Watches and their movements are accurate measuring devices that should both look good and suit customers' tastes. Combining these two requirements is not always easy.
Petra Möller, Head of Product Management at Sinn Spezialuhren, and her team regularly face the challenge of transforming product ideas into reality. To achieve this, they have recently started using the Form 3 stereolithography (SLA) 3D printer to create prototypes of their watch designs.
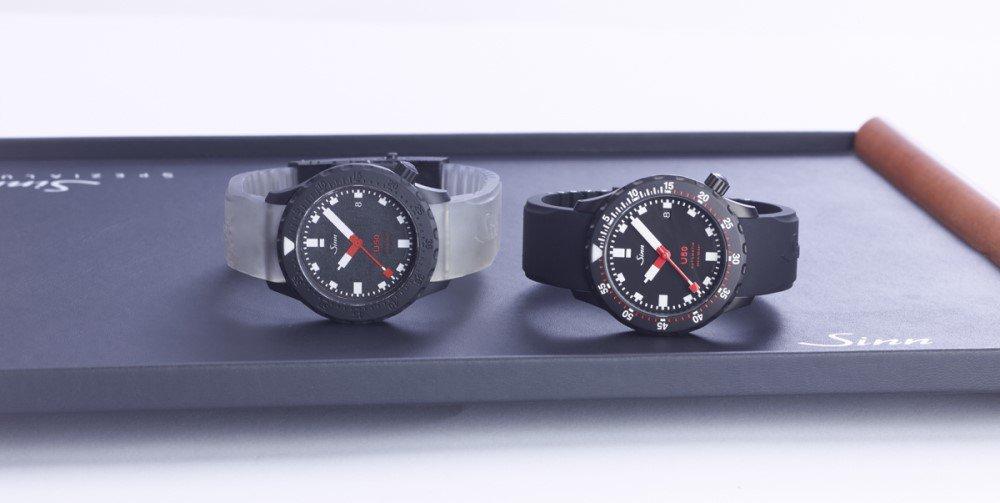
3D printed prototype of a watch produced using the Form 3 next to the final product.
For almost 60 years, Sinn Spezialuhren has been synonymous with feature-rich mechanical watches. Their product portfolio ranges from aviator's watches to diving watches, chronographs, and mission timers worn by pilots, divers, and the GSG 9 elite tactical unit of the German Federal Police. During the development process, the design of a watch is heavily influenced by its intended functionality, which often poses challenges for the team.
Enhancing Product Development With 3D Printed Prototypes
Nils Hunder works in Petra Möller's team on the development and engineering of watch cases, movements, and armbands. The team’s job is to drive product development to serial production and collaborate with all departments.
Watch parts are often small, with fine details significantly influencing the appearance and functionality of a timekeeping device. Some of the fundamental questions during the development process are whether the proportions of the watch are correct, how the case shape looks on the arm, or how the strap can best be attached to the case.
Oftentimes the computerized or handmade product drawings do not optimally convey the reality of the end product on the arm. For the product development to be successful, it is extremely useful to create prototypes before the watch goes into mass production.
