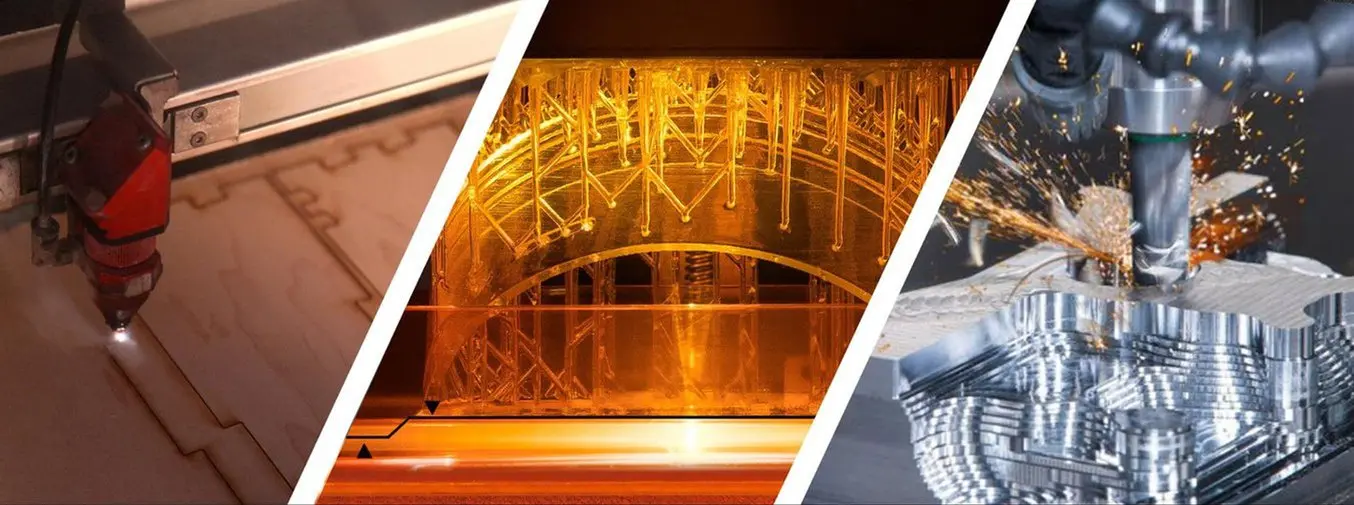
For any emerging or expanding business, it’s crucial to seek solutions for bringing products faster to market. Rapid manufacturing can expedite and increase the flexibility of production, and help cut the time and costs associated with traditional manufacturing for customized products and low-volume series parts.
In this guide, learn about the different rapid manufacturing methods and solutions available today, and how you can use them to choose the right one for your business.
What is Rapid Manufacturing?
Rapid manufacturing stands for the different manufacturing processes that empower the fast and flexible production of end-use parts for customized products, low-volume serial manufacturing, or bridge production.
Most traditional manufacturing processes such as injection molding and casting require tooling that is costly and time-consuming to manufacture. In contrast, rapid manufacturing processes allow for the production of complex parts at a lower cost and time commitment.
There are a variety of different processes involved with rapid manufacturing—additive manufacturing, CNC machining, and rapid tooling, for example. Most of these methods also combine digital design and software automation to accelerate the manufacturing process.
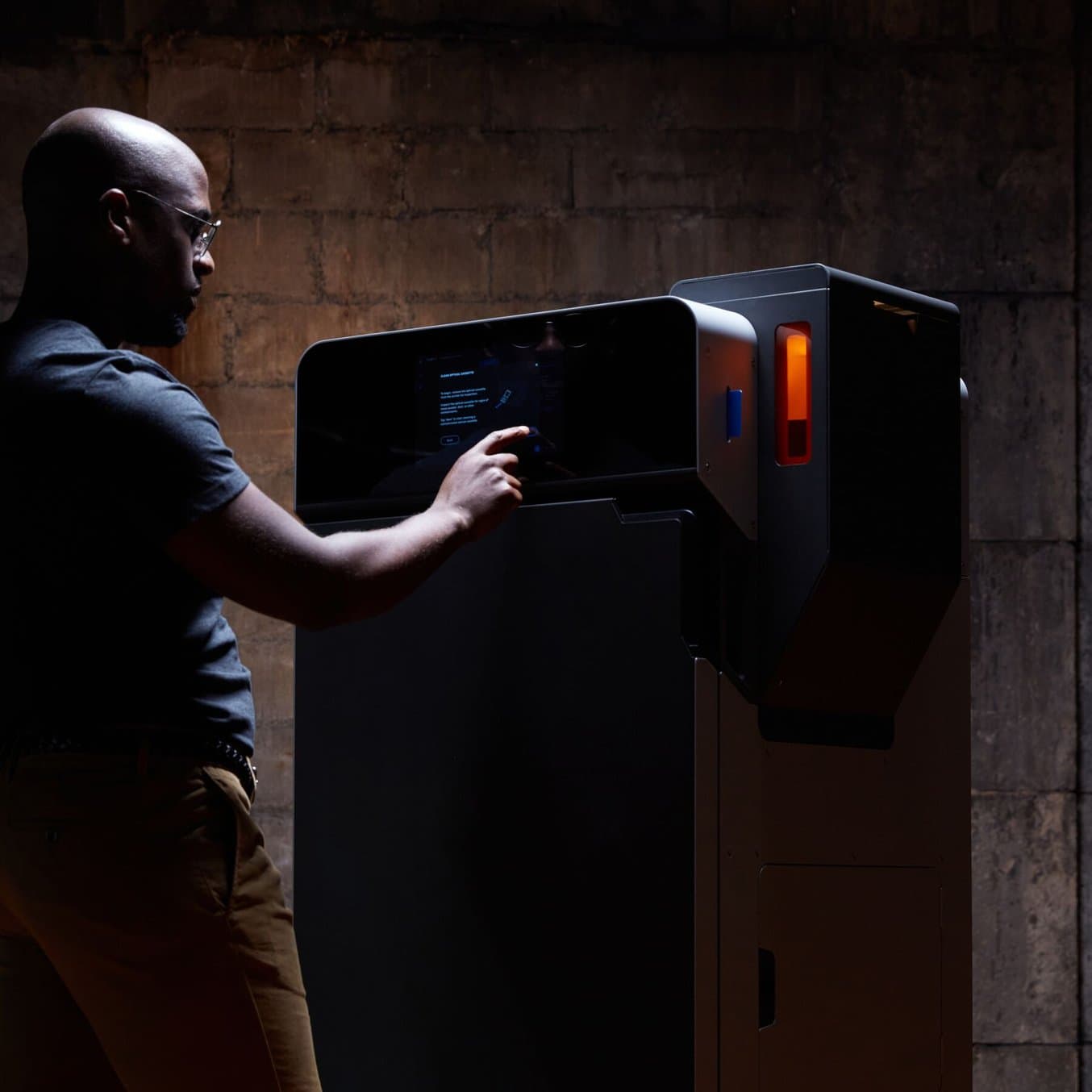
Outsourcing vs. In-House: When Does it Make Sense to Bring SLS 3D Printing In-House?
