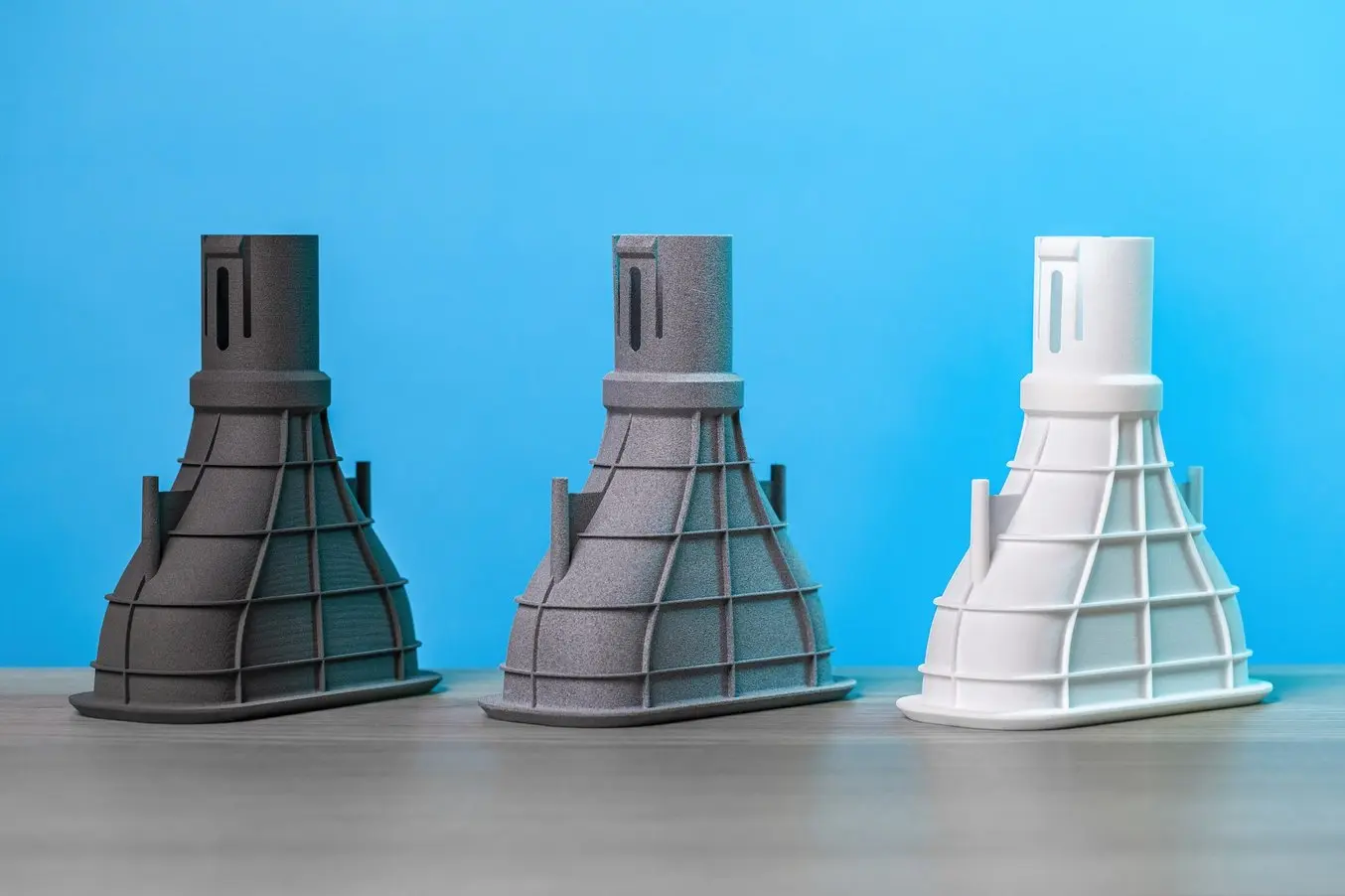
The same automotive manifold prototype printed on a Fuse 1+ 30W SLS 3D printer (left), HP Multi-Jet Fusion (MJF) 3D printer (center), and an EOS SLS 3D printer (right).
Powder bed fusion 3D printing technology, though not a recent invention, is one of the largest and fastest growing subdivisions of the 3D printing industry. For plastic-based powder 3D printing, the two most popular methods are selective laser sintering (SLS) and multi-jet fusion (MJF) technology.
Through innovations in hardware, software, and materials, 3D printer manufacturers are broadening the scope of possible applications for both SLS and MJF 3D printers, such as low volume production of end-use parts, functional prototyping, manufacturing aids, and replacement parts. Both of these forms of powder bed fusion technology have their specific advantages and disadvantages, and factors such as cost, footprint, intended application, and volume capacity should be considered when choosing between technologies.
In this guide, we’ll discuss how each technology works, the merits and drawbacks of each, and the different applications in which they can be utilized optimally.
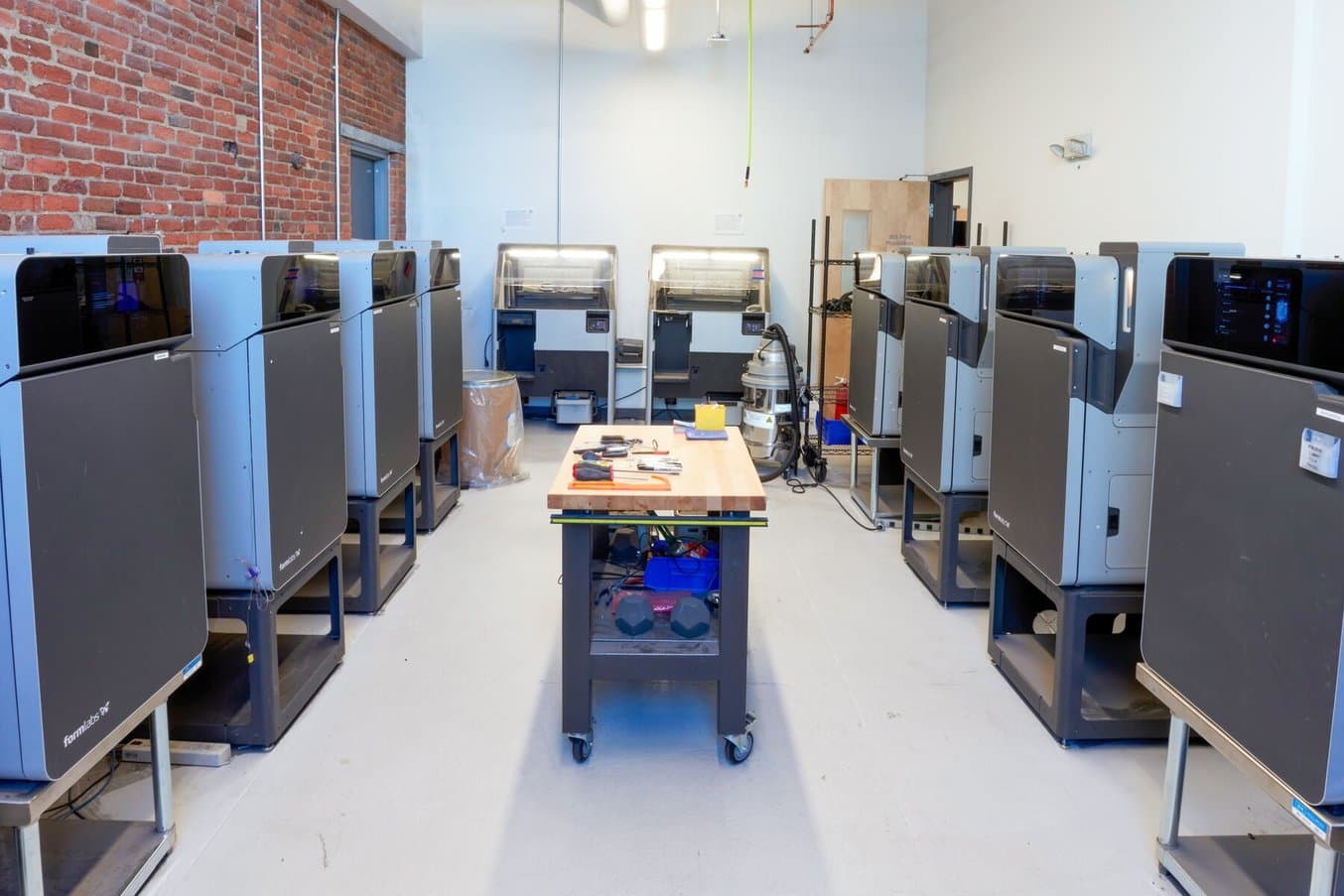
Fuse Series SLS Printers vs. Traditional Powder Bed Fusion Systems
This comparison guide will cover the main differences between compact SLS printers such as Formlabs Fuse Series and traditional large footprint machines.
Why Choose Plastic Powder Bed Fusion 3D Printing?
High Throughput and Low Cost Per Part
Powder bed fusion printers are typically larger than the more ubiquitous fused deposition modeling (FDM) or stereolithography (SLA) technologies, and are therefore more capable of producing many parts in each build. The build chamber and self-supporting nature of the powder bed allows for parts to be stacked vertically and even nested together. This feature enables operators of SLS or MJF 3D printers to maximize the utility of the space and pack the entire chamber as fully as possible. The lack of support structures also means that post-processing parts is easier and less labor-intensive, enabling parts to be produced consistently at a larger scale.
For example, Formlabs’ Fuse Series SLS 3D printers automate this feature through an optimized packing algorithm, which orients the parts so that every possible centimeter is filled. Fully packing the build chamber also aligns the packing density with refresh rate, so that all unsintered powder can be reused for a zero-waste printing workflow.
In summary, powder bed fusion 3D printing with a fully packed build chamber brings down cost per part by:
-
Producing more parts with fewer builds, increasing overall efficiency and reducing labor time.
-
Optimizing the amount of unsintered powder to minimize or even completely cut waste.
Familiarity of Materials
The main material group used in SLS and MJF printing is nylon, a highly capable engineering thermoplastic for both functional prototyping and end-use production, used for a wide range of modern day industrial and consumer products. Nylon is resistant to UV, light, heat, moisture, solvents, temperature, and water. 3D printed nylon parts can also be biocompatible and not sensitizing, which means that they are suitable for skin contact and safe to use in many contexts.
