Requirements, Post-Processing, Maintenance: Everything You Need To Know About Using the Fuse 1
With only one year on the market, the Fuse 1 selective laser sintering (SLS) 3D printer already accounts for almost half of all SLS printers sold since its launch. Due to its compact design, intuitive workflow, and affordable price point, the Fuse 1 printer enables small businesses to bring SLS printing in-house, and allows larger businesses to scale production easily and affordably. Drawing from the experience of our expert users, we’ve compiled the most important pieces of information for anyone considering adding SLS to their workflow.
In this article we’ll cover:
-
Infrastructure requirements for the Fuse 1 and Fuse Sift
-
Tips for workflow efficiency and productivity
-
Recommendations for post-processing
-
Common concerns about SLS printing and how the Fuse 1 addresses them
Accessibility: Size, Power, Accessories
Formlabs developed the Fuse 1 with accessibility in mind. Most businesses do not have lots of extra square footage in their facilities, nor the ability to add the multiple specialized circuits historically required by SLS systems. Many of our customers are operating out of office spaces, rather than warehouses and engineering facilities–they have limited ability to change their spaces’ size, electrical circuitry, and ventilation systems. The Fuse 1 offers a solution to that dilemma; it was designed to be compact, easy to install, safe and intuitive to use, and requires minimal cleanup.
Size: Delivery and Install
Most SLS systems require lift gates and forklifts to install. The Fuse 1 and Fuse Sift can be carried by two people (using a lifting strap between them), making office buildings, stairs, and narrow doorways easy to maneuver. Formlabs customer PrintParts has received and installed 12 Fuse 1 printers and six Fuse Sifts in their Manhattan office space, without having to use large lift gates, or change their site’s ventilation system.
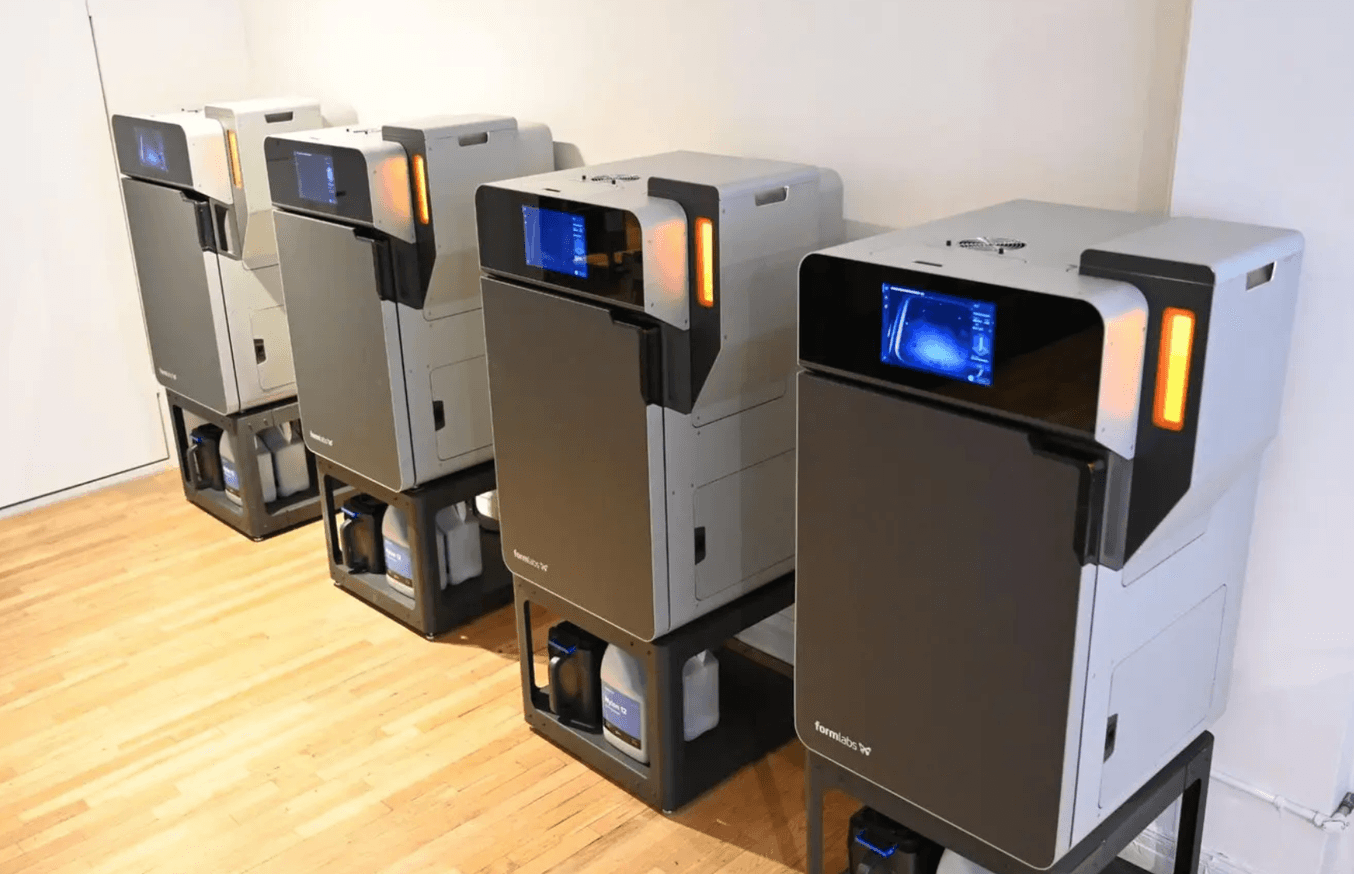
The initial PrintParts set-up of Fuse 1 printers
For the delivery of a Fuse 1, you can choose either:
- Plug-And-Play: Delivery team will bring machines off the truck, into your building, and to the printers final printing area. If there is a change of floor level, you’ll need a freight elevator.
