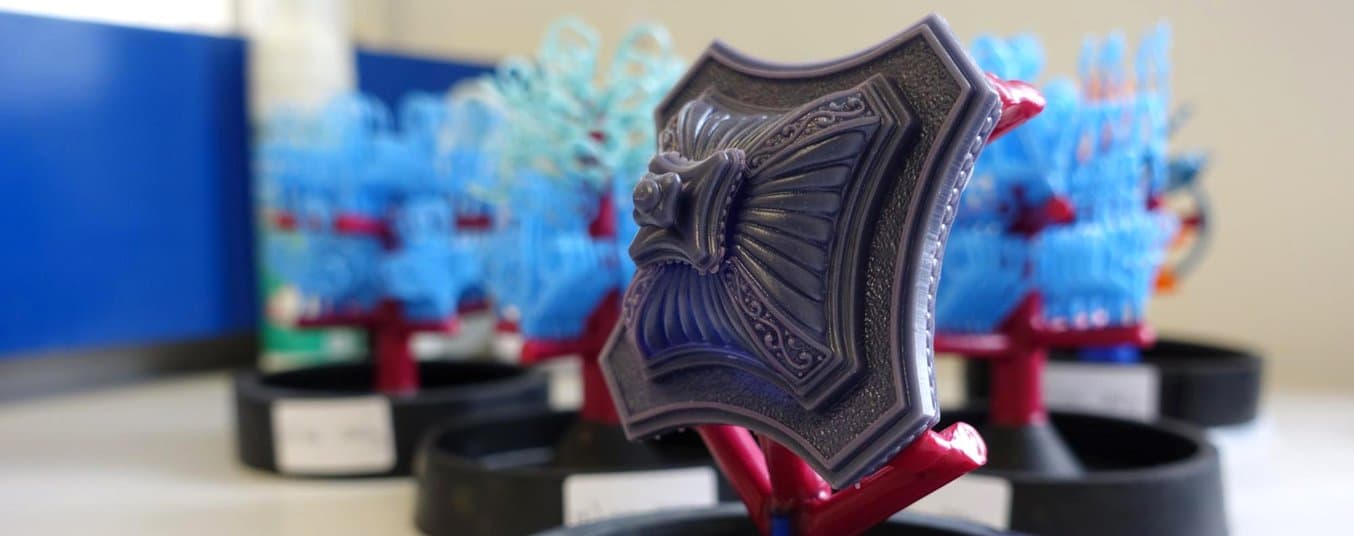
While some casting houses solely cast wax and resin pieces for independent jewelry designers, facilities with their own in-house machinery are able to not only cast, but also 3D print customer parts.
The number of casting houses accepting design files from jewelers to 3D print, cast, and polish is increasing.
Casting houses are finding more value in acquiring a desktop 3D printer to complement their industrial additive manufacturing tools in order to serve the ever-growing wave of “digital” jewelers.
The Rise of the Digital Jeweler
Digital jewelers work primarily with CAD and fabricate designs using 3D printing technology. In this post, we dive into the stories of two casting houses, Q Branch Bespoke Casting and Ulrich Wehpke GmbH, who have used the Formlabs Form 2 desktop stereolithography 3D printer as part of their all-inclusive printing and casting service for jewelry customers.
Q Branch Bespoke Castings and Wehpke GmbH are part of our list of Recommended Casting Houses for Formlabs resins.
Adding New Value to Bespoke Designs
Q Branch Bespoke Casting, based in the United Kingdom, was founded in 2016 by Dan Roe, who has been 3D printing since 2006 and casting since 2008.
Roe has been in the jewelry business since he was 15 years old. His company specializes in platinum, palladium, and gold castings, the most difficult metals to cast in the trade. Roe and team have been using the Form 2 since December 2017 as the only resin-based 3D printer in their facility.
3D Printing at Q Branch
Q Branch Bespoke Casting works with jewelry designers, manufacturers, and goldsmiths to 3D print CAD models in resin and cast parts into metal. They also create rubber molds to inject waxes into and work with 3D scanning.
The Form 2 is a part of the team’s daily workflows and offers the convenience and speed of prototyping designs for customers to view before making a final decision. Previously, the company had used an EnvisionTEC machine.
“We use the Form 2 most frequently for creating models for our customers and their clients to view and try on before taking the plunge in precious metal,” Roe said.
“A precious metal casting can only be as good as the model that is supplied. The Form 2, relative to the cost, provides a great balance of the two key components required: detail and surface finish.”