Though many businesses who outsource parts to a contract manufacturer or service bureau might not understand the differences between SLS and MJF technologies, they are familiar with the material, which means adopting powder 3D printing technologies is easier than most other processes.
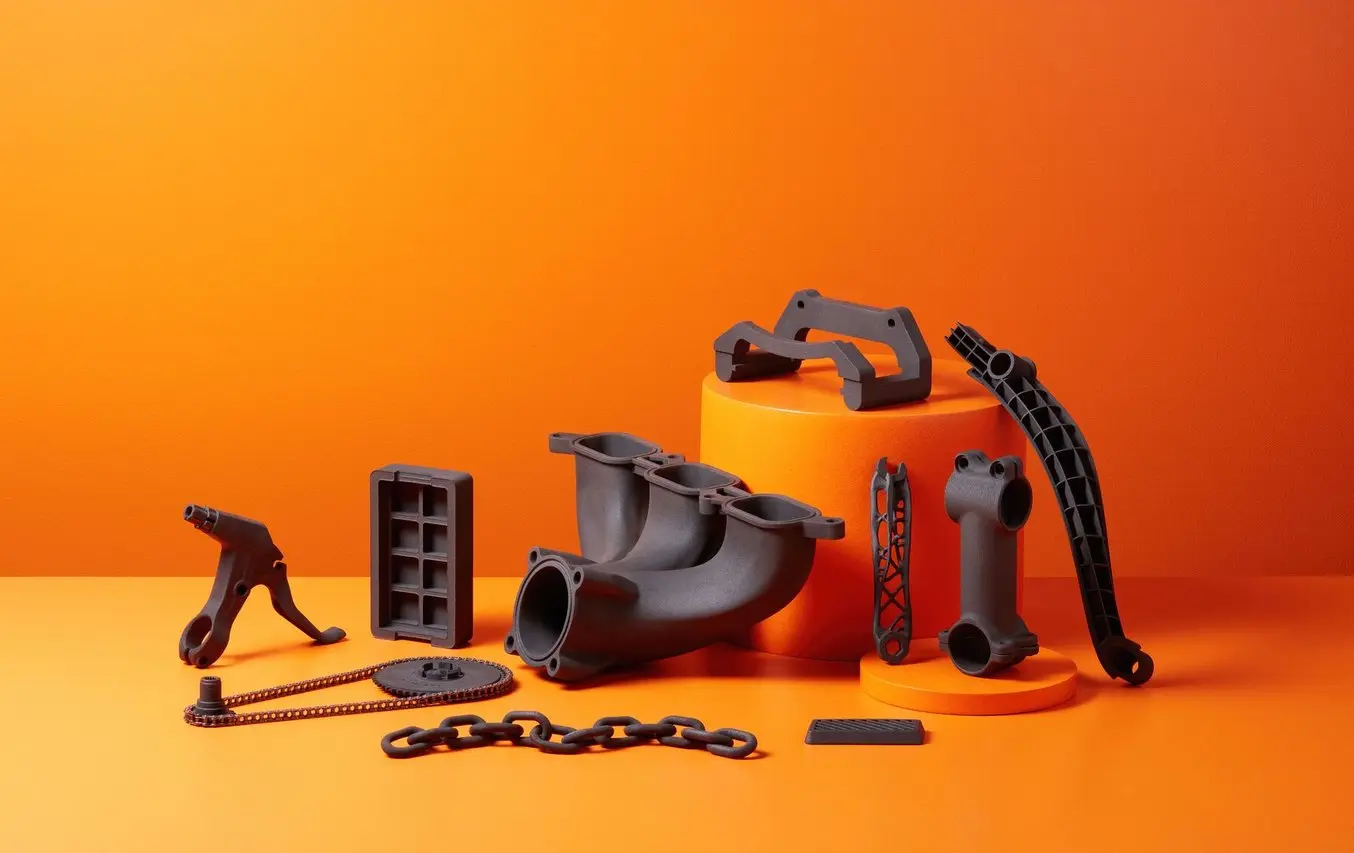
Powder bed fusion 3D printing materials are familiar to engineers and consumers, and are used for producing rugged, strong, end-use products.
What Is SLS 3D Printing?
SLS 3D printing was the first powder bed 3D printing technology, and has been a popular choice for engineers and manufacturers for decades. Invented in 1982 by a group of researchers at the University of Texas at Austin, SLS refers to technology in which a high powered laser sinters a thin layer of powder from above to form a solid cross section of the desired geometry. After each layer, the printer spreads another thin layer of powder across the top of the build chamber as the print platform drops down and the next layer is built. This method of laser powder bed fusion is attractive to manufacturers, engineers, and product designers because of its low cost per part, high volume capacity, and material familiarity.
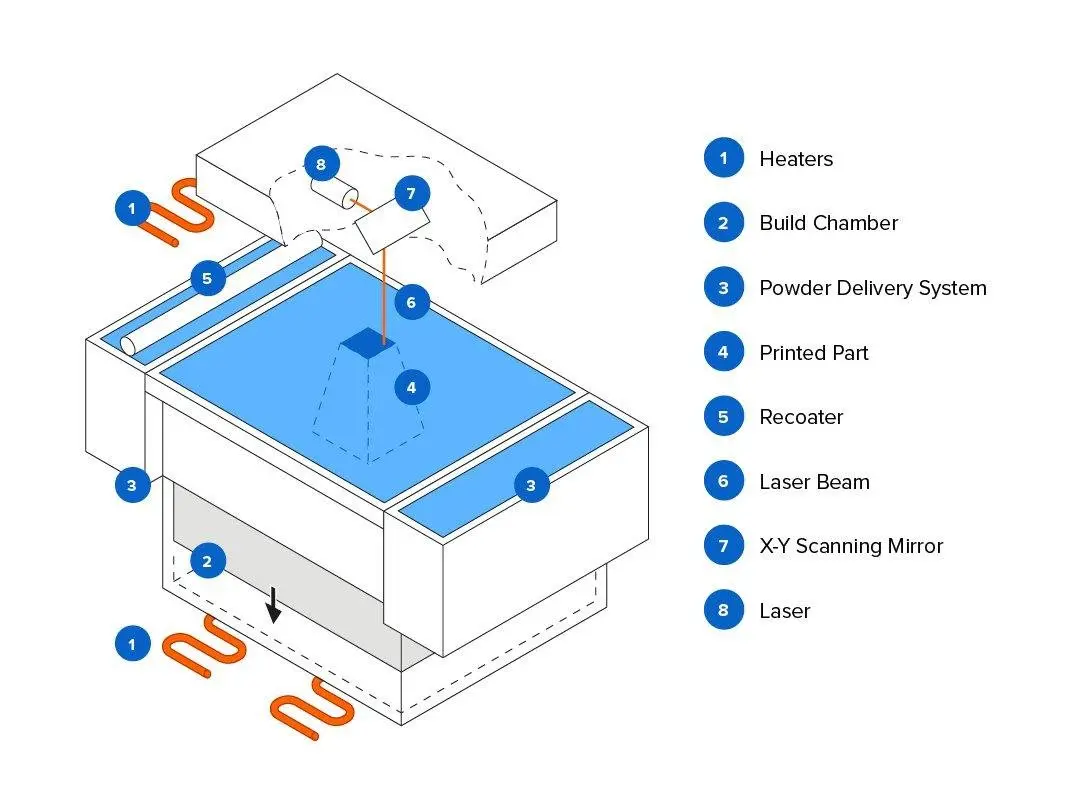
Schematic of the selective laser sintering process.
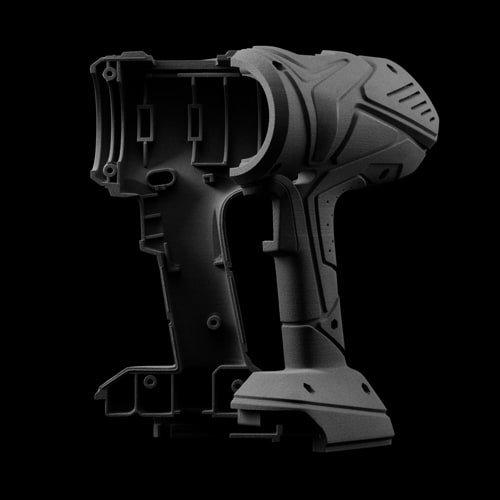
Introduction to Selective Laser Sintering (SLS) 3D Printing
Looking for a 3D printer to create strong, functional parts? Download our white paper to learn how SLS printing works and why it's a popular 3D printing process for functional prototyping and end-use production.
SLS 3D Printers On the Market Today
Industrial SLS printers have been available for decades, and have been utilized as another piece of heavy machinery or manufacturing equipment—excellent at the job for which they’ve been designed, but only possible for large institutions with space, funding, and dedicated operators.
Manufacturers like EOS or 3D Systems design these systems with very specific customers in mind. Their customers are spending hundreds of thousands, if not millions, on machinery, service, and upkeep each year, and have warehouses and infrastructure to support them. Their customers are not start-ups, small businesses, or individuals, simply because they’ve been priced out of powder 3D printing solutions.
In recent years there have been efforts to make smaller scale, less expensive SLS 3D printing solutions, something that is not available with MJF technology, which only offers large-format options.
Formlabs' Fuse Series was the first benchtop sized SLS 3D printer capable of producing industrial quality parts of comparable quality to those produced by expensive options like traditional SLS systems. With a footprint less than half the size of an EOS entry-level machine, a streamlined workflow, and an affordable price point (just under $30,000 for the Fuse 1+ 30W) have enabled hundreds of small to medium manufacturers to bring SLS in-house, while allowing large manufacturers to add machine capacity and decentralize aspects of their production.
