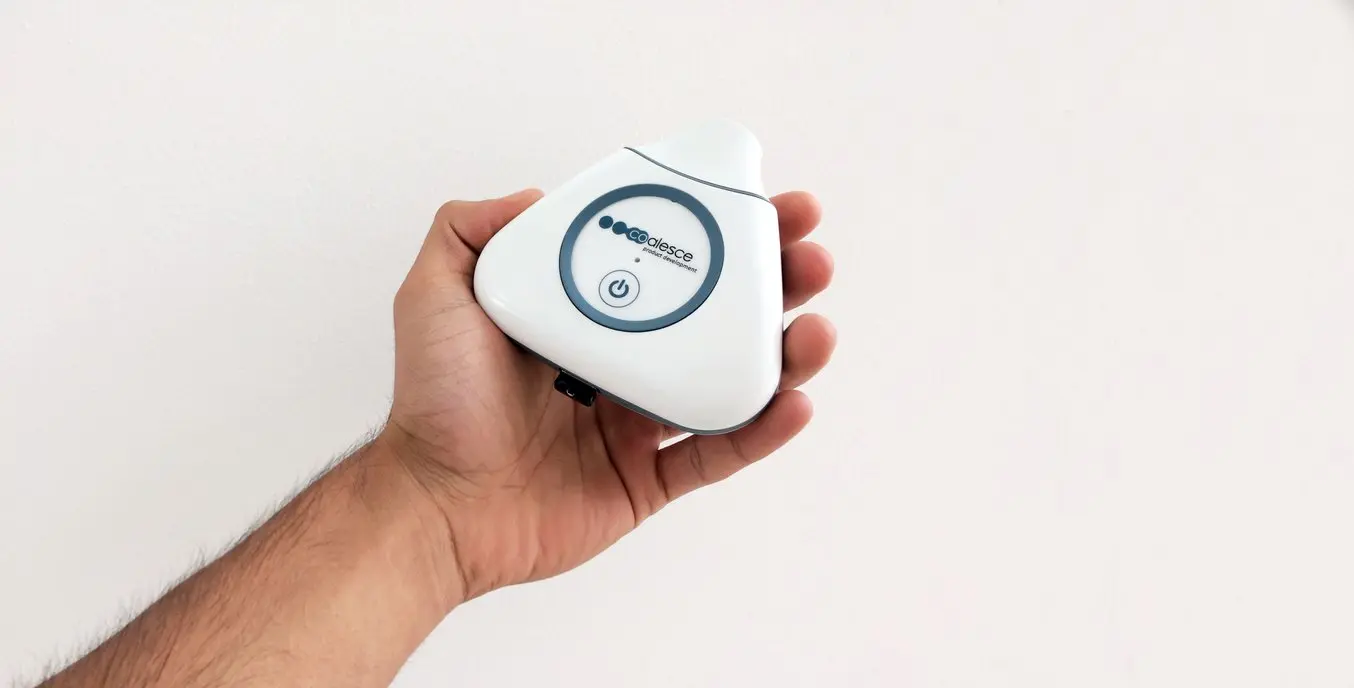
Il prototipo perfetto è quello che può essere scambiato per un prodotto già sul mercato. In particolare, i prototipi di dispositivi medici, devono aderire alle forme organiche del corpo umano, quindi, devono trovare il giusto equilibrio tra dimensioni, peso e forma e, al tempo stesso, essere totalmente funzionali per test e iterazioni.
Coalesce Product Development, un’azienda britannica che progetta dispositivi medici, sviluppa dispositivi per la somministrazione dei farmaci come inalatori e iniettori, ma anche fissaggi e attrezzatura per test. Con la stampa 3D stereolitografica (SLA), l’azienda ha trovato uno strumento per creare forme complesse e personalizzate che si dimostrano robuste, durevoli e facili da sottoporre a post-elaborazione.
In questa intervista Vinnay Chhabildas, un designer industriale di Coalesce, spiega come la stampa 3D in-house di prototipi di dispositivi medici permetta all’azienda di passare dal design a un prototipo identico al prodotto nel giro di pochi giorni anziché di settimane, e di farlo a una frazione dei costi rispetto all’esternalizzazione e allo stampaggio in silicone.
Perché Coalesce ha scelto di stampare in 3D i prototipi dei suoi dispositivi medici?