In this white paper, we evaluate the value proposition of bringing SLS 3D printers in-house, in comparison with outsourcing SLS parts from a service bureau.
Rapid Manufacturing vs. Rapid Prototyping
Rapid prototyping is the group of techniques used to quickly fabricate a scale model of a physical part or assembly using three-dimensional computer-aided design (CAD) data during product development. With rapid prototyping, designers and engineers can create prototypes directly from CAD data faster than ever before, and execute quick and frequent revisions of their designs based on real-world testing and feedback.
Because these parts or assemblies are usually constructed using additive fabrication techniques as opposed to traditional subtractive methods, the phrase has become synonymous with additive manufacturing and 3D printing.
As rapid prototyping tools continued to develop over the years, companies can now use these same techniques to create end-use parts. Thanks to resilient materials and decreasing costs, businesses can increasingly turn to these tools to substitute traditional manufacturing tools or complement their workflows to facilitate a quicker turnaround for finished products.
Rapid Manufacturing vs. Additive Manufacturing
Additive manufacturing (AM), or 3D printing, technologies create three-dimensional parts from computer-aided design (CAD) models by successively adding material layer by layer until a physical part is created.
AM technologies don’t require tooling and can create complex designs for prototyping or manufacturing that would otherwise be too costly or time-consuming, making them ideal for a wide range of engineering and manufacturing applications.
Additive manufacturing techniques are some of the processes rapid manufacturing relies on as a way to create new parts. By producing rapid tooling, additive manufacturing can also reduce the lead time and costs associated with traditional manufacturing processes.
Rapid Manufacturing Methods
Rapid manufacturing relies on a variety of tools and processes to create products. These include additive manufacturing, subtractive tools like CNC machining, and rapid tooling for traditional manufacturing methods.
Additive Manufacturing
Fused Deposition Modeling (FDM)
FDM 3D printing, also known as fused filament fabrication (FFF), is a 3D printing method that builds parts by melting and extruding thermoplastic filament, which a printer nozzle deposits layer by layer in the build area.
FDM is the most widely used form of 3D printing at the consumer level, fueled by the emergence of hobbyist 3D printers. Industrial FDM printers are, however, also popular with both design professionals and manufacturers.
FDM has the lowest resolution and accuracy when compared to other plastic 3D printing processes and is not the best option for printing complex designs or parts with intricate features. Higher-quality finishes may be obtained through chemical and mechanical polishing processes. Industrial FDM 3D printers use soluble supports to mitigate some of these issues.
FDM works with a range of standard thermoplastics, such as ABS, PLA, and their various blends. Industrial FDM printers also offer a wider range of engineering thermoplastics or even composites. For manufacturing, FDM printers are particularly useful for producing simple parts, such as parts that might typically be machined.
Stereolithography (SLA)
SLA 3D printers use a laser to cure liquid resin into hardened plastic in a process called photopolymerization. SLA is one of the most popular processes among professionals due to its high resolution, precision, and material versatility.
SLA parts have the highest resolution and accuracy, the clearest details, and the smoothest surface finish of all plastic 3D printing technologies, but the main benefit of SLA lies in its versatility. Material manufacturers have created innovative SLA photopolymer resin formulations with a wide range of optical, mechanical, and thermal properties to match those of standard, engineering, and industrial thermoplastics.
SLA is a great option for highly detailed parts requiring tight tolerances and smooth surfaces, such as molds, patterns, and other functional end-use parts. SLA is used for rapid manufacturing in a range of industries from dentistry, to jewelry, healthcare, model making, and increasingly, consumer products.