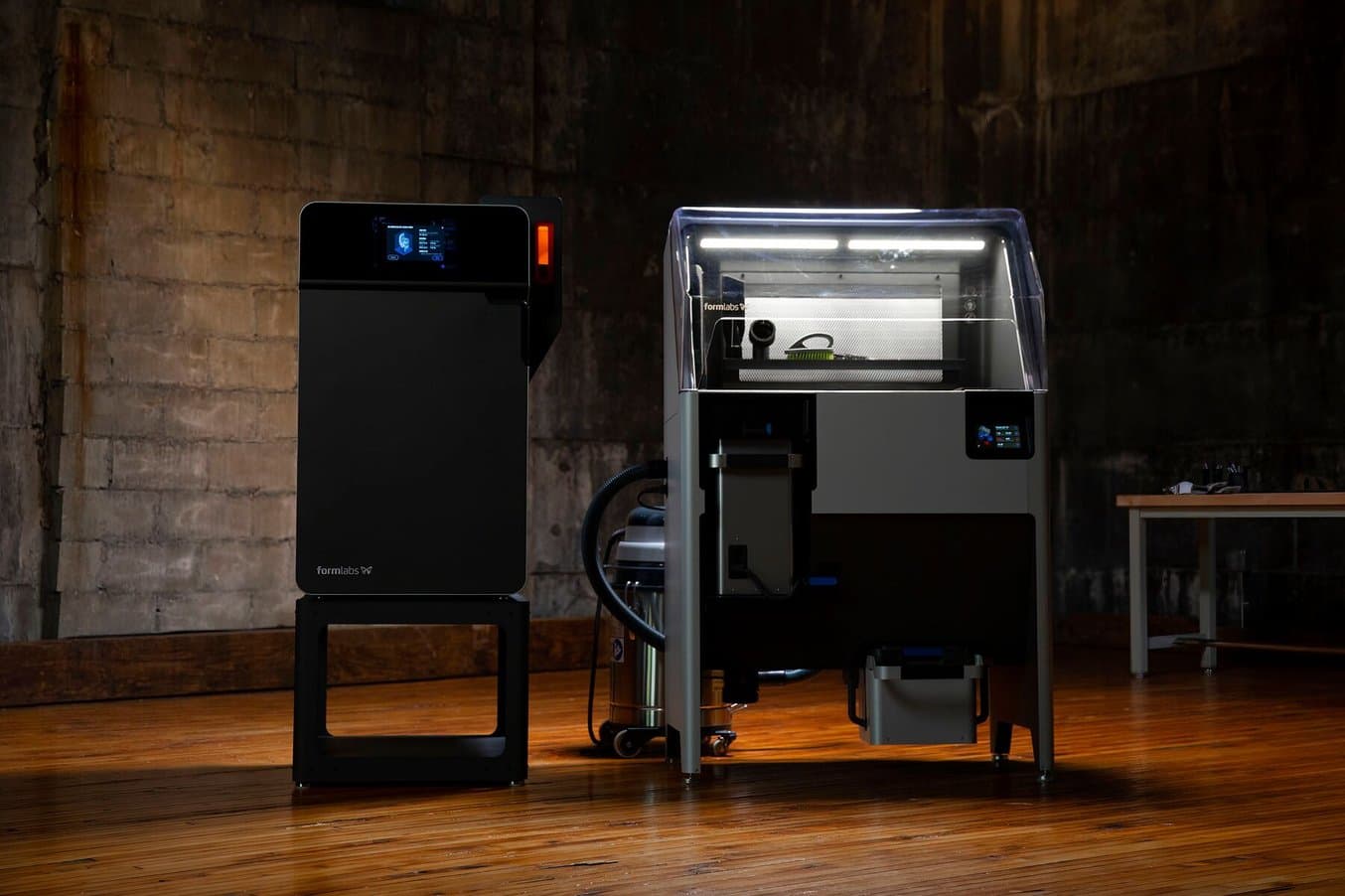
The Fuse 1+ 30W SLS 3D printer and the Fuse Sift all-in-one powder recovery station.
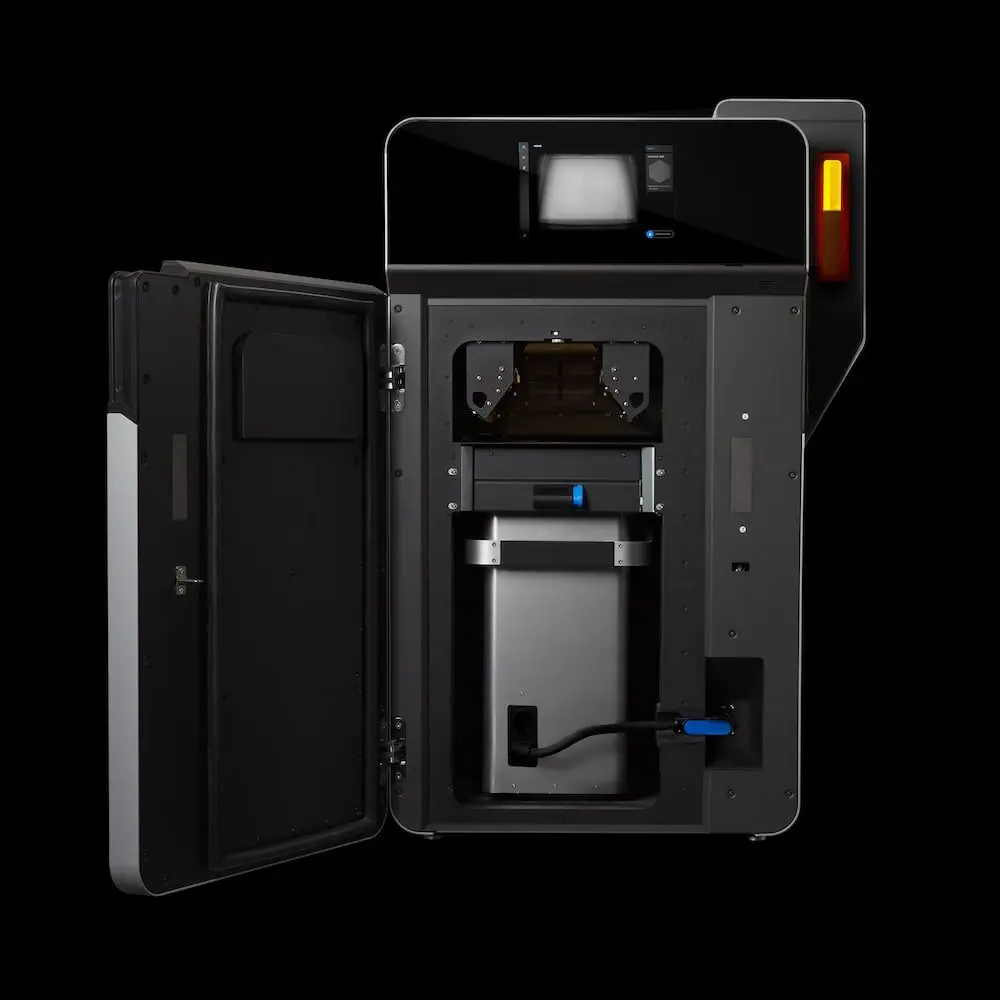
Rapid SLS Production of High Performance Parts with the New Fuse 1+ 30W
Watch our product demo for a walkthrough of the Fuse 1+ 30W and SLS 3D printing with Formlabs experts.
What is MJF 3D Printing?
Multi Jet Fusion 3D printing is a powder bed fusion additive manufacturing process that produces similar parts to SLS, using a slightly different process. To form parts, the printer dispenses a liquid binding agent from many small nozzles onto the powder bed, bringing the powders to a semi-solid state before finishing the process with heat. The infrared heat source then cures the semi-solid cross-shape before another layer of powder is deposited and the process repeats. The process was invented in 2016 by Hewlett Packard (HP), and remains patented under that brand.
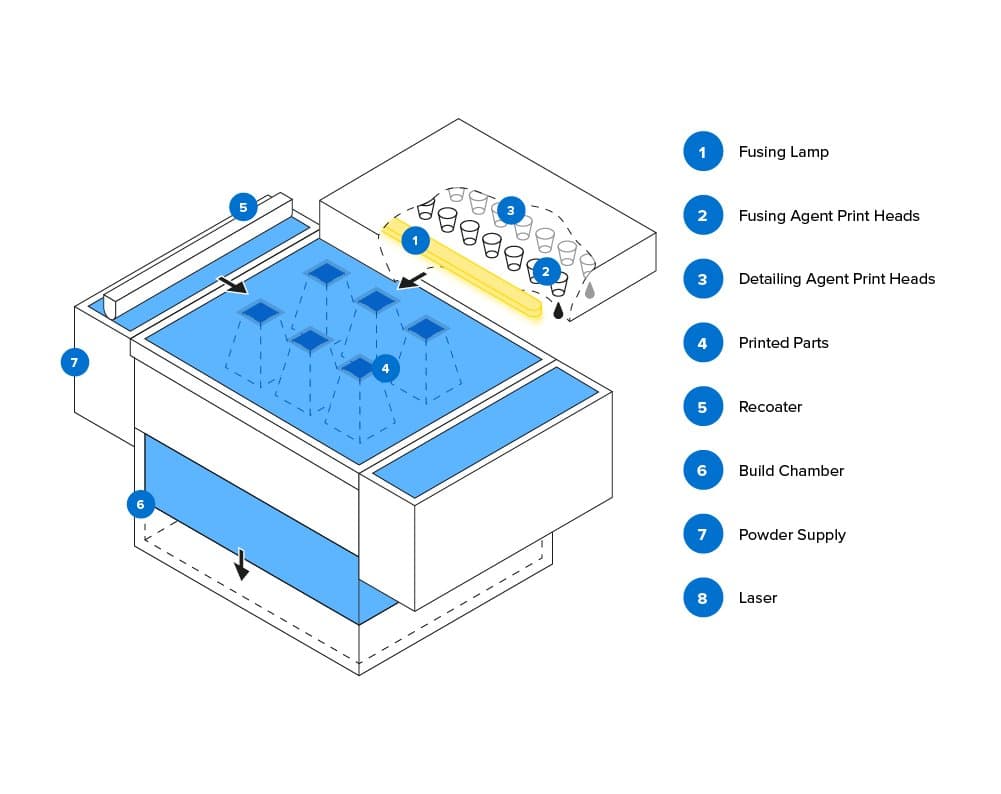
Schematic of the multi jet fusion process.
Multi jet fusion printers are often viewed as interchangeable with SLS 3D printers, especially when businesses are outsourcing 3D printed parts to service bureaus. These service bureaus will offer many types of 3D printing technologies, but often make no distinction between the two separate types of powder bed fusion printed parts, as the properties of the final parts are largely similar.
As with SLS 3D printers, MJF parts do not need supports, and therefore offer more design freedom and do not have the complicated post-processing steps that are necessary with some other 3D printing processes. The liquid binding agent and heat combination creates parts with almost identical mechanical properties as with laser sintering, and the parts are similarly mostly isotropic.
