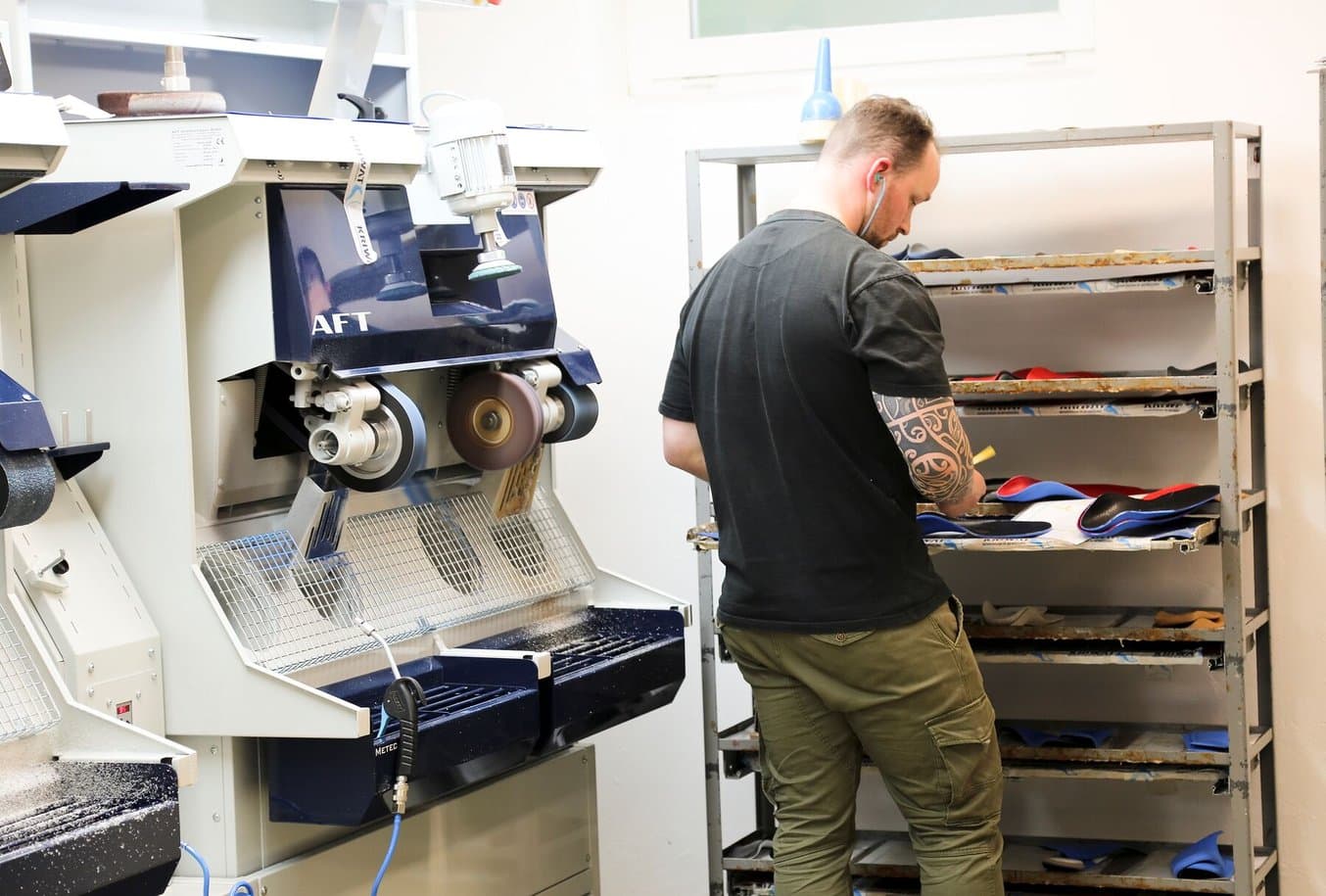
Il workflow tradizionale per la produzione di solette ortopediche richiede moltissima manodopera.
Kriwat ha iniziato a testare la stampa 3D nel 2017, stampando progetti e prototipi per hobby con una piccola stampante 3D a modellazione a deposizione fusa (FDM). Una volta acquisita una maggiore dimestichezza con la tecnologia, ha iniziato a studiare come implementarla nell'azienda di famiglia. Dopo aver scoperto la stereolitografia (SLA), l'azienda ha acquistato una stampante Form 3BL per la realizzazione di modelli a grandezza umana, aprendo così possibilità completamente nuove per la produzione di plantari. Poco a poco Kriwat ha iniziato a padroneggiare nuove applicazioni, per poi arrivare a dedicarsi al prodotto principale della propria attività: le solette.
