How the French National Research Institute for Development (IRD) Developed a Simple, High-Performance Water Pollution Sensor Using 3D Printing
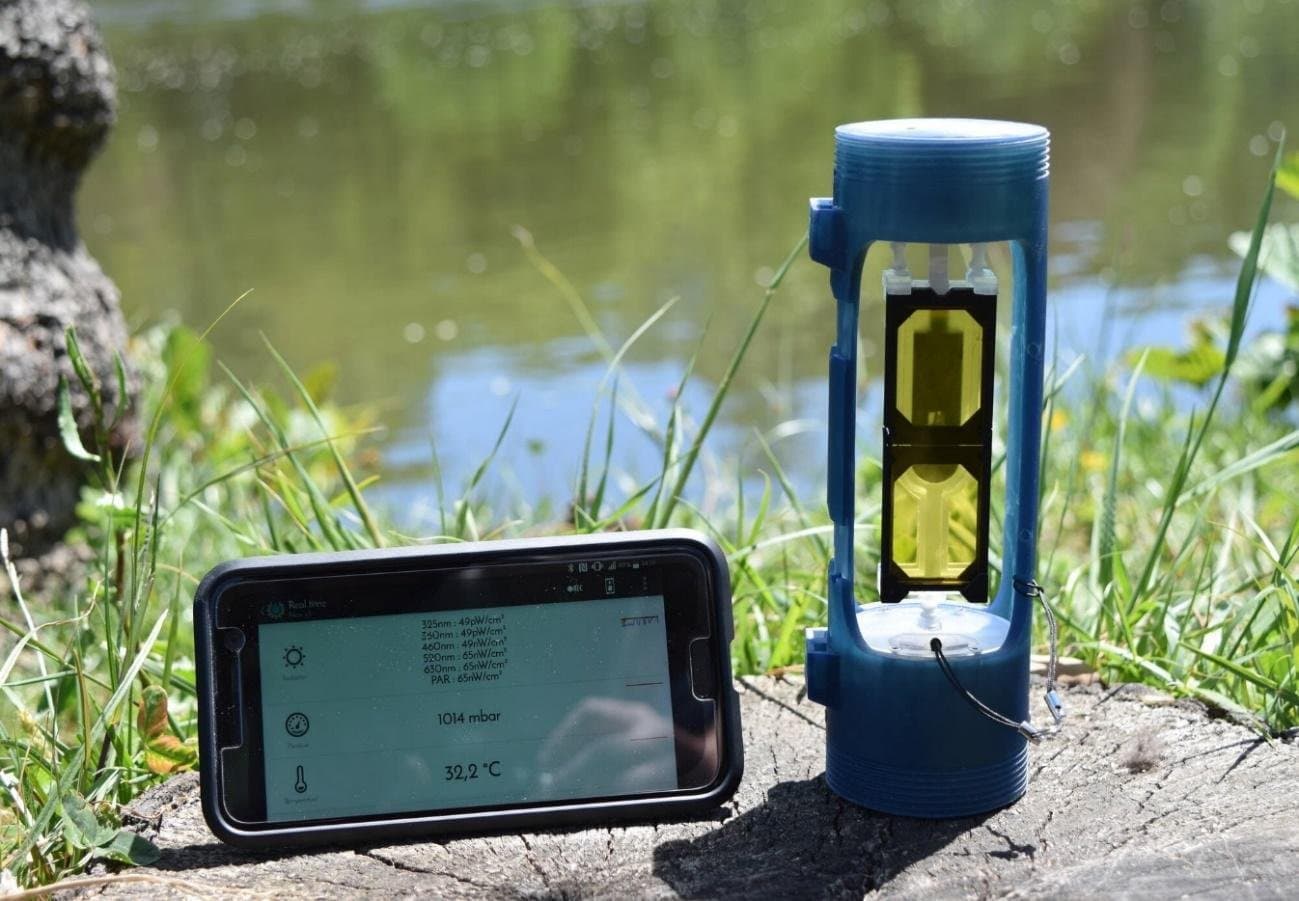
The French National Research Institute for Development (Institut de Recherche pour le Développement - IRD) is a public institution under the dual supervision of the Ministries of Higher Education, Research and Innovation, and Europe and Foreign Affairs. It combines research, expertise, training, and sharing of knowledge for the benefit of territories and countries that make science and innovation one of the first levers of their development.
An internationally recognized multidisciplinary organization, IRD is present in some fifty countries. The institute works mainly in partnership with the Mediterranean and intertropical countries on issues related to the impact of contamination on natural environments.
IRD’s mission is to develop low-cost alternative solutions for environmental monitoring in collaboration with NGOs and researchers. These solutions must be based on "low-cost" techniques to make it possible to manufacture new prototypes of sensors with tools that are commercially available, simple, and quick to implement.