- Dock Delivery: Delivery team will bring machines to a loading dock, which needs the ability to receive palletized or freight deliveries.
The set-up location, with one Fuse 1 printer and one Fuse Sift, placed side by side, will require a space at least 310 cm (10ft) wide and 146 cm (4.8ft) deep (out from a wall). A normal ceiling height of 2.5m (8ft) is just fine.
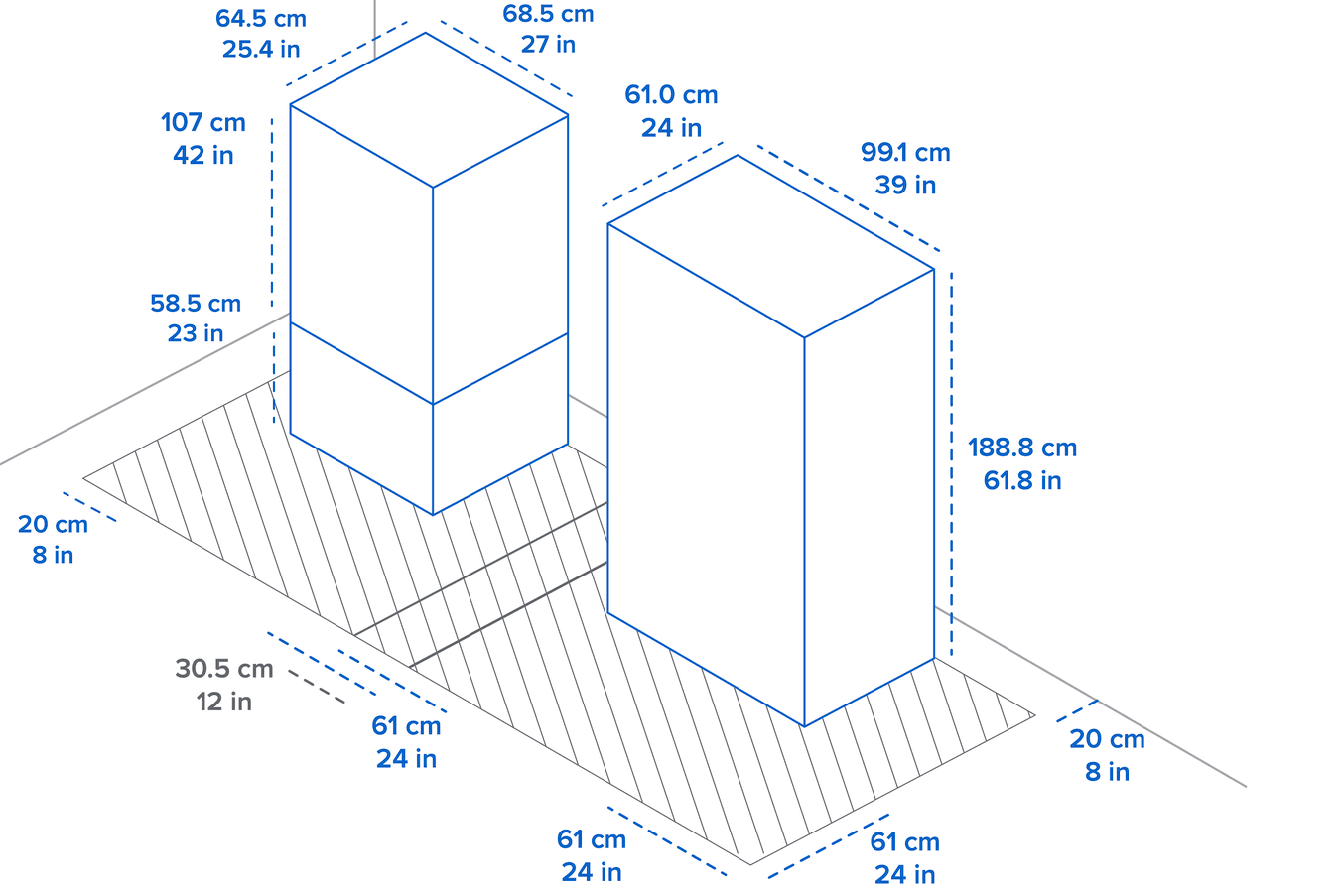
The clearances and access points might change if you scale up with machines (i.e. if you have four Fuse 1 printers lined up on a wall, you only need 30.5cm (12in) between them), but the cardinal rules to remember are:
-
Fuse 1 dimensions: Depth(64.5cm) x H(107cm) x W(68.5cm)
-
Clearance for Fuse 1:
-
20 cm (8in) away from any wall (side and back)
-
61 cm (24in) for door access, opening to the left
-
30.5 (12in) cm from the edge of an open door to the next machine
-
-
Fuse Sift dimensions: Depth(61cm) x H(188.8 cm) x W(99.1 cm) (24in x 61.8in x 39in)
-
Clearance for Fuse Sift:
-
20 cm (8in) away from any wall (side and back)
-
61 cm (24in) for access on front, left, and right (for vacuum, powder cartridges, etc)
-
In a space 4.56m (14.9ft) wide (measuring from left to right), you can fit two separate materials workflows: two Fuse 1 printers and two Fuse Sift units.
