Combining MJF and SLS Technologies to Make Science Fiction Feel Real at Legacy Effects
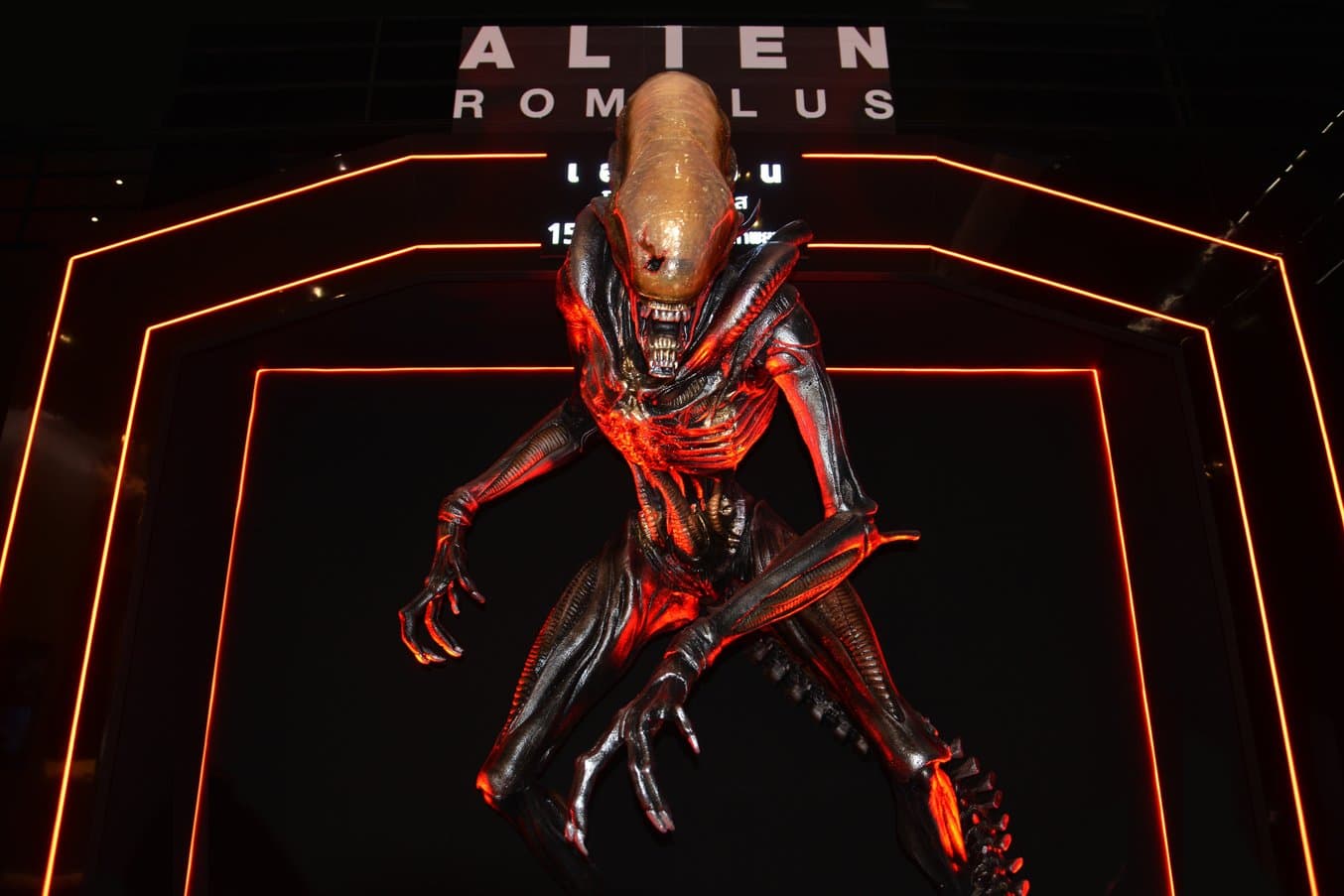
Legacy Effects created the xenomorph from Alien: Romulus using SLS and MJF 3D printing technologies as well as other traditional and advanced fabrication techniques. Several parts in the xenomorph’s hands were printed in TPU 90A Powder on the Fuse 1+ 30W. All photos courtesy of Legacy Effects.
The feelings evoked by Baby Yoda, Alien Romulus, or Iron Man may span the full range of human emotion, but they all are only possible because, just for a little while, we can believe these characters are real. The necessary suspension of disbelief is accomplished through the work done behind the scenes that makes these characters as endearing, terrifying, or inspiring, as possible.
For decades, Legacy Effects has been behind the scenes of the biggest blockbusters in history, crafting armor for superheroes or walking animatronics for galaxies far, far away. The team at Legacy Effects merges artistry with technology to create worlds that we feel are possible partly because 3D printing is one of the foundational pillars of their workflow. Legacy Effects’s 3D Lab Manager Samuel McBride spoke to us about how they evaluate different technologies for efficacy, and how adding scalable selective laser sintering (SLS) 3D printing with the Fuse Series has opened new possibilities in their creative process.
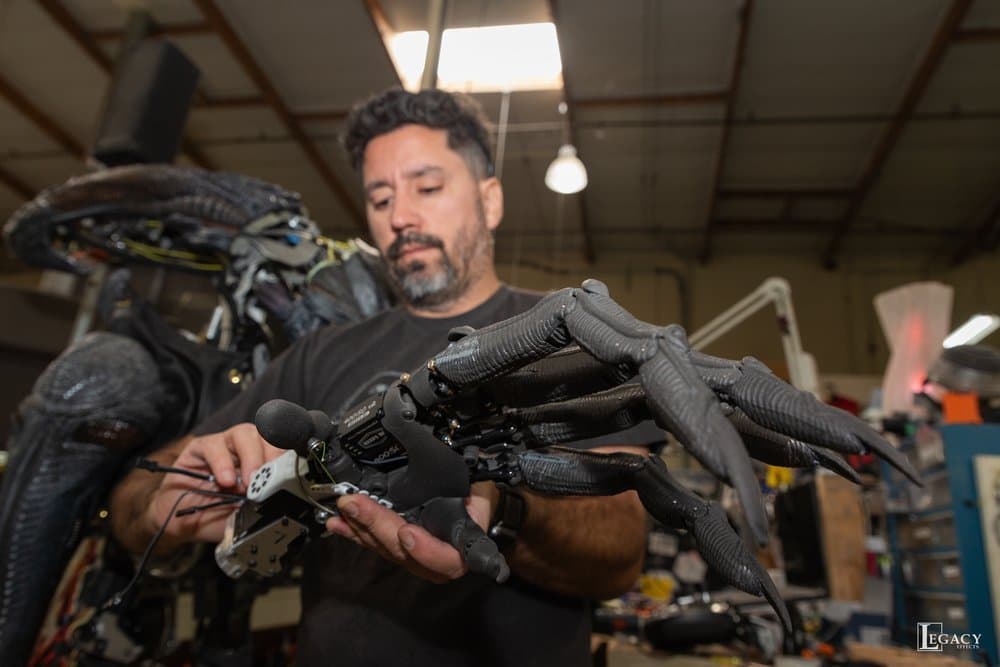
Combining MJF and SLS 3D Printing at Legacy Effects
Learn how Legacy Effects leverages both HP's MJF 500 Series and Formlabs' Fuse SLS Ecosystem to increase material versatility and throughput. Get your questions answered about comparing the two technologies from an HP Certified Engineer who relies on both MJF and SLS printers every day.
