In che modo il Renzo Piano Building Workshop crea plastici architettonici con la stampa 3D
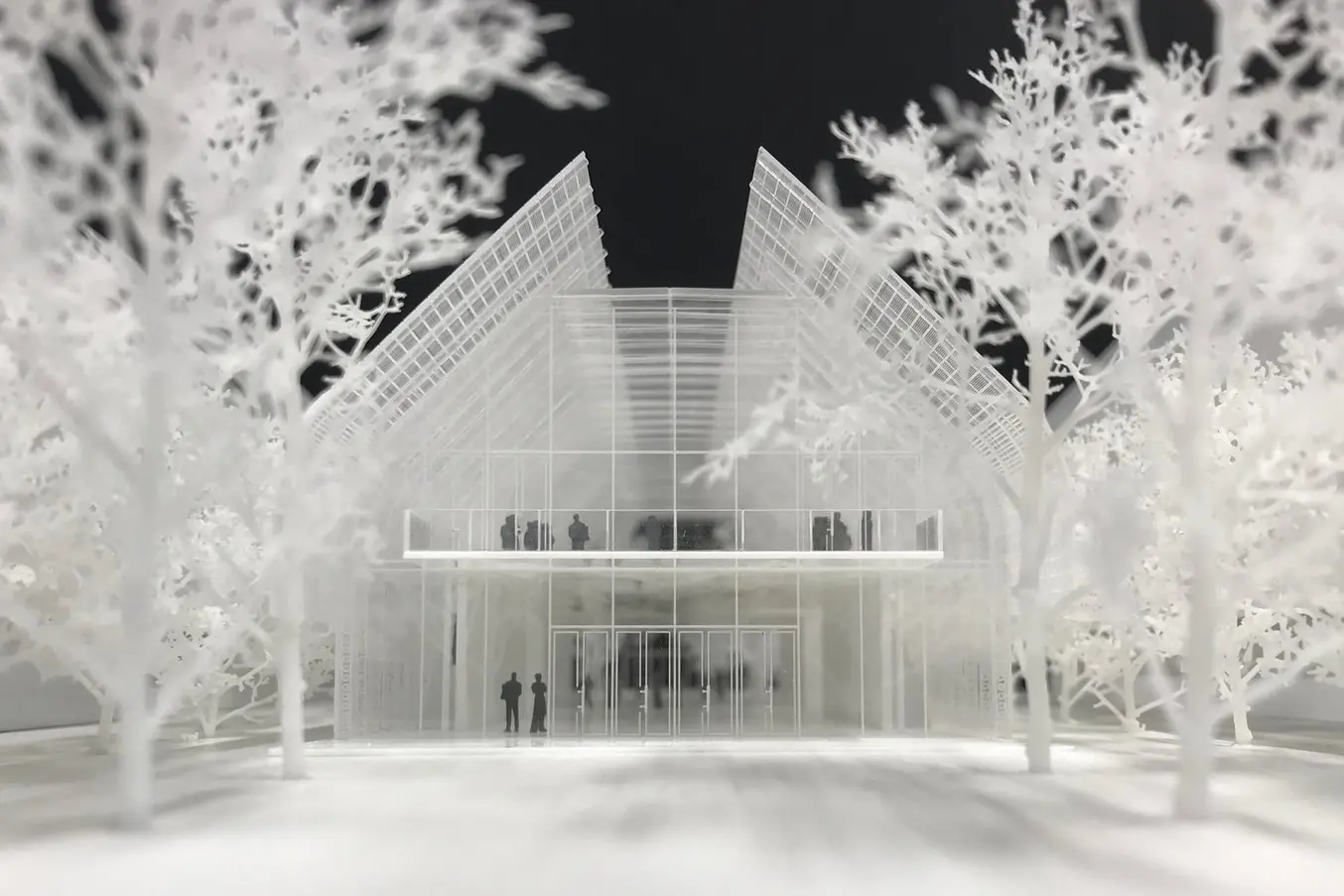
Il Renzo Piano Building Workshop (RPBW) è stato fondato da Renzo Piano nel 1981, con uffici a Genova e a Parigi. RPBW è guidato da 9 partner, tra i quali il fondatore e vincitore del Premio Pritzker Renzo Piano.
Lo studio impiega 110 architetti, coordinati a uno staff di supporto di 30 professionisti, tra cui artisti di visualizzazione 3D, modellisti, archivisti, personale amministrativo e di segreteria.