"All'inizio era tutto un progetto e ogni nuovo passaggio rappresentava un'incognita, così ho iniziato a cercare partner affidabili. Scoprire Formlabs è stato un vero colpo di fortuna, perché mi ha permesso di realizzare l'idea che avevo in mente. Avevo la possibilità di inviare loro i design e ricevere le parti stampate per verificare, prima di tutto, se fossero adatte alla stampa 3D. C'erano molti aspetti con cui non avevo familiarità e Formlabs mi ha aiutato a comprenderli", ha affermato Kriwat.
Kriwat ha gradualmente digitalizzato il workflow per la produzione di solette e ha convalidato i prodotti finali testandoli internamente e con i clienti. Grazie al nuovo workflow digitale, è possibile sostituire le impronte del piede con la scansione 3D, ridurre i numerosi passaggi manuali con la progettazione digitale e la stampa 3D e combinare le parti stampate in 3D con il workflow tradizionale per creare il prodotto finale.
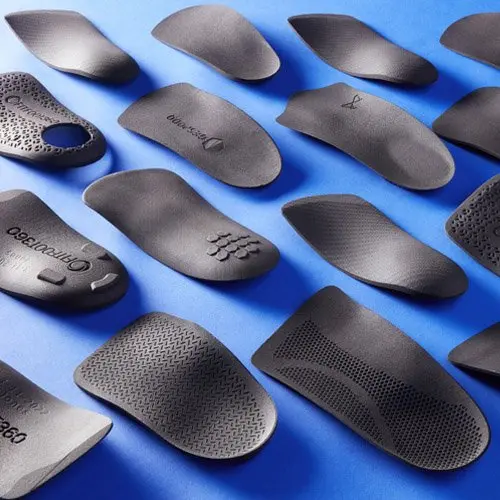
Stampa 3D di solette parziali rigide
Scopri come produrre solette parziali resistenti, duttili e in grado di superare 4 milioni di cicli di piegatura con l'ecosistema SLS compatto e conveniente di Formlabs. Questa guida completa ti aiuterà a partire in quarta con la produzione di solette parziali con la Fuse 1+ 30W.
Quali sono i vantaggi della stampa 3D nella produzione di solette?
Il team di Kriwat utilizza due stampanti 3D SLS Fuse 1+ 30W e la Nylon 11 Powder per realizzare tanto gli strati interni delle solette quanto solette complete. Naturalmente, prima di digitalizzare la produzione, Kriwat ha ritenuto estremamente importante dimostrare che il nuovo workflow offre vantaggi significativi sia per l'azienda che per i clienti. Vediamo quelli che ha evidenziato.
Risparmio di tempo
Il nuovo workflow consente di acquisire la scansione 3D, creare un modello digitale lo stesso giorno, raggrupparlo con altre solette e stampare tutto durante la notte con la Fuse 1+ 30W. Il team di Kriwat può successivamente eseguire la post-elaborazione delle parti, seguendo il workflow tradizionale a partire dall'anima centrale e completando le solette il giorno successivo.