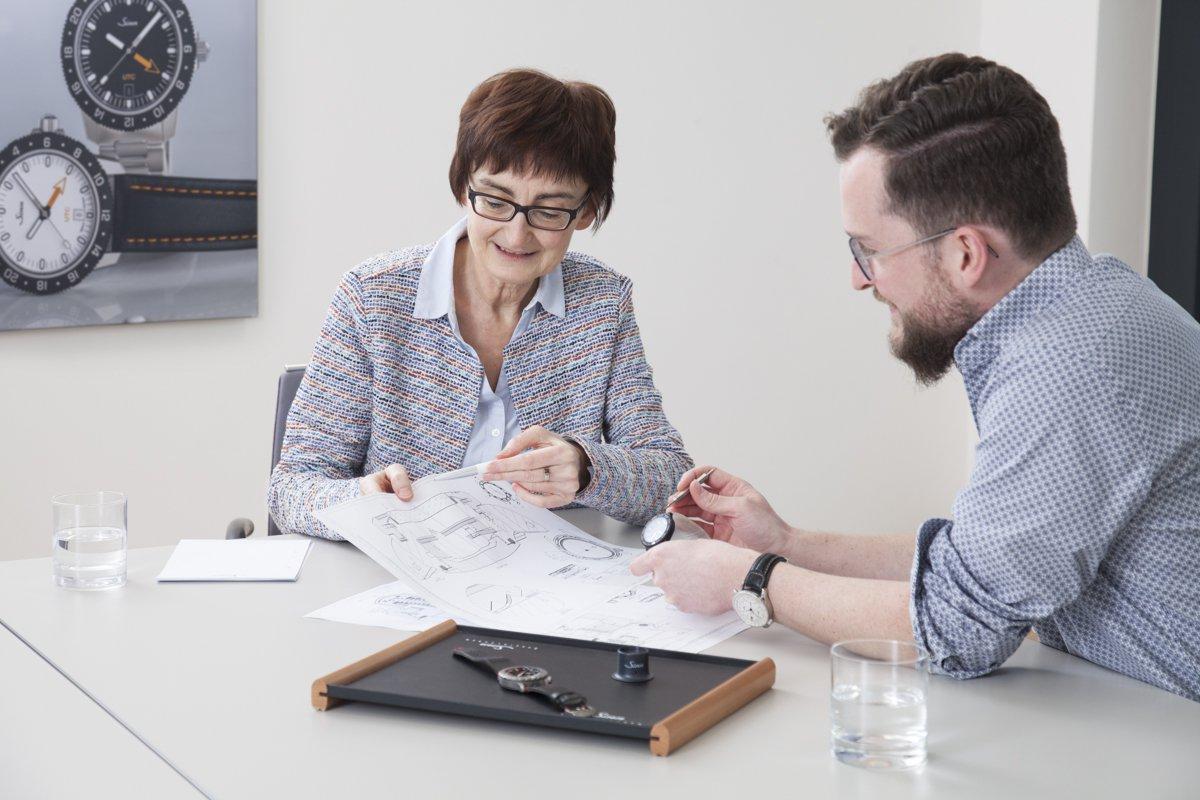
Petra Möller and Nils Hunder comparing the technical drawings with the 3D printed model of a watch.
“The early use of prototypes minimizes wasted investments and misguided developments.”
Petra Möller, Head of Product Management
Until now, Sinn commissioned an external service provider to produce the prototypes. At first, watch models were made from a synthetic resin using SLA 3D printing, which was very delicate and easy to break. It was not the right material for models that also need to be worn on the arm for the right look and feel. The team later switched to 3D printing using fused deposition modeling (FDM) 3D printers and a wax-like material. However, these still had to be cast in aluminum, which was very time-consuming and costly. “In the past, prototypes were used much later in the development process. Everything was already finished by that point, and before pressing the start button on the CNC machine, we looked at the watch a final time,” said Hunder.
The team's desire to bring 3D printing in-house meant that Hunder spent a long time following Formlabs. He was enthusiastic about the smooth surface quality of the SLA 3D printers, even if the Form 1 and Form 2 did not fully convince him of their added value. As it is often necessary to use support structures with SLA technology, the team was unsure for a long time whether an FDM printer with washable support structures and a coarser surface would be the better choice. In the end, it was the surface quality and the easily removable support structures of the Form 3 that convinced Petra Möller and Nils Hunder to purchase the Form 3 along with the Form Wash and Form Cure post-processing tools. Since then, their new Low Force Stereolithography (LFS) printer has been used regularly for prototype development.
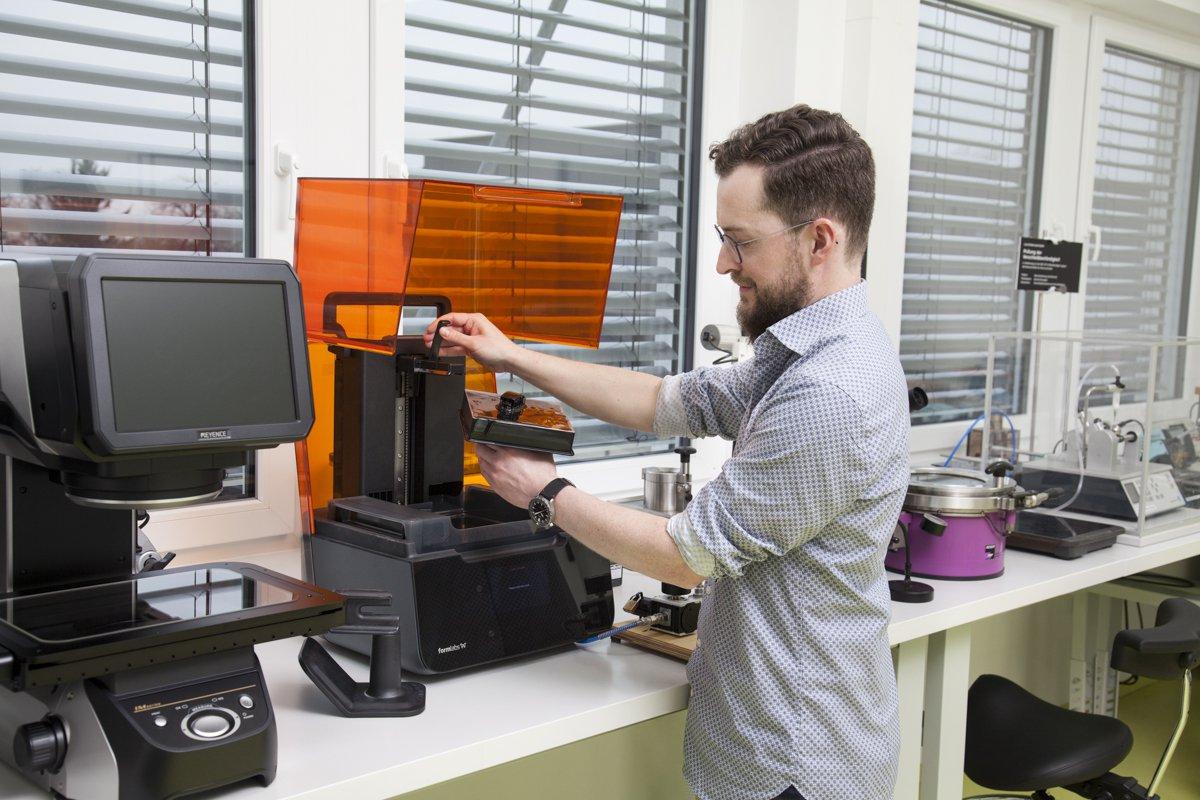
Nils Hunder using the Form 3.