RPBW ha una vasta esperienza nel lavoro con team multidisciplinari su progetti di costruzione in Francia, Italia e in altri paesi. Lo studio ha realizzato oltre 140 progetti nel mondo.
I team di architetti sono coinvolti nei progetti dall'inizio alla fine. Di solito forniscono servizi completi di design architettonico e consulenza nella fase di costruzione. Le competenze di design del team vanno oltre i semplici servizi architettonici: il lavoro include anche servizi di design degli interni, pianificazione urbanistica e paesaggistica e allestimento mostre.
Continua a leggere per scoprire come Francesco Terranova e Dimitri Lange, modellisti di RPBW nella sede di Genova, creano plastici architettonici complessi combinando strumenti tradizionali e tecnologie digitali come la stampa 3D.
Progettare per costruire
Uno dei concetti cardine del lavoro dell'RBPW è quello di "progettare per costruire", così da garantire sin dal principio che ogni dettaglio funzioni e rappresenti la costruzione finale nei minimi particolari. Nei laboratori di RPBW, per ciascun progetto vengono realizzate centinaia di plastici su piccola e larga scala per testare le diverse proposte.
Questi plastici sono una parte essenziale del flusso di lavoro degli architetti, che spesso si incontrano per esaminarli e valutare le idee per le varie parti del progetto.
"A volte la differenza è davvero minima. Ad esempio un bordo è più liscio di quello precedente. Spesso non so nemmeno come facciano gli architetti a notarlo", afferma Terranova con un sorriso.
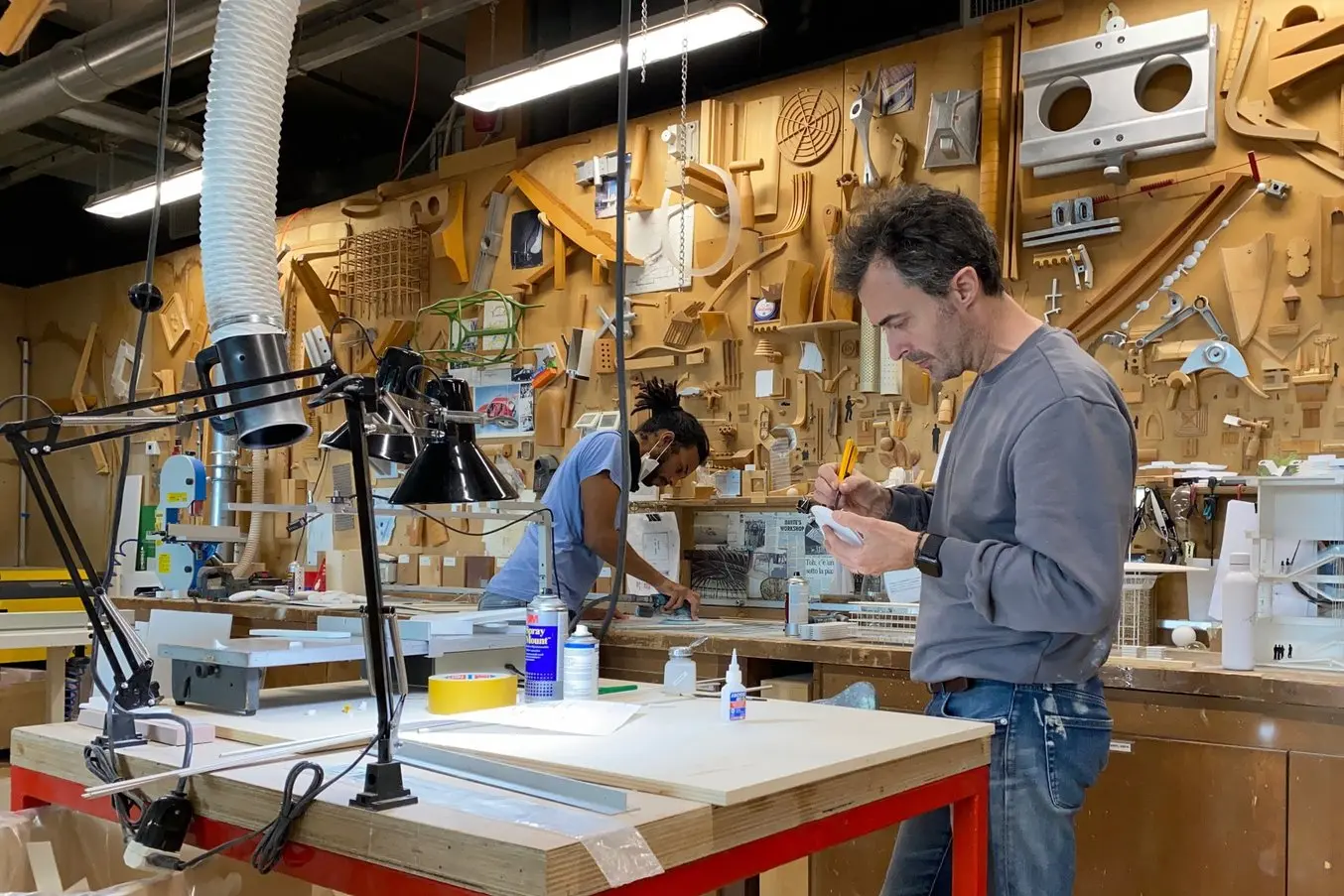
Francesco Terranova e Dimitri Lange, modellisti di RPBW. Per ciascun progetto vengono realizzate centinaia di plastici su piccola e larga scala per testare le diverse proposte.