I dispositivi medici hanno spesso forme 3D complesse che sono difficili da trasformare in prototipi se si usano i metodi tradizionali. La stampa 3D permette di prendere forme complesse e personalizzate, sviluppate in CAD, e di trasformarle in prototipi fisici in un breve lasso di tempo.
Questi prototipi possono essere forme esteriori per la valutazione di fattori umani, meccanismi interni per una valutazione tecnica o anche dime e fissaggi usati con attrezzature per test.
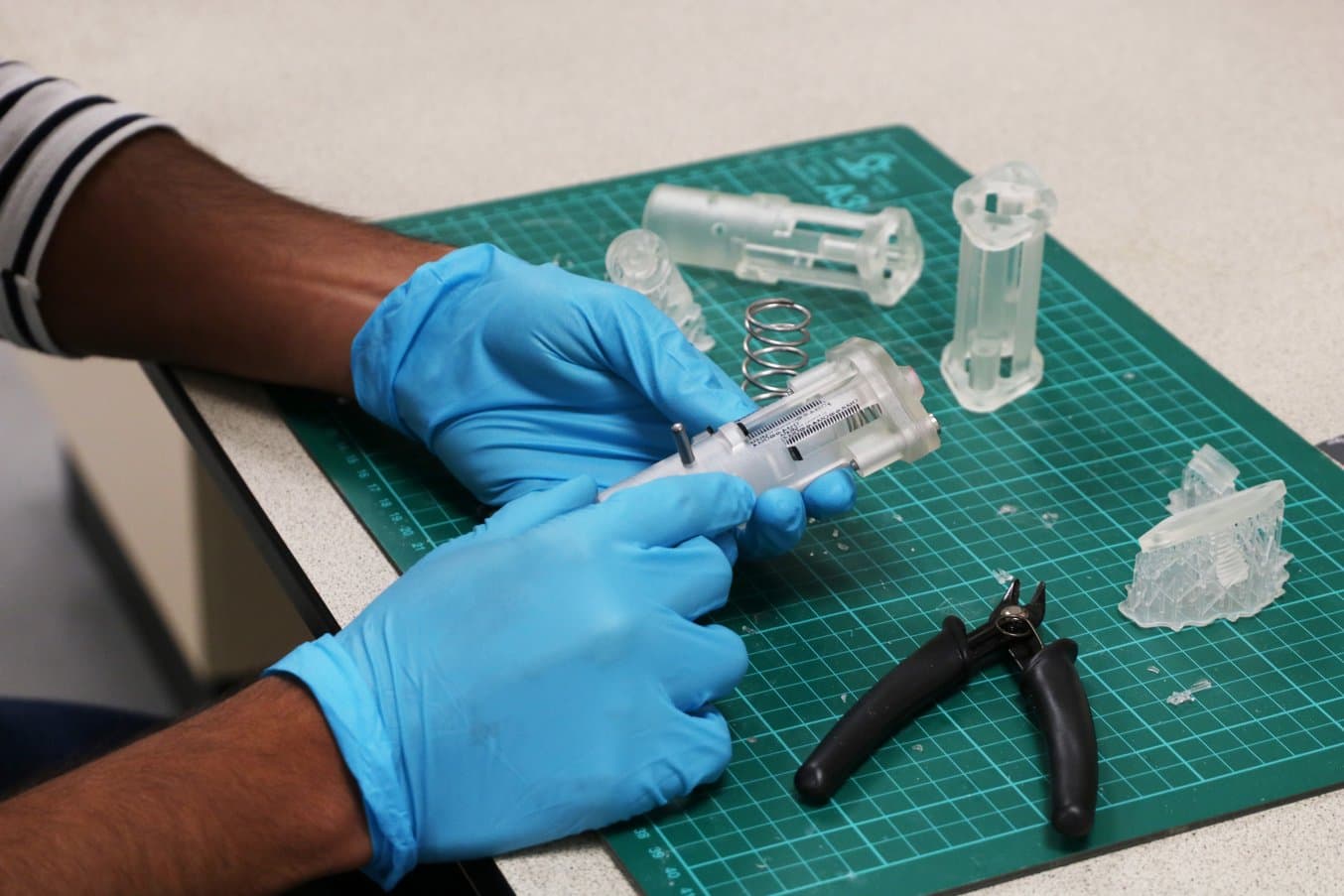
Coalesce usa i prototipi stampati in 3D per testare sia il design che la funzionalità. Chhabildas ha usato queste parti stampate con la Clear Resin per testare la velocità di rilascio di diversi tipi di molle.