The Form 2 complements the casting house’s facility of industrial 3D printers, and often relieves bottlenecks in their production workflow during the busy months.
“We use other 3D printers as well as the Form 2, which work well, but are slow. We recently had a big order for some really large pieces that would be assembled to create a box after they were cast. They would have tied up our other printers for days and days, but with the Form 2, I was able to have all the parts printed over the weekend,” Roe said.
“It’s a great machine for filling in the gaps–once the other printers have all been started, we often receive orders right at the end of the day. We have the capacity to grow the orders on the Form 2 so they are ready to invest the following day.”
Learn how students at the at Copenhagen School of Design and Technology (KEA) in Denmark use digital tools alongside traditional techniquest to stay ahead the curve and learn how to grow their businesses.
Evolution of Jewelry Making from a Caster’s Perspective
3D printing technology has drastically changed the jewelry production process, and Q Branch has used their knowledge of the technology to evolve with these changes.
“From the casting angle, I have seen things progress from hand-carved waxes, handmade master patterns which are molded, through to 2-axis wax milled models and the dawn of CAD-CAM to 3D printed thermoplastics and the current crop of photopolymer resins and stereolithography (SLA) and digital light processing (DLP) machines,” Roe said
“The proliferation of affordable 3D printing is making it so much easier to go the bespoke route and iterate on designs if you are planning for and putting together a collection.”
3D Printing as a Core Business Model
Traditional casting houses are moving from wax-based casting methods and industrial 3D printers to using desktop 3D printers like the Form 2 for printing and casting.
Ulrich Wehpke, a casting house based in Krefeld, Germany, switched to SLA-based 3D printing about three years ago. Having been in the casting business for more than 30 years, a team of three goldsmiths cast a range of metals including silver alloys, gold alloys, and platinum. They are known to cast engagement and wedding rings, as well as engraved men’s rings. Additionally, Wehpke has a supplementary business working in jewelry and watch repair.
- 1967: Wehpke founded by Ulrich Wehpke as a goldsmith workshop with a small store.
- 1980: Wehpke closed their store and began focusing entirely on their workshop to service jewelers throughout Germany.
- 2000: Purchased their first 3-axis CNC mill.
- 2001: Began using Rhino CAD.
- 2005: Acquired their first 5-axis CNC mill and a Solidscape T66 waxplotter and began to offer CAD, prototyping, and casting services, combined with their classic goldsmith workshop, to make finished jewelry products.
- 2008: Purchased their first industrial 3D printer.
- 2011: Began casting their first resin models.
- Today: 3D printing is a core part of the business, printing and casting models printed on the Form 2.
For a couple of years using Solidscape and EnvisionTEC were the core of the printing side of their business, along with using Asiga Pico for building models.
“Our first machines needed many repairs and took too much time to start up unless we were running it 24/7,” Wehpke said. “That’s when we decided to focus solely on resin printing for our customers. A friend of mine bought a Formlabs Form 2 printer and did some test prints for us. We were so impressed, the details were much better than we had initially expected.”

Expanding the Casting Business With the Form 2
Wehpke purchased a Form 2 3D printer and began printing models with Formlabs Castable Resin.
A side effect of working with Formlabs products was that the company began to receive customer models from other Form 2 owners to cast their designs.
“Since Formlabs became popular, many companies started sending their resin models printed on the Form 2 for us to cast, and this became a strong part of our business model,“ Wolfram said.
"Today’s independent jewelry designers who have adopted a digital workflow have begun working more frequently with a casting house like Wehpke, who knows how to cast Formlabs material with ease. Wehpke’s advantage is not only being able to cast resin-based material but to be intimately familiar with printing on the Form 2 and with SLA technology.
Wehpke uses the Form 2 largely to print Eternity and Solitaire rings, styles he finds suitable for printing due to their durability and attractiveness.
Casting Houses Evolving Towards Specialization
Wehpke is known for casting platinum-iridium. This material has become more popular over the years, but not many companies are able to cast this special metal.
“It took some time to find a way to obtain the best, consistent casting results with the wide range of metals we work with,” Wehpke said. “But it is worth all the work because now we can cast our own models and the models that customers send us with ease.”

Differentiating in an Evolving Jewelry Industry
Q Branch Bespoke Castings and Wehpke GmbH are only two of many casting houses offering 3D printing services in addition to their bread-and-butter portfolio of casting and finishing.
The Form 2 is an essential tool for these casters, who look to have a reliable, affordable, and accurate 3D printer that can respond to customer requests. Coupled with having the breadth of experience in casting resin-based models, which gives them an advantage over traditional casting houses who still largely cast wax models.
“The technology is absolutely amazing, but as a trade, we must not forget the traditional skills and apply that knowledge to our use of it in jewelry,” Roe said. “It’s a very exciting time to be working in jewelry making.”
Learn more about how the Form 2 desktop SLA 3D printer can benefit your casting facility, or contact Formlabs for more information on becoming a Formlabs Recommended Casting House.
See the quality firsthand with a complimentary sample part of our new Castable Wax Resin. This wax-filled material is designed for highly detailed and challenging jewelry and provides a reliable direct investment casting with zero ash content and clean burnout.