Spesso gli architetti apportano modifiche direttamente ai plastici e più avanti possono riprodurle in CAD. A intervalli di alcune settimane anche i clienti si recano presso lo studio per ricevere aggiornamenti sui progetti, e in queste occasioni i plastici sono fondamentali, perché rendono ben visibili le migliorie.
"I nostri plastici cambiano ogni giorno, o addirittura ogni ora. Gli architetti modificano il progetto con grande rapidità e spesso non abbiamo nemmeno il tempo di farlo manualmente. Quindi dobbiamo trovare un metodo più veloce", spiega Terranova.

Per accelerare la produzione di plastici in scala i modellisti di RPBW utilizzano una stampante SLA Form 3.
Come vengono realizzati i plastici in scala
"Per capire le dimensioni reali del plastico, innanzitutto lo stampiamo in scala su carta. Se il nostro plastico misura un metro per un metro, dobbiamo decidere come dividerlo, perché spesso, se il modello è troppo voluminoso per essere spostato o trasportato, dobbiamo considerare la possibilità di costruirlo già suddiviso in due o più parti, che verranno riassemblate a destinazione", afferma Terranova.
I modellisti si servono di strumenti tradizionali per realizzare i plastici manualmente e di strumenti digitali come stampanti 3D, fresatrici CNC e frese laser per creare le varie parti.