In che modo i prototipi stampati in 3D ti hanno aiutato a sviluppare il Breath Profiling Device?
Il nostro Breath Profiling Device (BPD) è stato progettato per valutare digitalmente il profilo del flusso inspiratorio dei pazienti asmatici. Le macchine spirometriche, che vengono usate dai medici per misurare le funzioni polmonari dei pazienti, si dividono in due categorie: o sono costose e voluminose, oppure sono portatili ma dotate di tecnologia limitata. Il BPD è un’alternativa poco costosa e portatile alle macchine spirometriche.
Inizialmente, i prototipi stampati in 3D sono stati usati per sviluppare l’architettura del prodotto. Una volta stabilizzato il design, le parti stampate sono state verniciate e presentate alla conferenza Drug Delivery to the Lungs (conferenza sulla somministrazione di farmaci per via polmonare).
I prototipi erano così ben fatti che sono stati scambiati per prodotti già sul mercato. Alla fine i prototipi dei dispositivi sono stati usati in uno studio clinico.
Consulta le nostre guide per applicazione del primer e verniciatura per scoprire come trasformare le stampe 3D in prototipi perfetti.
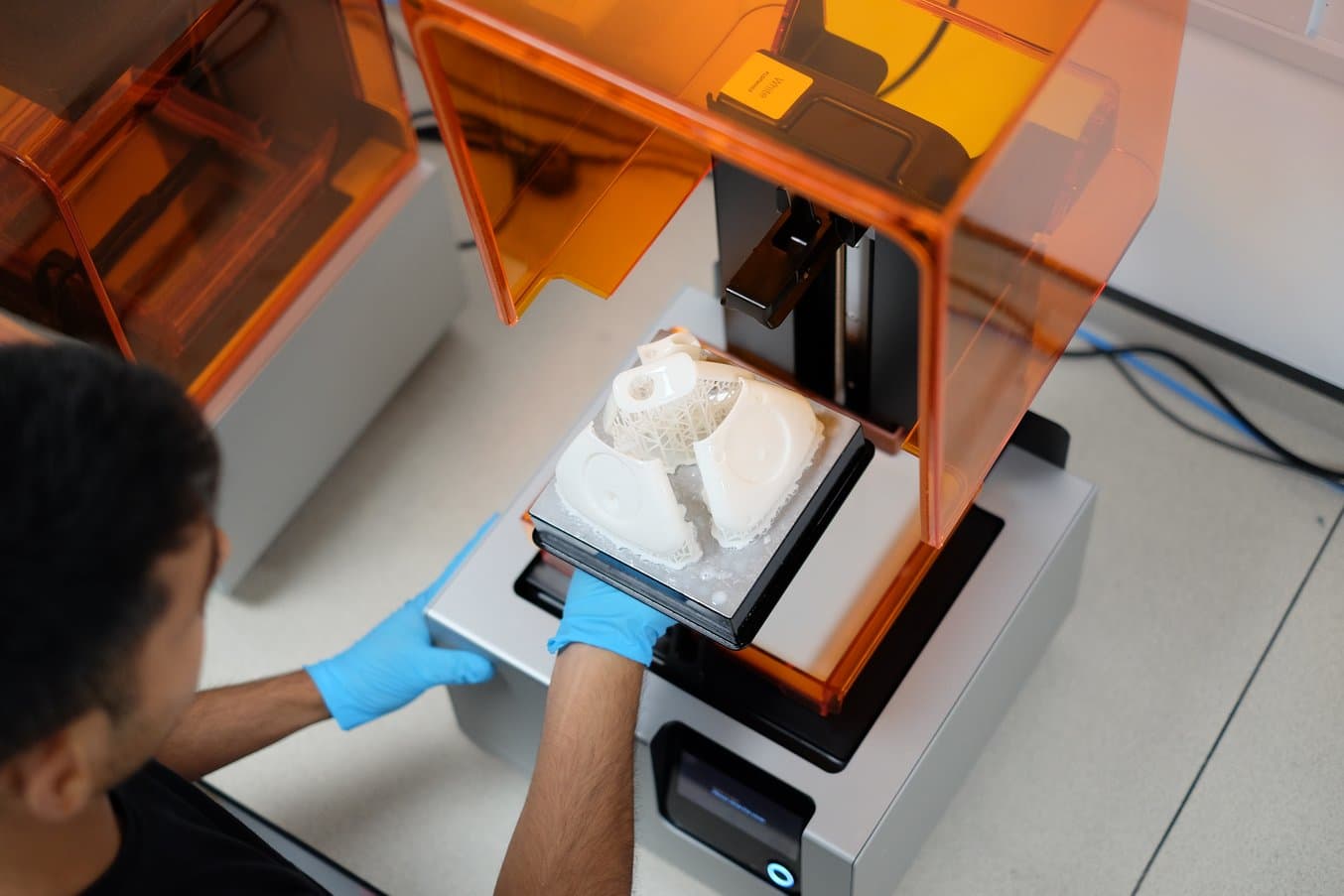
Il Breath Profiling Device di Coalesce è stato stampato in 3D con la White Resin a 25 micron.