Practical Effects in the Digital Age
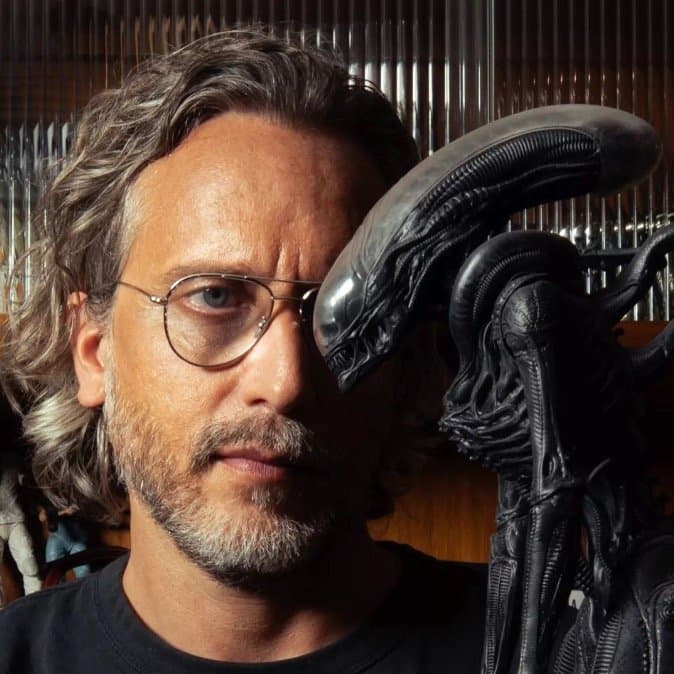
Alien: Romulus director Fede Alvarez likes actors to work with physical effects and animatronic monsters rather than CGI — their physical presence helps create the terror that gets audiences hooked.
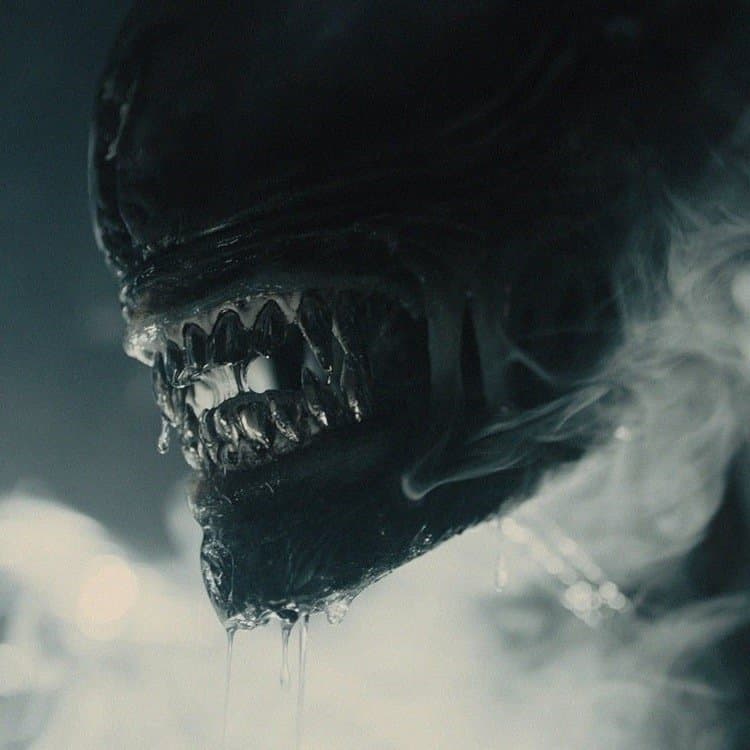
3D printing is one way Legacy Effects creates massive, larger-than-life monsters that stretch the imagination while still inspiring very real fear.
Most modern movie fans are familiar with footage of actors playing against green screens or tennis balls that take the place of their imagined counterparts, who will be added in later. But even in today’s modern, increasingly digital workflow, tangible set-pieces are still preferable in some situations, and for some directors.
“It comes down to what the vision is — CG moves in a way that’s sleeker and flows, but for classic styles of characters, we do that with animatronics to have that physical presence in the space,” says McBride. Certain directors, like Fede Alvarez, the director of 2024’s Alien: Romulus, like to provide practical effects so that actors have something to work off of. Legacy Effects jumped in on the 2024 summer blockbuster to design and build the larger-than-life aliens hunting young crew members in the tenth installment of the Alien franchise.