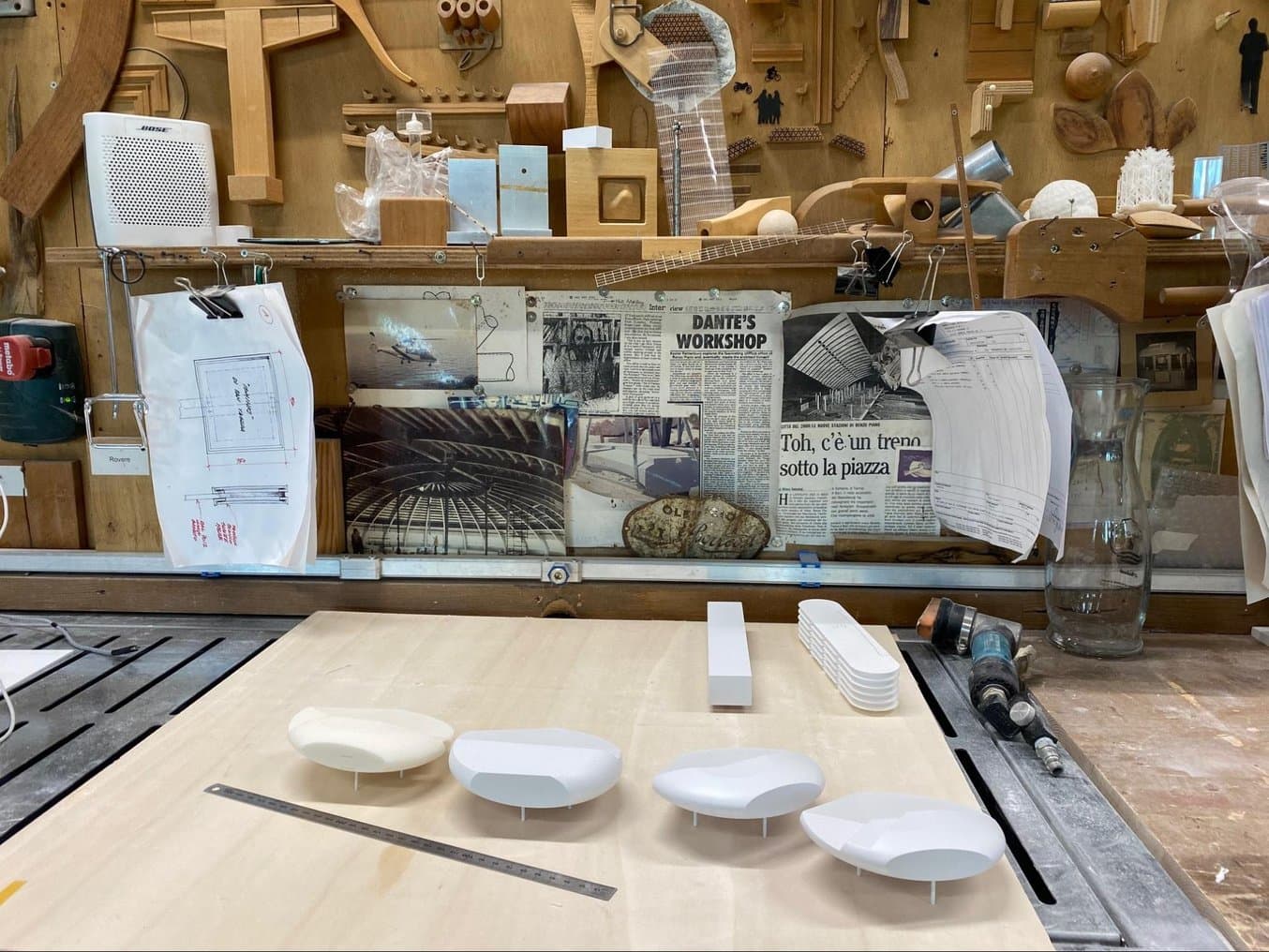
La stampa 3D è perfetta per geometrie che sarebbero complicate da realizzare manualmente, ad esempio sfere e superfici curve.
"Spesso un plastico è il risultato della combinazione di tutte queste tecnologie. Ad esempio per la base del plastico di solito è più efficace ed economico l'uso di una macchina a controllo numerico e di materiali robusti. Alcuni edifici sono realizzate con fresatrici CNC o frese laser", spiega Terranova.
"Certe geometrie, come ad esempio sfere e superfici curve, sarebbero complicate da realizzare manualmente. È quasi impossibile e ci vorrebbero diversi giorni, anziché poche ore. Ma se si ricorre alla stampa 3D naturalmente si può riprodurre con precisione ciò che si vede nel file 3D. Cerchiamo di sfruttare il più possibile le nostre stampanti 3D per facilitarci il lavoro."
Francesco Terranova
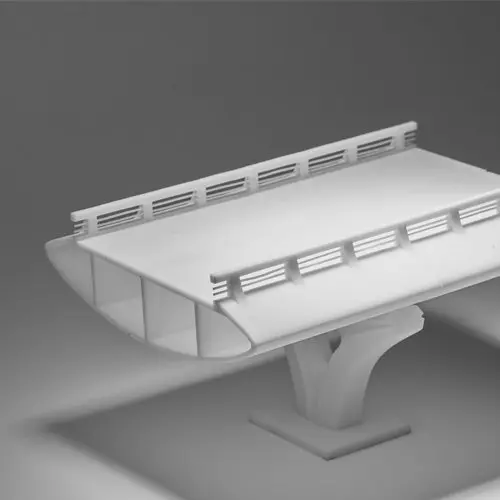
Stampa 3D di plastici architettonici: guida alla creazione strategica del modello e al workflow del software
Questo whitepaper suggerisce pratiche intelligenti in fase di modellazione, come la scelta della giusta dimensione scalare o la progettazione per l'assemblaggio, trattando anche la post-elaborazione e l'utilizzo di tali strategie nei più comuni ecosistemi software.