High-Precision Prototypes 3D Printed Overnight
Thanks to the Form 3's high-precision laser, fine details such as engravings or corrugations on the crown of the watch case can be printed. Their preferred material is Black Resin for printing watch cases. Details come out best with a layer thickness of 25 microns. There is almost no post-processing required and the case can be further finished later, for example, airbrushed to achieve the desired color.
“We mainly use the Form 3 during the design process to see the first drafts as soon as possible and to understand how the watch looks in terms of proportions and how it feels on the wrist.'”
Nils Hunder, Engineering and Product Development
The team found that using Form Wash and the correct washing process of the printed parts in tripropylene glycol monomethyl (TPM) with subsequent rinsing in isopropyl alcohol (IPA) was essential. The armbands feature fine channels that can get sealed and trap resin inside during post-curing if the models have not been thoroughly washed.
Aside from this detail, the implementation of 3D printing at Sinn Spezialuhren was child's play. 3D printing is now being used in the early stages of prototype and model development. Models are often printed overnight so that adjustments and new iterations can be made early on.
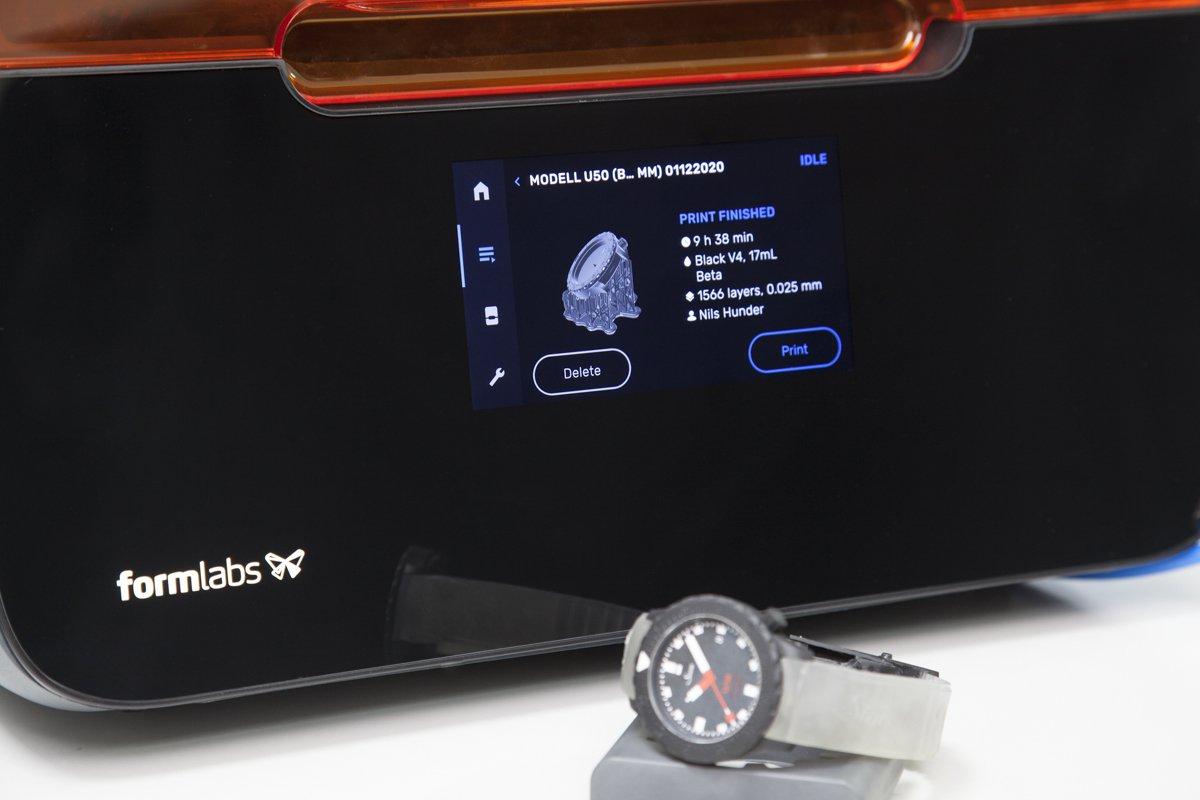
The prototype of a watch in front of the Form 3.