For complete workspace requirements, visit our Site Prep Guide.
Electrical Power
Because the Fuse 1 and Fuse Sift are built for compactness and efficiency, they don’t require the same high-level electrical power as other SLS systems. Though you’ll need one circuit for each machine, the wattage required is commonly found, and easily installed.
You’ll need:
-
Two independent circuits, each supplying 120 volts and at least 15 amps to a NEMA 5-20R socket.
-
The Fuse 1 and Fuse Sift cannot share a single circuit with each other, or any other appliance.
-
If your vacuum will draw more than 12 amps, your Fuse Sift will need an independent circuit supplying 120 volts and 20 amps to a NEMA 5-20R socket.
Connection: Internet, Software, and Dashboard
The Fuse 1 and Fuse Sift are easily added to your existing network–equipped with both ethernet and WiFi capabilities. New SLS users don’t need to purchase expensive software for managing the printers–the Fuse 1 and Fuse Sift are integrated into Formlabs’ free print orientation software, PreForm, which is CAD-agnostic.
PreForm also makes it easy to optimize powder usage (and thus minimize operating costs) through its automated packing algorithm, which ensures that each part is nested into the build chamber in a way that minimizes unsintered powder and wasted space.
There are also direct integrations for programs like Fusion 360, so that the integration and print preparation portion of your workflow is seamless and not time consuming. For businesses who have scaled up their SLS production, managing powder and maintenance schedules, starting prints remotely, and sharing files and print progress with your team is easy through Dashboard, a free online platform.
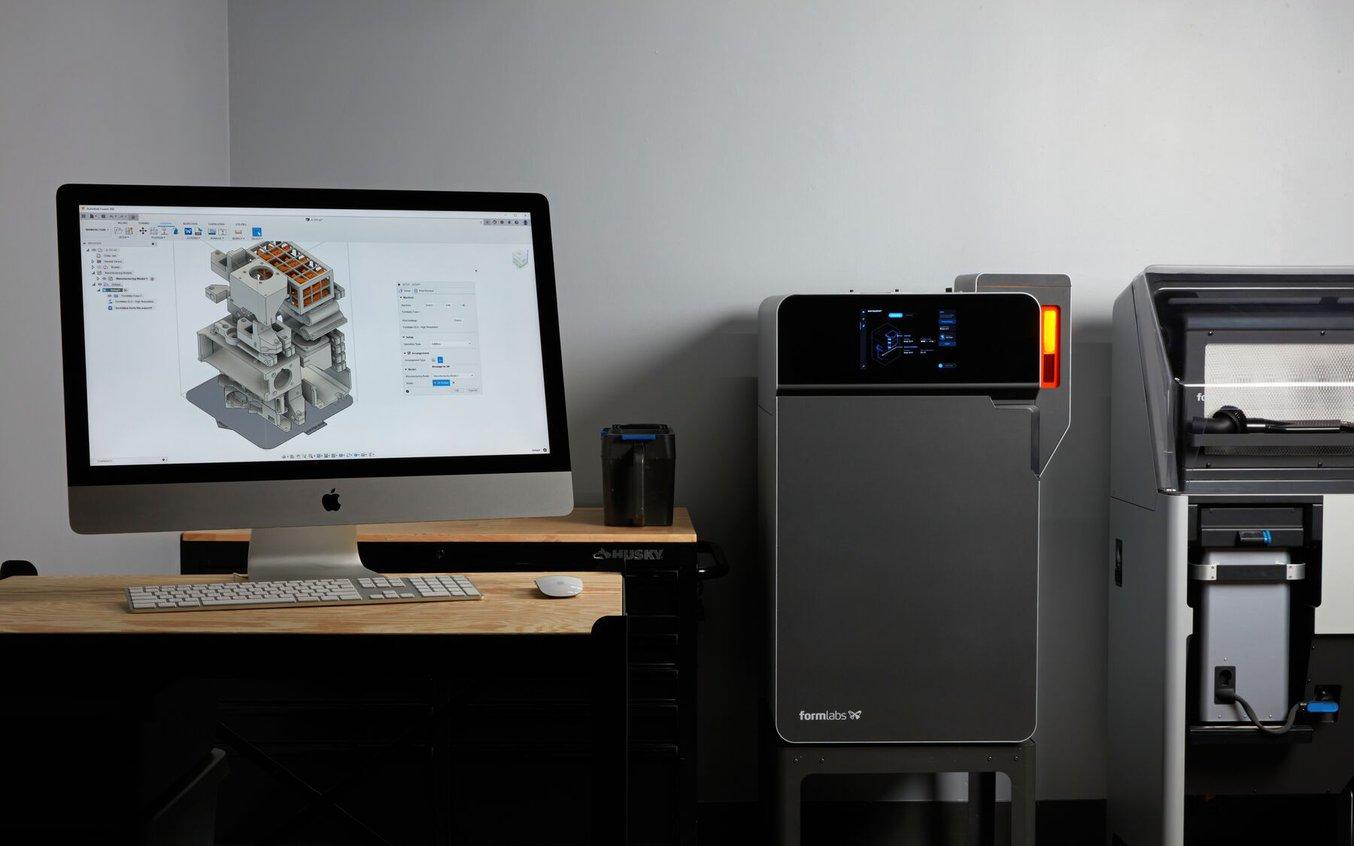
Fuse Sift: Mess-Free De-Powdering
A major factor holding customers back from SLS printing is the typically complicated and messy post-processing step. The biggest concern is often the powder itself, both in terms of safety and for the mess it can create.