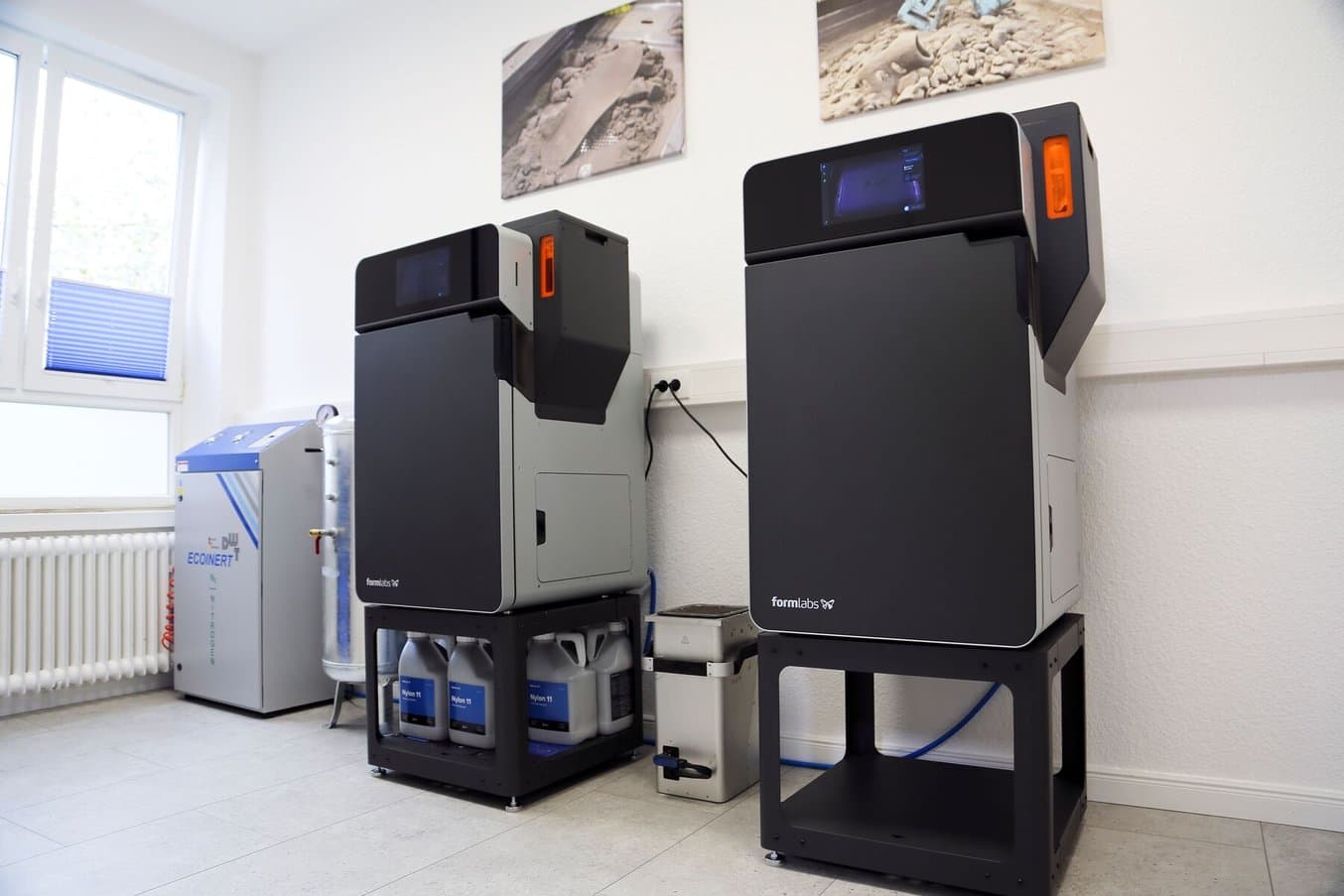
Al momento, Kriwat GmbH ha due stampanti 3D SLS Fuse 1+ 30W in-house.
"Ora abbiamo la possibilità di creare un plantare con un'aderenza perfetta nel giro di 24 ore. Poter accelerare la produzione è per noi un vantaggio, certo, ma la nostra priorità sono i pazienti: offrire la migliore soluzione ai loro problemi nel più breve tempo possibile è l'aspetto più importante."
Lais Kriwat, tecnico esperto in calzature ortopediche, direzione di Kriwat GmbH
Risparmio di costi
Rispetto all'artigianato tradizionale, il nuovo workflow digitale offre vantaggi economici sia in termini di costi dei materiali che, soprattutto, del personale. Con il nuovo workflow, molte delle fasi sono diventate digitali e non richiedono materiali o molta manodopera. A fronte dei volumi di produzione gestiti da Kriwat, è più economico acquistare una sola volta uno scanner 3D e un software di progettazione piuttosto che grandi quantità di schiuma e di sostanze chimiche liquide.
Inoltre, il personale può occuparsi di più pazienti in un giorno perché il workflow è più veloce, riducendo così i costi derivanti da una forza lavoro più numerosa. Kriwat ha stimato che i costi di produzione sono diminuiti di circa il 15-17%, grazie alla stampa 3D.