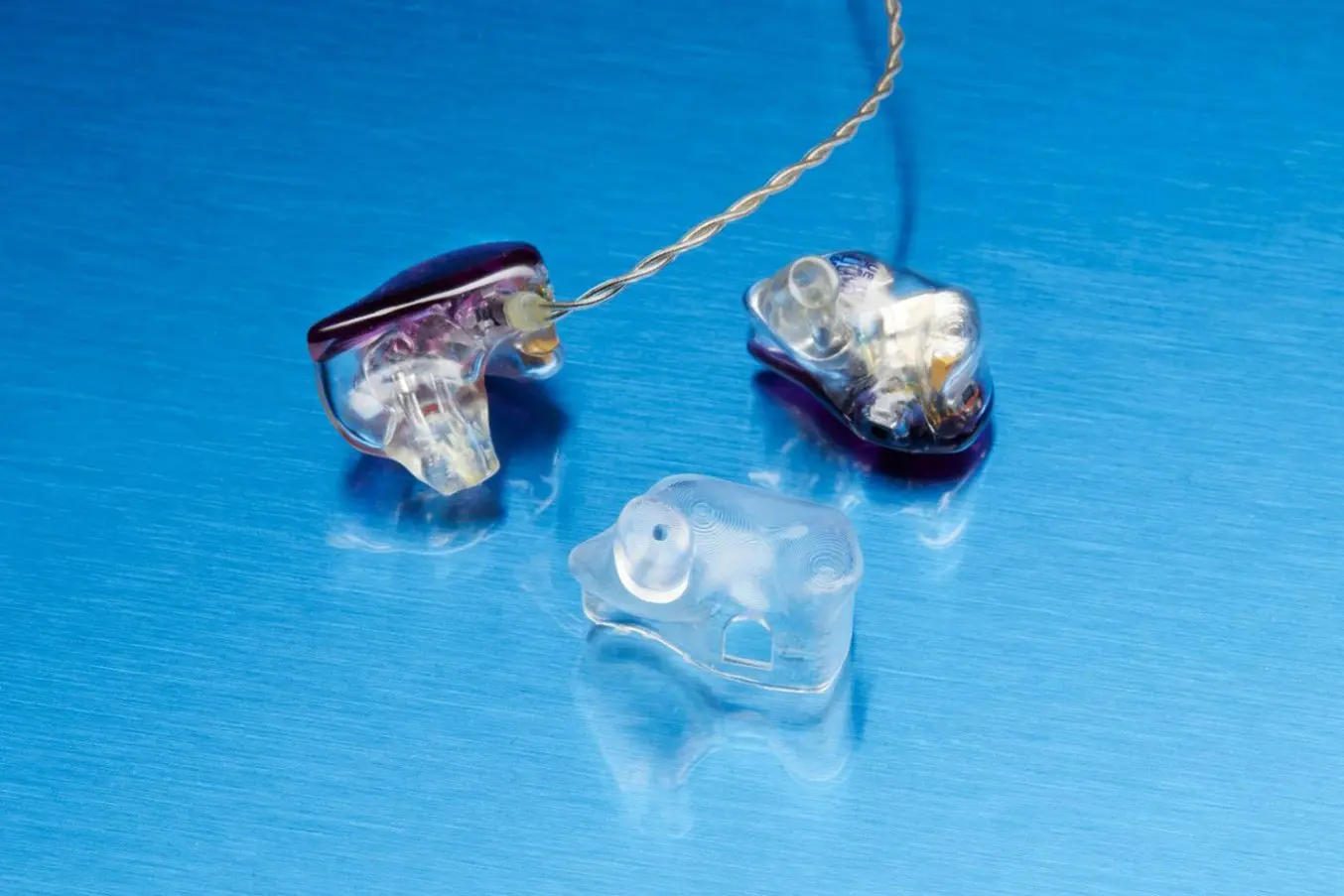
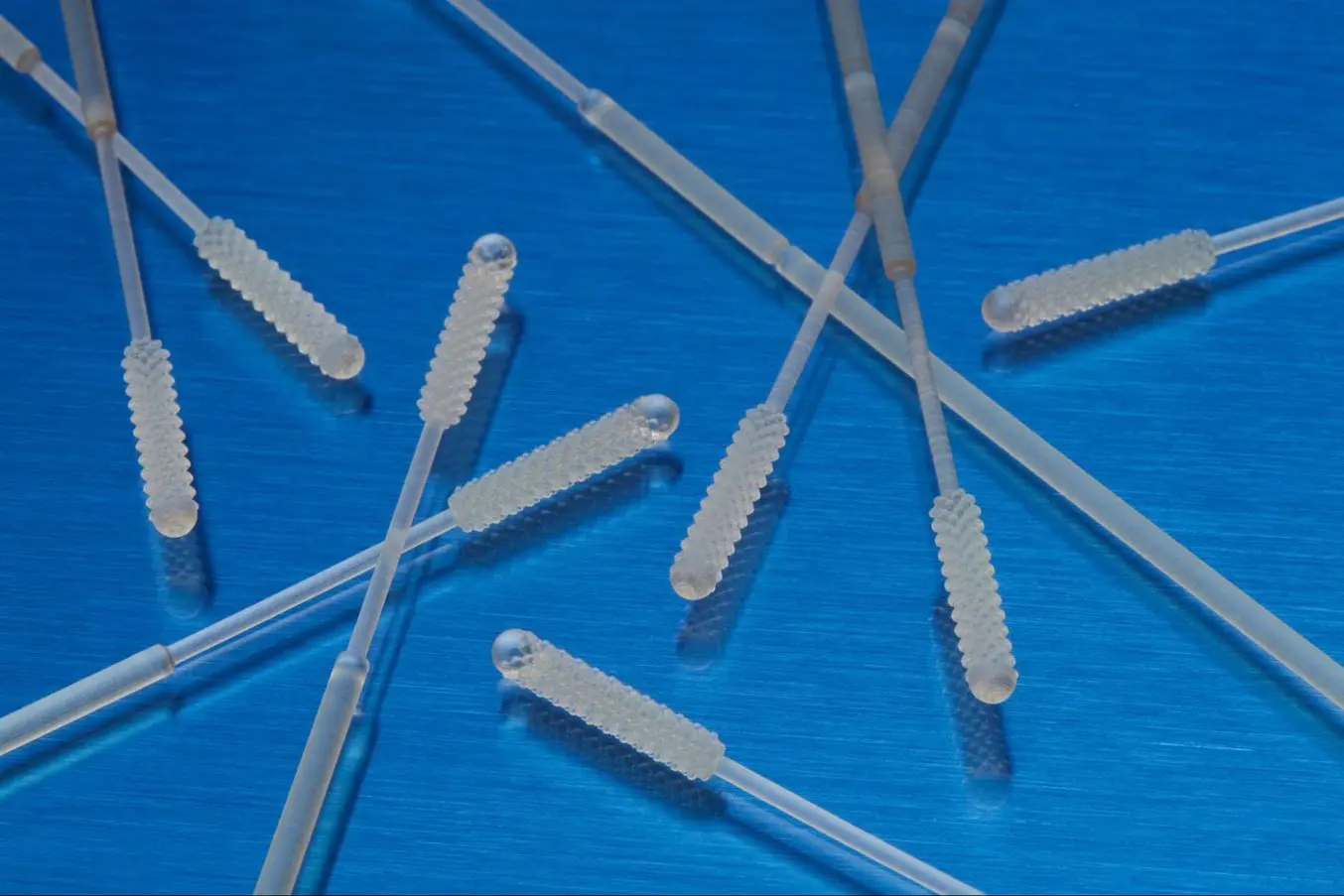
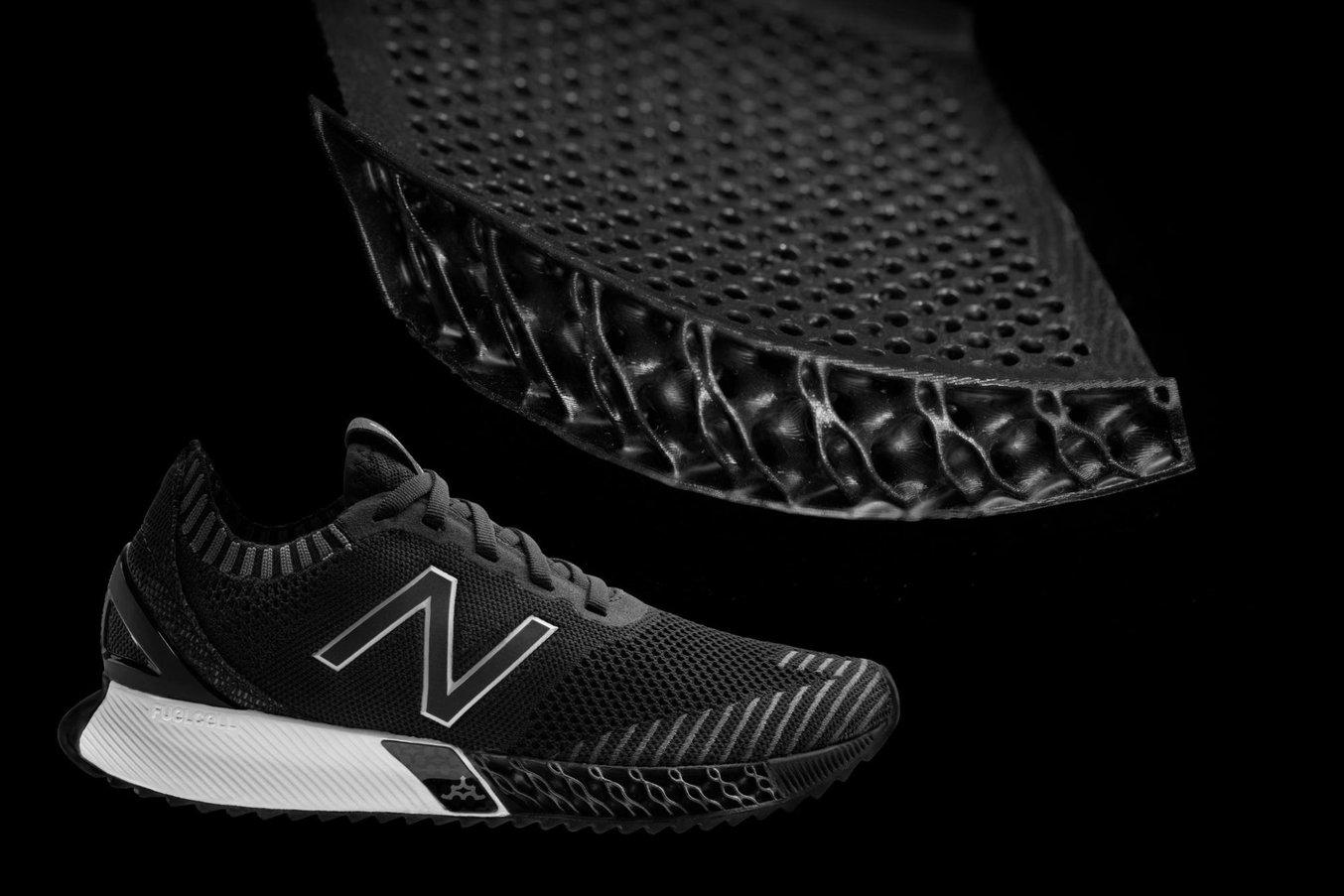
SLA 3D printing can be used for a variety of applications, including the rapid manufacturing of custom earphones, medical swabs, and shoe soles.
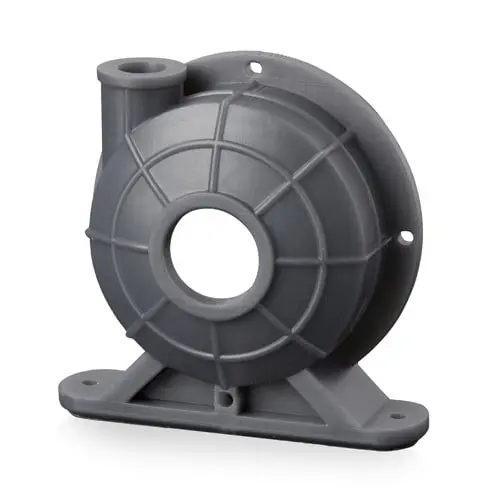
Request a Free Sample Part
See and feel Formlabs SLA quality firsthand. We’ll ship a free sample part to your office.