Early Additive Adopters
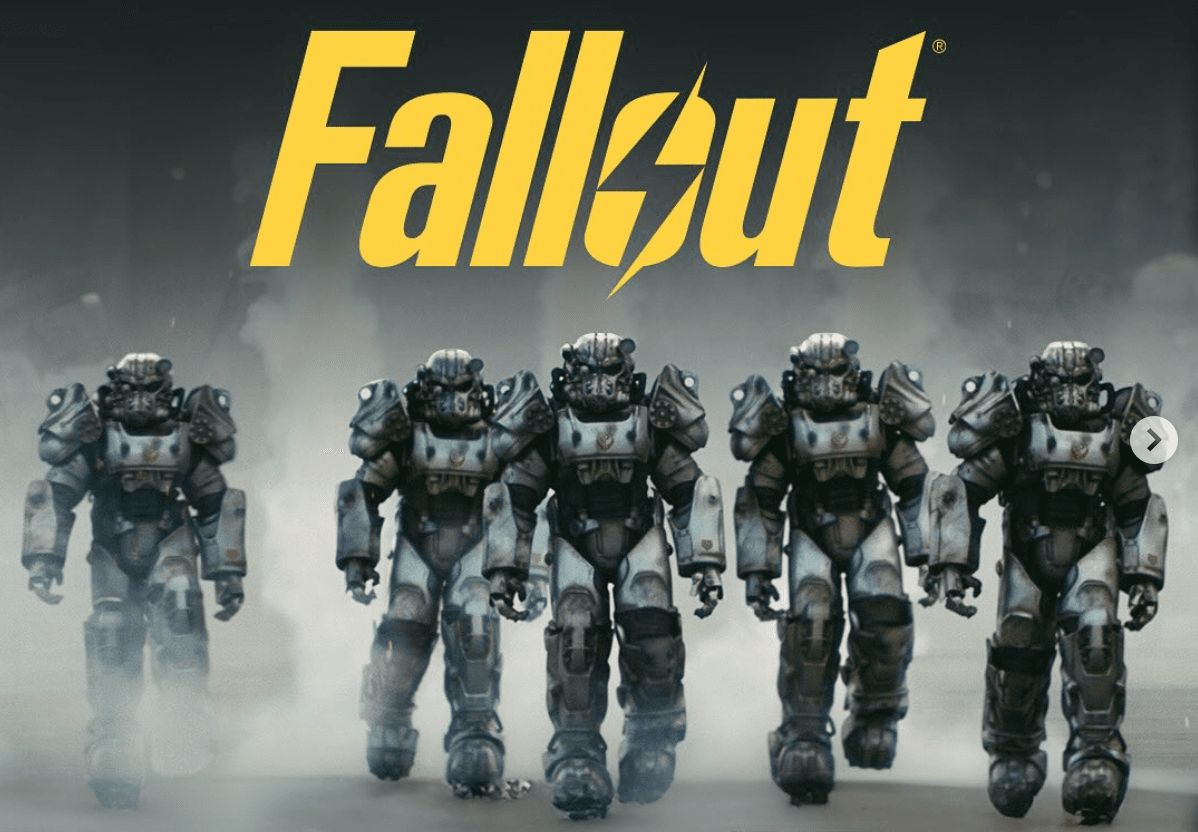
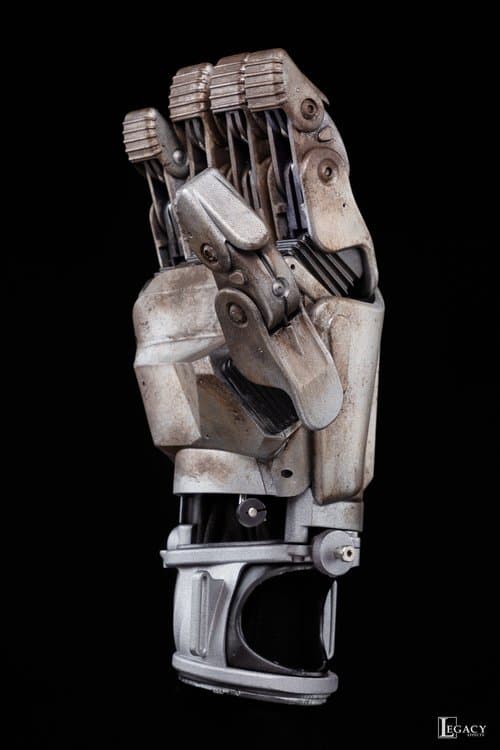
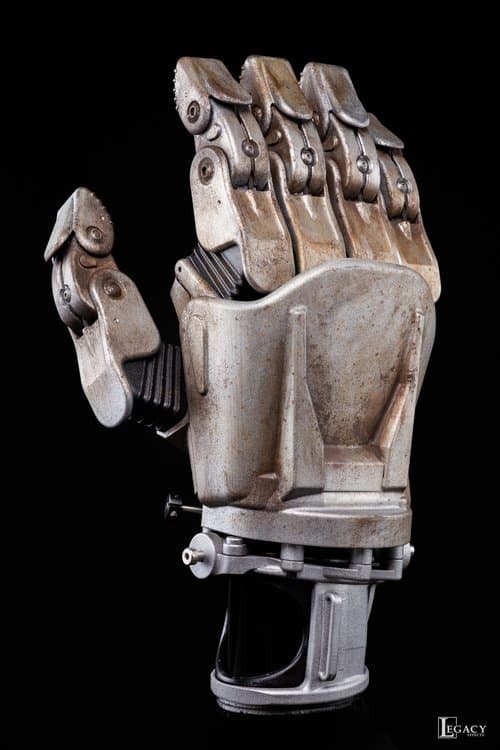
Amazon Prime's hit show 'Fallout' included these T6 Power Armour suits, which had multiple components made from MJF and SLS 3D printers. Creating functional armored suits that were comfortable enough for actors to move around in yet conveyed a sense of heaviness and inpenetrability required multiple rounds of iteration and the use of many different materials.
The short timelines, degree of customization, and organic geometries necessary for practical effects and animatronics assemblies make 3D printing an ideal tool. Legacy Effects recognized that early and has been using 3D printing for over a decade.
“3D printing at Legacy harkens back to before I was here… they had huge FDM machines and PolyJets. The Iron Man Mark III armor was the first ever fully 3D printed suit of armor used in film, but it was a lot of very slow prints at the time — it wasn’t great for functionality yet,” says McBride.
As 3D Lab Manager, McBride has scaled up Legacy’s 3D printing capabilities considerably. They added large-format resin 3D printers for high-resolution parts and molds, and scaled up with fleets of fused deposition modeling (FDM) printers for quick proof-of-concept models. “The technology for 3D printing is just so explosive and the growth is exponential. SLA printers got faster which is good for our molds, and then a big leap forward was powder-based printing — that was such a drastic change because it enabled new supportless geometries,” says McBride.