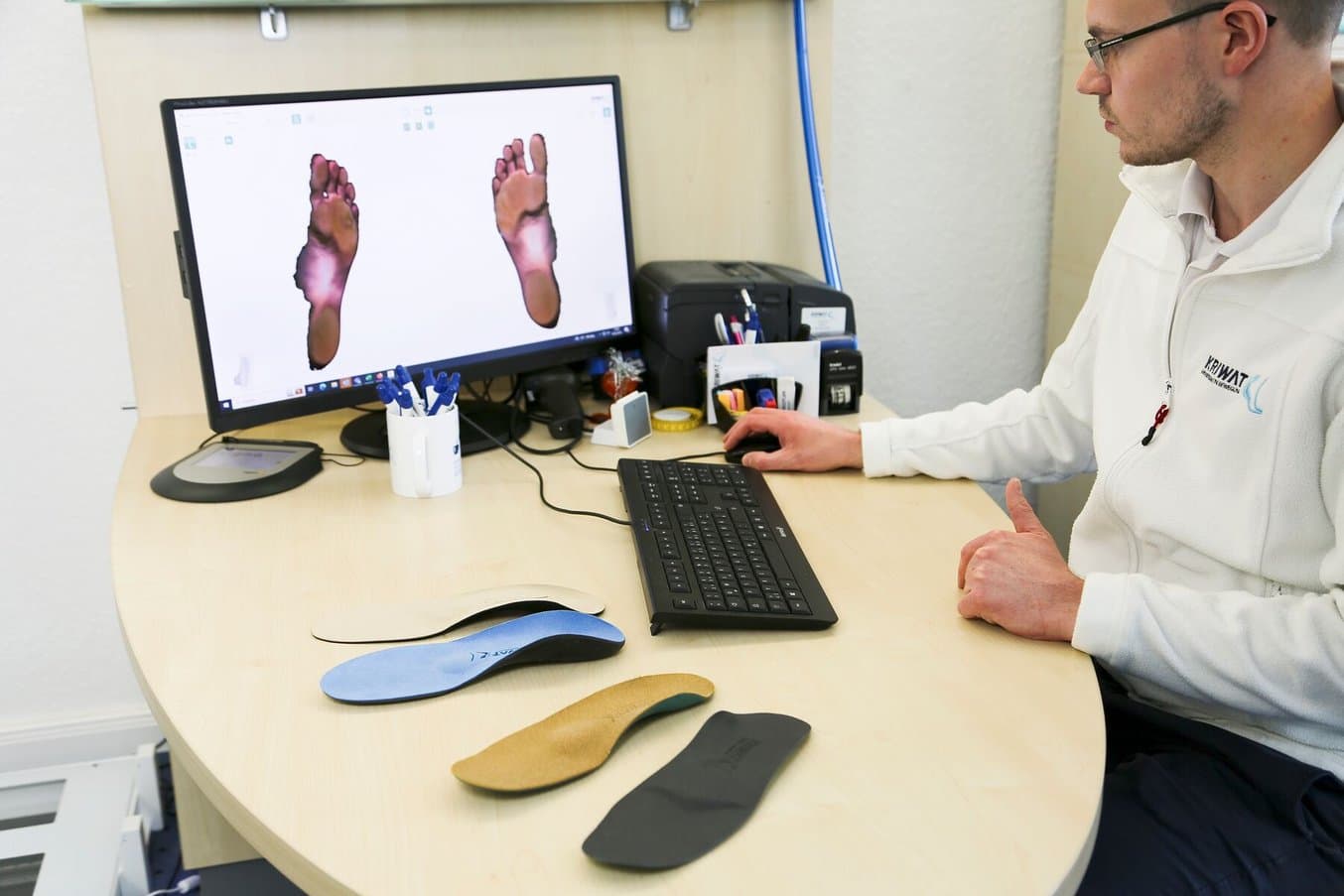
La scansione 3D consente di acquisire un'impronta più accurata e completa del piede e di inviare i dati in formato digitale con maggiore facilità.
Sebbene il team di Kriwat abbia immediatamente riconosciuto che l'adozione di stampanti 3D in-house era il modo migliore per ridurre i costi e migliorare il workflow, la maggior parte delle soluzioni di stampa 3D SLS aveva prezzi a sei cifre. La stampante SLS Fuse 1+ 30W era l'unico apparecchio in grado di fornire la soluzione industriale che il team stava cercando a un prezzo accessibile per aziende di piccole e medie dimensioni.