Che impatto ha avuto la stampa 3D in-house sul vostro processo di prototipazione?
Prima di investire sulle stampanti Form 2, ci affidavamo interamente a servizi esterni per la produzione di prototipi. Invece di eseguire diverse iterazioni in un giorno, così come facciamo con la Form 2, i cicli iterativi erano più lunghi e avevamo meno controllo sulla quantità delle finiture a mano delle geometrie essenziali.
Usare fornitori esterni è all’incirca 20 volte più costoso rispetto a stampare le parti in-house. Per esempio, produrre le custodie del BPD con la Form 2 costa ~ 11 £, mentre se ci fossimo affidati a un fornitore esterno avremmo speso circa 250 £. Ma il vero guadagno è in termini di tempo: ci vogliono solo 8 ore per stampare le parti e riusciamo a rifinire e verniciare i prototipi nel giro di pochi giorni. Con un fornitore esterno ci sarebbero volute una o due settimane.
Confronto dei costi per la prototipazione di una custodia verniciata.
Stampa 3D in-house | Stampa 3D esternalizzata | |
---|---|---|
Costo | ~£11 | ~£250 |
Tempi di realizzazione per la stampa 3D | 8 ore | 1-2 giorni |
Tempi di realizzazione per parte finita | 1-2 giorni | 1-2 settimane |
Perché avete scelto la stampa 3D stereolitografica?
Coalesce ha collaborato per molti anni con fornitori di servizi esterni per la stampa stereolitografica. Abbiamo testato varie soluzioni di prototipazione, ad esempio la stampa 3D a modellazione a deposizione fusa (FDM), ma ci siamo resi conto che non erano in grado di produrre una finitura superficiale con un livello di qualità paragonabile alla stereolitografia.
La stereolitografia offre un ottimo equilibrio tra risoluzione dei particolari, finitura superficiale, resistenza, scelta dei materiali e precisione dimensionale. Dato che sviluppiamo dispositivi con parti mobili, avevamo bisogno di un metodo efficace per produrre in-house prototipi di piccoli ingranaggi. Abbiamo tenuto d’occhio i progressi delle tecnologie di stampa 3D nel corso degli ultimi anni e ci è piaciuto l’approccio di Formlabs. Quando è stata lanciata la Form 2, ne abbiamo ordinata una immediatamente e, dopo appena un paio di settimane, un’altra.
Entrambe le nostre Form 2 sono quasi sempre in uso. Abbiamo capito come ottenere i migliori risultati dagli apparecchi e dai materiali e come rifinire le parti per farle assomigliare il più possibile alle parti prodotte. Possiamo progettare parti con ganci funzionanti o perfino aggiungere inserti filettati così da avvitare insieme le parti.
Variare nell’uso dei materiali ci aiuta anche a creare le caratteristiche frizionali di cui abbiamo bisogno per verificare che i nostri meccanismi stiano funzionando come previsto. Se un meccanismo funziona in stereolitografia, è quasi certo che funzioni una volta realizzato mediante stampaggio.
Nota del redattore: dopo questa intervista abbiamo lanciato la Form 3B, una stampante 3D in-house ottimizzata per materiali biocompatibili e ingegneristici.
Scopri come l’aggiunta di filettature alle parti stampate in 3D può aiutarti a creare prototipi funzionali.