Adding Powder Bed Fusion 3D Printing for Functional Parts
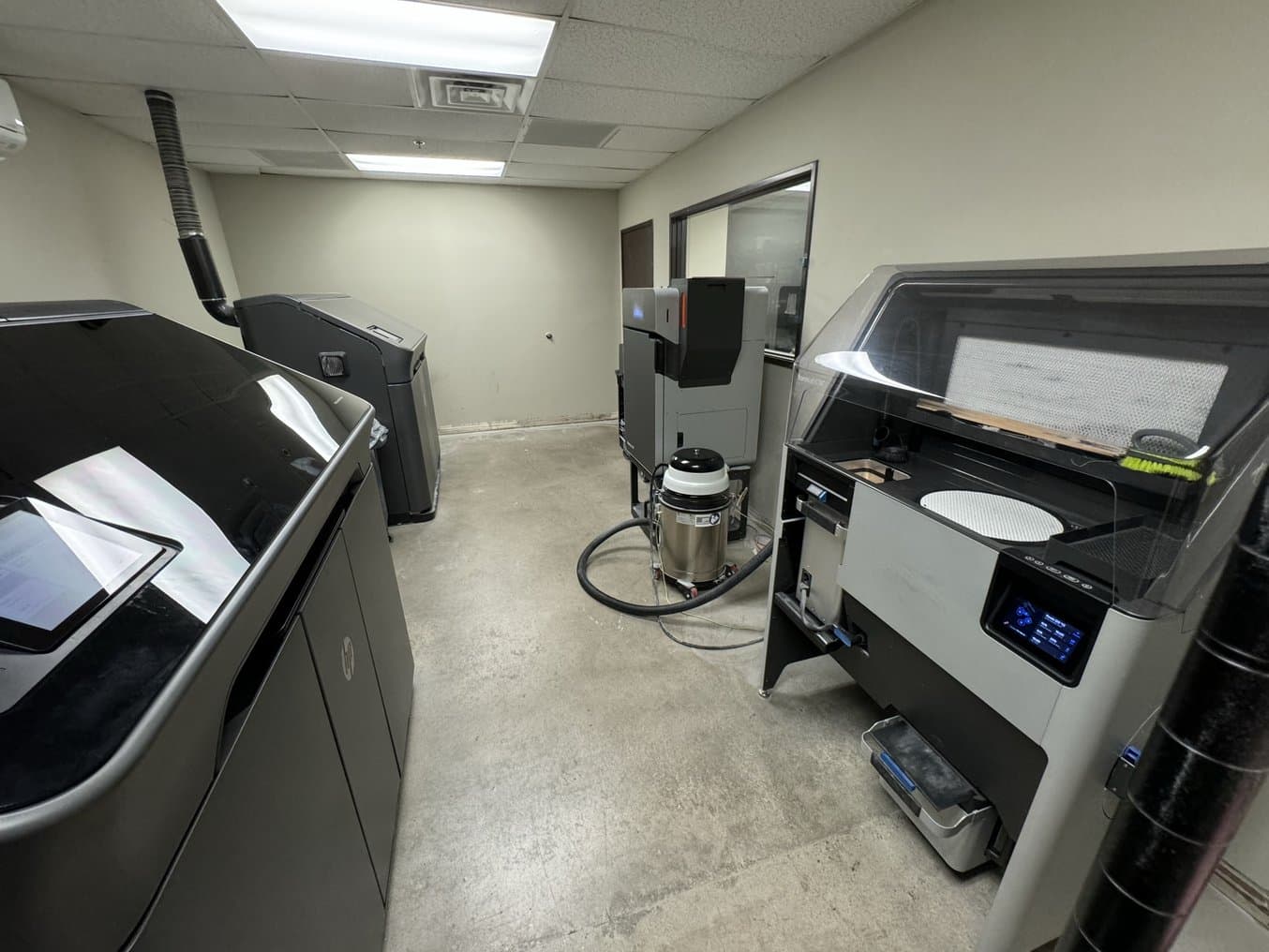
Both MJF and SLS technology provide unique advantages to the Legacy Effects workflow - the large-format printing possible on the HP MJF printers helps create big single pieces of armor, while the modularity and material versatility of the Fuse Series give the team more options and flexibility.
At Legacy Effects, their HP 500 Series MJF printers work alongside the Fuse 1+ 30W and Fuse Sift. McBride and his colleague are both HP Certified Engineers and rely on their HP large-format machines for large-scale pieces of armor and animatronics in nylon.
Adding powder bed fusion 3D printing enabled McBride’s team to create internal assemblies that could actually move an animatronic forward. SLS and MJF parts have the ruggedness and durability to handle substantial load — which, for a 10-foot-tall alien, is considerable. The support-less printing method enables organic shapes with lattice structures that can reduce overall weight while maintaining strength, and deliver the imaginative shapes necessary for fantastical creatures.
The Legacy team started with large-format industrial powder bed fusion printers: two multi-jet fusion (MJF) printers from HP. They needed the large build volume possible on the HP machines for parts like chest plates and alien heads. These kinds of prints need to be iterated multiple times, and breaking them up into smaller parts would mean other departments had to help assemble the pieces.
“MJF works really well for the larger build packs. We’re not creating one set of brackets and printing a thousand of them to sell retail — these are custom armor parts. It might be different if we were batch printing something industrial, but for us, we use the MJF for a very specific use case,” says McBride.
The HP 500 MJF printers print, reclaim, sift, and mix powder all in one machine, which typically makes post-processing a bit easier — when everything goes right. “This all-in-one system maximizes space efficiency, it also means more moving parts per printer and more internal systems that all must be routinely maintained,” says McBride.
But the team had to find another option when something went down on their MJF machine and production stopped. “Before we became certified HP engineers, the machine went down and we had to wait for tech support — so that was the original push to get a Fuse Series SLS printer, it was basically a stop-gap option for us,” says McBride.