"Con Formlabs, il grande vantaggio è anche l'aspetto finanziario. È un investimento sostenibile per un'azienda di medie dimensioni come la nostra. Le soluzioni della concorrenza erano semplicemente troppo costose, sia per noi sia per altre aziende del settore."
Lais Kriwat, tecnico esperto in calzature ortopediche, direzione di Kriwat GmbH
Workflow semplificato
La stampa 3D SLS con la serie Fuse offre molte funzionalità che semplificano il workflow per la produzione di solette. Data la natura autoportante del processo, è possibile stampare numerose solette in un unico volume di stampa, ottimizzando il workflow e riducendo i costi. Le parti stampate hanno una finitura superficiale leggermente ruvida, ideale per applicare gli agenti adesivi e le coperture per i diversi tipi di prodotti finali. Le parti in nylon possono anche essere lavorate e levigate per ottenere la finitura perfetta per il prodotto finale.
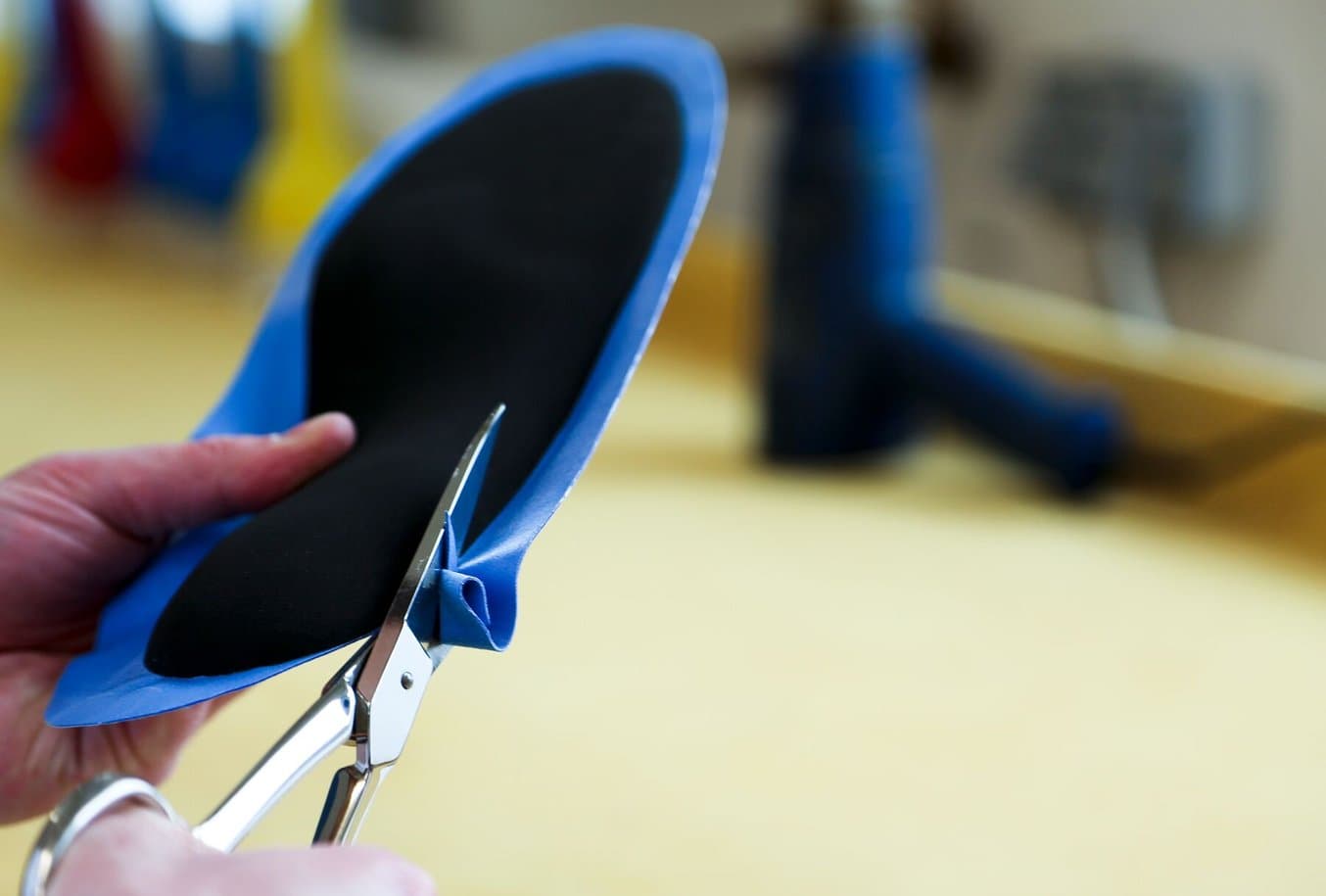
Le solette e gli strati interni stampati in 3D vengono assemblati con coperture e altri materiali per creare il prodotto finale.