The Fuse 1 and Fuse Sift take that concern off the table by enclosing most of the powder-handling steps (powder recovery, preparation, transportation and storage), limiting user interaction with the powder.
The Fuse Sift also creates a safe environment under the work hood for removing the parts from the powder cake (the body of partially sintered powder surrounding the parts) and removing excess unsintered powder. Post-processing parts used to require a technician, but the Fuse Sift makes it easy for anyone to clean powder using the set of tools provided–and even takes care of the declumping for you.
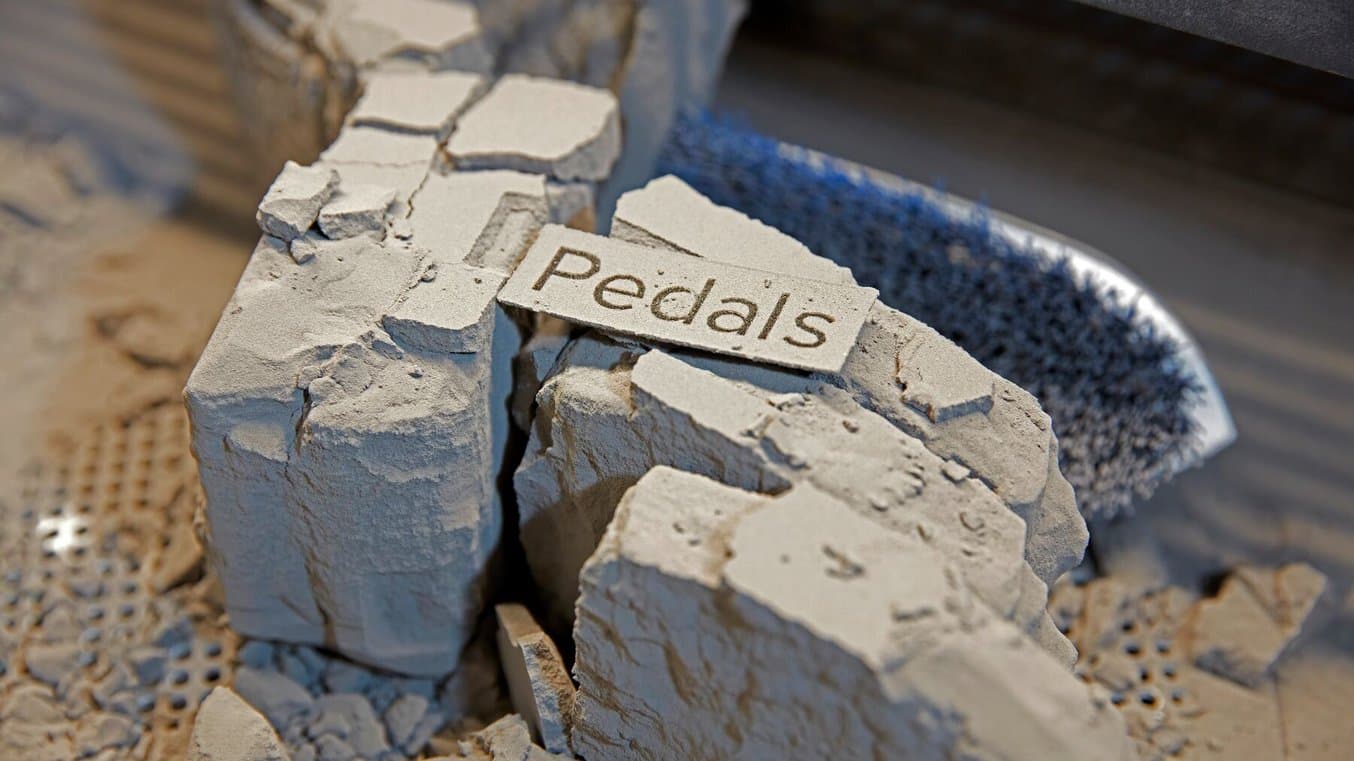
The powder cake breaks apart easily inside the Fuse Sift’s hooded workspace.