MJF 3D Printers on the Market Today
HP still holds a patent on MJF 3D printing technology, and so the only MJF printers on the market belong to HP’s line—the Multi Jet Fusion 3D Series. HP also controls the proprietary software needed to operate the printers. With prices ranging from about $350,000 to more than $600,000, the HP 3D printers deliver highly accurate parts, but require a larger investment in terms of cost, time, ongoing maintenance, and infrastructure, similar to traditional SLS 3D printing solutions. HP MJF 3D printers are most often used by service bureaus, large in-house additive manufacturing labs for Fortune 500 companies, and because of their multi-color capabilities, are frequently part of healthcare centers’ advanced manufacturing initiatives. HP used to offer a smaller format MJF 3D printer aimed at designers and product development teams, but it was recently discontinued.
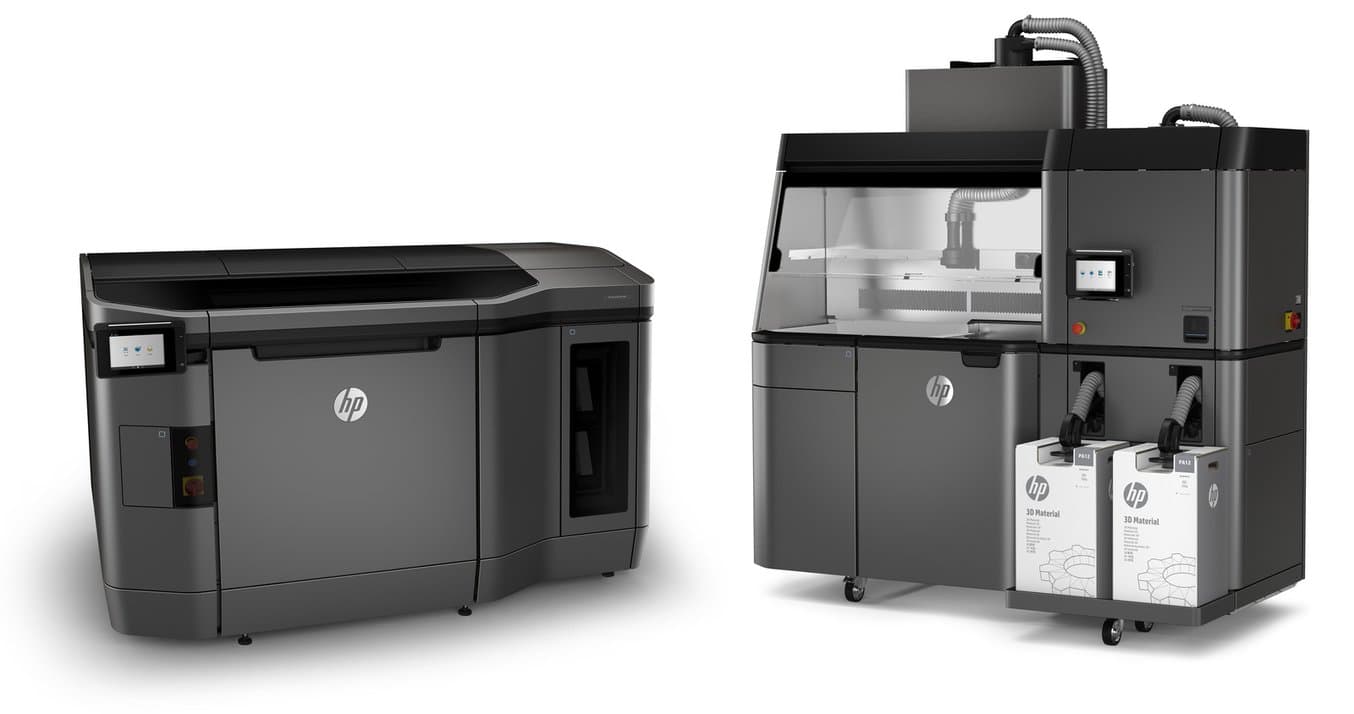
The HP Multi Jet Fusion 4200 3D printing solution.
SLS vs. MJF 3D Printing Comparison
Quality and Part Performance
As powder bed fusion 3D printing technologies are mostly being brought in-house for functional prototyping or production, accuracy and the mechanical strength are top of mind. With printers in this price range, the parts have to perform. Other technologies are appropriate for looks-like or fit-test prototypes, but SLS and MJF users are utilizing their parts in more demanding environments, and need to rely on their strength and durability. In this respect, SLS and MJF parts are virtually identical because the most common materials available are the same or similar—variations of nylon, nylon composites, and some powder printers have the ability to print flexible materials like TPU.
Nylon 12 Material Properties
Both forms of powder bed fusion technologies produce parts with a slightly grainy texture, and have similar recommendations for post-processing techniques. Engineers and manufacturers expect this texture from powder 3D printed parts, and there is not typically a distinction made between the texture of SLS and MJF printed surface finishes.
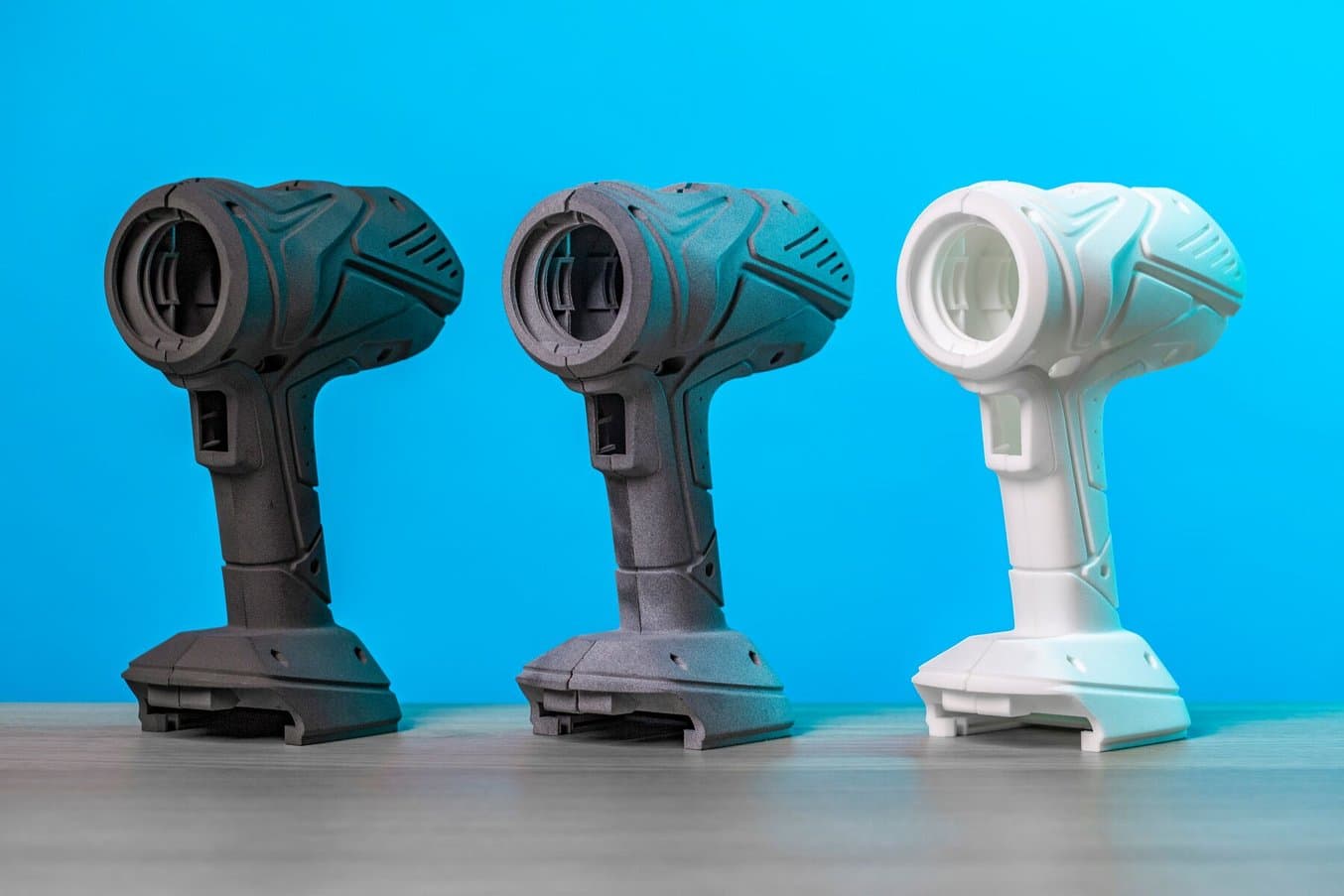
A prototype drill housing, printed on a Fuse 1+ 30W SLS printer (left), an HP MJF printer (center), and an EOS SLS printer (right).
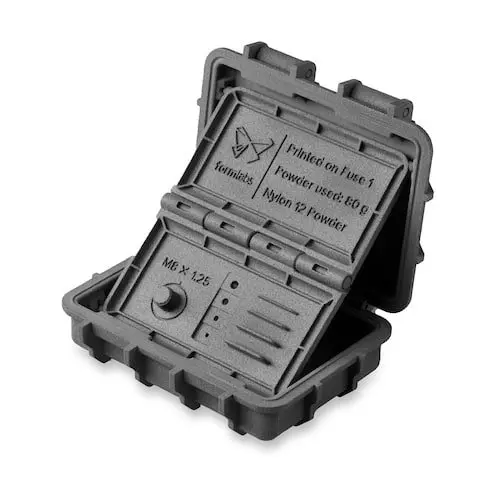
Request a Free SLS Sample Part
See and feel Formlabs quality firsthand. We’ll ship a free SLS sample part printed on the Fuse 1+ 30W to your office.
Costs and ROI
Those considering bringing an SLS or MJF powder 3D printer in-house must account for more than just the initial purchase price of the machine. To calculate ROI, one must understand how material costs, labor, and maintenance add up in the continued cost ownership. During the purchasing process, asking the right questions can help uncover hidden costs.
As mentioned before, prices for traditional industrial SLS printers start around $200,000, while MJF systems start even higher, around $350,000. SLS is also available in a more compact form, with the Fuse Series starting at $30,000 for the Fuse 1+ 30W printer and just below $60,000 for the complete package that includes the Fuse Sift powder-recovery station, Fuse Blast automated cleaning and polishing solution, a service plan, and all the essentials for printing.