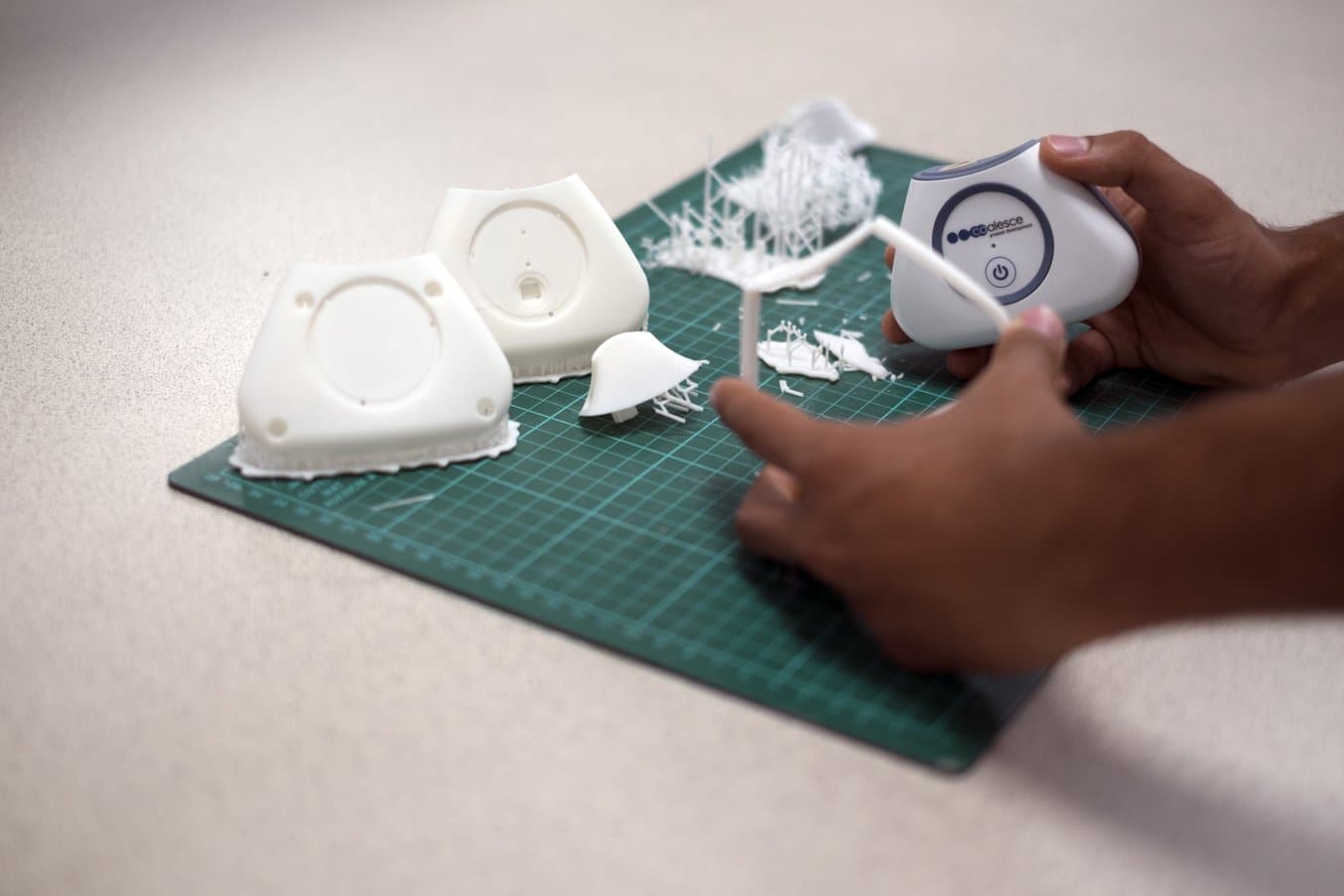
Nella fase di post-elaborazione, Chhabildas rimuove i supporti e prepara le parti stampate in 3D per l’applicazione del primer, la verniciatura e l’assemblaggio.
Come e quando incorporate diversi tipi di materiali nei vostri prototipi?
La Black Resin, la White Resin e la Clear Resin sono i materiali che usiamo più spesso, ma usiamo anche la Flexible Resin e la Tough Resin.