Dashboard di Formlabs è uno strumento online che permette di gestire diverse stampanti 3D, tenere traccia delle stampe e del consumo di materiali e ricevere notifiche sullo stato dei progetti, cosa che Kriwat ha ritenuto fondamentale per la pianificazione. Nel corso della sua carriera, dopo aver provato numerosi software di visualizzazione per strati per stampanti 3D, ha trovato PreForm, il software di preparazione della stampa per le stampanti di Formlabs, semplice e immediato.
"PreForm è il software perfetto per avviare velocemente una stampa. Per noi è anche importante accompagnare i membri del personale e mostrare loro la semplicità della stampa 3D. PreForm è la soluzione ideale perché è semplice da usare, facile da spiegare e, infine, consente di inviare velocemente i progetti alla stampante", ha dichiarato Kriwat.
Logistica migliorata
La digitalizzazione semplifica anche la gestione della logistica. Kriwat GmbH dispone ora di scanner 3D nelle filiali di Amburgo, per cui è molto più semplice inviare i dati digitali alla sede di Kiel, dove il team può progettare i singoli prodotti. In passato, bisognava trasportare le impronte prese manualmente alla sede centrale, dove si producono le solette, operazione molto più dispendiosa in termini di tempo e di costi, dato che si dovevano percorrere regolarmente lunghe distanze.
Sostenibilità
Oltre a ridurre le spese di trasporto, la stampa 3D rende il workflow più sostenibile in molti modi. Nel workflow digitale, la produzione del prodotto finale richiede una quantità inferiore di materie prime, in quanto non è più necessario creare l'impronta fisica del piede. Kriwat GmbH non deve più cercare metodi di smaltimento per le migliaia di modelli, la schiuma inutilizzata e i rifiuti chimici. Grazie all'efficiente sistema della serie Fuse, la polvere non fusa può essere riciclata nella stampa successiva, dando vita a un workflow circolare in grado di ridurre o addirittura eliminare completamente i rifiuti.
"La sostenibilità è un tema importantissimo per la mia generazione. Il mio obiettivo era evitare di buttare via così tanto materiale. Per esempio, qui abbiamo un bidone della spazzatura per la plastica: volevo che non venisse ritirato ogni settimana, ma che si riducessero al minimo i rifiuti in modo che venisse ritirato al massimo ogni quattro. Volevo anche ridurre l'uso di sostanze chimiche e smaltirne meno. La tecnologia SLS di Formlabs è perfetta, perché stampiamo solo ciò che ci serve davvero", ha affermato Kriwat.
Il futuro dell'innovazione delle solette
L'obiettivo di Kriwat per il primo anno è digitalizzare circa il 50% della produzione di solette e di stampare circa 10 000 paia tra strati interni e solette complete. Ma le due stampanti 3D SLS Fuse 1+ 30W offrono anche molte possibilità per il futuro.
"Nel passare al workflow digitale, l'obiettivo iniziale era digitalizzare il metodo artigianale tradizionale, ovvero portare le forme e i tipi specifici delle nostre solette su computer per poi stamparle in 3D. I prossimi passaggi prevederanno la creazione di nuovi prodotti basati solo sulla tecnologia 3D", ha affermato Kriwat.