On the topic of service plans, for traditional SLS and MJF printers they are typically priced at around 10% of the printer’s purchase price per year. When complete solutions can be as expensive as $600,000, an accompanying compulsory service plan can cost as much as multiple Fuse Series SLS printers each year.
For materials, the industry standard price is around $100/kg, but most manufacturers offer bulk pricing that can reduce it by more than 50% for production volumes. However, there’s a caveat, as SLS and MJF systems have varying levels of efficiency in using that powder. HP 3D printers require you to space parts widely apart to reduce the potential for thermal buildup. Recommended pack density is limited to roughly 8-10%, which means that you’ll need to throw away as much material as the amount that goes into the printed parts. This means that MJF systems create a lot of unrecyclable powder, driving up the ongoing cost of printing.
For both of these large systems, the energy required to run prints means that starting jobs for just a few small parts is inefficient, further emphasizing the fact that only manufacturers with predictable, high-volume 3D printing needs should add an industrial powder bed fusion system. In contrast, the Fuse Series printers can achieve a packing density over 30%-40%, and can nest parts within others in order to optimize the space provided. Because energy consumption is low, prints can be run for very little energy cost, and users can print only what they need, when they need it, without any harm to their bottom line.
SLS and MJF printers are popular because the lack of support structures means that post-processing is efficient and less labor-intensive than with most other 3D printing processes. However, when considering the cost of a complicated system like EOS’s SLS or HP's Multi Jet Fusion 3D printers, the need for a dedicated technician should also be considered.
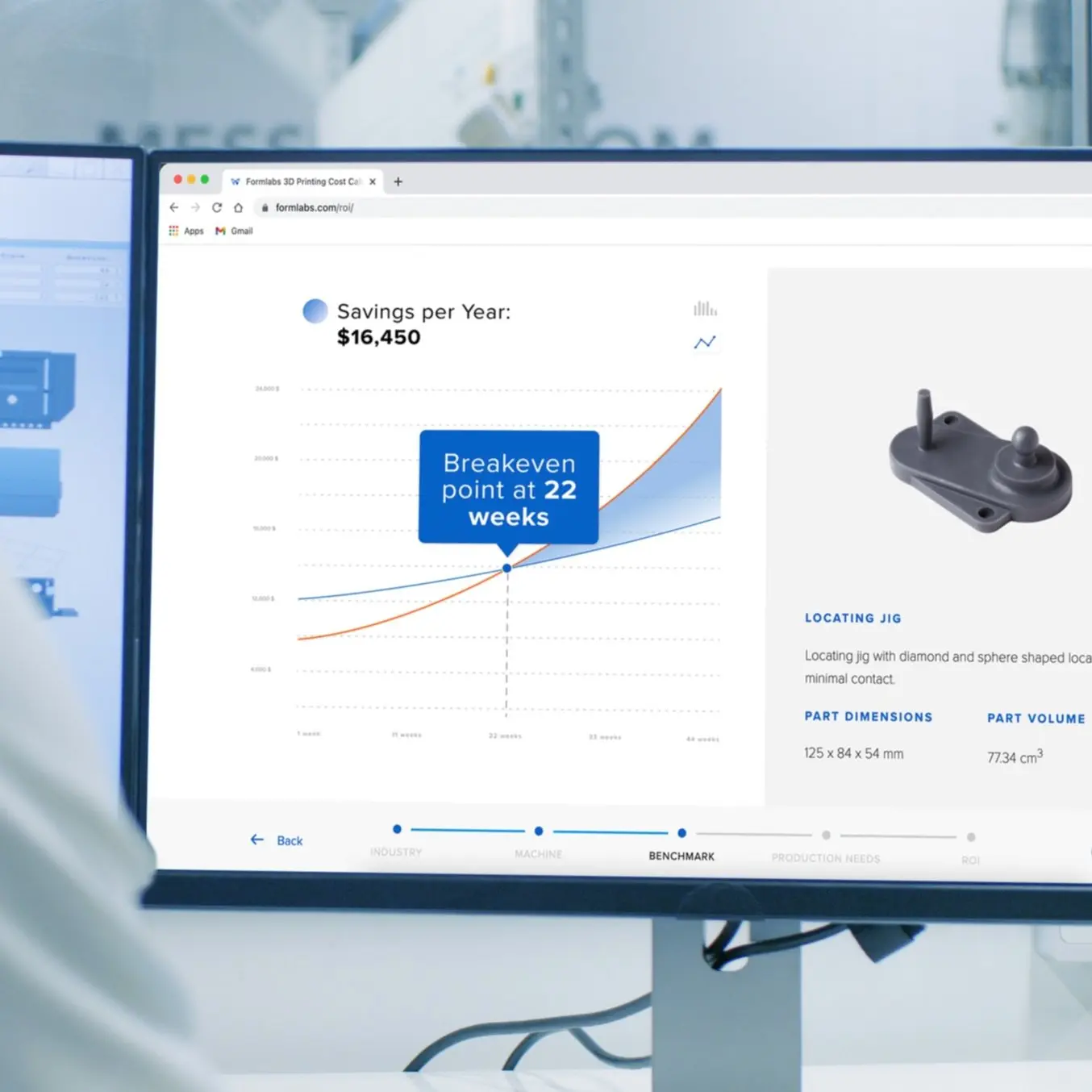
Calculate Your Time and Cost Savings
Try our interactive ROI tool to see how much time and cost you can save when 3D printing on Formlabs 3D printers.
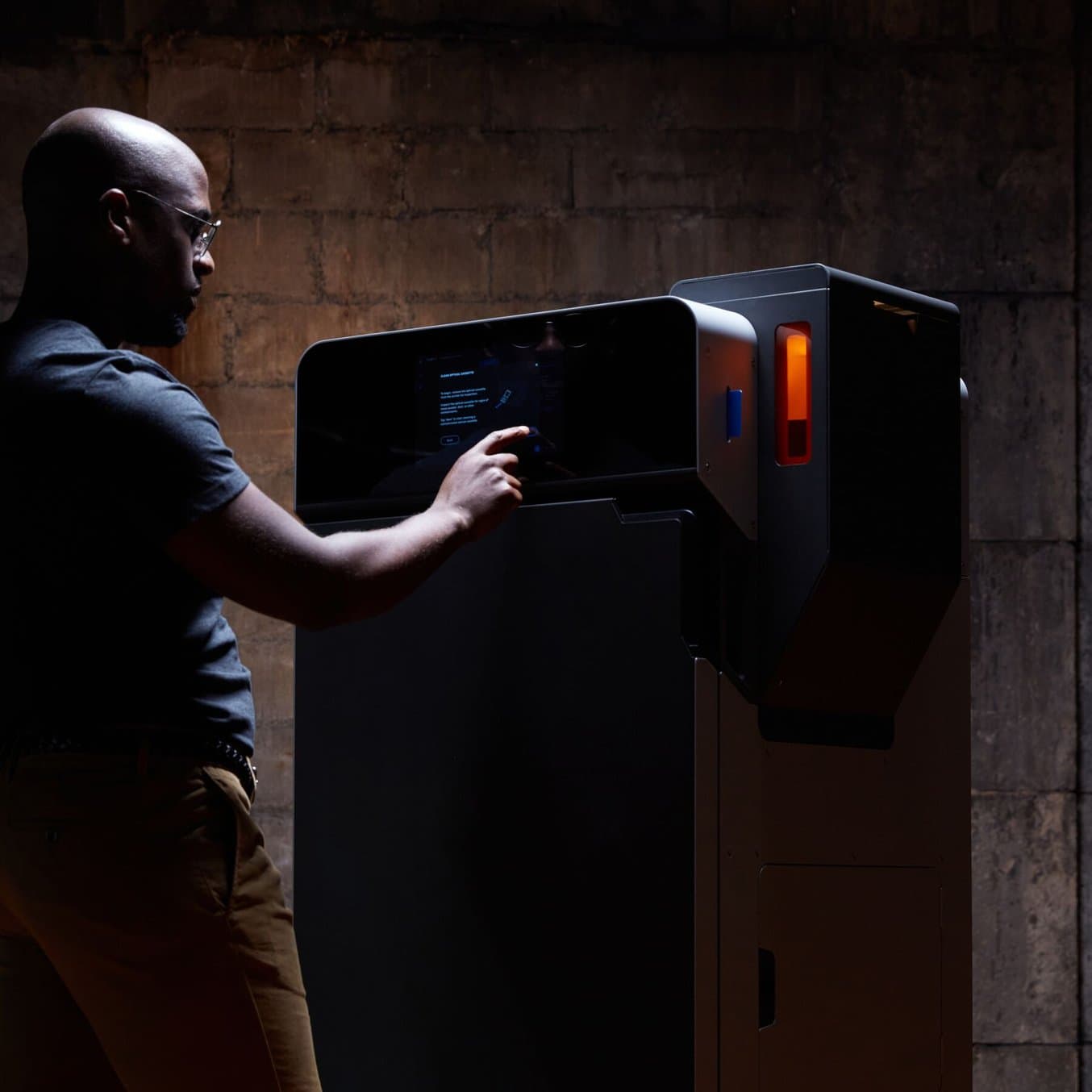
Outsourcing vs. In-House: When Does it Make Sense to Bring SLS 3D Printing In-House?
In this white paper, we evaluate the value proposition of bringing SLS 3D printers in-house, in comparison with outsourcing SLS parts from a service bureau.
Software
SLS and MJF 3D printers generally come with proprietary software print preparation, print management, monitoring, and maintenance. Beyond these standard functions, a software for efficiently packing parts into the build is also essential for powder 3D printing. Some companies build this function into their print preparation software, like Formlabs’ PreForm, which features an automated packing algorithm, while other manufacturers require customers to purchase off-the-shelf solutions separately, which can cost an additional $10,000+.