I modellisti utilizzano la stampa 3D anche per riprodurre parti elaborate come scale e alberi, che richiederebbero molto tempo se realizzate manualmente. Ad esempio hanno stampato in 3D i complessi giunti strutturali dei pilastri per il plastico del nuovo ponte San Giorgio di Genova, che ha di recente sostituito il vecchio ponte Morandi, crollato due anni fa.
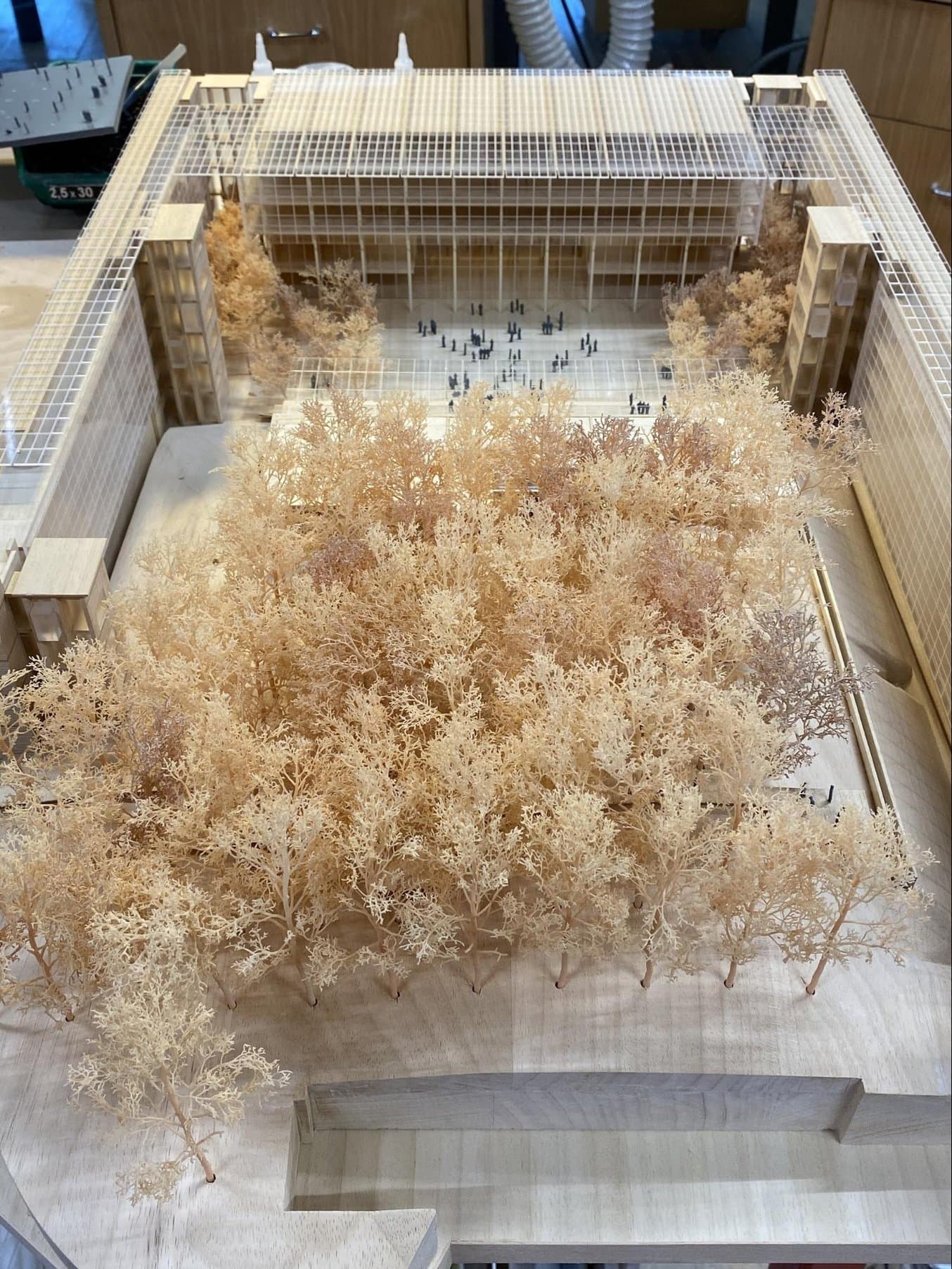
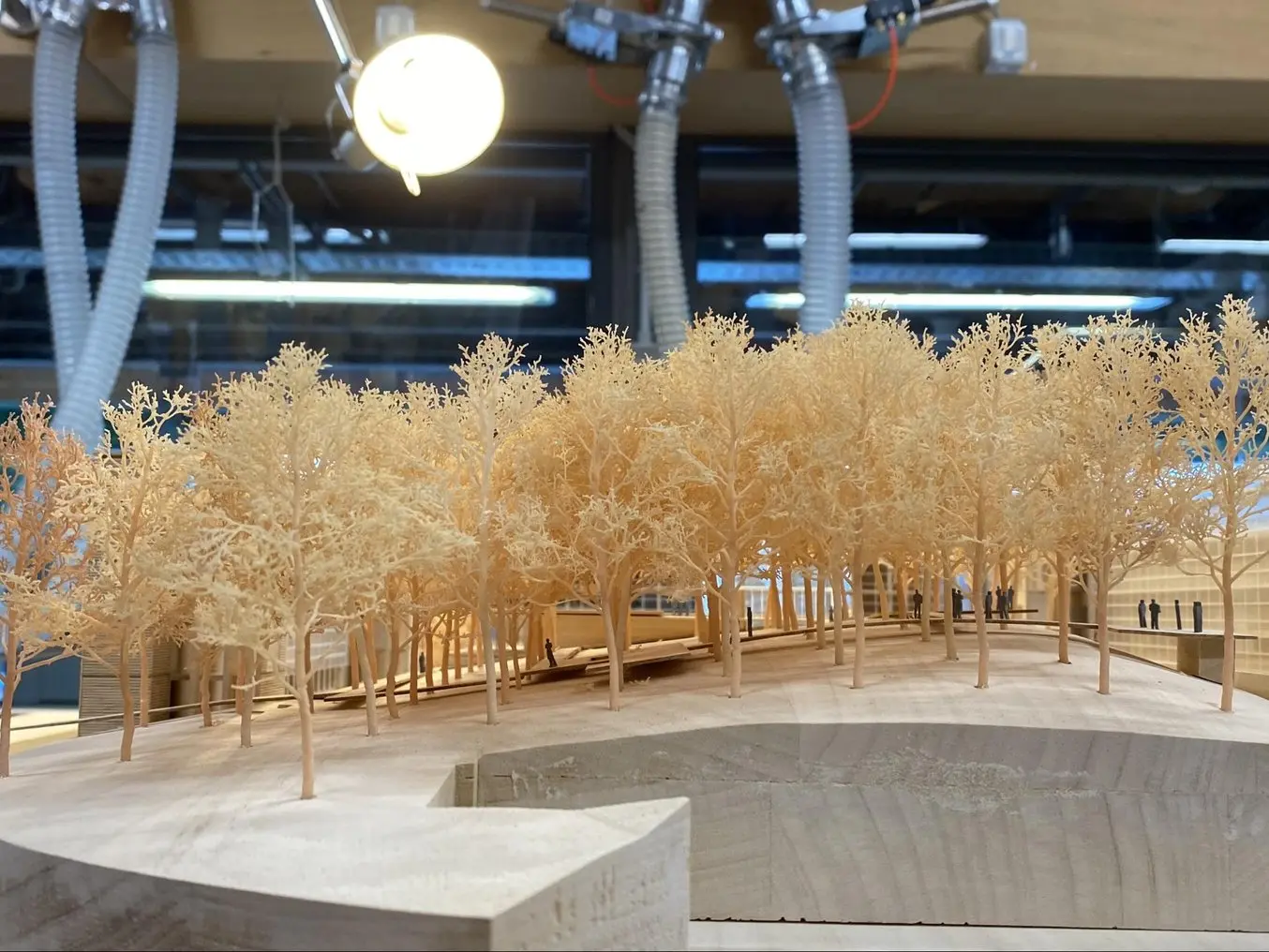
I modellisti uniscono diverse tecnologie per creare i plastici in scala. Le parti più elaborate di questo plastico, come gli alberi, sono state stampate in 3D con una stampante Formlabs, mentre altre sono state realizzate con fresatrici CNC o frese laser, oppure create manualmente.
"Abbiamo realizzato dei plastici per l'Academy Museum of Motion Pictures di Los Angeles. Ha una forma simile a quella di una sfera schiacciata. Credo che sia cambiata un centinaio di volte. Ogni giorno dovevamo creare un nuovo plastico, con modifiche minime rispetto al precedente. L'unico modo per farlo così velocemente era la stampa 3D. Il vantaggio è che possiamo avviare la stampa la sera e la mattina dopo, quando torniamo in studio, troviamo il plastico pronto. Così non perdiamo tempo durante la giornata."