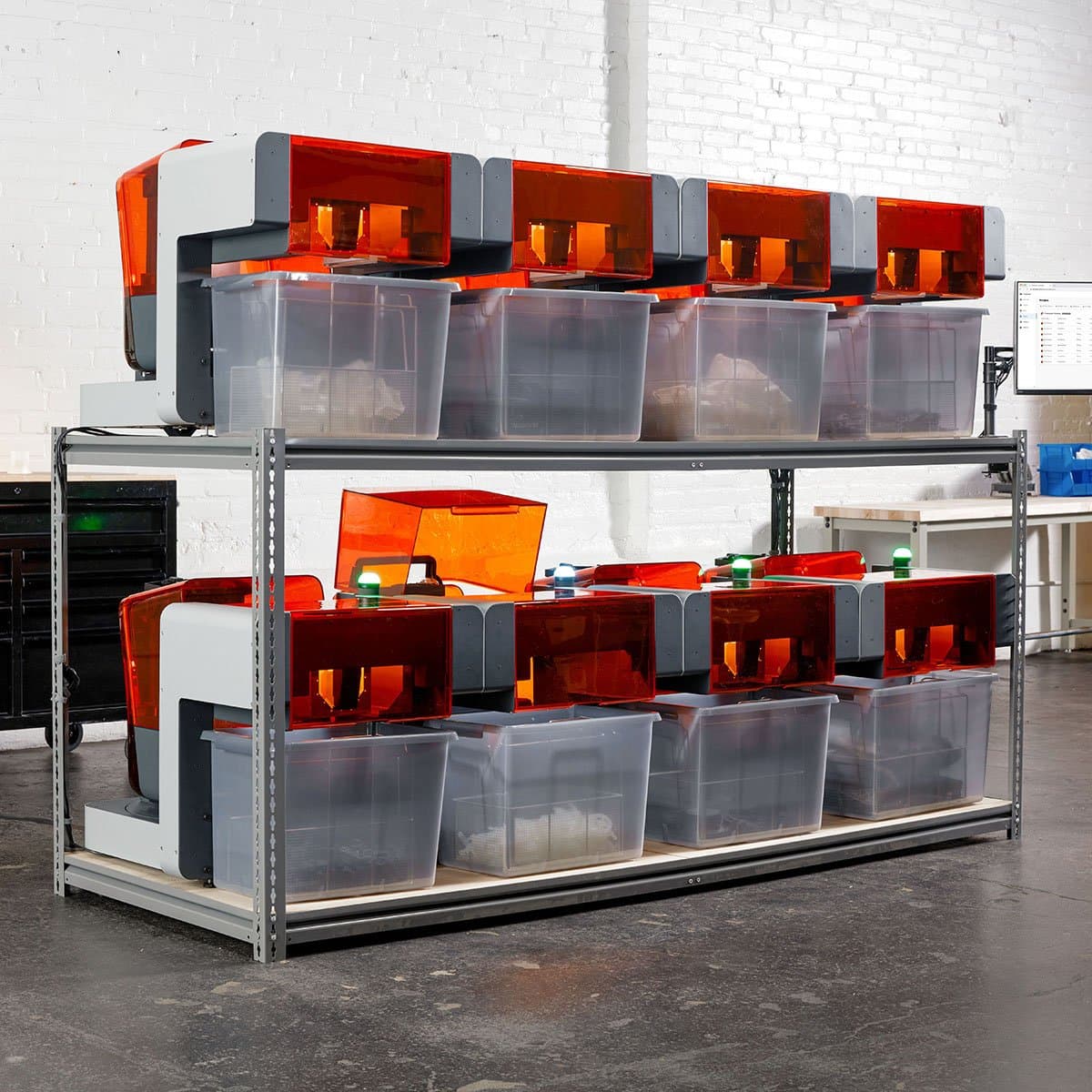
24/7 Production With Formlabs Automation Ecosystem
Reach new levels of productivity with a fully automated 3D printer fleet that you can operate at any place and from anywhere.
Selective Laser Sintering (SLS)
Selective laser sintering is the most common additive manufacturing technology for industrial applications, trusted by engineers and manufacturers across different industries for its ability to produce strong, functional parts.
SLS 3D printers use a high-powered laser to fuse small particles of polymer powder. The unfused powder supports the part during printing and eliminates the need for dedicated support structures. This makes SLS ideal for complex geometries, including interior features, undercuts, thin walls, and negative features. Parts produced with SLS printing have excellent mechanical characteristics, with strength resembling that of injection-molded parts.
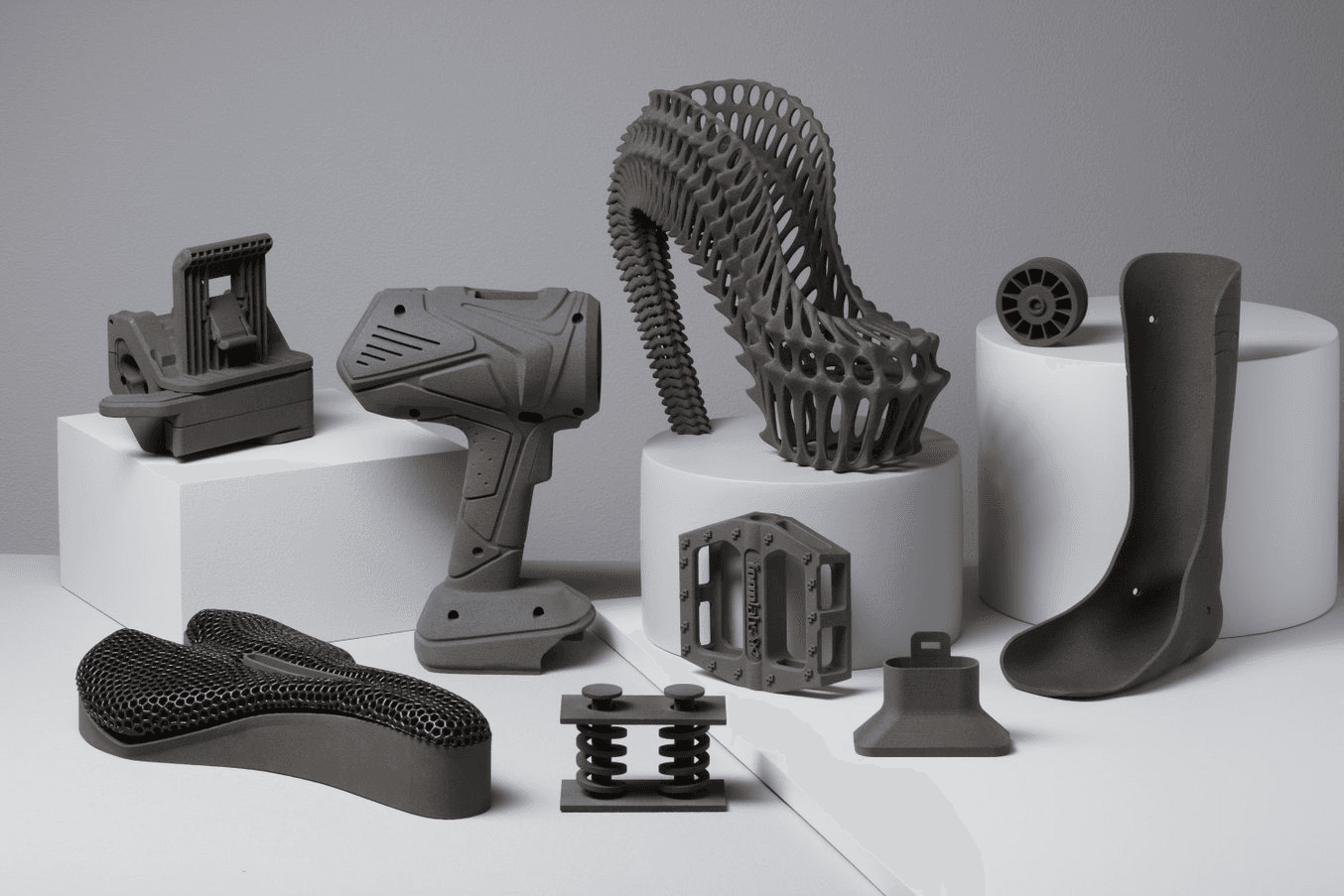
SLS 3D printing can produce strong, functional parts for applications like small-batch manufacturing, mass customized consumer products, and replacement parts.