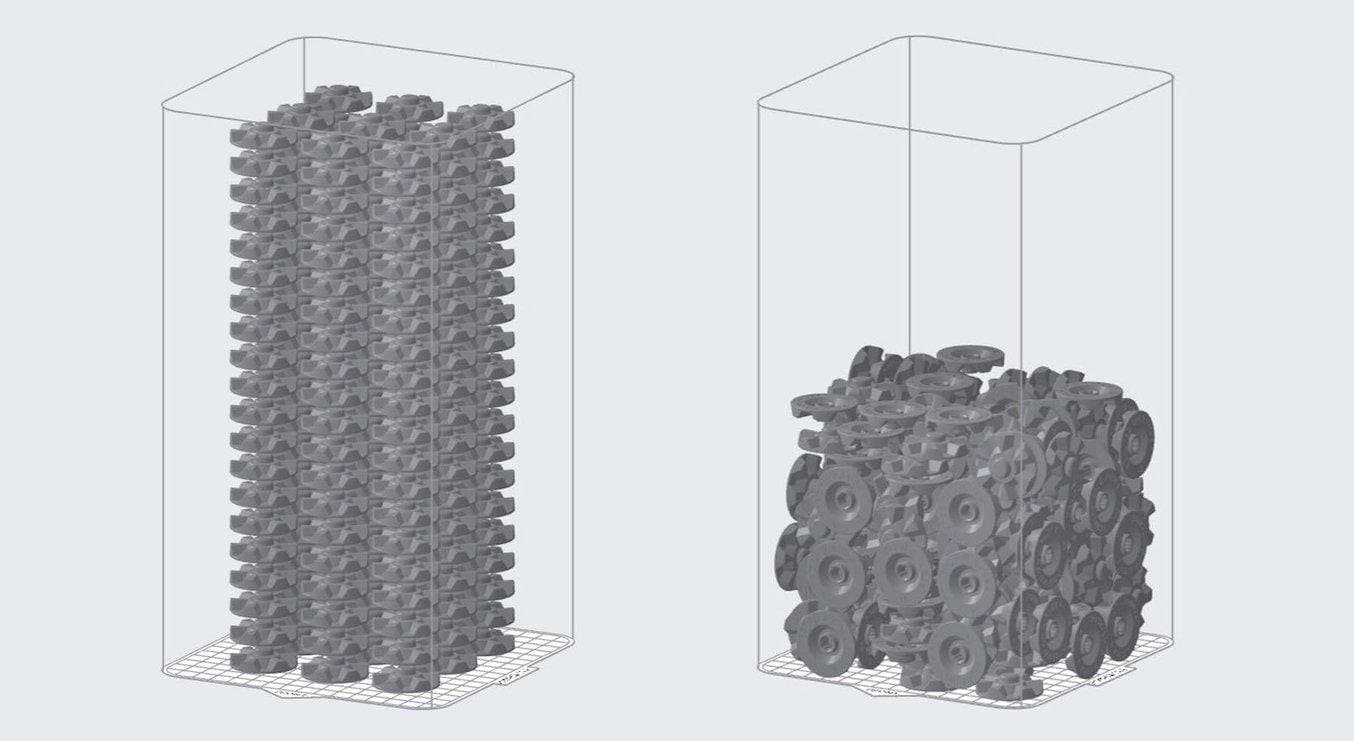
Fuse Series printers use PreForm print preparation software (free to download) that allows you to seamlessly duplicate and organize multiple parts within a 3D grid to use as much of the build space as possible for a single print. PreForm automatically suggests optimal orientation and part packing, with the ability to manually refine as needed.
Material Availability
The most common material for both SLS and MJF 3D printing is nylon, specifically nylon 12. Nylon is also available in multiple variants and composites, each tailored to different applications and optimized for specific properties like higher strength, stiffness, or flexibility. For example, nylon 11 is a more ductile, strong, flexible variant, glass-filled nylon with enhanced stiffness and thermal stability, while carbon-filled nylon offers light weight and high performance. Some SLS and MJF printers can also print with polypropylene (PP) and flexible materials such as TPU or TPE.
While most SLS and MJF printers offer multiple materials, switching between these materials is often not easy—for larger industrial printers, it might take a day or more because the machine has to be thoroughly cleaned of the prior material to avoid printing errors. As a result, customers of large SLS and MJF printers normally have printers dedicated to a single material. The Fuse Series simplifies this workflow and allows for switching within an hour between materials that use the same base component, and a couple of hours between other materials.
When comparing the most cost efficient options available on the market today, the most popular MJF printer and the most popular SLS platform offer the same number of materials—four. The HP Jet Fusion 5000 (starting at $350,000) offers five materials, nylon 12 (standard or glass-filled), nylon 11, PP, and TPU, while the Formlabs Fuse 1+ 30W (starting at $30,000) offers nylon 12 (standard, white, tough, or glass-filled), nylon 11 (standard or carbon-filled), and TPU, with more materials in development.
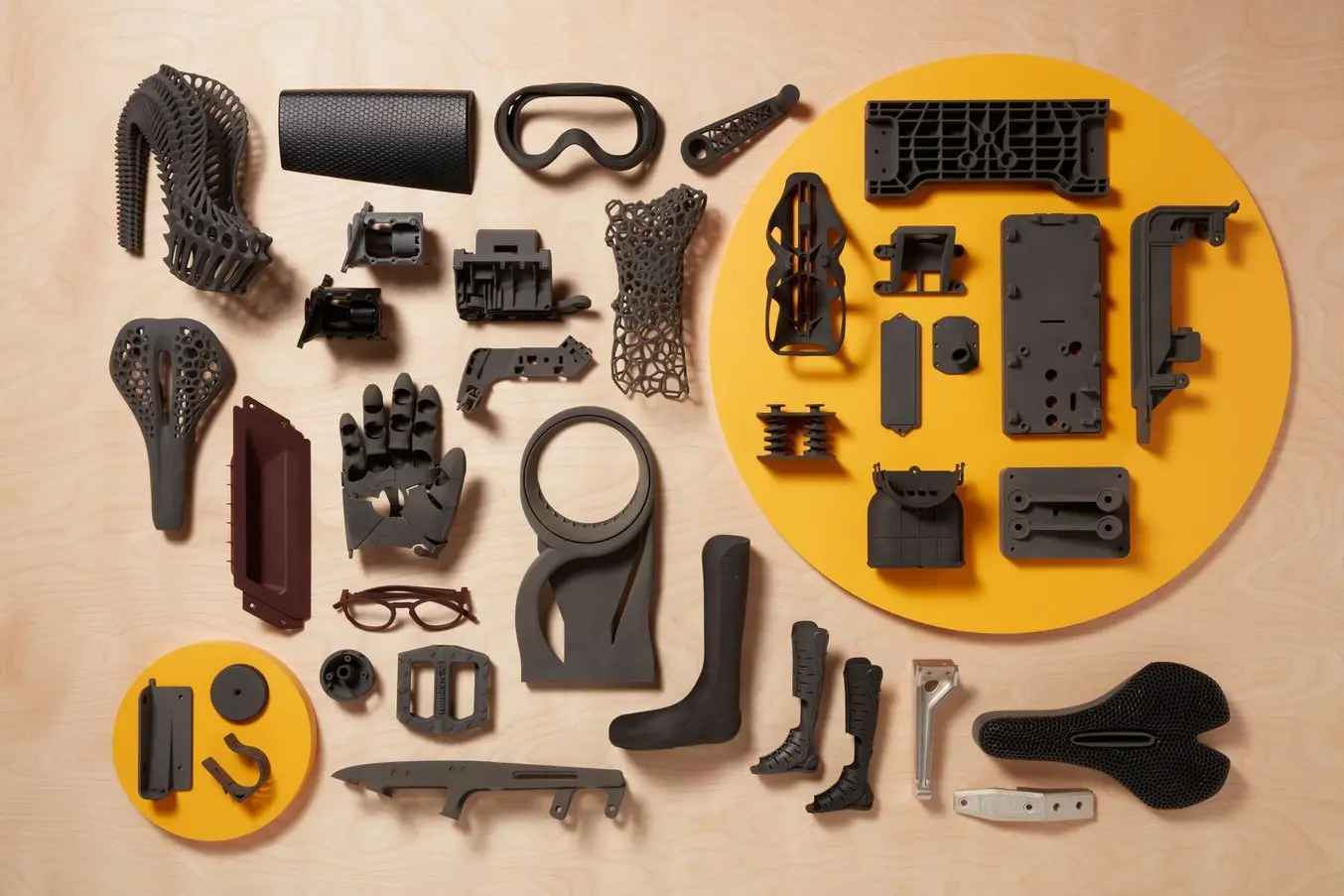
SLS 3D printing accelerates innovation and supports businesses across a wide range of industries, including engineering, manufacturing, and healthcare.
As with any 3D printing technology, the materials themselves are what have the largest impact on performance, and because both SLS and MJF parts are mostly isotropic, it’s the polymer structure that has the biggest impact on strength, ruggedness, and durability. In this respect, SLS and MJF printers are virtually identical.
Workflow
Watch this video to see the step by step process of using a Fuse Series selective laser sintering (SLS) 3D printer and the Fuse Sift powder recovery station.
The workflow for SLS and MJF printers is very similar; powder must be maintained in a controlled environment, post-processed using accessory hardware and tools, and for most printers, can be recycled back into new prints.
Traditional SLS printers and HP’s MJF 3D printer both require intensive, multi-day training for the initial set-up, so that a company technician can instruct the user in the necessary workflow and maintenance steps. Both traditional industrial SLS and MJF printers require ongoing maintenance steps in between each print, so all operators must be trained on the specific machine. For most large businesses, who have their 3D printers in a manufacturing environment with several other advanced machines, this isn’t an additional cost. For healthcare environments, small businesses, and educational institutions, this trained and available operator is an additional incurred cost.
In contrast, Fuse Series SLS printers are ‘plug and play,’ and require a simple set-up of one to two hours before starting the first print, or a virtual training if preferred. Small to medium businesses can add the Fuse Series printers without a full time technician or operator because of the streamlined nature of post-processing, intuitive pre-print setup in PreForm, the lack of daily maintenance tasks, and the small footprint. A product designer can start a print and post-process it each day while maintaining his or her normal workflow.