Nella maggior parte dei casi proviamo a replicare le caratteristiche di una parte realizzata con stampaggio a iniezione e la Black Resin, la White Resin e la Clear Resin si adattano molto bene a questo scopo. Se abbiamo intenzione di applicare forze meccaniche elevate a una parte (per esempio, un fissaggio di prova), allora useremo la Tough Resin. Se vogliamo replicare le caratteristiche di una parte in silicone o elastomero (per esempio, la guarnizione di un boccaglio), useremo invece la Flexible Resin.
Nota del redattore: dopo questa intervista, abbiamo lanciato un set di materiali biocompatibili per il settore medico. Li sviluppiamo e li produciamo in una struttura con certificazione ISO 13485.
Quanto è presente oggi la stampa 3D nel design industriale? Che cosa prevedi per il futuro?
Quando ho conseguito la laurea in design e tecnologia alla Loughborough University, ho scoperto che la stampa 3D è stata un pilastro del design industriale per molti anni.
Tuttavia, quello che è cambiato negli ultimi anni è che la tecnologia di stampa 3D è migliorata ed è diventata più accessibile. Grazie ad apparecchi come la Form 2, la tecnologia è direttamente a portata di mano dei designer industriali ed è diventata parte integrante dei processi di lavoro quotidiani.
Approfondisci l’argomento con il nostro whitepaper gratuito Engineering Fit: ottimizzare la progettazione di assemblaggi funzionali stampati in 3D.
La tecnologia continuerà a evolvere rapidamente e i progressi nella progettazione di apparecchiature e materiali apriranno nuove opportunità per il design industriale, soprattutto nel complicato settore dello sviluppo di dispositivi medici.
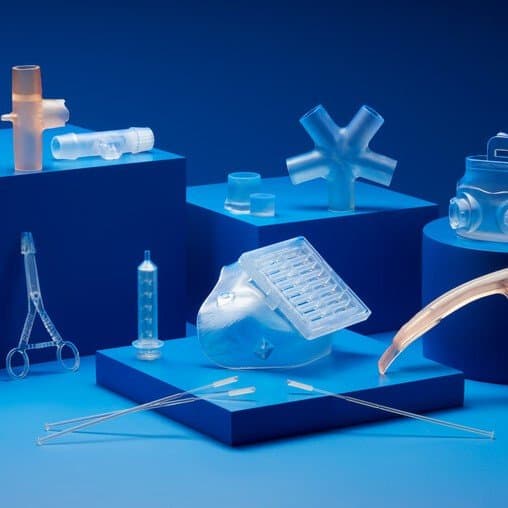
Scopri cosa puoi creare con una stampante 3D Formlabs
Scopri il nostro catalogo di materiali per il settore medico e trova quello più adatto alle tue esigenze.
Scopri di più sulla stampa 3D stereolitografica
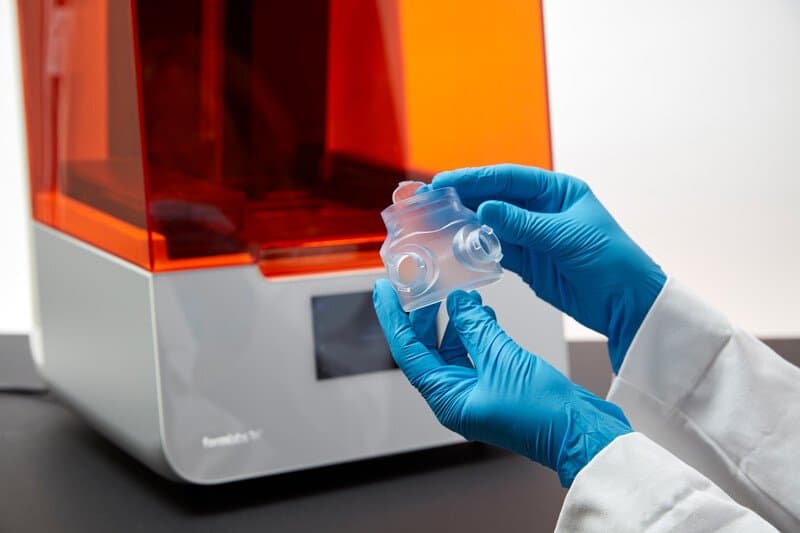
Ti piacerebbe trasformare la tua idea in formato digitale in un accurato prototipo? Contatta il nostro team vendite per il settore sanitario e scopri di più sulla stampa 3D stereolitografica (SLA) e sulla stampante 3D Form 3B di Formlabs.