In manufacturing, SLS 3D printing is used for small-batch manufacturing, the production of novel mass customization consumer products, replacement part production, as well as long-lasting, durable jigs and fixtures (e.g clips and clamps) and tooling. SLS can also be used to manufacture ready-to-use, patient-specific medical devices in-house, such as prosthetics, orthotics (i.e. limb replacements + braces), surgical models, and tools.
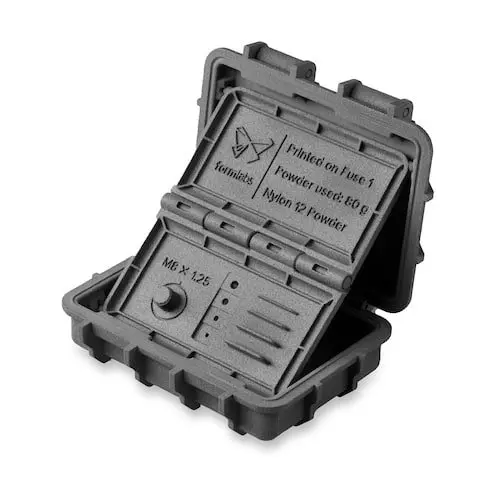
Request a Free Sample Part
See and feel Formlabs SLS quality firsthand. We’ll ship a free sample part to your office.
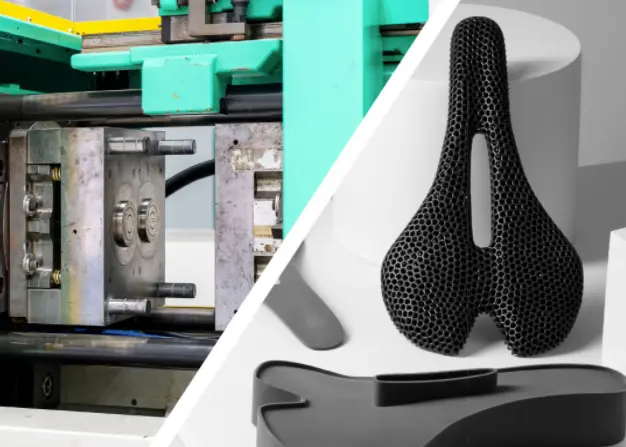
SLS 3D Printing vs. Injection Molding: When to Replace Molded Parts With 3D Printing?
This white paper showcases the cost-dynamics for real-life use cases, and presents guidelines for using SLS 3D printing, injection molding, or both.
CNC Tools
Computer numerical control (CNC) tools—unlike FDM, SLA, or SLS—are subtractive manufacturing processes. They start with solid blocks, bars, or rods of plastic, metal, or other materials that are shaped by removing material through cutting, boring, drilling, and grinding.
CNC tools include CNC machining, which removes material by either a spinning tool and fixed part (milling) or a spinning part with a fixed tool (lathe). Laser cutters use a laser to engrave or cut through a wide range of materials with high precision. Water jet cutters use water mixed with abrasive and high pressure to cut through practically any material. CNC milling machines and lathes can have multiple axes, which allows them to manage more complex designs. Laser and water jet cutters are more suited for flat parts.
CNC tools can shape parts from plastics, soft metals, hard metals (industrial machines), wood, acrylic, stone, glass, composites. For rapid manufacturing, they’re ideal for producing custom or low-volume end-use parts, structural parts, and tooling for a wide range of industries.
Compared to additive manufacturing tools, CNC tools are more complicated to set up and operate, while some materials and designs might require special tooling, handling, positioning, and processing. This makes them costly for one-off parts compared to additive processes and better suited for small production runs.
Rapid Tooling
Hybrid manufacturing combines rapid manufacturing tools with traditional manufacturing processes like injection molding, thermoforming, or casting. It enhances the production process by improving its flexibility, agility, scalability, and cost-efficiency. As a result, it enables manufacturers to meet changing business needs quickly.
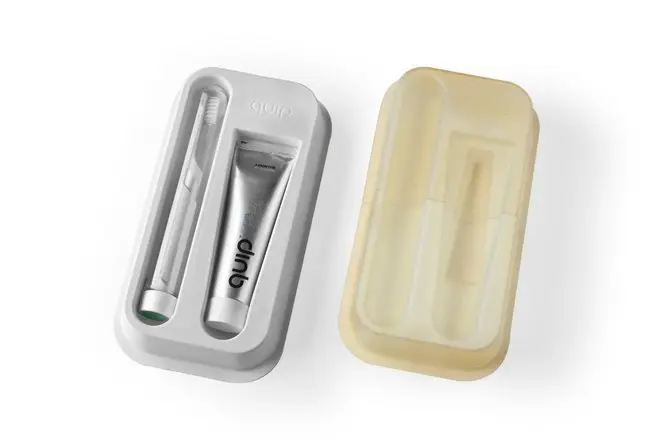
A 3D printed mold for vacuum forming product packaging.