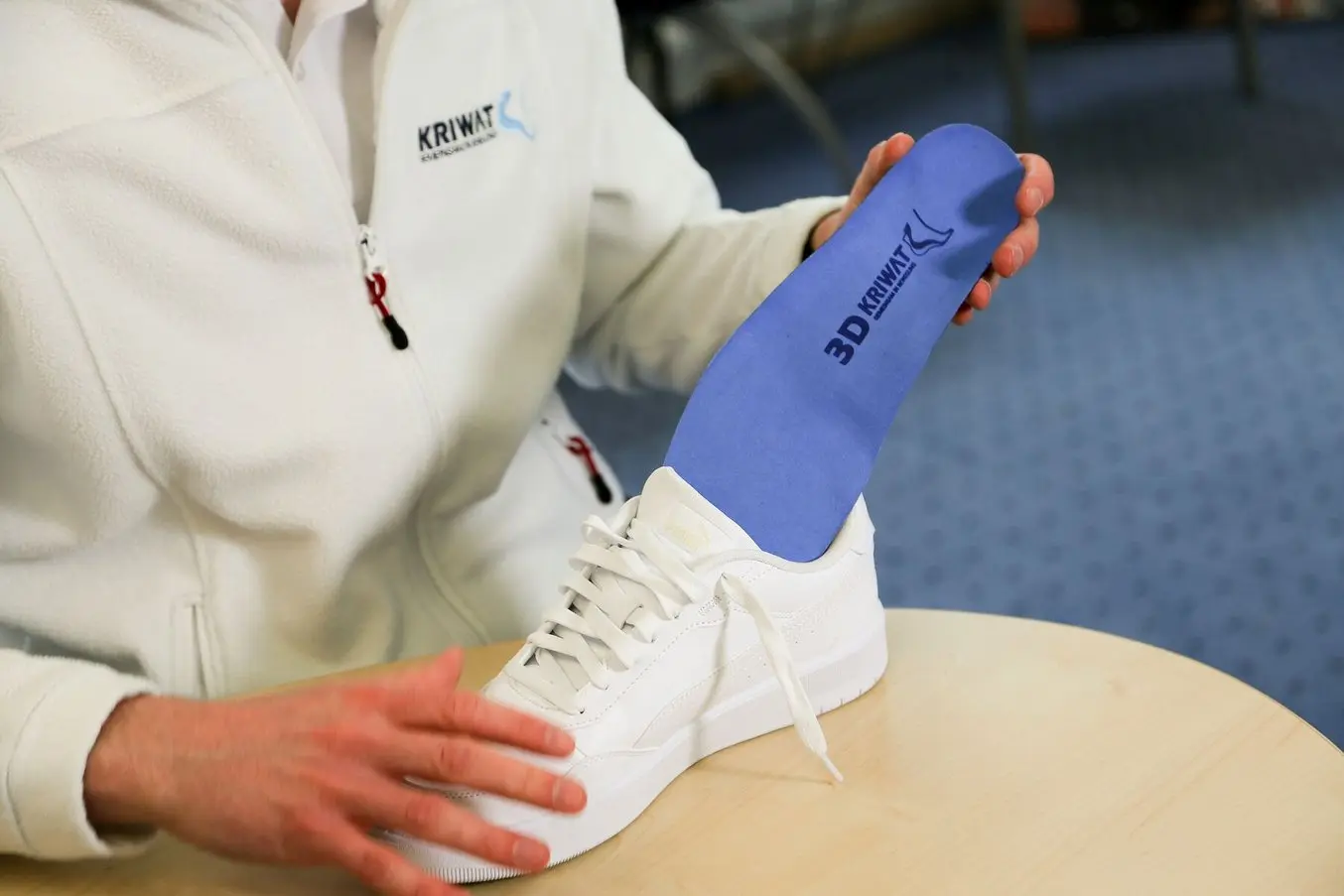
Dopo aver digitalizzato l'attuale linea di prodotti, l'obiettivo di Kriwat è offrire prodotti innovativi grazie alla stampa 3D.
Le possibilità offerte dalla libertà di design della stampa 3D SLS includono la ridistribuzione del carico durante la camminata, nonché la creazione di singoli prodotti esclusivi, di supporti impossibili da produrre con metodi tradizionali e di prodotti più sottili che forniscono comunque un sostegno ottimale per il piede in sport come la corsa e il calcio.
"Sono molto entusiasta del fatto che porteremo sul mercato innovazioni che 15 anni fa sarebbero state impossibili. Grazie alla tecnologia 3D, sviluppi che oggi non riusciamo nemmeno a immaginare diventeranno presto realtà."
Lais Kriwat, tecnico esperto in calzature ortopediche, direzione di Kriwat GmbH
Scopri di più sulla stampa 3D delle solette visitando la nostra pagina sulle applicazioni oppure contatta i nostri esperti del settore medico per domande sul workflow o sulle soluzioni di stampa 3D di Formlabs.