The HEPA filter provides a consistent pull, creating a negative air flow within the Fuse Sift hood–any powder particles that do rise up into the air are swiftly pulled down and away from the hood and user. The Fuse Sift Vacuum attachment makes cleaning tools easy, and when done post-processing, the user can store those tools inside the Fuse Sift for a clean and confined workspace.
The powder recovery, recycling, and mixing stage is set-up so that every user can get the most out of their printer and materials. From beginning to end, the workflow guides you through refresh rate, packing density, and powder mixing, so that there is as little waste as possible. You can see your packing density on PreForm, as well as how much recycled and fresh powder you’re using on each print. After the print is done, the Fuse Sift will walk you through the mixing process on its screen, and deliver a freshly mixed cartridge, ready for your next print.
Ongoing Maintenance: Service, Cleaning, Material Changeover
When purchasing a new piece of equipment, initial purchase cost may be top of mind, but it isn’t the only factor to consider. Many SLS printers come with mandatory service contracts at price points in the tens of thousands of dollars, and complicated maintenance schedules that require dedicated technicians or extensive training.
The Fuse 1 has two options for yearly service plans, to ensure that every customer can receive the level of support and training they need.
Part of what makes the Fuse 1 workflow truly an industrial solution in an accessible format is the low-frequency upkeep and maintenance. The only repeated tasks through the year (in between annual on-site checkups conducted by trained service technicians) are replacing the exhaust filter and HEPA filters in the Fuse 1 and Fuse Sift, and wiping down the Fuse 1 optical component in between prints, which generally takes about two minutes.
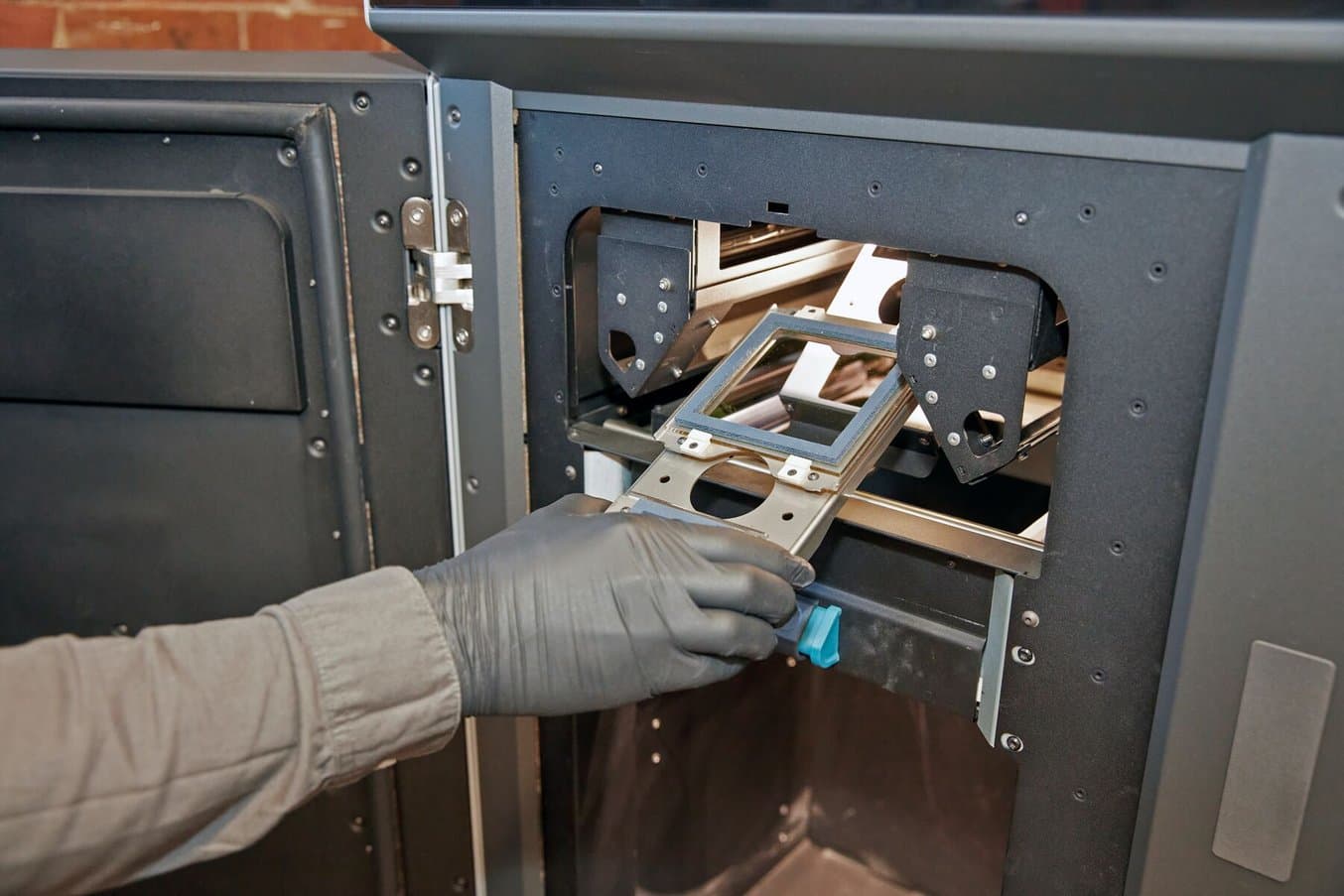
Wiping down the optical cassette is easy and quick.