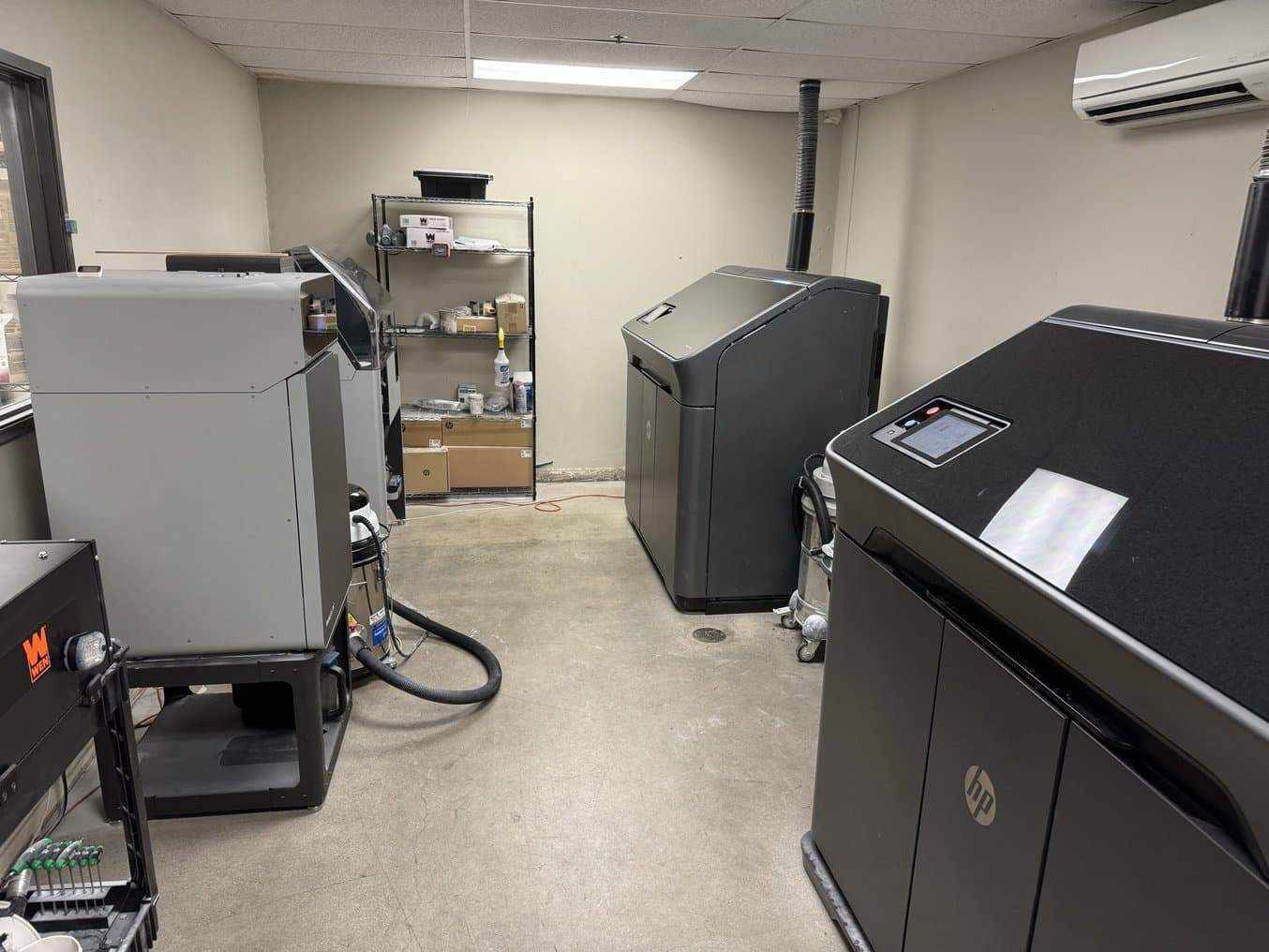
The HP 500 Series MJF printers have all-in-one systems that include printing, sifting, reclaiming, and mixing powder, but when one step in the process has an issue, it can halt the entire operation. McBridge added a Fuse 1+ 30W printer for nylon stop-gap parts when his HP went down, then switched it to TPU 90A Powder when the HP’s came back online.
While their HP machines were undergoing service repairs, the Legacy team started printing Nylon 12 Powder on their Fuse 1+ 30W printer. Accustomed to the complex nature of their MJF printers, McBride and his assistant found that adding a Fuse 1+ 30W printer was easy to integrate into their workflow, even as a temporary save.
“It has such a good built-in workflow. The user interface is something Formlabs has always, rightfully, taken pride in. It’s easy to use. Clear instructions, the slicer is straightforward, and it does a lot of automated stuff for us.”
Samuel McBride, 3D Lab Manager, Legacy Effects
But when the HP machines came back online and the large build volume was once again available, McBride decided to see what else the Fuse 1+ 30W could do. He switched over their workflow to Nylon 11 Powder first, to gain more ductility, then realized something more elastic was possible. The whole workflow changed when TPU 90A Powder came into the picture.
Pivoting to Elastomers and Expanding Capacity
TPU 90A Powder has the high tear strength and elongation at break of rubber, but can be directly 3D printed on the Fuse Series for strong, flexible parts. Legacy Effects uses this material for armor components that enhance the actors' comfort and functionality.
Legacy’s work requires a lot of customized soft parts. From actuators within alien animatronics, to helmet cushioning, to skin-like coverings for creatures, soft 3D printed parts are in constant demand. Fabrication methods range from SLA 3D printed molds to direct printed FDM rubbers and TPUs, but McBride wanted to try something that didn’t require extensive post-processing.
“There’s a laundry list of problems. If you’re doing it on FDM, there’s a lot of cleanup, and it’s hard to work with TPU filament. If you’re doing a soft resin, you’re limited by size, especially because of suction forces. Then there’s the Fuse. We just hit print and the next morning there’s a whole bucket of TPU parts that not only are done way faster than the other technologies, but there are no layer lines and they come almost ready for us to seal and get paint to stick.”
Samuel McBride, 3D Lab Manager, Legacy Effects
Adding powder bed fusion 3D printers like the MJF HP units and the Fuse 1+ 30W has been a ‘monkey wrench’ for the Legacy Effects team, allowing them to experiment with designs that they hadn’t been able to before. “Running TPU on the Fuse printers is something we’ve never done before, and it opened a whole new door — you’re bordering on completely replacing casted soft urethanes. We can pull parts right off the printer that are soft, flexible, and lightweight,” says McBride.