Francesco Terranova
Gli architetti usano il software CAD Autodesk Revit per creare file digitali, ma questi a volte non possono essere usati direttamente per creare plastici in scala fisica.
“I file esportati non sono pronti per l'utilizzo che ne facciamo. Gli edifici sono completi di tutti i dettagli: tubature, rubinetti, mobili ecc. Per il plastico non abbiamo bisogno di questi dettagli. Quindi è necessario pulire il file e valutare lo spessore adatto. Ad esempio una parete spessa 10 cm, in scala 1 a 200, si riduce a 0,2 mm. Questo valore non è adatto agli apparecchi, quindi dobbiamo modificare i file e adattarli a un modello 3D", spiega Terranova.
Inoltre, i file digitali per le stampanti 3D necessitano di superfici con volume chiuso. Alcuni design possono essere corretti automaticamente, ma spesso i modellisti devono ridisegnare l'intero plastico.
Come scegliere la tecnologia di stampa 3D giusta per te
Lo studio per la realizzazione dei plastici di Genova ha acquistato la sua prima stampante 3D sei anni fa. Da allora hanno aggiunto alla flotta altri tre apparecchi che usano tre diverse tecnologie e il team ne ha testati molti altri.
"Sei anni fa abbiamo cominciato con un apparecchio che usava materiali in polvere [e si serviva della tecnologia binder jetting]. Non era molto utile perché era molto sensibile all'umidità e non era abbastanza preciso. Così siamo passati alla Form 2 [che sfrutta la tecnologia di stampa 3D stereolitografica (SLA)]. Poi abbiamo aggiunto una [stampante di grande formato a getto di materiale] 3D Systems, che utilizza la resina per stampare. E abbiamo anche una piccola stampante 3D FDM che funziona con acido polilattico e acrilonitrile-butadiene-stirene", spiega Terranova.
"Ciò che apprezziamo di più degli apparecchi Formlabs è la solidità e la resistenza del materiale, ma anche la precisione dei modelli. Le resine Formlabs, una volta stampante, sono molto semplici da levigare. E questo è un grande vantaggio, perché verniciamo sempre i plastici. Anche quando usiamo la White Resin, il bianco non è esattamente lo stesso che usiamo per i nostri plastici. Quindi dobbiamo verniciare le parti del modello stampate in 3D, nonché le parti create con macchine a controllo numerico e altri strumenti. Perciò il fatto che sia semplice da levigare è molto utile", conclude Terranova.