-
Tooling
Build custom tooling that stands up to the rigors of the factory floor, and can help solve the toughest manufacturing challenges. Validate manufacturing processes, solve DFM issues, and increase flexibility by direct printing of tooling for applications ranging from injection molding to CNC tube bending.
-
Jigs and fixtures
Reduce costs and increase agility by bringing jig and fixture production in-house with no minimum order quantities, no toolpath programming (for 3D printing), wide material selection, and low capital equipment costs. Continuously improve products and respond quickly and effectively to issues on your manufacturing line with jigs and fixtures that improve assembly or QA processes.
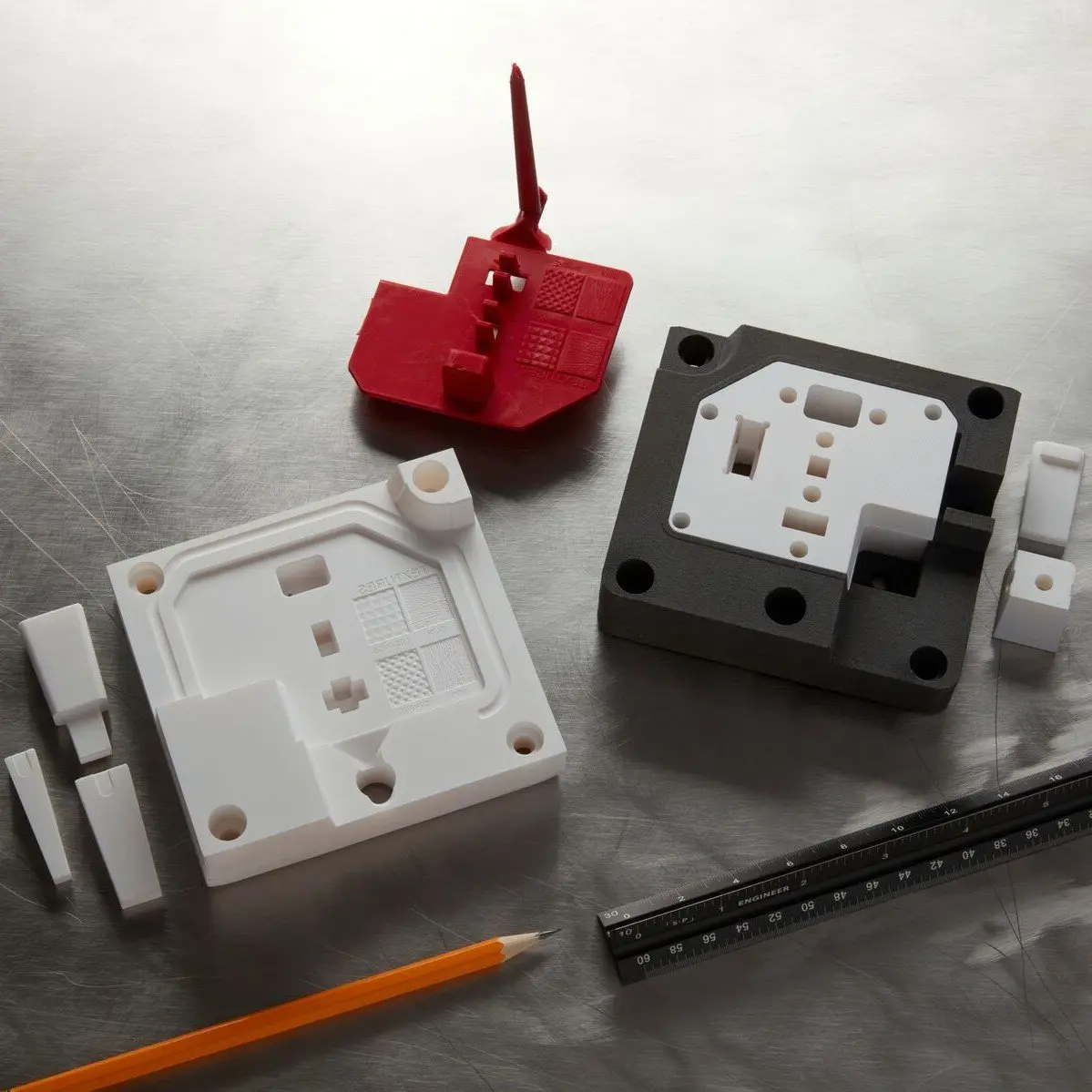
Guide to Rapid Tooling
In this white paper, learn how to combine rapid tooling with traditional manufacturing processes like injection molding, thermoforming, or casting.
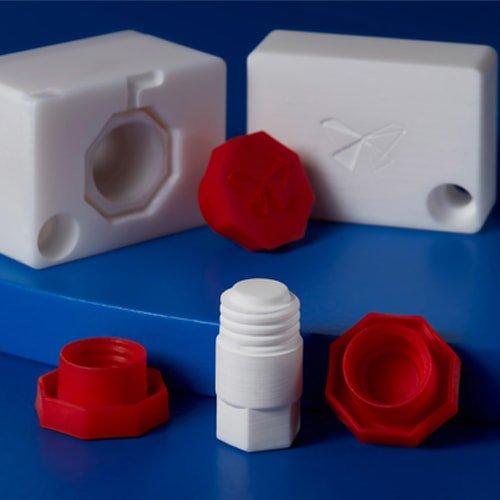
Low-Volume Rapid Injection Molding With 3D Printed Molds
Download our white paper for guidelines for using 3D printed molds in the injection molding process to lower costs and lead time and see real-life case studies with Braskem, Holimaker, and Novus Applications.
Choosing the Right Rapid Manufacturing Process
As manufacturing processes are constantly evolving, the inflection points where it makes sense to move from one technique to another are shifting due to improvements in equipment, materials, and economies of scale.
Rapid manufacturing tools are opening up to a wider range of low- to mid-volume applications as hardware and materials improve and cost per part continues to fall.