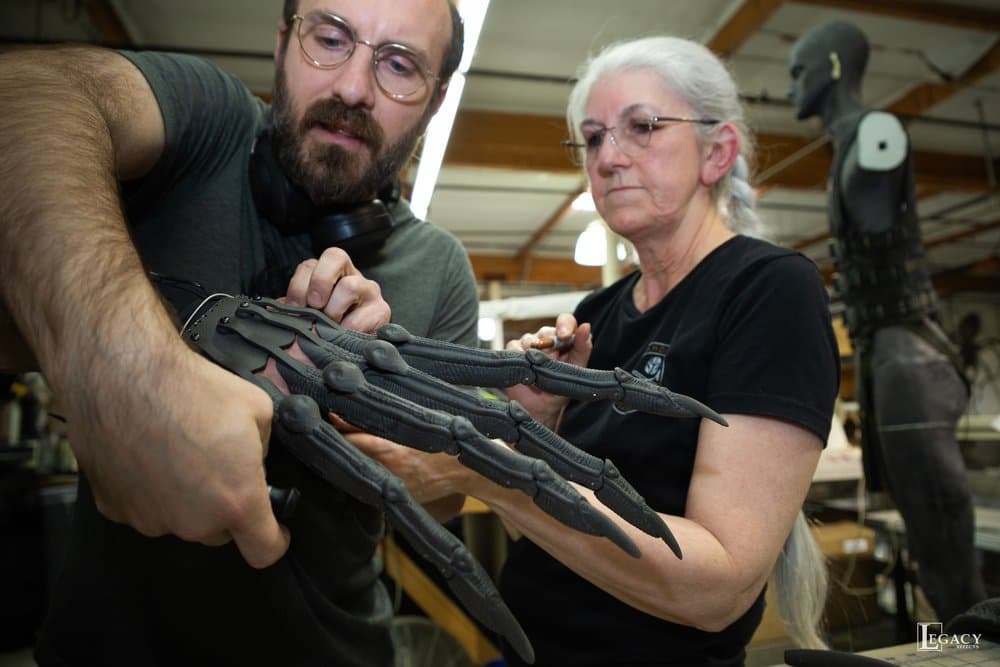
The xenomorph's hands from Alien: Romulus had TPU 90A Powder parts to help improve flexion and contraction for the animatronic claws.
They’ve been printing more and more TPU 90A Powder parts not just because of the mechanical properties, but because it has made their workflow easier, and streamlined a manual process that had been taking them multiple hours before. The process of casting a soft part previously meant they had to build a mold in FDM or SLA, pour urethanes, remove the mold, and then post-process and assemble the pieces.
With their Fuse Series printer dedicated entirely to TPU 90A Powder, they’ve removed much of the labor in the process. “Whether you’re making an Iron Man suit or a Fallout-style suit, it’s typically a very long process just to get one… [The Fuse] removed a whole middle section of our workflow and streamlined our process time,” says McBride. The addition of TPU 90A Powder to their workflow went so smoothly that they’ve ramped up considerably, now printing between 10 kg and 16 kg of TPU parts each month.
Setting Up for SLS Success
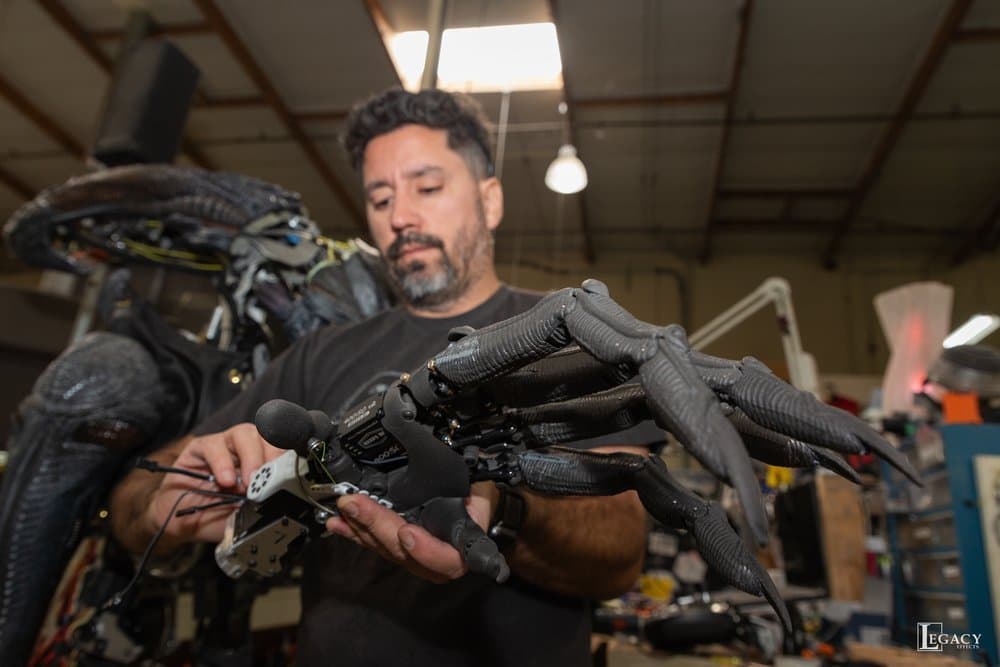
FDM-printed TPUs and rubbers require a lot of post-processing, while size is a limiting factor for resin rubber-adjacent materials. SLS 3D printed TPU on the Fuse Series streamlines McBride's workflow and makes it easy to deliver strong, flexible parts to the team by the next day for testing or assembly.
As long-time 3D printer users and HP-certified engineers, McBride and his assistant aren’t in favor of completely switching over their powder bed fusion 3D printing to the Fuse Series — their job is to select the tool that’s best for the job, and for right now, different jobs are sent to the large-format HP and the benchtop Fuse 1+ 30W.
For dimensional tolerances, McBride found that there was a learning curve when he added the Fuse Series — parts had the same tolerances as the HP, but often in the opposite direction. MJF detailing, fusing, and binding agents add volume (though very slight), so tolerances are slightly expanded from the original file. McBride found that the heat in the Fuse Series led to the same tolerances, but they had to account for shrinkage instead of expansion. “We have to design for the machine in question — the tolerances are minute on both of them, we’re talking 0.001 millimeters. They’re very similar, just in opposite direction,” says McBride.
Another difference between the two workflows is having the flexibility to scale. “For HP, it’s half a million for the whole setup, while the Fuse scalability means you can buy one post-processing station and add more machines for only about $20K each,” says McBride.