Using Multiple Materials
Formlabs is committed to expanding access to digital fabrication, and we know broad ranges of mechanical and optical properties are what enables customers to innovate. To that end, the SLS materials library now includes multiple options for materials on the Fuse 1 printer: Nylon 12 Powder, Nylon 11 Powder, and Nylon 12 GF Powder, with more to come.
Many SLS systems don’t support multi-material usage on printers, or mandate a cleaning protocol that can take up to two days for the user to complete.
The Fuse 1 and Fuse Sift can be used for more than one Formlabs material, and we’ve provided detailed cleaning instructions to prepare the printer and Fuse Sift for a new powder type. This switchover process should be completed thoroughly, but even with a total time of four hours, is still simpler and easier than with most SLS systems. That time can be even further reduced when switching between Nylon 12 Powder and Nylon 12 GF Powder. Due to their similar base consistency, when switching between these two materials, the cleaning process should only take about two hours. Compared to single-material systems, or complex industrial printer protocols, being able to produce parts in more than one SLS powder, on a single machine, opens up new possibilities for customers.
Post Processing
Post-processing is made easy by the Fuse Sift, including the de-caking, powder removal, and powder recycling/mixing stages. But what about after parts are de-powdered and post-processed?
We know that many applications require incredibly smooth surfaces, and necessitate an extra step after using the Fuse Sift. Media blasting and vapor smoothing are two processes that many customers use to create smoother finishes on the parts, and improve porosity and water tightness as well as overall aesthetics for end-use parts.
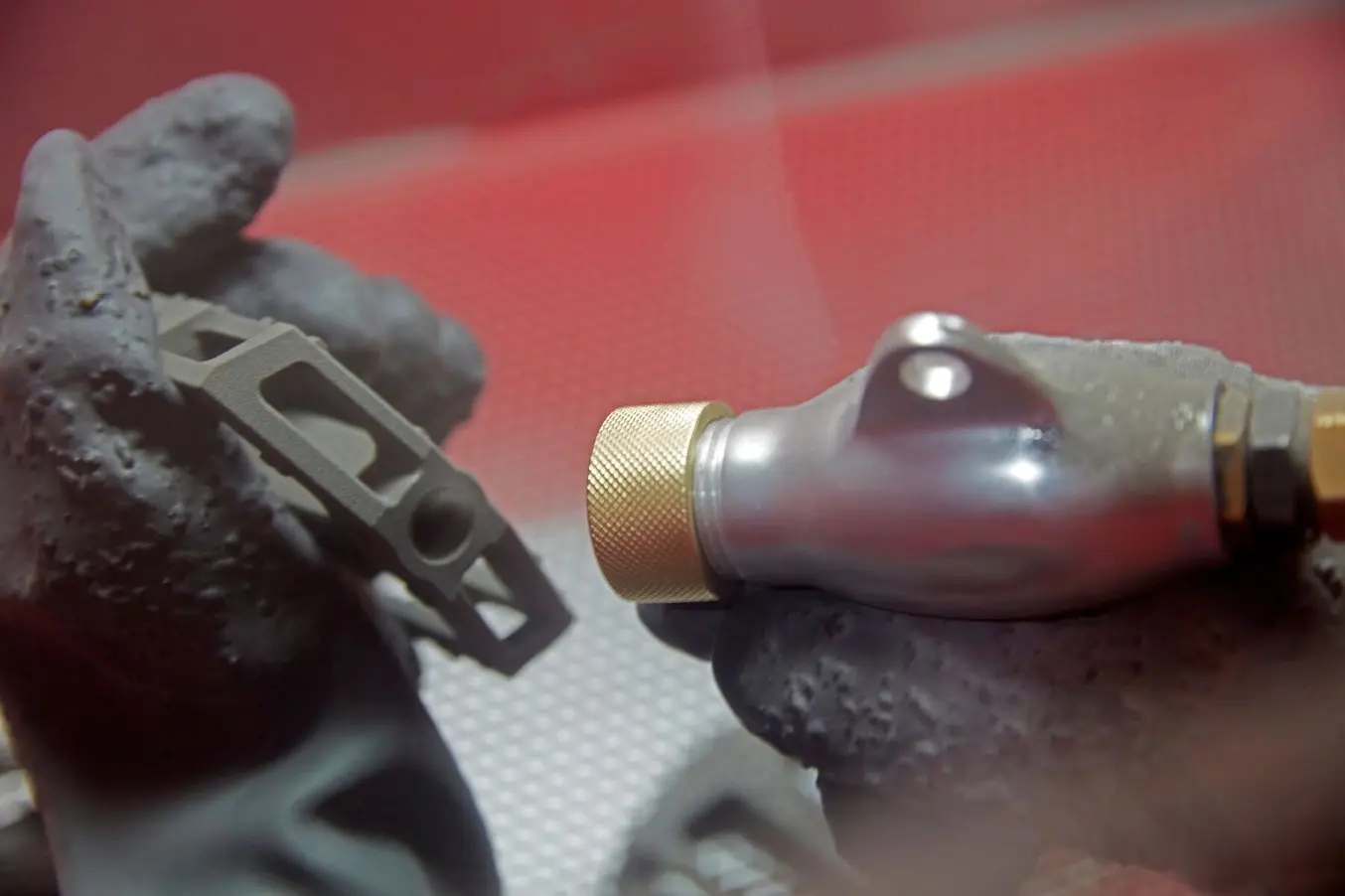
Sand blasting a Fuse 1 part.