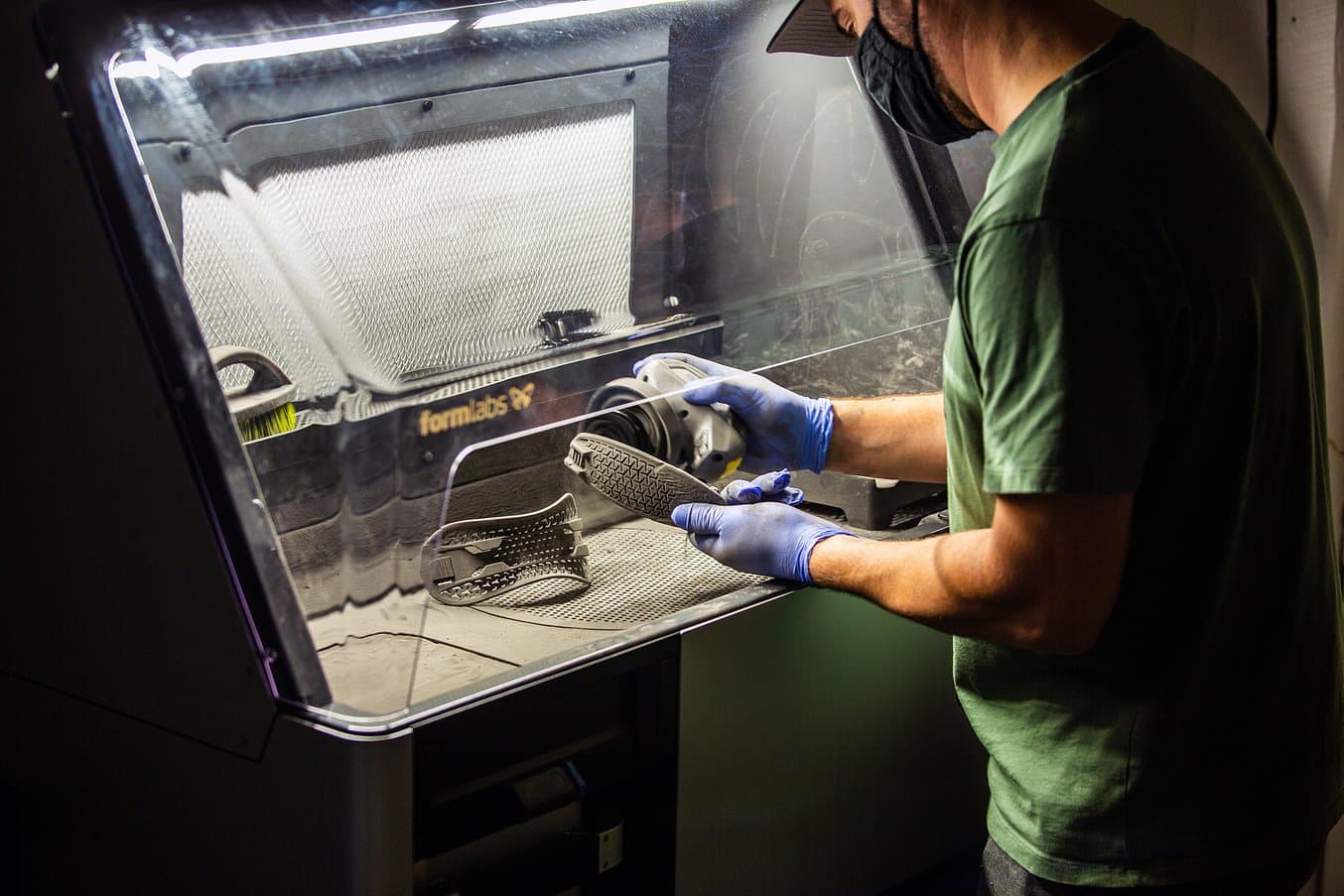
A key element of the workflow for SLS and MJF printers is part recovery, where finished parts are cleaned of excess powder. This process is typically completed manually at a cleaning station, such as the Fuse Sift pictured above, using compressed air or a media blaster.
Efficiency and Sustainability
Though HP’s printers have slightly better refresh rates on paper—requiring around 20% of fresh powder, compared to 30% with most SLS printers—their possible packing density is much lower, around 10%. Low packing density leads to a higher volume of unused powder that then needs to be recycled. Even with a very good refresh rate, like 20%, there is still more unusable powder leftover than there is with an SLS printer capable of high packing densities.
SLS printers are capable of zero waste printing workflows, where all purchased powder is used during a print when utilizing optimal packing densities, and creating the optimal printing environment. With HP Jet Fusion Series printers, users have to discard almost as much powder as they’re using to make parts.
Speed and Throughput
SLS and MJF 3D printers are touted as production machines, capable of high speed and large build volumes that can produce hundreds of parts with each production run. Both MJF printers from HP and traditional SLS systems have large build volumes, but the HP Multi Jet Fusion printers are able to print faster than SLS printers—the dispensing of binding agent and infrared heat exposure takes less time per layer than the scanning speed of lasers used in SLS 3D printers.
However, the high temperature sustained during SLS and MJF printing requires a longer cooldown process for large printers, up to 48 hours. HP offers a refrigeration feature for build chambers that quickens cooldown time, but also comes with an extended footprint and higher cost. Overall, this means that MJF printers are generally capable of a higher throughput than large SLS printers. More compact SLS printers, like the Fuse 1+ 30W have smaller build volume, which results in a shorter cooldown time of only 14 hours for a full build, empowering users to complete finished parts faster than both MJF and large SLS customers.
Scalability is also an important aspect—a business can purchase eight complete Fuse 1+ 30W printer solutions for the same price as a single HP Jet Fusion 4200, leading to comparable throughput. The improved print speed of the Fuse 1+ 30W also allows for double the production of the previous generation model. Most manufacturers do not have products made of only one material, and therefore the ability to print with multiple materials should be taken into account as well when considering throughput.
Footprint and Infrastructure Requirements
Traditional SLS and MJF printers require a three product set-up: the build chamber, which slots into the printer, and the post-processing station. Together, these three parts cover substantial footage and require multiple power sources. Compact SLS printers, like the Fuse Series, enable an efficient, streamlined workflow with the inclusion of the Fuse Sift, and all-in-one powder reclamation, cleaning, and recycling station. Fuse Series printers do not require specialized wiring either and can run on a typical AC power outlet.
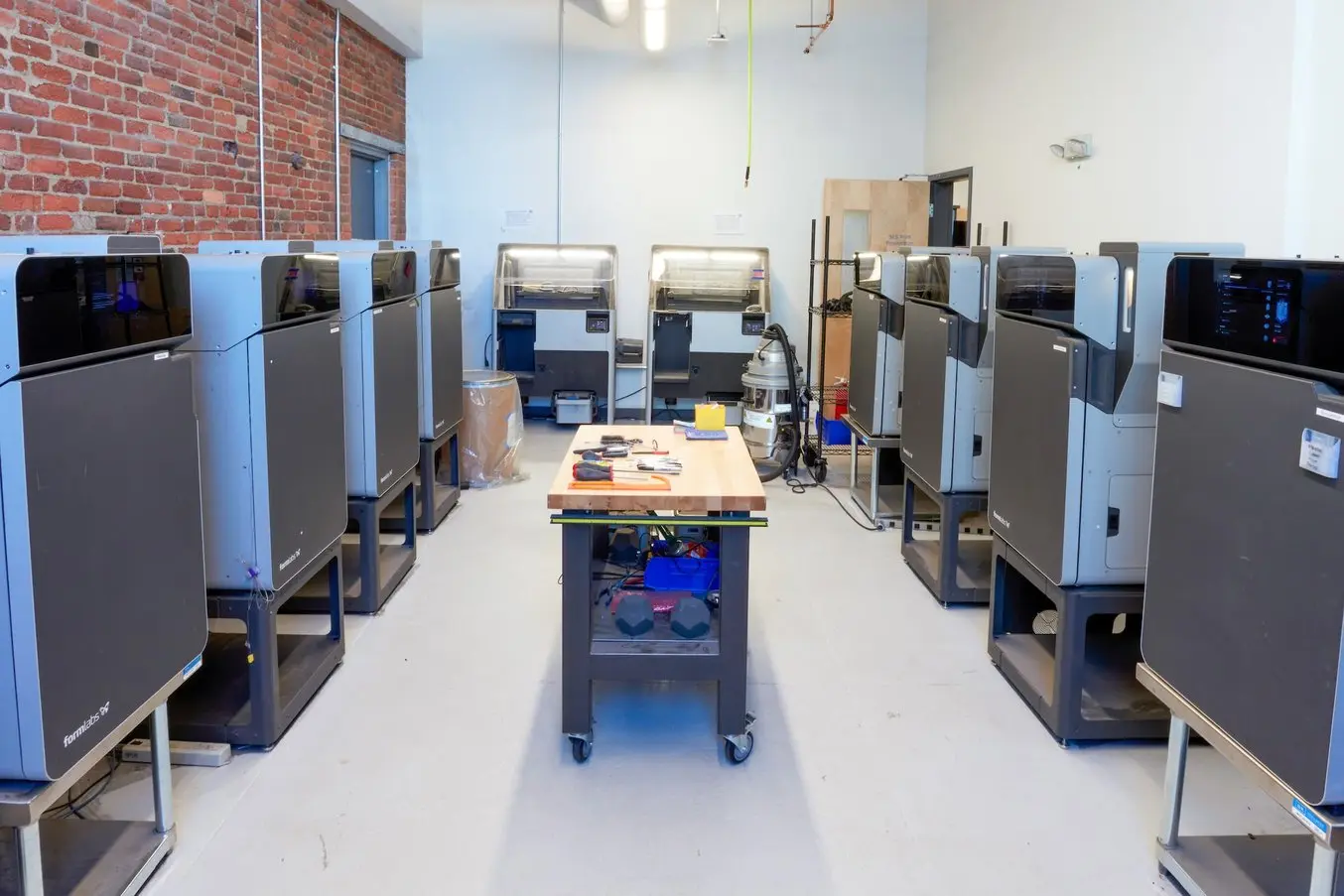
Scaling production with the Fuse Series SLS printers does not require specialized infrastructure or large spaces.