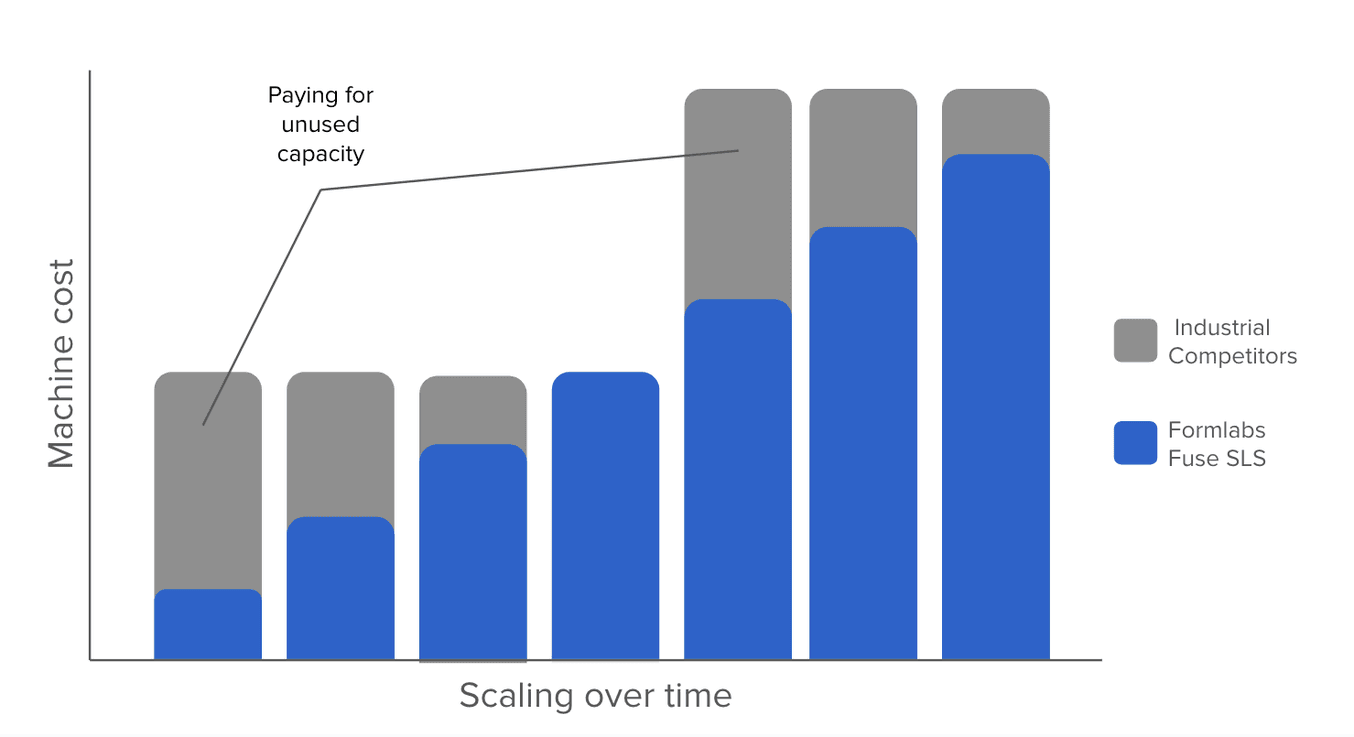
Finding the Right Maintenance Workflow
While McBride and his assistant became HP-certified engineers to maintain their machines past their scheduled end-of-service date, finding the right service workflow for the Fuse Series was comparatively easy. “There are learning curves for every machine, but the Fuse was one where it was definitely minimal, mostly just learning the slicer,” says McBride.
The Legacy team takes an extra few minutes after each print to wipe the optical lens and vacuum the printer cavity. Because multiple people are using the machine, there’s a risk of accidentally skipping a recommended maintenance, so instead, whoever removes the build chamber is in charge of the under ten minutes of maintenance tasks and set-up for the next print. “The maintenance is faster because Formlabs keeps the machine simpler. The HP was not going for a streamlined UI, they were going for an all-in-one kind of printer, and it works as that,” says McBride.
Suiting Up for the Future
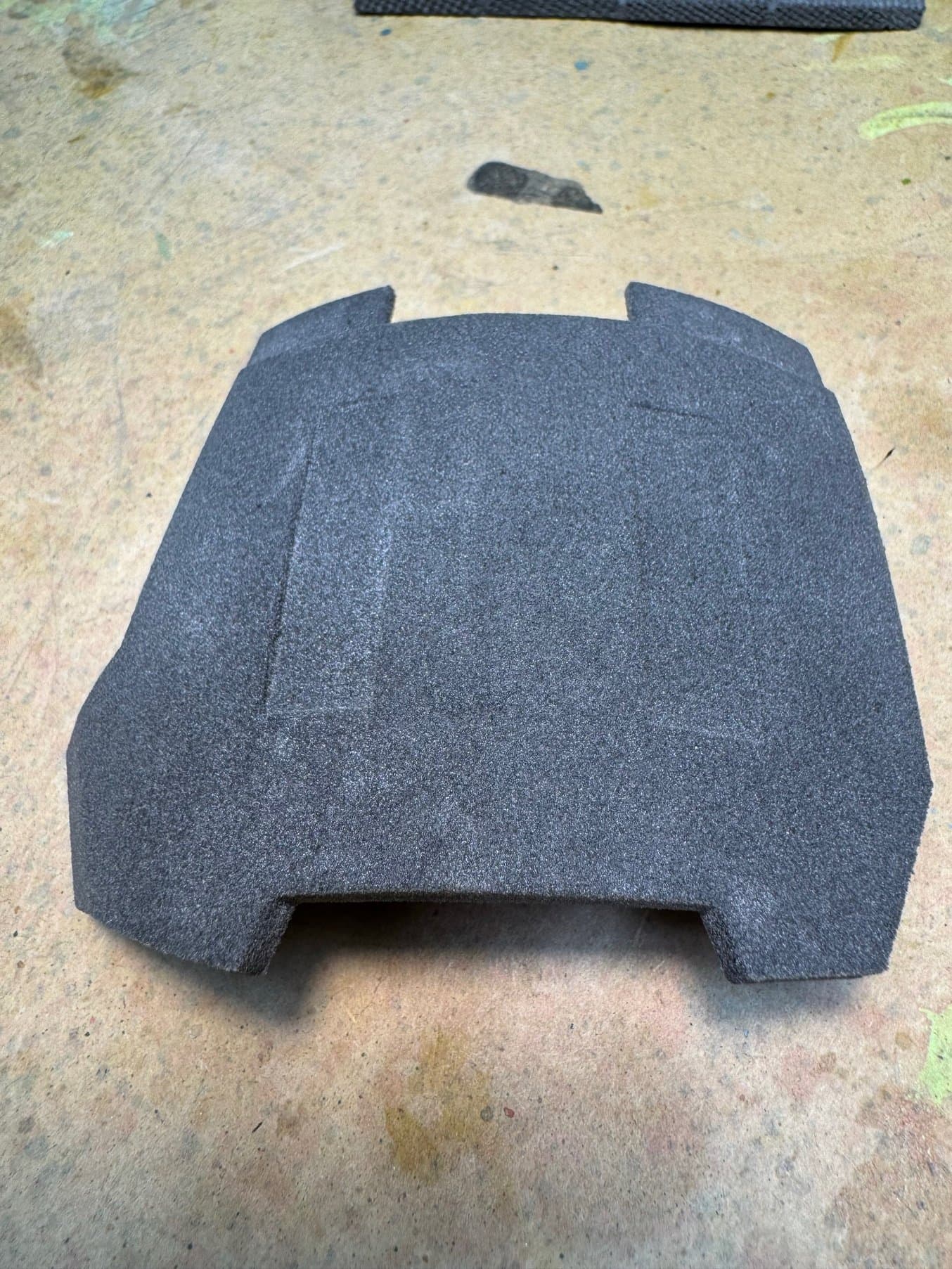
This TPU 90A Powder part is light, strong, and flexible - ideal qualities for the massive T60 Power armor suits made by Legacy Effects for Amazon Prime's Fallout.