Media blasting cabinets are quite affordable, and can be purchased for as little as $200. They should be kept in a separate room or workspace from the Fuse 1, and blasting material should be stored separately, away from Fuse 1 powders.
Vapor smoothing is a process wherein acetone vapor is used to smooth the surface of plastic parts, removing surface lines or divots, and creating a more slick surface. Vapor smoothing can be done by hand inexpensively, but the vast majority of customers send their parts out to be industrially treated.
Safety
One common misconception is that the powder particles are dangerous and can cause harm to the user’s lungs. This concern stems from a different 3D printing technology–fused deposition modeling (FDM) can emit tiny particles that float in the air and when inhaled, can cause harm.
Fuse 1 powders however, have a much larger particle size (40 microns in diameter) and are thus too heavy to lift easily into the air. They stay contained within the Fuse Sift because they’re too large to ride air currents into the user’s breathing environment.
The Fuse 1 and Fuse Sift also utilize industry standard HEPA filters that provide feedback to internal sensors, alerting the user to low filter performance, and prompting a filter change.
Those unfamiliar with SLS workflows might see the recommended N95 mask and gloves, and assume that the powder is toxic, like some of the vapors created during an FDM printing process. However, due to the large particle size, the industry standard HEPA and exhaust filters, and the semi-enclosed workspace, operating the Fuse 1 and Fuse Sift is safe for indoor use, and can be done in educational settings, research labs, office environments, and creative studios, as well as more traditional industrial settings.