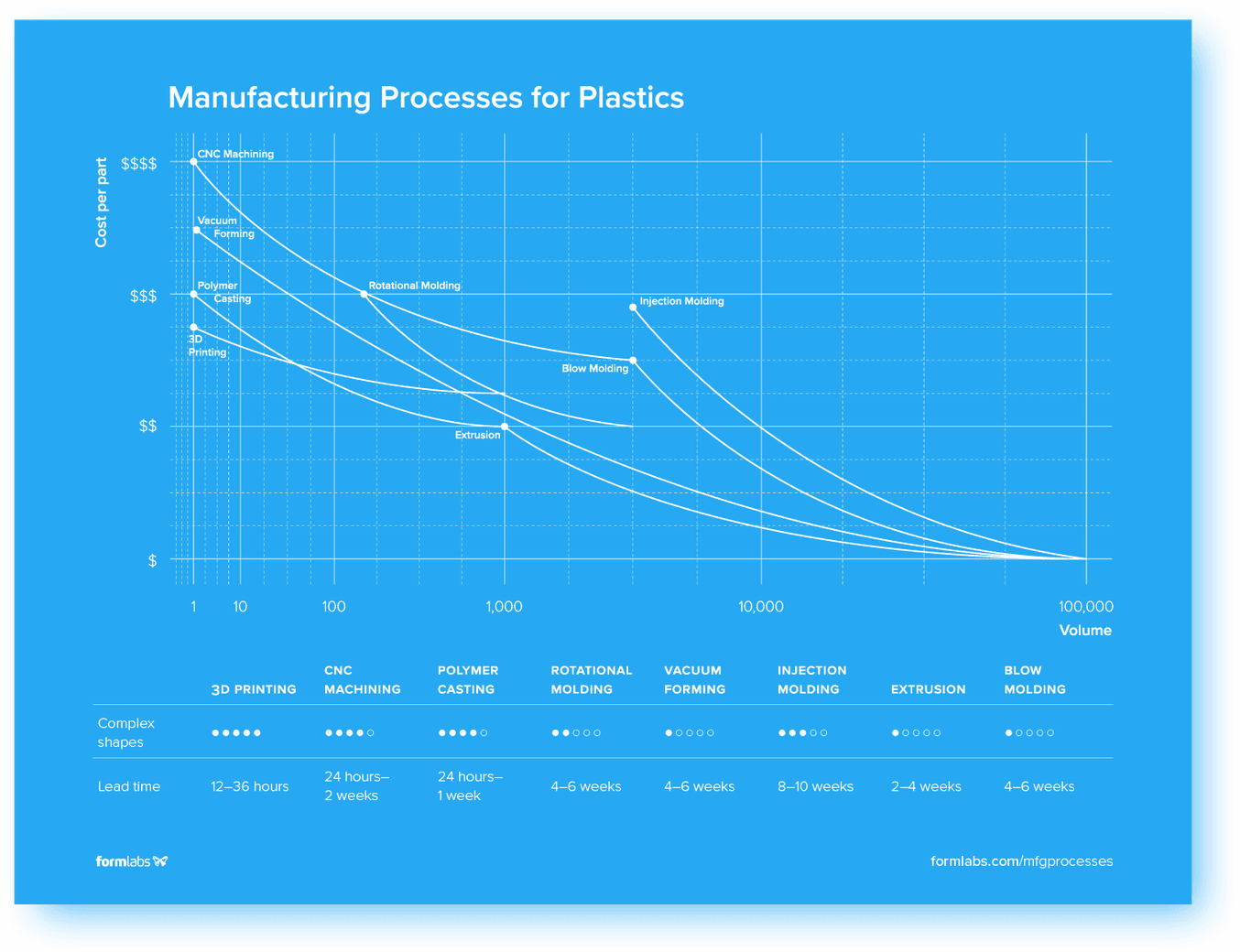
Consider the following factors when selecting a rapid manufacturing process:
-
Form: Do your parts have complex internal features or tight tolerance requirements? Depending on the geometry of a design, manufacturing options may be limited, or they may require significant design for manufacturing (DFM) optimization to make them economical to produce.
-
Volume/cost: What’s the total or the annual volume of parts you’re planning to manufacture? Some manufacturing processes have high upfront costs for tooling and setup, but produce parts that are inexpensive on a per-part basis. In contrast, low-volume manufacturing processes have low startup costs, but due to slower cycle times, less automation, and manual labor, cost per part remains constant or decreases only marginally when volume increases.
-
Lead time: How quickly do you need parts or finished goods produced? Some processes create the first parts within 24 hours, while tooling and setup for certain high volume production processes take months. In some cases, rapid tooling can shorten this lead time significantly.
-
Material: What stresses and strains will your product need to stand up to? The optimal material for a given application is determined by a number of factors. The cost must be balanced against functional and aesthetic requirements. Consider the ideal characteristics for your specific application and contrast them with the available choices in a given manufacturing process.
Outsourcing vs. In-House Production
Businesses looking to capitalize on the power of rapid manufacturing tools have the option to outsource the work to a service bureau or to produce in house.
Companies like 3D Hubs, Protolabs, Fictiv, or local service bureaus offer manufacturing and rapid prototyping services on demand. These bureaus typically have multiple technologies available, including both additive and subtractive processes.
The main downsides of outsourcing to service bureaus are cost and lead time. One of the greatest benefits of rapid manufacturing is its speed compared to traditional manufacturing methods, which quickly diminishes when an outsourced part takes a week or even multiple weeks to arrive.
Outsourcing the manufacturing of parts is also often very expensive. But depending on the number of parts and printing volume, a business can break even within a few months by simply investing in a 3D printer and printing in house.
Getting Started With Rapid Manufacturing
Traditional methods still hold a place in manufacturing because they are more suitable for mass production. But increasingly, companies are turning toward rapid manufacturing as a way to perform small-run productions. Technological advancements and beneficial associated processes—such as fast production tools and hybrid manufacturing—are influential in this shift.
See how Formlabs makes in-house rapid manufacturing accessible for businesses with affordable, high-performance 3D printers.