Measuring Pollutants in Water
The measurement of pollutants in water, especially mercury, is very complicated; concentrations are extremely low, so it is necessary to use specialized laboratories for sampling and analysis.
For this project, the objective of IRD was to develop a tool capable of facilitating sampling, that is simple to implement and usable by non-specialists. This tool would make it possible to pass from an "expert" observation to a participative observation, which means involving local residents for a real citizen observation network.
The team in charge of this project, composed of David Point, researcher of the IRD expert of the mercury cycle, and Anthony Gautier, consulting engineer in embedded systems, had the idea of an electronic probe encapsulated in a waterproof shell.
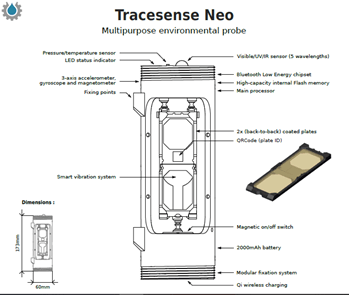
"An electronic sensor system isolates and concentrates mercury in the water on small plates that are then sent to an analytical laboratory. These electronic elements are protected from water by a mechanical infrastructure, all designed by Anthony,” said Mr. Point.
To achieve this mechanical infrastructure, Mr. Gautier first used an FDM printer. But these original tests did not provide satisfactory results. "We had a lot of problems with reliability, three-quarters of the parts did not work. Our probe must be able to withstand the pressure of water up to 200 meters deep. However, with FDM technology, we encountered micro-vacuoles. Under the effect of pressure, these micro-vacuoles were filled with water and the watertightness was not assured," recalls Mr. Gautier.
Searching for the Right Materials That Can Withstand the Elements
Faced with this observation, the IRD team looked for another 3D printing technology capable of addressing this constraint. After studying the different solutions available on the market, the team chose stereolithography (SLA) 3D printing equipment from Formlabs.
"At the time, we were both in Bolivia and we could not afford to invest in hardware without being certain to get reliable, accurate, and repeatable output," explained Mr. Point. "The efficiency, reliability, and cost ratio of Formlabs printers was therefore a determining factor in our choice."
"Before we started, we had a sample made, as proposed on the Formlabs website. So we were able to check the quality of the material: it seemed isotropic and well-sealed," said Mr. Gautier.
After that, the researchers carried out numerous tests in laboratories on different types of resins proposed by Formlabs (Standard Resin, Tough Resin, Flexible Resin, and others) to check how they respond to aggressive materials (for example, acids and others), synthetic waters, seawaters, natural waters.
"The materials performed very well during these tests," said Mr. Point. "We finally decided to use several types of resins: the main body, which must withstand shocks, is printed in Durable Resin, while the sub-housings are printed in Standard Resins in higher resolutions," added Mr. Gautier.
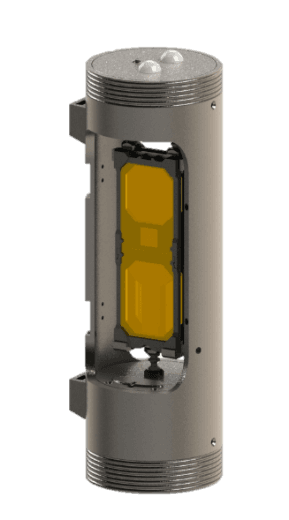
From Prototyping to Field Testing
Thanks to their Formlabs 3D printer, Mr. Point and Mr. Gautier were able to develop a prototype meeting all their specifications: a waterproof probe incorporating both a chemical sensor, electronic components, a Bluetooth module, and the batteries needed for their power supply.
This prototype enabled IRD to win the call for projects « Agir pour la Ressource en Eau » ("Acting for Water Resources") organized by the French-based utility company SUEZ to support innovative solutions to protect the water resource.
The team is now working on the production of about 15 copies of the probe that will be made available to users for testing in the wild, which will both increase the volume of collected data and allow them to check the handling of the device. In parallel, they plan to develop a new, more compact version, which is smaller and easier to handle, for beta testers by late 2020.
Eventually, the researchers test the ability of resins to limit bio-fulling. "A sensor immersed in water always ends up being colonized by microorganisms that distort the measurements," explains Mr. Point. "We will, therefore, test the resistance of resins to this phenomenon, in particular versus PVC currently used for this type of probe."
Mr. Gautier also continues to investigate new solutions proposed by Formlabs. Form 3L, in particular, would allow the team to print more parts at once and simplify post-processing processes; and the new Elastic Resin, that has properties similar to silicone, may be able to contribute to the reduction of vibrations.