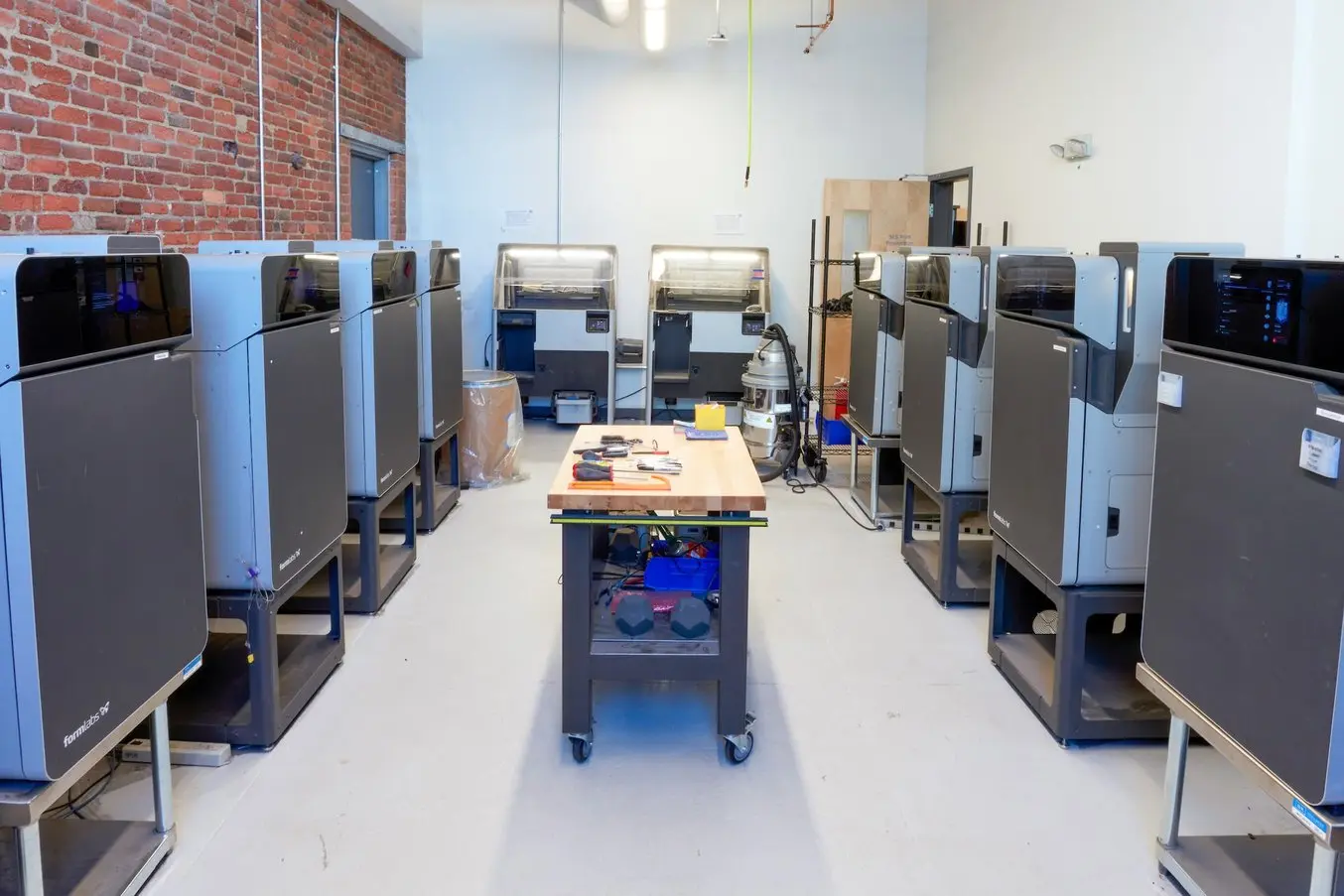
Managing 3D Printer Fleets
Managing multiple SLA and SLS printers doesn’t have to be complicated — any business can get a fleet of SLA and SLS printers up and running in just a day or two. By reviewing four different successful multi-printer scenarios, this guide will help you set up an efficient workflow for any volume or part type.
Color Printing
MJF printers present a big advantage in one area — color 3D printing without a post-print processing step. The binding agent dispensed by jets can include a color, or multiple colors. While SLS users have to paint, dye, or plate their parts to achieve a colored finish, MJF users can plug their color scheme directly into the software. In the healthcare industry, full color parts present a large value, as medical professionals value the ability to achieve a multi-colored anatomical model without additional labor involved.
However, producing full color parts is only possible on the more expensive systems—most of HP’s printers produce parts that are a light grey in color, and require the same painting and dyeing steps that SLS parts do. Full color printing also offers limited finish options. As a result, customers of powder 3D printers most often choose to finish parts and then paint them according to the requirements of the final parts.
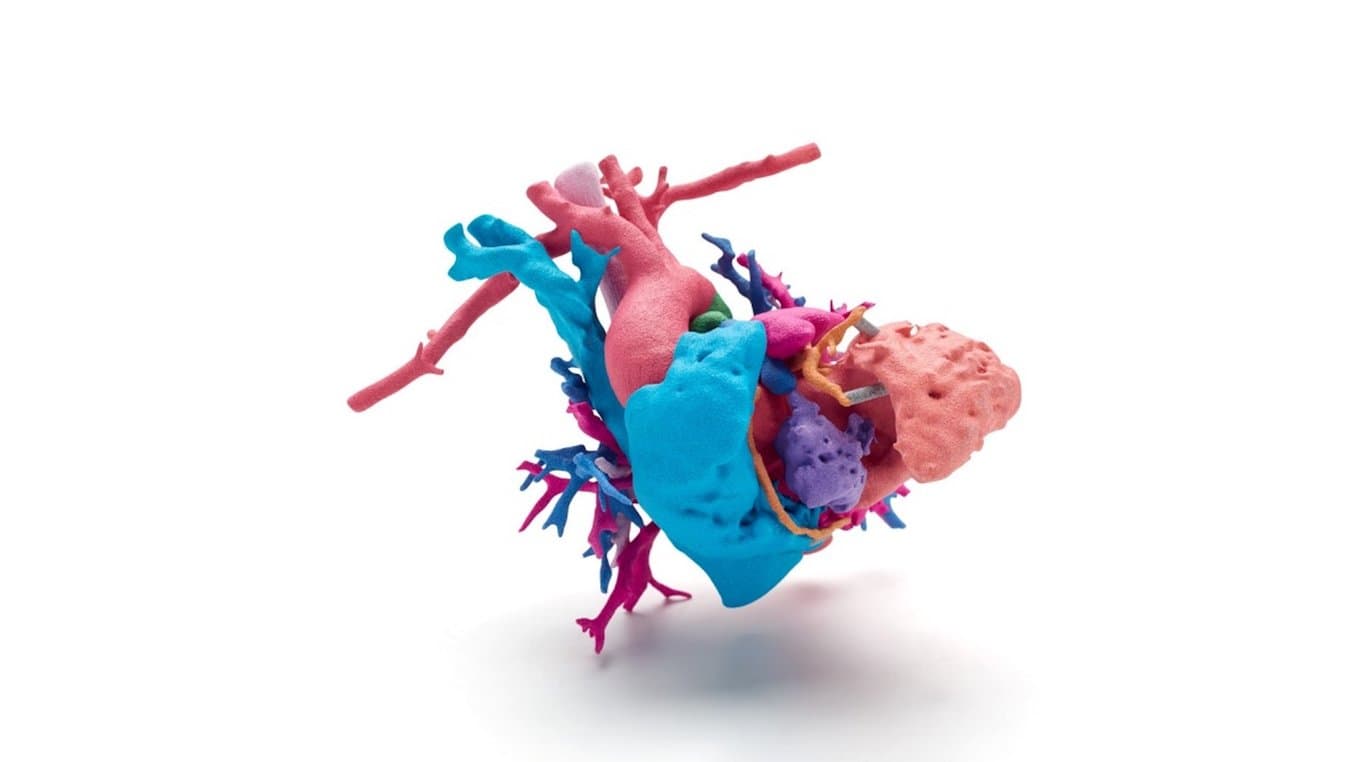
The healthcare industry is a prime example of the advantages of full color 3D printing. Photo courtesy of Phoenix Children’s Hospital.
SLS vs. MJF: Side by Side Comparison
Benchtop Industrial SLS (based on Formlabs Fuse 1+ 30W) | Traditional SLS (based on EOS’ product range) | MJF (based on HP’s MJF 3D printer product range) | ||
---|---|---|---|---|
Pros | Affordable High-quality parts High throughput Multiple material options Simplified workflow Small footprint Low maintenance | Large build volume High-quality parts High throughput Multiple material options | Large build volume High-quality parts High throughput Multiple material options Full color printing | |
Cons | Smaller build volume | Expensive machinery Large footprint Facility requirements High maintenance Complex material switching Requires a dedicated operator | Expensive machinery Wasteful Large footprint Facility requirements High maintenance Complex material switching Requires a dedicated operator | |
Ideal For: | Small, medium, and large businesses, service bureaus | Large businesses, service bureaus | Large businesses, service bureaus | |
Complete Solution Price | $30,000-$60,000 | $200,000 and up | $350,000-$600,000 | |
Maximum Build Volume | 16.5 x 16.5 x 30 cm | 20 x 25 x 33 cm at the entry level, up to 70 x 38 x 58 cm for the largest printers | 38 x 28.4 x 38 cm | |
Material Availability | Nylon 12, Nylon 11, Nylon 12 Glass Filled, Nylon 11 Carbon Fiber, TPU | Nylon 12, Nylon 11, Nylon 12 Glass Filled, Nylon 12 Flame Retardant, Aluminide, TPU | Nylon 12, Nylon 11, Nylon 12 Glass Filled, PP, TPA, TPU | |
Operating Area Requirements | 1.5 × 1.5 × 1.7 m | 3.2 x 3.5 x 3.0 m for the smallest printers, 4.8 x 4.8 x 3.0 m for the largest printers | 3.2 x 2.4 x 2.5 m |
Conclusion: SLS vs MJF 3D Printers For In-House Production
When requesting parts from a service bureau, the end-product, whether produced by an SLS or MJF printer, can be virtually identical. For one-off parts, or for new businesses getting their first product realized, service bureaus are excellent options, and the differences between SLS and MJF printers are not important. At a certain volume however, bringing a powder bed fusion 3D printer in-house is more cost-effective.
Before comparing technical specifications (materials, infrastructure requirements) every user has to first think about initial investment cost. SLS and MJF printers use slightly different technologies, have different sizes, and enable different material libraries, but the biggest difference, by far, is purchase price.
Most small to medium size businesses cannot afford the $340,000 initial investment into MJF printing, not to mention ongoing cost of operation and service contracts, limiting the target market of these machines to large manufacturers and service bureaus with predictable, high-volume 3D printing needs.
There are more options for SLS than MJF, and because the print quality between industrial systems is so comparable, more businesses will find more SLS options which fall within their operation budgets. Factors such as color printing, material availability, workflow, and footprint start to play a more important role once the budget has been established. A more compact SLS printer, such as the Fuse 1+ 30W, is appropriate for a more modest budget. When compared to the costs of outsourcing, it takes most businesses only a couple of months to pay off the initial purchase price.
To determine if the Fuse Series printers are right for your application, you can request a free sample in our four high performance materials, or speak with an SLS expert today.