Thanks to the constantly evolving material portfolio for Formlabs 3D printers, the team also regularly receives suggestions for new ideas to test in prototyping. For example, the new Flexible 80A Resin has the same shore hardness as the silicone used for actual watch armbands, so Sinn’s team has already used the material to 3D print silicone-like prototypes.
3D Printing Fast and Cost-Effective Manufacturing Tools for Watchmaking
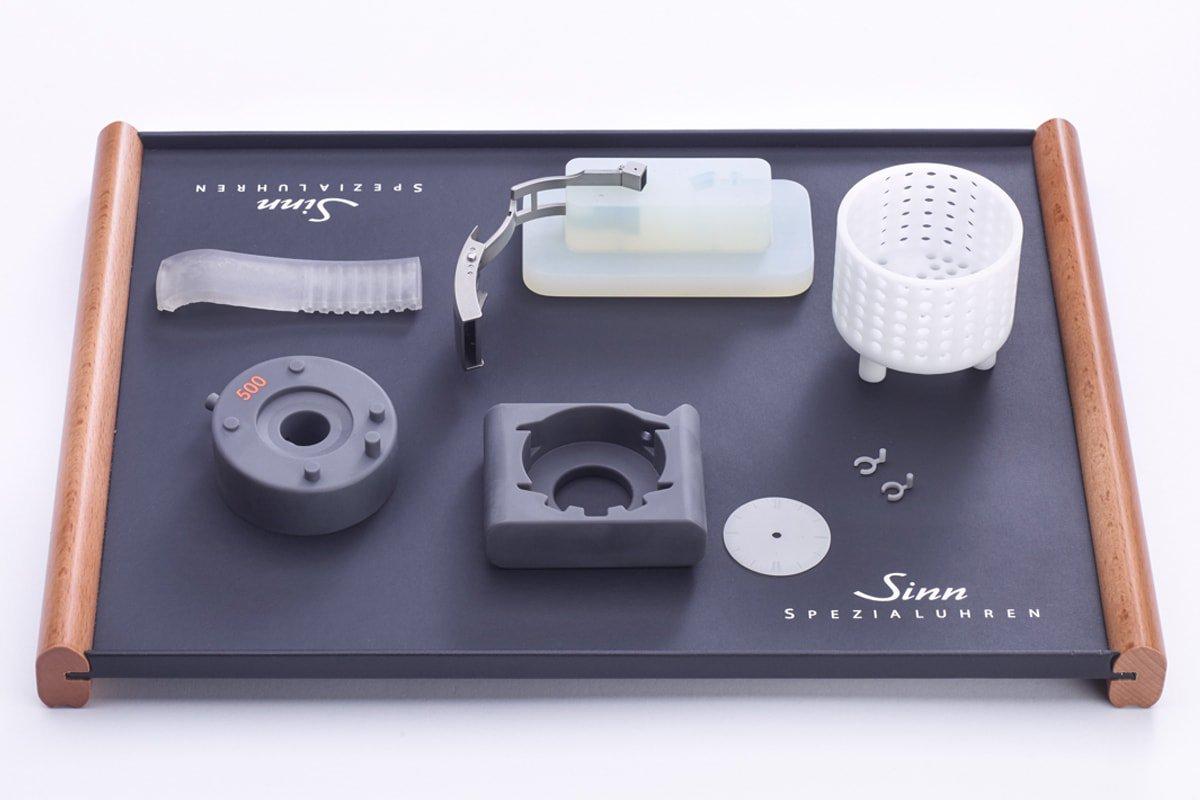
3D printed, prototype watch parts, fixtures, and testing equipment produced using the Form 3.
After purchasing their first 3D printer, Sinn’s team quickly discovered other valuable use cases for the machine beyond prototyping. The Form 3’s versatility and consistency in producing high-quality prints lend itself to different applications throughout product development and production.
Read our next article to learn how the company leveraged 3D printing for producing manufacturing tools, such as mounts, fixtures, and testing equipment.