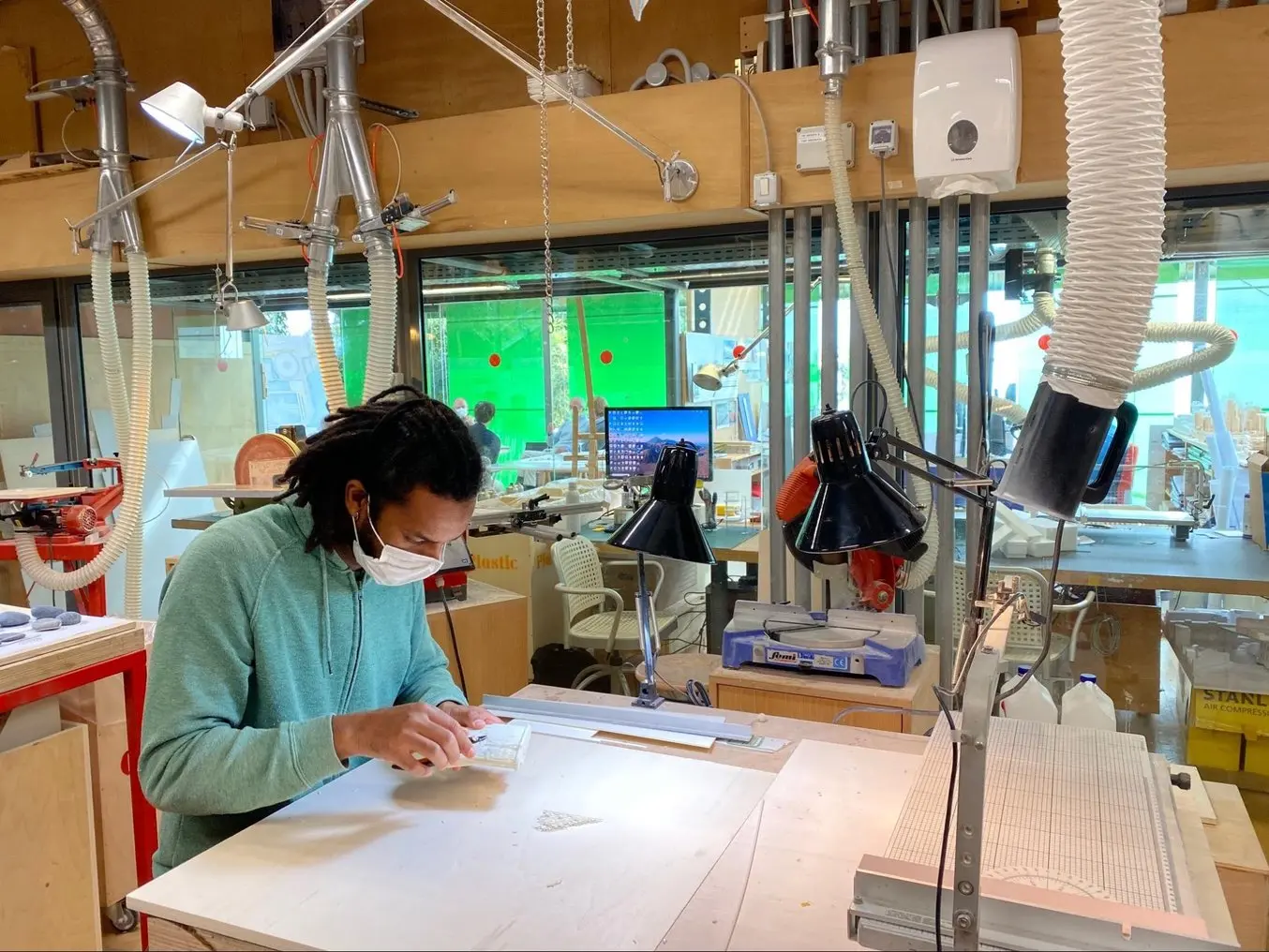
Le parti stampate in 3D possono essere levigate e verniciate per rispecchiare alla perfezione lo stile del plastico in scala.
"La stampante 3D FDM non ci consente la stessa precisione. Vediamo tutte le linee degli strati e, per le nostre esigenze, questo non è un buon risultato. La stampante 3D System è molto precisa e questo è utile quando dobbiamo realizzare modelli di particolari architettonici su larga scala (1:5, 1:10). Ma il materiale non è così solido una volta che è stato pulito. Ad esempio, se li stampiamo in 3D con quell’apparecchio, gli alberi cadono dopo mezza giornata al massimo. Sembra che si sciolgano", spiega Terranova.
Di recente lo studio ha sostituito la Form 2 con l'ultima stampante SLA di Formlabs, la Form 3, che ha permesso al team di stampare alcuni dei plastici più complessi e di risparmiare tempo sulla post-elaborazione.
"Gli alberi rappresentavano un grande sfida, perché erano molto fragili, molto sottili. Abbiamo cercato di realizzarli con la Form 2 [e con le altre stampanti, ma si rompevano facilmente]. Con la Form 3 non abbiamo questo problema e riusciamo a stamparli in 3D. Anche rimuovere i supporti risulta più semplice con la Form 3, perché ne possiamo usare di più piccoli", afferma Terranova
Il futuro del modellismo
Lo studio di Genova ha di recente trasferito la Form 2 all'ufficio di New York, così ora tutte tre le sedi di RPBW utilizzano stampanti 3D per realizzare i plastici. Terranova e Lange sperano che l'uso di strumenti digitali incoraggi lo scambio di conoscenze tra le filiali.
Terranova è inoltre convinto che in futuro le stampanti 3D saranno strumenti essenziali in quasi tutti i laboratori e gli studi di architettura.
"Penso che sia il futuro, anzi ne sono certo. Prima saranno necessari alcuni cambiamenti per permettere a ciascun modellista di utilizzare questa tecnologia. Ad esempio i costi dovranno scendere. Ma [Formlabs] ha già fatto un passo in questa direzione", conclude Terranova.