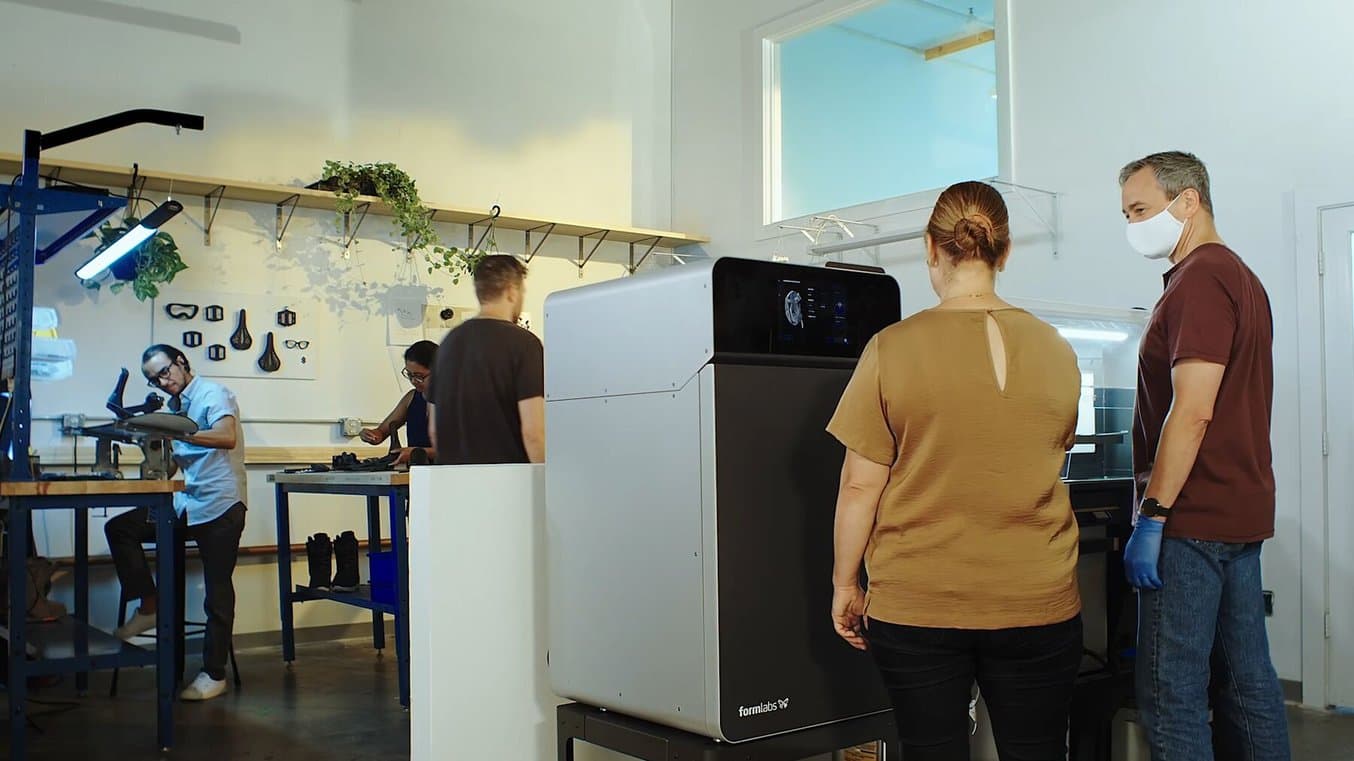
Scaling Up
The points outlined above are as relevant in a single-printer conversation as they are when considering scaling up with multiple machines. The Fuse 1 and Fuse Sift are ideal for manufacturing scenarios, or iterative prototyping because of their:
-
Size: easy to deliver in non-industrial environments, easy to set-up
-
Price: economical to use for existing workflows, affordable to scale
-
Low maintenance: infrequent and easy maintenance tasks, excellent support
-
Material variability: multiple materials enable greater production flexibility
-
Safety: utilize industry-standard filters, sensing systems, and enclosed workflows keep the user safe and separate
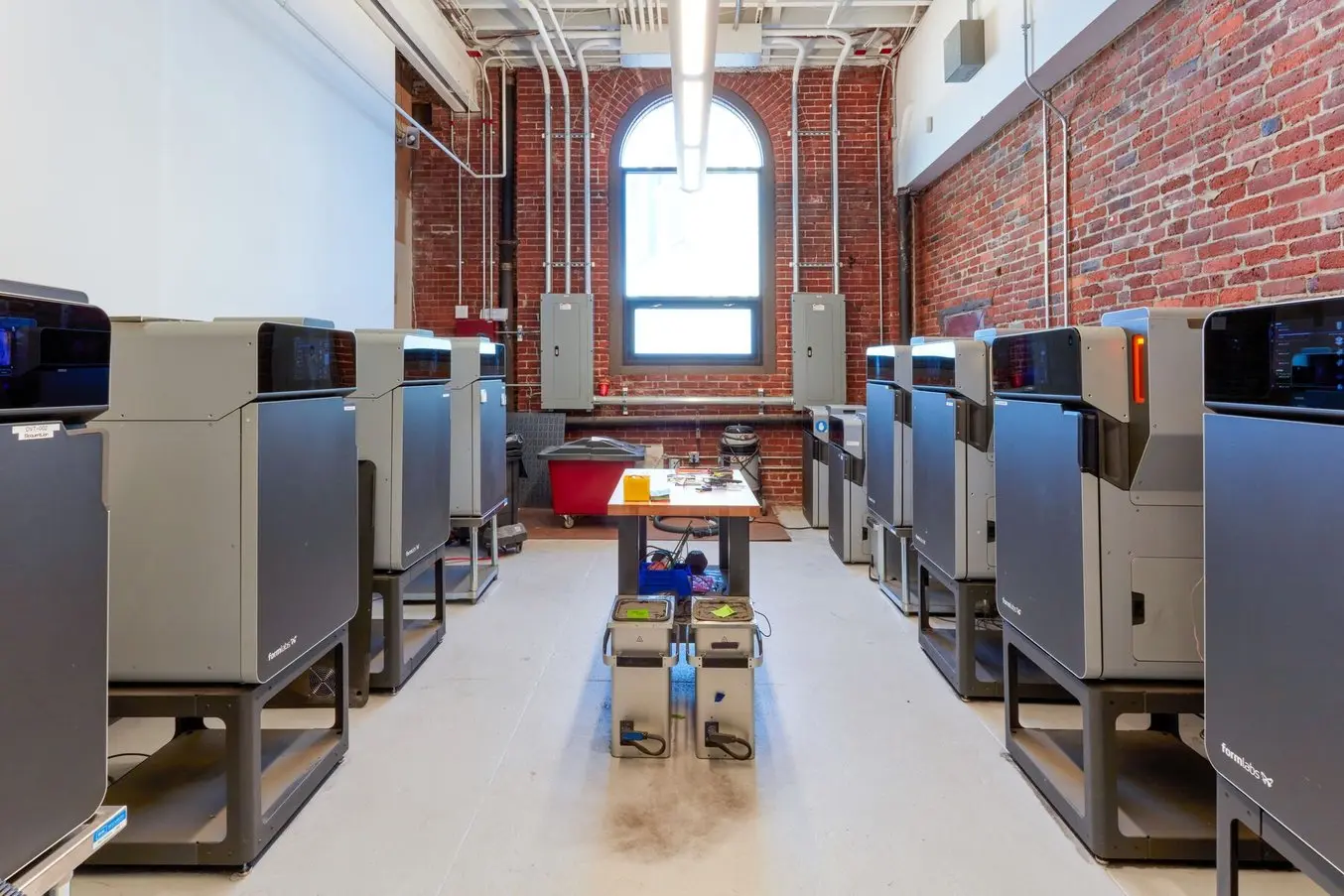
Talk to the Experts
The Fuse 1 printer and Fuse Sift are intuitively designed, and made to be utilized by customers both familiar with SLS printing or totally new to the technology. But if you have any questions regarding workflow, particular applications, or infrastructure requirements, our team of SLS experts is available for in-depth demonstrations and precise ROI calculations, inputting your own parts and production schedule.
Formlabs is proud that so many of our customers have scaled production with the Fuse 1. To hear from them, and see real-life examples of the printers in action, check out our story on Manhattan service bureau PrintParts or custom car manufacturer Vital Auto. To see how the SLS 3D printing market is growing across the globe, read our 3D Printing Applications Report.