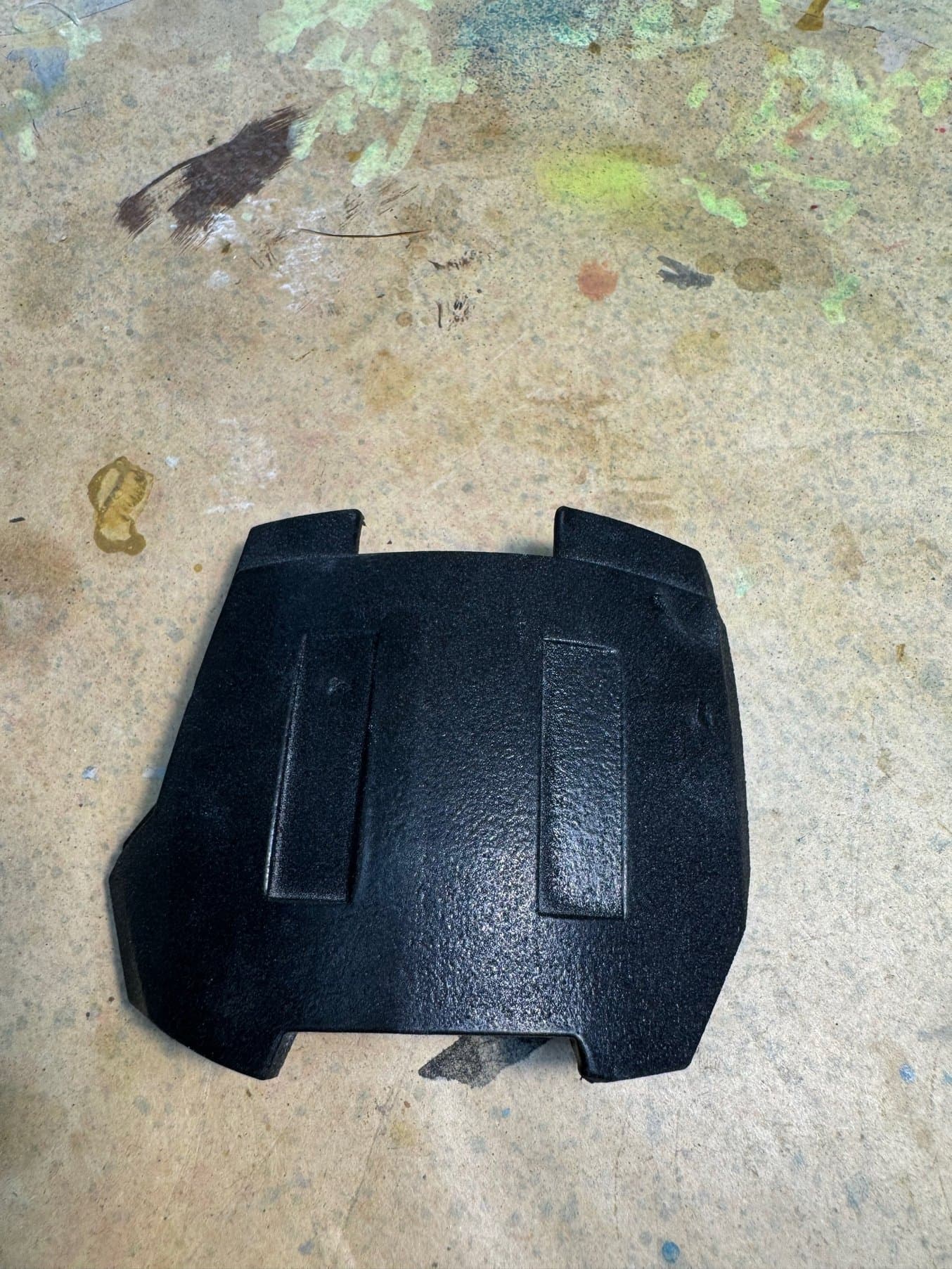
The armor component is finished using a quick in-house sealing method developed by McBride. "We can achieve looks-like leather, hammered metal, fabric textures, and other surfaces both hard and soft while being able to directly print our own patterns. No need for tooling or other machine work, just directly printed and applied," he says.
Legacy is dealing with science fiction all day, every day, and maybe because of that, they’re always open to trying new technologies and types of tools. They’ve collected so many different kinds of 3D printers over the years that McBride has actually been trying to consolidate their fleet recently.
He’d like to concentrate on the machines that deliver for them every time, and require less calibration and tuning. “We’ll always need the MJF stuff because of the build size, but if we are proving anything right now, there’s a need for more TPU and elastomerics, and having more Fuses around would be a huge help. When I get home at night, I don’t have nightmares about whether or not a print is going to succeed or fail,” says Mcbride.
The Fuse Series isn’t a one-stop shop for Legacy Effects, but it has expanded their capabilities and provided minimal labor, end-use, elastomeric parts. “Hopefully there’s more Formlabs stuff in the future for us to grow from just the one machine because the Fuse is the most streamlined SLS printer you can work on,” says McBride.
To learn more about SLS for higher volume production and powder pricing tiers, visit our site. To see the quality of SLS 3D printing for yourself, request a sample.